Your Ultimate Guide to Sourcing Ulta Vending Machine
Guide to Ulta Vending Machine Locations
- Introduction: Navigating the Global Market for ulta vending machine locations
- Understanding ulta vending machine locations Types and Variations
- Key Industrial Applications of ulta vending machine locations
- Strategic Material Selection Guide for ulta vending machine locations
- In-depth Look: Manufacturing Processes and Quality Assurance for ulta vending machine locations
- Comprehensive Cost and Pricing Analysis for ulta vending machine locations Sourcing
- Spotlight on Potential ulta vending machine locations Manufacturers and Suppliers
- Essential Technical Properties and Trade Terminology for ulta vending machine locations
- Navigating Market Dynamics, Sourcing Trends, and Sustainability in the ulta vending machine locations Sector
- Frequently Asked Questions (FAQs) for B2B Buyers of ulta vending machine locations
- Strategic Sourcing Conclusion and Outlook for ulta vending machine locations
Introduction: Navigating the Global Market for ulta vending machine locations
In today’s competitive marketplace, the strategic placement of Ulta vending machine locations plays a pivotal role in maximizing product visibility and consumer access. These automated retail solutions offer an innovative way to cater to the growing demand for convenience, especially in urban areas and high-traffic venues. For international B2B buyers, particularly those from Africa, South America, the Middle East, and Europe, understanding the nuances of these locations can significantly enhance sourcing decisions and operational efficiency.
This comprehensive guide delves into the critical aspects of Ulta vending machine locations, covering various types, materials, manufacturing processes, and quality control standards. By examining potential suppliers and associated costs, this resource empowers businesses to make informed choices that align with their operational needs and market dynamics. Moreover, it addresses frequently asked questions, providing clarity on common concerns that may arise during the procurement process.
Navigating the complexities of the global market requires not only insight into product specifications but also an understanding of regional preferences and logistical considerations. This guide aims to equip B2B buyers with the knowledge necessary to leverage Ulta vending machines as effective retail solutions, ensuring that they remain competitive and responsive to consumer trends. Whether you are based in bustling cities or emerging markets, this resource will serve as an invaluable tool in optimizing your vending machine strategy and enhancing your business’s bottom line.
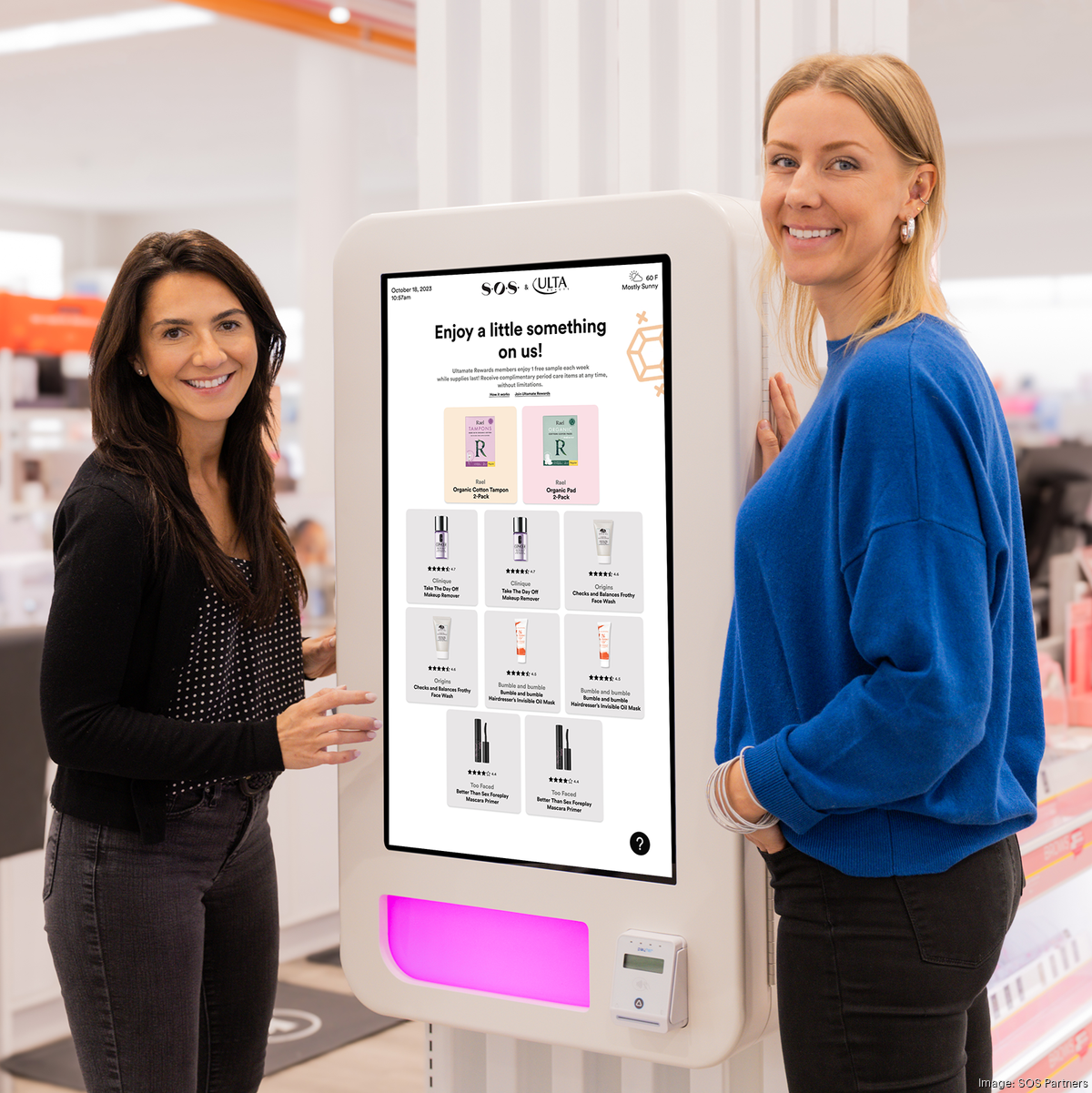
Illustrative Image (Source: Google Search)
Understanding ulta vending machine locations Types and Variations
Type Name | Key Distinguishing Features | Primary B2B Applications | Brief Pros & Cons for Buyers |
---|---|---|---|
Retail Store Vending Units | Located within or near retail stores, offering beauty products | Retail partnerships, beauty supply chains | Pros: High foot traffic, brand exposure. Cons: Limited space for product variety. |
Mobile Vending Machines | Transportable units that can be placed at events or festivals | Trade shows, festivals, pop-up events | Pros: Flexibility in location, ability to reach diverse audiences. Cons: Requires logistics for transport and setup. |
Automated Kiosks | High-tech machines with touch screens and payment options | Airports, malls, high-traffic areas | Pros: 24/7 operation, advanced user interface. Cons: Higher initial investment and maintenance costs. |
Standalone Vending Stations | Independent units located in public spaces like parks or schools | Community engagement, brand activation | Pros: Accessibility to a wide audience, low operational costs. Cons: Vulnerability to vandalism or theft. |
Subscription-Based Vending | Machines that offer subscription services for regular customers | Loyalty programs, customer retention | Pros: Predictable revenue stream, fosters customer loyalty. Cons: Requires robust inventory management and customer service. |
Retail Store Vending Units
Retail store vending units are strategically placed within or near beauty retail outlets, providing customers with quick access to beauty products. These units often feature popular brands and seasonal items, capitalizing on high foot traffic. For B2B buyers, partnering with retail chains can enhance brand visibility and drive sales. However, space limitations may restrict the variety of products offered, necessitating careful selection of merchandise to maximize appeal.
Mobile Vending Machines
Mobile vending machines are versatile units designed for events such as trade shows, festivals, and pop-up shops. Their portability allows businesses to reach diverse audiences and adapt to various market conditions. B2B buyers should consider the logistics involved in transporting and setting up these machines, as well as the potential for increased brand engagement at high-profile events. While they provide flexibility, operational efficiency is crucial to ensure profitability.
Automated Kiosks
Automated kiosks represent a high-tech option for vending, often equipped with touch screens and advanced payment systems. These machines are typically found in airports, shopping malls, and other high-traffic locations, offering a 24/7 service model. For B2B buyers, investing in automated kiosks can enhance customer experience through convenience and efficiency. However, the initial investment and ongoing maintenance can be significant, requiring a solid business case to justify the costs.
Standalone Vending Stations
Standalone vending stations are independent units located in public areas like parks, schools, and community centers. These machines aim to engage the community and provide easy access to beauty products. For B2B buyers, these stations can be a cost-effective way to reach potential customers without the overhead of a physical store. However, they may be susceptible to vandalism and theft, which could impact overall profitability and operational reliability.
Subscription-Based Vending
Subscription-based vending machines offer a unique approach by providing regular customers with a curated selection of beauty products through a subscription model. This strategy can enhance customer loyalty and create a predictable revenue stream. B2B buyers should consider the importance of inventory management and customer service to ensure a seamless experience for subscribers. While this model fosters loyalty, it also requires a commitment to maintaining product quality and customer satisfaction.
Related Video: Machine Learning in 2024 – Beginner’s Course
Key Industrial Applications of ulta vending machine locations
Industry/Sector | Specific Application of ulta vending machine locations | Value/Benefit for the Business | Key Sourcing Considerations for this Application |
---|---|---|---|
Retail | Automated beauty product sales | Increased sales volume and customer convenience | Product variety, machine placement, and payment options |
Hospitality | On-demand personal care products for guests | Enhanced guest experience and satisfaction | Inventory management, branding, and machine aesthetics |
Corporate Offices | Employee wellness and grooming supplies | Boosted employee morale and productivity | Product selection, machine accessibility, and maintenance |
Education | Student access to beauty and personal care items | Improved student satisfaction and convenience | Location analysis, pricing strategies, and product mix |
Events & Festivals | Temporary beauty product sales in high-traffic areas | Maximized revenue opportunities during peak times | Logistics planning, machine capacity, and product relevance |
In the retail sector, ulta vending machine locations serve as automated sales points for beauty products, allowing customers to purchase items conveniently without needing staff assistance. This application not only increases sales volume but also enhances the shopping experience, especially in high-traffic areas. For international B2B buyers, factors such as product variety, optimal machine placement, and diverse payment options are crucial for maximizing effectiveness.
Within the hospitality industry, these vending machines can be strategically placed in hotels and resorts to offer on-demand personal care products, such as skincare or cosmetics. This approach not only enriches the guest experience but also provides an additional revenue stream for the establishment. Buyers in this sector should consider inventory management systems, branding opportunities, and the aesthetic appeal of machines to align with their brand identity.
In corporate offices, ulta vending machines can be utilized to provide employees with easy access to grooming and wellness products. This application can significantly boost employee morale and productivity by addressing personal care needs in the workplace. B2B buyers should focus on product selection that resonates with their workforce, ensuring the machines are easily accessible and are regularly maintained to provide a consistent supply.
In the education sector, universities and colleges can install ulta vending machines to cater to students’ needs for beauty and personal care items. This initiative enhances student satisfaction by providing convenient access to products between classes or during late-night study sessions. Buyers must analyze location effectiveness, implement competitive pricing strategies, and curate a product mix that appeals to the student demographic.
Finally, during events and festivals, ulta vending machines can capitalize on the influx of attendees by offering beauty products in high-traffic areas. This temporary application maximizes revenue opportunities and caters to the spontaneous purchasing behavior of event-goers. Key considerations for B2B buyers include effective logistics planning, ensuring machines can handle peak capacity, and selecting products that are relevant to the event’s theme or audience.
Related Video: Kooler Ice Vending Machines – IM600XL vs. IM1000
Strategic Material Selection Guide for ulta vending machine locations
When selecting materials for ulta vending machine locations, it is essential to consider various factors that influence performance, durability, and compliance with international standards. Below is an analysis of four common materials used in the construction of vending machines, focusing on their properties, advantages, disadvantages, and specific considerations for international B2B buyers.
Stainless Steel
Key Properties: Stainless steel is known for its excellent corrosion resistance, high strength, and ability to withstand extreme temperatures. It typically has a temperature rating up to 800°F (427°C) and is resistant to oxidation.
Pros & Cons: The durability of stainless steel makes it ideal for high-traffic areas, as it can withstand impacts and abrasions. However, it is more expensive than other materials, which can increase the overall cost of the vending machine. Manufacturing complexity can also be higher due to the need for specialized welding techniques.
Impact on Application: Stainless steel is compatible with a wide range of media, including beverages and snacks, making it suitable for diverse vending machine applications. Its hygienic properties are particularly important in food service environments.
Considerations for International Buyers: Buyers must ensure compliance with food safety standards and regulations in their respective regions. For instance, in Europe, materials must meet EU food contact regulations. Buyers should also consider the availability of stainless steel grades that comply with ASTM or DIN standards.
Aluminum
Key Properties: Aluminum is lightweight, corrosion-resistant, and has a good strength-to-weight ratio. It can withstand temperatures up to 600°F (316°C) and is often anodized for additional corrosion protection.
Pros & Cons: The low weight of aluminum makes it easier to transport and install, reducing shipping costs. However, it is less durable than stainless steel, making it more susceptible to dents and scratches. The cost is generally moderate, but high-quality aluminum can be expensive.
Impact on Application: Aluminum is suitable for vending machines that dispense lightweight products. Its corrosion resistance makes it suitable for humid environments, but it may not be ideal for machines exposed to harsh chemicals.
Considerations for International Buyers: Buyers should be aware of local regulations regarding aluminum use, especially in food applications. Compliance with JIS standards in Japan or ASTM standards in the U.S. is crucial for ensuring product safety.
Polycarbonate
Key Properties: Polycarbonate is a high-impact, transparent thermoplastic known for its excellent optical clarity and resistance to UV light. It can withstand temperatures up to 250°F (121°C).
Pros & Cons: The transparency of polycarbonate allows for attractive product displays, enhancing customer engagement. However, it is less durable than metals and can scratch easily. The cost is generally lower than metals, making it an economical choice for certain applications.
Impact on Application: Polycarbonate is ideal for vending machine windows and panels, allowing visibility of products. However, it may not be suitable for areas exposed to high temperatures or heavy physical impacts.
Considerations for International Buyers: Buyers should ensure that polycarbonate materials meet relevant safety and environmental regulations. For example, compliance with REACH in Europe is essential for materials used in consumer products.
Glass
Key Properties: Glass is a rigid, transparent material that offers excellent visibility and aesthetic appeal. It can withstand high temperatures but is fragile and can shatter upon impact.
Pros & Cons: The primary advantage of glass is its ability to provide a premium look and feel, enhancing the overall customer experience. However, its fragility makes it less suitable for high-traffic areas, and it may require protective coatings to prevent scratches.
Impact on Application: Glass is often used in vending machines that require a high-end appearance, such as those found in luxury settings. However, its use is limited in environments where durability is a concern.
Considerations for International Buyers: Compliance with safety standards is crucial, especially regarding shatterproof regulations. Buyers should also consider the logistics of transporting glass, as it requires careful handling to avoid breakage.
Material | Typical Use Case for ulta vending machine locations | Key Advantage | Key Disadvantage/Limitation | Relative Cost (Low/Med/High) |
---|---|---|---|---|
Stainless Steel | High-traffic areas, food service applications | Excellent durability and corrosion resistance | Higher cost and manufacturing complexity | High |
Aluminum | Lightweight vending machines, outdoor applications | Lightweight and corrosion-resistant | Less durable than stainless steel | Medium |
Polycarbonate | Vending machine windows and panels | Attractive product visibility | Scratches easily and lower durability | Low |
Glass | Premium vending machines in luxury settings | High aesthetic appeal | Fragile and requires careful handling | Medium |
This strategic material selection guide provides insights into the materials most commonly used in ulta vending machine locations, helping international B2B buyers make informed decisions that align with their operational needs and regional compliance requirements.
In-depth Look: Manufacturing Processes and Quality Assurance for ulta vending machine locations
When considering the manufacturing processes and quality assurance for ulta vending machine locations, international B2B buyers must understand the critical stages involved in production as well as the standards that ensure product reliability and safety. This section provides an in-depth overview of typical manufacturing processes, quality control measures, and actionable insights for buyers across Africa, South America, the Middle East, and Europe.
Manufacturing Processes
The manufacturing of ulta vending machines involves several key stages, each crucial for delivering a high-quality product. Understanding these stages can help buyers assess potential suppliers more effectively.
1. Material Preparation
The first stage involves sourcing and preparing materials, which typically include metals, plastics, and electronic components. Key considerations for buyers include:
- Material Quality: Ensure that suppliers use materials that meet international standards, such as ASTM for metals and ISO standards for plastics.
- Sustainability: Increasingly, buyers are prioritizing eco-friendly materials. Suppliers that offer recyclable or sustainably sourced materials may provide a competitive advantage.
2. Forming
In this stage, raw materials are shaped into components using various techniques, including:
- CNC Machining: Offers precision in creating metal parts.
- Injection Molding: Commonly used for plastic components, providing high efficiency and repeatability.
- Sheet Metal Fabrication: Essential for creating the outer shell of the vending machines.
Buyers should verify that suppliers use advanced technologies that enhance accuracy and minimize waste.
3. Assembly
The assembly stage involves bringing together all components to create the final product. Key aspects include:
- Automated Assembly Lines: Many manufacturers utilize robotics to improve efficiency and reduce labor costs.
- Modular Design: Some vending machines are designed in modules, allowing for easier upgrades and repairs.
For buyers, understanding the assembly process can highlight a supplier’s capability to meet specific requirements or customizations.
4. Finishing
Finishing processes enhance the durability and aesthetics of the vending machines. Common techniques include:
- Powder Coating: Provides a durable finish that resists scratches and corrosion.
- Screen Printing: Used for branding and user interface displays.
Buyers should assess whether the finishing techniques used align with their brand requirements and durability expectations.
Quality Assurance
Quality assurance is paramount in the manufacturing of ulta vending machines, ensuring that products meet international safety and performance standards. Here are the key components:
International Standards
Familiarity with relevant international standards is crucial for B2B buyers:
- ISO 9001: This standard focuses on quality management systems and is applicable to all manufacturers. It ensures that suppliers follow consistent quality processes.
- CE Marking: Required in Europe, this certification indicates that the product meets EU safety and health requirements.
- API Standards: Relevant in specific industries, ensuring that vending machines comply with safety and operational standards.
Quality Control Checkpoints
Quality control processes typically involve several checkpoints:
- Incoming Quality Control (IQC): Inspects materials upon arrival to ensure they meet specified standards.
- In-Process Quality Control (IPQC): Conducted during production to monitor and control the manufacturing process.
- Final Quality Control (FQC): Takes place at the end of the production line, where finished products are tested for functionality and quality.
Buyers should inquire about the specific QC processes employed by suppliers to ensure comprehensive coverage.
Common Testing Methods
To verify the quality of ulta vending machines, manufacturers may employ various testing methods, such as:
- Electrical Testing: Ensures that all electronic components function correctly.
- Mechanical Testing: Assesses the durability and strength of the machine’s structure.
- Usability Testing: Ensures that the user interface is intuitive and functional.
Verifying Supplier Quality Control
For international B2B buyers, verifying a supplier’s quality control processes is essential. Here are some actionable steps:
- Conduct Audits: Regular audits can provide insights into the supplier’s manufacturing practices and compliance with quality standards.
- Request Quality Reports: Suppliers should provide documentation of their QC processes, including test results and certifications.
- Engage Third-Party Inspectors: Utilizing third-party inspection services can offer an unbiased evaluation of product quality and compliance with industry standards.
Quality Control Nuances for International Buyers
International buyers, particularly those from diverse regions like Africa, South America, the Middle East, and Europe, should be aware of certain nuances:
- Regulatory Differences: Each region may have specific regulatory requirements that affect product compliance. Buyers should ensure that suppliers are knowledgeable about local regulations.
- Cultural Considerations: Understanding cultural differences in business practices can facilitate smoother negotiations and foster stronger supplier relationships.
- Supply Chain Risks: Factors such as political stability, logistics, and economic conditions can impact the quality of products. Buyers should assess these risks when selecting suppliers.
Conclusion
Navigating the complexities of manufacturing processes and quality assurance for ulta vending machine locations is vital for international B2B buyers. By understanding the key stages of production, relevant standards, and effective quality control measures, buyers can make informed decisions and establish strong partnerships with reliable suppliers. This knowledge not only enhances product quality but also contributes to long-term business success in the global marketplace.
Related Video: The Production Planning Process
Comprehensive Cost and Pricing Analysis for ulta vending machine locations Sourcing
When sourcing ulta vending machines, understanding the comprehensive cost structure and pricing dynamics is crucial for international B2B buyers. This analysis will help navigate the complexities involved and ensure informed decision-making.
Cost Components
-
Materials: The primary costs stem from the raw materials used in manufacturing vending machines, such as steel, plastics, and electronic components. Fluctuations in global commodity prices can significantly affect overall costs, so staying updated on market trends is advisable.
-
Labor: Labor costs vary greatly depending on the manufacturing location. Countries with lower labor costs, such as those in Southeast Asia or parts of Africa, may offer more competitive pricing. However, this can sometimes come at the expense of quality and compliance with international standards.
-
Manufacturing Overhead: This encompasses costs related to factory operations, including utilities, rent, and administrative expenses. Efficient manufacturing processes can lower these costs, so buyers should inquire about the operational efficiencies of potential suppliers.
-
Tooling: The cost of specialized tooling for custom features can be substantial. If customizations are required, it is essential to assess whether the tooling investment justifies the potential return on investment.
-
Quality Control (QC): Implementing strict QC measures ensures the machines meet required specifications and certifications. Investing in quality control can prevent costly returns and improve long-term customer satisfaction.
-
Logistics: Shipping costs are a major consideration for international buyers. Factors such as distance, shipping method, and customs duties play a significant role in total logistics expenses. It is advisable to compare different logistics providers to identify the most cost-effective solutions.
-
Margin: Suppliers typically include a margin to cover their risks and profits. Understanding the competitive landscape can help buyers negotiate better terms, especially if they are purchasing in bulk.
Price Influencers
-
Volume/MOQ: Minimum order quantities (MOQ) can significantly impact pricing. Higher volumes usually lead to lower per-unit costs, so consider consolidating orders to maximize savings.
-
Specifications/Customization: Custom features may lead to increased costs. Clearly defining specifications can help avoid unnecessary expenses during production.
-
Materials: The choice of materials directly affects the cost. Opting for high-quality materials may increase upfront costs but can lead to lower maintenance and replacement costs in the long run.
-
Quality/Certifications: Machines that meet specific quality certifications may command higher prices. These certifications can enhance the resale value and marketability of the machines.
-
Supplier Factors: Supplier reliability, reputation, and financial stability are critical factors in pricing. Conduct thorough due diligence to mitigate risks associated with supplier selection.
-
Incoterms: The chosen Incoterms (International Commercial Terms) influence the distribution of costs and risks between buyers and sellers. Understanding these terms is essential to avoid unexpected expenses.
Buyer Tips
-
Negotiation: Always negotiate pricing and terms. Suppliers may have flexibility, especially for larger orders or long-term contracts.
-
Cost Efficiency: Focus on the Total Cost of Ownership (TCO) rather than just the initial purchase price. Consider factors such as maintenance, energy consumption, and warranty terms.
-
Pricing Nuances: International buyers should be aware of currency fluctuations and their impact on pricing. Additionally, cultural differences may influence negotiation styles, so adapt accordingly.
-
Disclaimer for Indicative Prices: Pricing can vary widely based on numerous factors. Buyers should seek quotes tailored to their specific needs to ensure accuracy.
By understanding these cost components, price influencers, and actionable tips, international B2B buyers can make well-informed decisions when sourcing ulta vending machines, ultimately leading to better investment outcomes.
Spotlight on Potential ulta vending machine locations Manufacturers and Suppliers
This section offers a look at a few manufacturers active in the ‘ulta vending machine locations’ market. This is a representative sample for illustrative purposes; B2B buyers must conduct their own extensive due diligence before any engagement. Information is synthesized from public sources and general industry knowledge.
Essential Technical Properties and Trade Terminology for ulta vending machine locations
Key Technical Properties of Ulta Vending Machines
When considering the procurement of Ulta vending machines, understanding their technical specifications is crucial for ensuring product reliability and meeting business needs. Here are some essential properties to consider:
-
Material Grade
The material used in vending machines, typically stainless steel or high-grade plastic, impacts durability and maintenance. Stainless steel offers resistance to rust and corrosion, making it suitable for high-traffic environments. For B2B buyers, selecting machines with high-quality materials can reduce long-term operational costs. -
Size and Dimensions
The physical dimensions of vending machines dictate their placement and the volume of products they can hold. Standard sizes may vary, and it’s essential to choose a machine that fits the intended space while maximizing inventory capacity. Buyers should consider location constraints to ensure seamless installation and operation. -
Power Consumption
Energy efficiency is a growing concern, especially in regions with high electricity costs. Buyers should look for vending machines that specify power consumption ratings, ideally those compliant with international energy standards. This helps in reducing operational costs and aligns with sustainability goals. -
Temperature Control
For vending machines offering perishable items, maintaining specific temperature ranges is vital. Machines equipped with advanced refrigeration technology ensure product quality and safety. Understanding temperature control specifications can prevent product spoilage and enhance customer satisfaction. -
User Interface
A user-friendly interface enhances customer experience and can increase sales. Look for machines with touch screens, multiple language options, and easy payment methods (including mobile payments). A good user interface can differentiate your business in competitive markets. -
Payment Acceptance
The variety of payment methods accepted (cash, credit/debit cards, mobile payments) can significantly influence sales. Machines that support diverse payment options cater to a broader customer base, enhancing revenue potential. B2B buyers should prioritize machines with flexible payment systems.
Common Trade Terms in Vending Machine Procurement
Understanding industry jargon is essential for effective communication and negotiation in B2B transactions. Here are some common terms relevant to Ulta vending machine procurement:
-
OEM (Original Equipment Manufacturer)
This term refers to companies that produce parts or equipment that may be marketed by another manufacturer. In the vending machine industry, knowing the OEM can help buyers assess quality and reliability. -
MOQ (Minimum Order Quantity)
MOQ indicates the smallest quantity of a product that a supplier is willing to sell. This term is crucial for buyers to understand, as it impacts inventory management and initial investment costs. -
RFQ (Request for Quotation)
An RFQ is a formal document that buyers send to suppliers to request pricing for specific quantities of products. This process helps buyers compare prices and terms from multiple vendors, enabling informed decision-making. -
Incoterms (International Commercial Terms)
These are standardized terms used in international trade to clarify responsibilities between buyers and sellers. Understanding Incoterms can help B2B buyers negotiate shipping costs, risks, and delivery responsibilities effectively. -
Lead Time
Lead time refers to the time it takes from placing an order to receiving the goods. For vending machines, understanding lead time is critical for planning installations and ensuring product availability. -
Warranty and Service Agreements
These terms outline the conditions under which a product is covered for repairs or replacements. Understanding warranty terms can protect buyers from unexpected costs and ensure ongoing support for their vending machines.
By familiarizing themselves with these essential properties and trade terms, international B2B buyers can make more informed decisions and enhance their procurement strategies for Ulta vending machines.
Navigating Market Dynamics, Sourcing Trends, and Sustainability in the ulta vending machine locations Sector
Market Overview & Key Trends
The ulta vending machine locations sector is experiencing significant transformation driven by several global factors. With the rise of urbanization and a growing demand for convenience, international B2B buyers from regions like Africa, South America, the Middle East, and Europe are increasingly investing in vending technology. Key trends include the integration of IoT technology for real-time inventory management, cashless payment solutions, and personalized customer experiences through data analytics.
Moreover, sustainability is becoming a crucial driver for this sector. Buyers are now looking for vending machines that not only meet consumer demands but also adhere to eco-friendly practices. The emergence of smart vending machines that utilize renewable energy sources and energy-efficient designs is gaining traction. Additionally, the shift towards healthier snack and beverage options is reshaping product offerings, as businesses respond to consumer preferences for wellness and nutrition.
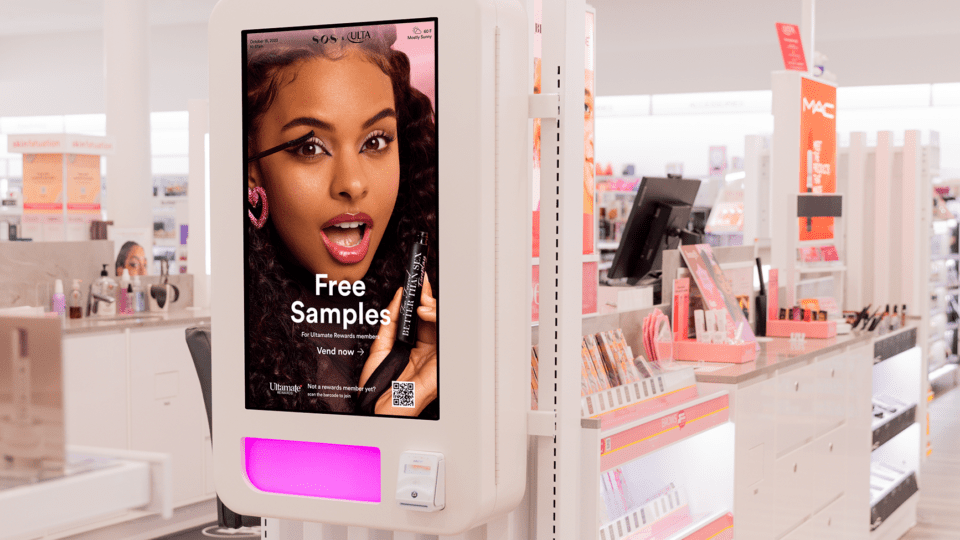
Illustrative Image (Source: Google Search)
As these dynamics evolve, B2B buyers must stay informed about local regulations and market entry barriers specific to their regions. This knowledge is essential for navigating partnerships and ensuring compliance with diverse consumer expectations and environmental standards. For instance, understanding the unique logistical challenges in South America or the regulatory frameworks in the Middle East can significantly influence sourcing strategies and operational efficiency.
Sustainability & Ethical Sourcing in B2B
The environmental impact of vending machines, particularly regarding waste management and energy consumption, is a growing concern among B2B buyers. Companies in this sector are increasingly prioritizing sustainability by adopting practices that reduce their carbon footprint. This includes sourcing materials that are recyclable or biodegradable, and implementing energy-efficient technologies in machine design.
Ethical sourcing is also gaining importance. Buyers are encouraged to partner with suppliers who adhere to fair labor practices and sustainable sourcing of raw materials. Certifications such as Fair Trade, Forest Stewardship Council (FSC), and Energy Star can provide assurance that products meet high environmental and ethical standards.
Moreover, the concept of a circular economy is becoming pivotal. By embracing recycling and reusing materials, businesses can minimize waste and enhance their brand reputation. This shift not only appeals to environmentally-conscious consumers but also aligns with the growing regulatory pressures to adopt sustainable practices across various markets.
Brief Evolution/History (Optional)
The vending machine industry has evolved significantly since its inception in the late 19th century. Initially designed to dispense simple products like postcards and chewing gum, the sector has expanded to include sophisticated machines capable of delivering a wide range of items, including fresh food and high-tech gadgets. The introduction of cashless payments and smart technology has further transformed the landscape, enabling real-time monitoring and enhancing user convenience.
As global awareness of environmental issues has risen, the industry has shifted towards sustainability, prompting innovations that prioritize eco-friendly materials and energy-efficient operations. This evolution reflects broader societal trends and changing consumer preferences, underscoring the importance of adaptability in the ulta vending machine locations sector for B2B buyers.
Related Video: Global Trade & Logistics – What is Global Trade?
Frequently Asked Questions (FAQs) for B2B Buyers of ulta vending machine locations
-
What key factors should I consider when vetting suppliers for ulta vending machines?
When vetting suppliers, prioritize their experience in the vending machine industry, reputation, and compliance with international standards. Look for suppliers with a solid track record of successful installations and positive customer testimonials. Assess their financial stability and ask for references from other international clients. Additionally, ensure they possess necessary certifications, such as ISO or CE, which indicate adherence to quality and safety standards. -
Can I customize ulta vending machines to meet specific market needs?
Yes, many suppliers offer customization options for ulta vending machines. This may include branding, product selection tailored to local preferences, and machine features such as payment systems or touchscreen interfaces. Discuss your requirements with potential suppliers early in the negotiation process to ensure they can accommodate your needs. Customization can enhance consumer engagement and improve sales performance in diverse markets. -
What are the typical minimum order quantities (MOQ) and lead times for ulta vending machines?
MOQs can vary significantly between suppliers and may depend on the level of customization required. Generally, you might expect an MOQ of 10-50 units for standard machines. Lead times also vary based on customization, production schedules, and shipping logistics, typically ranging from 4-12 weeks. Always clarify these details upfront to manage your procurement timeline effectively. -
What payment methods are commonly accepted by suppliers of ulta vending machines?
Payment methods can vary by supplier, but common options include wire transfers, letters of credit, and credit cards. Some suppliers may offer payment terms that allow for partial payment upfront and the remainder upon delivery. It is essential to establish clear payment terms before finalizing contracts to avoid disputes and ensure a smooth transaction process. -
What quality assurance measures should I expect from suppliers?
Reputable suppliers should have robust quality assurance (QA) processes in place. This typically includes pre-production samples, in-process inspections, and final product testing. Ask suppliers for details about their QA protocols, including any relevant certifications like ISO 9001, which indicates a commitment to quality management. A thorough QA process can significantly reduce the risk of receiving defective products.
-
How do logistics and shipping work for ulta vending machines?
Logistics for ulta vending machines involve careful planning for both domestic and international shipping. Discuss with suppliers their preferred shipping methods and timelines, as well as the associated costs. Ensure that they have experience with customs clearance and handling international regulations, particularly if you are importing to regions like Africa or South America. Proper logistics management is crucial for timely deliveries and minimizing additional costs. -
What steps should I take if a dispute arises with a supplier?
In the event of a dispute, first attempt to resolve the issue through direct communication with the supplier. Document all communications for reference. If direct negotiations fail, refer to the contract terms regarding dispute resolution, which may include mediation or arbitration. Engage legal counsel familiar with international trade if necessary. Establishing clear contract terms upfront can help mitigate the risks of disputes. -
Are there specific certifications I should look for when sourcing from suppliers?
Yes, when sourcing ulta vending machines, look for certifications that ensure compliance with international standards, such as ISO, CE, or UL. These certifications indicate that the machines meet safety, quality, and environmental standards. Additionally, consider checking for certifications specific to the electronics industry, which can provide assurance of the machine’s durability and reliability in diverse operating conditions.
Strategic Sourcing Conclusion and Outlook for ulta vending machine locations
As the global market for ulta vending machines expands, strategic sourcing emerges as a crucial component for international B2B buyers, particularly those from Africa, South America, the Middle East, and Europe. The key takeaways from this guide highlight the importance of identifying optimal locations, understanding local consumer behavior, and leveraging technology for efficient operations.
By prioritizing strategic sourcing, businesses can enhance their supply chain resilience, reduce costs, and improve service delivery. This is particularly vital in diverse markets where cultural nuances and purchasing preferences significantly influence consumer engagement.
Looking ahead, B2B buyers should remain proactive in exploring partnerships that facilitate market entry and expansion. Investing in local market research and establishing robust supplier relationships will not only optimize product offerings but also position brands favorably in competitive landscapes.
Take action now: Engage with local distributors, analyze market trends, and invest in innovative vending solutions that cater to the specific needs of your target audience. By doing so, you can capitalize on the growing demand for ulta vending machines and drive sustainable growth in your business.