Your Ultimate Guide to Sourcing Used Underwear Vending
Guide to Used Underwear Vending Machine
- Introduction: Navigating the Global Market for used underwear vending machine
- Understanding used underwear vending machine Types and Variations
- Key Industrial Applications of used underwear vending machine
- Strategic Material Selection Guide for used underwear vending machine
- In-depth Look: Manufacturing Processes and Quality Assurance for used underwear vending machine
- Comprehensive Cost and Pricing Analysis for used underwear vending machine Sourcing
- Spotlight on Potential used underwear vending machine Manufacturers and Suppliers
- Essential Technical Properties and Trade Terminology for used underwear vending machine
- Navigating Market Dynamics, Sourcing Trends, and Sustainability in the used underwear vending machine Sector
- Frequently Asked Questions (FAQs) for B2B Buyers of used underwear vending machine
- Strategic Sourcing Conclusion and Outlook for used underwear vending machine
Introduction: Navigating the Global Market for used underwear vending machine
In an increasingly diverse global marketplace, the demand for innovative products continues to grow, and the used underwear vending machine is no exception. This unique offering caters to niche markets, providing a blend of convenience and novelty that appeals to a variety of consumers. International B2B buyers, especially from regions such as Africa, South America, the Middle East, and Europe, are presented with a compelling opportunity to tap into this emerging sector.
Understanding the critical importance of used underwear vending machines involves recognizing their potential to drive revenue and attract a distinct clientele. This guide aims to equip you with comprehensive insights into the various types of vending machines available, the materials used in their construction, and the manufacturing and quality control processes that ensure product reliability. Additionally, we delve into supplier options, cost considerations, and market trends, all tailored to facilitate informed sourcing decisions.
With a focus on actionable insights and real-world applications, this guide empowers B2B buyers to navigate the complexities of the used underwear vending machine market. By leveraging this information, you can enhance your strategic sourcing capabilities, optimize your supply chain, and ultimately increase your competitive edge in a rapidly evolving industry. Embrace the opportunity to innovate within your offerings and cater to a market that craves uniqueness and convenience.
Understanding used underwear vending machine Types and Variations
Type Name | Key Distinguishing Features | Primary B2B Applications | Brief Pros & Cons for Buyers |
---|---|---|---|
Standard Vending Machine | Dispenses used underwear in various sizes and styles | Retail locations, adult novelty shops | Pros: Familiar technology, easy to maintain. Cons: Limited product variety. |
Automated Selection Unit | Touchscreen interface for customized selections | High-end boutiques, specialty retailers | Pros: Enhanced customer engagement, higher sales potential. Cons: Higher upfront costs, requires tech support. |
Mobile Vending Units | Compact, transportable machines for events and festivals | Outdoor events, pop-up shops | Pros: Flexibility in location, caters to transient markets. Cons: Limited inventory, potential for lower sales volume. |
Subscription Model Machines | Monthly subscription service for regular users | Subscription box services, niche markets | Pros: Steady revenue stream, builds customer loyalty. Cons: Complexity in inventory management, requires ongoing marketing. |
Luxury Experience Machines | High-end design with premium product offerings | Luxury retail spaces, exclusive events | Pros: Attracts affluent clientele, enhances brand image. Cons: High operational costs, niche market appeal. |
Standard Vending Machine
Standard vending machines are the most common type for dispensing used underwear. They typically offer a variety of sizes and styles, making them suitable for retail locations and adult novelty shops. When considering a purchase, buyers should evaluate the machine’s durability and ease of maintenance, as these factors significantly impact operational costs. The familiarity of this technology can be an advantage, but the limited product variety may restrict market appeal.
Automated Selection Unit
These machines feature a touchscreen interface that allows customers to customize their selections. This type is particularly beneficial for high-end boutiques and specialty retailers, as it enhances customer engagement and potentially increases sales. However, buyers should be aware of the higher upfront costs and the need for ongoing technical support. The investment in technology can pay off through improved customer satisfaction and loyalty.
Mobile Vending Units
Mobile vending units are compact machines designed for transport to various events and festivals. They cater to outdoor events and pop-up shops, providing flexibility in location and the ability to tap into transient markets. While this type allows for a diverse customer base, buyers must consider inventory limitations and the potential for lower sales volume due to the transient nature of the clientele.
Subscription Model Machines
These machines offer a monthly subscription service, appealing to regular users who prefer convenience and consistency. They are ideal for niche markets and subscription box services. Buyers should consider the complexity involved in inventory management and the necessity of ongoing marketing efforts to maintain customer interest. However, the steady revenue stream and potential for building customer loyalty make this model attractive for long-term profitability.
Luxury Experience Machines
Luxury experience machines are designed with high-end aesthetics and offer premium product selections. They are best suited for luxury retail spaces and exclusive events, attracting affluent clientele and enhancing brand image. While they can command higher prices and create a unique shopping experience, buyers should be mindful of the high operational costs and the niche market appeal, which may limit broader market penetration.
Related Video: THE TRUTH BEHIND JAPANS USED PANTY VENDING MACHINES
Key Industrial Applications of used underwear vending machine
Industry/Sector | Specific Application of used underwear vending machine | Value/Benefit for the Business | Key Sourcing Considerations for this Application |
---|---|---|---|
Hospitality | Providing unique guest amenities in hotels | Enhances guest experience and differentiation | Compliance with hygiene standards, machine reliability |
Retail | Novelty item sales in urban locations | Attracts a niche market, increases foot traffic | Location analysis, machine customization options |
Entertainment Venues | Unique merchandise for events and concerts | Offers a memorable experience, boosts merchandise sales | Event-specific branding, inventory management |
Fitness Centers | Convenience for members post-workout | Increases member satisfaction, enhances services | Space requirements, machine maintenance |
Travel and Tourism | Unique offerings at airports or tourist attractions | Captures impulse purchases, enhances visitor experience | High visibility locations, regulatory compliance |
Hospitality
In the hospitality sector, used underwear vending machines can serve as a unique amenity in hotels, particularly in boutique or themed establishments. These machines offer guests an unconventional option that enhances their experience and sets the hotel apart from competitors. Buyers in this sector should prioritize compliance with hygiene standards and ensure the machines are reliable and easy to maintain to avoid service disruptions.
Retail
In retail, particularly in urban settings, these vending machines can act as novelty item sales points. They attract a niche market looking for unique or quirky purchases. International B2B buyers should conduct thorough location analyses to determine high-traffic areas and consider customization options to align with local market trends and cultural sensitivities.
Entertainment Venues
Entertainment venues, such as concert halls or sports arenas, can utilize used underwear vending machines to offer unique merchandise that enhances the visitor experience. This application not only provides a memorable purchase option but also boosts merchandise sales. Buyers should focus on event-specific branding and effective inventory management strategies to optimize sales during events.
Fitness Centers
Fitness centers can implement these machines to provide convenience for members who may need extra undergarments after workouts. This service improves member satisfaction and adds value to their membership. Key considerations for buyers include ensuring the machines fit within the available space and establishing a maintenance schedule to keep the machines in optimal working condition.
Travel and Tourism
In the travel and tourism industry, placing used underwear vending machines in airports or tourist attractions can capture impulse purchases from travelers. This application enhances the visitor experience by offering unique products in high-traffic areas. Buyers should focus on securing high visibility locations and ensuring compliance with local regulations regarding vending operations.
Strategic Material Selection Guide for used underwear vending machine
When selecting materials for used underwear vending machines, international B2B buyers must consider various factors, including durability, cost, and compliance with regional standards. Below is an analysis of four common materials used in the construction of these machines, focusing on their properties, advantages, disadvantages, and specific considerations for buyers from Africa, South America, the Middle East, and Europe.
1. Stainless Steel (e.g., AISI 304)
Key Properties:
Stainless steel is known for its excellent corrosion resistance, high strength, and ability to withstand high temperatures. It is also non-reactive, making it suitable for environments where hygiene is paramount.
Pros & Cons:
– Pros: Highly durable, easy to clean, and resistant to rust and corrosion. Its aesthetic appeal also makes it suitable for consumer-facing applications.
– Cons: Higher initial cost compared to other materials and may require specialized manufacturing processes for complex designs.
Impact on Application:
Stainless steel is ideal for vending machines that will be exposed to varying environmental conditions, ensuring longevity and reliability.
Considerations for International Buyers:
Buyers should ensure compliance with local health and safety regulations and look for certifications that meet ASTM or DIN standards. In regions like the UAE and Europe, the demand for high-quality materials is significant, making stainless steel a preferred choice.
2. Mild Steel (e.g., A36)
Key Properties:
Mild steel is characterized by its good tensile strength and ductility. It is more affordable than stainless steel but lacks corrosion resistance unless coated.
Pros & Cons:
– Pros: Cost-effective and easy to work with, making it suitable for mass production.
– Cons: Prone to rust and corrosion without protective coatings, which can affect durability.
Impact on Application:
Mild steel may be suitable for indoor vending machines where exposure to moisture is limited. However, it may not be ideal for outdoor applications.
Considerations for International Buyers:
Buyers should consider the cost of protective coatings and ensure compliance with local corrosion resistance standards. In regions with high humidity, such as parts of Africa and South America, additional protective measures may be necessary.
3. Aluminum (e.g., 6061-T6)
Key Properties:
Aluminum is lightweight, corrosion-resistant, and has good thermal conductivity. It is often used in applications where weight is a concern.
Pros & Cons:
– Pros: Lightweight and resistant to corrosion, making it easy to transport and install. It also has a good strength-to-weight ratio.
– Cons: More expensive than mild steel and can be less durable under heavy loads or impacts.
Impact on Application:
Aluminum is suitable for vending machines that require mobility or are used in environments where weight is a critical factor.
Considerations for International Buyers:
Buyers should verify that aluminum components meet local standards for strength and corrosion resistance. In Europe, adherence to EU regulations on materials is crucial.
4. High-Density Polyethylene (HDPE)
Key Properties:
HDPE is a durable plastic known for its impact resistance and low moisture absorption. It is also resistant to many chemicals.
Pros & Cons:
– Pros: Lightweight, cost-effective, and resistant to corrosion and impact. It is also easy to mold into various shapes.
– Cons: Less durable than metals under extreme conditions and may not provide the same aesthetic appeal.
Impact on Application:
HDPE is ideal for components that require flexibility and resistance to chemicals, making it suitable for specific internal parts of vending machines.
Considerations for International Buyers:
Buyers should ensure that HDPE complies with food safety regulations if the vending machine dispenses consumables. Standards such as FDA or EU food contact regulations should be considered.
Summary Table
Material | Typical Use Case for used underwear vending machine | Key Advantage | Key Disadvantage/Limitation | Relative Cost (Low/Med/High) |
---|---|---|---|---|
Stainless Steel (e.g., AISI 304) | Exterior casing, high-traffic areas | Excellent corrosion resistance and durability | Higher initial cost | High |
Mild Steel (e.g., A36) | Indoor vending machines | Cost-effective and easy to manufacture | Prone to rust without coatings | Low |
Aluminum (e.g., 6061-T6) | Lightweight, portable vending machines | Lightweight and corrosion-resistant | Less durable under heavy loads | Medium |
High-Density Polyethylene (HDPE) | Internal components, flexible parts | Impact-resistant and cost-effective | Less durable than metals | Low |
This guide provides a comprehensive overview of material options for used underwear vending machines, enabling international B2B buyers to make informed decisions based on their specific needs and regional requirements.
In-depth Look: Manufacturing Processes and Quality Assurance for used underwear vending machine
Manufacturing Processes for Used Underwear Vending Machines
The manufacturing of used underwear vending machines involves several critical stages that ensure the final product is functional, reliable, and safe for consumers. Understanding these processes is vital for international B2B buyers looking to source high-quality machines.
1. Material Preparation
Selection of Materials: The first step involves choosing high-quality materials suitable for vending machine construction. Common materials include:
- Steel or Aluminum: For structural integrity and durability.
- Plastic Composites: Used in components like doors or dispensers for lightweight and corrosion resistance.
- Electronics: Circuit boards and sensors for payment systems and inventory management.
Pre-treatment Processes: Materials undergo treatments such as cleaning, coating, or painting to ensure longevity and resistance to environmental factors. This step is crucial for machines that will be placed outdoors or in humid environments.
2. Forming
Cutting and Shaping: After material preparation, the next stage involves cutting and shaping the materials into parts. Techniques include:
- Laser Cutting: Provides precision in cutting metal sheets to specified dimensions.
- Injection Molding: Used for creating plastic components that require complex shapes.
- Bending and Forming: Metal sheets are bent into required shapes using press brakes.
Assembly of Subcomponents: Individual parts are assembled into subcomponents, such as the housing unit, door mechanisms, and internal compartments for holding the underwear.
3. Assembly
Main Assembly Line: The subcomponents move to the main assembly line where they are put together. This process typically involves:
- Welding or Riveting: For joining metal parts securely.
- Screw Fastening: Used for attaching panels and securing internal components.
- Electrical Wiring: Integrating the electronic components such as payment systems, sensors, and lighting.
Integration of Technology: Advanced vending machines may include IoT capabilities for remote monitoring and inventory management, which requires careful integration of software and hardware.
4. Finishing
Surface Treatment: Once assembled, the machine surfaces are treated to enhance aesthetics and durability. This may include:
- Powder Coating: For a uniform and durable finish.
- Painting: To achieve specific colors or branding.
Final Inspection and Testing: Before the machines are shipped, they undergo rigorous testing to ensure functionality. This includes:
- Electrical Testing: Ensuring all electronic components function correctly.
- Mechanical Testing: Checking the operation of moving parts.
Quality Assurance for Used Underwear Vending Machines
Quality assurance is paramount in the manufacturing of used underwear vending machines. It ensures that the machines are safe, reliable, and meet international standards, which is particularly crucial for B2B buyers in diverse markets such as Africa, South America, the Middle East, and Europe.
Relevant International Standards
ISO 9001: This standard outlines the requirements for a quality management system (QMS). Manufacturers that comply with ISO 9001 demonstrate their ability to consistently provide products that meet customer and regulatory requirements.
CE Marking: In Europe, the CE mark indicates conformity with health, safety, and environmental protection standards. It is essential for machines sold in the European market.
API Standards: For machines that may interact with hazardous materials or require specific safety measures, adherence to API (American Petroleum Institute) standards may be necessary.
Quality Control Checkpoints
- Incoming Quality Control (IQC): Materials are inspected upon arrival to ensure they meet specified standards before production begins.
- In-Process Quality Control (IPQC): Regular checks during manufacturing to monitor the quality of work in progress. This includes verifying dimensions, assembly processes, and functionality.
- Final Quality Control (FQC): Comprehensive testing of the finished product to ensure it meets all specifications and functions correctly.
Common Testing Methods
- Functional Testing: Verifying that all components work as intended, including the vending mechanism and electronic systems.
- Durability Testing: Assessing how the machine withstands various environmental conditions, such as humidity and temperature fluctuations.
- Safety Testing: Ensuring that machines comply with safety standards to prevent electrical hazards or mechanical failures.
Verifying Supplier Quality Control
B2B buyers must ensure that their suppliers maintain high-quality standards. Here are actionable strategies:
-
Supplier Audits: Conduct regular audits of your suppliers’ manufacturing processes and quality control systems. This helps verify compliance with international standards.
-
Request Quality Reports: Ask suppliers for documentation of their quality control processes, including test results and compliance certifications.
-
Third-party Inspections: Consider hiring independent third-party inspection agencies to evaluate the manufacturing facilities and quality control processes.
-
Certifications Verification: Verify that suppliers hold relevant certifications (e.g., ISO 9001, CE) by checking with the certifying bodies.
Navigating QC Nuances for International Buyers
International buyers must be aware of specific regulations and cultural expectations in their regions:
- Local Regulations: Understand the regulations governing vending machines in your target market, which may differ significantly between regions such as the UAE, UK, and South America.
- Cultural Sensitivities: In markets like Africa and the Middle East, cultural perceptions of used items may affect consumer acceptance. Ensure that machines are marketed appropriately and comply with local norms.
- Customization Needs: Be prepared to discuss specific customization requirements based on local consumer preferences, which can affect design and functionality.
By focusing on these manufacturing processes and quality assurance practices, B2B buyers can make informed decisions when sourcing used underwear vending machines, ensuring they invest in reliable and compliant products.
Related Video: Complete Process of Textile Manufacturing Fiber to Complete Garments
Comprehensive Cost and Pricing Analysis for used underwear vending machine Sourcing
When considering the sourcing of used underwear vending machines, understanding the comprehensive cost structure and pricing dynamics is crucial for international B2B buyers, particularly those from Africa, South America, the Middle East, and Europe. Below is a detailed analysis of the cost components, price influencers, and actionable tips for effective procurement.
Cost Components
-
Materials: The primary materials include the machine structure, vending mechanism, and electronic components. Sourcing high-quality materials can significantly impact the durability and efficiency of the vending machine. Buyers should consider suppliers that offer sustainable and reliable materials, as this can enhance the machine’s longevity.
-
Labor: Labor costs encompass the wages of workers involved in the manufacturing process. This can vary significantly based on the supplier’s location. For instance, labor costs in Southeast Asia may be lower compared to those in Europe, which could influence the overall pricing.
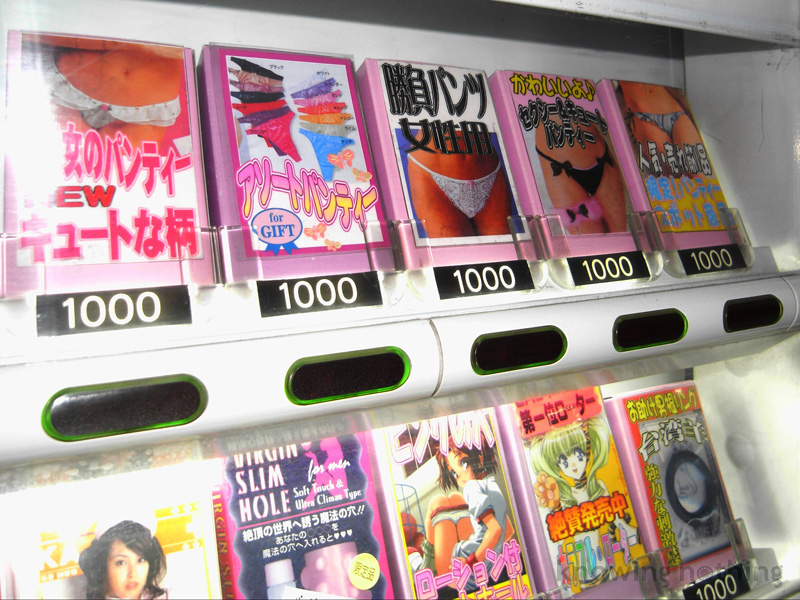
Illustrative Image (Source: Google Search)
-
Manufacturing Overhead: This includes indirect costs related to production, such as utilities, rent, and equipment maintenance. Understanding the overhead structure can provide insight into a supplier’s pricing strategy.
-
Tooling: Customization of machines may require specific tooling, which can add to initial costs. Buyers should inquire about tooling costs upfront, especially if they need specialized machines tailored to their markets.
-
Quality Control (QC): Implementing robust QC processes ensures that machines meet international standards. While this may raise costs, it is essential for maintaining quality and reducing the risk of defects, which can lead to additional expenses down the line.
-
Logistics: Shipping and handling costs can vary based on the machine’s size, weight, and the distance to the buyer’s location. Understanding the logistics involved is critical for budgeting accurately.
-
Margin: Suppliers typically include a profit margin in their pricing. This can vary based on market demand, competition, and the supplier’s business model.
Price Influencers
-
Volume/MOQ: Minimum order quantities (MOQ) can significantly affect pricing. Larger orders often lead to discounts, so buyers should assess their needs carefully to maximize cost efficiency.
-
Specifications/Customization: Custom features can increase costs. Buyers must balance the need for customization with budget constraints and assess whether standard models could suffice.
-
Materials: The choice of materials affects both the cost and quality of the machines. High-grade materials may come at a premium but can lead to lower maintenance costs in the long run.
-
Quality/Certifications: Machines that meet international safety and quality certifications may have higher upfront costs but can save money on compliance and potential recalls.
-
Supplier Factors: The reputation and reliability of suppliers play a crucial role in pricing. Established suppliers may charge more but offer better service and reliability.
-
Incoterms: Understanding Incoterms is vital for international transactions, as they define the responsibilities of buyers and sellers regarding shipping, insurance, and tariffs. This can impact the total cost of procurement.
Buyer Tips
-
Negotiation: Buyers should engage in negotiations to secure the best possible price, leveraging factors like order volume and payment terms.
-
Cost-Efficiency: Assess the Total Cost of Ownership (TCO) rather than just the purchase price. This includes maintenance, operational costs, and potential downtime.
-
Pricing Nuances: International buyers should be aware of currency fluctuations and local economic conditions that may affect pricing. Understanding the regional market dynamics can provide leverage during negotiations.
-
Supplier Relationships: Establishing strong relationships with suppliers can lead to better pricing, improved service, and priority access to new products.
-
Research and Due Diligence: Conduct thorough research on potential suppliers, including reviews, certifications, and past performance. This helps mitigate risks associated with international sourcing.
Disclaimer
Prices may vary based on market conditions and specific supplier agreements. It is advisable for buyers to obtain detailed quotes and ensure transparency regarding all cost components before finalizing any agreements.
Spotlight on Potential used underwear vending machine Manufacturers and Suppliers
This section offers a look at a few manufacturers active in the ‘used underwear vending machine’ market. This is a representative sample for illustrative purposes; B2B buyers must conduct their own extensive due diligence before any engagement. Information is synthesized from public sources and general industry knowledge.
Essential Technical Properties and Trade Terminology for used underwear vending machine
Key Technical Properties of Used Underwear Vending Machines
When considering the procurement of used underwear vending machines, several technical properties are essential for ensuring that the machines meet operational requirements and safety standards. Understanding these properties can significantly influence purchasing decisions.
-
Material Grade
– Definition: The quality and type of materials used in the construction of the vending machine, typically metal or high-grade plastics.
– B2B Importance: Higher material grades enhance durability and resistance to wear and tear, which is vital for machines located in high-traffic areas. For international buyers, material compliance with local regulations is crucial. -
Operating Temperature Range
– Definition: The range of temperatures within which the vending machine can function effectively, usually from -10°C to 50°C.
– B2B Importance: This property is particularly relevant in regions with extreme weather conditions. Ensuring the machine operates effectively in local climates can prevent operational failures and reduce maintenance costs. -
Power Supply Requirements
– Definition: The electrical specifications needed for the vending machine to function, often requiring a specific voltage and current.
– B2B Importance: Understanding power requirements helps buyers ensure compatibility with local electrical systems. This is crucial for preventing electrical issues and ensuring compliance with safety standards. -
Capacity
– Definition: The number of items the vending machine can store and dispense at any given time.
– B2B Importance: A higher capacity can lead to increased sales and reduced frequency of restocking. Buyers should assess their expected foot traffic and sales volume to select an appropriate capacity.
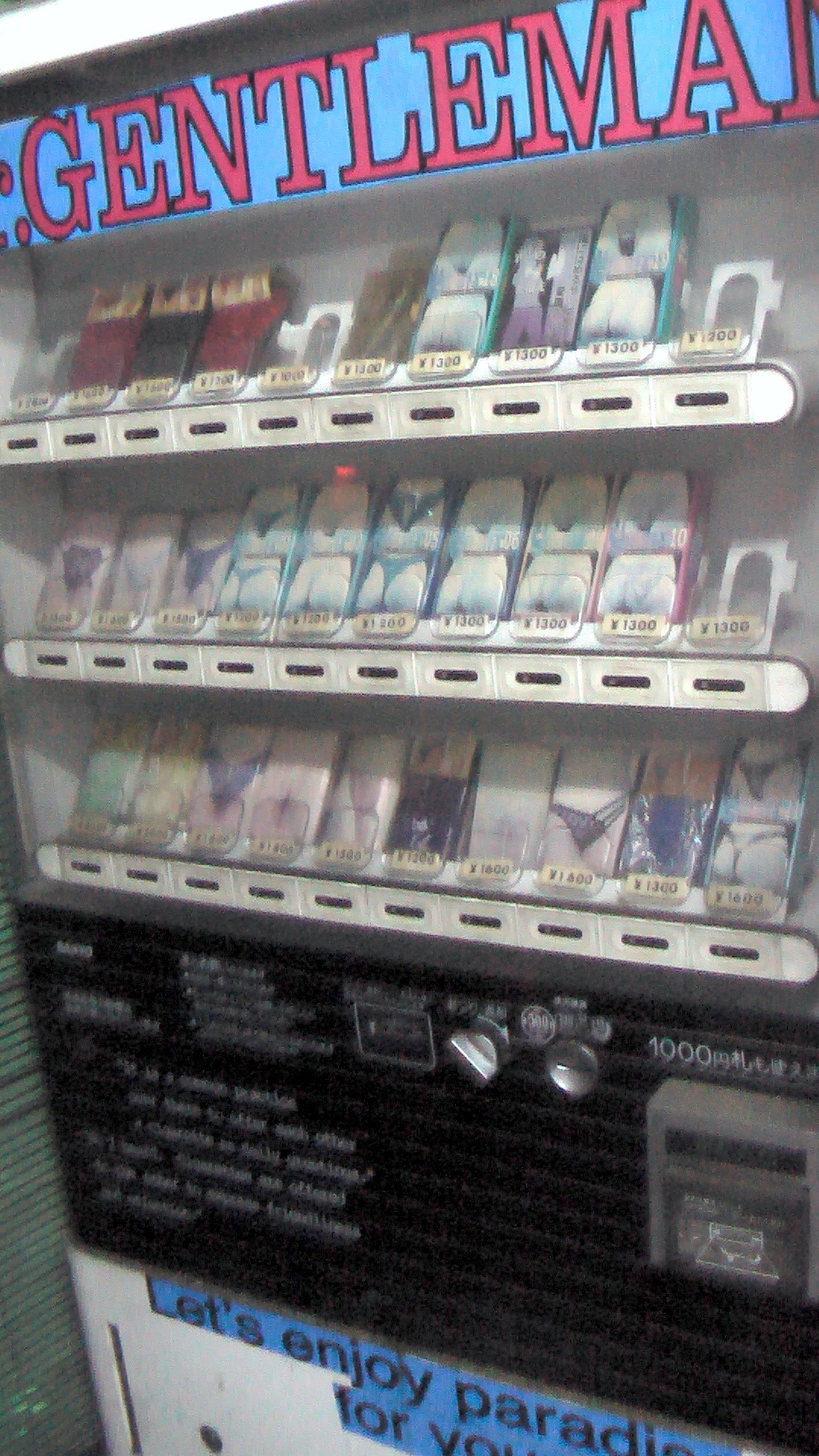
Illustrative Image (Source: Google Search)
- User Interface Specifications
– Definition: The design and functionality of the machine’s user interface, including payment methods (cash, card, mobile payment).
– B2B Importance: A user-friendly interface can enhance customer satisfaction and increase sales. Buyers must consider the payment preferences of their target market to ensure compatibility.
Common Trade Terms in the Used Underwear Vending Machine Industry
Understanding industry jargon is crucial for effective communication and negotiation in B2B transactions. Here are some key terms to know:
-
OEM (Original Equipment Manufacturer)
– Definition: A company that produces parts and equipment that may be marketed by another manufacturer.
– Relevance: Buyers should identify whether they are purchasing machines directly from the OEM or through a distributor, as this can affect warranty and service agreements. -
MOQ (Minimum Order Quantity)
– Definition: The smallest number of units a supplier is willing to sell.
– Relevance: Understanding MOQ is essential for budgeting and inventory management. Buyers should negotiate this term to align with their sales forecasts and storage capabilities. -
RFQ (Request for Quotation)
– Definition: A document sent to suppliers to request pricing and other terms for products or services.
– Relevance: Buyers should issue RFQs to multiple vendors to ensure competitive pricing and favorable terms. This can lead to cost savings and better supplier relationships. -
Incoterms (International Commercial Terms)
– Definition: A series of pre-defined commercial terms published by the International Chamber of Commerce (ICC) that are widely used in international commercial transactions.
– Relevance: Familiarity with Incoterms helps buyers understand shipping responsibilities, costs, and risks associated with the delivery of vending machines. This is crucial for ensuring compliance and minimizing disputes. -
Lead Time
– Definition: The time taken from placing an order to the delivery of goods.
– Relevance: Understanding lead times can help buyers plan their inventory and sales strategies. Longer lead times may require adjustments to stock levels to avoid shortages. -
Warranty Period
– Definition: The duration during which the manufacturer guarantees the performance of the vending machine.
– Relevance: A longer warranty period can indicate higher quality and reliability. Buyers should evaluate warranty terms as part of their overall risk management strategy.
By familiarizing themselves with these technical properties and trade terms, international B2B buyers can make informed decisions when sourcing used underwear vending machines, ensuring they meet both operational and market demands effectively.
Navigating Market Dynamics, Sourcing Trends, and Sustainability in the used underwear vending machine Sector
Market Overview & Key Trends
The used underwear vending machine sector is experiencing notable growth, driven by a combination of changing consumer behaviors, technological advancements, and a rising awareness of sustainability. Globally, the demand for unique vending experiences has surged, particularly in urban areas where convenience and novelty are highly valued. For international B2B buyers, especially those in Africa, South America, the Middle East, and Europe, understanding these market dynamics is crucial.
Emerging technologies such as mobile payment systems and smart vending solutions are reshaping how businesses operate within this sector. For instance, integrating contactless payment options can enhance user experience, making transactions faster and more secure. Additionally, the trend towards personalization—where machines can offer tailored selections based on user preferences—is gaining traction, supported by data analytics and machine learning.
In terms of sourcing trends, buyers are increasingly looking for suppliers that can provide innovative designs and efficient logistics. The rise of e-commerce platforms has made sourcing easier and more competitive, allowing businesses to access a broader range of suppliers from different regions. This trend is particularly beneficial for businesses in developing markets, where traditional supply chains may be less established.
Sustainability & Ethical Sourcing in B2B
Sustainability is becoming a cornerstone of the used underwear vending machine industry. As consumers become more environmentally conscious, there is a growing expectation for businesses to adopt sustainable practices. For B2B buyers, this means prioritizing suppliers who demonstrate a commitment to ethical sourcing and environmental responsibility.
The environmental impact of textile waste is significant, with millions of tons ending up in landfills each year. This has led to a greater emphasis on recycling and the use of sustainable materials in the production of used underwear. Certifications such as Global Organic Textile Standard (GOTS) and OEKO-TEX® can provide assurance that the products meet rigorous environmental and social standards.
Buyers should also consider the entire supply chain when evaluating sustainability efforts. This includes looking for suppliers who engage in fair labor practices, ensure safe working conditions, and minimize their carbon footprint. By choosing partners that align with these values, businesses can not only enhance their brand reputation but also meet the increasing demand for ethically sourced products.
Brief Evolution/History
The concept of vending machines has evolved significantly since their inception in the late 19th century. Originally designed to dispense simple items like snacks and drinks, the introduction of specialized vending machines, including those for used underwear, marks a unique niche within the industry. This evolution is largely fueled by changing consumer preferences and the desire for novelty in retail experiences.
In recent years, the used underwear vending machine has gained popularity in urban settings, particularly in countries where cultural attitudes towards personal hygiene and fashion are shifting. This evolution reflects broader trends in the retail landscape, where convenience, accessibility, and innovation are becoming key drivers of consumer engagement. For B2B buyers, understanding this history provides context for the current market dynamics and the potential for future growth in this unique sector.
Related Video: Global Trade & Logistics – What is Global Trade?
Frequently Asked Questions (FAQs) for B2B Buyers of used underwear vending machine
-
What should I consider when vetting suppliers for used underwear vending machines?
When vetting suppliers, focus on their reputation, experience, and compliance with international regulations. Request references and check their history in the industry. Assess their production capabilities and whether they can meet your specific needs, including customization options. Ensure that they have relevant certifications, such as ISO standards, to guarantee quality. Additionally, consider suppliers who have experience shipping to your region, as they will understand the logistics and regulatory requirements involved. -
Can I customize the vending machines to fit my branding needs?
Yes, many suppliers offer customization options for used underwear vending machines. This can include branding elements such as color schemes, logos, and design modifications. Discuss your specific requirements upfront to ensure the supplier can accommodate your needs. Additionally, inquire about the minimum order quantity (MOQ) for customized units, as this may vary between suppliers and could impact your initial investment. -
What are typical lead times for ordering used underwear vending machines?
Lead times can vary significantly based on the supplier’s location, order volume, and production capacity. Generally, expect anywhere from 4 to 12 weeks from order placement to delivery. Factors that can influence lead times include customization requests and shipping logistics. Always confirm lead times with your supplier before placing an order, and consider potential delays due to customs or regulatory checks in your region. -
What payment terms are common when sourcing vending machines internationally?
Payment terms can differ by supplier, but common practices include a deposit upfront (typically 30-50%) with the balance due before shipment. Some suppliers may offer letters of credit or escrow services to protect both parties. Ensure that you discuss payment methods accepted, including wire transfers and credit cards, and confirm any additional fees associated with international transactions. Understanding these terms upfront can help avoid disputes later on. -
How can I ensure quality assurance and certifications for the vending machines?
Request documentation that verifies the quality standards of the vending machines, such as ISO certifications or compliance with local regulations. A reputable supplier should be willing to provide test reports and quality control processes they follow. Additionally, consider arranging a factory visit or third-party inspection to assess the machines firsthand before shipment. This proactive approach helps mitigate risks associated with quality and compliance issues. -
What logistics considerations should I keep in mind for international shipping?
Logistics play a critical role in the procurement of used underwear vending machines. Ensure that your supplier has experience with international shipping and can provide details on shipping methods, costs, and estimated delivery times. Discuss customs clearance procedures and whether the supplier can assist with documentation. Additionally, consider insurance options for your shipment to protect against loss or damage during transit. -
What steps should I take if a dispute arises with my supplier?
In the event of a dispute, start by communicating directly with the supplier to resolve the issue amicably. Document all interactions and agreements for reference. If the dispute cannot be resolved, refer to the contract terms regarding dispute resolution, which may include mediation or arbitration. Consider involving a legal advisor if necessary, especially if the dispute involves significant financial implications or contractual obligations. -
Are there specific regulations I should be aware of when importing used underwear vending machines?
Yes, importing used vending machines may be subject to various regulations depending on your country. Familiarize yourself with local health and safety regulations, customs requirements, and any specific import restrictions regarding used goods. Consult with a customs broker or legal expert to ensure compliance with all importation laws. This due diligence will help avoid potential fines or delays upon arrival of your shipment.
Strategic Sourcing Conclusion and Outlook for used underwear vending machine
In conclusion, the strategic sourcing of used underwear vending machines presents a unique opportunity for international B2B buyers, particularly in Africa, South America, the Middle East, and Europe. This sector is not only innovative but also taps into growing consumer trends focused on sustainability and convenience. Buyers should prioritize suppliers who demonstrate a commitment to quality control, hygiene standards, and ethical sourcing practices, ensuring that their products meet local regulations and consumer expectations.
Key Takeaways:
– Market Demand: There is a rising demand for unconventional retail solutions, particularly in urban areas where convenience is paramount.
– Sustainability Focus: Aligning your sourcing strategy with sustainable practices can enhance brand reputation and attract eco-conscious consumers.
– Supplier Relationships: Building strong partnerships with reliable suppliers can lead to better pricing, improved product quality, and innovative vending solutions.
As the market for used underwear vending machines continues to evolve, forward-thinking B2B buyers are encouraged to leverage these insights and explore potential collaborations. By embracing this innovative retail model, businesses can tap into new revenue streams while meeting the demands of a changing consumer landscape. Engage with suppliers today to position your company at the forefront of this emerging market.