Your Ultimate Guide to Sourcing Vending Machine Police
Guide to Vending Machine Police Station
- Introduction: Navigating the Global Market for vending machine police station
- Understanding vending machine police station Types and Variations
- Key Industrial Applications of vending machine police station
- Strategic Material Selection Guide for vending machine police station
- In-depth Look: Manufacturing Processes and Quality Assurance for vending machine police station
- Comprehensive Cost and Pricing Analysis for vending machine police station Sourcing
- Spotlight on Potential vending machine police station Manufacturers and Suppliers
- Essential Technical Properties and Trade Terminology for vending machine police station
- Navigating Market Dynamics, Sourcing Trends, and Sustainability in the vending machine police station Sector
- Frequently Asked Questions (FAQs) for B2B Buyers of vending machine police station
- Strategic Sourcing Conclusion and Outlook for vending machine police station
Introduction: Navigating the Global Market for vending machine police station
In the evolving landscape of public safety and community engagement, vending machine police stations represent a groundbreaking solution. These innovative kiosks not only enhance accessibility to police services but also promote community interaction and trust. As international B2B buyers from regions like Africa, South America, the Middle East, and Europe seek to invest in public safety solutions, understanding the critical elements of vending machine police stations becomes essential.
This comprehensive guide delves into the various types of vending machine police stations available in the market, highlighting their unique features and functionalities. Buyers will gain insights into the materials used in their construction, manufacturing processes, and quality control measures that ensure durability and reliability. Furthermore, the guide provides a thorough overview of potential suppliers, enabling informed sourcing decisions based on performance and reputation.
Cost considerations are also addressed, offering a transparent view of pricing structures to assist in budgeting and financial planning. Additionally, the guide answers frequently asked questions, clarifying common concerns and operational queries that potential buyers may have.
By equipping B2B buyers with detailed knowledge and actionable insights, this guide empowers them to make informed decisions that align with their community safety goals and budgetary constraints. Investing in vending machine police stations not only enhances public safety but also fosters a stronger connection between law enforcement and the communities they serve.
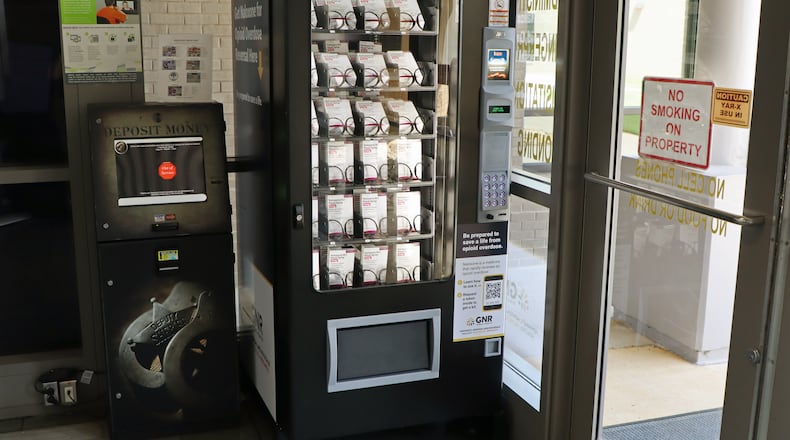
Illustrative Image (Source: Google Search)
Understanding vending machine police station Types and Variations
Type Name | Key Distinguishing Features | Primary B2B Applications | Brief Pros & Cons for Buyers |
---|---|---|---|
Traditional Vending Machine | Dispenses snacks and drinks; cash and card payment options | Retail environments, schools, offices | Pros: Low maintenance, easy to restock. Cons: Limited product range. |
Automated Police Report Kiosk | Touchscreen interface for filing reports; digital submission | Police precincts, community centers | Pros: Reduces wait times, enhances reporting efficiency. Cons: Initial setup costs can be high. |
Evidence Collection Station | Secure storage for evidence; integrated tracking system | Police departments, law enforcement | Pros: Improves evidence handling, increases security. Cons: Requires ongoing maintenance and monitoring. |
Community Engagement Kiosk | Offers information on local services; interactive maps | Public spaces, community events | Pros: Enhances community relations, provides valuable info. Cons: May require regular updates and tech support. |
Mobile Vending Unit | Compact, transportable units for temporary setups | Events, festivals, emergency services | Pros: Flexible location, quick deployment. Cons: Limited inventory capacity. |
Traditional Vending Machine
Traditional vending machines are widely used in various environments such as schools, offices, and retail settings. They primarily dispense snacks and beverages while offering payment options through cash or cards. B2B buyers should consider their low maintenance needs and ease of restocking, making them a practical choice for high-traffic areas. However, the limited product range may not cater to all customer preferences, potentially impacting sales.
Automated Police Report Kiosk
These kiosks allow citizens to file police reports digitally via a touchscreen interface, streamlining the reporting process. They are particularly beneficial for police precincts and community centers, reducing wait times for individuals needing to report incidents. While they enhance operational efficiency, B2B buyers should be aware of the initial setup costs, which can be significant, especially for smaller departments.
Evidence Collection Station
Designed for law enforcement, evidence collection stations provide secure storage for collected evidence, often featuring an integrated tracking system. This ensures that evidence is handled correctly and securely, thereby improving the overall integrity of law enforcement processes. B2B buyers must weigh the benefits of increased security against the ongoing maintenance and monitoring required to keep the system functioning effectively.
Community Engagement Kiosk
These kiosks serve as information hubs in public spaces, offering residents access to local services, interactive maps, and community resources. They are particularly effective at community events and within public parks. B2B buyers should consider the kiosks’ ability to enhance community relations and provide valuable information, although regular updates and technical support may be necessary to maintain their relevance.
Mobile Vending Unit
Mobile vending units are compact and transportable, making them ideal for temporary setups at events, festivals, or emergency situations. They provide flexibility in location and quick deployment, appealing to B2B buyers looking for adaptable solutions. However, their limited inventory capacity may restrict the range of products offered, which is an important consideration for maximizing sales potential at larger gatherings.
Related Video: Machine Learning in 2024 – Beginner’s Course
Key Industrial Applications of vending machine police station
Industry/Sector | Specific Application of vending machine police station | Value/Benefit for the Business | Key Sourcing Considerations for this Application |
---|---|---|---|
Law Enforcement | Automated reporting and evidence collection | Streamlined processes, reduced paperwork, enhanced security | Compliance with local regulations, user-friendly interface |
Public Safety | Emergency response and first-aid supplies distribution | Immediate access to essential items during emergencies | Robust supply chain, durability in various climates |
Community Services | Community engagement and information dissemination | Improved public relations, increased community trust | Multi-language support, adaptability to local needs |
Transportation Hubs | Crime prevention and reporting kiosks | Enhanced safety perception, real-time reporting capabilities | Integration with local law enforcement systems, ease of use |
Educational Institutions | Student safety and anonymous reporting systems | Increased student security, proactive crime prevention | User privacy measures, integration with school safety protocols |
Law Enforcement
The vending machine police station serves as a vital tool for law enforcement agencies, facilitating automated reporting and evidence collection. By allowing citizens to report incidents directly, these machines streamline the process, significantly reducing paperwork and administrative burdens. International buyers must ensure that these machines comply with local regulations and offer a user-friendly interface, which can vary across regions like Africa and Europe.
Public Safety
In public safety applications, vending machine police stations can distribute emergency response supplies, such as first-aid kits or personal safety devices. This immediate access to essential items can be crucial during emergencies, potentially saving lives. Buyers should consider sourcing machines that ensure a robust supply chain and are durable enough to withstand various climate conditions, particularly in regions prone to extreme weather.
Community Services
These vending machines can enhance community engagement by providing information about local services, reporting mechanisms, and safety tips. By improving public relations and building trust within the community, they foster a safer environment. For international buyers, it’s essential to look for machines that offer multi-language support and can be adapted to meet local needs, ensuring accessibility for diverse populations.
Transportation Hubs
In transportation hubs, vending machine police stations can act as crime prevention kiosks, enabling real-time reporting of suspicious activities. This enhances the safety perception of these public spaces, encouraging more people to use them. Buyers should prioritize machines that can integrate seamlessly with local law enforcement systems, ensuring ease of use and immediate response capabilities.
Educational Institutions
In educational settings, these machines can serve as anonymous reporting systems for students to communicate safety concerns. This proactive approach to crime prevention increases student security and promotes a culture of safety within schools. Buyers must focus on privacy measures and the integration of these machines with existing school safety protocols to ensure their effectiveness and acceptance among students and staff.
Related Video: DIY Vending Machine – Arduino based Mechatronics Project
Strategic Material Selection Guide for vending machine police station
When selecting materials for vending machines in police stations, it is crucial to consider properties that ensure durability, security, and functionality. The following analysis covers four common materials used in the construction of these vending machines, focusing on their key properties, advantages, disadvantages, and specific considerations for international B2B buyers.
1. Stainless Steel
Key Properties:
Stainless steel is known for its excellent corrosion resistance, high strength, and ability to withstand a wide range of temperatures. It typically has a temperature rating of up to 800°F (427°C) and is resistant to various chemicals, making it ideal for public environments.
Pros & Cons:
The durability of stainless steel is one of its main advantages, as it can withstand physical impacts and is easy to clean. However, it is relatively expensive compared to other materials and may require complex manufacturing processes, particularly for intricate designs.
Impact on Application:
Stainless steel is compatible with a wide range of media, including food and beverages, which is essential for vending machines. Its durability ensures a long lifespan, reducing maintenance costs.
Considerations for International Buyers:
Buyers should ensure compliance with international standards such as ASTM A240 for stainless steel. In regions like Europe, specific grades like AISI 304 or AISI 316 are preferred due to their corrosion resistance in marine environments.
2. Aluminum
Key Properties:
Aluminum is lightweight, has good corrosion resistance, and can operate effectively at temperatures ranging from -40°F to 400°F (-40°C to 204°C). Its strength-to-weight ratio is excellent, making it suitable for portable vending machines.
Pros & Cons:
Aluminum is cost-effective and easy to manufacture, allowing for quick production times. However, it is less durable than stainless steel and can be prone to dents and scratches, which may affect its aesthetic appeal over time.
Impact on Application:
Aluminum’s compatibility with various media makes it suitable for vending machines that dispense snacks and drinks. However, its lower durability may require more frequent replacements or repairs.
Considerations for International Buyers:
Buyers should be aware of the specific aluminum grades used, such as 6061 or 5052, which comply with standards like ASTM B221. In regions like Africa and South America, where environmental conditions can be harsh, selecting a high-grade aluminum can enhance performance.
3. Polycarbonate
Key Properties:
Polycarbonate is a high-impact plastic known for its transparency and UV resistance. It can withstand temperatures from -40°F to 240°F (-40°C to 116°C) and has a high strength-to-weight ratio.
Pros & Cons:
The primary advantage of polycarbonate is its impact resistance, making it ideal for high-traffic areas. However, it is less resistant to scratches compared to glass and may yellow over time when exposed to UV light.
Impact on Application:
Polycarbonate is often used for protective covers or panels in vending machines, allowing visibility while protecting the contents. Its lightweight nature aids in reducing the overall weight of the machine.
Considerations for International Buyers:
When sourcing polycarbonate, buyers should look for compliance with standards such as ASTM D3935. In Europe, certifications for safety and environmental impact may also be necessary.
4. Carbon Steel
Key Properties:
Carbon steel is known for its strength and durability, with a temperature rating of up to 400°F (204°C). It is less resistant to corrosion compared to stainless steel but can be treated with coatings for enhanced protection.
Pros & Cons:
Carbon steel is one of the most cost-effective materials, making it a popular choice for budget-conscious projects. However, its susceptibility to rust and corrosion without proper treatment can be a significant drawback.
Impact on Application:
Carbon steel is suitable for structural components of vending machines but may require protective coatings to ensure longevity in outdoor or humid environments.
Considerations for International Buyers:
Buyers should consider compliance with standards like ASTM A36 for carbon steel. In regions with high humidity, such as parts of South America and the Middle East, additional protective measures are essential.
Summary Table
Material | Typical Use Case for vending machine police station | Key Advantage | Key Disadvantage/Limitation | Relative Cost (Low/Med/High) |
---|---|---|---|---|
Stainless Steel | Structural components, exterior panels | Excellent durability and corrosion resistance | High cost, complex manufacturing | High |
Aluminum | Body and structural components | Lightweight and cost-effective | Less durable, prone to dents | Medium |
Polycarbonate | Protective covers and panels | High impact resistance | Scratches easily, UV yellowing | Medium |
Carbon Steel | Structural elements | Cost-effective, strong | Susceptible to corrosion without treatment | Low |
In-depth Look: Manufacturing Processes and Quality Assurance for vending machine police station
Manufacturing Processes for Vending Machine Police Stations
The manufacturing of vending machine police stations involves several critical stages, each designed to ensure that the final product meets stringent requirements for safety, functionality, and durability. Understanding these processes can help international B2B buyers assess the capabilities of potential suppliers.
Main Stages of Manufacturing
-
Material Preparation
– Selection: The first step involves selecting high-quality materials such as stainless steel for the outer casing to withstand environmental factors and potential vandalism.
– Procurement: Materials must be sourced from reputable suppliers, ensuring compliance with international standards. Buyers should verify certifications like ISO 9001 for suppliers to ensure quality control. -
Forming
– Cutting and Shaping: Advanced machinery is used for precision cutting and shaping of metal sheets. Techniques such as laser cutting or CNC machining provide high accuracy.
– Bending: The shaped materials are then bent to form the outer structure of the vending machine. This process often employs hydraulic presses for efficiency. -
Assembly
– Component Integration: All internal components, including electronic systems, payment mechanisms, and security features, are assembled. This stage is crucial as it affects the operational efficiency of the machine.
– Wiring: Proper wiring is essential for the connectivity of payment systems, cameras, and other electronic elements. Assembly teams must follow schematics meticulously to avoid malfunctions. -
Finishing
– Surface Treatment: After assembly, the surface of the vending machine is treated for corrosion resistance and aesthetic appeal. Techniques such as powder coating or galvanization are commonly employed.
– Quality Checks: Before the final product leaves the factory, it undergoes rigorous quality checks to ensure it meets the specified standards.
Quality Assurance in Manufacturing
Quality assurance (QA) plays a vital role in ensuring that vending machine police stations are reliable and safe. For international B2B buyers, understanding the QA processes can facilitate better decision-making when selecting suppliers.
Relevant International Standards
- ISO 9001: This standard outlines the requirements for a quality management system. Suppliers certified under ISO 9001 demonstrate their commitment to quality and continuous improvement.
- CE Marking: Products sold in the European Economic Area must meet health, safety, and environmental protection standards. CE marking indicates compliance with these regulations.
- API Standards: For specific components, adherence to American Petroleum Institute (API) standards may be required, particularly for vending machines that dispense liquid products.
Quality Control Checkpoints
-
Incoming Quality Control (IQC)
– This initial checkpoint assesses the quality of materials received from suppliers. Verification of certifications and testing for defects is conducted to ensure that only high-quality materials proceed to the next stage. -
In-Process Quality Control (IPQC)
– During the manufacturing process, regular inspections are carried out to identify any issues that may arise. This includes checking dimensions, functionality of components, and adherence to assembly protocols. -
Final Quality Control (FQC)
– Before shipment, the finished products undergo comprehensive testing. This includes operational tests, safety checks, and compliance verification against relevant standards.
Common Testing Methods
- Functional Testing: Verifying that all components operate correctly under various scenarios.
- Durability Testing: Assessing how well the machine withstands physical stress and environmental conditions.
- Electrical Safety Testing: Ensuring that electrical components meet safety standards to prevent hazards.
Verifying Supplier Quality Control
B2B buyers should take proactive steps to verify the quality control processes of potential suppliers. Here are some strategies:
-
Supplier Audits
– Conducting on-site audits allows buyers to assess the manufacturing processes and quality control measures in place. This firsthand observation can reveal the supplier’s commitment to quality. -
Quality Reports
– Request detailed quality assurance reports from suppliers. These documents should outline the testing methodologies, results, and corrective actions taken for any identified issues. -
Third-Party Inspections
– Engaging third-party inspection services can provide an unbiased evaluation of the supplier’s quality control practices. These firms can conduct inspections at various stages of the manufacturing process.
Quality Control and Certification Nuances for International Buyers
International buyers must be aware of specific nuances regarding quality control and certification:
- Regulatory Compliance: Different regions may have varying regulations regarding product safety and quality. Buyers should ensure that suppliers comply with local laws and international standards relevant to their market.
- Cultural Considerations: Understanding the cultural context in which suppliers operate can help buyers navigate potential communication barriers and foster better relationships.
- Documentation: Buyers should ensure that all certifications and quality control documentation are available in a language they understand to facilitate transparency and trust.
In summary, a thorough understanding of the manufacturing processes and quality assurance measures for vending machine police stations is crucial for international B2B buyers. By focusing on supplier capabilities, compliance with international standards, and rigorous quality control practices, buyers can make informed decisions that lead to successful procurement outcomes.
Related Video: SMART Quality Control for Manufacturing
Comprehensive Cost and Pricing Analysis for vending machine police station Sourcing
Cost Structure of Vending Machine Police Stations
Understanding the cost structure of vending machine police stations is crucial for international B2B buyers. The primary components include:
-
Materials: The cost of raw materials such as metal, plastics, and electronic components can vary significantly based on quality and supplier location. High-grade materials may incur higher upfront costs but can lead to lower maintenance and replacement expenses over time.
-
Labor: Labor costs will differ by region. For example, sourcing from countries with lower labor costs can reduce overall expenses, but be mindful of potential trade-offs in quality and skill levels.
-
Manufacturing Overhead: This encompasses costs related to factory operations, including utilities, rent, and administrative expenses. Efficient manufacturing processes can reduce overhead, thus lowering the final product price.
-
Tooling: Initial tooling costs for custom vending machines can be substantial, especially if specific designs or functions are required. Consider whether a supplier can absorb these costs or if they will be passed onto you.
-
Quality Control (QC): Investing in robust QC processes ensures that the machines meet safety and operational standards. While this may increase initial costs, it can prevent costly recalls or repairs later.
-
Logistics: Shipping and handling costs can vary widely based on the destination and chosen Incoterms. Consider whether the supplier provides DDP (Delivered Duty Paid) or EXW (Ex Works) terms, as these significantly impact overall costs.
-
Margin: Suppliers will typically add a profit margin to cover their costs and risks. Understanding the typical margins in your industry can help in negotiations.
Price Influencers
Several factors can influence the pricing of vending machine police stations:
-
Volume/MOQ: Larger orders usually benefit from bulk pricing, which can lead to significant savings. Determine the minimum order quantities (MOQs) that suppliers require to qualify for discounts.
-
Specifications/Customization: Custom features may increase costs. Clarify your requirements early to get accurate pricing and consider whether off-the-shelf solutions could meet your needs without the added expense of customization.
-
Materials and Quality Certifications: Higher quality materials and internationally recognized certifications (ISO, CE) may lead to higher prices but can enhance durability and reliability, which is critical for police station environments.
-
Supplier Factors: The reputation and reliability of the supplier can affect pricing. Established suppliers may charge more due to their proven track record, but they may also offer better support and warranty terms.
-
Incoterms: Different shipping terms can lead to varying costs. Understand the implications of Incoterms on your total cost, including duties, taxes, and insurance.
Buyer Tips
For international B2B buyers, particularly from Africa, South America, the Middle East, and Europe, consider the following strategies:
-
Negotiation: Don’t hesitate to negotiate pricing based on your order volume or long-term partnership potential. Suppliers often have flexibility in pricing, especially for bulk orders.
-
Cost-Efficiency: Evaluate the Total Cost of Ownership (TCO) rather than just the purchase price. Consider maintenance, operational costs, and potential downtime when assessing value.
-
Pricing Nuances: Be aware of currency fluctuations and regional economic conditions that might impact pricing. Establishing contracts in a stable currency can mitigate risks.
-
Supplier Diversification: Engaging multiple suppliers can provide leverage during negotiations and reduce dependency on a single source, enhancing supply chain resilience.
Disclaimer: Prices can vary based on market conditions, and it is advisable to obtain quotes from multiple suppliers for an accurate assessment. Always conduct due diligence to ensure quality and reliability in your sourcing decisions.
Spotlight on Potential vending machine police station Manufacturers and Suppliers
This section offers a look at a few manufacturers active in the ‘vending machine police station’ market. This is a representative sample for illustrative purposes; B2B buyers must conduct their own extensive due diligence before any engagement. Information is synthesized from public sources and general industry knowledge.
Essential Technical Properties and Trade Terminology for vending machine police station
Key Technical Properties for Vending Machine Police Stations
When considering the procurement of vending machines specifically designed for police stations, several critical technical properties must be evaluated to ensure functionality, durability, and security. Here are some essential specifications:
-
Material Grade
The construction materials of the vending machine are crucial for durability and security. High-grade stainless steel is often preferred due to its resistance to corrosion and impact. For police station environments, machines must withstand potential vandalism and weather elements. -
Security Features
Vending machines in police stations should incorporate advanced security features. This includes reinforced locking mechanisms and tamper-resistant designs. A robust security system not only protects the contents but also ensures the safety of users. -
Temperature Control Range
Depending on the items sold, temperature control can be vital. Machines designed for perishable goods should maintain specific temperature ranges (e.g., 0-5°C for cold beverages) to ensure product safety and quality. Understanding these specifications helps in compliance with health regulations. -
Power Consumption and Efficiency
Energy-efficient models are essential for reducing operational costs. Buyers should look for machines with low power consumption ratings and energy-saving modes. This is particularly important in regions where electricity costs can be high. -
User Interface Technology
The vending machine should feature an intuitive user interface, which may include touch screens, multilingual options, and accessibility features for individuals with disabilities. This enhances user experience and ensures that the machine can cater to a diverse population. -
Capacity and Size
The dimensions and storage capacity of the vending machine must align with the expected foot traffic and product offerings. Machines should be compact enough to fit in designated spaces while providing ample product selection.
These properties not only ensure that the vending machines are suited for their intended purpose but also enhance their longevity and operational efficiency in a high-security environment.
Common Trade Terminology
Understanding industry-specific terminology is crucial for successful negotiations and transactions in the vending machine market. Here are some key terms:
-
OEM (Original Equipment Manufacturer)
This term refers to companies that produce parts or equipment that may be marketed by another manufacturer. In the context of vending machines, an OEM might provide the machine itself or specific components, ensuring quality and compatibility. -
MOQ (Minimum Order Quantity)
MOQ indicates the smallest quantity of a product that a supplier is willing to sell. For B2B buyers, understanding MOQ is essential for budgeting and inventory management, especially when planning for multiple installations. -
RFQ (Request for Quotation)
An RFQ is a document that a buyer sends to suppliers to request pricing and terms for specific goods or services. This is a critical step in the procurement process, allowing buyers to compare costs and terms from multiple vendors.
-
Incoterms (International Commercial Terms)
These are a series of pre-defined commercial terms published by the International Chamber of Commerce (ICC) relating to international commercial law. Incoterms clarify the responsibilities of buyers and sellers regarding shipping, insurance, and tariffs, which is vital for international procurement. -
Lead Time
Lead time refers to the time taken from placing an order to the delivery of the product. Understanding lead times helps buyers plan accordingly, especially in environments where quick deployment of vending machines is necessary. -
Warranty and Service Level Agreement (SLA)
A warranty provides assurance regarding the quality and durability of the vending machine, while an SLA outlines the expected service levels post-purchase, including maintenance and response times for repairs. These agreements are critical for ensuring ongoing support and minimizing downtime.
By familiarizing themselves with these technical properties and trade terms, B2B buyers can make informed decisions, ensuring that they select the right vending machines for police stations that meet both operational needs and security requirements.
Navigating Market Dynamics, Sourcing Trends, and Sustainability in the vending machine police station Sector
Market Overview & Key Trends
The vending machine police station sector is witnessing significant transformation driven by several global trends. Technological advancements are at the forefront, with the integration of IoT and AI enabling real-time monitoring and data analytics. These technologies facilitate efficient inventory management and predictive maintenance, appealing to international B2B buyers looking to optimize operations. Furthermore, contactless payment systems have surged in popularity, particularly post-pandemic, enhancing user experience while ensuring safety and security.
In terms of sourcing trends, there is a growing emphasis on modular and customizable vending solutions. Buyers from diverse regions, including Africa and South America, are increasingly seeking machines that can be tailored to meet local needs, such as offering culturally relevant products or supporting multiple languages. Additionally, sustainability is becoming a crucial factor; buyers are now prioritizing vendors that offer energy-efficient machines and sustainable product options.
The market dynamics are also influenced by regional regulations and consumer preferences. In Europe, for example, there is a strong push for smart vending solutions that comply with stringent data protection laws. Meanwhile, in the Middle East, the focus is shifting towards enhancing public safety and community engagement through innovative vending solutions that can provide essential services in police stations.
Sustainability & Ethical Sourcing in B2B
The environmental impact of vending machines is under scrutiny, prompting buyers to consider sustainability in their purchasing decisions. The sector is increasingly aligning with eco-friendly practices, such as using recyclable materials in vending machine construction and ensuring energy-efficient operations. International B2B buyers are encouraged to seek vendors who are transparent about their manufacturing processes and who adhere to sustainable practices throughout the supply chain.
Ethical sourcing is another critical aspect, especially for buyers in regions like Europe where consumers are more socially conscious. Companies are now looking for certifications that validate their commitment to sustainability, such as ISO 14001 for environmental management or Fair Trade certifications for products offered in vending machines. By prioritizing vendors with recognized sustainability certifications, buyers can not only reduce their environmental footprint but also enhance their brand reputation, appealing to a growing demographic that values corporate responsibility.
Brief Evolution/History
The concept of vending machines has evolved significantly since their inception in the early 1880s. Originally designed for simple transactions, these machines have transformed into sophisticated platforms capable of delivering a wide array of products and services. The introduction of technology in the 21st century has further revolutionized the sector, allowing for real-time interactions and data collection. As police stations begin to integrate vending solutions for community engagement and service delivery, this evolution highlights the importance of adaptability and innovation in meeting the unique needs of diverse markets worldwide. Today, vending machines serve not just as retail units but as essential tools for enhancing public safety and convenience, marking a new era in their application.
Related Video: Global National: April 5, 2025 | “Hands off” protests worldwide in response to Trump’s trade war
Frequently Asked Questions (FAQs) for B2B Buyers of vending machine police station
-
What should I consider when vetting suppliers for vending machine police stations?
When vetting suppliers, prioritize their experience in the vending machine industry, particularly with police stations or similar environments. Request references and case studies showcasing previous installations. Ensure they have the necessary certifications and compliance with local regulations in your region. Conduct a site visit if possible, or request virtual tours of their facilities to assess their manufacturing capabilities. Also, check their financial stability and customer reviews to ensure they can meet your long-term needs. -
Can I customize the vending machines for my police station?
Yes, most suppliers offer customization options to meet specific needs. This can include branding, machine size, product selection, and payment options. Clearly communicate your requirements during the initial discussions and request samples or prototypes if available. Ensure that the supplier has experience in creating custom solutions for law enforcement environments, as this can affect both functionality and compliance with regulations. -
What are the typical minimum order quantities (MOQ) and lead times for vending machines?
MOQs can vary significantly based on the supplier and the complexity of the machines. Typically, you might expect MOQs to range from 5 to 50 units. Lead times usually depend on customization and supplier capacity, ranging from 4 to 12 weeks. Always confirm these details upfront to avoid delays in deployment. Establishing a good relationship with your supplier can also lead to more favorable terms for future orders. -
What payment terms should I expect when purchasing vending machines?
Payment terms vary by supplier but commonly include a deposit upfront (usually 30-50%) with the balance due upon delivery or installation. Some suppliers may offer financing options or extended payment terms for large orders. Discuss payment methods accepted, such as bank transfers or letters of credit, and ensure they align with your company’s financial practices. Always clarify any potential additional costs, such as shipping or customs duties. -
How can I ensure the quality and safety of the vending machines?
To ensure quality, request detailed product specifications and certifications, such as ISO or CE marks, which indicate compliance with international safety standards. Conduct quality assurance checks at various stages of production, and consider third-party inspections. Additionally, inquire about warranty and service agreements to cover potential defects or maintenance needs. Establishing clear quality benchmarks in your contract can help enforce these standards. -
What logistics considerations should I keep in mind when importing vending machines?
Logistics can be complex, especially when dealing with international shipments. Ensure that your supplier provides detailed shipping terms, including Incoterms that clarify responsibilities for shipping, insurance, and tariffs. Work with a reliable freight forwarder experienced in handling heavy machinery and customs regulations in your country. Consider the delivery location’s accessibility to ensure smooth unloading and installation. -
How should I handle disputes with my supplier?
Establish a clear dispute resolution process in your contract, including timelines for addressing issues and escalation procedures. Maintain open communication with your supplier to resolve problems amicably. If disputes arise, refer to the agreed-upon terms in your contract, and consider mediation or arbitration as alternatives to litigation, which can be costly and time-consuming. Document all communications and agreements to support your case if necessary. -
Are there any specific certifications or standards for vending machines used in police stations?
Yes, vending machines intended for use in police stations may need to comply with specific safety and operational standards, including those related to security features, accessibility, and environmental considerations. Research local regulations governing vending operations in public spaces, particularly in sensitive environments like police stations. Request documentation of compliance from your supplier and ensure their machines are designed to withstand the unique demands of law enforcement use.
Strategic Sourcing Conclusion and Outlook for vending machine police station
In conclusion, the implementation of vending machine police stations offers a transformative approach to enhancing community safety and accessibility. International B2B buyers, especially those from Africa, South America, the Middle East, and Europe, must recognize the strategic advantages of sourcing these innovative solutions. Key takeaways include the importance of selecting reliable vendors who provide comprehensive support and maintenance, as well as ensuring that machines are stocked with relevant and culturally appropriate products.
Strategic sourcing is vital for maximizing the return on investment in vending machine police stations. By leveraging technology and data analytics, buyers can assess usage patterns and optimize inventory management, ultimately enhancing user experience and operational efficiency.
As we look to the future, the demand for smart, integrated public safety solutions will only grow. Now is the time for international buyers to engage with manufacturers and technology providers to explore customized solutions that meet their unique needs. Investing in vending machine police stations not only enhances public safety but also demonstrates a commitment to community welfare. Embrace this opportunity to lead in innovative public service solutions and make a meaningful impact in your region.