Your Ultimate Guide to Sourcing Starbucks Vending Machine
Guide to Starbucks Vending Machine
- Introduction: Navigating the Global Market for starbucks vending machine
- Understanding starbucks vending machine Types and Variations
- Key Industrial Applications of starbucks vending machine
- Strategic Material Selection Guide for starbucks vending machine
- In-depth Look: Manufacturing Processes and Quality Assurance for starbucks vending machine
- Comprehensive Cost and Pricing Analysis for starbucks vending machine Sourcing
- Spotlight on Potential starbucks vending machine Manufacturers and Suppliers
- Essential Technical Properties and Trade Terminology for starbucks vending machine
- Navigating Market Dynamics, Sourcing Trends, and Sustainability in the starbucks vending machine Sector
- Frequently Asked Questions (FAQs) for B2B Buyers of starbucks vending machine
- Strategic Sourcing Conclusion and Outlook for starbucks vending machine
Introduction: Navigating the Global Market for starbucks vending machine
In an era where convenience meets quality, the Starbucks vending machine stands out as a pivotal solution for businesses seeking to elevate their beverage offerings. As international B2B buyers from regions such as Africa, South America, the Middle East, and Europe (including Poland and Kenya) navigate the complexities of the global market, understanding the dynamics of this product is crucial. The Starbucks vending machine not only provides premium coffee experiences but also enhances customer satisfaction and operational efficiency.
This guide delves into the multifaceted world of Starbucks vending machines, addressing critical aspects such as the various types available, the materials used in their manufacturing, and the quality control measures that ensure consistent performance. Additionally, we will explore reliable suppliers, cost considerations, and market trends that are shaping the vending landscape.
Empowering informed sourcing decisions, this comprehensive resource is designed to help B2B buyers identify the best solutions tailored to their specific needs. Whether you are looking to penetrate new markets or enhance your current offerings, understanding the nuances of Starbucks vending machines can be a game-changer. With actionable insights and strategic guidance, this guide positions you to make decisions that not only meet customer demands but also drive business growth in an increasingly competitive environment.
Understanding starbucks vending machine Types and Variations
Type Name | Key Distinguishing Features | Primary B2B Applications | Brief Pros & Cons for Buyers |
---|---|---|---|
Traditional Vending Machines | Standard design with a selection of drinks | Offices, educational institutions | Pros: Familiarity, easy maintenance. Cons: Limited customization, slower service. |
High-Tech Touchscreen Models | Interactive screens with customizable options | Retail environments, airports | Pros: Engaging user experience, diverse offerings. Cons: Higher initial investment, tech support needed. |
Compact Vending Solutions | Space-efficient designs for limited spaces | Small offices, cafes, remote locations | Pros: Space-saving, cost-effective. Cons: Limited capacity, fewer options. |
Mobile Vending Units | Transportable units for events and festivals | Outdoor events, corporate gatherings | Pros: Flexibility, on-demand service. Cons: Requires logistical planning, weather-dependent. |
Specialty Beverage Machines | Focused on premium or unique beverage options | High-end venues, specialty shops | Pros: Niche market appeal, premium quality. Cons: Higher operating costs, target audience limitation. |
Traditional Vending Machines
Traditional Starbucks vending machines offer a classic approach to beverage dispensing, featuring a straightforward selection of popular drinks. These machines are well-suited for environments like offices and educational institutions where familiarity and ease of use are paramount. When considering a purchase, B2B buyers should evaluate the machine’s maintenance requirements and the available drink options, as these factors will impact user satisfaction and operational efficiency.
High-Tech Touchscreen Models
High-tech touchscreen models represent the cutting edge of vending technology, providing an interactive experience for users. These machines allow customers to customize their drinks and explore a broader range of offerings, making them ideal for retail environments and high-traffic areas such as airports. Buyers should consider the initial investment and ongoing tech support, as these machines require more upkeep than traditional models but can significantly enhance customer engagement.
Compact Vending Solutions
Compact vending machines are designed for spaces where real estate is at a premium, making them perfect for small offices, cafes, and remote locations. They maintain a selection of Starbucks beverages while maximizing space efficiency. B2B buyers should assess the capacity and variety of drinks offered, as limited space may restrict the range of available products, potentially affecting customer satisfaction.
Mobile Vending Units
Mobile vending units provide a flexible solution for serving Starbucks beverages at outdoor events and corporate gatherings. These transportable units can be set up quickly and cater to diverse customer needs. When purchasing, businesses should consider logistical factors such as transportation, setup time, and weather conditions, as these can impact service delivery and operational success.
Specialty Beverage Machines
Specialty beverage machines focus on delivering premium or unique Starbucks drink options, appealing to high-end venues and specialty shops. These machines can attract a niche market willing to pay more for quality. However, B2B buyers must be mindful of the higher operating costs and the specific target audience, ensuring that their investment aligns with their business model and customer demographics.
Related Video: Machine Learning in 2024 – Beginner’s Course
Key Industrial Applications of starbucks vending machine
Industry/Sector | Specific Application of Starbucks Vending Machine | Value/Benefit for the Business | Key Sourcing Considerations for this Application |
---|---|---|---|
Hospitality | Lobby or waiting area coffee service | Enhances guest experience, reduces wait times | Machine capacity, payment options, product variety |
Corporate Offices | Employee break rooms | Boosts employee morale and productivity | Reliability, maintenance support, coffee quality |
Educational Institutions | Campus convenience stores | Provides students with accessible quality beverages | Space requirements, user-friendly interface, product selection |
Transport Hubs | Airports and train stations coffee stations | Captures high foot traffic, increases sales | Location strategy, energy consumption, service frequency |
Retail | Shopping mall kiosks | Attracts customers, complements retail offerings | Branding options, machine aesthetics, integration with loyalty programs |
Hospitality Sector
In hotels and resorts, Starbucks vending machines can be strategically placed in lobbies or waiting areas to provide guests with immediate access to high-quality coffee. This not only enhances the guest experience by reducing wait times but also serves as a branding opportunity for the establishment. For international buyers, particularly in regions like Africa and the Middle East, it is crucial to consider the machine’s capacity and ability to handle local demand fluctuations. Additionally, payment options should cater to diverse customer preferences, including mobile payments, to maximize convenience.
Corporate Offices
In corporate environments, Starbucks vending machines serve as an excellent solution for employee break rooms, offering a range of beverages that can boost morale and productivity. Such machines can help companies in South America and Europe create a more inviting workplace. Buyers should prioritize reliability and maintenance support when sourcing these machines, as downtime can significantly affect employee satisfaction. Furthermore, ensuring that the coffee quality meets local tastes is essential for successful implementation.
Educational Institutions
Universities and colleges can benefit from installing Starbucks vending machines in campus convenience stores, providing students with quick access to quality beverages between classes. This application addresses the need for convenience and quality, particularly in regions like Africa, where student populations are rapidly growing. Buyers should focus on space requirements and ensure that the machines have a user-friendly interface to accommodate a diverse student body. Additionally, offering a variety of products can cater to different tastes and dietary restrictions.
Transport Hubs
Airports and train stations present high-foot-traffic environments where Starbucks vending machines can generate significant sales. By providing travelers with convenient access to quality coffee, businesses in the Middle East and Europe can capitalize on the transient nature of these locations. Key sourcing considerations include developing a strategic location plan and evaluating the energy consumption of the machines, as these factors can directly influence profitability. Moreover, service frequency should be optimized to ensure that machines are always stocked and operational.
Retail
In shopping malls, Starbucks vending machines can act as kiosks that attract customers and complement existing retail offerings. This application is particularly effective in regions like South America, where shopping experiences are increasingly focused on convenience. Retailers should consider branding options and the aesthetics of the machines to align with their overall store design. Integration with loyalty programs can further enhance customer engagement and drive repeat purchases, making it a worthwhile investment for retail environments.
Related Video: How to Start a Vending Machine Business, Cost, Tips, How Much You Make
Strategic Material Selection Guide for starbucks vending machine
When selecting materials for Starbucks vending machines, international B2B buyers must consider various factors that influence performance, durability, and compliance with regional standards. Below, we analyze four common materials used in the construction of these machines, highlighting their properties, advantages, disadvantages, and specific considerations for buyers from Africa, South America, the Middle East, and Europe.
Stainless Steel
Key Properties: Stainless steel is renowned for its excellent corrosion resistance, high strength-to-weight ratio, and ability to withstand high temperatures and pressures. Its non-reactive nature makes it suitable for food and beverage applications.
Pros & Cons: The durability of stainless steel is a significant advantage, as it can withstand harsh environments and frequent cleaning. However, it tends to be more expensive than other materials, and manufacturing processes can be complex, leading to longer lead times.
Impact on Application: Stainless steel is ideal for components that come into direct contact with beverages, ensuring that the taste and quality remain unaffected. It is compatible with various media, including hot water and coffee.
Considerations for International Buyers: Buyers should ensure compliance with food safety standards, such as FDA regulations in the U.S. or EU food safety directives. Stainless steel grades (e.g., 304 or 316) should be selected based on local climate conditions, especially in humid regions.
Aluminum
Key Properties: Aluminum is lightweight, has good corrosion resistance, and offers excellent thermal conductivity. It is also relatively easy to fabricate.
Pros & Cons: The primary advantage of aluminum is its low weight, which can reduce shipping costs and make installation easier. However, it is less durable than stainless steel and can be prone to denting and scratching.
Impact on Application: Aluminum is suitable for non-structural components and external panels of vending machines. Its thermal properties make it effective for heat dissipation in electronic components.
Considerations for International Buyers: Buyers must consider local regulations regarding aluminum usage, particularly in food contact applications. Standards such as ASTM B221 for aluminum extrusions should be adhered to, ensuring quality and safety.
Polycarbonate
Key Properties: Polycarbonate is a high-impact thermoplastic known for its clarity, strength, and resistance to UV radiation. It can withstand a wide range of temperatures.
Pros & Cons: The transparency of polycarbonate allows for attractive displays of products inside vending machines. However, it is less heat-resistant than metals and can be susceptible to scratching.
Impact on Application: Polycarbonate is commonly used for windows and display panels, providing visibility while protecting the contents from environmental factors. Its lightweight nature also contributes to overall energy efficiency.
Considerations for International Buyers: Buyers should check for compliance with regional plastics regulations, such as REACH in Europe. Additionally, understanding the specific grades of polycarbonate suitable for food contact is essential.
Mild Steel
Key Properties: Mild steel is characterized by its good tensile strength and ductility. It is less expensive than stainless steel and can be treated for corrosion resistance.
Pros & Cons: The cost-effectiveness of mild steel makes it an attractive option for structural components. However, it is prone to rusting if not properly coated or maintained, which can be a significant drawback in humid environments.
Impact on Application: Mild steel is often used for the frame and structural supports of vending machines. It can handle mechanical stress but requires protective coatings to ensure longevity.
Considerations for International Buyers: Buyers should be aware of local corrosion resistance standards and ensure that the mild steel used is appropriately treated. Compliance with standards such as ASTM A36 can help ensure quality.
Material | Typical Use Case for Starbucks Vending Machine | Key Advantage | Key Disadvantage/Limitation | Relative Cost (Low/Med/High) |
---|---|---|---|---|
Stainless Steel | Components in direct contact with beverages | Excellent corrosion resistance | Higher cost and manufacturing complexity | High |
Aluminum | External panels and non-structural components | Lightweight and easy to fabricate | Less durable, prone to dents | Medium |
Polycarbonate | Windows and display panels | High impact resistance and clarity | Less heat-resistant, scratches easily | Medium |
Mild Steel | Structural supports and frames | Cost-effective and strong | Prone to rust without treatment | Low |
This strategic material selection guide provides a comprehensive overview for international B2B buyers, helping them make informed decisions based on performance, cost, and regional compliance requirements.
In-depth Look: Manufacturing Processes and Quality Assurance for starbucks vending machine
Manufacturing Processes for Starbucks Vending Machines
The manufacturing process for Starbucks vending machines involves several critical stages that ensure both functionality and quality. Understanding these processes is vital for B2B buyers looking to invest in reliable and efficient vending solutions.
Main Stages of Manufacturing
-
Material Preparation
– The first step involves selecting high-quality materials suitable for vending machine construction. Common materials include stainless steel for the exterior, durable plastics for internal components, and electronic components for payment systems.
– Suppliers should provide certifications for materials to ensure compliance with international standards, especially regarding food safety and durability. -
Forming
– This stage includes shaping materials into the necessary components using techniques such as stamping, molding, and extrusion.
– Advanced technologies like CNC machining may be employed to achieve precise specifications. For B2B buyers, it’s crucial to inquire about the technology used, as it directly impacts the machine’s longevity and performance. -
Assembly
– The assembly process integrates all components, including the brewing system, refrigeration units, and electronic interfaces. This stage often utilizes automated assembly lines to enhance efficiency and reduce human error.
– Quality control measures are vital during assembly to ensure that each unit meets design specifications. B2B buyers should confirm that suppliers have trained personnel and automated systems to maintain high assembly standards. -
Finishing
– The final stage involves applying finishes that enhance aesthetic appeal and protect against wear. This may include powder coating, painting, or applying anti-corrosion treatments.
– Buyers should inquire about the types of finishes used, as they can affect the machine’s resilience, especially in diverse climates found in regions like Africa or South America.
Quality Assurance in Manufacturing
Quality assurance (QA) is a crucial aspect of the manufacturing process, ensuring that each vending machine meets stringent operational standards.
Relevant International Standards
- ISO 9001: This standard focuses on quality management systems and is essential for manufacturers to demonstrate their commitment to quality. Buyers should prioritize suppliers with ISO 9001 certification, indicating a systematic approach to quality management.
- CE Marking: This European conformity marking signifies compliance with health, safety, and environmental protection standards. For buyers in Europe, especially Poland, CE marking is often mandatory.
- API Certification: For components related to food and beverage dispensing, API standards ensure safety and quality. This is particularly relevant for regions where food safety regulations are stringent.
Quality Control Checkpoints
-
Incoming Quality Control (IQC)
– This initial checkpoint assesses the quality of raw materials and components before they enter the production line. It ensures that only materials that meet specified standards are used.
– B2B buyers should request IQC reports to verify that their suppliers maintain rigorous material quality assessments. -
In-Process Quality Control (IPQC)
– Continuous monitoring during the assembly process helps identify defects early. Techniques such as visual inspections and automated testing are common.
– Suppliers should provide documentation of IPQC activities, which can be reviewed by buyers to ensure adherence to quality standards throughout production. -
Final Quality Control (FQC)
– The FQC stage involves comprehensive testing of the finished vending machines. This may include performance tests, safety checks, and aesthetic evaluations.
– Buyers should ask for FQC reports and any certifications obtained during this stage, as they provide insights into the reliability of the vending machines.
Common Testing Methods
- Functional Testing: Ensures that all machine features operate correctly, including payment systems and beverage dispensing.
- Stress Testing: Assesses the machine’s durability under various conditions, simulating real-world usage.
- Compliance Testing: Validates that the machine meets all regulatory standards relevant to the target market.
Verifying Supplier Quality Control
For international B2B buyers, especially those from Africa, South America, the Middle East, and Europe, verifying supplier quality control is paramount. Here are some actionable strategies:
- Conduct Audits: Regularly auditing suppliers can provide an in-depth view of their manufacturing processes and quality management systems. This is essential for understanding their commitment to quality.
- Request Documentation: Buyers should ask for quality assurance documents, including IQC, IPQC, and FQC reports. These documents serve as proof of adherence to quality standards.
- Third-Party Inspections: Engaging third-party inspection services can provide unbiased assessments of the manufacturing process and product quality. This is particularly useful for buyers unfamiliar with local manufacturing practices.
QC and Certification Nuances for International Buyers
Understanding the nuances of quality control and certification is crucial for B2B buyers operating in diverse markets:
- Regional Regulations: Different regions have unique regulatory requirements. Buyers from Africa or South America should familiarize themselves with local standards, which may differ from those in Europe or the Middle East.
- Cultural Considerations: Cultural attitudes towards quality and compliance may vary, influencing supplier reliability. Buyers should consider these factors when selecting suppliers.
- Documentation and Traceability: Ensuring that suppliers maintain detailed documentation and traceability of all components can help mitigate risks associated with quality issues. Buyers should prioritize suppliers who can demonstrate strong traceability practices.
In conclusion, a comprehensive understanding of the manufacturing processes and quality assurance practices for Starbucks vending machines enables international B2B buyers to make informed decisions. By focusing on verified suppliers with robust quality management systems, buyers can ensure they invest in reliable vending solutions that meet both operational and regulatory standards.
Related Video: SMART Quality Control for Manufacturing
Comprehensive Cost and Pricing Analysis for starbucks vending machine Sourcing
When considering the sourcing of Starbucks vending machines, B2B buyers must navigate a multifaceted cost structure that influences pricing. Understanding the key components and the factors that affect them is essential for making informed purchasing decisions.
Cost Components
-
Materials: The primary materials used in vending machines include metal, plastic, and electronic components. The cost of these materials can fluctuate based on global supply chain dynamics, currency exchange rates, and local availability. Buyers should consider sourcing materials from regions with lower costs or stable supply chains to mitigate price volatility.
-
Labor: Labor costs can vary significantly based on the manufacturing location. Countries with lower labor costs, such as those in parts of Africa and South America, may offer competitive pricing. However, it’s crucial to ensure that labor practices comply with international standards, as this can impact the brand reputation.
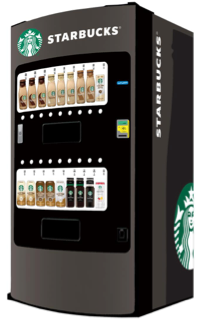
Illustrative Image (Source: Google Search)
-
Manufacturing Overhead: This includes expenses related to factory operations, utilities, and administrative costs. Understanding a supplier’s overhead structure can provide insights into their pricing strategies. Efficient manufacturers may pass on cost savings to buyers.
-
Tooling: Custom vending machines often require specific tooling, which can be a substantial upfront cost. Buyers looking for unique designs or functionalities should factor in these expenses, as they can significantly affect the overall price.
-
Quality Control (QC): Implementing robust QC measures is essential for ensuring product reliability and performance. Buyers should inquire about a supplier’s QC processes, as high-quality standards may come with increased costs but ultimately lead to better long-term value.
-
Logistics: The cost of transporting vending machines can be a significant part of the total cost. This includes shipping, customs duties, and insurance. Buyers should consider Incoterms that minimize risk and cost, such as DDP (Delivered Duty Paid), where the seller assumes responsibility for logistics.
-
Margin: Suppliers will include a profit margin in their pricing. This can vary based on the supplier’s market positioning and the perceived value of their product. Understanding the competitive landscape can provide leverage in negotiations.
Price Influencers
Several factors influence the final price of Starbucks vending machines:
-
Volume/MOQ: Larger orders often qualify for volume discounts. B2B buyers should assess their long-term needs to leverage better pricing through minimum order quantities (MOQ).
-
Specifications/Customization: Custom features can increase costs. Buyers should clearly define their requirements to avoid unnecessary expenses.
-
Materials and Quality/Certifications: Higher quality materials and certifications (e.g., ISO, CE) can enhance the machine’s reliability but also increase the price. Buyers must balance quality with budget constraints.
-
Supplier Factors: The reputation, experience, and production capabilities of suppliers can affect pricing. Established suppliers may charge a premium for their proven track record.
-
Incoterms: The choice of Incoterms can impact costs significantly. Understanding the responsibilities of both buyer and seller can help manage logistics expenses and risks effectively.
Buyer Tips
-
Negotiation: Always negotiate pricing and terms. Suppliers often have room for flexibility, especially for bulk orders or long-term contracts.
-
Cost-Efficiency: Look beyond the sticker price. Evaluate the Total Cost of Ownership (TCO), which includes maintenance, operational efficiency, and potential downtime costs.
-
Pricing Nuances for International Buyers: Buyers from Africa, South America, the Middle East, and Europe should be aware of regional market conditions that can affect pricing. Currency fluctuations, local tariffs, and trade agreements may influence the overall cost.
-
Disclaimer for Indicative Prices: Prices can vary widely based on market conditions, supplier negotiations, and other factors. Buyers should conduct thorough research and obtain multiple quotes to ensure they receive competitive pricing.
In summary, a comprehensive understanding of the cost components and pricing influencers for Starbucks vending machines can empower international B2B buyers to make informed decisions, ultimately leading to more successful sourcing outcomes.
Spotlight on Potential starbucks vending machine Manufacturers and Suppliers
- (No specific manufacturer data was available or requested for detailed profiling in this section for starbucks vending machine.)*
Essential Technical Properties and Trade Terminology for starbucks vending machine
Essential Technical Properties for Starbucks Vending Machines
When evaluating Starbucks vending machines for international procurement, understanding their essential technical properties is crucial for making informed decisions. Below are key specifications that buyers should consider:
-
Material Grade
The material grade refers to the quality and type of materials used in the construction of the vending machine. Common materials include stainless steel and high-grade plastics, which offer durability and resistance to corrosion. For B2B buyers, selecting machines made from high-quality materials ensures longevity and reduces maintenance costs, especially in diverse climates found in Africa, South America, and the Middle East. -
Power Consumption
Power consumption is a critical specification that indicates how much electricity the vending machine requires to operate effectively. Understanding this metric helps buyers estimate operational costs and determine compatibility with local power supply standards. Machines with lower energy consumption are particularly advantageous in regions where energy costs are high. -
Capacity and Dimensions
The capacity of a vending machine refers to the number of products it can store and dispense at one time. Dimensions are equally important as they dictate the space required for installation. Buyers need to assess their location constraints and anticipated customer volume to select a machine that meets their needs without taking up excessive space. -
User Interface
The user interface includes elements such as touchscreen displays, payment systems (e.g., cash, card, mobile payments), and language options. A user-friendly interface can significantly enhance customer experience, which is essential for maximizing sales. For B2B buyers, investing in machines with intuitive interfaces can lead to higher customer satisfaction and repeat business. -
Temperature Control
Effective temperature control is vital for maintaining the quality of beverages, especially in warmer climates. This property ensures that drinks are served at optimal temperatures, enhancing the overall product experience. Buyers should prioritize machines that incorporate advanced temperature regulation technologies to avoid spoilage and ensure customer satisfaction.
Common Trade Terminology
Understanding industry jargon is essential for navigating the procurement process effectively. Here are some common terms that B2B buyers should be familiar with:
-
OEM (Original Equipment Manufacturer)
This term refers to a company that produces parts or equipment that may be marketed by another manufacturer. In the context of vending machines, knowing whether you are dealing with an OEM can affect warranty, service options, and product reliability. Buyers should verify the OEM’s reputation and support services. -
MOQ (Minimum Order Quantity)
MOQ denotes the smallest quantity of a product that a supplier is willing to sell. Understanding MOQ is crucial for budgeting and inventory management. Buyers should negotiate MOQs that align with their operational needs without overcommitting resources. -
RFQ (Request for Quotation)
An RFQ is a document sent to suppliers requesting pricing and terms for specific products or services. It is an essential tool for B2B buyers to obtain competitive pricing and assess different vendors. Crafting a detailed RFQ can help streamline the procurement process and ensure all necessary specifications are covered. -
Incoterms (International Commercial Terms)
Incoterms are internationally recognized standard trade terms that define the responsibilities of buyers and sellers in international transactions. Familiarity with these terms can prevent misunderstandings regarding shipping, insurance, and liability. Buyers should ensure they understand the applicable Incoterms in their agreements to mitigate risks. -
Lead Time
Lead time refers to the amount of time from placing an order to receiving the product. Knowing the lead time is essential for planning and inventory management. B2B buyers should inquire about lead times during negotiations to align with their operational timelines.
By understanding these technical properties and trade terminologies, international B2B buyers can make well-informed decisions when sourcing Starbucks vending machines, ensuring they meet operational demands and customer expectations.
Navigating Market Dynamics, Sourcing Trends, and Sustainability in the starbucks vending machine Sector
Market Overview & Key Trends
The Starbucks vending machine sector is witnessing significant growth fueled by changing consumer preferences and technological advancements. Global drivers include the increasing demand for convenience and premium coffee experiences, particularly in urban areas across Africa, South America, the Middle East, and Europe. B2B buyers should note that the rise of the “on-the-go” culture is prompting businesses to seek innovative solutions like vending machines that deliver high-quality beverages quickly and efficiently.
Emerging trends in B2B tech involve the integration of IoT (Internet of Things) capabilities into vending machines. These smart machines offer real-time data analytics, allowing businesses to monitor inventory levels, customer preferences, and machine performance. This tech-savvy approach not only enhances operational efficiency but also improves customer satisfaction by ensuring product availability and freshness. Additionally, mobile payment options are becoming standard, reflecting a shift towards cashless transactions, which is particularly relevant for international buyers in regions like Europe and the Middle East.
Market dynamics also suggest a growing emphasis on localized sourcing and partnerships. B2B buyers are encouraged to engage with local suppliers to enhance supply chain resilience while also catering to regional tastes. For instance, in Africa and South America, incorporating locally sourced ingredients can differentiate offerings and appeal to the consumer’s preference for authenticity. Understanding these market trends is crucial for international buyers looking to capitalize on the growing demand for Starbucks vending machines.
Sustainability & Ethical Sourcing in B2B
As environmental concerns become increasingly prominent, the Starbucks vending machine sector is under pressure to adopt sustainable practices. B2B buyers must prioritize suppliers who demonstrate a commitment to reducing their environmental impact. This includes evaluating the energy efficiency of vending machines and the carbon footprint associated with their operation and maintenance. Choosing machines powered by renewable energy sources can significantly reduce overall emissions.
Moreover, ethical sourcing is a vital aspect of sustainability that B2B buyers should consider. Engaging with suppliers who adhere to fair trade practices ensures that coffee beans and other ingredients are sourced responsibly, supporting farmers and communities. Certifications such as Fair Trade and Rainforest Alliance are indicators of ethical practices that resonate with socially conscious consumers. Buyers should actively seek out vending machine suppliers who prioritize these certifications, as they not only align with sustainability goals but also enhance brand reputation.
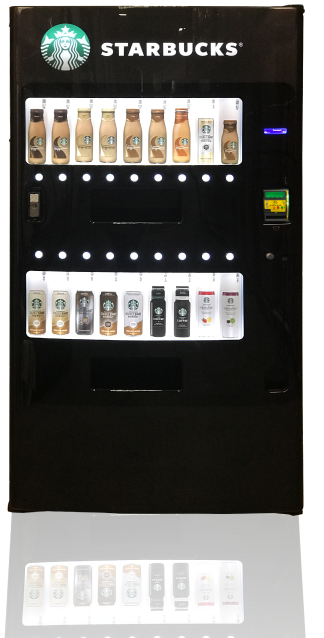
Illustrative Image (Source: Google Search)
Incorporating ‘green’ materials into vending machine design—such as recycled plastics and biodegradable components—can further bolster a company’s sustainability credentials. Buyers should inquire about the lifecycle of vending machines and the materials used, ensuring that their investments contribute positively to environmental sustainability.
Brief Evolution/History
The concept of vending machines has evolved significantly since their inception in the early 20th century. Initially offering simple snacks and beverages, the introduction of premium brands like Starbucks into the vending machine sector marked a pivotal shift. This evolution has been characterized by advancements in technology, such as cashless payment systems and sophisticated inventory management, allowing for a more personalized consumer experience.
As coffee culture has grown globally, especially in urban centers, the demand for high-quality, on-the-go options has surged. Starbucks vending machines have adapted to this trend by offering a diverse range of beverages, from classic coffees to seasonal specialties. This evolution reflects a broader change in consumer expectations, where convenience must be paired with quality, making it essential for B2B buyers to stay informed about ongoing developments in this dynamic sector.
Related Video: Is global trade transforming? | Counting the Cost
Frequently Asked Questions (FAQs) for B2B Buyers of starbucks vending machine
-
What should I consider when vetting suppliers for Starbucks vending machines?
When vetting suppliers, prioritize their experience with vending machines and their specific relationship with Starbucks. Check for certifications and compliance with international standards, especially for your region. Ask for references and case studies that demonstrate their capability in managing logistics and after-sales support. It’s also wise to conduct site visits or virtual meetings to assess their operations and ensure they can meet your quality expectations. -
Can I customize the Starbucks vending machine to fit my brand?
Yes, many suppliers offer customization options for Starbucks vending machines. You can request branding elements such as logos, colors, and packaging designs. Discuss your specific needs with potential suppliers to understand the extent of customization available. Keep in mind that extensive customizations may impact lead times and costs, so ensure you have a clear agreement on what can be achieved within your budget. -
What are the minimum order quantities (MOQ) and lead times for Starbucks vending machines?
Minimum order quantities vary by supplier and region, but typically they range from 5 to 50 units. Lead times can also differ significantly based on order size and customization requirements, often ranging from 6 to 12 weeks. Always clarify these details upfront to avoid any surprises. Additionally, consider your market demand to ensure that your order size aligns with your business strategy. -
What payment terms should I expect when sourcing from international suppliers?
Payment terms can vary widely, but common practices include upfront deposits (usually 30-50%) with the balance due upon delivery or after installation. Some suppliers may offer letters of credit or escrow services for added security. It’s essential to negotiate terms that protect your interests while being flexible enough to meet the supplier’s needs. Ensure that all payment agreements are documented to avoid disputes later. -
What quality assurance measures should I look for in a supplier?
Look for suppliers who adhere to international quality standards such as ISO certifications. Ask about their quality control processes, including testing procedures for the machines before shipment. Request documentation of these processes, as well as any warranties or guarantees they provide. A reputable supplier should be willing to share their QA protocols to ensure you receive reliable and high-quality products. -
What certifications should the vending machines have for international trade?
Ensure that the vending machines comply with the relevant health and safety regulations in your target market. Certifications such as CE marking in Europe or FDA approval in the U.S. can be important indicators of compliance. Additionally, check for energy efficiency ratings and other environmental certifications that may be mandatory in your region. This not only ensures compliance but can also enhance your brand’s reputation. -
How can I handle disputes with suppliers effectively?
To manage disputes effectively, establish clear contracts outlining terms, responsibilities, and dispute resolution processes before any transactions occur. Include clauses for mediation or arbitration to avoid lengthy legal battles. Maintain open communication with your supplier to resolve issues amicably. If a dispute arises, document all interactions and agreements to support your case in negotiations or formal proceedings. -
What logistics considerations should I keep in mind when importing Starbucks vending machines?
Logistics are critical when importing vending machines. Consider the shipping methods available, such as air freight or sea freight, and their associated costs and transit times. Ensure that your supplier has experience in international shipping and can handle customs clearance. Additionally, assess the storage and installation requirements upon arrival, as well as the potential need for local service support to maintain the machines effectively.
Strategic Sourcing Conclusion and Outlook for starbucks vending machine
In summary, strategic sourcing for Starbucks vending machines presents a compelling opportunity for international B2B buyers seeking to enhance their beverage offerings. By understanding local market dynamics and consumer preferences, businesses in Africa, South America, the Middle East, and Europe can effectively align their procurement strategies to maximize value. Key takeaways include the importance of supplier relationships, the necessity of adapting to regional tastes, and the potential for leveraging technology to streamline operations.
Investing in Starbucks vending machines not only enhances brand appeal but also meets the growing demand for convenient, high-quality coffee solutions. As markets evolve, maintaining flexibility in sourcing strategies will be crucial. Buyers should prioritize partnerships with reliable suppliers who can provide consistent quality and support.
Looking ahead, the expansion of Starbucks vending solutions is poised to grow, driven by urbanization and changing consumer behaviors. Now is the time to act. By embracing strategic sourcing, businesses can position themselves at the forefront of this trend, ensuring they remain competitive in a rapidly changing landscape. Engage with suppliers today to explore how Starbucks vending machines can elevate your business offerings and satisfy the evolving needs of your customers.