Your Ultimate Guide to Sourcing Vending Machine Warehouse
Guide to Vending Machine Warehouse Near Me
- Introduction: Navigating the Global Market for vending machine warehouse near me
- Understanding vending machine warehouse near me Types and Variations
- Key Industrial Applications of vending machine warehouse near me
- Strategic Material Selection Guide for vending machine warehouse near me
- In-depth Look: Manufacturing Processes and Quality Assurance for vending machine warehouse near me
- Comprehensive Cost and Pricing Analysis for vending machine warehouse near me Sourcing
- Spotlight on Potential vending machine warehouse near me Manufacturers and Suppliers
- Essential Technical Properties and Trade Terminology for vending machine warehouse near me
- Navigating Market Dynamics, Sourcing Trends, and Sustainability in the vending machine warehouse near me Sector
- Frequently Asked Questions (FAQs) for B2B Buyers of vending machine warehouse near me
- Strategic Sourcing Conclusion and Outlook for vending machine warehouse near me
Introduction: Navigating the Global Market for vending machine warehouse near me
In an increasingly interconnected global market, the demand for vending machines continues to rise, providing businesses with an opportunity to enhance their service offerings and customer engagement. For international B2B buyers, particularly those hailing from Africa, South America, the Middle East, and Europe—countries like France and Poland—identifying the right vending machine warehouse is essential. It not only ensures a steady supply of quality machines but also facilitates streamlined operations and localized support.
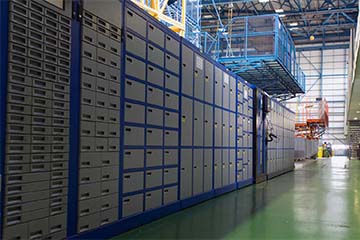
Illustrative Image (Source: Google Search)
This comprehensive guide serves as a strategic resource, delving into the myriad aspects of sourcing vending machines. From understanding the different types of vending machines available, including snack, beverage, and specialized machines, to examining the materials used in their construction, our analysis provides invaluable insights. We will explore manufacturing and quality control standards, highlight reputable suppliers, and discuss the cost structures associated with various models.
Furthermore, the guide addresses essential market trends, enabling buyers to make informed decisions that align with their business goals. A dedicated FAQ section will tackle common queries, ensuring that buyers are well-equipped to navigate the complexities of this market.
By empowering B2B buyers with actionable insights and strategic knowledge, this guide facilitates informed sourcing decisions, ultimately fostering successful partnerships in the global vending machine landscape.
Understanding vending machine warehouse near me Types and Variations
Type Name | Key Distinguishing Features | Primary B2B Applications | Brief Pros & Cons for Buyers |
---|---|---|---|
Traditional Snack Vending | Offers a variety of snacks and beverages | Office break rooms, schools | Pros: Wide selection, easy to stock. Cons: Limited to snacks, less healthy options. |
Healthy Vending Machines | Focus on nutritious snacks and drinks | Gyms, hospitals, corporate wellness | Pros: Aligns with health trends, appeals to health-conscious buyers. Cons: Higher initial costs, niche market. |
Specialty Product Machines | Customizable for niche products (e.g., tech) | Airports, universities, events | Pros: Unique offerings, attracts specific demographics. Cons: May require more maintenance and stock management. |
Cashless Payment Vending | Accepts mobile payments and cards | Urban areas, tech-savvy locations | Pros: Convenient for users, reduces cash handling. Cons: Initial investment in technology, potential tech issues. |
Micro Markets | Self-service kiosks with a broader range | Large offices, warehouses | Pros: 24/7 access, diverse product range. Cons: Requires space, higher operational costs. |
Traditional Snack Vending Machines
Traditional snack vending machines are widely recognized for their diverse offerings, including chips, candies, and soft drinks. These machines are particularly suited for locations such as office break rooms and schools where quick snacks are in demand. When purchasing, B2B buyers should consider factors such as the machine’s capacity, variety of products offered, and ease of restocking. While these machines are cost-effective and easy to maintain, they may not cater to health-conscious consumers, potentially limiting appeal in certain markets.
Healthy Vending Machines
Healthy vending machines are designed to provide nutritious options, such as protein bars, fruit, and low-calorie beverages. This type is increasingly popular in gyms, hospitals, and corporate wellness programs, catering to the growing demand for healthier lifestyle choices. B2B buyers should evaluate the product selection and sourcing practices to ensure quality. Although these machines can attract a niche market, they often come with higher initial costs and may require more frequent restocking to keep up with consumer preferences.
Specialty Product Machines
Specialty product vending machines allow for customization and can be tailored to specific markets, such as electronics or gourmet foods. These machines are ideal for high-traffic locations like airports and universities, where unique offerings can draw in customers. Buyers should assess the potential return on investment based on foot traffic and demand for specialized products. While they can be lucrative, specialty machines may require more maintenance and careful inventory management to meet customer expectations.
Cashless Payment Vending Machines
Cashless payment vending machines facilitate transactions via mobile payments and credit cards, catering to tech-savvy consumers in urban areas. This modern approach enhances convenience and minimizes cash handling, making it an attractive option for businesses looking to streamline operations. B2B buyers should consider the technology’s reliability and the cost of integrating payment systems. However, the initial investment can be significant, and potential technical issues may arise, necessitating ongoing support.
Micro Markets
Micro markets consist of self-service kiosks that offer a broader range of products, including fresh food, snacks, and beverages. They are particularly effective in large office environments and warehouses where employees seek convenient dining options. Buyers should evaluate the space required and the operational costs associated with maintaining a micro market. While they provide 24/7 access and a diverse product range, they also demand more investment and management compared to traditional vending solutions.
Related Video: What is E-Commerce? Definition, Types, and Business Models
Key Industrial Applications of vending machine warehouse near me
Industry/Sector | Specific Application of vending machine warehouse near me | Value/Benefit for the Business | Key Sourcing Considerations for this Application |
---|---|---|---|
Retail | Automated retail solutions for convenience stores | Increased sales through 24/7 product access | Product variety, payment systems, and inventory management |
Corporate Offices | Snack and beverage provisioning for employees | Improved employee satisfaction and productivity | Healthy options, maintenance support, and user feedback |
Healthcare | Dispensing medical supplies and personal care items | Enhanced patient experience and quick access | Compliance with health regulations and supply chain reliability |
Education | Student meal and snack services in schools | Promotes healthy eating habits and convenience | Nutritional value, pricing strategies, and payment options |
Transportation Hubs | Food and beverage services in airports and train stations | Captures transient customers and boosts revenue | Location, product freshness, and customer service standards |
Retail
In the retail sector, vending machine warehouses can provide automated retail solutions tailored for convenience stores. These machines enable businesses to offer a wide range of products, including snacks, beverages, and essential items, 24/7. This accessibility can significantly increase sales, especially in urban areas where consumers expect instant gratification. For international B2B buyers, key considerations include sourcing diverse product varieties, integrating efficient payment systems, and implementing robust inventory management systems to ensure product availability and minimize downtime.
Corporate Offices
Vending machine warehouses serve a vital role in corporate settings by providing snack and beverage options for employees. This not only enhances employee satisfaction but also boosts productivity, as easy access to refreshments can lead to higher morale and reduced downtime. Buyers in this sector should consider sourcing machines that offer healthy options, maintenance support, and the ability to gather user feedback, ensuring that the offerings align with employee preferences and wellness initiatives.
Healthcare
In healthcare environments, vending machines can dispense medical supplies and personal care items, offering patients and visitors quick access to necessary products. This enhances the patient experience by reducing wait times and providing convenience. For international buyers in this sector, compliance with health regulations is paramount, along with ensuring the reliability of the supply chain to maintain consistent stock levels and quality standards.
Education
Vending machine warehouses are increasingly utilized in educational institutions to provide students with meal and snack services. This initiative promotes healthy eating habits and offers convenience for busy students. Buyers in this industry should focus on sourcing machines that provide nutritious options, implement effective pricing strategies, and offer flexible payment options to cater to a diverse student population.
Transportation Hubs
Vending machines in transportation hubs, such as airports and train stations, cater to transient customers by offering food and beverage services. This can significantly boost revenue by capturing the attention of travelers looking for quick meal options. For B2B buyers in this sector, key sourcing considerations include the strategic placement of machines, ensuring product freshness, and maintaining high customer service standards to enhance the overall travel experience.
Related Video: How to Start a Vending Machine Business, Cost, Tips, How Much You Make
Strategic Material Selection Guide for vending machine warehouse near me
When selecting materials for vending machine warehouses, it is essential to consider various factors that influence performance, durability, and cost-effectiveness. Below, we analyze four common materials used in vending machine applications, focusing on their properties, advantages, disadvantages, and specific considerations for international B2B buyers.
Stainless Steel
Key Properties: Stainless steel is known for its excellent corrosion resistance, high strength, and ability to withstand extreme temperatures. It typically has a temperature rating up to 1,000°F (538°C) and can handle significant pressure, making it suitable for various environments.
Pros & Cons: The primary advantage of stainless steel is its durability and resistance to rust and staining, which is crucial for maintaining hygiene in vending applications. However, it can be more expensive than other materials and may require specialized manufacturing processes, increasing overall costs.
Impact on Application: Stainless steel is compatible with a wide range of media, including water, soft drinks, and snacks, making it ideal for vending machines. Its hygienic properties are particularly important in food-related applications.
Considerations for International Buyers: Buyers from regions such as Europe and the Middle East should ensure compliance with local health and safety regulations. Standards like ASTM and EN are often referenced in procurement specifications.
Aluminum
Key Properties: Aluminum is lightweight, with a high strength-to-weight ratio, and is resistant to corrosion. It can withstand temperatures up to 400°F (204°C) and is often treated for enhanced durability.
Pros & Cons: The advantages of aluminum include its low weight, which reduces shipping costs, and its resistance to corrosion, making it suitable for outdoor vending applications. However, it may not be as strong as stainless steel and can be more susceptible to dents and scratches.
Impact on Application: Aluminum is compatible with a variety of media, particularly non-corrosive fluids and snacks. Its lightweight nature allows for easier handling and installation.
Considerations for International Buyers: Buyers in Africa and South America should consider local availability and potential tariffs on aluminum products. Compliance with regional standards, such as JIS in Japan or DIN in Germany, may also be necessary.
Plastic (Polypropylene and Polyethylene)
Key Properties: Plastics like polypropylene and polyethylene are known for their chemical resistance and low density. They can typically withstand temperatures from -40°F to 180°F (-40°C to 82°C) and are resistant to many solvents.
Pros & Cons: The primary advantage of plastic materials is their cost-effectiveness and versatility. They are lightweight and can be molded into complex shapes. However, they may not offer the same level of durability as metals and can degrade under UV exposure if not treated.
Impact on Application: Plastic is suitable for vending machine components that do not require high strength or temperature resistance, such as trays and panels. Their chemical resistance makes them ideal for use with a variety of snacks and beverages.
Considerations for International Buyers: Buyers should be aware of the varying regulations regarding plastic materials in their regions, particularly in Europe where restrictions on certain plastics are more stringent. Compliance with standards such as ASTM D6400 for compostability may also be relevant.
Glass
Key Properties: Glass offers excellent clarity and is resistant to chemical corrosion. It can withstand a wide range of temperatures, generally up to 400°F (204°C), depending on the type of glass.
Pros & Cons: The main advantage of glass is its aesthetic appeal and the ability to showcase products clearly. However, it is fragile and can break easily, which poses a risk in high-traffic areas. Additionally, glass is heavier than other materials, increasing shipping costs.
Impact on Application: Glass is often used in vending machines that dispense beverages, as it maintains product integrity and visibility. However, its fragility limits its use in high-impact environments.
Considerations for International Buyers: Buyers should consider the logistics of handling glass products, particularly in regions with less developed infrastructure. Compliance with safety standards, such as EN 12600 for impact resistance, is crucial.
Summary Table
Material | Typical Use Case for vending machine warehouse near me | Key Advantage | Key Disadvantage/Limitation | Relative Cost (Low/Med/High) |
---|---|---|---|---|
Stainless Steel | Vending machines for food and beverages requiring hygiene | Excellent corrosion resistance and durability | Higher cost and complex manufacturing | High |
Aluminum | Outdoor vending machines and lightweight components | Lightweight, reducing shipping costs | Less durable than stainless steel, prone to dents | Medium |
Plastic (Polypropylene/Polyethylene) | Non-structural components like trays and panels | Cost-effective and versatile | Less durable, can degrade under UV exposure | Low |
Glass | Beverage vending machines for product visibility | Aesthetic appeal and product integrity | Fragile and heavy, increasing shipping costs | Medium |
This strategic material selection guide provides B2B buyers with actionable insights to make informed decisions when sourcing materials for vending machine warehouses, ensuring compliance with regional standards and optimizing performance.
In-depth Look: Manufacturing Processes and Quality Assurance for vending machine warehouse near me
Manufacturing Processes for Vending Machines
Understanding the manufacturing processes involved in producing vending machines is crucial for international B2B buyers. This knowledge helps in assessing the capabilities and reliability of suppliers, ensuring that the machines meet operational needs and quality standards.
Main Stages of Manufacturing
-
Material Preparation
– Raw Material Selection: High-quality materials such as stainless steel, plastics, and electronic components are selected based on durability and functionality.
– Pre-Processing: Materials are cut, shaped, and treated to prepare them for forming processes. For instance, steel sheets are often cut to size using laser cutting technology, which ensures precision and reduces waste. -
Forming
– Shaping Components: Techniques like stamping and bending are employed to form the outer casing and internal parts of the vending machines. CNC (Computer Numerical Control) machinery is commonly used for high precision.
– Injection Molding: This is used for plastic components, allowing for complex shapes and high-volume production with minimal defects. -
Assembly
– Component Integration: After forming, the components are assembled in a systematic manner. This includes the integration of electronic systems, refrigeration units, and payment mechanisms.
– Use of Automation: Many manufacturers employ automated assembly lines that enhance efficiency and consistency while reducing labor costs. -
Finishing
– Surface Treatment: Finishing processes such as powder coating or painting improve aesthetics and provide additional protection against wear and corrosion.
– Quality Checks: Each finished unit undergoes a preliminary inspection to ensure it meets design specifications before being packaged for delivery.
Quality Assurance in Manufacturing
Quality assurance is vital in the manufacturing of vending machines to ensure reliability and safety for end-users. Various international and industry-specific standards guide these practices.
Relevant International Standards
- ISO 9001: This standard focuses on quality management systems and is applicable to any organization. It ensures that companies consistently provide products that meet customer and regulatory requirements.
- CE Marking: For European markets, CE marking indicates conformity with health, safety, and environmental protection standards.
- API Standards: In certain markets, adherence to American Petroleum Institute standards may be required, especially for vending machines that dispense fuel or specialized products.
Quality Control Checkpoints
-
Incoming Quality Control (IQC)
– This initial checkpoint involves inspecting raw materials upon arrival. Suppliers must provide certificates of conformity and test reports for critical components. -
In-Process Quality Control (IPQC)
– During manufacturing, continuous monitoring occurs at various stages. Techniques such as statistical process control (SPC) can help identify defects early, minimizing waste and rework. -
Final Quality Control (FQC)
– Before shipment, a comprehensive inspection of the completed vending machines is conducted. This includes functional testing and safety assessments to ensure compliance with relevant standards.
Common Testing Methods
- Functional Testing: Ensures that all features of the vending machine operate as intended. This includes payment processing, product dispensing, and user interface functionality.
- Durability Testing: Machines are subjected to stress tests to simulate real-world usage, assessing their resilience against wear and tear.
- Electrical Safety Testing: Ensures that all electrical components meet safety regulations and do not pose hazards to users.
Verifying Supplier Quality Control
For international B2B buyers, verifying the quality control processes of suppliers is essential to mitigate risks. Here are several strategies:
-
Conducting Audits
– Schedule regular audits of potential suppliers to assess their manufacturing processes and quality control systems. This can include checking their adherence to ISO standards and reviewing their quality management documentation. -
Requesting Quality Reports
– Ask for detailed quality assurance reports that document the results of inspections and tests conducted at various stages of production. This transparency can provide insights into the supplier’s commitment to quality. -
Third-Party Inspections
– Engage third-party inspection companies to conduct independent assessments of the manufacturing processes and quality control practices. This adds an extra layer of assurance, especially for international transactions where trust may be a concern.
Quality Control and Certification Nuances for International Buyers
Understanding the nuances of quality control and certification is critical for B2B buyers, particularly in regions like Africa, South America, the Middle East, and Europe.
- Regional Standards Compliance: Different regions may have specific requirements. For example, European countries often require CE marking, while Middle Eastern countries may have unique local standards.
- Documentation and Traceability: Ensure that suppliers maintain proper documentation for all quality checks and certifications. This is particularly important when dealing with multiple jurisdictions, as it helps in regulatory compliance and product recalls if necessary.
- Cultural Considerations: Be aware of cultural differences that may affect communication and expectations regarding quality assurance. Establishing clear guidelines and regular communication can help bridge these gaps.
By understanding the manufacturing processes and quality assurance measures in place for vending machines, B2B buyers can make informed decisions and select reliable suppliers that meet their operational needs and quality expectations.
Related Video: SMART Quality Control for Manufacturing
Comprehensive Cost and Pricing Analysis for vending machine warehouse near me Sourcing
When sourcing from a vending machine warehouse, understanding the comprehensive cost structure and pricing dynamics is essential for making informed decisions. The cost components involved in this process can be broken down into several key areas:
Cost Components
-
Materials: The choice of materials significantly impacts the overall cost. High-quality, durable materials may have higher upfront costs but can lead to lower maintenance expenses over time. For example, stainless steel machines may cost more initially but offer longevity and reduced replacement needs.
-
Labor: Labor costs vary widely depending on the location of the warehouse and the expertise required for assembling and maintaining the vending machines. Regions with higher labor costs may influence overall pricing, so it’s beneficial to assess the cost of skilled versus unskilled labor in the supplier’s country.
-
Manufacturing Overhead: This includes expenses related to factory operations, such as utilities, rent, and equipment depreciation. Understanding the overhead costs can provide insights into pricing strategies and potential areas for negotiation.
-
Tooling: If customization is required, tooling costs can become significant. Custom molds or specialized machinery may be necessary, which can escalate the initial investment.
-
Quality Control (QC): Implementing stringent QC measures ensures that the vending machines meet required standards. However, these processes add to the overall cost. International buyers should inquire about the QC practices of suppliers to ensure product reliability.
-
Logistics: Shipping costs can vary based on distance, weight, and the mode of transport. Understanding the implications of Incoterms is crucial; they define the responsibilities of buyers and sellers in shipping arrangements, affecting the total cost.
-
Margin: Suppliers typically add a profit margin on top of their costs. This margin can fluctuate based on market demand, competition, and the supplier’s pricing strategy.
Price Influencers
Several factors can influence the pricing of vending machines:
-
Volume/MOQ (Minimum Order Quantity): Purchasing in larger quantities often leads to volume discounts. Buyers should assess their immediate needs against potential savings from bulk buying.
-
Specifications/Customization: Custom features or specifications can increase costs. Buyers should clearly define their requirements to avoid unexpected expenses.
-
Materials and Quality/Certifications: Higher quality materials and compliance with international certifications (e.g., ISO standards) can raise costs but may be necessary for specific markets.
-
Supplier Factors: The reputation, reliability, and financial stability of suppliers can impact pricing. Engaging with well-established suppliers may offer more stability, albeit at a higher price point.
-
Incoterms: Understanding Incoterms (like FOB, CIF) is vital as they dictate who bears the costs and risks during shipping, significantly affecting the total cost.
Buyer Tips
To navigate the cost landscape effectively, international B2B buyers can adopt several strategies:
-
Negotiation: Engage in proactive negotiations with suppliers to secure better pricing. Highlighting potential for long-term partnership can incentivize suppliers to offer more favorable terms.
-
Cost-Efficiency: Assess the Total Cost of Ownership (TCO) rather than just the upfront cost. Consider factors like maintenance, energy consumption, and potential downtime when evaluating machines.
-
Pricing Nuances: Be aware of regional pricing differences. For instance, suppliers in Europe may offer higher quality at a premium, while options from Africa and South America may provide competitive pricing but vary in quality and compliance standards.
-
Research and Compare: Utilize multiple suppliers to understand market rates and practices. This can provide leverage during negotiations and ensure that you are getting a competitive price.
Disclaimer
Prices can fluctuate based on market conditions, currency exchange rates, and specific supplier offerings. It is advisable for buyers to conduct thorough due diligence and obtain multiple quotes before making purchasing decisions.
Spotlight on Potential vending machine warehouse near me Manufacturers and Suppliers
- (No specific manufacturer data was available or requested for detailed profiling in this section for vending machine warehouse near me.)*
Essential Technical Properties and Trade Terminology for vending machine warehouse near me
Essential Technical Properties
When sourcing vending machines from warehouses, understanding the following technical properties is vital for international B2B buyers. These specifications can significantly impact the performance, longevity, and suitability of vending machines for specific markets.
-
Material Grade
The quality of materials used in vending machines, such as stainless steel or high-grade plastic, is crucial. Higher material grades often correlate with better durability and resistance to corrosion, which is particularly important in humid or harsh environments. Buyers should ensure that the material grade meets local regulations and is suitable for the intended use case. -
Tolerance
Tolerance refers to the allowable deviation from a specified dimension in the manufacturing of parts. In vending machines, precise tolerances are essential for components like coin mechanisms and product dispensing systems. Ensuring tight tolerances can reduce maintenance costs and improve reliability, making it a key consideration for B2B buyers. -
Energy Efficiency Rating
The energy efficiency of vending machines is increasingly important due to rising energy costs and environmental concerns. Machines with higher energy efficiency ratings can lead to significant cost savings over time and may also qualify for government incentives in certain regions. B2B buyers should prioritize machines that meet or exceed local energy efficiency standards. -
Capacity
The capacity of a vending machine refers to the number of products it can hold. This is an essential factor for businesses looking to maximize sales while minimizing restocking frequency. Understanding the capacity helps buyers choose machines that align with their sales volume and product variety needs. -
Compatibility with Payment Systems
As cashless transactions become more prevalent, compatibility with various payment systems (e.g., mobile payments, credit cards) is crucial. Ensuring that the vending machine supports the preferred payment methods in the target market can enhance customer satisfaction and sales.
Common Trade Terms
Familiarity with industry jargon is essential for navigating procurement and logistics in the vending machine sector. Here are some key terms that buyers should understand:
-
OEM (Original Equipment Manufacturer)
OEM refers to companies that produce components or products that are sold by another company under its brand name. When purchasing vending machines, understanding whether a supplier is an OEM can provide insights into product quality and warranty support. -
MOQ (Minimum Order Quantity)
MOQ indicates the smallest quantity of goods that a supplier is willing to sell. This term is crucial for B2B buyers to understand, as it can affect inventory management and cash flow. Buyers should negotiate MOQs that align with their operational needs. -
RFQ (Request for Quotation)
An RFQ is a document sent to suppliers requesting a price quote for specific products or services. For vending machine buyers, issuing an RFQ can streamline the procurement process and ensure competitive pricing. Clear specifications in the RFQ can lead to more accurate quotes and better decision-making. -
Incoterms (International Commercial Terms)
Incoterms are a set of predefined international trade terms that clarify the responsibilities of buyers and sellers regarding shipping, insurance, and tariffs. Familiarity with Incoterms is essential for B2B buyers to avoid misunderstandings and ensure compliance with international shipping regulations. -
Lead Time
Lead time refers to the amount of time it takes from placing an order to receiving the goods. Understanding lead times is crucial for inventory planning and can impact sales and customer satisfaction. Buyers should inquire about lead times during the procurement process to ensure timely delivery.
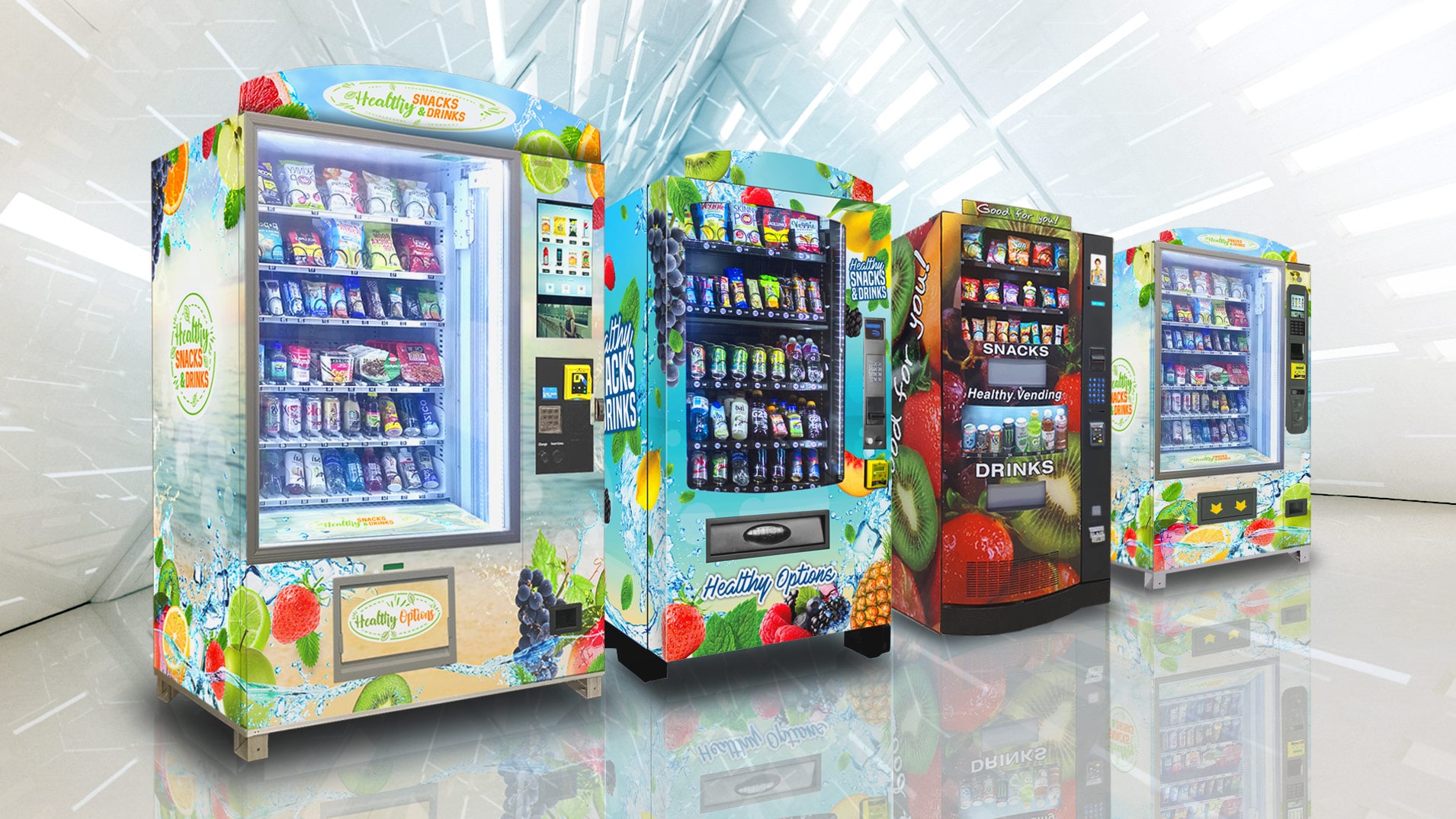
Illustrative Image (Source: Google Search)
By grasping these technical properties and trade terminologies, international B2B buyers can make informed decisions, optimize their procurement strategies, and enhance their operational efficiency in the vending machine market.
Navigating Market Dynamics, Sourcing Trends, and Sustainability in the vending machine warehouse near me Sector
Market Overview & Key Trends
The vending machine sector is experiencing dynamic shifts driven by technological advancements and changing consumer preferences. For international B2B buyers, particularly from regions such as Africa, South America, the Middle East, and Europe, understanding these market drivers is crucial. One of the most significant trends is the integration of IoT (Internet of Things) technology in vending machines, enabling real-time inventory management and customer interaction. This tech-savvy approach not only enhances operational efficiency but also improves customer engagement through personalized offerings.
Another critical trend is the rise of cashless payment systems. As digital payment methods become more prevalent, vending machines equipped with mobile payment options are gaining traction. This shift aligns with the global move toward contactless transactions, particularly accelerated by the COVID-19 pandemic. B2B buyers should consider sourcing vending machines that support these technologies to meet evolving consumer expectations.
Moreover, the trend towards health and wellness is reshaping product offerings in vending machines. Increased demand for healthy snacks and beverages presents opportunities for suppliers to diversify their inventory. Buyers are encouraged to identify local or international vendors who can provide innovative, health-conscious products that cater to this growing market segment.
Lastly, the competitive landscape is becoming increasingly globalized. B2B buyers must stay informed about emerging players and their unique value propositions, particularly in regions like Europe and Africa where local preferences may differ significantly. Engaging with suppliers who understand these regional nuances can lead to strategic advantages in sourcing.
Sustainability & Ethical Sourcing in B2B
In an era where environmental concerns are paramount, sustainability has become a pivotal factor in B2B sourcing decisions. For the vending machine sector, this translates into the need for environmentally friendly practices throughout the supply chain. Buyers should prioritize suppliers who demonstrate commitment to sustainable sourcing, such as using recyclable materials and minimizing carbon footprints in their operations.
The impact of vending machines on the environment can be mitigated through the adoption of energy-efficient technologies. Machines that consume less energy not only reduce operational costs but also align with global sustainability goals. B2B buyers should seek out vending solutions that carry certifications, such as Energy Star or similar green labels, which indicate compliance with strict energy efficiency standards.
Moreover, ethical sourcing practices are gaining traction, particularly in regions sensitive to social responsibility. This includes ensuring fair labor practices and transparency in the supply chain. Buyers can enhance their brand reputation and customer loyalty by partnering with vendors who adhere to these principles. Certifications like Fair Trade or those from recognized organizations can serve as benchmarks when assessing potential suppliers.
Brief Evolution/History
The vending machine industry has evolved significantly since its inception in the late 19th century. Initially focused on dispensing simple products like postcards and chewing gum, the sector has transformed into a sophisticated market characterized by diverse offerings, including fresh food and beverages. The introduction of advanced technologies, such as cashless payments and IoT connectivity, has revolutionized consumer interaction and operational efficiency.
This evolution has been particularly pronounced in Europe and North America, where vending machines are now seen as integral to convenience retailing. As global markets expand, particularly in Africa and South America, the potential for innovation and growth in the vending machine sector remains substantial. B2B buyers looking to enter or expand in this market must remain agile and informed about ongoing trends and technological advancements to succeed.
Related Video: Incoterms for beginners | Global Trade Explained
Frequently Asked Questions (FAQs) for B2B Buyers of vending machine warehouse near me
-
What criteria should I use for vetting vending machine suppliers?
When vetting suppliers, focus on their industry experience, client testimonials, and certifications. Assess their production capacity, quality control measures, and compliance with international standards. It’s also beneficial to request samples to evaluate product quality firsthand. Additionally, check their financial stability and the ability to handle your specific requirements, particularly regarding customization and after-sales service. -
Can I customize vending machines to suit my business needs?
Yes, many suppliers offer customization options for vending machines. This may include branding, size, and the types of products dispensed. When discussing customization, be clear about your specifications and ensure that the supplier can meet these needs. Additionally, inquire about the associated costs and lead times for customized orders to align with your business strategy. -
What are the typical minimum order quantities (MOQs) and lead times?
MOQs can vary widely among suppliers, often depending on the type of vending machines and customization required. Generally, expect MOQs ranging from 5 to 50 units for standard models. Lead times typically range from 4 to 12 weeks, depending on the complexity of the order and the supplier’s production schedule. Always confirm these details upfront to avoid unexpected delays in your supply chain. -
What payment options are available for international purchases?
Payment methods for international orders typically include bank transfers, letters of credit, and payment platforms like PayPal. It’s important to discuss payment terms upfront, including deposit requirements and payment schedules. Additionally, consider using escrow services for large transactions to ensure protection against fraud and to facilitate smoother transactions. -
How can I ensure quality assurance and compliance with standards?
Request documentation that confirms compliance with relevant international quality standards, such as ISO certifications. Ask suppliers about their quality assurance processes, including inspections and testing protocols. Additionally, consider third-party quality audits or inspections to verify product quality before shipping, particularly for large or customized orders. -
What logistics considerations should I be aware of when sourcing vending machines?
Logistics is crucial when sourcing vending machines internationally. Ensure that the supplier can handle shipping logistics, including customs clearance and delivery to your location. Discuss shipping options, costs, and estimated delivery times to avoid unexpected delays. It’s also wise to consider local regulations regarding the import of vending machines to ensure compliance. -
How should I handle disputes with suppliers?
To mitigate disputes, establish clear contracts that outline terms of sale, delivery expectations, and warranties. In case of disputes, maintain open communication with the supplier to resolve issues amicably. If necessary, refer to the terms of the contract for dispute resolution mechanisms, such as mediation or arbitration. Having a legal expert review contracts can also provide additional protection. -
Are there specific certifications I should look for in vending machines?
Yes, look for certifications that validate safety, energy efficiency, and environmental impact, such as CE marking in Europe or UL certification in the U.S. These certifications ensure that the machines comply with local regulations and industry standards. Additionally, inquire about any specific certifications relevant to your market, as these can enhance your product’s credibility and acceptance.
Strategic Sourcing Conclusion and Outlook for vending machine warehouse near me
In conclusion, the strategic sourcing of vending machines represents a pivotal opportunity for international B2B buyers, particularly in regions like Africa, South America, the Middle East, and Europe. By understanding local market dynamics and leveraging regional suppliers, businesses can ensure a steady supply of quality vending machines tailored to their specific needs. Key takeaways include the importance of establishing reliable supplier relationships, conducting thorough market research, and adopting a flexible sourcing strategy that accommodates varying consumer preferences and economic conditions.
Emphasizing value, strategic sourcing not only enhances operational efficiency but also fosters innovation in product offerings, enabling businesses to stay competitive in an evolving market landscape. As businesses navigate the complexities of sourcing, they should prioritize sustainability and ethical practices to appeal to increasingly conscious consumers.
Looking ahead, the vending machine industry is poised for growth, driven by technological advancements and a shift towards healthier options. International B2B buyers are encouraged to actively engage with local suppliers and explore new partnerships to capitalize on these trends. Embrace the future of vending by strategically sourcing your next machine today, ensuring your business remains at the forefront of this dynamic market.