Your Ultimate Guide to Sourcing Smoothie Vending Machine
Guide to Smoothie Vending Machine
- Introduction: Navigating the Global Market for smoothie vending machine
- Understanding smoothie vending machine Types and Variations
- Key Industrial Applications of smoothie vending machine
- Strategic Material Selection Guide for smoothie vending machine
- In-depth Look: Manufacturing Processes and Quality Assurance for smoothie vending machine
- Comprehensive Cost and Pricing Analysis for smoothie vending machine Sourcing
- Spotlight on Potential smoothie vending machine Manufacturers and Suppliers
- Essential Technical Properties and Trade Terminology for smoothie vending machine
- Navigating Market Dynamics, Sourcing Trends, and Sustainability in the smoothie vending machine Sector
- Frequently Asked Questions (FAQs) for B2B Buyers of smoothie vending machine
- Strategic Sourcing Conclusion and Outlook for smoothie vending machine
Introduction: Navigating the Global Market for smoothie vending machine
In an increasingly health-conscious world, smoothie vending machines are emerging as a pivotal solution for businesses seeking to meet the demand for nutritious, on-the-go options. These innovative machines not only cater to the growing trend of healthier lifestyles but also provide a lucrative opportunity for B2B buyers looking to invest in automated food and beverage solutions. As urbanization continues to rise in regions such as Africa, South America, the Middle East, and Europe, the appeal of smoothie vending machines becomes more pronounced, offering a convenient and efficient way to serve fresh products.
This comprehensive guide will delve into essential aspects of the smoothie vending machine market, covering a variety of machine types, materials, and manufacturing quality control (QC) processes. It will also outline key suppliers, cost considerations, and market dynamics to provide a holistic view of the landscape. By addressing common FAQs, this guide empowers international B2B buyers to make informed sourcing decisions that align with their specific needs and market conditions.
Investing in smoothie vending machines can enhance customer satisfaction and drive revenue growth, especially in regions where health and convenience are paramount. Whether you’re a buyer in South Africa looking for local suppliers or a distributor in Europe seeking cutting-edge technology, this guide will equip you with the knowledge and insights necessary to navigate the global market effectively. Embrace the opportunity to stay ahead of the curve and elevate your business offerings with this innovative solution.
Understanding smoothie vending machine Types and Variations
Type Name | Key Distinguishing Features | Primary B2B Applications | Brief Pros & Cons for Buyers |
---|---|---|---|
Traditional Smoothie Vending Machine | Manual selection with pre-packaged ingredients | Gyms, schools, office complexes | Pros: Simple operation; Cons: Limited customization options. |
Automated Blender Vending Machine | On-demand blending with fresh ingredients | Health-focused locations, events | Pros: Fresh product; Cons: Higher maintenance costs. |
Compact Countertop Smoothie Machine | Space-efficient design for smaller venues | Cafés, small businesses | Pros: Saves space; Cons: Limited output capacity. |
Mobile Smoothie Vending Cart | Portable unit for events and festivals | Outdoor events, markets | Pros: Flexibility; Cons: Weather-dependent operations. |
Smart Smoothie Vending Machine | Integrated technology for remote monitoring and payment | High-traffic areas, tech-savvy locations | Pros: Advanced features; Cons: Higher initial investment. |
Traditional Smoothie Vending Machine
Traditional smoothie vending machines are designed for ease of use, allowing customers to select from a menu of pre-packaged ingredients. These machines are commonly found in gyms, schools, and office complexes where convenience is paramount. For B2B buyers, the key consideration is the balance between initial investment and operational simplicity. While these machines are straightforward to operate, they may limit customer customization, which could affect sales in markets that favor personalized options.
Automated Blender Vending Machine
Automated blender vending machines offer a modern twist by blending fresh ingredients on-demand. This type is particularly suitable for health-focused locations and events where customers value freshness. B2B buyers should evaluate the potential for higher sales due to the appeal of fresh smoothies. However, it’s crucial to consider the increased maintenance requirements and potential downtime, which could impact profitability.
Compact Countertop Smoothie Machine
The compact countertop smoothie machine is an excellent choice for cafés and small businesses that have limited space. These machines provide a convenient solution for serving smoothies without requiring extensive floor space. Buyers should assess their output capacity and the variety of smoothies they wish to offer. While these machines are ideal for smaller venues, their limited output could restrict service during peak hours.
Mobile Smoothie Vending Cart
Mobile smoothie vending carts are designed for flexibility, allowing businesses to operate at outdoor events and markets. These units can capitalize on foot traffic and seasonal events, making them an attractive option for B2B buyers looking to diversify their offerings. However, the weather dependency of outdoor operations can pose challenges, and buyers must consider logistics and storage when investing in this type of machine.
Smart Smoothie Vending Machine
Smart smoothie vending machines incorporate technology for remote monitoring, inventory management, and cashless payment options. They are well-suited for high-traffic areas and tech-savvy locations where convenience is key. B2B buyers should weigh the advantages of advanced features against the higher initial investment. While these machines can enhance customer experience and streamline operations, the complexity of the technology may require additional training for staff.
Related Video: Fitgo Smoothie Vending Machine: Your Money making machine
Key Industrial Applications of smoothie vending machine
Industry/Sector | Specific Application of Smoothie Vending Machine | Value/Benefit for the Business | Key Sourcing Considerations for this Application |
---|---|---|---|
Health & Wellness | Gyms and Fitness Centers | Enhances customer experience with healthy options | Machine durability, ingredient sourcing, and nutritional options |
Education | Schools and Universities | Provides quick, nutritious snacks for students | Compliance with health regulations, ease of operation, and cost |
Hospitality | Hotels and Resorts | Offers guests convenient access to healthy drinks | Aesthetic design, maintenance support, and variety of offerings |
Corporate Offices | Employee Break Rooms | Promotes healthy eating and boosts employee morale | Machine footprint, energy efficiency, and flexibility in payment options |
Retail | Shopping Malls | Attracts health-conscious consumers and increases foot traffic | Location analysis, customer interaction features, and refill logistics |
Health & Wellness
In gyms and fitness centers, smoothie vending machines serve as a perfect solution for health-conscious consumers seeking quick, nutritious snacks post-workout. These machines can offer a variety of smoothies made from fresh fruits and vegetables, catering to diverse dietary preferences. For international buyers, sourcing machines that can maintain ingredient freshness and durability in high-traffic environments is crucial. Ensuring the machine can handle a range of ingredients while offering customizable options can significantly enhance customer satisfaction.
Education
Schools and universities are increasingly adopting smoothie vending machines to provide students with healthy snack alternatives. These machines address the challenge of student nutrition by offering convenient access to smoothies that are rich in vitamins and minerals. For B2B buyers in the education sector, compliance with local health regulations and ease of use for students are paramount. Additionally, machines that require minimal maintenance and provide nutritional information can further enhance their appeal to educational institutions.
Hospitality
In the hospitality sector, hotels and resorts benefit from smoothie vending machines by offering guests quick access to refreshing and healthy beverages. This amenity can enhance the overall guest experience and serve as an attractive selling point. When sourcing these machines, businesses should consider aesthetic design to fit the hotel’s branding, as well as robust maintenance support to minimize downtime. A diverse menu that caters to various tastes can also help in attracting a wider range of guests.
Corporate Offices
Smoothie vending machines in corporate offices promote a healthy workplace culture by providing employees with nutritious drink options. This can lead to increased morale and productivity, as well as a reduction in unhealthy snacking. For international buyers, it’s essential to evaluate the machine’s footprint to ensure it fits within the office layout and to consider energy efficiency to reduce operational costs. Flexible payment options, such as mobile payments, can also enhance user convenience.
Retail
In shopping malls, smoothie vending machines can attract health-conscious consumers and increase foot traffic. These machines can be strategically placed near fitness stores or health food shops to cater to a targeted audience. B2B buyers in retail should focus on location analysis to maximize visibility and sales. Additionally, incorporating customer interaction features, such as touch screens for customization, can improve the overall shopping experience and encourage repeat visits. Efficient refill logistics are also critical to ensure that machines are consistently stocked with fresh ingredients.
Related Video: Alberts Smoothie Station | Your automated solution for fresh, personalized smoothies at work
Strategic Material Selection Guide for smoothie vending machine
When selecting materials for smoothie vending machines, it is essential to consider various factors that affect performance, durability, and compliance with international standards. Below is an analysis of four common materials used in the construction of smoothie vending machines, highlighting their properties, advantages, disadvantages, and specific considerations for international B2B buyers.
Stainless Steel
Key Properties: Stainless steel is renowned for its excellent corrosion resistance, high strength, and ability to withstand a wide range of temperatures. It typically has a pressure rating suitable for various mechanical applications.
Pros & Cons: The primary advantage of stainless steel is its durability and resistance to rust and staining, making it ideal for food-related applications. However, it can be more expensive than other materials, and its manufacturing process can be complex due to the need for specialized welding techniques.
Impact on Application: Stainless steel is compatible with food media, ensuring hygiene and safety in smoothie production. Its non-reactive nature prevents contamination of flavors.
Considerations for International Buyers: Buyers should ensure compliance with health and safety regulations specific to their region, such as the European Union’s food safety standards. Common grades like 304 and 316 are preferred, with the latter offering higher corrosion resistance, particularly in humid environments.
Polycarbonate
Key Properties: Polycarbonate is a strong, lightweight thermoplastic with high impact resistance and clarity. It can withstand temperatures up to 120°C and has good dimensional stability.
Pros & Cons: The main advantage of polycarbonate is its lightweight nature and ease of fabrication, which can reduce manufacturing costs. However, it is less resistant to scratches and UV degradation compared to glass or metals, which may limit its longevity in outdoor applications.
Impact on Application: Polycarbonate is suitable for transparent components, allowing visibility of the smoothie preparation process, which can enhance customer engagement.
Considerations for International Buyers: Buyers should verify that the polycarbonate used is BPA-free to meet health regulations in various regions. Compliance with standards such as ASTM D6400 for biodegradability may also be relevant, especially in environmentally conscious markets.
Aluminum
Key Properties: Aluminum is lightweight, corrosion-resistant, and has good thermal conductivity. It can handle moderate pressure and temperature variations.
Pros & Cons: Aluminum’s lightweight nature makes it easy to transport and install, reducing overall costs. However, it is less durable than stainless steel and can be susceptible to denting and scratching, which may affect its aesthetic appeal over time.
Impact on Application: Aluminum is often used in structural components and panels, providing a good balance between weight and strength. Its corrosion resistance makes it suitable for humid environments.
Considerations for International Buyers: Buyers should be aware of the specific alloys used, as some may not meet the required strength standards. Compliance with international standards like ISO 9001 for quality management can also be a crucial factor in supplier selection.
Glass
Key Properties: Glass is a non-porous material that offers excellent clarity and aesthetic appeal. It can withstand high temperatures but is fragile and requires careful handling.
Pros & Cons: The primary advantage of glass is its ability to provide a premium look and feel to the vending machine. However, its fragility can be a significant drawback, as it is prone to breakage and may require additional protective measures.
Impact on Application: Glass is often used for display panels, allowing customers to see the smoothies being prepared. Its non-reactive nature makes it safe for food contact.
Considerations for International Buyers: Buyers should consider the local market’s acceptance of glass in vending machines, as some regions may prefer more durable materials. Compliance with safety regulations regarding glass use in public spaces is also essential.
Summary Table
Material | Typical Use Case for smoothie vending machine | Key Advantage | Key Disadvantage/Limitation | Relative Cost (Low/Med/High) |
---|---|---|---|---|
Stainless Steel | Structural components, food contact surfaces | Excellent corrosion resistance | Higher cost, complex manufacturing | High |
Polycarbonate | Transparent panels, protective covers | Lightweight, easy to fabricate | Less scratch-resistant, UV degradation | Medium |
Aluminum | Structural components, panels | Lightweight, corrosion-resistant | Less durable, prone to denting | Medium |
Glass | Display panels for smoothies | Premium look, non-reactive | Fragile, requires careful handling | Medium |
This strategic material selection guide aims to equip international B2B buyers with actionable insights to make informed decisions when sourcing materials for smoothie vending machines. By understanding the properties and implications of each material, buyers can align their choices with market demands and regulatory requirements.
In-depth Look: Manufacturing Processes and Quality Assurance for smoothie vending machine
Manufacturing a smoothie vending machine involves a series of well-defined stages, each crucial to ensuring the final product meets the high standards required for performance, reliability, and safety. For international B2B buyers, particularly from regions such as Africa, South America, the Middle East, and Europe, understanding these processes is essential for making informed purchasing decisions.
Manufacturing Process
1. Material Preparation
The first step in the manufacturing process is material preparation, which involves sourcing high-quality raw materials. Common materials used include stainless steel for durability and hygiene, food-grade plastics for various components, and electronic parts for the machine’s operating system. Buyers should seek suppliers who provide certifications for material safety, especially those adhering to international standards such as FDA regulations for food contact materials.
2. Forming
Forming techniques vary based on the components being produced. For instance, metal components may undergo processes such as stamping or laser cutting, while plastic parts might be manufactured through injection molding. Each technique has its advantages:
– Stamping offers precision for metal parts, which is critical for the machine’s structural integrity.
– Injection molding allows for complex shapes and designs in plastic components, enhancing the aesthetic appeal and functionality of the vending machine.
Buyers should inquire about the forming technologies employed by their suppliers to ensure they use advanced methods that minimize waste and maximize efficiency.
3. Assembly
During the assembly phase, individual components are brought together. This stage often involves both automated processes and manual labor. Key assembly techniques may include:
– Robotic assembly for high precision and speed in putting together complex parts.
– Manual assembly for intricate components that require human oversight.
Quality control measures should be in place throughout this stage to catch any defects early. Buyers should ask suppliers about their assembly line practices and whether they utilize lean manufacturing principles to reduce errors.
4. Finishing
The finishing stage involves surface treatments, painting, and coating to enhance the machine’s appearance and protect it from environmental factors. Techniques such as powder coating or anodizing are commonly used to ensure longevity and resistance to corrosion. Buyers should verify that the finishing processes comply with international standards, as these can affect the machine’s performance and lifespan.
Quality Assurance
Quality assurance is a critical component of the manufacturing process, ensuring that each machine meets specified standards before it reaches the market. For international buyers, understanding the quality assurance landscape is vital.
Relevant International Standards
Several standards govern the quality and safety of vending machines:
– ISO 9001: This standard focuses on quality management systems and is applicable to any organization. It ensures that suppliers have a consistent approach to quality.
– CE Marking: Required for products sold in the European Economic Area, this marking indicates conformity with health, safety, and environmental protection standards.
– API Standards: For machines that involve food and beverage dispensing, adherence to American Petroleum Institute (API) standards may also be relevant, particularly regarding food safety.
Quality Control Checkpoints
Quality control checkpoints are strategically placed throughout the manufacturing process:
– Incoming Quality Control (IQC): Inspecting raw materials upon arrival to ensure they meet specifications.
– In-Process Quality Control (IPQC): Monitoring processes during manufacturing to catch defects early.
– Final Quality Control (FQC): Conducting thorough inspections of the finished product before shipment.
B2B buyers should inquire about the specific checkpoints implemented by their suppliers and the frequency of inspections at each stage.
Common Testing Methods
Various testing methods are employed to ensure product quality, including:
– Functional Testing: Verifying that all components operate as intended.
– Durability Testing: Assessing the machine’s resilience under real-world conditions.
– Safety Testing: Ensuring compliance with electrical safety standards and food safety regulations.
Buyers can request documentation of these tests to verify compliance with industry standards.
Verifying Supplier Quality Control
International buyers must take proactive steps to ensure their suppliers maintain high-quality standards. Here are several strategies to consider:
- Conduct Supplier Audits: Regular audits can help assess a supplier’s quality control processes and adherence to standards. Buyers can either perform these audits in-house or hire third-party services.
- Request Quality Reports: Suppliers should provide detailed quality reports that outline their quality assurance processes, results of inspections, and testing outcomes.
- Engage Third-Party Inspectors: Utilizing third-party inspection services can provide an unbiased assessment of the manufacturing processes and final products.
Quality Control and Certification Nuances
Different regions may have specific regulations or certifications that impact the quality assurance process. For instance, in Europe, compliance with CE marking is mandatory, whereas African and South American markets might prioritize local health and safety certifications. Understanding these nuances helps B2B buyers navigate compliance requirements effectively.
In conclusion, a thorough understanding of manufacturing processes and quality assurance is essential for B2B buyers interested in smoothie vending machines. By focusing on material preparation, forming, assembly, and finishing, along with a robust quality assurance strategy, buyers can ensure they partner with reliable suppliers, leading to successful product launches and customer satisfaction.
Related Video: Parle-G Biscuits Manufacturing process – Food Factory Tour- Modern Food factory, Mega Factory II
Comprehensive Cost and Pricing Analysis for smoothie vending machine Sourcing
When sourcing smoothie vending machines, understanding the comprehensive cost structure and pricing dynamics is crucial for international B2B buyers. This analysis breaks down the cost components and price influencers while providing actionable insights tailored to buyers from regions such as Africa, South America, the Middle East, and Europe.
Cost Components
-
Materials: The primary materials include stainless steel, plastics, refrigeration components, and electronic parts. Sourcing high-quality materials can significantly impact durability and performance, thus influencing the machine’s total cost.
-
Labor: Labor costs vary widely by region. In countries with higher labor costs, such as parts of Europe, manufacturers may pass these costs onto buyers. Conversely, sourcing from regions with lower labor costs can offer savings but may require careful consideration of quality and compliance standards.
-
Manufacturing Overhead: This includes factory costs, utilities, and indirect labor. Buyers should consider manufacturers’ operational efficiencies, which can affect pricing. For example, automated production lines may reduce costs compared to manual labor-intensive processes.
-
Tooling: Custom tooling for specific machine designs can incur significant upfront costs. It’s essential to evaluate whether customization is necessary, as it can lead to higher initial expenses but potentially better long-term returns through increased sales.
-
Quality Control (QC): Investing in rigorous QC processes ensures product reliability and compliance with international standards. Although this might slightly increase the cost, it can mitigate risks associated with product defects, especially for markets with strict regulations.
-
Logistics: Shipping costs can fluctuate based on the chosen Incoterms. Factors such as distance, shipping method, and freight volume should be considered. For international buyers, understanding the logistics landscape is essential for budget forecasting.
-
Margin: Suppliers typically incorporate a margin to cover their operational costs and profit. This margin can vary based on the supplier’s market position, brand reputation, and the competitive landscape.
Price Influencers
-
Volume/MOQ: Purchasing in larger quantities often leads to significant discounts. Understanding minimum order quantities (MOQ) can help buyers negotiate better pricing.
-
Specifications/Customization: Customized machines tailored to specific market needs may incur additional costs. Buyers should weigh the benefits of customization against the potential increase in price.
-
Materials: The choice of materials directly affects both the cost and quality of the vending machines. Opting for premium materials may enhance the product’s longevity but at a higher price point.
-
Quality/Certifications: Machines that meet international quality standards or possess certifications may command a higher price. Buyers should consider the importance of these certifications in their respective markets.
-
Supplier Factors: The supplier’s reputation, financial stability, and production capacity can significantly influence pricing. Building relationships with reliable suppliers can lead to more favorable terms.
-
Incoterms: Understanding shipping terms (e.g., FOB, CIF) is critical, as they dictate the responsibilities of both buyer and seller during transportation. This can affect overall cost and delivery timelines.
Buyer Tips
-
Negotiation: Engage in price discussions with suppliers, focusing on bulk orders or long-term contracts to secure better rates. Establishing a rapport can also facilitate more favorable terms.
-
Cost-Efficiency: Conduct a Total Cost of Ownership (TCO) analysis, including maintenance, energy consumption, and potential downtime, to evaluate the true value of the vending machine.
-
Pricing Nuances: Be aware of local market conditions and competitive pricing strategies in your region. For instance, certain markets may prioritize cost over advanced features, which can influence supplier pricing strategies.
-
Regional Considerations: Buyers from Africa, South America, the Middle East, and Europe should consider local economic conditions, currency fluctuations, and import tariffs that could affect the overall cost.
Disclaimer
Prices and costs mentioned in this analysis are indicative and subject to change based on market fluctuations, supplier negotiations, and evolving economic conditions. Buyers should conduct thorough market research and consult with suppliers for the most accurate and current pricing.
Spotlight on Potential smoothie vending machine Manufacturers and Suppliers
- (No specific manufacturer data was available or requested for detailed profiling in this section for smoothie vending machine.)*
Essential Technical Properties and Trade Terminology for smoothie vending machine
Key Technical Properties of Smoothie Vending Machines
When considering the procurement of smoothie vending machines, understanding the essential technical properties is crucial for making informed purchasing decisions. Here are some of the critical specifications to evaluate:
-
Material Grade
– Definition: The quality of materials used in the construction of the vending machine, typically stainless steel, plastic, or glass.
– Importance: High-grade materials ensure durability, resistance to corrosion, and ease of cleaning, which is particularly important in the food and beverage industry. For buyers in regions with high humidity or saline environments, such as coastal areas in South America or Africa, choosing the right material is vital for longevity. -
Power Consumption
– Definition: The amount of electrical energy the machine requires to operate, usually measured in watts.
– Importance: Understanding power consumption helps buyers estimate operating costs. Machines with lower power consumption may have a higher upfront cost but can lead to significant savings over time, especially in energy-conscious markets like Europe and the Middle East. -
Capacity
– Definition: The maximum amount of product the vending machine can hold, often measured in liters or the number of servings.
– Importance: Selecting a machine with the right capacity ensures that it meets the demand in various settings, from busy urban locations to smaller establishments. A larger capacity may be beneficial in high-traffic areas, while smaller machines may suffice in niche markets. -
Temperature Control
– Definition: The ability of the machine to maintain specific temperatures for ingredient preservation and product serving.
– Importance: Effective temperature control is critical for maintaining the freshness of ingredients and the quality of smoothies. This feature is particularly relevant in warmer climates, ensuring that products remain safe for consumption. -
User Interface
– Definition: The design and functionality of the machine’s operating system, including touchscreens and payment options.
– Importance: A user-friendly interface can enhance customer experience, leading to higher sales. For international buyers, it’s essential to consider language options and payment methods that cater to local preferences, thereby increasing accessibility. -
Maintenance Requirements
– Definition: The frequency and complexity of upkeep needed to keep the machine operational.
– Importance: Machines that require less frequent maintenance can reduce operational downtime and labor costs. Understanding maintenance requirements is crucial for businesses that want to ensure consistent service delivery.
Common Trade Terminology
Navigating the procurement process requires familiarity with specific industry jargon. Here are some essential terms:
-
OEM (Original Equipment Manufacturer)
– Definition: A company that produces parts or equipment that may be marketed by another manufacturer.
– Importance: Buyers should seek OEMs for reliable quality and support. Purchasing from an OEM often guarantees that parts are readily available, which is essential for maintenance and repairs. -
MOQ (Minimum Order Quantity)
– Definition: The smallest quantity of a product that a supplier is willing to sell.
– Importance: Understanding MOQ helps buyers gauge the investment needed for bulk purchases. For businesses in emerging markets, negotiating lower MOQs can be crucial for managing cash flow. -
RFQ (Request for Quotation)
– Definition: A document sent to suppliers requesting a quote for specific products or services.
– Importance: An RFQ allows buyers to compare pricing and terms from different suppliers, ensuring they make cost-effective decisions. Crafting a detailed RFQ can lead to better pricing and service terms. -
Incoterms (International Commercial Terms)
– Definition: A series of predefined commercial terms published by the International Chamber of Commerce that define the responsibilities of buyers and sellers.
– Importance: Familiarity with Incoterms helps buyers understand shipping costs, insurance, and risk during transit. Selecting the right Incoterm can minimize potential disputes and clarify responsibilities in international transactions.
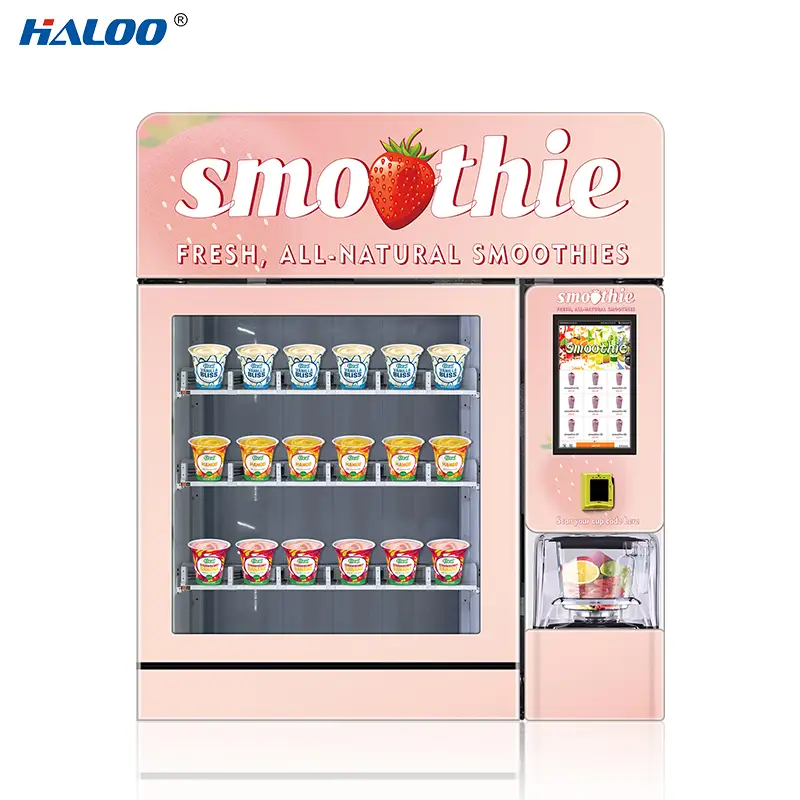
Illustrative Image (Source: Google Search)
- Lead Time
– Definition: The total time it takes from placing an order to receiving the goods.
– Importance: Understanding lead times is vital for inventory management. Buyers in fast-paced markets need to ensure timely delivery to meet consumer demand.
By grasping these technical properties and trade terminologies, international B2B buyers can make more strategic decisions when investing in smoothie vending machines, ultimately enhancing their operational efficiency and market competitiveness.
Navigating Market Dynamics, Sourcing Trends, and Sustainability in the smoothie vending machine Sector
Market Overview & Key Trends
The smoothie vending machine sector is witnessing transformative growth, driven by several global factors. The increasing consumer demand for healthy and convenient food options is a primary driver, particularly in urban areas where busy lifestyles prevail. As more people prioritize wellness, the trend towards on-the-go nutritious choices has made smoothie vending machines an attractive investment for B2B buyers across various regions, including Africa, South America, the Middle East, and Europe.
Emerging technologies are reshaping the landscape of smoothie vending. Smart vending machines equipped with IoT capabilities are gaining traction, allowing operators to monitor inventory levels, track sales data in real-time, and optimize machine placement based on consumer behavior. This technology not only enhances operational efficiency but also improves customer engagement through personalized offerings and loyalty programs.
Furthermore, sourcing trends are shifting towards local and organic ingredients. B2B buyers are increasingly seeking suppliers that can provide fresh, high-quality produce to cater to health-conscious consumers. This demand for freshness is particularly pronounced in regions like South Africa and Brazil, where local sourcing can also reduce transportation costs and carbon footprints. Additionally, the rise of plant-based diets is influencing product offerings, prompting vending machine operators to diversify their menus to include vegan and gluten-free options.
Sustainability & Ethical Sourcing in B2B
Sustainability has become a cornerstone of business strategy in the smoothie vending machine sector. As international buyers become more environmentally conscious, they are increasingly prioritizing suppliers that adhere to sustainable practices. This includes sourcing ingredients from suppliers who use regenerative agriculture techniques or those who are certified organic. The environmental impact of sourcing practices is significant; thus, buyers should evaluate the entire supply chain to ensure minimal ecological disruption.
Moreover, ethical sourcing is vital for building a reputable brand. Consumers are more likely to support businesses that demonstrate a commitment to social responsibility, which includes fair labor practices and community support. Certifications such as Fair Trade and Rainforest Alliance can enhance credibility and appeal to a growing demographic of ethically minded consumers.
Incorporating sustainable materials into the vending machines themselves is another way to reinforce commitment to environmental responsibility. Options include using recyclable plastics, biodegradable components, and energy-efficient technologies. By emphasizing sustainability and ethical sourcing, B2B buyers not only align with global trends but also position themselves favorably in a competitive market.
Brief Evolution/History
The smoothie vending machine concept has evolved significantly since its inception in the early 2000s. Initially perceived as a novelty, these machines have transformed into sophisticated retail solutions. The introduction of fresh ingredients and high-quality blends has elevated consumer expectations. With advancements in technology, modern machines now offer customizable options, real-time inventory management, and enhanced user experiences, reflecting the broader changes in consumer preferences towards health and convenience. As a result, the smoothie vending machine industry is now seen as a viable business model that aligns with contemporary consumer lifestyles.
Related Video: Global Trade & Logistics – What is Global Trade?
Frequently Asked Questions (FAQs) for B2B Buyers of smoothie vending machine
-
What key factors should I consider when vetting suppliers for smoothie vending machines?
When vetting suppliers, prioritize their reputation, experience, and product quality. Check for customer reviews and case studies, especially from businesses in your region. Request samples to evaluate the machine’s performance and reliability. Ensure the supplier has a robust customer service structure and consider their after-sales support and warranty terms. Additionally, verify their compliance with local regulations and certifications, as these can greatly impact your operation’s legality and safety. -
Can I customize the smoothie vending machine according to my business needs?
Many suppliers offer customization options for smoothie vending machines. This can include branding, machine size, flavor options, and payment systems. When discussing customization, clearly outline your requirements and ask for a detailed proposal, including costs and timelines. It’s advisable to work with suppliers who have experience in your market and can guide you on popular trends and flavors to cater to local preferences. -
What are the typical minimum order quantities (MOQ) and lead times for ordering smoothie vending machines?
MOQs vary by supplier and can range from a single unit to several dozen. It’s essential to clarify these details upfront to avoid unexpected costs. Lead times can also differ based on customization and production schedules, typically ranging from 4 to 12 weeks. Ensure you communicate your timelines clearly, especially if you’re aligning your launch with a specific event or season. -
What payment options are commonly available when purchasing smoothie vending machines?
Payment options can vary, with many suppliers offering flexible terms including bank transfers, letters of credit, and payment through escrow services. Some suppliers may request a deposit upfront, with the remainder due upon delivery. It’s crucial to establish clear payment terms in the contract to protect your interests. Always consider using secure payment methods to mitigate risks associated with international transactions. -
How can I ensure quality assurance and necessary certifications for the smoothie vending machines?
Request documentation that certifies the machines meet international quality standards, such as ISO certifications or safety compliance relevant to your region. Many suppliers will provide quality assurance guarantees or warranties for their products. Additionally, consider third-party testing for additional assurance. Establish a clear quality control process during production, including inspections at various stages to ensure the machines meet your specifications. -
What logistics considerations should I keep in mind when importing smoothie vending machines?
Logistics play a critical role in the import process. Understand the shipping options available, including air freight for faster delivery or sea freight for cost savings. Be aware of customs regulations in your country and ensure all necessary documentation is prepared to avoid delays. Collaborating with experienced freight forwarders can help navigate the complexities of international shipping and customs clearance. -
How should I handle potential disputes with suppliers?
To minimize disputes, establish clear communication from the outset and document all agreements in a contract, including delivery timelines, payment terms, and quality expectations. In case of a dispute, attempt to resolve issues amicably through direct communication first. If necessary, refer to the dispute resolution clause in your contract, which may include mediation or arbitration. Understanding local laws and regulations can also provide guidance on your rights and obligations. -
What are some common challenges faced when sourcing smoothie vending machines internationally?
Challenges can include language barriers, varying quality standards, and differing regulations across countries. Additionally, time zone differences can complicate communication. To mitigate these issues, work with suppliers who have experience in your market and are familiar with local preferences and regulations. Building strong relationships with your suppliers can also help facilitate smoother transactions and better problem-solving when challenges arise.
Strategic Sourcing Conclusion and Outlook for smoothie vending machine
The landscape of smoothie vending machines presents a wealth of opportunities for international B2B buyers, particularly in emerging markets across Africa, South America, the Middle East, and Europe. Strategic sourcing remains a cornerstone of success in this sector, enabling businesses to optimize costs while ensuring the highest quality and innovation in products. By carefully evaluating suppliers, understanding local market dynamics, and leveraging technology, companies can enhance their competitive edge and meet consumer demand for healthy, convenient options.
Key takeaways include the importance of selecting suppliers who not only provide high-quality machines but also offer robust after-sales support and maintenance. Additionally, understanding regional preferences and health trends can help tailor offerings that resonate with local consumers. Investing in technology such as cashless payment systems and customizable flavors can significantly improve customer engagement and operational efficiency.
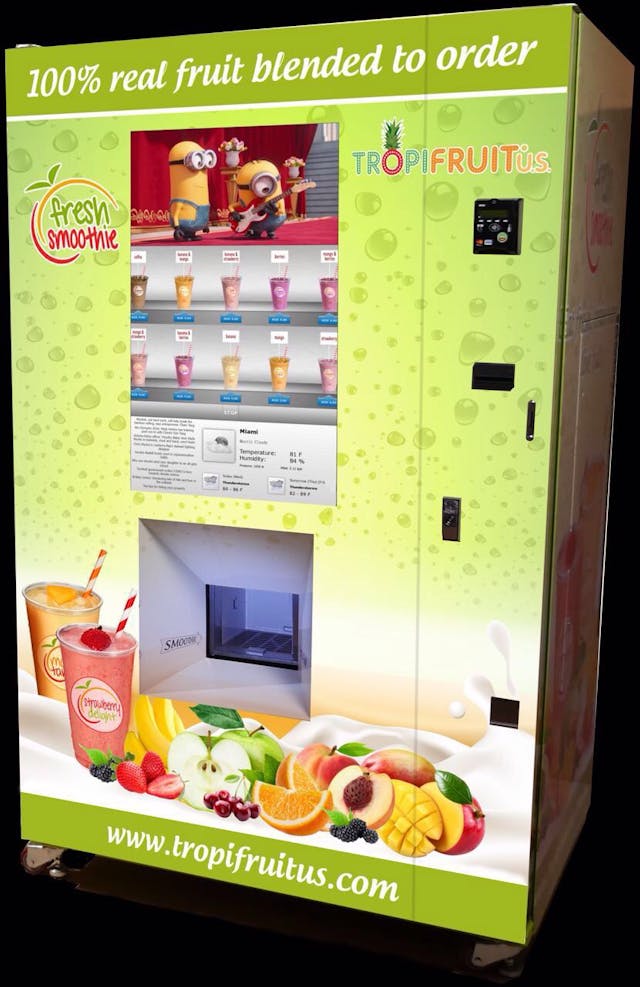
Illustrative Image (Source: Google Search)
As we look ahead, the smoothie vending machine market is poised for growth, driven by an increasing focus on health and wellness. International B2B buyers are encouraged to explore innovative partnerships and stay abreast of technological advancements that can enhance their offerings. Embrace this opportunity to lead in a thriving market, and ensure your business is positioned for future success.