Your Ultimate Guide to Sourcing Soft Serve Ice Cream
Guide to Soft Serve Ice Cream Vending Machine
- Introduction: Navigating the Global Market for soft serve ice cream vending machine
- Understanding soft serve ice cream vending machine Types and Variations
- Key Industrial Applications of soft serve ice cream vending machine
- Strategic Material Selection Guide for soft serve ice cream vending machine
- In-depth Look: Manufacturing Processes and Quality Assurance for soft serve ice cream vending machine
- Comprehensive Cost and Pricing Analysis for soft serve ice cream vending machine Sourcing
- Spotlight on Potential soft serve ice cream vending machine Manufacturers and Suppliers
- Essential Technical Properties and Trade Terminology for soft serve ice cream vending machine
- Navigating Market Dynamics, Sourcing Trends, and Sustainability in the soft serve ice cream vending machine Sector
- Frequently Asked Questions (FAQs) for B2B Buyers of soft serve ice cream vending machine
- Strategic Sourcing Conclusion and Outlook for soft serve ice cream vending machine
Introduction: Navigating the Global Market for soft serve ice cream vending machine
In today’s dynamic global market, the demand for soft serve ice cream vending machines is surging, driven by changing consumer preferences and the need for convenient, on-the-go dessert options. These innovative machines not only provide a delightful treat but also represent a profitable business opportunity for international B2B buyers. Whether operating in bustling urban centers or vibrant tourist hotspots, businesses can leverage soft serve ice cream vending machines to attract customers and enhance their service offerings.
This comprehensive guide is designed to empower B2B buyers from regions such as Africa, South America, the Middle East, and Europe—including key markets like Brazil and Colombia. It delves into the various types of soft serve ice cream vending machines available, examining their materials, manufacturing processes, and quality control standards. Buyers will gain insights into identifying reliable suppliers and understanding cost structures, enabling them to make informed purchasing decisions.
Additionally, the guide addresses frequently asked questions, equipping buyers with the knowledge to navigate the complexities of sourcing and operating these machines. By providing a holistic view of the market landscape, this resource serves as a strategic tool for businesses looking to capitalize on the lucrative soft serve ice cream segment. With the right insights, international buyers can enhance their competitive edge and successfully integrate these machines into their business models.
Understanding soft serve ice cream vending machine Types and Variations
Type Name | Key Distinguishing Features | Primary B2B Applications | Brief Pros & Cons for Buyers |
---|---|---|---|
Traditional Soft Serve Machine | Manual operation with a single flavor output | Ice cream shops, events | Pros: Cost-effective, simple design. Cons: Limited flavor variety, labor-intensive. |
Multi-Flavor Soft Serve Machine | Allows for multiple flavors and combinations | Amusement parks, food trucks | Pros: Versatile, attracts diverse customers. Cons: Higher maintenance, more complex operation. |
Self-Service Soft Serve Kiosk | Automated dispensing with user control | Shopping malls, convenience stores | Pros: Reduces labor costs, enhances customer experience. Cons: Initial investment can be high, requires regular maintenance. |
Mobile Soft Serve Cart | Portable setup for outdoor events | Festivals, fairs | Pros: Flexibility in location, lower overhead costs. Cons: Limited capacity, weather-dependent. |
Compact Tabletop Soft Serve Machine | Space-saving design suitable for small venues | Cafes, small restaurants | Pros: Ideal for limited spaces, easy to operate. Cons: Lower output, may not meet high demand. |
Traditional Soft Serve Machine
Traditional soft serve machines are typically manual and designed to produce a single flavor of ice cream. They are widely used in smaller ice cream shops and events where simplicity and cost-effectiveness are key. When considering this type, buyers should evaluate their expected volume of sales and whether a single flavor offering aligns with their customer preferences. While these machines are straightforward and less expensive, they may not meet the demands of high-traffic venues.
Multi-Flavor Soft Serve Machine
This type of machine provides the ability to serve multiple flavors, often with swirled combinations. Ideal for amusement parks and food trucks, these machines cater to a wide range of customer tastes, making them a popular choice for businesses looking to attract a diverse clientele. However, potential buyers should be aware of the increased maintenance requirements and the complexity of operation, which may necessitate additional staff training.
Self-Service Soft Serve Kiosk
Self-service kiosks allow customers to dispense their own ice cream, providing a unique and interactive experience. Commonly found in shopping malls and convenience stores, these machines can significantly reduce labor costs and improve customer satisfaction. However, the initial investment can be substantial, and regular maintenance is crucial to ensure hygiene and operational efficiency. Businesses must assess their target market to determine if this model suits their service style.
Mobile Soft Serve Cart
Mobile soft serve carts are perfect for outdoor events, allowing vendors to easily transport their offerings to various locations. This flexibility makes them ideal for festivals and fairs, where foot traffic can be unpredictable. While they have lower overhead costs compared to fixed locations, buyers should consider their limited capacity and the potential impact of weather on sales. Proper planning for events and locations is essential for maximizing profitability.
Compact Tabletop Soft Serve Machine
Designed for small venues like cafes and small restaurants, compact tabletop machines save space while still delivering quality soft serve. They are easy to operate and maintain, making them suitable for businesses with limited staff. However, buyers should keep in mind that these machines may not produce enough output to satisfy high demand during peak hours. Assessing the expected customer flow and demand is crucial for ensuring that this type of machine will meet business needs effectively.
Related Video: Soft serve ice cream machine PROTELEX
Key Industrial Applications of soft serve ice cream vending machine
Industry/Sector | Specific Application of soft serve ice cream vending machine | Value/Benefit for the Business | Key Sourcing Considerations for this Application |
---|---|---|---|
Hospitality & Food Service | Self-service ice cream stations in hotels and restaurants | Enhances guest experience, increases dessert sales | Machine capacity, ease of use, flavor variety |
Retail | Vending machines in shopping malls and supermarkets | Attracts foot traffic, boosts impulse purchases | Location, payment options, machine reliability |
Education | Ice cream vending in schools and universities | Provides a fun treat for students, increases revenue | Health regulations, machine hygiene standards, flavor options |
Healthcare | Soft serve machines in hospitals and care facilities | Offers comfort food for patients, promotes satisfaction | Compliance with health standards, ease of cleaning, ingredient sourcing |
Events & Catering | Portable soft serve machines for events and festivals | Adds value to catering services, customizable options | Portability, setup time, power requirements |
Hospitality & Food Service
In the hospitality sector, soft serve ice cream vending machines can be strategically placed in hotels and restaurants as self-service stations. This application enhances the guest experience by providing a customizable dessert option that can cater to various tastes. Additionally, it can significantly increase dessert sales, especially during peak dining hours. Buyers in this sector should consider machine capacity, ease of use, and the variety of flavors offered to ensure they meet customer expectations.
Retail
In retail environments such as shopping malls and supermarkets, soft serve ice cream vending machines serve as a key attraction. These machines can boost impulse purchases, drawing foot traffic and encouraging customers to linger longer. For international buyers, particularly in regions like Africa and South America, understanding the local consumer behavior and preferences is crucial. Key sourcing considerations include the machine’s location, payment options (including cashless payments), and overall reliability to ensure consistent service.
Education
Soft serve ice cream vending machines in educational institutions like schools and universities provide a delightful treat for students, contributing to a positive campus atmosphere. These machines can also serve as a revenue stream for educational facilities. Buyers must navigate health regulations and machine hygiene standards, especially when catering to younger audiences. Flavor options should also be diverse to accommodate various dietary needs and preferences.
Healthcare
In healthcare settings, such as hospitals and care facilities, soft serve ice cream machines can offer patients comfort food, enhancing their overall satisfaction during recovery. These machines can be particularly beneficial in pediatric wards or long-term care facilities where patients may appreciate a sweet treat. Buyers in this sector need to ensure compliance with health standards, prioritize ease of cleaning, and source quality ingredients that align with dietary restrictions.
Events & Catering
Portable soft serve ice cream machines are ideal for events and catering services, allowing for customizable dessert options at festivals, weddings, and corporate events. This application adds significant value to catering offerings, providing guests with a unique experience. Buyers should consider the machine’s portability, setup time, and power requirements to ensure seamless operation during events, particularly in diverse international settings.
Related Video: Operating the Vevor Soft Serve ice cream machine
Strategic Material Selection Guide for soft serve ice cream vending machine
When selecting materials for soft serve ice cream vending machines, it is crucial to consider properties that directly impact performance, durability, and compliance with international standards. Below is an analysis of four common materials used in the construction of these machines.
Stainless Steel
Key Properties:
Stainless steel is known for its excellent corrosion resistance, high strength, and ability to withstand high temperatures and pressures. Its non-reactive nature makes it ideal for food applications.
Pros & Cons:
Stainless steel is durable and easy to clean, making it suitable for hygiene-sensitive environments. However, it is more expensive than other materials and can be challenging to machine, which may increase manufacturing complexity.
Impact on Application:
Due to its corrosion resistance, stainless steel is compatible with various cleaning agents and food products. It is particularly well-suited for areas exposed to moisture and temperature fluctuations.
Considerations for International Buyers:
Buyers should ensure that the stainless steel grades meet local and international standards such as ASTM A240 or DIN EN 10088. In regions like Africa and South America, the availability of specific grades may vary, impacting sourcing decisions.
Aluminum
Key Properties:
Aluminum is lightweight, has good thermal conductivity, and is resistant to corrosion, especially when anodized. It can also withstand moderate temperatures and pressures.
Pros & Cons:
The main advantage of aluminum is its low weight, which facilitates easier handling and installation. However, it is less durable than stainless steel and can be prone to denting and scratching. Additionally, it may require protective coatings to enhance its longevity.
Impact on Application:
Aluminum is suitable for components that do not come into direct contact with ice cream, such as frames and supports. Its thermal properties can also help in maintaining temperature control in the machine.
Considerations for International Buyers:
Buyers should consider the local availability of aluminum grades and whether they comply with standards such as ASTM B221. In regions like the Middle East, where high temperatures are common, ensuring adequate thermal management is essential.
Polycarbonate
Key Properties:
Polycarbonate is a strong, transparent thermoplastic known for its impact resistance and clarity. It can withstand moderate temperatures but is less effective against high heat and pressure.
Pros & Cons:
This material is lightweight and provides excellent visibility for product displays. However, it is susceptible to scratching and may not be as durable as metals. Its chemical resistance is also limited compared to metals.
Impact on Application:
Polycarbonate is often used for protective covers and display panels in vending machines. Its transparency allows customers to see the product, enhancing sales potential.
Considerations for International Buyers:
When sourcing polycarbonate, buyers should verify compliance with food safety regulations in their respective regions. In Europe, for example, materials must meet EU regulations regarding food contact safety.
Food-Grade Plastic
Key Properties:
Food-grade plastics, such as HDPE and polypropylene, are designed to be safe for food contact. They are lightweight, resistant to moisture, and can withstand a range of temperatures.
Pros & Cons:
These plastics are cost-effective and easy to mold into complex shapes, making them suitable for various components. However, they may not have the same strength or longevity as metals and can be affected by UV exposure over time.
Impact on Application:
Food-grade plastics are often used for internal components that come into direct contact with ice cream, such as hoppers and dispensing nozzles. Their moisture resistance is crucial for maintaining product quality.
Considerations for International Buyers:
Buyers should ensure that food-grade plastics comply with standards such as FDA regulations in the U.S. or EU food safety standards. Availability may vary by region, impacting sourcing strategies.
Summary Table
Material | Typical Use Case for soft serve ice cream vending machine | Key Advantage | Key Disadvantage/Limitation | Relative Cost (Low/Med/High) |
---|---|---|---|---|
Stainless Steel | Machine body and internal components | Excellent durability and corrosion resistance | Higher cost, manufacturing complexity | High |
Aluminum | Frames and non-contact components | Lightweight, good thermal conductivity | Less durable, prone to dents | Medium |
Polycarbonate | Protective covers and display panels | Impact-resistant, good visibility | Susceptible to scratching, limited durability | Medium |
Food-Grade Plastic | Hoppers and dispensing nozzles | Cost-effective, easy to mold | Lower strength, UV sensitivity | Low |
This strategic material selection guide provides international B2B buyers with essential insights into the materials used in soft serve ice cream vending machines, helping them make informed decisions that align with their operational needs and regional compliance requirements.
In-depth Look: Manufacturing Processes and Quality Assurance for soft serve ice cream vending machine
The manufacturing of soft serve ice cream vending machines involves several critical processes that ensure both functionality and compliance with quality standards. Understanding these processes is essential for B2B buyers looking to procure reliable equipment. Below is a comprehensive overview of the typical manufacturing stages and quality assurance measures relevant to these machines.
Manufacturing Processes
1. Material Preparation
The first step in the manufacturing process involves selecting and preparing materials. Common materials include:
- Stainless Steel: For the exterior and internal components, chosen for its durability and resistance to corrosion.
- Plastics: Used for certain components like hoppers and panels, which require lightweight and non-reactive materials.
- Insulation Materials: Essential for maintaining optimal temperature during storage and serving.
Material quality is assessed through visual inspections and material certifications, ensuring that all components meet the required specifications.
2. Forming
In this stage, raw materials are shaped into specific components through various techniques:
- Metal Fabrication: Techniques such as laser cutting, bending, and welding are employed to form the chassis and structural elements of the machine.
- Injection Molding: Used for plastic components, allowing for precise shapes and lightweight construction.
- Sheet Metal Forming: This includes processes like stamping and deep drawing to create the outer casing and internal supports.
Precision in forming is critical as it impacts the machine’s overall performance and durability.
3. Assembly
Once components are formed, they undergo assembly, which involves:
- Mechanical Assembly: Components are assembled using screws, bolts, and other fasteners. This stage often includes the installation of motors, compressors, and refrigeration systems.
- Electrical Assembly: Wiring and electrical components are installed, ensuring proper connectivity and functionality of control panels and user interfaces.
During assembly, manufacturers often use jigs and fixtures to ensure alignment and repeatability, which is crucial for maintaining quality across multiple units.
4. Finishing
The finishing stage includes processes that enhance the aesthetic and functional qualities of the machine:
- Surface Treatment: Techniques such as polishing, powder coating, or painting are applied to improve appearance and protect against environmental factors.
- Quality Control Checks: Final inspections are conducted to ensure that all components are functioning as intended.
This stage is pivotal for both the longevity of the machine and customer satisfaction.
Quality Assurance
Quality assurance is integral to the manufacturing process, ensuring that the machines meet international and industry-specific standards. Here are the key elements:
International Standards
B2B buyers should be aware of relevant quality standards, including:
- ISO 9001: This standard focuses on quality management systems and is crucial for manufacturers aiming to provide consistent quality in their products.
- CE Marking: Indicates compliance with European health, safety, and environmental protection standards, often required for machines sold in the European market.
- API Standards: Relevant for components that may involve refrigeration systems, ensuring safety and efficiency.
Quality Control Checkpoints
Quality control is typically structured around several key checkpoints:
- Incoming Quality Control (IQC): Materials and components are inspected upon arrival at the manufacturing facility to ensure they meet specifications.
- In-Process Quality Control (IPQC): Inspections during manufacturing processes help catch defects early, reducing waste and rework.
- Final Quality Control (FQC): A comprehensive check is performed on the completed machine to ensure all systems operate correctly and meet standards before shipment.
Common Testing Methods
Manufacturers employ various testing methods to validate machine performance:
- Functional Testing: Ensures that the machine operates as designed, including freezing and dispensing capabilities.
- Safety Testing: Assess electrical and mechanical safety, including emergency shut-off mechanisms and insulation integrity.
- Durability Testing: Simulates extended use to identify potential failure points.
Verifying Supplier Quality Control
B2B buyers must take proactive steps to verify supplier quality control measures:
- Supplier Audits: Conducting audits of suppliers’ manufacturing facilities can provide insights into their quality management practices and compliance with standards.
- Requesting Quality Reports: Buyers should ask for detailed quality assurance reports, including results from IQC, IPQC, and FQC stages.
- Third-Party Inspections: Engaging independent inspection services can provide unbiased assessments of product quality and compliance with international standards.
Quality Control Nuances for International Buyers
B2B buyers from regions like Africa, South America, the Middle East, and Europe should consider specific nuances:
- Regulatory Compliance: Understanding local regulations regarding food safety and equipment standards is crucial, as compliance may vary significantly by region.
- Logistical Considerations: Shipping and customs regulations may affect the certification and warranty of the equipment, so buyers should ensure that their suppliers are familiar with these requirements.
- Cultural Differences: Communication styles and negotiation practices can differ across regions, impacting supplier relationships. Establishing clear expectations and maintaining open lines of communication is vital.
By understanding the manufacturing processes and quality assurance protocols of soft serve ice cream vending machines, B2B buyers can make informed decisions, ensuring they select reliable suppliers who meet their specific needs and standards.
Related Video: INSIDE THE FACTORY HÄAGEN DAZS ICE CREAM MAKING MACHINES
Comprehensive Cost and Pricing Analysis for soft serve ice cream vending machine Sourcing
In the competitive landscape of soft serve ice cream vending machines, understanding the comprehensive cost structure and pricing dynamics is crucial for international B2B buyers, especially those operating in diverse markets such as Africa, South America, the Middle East, and Europe.
Cost Components
-
Materials: The primary materials include stainless steel for the machine body, refrigeration components, and electronic controls. High-quality materials may increase initial costs but lead to better durability and performance.
-
Labor: Labor costs encompass wages for manufacturing workers, engineers, and technicians involved in the production process. In regions with higher labor costs, such as parts of Europe, the overall price may reflect these expenses.
-
Manufacturing Overhead: This includes costs related to utilities, facility maintenance, and indirect labor. Efficient manufacturing processes can help reduce these overhead costs, impacting the final pricing of machines.
-
Tooling: The cost of molds and tools for production can be significant, particularly for custom designs. Investing in high-quality tooling can lead to better product consistency and longevity.
-
Quality Control (QC): Rigorous QC processes ensure that machines meet safety and operational standards. While this adds to costs, it is essential for maintaining product reliability and customer satisfaction.
-
Logistics: Shipping costs vary significantly depending on the origin and destination of the machines. Factors such as distance, mode of transportation, and tariffs can all influence logistics costs.
-
Margin: Suppliers typically add a profit margin to cover their costs and ensure profitability. This margin can vary based on the supplier’s market position and competitiveness.
Price Influencers
-
Volume/MOQ: Buying in larger quantities often results in lower per-unit prices due to economies of scale. Understanding minimum order quantities (MOQ) can help buyers negotiate better deals.
-
Specifications/Customization: Custom features and specifications can significantly impact pricing. Buyers should clearly communicate their requirements to avoid unexpected costs.
-
Materials: The choice of materials affects both the cost and the quality of the machine. High-grade materials may lead to higher upfront costs but can lower long-term maintenance expenses.
-
Quality/Certifications: Machines that meet specific quality standards or certifications (like ISO or CE marking) may carry a premium price. However, such certifications often justify the higher cost through enhanced reliability and marketability.
-
Supplier Factors: The reputation, location, and capabilities of the supplier can influence pricing. Established suppliers with a track record of quality may charge more but can offer better assurance of service and support.
-
Incoterms: Understanding the terms of sale (Incoterms) is vital for calculating total costs. Different terms can affect who bears responsibility for shipping and insurance, impacting the overall price.
Buyer Tips
-
Negotiation: Engage in thorough negotiations with suppliers to explore potential discounts, especially for bulk purchases or long-term contracts. Highlighting competitive quotes can leverage negotiations.
-
Cost-Efficiency: Assess the total cost of ownership (TCO), not just the initial purchase price. Consider maintenance, energy consumption, and potential downtime when evaluating costs.
-
Pricing Nuances: Be aware of regional pricing differences. For example, prices in Europe may be higher due to stricter regulations, while sourcing from regions with lower labor costs, like parts of South America, may offer savings.
-
Research and Due Diligence: Conduct market research to understand average pricing and supplier capabilities in your target regions. This information can empower buyers during negotiations and sourcing decisions.
Disclaimer
Prices for soft serve ice cream vending machines can vary widely based on numerous factors. The information provided here is indicative and should be verified with suppliers for the most accurate and current pricing.
Spotlight on Potential soft serve ice cream vending machine Manufacturers and Suppliers
This section offers a look at a few manufacturers active in the ‘soft serve ice cream vending machine’ market. This is a representative sample for illustrative purposes; B2B buyers must conduct their own extensive due diligence before any engagement. Information is synthesized from public sources and general industry knowledge.
Essential Technical Properties and Trade Terminology for soft serve ice cream vending machine
Critical Technical Properties of Soft Serve Ice Cream Vending Machines
When evaluating soft serve ice cream vending machines, international B2B buyers should prioritize the following technical specifications to ensure they are investing in high-quality, efficient equipment.
-
Material Grade
– Definition: This refers to the type of materials used in the construction of the machine, typically stainless steel or food-grade plastics.
– Importance: High-grade materials ensure durability, resistance to corrosion, and compliance with health regulations. For buyers in regions with humid climates, such as parts of Africa and South America, corrosion resistance is particularly crucial. -
Production Capacity
– Definition: This specification indicates how much ice cream the machine can produce within a specific timeframe, often measured in liters per hour.
– Importance: Understanding production capacity is essential for businesses to meet demand, especially during peak seasons or events. Buyers should align this capacity with their expected customer volume to maximize profitability. -
Energy Efficiency Rating
– Definition: This rating measures the energy consumption of the machine relative to its output.
– Importance: Energy-efficient machines reduce operational costs, which is a significant consideration for businesses in developing markets. Choosing a machine with a high efficiency rating can lead to long-term savings.
-
Temperature Control Range
– Definition: This specification refers to the range of temperatures the machine can maintain for optimal ice cream consistency.
– Importance: Proper temperature control ensures that the ice cream is served at the ideal texture and quality, affecting customer satisfaction. This is critical in competitive markets like Europe, where consumer preferences for quality are high. -
Hopper Capacity
– Definition: The hopper is the storage compartment where the ice cream mix is held before being dispensed.
– Importance: A larger hopper capacity allows for longer periods of operation without the need for frequent refills, enhancing service efficiency. This can be particularly advantageous in high-traffic locations. -
Maintenance Requirements
– Definition: This refers to the frequency and complexity of upkeep needed to keep the machine running efficiently.
– Importance: Machines that require less frequent maintenance can reduce downtime and operational costs. Buyers should consider machines with self-cleaning features or easy-access components for maintenance.
Common Trade Terminology in the Soft Serve Ice Cream Machine Industry
Understanding industry-specific terminology is essential for effective communication and negotiation in B2B transactions.
- OEM (Original Equipment Manufacturer)
– Definition: A company that produces parts or equipment that may be marketed by another manufacturer.
– Importance: Buyers should be aware of whether they are purchasing directly from the OEM or a reseller, as this can affect warranty, service, and pricing.
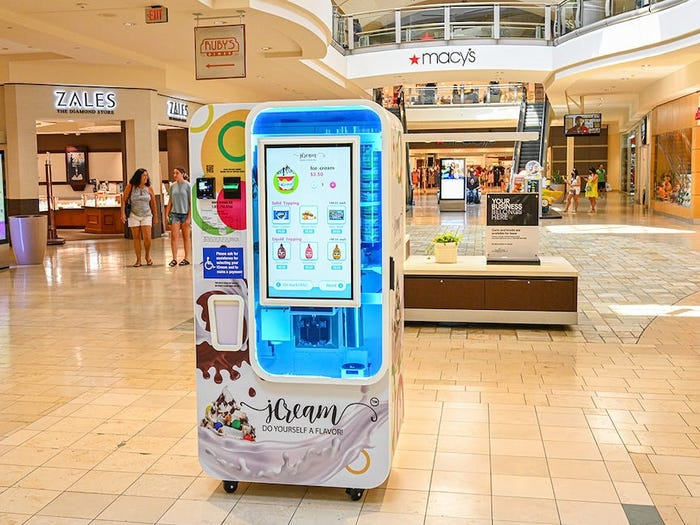
Illustrative Image (Source: Google Search)
-
MOQ (Minimum Order Quantity)
– Definition: The smallest number of units that a supplier is willing to sell.
– Importance: Understanding the MOQ helps buyers plan their inventory and manage cash flow. It is especially relevant for startups or small businesses looking to enter the market without significant upfront investment. -
RFQ (Request for Quotation)
– Definition: A document sent to suppliers requesting a quote for specific products or services.
– Importance: Issuing an RFQ allows buyers to compare prices and terms from different suppliers, ensuring they receive the best possible deal. -
Incoterms (International Commercial Terms)
– Definition: A set of predefined international trade terms that clarify the responsibilities of buyers and sellers.
– Importance: Familiarity with Incoterms is crucial for international transactions, as they define who is responsible for shipping, insurance, and tariffs, minimizing potential disputes.
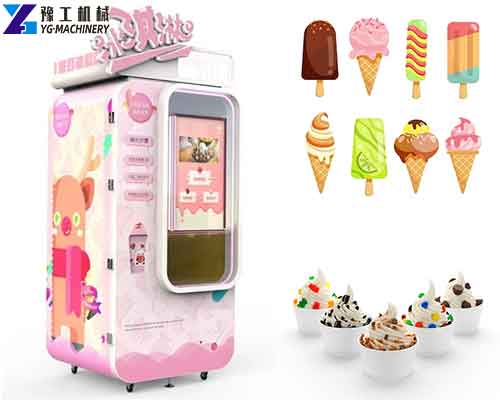
Illustrative Image (Source: Google Search)
-
Lead Time
– Definition: The amount of time between the initiation of an order and its completion.
– Importance: Understanding lead times is essential for inventory management and planning. Buyers should factor in lead times to ensure they can meet customer demand without delays. -
Warranty Period
– Definition: The duration during which a manufacturer guarantees the performance and quality of the machine.
– Importance: A longer warranty period often indicates higher confidence in product quality. Buyers should consider warranty terms to mitigate risks associated with equipment failure.
By understanding these technical properties and trade terminologies, international B2B buyers can make informed decisions that align with their business goals and operational needs.
Navigating Market Dynamics, Sourcing Trends, and Sustainability in the soft serve ice cream vending machine Sector
Market Overview & Key Trends
The global soft serve ice cream vending machine market is experiencing robust growth, driven by rising consumer demand for convenient and indulgent dessert options. Key factors influencing this market include the increasing urbanization in regions like Africa, South America, the Middle East, and Europe, coupled with a growing trend towards automation in food service. B2B buyers are increasingly seeking innovative solutions that enhance customer experience, which has led to the emergence of technologically advanced vending machines that offer customization features, cashless payment options, and real-time inventory management.
Emerging trends indicate a shift towards healthier product offerings, with many manufacturers exploring low-fat and dairy-free alternatives to cater to diverse dietary preferences. This aligns with the global health consciousness trend and presents opportunities for international buyers to source machines that can accommodate these product variations. Furthermore, advancements in machine technology, such as IoT integration, allow for remote monitoring and maintenance, enhancing operational efficiency and reducing downtime.
For B2B buyers, understanding local market dynamics is crucial. In regions like Brazil and Colombia, where street food culture is prevalent, soft serve machines that are compact and mobile can tap into the growing trend of outdoor food service. Additionally, the Middle East market is seeing an uptick in demand for premium offerings, which could lead to partnerships with local suppliers who can provide high-quality ingredients for soft serve ice cream.
Sustainability & Ethical Sourcing in B2B
Sustainability has become a pivotal consideration in the soft serve ice cream vending machine sector. The environmental impact of manufacturing processes and the sourcing of ingredients is under scrutiny, making it essential for B2B buyers to prioritize ethical supply chains. This involves selecting suppliers who adhere to sustainable practices, such as using responsibly sourced dairy and plant-based ingredients that minimize ecological footprints.
Buyers should look for vendors that offer ‘green’ certifications, which demonstrate a commitment to environmental stewardship. These certifications may include organic labels for ingredients, energy-efficient machinery, and recyclable or biodegradable packaging options. By investing in sustainable practices, businesses not only enhance their brand reputation but also meet the increasing consumer demand for environmentally friendly products.
Moreover, incorporating sustainability into the procurement process can lead to cost savings in the long run. Energy-efficient vending machines reduce operational costs, while sustainable sourcing of ingredients can open avenues for marketing premium products, appealing to eco-conscious consumers. As more regulations emerge globally aimed at reducing carbon footprints, aligning with sustainable suppliers is not just a trend but a necessity for long-term viability in the market.
Brief Evolution/History
The soft serve ice cream vending machine has evolved significantly since its inception in the 1930s. Initially designed for simplicity and efficiency, these machines have progressed to incorporate advanced technology and design elements that appeal to modern consumers. The introduction of self-serve options in the 1980s marked a pivotal shift, allowing customers to customize their desserts, which heightened engagement and sales.
In recent years, the rise of automation and digital payment systems has transformed the landscape further, making it easier for businesses to manage operations and cater to consumer preferences. As the market continues to expand, innovation remains a driving force, with manufacturers focusing on developing machines that not only meet current consumer demands but are also adaptable to future trends in health and sustainability. This evolution presents a unique opportunity for B2B buyers to invest in cutting-edge technology that aligns with both consumer expectations and environmental responsibilities.
Related Video: Incoterms for beginners | Global Trade Explained
Frequently Asked Questions (FAQs) for B2B Buyers of soft serve ice cream vending machine
-
What should I consider when vetting suppliers for soft serve ice cream vending machines?
When vetting suppliers, prioritize their experience in the industry and their reputation. Request references from previous clients and check their online reviews. Ensure they have a valid business license and certifications relevant to food safety and machinery standards. It’s also beneficial to visit their facilities if possible, to assess their production capabilities and quality control measures. -
Can I customize the soft serve ice cream vending machines to meet specific needs?
Yes, many suppliers offer customization options for their machines. You can request modifications such as size, color, branding, and even specific functionalities like flavor options or payment systems. Discuss your requirements during the initial conversations to ensure the supplier can meet your specifications and to understand any additional costs involved. -
What are the typical minimum order quantities (MOQ) and lead times for soft serve ice cream vending machines?
MOQs can vary significantly based on the supplier and the type of machine. Generally, expect MOQs to range from 5 to 20 units. Lead times can also differ, typically ranging from 4 to 12 weeks depending on the customization and production schedules. Always confirm these details upfront to align your purchasing timeline with your business needs. -
What payment terms are common when sourcing from international suppliers?
Payment terms can vary, but many suppliers require a deposit (often 30-50%) upfront, with the balance due upon delivery or prior to shipment. It’s advisable to use secure payment methods, such as letters of credit or escrow services, especially for large orders. Discuss and negotiate payment terms early in the negotiation process to avoid misunderstandings later. -
How can I ensure the quality of the machines I am purchasing?
To ensure quality, request detailed product specifications and quality assurance certifications from your supplier. Ask about their testing processes and warranty policies. If possible, request samples or visit the factory to observe the production process. Establishing clear quality benchmarks in your agreement can also protect your interests. -
What certifications should I look for in soft serve ice cream vending machines?
Look for certifications that comply with international food safety and quality standards, such as ISO 9001 for quality management systems and CE marking for compliance with European health, safety, and environmental protection standards. Certifications specific to food safety, like NSF or HACCP, are also critical to ensure the machines meet health regulations in your target market. -
What logistics considerations should I keep in mind when importing vending machines?
Consider the shipping methods available, including air and sea freight, and select the one that balances cost and delivery speed. Be aware of import duties and taxes in your country, and factor these into your total cost. It’s also essential to choose a reliable logistics partner who can manage customs clearance and delivery to your location. -
How should I handle disputes with suppliers?
Establish clear terms and conditions in your contract, including dispute resolution processes. Communicate any issues promptly and professionally to the supplier, aiming for a collaborative resolution. If disputes escalate, consider mediation or arbitration as alternatives to legal action, as these methods can be more cost-effective and quicker than traditional litigation. Always document all communications for reference.
Strategic Sourcing Conclusion and Outlook for soft serve ice cream vending machine
In conclusion, the landscape for soft serve ice cream vending machines is ripe with opportunity, particularly for international B2B buyers from regions such as Africa, South America, the Middle East, and Europe. Strategic sourcing remains essential, enabling businesses to optimize costs, enhance product quality, and ensure reliable supply chains. Key takeaways include the importance of selecting reputable suppliers, understanding local market preferences, and leveraging technological advancements for operational efficiency.
By engaging in a thorough sourcing strategy, companies can not only improve their competitive edge but also cater to the growing consumer demand for convenient and quality dessert options. As the market continues to evolve, buyers should remain vigilant in identifying trends and adapting their offerings accordingly.
Looking ahead, the potential for growth in the soft serve ice cream sector is significant. We encourage international buyers to seize this moment—invest in innovative vending solutions, foster partnerships with trusted suppliers, and stay informed about market dynamics. This proactive approach will position your business for success in a vibrant and expanding marketplace.