Your Ultimate Guide to Sourcing Used Soda Vending Machine
Guide to Used Soda Vending Machine For Sale
- Introduction: Navigating the Global Market for used soda vending machine for sale
- Understanding used soda vending machine for sale Types and Variations
- Key Industrial Applications of used soda vending machine for sale
- Strategic Material Selection Guide for used soda vending machine for sale
- In-depth Look: Manufacturing Processes and Quality Assurance for used soda vending machine for sale
- Comprehensive Cost and Pricing Analysis for used soda vending machine for sale Sourcing
- Spotlight on Potential used soda vending machine for sale Manufacturers and Suppliers
- Essential Technical Properties and Trade Terminology for used soda vending machine for sale
- Navigating Market Dynamics, Sourcing Trends, and Sustainability in the used soda vending machine for sale Sector
- Frequently Asked Questions (FAQs) for B2B Buyers of used soda vending machine for sale
- Strategic Sourcing Conclusion and Outlook for used soda vending machine for sale
Introduction: Navigating the Global Market for used soda vending machine for sale
In today’s competitive landscape, investing in used soda vending machines can be a game-changer for businesses across various sectors. These machines not only provide a steady revenue stream but also cater to the growing demand for convenient beverage options in locations ranging from offices and schools to shopping malls and public transport hubs. As international B2B buyers from regions such as Africa, South America, the Middle East, and Europe (including markets like Kenya and South Africa) seek cost-effective solutions, understanding the intricacies of sourcing these machines becomes essential.
This guide delves into the multifaceted world of used soda vending machines, offering insights into types, materials, manufacturing processes, quality control, and suppliers. Buyers will gain a comprehensive overview of the market landscape, including cost considerations and frequently asked questions that address common concerns and challenges. By equipping themselves with this knowledge, B2B buyers can make informed sourcing decisions that not only enhance operational efficiency but also align with their business goals.
Whether you are a retailer looking to expand your offerings or an entrepreneur venturing into the vending business, this guide serves as a crucial resource. It empowers you to navigate the global market with confidence, ensuring that your investment in used soda vending machines is both strategic and profitable.
Understanding used soda vending machine for sale Types and Variations
Type Name | Key Distinguishing Features | Primary B2B Applications | Brief Pros & Cons for Buyers |
---|---|---|---|
Standard Soda Vending Machine | Typically holds a variety of soda brands; user-friendly interface | Office buildings, schools, public areas | Pros: Versatile, widely available; Cons: May require frequent maintenance and restocking. |
Combo Vending Machine | Offers both snacks and beverages; larger capacity | Cafeterias, convenience stores | Pros: Space-efficient, caters to diverse consumer preferences; Cons: More complex mechanics may lead to higher repair costs. |
Can-Only Vending Machine | Exclusively dispenses canned beverages; compact design | Gyms, small offices | Pros: Lower initial cost, easy to maintain; Cons: Limited product selection may not attract all customers. |
Touchscreen Vending Machine | Interactive interface; customizable options | High-traffic locations, events | Pros: Engaging user experience; customizable branding; Cons: Higher upfront investment and potential tech issues. |
Outdoor Vending Machine | Weather-resistant design; larger storage capacity | Parks, outdoor events, festivals | Pros: Durable, designed for harsh conditions; Cons: May require additional security measures to prevent vandalism. |
Detailed Insights on Used Soda Vending Machines
Standard Soda Vending Machine
Standard soda vending machines are the most common type found in various locations such as offices, schools, and public areas. They typically feature a user-friendly interface and can hold a variety of soda brands. For B2B buyers, the key consideration is the machine’s reliability and maintenance requirements. Frequent restocking and maintenance can impact profitability, so it’s essential to evaluate the service agreements offered by sellers.
Combo Vending Machine
Combo vending machines provide an excellent solution for businesses looking to maximize product offerings. These machines can dispense both snacks and beverages, making them ideal for cafeterias and convenience stores. When considering a purchase, B2B buyers should assess the machine’s capacity and the variety of products they can offer. While they cater to diverse consumer preferences, the added complexity in mechanics can lead to higher repair costs.
Can-Only Vending Machine
These machines focus exclusively on canned beverages and are often chosen for their compact design, making them suitable for gyms and small office environments. B2B buyers benefit from a lower initial investment and easier maintenance. However, the limited selection may not attract all customers, which is a crucial consideration for businesses that want to ensure steady sales.
Touchscreen Vending Machine
Touchscreen vending machines offer an interactive user experience, allowing customers to customize their orders. They are particularly effective in high-traffic locations and events where engagement is key. For international B2B buyers, the customization options can enhance branding efforts. However, these machines come with a higher upfront investment and potential technical issues that may require specialized support.
Outdoor Vending Machine
Designed to withstand harsh weather conditions, outdoor vending machines are perfect for parks and outdoor events. Their larger storage capacity allows for extended product offerings. B2B buyers should consider the durability of the machine and any additional security measures that may be necessary to prevent vandalism. While they provide a robust solution for outdoor sales, the initial costs and ongoing maintenance can be higher than traditional machines.
Related Video: How a soda machine works – Dixie Narco vending machine
Key Industrial Applications of used soda vending machine for sale
Industry/Sector | Specific Application of used soda vending machine for sale | Value/Benefit for the Business | Key Sourcing Considerations for this Application |
---|---|---|---|
Education | Student Cafeterias | Provides quick access to beverages, enhancing student satisfaction | Condition of the machine, capacity, and payment options |
Corporate Offices | Break Rooms | Increases employee morale by offering refreshments | Energy efficiency, size, and maintenance history |
Healthcare | Patient Waiting Areas | Offers convenience to patients and visitors | Sanitation standards, ease of use, and reliability |
Hospitality | Hotels and Resorts | Enhances guest experience with 24/7 beverage access | Brand compatibility, aesthetics, and warranty options |
Retail | Shopping Malls and Supermarkets | Drives impulse purchases and increases foot traffic | Product selection, machine size, and operational costs |
Education Sector
Used soda vending machines are increasingly utilized in educational institutions, particularly in student cafeterias. They provide students with quick access to beverages, improving satisfaction and encouraging longer stays on campus. For international buyers, especially in regions like Africa and South America, it’s essential to consider the machine’s capacity and whether it can accommodate local beverage preferences. Additionally, understanding the payment options available, such as cash or mobile payments, can help streamline operations in diverse environments.
Corporate Offices
In corporate settings, used soda vending machines are often installed in break rooms to enhance employee morale and productivity. By offering a variety of beverages, companies can create a more enjoyable workplace atmosphere. When sourcing these machines, buyers should prioritize energy efficiency and reliability to minimize operational costs. Additionally, the machine’s size must fit within the available space while still meeting the beverage needs of employees, especially in busy offices across Europe and the Middle East.
Healthcare Sector
In healthcare facilities, used soda vending machines serve a crucial role in patient waiting areas. They provide convenience for patients and visitors who may spend extended periods at the facility. Buyers in this sector must focus on sanitation standards, ensuring that machines can be easily cleaned and maintained. Reliability is also paramount, as downtime could lead to patient dissatisfaction, particularly in fast-paced environments. Understanding local regulations regarding food and beverage services is vital for compliance.
Hospitality Industry
Hotels and resorts leverage used soda vending machines to enhance guest experiences by providing 24/7 access to beverages. This convenience can significantly improve guest satisfaction and encourage repeat visits. When purchasing these machines, buyers should consider brand compatibility to ensure that the machine aligns with the hotel’s image. Aesthetics and warranty options are also crucial, as they can affect both guest perception and long-term maintenance costs.
Retail Sector
In retail environments like shopping malls and supermarkets, used soda vending machines can drive impulse purchases and increase foot traffic. They act as an additional sales channel, especially in high-traffic areas. Buyers should evaluate product selection and the machine’s size to ensure it fits the retail space and meets customer demands. Additionally, understanding operational costs, including electricity usage and maintenance, is essential for maximizing profitability in competitive retail landscapes.
Related Video: Dixie Narco Bevmax 2 soda vending machine used refurbished for sale
Strategic Material Selection Guide for used soda vending machine for sale
When selecting materials for used soda vending machines, international B2B buyers must consider several factors that influence performance, durability, and compliance with regional standards. The following analysis covers common materials used in the construction of these machines, focusing on their properties, advantages, disadvantages, and specific considerations for buyers from Africa, South America, the Middle East, and Europe.
Stainless Steel
Key Properties:
Stainless steel is known for its excellent corrosion resistance, high strength, and ability to withstand high temperatures and pressures. It is often used in environments where hygiene is critical, making it suitable for food and beverage applications.
Pros & Cons:
The primary advantages of stainless steel include its durability and resistance to rust and staining, which prolongs the lifespan of vending machines. However, it is relatively expensive compared to other materials and may require specialized manufacturing processes.
Impact on Application:
Stainless steel is compatible with various beverages, including carbonated drinks, and does not impart any flavors or contaminants, ensuring product integrity.
Considerations for International Buyers:
Buyers should ensure compliance with local food safety regulations and standards such as ASTM A240 for stainless steel. In regions like Africa and the Middle East, sourcing stainless steel may involve navigating import tariffs and standards compliance.
Carbon Steel
Key Properties:
Carbon steel offers good mechanical properties and is often used in structural components of vending machines. It is strong and can handle significant loads, making it suitable for frames and supports.
Pros & Cons:
While carbon steel is cost-effective and readily available, it is prone to corrosion if not adequately coated or treated. This susceptibility can lead to increased maintenance costs over time.
Impact on Application:
Carbon steel is suitable for non-corrosive environments but may not be ideal for direct contact with beverages unless protected by coatings or linings.
Considerations for International Buyers:
Buyers should consider the local climate when using carbon steel, as high humidity or corrosive environments may necessitate additional protective measures. Compliance with standards like ASTM A36 is essential for structural integrity.
Plastic (Polyethylene/Polypropylene)
Key Properties:
Plastics such as polyethylene and polypropylene are lightweight, corrosion-resistant, and can be molded into complex shapes. They are often used for internal components and storage bins within vending machines.
Pros & Cons:
The main advantages of plastic are its low cost and ease of manufacturing. However, plastics may not withstand high temperatures and can degrade over time when exposed to UV light or certain chemicals.
Impact on Application:
These materials are suitable for storing non-carbonated beverages and snacks but may not be ideal for high-pressure environments or direct contact with carbonated drinks.
Considerations for International Buyers:
Buyers should verify that the plastics used comply with food safety standards, such as FDA regulations, especially in regions with stringent food safety laws. Additionally, understanding local recycling regulations can inform material selection.
Aluminum
Key Properties:
Aluminum is lightweight, corrosion-resistant, and has good thermal conductivity. It is often used in the construction of vending machine exteriors and components that require weight savings.
Pros & Cons:
Aluminum’s lightweight nature makes it easy to transport and install, while its resistance to corrosion enhances durability. However, it can be more expensive than carbon steel and may require additional coatings for optimal performance.
Impact on Application:
Aluminum is compatible with various beverages and can withstand the rigors of outdoor use, making it ideal for vending machines in diverse environments.
Considerations for International Buyers:
Buyers should ensure compliance with local standards for aluminum, such as ASTM B221. In regions like South America and Africa, understanding the availability and cost of aluminum can influence purchasing decisions.
Summary Table
Material | Typical Use Case for used soda vending machine for sale | Key Advantage | Key Disadvantage/Limitation | Relative Cost (Low/Med/High) |
---|---|---|---|---|
Stainless Steel | Structural components, exterior panels | Excellent corrosion resistance | Higher cost, requires specialized mfg | High |
Carbon Steel | Frames, supports | Cost-effective, good strength | Susceptible to corrosion | Low |
Plastic (Polyethylene/PP) | Internal components, storage bins | Lightweight, low cost | Limited temperature resistance | Low |
Aluminum | Exterior panels, lightweight components | Lightweight, corrosion-resistant | More expensive than carbon steel | Medium |
This strategic material selection guide provides essential insights for international B2B buyers considering used soda vending machines. By evaluating the properties and implications of each material, buyers can make informed decisions that align with their operational needs and local compliance requirements.
In-depth Look: Manufacturing Processes and Quality Assurance for used soda vending machine for sale
The manufacturing process and quality assurance (QA) for used soda vending machines are crucial for ensuring that these machines meet international standards and provide reliable service. Understanding these processes can empower B2B buyers, particularly from regions like Africa, South America, the Middle East, and Europe, to make informed purchasing decisions. Below is an in-depth look at the typical manufacturing processes and quality assurance measures involved.
Manufacturing Processes
Material Preparation
The first step in the manufacturing of used soda vending machines involves the careful selection and preparation of materials. Common materials include:
- Steel: Used for the chassis and structural components, ensuring durability.
- Plastic: For the vending door and internal components, chosen for its lightweight and corrosion-resistant properties.
- Electronic Components: These include payment systems, sensors, and microcontrollers that manage the machine’s operations.
The materials undergo rigorous inspection to ensure they meet the necessary specifications before proceeding to the next stage.
Forming
In the forming stage, raw materials are shaped into the necessary components through various techniques:
- Cutting: Steel sheets are cut to size using laser cutting or plasma cutting technologies.
- Bending: The cut sheets are bent into shape using hydraulic presses.
- Molding: Plastic components are produced using injection molding techniques, which allow for complex shapes and designs.
This stage ensures that all parts fit together correctly and are structurally sound.
Assembly
During assembly, the formed components are put together to create the vending machine. This includes:
- Mechanical Assembly: Components like the chassis, vending door, and internal shelving are assembled.
- Electrical Assembly: Wiring and installation of electronic components are performed. This includes setting up the payment systems and ensuring all sensors are properly connected.
- Integration: All components are integrated to ensure they function cohesively.
Proper assembly techniques are vital to minimize future maintenance issues and ensure longevity.
Finishing
The finishing stage involves several processes aimed at enhancing the machine’s appearance and durability:
- Painting: The exterior is painted with weather-resistant coatings to protect against corrosion and wear.
- Quality Checks: Each machine undergoes a series of inspections to ensure all components are functioning correctly and meet aesthetic standards.
Finishing not only improves the machine’s visual appeal but also its durability, which is critical for outdoor installations.
Quality Assurance
Quality assurance is a fundamental part of the manufacturing process for used soda vending machines. It ensures that products meet both customer expectations and regulatory requirements.
International Standards
Many manufacturers adhere to international standards such as:
- ISO 9001: This standard outlines the criteria for a quality management system, ensuring consistent quality in products and services.
- CE Marking: Required in the European Union, this certification indicates conformity with health, safety, and environmental protection standards.
- API Standards: These are specific to the beverage and food service industries, ensuring that machines are safe and reliable for consumer use.
Adhering to these standards not only enhances product credibility but also facilitates smoother international trade.
Quality Control Checkpoints
The quality control process typically includes several key checkpoints:
- Incoming Quality Control (IQC): Materials and components are inspected upon arrival to ensure they meet predefined specifications.
- In-Process Quality Control (IPQC): This involves monitoring the manufacturing process at various stages to catch any defects early on.
- Final Quality Control (FQC): The finished machines undergo a thorough inspection to ensure they meet all operational and safety standards before shipping.
These checkpoints help to maintain high-quality standards throughout the manufacturing process.
Common Testing Methods
Manufacturers employ several testing methods to verify the functionality and safety of vending machines:
- Functional Testing: Ensures all mechanical and electronic components work correctly.
- Durability Testing: Simulates long-term use to identify potential points of failure.
- Safety Testing: Checks for electrical safety and compliance with international safety standards.
These tests are essential for ensuring that the machines will perform reliably in various environments.
Verification of Supplier Quality Control
For B2B buyers, especially those sourcing internationally, verifying a supplier’s quality control processes is critical. Here are some actionable steps:
- Supplier Audits: Conduct on-site audits to evaluate manufacturing capabilities and quality control measures.
- Request Quality Reports: Ask for documentation of quality control processes, including results from IQC, IPQC, and FQC stages.
- Third-Party Inspections: Engage third-party inspection agencies to assess the quality of machines before shipment.
These steps can help mitigate risks associated with purchasing used vending machines, ensuring that they meet required standards.
QC and Certification Nuances for International Buyers
When sourcing used soda vending machines, international buyers should be aware of specific nuances:
- Regional Regulations: Different regions may have unique safety and quality regulations. For instance, machines sold in the EU must meet CE marking requirements, while those in the Middle East may require specific certifications.
- Understanding Certification Marks: Familiarize yourself with various certification marks (e.g., UL, NSF) relevant to your market to ensure compliance.
- Cultural Considerations: Be aware that quality perceptions can vary across regions. Engage with local partners to understand market expectations.
By taking these factors into account, B2B buyers can navigate the complexities of international purchasing more effectively.
Conclusion
Understanding the manufacturing processes and quality assurance measures for used soda vending machines is essential for international B2B buyers. By focusing on material preparation, forming, assembly, and finishing, along with robust quality control practices, buyers can ensure they procure reliable, high-quality machines that meet their operational needs. Engaging in thorough supplier verification processes will further enhance confidence in purchasing decisions, particularly in diverse markets across Africa, South America, the Middle East, and Europe.
Related Video: How Coca-Cola Is Made In Factory | Coca-Cola Factory Process
Comprehensive Cost and Pricing Analysis for used soda vending machine for sale Sourcing
In the market for used soda vending machines, understanding the cost structure and pricing dynamics is crucial for international B2B buyers. This analysis will break down the cost components involved in sourcing these machines, explore the factors influencing pricing, and provide actionable tips for negotiating effectively.
Cost Components
-
Materials: The primary material costs include the machine’s body, components like dispensers and refrigeration units, and any necessary electrical parts. The quality of materials can significantly affect the durability and maintenance needs of the machine.
-
Labor: Labor costs encompass assembly, repairs, and refurbishing efforts. Depending on the region where the machine is sourced, labor costs can vary widely. For instance, sourcing from countries with lower labor costs may lead to significant savings.
-
Manufacturing Overhead: This includes the indirect costs associated with production, such as facility maintenance, utilities, and administrative expenses. Efficient manufacturing processes can reduce overhead, impacting the final price.
-
Tooling: Tooling costs relate to the equipment and technology used to manufacture and refurbish the vending machines. Advanced tooling can enhance production efficiency but may increase initial costs.
-
Quality Control (QC): Implementing rigorous QC processes ensures the machines meet safety and operational standards, which can add to the overall cost but is essential for maintaining quality.
-
Logistics: Transportation costs to ship the vending machines to the buyer’s location can vary based on distance and shipping method. It’s crucial to consider both the cost and delivery time.
-
Margin: Suppliers will typically add a profit margin to cover their costs and risks. This margin can fluctuate based on market demand and competition.
Price Influencers
-
Volume/MOQ: The minimum order quantity (MOQ) can significantly influence pricing. Larger orders often result in lower per-unit costs due to economies of scale.
-
Specifications/Customization: Custom features or specific configurations may increase the cost. Buyers should evaluate the necessity of customizations against budget constraints.
-
Materials Quality/Certifications: Machines made from higher-quality materials or those that meet specific certifications (e.g., safety standards) may command higher prices.
-
Supplier Factors: The reputation and reliability of suppliers can affect pricing. Established suppliers may charge more due to their proven track record, while newer entrants might offer lower prices to gain market share.
-
Incoterms: The terms of sale (e.g., FOB, CIF) can impact total costs. Buyers should understand these terms to factor in shipping and insurance costs effectively.
Buyer Tips
-
Negotiation: Leverage the volume of your order to negotiate better prices. Suppliers may be willing to offer discounts for larger purchases.
-
Cost-Efficiency: Always calculate the Total Cost of Ownership (TCO), which includes purchase price, maintenance, and operational costs. A lower upfront cost may lead to higher long-term expenses.
-
Pricing Nuances: Be aware of regional pricing trends and currency fluctuations, especially when sourcing from different continents. This knowledge can enhance your negotiation strategy.
-
Quality Assessment: Request samples or inspect the machines before finalizing a purchase to ensure they meet your quality standards.
-
Market Research: Conduct thorough market research to compare prices across different suppliers and regions. This can help you identify the best deals and avoid overpaying.
Disclaimer
Prices for used soda vending machines can vary widely based on the factors mentioned above. Always seek multiple quotes and verify details before making a purchasing decision.
Spotlight on Potential used soda vending machine for sale Manufacturers and Suppliers
This section offers a look at a few manufacturers active in the ‘used soda vending machine for sale’ market. This is a representative sample for illustrative purposes; B2B buyers must conduct their own extensive due diligence before any engagement. Information is synthesized from public sources and general industry knowledge.
Essential Technical Properties and Trade Terminology for used soda vending machine for sale
When considering the purchase of a used soda vending machine, understanding its technical properties and relevant trade terminology is crucial for making informed B2B decisions. Here, we outline essential specifications and commonly used terms that will aid buyers in navigating the market effectively.
Key Technical Properties of Used Soda Vending Machines
-
Material Grade
– This refers to the quality of materials used in the construction of the vending machine. Common materials include stainless steel and high-grade plastics. Importance: High-quality materials enhance durability and resistance to corrosion, which is critical for machines placed in outdoor or high-traffic environments. -
Capacity
– This specification indicates the number of beverage cans or bottles the machine can hold, typically ranging from 300 to 700 units. Importance: Understanding capacity is vital for aligning the machine’s supply with expected demand, ensuring that it meets the needs of your customer base without frequent restocking. -
Power Consumption
– This measures the electrical energy the machine uses, usually expressed in watts. Importance: Knowing the power consumption is essential for evaluating operational costs and ensuring that the machine is compatible with local electrical standards, which can vary significantly across regions. -
Temperature Range
– This specifies the operational temperature for cooling beverages, typically between 32°F to 50°F (0°C to 10°C). Importance: A suitable temperature range ensures that drinks are served at optimal freshness, which can influence customer satisfaction and sales volume. -
Payment Systems
– Modern vending machines may accept cash, credit/debit cards, or mobile payments. Importance: Understanding the payment options available is crucial for targeting specific consumer demographics and ensuring that the machine can operate in various markets. -
Size and Weight
– The dimensions and weight of the machine can affect placement and transportation logistics. Importance: Knowing the size and weight helps buyers determine if the machine fits in the intended location and ensures that appropriate handling equipment is available for installation.
Common Trade Terminology
-
OEM (Original Equipment Manufacturer)
– Refers to companies that manufacture products that are sold under another company’s brand. Context: Understanding whether a vending machine is an OEM product can inform you about its reliability and support options. -
MOQ (Minimum Order Quantity)
– This term indicates the smallest quantity of goods a supplier is willing to sell. Context: For B2B buyers, knowing the MOQ is vital for budgeting and inventory management, especially when procuring multiple units. -
RFQ (Request for Quotation)
– A formal process where buyers request pricing and terms from suppliers. Context: Submitting an RFQ can help buyers compare offers and negotiate better terms, ensuring they get the best deal. -
Incoterms (International Commercial Terms)
– These are a set of predefined international rules that clarify the responsibilities of buyers and sellers in international transactions. Context: Familiarity with Incoterms helps buyers understand shipping responsibilities, insurance, and risk management.
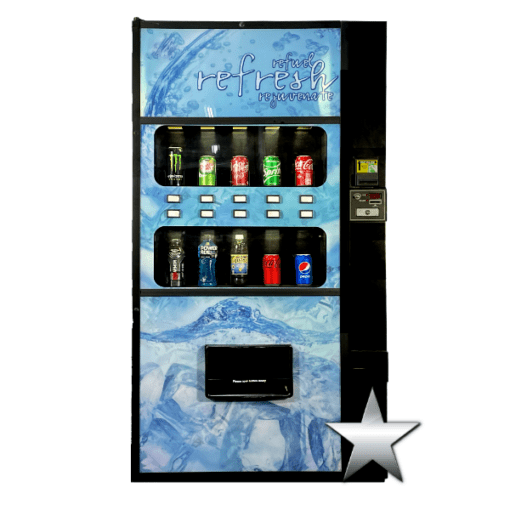
Illustrative Image (Source: Google Search)
-
Lead Time
– The amount of time it takes from placing an order to receiving it. Context: Knowing the lead time is essential for planning inventory and ensuring that the vending machines are available when needed. -
Warranty Period
– This specifies the duration for which the manufacturer or seller offers repairs or replacements for defects. Context: A clear understanding of warranty terms can provide peace of mind and protect your investment in case of equipment failure.
By grasping these technical properties and trade terminologies, international B2B buyers can enhance their purchasing strategies, ensuring they select the right used soda vending machines that meet their operational requirements and market demands.
Navigating Market Dynamics, Sourcing Trends, and Sustainability in the used soda vending machine for sale Sector
Market Overview & Key Trends
The global used soda vending machine market is experiencing a significant transformation driven by several factors. Increasing demand for convenience, coupled with a growing trend towards automated retail solutions, is reshaping how consumers access beverages. In regions such as Africa and South America, rising urbanization and a burgeoning middle class are propelling the need for accessible vending solutions. Furthermore, technological advancements, particularly in cashless payment systems and IoT integration, are enhancing the functionality and appeal of vending machines, making them more attractive to B2B buyers.
Emerging sourcing trends indicate a shift towards purchasing refurbished machines rather than new units, driven by cost-effectiveness and sustainability concerns. Buyers are increasingly favoring suppliers that offer comprehensive after-sales support, including maintenance and technical assistance, which is crucial for the longevity of these machines. Additionally, the emphasis on data analytics is growing, with operators seeking machines that can provide insights on consumer behavior and inventory management, thereby optimizing operations and maximizing profitability.
For international B2B buyers, particularly from regions like the Middle East and Europe, understanding the competitive landscape is essential. Key players are not only competing on price but also on technology and service offerings, which can significantly influence purchasing decisions. As such, buyers should consider partnerships with suppliers who demonstrate innovation and a commitment to customer service to secure a competitive edge.
Sustainability & Ethical Sourcing in B2B
Sustainability is becoming a pivotal concern in the used soda vending machine sector. The environmental impact of manufacturing new machines is prompting buyers to consider refurbished options as a viable alternative. These machines often have a lower carbon footprint, as they involve less resource-intensive production processes.
Moreover, ethical sourcing is gaining traction among B2B buyers. Companies are increasingly aware of the importance of maintaining transparent supply chains that prioritize fair labor practices and environmental stewardship. Buyers are encouraged to seek out suppliers who hold certifications such as ISO 14001, which indicates a commitment to effective environmental management systems.
In addition, incorporating ‘green’ materials into vending machines—such as energy-efficient components and recyclable materials—can further enhance a company’s sustainability profile. By prioritizing these aspects, international buyers not only contribute to environmental preservation but also align with consumer preferences for responsible brands, potentially increasing their market share.
Brief Evolution/History
The used soda vending machine sector has evolved significantly over the past few decades. Initially viewed as a simple solution for beverage distribution, these machines have transformed into sophisticated retail platforms. The introduction of digital payment systems in the late 1990s marked a pivotal shift, allowing consumers to purchase items conveniently.
As technology advanced, so did the capabilities of vending machines, incorporating features such as touchscreens and real-time inventory tracking. This evolution has made used soda vending machines an attractive option for B2B buyers looking to enhance their operational efficiency while meeting the changing demands of consumers. Today, the focus on sustainability and ethical practices is shaping the future trajectory of this market, pushing suppliers and buyers alike to adapt to new expectations and standards.
Related Video: Incoterms for beginners | Global Trade Explained
Frequently Asked Questions (FAQs) for B2B Buyers of used soda vending machine for sale
-
What should I consider when vetting suppliers for used soda vending machines?
When vetting suppliers, prioritize their reputation, experience, and customer reviews. Check for certifications or memberships in relevant trade organizations. Establish direct communication to evaluate their responsiveness and willingness to share references. Additionally, request a detailed company profile, including financial stability, to ensure they can meet your demands consistently. Consider visiting their facilities if feasible, or arrange for a virtual tour to assess their operations. -
Can I customize the used soda vending machines to fit my branding?
Yes, many suppliers offer customization options for used soda vending machines. You can typically request branding elements such as colors, logos, and specific product selections tailored to your market preferences. Before finalizing a purchase, confirm the customization capabilities with the supplier and any additional costs that may be involved. Early discussions about your branding needs can help avoid misunderstandings later in the process. -
What are the typical minimum order quantities (MOQ) and lead times for these machines?
MOQs for used soda vending machines can vary significantly by supplier, often ranging from one unit to several dozen. Lead times generally depend on the supplier’s stock availability and customization requirements, typically taking 4 to 12 weeks. To avoid disruptions, discuss these factors upfront and plan your procurement strategy accordingly, especially if you anticipate demand fluctuations in your market. -
What payment options are available when purchasing used soda vending machines?
Payment methods vary by supplier and may include bank transfers, letters of credit, and online payment platforms. It’s essential to negotiate terms that protect your interests, such as partial upfront payments and milestone payments tied to delivery stages. Always verify the supplier’s payment terms and conditions to ensure they align with your financial processes and risk management strategies. -
How can I ensure the quality of the used soda vending machines I purchase?
Request a comprehensive quality assurance (QA) report or certification from the supplier to ensure that the machines meet industry standards. Additionally, inquire about the machine’s maintenance history and any refurbishments made prior to sale. If possible, arrange for a third-party inspection before finalizing the purchase to verify the machine’s condition and functionality. -
What logistics considerations should I keep in mind for shipping these machines?
Logistics for shipping used soda vending machines can involve several factors, including freight costs, customs duties, and delivery timelines. Ensure that the supplier provides detailed shipping terms, including packaging methods to prevent damage during transit. Consider working with a logistics partner experienced in international shipping to navigate customs regulations and ensure timely delivery. -
What should I do if there are disputes or issues with my order?
Establish a clear process for resolving disputes with your supplier before completing the transaction. This includes defining acceptable quality standards, delivery timelines, and return policies in your purchase agreement. If issues arise, maintain open communication with the supplier to discuss resolutions. If necessary, consider mediation or legal assistance based on the terms of your contract to protect your interests. -
Are there any certifications or standards I should look for in used soda vending machines?
When sourcing used soda vending machines, look for certifications such as CE, UL, or ISO to ensure compliance with safety and quality standards relevant to your region. These certifications indicate that the machines meet specific manufacturing and operational guidelines. Request documentation from suppliers that confirm these certifications to ensure you are making a safe and compliant investment.

Illustrative Image (Source: Google Search)
Strategic Sourcing Conclusion and Outlook for used soda vending machine for sale
In the dynamic landscape of B2B commerce, strategic sourcing for used soda vending machines represents a vital opportunity for international buyers, particularly in regions like Africa, South America, the Middle East, and Europe. By leveraging a strategic approach, buyers can optimize their procurement processes, ensuring cost-effectiveness while securing quality machines that meet their operational needs.
Key takeaways include the importance of conducting thorough market research, understanding local regulations, and fostering relationships with reliable suppliers. This not only mitigates risks associated with procurement but also enhances the potential for long-term partnerships that can drive business growth.
Looking ahead, as the demand for vending solutions continues to rise, international buyers are encouraged to act decisively. Investing in used soda vending machines not only offers a sustainable choice but also aligns with evolving consumer preferences for convenience and accessibility. Embrace this opportunity to enhance your offerings, expand market reach, and stay competitive in an increasingly interconnected global market. Your strategic sourcing decisions today will pave the way for success tomorrow.