Your Ultimate Guide to Sourcing Vending Machines Warehouse
Guide to Vending Machines Warehouse
- Introduction: Navigating the Global Market for vending machines warehouse
- Understanding vending machines warehouse Types and Variations
- Key Industrial Applications of vending machines warehouse
- Strategic Material Selection Guide for vending machines warehouse
- In-depth Look: Manufacturing Processes and Quality Assurance for vending machines warehouse
- Comprehensive Cost and Pricing Analysis for vending machines warehouse Sourcing
- Spotlight on Potential vending machines warehouse Manufacturers and Suppliers
- Essential Technical Properties and Trade Terminology for vending machines warehouse
- Navigating Market Dynamics, Sourcing Trends, and Sustainability in the vending machines warehouse Sector
- Frequently Asked Questions (FAQs) for B2B Buyers of vending machines warehouse
- Strategic Sourcing Conclusion and Outlook for vending machines warehouse
Introduction: Navigating the Global Market for vending machines warehouse
In today’s fast-paced consumer environment, vending machines have emerged as vital tools for businesses seeking to enhance accessibility and convenience. For B2B buyers, especially those operating in Africa, South America, the Middle East, and Europe, understanding the intricacies of vending machine warehouses is critical to making informed purchasing decisions. This guide serves as an essential resource, equipping buyers with the knowledge necessary to navigate the complexities of sourcing vending machines effectively.
A well-structured vending machines warehouse not only streamlines the procurement process but also ensures that businesses can offer their customers a diverse range of products. This guide comprehensively covers various aspects, including types of vending machines, materials used, manufacturing and quality control processes, reliable suppliers, and cost considerations. Additionally, it delves into market trends and addresses frequently asked questions that can assist buyers in their decision-making journey.
By empowering international B2B buyers with actionable insights and industry knowledge, this guide aims to facilitate strategic sourcing and enhance operational efficiency. Whether you are expanding into new markets or optimizing existing vending operations, understanding the dynamics of vending machines warehouses will provide you with a competitive edge in today’s global marketplace.
Understanding vending machines warehouse Types and Variations
Type Name | Key Distinguishing Features | Primary B2B Applications | Brief Pros & Cons for Buyers |
---|---|---|---|
Traditional Vending Machines | Standard machines for snacks and beverages | Offices, schools, public spaces | Pros: Familiar technology, easy maintenance. Cons: Limited product variety, less engaging. |
Smart Vending Machines | Equipped with touch screens and cashless payment options | Retail, transportation hubs | Pros: Enhanced customer experience, real-time inventory tracking. Cons: Higher initial investment, requires tech support. |
Health-Conscious Vending Machines | Focused on healthier food and beverage options | Gyms, hospitals, schools | Pros: Appeals to health-conscious consumers, promotes wellness. Cons: Potentially lower sales if not marketed well. |
Customized Vending Solutions | Tailored machines for specific products (e.g., electronics) | Specialty stores, events | Pros: Meets niche market demands, unique offerings. Cons: Higher costs, longer lead times for production. |
Automated Retail Kiosks | Advanced vending solutions that offer a wide range of products | Airports, shopping malls, events | Pros: 24/7 operation, diverse product range. Cons: Complex logistics, maintenance challenges. |
Traditional Vending Machines
Traditional vending machines are the most common type, typically offering snacks and beverages. They are straightforward in design and operation, making them suitable for a wide range of environments like offices, schools, and public spaces. Buyers should consider their maintenance needs and product selection, as these machines often have limited offerings. While they are generally cost-effective, they may not attract as much consumer engagement compared to more innovative options.
Smart Vending Machines
Smart vending machines incorporate modern technology such as touch screens and cashless payment systems. They are particularly useful in retail and transportation hubs where customer experience is paramount. These machines allow for real-time inventory management and can offer personalized promotions. However, they require a higher initial investment and ongoing technical support, making them a consideration for businesses looking to enhance their service offerings.
Health-Conscious Vending Machines
Focusing on healthier food and beverage options, health-conscious vending machines cater to a growing market of health-aware consumers. They are ideal for placement in gyms, hospitals, and schools where wellness is a priority. While they can attract a niche audience, buyers must effectively market these machines to ensure adequate sales. The investment in these machines could yield higher returns if aligned with consumer health trends.
Customized Vending Solutions
Customized vending solutions are tailored to meet specific market demands, such as electronics or specialty foods. These machines are often found in specialty stores or at events where unique product offerings can draw attention. While they can fulfill niche needs and stand out in a crowded market, buyers must be aware of the higher costs and longer lead times associated with these bespoke solutions.
Automated Retail Kiosks
Automated retail kiosks represent the next evolution in vending technology, offering a wide array of products, from snacks to electronics, in a retail format. They are particularly effective in high-traffic areas like airports and shopping malls, operating around the clock. However, the complexity of logistics and maintenance can pose challenges for businesses. Buyers should weigh the benefits of diverse product offerings against the operational demands of these kiosks.
Related Video: My New $500,000 Vending Business Warehouse!
Key Industrial Applications of vending machines warehouse
Industry/Sector | Specific Application of vending machines warehouse | Value/Benefit for the Business | Key Sourcing Considerations for this Application |
---|---|---|---|
Retail | Automated retail for convenience products | Increased sales through 24/7 availability | Machine reliability, product variety, payment options |
Healthcare | Dispensing medical supplies | Quick access to essential items for patients | Compliance with health regulations, inventory management |
Education | Snack and beverage vending for schools | Improved student satisfaction and retention | Nutrition standards, machine placement, cashless payment options |
Transportation | On-the-go snacks and drinks at transit hubs | Enhanced passenger experience, increased revenue | Space constraints, product selection, machine durability |
Hospitality | Mini-bar vending solutions in hotels | Increased guest satisfaction, reduced staffing costs | Product variety, machine aesthetics, inventory turnover rate |
Retail
In the retail sector, vending machines warehouses serve as automated retail solutions, offering convenience products ranging from snacks to electronics. They provide businesses with the ability to operate 24/7, increasing sales opportunities without the need for additional staff. International B2B buyers should focus on sourcing machines that offer a variety of payment options, including cashless transactions, to cater to diverse customer preferences. Additionally, machine reliability is crucial to ensure consistent operation and minimize downtime.
Healthcare
Healthcare facilities utilize vending machines warehouses to dispense medical supplies, such as personal protective equipment (PPE) and first-aid kits. This application addresses the need for quick access to essential items, especially in emergencies. Buyers in this sector must ensure that the machines comply with health regulations and are capable of managing inventory effectively to avoid stockouts. Furthermore, machines should be designed for easy sanitization to meet hygiene standards.
Education
In educational institutions, vending machines warehouses provide snack and beverage options for students, enhancing their overall experience and satisfaction. These machines can be strategically placed in high-traffic areas to maximize usage. When sourcing for this application, B2B buyers should consider nutrition standards to promote healthy eating habits among students. Additionally, cashless payment options can streamline transactions and make the process more efficient.
Transportation
Transportation hubs like airports and bus stations benefit from vending machines warehouses by offering on-the-go snacks and drinks to travelers. This application improves the passenger experience and generates additional revenue for operators. Buyers should evaluate the space constraints of the location when selecting vending machines and consider product selection that caters to a diverse customer base. Durability is also key, as machines must withstand high traffic and potential vandalism.
Hospitality
In the hospitality sector, vending machines warehouses can serve as mini-bar solutions in hotels, providing guests with easy access to snacks and beverages. This application enhances guest satisfaction while reducing the need for extensive staffing. When sourcing machines for this purpose, buyers should focus on product variety and aesthetics to align with the hotel’s branding. Additionally, understanding inventory turnover rates is essential to optimize stock levels and minimize waste.
Related Video: Kooler Ice Vending Machines – IM600XL vs. IM1000
Strategic Material Selection Guide for vending machines warehouse
Material Analysis for Vending Machines Warehouse
When selecting materials for vending machines warehouses, it’s crucial to consider properties such as durability, corrosion resistance, and compatibility with various media. Here, we analyze four common materials used in the construction and operation of vending machines, focusing on their key properties, advantages, disadvantages, and implications for international B2B buyers.
1. Stainless Steel (e.g., 304 and 316 grades)
Key Properties: Stainless steel is known for its excellent corrosion resistance, particularly in humid or moist environments. Grades 304 and 316 offer good temperature ratings, with 316 providing enhanced resistance to chlorides.
Pros & Cons: The primary advantage of stainless steel is its durability and resistance to rust and corrosion, making it suitable for various environments. However, it is generally more expensive than carbon steel and can be challenging to machine due to its hardness.
Impact on Application: Stainless steel is compatible with a wide range of products, including food and beverages, making it ideal for vending machines. Its non-reactive nature ensures that it does not alter the taste or quality of the products stored within.
Considerations for International Buyers: Buyers from regions like Europe and the Middle East should ensure compliance with local food safety standards (e.g., EU regulations) and consider the specific grades required for their applications. Common standards such as ASTM and DIN are applicable.
2. Carbon Steel (e.g., A36)
Key Properties: Carbon steel is characterized by its strength and toughness. It has a lower corrosion resistance compared to stainless steel and is typically rated for moderate temperatures and pressures.
Pros & Cons: The cost-effectiveness of carbon steel makes it a popular choice for structural components of vending machines. However, its susceptibility to rust and corrosion means it often requires protective coatings, which can add to the overall cost and complexity of manufacturing.
Impact on Application: Carbon steel is suitable for non-corrosive environments. Its use in vending machines is generally limited to structural components rather than areas in direct contact with food or beverages.
Considerations for International Buyers: Buyers should be aware of the need for protective coatings in humid environments, particularly in regions like Africa and South America. Compliance with relevant standards (e.g., ASTM A36) is essential to ensure product quality.
3. Aluminum Alloys (e.g., 6061-T6)
Key Properties: Aluminum alloys are lightweight and have good corrosion resistance, particularly when anodized. They can withstand a range of temperatures and pressures but are less strong than steel.
Pros & Cons: The lightweight nature of aluminum makes it easy to handle and install. However, its lower strength compared to steel can be a limitation in high-stress applications, and it is typically more expensive than carbon steel.
Impact on Application: Aluminum is often used in the exterior casing of vending machines due to its aesthetic appeal and resistance to corrosion. It is also suitable for applications where weight is a concern.
Considerations for International Buyers: Buyers should ensure that the aluminum used meets local standards (e.g., JIS in Japan or EN in Europe) and consider the specific alloy grades that offer the best performance for their needs.
4. High-Density Polyethylene (HDPE)
Key Properties: HDPE is a thermoplastic known for its high strength-to-density ratio and excellent chemical resistance. It performs well in a wide range of temperatures and is highly impact-resistant.
Pros & Cons: The primary advantage of HDPE is its resistance to corrosion and chemicals, making it ideal for various applications. However, it may not provide the same structural strength as metals, which could limit its use in load-bearing applications.
Impact on Application: HDPE is often used for internal components of vending machines, such as product trays and storage bins, due to its lightweight and durable nature.
Considerations for International Buyers: Compliance with food safety standards is crucial for applications involving food products. Buyers should also check for relevant certifications (e.g., FDA compliance in the U.S.) and consider the availability of HDPE in their region.
Summary Table
Material | Typical Use Case for vending machines warehouse | Key Advantage | Key Disadvantage/Limitation | Relative Cost (Low/Med/High) |
---|---|---|---|---|
Stainless Steel (e.g., 304) | Exterior and interior components, food contact | Excellent corrosion resistance | Higher cost, machining complexity | High |
Carbon Steel (e.g., A36) | Structural components | Cost-effective, good strength | Susceptible to corrosion, requires coating | Low |
Aluminum Alloys (e.g., 6061) | Exterior casing, lightweight components | Lightweight, good corrosion resistance | Lower strength compared to steel | Medium |
High-Density Polyethylene (HDPE) | Internal trays and bins | Excellent chemical resistance, lightweight | Limited load-bearing capacity | Medium |
This analysis provides actionable insights for international B2B buyers, enabling informed decisions regarding material selection for vending machines warehouses.
In-depth Look: Manufacturing Processes and Quality Assurance for vending machines warehouse
Manufacturing vending machines involves several critical stages, each essential for ensuring that the final product meets quality standards and operates efficiently. Understanding these processes is vital for B2B buyers, particularly those from diverse regions like Africa, South America, the Middle East, and Europe.
Manufacturing Processes
1. Material Preparation
The manufacturing process begins with the selection and preparation of materials. Key components typically include:
- Metal Sheets: Used for the casing and structural framework.
- Plastic Components: Employed for the display panels and internal mechanisms.
- Electronic Parts: Including payment systems, sensors, and controllers.
Before fabrication, materials undergo thorough inspection to ensure they meet specified standards. Buyers should request material certifications from suppliers to verify compliance with international standards.
2. Forming
Once materials are prepared, they are shaped into parts using various techniques:
- Laser Cutting: This method provides precision in shaping metal sheets and plastic components.
- Bending: Metal sheets are bent to create the frame of the vending machine.
- Injection Molding: Used for creating plastic parts, ensuring uniformity and durability.
Using advanced forming techniques not only enhances product quality but also reduces waste, aligning with sustainability goals.
3. Assembly
The assembly phase is where all components come together. This stage includes:
- Mechanical Assembly: Joining the metal frame with plastic parts and installing internal mechanisms.
- Electrical Assembly: Integrating electronic components, including wiring and control systems.
- Software Integration: Programming the vending machine’s operating system and payment processing functionalities.
Efficient assembly lines often employ Lean Manufacturing principles to minimize waste and optimize productivity. B2B buyers should consider suppliers that utilize these methodologies, as they often lead to faster turnaround times and lower costs.
4. Finishing
The final stage is finishing, which enhances the machine’s aesthetics and durability. This includes:
- Painting and Coating: Protective coatings are applied to prevent corrosion and wear.
- Quality Checks: Final inspections ensure that each unit meets design specifications and functionality.
Buyers should inquire about finishing techniques and materials used, as these can significantly impact the product’s lifespan and operational reliability.
Quality Assurance
Implementing a robust quality assurance (QA) system is crucial for maintaining high manufacturing standards. Here are the main components of a comprehensive QA process:
International Standards
Several international standards guide quality assurance in manufacturing:
- ISO 9001: This standard focuses on quality management systems and is essential for ensuring consistent product quality.
- CE Marking: Required in the European market, it indicates that the product meets health, safety, and environmental protection standards.
- API Standards: Relevant for electronic components, ensuring reliability and safety.
B2B buyers should confirm that their suppliers are certified under these standards, as this reflects a commitment to quality.
QC Checkpoints
Quality control (QC) involves several key checkpoints throughout the manufacturing process:
- Incoming Quality Control (IQC): Inspection of raw materials before production begins.
- In-Process Quality Control (IPQC): Ongoing checks during manufacturing to catch defects early.
- Final Quality Control (FQC): Comprehensive testing of the finished product to ensure it meets all specifications.
Implementing these checkpoints helps identify potential issues early, reducing the risk of defective products reaching the market.
Common Testing Methods
Testing methods vary based on the components being inspected, but may include:
- Functional Testing: Ensuring the vending machine operates correctly, including payment processing and dispensing mechanisms.
- Durability Testing: Assessing the machine’s ability to withstand environmental factors like humidity, temperature, and mechanical stress.
- Safety Testing: Verifying that the machine complies with electrical safety standards.
Buyers should request detailed testing reports from suppliers to ensure transparency and accountability.
Verifying Supplier Quality Control
For international B2B buyers, verifying the quality control processes of potential suppliers is critical. Here are effective strategies to ensure quality:
- Supplier Audits: Conduct on-site audits to assess manufacturing practices, QA systems, and compliance with standards.
- Quality Reports: Request regular quality assurance reports, including IQC, IPQC, and FQC documentation.
- Third-Party Inspections: Engage independent inspection agencies to evaluate the manufacturing process and product quality. This is particularly beneficial for buyers from regions like Africa and South America, where local regulations may differ.
Navigating QC and Certification Nuances
International buyers must be aware of the nuances in quality control and certification processes across different markets. For example:
- European Union: Strict CE marking requirements necessitate rigorous testing and compliance checks.
- Middle Eastern Markets: May have additional certifications related to energy efficiency and environmental impact.
- African Markets: Buyers should consider local standards and certifications, which may vary significantly by country.
It’s crucial for B2B buyers to communicate their specific quality requirements and certifications needed based on their target market. This proactive approach helps avoid delays and ensures compliance with local regulations.
Conclusion
Understanding the manufacturing processes and quality assurance measures for vending machines is essential for B2B buyers. By focusing on material preparation, forming, assembly, and finishing, along with a robust QA framework, buyers can make informed decisions that align with their operational needs and market expectations. Engaging with suppliers who prioritize quality and compliance will ultimately lead to successful partnerships and satisfied customers.
Related Video: Most Satisfying Factory Production Processes And Heavy-Duty Factory Machines!
Comprehensive Cost and Pricing Analysis for vending machines warehouse Sourcing
When sourcing vending machines, understanding the cost structure and pricing dynamics is crucial for international B2B buyers, especially in regions like Africa, South America, the Middle East, and Europe. This analysis will help you navigate the complexities of vending machine warehouse sourcing effectively.
Cost Components
-
Materials: The primary cost driver in vending machine production includes the raw materials used, such as metals for the chassis, plastics for the casing, and electronic components for operation. Sourcing high-quality materials can significantly impact the overall cost.
-
Labor: Labor costs vary by region and can include direct labor for assembly and indirect labor for support functions. Regions with lower wage structures may offer competitive pricing, but it’s essential to consider the skill level and training of the workforce.
-
Manufacturing Overhead: This encompasses the indirect costs associated with production, such as utilities, rent, and administrative expenses. Efficient manufacturing processes can help reduce these overhead costs.
-
Tooling: Investment in tooling is necessary for producing vending machines. Custom tooling for unique designs can increase upfront costs but may yield long-term savings through improved production efficiency.
-
Quality Control (QC): Implementing robust QC processes ensures product reliability and compliance with international standards. While this may add to the cost, it can prevent expensive recalls and enhance brand reputation.
-
Logistics: Transportation and warehousing costs are significant, particularly for international shipping. Factors like distance, shipping method, and Incoterms can greatly influence logistics expenses.
-
Margin: Suppliers typically add a margin to cover their costs and profit. Understanding a supplier’s margin can provide insight into their pricing strategy and flexibility in negotiations.
Price Influencers
-
Volume/MOQ: Minimum Order Quantities (MOQs) can influence pricing. Bulk orders often lead to lower per-unit costs, making it advantageous for buyers to consolidate their purchases.
-
Specifications/Customization: Custom features or specifications can increase costs. Clearly defining your requirements upfront can help suppliers provide accurate quotes and avoid unexpected charges later.
-
Materials and Quality/Certifications: The choice of materials and the level of certification required (e.g., CE marking in Europe) can impact costs. Buyers should weigh the benefits of higher-quality materials against their budget constraints.
-
Supplier Factors: Supplier reputation, reliability, and location can affect pricing. Established suppliers may command higher prices but offer better quality assurance and customer support.
-
Incoterms: Understanding Incoterms is vital for international transactions. They dictate the responsibilities of buyers and sellers regarding shipping, insurance, and tariffs, impacting the total cost of ownership.
Buyer Tips
-
Negotiation: Effective negotiation can significantly reduce costs. Prepare by researching market prices, understanding your supplier’s cost structure, and being clear about your budget constraints.
-
Cost-Efficiency: Look beyond initial purchase prices to the Total Cost of Ownership (TCO). Consider long-term factors like maintenance, energy consumption, and potential downtime when evaluating vendors.
-
Pricing Nuances: Be aware of regional pricing variations. For example, suppliers in Europe may have different cost structures than those in Africa or South America due to labor and regulatory environments.
-
Local Regulations: Familiarize yourself with import regulations and tariffs that may affect the final cost. Compliance with local laws can also help avoid delays and additional costs.
- Supplier Relationships: Building strong relationships with suppliers can lead to better pricing and terms. Consider long-term partnerships that may offer benefits like preferred pricing or priority service.
Disclaimer
Prices can vary widely based on factors like location, supplier, and market conditions. Always obtain multiple quotes and conduct thorough due diligence before making purchasing decisions to ensure you receive the best value for your investment.
Spotlight on Potential vending machines warehouse Manufacturers and Suppliers
This section offers a look at a few manufacturers active in the ‘vending machines warehouse’ market. This is a representative sample for illustrative purposes; B2B buyers must conduct their own extensive due diligence before any engagement. Information is synthesized from public sources and general industry knowledge.
Essential Technical Properties and Trade Terminology for vending machines warehouse
In the context of vending machine warehouses, understanding key technical properties and trade terminology is crucial for international B2B buyers. This knowledge facilitates informed decision-making and optimizes procurement processes, especially for buyers from diverse markets such as Africa, South America, the Middle East, and Europe.
Essential Technical Properties
-
Material Grade
– Definition: Refers to the type and quality of materials used in the construction of vending machines, often categorized by strength, durability, and resistance to corrosion.
– Importance: High-quality materials ensure longevity and reliability, reducing maintenance costs and downtime. Buyers should prioritize vendors that provide detailed material specifications to ensure compliance with local regulations and standards. -
Tolerance Levels
– Definition: Tolerance levels indicate the allowable variation in dimensions and specifications during the manufacturing process.
– Importance: Precise tolerances are essential for the proper functioning of vending machines, particularly in components that require accurate alignment for mechanical operations. Understanding tolerance levels helps buyers gauge the quality control processes of manufacturers. -
Power Consumption
– Definition: This refers to the amount of energy consumed by the vending machines during operation.
– Importance: Lower power consumption translates into reduced operational costs and enhanced sustainability. Buyers should inquire about energy efficiency ratings to support eco-friendly initiatives. -
Capacity and Dimensions
– Definition: Capacity pertains to the number of products a vending machine can hold, while dimensions refer to its physical size.
– Importance: Buyers must match machine capacities with expected demand and available space. Custom dimensions may be necessary for specific locations, making it essential to clearly communicate requirements to manufacturers. -
Security Features
– Definition: Security features include locks, alarms, and anti-theft mechanisms integrated into the vending machine design.
– Importance: Enhanced security reduces the risk of theft and vandalism, which is particularly crucial in high-traffic or vulnerable locations. Buyers should evaluate the robustness of security features when selecting machines.
Common Trade Terms
-
OEM (Original Equipment Manufacturer)
– Definition: An OEM is a company that produces parts or equipment that may be marketed by another manufacturer.
– Significance: Understanding OEM relationships helps buyers identify reputable manufacturers and potential cost-saving opportunities through partnerships. -
MOQ (Minimum Order Quantity)
– Definition: MOQ refers to the smallest quantity of a product that a supplier is willing to sell.
– Significance: Knowing the MOQ is essential for budgeting and inventory planning. Buyers should negotiate MOQs that align with their procurement strategies to avoid excess inventory costs.
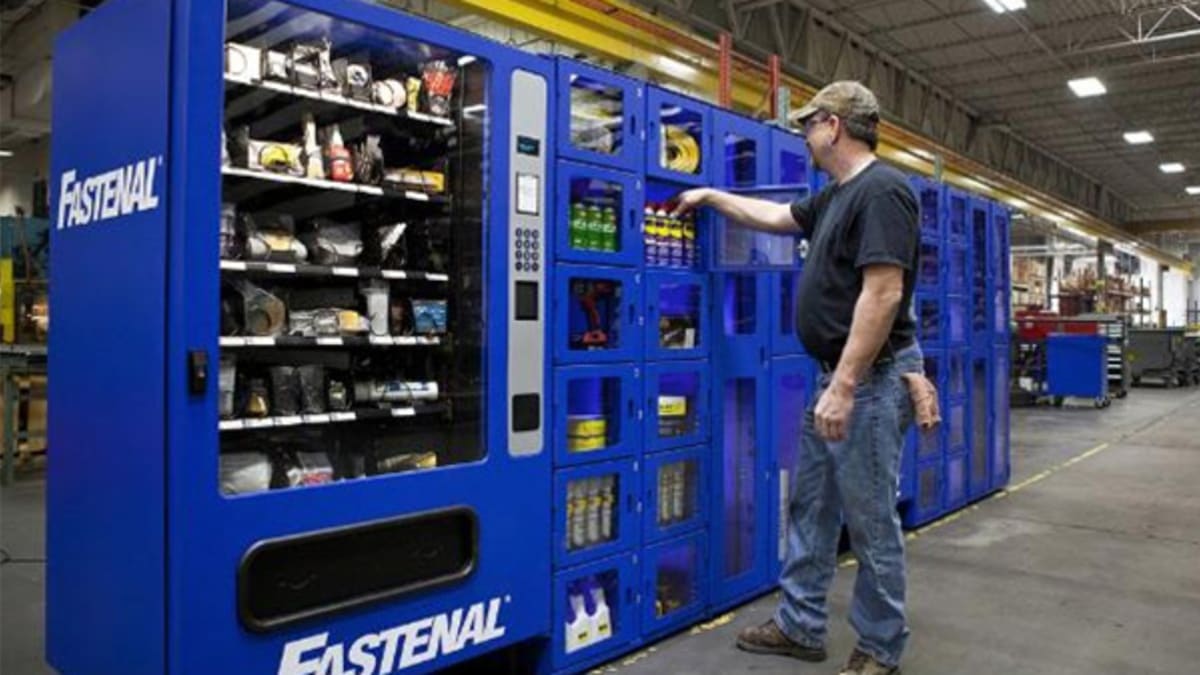
Illustrative Image (Source: Google Search)
-
RFQ (Request for Quotation)
– Definition: An RFQ is a document issued by a buyer requesting pricing information from suppliers for specific products.
– Significance: RFQs streamline the procurement process by providing a standardized method for comparing prices and terms across multiple vendors, facilitating better negotiation outcomes. -
Incoterms (International Commercial Terms)
– Definition: Incoterms are internationally recognized standard terms that define the responsibilities of buyers and sellers in international trade, including shipping, insurance, and tariffs.
– Significance: Familiarity with Incoterms helps buyers clarify shipping responsibilities and costs, reducing the risk of disputes and unexpected charges. -
Lead Time
– Definition: Lead time is the period between the initiation of an order and its completion.
– Significance: Understanding lead times is crucial for effective supply chain management. Buyers should factor in lead times when planning inventory levels to ensure product availability aligns with demand.
By grasping these technical properties and trade terms, international B2B buyers can enhance their decision-making processes, optimize procurement strategies, and ensure successful transactions in the vending machine warehouse sector.
Navigating Market Dynamics, Sourcing Trends, and Sustainability in the vending machines warehouse Sector
Market Overview & Key Trends
The global vending machine warehouse sector is witnessing a transformative phase driven by several key factors. The rise in consumer demand for convenience and instant access to products has led to an increase in vending machine placements across various locations, including airports, offices, and educational institutions. Furthermore, the integration of technology is reshaping the landscape. Contactless payment systems, IoT connectivity, and machine learning are becoming standard features, allowing for real-time inventory management and enhanced customer experiences.
International B2B buyers, particularly from Africa, South America, the Middle East, and Europe, should pay attention to emerging trends such as smart vending solutions that utilize data analytics to optimize product offerings based on consumer preferences. These advancements not only improve operational efficiency but also reduce overhead costs. Moreover, the growing popularity of healthy snacks and beverages reflects changing consumer preferences, prompting vendors to diversify their product ranges to include organic and nutritious options.
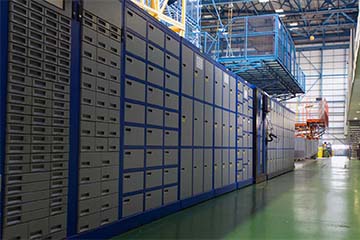
Illustrative Image (Source: Google Search)
Additionally, the market dynamics are influenced by regional factors such as varying economic conditions and regulatory frameworks. For instance, European buyers may focus on compliance with strict environmental regulations, while buyers from emerging markets might prioritize cost-effectiveness and scalability. Understanding these regional nuances is crucial for successful sourcing and partnership strategies.
Sustainability & Ethical Sourcing in B2B
Sustainability has become a central theme in the vending machines warehouse sector, with increasing pressure from consumers and regulatory bodies to adopt eco-friendly practices. The environmental impact of traditional vending machines, particularly concerning energy consumption and waste generation, has prompted a shift toward energy-efficient models that utilize renewable energy sources.
For B2B buyers, prioritizing ethical sourcing is vital. This involves ensuring that suppliers adhere to sustainable practices, such as using recyclable materials and minimizing the carbon footprint throughout the supply chain. Certifications like ISO 14001 for environmental management and LEED for energy-efficient buildings can serve as reliable indicators of a supplier’s commitment to sustainability.
Moreover, the adoption of biodegradable packaging and the sourcing of materials from certified sustainable forests can enhance a company’s reputation while meeting the growing consumer demand for environmentally responsible products. Buyers should actively seek partnerships with suppliers who prioritize sustainability in their operations, as this can significantly impact brand loyalty and market competitiveness.
Brief Evolution/History
The vending machine industry has evolved significantly since its inception in the late 19th century, transitioning from simple coin-operated mechanisms to sophisticated smart machines equipped with advanced technology. Initially designed to dispense simple items like snacks and beverages, the introduction of electronic payment systems in the 1990s marked a pivotal point, enhancing convenience for consumers.
In recent years, the focus has shifted toward integrating smart technology, allowing machines to connect to the internet for real-time data analysis and inventory management. This evolution not only improves operational efficiency but also aligns with contemporary consumer expectations for seamless and personalized shopping experiences. As the sector continues to innovate, international B2B buyers must stay informed about these developments to leverage opportunities in this dynamic market.
Related Video: Global Trade & Logistics – What is Global Trade?
Frequently Asked Questions (FAQs) for B2B Buyers of vending machines warehouse
-
What criteria should I use for vetting suppliers of vending machines?
When vetting suppliers, prioritize their experience in the industry, customer reviews, and compliance with international standards. Request references from previous clients to gauge reliability. Additionally, verify their manufacturing capabilities and quality control processes to ensure they can meet your expectations. It’s also beneficial to check if they have experience with export regulations specific to your region, which can streamline logistics and reduce potential legal issues. -
Can I customize the vending machines to fit my brand?
Yes, many suppliers offer customization options for vending machines, including branding, size, and product selection. When discussing customization, be clear about your requirements, such as design specifications, color schemes, and the range of products you want to offer. Ensure that the supplier has the capacity and expertise to deliver on these customizations without compromising quality or lead times. -
What are the typical minimum order quantities (MOQ) and lead times for vending machines?
MOQs can vary significantly based on the supplier and the level of customization. Generally, for standard machines, the MOQ might range from 10 to 50 units, while custom machines could require a higher MOQ. Lead times also depend on the complexity of the order, usually ranging from 4 to 12 weeks. Always confirm these details upfront to align your expectations and production schedules. -
What payment terms should I expect when sourcing vending machines?
Payment terms vary by supplier but typically include a deposit of 30-50% upon order confirmation, with the balance due before shipping. For larger orders, some suppliers may offer financing options or staggered payment plans. Ensure you discuss payment methods that are secure and suitable for international transactions, such as letters of credit or escrow services, to protect your investment. -
How can I ensure the quality of the vending machines I am purchasing?
To ensure quality, request certifications such as ISO 9001 or CE marking, which indicate adherence to international quality standards. Additionally, ask for samples or prototypes before making a large order. Establishing a quality assurance agreement with the supplier can also be beneficial, detailing inspection processes and acceptable quality levels to prevent issues upon delivery. -
What logistics considerations should I keep in mind when importing vending machines?
Logistics is crucial in the import process. Assess the supplier’s ability to handle shipping logistics, including customs clearance and freight forwarding. Determine who will be responsible for shipping costs and ensure you have a reliable logistics partner familiar with international trade regulations. Also, consider potential tariffs and taxes that may apply in your country, which can impact overall costs. -
How should I handle disputes with a vending machine supplier?
To manage disputes effectively, establish clear communication channels and maintain documentation of all transactions and agreements. It’s advisable to include a dispute resolution clause in your contract, specifying mediation or arbitration procedures. If issues arise, address them promptly and professionally, aiming for a resolution that maintains a positive business relationship while protecting your interests.
- What certifications should I look for in vending machines?
Look for certifications that demonstrate compliance with safety and environmental regulations, such as UL (Underwriters Laboratories) for electrical safety and RoHS (Restriction of Hazardous Substances) for environmental compliance. Depending on your market, additional certifications may be required to ensure the machines meet local standards. Always verify that the supplier can provide documentation for any claimed certifications.
Strategic Sourcing Conclusion and Outlook for vending machines warehouse
In summary, effective strategic sourcing is paramount for B2B buyers in the vending machine warehouse sector. By leveraging comprehensive market insights and supplier relationships, companies can optimize their procurement processes, reduce costs, and enhance operational efficiency. Key takeaways include the importance of understanding regional market dynamics, ensuring compliance with local regulations, and fostering sustainable partnerships with suppliers.
As international buyers from Africa, South America, the Middle East, and Europe navigate this evolving landscape, it is crucial to adopt a proactive approach to sourcing. This involves not only identifying reliable vendors but also assessing their technological capabilities and service offerings. By prioritizing these aspects, businesses can ensure they are well-positioned to meet the demands of their customers and stay ahead of competitors.
Looking ahead, the vending machine industry is poised for growth, driven by innovations in technology and changing consumer preferences. Now is the time for B2B buyers to act decisively—embracing strategic sourcing will not only enhance their supply chain resilience but also unlock new opportunities in this dynamic market. Engage with suppliers today to secure your competitive edge for tomorrow.