Your Ultimate Guide to Sourcing Sticker Vending Machine
Guide to Sticker Vending Machine
- Introduction: Navigating the Global Market for sticker vending machine
- Understanding sticker vending machine Types and Variations
- Key Industrial Applications of sticker vending machine
- Strategic Material Selection Guide for sticker vending machine
- In-depth Look: Manufacturing Processes and Quality Assurance for sticker vending machine
- Manufacturing Processes for Sticker Vending Machines
- Quality Assurance Processes
- Conclusion
- Comprehensive Cost and Pricing Analysis for sticker vending machine Sourcing
- Spotlight on Potential sticker vending machine Manufacturers and Suppliers
- Essential Technical Properties and Trade Terminology for sticker vending machine
- Navigating Market Dynamics, Sourcing Trends, and Sustainability in the sticker vending machine Sector
- Frequently Asked Questions (FAQs) for B2B Buyers of sticker vending machine
- Strategic Sourcing Conclusion and Outlook for sticker vending machine
Introduction: Navigating the Global Market for sticker vending machine
In today’s fast-paced retail landscape, sticker vending machines are emerging as innovative solutions that cater to diverse consumer demands while offering B2B buyers lucrative opportunities. These machines not only provide instant gratification but also serve as a unique marketing tool, allowing businesses to engage with customers in vibrant and interactive ways. As the market for sticker vending machines grows, understanding the nuances of this segment becomes essential for international B2B buyers, especially those operating in regions like Africa, South America, the Middle East, and Europe.
This comprehensive guide delves into the various aspects of sticker vending machines, including types, materials, manufacturing processes, quality control measures, and supplier options. It also addresses cost considerations and market trends, ensuring that buyers have a holistic view of the landscape. By providing insights into frequently asked questions, this guide empowers businesses to make informed sourcing decisions that align with their operational goals and customer preferences.
For B2B buyers in emerging markets such as Brazil and Kenya, leveraging the potential of sticker vending machines can enhance customer engagement and drive sales. With the right knowledge and strategies, businesses can capitalize on this growing trend, ensuring they remain competitive in a dynamic marketplace. Explore the opportunities that sticker vending machines present, and unlock the potential for sustained growth and innovation in your operations.
Understanding sticker vending machine Types and Variations
Type Name | Key Distinguishing Features | Primary B2B Applications | Brief Pros & Cons for Buyers |
---|---|---|---|
Traditional Sticker Vending Machine | Mechanical operation, coin-operated, limited selection | Schools, amusement parks, retail stores | Pros: Low initial investment; Cons: Limited payment options, requires manual restocking. |
Digital Sticker Vending Machine | Touchscreen interface, cashless payment options, customizable displays | Events, malls, art galleries | Pros: Interactive experience; Cons: Higher initial cost, requires regular software updates. |
Smart Sticker Vending Machine | IoT-enabled, real-time inventory tracking, data analytics | Shopping centers, airports, universities | Pros: Efficient inventory management; Cons: Complex setup, dependency on stable internet connection. |
Eco-Friendly Sticker Vending Machine | Uses sustainable materials, offers biodegradable stickers | Eco-conscious retailers, festivals | Pros: Appeals to environmentally aware consumers; Cons: Potentially higher product costs. |
Customizable Sticker Vending Machine | Allows users to select and create their own stickers on-site | Creative events, workshops, trade shows | Pros: Unique customer engagement; Cons: Requires more space and higher maintenance. |
Traditional Sticker Vending Machine
Traditional sticker vending machines are typically mechanical and coin-operated, offering a limited selection of stickers. They are commonly placed in high-traffic areas such as schools, amusement parks, and retail stores. For B2B buyers, the main considerations include the low initial investment and straightforward operation. However, these machines may require manual restocking and often lack modern payment options, which could limit customer engagement.
Digital Sticker Vending Machine
Digital sticker vending machines feature a touchscreen interface and support cashless payment options, providing a more modern and interactive experience. These machines are ideal for locations like events, malls, and art galleries, where customer engagement is crucial. B2B buyers should note that while these machines attract tech-savvy consumers, they come with a higher initial cost and require regular software updates to function optimally.
Smart Sticker Vending Machine
Smart sticker vending machines leverage IoT technology for real-time inventory tracking and data analytics. They are particularly suited for high-traffic environments such as shopping centers, airports, and universities, allowing operators to optimize product offerings based on customer preferences. While they offer significant advantages in inventory management, buyers should consider the complexity of setup and the need for a reliable internet connection.
Eco-Friendly Sticker Vending Machine
Eco-friendly sticker vending machines focus on sustainability by using biodegradable stickers and materials. They cater to eco-conscious retailers and festivals, appealing to consumers who prioritize environmental responsibility. B2B buyers should weigh the benefits of attracting a niche market against potentially higher product costs, which may affect profit margins.
Customizable Sticker Vending Machine
Customizable sticker vending machines allow users to create their own stickers on-site, providing a unique and engaging experience. These machines are perfect for creative events, workshops, and trade shows. For B2B buyers, the ability to offer a distinctive customer experience is a significant advantage, but they require more space and ongoing maintenance, which can impact operational efficiency.
Related Video: DIY Card Vending Machine – Easy Cardboard Craft
Key Industrial Applications of sticker vending machine
Industry/Sector | Specific Application of sticker vending machine | Value/Benefit for the Business | Key Sourcing Considerations for this Application |
---|---|---|---|
Retail | Branding and promotional stickers | Enhances brand visibility and customer engagement | Quality of stickers, customization options, machine reliability |
Education | School and event stickers | Boosts school spirit and promotes events | Durability of stickers, ease of use for students, machine security |
Entertainment & Events | Event-specific stickers for concerts and festivals | Creates memorable experiences and boosts merchandise sales | Customization capabilities, inventory management, payment options |
Tourism & Hospitality | Souvenir stickers for tourists | Increases revenue from tourists and enhances local culture | Local themes, quality of materials, machine placement strategies |
Marketing & Advertising | Interactive marketing campaigns | Engages customers directly and provides instant gratification | Integration with digital platforms, analytics capabilities, design flexibility |
In the retail sector, sticker vending machines serve as an innovative branding tool. Businesses can utilize these machines to distribute promotional stickers that enhance brand visibility and foster customer engagement. By offering unique and eye-catching designs, retailers can attract foot traffic and encourage impulse purchases. International buyers should consider the quality and customization options of stickers, as well as the reliability of the vending machines themselves.
In educational settings, sticker vending machines can be used to distribute school-themed stickers that promote school spirit and various events. This application not only generates additional revenue for schools but also fosters a sense of community among students. Buyers should focus on the durability of the stickers, ease of use for students, and security features of the vending machines to prevent theft.
Within the entertainment and events industry, sticker vending machines can be strategically placed at concerts and festivals to offer event-specific stickers. This creates memorable experiences for attendees and provides an additional revenue stream through merchandise sales. Buyers in this sector should prioritize customization capabilities for stickers, effective inventory management systems, and flexible payment options to cater to diverse audiences.
In the tourism and hospitality industry, sticker vending machines can serve tourists by offering local souvenir stickers that reflect the culture and attractions of the area. This not only enhances visitors’ experiences but also contributes to local economies. When sourcing machines for this application, it is crucial to focus on local themes and the quality of materials used, as well as effective machine placement strategies in high-traffic tourist areas.
Lastly, in marketing and advertising, sticker vending machines can facilitate interactive marketing campaigns. By allowing customers to create or select stickers that resonate with them, businesses can engage consumers directly and provide instant gratification. Buyers should consider how well the vending machines can integrate with digital platforms, the analytics capabilities available, and the flexibility of designs to align with their marketing strategies.
Related Video: DIY Vending Machine – Arduino based Mechatronics Project
Strategic Material Selection Guide for sticker vending machine
When selecting materials for sticker vending machines, international B2B buyers must consider various factors that influence performance, durability, and cost-effectiveness. Below, we analyze four common materials used in the construction of vending machines, focusing on their properties, advantages, disadvantages, and specific considerations for buyers in regions like Africa, South America, the Middle East, and Europe.
1. Stainless Steel
Key Properties: Stainless steel is known for its excellent corrosion resistance, high strength, and ability to withstand extreme temperatures. It typically has a temperature rating of up to 800°F (427°C) and can handle pressures of up to 3000 psi, depending on the grade.
Pros & Cons: The primary advantage of stainless steel is its durability and resistance to rust, making it ideal for outdoor installations or humid environments. However, it is more expensive than other materials and can be challenging to fabricate, which may increase manufacturing costs.
Impact on Application: Stainless steel is compatible with various media, including water and certain chemicals, making it suitable for vending machines that dispense beverages or food items.
Considerations for International Buyers: Buyers should ensure compliance with local standards such as ASTM or DIN for food safety. In regions like Europe, the preference for stainless steel is often higher due to its hygienic properties.
2. High-Density Polyethylene (HDPE)
Key Properties: HDPE is a lightweight thermoplastic with excellent impact resistance and a temperature tolerance of up to 120°F (49°C). It is also resistant to many chemicals and UV radiation.
Pros & Cons: HDPE is cost-effective and easy to mold into various shapes, making it suitable for custom designs. However, it may not be as durable as metals and can warp under high temperatures, limiting its use in certain environments.
Impact on Application: This material is best for internal components or external parts that are not exposed to extreme conditions, such as vending machine casings in indoor settings.
Considerations for International Buyers: Buyers should verify that HDPE complies with local regulations regarding food contact materials, especially in regions with strict health standards.
3. Aluminum
Key Properties: Aluminum is lightweight, corrosion-resistant, and has a melting point of around 1220°F (660°C). It can handle moderate temperatures and pressures, making it versatile for various applications.
Pros & Cons: The main advantage of aluminum is its lightweight nature, which reduces shipping costs. However, it is softer than steel, making it more susceptible to dents and scratches, which can affect the aesthetics and longevity of the vending machine.
Impact on Application: Aluminum is suitable for components that require a good strength-to-weight ratio, such as machine frames and panels.
Considerations for International Buyers: Buyers should consider the local availability of aluminum and its alloys, as well as compliance with international standards for recycling and sustainability, particularly in Europe and South America.
4. Glass-Fiber Reinforced Plastic (GFRP)
Key Properties: GFRP combines glass fibers with a plastic matrix, providing high strength and low weight. It has good chemical resistance and can withstand temperatures up to 200°F (93°C).
Pros & Cons: GFRP is highly durable and resistant to corrosion, making it ideal for outdoor applications. However, it can be more expensive to produce and may require specialized fabrication techniques.
Impact on Application: GFRP is excellent for aesthetic components of vending machines, such as decorative panels or casings that require a modern look.
Considerations for International Buyers: Buyers should check for compliance with local environmental regulations, as GFRP can be less recyclable than other materials. Understanding the regional market for GFRP can also help in sourcing and cost management.
Summary Table
Material | Typical Use Case for sticker vending machine | Key Advantage | Key Disadvantage/Limitation | Relative Cost (Low/Med/High) |
---|---|---|---|---|
Stainless Steel | External casing and structural components | Excellent corrosion resistance and durability | Higher cost and manufacturing complexity | High |
High-Density Polyethylene (HDPE) | Internal components and casings | Cost-effective and easy to mold | Less durable under high temperatures | Low |
Aluminum | Frames and panels | Lightweight and corrosion-resistant | Susceptible to dents and scratches | Medium |
Glass-Fiber Reinforced Plastic (GFRP) | Decorative panels and aesthetic components | High strength and corrosion resistance | Higher production costs and specialized fabrication | Medium |
This strategic material selection guide provides B2B buyers with essential insights into the materials used in sticker vending machines, enabling informed decisions that align with their operational needs and regional compliance requirements.
In-depth Look: Manufacturing Processes and Quality Assurance for sticker vending machine
Manufacturing Processes for Sticker Vending Machines
The manufacturing of sticker vending machines involves several critical stages that ensure the final product is functional, durable, and meets customer expectations. Below, we break down the main stages of the manufacturing process, highlighting key techniques and considerations for B2B buyers.
1. Material Preparation
The first step in manufacturing sticker vending machines is material preparation. This involves sourcing high-quality materials such as steel for the frame, acrylic or glass for the display, and electronic components for the vending mechanism.
- Material Selection: It’s essential to select materials that are not only durable but also cost-effective. Stainless steel is often preferred for its resistance to corrosion, especially in humid environments common in regions like Africa and South America.
- Sourcing: B2B buyers should ensure that suppliers can provide certifications for their materials, confirming compliance with international standards such as ISO 9001.
2. Forming
Once materials are prepared, they undergo forming processes to shape the various components of the vending machine.
- Techniques: Common techniques include laser cutting, bending, and stamping for metal parts, while injection molding is used for plastic components. Each technique impacts the precision and quality of the final product.
- Automation: Utilizing automated machinery can increase production efficiency and maintain consistent quality. Buyers should inquire about the level of automation in the manufacturing facility, as this can influence lead times and costs.
3. Assembly
After forming, the next stage is assembly, where all components are brought together to create the finished product.
- Sub-assemblies: Components like the vending mechanism, control panel, and coin acceptor are often assembled separately before being integrated into the main structure.
- Workforce Skills: Skilled labor is crucial in this stage to ensure that components are assembled correctly. B2B buyers should assess the expertise of the workforce at the manufacturing site.
4. Finishing
The finishing stage involves applying coatings and treatments to enhance the aesthetics and durability of the vending machine.
- Coating: Powder coating or painting is commonly used to provide a protective layer against wear and environmental factors. This is particularly important for machines placed in outdoor or high-traffic areas.
- Quality Checks: Before moving to the quality assurance phase, the finished products should undergo visual inspections to identify any cosmetic defects.
Quality Assurance Processes
Quality assurance (QA) is critical in ensuring that sticker vending machines meet international standards and customer expectations. Here are the key aspects of QA relevant to B2B buyers.
International Standards
Adhering to recognized international standards is essential for ensuring product quality and safety.
- ISO 9001: This standard focuses on quality management systems and is applicable to organizations of any size. Compliance demonstrates a commitment to quality and customer satisfaction.
- CE Marking: For machines sold in Europe, CE marking indicates conformity with health, safety, and environmental protection standards. B2B buyers in Europe should verify that their suppliers have this certification.
- Other Certifications: Depending on the market, additional certifications like API (American Petroleum Institute) may be relevant, especially if the vending machine is used for specific products.
Quality Control Checkpoints
Quality control (QC) is conducted at various stages of the manufacturing process to ensure that the machines meet the required standards.
- Incoming Quality Control (IQC): This initial checkpoint involves inspecting raw materials and components as they arrive at the factory. Buyers should request IQC reports to ensure the quality of materials used.
- In-Process Quality Control (IPQC): During assembly, IPQC checks are conducted to monitor processes and identify defects early. This can include measurements of component dimensions and functional tests.
- Final Quality Control (FQC): After assembly, the completed machines undergo rigorous testing, which may include functionality tests, safety checks, and performance evaluations. B2B buyers should ask for FQC documentation before finalizing purchases.
Common Testing Methods
Testing methods play a significant role in quality assurance, providing insights into the machine’s reliability and performance.
- Functional Testing: Ensures that all mechanical and electronic components operate as intended. This includes testing the vending mechanism, payment acceptance, and user interface.
- Durability Testing: Machines may undergo stress tests to simulate real-world use, assessing their performance under various conditions.
- Safety Testing: Compliance with safety standards is verified through electrical safety tests and hazard assessments.
Verifying Supplier Quality Control
B2B buyers must be proactive in verifying the quality control processes of their suppliers.
- Audits: Conducting regular audits of the manufacturing facility can provide insights into their quality management practices. Buyers should look for ISO 9001 certification as a baseline for quality assurance.
- Reports: Requesting detailed QC reports, including IQC, IPQC, and FQC results, can help buyers assess the consistency of the supplier’s quality practices.
- Third-Party Inspections: Engaging third-party inspection services can provide an unbiased assessment of the manufacturing process and product quality, especially beneficial for international buyers.
Quality Control Considerations for International Buyers
For buyers from Africa, South America, the Middle East, and Europe, understanding the nuances of quality control is vital.
- Local Regulations: Buyers should familiarize themselves with local regulations and standards that may affect product acceptance in their markets.
- Cultural Differences: Communication and expectations regarding quality can vary by region. Establishing clear guidelines and maintaining open lines of communication with suppliers can mitigate misunderstandings.
- Logistics and Supply Chain: Consider the logistics of transporting machines across borders, as this can impact quality. Ensure that suppliers have robust packaging and handling processes to minimize damage during transit.
Conclusion
Manufacturing and quality assurance processes for sticker vending machines are multifaceted, requiring careful attention to detail and adherence to international standards. By understanding these processes, B2B buyers can make informed decisions, ensuring they select reliable suppliers that deliver high-quality products tailored to their specific market needs.
Related Video: Business English Vocabulary : VV 47 – Manufacturing & Production Process (1) | English Vocabulary
Comprehensive Cost and Pricing Analysis for sticker vending machine Sourcing
Understanding the Cost Structure of Sticker Vending Machines
When sourcing sticker vending machines, understanding the comprehensive cost structure is essential for international B2B buyers. The primary cost components include:
-
Materials: This encompasses the cost of raw materials such as metal, plastic, and electronic components used in the machine’s construction. The choice of materials can significantly influence durability and aesthetics.
-
Labor: Labor costs are associated with the workforce required for assembly, quality control, and installation. These costs can vary based on the manufacturing location and local wage standards.
-
Manufacturing Overhead: This includes indirect costs related to production, such as utilities, facility maintenance, and equipment depreciation. A higher overhead can lead to increased pricing.
-
Tooling: Initial investments in tooling and molds for machine components are crucial. Custom designs may require more significant tooling investment, impacting the overall cost.
-
Quality Control (QC): Ensuring the machines meet specific standards involves costs related to testing and inspection. Higher QC standards can lead to increased manufacturing costs.
-
Logistics: This encompasses shipping, warehousing, and distribution costs. International shipments may incur additional fees related to customs and import duties, which should be factored into the total cost.
-
Margin: Manufacturers will typically add a profit margin to the production costs. This margin can vary based on market demand, competition, and perceived value.
Influencers on Pricing
Several factors influence the pricing of sticker vending machines, including:
-
Volume and Minimum Order Quantity (MOQ): Larger orders often qualify for discounts, making it crucial to assess your needs and negotiate terms that minimize costs.
-
Specifications and Customization: Custom features or specifications can increase costs. Buyers should evaluate the necessity of customizations against their budget and expected return on investment.
-
Materials: The choice between standard and premium materials will affect pricing. Understanding the trade-offs in terms of durability and aesthetics is essential.
-
Quality and Certifications: Machines with higher quality standards or certifications (e.g., CE, ISO) may command higher prices. However, they often provide better long-term value.
-
Supplier Factors: Supplier reputation, reliability, and location can influence pricing. Engaging with well-reviewed suppliers may yield better service and product quality.
-
Incoterms: Understanding shipping terms (e.g., FOB, CIF) can significantly impact total costs. Clarifying responsibilities for shipping costs, insurance, and customs duties is vital.
Tips for International B2B Buyers
-
Negotiation: Leverage your purchasing power, especially when placing bulk orders. Always be prepared to negotiate terms, including price, payment terms, and delivery schedules.
-
Cost-Efficiency: Focus on the Total Cost of Ownership (TCO) rather than just the initial purchase price. Consider maintenance, operational costs, and potential downtime when evaluating machine options.
-
Pricing Nuances: Be aware of pricing fluctuations in different markets. Factors such as currency exchange rates, local demand, and economic conditions can affect pricing stability.
-
Research Local Market Conditions: Understanding the market dynamics in regions like Africa, South America, the Middle East, and Europe can aid in making informed sourcing decisions. Different regions may have varying levels of demand and competition.
-
Supplier Relationships: Building strong relationships with suppliers can lead to better pricing, priority service, and insider knowledge on upcoming trends or products.
-
Disclaimer on Prices: Always note that indicative prices may fluctuate based on market conditions, material costs, and currency exchange rates. Regularly review and confirm pricing before finalizing orders.
By comprehensively analyzing these components and influencers, B2B buyers can make informed decisions that align with their strategic goals while ensuring a cost-effective sourcing process for sticker vending machines.
Spotlight on Potential sticker vending machine Manufacturers and Suppliers
This section offers a look at a few manufacturers active in the ‘sticker vending machine’ market. This is a representative sample for illustrative purposes; B2B buyers must conduct their own extensive due diligence before any engagement. Information is synthesized from public sources and general industry knowledge.
Essential Technical Properties and Trade Terminology for sticker vending machine
When considering the acquisition of a sticker vending machine, international B2B buyers must be well-informed about the essential technical properties and industry-specific terminology. Understanding these elements not only aids in selecting the right equipment but also enhances negotiation and operational efficiency.
Key Technical Properties
-
Material Grade
– The material grade refers to the quality of the materials used in the construction of the vending machine. Common materials include stainless steel for durability and acrylic for visibility. High-grade materials ensure longevity and resistance to wear and tear, which is crucial for machines placed in high-traffic areas. -
Capacity
– This specification indicates the number of stickers the machine can hold at any given time. A higher capacity means fewer restocking sessions, which can significantly reduce operational costs and labor. Buyers should assess expected foot traffic and sales volume to determine the appropriate capacity. -
Dimensions and Weight
– The dimensions (height, width, depth) and weight of the vending machine are vital for space planning and transportation. Buyers must ensure that the chosen machine fits the intended location without obstructing pathways or access points. -
Power Requirements
– Understanding the power requirements is essential for installation. Most vending machines operate on standard electrical outlets, but some may require specific voltage or amperage. Misjudging these requirements can lead to additional installation costs or operational failures. -
User Interface
– The user interface includes the buttons, touchscreen, or card reader that customers use to make purchases. A more intuitive interface can enhance user experience, potentially increasing sales. Machines with advanced interfaces may support cashless payments, which are increasingly preferred in modern retail environments. -
Warranty and Support
– This property outlines the manufacturer’s commitment to maintenance and repair. A robust warranty can mitigate risks associated with equipment failure, while responsive support services ensure quick resolutions to operational issues, essential for maintaining customer satisfaction.
Common Trade Terminology
-
OEM (Original Equipment Manufacturer)
– An OEM refers to a company that produces parts or equipment that may be marketed by another manufacturer. In the context of vending machines, understanding whether you are dealing with an OEM can impact pricing and customization options. -
MOQ (Minimum Order Quantity)
– MOQ is the smallest quantity of a product that a supplier is willing to sell. This term is critical for budgeting, as it influences the initial investment required for stocking sticker vending machines. -
RFQ (Request for Quotation)
– An RFQ is a document sent to suppliers to request a quote for specific products or services. This process is essential for buyers to compare prices and terms from different manufacturers, ensuring they secure the best deal. -
Incoterms (International Commercial Terms)
– Incoterms are a set of international rules that define the responsibilities of buyers and sellers in international transactions. Familiarity with these terms helps buyers understand shipping responsibilities, risk allocation, and costs involved in transporting vending machines across borders. -
Lead Time
– This term indicates the amount of time it takes from placing an order to receiving the product. Knowing the lead time is crucial for planning, especially in markets where demand is volatile, as it affects inventory management and customer satisfaction. -
Technical Specification Sheet
– A technical specification sheet outlines the detailed specifications of a product, including dimensions, materials, and performance standards. This document is vital for buyers to ensure that the vending machine meets their operational needs and regulatory requirements.
By grasping these technical properties and industry terms, B2B buyers can make informed purchasing decisions regarding sticker vending machines, ensuring they choose equipment that aligns with their business objectives and market demands.
Navigating Market Dynamics, Sourcing Trends, and Sustainability in the sticker vending machine Sector
Market Overview & Key Trends
The sticker vending machine market is experiencing a resurgence driven by the growing demand for customized and unique merchandise, particularly among younger demographics. Global drivers include the rising trend of personalization in consumer products and the increasing popularity of collectibles, which are particularly resonant in regions like Africa and South America. For B2B buyers, understanding these trends is crucial for capitalizing on emerging opportunities.
Current and emerging B2B tech trends include the integration of smart vending solutions equipped with real-time inventory management systems. These systems enable operators to track sales and customer preferences dynamically, allowing for optimized product offerings tailored to local tastes. In addition, the use of contactless payment options has become essential, especially in the wake of the COVID-19 pandemic, enhancing customer convenience and safety.
Market dynamics are also influenced by geographic preferences. For instance, in Europe, sticker vending machines may cater to a more artistic clientele, while in regions like Brazil and Kenya, vibrant and culturally relevant designs can attract attention. B2B buyers should prioritize sourcing from manufacturers who understand these local nuances and can provide region-specific sticker designs that resonate with target markets.
Sustainability & Ethical Sourcing in B2B
Sustainability is an increasingly vital concern in the vending machine sector, including sticker vending machines. The environmental impact of production and waste generation underscores the importance of ethical supply chains. B2B buyers should seek suppliers that demonstrate a commitment to sustainable practices, such as using eco-friendly materials for stickers and packaging.
Green certifications play a significant role in establishing credibility in this space. Look for suppliers that offer products made from recycled materials or those that have certifications such as FSC (Forest Stewardship Council) for paper products. Additionally, implementing efficient inventory management systems can reduce waste, ensuring that only the most popular designs are stocked, thereby minimizing excess inventory and associated waste.
Moreover, embracing sustainable practices not only aids in compliance with increasing regulatory demands but also appeals to a growing segment of environmentally-conscious consumers. This can enhance brand loyalty and open new markets, particularly in Europe and the Middle East, where sustainability is often a key purchasing factor.
Brief Evolution/History
The concept of vending machines dates back to the late 19th century, primarily dispensing items like cigarettes and postcards. However, the introduction of sticker vending machines in the late 20th century marked a pivotal shift, catering to niche markets such as children and collectors. As the digital age progressed, vending machines evolved further, incorporating technology that enabled customization and interaction, making them more appealing to younger audiences. Today, the sticker vending machine sector continues to innovate with smart technologies and sustainable practices, reflecting broader market trends that prioritize personalization and environmental consciousness. This evolution presents unique opportunities for B2B buyers to engage with a diverse range of products that meet modern consumer expectations.
Related Video: International Trade 101 | Economics Explained
Frequently Asked Questions (FAQs) for B2B Buyers of sticker vending machine
-
What factors should I consider when vetting suppliers for sticker vending machines?
When vetting suppliers, prioritize their experience in the vending machine industry and their track record with international clients. Check for verified customer reviews and testimonials. Evaluate their manufacturing capabilities, particularly regarding customization options and quality control processes. Ensure they have the necessary certifications, such as ISO standards, which indicate compliance with international quality benchmarks. Additionally, assess their communication responsiveness and willingness to provide after-sales support, as these are crucial for long-term partnerships. -
Can sticker vending machines be customized to suit my brand?
Yes, many suppliers offer customization options for sticker vending machines, allowing you to align the design and branding with your business identity. Customization can include exterior graphics, machine colors, and product selection tailored to your target market. When discussing customization, request samples or prototypes to ensure the final product meets your expectations. It’s also advisable to clarify any additional costs associated with custom features and the lead times required for production. -
What are the typical minimum order quantities (MOQ) and lead times for sticker vending machines?
Minimum order quantities can vary significantly by supplier, often ranging from a single unit to dozens, depending on their production capabilities. Lead times typically range from 4 to 12 weeks, influenced by factors such as customization requirements and the supplier’s current workload. Always confirm these details before placing an order to avoid unexpected delays. Additionally, inquire about bulk order discounts, as purchasing in larger quantities can often lead to cost savings. -
What payment options are available when sourcing sticker vending machines internationally?
Payment options for international transactions may include wire transfers, letters of credit, and online payment platforms like PayPal. Some suppliers may offer financing options or installment plans for larger orders. Ensure you discuss the payment terms upfront, including any upfront deposits required and the timeline for final payments. Be aware of currency exchange rates and potential fees associated with international transactions, and consider using escrow services for added security. -
What quality assurance measures should I expect from suppliers?
Reputable suppliers should implement robust quality assurance measures throughout their production process. This typically includes raw material inspections, in-process quality checks, and final product testing before shipment. Request documentation of their quality control processes and any relevant certifications, such as CE marking or ISO 9001. Additionally, consider asking for a warranty or guarantee period for the machines, which can provide assurance of their reliability and durability. -
How should logistics be handled for shipping sticker vending machines internationally?
Logistics can be complex when shipping vending machines internationally. Discuss with your supplier whether they handle logistics or if you need to arrange shipping independently. Consider factors like shipping methods (air vs. sea), freight costs, and estimated delivery times. Ensure that the supplier provides proper packaging to prevent damage during transit. Additionally, clarify who is responsible for customs duties and taxes, and ensure all necessary documentation is prepared for smooth clearance.
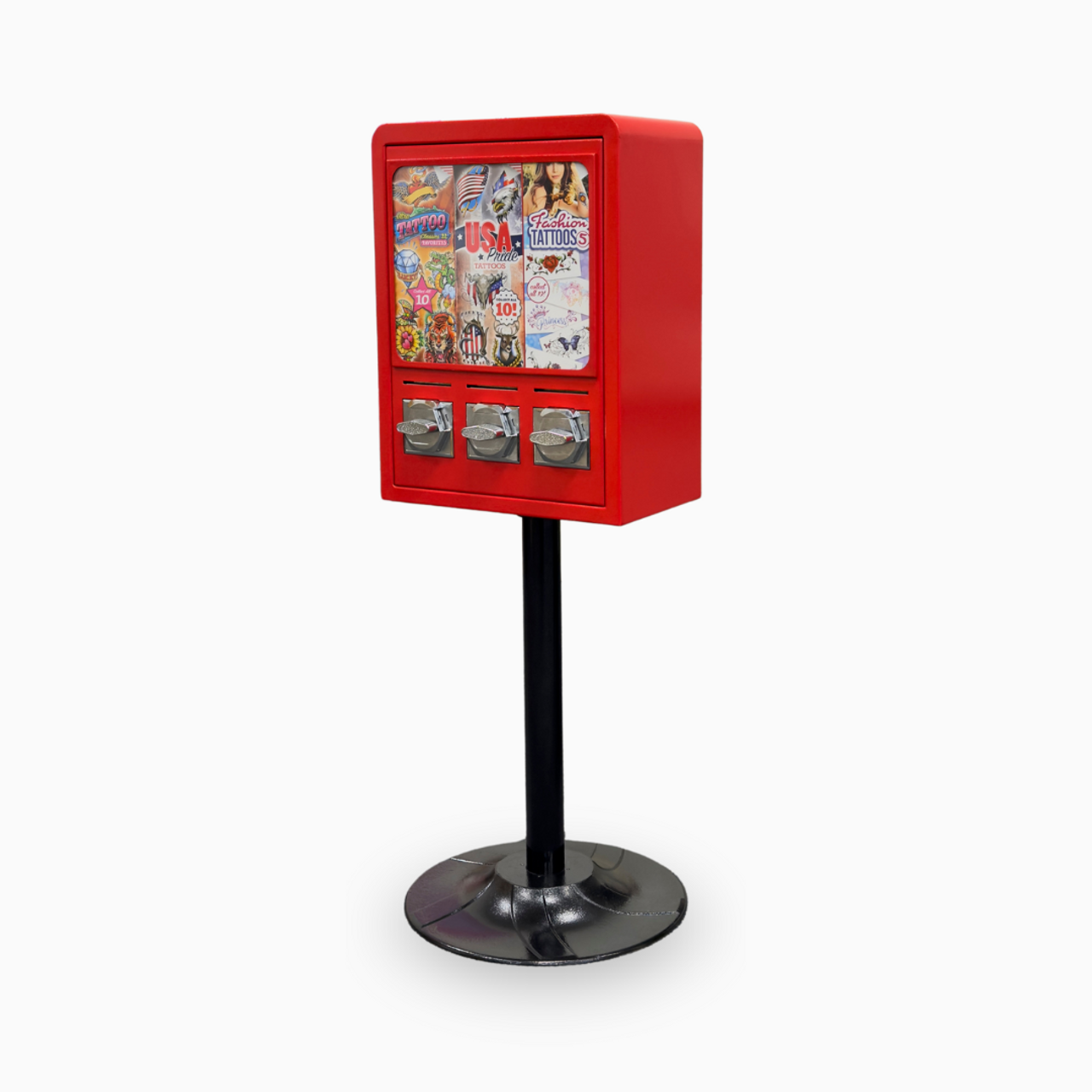
Illustrative Image (Source: Google Search)
- What steps can I take to resolve disputes with suppliers?
To resolve disputes effectively, first, try to communicate directly with the supplier to address the issue. Document all correspondence and keep records of agreements made. If direct negotiation fails, consider mediation or arbitration as stipulated in your contract. Ensure that your contracts include clear terms regarding dispute resolution processes. Understanding local laws and international trade agreements can also provide leverage in resolving conflicts amicably and efficiently.
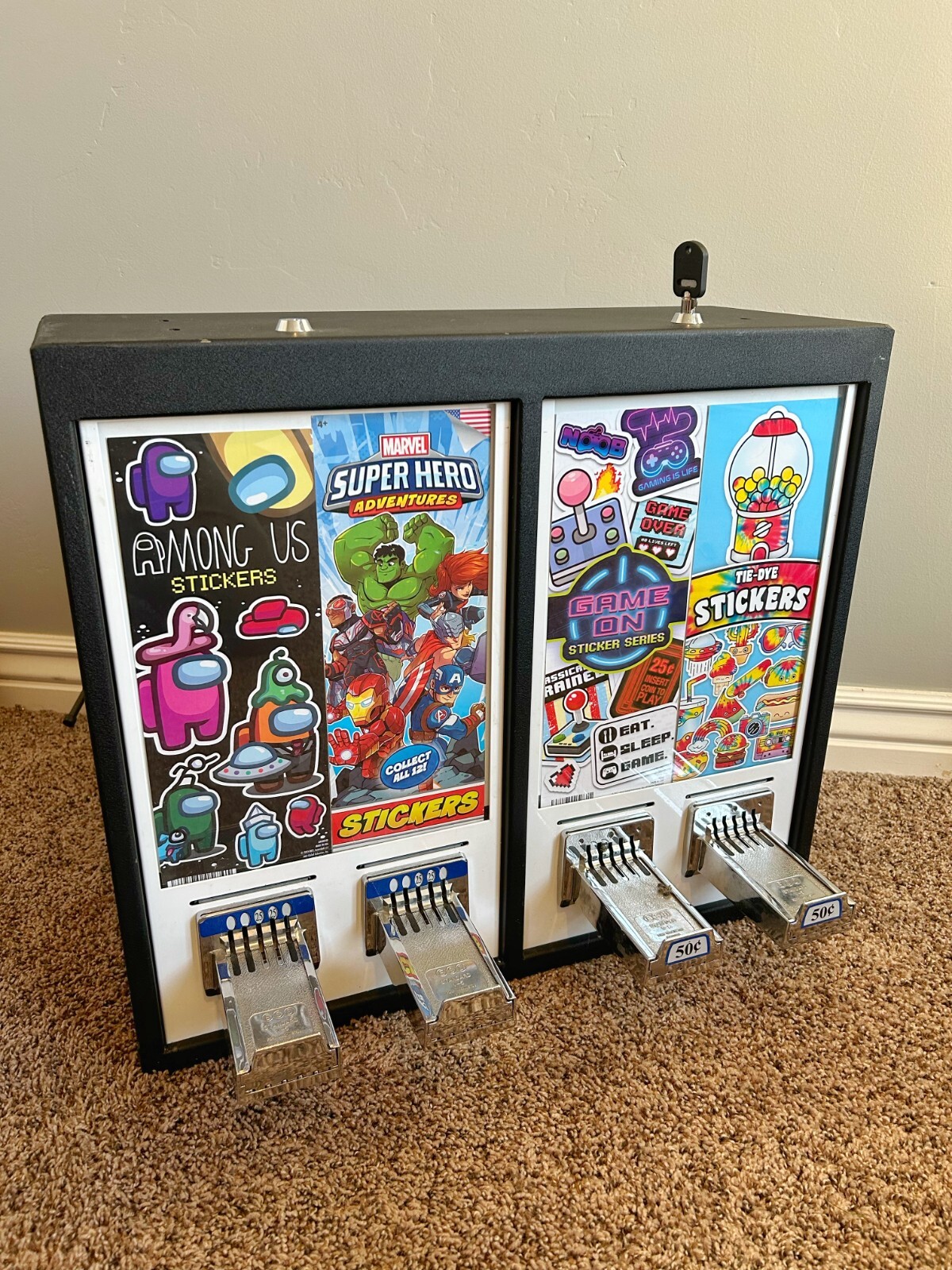
Illustrative Image (Source: Google Search)
- What certifications should I look for in sticker vending machines?
When sourcing sticker vending machines, look for certifications that indicate compliance with safety and quality standards. Common certifications include CE marking in Europe, UL certification in the U.S., and ISO certifications relevant to manufacturing and quality management. These certifications not only ensure the machines meet industry standards but also enhance their marketability in your region. Verify the authenticity of these certifications with the supplier, and request documentation for your records.
Strategic Sourcing Conclusion and Outlook for sticker vending machine
As the sticker vending machine market continues to evolve, strategic sourcing emerges as a vital component for international B2B buyers. By carefully selecting suppliers, understanding local market dynamics, and leveraging technology, businesses can enhance operational efficiency and customer satisfaction. Key takeaways include the importance of conducting thorough market research, identifying high-traffic locations, and utilizing smart inventory management systems to maximize profitability.
Investing in innovative vending solutions not only meets the demand for instant gratification but also aligns with sustainability goals by minimizing waste through effective inventory management practices. As the market expands across diverse regions, including Africa, South America, the Middle East, and Europe, buyers must remain agile and responsive to consumer preferences.
Looking ahead, the sticker vending machine sector presents a wealth of opportunities for growth and diversification. International B2B buyers are encouraged to embrace strategic sourcing as a pathway to capitalize on these trends. By prioritizing quality suppliers and leveraging advanced technologies, you can position your business for success in this dynamic market. Engage now to unlock the potential of sticker vending machines and drive your business forward.