Your Ultimate Guide to Sourcing Vending Machine Jobs
Guide to Vending Machine Jobs
- Introduction: Navigating the Global Market for vending machine jobs
- Understanding vending machine jobs Types and Variations
- Key Industrial Applications of vending machine jobs
- Strategic Material Selection Guide for vending machine jobs
- In-depth Look: Manufacturing Processes and Quality Assurance for vending machine jobs
- Comprehensive Cost and Pricing Analysis for vending machine jobs Sourcing
- Spotlight on Potential vending machine jobs Manufacturers and Suppliers
- Essential Technical Properties and Trade Terminology for vending machine jobs
- Navigating Market Dynamics, Sourcing Trends, and Sustainability in the vending machine jobs Sector
- Frequently Asked Questions (FAQs) for B2B Buyers of vending machine jobs
- Strategic Sourcing Conclusion and Outlook for vending machine jobs
Introduction: Navigating the Global Market for vending machine jobs
In an increasingly competitive global landscape, vending machines have emerged as a lucrative business opportunity across various sectors, from retail to hospitality. The demand for vending machine jobs—encompassing roles in manufacturing, maintenance, and operations—has surged as businesses seek efficient, automated solutions to meet consumer needs. For international B2B buyers, particularly those in Africa, South America, the Middle East, and Europe, understanding this market is essential for making informed sourcing decisions.
This comprehensive guide delves into the multifaceted world of vending machine jobs, offering insights into various types of machines, essential materials, manufacturing processes, and quality control standards. Buyers will benefit from detailed analyses of suppliers, cost structures, and market trends that are critical for strategic planning and investment. Furthermore, we address frequently asked questions to clarify common uncertainties that may arise when entering this dynamic sector.
By equipping B2B buyers with actionable insights and a robust understanding of the vending machine job market, this guide empowers businesses to capitalize on emerging opportunities. Whether you are looking to expand your operations or optimize existing ones, the information contained herein will serve as a vital resource in navigating the complexities of this global market, ensuring you stay ahead of the curve in a rapidly evolving industry.
Understanding vending machine jobs Types and Variations
Type Name | Key Distinguishing Features | Primary B2B Applications | Brief Pros & Cons for Buyers |
---|---|---|---|
Traditional Snack Vending | Offers a variety of snacks and beverages | Offices, schools, public areas | Pros: Low maintenance, quick ROI. Cons: Limited product range compared to specialized machines. |
Healthy Food Vending | Focuses on nutritious options, often refrigerated | Gyms, health clubs, corporate offices | Pros: Appeals to health-conscious consumers. Cons: Higher initial costs and more complex maintenance. |
Coffee Vending Machines | Provides freshly brewed coffee and related beverages | Cafés, offices, hotels | Pros: High demand, potential for premium pricing. Cons: Requires regular servicing and quality control. |
Automated Retail Kiosks | Advanced technology with touchscreen interfaces | Airports, malls, high-traffic areas | Pros: Engages consumers with interactive options. Cons: Higher initial investment and tech reliance. |
Specialty Product Machines | Focuses on niche markets (e.g., electronics, cosmetics) | Retail stores, events, trade shows | Pros: Targets specific consumer needs, potentially higher margins. Cons: Limited audience and higher operational complexity. |
Traditional Snack Vending
Traditional snack vending machines are characterized by their ability to dispense a wide variety of snacks and beverages. These machines are commonly found in workplaces, schools, and public areas, making them a staple in many environments. For B2B buyers, the key considerations include initial investment costs, product selection, and maintenance requirements. While they offer a quick return on investment due to their popularity, buyers should be aware of the limited product range compared to more specialized vending options.
Healthy Food Vending
Healthy food vending machines cater to the growing demand for nutritious food options, often featuring refrigerated compartments to keep items fresh. These machines are particularly suitable for gyms, health clubs, and corporate offices where health-conscious consumers are prevalent. B2B buyers should consider the higher initial investment and maintenance complexity, as these machines typically require more frequent restocking and quality checks. However, they can significantly enhance brand image and employee satisfaction.
Coffee Vending Machines
Coffee vending machines provide freshly brewed coffee and related beverages, making them ideal for environments like cafés, offices, and hotels. These machines are distinguished by their ability to deliver high-quality beverages on-demand. For B2B purchasers, the demand for coffee can lead to higher profit margins, but they must also consider the need for regular servicing and quality control to maintain customer satisfaction. The initial investment can be higher, but the potential for premium pricing makes them an attractive option.
Automated Retail Kiosks
Automated retail kiosks are a modern evolution in vending technology, featuring touchscreen interfaces and a wide range of products. These machines are best suited for high-traffic areas such as airports and malls, where consumer engagement is crucial. B2B buyers should weigh the benefits of increased interactivity and consumer engagement against the higher initial investment and reliance on technology. While these kiosks can attract a diverse customer base, they also require ongoing technical support and maintenance.
Specialty Product Machines
Specialty product machines focus on niche markets, offering unique items such as electronics, cosmetics, or gourmet snacks. These machines are often deployed in retail stores, events, and trade shows, targeting specific consumer needs. B2B buyers should consider the potential for higher profit margins and the ability to cater to a specific audience. However, the limited audience and operational complexity may pose challenges, requiring careful market analysis and strategic placement to ensure success.
Related Video: 10 Business Models for Every Entrepreneur
Key Industrial Applications of vending machine jobs
Industry/Sector | Specific Application of vending machine jobs | Value/Benefit for the Business | Key Sourcing Considerations for this Application |
---|---|---|---|
Retail | Automated retail solutions | Increased sales volume, 24/7 availability | Machine size, product variety, payment systems |
Healthcare | Medication dispensing | Improved patient compliance, reduced pharmacy workload | Regulatory compliance, security features, inventory management |
Education | Campus snack and beverage services | Enhanced student satisfaction, convenience | Custom branding, nutritional options, payment flexibility |
Hospitality | In-room vending for hotels | Increased guest convenience, additional revenue stream | Product selection, machine maintenance, location strategy |
Manufacturing | Employee break room solutions | Boosted employee morale, reduced downtime | Machine durability, service agreements, product rotation |
Retail: Automated Retail Solutions
In the retail sector, vending machine jobs are increasingly utilized to create automated retail solutions. These machines can dispense a wide variety of products, from snacks to electronics, providing customers with 24/7 access. This not only increases sales volume but also reduces the need for staffing during off-peak hours. For international buyers, especially in developing regions, the ability to offer diverse product selections and secure payment systems is crucial to meet local market demands.
Healthcare: Medication Dispensing
In healthcare settings, vending machines serve as medication dispensing units, ensuring patients have easy access to their prescribed medications. This application addresses the challenges of patient compliance and reduces the workload on pharmacy staff. Buyers from regions with stringent regulatory environments must prioritize machines that comply with healthcare regulations and offer robust security features to protect sensitive information and medications.
Education: Campus Snack and Beverage Services
Vending machines in educational institutions provide students with easy access to snacks and beverages, enhancing overall student satisfaction. These machines can be strategically placed in high-traffic areas to maximize visibility and usage. For buyers in the education sector, considerations such as custom branding, nutritional options, and flexible payment methods are essential to cater to diverse student needs and preferences.
Hospitality: In-Room Vending for Hotels
In the hospitality industry, vending machines placed in hotel rooms offer guests convenience and additional revenue streams for hotel operators. This application allows hotels to provide a range of snacks and beverages without the need for extensive room service operations. Buyers must consider product selection, machine maintenance, and the strategic placement of machines within the hotel to maximize guest engagement and satisfaction.
Manufacturing: Employee Break Room Solutions
Vending machines in manufacturing facilities serve as essential solutions for employee break rooms, providing quick access to refreshments and snacks. This application boosts employee morale and minimizes downtime during breaks. B2B buyers in this sector should focus on the durability of machines, service agreements for maintenance, and the ability to rotate products regularly to keep offerings fresh and appealing to employees.
Related Video: How to Start a Vending Machine Business, Cost, Tips, How Much You Make
Strategic Material Selection Guide for vending machine jobs
When selecting materials for vending machine jobs, it is essential to consider their properties, advantages, disadvantages, and compliance with international standards. Below, we analyze four common materials used in vending machine applications, focusing on their performance characteristics and implications for international B2B buyers.
Stainless Steel
Key Properties: Stainless steel is known for its excellent corrosion resistance, high strength, and ability to withstand high temperatures and pressures. It typically has a temperature rating up to 800°F (427°C) and can handle various environmental conditions.
Pros & Cons: The durability of stainless steel makes it ideal for vending machines that are exposed to diverse climates. However, its higher cost compared to other materials can be a drawback. Manufacturing complexity is moderate, as stainless steel requires specialized welding techniques.
Impact on Application: Stainless steel is compatible with a wide range of media, including food and beverages, making it a preferred choice for vending machines. Its hygienic properties also make it suitable for applications requiring cleanliness.
Considerations for International Buyers: Buyers in Africa, South America, the Middle East, and Europe should ensure compliance with food safety standards such as ASTM and ISO. The availability of stainless steel grades may vary by region, impacting sourcing decisions.
Polycarbonate
Key Properties: Polycarbonate is a lightweight, impact-resistant thermoplastic with a temperature tolerance of around -40°F to 240°F (-40°C to 115°C). It exhibits good clarity and UV resistance.
Pros & Cons: The primary advantage of polycarbonate is its high impact resistance, making it suitable for vending machines in high-traffic areas. However, it is less durable than metals and can be prone to scratching. Manufacturing processes are generally simpler and less costly.
Impact on Application: Polycarbonate is often used for transparent components, such as windows and panels, allowing visibility of the products inside. Its chemical resistance is suitable for non-corrosive environments.
Considerations for International Buyers: Buyers should check compliance with regional standards like JIS or DIN for plastic materials. The availability of high-quality polycarbonate can vary significantly, so sourcing from reputable suppliers is crucial.
Aluminum
Key Properties: Aluminum is lightweight, corrosion-resistant, and has a temperature rating of up to 1,200°F (649°C). It is also a good conductor of heat and electricity.
Pros & Cons: Aluminum’s lightweight nature makes it easy to handle and install, reducing shipping costs. However, it can be less durable than stainless steel in certain applications and may require additional coatings for enhanced corrosion resistance.
Impact on Application: Aluminum is suitable for vending machines that require lightweight components, such as frames and brackets. Its compatibility with various media is good, although care should be taken with highly acidic or alkaline substances.
Considerations for International Buyers: Compliance with international aluminum standards is essential, especially in regions with strict regulations. Buyers should also consider the availability of specific aluminum alloys that meet their project requirements.
Glass
Key Properties: Glass is a rigid, transparent material that can withstand moderate pressure and has excellent chemical resistance. Its temperature tolerance varies by type, with tempered glass handling higher thermal stress.
Pros & Cons: Glass provides an aesthetic appeal and allows for product visibility, enhancing customer engagement. However, it is fragile and can break easily, which poses a risk in high-traffic environments. Manufacturing complexity can be high due to the need for precise cutting and tempering.
Impact on Application: Glass is commonly used for vending machine fronts and display cases, providing a clear view of the products. Its compatibility with food and beverages is excellent, provided it meets safety standards.
Considerations for International Buyers: Buyers should ensure that the glass used complies with safety standards, such as those outlined by ASTM. Additionally, sourcing tempered glass can mitigate risks associated with breakage.
Summary Table
Material | Typical Use Case for vending machine jobs | Key Advantage | Key Disadvantage/Limitation | Relative Cost (Low/Med/High) |
---|---|---|---|---|
Stainless Steel | Structural components and surfaces in food vending machines | Excellent durability and corrosion resistance | Higher cost compared to other materials | High |
Polycarbonate | Transparent panels and protective covers | High impact resistance | Less durable than metals, prone to scratches | Medium |
Aluminum | Lightweight frames and internal components | Lightweight and easy to handle | May require coatings for corrosion resistance | Medium |
Glass | Front panels and display cases | Aesthetic appeal and product visibility | Fragile and can break easily | Medium |
This strategic material selection guide provides B2B buyers with critical insights into the materials used in vending machine jobs, helping them make informed decisions that align with their operational needs and regional compliance requirements.
In-depth Look: Manufacturing Processes and Quality Assurance for vending machine jobs
Manufacturing Processes for Vending Machines
Understanding the manufacturing processes behind vending machines is crucial for B2B buyers looking to ensure product quality and reliability. The typical manufacturing process can be broken down into four main stages: material preparation, forming, assembly, and finishing.
Material Preparation
This initial stage involves sourcing and preparing raw materials, including metals, plastics, and electronic components. For vending machines, high-quality materials are essential to ensure durability and functionality. B2B buyers should prioritize suppliers who utilize sustainable sourcing practices to align with global trends towards environmental responsibility.
Key activities in this phase include:
– Material Selection: Choosing materials that meet industry standards for strength, corrosion resistance, and thermal stability.
– Quality Inspection: Conducting initial quality checks on incoming materials to ensure they meet specifications. This is often referred to as Incoming Quality Control (IQC).
Forming
The forming stage involves transforming raw materials into the components required for the vending machine. Techniques used can include:
– Stamping: Commonly used for metal parts, where sheets of metal are cut and shaped using dies.
– Injection Molding: A prevalent method for producing plastic components, allowing for intricate designs and high-volume production.
During this phase, manufacturers must adhere to industry standards to ensure consistency and reliability. Buyers should inquire about the specific forming techniques used by suppliers and any certifications they hold, which can assure quality.
Assembly
Once components are formed, they proceed to assembly. This stage is critical as it brings together the various parts into a complete unit. Key practices include:
– Automated Assembly Lines: Many manufacturers utilize automated processes to enhance efficiency and reduce human error.
– Manual Assembly: For more complex or delicate components, skilled labor may be employed.
Quality checks during assembly, known as In-Process Quality Control (IPQC), are vital. These checks ensure that components are correctly installed and function as intended. B2B buyers should confirm that suppliers have robust assembly protocols in place, which can be verified through audits and quality reports.
Finishing
The finishing stage enhances the aesthetic and functional qualities of the vending machines. It includes processes such as:
– Painting and Coating: Applying protective and decorative finishes to metal and plastic surfaces.
– Testing and Calibration: Ensuring that all electronic components work correctly and that the machine operates as intended.
Quality assurance during this phase is critical, as it influences both the appearance and longevity of the product. Final Quality Control (FQC) checks should be conducted to assess the overall quality and functionality before shipment.
Quality Assurance in Vending Machine Manufacturing
Quality assurance (QA) is paramount in the manufacturing process, particularly in the vending machine industry where reliability directly impacts customer satisfaction. International standards, such as ISO 9001, provide a framework for ensuring quality management systems are in place.
Relevant International Standards
B2B buyers should look for suppliers that comply with recognized standards:
– ISO 9001: A widely recognized quality management standard that focuses on meeting customer requirements and enhancing satisfaction.
– CE Marking: Indicates conformity with health, safety, and environmental protection standards for products sold within the European Economic Area.
– API Standards: For vending machines that dispense consumables, adherence to American Petroleum Institute standards can be relevant, especially for machines handling beverages.
Quality Control Checkpoints
To ensure quality throughout the manufacturing process, key checkpoints should be established:
– Incoming Quality Control (IQC): Checks on raw materials before they enter the production process.
– In-Process Quality Control (IPQC): Ongoing inspections during the manufacturing stages to catch defects early.
– Final Quality Control (FQC): Comprehensive testing of finished products before they are shipped to customers.
Common testing methods employed include:
– Functional Testing: Ensuring that all components operate correctly.
– Durability Testing: Assessing the machine’s performance under simulated usage conditions.
Verifying Supplier Quality Control
B2B buyers must take proactive steps to verify supplier quality control practices. Here are several approaches to consider:
-
Supplier Audits: Conduct regular audits of potential suppliers to assess their manufacturing processes and quality control measures. This can include reviewing their production facilities and meeting with quality assurance teams.
-
Quality Reports: Request detailed quality reports that outline the results of IQC, IPQC, and FQC processes. Look for transparency in how defects are managed and rectified.
-
Third-Party Inspections: Engage third-party inspection services to perform independent quality assessments. This adds an extra layer of assurance that products meet required standards.
Quality Control Nuances for International Buyers
When sourcing from international suppliers, especially from regions like Africa, South America, the Middle East, and Europe, B2B buyers should be aware of specific nuances in quality control:
-
Cultural Differences: Different regions may have varying standards and practices regarding quality assurance. Understanding these cultural contexts can help in establishing effective communication and expectations.
-
Regulatory Compliance: Ensure that suppliers comply with both local and international regulations. For example, European suppliers must meet CE marking requirements, while South American suppliers may have different certifications.
-
Logistics and Delivery: Consider the impact of logistics on product quality. Ensure that your suppliers have robust shipping practices to prevent damage during transit.
Conclusion
For B2B buyers in the vending machine industry, understanding the manufacturing processes and quality assurance protocols is essential for making informed purchasing decisions. By focusing on reliable suppliers who adhere to international standards and employing thorough verification methods, buyers can significantly mitigate risks and enhance the overall success of their vending machine operations.
Related Video: Amazing scenes。Top 6 Most Popular Factory Manufacturing Videos in China
Comprehensive Cost and Pricing Analysis for vending machine jobs Sourcing
Vending machine jobs sourcing involves a multifaceted cost structure that buyers must understand to navigate the market effectively. This analysis breaks down the various cost components and pricing influencers while offering actionable insights for international B2B buyers, particularly those from Africa, South America, the Middle East, and Europe.
Cost Components
-
Materials: The primary cost driver in vending machine jobs is the materials used in production. This includes metal, plastic, electronic components, and any specialized parts. Buyers should consider sourcing from regions with lower raw material costs to optimize expenses.
-
Labor: Labor costs can vary significantly based on geographic location. For instance, countries with lower wage standards may offer more competitive pricing, but buyers should also assess the skill level and productivity of the workforce.
-
Manufacturing Overhead: This includes costs related to factory operations such as utilities, rent, and administrative expenses. Understanding a supplier’s overhead can provide insights into their pricing strategies.
-
Tooling: Custom tooling for specific vending machine designs can be a substantial upfront investment. Buyers should evaluate whether the tooling costs are included in the quoted price or will be additional.
-
Quality Control (QC): Implementing rigorous QC processes ensures product reliability but also adds to overall costs. Buyers should inquire about the QC measures a supplier has in place and their associated costs.
-
Logistics: Transportation costs can significantly impact the final price, especially for international buyers. Factors such as distance, shipping method, and local tariffs should be considered.
-
Margin: Suppliers typically include a profit margin in their pricing. Understanding the average margins in different regions can aid in negotiation.
Price Influencers
-
Volume/MOQ (Minimum Order Quantity): Larger orders often lead to reduced per-unit costs. Buyers should assess their needs carefully and negotiate terms that align with their purchasing power.
-
Specifications/Customization: Custom features can lead to higher costs. Buyers should determine which specifications are essential and where they can compromise to save money.
-
Materials: Higher quality materials come with increased costs. Buyers need to balance the quality of materials with their budget constraints.
-
Quality/Certifications: Certifications for safety and quality can influence costs. Buyers should verify if certifications are necessary for their market and factor these costs into their budgeting.
-
Supplier Factors: Supplier reputation, reliability, and history can impact pricing. Engaging with established suppliers may offer better security and quality assurance but could come at a higher price.
-
Incoterms: The terms of shipping and delivery (Incoterms) can significantly affect pricing. Buyers should clarify responsibilities for shipping costs, insurance, and risks.
Buyer Tips
-
Negotiation: Always negotiate pricing, especially for larger orders. Leverage your purchasing volume to secure better rates.
-
Cost-Efficiency: Look beyond the initial price tag. Analyze the Total Cost of Ownership (TCO), which includes maintenance, operational costs, and potential downtime.
-
Pricing Nuances: Understand regional pricing differences. For instance, European suppliers may have different pricing structures compared to those in Africa or South America due to economic factors.
-
Local Partnerships: Establishing partnerships with local suppliers can reduce logistics costs and improve service responsiveness.
-
Research and Benchmarking: Conduct thorough market research and compare quotes from multiple suppliers to ensure competitive pricing.
Disclaimer
All prices mentioned in this analysis are indicative and subject to fluctuations based on market conditions, currency exchange rates, and supplier negotiations. Buyers are encouraged to conduct their own research and due diligence when sourcing vending machine jobs.
Spotlight on Potential vending machine jobs Manufacturers and Suppliers
- (No specific manufacturer data was available or requested for detailed profiling in this section for vending machine jobs.)*
Essential Technical Properties and Trade Terminology for vending machine jobs
Key Technical Properties for Vending Machine Jobs
Understanding the technical specifications of vending machines is crucial for B2B buyers to ensure they select the right equipment for their needs. Here are some essential properties to consider:
-
Material Grade
– Vending machines are typically constructed from materials like stainless steel, plastic, and tempered glass. The material grade affects durability, corrosion resistance, and overall lifespan. For instance, higher-grade stainless steel is preferred for outdoor machines due to its resistance to weathering. -
Power Consumption
– This specification indicates how much energy the vending machine will use during operation. Lower power consumption is essential for cost management and sustainability. B2B buyers should assess the energy efficiency ratings to align with their operational budgets and environmental goals.
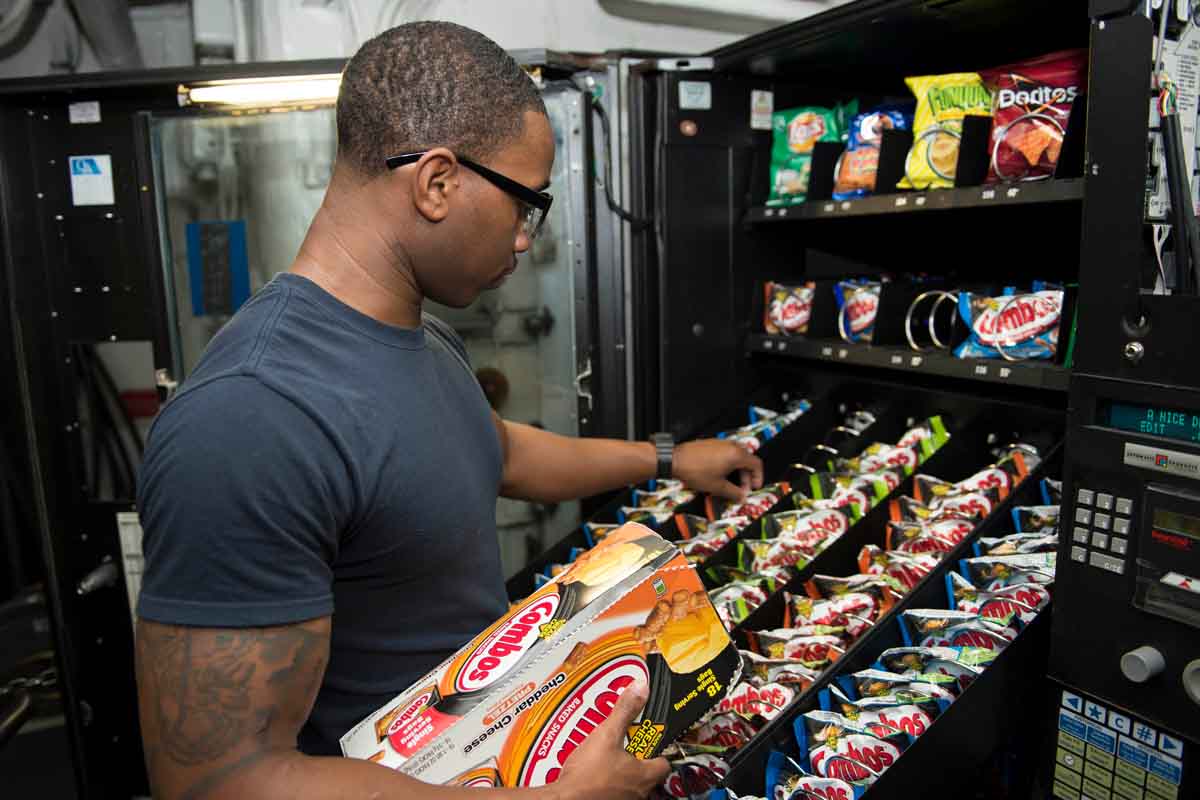
Illustrative Image (Source: Google Search)
-
Capacity and Dimensions
– The capacity refers to the number of items a vending machine can hold, while dimensions are critical for ensuring the machine fits in the designated location. Buyers need to evaluate their product offerings and space constraints to choose a machine that optimizes product availability without compromising accessibility. -
Temperature Control
– For machines dispensing perishable goods, effective temperature control is vital. Specifications should include cooling efficiency and temperature range to ensure that products remain fresh and safe for consumption. This is particularly important in regions with varying climates. -
Payment Systems Compatibility
– Modern vending machines should support multiple payment methods, including cash, credit/debit cards, and mobile payments. Compatibility with various payment systems is crucial for maximizing sales opportunities and catering to consumer preferences. -
User Interface
– The design and functionality of the user interface can greatly affect customer experience. A clear, intuitive interface with options for multiple languages can improve user satisfaction, particularly in diverse markets.
Important Trade Terminology
Familiarity with industry jargon is essential for effective communication and negotiation in the vending machine sector. Here are some key terms:
-
OEM (Original Equipment Manufacturer)
– An OEM is a company that produces parts and equipment that may be marketed by another manufacturer. Understanding OEM relationships is vital for buyers looking to source high-quality vending machines or components. -
MOQ (Minimum Order Quantity)
– MOQ refers to the smallest quantity of a product that a supplier is willing to sell. B2B buyers must consider MOQs when negotiating with manufacturers, as this can impact inventory management and cash flow. -
RFQ (Request for Quotation)
– An RFQ is a document sent to suppliers requesting a price quote for specific goods or services. For vending machine buyers, issuing an RFQ allows for competitive pricing and better negotiation leverage. -
Incoterms (International Commercial Terms)
– These are a set of predefined international trade terms published by the International Chamber of Commerce. They clarify the responsibilities of buyers and sellers in terms of shipping, insurance, and freight costs. Understanding Incoterms is crucial for minimizing risks and ensuring compliance in international transactions.
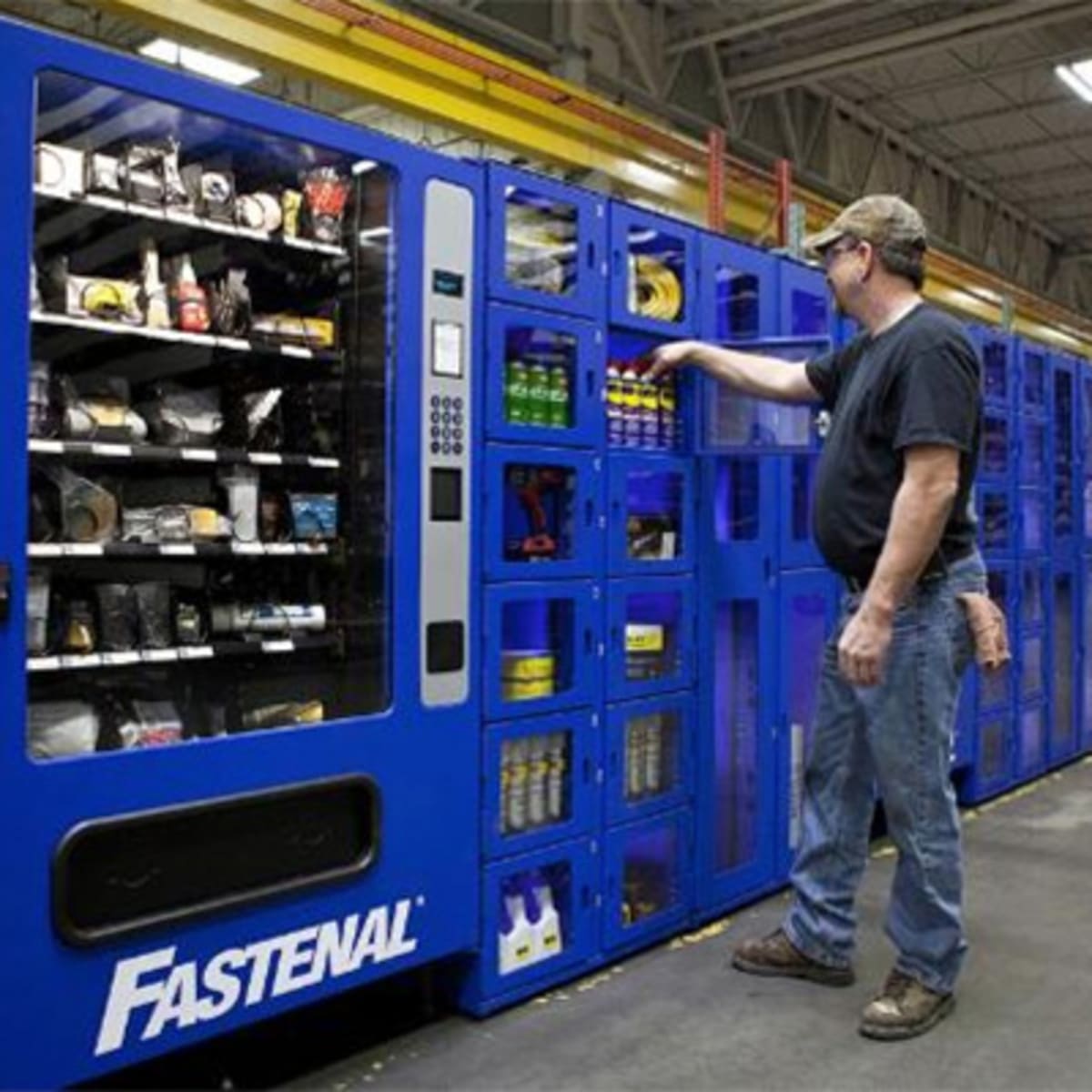
Illustrative Image (Source: Google Search)
-
Lead Time
– Lead time refers to the time taken from placing an order to receiving the product. For vending machine jobs, knowing lead times helps in planning deployment schedules and managing customer expectations. -
Warranty and Service Agreements
– Warranties cover defects and issues arising from manufacturing, while service agreements outline the maintenance and repair services provided. Understanding these terms helps buyers ensure they are protected against potential equipment failures and can maintain operational efficiency.
By grasping these technical properties and industry terminologies, international B2B buyers can make informed decisions, optimize their vending machine investments, and enhance their overall operational efficiency.
Navigating Market Dynamics, Sourcing Trends, and Sustainability in the vending machine jobs Sector
Market Overview & Key Trends
The global vending machine jobs sector is experiencing significant growth, driven by technological advancements, consumer preferences, and changing business landscapes. Key drivers include the rise of cashless transactions, increased demand for convenience, and a growing trend toward automation. International B2B buyers, particularly from Africa, South America, the Middle East, and Europe, must stay attuned to these trends to capitalize on emerging opportunities.
Current and emerging B2B tech trends include the integration of IoT (Internet of Things) devices, which enhance operational efficiency and provide real-time data analytics. This enables businesses to monitor inventory levels, track sales patterns, and optimize supply chains. Additionally, artificial intelligence is being deployed to improve customer engagement through personalized experiences and targeted marketing strategies.
Market dynamics are shifting as companies pivot towards healthier snack options and sustainable products. This trend is particularly pronounced in Europe and North America, but it is gaining traction in regions like Africa and South America as well, where health-conscious consumers are on the rise. B2B buyers should consider sourcing products that align with these preferences, as they can enhance brand reputation and meet consumer demand.
Furthermore, the impact of the COVID-19 pandemic has accelerated the adoption of contactless payment systems and hygiene-focused vending solutions. As a result, international buyers need to evaluate their sourcing strategies to include vendors who prioritize safety and hygiene in their offerings.
Sustainability & Ethical Sourcing in B2B
Sustainability is becoming a critical factor for B2B buyers in the vending machine jobs sector. The environmental impact of traditional vending operations is significant, primarily due to energy consumption and waste generation. Businesses are increasingly required to adopt sustainable practices, such as using energy-efficient machines and minimizing single-use plastics.
Ethical supply chains are paramount in today’s market. Buyers should prioritize partnerships with suppliers who demonstrate commitment to sustainable practices. This includes sourcing materials that are recyclable or biodegradable and ensuring fair labor practices throughout the supply chain. Such initiatives not only reduce environmental impact but also enhance brand image and consumer trust.
Green certifications are valuable tools for B2B buyers looking to validate their sustainability claims. Certifications like Energy Star, Fair Trade, and ISO 14001 can help buyers identify suppliers who adhere to strict environmental and ethical standards. By investing in certified products, companies can differentiate themselves in a competitive market while contributing to a more sustainable future.
Brief Evolution/History
The vending machine industry has evolved significantly since its inception in the early 1880s. Initially focused on dispensing simple products like postcards and chewing gum, the sector has transformed into a sophisticated ecosystem that offers diverse products ranging from fresh food to electronics. The integration of technology has played a pivotal role in this evolution, with modern machines now equipped with touch screens, mobile payment options, and advanced inventory management systems.
The rise of e-commerce and changing consumer behaviors have further influenced the industry, prompting businesses to rethink their vending strategies. Today, the focus is not only on convenience but also on sustainability and ethical sourcing, reflecting broader societal shifts toward responsible consumption. As the industry continues to adapt, international B2B buyers must remain vigilant and proactive in sourcing innovative, sustainable solutions to meet the demands of the modern marketplace.
Related Video: How realistic is the BRICS ambition to reshape global trade without the US Dollar? | DW News
Frequently Asked Questions (FAQs) for B2B Buyers of vending machine jobs
-
How can I effectively vet suppliers for vending machine jobs?
To vet suppliers, start by researching their background and reputation in the industry. Look for reviews and testimonials from other B2B buyers. Request references and check their business licenses and certifications. Additionally, consider visiting their facilities if possible, or conduct virtual meetings to assess their operations. Utilize platforms like Alibaba or Global Sources to find verified suppliers and review their trade history. A thorough vetting process ensures that you partner with reliable suppliers, minimizing risks associated with quality and delivery. -
What customization options should I expect for vending machines?
Many suppliers offer customization options tailored to your specific market needs. This can include branding, machine size, product selection, and payment systems (e.g., cashless transactions). When discussing customization, clearly communicate your requirements and preferences to the supplier. Request prototypes or samples to evaluate the quality of custom features. Be aware that extensive customization may affect lead times and costs, so plan accordingly to ensure that your vending machine meets local market demands. -
What are the typical minimum order quantities (MOQ) and lead times?
MOQs for vending machines can vary significantly based on the supplier and the complexity of the order. Generally, you may find MOQs ranging from 5 to 50 units. Lead times also differ, often taking anywhere from 4 to 12 weeks depending on the supplier’s production capacity and the level of customization required. It’s essential to discuss these factors upfront and obtain written agreements to avoid unexpected delays or costs. Always factor in potential shipping times to ensure timely delivery to your location. -
What payment terms are common in international vending machine transactions?
Common payment terms for international transactions include upfront deposits (typically 30-50%) with the balance paid upon delivery or prior to shipment. Payment methods may involve wire transfers, letters of credit, or escrow services for added security. Ensure that your payment terms are clearly defined in your contract to avoid disputes. Consider the financial regulations and currency exchange rates relevant to your region, as these can impact transaction costs and payment timelines. -
How do I ensure quality assurance and certification for vending machines?
Quality assurance is crucial when sourcing vending machines. Request detailed information about the supplier’s quality management system and any relevant certifications (e.g., ISO 9001). Ask for product samples to evaluate quality firsthand and conduct a thorough inspection before finalizing the order. Additionally, consider third-party quality control services to conduct inspections during production and before shipment. Certifications that comply with international standards can significantly enhance the credibility of your supplier. -
What logistics considerations should I keep in mind when importing vending machines?
Logistics play a vital role in the successful import of vending machines. Ensure that you understand the shipping methods available (e.g., sea freight, air freight) and choose one that balances cost and delivery time. Confirm the supplier’s shipping capabilities and whether they offer support with customs clearance. Be aware of import duties and taxes in your country and factor these costs into your budget. A reliable logistics partner can also help navigate any potential challenges during transit. -
How should I handle disputes with suppliers?
To manage disputes effectively, maintain clear and open communication with your supplier from the outset. Ensure that all agreements are documented in detail, covering aspects like delivery timelines, product specifications, and payment terms. In case of a dispute, try to resolve the issue amicably through discussions. If necessary, refer to a mediation service or arbitration, as specified in your contract. Being proactive in conflict resolution can preserve relationships and lead to better outcomes for both parties. -
What are the key considerations for after-sales support and maintenance?
After-sales support is critical for the long-term success of your vending machine operations. Discuss warranty terms with your supplier, including the duration and coverage of parts and labor. Inquire about their procedures for handling repairs and replacements, as well as the availability of spare parts. Establish a clear communication channel for troubleshooting issues and ensure that your supplier provides adequate training for your staff on maintenance and operation. Reliable after-sales support enhances customer satisfaction and can drive repeat business.
Strategic Sourcing Conclusion and Outlook for vending machine jobs
As the vending machine industry continues to evolve, strategic sourcing remains a critical component for international B2B buyers aiming to optimize their operations. Key takeaways highlight the importance of identifying reliable suppliers, leveraging technology for inventory management, and understanding regional market dynamics. By focusing on these areas, businesses can enhance their operational efficiency and customer satisfaction.
Value of Strategic Sourcing
Strategic sourcing not only reduces costs but also fosters long-term partnerships with suppliers. Engaging with vendors who are aligned with your business values can lead to innovation and improved service delivery. Additionally, diversifying your supplier base can mitigate risks associated with supply chain disruptions, a vital consideration in today’s global market.
Looking Ahead
As we look toward the future, it’s essential for B2B buyers in Africa, South America, the Middle East, and Europe to stay informed about emerging trends such as contactless payments and healthier vending options. Embracing these innovations will position businesses competitively in the market. Now is the time to act—evaluate your current sourcing strategies, explore new partnerships, and invest in technology that enhances your vending operations. The future of vending machine jobs is bright, and your proactive approach will be key to seizing new opportunities.