Your Ultimate Guide to Sourcing Vending Machine For
Guide to Vending Machine For Medications
- Introduction: Navigating the Global Market for vending machine for medications
- Understanding vending machine for medications Types and Variations
- Key Industrial Applications of vending machine for medications
- Strategic Material Selection Guide for vending machine for medications
- In-depth Look: Manufacturing Processes and Quality Assurance for vending machine for medications
- Comprehensive Cost and Pricing Analysis for vending machine for medications Sourcing
- Spotlight on Potential vending machine for medications Manufacturers and Suppliers
- Essential Technical Properties and Trade Terminology for vending machine for medications
- Navigating Market Dynamics, Sourcing Trends, and Sustainability in the vending machine for medications Sector
- Frequently Asked Questions (FAQs) for B2B Buyers of vending machine for medications
- Strategic Sourcing Conclusion and Outlook for vending machine for medications
Introduction: Navigating the Global Market for vending machine for medications
In today’s rapidly evolving healthcare landscape, the integration of vending machines for medications is revolutionizing the way pharmaceuticals are dispensed, offering a vital solution to enhance accessibility and efficiency. These automated systems not only facilitate convenient access to medications but also play a crucial role in managing inventory and reducing the burden on healthcare facilities. For international B2B buyers, particularly those from Africa, South America, the Middle East, and Europe, understanding the global market for medication vending machines is essential for making informed sourcing decisions.
This comprehensive guide delves into the multifaceted world of medication vending machines, exploring various types tailored to different environments, including hospitals, pharmacies, and public spaces. We will cover materials used in manufacturing, ensuring durability and safety, and discuss the importance of manufacturing quality control (QC) standards that guarantee reliability.
Additionally, the guide will provide insights into evaluating suppliers, understanding cost structures, and analyzing market trends, empowering buyers to navigate potential partnerships effectively. A dedicated FAQ section will address common inquiries, further enhancing your understanding and confidence in this innovative solution.
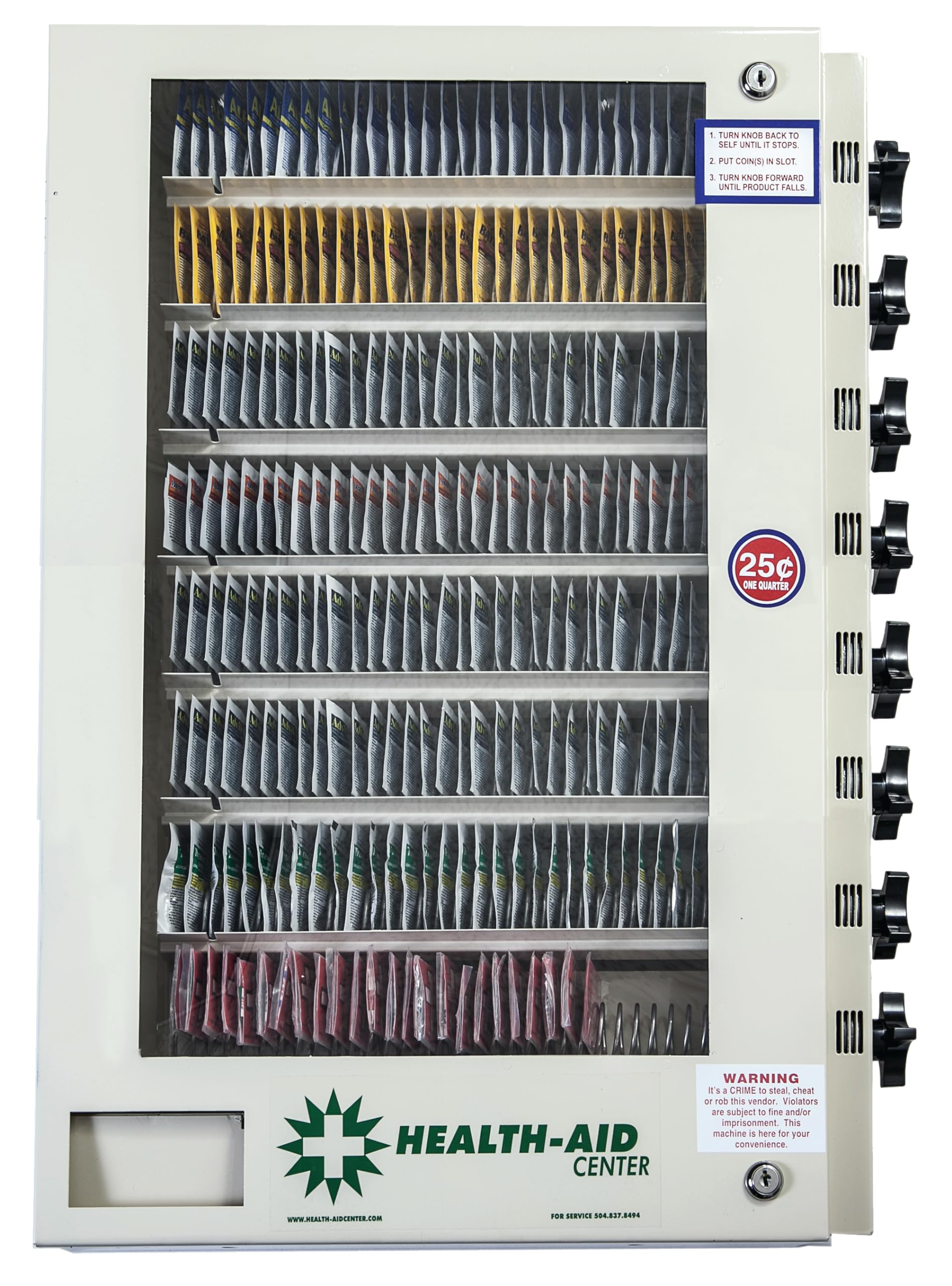
Illustrative Image (Source: Google Search)
By equipping yourself with this knowledge, you will be better positioned to leverage the benefits of vending machines for medications, ultimately contributing to improved patient care and operational efficiency in your region.
Understanding vending machine for medications Types and Variations
Type Name | Key Distinguishing Features | Primary B2B Applications | Brief Pros & Cons for Buyers |
---|---|---|---|
Automated Pharmacy Kiosks | Offers a wide range of prescription medications | Hospitals, clinics, pharmacies | Pros: Reduces wait times; enhances access to medications. Cons: High initial investment; requires maintenance. |
Over-the-Counter (OTC) Vending Machines | Dispenses non-prescription medications and health products | Airports, shopping malls, convenience stores | Pros: Low operational cost; easy to refill. Cons: Limited product range; regulatory compliance needed. |
Cold Storage Medication Dispensers | Maintains temperature-sensitive medications | Hospitals, pharmacies, long-term care facilities | Pros: Essential for certain medications; ensures efficacy. Cons: Higher energy costs; requires regular monitoring. |
Smart Medication Dispensers | Integrates technology for tracking and reminders | Elderly care facilities, home healthcare | Pros: Improves medication adherence; provides data analytics. Cons: Complexity in setup; potential tech issues. |
Customized Vending Solutions | Tailored to specific medication needs or environments | Specialty clinics, remote areas | Pros: Meets unique demands; flexible design. Cons: Longer lead times; potentially higher costs. |
Automated Pharmacy Kiosks
Automated pharmacy kiosks are designed to dispense a wide range of prescription medications, making them ideal for hospitals, clinics, and pharmacies. These machines reduce patient wait times and enhance accessibility to essential medications. However, buyers should consider the high initial investment and ongoing maintenance costs associated with these systems.
Over-the-Counter (OTC) Vending Machines
OTC vending machines provide non-prescription medications and health products, making them popular in high-traffic areas such as airports and shopping malls. Their low operational costs and ease of restocking are significant advantages. However, buyers must be aware of the limited product range and the need for compliance with local regulations.
Cold Storage Medication Dispensers
Cold storage medication dispensers are crucial for maintaining the integrity of temperature-sensitive medications. They are primarily used in hospitals, pharmacies, and long-term care facilities. While these machines ensure the efficacy of medications, they also incur higher energy costs and require regular monitoring to maintain appropriate temperatures.
Smart Medication Dispensers
Smart medication dispensers incorporate technology to track usage and send reminders, making them particularly useful in elderly care facilities and home healthcare settings. They enhance medication adherence and provide valuable data analytics. However, buyers should be prepared for the complexity of setup and the potential for technical issues that may arise.
Customized Vending Solutions
Customized vending solutions are tailored to meet specific medication needs or environmental requirements, making them suitable for specialty clinics and remote areas. These machines can address unique demands and offer flexible designs. However, buyers should consider longer lead times for production and the possibility of higher costs due to customization.
Related Video: How our 24/7 prescription vending machine works
Key Industrial Applications of vending machine for medications
Industry/Sector | Specific Application of Vending Machine for Medications | Value/Benefit for the Business | Key Sourcing Considerations for this Application |
---|---|---|---|
Healthcare Facilities | Automated dispensing in hospitals and clinics | Increased efficiency, reduced wait times for patients | Compliance with health regulations, reliability of dispensing systems |
Pharmacies | 24/7 medication access | Enhanced customer service, increased sales volume | Integration with existing pharmacy software, security features |
Corporate Wellness Programs | On-site medication access for employees | Improved employee health management, reduced absenteeism | Customization options for medication types, user-friendly interface |
Remote Healthcare Services | Mobile medication dispensers for rural areas | Better healthcare access, increased patient adherence | Durability in various climates, ease of transport and setup |
Educational Institutions | Medication access for students with chronic conditions | Support for student health, reduced emergency incidents | Compliance with educational regulations, inventory management capabilities |
Detailed Applications
Healthcare Facilities
In hospitals and clinics, vending machines for medications serve as automated dispensing units that streamline the process of providing medications to patients. These machines can be stocked with essential medications and equipped with technology to track inventory levels. By reducing the time healthcare professionals spend on medication distribution, they can focus more on patient care. Buyers in this sector must ensure that the machines comply with local health regulations and have reliable dispensing systems to avoid errors.
Pharmacies
Pharmacies can leverage vending machines to offer 24/7 access to over-the-counter medications, enhancing customer service and potentially increasing sales. The machines can be strategically placed in high-traffic areas, allowing customers to purchase medications outside regular hours. When sourcing these machines, pharmacies should consider the integration capabilities with their existing software systems and the security features to protect against theft or vandalism.
Corporate Wellness Programs
Companies implementing wellness programs can install vending machines that dispense medications for common ailments, such as pain relievers or allergy medications, directly on-site. This promotes a healthier workforce and can reduce absenteeism by making it easier for employees to access necessary medications. Corporate buyers should look for machines that allow customization of medication types and ensure that they have user-friendly interfaces to cater to a diverse workforce.
Remote Healthcare Services
For healthcare providers operating in rural or remote areas, mobile medication vending machines can significantly improve access to essential medications. These machines can be transported to various locations, ensuring that patients who may not have easy access to pharmacies can still receive necessary treatments. Buyers should prioritize durability, ensuring that the machines can withstand varying climates and are easy to transport and set up.
Educational Institutions
Schools and universities can install vending machines for students with chronic conditions, providing timely access to medications during school hours. This initiative supports student health and can reduce incidents related to medication non-adherence. Buyers in educational sectors must ensure that the machines comply with educational regulations and include inventory management capabilities to keep track of medication supplies efficiently.
Related Video: What are all the Laboratory Apparatus and their uses?
Strategic Material Selection Guide for vending machine for medications
When selecting materials for vending machines designed for medications, it is crucial to consider various factors that influence product performance, durability, and compliance with international standards. Below is an analysis of four common materials used in these vending machines, focusing on their properties, advantages, disadvantages, and relevant considerations for international B2B buyers.
1. Stainless Steel
Key Properties: Stainless steel offers excellent corrosion resistance, high strength, and durability. Its temperature rating typically ranges from -200°C to 800°C, depending on the grade.
Pros & Cons: The primary advantage of stainless steel is its ability to withstand harsh environments without rusting. It is easy to clean, making it suitable for maintaining hygiene in medication vending machines. However, it can be more expensive than other materials, and its manufacturing processes can be complex, particularly for intricate designs.
Impact on Application: Stainless steel is compatible with a wide range of media, including various medications and cleaning agents, ensuring the integrity of the products dispensed.
Considerations for International Buyers: Buyers should ensure compliance with local health and safety regulations. Standards such as ASTM A240 for stainless steel sheets are critical in regions like Europe and the Middle East.
2. Polycarbonate
Key Properties: Polycarbonate is a high-performance plastic known for its impact resistance and clarity. It can withstand temperatures up to 135°C and has good UV resistance.
Pros & Cons: The main advantage of polycarbonate is its lightweight nature and high impact resistance, making it ideal for transparent panels in vending machines. However, it is less resistant to scratches compared to glass and may not withstand high temperatures as effectively.
Impact on Application: Polycarbonate is suitable for applications where visibility of the products is essential, such as in medication vending machines. However, it may not be compatible with certain solvents or harsh chemicals.
Considerations for International Buyers: Buyers should look for compliance with standards like ISO 1183 for plastic materials. In regions such as Africa and South America, understanding local regulations regarding plastic use is vital.
3. Aluminum
Key Properties: Aluminum is lightweight, corrosion-resistant, and has a temperature rating of -50°C to 150°C. It is also a good conductor of heat.
Pros & Cons: Aluminum’s lightweight nature makes it easy to handle and install, which can reduce shipping costs. However, it can be more expensive than steel and may require additional coatings for enhanced corrosion resistance.
Impact on Application: Aluminum is suitable for structural components in vending machines but may not be ideal for direct contact with medications unless properly coated.
Considerations for International Buyers: Buyers must ensure that aluminum components meet standards such as ASTM B221 for aluminum extrusions. In Europe, compliance with the REACH regulation concerning chemical safety is also essential.
4. Glass
Key Properties: Glass is non-reactive, providing excellent visibility and protection for the contents inside the vending machine. It can withstand temperatures up to 300°C, depending on the type of glass.
Pros & Cons: The primary advantage of glass is its chemical inertness and aesthetic appeal. However, it is fragile and can break easily, posing safety risks.
Impact on Application: Glass is ideal for display panels and containers in medication vending machines, ensuring that the products are visible and protected from contamination.
Considerations for International Buyers: Compliance with safety standards such as ASTM C1036 for flat glass is crucial, particularly in regions like Europe and the Middle East, where safety regulations are stringent.
Summary Table
Material | Typical Use Case for vending machine for medications | Key Advantage | Key Disadvantage/Limitation | Relative Cost (Low/Med/High) |
---|---|---|---|---|
Stainless Steel | Structural components, exterior casing | Excellent corrosion resistance | Higher cost, complex manufacturing | High |
Polycarbonate | Transparent panels, internal components | Lightweight, impact-resistant | Scratches easily, limited temperature tolerance | Medium |
Aluminum | Structural elements, frames | Lightweight, good corrosion resistance | More expensive, may require coatings | Medium |
Glass | Display panels, protective containers | Chemical inertness, aesthetic appeal | Fragile, risk of breakage | Medium to High |
This material selection guide provides a comprehensive overview for international B2B buyers, emphasizing the importance of material properties, compliance with standards, and specific applications in the context of medication vending machines.
In-depth Look: Manufacturing Processes and Quality Assurance for vending machine for medications
Manufacturing Processes for Vending Machines for Medications
The manufacturing of vending machines for medications involves a series of meticulously planned stages, each designed to ensure the final product meets stringent quality and safety standards. For B2B buyers, understanding these processes is essential for selecting reliable suppliers and ensuring that the machines they purchase are fit for purpose.
Main Stages of Manufacturing
-
Material Preparation
– Material Selection: The choice of materials is critical, particularly for components that will come into contact with medications. Stainless steel and high-grade plastics are commonly used due to their resistance to corrosion and ease of cleaning.
– Pre-treatment: Materials may undergo pre-treatment processes such as cleaning, surface treatment, or coating to enhance durability and functionality. -
Forming
– Sheet Metal Fabrication: This involves cutting and shaping metal sheets into the required components using techniques like laser cutting, bending, and stamping.
– Injection Molding: For plastic parts, injection molding is often employed. This technique allows for precision manufacturing of complex shapes that are lightweight yet strong. -
Assembly
– Component Assembly: This stage involves putting together various components, including the vending mechanism, electronic systems, and medication storage compartments. Automated assembly lines are often used to enhance efficiency and precision.
– Integration of Technology: Advanced technologies, such as IoT connectivity and user interfaces, are integrated during assembly to ensure the machines can be monitored and managed remotely. -
Finishing
– Surface Treatment: Finishing processes such as powder coating or painting are applied to enhance aesthetics and provide additional protection against wear and tear.
– Quality Control (QC) Preparation: At this stage, machines are prepared for rigorous testing to ensure they meet all specifications and regulations.
Quality Assurance Procedures
Quality assurance in the manufacturing of medication vending machines is paramount, as these machines must comply with international safety standards and regulations. The following outlines the key aspects of QC relevant to B2B buyers.
International Standards
- ISO 9001: This is a widely recognized standard for quality management systems. Suppliers should be certified to this standard to ensure they follow consistent quality processes.
- CE Marking: In Europe, CE marking signifies that the product meets EU safety, health, and environmental protection standards. It is crucial for B2B buyers in Europe to verify this certification for compliance.
- API Standards: For machines dispensing medications, adherence to API (Active Pharmaceutical Ingredient) standards is essential to ensure that the machines are safe for pharmaceutical use.
QC Checkpoints
-
Incoming Quality Control (IQC)
– Conducts inspections on raw materials and components upon arrival to ensure they meet specified requirements before production begins. -
In-Process Quality Control (IPQC)
– Continuous monitoring throughout the manufacturing process, including checks during assembly and forming to catch any defects early. -
Final Quality Control (FQC)
– A comprehensive inspection of the finished product, including functional testing to ensure that all components work as intended and that the machine meets all regulatory requirements.
Common Testing Methods
- Functional Testing: Verifying that the machine operates correctly under various conditions.
- Stress Testing: Assessing the machine’s durability by simulating prolonged use and exposure to environmental factors.
- Electrical Safety Testing: Ensuring that all electronic components meet safety standards to prevent hazards.
Verifying Supplier Quality Control
For B2B buyers, especially those from Africa, South America, the Middle East, and Europe, verifying a supplier’s quality control processes is essential. Here are strategies to consider:
- Supplier Audits: Conduct on-site audits of manufacturing facilities to assess compliance with quality standards and manufacturing practices.
- Quality Reports: Request detailed quality assurance reports and documentation demonstrating adherence to international standards.
- Third-Party Inspections: Engage independent inspectors to evaluate the manufacturing process and finished products. This can provide an unbiased assessment of quality.
QC and Certification Nuances for International Buyers
When sourcing vending machines for medications internationally, buyers should be aware of specific nuances that may affect quality and certification:
- Local Regulations: Different countries may have varying regulations regarding the manufacture and sale of medical devices. Familiarize yourself with local laws to ensure compliance.
- Cultural and Economic Factors: Understand that manufacturers in different regions may have different capabilities and resources, which can influence quality and delivery timelines.
- Communication: Establish clear communication channels with suppliers to discuss quality expectations and requirements, ensuring alignment on standards from the outset.
Conclusion
The manufacturing processes and quality assurance protocols for vending machines for medications are intricate and essential for ensuring safety and reliability. By understanding these processes, B2B buyers can make informed decisions when selecting suppliers and ensure that the machines they procure meet all necessary standards. Implementing thorough verification methods will further safeguard against potential risks associated with sourcing in the international marketplace.
Related Video: Inside AstraZeneca Modern Pharmaceutical Production Plant | Modern Factory
Comprehensive Cost and Pricing Analysis for vending machine for medications Sourcing
The cost structure for vending machines specifically designed for medications encompasses several critical components. Understanding these costs is essential for international B2B buyers looking to optimize their sourcing strategies.
Cost Components
-
Materials: The primary materials include high-grade metals for the frame, glass or durable plastics for the front, and electronic components for payment systems and inventory management. The choice of materials directly impacts both durability and cost. For instance, stainless steel might be preferred for its longevity and hygiene standards, but it comes at a higher price.
-
Labor: Labor costs vary significantly by region. In countries with lower labor costs, such as certain nations in Africa or South America, buyers might find competitive manufacturing rates. However, labor costs can increase if specialized skills are required for assembly or installation.
-
Manufacturing Overhead: This includes costs related to facilities, utilities, and administrative expenses. Effective overhead management can lead to lower overall pricing. Buyers should inquire about how suppliers allocate these costs when quoting prices.
-
Tooling: Customization of vending machines requires specific tooling, which can be a significant upfront cost. Buyers should assess whether suppliers can absorb these costs or if they will be passed on, particularly for low-volume orders.
-
Quality Control (QC): Ensuring compliance with health and safety regulations for medication dispensing is crucial. QC processes may add to the cost but are essential for maintaining product integrity and buyer trust.
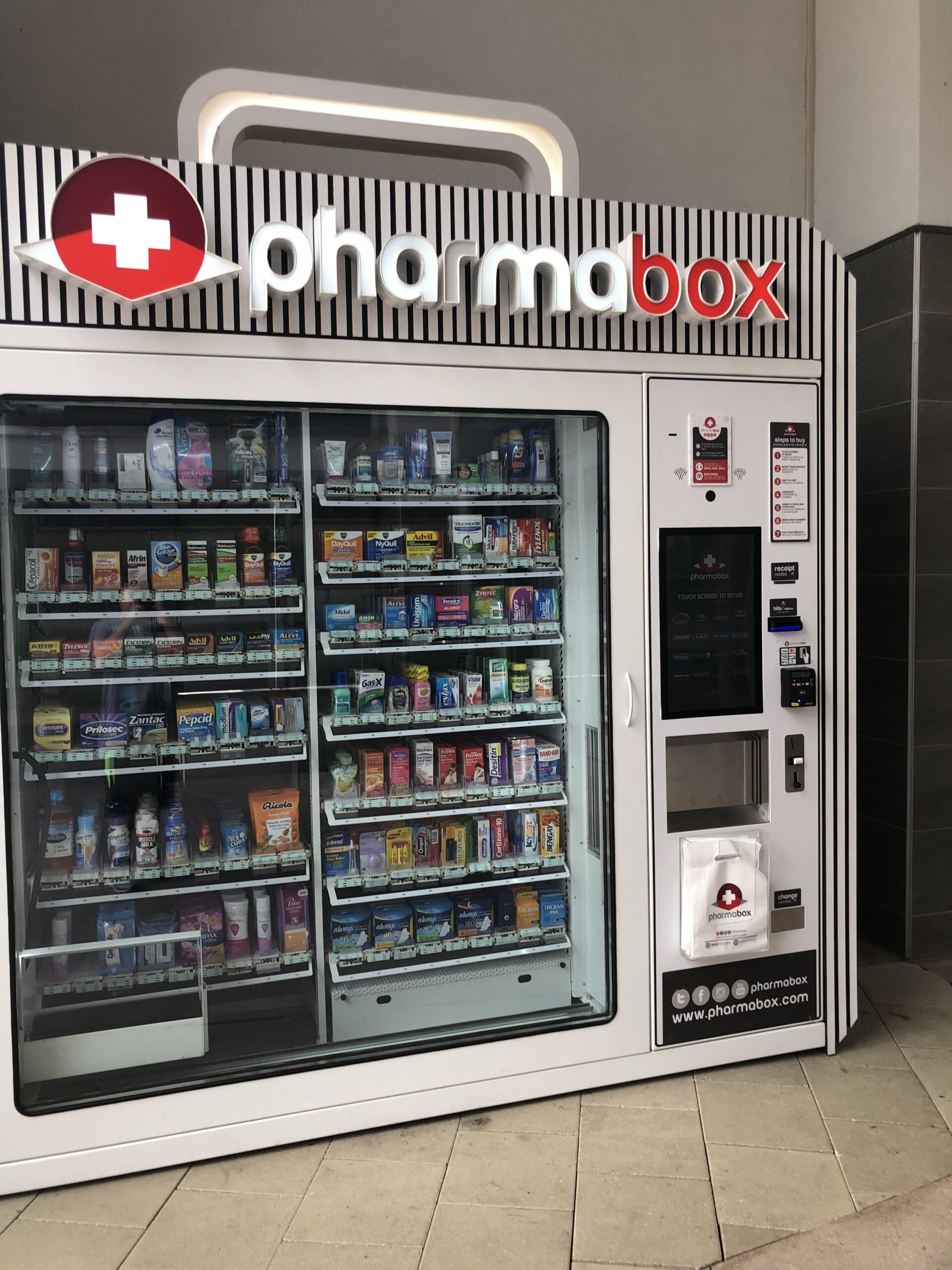
Illustrative Image (Source: Google Search)
-
Logistics: Shipping costs can be substantial, especially for international transactions. Factors such as distance, shipping method, and Incoterms (International Commercial Terms) will influence these costs. Buyers should consider local warehousing options to mitigate high shipping costs.
-
Margin: Suppliers typically add a markup to cover their risks and profit. Understanding the market dynamics can help buyers gauge reasonable margins based on industry standards.
Price Influencers
-
Volume/MOQ: Bulk orders often lead to lower per-unit prices. Establishing a minimum order quantity (MOQ) can provide leverage for better pricing.
-
Specifications/Customization: Custom features such as branding, additional functionalities, or specific sizes can increase costs. Buyers should clearly define their requirements to avoid unexpected expenses.
-
Materials: The choice of materials not only affects durability and aesthetics but also the cost. Premium materials will elevate the price.
-
Quality/Certifications: Machines that meet rigorous safety and quality standards, especially for medication dispensing, may carry higher costs. Certifications can also enhance the perceived value.
-
Supplier Factors: Supplier reputation, reliability, and experience can influence pricing. Established suppliers may charge more but offer better support and product reliability.
-
Incoterms: Understanding the terms of trade is crucial for international buyers. Incoterms dictate who is responsible for shipping, insurance, and tariffs, which can significantly impact total costs.
Buyer Tips
-
Negotiation: Effective negotiation can yield favorable terms. Buyers should come prepared with market research to substantiate their requests.
-
Cost-Efficiency: Evaluate the total cost of ownership (TCO), which includes not only the purchase price but also installation, maintenance, and operational costs over the machine’s lifecycle.
-
Pricing Nuances: Be aware that pricing may fluctuate based on economic conditions, exchange rates, and local market demand. Regularly monitoring these factors can inform better purchasing decisions.
Disclaimer
Prices and costs mentioned in this analysis are indicative and may vary based on specific supplier negotiations, market conditions, and individual project requirements. It is advisable for buyers to conduct thorough due diligence and obtain multiple quotes to ensure competitive pricing.
Spotlight on Potential vending machine for medications Manufacturers and Suppliers
This section offers a look at a few manufacturers active in the ‘vending machine for medications’ market. This is a representative sample for illustrative purposes; B2B buyers must conduct their own extensive due diligence before any engagement. Information is synthesized from public sources and general industry knowledge.
Essential Technical Properties and Trade Terminology for vending machine for medications
When considering the procurement of vending machines for medications, international B2B buyers must navigate a complex landscape of technical specifications and trade terminology. Understanding these elements can enhance decision-making and ensure compliance with local regulations, particularly in regions such as Africa, South America, the Middle East, and Europe.
Critical Technical Specifications
-
Material Grade
– Definition: The quality and type of materials used in the construction of the vending machine, typically stainless steel or high-grade plastics.
– Importance: Material quality affects durability, hygiene, and the ability to withstand environmental factors, which is crucial for machines dispensing medications. Buyers should ensure that materials comply with local health regulations. -
Temperature Control Range
– Definition: The operational temperature range that the vending machine can maintain for stored medications.
– Importance: Many medications require specific storage conditions to remain effective. Understanding this range helps buyers select machines that ensure the integrity of pharmaceuticals, especially in regions with extreme temperatures. -
Power Supply Specifications
– Definition: Details about the voltage, frequency, and power consumption of the vending machine.
– Importance: Ensuring compatibility with local power supply standards is essential to avoid operational disruptions and additional costs for converters or transformers. -
Capacity
– Definition: The maximum number of items the machine can hold, typically measured in units or volume.
– Importance: Capacity affects inventory management and can influence the return on investment. Buyers should assess expected demand to determine the appropriate size.
-
User Interface Technology
– Definition: The type of interface used for customer interaction, such as touch screens or keypad systems.
– Importance: A user-friendly interface is critical for customer satisfaction and can affect usage rates. Machines with intuitive designs can enhance user experience, particularly in multilingual regions. -
Security Features
– Definition: Includes locks, alarms, and surveillance options to protect against theft and tampering.
– Importance: Security is paramount for vending machines dispensing medications. Buyers should ensure that the machines are equipped with adequate security features to safeguard valuable inventory.
Common Trade Terms
-
OEM (Original Equipment Manufacturer)
– Definition: A company that produces parts or equipment that may be marketed by another manufacturer.
– Importance: Understanding OEM relationships can help buyers identify potential suppliers and negotiate better terms based on the quality and reliability of components. -
MOQ (Minimum Order Quantity)
– Definition: The smallest quantity of a product that a supplier is willing to sell.
– Importance: Knowing the MOQ helps buyers manage budgets and inventory levels, especially when entering new markets or testing demand. -
RFQ (Request for Quotation)
– Definition: A document sent to suppliers requesting pricing information for specific products or services.
– Importance: An RFQ is essential for comparing costs and features across multiple vendors, allowing buyers to make informed purchasing decisions. -
Incoterms (International Commercial Terms)
– Definition: A set of predefined international rules that clarify the responsibilities of buyers and sellers regarding shipping, insurance, and tariffs.
– Importance: Familiarity with Incoterms helps buyers understand shipping costs and liability, ensuring that all parties are clear on their obligations during the transaction. -
Lead Time
– Definition: The amount of time it takes from placing an order to receiving the goods.
– Importance: Understanding lead times is crucial for inventory planning and ensuring timely access to medications, particularly in urgent care scenarios. -
Certification Compliance
– Definition: Adherence to specific standards set by regulatory bodies regarding product safety and efficacy.
– Importance: Buyers must ensure that vending machines comply with local and international regulations to avoid legal issues and ensure consumer safety.
By grasping these technical properties and trade terms, B2B buyers can enhance their procurement strategy for vending machines intended for medication distribution, ensuring both compliance and operational efficiency.
Navigating Market Dynamics, Sourcing Trends, and Sustainability in the vending machine for medications Sector
Market Overview & Key Trends
The global market for vending machines for medications is witnessing rapid growth, driven by the increasing demand for convenient healthcare solutions. Key factors propelling this trend include the rise in chronic diseases, the need for 24/7 access to medications, and the expansion of telemedicine. International B2B buyers, especially from Africa, South America, the Middle East, and Europe, must recognize the importance of integrating advanced technologies such as IoT and AI in these vending solutions. These technologies not only enhance operational efficiency but also improve customer engagement through personalized services.
Emerging trends in sourcing reveal a shift towards modular vending machines that can be easily customized and upgraded. This flexibility allows businesses to adapt to changing healthcare regulations and consumer preferences. Additionally, the rise of mobile payment solutions and contactless transactions is reshaping the purchasing experience, making it crucial for suppliers to offer systems that accommodate these payment methods. For buyers in diverse markets, understanding local regulations and consumer behavior is essential for successful product implementation.
Furthermore, as countries strive to improve their healthcare infrastructure, partnerships between vending machine manufacturers and pharmaceutical companies are becoming more common. These collaborations can facilitate access to a broader range of medications and provide valuable data for inventory management, ultimately benefiting healthcare providers and patients alike.
Sustainability & Ethical Sourcing in B2B
Sustainability is becoming a critical consideration in the vending machine sector, particularly in light of increasing environmental regulations and consumer demand for eco-friendly products. For international B2B buyers, understanding the environmental impact of their supply chains is essential. This includes assessing the carbon footprint of the materials used in vending machines and the logistics involved in their distribution.
Ethical sourcing practices are increasingly important, as buyers seek suppliers who prioritize responsible manufacturing processes and fair labor practices. Companies that can demonstrate compliance with international sustainability standards, such as ISO 14001, or those that utilize green certifications, will have a competitive edge. Additionally, incorporating recycled materials and energy-efficient technologies in vending machines can significantly reduce environmental impact while appealing to environmentally conscious consumers.
Investing in sustainable vending solutions not only aligns with global sustainability goals but also enhances brand reputation. As buyers increasingly prioritize eco-friendly practices, suppliers who adopt green innovations are likely to foster loyalty and attract new business.
Brief Evolution/History
The concept of vending machines for medications has evolved significantly over the past few decades. Initially, these machines offered only a limited selection of over-the-counter drugs. However, advancements in technology have transformed them into sophisticated healthcare solutions capable of dispensing prescription medications, monitoring inventory, and providing real-time data to healthcare providers.
The integration of telemedicine into vending solutions has further revolutionized the industry, enabling remote consultations and medication dispensing. This evolution has made it essential for B2B buyers to stay informed about technological advancements and regulatory changes that may impact the vending machine landscape. As the healthcare sector continues to innovate, the demand for intelligent and sustainable vending solutions will only grow, presenting ample opportunities for strategic partnerships and investment.
Related Video: Incoterms for beginners | Global Trade Explained
Frequently Asked Questions (FAQs) for B2B Buyers of vending machine for medications
-
How can I effectively vet suppliers of vending machines for medications?
When vetting suppliers, prioritize their experience in the medical vending machine sector. Check for certifications relevant to health and safety standards, such as ISO or CE marks. Request references from previous clients and assess their product range and customization options. Additionally, visit their production facilities if possible, or utilize third-party audits to ensure compliance with local regulations, especially in markets like Africa and South America where standards may vary. -
What customization options are typically available for medication vending machines?
Many suppliers offer customization options, including size, design, and software interfaces tailored to your business needs. You may also request features like temperature control for sensitive medications, user-friendly interfaces in multiple languages, and secure payment systems. Discuss your specific requirements during initial consultations to ensure that the machines meet local regulations and customer preferences in your target market. -
What are the common minimum order quantities (MOQ) and lead times for these machines?
MOQs can vary significantly based on the supplier and the complexity of the machines. Typically, you may encounter MOQs ranging from 10 to 50 units for custom orders. Lead times can range from 4 to 12 weeks, depending on the level of customization and production capacity. Always confirm these details upfront to align with your business timelines and inventory planning. -
What payment terms should I expect when sourcing medication vending machines internationally?
Payment terms often depend on the supplier’s policies and your negotiation skills. Common arrangements include a deposit of 30-50% upfront, with the balance due upon delivery or installation. Consider using secure payment methods such as letters of credit or escrow services to protect your investment, especially in regions with fluctuating currencies or economic instability. -
What quality assurance measures should be in place for these vending machines?
Ensure that the supplier implements rigorous quality assurance protocols, including pre-production samples, in-process inspections, and final testing before shipment. Request documentation of quality certifications and any compliance checks performed during production. Additionally, inquire about warranties and after-sales support, as these can be critical for maintaining operational efficiency. -
How should I approach logistics for importing vending machines to my country?
Collaborate with logistics experts familiar with international shipping regulations and customs clearance procedures. Assess the best shipping methods, considering factors such as cost, speed, and handling requirements for sensitive medical equipment. Ensure that the supplier provides adequate packaging to prevent damage during transit, and consider insurance options to safeguard your investment. -
What steps can I take to resolve disputes with suppliers?
Establish clear contracts that outline terms, delivery schedules, and penalties for non-compliance to minimize disputes. In the event of a disagreement, attempt to resolve issues through open communication first. If necessary, consider mediation or arbitration as a next step, especially if the supplier is based in a different country. Familiarize yourself with international trade laws relevant to your agreement, as this may influence your approach to dispute resolution. -
What certifications should medication vending machines have to ensure compliance?
Look for certifications that demonstrate compliance with local and international health and safety standards. Key certifications include ISO 13485 for medical devices, CE marking for products sold in Europe, and FDA approval for machines used in the U.S. Understanding the specific regulations in your target market—whether in Africa, South America, the Middle East, or Europe—is crucial to ensure your machines are compliant and operationally viable.
Strategic Sourcing Conclusion and Outlook for vending machine for medications
In conclusion, strategic sourcing for vending machines that dispense medications offers significant opportunities for international B2B buyers. By prioritizing quality suppliers, understanding local regulations, and investing in technology, businesses can enhance their operational efficiency and customer satisfaction. Key takeaways include the importance of evaluating supplier capabilities, ensuring compliance with health and safety standards, and leveraging data analytics to optimize inventory management.
Moreover, as the demand for automated healthcare solutions grows, particularly in regions like Africa, South America, the Middle East, and Europe, there is an urgent need for businesses to adapt. Emphasizing local partnerships can facilitate smoother market entry and compliance with regional regulations.
As you consider your sourcing strategies, remember that the future of medication delivery is evolving rapidly. Engage with innovative vendors who can provide not only machines but also integrated solutions that enhance patient care. Now is the time to act—invest in strategic sourcing to position your business at the forefront of this transformative market. Together, we can redefine healthcare accessibility and efficiency across the globe.