Your Ultimate Guide to Sourcing Vending Machine Gun Safe
Guide to Vending Machine Gun Safe
- Introduction: Navigating the Global Market for vending machine gun safe
- Understanding vending machine gun safe Types and Variations
- Key Industrial Applications of vending machine gun safe
- Strategic Material Selection Guide for vending machine gun safe
- In-depth Look: Manufacturing Processes and Quality Assurance for vending machine gun safe
- Comprehensive Cost and Pricing Analysis for vending machine gun safe Sourcing
- Spotlight on Potential vending machine gun safe Manufacturers and Suppliers
- Essential Technical Properties and Trade Terminology for vending machine gun safe
- Navigating Market Dynamics, Sourcing Trends, and Sustainability in the vending machine gun safe Sector
- Frequently Asked Questions (FAQs) for B2B Buyers of vending machine gun safe
- Strategic Sourcing Conclusion and Outlook for vending machine gun safe
Introduction: Navigating the Global Market for vending machine gun safe
In an era where security and convenience are paramount, vending machine gun safes have emerged as innovative solutions for firearm storage and access. These specialized units are designed to enhance safety while providing a streamlined method for authorized users to access firearms quickly. For international B2B buyers, particularly those operating in regions like Africa, South America, the Middle East, and Europe, understanding the nuances of this market is critical.
This comprehensive guide delves into the essential aspects of vending machine gun safes, equipping decision-makers with the knowledge to make informed purchasing choices. We explore various types of vending machine gun safes, highlighting their unique features and applications. Buyers will benefit from insights into the materials used in manufacturing, which influence durability and security levels.
Additionally, we examine manufacturing and quality control standards, ensuring that buyers can differentiate between reputable suppliers and those that may compromise on safety. Cost considerations are also addressed, providing a clear understanding of pricing structures and what to expect in terms of return on investment.
Finally, our guide answers common FAQs, addressing potential concerns and clarifying the practicalities of integrating these safes into existing security frameworks. By empowering buyers with this knowledge, we aim to facilitate better sourcing decisions that not only enhance security but also align with regional compliance and operational needs.
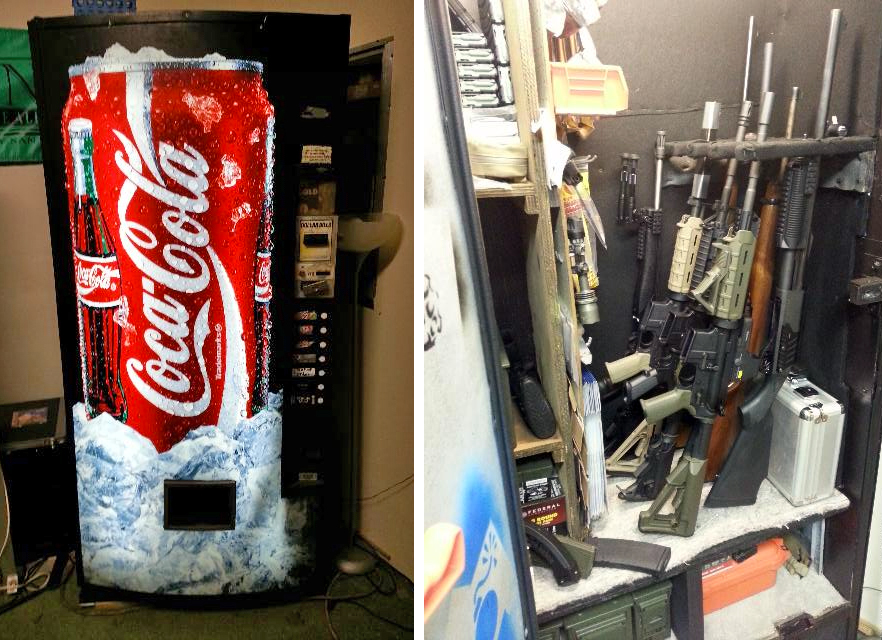
Illustrative Image (Source: Google Search)
Understanding vending machine gun safe Types and Variations
Type Name | Key Distinguishing Features | Primary B2B Applications | Brief Pros & Cons for Buyers |
---|---|---|---|
Traditional Vending Safe | Mechanical lock and secure storage compartments | Retail, firearms training facilities | Pros: Reliable, easy to use. Cons: Limited tech features; potential for lock malfunctions. |
Smart Vending Safe | Digital locks with biometric access and tracking | Military, law enforcement, secure storage facilities | Pros: Enhanced security and monitoring. Cons: Higher cost; requires power source. |
Modular Vending Safe | Customizable sections for varied storage needs | Gun shops, rental services | Pros: Flexibility in configuration. Cons: Installation complexity; may require professional setup. |
Portable Vending Safe | Lightweight and compact design for mobile use | Events, exhibitions, temporary setups | Pros: Easy transport; quick setup. Cons: Less secure; limited capacity. |
High-Security Vending Safe | Reinforced steel construction and advanced locking mechanisms | High-risk environments, government contracts | Pros: Maximum protection; durable. Cons: Heavy; often requires permanent installation. |
Traditional Vending Safe
Traditional vending gun safes are characterized by their mechanical locks and secure storage compartments, making them a popular choice for businesses that prioritize reliability and ease of use. These safes are particularly suitable for retail environments and firearms training facilities where quick access is necessary. When considering this type, buyers should evaluate the trade-off between simplicity and potential vulnerabilities, such as lock malfunctions.
Smart Vending Safe
Smart vending gun safes incorporate digital locks, biometric access, and tracking features, catering to businesses with stringent security requirements. Ideal for military applications, law enforcement agencies, and secure storage facilities, these safes offer enhanced monitoring capabilities. However, buyers must consider the initial investment cost and the necessity of a power source, which may not be feasible in all environments.
Modular Vending Safe
Modular vending gun safes provide customizable sections that allow businesses to adjust the storage layout according to their needs. This flexibility makes them particularly suitable for gun shops and rental services that require varied storage configurations. Buyers should be aware of the potential complexity involved in installation, which may necessitate professional assistance, as well as the need for ongoing adjustments based on inventory changes.
Portable Vending Safe
Portable vending gun safes are designed for lightweight and compact use, making them ideal for events, exhibitions, and temporary setups. Their ease of transport and quick setup are significant advantages for businesses that require mobility. However, the trade-off includes reduced security features and limited storage capacity, which may not be suitable for high-value items or environments where theft risk is higher.
High-Security Vending Safe
High-security vending gun safes are built with reinforced steel construction and advanced locking mechanisms, making them the go-to choice for high-risk environments, including government contracts and sensitive operations. These safes provide maximum protection and durability, but their weight and the requirement for permanent installation can pose challenges in terms of placement and relocation. Buyers should ensure that their facilities can accommodate these substantial units while considering the long-term security benefits they provide.
Related Video: CS 198-126: Lecture 12 – Diffusion Models
Key Industrial Applications of vending machine gun safe
Industry/Sector | Specific Application of Vending Machine Gun Safe | Value/Benefit for the Business | Key Sourcing Considerations for this Application |
---|---|---|---|
Law Enforcement | On-site firearm storage for police departments | Enhances safety and accountability of firearm access | Compliance with local laws, secure locking mechanisms |
Military & Defense | Secure storage for military personnel’s firearms | Protects weapons from theft and unauthorized access | Durability under extreme conditions, modular design |
Sporting Goods Retail | Gun rental services for shooting ranges | Streamlines rental process, improves customer experience | Robust construction, ease of use, and maintenance |
Event Management | Temporary firearm storage for events with security needs | Ensures safety and compliance during high-profile events | Quick deployment, mobile design, and weather resistance |
Educational Institutions | Safe storage for firearms in educational facilities | Promotes safety and responsible firearm ownership | Customization options, adherence to educational policies |
Law Enforcement
In law enforcement, vending machine gun safes serve as on-site storage solutions for police departments. These safes allow for the secure and accountable access of firearms by authorized personnel. By implementing this system, departments can significantly reduce the risk of theft or misuse of firearms, enhancing overall safety. International buyers should ensure these safes comply with local regulations and include robust locking mechanisms to meet the stringent requirements of law enforcement agencies.
Military & Defense
In the military and defense sectors, vending machine gun safes provide secure storage for personnel’s firearms, ensuring that weapons are protected against theft and unauthorized access. The durability of these safes is paramount, as they must withstand extreme environmental conditions. When sourcing for this application, buyers should prioritize features such as modular designs that can adapt to various storage needs and ensure compliance with military specifications to enhance operational efficiency.
Sporting Goods Retail
For sporting goods retailers, vending machine gun safes facilitate a streamlined rental process for firearms at shooting ranges. These systems improve the customer experience by allowing quick and secure access to firearms while maintaining safety protocols. Retailers should consider robust construction and ease of use when sourcing these safes, as well as their maintenance requirements, to ensure long-term operational success and customer satisfaction.
Event Management
In event management, particularly for high-profile events where security is paramount, vending machine gun safes provide a temporary yet secure solution for firearm storage. These safes help ensure compliance with safety regulations while allowing for quick access when needed. Buyers in this sector should focus on features like quick deployment capabilities and mobile designs to adapt to varying event layouts, as well as weather resistance to protect the firearms during outdoor events.
Educational Institutions
Educational institutions that allow for firearm training or storage must prioritize safety, making vending machine gun safes an essential investment. These safes promote responsible firearm ownership and ensure that access is limited to authorized individuals. Buyers in this sector should look for customization options that align with their specific policies and ensure adherence to educational guidelines, thereby fostering a secure learning environment.
Related Video: Uses and Gratifications Theory – UGT
Strategic Material Selection Guide for vending machine gun safe
When selecting materials for vending machine gun safes, international B2B buyers must consider various factors that affect performance, durability, and compliance with regional standards. Below, we analyze several common materials used in the construction of these safes, focusing on their properties, advantages, disadvantages, and specific considerations relevant to buyers from Africa, South America, the Middle East, and Europe.
Steel Alloys
Key Properties: Steel alloys, particularly those with higher carbon content, offer excellent tensile strength and impact resistance. They can withstand high temperatures and pressures, making them suitable for secure applications.
Pros & Cons: The primary advantage of steel alloys is their durability and strength, which provide effective protection against unauthorized access. However, they can be prone to corrosion if not properly treated or coated, which may necessitate additional maintenance costs. The manufacturing complexity can also be higher due to the need for specialized fabrication techniques.
Impact on Application: Steel alloys are compatible with a wide range of environments, but their susceptibility to rust in humid climates can be a concern. Buyers must ensure that appropriate coatings or treatments are applied to enhance corrosion resistance.
Considerations for International Buyers: Compliance with standards such as ASTM A36 or DIN EN 10025 is essential. Buyers in regions like Europe may prefer specific grades that meet local regulations, while those in Africa and South America should consider the availability of local suppliers who can provide treated materials.
Aluminum
Key Properties: Aluminum is lightweight and resistant to corrosion, making it an attractive option for vending machine gun safes. It has a good strength-to-weight ratio and performs well in various environmental conditions.
Pros & Cons: The lightweight nature of aluminum allows for easier handling and installation, which can reduce shipping costs. However, it may not provide the same level of security as steel alloys, making it less suitable for high-risk environments. Additionally, aluminum can be more expensive than some steel options.
Impact on Application: Aluminum is particularly suitable for environments with high humidity or exposure to corrosive elements, such as coastal areas. However, its lower strength may limit its use in high-security applications.
Considerations for International Buyers: Buyers should look for compliance with JIS H 4000 standards for aluminum alloys. In Europe, specific grades may be preferred, and buyers should consider local market conditions that affect pricing and availability.
High-Strength Composite Materials
Key Properties: Composite materials, often made from a combination of polymers and fibers, offer unique properties such as high impact resistance and lightweight characteristics. They can be engineered to meet specific performance criteria.
Pros & Cons: The primary advantage of composites is their ability to resist corrosion and environmental degradation. They are also customizable, allowing for tailored solutions. However, the manufacturing process can be complex and costly, which may affect the overall pricing of the product.
Impact on Application: Composites are suitable for environments where weight is a critical factor, such as mobile installations. However, their performance under extreme conditions (temperature and pressure) may vary based on the specific formulation.
Considerations for International Buyers: Buyers should verify compliance with relevant standards such as ASTM D3039 for composite materials. In regions like the Middle East, where temperature fluctuations can be significant, it is crucial to select composites that can withstand such conditions.
Cold-Rolled Steel
Key Properties: Cold-rolled steel is known for its smooth finish and precise dimensions. It has good strength and is often used in applications requiring a high-quality surface finish.
Pros & Cons: The main advantage of cold-rolled steel is its aesthetic appeal and strength. However, it is more susceptible to corrosion than hot-rolled steel, which may require additional protective coatings. The cost can also be higher due to the additional processing involved.
Impact on Application: Cold-rolled steel is suitable for applications where appearance matters, such as in retail environments. However, its corrosion resistance must be managed through coatings, especially in humid climates.
Considerations for International Buyers: Compliance with standards such as ASTM A1008 is important. Buyers in Europe may need to consider specific finish requirements, while those in Africa should assess local climate impacts on material performance.
Summary Table
Material | Typical Use Case for vending machine gun safe | Key Advantage | Key Disadvantage/Limitation | Relative Cost (Low/Med/High) |
---|---|---|---|---|
Steel Alloys | High-security applications | Excellent strength and durability | Susceptible to corrosion | Medium |
Aluminum | Lightweight, corrosion-resistant safes | Lightweight and easy to handle | Lower security compared to steel | High |
High-Strength Composite Materials | Mobile installations | Corrosion-resistant and customizable | Complex manufacturing process | High |
Cold-Rolled Steel | Retail environments requiring aesthetics | Aesthetic appeal and good strength | More prone to corrosion | Medium |
This guide provides a comprehensive overview of material options for vending machine gun safes, allowing international B2B buyers to make informed decisions based on their specific needs and regional considerations.
In-depth Look: Manufacturing Processes and Quality Assurance for vending machine gun safe
Manufacturing Processes for Vending Machine Gun Safes
The manufacturing of vending machine gun safes is a meticulous process that combines advanced technology with skilled craftsmanship. Understanding this process is crucial for international B2B buyers, particularly those from Africa, South America, the Middle East, and Europe, as it directly impacts the quality, durability, and reliability of the product.
Main Stages of Manufacturing
-
Material Preparation
– Selection of Materials: The first step involves selecting high-quality materials, typically steel or reinforced alloys, that meet strength and durability standards. Buyers should inquire about the grade of steel used, as this significantly affects the safe’s resistance to tampering and environmental factors.
– Cutting and Shaping: Materials are then cut into required dimensions using laser cutting or water jet cutting techniques. Precision is key here, as it ensures that all components fit together seamlessly during assembly. -
Forming
– Bending and Forming: The cut materials undergo bending processes using hydraulic presses to create the shell of the gun safe. This stage is crucial for ensuring that the safe can withstand physical attacks.
– Welding: Once shaped, components are welded together. Techniques such as MIG or TIG welding are commonly used to ensure strong joints that enhance the overall integrity of the safe. -
Assembly
– Component Integration: After forming, the safe is assembled. This includes integrating locks, hinges, and electronic components. The quality of these components is critical; therefore, buyers should verify the specifications and sourcing of these parts.
– Functional Testing: Each safe undergoes initial functional testing to ensure that all components work correctly before finishing. -
Finishing
– Surface Treatment: The final stage involves surface treatments such as powder coating or galvanizing, which provide corrosion resistance and aesthetic appeal. Buyers should inquire about the finishing processes to ensure they meet their specific environmental conditions.
– Quality Control Checks: Final inspections are conducted to ensure that the product meets the required specifications and standards.
Quality Assurance in Manufacturing
Quality assurance is a critical aspect of the manufacturing process for vending machine gun safes. It ensures that the final product is reliable and meets international standards.
Relevant International Standards
- ISO 9001: This standard outlines the criteria for a quality management system and is essential for manufacturers to demonstrate their ability to consistently provide products that meet customer and regulatory requirements.
- CE Marking: For European markets, CE marking indicates compliance with health, safety, and environmental protection standards.
- API Standards: The American Petroleum Institute (API) standards are relevant for manufacturers producing products intended for use in hazardous environments.
Quality Control Checkpoints
-
Incoming Quality Control (IQC)
– At this stage, raw materials are inspected for quality and compliance with specifications. Buyers should ensure that suppliers maintain rigorous IQC processes to prevent defects from entering the production line. -
In-Process Quality Control (IPQC)
– During manufacturing, ongoing inspections are conducted to monitor the production process. This includes checks on welding quality, dimensional accuracy, and assembly integrity. -
Final Quality Control (FQC)
– Once the product is completed, FQC involves comprehensive testing of the final product to ensure it meets all specifications. This may include functional tests, stress tests, and safety checks.
Common Testing Methods
- Load Testing: Verifying that the safe can withstand specified weights without deformation.
- Environmental Testing: Ensuring the safe’s durability under various environmental conditions, such as humidity, temperature fluctuations, and exposure to corrosive elements.
- Tamper Resistance Testing: Assessing how well the safe can resist unauthorized access attempts.
Verifying Supplier Quality Control
For B2B buyers, especially those in international markets, verifying supplier quality control processes is essential to mitigate risks associated with product reliability.
-
Conducting Audits
– Regular audits of manufacturing facilities can provide insights into the supplier’s adherence to quality standards. Buyers should request audit reports and verify their findings. -
Reviewing Quality Control Reports
– Suppliers should provide detailed quality control reports that outline their processes, testing results, and compliance with international standards. Buyers should scrutinize these documents for transparency. -
Engaging Third-Party Inspectors
– Utilizing third-party inspection services can offer an impartial assessment of the manufacturing processes and product quality. This is particularly useful for buyers who may not be able to physically inspect the manufacturing facilities.
Quality Control and Certification Nuances for International Buyers
For B2B buyers from diverse regions such as Africa, South America, the Middle East, and Europe, understanding the nuances of quality control and certification is vital.
- Regional Standards Compliance: Different regions may have specific standards that products must meet. Buyers should familiarize themselves with these standards to ensure compliance and avoid legal issues.
- Cultural Considerations: Communication styles and business practices vary by region. Building strong relationships with suppliers can facilitate better quality assurance practices.
- Logistics and Supply Chain Challenges: Buyers should consider logistics when sourcing from international suppliers. Delays in shipping can affect the timely delivery of quality products.
In conclusion, understanding the manufacturing processes and quality assurance protocols for vending machine gun safes is essential for international B2B buyers. By focusing on material quality, manufacturing techniques, and rigorous quality control measures, buyers can ensure they procure reliable products that meet their specific needs.
Related Video: ▶️GUN Production💣2025: Manufacturing weapon from Start to Finish – Assembly by Factory workers
Comprehensive Cost and Pricing Analysis for vending machine gun safe Sourcing
When considering the sourcing of vending machine gun safes, it is essential to understand the comprehensive cost structure and pricing dynamics involved. This analysis will provide actionable insights for international B2B buyers, particularly in Africa, South America, the Middle East, and Europe.
Cost Components
-
Materials: The primary materials involved in the production of vending machine gun safes include steel, locking mechanisms, and electronic components. Quality and type of materials significantly affect the overall cost. High-grade steel and advanced locking systems may lead to higher upfront costs but offer enhanced security and durability.
-
Labor: Labor costs vary significantly across regions. In countries with lower labor costs, such as some in South America and Africa, manufacturers may offer competitive pricing. However, it is crucial to evaluate the skill level of the workforce, as experienced labor can contribute to better craftsmanship.
-
Manufacturing Overhead: This includes costs related to utilities, facility maintenance, and equipment depreciation. Buyers should inquire about the manufacturing environment and any certifications (e.g., ISO) that ensure quality standards are met.
-
Tooling: Customization often requires specialized tooling, which can increase initial costs. Buyers looking for unique designs or features should factor in the tooling expenses and time required for production.
-
Quality Control (QC): A rigorous QC process is vital in ensuring the safety and functionality of vending machine gun safes. Suppliers with established QC protocols may charge a premium, but this investment can prevent costly recalls or safety issues.
-
Logistics: Shipping costs can vary based on distance, shipping method, and Incoterms. Buyers should consider the total logistics costs, including duties, taxes, and insurance, when evaluating supplier quotes.
-
Margin: Suppliers will add a margin to cover their operational costs and profit. Understanding the typical margins in the industry can help buyers assess whether a quoted price is fair.
Price Influencers
-
Volume/MOQ: Many suppliers offer discounts for bulk purchases or higher minimum order quantities (MOQs). Negotiating for larger orders can significantly reduce per-unit costs.
-
Specifications/Customization: Custom features can increase costs. Buyers should clearly define their requirements to avoid unexpected charges.
-
Materials: The choice of materials will impact both price and quality. Opting for lower-cost materials may reduce upfront costs but could affect longevity and security.
-
Quality/Certifications: Products with recognized certifications (e.g., UL listed) may command higher prices but provide assurance of quality and compliance with safety standards.
-
Supplier Factors: Established suppliers with a track record of reliability may charge more due to their brand reputation. However, this often correlates with better service and product quality.
-
Incoterms: Understanding Incoterms (International Commercial Terms) is crucial for determining who bears the cost and risk during shipping. Different terms can lead to significant cost variations.
Buyer Tips
-
Negotiation: Engage suppliers in discussions about pricing and terms. Leverage your purchasing power by comparing multiple quotes and negotiating for better terms.
-
Cost-Efficiency: Evaluate the total cost of ownership (TCO), which includes purchase price, maintenance, and potential replacement costs. A higher initial investment in a quality product may result in lower long-term expenses.
-
Pricing Nuances: Be aware of currency fluctuations and their impact on pricing, especially when dealing with international suppliers. Consider locking in prices when favorable exchange rates are available.
-
Regional Considerations: Buyers in Africa, South America, the Middle East, and Europe should be mindful of local regulations regarding gun safes, as compliance can influence pricing and availability.
Disclaimer
Prices for vending machine gun safes can vary widely based on the factors outlined above. This analysis serves as a guide, and it is advisable for buyers to conduct thorough market research and obtain multiple quotes to ensure they are making informed decisions.
Spotlight on Potential vending machine gun safe Manufacturers and Suppliers
This section offers a look at a few manufacturers active in the ‘vending machine gun safe’ market. This is a representative sample for illustrative purposes; B2B buyers must conduct their own extensive due diligence before any engagement. Information is synthesized from public sources and general industry knowledge.
Essential Technical Properties and Trade Terminology for vending machine gun safe
Key Technical Properties for Vending Machine Gun Safes
When evaluating vending machine gun safes, understanding their technical properties is crucial for making informed purchasing decisions. Here are some essential specifications to consider:
-
Material Grade
The material grade indicates the quality and durability of the safe. Common materials include high-grade steel, which offers superior resistance to tampering and environmental conditions. For B2B buyers, selecting a high-grade material ensures longevity and reliability, reducing the need for replacements and enhancing security. -
Locking Mechanism
This refers to the type of locking system used, which may include electronic locks, biometric systems, or traditional key locks. A robust locking mechanism is essential for ensuring that firearms are securely stored and can only be accessed by authorized personnel. B2B buyers should prioritize safes with advanced locking technologies that meet international security standards. -
Weight and Size
The weight and dimensions of the safe are critical factors that impact both transport and installation. Heavier safes often provide increased security but may pose logistical challenges. Buyers should assess their space constraints and transportation capabilities to ensure that the selected safe fits their operational needs. -
Fire Resistance Rating
This rating indicates how well the safe can withstand fire exposure. A higher fire resistance rating means that the contents will be better protected in the event of a fire. For businesses in regions prone to such risks, investing in safes with high fire ratings is advisable to safeguard valuable assets. -
Water Resistance
Similar to fire resistance, this property ensures that the safe can protect its contents from water damage. This is particularly important in areas with high humidity or flooding risks. A water-resistant safe can prevent significant financial losses due to environmental factors, making it a vital consideration for international buyers.
Common Trade Terminology
Familiarity with industry-specific terminology is essential for effective communication and negotiation in the B2B landscape. Here are some key terms related to vending machine gun safes:
-
OEM (Original Equipment Manufacturer)
This term refers to companies that produce parts or equipment that may be marketed by another manufacturer. In the context of vending machine gun safes, understanding OEM relationships can help buyers identify reliable suppliers and assess product authenticity. -
MOQ (Minimum Order Quantity)
MOQ indicates the smallest quantity of a product that a supplier is willing to sell. For international buyers, negotiating MOQs can significantly impact inventory management and cash flow. It’s important to strike a balance between cost-effectiveness and ensuring adequate stock levels. -
RFQ (Request for Quotation)
An RFQ is a document sent to suppliers requesting pricing and terms for specific products. In the vending machine gun safe market, issuing RFQs allows buyers to compare offers from multiple vendors, ensuring competitive pricing and better procurement decisions. -
Incoterms (International Commercial Terms)
These are standardized terms used in international trade to define responsibilities between buyers and sellers. Understanding Incoterms is crucial for B2B transactions, as they clarify who is responsible for shipping costs, insurance, and risks associated with the transport of goods. -
Lead Time
Lead time refers to the amount of time from placing an order until the product is delivered. In the B2B environment, knowing the lead time is essential for inventory planning and ensuring timely availability of products, particularly for businesses with tight deadlines.
By grasping these essential properties and trade terms, international B2B buyers can make more informed decisions regarding the procurement of vending machine gun safes, ensuring both security and operational efficiency.
Navigating Market Dynamics, Sourcing Trends, and Sustainability in the vending machine gun safe Sector
Market Overview & Key Trends
The global market for vending machine gun safes is witnessing significant growth, driven by increasing awareness of firearm safety and the rising demand for secure storage solutions. B2B buyers from regions such as Africa, South America, the Middle East, and Europe are particularly influenced by several key dynamics. Regulatory frameworks in many countries are tightening, mandating enhanced security measures for firearm storage, which in turn propels the demand for advanced vending machine gun safes that comply with these regulations.
Emerging technologies such as smart locking systems and integrated inventory management are becoming increasingly prevalent. These innovations not only enhance security but also improve user accessibility and inventory tracking, appealing to B2B buyers looking for efficiency and accountability in their operations. Moreover, the trend toward automation in the vending machine sector is paving the way for more sophisticated solutions that offer real-time data analytics and remote monitoring capabilities.
Additionally, the sustainability movement is influencing purchasing decisions, as international buyers prioritize products that align with eco-friendly practices. As a result, suppliers are adapting their offerings to include sustainable materials and energy-efficient technologies, catering to the evolving preferences of conscious consumers. For B2B buyers, understanding these trends is crucial for making informed sourcing decisions that align with both regulatory requirements and market expectations.
Sustainability & Ethical Sourcing in B2B
Sustainability has become a cornerstone of purchasing decisions in the vending machine gun safe sector. The environmental impact of manufacturing processes, from material sourcing to production waste, is under scrutiny. B2B buyers are increasingly seeking suppliers who demonstrate a commitment to ethical sourcing and sustainable manufacturing practices.
Utilizing recycled materials and ensuring that production processes are energy-efficient are essential factors to consider. Buyers should look for certifications such as ISO 14001, which indicates a company’s adherence to effective environmental management systems. Furthermore, the use of green certifications can enhance the product’s marketability and appeal to end-users who value sustainability.
Engaging with suppliers who prioritize ethical labor practices ensures that the entire supply chain upholds social responsibility. This includes avoiding materials sourced from conflict zones and ensuring fair labor practices in the manufacturing process. B2B buyers should conduct thorough due diligence to verify the ethical practices of potential suppliers to build a resilient and responsible supply chain.
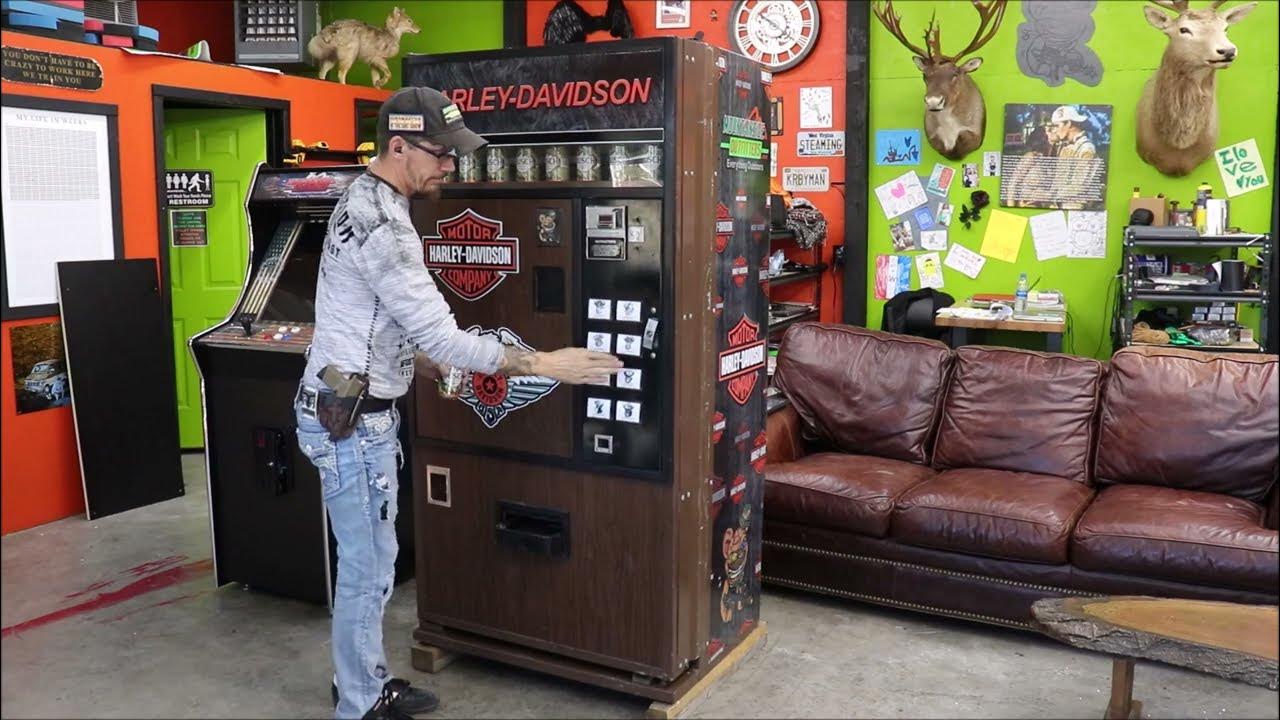
Illustrative Image (Source: Google Search)
Brief Evolution/History
The concept of vending machine gun safes has evolved significantly over the last few decades. Initially, these products were simple mechanical locks with limited functionality. However, technological advancements have transformed them into sophisticated systems equipped with digital locks, biometric access, and even smartphone connectivity. This evolution reflects broader trends in both the vending machine industry and firearm safety, with a growing emphasis on security, accessibility, and user experience.
As the market continues to evolve, B2B buyers must stay informed about the latest innovations and regulatory changes that shape the industry landscape. Understanding this historical context can provide valuable insights into future trends and sourcing strategies.
Related Video: Is global trade transforming? | Counting the Cost
Frequently Asked Questions (FAQs) for B2B Buyers of vending machine gun safe
-
What key factors should I consider when vetting suppliers for vending machine gun safes?
When vetting suppliers, prioritize their industry experience, reputation, and production capabilities. Check for certifications relevant to safety and security standards in your region, such as ISO or CE marks. Conduct background checks by requesting references from previous clients and reviewing their financial stability. Additionally, assess their ability to customize products to meet specific regulations or preferences in your target market. -
Can I customize the vending machine gun safes to meet local market needs?
Yes, many suppliers offer customization options for vending machine gun safes. You can request modifications such as size, locking mechanisms, and branding elements to align with local regulations or customer preferences. Ensure you communicate your specific requirements clearly during initial discussions. Additionally, inquire about the supplier’s flexibility in adapting designs for different markets, as this may affect lead times and costs. -
What are the typical minimum order quantities (MOQs) and lead times for vending machine gun safes?
MOQs for vending machine gun safes can vary significantly based on the supplier and customization requirements. Standard orders might range from 50 to 200 units. Lead times typically range from 6 to 12 weeks, depending on the complexity of the order and supplier capacity. It’s advisable to discuss your needs upfront to negotiate MOQs and lead times that suit your business model and market demand. -
What payment terms are commonly offered by suppliers, and how can I ensure secure transactions?
Payment terms can vary; common arrangements include upfront deposits of 30-50% with the balance due before shipment. To ensure secure transactions, consider using letters of credit or escrow services, especially for large orders. Verify the supplier’s payment methods and be cautious of any requests for payment via unconventional methods. Establish clear agreements on payment schedules in your contract to avoid disputes. -
What quality assurance practices should I expect from suppliers of vending machine gun safes?
Reputable suppliers should adhere to stringent quality assurance (QA) practices, including regular inspections throughout the production process. Request details about their QA protocols, including third-party testing and certifications. It’s also beneficial to ask for samples before placing a larger order to evaluate the product quality firsthand. Ensure that the supplier provides warranties or guarantees to protect your investment. -
Are there specific certifications or compliance documents I need to request from suppliers?
Yes, depending on your region, specific certifications might be required to ensure compliance with local laws and safety standards. Common certifications include ISO 9001 for quality management systems and CE marking for products sold within the European Union. Additionally, inquire about any regional compliance documents that may be necessary for importation, such as safety testing reports or product liability insurance. -
What logistics considerations should I keep in mind when importing vending machine gun safes?
Logistics play a crucial role in the successful importation of vending machine gun safes. Consider shipping methods, customs regulations, and potential tariffs in your destination country. Work with logistics partners who have experience with heavy or bulky goods to ensure timely delivery. It’s also wise to understand the local distribution channels and warehousing options available to facilitate market entry. -
How should I handle disputes with suppliers regarding product quality or delivery issues?
To effectively manage disputes, establish clear terms and conditions in your contract regarding quality expectations and delivery timelines. Maintain open communication with your supplier to address issues promptly. If disputes arise, document all correspondence and evidence related to the problem. Consider mediation or arbitration as a resolution method to avoid lengthy legal battles. Having a well-defined dispute resolution process in place can significantly streamline conflict management.
Strategic Sourcing Conclusion and Outlook for vending machine gun safe
In conclusion, strategic sourcing for vending machine gun safes is a vital consideration for international B2B buyers aiming to enhance security solutions in their markets. By prioritizing quality, compliance with local regulations, and supplier reliability, organizations can ensure they are investing in products that not only meet their operational needs but also foster trust with their customers.
Key Takeaways:
– Market Research: Conduct thorough research to identify suppliers with a proven track record in the vending machine gun safe sector, especially those who understand regional security concerns.
– Supplier Relationships: Build strong partnerships with suppliers that offer flexibility and customization options, addressing the unique demands of your local market.
– Cost-Benefit Analysis: Evaluate total cost of ownership, considering factors such as maintenance, warranty, and long-term durability, to make informed purchasing decisions.
As the global landscape continues to evolve, staying ahead of emerging trends and regulatory changes will be crucial for success. Buyers from Africa, South America, the Middle East, and Europe should actively engage with industry networks and attend trade shows to stay informed and connected. Embrace this opportunity to secure your investments and lead in the competitive landscape of gun safety solutions.