Your Ultimate Guide to Sourcing Vending Machine Profit Per
Guide to Vending Machine Profit Per Month
- Introduction: Navigating the Global Market for vending machine profit per month
- Understanding vending machine profit per month Types and Variations
- Key Industrial Applications of vending machine profit per month
- Strategic Material Selection Guide for vending machine profit per month
- In-depth Look: Manufacturing Processes and Quality Assurance for vending machine profit per month
- Comprehensive Cost and Pricing Analysis for vending machine profit per month Sourcing
- Spotlight on Potential vending machine profit per month Manufacturers and Suppliers
- Essential Technical Properties and Trade Terminology for vending machine profit per month
- Navigating Market Dynamics, Sourcing Trends, and Sustainability in the vending machine profit per month Sector
- Frequently Asked Questions (FAQs) for B2B Buyers of vending machine profit per month
- Strategic Sourcing Conclusion and Outlook for vending machine profit per month
Introduction: Navigating the Global Market for vending machine profit per month
Navigating the global market for vending machines presents a significant opportunity for international B2B buyers looking to diversify and enhance their revenue streams. Understanding vending machine profit per month is critical, as it not only influences operational decisions but also shapes the long-term viability of vending machine investments. With the increasing demand for automated retail solutions across Africa, South America, the Middle East, and Europe, this guide aims to equip buyers with the essential knowledge to make informed sourcing decisions.
This comprehensive resource will delve into various aspects of vending machine profitability, including types of vending machines, materials used, manufacturing and quality control processes, and supplier options. Additionally, we will explore the cost structures associated with vending operations and analyze current market trends. By addressing frequently asked questions (FAQs), we will provide clarity on common concerns that B2B buyers face when entering this market.
Empowered with this information, international buyers can navigate the complexities of the vending machine landscape, identify profitable opportunities, and establish strategic partnerships. Whether you are a seasoned player in the vending industry or a newcomer eager to explore the potential of this automated retail sector, this guide serves as your roadmap to maximizing profitability in the global vending machine market.
Understanding vending machine profit per month Types and Variations
Type Name | Key Distinguishing Features | Primary B2B Applications | Brief Pros & Cons for Buyers |
---|---|---|---|
Snack Vending Machines | Focus on snacks and beverages, high turnover | Offices, schools, hospitals | Pros: Quick sales, low maintenance. Cons: Limited product range can lead to stale inventory. |
Healthy Vending Machines | Offers nutritious snacks and beverages | Gyms, schools, corporate offices | Pros: Appeals to health-conscious consumers. Cons: Higher costs for premium products. |
Specialty Vending Machines | Unique offerings (electronics, personal care) | Airports, malls, specialty stores | Pros: High margins on niche products. Cons: Requires targeted marketing and placement. |
Coffee Vending Machines | Focus on coffee and hot beverages | Offices, factories, hospitals | Pros: High demand, repeat customers. Cons: Requires regular maintenance and ingredient supply. |
Combination Vending Machines | Offers both snacks and drinks in one unit | Universities, public transport hubs | Pros: Versatile, caters to diverse customer needs. Cons: More complex to manage inventory. |
Snack Vending Machines
Snack vending machines are designed primarily for high turnover of snacks and beverages. They are commonly found in locations such as offices, schools, and hospitals. The key advantage of these machines is their quick sales potential and low maintenance requirements. However, a significant downside is that they often have a limited product range, which can lead to stale inventory if not managed properly. Buyers should consider the location’s traffic patterns and customer preferences to maximize profitability.
Healthy Vending Machines
Healthy vending machines focus on providing nutritious snacks and beverages, catering to the growing health-conscious market. These machines are typically placed in gyms, schools, and corporate offices. The primary advantage is their appeal to consumers looking for healthier options, which can drive sales. However, the cost of sourcing premium products can be higher, impacting the overall profit margins. B2B buyers should evaluate the target demographic and market trends to ensure a successful placement.
Specialty Vending Machines
Specialty vending machines offer unique products such as electronics, personal care items, or local artisan goods. They are often strategically placed in high-traffic areas like airports, malls, and specialty stores. The high margins on niche products can be very profitable, but these machines require targeted marketing and careful placement to attract the right customers. B2B buyers must assess the local market demand and competitive landscape before investing in specialty vending options.
Coffee Vending Machines
Coffee vending machines cater to the high demand for coffee and hot beverages, making them popular in offices, factories, and hospitals. Their main advantages include repeat customers and the potential for high demand, especially during morning hours. However, they require regular maintenance and a consistent supply of ingredients, which can complicate operations. Buyers should consider the frequency of use and potential partnerships with local coffee suppliers to enhance service quality.
Combination Vending Machines
Combination vending machines provide a versatile solution by offering both snacks and drinks in one unit. They are ideal for locations such as universities and public transport hubs where consumer needs vary widely. The main benefit is their ability to cater to diverse customer preferences, increasing sales potential. However, managing inventory can be more complex, as it requires balancing stock levels for both snacks and beverages. B2B buyers should analyze foot traffic and customer demographics to optimize product offerings in these machines.
Related Video: Economic models | Basic economics concepts | AP Macroeconomics and Microeconomics | Khan Academy
Key Industrial Applications of vending machine profit per month
Industry/Sector | Specific Application of vending machine profit per month | Value/Benefit for the Business | Key Sourcing Considerations for this Application |
---|---|---|---|
Food & Beverage | Automated snack and beverage sales | Increased revenue from high-traffic areas | Product variety, shelf life, and local preferences |
Healthcare | Dispensing medical supplies and hygiene products | Improved accessibility for essential items | Compliance with health regulations, secure payment options |
Education | Selling school supplies and snacks | Convenient access for students and staff | Location within campus, product selection aligned with student needs |
Transportation | Providing travel essentials at transit hubs | Enhanced passenger experience and additional revenue | High-demand products, payment flexibility, and machine maintenance |
Corporate Offices | Offering refreshments and snacks in break rooms | Boosts employee satisfaction and productivity | Stock rotation, machine reliability, and variety of healthy options |
Food & Beverage Industry
Vending machines in the food and beverage sector are utilized to automate snack and drink sales in high-traffic areas such as malls, airports, and office complexes. This application allows businesses to capitalize on impulse purchases, thus increasing revenue without the need for additional staff. For international buyers, understanding local preferences for snacks and beverages is crucial, as is ensuring compliance with local health regulations regarding food safety.
Healthcare Sector
In healthcare settings, vending machines are increasingly being used to dispense medical supplies and hygiene products. This application enhances accessibility to essential items like first-aid kits, hand sanitizers, and personal protective equipment (PPE). For buyers in this sector, key considerations include compliance with healthcare regulations, the need for secure payment options, and the ability to maintain inventory levels that align with patient needs.
Education Sector
Educational institutions leverage vending machines to provide students and staff with easy access to school supplies, snacks, and beverages. This application not only meets the convenience needs of students but also serves as an additional revenue stream for schools. Buyers should focus on machine placement within campuses, ensuring that products cater to students’ preferences, and maintaining a consistent supply of popular items.
Transportation Sector
Vending machines positioned in transportation hubs, such as train stations and airports, offer travelers essential items like snacks, drinks, and travel accessories. This application enhances the passenger experience while generating additional revenue for the operators. Key sourcing considerations include stocking high-demand products, providing flexible payment options, and ensuring machines are regularly maintained to minimize downtime.
Corporate Offices
In corporate environments, vending machines are used to offer refreshments and snacks in break rooms, contributing to employee satisfaction and productivity. This application allows companies to cater to diverse dietary preferences while providing convenience. B2B buyers in this sector should consider factors such as stock rotation practices, machine reliability, and the variety of healthy options to meet the needs of a modern workforce.
Related Video: How to Start a $30K Per Month Vending Machine Business
Strategic Material Selection Guide for vending machine profit per month
When selecting materials for vending machines, particularly with the aim of maximizing profit per month, it is essential to consider the properties, advantages, and limitations of each material. This analysis will focus on four common materials: stainless steel, aluminum, plastic, and glass. Each material has unique characteristics that can impact the performance and profitability of vending machines in diverse international markets.
Stainless Steel
Key Properties: Stainless steel is known for its excellent corrosion resistance, high strength, and ability to withstand high temperatures and pressures. It is often used in environments where hygiene is paramount, such as food and beverage vending machines.
Pros & Cons: The primary advantage of stainless steel is its durability and resistance to rust and stains, making it ideal for outdoor and high-use environments. However, it tends to be more expensive than other materials, and its manufacturing process can be complex, leading to higher initial costs.
Impact on Application: Stainless steel is compatible with a wide range of media, including water, soft drinks, and snacks. Its hygienic properties make it suitable for food applications, which is critical in regions with strict health regulations.
Considerations for International Buyers: Buyers from Africa, South America, the Middle East, and Europe should ensure compliance with local health and safety standards, such as ASTM or DIN. The preference for stainless steel may vary based on local market conditions and consumer expectations regarding quality.
Aluminum
Key Properties: Aluminum is lightweight, corrosion-resistant, and has good thermal conductivity. It is often used for vending machine exteriors and components.
Pros & Cons: The lightweight nature of aluminum makes it easier to transport and install, reducing overall shipping costs. However, it is less durable than stainless steel and can be prone to dents and scratches, which may affect the aesthetic appeal of vending machines.
Impact on Application: Aluminum is suitable for a variety of products, including canned beverages and packaged snacks. Its thermal properties help maintain the temperature of cold drinks, enhancing customer satisfaction.
Considerations for International Buyers: When sourcing aluminum components, buyers should consider local regulations regarding recycling and environmental impact. Compliance with standards like JIS may also be necessary, particularly in Japan and other Asian markets.
Plastic
Key Properties: Plastic materials, such as polyethylene and polypropylene, are lightweight, flexible, and resistant to moisture and chemicals. They are commonly used for internal components and some external parts of vending machines.
Pros & Cons: The primary advantage of plastic is its low cost and ease of manufacturing. It can be molded into complex shapes, allowing for innovative designs. However, plastics can be less durable than metals and may degrade over time, especially under UV exposure.
Impact on Application: Plastic is suitable for holding non-perishable items and can be used in vending machines for snacks and drinks. However, its use in food applications may require compliance with specific food safety standards.
Considerations for International Buyers: Buyers should be aware of regulations regarding plastic use and recycling in their respective regions. For instance, Europe has stringent regulations on plastic waste, which may influence material selection.
Glass
Key Properties: Glass is known for its aesthetic appeal and excellent barrier properties, making it a popular choice for displaying beverages. It is non-reactive and can maintain the integrity of the product.
Pros & Cons: The key advantage of glass is its ability to preserve product quality and enhance visual appeal. However, it is heavier and more fragile than other materials, which can increase shipping costs and the risk of breakage.
Impact on Application: Glass is particularly suitable for vending machines selling bottled beverages, as it provides an upscale appearance. However, its weight can limit the number of units that can be installed in a single machine.
Considerations for International Buyers: Buyers should consider the transportation and handling challenges associated with glass. Compliance with safety standards, particularly in regions with high breakage rates, is crucial.
Summary Table
Material | Typical Use Case for vending machine profit per month | Key Advantage | Key Disadvantage/Limitation | Relative Cost (Low/Med/High) |
---|---|---|---|---|
Stainless Steel | Food and beverage vending machines | Durable, corrosion-resistant | Higher cost, complex manufacturing | High |
Aluminum | Exteriors and components for vending machines | Lightweight, easy to transport | Less durable, prone to dents | Medium |
Plastic | Internal components and non-perishable items | Low cost, easy to manufacture | Less durable, UV degradation | Low |
Glass | Bottled beverage vending machines | Preserves product quality, aesthetic | Heavy, fragile | Medium |
This strategic material selection guide provides a comprehensive overview of the materials commonly used in vending machines, emphasizing their properties and implications for international B2B buyers. Understanding these factors can significantly impact profitability and operational efficiency in diverse markets.
In-depth Look: Manufacturing Processes and Quality Assurance for vending machine profit per month
Manufacturing processes and quality assurance are critical components in the production of vending machines, influencing not only their performance but also the profitability of B2B buyers. Understanding these processes can help international buyers, especially from Africa, South America, the Middle East, and Europe, make informed purchasing decisions.
Manufacturing Processes
1. Material Preparation
The first stage in the manufacturing of vending machines involves selecting and preparing the materials. Common materials include steel, plastics, and electronic components.
- Steel: Used for the frame and exterior, steel provides durability and security.
- Plastics: Utilized for internal components and display panels, plastics can be molded into various shapes.
- Electronics: Components like circuit boards, sensors, and payment systems are crucial for the machine’s operation.
Before manufacturing begins, materials undergo inspection to ensure they meet specified standards, including dimensional accuracy and material properties.
2. Forming
In this stage, raw materials are shaped into the necessary components through various techniques:
- Cutting: Steel sheets are cut into specific dimensions using laser or water jet cutting for precision.
- Bending: Metal parts are bent into required shapes using press brakes or CNC machines.
- Molding: Plastics are molded into specific forms, such as trays or panels, using injection molding processes.
These forming techniques are essential to ensure that each part fits together correctly and functions as intended.
3. Assembly
Once individual parts are formed, they are assembled into the final product. This stage includes:
- Sub-assembly: Components like coin mechanisms, product trays, and electronic systems are pre-assembled.
- Main Assembly: The sub-assemblies are integrated into the vending machine frame. Automated assembly lines may be used to enhance efficiency.
- Quality Checks: During assembly, operators conduct initial quality checks to catch defects early in the process.
4. Finishing
The finishing stage involves applying surface treatments and coatings to enhance durability and aesthetics.
- Painting: Machines are painted with weather-resistant coatings to protect against corrosion.
- Labeling: Branding and instructional labels are applied to ensure usability.
- Final Assembly: All components, including locks and payment systems, are finalized in this stage.
This stage not only improves the product’s appearance but also extends its lifespan, which is crucial for maintaining profitability.
Quality Assurance
Quality assurance (QA) processes ensure that vending machines meet international standards and customer expectations. A robust QA system involves several key elements:
International Standards
International standards such as ISO 9001 provide a framework for quality management systems that help manufacturers ensure consistent quality. Compliance with these standards is a critical factor for B2B buyers looking for reliable suppliers.
- CE Marking: In Europe, CE marking indicates compliance with health, safety, and environmental protection standards.
- API Certification: For machines that dispense pharmaceuticals or food, API certification can be essential, ensuring adherence to additional safety standards.
Quality Control Checkpoints
Quality control (QC) checkpoints are integral to the manufacturing process. Key checkpoints include:
- Incoming Quality Control (IQC): Materials are inspected upon arrival to verify they meet specifications before production begins.
- In-Process Quality Control (IPQC): Ongoing checks during manufacturing help identify defects early, preventing costly rework.
- Final Quality Control (FQC): The finished product undergoes thorough inspections and testing to ensure it functions correctly and meets quality standards.
Common Testing Methods
To ensure quality, various testing methods are employed, such as:
- Functional Testing: Machines are powered on to check the operation of electronic components.
- Durability Testing: Vending machines are subjected to stress tests to simulate long-term usage.
- Safety Testing: Compliance with electrical safety standards is verified through rigorous testing.
Verifying Supplier Quality Control
B2B buyers must take proactive steps to verify the quality control processes of their suppliers. Here are some actionable strategies:
-
Supplier Audits: Conducting regular audits of suppliers can provide insights into their manufacturing processes and quality management systems. This includes reviewing their compliance with international standards.
-
Quality Reports: Requesting detailed quality reports can help assess the reliability of the supplier’s products. These reports should include data on defect rates and corrective actions taken.
-
Third-Party Inspections: Engaging third-party inspection services can provide an unbiased evaluation of the manufacturing process and finished products. This is particularly beneficial for buyers in regions with varying quality standards.
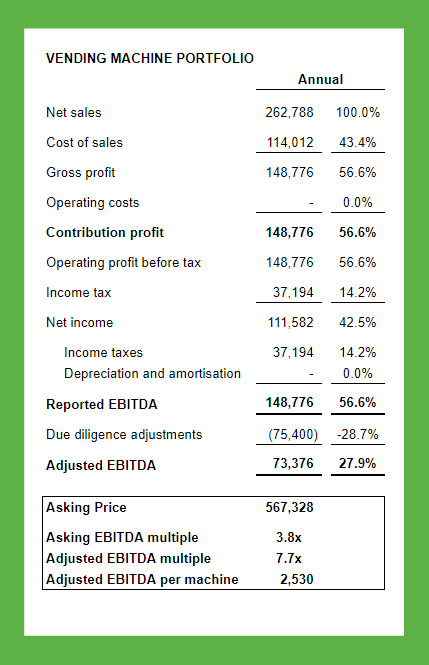
Illustrative Image (Source: Google Search)
Quality Control and Certification Nuances
International B2B buyers should be aware of specific nuances related to quality control and certification in different regions:
-
Africa: Local regulations may vary significantly, and certifications may not be universally recognized. Buyers should ensure that suppliers are compliant with both local and international standards.
-
South America: Many countries have unique requirements for product safety and performance. Understanding these can prevent compliance issues.
-
Middle East: Import regulations can be stringent, necessitating thorough documentation to ensure that products meet local standards.
-
Europe: The CE marking is critical for market entry, and buyers must verify that all components of the vending machines are compliant.
By focusing on these manufacturing and quality assurance processes, international B2B buyers can make informed decisions that enhance their vending machine profitability while ensuring compliance and quality.
Related Video: Business English Vocabulary : VV 47 – Manufacturing & Production Process (1) | English Vocabulary
Comprehensive Cost and Pricing Analysis for vending machine profit per month Sourcing
When analyzing the cost structure and pricing for vending machine profit per month sourcing, it is essential to break down the various components that contribute to the overall expense. Understanding these elements will enable international B2B buyers, particularly from regions such as Africa, South America, the Middle East, and Europe, to make informed purchasing decisions.
Cost Components
-
Materials: The primary materials for vending machines include metals, plastics, and electronic components. Prices can vary significantly based on the quality and source of these materials. For instance, sourcing high-grade steel from Europe may incur higher costs compared to locally sourced alternatives in Africa or South America.
-
Labor: Labor costs are influenced by local wage rates and the complexity of assembly processes. Regions with higher labor costs may see increased pricing. For instance, labor in Western Europe is typically more expensive than in Eastern Europe or Turkey, impacting the final pricing.
-
Manufacturing Overhead: This encompasses the indirect costs associated with production, such as utilities, rent, and administrative expenses. Efficient manufacturing processes can help reduce overhead, thus lowering the overall cost.
-
Tooling: Tooling costs include the expenses related to the equipment needed for production. Custom tooling for specialized machines can significantly increase costs, especially for low-volume orders.
-
Quality Control (QC): Implementing stringent quality control measures is crucial for ensuring product reliability and safety. However, this also adds to the overall cost structure. Buyers should consider suppliers that offer robust QC processes as a long-term investment.
-
Logistics: Shipping and handling costs can vary widely based on the distance, mode of transport, and Incoterms chosen. For international buyers, understanding the implications of logistics costs is vital, as these can significantly affect the total expense.
-
Margin: Suppliers typically add a profit margin to cover their costs and earn a profit. This margin can vary based on competition, market demand, and the perceived value of the product.
Price Influencers
-
Volume/MOQ (Minimum Order Quantity): Bulk purchasing can lead to significant discounts. Buyers should negotiate for lower prices by increasing order quantities when feasible.
-
Specifications/Customization: Customized machines tailored to specific needs may incur additional costs. Buyers must balance the need for customization with their budget constraints.
-
Quality/Certifications: Machines that meet international quality standards and certifications can command higher prices. However, they often offer better reliability and lower maintenance costs in the long run.
-
Supplier Factors: The reputation and reliability of suppliers can influence pricing. Established suppliers with proven track records may charge more due to their quality assurance.
-
Incoterms: Different Incoterms can affect the total cost. For example, choosing FOB (Free On Board) can reduce upfront costs but may increase logistical challenges and risks for buyers.
Buyer Tips
-
Negotiation: Always negotiate terms and pricing. Suppliers may have flexibility in pricing, especially if they see potential for ongoing business.
-
Cost-Efficiency: Analyze the Total Cost of Ownership (TCO), which includes not only the initial purchase price but also maintenance, operation, and logistics over the machine’s lifespan.
-
Pricing Nuances: Be aware of regional pricing variations. For example, machines sourced from Europe may be priced higher due to labor and material costs, while those from Asia might offer lower prices but require careful scrutiny of quality.
Disclaimer
Prices and cost structures mentioned herein are indicative and may vary based on market conditions, supplier negotiations, and specific buyer requirements. It is advisable to conduct thorough research and obtain multiple quotes to ensure competitive pricing.
By understanding these cost components and pricing influencers, international B2B buyers can navigate the complexities of sourcing vending machines more effectively, ensuring a profitable investment tailored to their market needs.
Spotlight on Potential vending machine profit per month Manufacturers and Suppliers
This section offers a look at a few manufacturers active in the ‘vending machine profit per month’ market. This is a representative sample for illustrative purposes; B2B buyers must conduct their own extensive due diligence before any engagement. Information is synthesized from public sources and general industry knowledge.
Essential Technical Properties and Trade Terminology for vending machine profit per month
In the vending machine industry, understanding key technical properties and trade terminology is vital for optimizing profit margins and ensuring successful operations. Below are essential specifications and terms that B2B buyers should be familiar with when assessing vending machines and their potential profitability.
Essential Technical Properties
-
Material Grade
– Definition: Material grade refers to the type and quality of materials used in the construction of vending machines, such as stainless steel or high-density polyethylene.
– Importance: Higher-grade materials enhance durability, reduce maintenance costs, and ensure longevity, which translates to lower total cost of ownership over time. This is especially critical for machines located in high-traffic areas or harsh environments. -
Dimensions and Capacity
– Definition: This includes the overall size of the vending machine and its storage capacity for products, typically measured in cubic feet or number of slots.
– Importance: Selecting the right dimensions and capacity affects product selection and inventory turnover. A larger capacity can cater to higher demand, while compact machines are ideal for limited spaces.
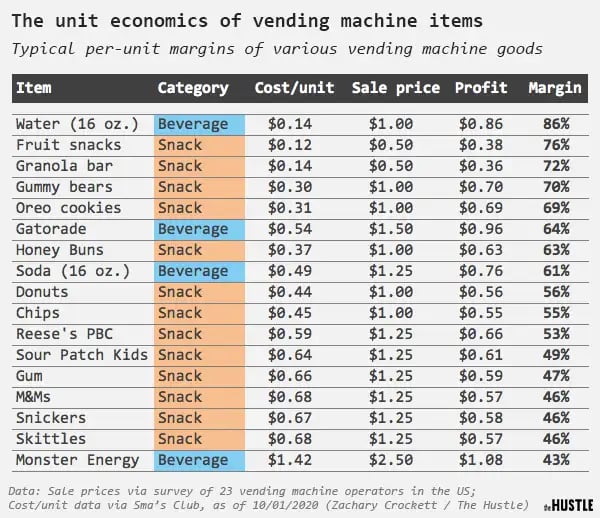
Illustrative Image (Source: Google Search)
-
Power Consumption
– Definition: Power consumption indicates the amount of electricity the vending machine uses, often measured in watts.
– Importance: Lower power consumption reduces operational costs, making the machine more appealing to businesses looking to minimize expenses. Energy-efficient models can also qualify for green certifications, enhancing marketability. -
Payment Options
– Definition: This refers to the types of payment systems integrated into the vending machine, such as cash, credit/debit cards, and mobile payments.
– Importance: Offering diverse payment options can significantly increase sales by catering to customer preferences. In regions with high mobile payment adoption, machines equipped for these transactions can experience higher profitability. -
Temperature Control
– Definition: This specification relates to the machine’s ability to maintain specific temperatures for perishable items, typically measured in degrees Celsius or Fahrenheit.
– Importance: Proper temperature control is essential for vending machines that dispense food and beverages. Maintaining appropriate temperatures ensures product quality and safety, which is critical for customer satisfaction and compliance with health regulations.
Trade Terminology
-
OEM (Original Equipment Manufacturer)
– Definition: An OEM is a company that produces parts or equipment that may be marketed by another manufacturer.
– Relevance: Understanding OEM relationships is important for buyers looking to source high-quality machines or components, as they can affect warranty, service, and support. -
MOQ (Minimum Order Quantity)
– Definition: MOQ is the smallest quantity of a product that a supplier is willing to sell.
– Relevance: Knowing the MOQ is crucial for budgeting and inventory planning. Buyers must assess whether the MOQ aligns with their demand and storage capabilities.
-
RFQ (Request for Quotation)
– Definition: An RFQ is a document issued to suppliers to solicit price proposals for specific products or services.
– Relevance: Using an RFQ helps buyers compare pricing and terms across different vendors, facilitating informed purchasing decisions. -
Incoterms (International Commercial Terms)
– Definition: Incoterms are a series of pre-defined commercial terms published by the International Chamber of Commerce (ICC) that clarify the responsibilities of buyers and sellers in international transactions.
– Relevance: Familiarity with Incoterms helps buyers understand shipping costs, risks, and responsibilities associated with their purchases, ensuring smoother international transactions. -
Lead Time
– Definition: Lead time refers to the amount of time between placing an order and receiving the product.
– Relevance: Understanding lead times is essential for inventory management and sales planning, especially in fast-moving markets where demand can fluctuate rapidly.
By being well-versed in these technical properties and trade terms, international B2B buyers can make more informed decisions that enhance profitability in the vending machine sector.
Navigating Market Dynamics, Sourcing Trends, and Sustainability in the vending machine profit per month Sector
Market Overview & Key Trends
The global vending machine market is experiencing significant growth, driven by increasing consumer demand for convenience and the rapid evolution of technology. Key drivers include urbanization, changing lifestyles, and a growing preference for cashless transactions. B2B buyers, particularly from regions such as Africa, South America, the Middle East, and Europe, should note that technological advancements, such as IoT-enabled vending machines, are reshaping the landscape. These machines provide real-time data analytics, enhancing inventory management and improving customer engagement through personalized offerings.
Emerging trends include a shift towards healthy vending options as consumers become more health-conscious. This is particularly notable in Europe and North America, where buyers are prioritizing healthier snack and beverage choices in their vending selections. Additionally, the integration of sustainability practices into vending operations is gaining traction. International buyers are increasingly looking for suppliers that offer eco-friendly machines and products, responding to consumer preferences for sustainable and ethically sourced goods.
As competition intensifies, B2B buyers should focus on collaboration with tech providers to leverage innovations that enhance operational efficiency. Understanding local market dynamics, regulatory requirements, and consumer preferences is crucial for successfully navigating the vending machine sector, especially in diverse markets like Turkey and Indonesia.
Sustainability & Ethical Sourcing in B2B
Sustainability is becoming a cornerstone of the vending machine industry, influencing sourcing strategies and product offerings. B2B buyers must prioritize the environmental impact of their supply chains, emphasizing the importance of ethical sourcing. This includes selecting suppliers who adhere to sustainable practices, such as reducing carbon footprints and using renewable resources.
The demand for green certifications is also on the rise. Buyers should seek out products that carry certifications like Energy Star or eco-labels, which indicate compliance with environmental standards. Furthermore, utilizing recyclable materials in machine construction and packaging can significantly minimize waste and enhance brand reputation among environmentally conscious consumers.
As consumers increasingly prefer brands that reflect their values, B2B buyers are urged to evaluate their supply chains for sustainability. This not only fosters customer loyalty but also aligns with global trends towards corporate responsibility. By investing in sustainable practices, companies can enhance their market positioning and drive profitability in the vending machine sector.
Brief Evolution/History
The vending machine industry has evolved significantly since its inception in the early 20th century. Initially focused on simple transactions for items like cigarettes and candies, the sector has transformed into a sophisticated market integrating advanced technologies and diverse product offerings. The introduction of cashless payment systems and digital interfaces has revolutionized consumer interactions, allowing for greater convenience and efficiency.
As consumer preferences shifted over time, the industry adapted by offering healthier and more varied options, reflecting broader societal trends towards wellness and convenience. This evolution is critical for B2B buyers to understand, as it underscores the necessity of staying attuned to market demands and technological advancements to remain competitive in the global vending machine landscape.
Related Video: Incoterms for beginners | Global Trade Explained
Frequently Asked Questions (FAQs) for B2B Buyers of vending machine profit per month
-
What factors influence the profit per month for vending machines?
The profit from vending machines is affected by several factors, including location, product selection, pricing strategy, and operational costs. High-traffic areas such as offices, schools, and transportation hubs generally yield higher profits. Additionally, offering popular products, such as healthy snacks or beverages tailored to local preferences, can significantly enhance sales. Regularly analyzing sales data helps in optimizing inventory and product offerings, which can further boost profitability. -
How can I vet suppliers to ensure quality vending machines?
To vet suppliers, start by researching their reputation in the market. Request references and case studies from other B2B buyers to gauge customer satisfaction. Assess the supplier’s certifications, such as ISO or local quality standards, to ensure compliance with safety and quality regulations. Conduct site visits if possible, and evaluate their production processes and quality control measures. Engaging in discussions about warranties and after-sales support can also provide insights into their reliability. -
What customization options are available for vending machines?
Many suppliers offer customization options to suit specific market needs. This can include personalized branding, product configurations, and payment systems. For instance, you can choose machines that accept mobile payments or offer healthy product selections based on regional preferences. Discuss your requirements with suppliers to understand the extent of customization they can provide and how it can enhance your vending machine’s appeal to local consumers. -
What are the typical minimum order quantities (MOQ) and lead times for vending machines?
Minimum order quantities for vending machines can vary widely based on the supplier and the type of machines ordered. Generally, MOQs range from one unit for standard models to several for customized options. Lead times can also differ, typically ranging from a few weeks to several months, depending on production schedules and customization requirements. It’s advisable to confirm these details with the supplier during initial discussions to plan your inventory and cash flow accordingly. -
What payment methods are usually accepted by vending machine suppliers?
Vending machine suppliers typically accept various payment methods, including bank transfers, credit cards, and payment platforms like PayPal. For larger orders, some suppliers may offer financing options or extended payment terms. It’s essential to clarify payment terms upfront, including any deposits required and payment schedules, to avoid misunderstandings later in the purchasing process. -
How can I ensure quality assurance and compliance with regulations?
Quality assurance can be ensured by selecting suppliers who adhere to internationally recognized quality standards and certifications. Request documentation that verifies compliance with local regulations, including health and safety standards. Regular audits and inspections of the machines upon delivery can help identify any issues early on. Establishing a clear communication channel with your supplier for ongoing support and quality feedback is also crucial for maintaining standards. -
What logistics considerations should I be aware of when importing vending machines?
Logistics play a critical role in the successful importation of vending machines. Key considerations include shipping methods, customs clearance, and potential tariffs or duties. Partnering with experienced logistics providers can help navigate these challenges. Be aware of the local regulations in your region regarding the importation of machinery, and ensure that all documentation is complete to avoid delays in delivery. -
What steps should I take if I encounter disputes with a supplier?
In the event of a dispute with a supplier, the first step is to communicate directly with them to resolve the issue amicably. Document all communications and agreements to maintain a clear record. If a resolution cannot be reached, refer to the terms of your contract, which may include mediation or arbitration clauses. Consider involving legal counsel if necessary, especially for international transactions where jurisdiction can complicate matters.
Strategic Sourcing Conclusion and Outlook for vending machine profit per month
In today’s competitive landscape, the potential for vending machine profits is significant, driven by strategic sourcing and smart operational practices. B2B buyers must prioritize cost-effective procurement of high-demand products, leveraging local suppliers to reduce shipping costs and improve inventory turnover. Additionally, investing in technology—such as cashless payment systems and inventory management software—can enhance customer experience and streamline operations, leading to increased sales.
Understanding market trends and consumer preferences is essential for maximizing profits. For instance, targeting specific demographics with tailored product selections can significantly boost machine performance. As you navigate the complexities of the vending industry, remember that data analytics can provide actionable insights, helping you make informed decisions about product offerings and locations.
Looking ahead, the vending machine sector presents ample opportunities for growth, particularly in emerging markets across Africa, South America, the Middle East, and Europe. International B2B buyers are encouraged to embrace innovative solutions and foster strong supplier relationships to capitalize on these opportunities. By doing so, you position your business not just to survive, but to thrive in the evolving landscape of vending. Engage actively with your suppliers, and start exploring new avenues for profit today!