Your Ultimate Guide to Sourcing Used Snack Vending Machine
Guide to Used Snack Vending Machine
- Introduction: Navigating the Global Market for used snack vending machine
- Understanding used snack vending machine Types and Variations
- Key Industrial Applications of used snack vending machine
- Strategic Material Selection Guide for used snack vending machine
- In-depth Look: Manufacturing Processes and Quality Assurance for used snack vending machine
- Comprehensive Cost and Pricing Analysis for used snack vending machine Sourcing
- Spotlight on Potential used snack vending machine Manufacturers and Suppliers
- Essential Technical Properties and Trade Terminology for used snack vending machine
- Navigating Market Dynamics, Sourcing Trends, and Sustainability in the used snack vending machine Sector
- Frequently Asked Questions (FAQs) for B2B Buyers of used snack vending machine
- Strategic Sourcing Conclusion and Outlook for used snack vending machine
Introduction: Navigating the Global Market for used snack vending machine
As the demand for convenient and accessible food options continues to rise globally, the market for used snack vending machines has become a lucrative opportunity for B2B buyers. These machines not only cater to the growing consumer preference for on-the-go snacks but also offer businesses an efficient solution to enhance their service offerings without the substantial capital investment required for new units. For international buyers, particularly from regions like Africa, South America, the Middle East, and Europe, understanding the intricacies of sourcing used snack vending machines can lead to significant cost savings and improved operational efficiency.
This comprehensive guide serves as a vital resource for navigating the used snack vending machine market. It covers essential aspects such as types of machines, materials used, manufacturing and quality control processes, reliable suppliers, and cost considerations. Additionally, the guide addresses prevalent market trends and answers frequently asked questions, empowering buyers to make informed decisions.
By leveraging this information, international B2B buyers can confidently evaluate their options, ensuring they select machines that align with their business needs and market demands. Whether you are a distributor in Kenya or a retailer in Spain, this guide is designed to equip you with the insights necessary for successful sourcing in the dynamic landscape of used snack vending machines.
Understanding used snack vending machine Types and Variations
Type Name | Key Distinguishing Features | Primary B2B Applications | Brief Pros & Cons for Buyers |
---|---|---|---|
Traditional Snack Vending Machine | Mechanical design, coin-operated, simple interface | Offices, schools, public spaces | Pros: Low maintenance, cost-effective. Cons: Limited payment options; lower product variety. |
Smart Vending Machine | Digital interface, cashless payment options, inventory tracking | Retail environments, transportation hubs | Pros: Enhanced user experience, real-time inventory data. Cons: Higher initial investment, requires internet connectivity. |
Healthy Snack Vending Machine | Focus on nutritious snacks, often refrigerated | Gyms, health facilities, schools | Pros: Appeals to health-conscious consumers, promotes healthy eating. Cons: Potentially higher costs for products and maintenance. |
Combination Vending Machine | Offers both snacks and beverages, multi-selection options | Airports, malls, event venues | Pros: Versatile product offerings, maximizes sales potential. Cons: More complex maintenance and higher upfront costs. |
Customized Vending Machine | Tailored design and product selection based on location needs | Corporate offices, specialized events | Pros: Meets specific customer demands, improves customer satisfaction. Cons: Longer lead times for production and potentially higher costs. |
Traditional Snack Vending Machine
Traditional snack vending machines are the most common type, characterized by their mechanical design and coin-operated functionality. These machines typically offer a limited selection of snacks, such as chips, candy bars, and soft drinks. They are widely used in offices, schools, and public spaces due to their low maintenance requirements and cost-effectiveness. However, buyers should consider the limited payment options and lower product variety, which may not cater to modern consumer preferences for healthier choices or cashless transactions.
Smart Vending Machine
Smart vending machines incorporate advanced technology, featuring digital interfaces and cashless payment options like credit cards and mobile payments. They often include inventory tracking systems that provide real-time data on product availability. These machines are suitable for retail environments and transportation hubs, where convenience is paramount. While they offer an enhanced user experience and can attract tech-savvy customers, the higher initial investment and dependency on internet connectivity may deter some buyers.
Healthy Snack Vending Machine
These machines focus on providing nutritious snack options, often including refrigerated items such as yogurt, fruit, and protein bars. They are particularly popular in gyms, health facilities, and schools, where there is a demand for healthier eating options. B2B buyers should consider that while these machines appeal to health-conscious consumers and promote wellness, they may come with higher costs for both products and maintenance due to the need for refrigeration and specialized inventory.
Combination Vending Machine
Combination vending machines offer a diverse selection of both snacks and beverages, making them suitable for high-traffic areas like airports, malls, and event venues. Their versatility allows businesses to maximize sales potential by catering to a wider audience. However, the complexity of maintaining a combination machine and the higher upfront costs can be challenging for some buyers, who need to assess the demand in their specific locations carefully.
Customized Vending Machine
Customized vending machines are designed to meet specific customer needs, allowing businesses to tailor product selections and machine designs based on location and consumer preferences. This type of machine is particularly beneficial for corporate offices and specialized events, where unique offerings can enhance customer satisfaction. While they offer significant advantages in terms of meeting specific demands, buyers must be prepared for longer lead times for production and potentially higher costs associated with customization.
Related Video: Automatic Products Snack Vending Machine @Multigenerational Center – Henderson, NV USA
Key Industrial Applications of used snack vending machine
Industry/Sector | Specific Application of used snack vending machine | Value/Benefit for the Business | Key Sourcing Considerations for this Application |
---|---|---|---|
Education | On-campus snack provisions | Increases student satisfaction and retention rates | Compatibility with local payment systems, energy efficiency |
Healthcare | Staff and visitor refreshments | Enhances convenience, improves staff morale | Hygiene standards, machine reliability, product variety |
Corporate Offices | Breakroom snack supply | Boosts employee productivity and morale | Size and capacity, payment options, maintenance support |
Transportation Hubs | Waiting area snack options | Provides quick access to snacks, improves customer experience | Durability, ease of restocking, payment technology |
Retail Environments | In-store impulse purchases | Drives additional revenue through convenience | Location analytics, product mix, customization options |
Education
In educational institutions, used snack vending machines are deployed to provide convenient snack options for students on campus. This application addresses the need for quick and accessible nourishment during busy academic schedules, thereby enhancing student satisfaction and retention rates. International buyers, particularly from Africa and South America, should consider local preferences for snack types and ensure that the machines are compatible with local payment systems, such as mobile payments or contactless cards.
Healthcare
In healthcare settings, used snack vending machines serve both staff and visitors, offering refreshments that enhance convenience and improve the overall experience. This application is particularly valuable in hospitals and clinics where time is of the essence, and access to food options can be limited. Buyers in the Middle East and Europe must prioritize hygiene standards, ensure the machines are reliable, and offer a diverse product range to cater to different dietary needs.
Corporate Offices
Corporate environments benefit from used snack vending machines by providing employees with easy access to snacks in break rooms. This application not only boosts productivity but also improves employee morale by offering a convenient way to recharge during work hours. Buyers from Europe and Africa should focus on the machine’s size and capacity to accommodate high foot traffic, as well as the availability of various payment options to suit a diverse workforce.
Transportation Hubs
Used snack vending machines are effectively utilized in transportation hubs, such as airports and bus stations, where they provide quick snack options for travelers. This application enhances customer experience by reducing wait times and catering to the needs of people on the go. For international buyers, particularly from Africa and South America, durability and ease of restocking are critical considerations, as machines must withstand high usage and varying environmental conditions.
Retail Environments
In retail settings, used snack vending machines can drive impulse purchases by offering convenient snack options near checkout lines or in high-traffic areas. This application is particularly effective in generating additional revenue and enhancing customer satisfaction. Buyers should consider location analytics to optimize machine placement, the product mix to attract diverse consumers, and customization options that align with local tastes and preferences.
Related Video: Vending.com – Snack and Drink Vending Machine Sales
Strategic Material Selection Guide for used snack vending machine
When selecting materials for used snack vending machines, it is essential to consider the properties, advantages, disadvantages, and specific regional compliance requirements. Below, we analyze four common materials used in the construction of these machines, focusing on their implications for international B2B buyers, particularly in Africa, South America, the Middle East, and Europe.
1. Stainless Steel
Key Properties:
Stainless steel is known for its excellent corrosion resistance, high tensile strength, and ability to withstand high temperatures. It is non-reactive, making it ideal for food applications.
Pros & Cons:
The durability of stainless steel is unmatched, providing a long service life with minimal maintenance. However, it is more expensive than other materials, which can impact overall project costs. The manufacturing complexity can also be higher due to the need for specialized equipment for cutting and welding.
Impact on Application:
Stainless steel is compatible with a wide range of food items, ensuring that there is no contamination. Its robustness allows it to withstand the rigors of frequent use in public spaces.
Considerations for International Buyers:
Compliance with food safety standards is crucial, particularly in regions with strict regulations. Buyers should ensure that the stainless steel used meets standards such as ASTM A240 or EN 10088.
2. Mild Steel
Key Properties:
Mild steel offers good strength and ductility but lacks corrosion resistance unless coated.
Pros & Cons:
It is cost-effective and easy to manufacture, making it a popular choice for budget-conscious projects. However, its susceptibility to rust and corrosion can lead to increased maintenance costs and a shorter lifespan if not properly treated.
Impact on Application:
Mild steel can be used for structural components of vending machines but is less suitable for areas in direct contact with food unless adequately protected.
Considerations for International Buyers:
Buyers should consider coating options like powder coating to enhance corrosion resistance. Compliance with local standards, such as ISO or ASTM, should also be verified.
3. Polycarbonate
Key Properties:
Polycarbonate is a lightweight, impact-resistant plastic known for its transparency and UV resistance.
Pros & Cons:
Its lightweight nature makes it easy to handle and install, while its clarity allows for visibility of products inside the vending machine. However, polycarbonate can be more susceptible to scratching and may not withstand high temperatures as effectively as metals.
Impact on Application:
This material is ideal for transparent panels and protective covers, allowing customers to see the available snacks. It is not suitable for structural components due to its lower strength compared to metals.
Considerations for International Buyers:
Buyers should ensure that polycarbonate materials comply with relevant safety and food contact regulations, such as FDA standards in the U.S. or EU regulations in Europe.
4. Aluminum
Key Properties:
Aluminum is lightweight, corrosion-resistant, and has good thermal conductivity.
Pros & Cons:
Aluminum’s resistance to corrosion makes it suitable for outdoor vending machines. It is also relatively easy to fabricate. However, its lower strength compared to stainless steel may limit its use in structural applications.
Impact on Application:
Aluminum is often used for frames and panels in vending machines, providing a good balance of weight and strength. It is suitable for various environmental conditions.
Considerations for International Buyers:
When sourcing aluminum, buyers should check for compliance with standards such as ASTM B221 or EN 573. Additionally, regional preferences for recycled materials may influence purchasing decisions.
Summary Table
Material | Typical Use Case for used snack vending machine | Key Advantage | Key Disadvantage/Limitation | Relative Cost (Low/Med/High) |
---|---|---|---|---|
Stainless Steel | Structural components, food contact surfaces | Excellent corrosion resistance, durability | Higher cost, complex manufacturing | High |
Mild Steel | Structural elements, frames | Cost-effective, easy to fabricate | Susceptible to corrosion, requires coating | Low |
Polycarbonate | Transparent panels, protective covers | Lightweight, impact-resistant | Susceptible to scratching, lower heat resistance | Medium |
Aluminum | Frames, panels | Lightweight, corrosion-resistant | Lower strength compared to stainless steel | Medium |
This strategic material selection guide aims to equip international B2B buyers with the necessary insights to make informed decisions when sourcing materials for used snack vending machines, ensuring compliance with local standards and suitability for their specific applications.
In-depth Look: Manufacturing Processes and Quality Assurance for used snack vending machine
Manufacturing Processes for Used Snack Vending Machines
The manufacturing process for used snack vending machines involves several critical stages that ensure both the functionality and reliability of the machines. Understanding these stages is essential for B2B buyers who are looking to procure high-quality equipment.
Material Preparation
The first stage in manufacturing involves the careful selection and preparation of materials. Key materials include:
- Metal Panels: Typically steel or aluminum, chosen for their durability and ability to withstand wear and tear.
- Plastic Components: Used for the machine’s front panel and internal mechanisms, ensuring lightweight and ease of use.
- Electrical Components: This includes wiring, motors, and control boards, which are crucial for the machine’s operation.
Materials undergo rigorous quality checks to confirm they meet specific standards before moving to the next stage.
Forming
In this phase, materials are shaped into the necessary components of the vending machine. Techniques used include:
- Cutting: Metals and plastics are cut to size using CNC machines for precision.
- Bending and Stamping: Metal panels are bent and stamped to create the desired shapes and features of the machine.
- Injection Molding: Plastic parts are often produced through injection molding, allowing for complex designs and high-volume production.
These techniques help in achieving the desired aesthetics and functionality while maintaining structural integrity.
Assembly
Once individual components are formed, they are assembled into the final product. The assembly process typically involves:
- Mechanical Assembly: Components such as the product dispensing mechanism, coin acceptor, and control panel are assembled.
- Electrical Wiring: This step includes connecting all electrical parts to ensure proper functionality.
- Testing During Assembly: As components are assembled, preliminary tests are conducted to catch any issues early.
Ensuring each part is correctly installed is critical for the machine’s operational reliability.
Finishing
The final stage involves finishing touches that enhance the machine’s appearance and durability:
- Surface Treatment: Components may be painted, coated, or treated to prevent corrosion and wear.
- Quality Control: Each machine undergoes a final inspection to ensure it meets quality standards before packaging and shipping.
This stage is vital for enhancing the longevity and appeal of the vending machines.
Quality Assurance in Manufacturing
Quality assurance (QA) is paramount in the manufacturing of used snack vending machines, ensuring that every unit meets international standards and customer expectations.
Relevant International Standards
For B2B buyers, understanding the standards relevant to vending machine manufacturing is crucial:
- ISO 9001: This standard focuses on quality management systems, ensuring a consistent quality of products and services.
- CE Marking: Indicates conformity with health, safety, and environmental protection standards for products sold within the European Economic Area.
- API Standards: While primarily focused on the oil and gas industry, similar principles of operational excellence can apply to vending machine manufacturers.
Compliance with these standards assures buyers of the machine’s reliability and safety.
Quality Control Checkpoints
The quality control process in manufacturing typically involves several checkpoints:
- Incoming Quality Control (IQC): Raw materials are inspected upon arrival to ensure they meet specified requirements.
- In-Process Quality Control (IPQC): Regular checks during the manufacturing process to ensure that each step meets quality standards.
- Final Quality Control (FQC): A comprehensive inspection of the completed machines to verify that all specifications are met before shipping.
These checkpoints help identify issues at various stages, reducing the risk of defects in the final product.
Common Testing Methods
B2B buyers should be aware of the common testing methods employed during the QA process, which include:
- Functional Testing: Verifying that all machine functions operate correctly, including the dispensing mechanism and payment systems.
- Durability Testing: Simulating long-term use to ensure the machine can withstand daily wear and tear.
- Safety Testing: Ensuring compliance with safety regulations to protect users from electrical and mechanical hazards.
These tests are essential for assuring product quality and reliability.
Verifying Supplier Quality Control
For international B2B buyers, particularly in regions like Africa, South America, the Middle East, and Europe, verifying a supplier’s quality control processes is critical. Here are several actionable steps:
- Conduct Audits: Regular audits of suppliers can help verify adherence to quality standards and identify areas for improvement.
- Request Quality Reports: Suppliers should provide detailed quality reports that outline their QA processes, testing methods, and compliance with standards.
- Third-Party Inspections: Engaging third-party inspection agencies can provide an unbiased assessment of the manufacturing and quality control processes.
These actions can help build trust in supplier capabilities and ensure that the products meet the required standards.
Conclusion
In conclusion, understanding the manufacturing processes and quality assurance protocols for used snack vending machines is crucial for B2B buyers. By focusing on material preparation, forming, assembly, and finishing, alongside rigorous quality control measures, buyers can make informed decisions that align with their operational needs and quality expectations. Engaging with suppliers who adhere to international standards and demonstrating robust QA practices will ultimately lead to successful procurement outcomes.
Related Video: Parle-G Biscuits Manufacturing process – Food Factory Tour- Modern Food factory, Mega Factory II
Comprehensive Cost and Pricing Analysis for used snack vending machine Sourcing
Cost Structure of Used Snack Vending Machines
When sourcing used snack vending machines, understanding the cost structure is crucial for international B2B buyers. The total cost can be broken down into several key components:
-
Materials: This includes the cost of the machine itself, any necessary replacement parts, and consumables like electronic components. The condition of the machine significantly impacts this cost; machines in better condition generally command higher prices.
-
Labor: Costs associated with the disassembly, inspection, and refurbishment of the machines. Skilled labor may be required for repairs or upgrades, which can vary by region.
-
Manufacturing Overhead: This encompasses the indirect costs associated with the production of the machines, such as utilities, rent, and administrative expenses. Buyers should inquire about the manufacturing processes used by suppliers to gauge overhead costs.
-
Tooling: If customization is needed, the costs for tools and equipment to modify the machines should be factored in. Customization can significantly increase the initial investment.
-
Quality Control (QC): Ensuring the machine meets certain operational standards involves inspection and testing, which can add to the overall cost. Certificates of compliance may also be required for some markets.
-
Logistics: Shipping and handling costs must be considered, especially for international buyers. This includes freight charges, import duties, and local transportation costs.
-
Margin: Suppliers typically add a profit margin to their costs. Understanding the typical margins in the industry can help buyers negotiate better prices.
Price Influencers
Several factors can influence the pricing of used snack vending machines:
-
Volume/MOQ: Bulk purchases often lead to lower per-unit costs. Negotiating minimum order quantities (MOQ) can yield significant savings.
-
Specifications/Customization: Machines tailored to specific needs or featuring advanced technology may incur higher costs. Be clear about your requirements to avoid unnecessary expenditures.
-
Materials: The quality and type of materials used in the machine (e.g., metal vs. plastic) can affect pricing. Machines made from durable materials may be more expensive but offer better longevity.
-
Quality/Certifications: Machines that meet international standards or possess certifications (like CE or ISO) may have higher prices due to the assurance of quality and safety they provide.
-
Supplier Factors: Established suppliers with a proven track record may charge more due to their reliability and service quality. Newer or less experienced suppliers might offer lower prices but could pose risks regarding quality and support.
-
Incoterms: Understanding the international shipping terms (e.g., FOB, CIF) is essential, as these will affect the total landed cost of the machines. Buyers should clarify responsibilities and costs associated with shipping and customs.
Buyer Tips
To navigate the complexities of sourcing used snack vending machines, consider the following actionable insights:
-
Negotiation: Always negotiate prices and terms. Suppliers may have flexibility, particularly for bulk orders or long-term partnerships.
-
Cost-Efficiency: Evaluate the total cost of ownership (TCO), which includes purchase price, maintenance, and operational costs. A lower initial price may result in higher long-term expenses if the machine requires frequent repairs.
-
Pricing Nuances: International buyers should be aware of currency fluctuations and how they can impact pricing. Additionally, consider potential tariffs and duties that could affect the overall budget.
-
Local Market Insight: Familiarize yourself with local market conditions in regions like Africa, South America, the Middle East, and Europe. Understanding regional demand and competition can provide leverage in negotiations.
Disclaimer
Prices for used snack vending machines can vary widely based on condition, specifications, and regional factors. The information provided serves as a guideline; actual prices may differ based on market conditions and supplier negotiations. Always conduct thorough due diligence before making purchasing decisions.
Spotlight on Potential used snack vending machine Manufacturers and Suppliers
This section offers a look at a few manufacturers active in the ‘used snack vending machine’ market. This is a representative sample for illustrative purposes; B2B buyers must conduct their own extensive due diligence before any engagement. Information is synthesized from public sources and general industry knowledge.
Essential Technical Properties and Trade Terminology for used snack vending machine
Key Technical Properties of Used Snack Vending Machines
When purchasing used snack vending machines, understanding their technical specifications is crucial for ensuring compatibility, reliability, and performance in your business environment. Here are some essential properties to consider:
-
Material Grade
– The material grade of a vending machine typically refers to the quality of metals and plastics used in its construction. High-grade stainless steel is often preferred for durability and corrosion resistance. This is important for international buyers who need machines that can withstand varying climates, especially in humid or coastal regions. -
Power Requirements
– Used snack vending machines may have specific voltage and amperage requirements. Understanding these specifications helps in determining compatibility with local power sources. This is particularly relevant for buyers in regions like Africa and South America, where power supply standards may vary widely. -
Capacity
– Capacity refers to the number of snack items a vending machine can hold. This is critical for businesses looking to meet consumer demand efficiently. A larger capacity may be more beneficial in high-traffic areas, while smaller machines could suffice in low-traffic settings. -
Temperature Control
– Some vending machines are equipped with refrigeration systems to keep snacks fresh. The effectiveness of this system, including temperature range and energy efficiency, is essential for maintaining product quality. B2B buyers should verify the refrigeration capabilities, especially in warmer climates. -
User Interface
– The user interface includes the display and payment options available on the machine. A modern interface can enhance customer experience and increase sales. Look for machines with touch screens or mobile payment capabilities, as these are becoming standard in many markets. -
Maintenance Requirements
– Understanding the maintenance needs of a used vending machine can save costs in the long run. Machines that are easy to service, with readily available parts, are preferred to minimize downtime. Buyers should inquire about the history of maintenance and any repairs that may have been done.
Common Trade Terminology
Familiarizing yourself with key trade terms is equally important when navigating the purchase of used snack vending machines:
-
OEM (Original Equipment Manufacturer)
– This term refers to companies that produce parts or equipment that may be marketed by another manufacturer. For buyers, understanding whether the vending machine is an OEM product can indicate quality and reliability. -
MOQ (Minimum Order Quantity)
– MOQ is the smallest number of units that a supplier is willing to sell. Buyers should consider this when planning their purchases, as it can affect inventory levels and cash flow, especially for smaller businesses. -
RFQ (Request for Quotation)
– An RFQ is a document used to solicit price bids from suppliers. It’s essential for buyers to submit a detailed RFQ to ensure they receive accurate pricing and terms that reflect their specific needs. -
Incoterms
– Short for International Commercial Terms, these are predefined commercial terms that dictate the responsibilities of buyers and sellers in international transactions. Understanding Incoterms is vital for clarifying shipping costs, insurance, and risk transfer. -
Lead Time
– This term refers to the amount of time it takes from placing an order until the goods are delivered. Knowing the lead time is crucial for planning inventory and ensuring that vending machines are available when needed. -
Warranty
– A warranty is a guarantee provided by the seller regarding the condition of the machine and the timeframe for which repairs or replacements will be covered. Buyers should assess warranty terms carefully to protect their investment.
By understanding these technical properties and trade terms, international B2B buyers can make informed decisions when sourcing used snack vending machines, ensuring they meet operational needs and market demands effectively.
Navigating Market Dynamics, Sourcing Trends, and Sustainability in the used snack vending machine Sector
Market Overview & Key Trends
The used snack vending machine sector is witnessing a transformative phase, driven by several global factors that are reshaping the market landscape. Key drivers include the increasing demand for convenience in food purchasing, particularly in urban areas across Africa, South America, the Middle East, and Europe. Rapid urbanization, coupled with a growing middle class, has led to a surge in the adoption of vending machines in workplaces, schools, and public spaces. Furthermore, the COVID-19 pandemic has accelerated the shift towards contactless transactions, pushing B2B buyers to seek vending solutions that integrate cashless payment systems and touchless interfaces.
Emerging technologies are also influencing sourcing trends within this sector. The integration of IoT (Internet of Things) technologies is allowing vending machine operators to remotely monitor inventory levels, optimize stock replenishment schedules, and enhance machine performance. Additionally, the rise of data analytics is enabling businesses to better understand consumer behavior, leading to more strategic product placements and personalized offerings. International B2B buyers should pay close attention to these technological advancements, as they can significantly enhance operational efficiency and profitability.
Market dynamics are characterized by a competitive landscape where suppliers from various regions are vying for market share. Buyers in Africa, South America, the Middle East, and Europe should consider not only the cost-effectiveness of used vending machines but also the reliability and service support provided by vendors. Establishing partnerships with local suppliers who understand regional consumer preferences and regulatory frameworks can be a strategic advantage.
Sustainability & Ethical Sourcing in B2B
Sustainability is increasingly becoming a focal point for businesses involved in the used snack vending machine sector. The environmental impact of manufacturing new machines and the increasing pressure to reduce waste are prompting companies to adopt more sustainable practices. For B2B buyers, sourcing used vending machines can significantly lower carbon footprints, as it promotes recycling and reduces the demand for new materials.
Moreover, the importance of ethical supply chains cannot be overstated. Buyers should prioritize vendors who adhere to ethical sourcing practices, ensuring that the machines are refurbished responsibly and that labor conditions in the supply chain meet international standards. Certifications such as ISO 14001 for environmental management and Fair Trade can serve as indicators of a supplier’s commitment to sustainability and ethical practices.
In terms of materials, opting for machines made from recycled or sustainably sourced components can further enhance a company’s green credentials. Additionally, implementing energy-efficient technologies in vending machines not only reduces operational costs but also aligns with global sustainability goals.
Brief Evolution/History
The evolution of snack vending machines can be traced back to the early 20th century, initially serving simple snacks in public spaces. Over the decades, technological advancements have transformed these machines into sophisticated retail solutions capable of offering a wide variety of products, including fresh food and beverages. The rise of digital payment systems and smart technology has further enhanced their functionality, making them an attractive option for businesses looking to diversify their sales channels.
As the global focus shifts toward sustainability, the used vending machine sector is poised for significant growth, driven by the dual needs of convenience and environmental responsibility. International B2B buyers can leverage this evolution to find innovative solutions that meet both consumer demands and sustainability goals.
Related Video: Is global trade transforming? | Counting the Cost
Frequently Asked Questions (FAQs) for B2B Buyers of used snack vending machine
-
What should I consider when vetting suppliers for used snack vending machines?
When vetting suppliers, prioritize their experience in the vending machine industry and check for customer reviews or testimonials. Verify their operational history, warranty policies, and after-sales support. It’s also crucial to assess their compliance with local regulations and industry standards, especially for the countries you are sourcing from, such as Kenya or Brazil. Engaging with suppliers who have a proven track record in international trade can mitigate risks associated with quality and service. -
Can I customize the vending machines to fit my brand?
Yes, many suppliers offer customization options for used snack vending machines, including branding, color schemes, and product configurations. It’s advisable to discuss your specific requirements upfront to understand what modifications are possible. Be sure to inquire about any additional costs associated with customization and the expected lead times for these modifications to ensure alignment with your business goals. -
What are the typical minimum order quantities (MOQs) and lead times for used vending machines?
MOQs can vary significantly based on the supplier and the condition of the machines. Generally, suppliers may require orders of at least 5-10 units for bulk purchases. Lead times can also differ; expect anywhere from 2 to 8 weeks depending on the supplier’s inventory and your customization requests. Always confirm these details before placing an order to avoid unexpected delays. -
What payment methods are commonly accepted for international transactions?
Most suppliers accept various payment methods, including bank transfers, letters of credit, and escrow services. It’s essential to choose a payment method that offers security and minimizes risk. Additionally, clarify the payment terms, such as deposits required and final payment schedules, to ensure a smooth transaction process. If sourcing from regions like Africa or South America, consider currency exchange rates and transaction fees.
-
How can I ensure the quality of used snack vending machines?
Request detailed quality assurance (QA) documentation, including inspection reports and certifications from the supplier. It may also be beneficial to request a sample machine for evaluation before committing to a larger order. Additionally, inquire about the supplier’s refurbishment process to understand how they maintain the quality of their machines. Establishing clear expectations for quality standards will help protect your investment. -
What certifications should I look for in used vending machines?
Look for machines that comply with international safety and quality standards, such as CE, UL, or ISO certifications. These certifications indicate that the machines have met specific safety and performance criteria. If you are importing into Europe or the Middle East, ensure that the machines comply with regional regulations, as this can affect customs clearance and operational safety. -
What logistics options are available for shipping used vending machines?
Logistics for shipping used vending machines can include sea freight, air freight, or road transport, depending on your budget and urgency. Discuss shipping terms with your supplier, including incoterms (like FOB or CIF) that define who is responsible for shipping costs and risks. Also, consider working with a logistics partner experienced in handling bulky items to ensure proper handling and timely delivery. -
How should I handle disputes with suppliers regarding used vending machines?
To handle disputes effectively, maintain clear and documented communication with your supplier throughout the transaction. Establish a written agreement outlining the terms of sale, including warranties and return policies. In the event of a dispute, try to resolve issues amicably through negotiation. If necessary, consider mediation or arbitration services, especially for international transactions, to avoid costly legal battles.
Strategic Sourcing Conclusion and Outlook for used snack vending machine
In the evolving landscape of vending solutions, the strategic sourcing of used snack vending machines presents significant opportunities for international B2B buyers. By leveraging the cost-effectiveness of pre-owned equipment, businesses can enhance their service offerings while minimizing capital expenditure. Key takeaways include the importance of thorough supplier vetting, understanding regional market demands, and ensuring compliance with local regulations, particularly in diverse markets such as Africa, South America, the Middle East, and Europe.
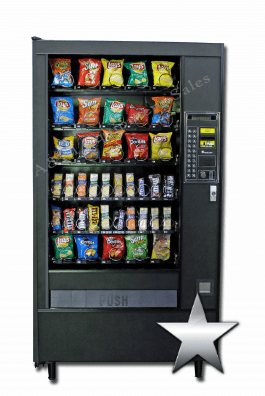
Illustrative Image (Source: Google Search)
Value Proposition: Investing in used vending machines not only supports sustainability by reducing waste but also allows companies to quickly adapt to changing consumer preferences. By focusing on strategic sourcing, buyers can secure high-quality machines that align with their operational goals.
As we look to the future, the demand for convenient food solutions will continue to grow, particularly in urban areas. Buyers are encouraged to explore partnerships with reliable suppliers who can provide not just machines, but also support in terms of maintenance and product selection. Act now to capitalize on this opportunity and position your business at the forefront of the vending market.