Your Ultimate Guide to Sourcing Vending Machine With Card
Guide to Vending Machine With Card Reader
- Introduction: Navigating the Global Market for vending machine with card reader
- Understanding vending machine with card reader Types and Variations
- Key Industrial Applications of vending machine with card reader
- Strategic Material Selection Guide for vending machine with card reader
- In-depth Look: Manufacturing Processes and Quality Assurance for vending machine with card reader
- Comprehensive Cost and Pricing Analysis for vending machine with card reader Sourcing
- Spotlight on Potential vending machine with card reader Manufacturers and Suppliers
- Essential Technical Properties and Trade Terminology for vending machine with card reader
- Navigating Market Dynamics, Sourcing Trends, and Sustainability in the vending machine with card reader Sector
- Frequently Asked Questions (FAQs) for B2B Buyers of vending machine with card reader
- Strategic Sourcing Conclusion and Outlook for vending machine with card reader
Introduction: Navigating the Global Market for vending machine with card reader
In today’s fast-paced global economy, the demand for vending machines equipped with card readers is witnessing exponential growth. This trend is driven by a shift in consumer behavior towards cashless transactions, which not only enhances convenience but also boosts sales for businesses. For international B2B buyers, particularly those based in Africa, South America, the Middle East, and Europe, understanding the intricacies of this market is crucial for making informed sourcing decisions.
This guide provides a comprehensive analysis of the vending machine landscape, detailing various types of machines, the materials used in their construction, and the manufacturing processes that ensure quality and reliability. It also highlights key suppliers and their offerings, enabling buyers to identify the best partners for their needs. Additionally, an overview of cost factors will help you budget effectively while maximizing value.
By exploring market trends and consumer preferences, this guide equips you with actionable insights to navigate the complexities of sourcing vending machines with card readers. You’ll find answers to frequently asked questions, helping to demystify the procurement process and clarify any uncertainties. Ultimately, this resource is designed to empower you with the knowledge needed to secure the right vending solutions that cater to your market, ensuring competitive advantage and operational efficiency.
Understanding vending machine with card reader Types and Variations
Type Name | Key Distinguishing Features | Primary B2B Applications | Brief Pros & Cons for Buyers |
---|---|---|---|
Traditional Snack Vending | Dispenses packaged snacks and beverages; card reader integration | Offices, schools, hospitals | Pros: Familiarity, low maintenance; Cons: Limited product range compared to modern options. |
Fresh Food Vending | Refrigerated units for perishable items; touchless payment | Corporate campuses, gyms, universities | Pros: High demand for healthy options; Cons: Requires regular restocking and maintenance. |
Coffee Vending Machines | Offers a variety of coffee drinks; often equipped with grinders | Cafés, office break rooms, event venues | Pros: High profit margins; Cons: Can be costly to maintain and refill. |
Specialty Vending Machines | Niche products (e.g., electronics, cosmetics); customizable | Airports, shopping malls, hotels | Pros: Attracts diverse clientele; Cons: Higher initial investment and potential for theft. |
Automated Retail Kiosks | Larger units with touchscreen interfaces; integrated inventory management | Retail stores, trade shows, exhibitions | Pros: Sophisticated technology; Cons: Higher operational complexity and cost. |
Traditional Snack Vending
Traditional snack vending machines are the most recognizable type, primarily offering packaged snacks and beverages. These machines typically feature a card reader for cashless transactions, appealing to a wide range of B2B applications such as offices, schools, and hospitals. When considering this option, buyers should focus on the machine’s reliability and ease of maintenance. While they are generally low-cost and familiar to users, their limited product range may not meet the growing demand for healthier options.
Fresh Food Vending
Fresh food vending machines cater to the increasing consumer preference for healthy eating. These units are equipped with refrigeration to store perishable items, and they often utilize touchless payment systems for convenience. They are particularly suitable for corporate campuses, gyms, and universities, where consumers seek nutritious meal options. B2B buyers should consider the need for regular restocking and maintenance, as these machines require a commitment to freshness. While they can attract a health-conscious clientele, operational costs may be higher due to the perishability of the products.
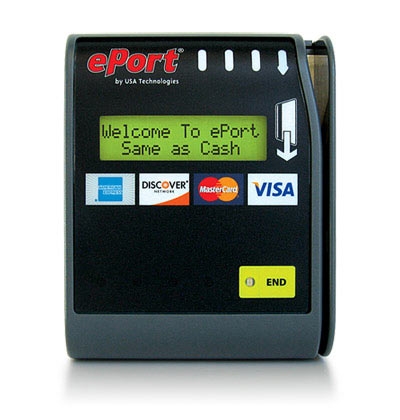
Illustrative Image (Source: Google Search)
Coffee Vending Machines
Coffee vending machines have gained popularity in various settings, including cafés, office break rooms, and event venues. These machines can dispense a variety of coffee drinks, often featuring built-in grinders for fresh coffee. The integration of card readers enhances user convenience, making them an attractive option for B2B buyers. While coffee vending machines can yield high profit margins, prospective buyers must weigh the initial investment and ongoing maintenance costs, as these machines can be more complex than traditional snack dispensers.
Specialty Vending Machines
Specialty vending machines are designed to offer niche products, such as electronics, cosmetics, or unique gourmet foods. These machines often feature customizable designs and advanced technology, appealing to high-traffic locations like airports, shopping malls, and hotels. B2B buyers should evaluate the potential for attracting a diverse clientele against the higher initial investment and security concerns, as specialty items may be more susceptible to theft. Despite these challenges, the unique offerings can significantly enhance customer engagement.
Automated Retail Kiosks
Automated retail kiosks represent the next evolution in vending technology, combining sophisticated touchscreen interfaces with integrated inventory management systems. These kiosks can provide a wide range of products and are ideal for retail stores, trade shows, and exhibitions. For B2B buyers, the appeal lies in the advanced technology and data collection capabilities, which can improve inventory tracking and customer insights. However, the complexity of operation and higher costs may pose challenges, requiring careful consideration of the target market and operational capacity.
Related Video: Install a Vending Credit Card Reader in 5 Minutes
Key Industrial Applications of vending machine with card reader
Industry/Sector | Specific Application of vending machine with card reader | Value/Benefit for the Business | Key Sourcing Considerations for this Application |
---|---|---|---|
Healthcare | Medicine and medical supplies dispensing | Improved access to essential items, reduced wait times | Compliance with health regulations, temperature control |
Education | Campus convenience stores for snacks and supplies | Enhanced student satisfaction, increased sales | Payment integration, robust inventory management |
Corporate Offices | Employee break rooms with healthy snack options | Boosts employee morale, promotes healthy eating | Customization options, user-friendly interface |
Transportation | Ticketing and snack vending in transit hubs | Streamlined operations, increased passenger convenience | Secure payment processing, robust machine design |
Hospitality | Mini-bar vending solutions in hotels | Increased revenue, reduced labor costs | Compact design, variety of product offerings |
Healthcare Applications
In healthcare settings, vending machines with card readers can provide immediate access to medicines and medical supplies. These machines can be strategically placed in hospitals or clinics to ensure that staff and patients can quickly obtain essential items like first-aid supplies or over-the-counter medications. This application addresses the problem of long wait times in pharmacies and enhances patient care. For B2B buyers in Africa and the Middle East, compliance with local health regulations and the ability to maintain temperature-sensitive products are critical factors to consider.
Education Applications
In educational institutions, vending machines equipped with card readers serve as convenient stores offering snacks and school supplies. By placing these machines in high-traffic areas like libraries or student lounges, schools can enhance student satisfaction and drive additional revenue. This application is particularly relevant in regions like South America, where access to healthy snacks can be limited. Buyers should focus on payment integration and robust inventory management systems to ensure smooth operations and minimize downtime.
Corporate Office Applications
Corporate offices are increasingly adopting vending machines with card readers to provide employees with healthy snack options in break rooms. This initiative not only boosts employee morale but also encourages healthier eating habits, which can lead to increased productivity. For international B2B buyers, customization options and a user-friendly interface are essential considerations to ensure the machines meet the specific needs of their workforce.
Transportation Applications
In the transportation sector, vending machines with card readers can simplify ticketing and provide snacks in transit hubs like airports and train stations. This application enhances passenger convenience and streamlines operations by reducing the need for staff involvement in minor transactions. For buyers in Europe and Africa, ensuring secure payment processing and a robust machine design that can withstand high traffic is crucial for success in this competitive environment.
Hospitality Applications
In the hospitality industry, vending machines can serve as mini-bars within hotel rooms, offering guests a variety of snacks and beverages. This solution can significantly increase revenue while reducing labor costs associated with traditional mini-bar services. Buyers in regions like the Middle East should consider compact designs and a diverse range of product offerings to cater to different guest preferences, ensuring a positive experience that encourages repeat business.
Related Video: How to Install a Credit Card Reader on a Vending Machine
Strategic Material Selection Guide for vending machine with card reader
When selecting materials for vending machines equipped with card readers, it is crucial to consider the specific performance requirements and environmental conditions these machines will face. The choice of material will impact durability, cost, compliance with international standards, and overall functionality. Below is an analysis of four common materials used in the construction of vending machines, focusing on their properties, advantages, disadvantages, and considerations for international B2B buyers.
Stainless Steel
Key Properties:
Stainless steel is known for its excellent corrosion resistance, high strength, and ability to withstand high temperatures. It is often rated for various environments, making it suitable for both indoor and outdoor applications.
Pros & Cons:
The durability of stainless steel is a significant advantage, as it can withstand harsh conditions without compromising structural integrity. However, it is relatively expensive compared to other materials, which may impact the overall cost of the vending machine. Manufacturing complexity can also be higher due to the need for specialized tools and techniques.
Impact on Application:
Stainless steel is compatible with a wide range of media, including food and beverages, which is essential for vending machines. Its non-porous surface helps maintain hygiene, a critical factor in food safety.
Considerations for International Buyers:
Buyers from regions like Europe and the Middle East should ensure compliance with standards such as ASTM A240 for stainless steel. Additionally, buyers should consider local sourcing options to mitigate import costs.
Mild Steel
Key Properties:
Mild steel is characterized by its good weldability and machinability, with a moderate strength-to-weight ratio. It is not inherently corrosion-resistant, which makes protective coatings necessary.
Pros & Cons:
One of the primary advantages of mild steel is its low cost, making it an attractive option for budget-conscious projects. However, its susceptibility to rust and corrosion can lead to increased maintenance costs and reduced lifespan if not properly coated.
Impact on Application:
Mild steel is suitable for structural components of vending machines but may not be ideal for areas exposed to moisture or harsh environments without adequate protection.
Considerations for International Buyers:
For buyers in Africa and South America, understanding local climate conditions is crucial, as high humidity can accelerate corrosion. Compliance with local standards for coatings and finishes is also essential.
Aluminum
Key Properties:
Aluminum is lightweight, corrosion-resistant, and has good thermal conductivity. It is often used in applications where weight savings are essential.
Pros & Cons:
The lightweight nature of aluminum allows for easier transport and installation of vending machines. However, it is less durable than stainless steel and may not withstand heavy impacts, which could be a drawback in high-traffic areas.
Impact on Application:
Aluminum is compatible with various media but should be evaluated for specific applications, especially concerning food safety standards.
Considerations for International Buyers:
Buyers should be aware of the different grades of aluminum and their respective properties. Compliance with standards such as ASTM B221 is important, particularly in regions with strict regulations like Europe.
Polycarbonate
Key Properties:
Polycarbonate is a durable thermoplastic known for its high impact resistance and transparency. It can withstand a wide temperature range, making it suitable for various environments.
Pros & Cons:
The primary advantage of polycarbonate is its lightweight and shatter-resistant properties, making it ideal for protective covers and panels. However, it may not have the same long-term durability as metals when exposed to UV light or extreme temperatures.
Impact on Application:
Polycarbonate is suitable for transparent components of vending machines, allowing visibility of products while providing protection. However, it may require additional treatments for UV resistance.
Considerations for International Buyers:
Buyers should ensure that the polycarbonate used meets relevant safety standards, especially in regions with stringent consumer protection laws. Understanding local regulations regarding plastics is also essential.
Summary Table
Material | Typical Use Case for vending machine with card reader | Key Advantage | Key Disadvantage/Limitation | Relative Cost (Low/Med/High) |
---|---|---|---|---|
Stainless Steel | Structural components, exterior panels | Excellent corrosion resistance | Higher cost and manufacturing complexity | High |
Mild Steel | Structural frames, non-exposed components | Cost-effective | Susceptible to rust without coating | Low |
Aluminum | Panels, lightweight structures | Lightweight and corrosion-resistant | Less durable under heavy impact | Medium |
Polycarbonate | Transparent covers, protective panels | High impact resistance | May degrade under UV exposure | Medium |
This guide provides insights into material selection for vending machines with card readers, helping international B2B buyers make informed decisions based on performance, cost, and compliance considerations.
In-depth Look: Manufacturing Processes and Quality Assurance for vending machine with card reader
Manufacturing Processes for Vending Machines with Card Readers
The manufacturing process for vending machines equipped with card readers involves several critical stages that ensure both functionality and durability. Understanding these processes can help B2B buyers assess potential suppliers and make informed decisions.
1. Material Preparation
The first step in manufacturing vending machines is material preparation. This includes sourcing high-quality raw materials such as:
- Metal Enclosures: Typically made from stainless steel or coated steel for durability and corrosion resistance.
- Electronic Components: Including card readers, control boards, and payment processors, which should comply with international electrical standards.
- Display Units: LCD or LED screens that provide user interfaces.
- Mechanical Parts: Such as motors, gears, and dispensers that ensure smooth operation.
Buyers should ensure that suppliers source materials from reputable vendors to guarantee quality and reliability.
2. Forming
Once materials are prepared, the next stage is forming. This is where raw materials are shaped into the necessary components of the vending machine. Common techniques include:
- Laser Cutting: For precise cuts in metal sheets.
- Bending and Stamping: To create structural components.
- Injection Molding: For producing plastic parts such as buttons and casing.
Each of these processes requires specialized machinery and skilled labor to ensure that components meet design specifications.
3. Assembly
The assembly process involves integrating all components into a complete vending machine. Key steps include:
- Integration of Electronic Systems: This includes installing the card reader, wiring the control board, and ensuring connectivity with payment systems.
- Mechanical Assembly: Assembling the mechanical components that facilitate product dispensing.
- User Interface Installation: Installing screens and buttons, ensuring they are user-friendly.
During assembly, it is crucial to follow a well-documented process to minimize errors and ensure consistency across units.
4. Finishing
Finishing touches enhance both the aesthetic and functional aspects of the vending machines. This stage includes:
- Painting and Coating: Applying finishes that provide protection against wear and environmental factors.
- Quality Control Inspections: Conducting tests to ensure all components function correctly before packaging.
Each machine should be thoroughly checked for defects or issues that could impact performance.
Quality Assurance in Manufacturing
Quality assurance (QA) is vital in the manufacturing of vending machines with card readers, ensuring that products meet international standards and customer expectations.
International Standards
To maintain quality, manufacturers often adhere to recognized international standards, including:
- ISO 9001: This standard focuses on quality management systems and is crucial for ensuring consistent product quality.
- CE Marking: Indicates compliance with European health, safety, and environmental protection standards.
- API Standards: Relevant for electronic components, especially concerning safety and interoperability.
B2B buyers should seek suppliers who hold relevant certifications, as these are indicators of a manufacturer’s commitment to quality.
Quality Control Checkpoints
Quality control involves various checkpoints throughout the manufacturing process:
- Incoming Quality Control (IQC): Inspection of raw materials upon arrival to ensure they meet specifications.
- In-Process Quality Control (IPQC): Ongoing checks during production to catch defects early.
- Final Quality Control (FQC): Comprehensive testing of the finished product before it leaves the factory.
These checkpoints are essential to identifying and rectifying issues at different stages, thus minimizing the risk of defective products reaching the market.
Common Testing Methods
Manufacturers employ various testing methods to ensure the reliability of vending machines:
- Functional Testing: Ensures that all electronic components, including card readers, operate correctly.
- Durability Testing: Simulates real-world conditions to assess the longevity of components.
- Electrical Safety Testing: Verifies compliance with electrical safety standards to prevent hazards.
B2B buyers should inquire about the specific testing protocols followed by suppliers to ensure product reliability.
Verifying Supplier Quality Control
For B2B buyers, verifying a supplier’s quality control processes is crucial in mitigating risks associated with international procurement.
Audits and Reports
Conducting regular audits of potential suppliers can provide insights into their manufacturing processes and quality assurance measures. Buyers should request:
- Quality Assurance Reports: Detailing inspection and testing results.
- Audit Reports: From third-party inspectors who assess compliance with international standards.
Third-Party Inspections
Engaging third-party inspection services can provide an unbiased evaluation of a supplier’s quality control measures. These inspections can occur at various stages, including:
- Pre-production: To assess readiness and capability.
- During Production: To monitor compliance with agreed standards.
- Post-production: To ensure final products meet quality expectations.
Navigating QC/CERT Nuances for International Buyers
International B2B buyers must be aware of the specific quality control and certification nuances that may affect their procurement decisions:
- Regional Standards Variability: Different regions may have varying standards and certification requirements. For instance, CE marking is essential for European markets, while UL certification may be more relevant in the U.S.
- Supply Chain Transparency: Buyers should seek suppliers who provide clear documentation of their QC processes and certifications to ensure compliance with local regulations.
Understanding these nuances will help buyers from Africa, South America, the Middle East, and Europe navigate the complexities of international procurement effectively. By prioritizing quality assurance and verifying supplier capabilities, businesses can secure reliable vending machines that meet their operational needs.
Related Video: SMART Quality Control for Manufacturing
Comprehensive Cost and Pricing Analysis for vending machine with card reader Sourcing
Understanding the Cost Structure
When sourcing vending machines equipped with card readers, it’s crucial to grasp the comprehensive cost structure. The primary components influencing costs include:
-
Materials: The choice of materials for the machine’s casing, internal components, and card reader technology significantly impacts pricing. High-quality, durable materials will increase upfront costs but can reduce long-term maintenance.
-
Labor: Labor costs can vary by region. In countries with lower labor costs, such as some parts of Africa and South America, you may find competitive pricing, but consider the trade-offs in terms of quality and expertise.
-
Manufacturing Overhead: This encompasses indirect costs related to production, such as utilities, rent, and equipment maintenance. Efficient manufacturing processes can help lower these costs.
-
Tooling: For customized vending machines, tooling costs can be significant. This includes the expenses associated with creating molds or special machinery for unique designs.
-
Quality Control (QC): Investing in robust QC processes ensures that machines meet safety and operational standards, which can prevent costly recalls or warranty claims later.
-
Logistics: Shipping and handling costs should be factored into the total price. This includes freight charges, customs duties, and local transportation. Understanding Incoterms is vital to clarify who bears these costs.
-
Margin: Suppliers typically apply a markup to their costs to achieve profitability. This margin can vary widely depending on the supplier’s market positioning and operational efficiencies.
Price Influencers
Several factors can influence the pricing of vending machines with card readers:
-
Volume/MOQ: Purchasing in bulk often leads to lower per-unit costs. Negotiate minimum order quantities (MOQ) to secure better pricing.
-
Specifications/Customization: Custom features, such as branding or additional technology, can increase costs. Clearly define your requirements to avoid unexpected price hikes.
-
Materials: Selecting premium materials can enhance durability but will raise costs. Balance quality with budget constraints.
-
Quality Certifications: Machines that meet international quality standards may command higher prices. However, these certifications can enhance reliability and reduce long-term costs.
-
Supplier Factors: The reputation and reliability of the supplier can affect pricing. Established suppliers may charge more due to their proven track record, while new entrants might offer lower prices to gain market share.
-
Incoterms: Understanding the implications of shipping terms is essential. Costs can vary significantly based on whether you’re dealing with FOB (Free on Board), CIF (Cost Insurance and Freight), or other terms.
Buyer Tips
International B2B buyers should consider the following strategies when sourcing vending machines:
-
Negotiation: Leverage your purchasing power, especially if considering bulk orders. Be prepared to discuss pricing based on volume and long-term partnership potential.
-
Cost-Efficiency: Look beyond the initial purchase price. Evaluate the total cost of ownership, including installation, maintenance, and energy consumption, which can vary significantly across models.
-
Pricing Nuances: Be aware of regional pricing differences. In markets like Egypt and Kenya, local economic conditions may influence supplier pricing strategies. Conduct market research to understand local dynamics.
-
Long-Term Relationships: Building a long-term relationship with suppliers can lead to better pricing, improved service, and priority access to new technology.
Disclaimer
Prices for vending machines with card readers can vary widely based on the factors outlined above. The information provided here is indicative and should be supplemented with specific quotes from suppliers to ensure accurate budgeting and planning.
Spotlight on Potential vending machine with card reader Manufacturers and Suppliers
- (No specific manufacturer data was available or requested for detailed profiling in this section for vending machine with card reader.)*
Essential Technical Properties and Trade Terminology for vending machine with card reader
Key Technical Properties
-
Material Grade
– The material grade of a vending machine significantly impacts its durability and lifespan. Common materials include stainless steel, which is resistant to corrosion and ideal for high-traffic environments. When sourcing, buyers should ensure the material meets local standards for safety and environmental regulations, particularly in regions like Africa and the Middle East where climate can affect machine integrity. -
Power Consumption
– Vending machines with card readers require a reliable power supply. Understanding the power consumption specification (measured in watts) is crucial for evaluating energy costs and compatibility with local electrical systems. Machines that are energy-efficient not only reduce operational costs but can also enhance sustainability credentials, which is increasingly important in markets across Europe and South America. -
Card Reader Compatibility
– The type of card reader integrated into the vending machine should support various payment methods, including EMV (Europay, MasterCard, and Visa) and NFC (Near Field Communication). This flexibility is essential for attracting a wider customer base, particularly in regions with diverse payment preferences. B2B buyers should inquire about the machine’s ability to accept mobile payments and digital wallets, as this can drive sales. -
Capacity and Dimensions
– The machine’s capacity, which refers to the number of products it can hold, is vital for inventory management and sales potential. Dimensions matter for placement in retail environments; thus, understanding the spatial requirements and ensuring they align with local store layouts is critical. Buyers should consider both the product size and the expected foot traffic when determining the appropriate machine specifications. -
User Interface
– A user-friendly interface is paramount for customer satisfaction. Features such as touchscreen displays, multiple language options, and clear instructions can enhance the buying experience. For B2B buyers, investing in machines with superior user interfaces can lead to increased sales and lower customer service inquiries, making it a worthwhile consideration.
Trade Terminology
- OEM (Original Equipment Manufacturer)
– OEM refers to a company that produces parts or equipment that may be marketed by another manufacturer. In the context of vending machines, knowing whether a vendor is an OEM can help buyers assess the quality and reliability of the machine components. Engaging with OEMs can also provide opportunities for customization to meet specific market needs.
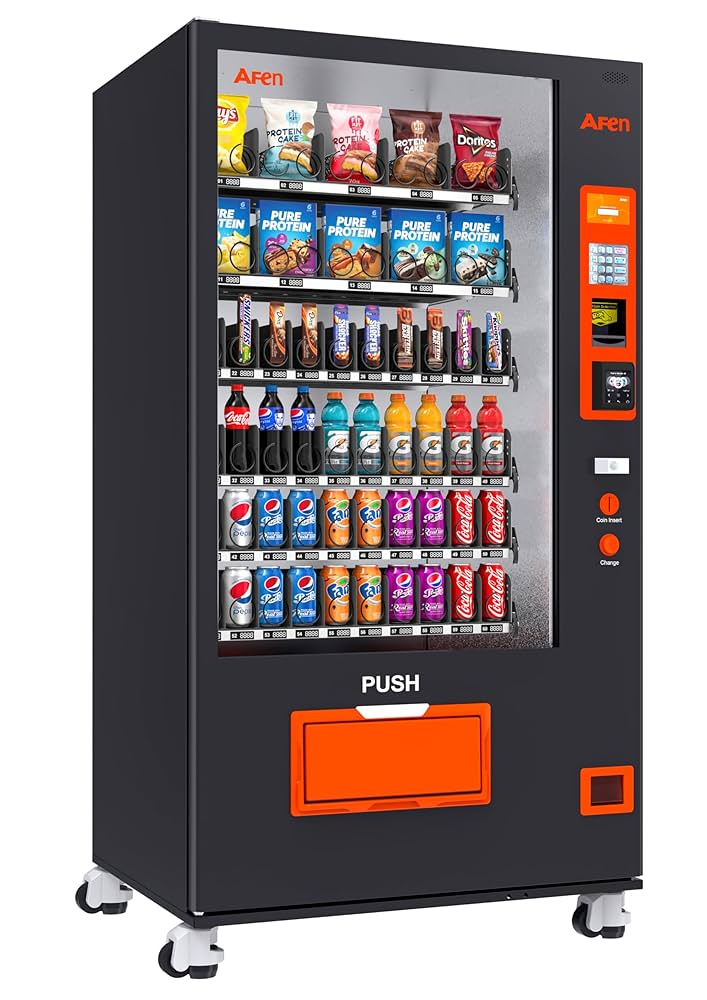
Illustrative Image (Source: Google Search)
-
MOQ (Minimum Order Quantity)
– MOQ is the smallest number of units that a supplier is willing to sell. Understanding MOQ is crucial for buyers, especially those in Africa or South America, as it impacts inventory management and cash flow. Buyers should negotiate MOQs that align with their sales forecasts and storage capabilities to avoid excess stock. -
RFQ (Request for Quotation)
– An RFQ is a standard business process where buyers request pricing and terms from suppliers. It is an essential step in procurement, allowing buyers to compare offers and ensure they receive competitive pricing. Crafting a well-defined RFQ can lead to better negotiations and cost savings. -
Incoterms (International Commercial Terms)
– Incoterms are a set of internationally recognized rules that define the responsibilities of buyers and sellers in international transactions. Understanding these terms is vital for B2B buyers to manage shipping costs and risks effectively. Common terms include FOB (Free on Board) and CIF (Cost, Insurance, and Freight), which dictate who pays for shipping and insurance during transit. -
Warranty and Support Terms
– Warranty terms outline the manufacturer’s obligations regarding repairs or replacements of defective machines. Buyers should thoroughly review these terms to ensure adequate support post-purchase, which can significantly affect long-term operational efficiency and customer satisfaction. -
Lead Time
– Lead time refers to the time taken from placing an order to delivery. For B2B buyers, understanding lead times is crucial for inventory planning and minimizing downtime. It is advisable to factor in lead times when forecasting demand and scheduling promotions to ensure product availability.
By familiarizing themselves with these technical properties and trade terminologies, international B2B buyers can make informed decisions that align with their operational needs and market conditions.
Navigating Market Dynamics, Sourcing Trends, and Sustainability in the vending machine with card reader Sector
Market Overview & Key Trends
The global vending machine market, particularly those equipped with card readers, is undergoing significant transformation driven by several key factors. Firstly, the increasing demand for cashless transactions is reshaping consumer preferences, making card readers a necessity for modern vending solutions. This trend is particularly pronounced in regions such as Europe and parts of South America, where digital payment adoption is high. In Africa and the Middle East, the expansion of mobile payment solutions is also influencing vending machine designs, with a rising number of consumers preferring mobile wallets over cash.
Emerging technologies such as IoT (Internet of Things) are enabling real-time inventory management and enhanced customer engagement through personalized marketing. International B2B buyers should look for machines that integrate with cloud-based platforms, allowing for data analytics to optimize product offerings based on consumer behavior. Sustainability is becoming a crucial factor in purchasing decisions, with buyers increasingly favoring vending machines that support eco-friendly practices and materials.
Additionally, the market is seeing a shift towards hybrid vending machines that offer a wider range of products, including healthy snacks and beverages, catering to the growing health-conscious consumer base. For buyers from Africa, South America, the Middle East, and Europe, understanding local consumer trends and preferences is vital for successful market entry and product selection.
Sustainability & Ethical Sourcing in B2B
Sustainability is no longer just a buzzword; it is a critical component of the B2B purchasing process, particularly in the vending machine sector. The environmental impact of vending machines—ranging from energy consumption to waste generation—demands attention. Buyers should prioritize machines that are energy-efficient and use eco-friendly refrigerants to minimize their carbon footprint.
Ethical sourcing is equally important, with an emphasis on supply chains that prioritize fair labor practices and transparency. B2B buyers should seek manufacturers who adhere to recognized sustainability certifications such as ISO 14001, which focuses on effective environmental management systems. Additionally, look for machines made from recyclable materials or those that incorporate biodegradable components.
Incorporating sustainable practices not only meets regulatory requirements but also resonates with consumers who increasingly prefer brands that demonstrate environmental responsibility. For international buyers, aligning procurement strategies with sustainability goals can enhance brand reputation and customer loyalty, particularly in markets that value corporate social responsibility.
Brief Evolution/History
The vending machine industry has evolved significantly since its inception in the early 20th century. Originally designed to dispense simple products like candy and cigarettes, the introduction of electronic payment systems in the late 20th century marked a pivotal shift. This evolution paved the way for the integration of card readers, allowing consumers to make cashless transactions.
In recent years, the focus has shifted towards enhancing user experience and operational efficiency. The advent of smart vending machines equipped with IoT capabilities has transformed the landscape, enabling operators to monitor machine performance and consumer preferences in real-time. This evolution reflects broader technological advancements and the growing importance of data-driven decision-making in the B2B sector, particularly for international buyers seeking to optimize their vending machine offerings.
Related Video: Incoterms for beginners | Global Trade Explained
Frequently Asked Questions (FAQs) for B2B Buyers of vending machine with card reader
-
What criteria should I use to vet suppliers of vending machines with card readers?
When vetting suppliers, consider their experience in the vending machine industry, particularly with card readers. Request references from other international buyers and check online reviews. Ensure they provide necessary certifications, such as ISO standards, which indicate adherence to quality management systems. Additionally, assess their financial stability and production capacity to meet your demands. Conducting a site visit, if possible, can also provide insights into their operations and quality control processes. -
Can I customize vending machines to suit my market needs?
Yes, many manufacturers offer customization options for vending machines. You can specify features such as size, design, product selection, and payment options tailored to your target audience. It’s essential to communicate your requirements clearly during initial discussions. Furthermore, inquire about the design process and lead times for customization to ensure timely delivery. Be prepared for possible additional costs associated with these customizations. -
What are the typical minimum order quantities (MOQs) and lead times for vending machines?
MOQs for vending machines can vary significantly depending on the supplier and the customization involved. Generally, manufacturers may require orders ranging from 5 to 20 units to ensure cost-efficiency. Lead times also depend on the complexity of your order, with standard machines typically taking 4 to 8 weeks to manufacture and deliver. For customized machines, lead times may extend up to 12 weeks. Always confirm these details upfront to plan your inventory and launch accordingly. -
What payment terms should I expect when purchasing vending machines?
Payment terms can vary widely among suppliers, but common practices include a deposit (typically 30-50%) upon order confirmation, with the balance due before shipment. Some suppliers may offer financing options or extended payment terms for larger orders. It’s crucial to discuss payment methods accepted, such as wire transfers or letters of credit, and ensure they align with your financial practices. Additionally, consider the implications of currency exchange rates if dealing with international suppliers. -
How can I ensure quality assurance and certification for the machines?
To ensure quality, ask suppliers for product certifications relevant to your region, such as CE marking for Europe or ISO certifications. Request detailed documentation of their quality assurance processes, including testing procedures for the machines and card readers. Conducting a factory audit or using third-party inspection services can further verify compliance with international quality standards. This diligence helps mitigate risks associated with product quality and functionality. -
What are the logistics considerations for importing vending machines?
Logistics for importing vending machines involve several key factors, including shipping methods, customs clearance, and delivery timelines. Choose a reputable freight forwarder experienced in handling machinery to navigate international shipping regulations. Ensure you understand the import duties and taxes applicable in your country, as these can significantly affect your total costs. Plan for potential delays in customs and coordinate with your supplier to provide necessary documentation for a smooth import process. -
How can I resolve disputes with suppliers regarding vending machine orders?
Dispute resolution should begin with clear communication. Establish a formal channel for addressing issues and ensure both parties understand the terms of the contract. Include clauses in your agreement regarding dispute resolution processes, such as mediation or arbitration. If disputes arise, document all communications and agreements, which can serve as evidence if legal action is necessary. Consider using a local legal advisor familiar with international trade laws to guide you through complex situations. -
What after-sales support should I expect from vending machine suppliers?
After-sales support is crucial for the successful operation of your vending machines. Inquire about warranty periods and what they cover, including parts and technical support. A good supplier should provide training for your staff on machine operation and maintenance. Additionally, confirm the availability of spare parts and the supplier’s response time for service requests. Reliable after-sales support can significantly reduce downtime and enhance customer satisfaction in your vending operations.
Strategic Sourcing Conclusion and Outlook for vending machine with card reader
In the evolving landscape of vending solutions, the integration of card readers represents a critical shift towards convenience and accessibility. International B2B buyers are encouraged to prioritize strategic sourcing as a means to optimize their procurement processes, ensuring they select vendors that not only meet quality and functionality standards but also align with their business objectives. Key considerations include evaluating suppliers based on technological capabilities, warranty provisions, and support services, particularly in regions such as Africa, South America, the Middle East, and Europe.
The demand for vending machines equipped with card readers is projected to grow, driven by consumer preferences for cashless transactions and the rising trend of contactless payments. This presents a unique opportunity for businesses to enhance customer satisfaction and operational efficiency. Buyers should leverage this trend by seeking partnerships with manufacturers that offer innovative solutions, robust customer support, and competitive pricing.
As you look ahead, consider the potential of strategically sourcing vending machines with card readers to not only streamline your operations but also position your business for future growth. Engage with suppliers who understand the nuances of your market and can provide tailored solutions that meet your specific needs. Embrace this opportunity to transform your vending offerings into a modern, customer-friendly experience.