Your Ultimate Guide to Sourcing Small Touch Screen Vending
Guide to Small Touch Screen Vending Machine
- Introduction: Navigating the Global Market for small touch screen vending machine
- Understanding small touch screen vending machine Types and Variations
- Key Industrial Applications of small touch screen vending machine
- Strategic Material Selection Guide for small touch screen vending machine
- In-depth Look: Manufacturing Processes and Quality Assurance for small touch screen vending machine
- Comprehensive Cost and Pricing Analysis for small touch screen vending machine Sourcing
- Spotlight on Potential small touch screen vending machine Manufacturers and Suppliers
- Essential Technical Properties and Trade Terminology for small touch screen vending machine
- Navigating Market Dynamics, Sourcing Trends, and Sustainability in the small touch screen vending machine Sector
- Frequently Asked Questions (FAQs) for B2B Buyers of small touch screen vending machine
- Strategic Sourcing Conclusion and Outlook for small touch screen vending machine
Introduction: Navigating the Global Market for small touch screen vending machine
In today’s fast-paced global marketplace, small touch screen vending machines are transforming the way businesses engage with consumers. These innovative machines not only provide a convenient purchasing option but also enhance the customer experience through interactive interfaces. For international B2B buyers, particularly from regions like Africa, South America, the Middle East, and Europe, understanding the dynamics of this market is crucial for successful sourcing and investment.
This comprehensive guide delves into various aspects of small touch screen vending machines, including their types, materials, manufacturing processes, and quality control standards. Buyers will gain insights into reputable suppliers, enabling them to make informed choices that align with their operational needs and budget constraints. Additionally, we will explore market trends and pricing strategies, providing a holistic view of the economic landscape surrounding these machines.
By leveraging the information presented in this guide, B2B buyers can confidently navigate the complexities of sourcing small touch screen vending machines. Whether you’re looking to enhance your retail offerings or streamline service delivery, this resource is designed to empower your decision-making process. With actionable insights tailored to diverse geographical markets, you will be well-equipped to capitalize on opportunities and drive business growth in a competitive environment.
Understanding small touch screen vending machine Types and Variations
Type Name | Key Distinguishing Features | Primary B2B Applications | Brief Pros & Cons for Buyers |
---|---|---|---|
Snack and Beverage Machines | Combines snacks and drinks in a compact design | Offices, schools, public spaces | Pros: High demand for convenience; Cons: Limited to popular items, may require frequent restocking. |
Healthy Options Vending Machines | Focuses on nutritious snacks and beverages | Gyms, health clubs, corporate offices | Pros: Appeals to health-conscious consumers; Cons: Higher costs for healthier products. |
Customizable Product Machines | Allows businesses to select products based on demand | Retail stores, event venues | Pros: Tailored offerings can increase sales; Cons: Requires initial market research and investment. |
Cashless Payment Machines | Supports mobile and card payments only | Tech-savvy environments, urban areas | Pros: Faster transactions, reduces cash handling; Cons: May alienate customers preferring cash. |
Interactive Experience Machines | Offers games or quizzes for discounts and rewards | Malls, entertainment centers | Pros: Engages customers, enhances brand loyalty; Cons: Requires ongoing content updates and maintenance. |
Snack and Beverage Machines
Snack and beverage vending machines are designed to provide a variety of snacks and drinks in a single unit. They are particularly suitable for high-traffic areas like offices, schools, and public spaces, where convenience is paramount. When considering a purchase, businesses should evaluate the product selection, ease of restocking, and maintenance requirements. The high demand for convenience can lead to steady sales, but the need for frequent restocking may increase operational costs.
Healthy Options Vending Machines
These machines prioritize nutritious snacks and beverages, catering to the growing trend of health-conscious consumers. They are ideal for gyms, health clubs, and corporate offices that promote wellness among employees. Buyers should consider the higher costs associated with healthier products and the potential for a niche market. While they can attract a dedicated customer base, the limited product variety may affect sales volume compared to traditional vending machines.
Customizable Product Machines
Customizable vending machines allow businesses to select the products offered based on local demand and consumer preferences. This adaptability makes them suitable for retail stores and event venues where specific products can drive sales. Buyers should weigh the benefits of tailored offerings against the initial investment and market research required to identify the best-selling items. Customization can significantly enhance sales potential, but it requires ongoing analysis and adjustment.
Cashless Payment Machines
Cashless vending machines facilitate transactions through mobile payments and credit/debit cards, appealing to tech-savvy consumers in urban environments. These machines are efficient and reduce the burden of cash handling for operators. Businesses should consider the potential alienation of customers who prefer cash transactions. While the speed of transactions can enhance customer satisfaction, the initial investment in cashless technology may be a barrier for some operators.
Interactive Experience Machines
These innovative vending machines engage customers through interactive games or quizzes that offer discounts or rewards. They are perfect for malls and entertainment centers, where customer engagement is crucial. B2B buyers should assess the ongoing content management and maintenance needed to keep these machines attractive and functional. While they can foster brand loyalty and customer interaction, the complexity of managing the interactive elements can pose challenges for operators.
Related Video: What Makes Large Language Models Expensive?
Key Industrial Applications of small touch screen vending machine
Industry/Sector | Specific Application of small touch screen vending machine | Value/Benefit for the Business | Key Sourcing Considerations for this Application |
---|---|---|---|
Retail | Automated snack and beverage dispensing | Increases sales through 24/7 availability | Size and space requirements, payment system integration |
Education | Campus convenience stores | Provides easy access to snacks and supplies for students | Custom branding options, security features |
Healthcare | Medication dispensing in hospitals | Improves patient adherence to medication schedules | Compliance with health regulations, user-friendly design |
Transportation | Ticket and pass vending at transit stations | Streamlines passenger flow and reduces queues | Durability for outdoor use, software updates for pricing |
Corporate Offices | Employee refreshment stations | Enhances workplace satisfaction and productivity | Inventory management systems, eco-friendly options |
Retail
In the retail sector, small touch screen vending machines serve as automated snack and beverage dispensers. These machines allow businesses to operate round-the-clock, catering to customer demands outside of regular hours. This is particularly valuable in urban areas or locations with high foot traffic. International buyers should consider the machine’s size, integration with existing payment systems, and the potential for custom branding to enhance visibility and sales.
Education
Within educational institutions, these vending machines are deployed in campus convenience stores, providing students with easy access to snacks, beverages, and essential supplies. This not only meets the immediate needs of students but also drives revenue for the institution. Buyers from Africa, South America, and Europe should focus on customization options that align with student preferences and ensure robust security features to prevent theft.
Healthcare
In healthcare settings, small touch screen vending machines are utilized for medication dispensing, significantly improving patient adherence to prescribed schedules. These machines can be strategically placed in hospitals or clinics, allowing for easy access to essential medications. Buyers must ensure compliance with health regulations and consider user-friendly designs that accommodate various patient demographics, including the elderly.
Transportation
Transportation hubs, such as bus and train stations, benefit from vending machines that dispense tickets and passes. This application streamlines passenger flow, reduces waiting times, and enhances the overall travel experience. For B2B buyers, durability for outdoor use and the capability for software updates to reflect pricing changes are critical considerations when sourcing these machines.
Corporate Offices
In corporate environments, small touch screen vending machines can serve as employee refreshment stations, offering snacks and beverages that enhance workplace satisfaction and productivity. This convenience can lead to increased morale and decreased downtime for employees. Key sourcing considerations include inventory management systems to monitor stock levels and the availability of eco-friendly product options to align with corporate sustainability goals.
Related Video: simple pos system for small business with Bill Printing in java | Touch screen POS
Strategic Material Selection Guide for small touch screen vending machine
When selecting materials for small touch screen vending machines, it’s crucial to consider properties that directly impact performance, durability, and user experience. Below is an analysis of four common materials used in the construction of these machines, including their key properties, advantages, disadvantages, and considerations for international B2B buyers.
1. Stainless Steel
Key Properties:
Stainless steel is known for its excellent corrosion resistance, high strength, and ability to withstand high temperatures. It typically has a temperature rating of up to 800°F (427°C) and is resistant to a variety of chemicals, making it suitable for various environments.
Pros & Cons:
The primary advantage of stainless steel is its durability and resistance to corrosion, which extends the lifespan of vending machines in humid or harsh environments. However, it can be more expensive than other materials and may require complex manufacturing processes, such as welding and polishing.
Impact on Application:
Stainless steel is particularly effective in applications where hygiene is paramount, such as food and beverage vending machines. Its smooth surface is easy to clean, which is essential for maintaining health standards.
Considerations for International Buyers:
Buyers should ensure compliance with local food safety standards and certifications, such as ISO 22000. Additionally, preferences for stainless steel grades may vary by region, with European markets favoring AISI 304 or 316 grades.
2. Polycarbonate
Key Properties:
Polycarbonate is a high-impact resistant plastic that can withstand temperatures ranging from -40°F to 240°F (-40°C to 115°C). It is also lightweight and offers good optical clarity.
Pros & Cons:
The main advantage of polycarbonate is its excellent impact resistance, making it ideal for protecting touch screens from vandalism. However, it is less resistant to scratches compared to glass and can be more susceptible to UV degradation if not treated.
Impact on Application:
Polycarbonate is often used for touch screen covers and transparent panels, providing a balance between visibility and protection. Its lightweight nature can also reduce shipping costs.
Considerations for International Buyers:
Buyers should look for compliance with ASTM standards for impact resistance and UV stability. In regions with high UV exposure, selecting UV-stabilized polycarbonate is advisable.
3. Aluminum
Key Properties:
Aluminum is lightweight, corrosion-resistant, and has a melting point of around 1,221°F (660°C). It is also a good conductor of heat, which can be beneficial for thermal management in electronic components.
Pros & Cons:
Aluminum’s lightweight nature makes it easy to transport and install, while its corrosion resistance allows for outdoor applications. However, it can be more expensive than steel and may require additional treatments (like anodizing) to enhance its corrosion resistance.
Impact on Application:
Aluminum is often used for the structural components of vending machines, providing strength without excessive weight. Its thermal properties can help manage heat dissipation from electronic components.
Considerations for International Buyers:
Buyers should verify compliance with local regulations concerning aluminum alloys and coatings. Different regions may have specific preferences for alloy types, such as 6061 or 5052.
4. Glass
Key Properties:
Glass is a rigid material with excellent optical clarity and resistance to scratching. It can handle temperatures up to 1,000°F (538°C) depending on the type of glass used.
Pros & Cons:
The key advantage of glass is its aesthetic appeal and durability. However, it is more fragile than other materials and can shatter upon impact, which poses a risk in high-traffic areas.
Impact on Application:
Glass is commonly used for touch screen interfaces, providing a high-quality user experience. Its smooth surface is also easy to clean, which is beneficial for hygiene.
Considerations for International Buyers:
Buyers should ensure that the glass used meets safety standards, such as tempered glass regulations. Additionally, considerations for weight and fragility are crucial in regions prone to vandalism.
Summary Table
Material | Typical Use Case for small touch screen vending machine | Key Advantage | Key Disadvantage/Limitation | Relative Cost (Low/Med/High) |
---|---|---|---|---|
Stainless Steel | Structural components, outer casing | Excellent durability and corrosion resistance | Higher cost and complex manufacturing | High |
Polycarbonate | Touch screen covers, protective panels | High impact resistance | Susceptible to scratching and UV degradation | Medium |
Aluminum | Structural components, framing | Lightweight and corrosion-resistant | More expensive than steel, may need coatings | Medium |
Glass | Touch screen interfaces, display panels | Aesthetic appeal and scratch resistance | Fragile and can shatter easily | Medium |
This guide provides actionable insights for international B2B buyers, enabling them to make informed material selections for small touch screen vending machines based on performance, cost, and compliance considerations.
In-depth Look: Manufacturing Processes and Quality Assurance for small touch screen vending machine
Manufacturing Processes for Small Touch Screen Vending Machines
The manufacturing of small touch screen vending machines involves several critical stages, each with specific techniques and quality assurance practices. Understanding these processes can help international B2B buyers make informed decisions when sourcing these machines.
1. Material Preparation
Key Components: The initial stage involves selecting high-quality raw materials, including metals for the chassis, plastics for the casing, and electronic components for the touch screen interface.
Techniques:
– Sourcing: Suppliers should be vetted for their ability to provide materials that meet international standards, particularly for durability and safety.
– Pre-processing: This includes cutting, molding, and treating materials to ensure they meet specifications before assembly.
2. Forming
Processes: This stage includes shaping the chassis and housing of the vending machine.
Techniques:
– Metal Stamping: Used for creating precise metal parts that form the structure of the machine.
– Injection Molding: Commonly used for plastic parts, this process allows for complex shapes and designs.
– Laser Cutting: Employed for intricate designs and to ensure high precision in part dimensions.
3. Assembly
Steps:
– Sub-assembly: Smaller components such as the touch screen, payment systems, and internal electronics are assembled separately before integration.
– Main Assembly: The main frame is assembled with the touch screen, wiring, and other internal components. This is a critical phase where attention to detail ensures all parts fit correctly and function together.
Techniques:
– Robotic Automation: Many manufacturers use robotic arms for repetitive tasks, ensuring consistency and reducing human error.
– Manual Assembly: Skilled workers perform tasks that require precision, such as installing sensitive electronic components.
4. Finishing
Processes: The final stage involves polishing, painting, and applying protective coatings.
Techniques:
– Powder Coating: A durable finish that provides resistance to scratches and corrosion, enhancing the machine’s lifespan.
– Quality Checkpoints: Each machine undergoes visual inspections and functionality tests to ensure it meets design specifications.
Quality Assurance for Small Touch Screen Vending Machines
Quality assurance (QA) is integral to the manufacturing process, particularly for international B2B transactions. Buyers should be aware of the relevant standards and practices.
International Standards
- ISO 9001: This standard ensures that manufacturers maintain a quality management system that consistently meets customer and regulatory requirements.
- CE Marking: Required for products sold in the European Economic Area, indicating compliance with health, safety, and environmental protection standards.
- API Standards: In some regions, adherence to industry-specific standards such as the American Petroleum Institute (API) may be relevant, especially for machines involved in the distribution of food or beverages.
QC Checkpoints
- Incoming Quality Control (IQC): Inspection of raw materials and components upon arrival to ensure they meet specifications.
- In-Process Quality Control (IPQC): Ongoing checks during the manufacturing process to identify and rectify issues early.
- Final Quality Control (FQC): Comprehensive testing of the finished product, including functionality tests for the touch screen, payment systems, and overall performance.
Common Testing Methods
- Functional Testing: Verifying that all features of the vending machine operate as intended.
- Environmental Testing: Assessing the machine’s performance under various conditions, such as temperature extremes and humidity.
- Safety Testing: Ensuring that the machine meets safety standards to protect users from electrical hazards.
Verifying Supplier Quality Control
For B2B buyers, particularly those from Africa, South America, the Middle East, and Europe, ensuring supplier quality is essential. Here are actionable steps:
- Supplier Audits: Conduct on-site audits of manufacturing facilities to assess compliance with international standards and practices.
- Quality Reports: Request detailed quality control reports and documentation from suppliers to understand their QA processes.
- Third-Party Inspections: Engage independent inspection services to evaluate the manufacturing process and finished products before shipment.
- Certifications: Verify that suppliers possess the necessary certifications (e.g., ISO, CE) and that these are current.
QC and Certification Nuances for International Buyers
When engaging with suppliers in various regions, B2B buyers must consider:
- Regional Standards: Different countries may have specific regulations that affect product compliance. Understanding local standards can help prevent costly delays or rejections at customs.
- Cultural Differences: Communication styles and business practices may vary significantly. Building relationships and understanding local business etiquette can facilitate smoother transactions.
- Logistics and Shipping: Ensure that the quality assurance measures are maintained throughout the shipping process to prevent damage or loss of quality.
By understanding the manufacturing processes and quality assurance practices for small touch screen vending machines, international buyers can make informed decisions and establish productive relationships with their suppliers. This knowledge is essential for ensuring the machines meet their operational needs while adhering to local and international regulations.
Related Video: The Production Planning Process
Comprehensive Cost and Pricing Analysis for small touch screen vending machine Sourcing
Cost Structure of Small Touch Screen Vending Machines
When sourcing small touch screen vending machines, understanding the cost structure is crucial for B2B buyers. The primary cost components include:
-
Materials: This covers the components used in the machine, such as the touch screen, frame, dispensing mechanisms, and electronic parts. Higher quality materials can significantly increase costs but also enhance durability and functionality.
-
Labor: Labor costs involve wages for the workforce involved in assembly and manufacturing. Regions with lower labor costs, such as parts of Africa and South America, may provide cost advantages.
-
Manufacturing Overhead: This includes costs associated with factory operations, such as utilities, rent, and equipment maintenance. Overheads can vary widely depending on the location of the manufacturing facility.
-
Tooling: Costs related to the creation and maintenance of molds and other tools required for production. Custom designs may lead to higher tooling costs.
-
Quality Control (QC): Ensuring that products meet specified standards incurs additional costs. Implementing stringent QC processes is essential for maintaining product quality, especially for international buyers.
-
Logistics: This encompasses transportation, warehousing, and distribution costs. Logistics can be a significant expense, particularly for international shipments.
-
Margin: Suppliers will add a profit margin to the total cost, which can vary based on market competition and the supplier’s financial objectives.
Price Influencers
The pricing of small touch screen vending machines is influenced by several factors:
-
Volume/MOQ (Minimum Order Quantity): Larger orders typically lead to lower per-unit costs due to economies of scale. Buyers should evaluate their demand to negotiate favorable terms.
-
Specifications/Customization: Custom features or specifications can increase costs. Buyers need to assess whether the added functionality justifies the price increase.
-
Materials: The choice of materials directly impacts the price. Premium materials often lead to higher costs but can enhance the machine’s longevity and appeal.
-
Quality/Certifications: Machines that comply with international quality standards (e.g., CE, ISO) may have higher prices. However, these certifications can be crucial for market acceptance in regions like Europe and the Middle East.
-
Supplier Factors: The supplier’s reputation, reliability, and production capacity can affect pricing. Established suppliers may charge a premium for their experience and quality assurance.
-
Incoterms: The chosen Incoterms (International Commercial Terms) will influence the overall cost structure. Understanding the implications of terms like FOB (Free on Board) or CIF (Cost, Insurance, and Freight) is essential for cost management.
Buyer Tips
For international B2B buyers, particularly from Africa, South America, the Middle East, and Europe, here are actionable tips:
-
Negotiate: Always negotiate pricing, especially for bulk purchases. Suppliers may have flexibility in their margins.
-
Evaluate Total Cost of Ownership (TCO): Consider not just the purchase price but also the operational costs, maintenance, and expected lifespan of the vending machines.
-
Understand Pricing Nuances: Be aware that currency fluctuations, import duties, and local taxes can significantly impact the final cost of the machines.
-
Conduct Market Research: Benchmark prices from multiple suppliers to ensure competitiveness. This will provide leverage during negotiations.
-
Consider Local Partnerships: Partnering with local distributors or suppliers can reduce logistics costs and improve service delivery.
Disclaimer
Prices and cost structures are indicative and may vary based on market conditions, supplier negotiations, and specific project requirements. It’s advisable to conduct thorough due diligence and consult with multiple suppliers for accurate pricing.
Spotlight on Potential small touch screen vending machine Manufacturers and Suppliers
This section offers a look at a few manufacturers active in the ‘small touch screen vending machine’ market. This is a representative sample for illustrative purposes; B2B buyers must conduct their own extensive due diligence before any engagement. Information is synthesized from public sources and general industry knowledge.
Essential Technical Properties and Trade Terminology for small touch screen vending machine
Key Technical Properties of Small Touch Screen Vending Machines
Understanding the essential technical properties of small touch screen vending machines is crucial for B2B buyers, especially when making informed purchasing decisions. Here are several key specifications that should be considered:
-
Material Grade
The material used in the construction of the vending machine impacts durability and aesthetics. Common materials include stainless steel for the body, tempered glass for the screen, and high-grade plastics for internal components. Selecting high-quality materials ensures longevity and reduces maintenance costs, which is critical for businesses operating in diverse environments. -
Screen Resolution and Size
The resolution of the touch screen affects user experience and interaction. A higher resolution (e.g., 1920 x 1080 pixels) provides clearer visuals, enhancing customer engagement. Screen size, typically ranging from 10 to 22 inches, should be chosen based on the intended placement and user accessibility. This feature is important in ensuring that the interface is user-friendly and visually appealing. -
Power Consumption
Energy efficiency is a vital specification, particularly for businesses looking to minimize operational costs. Vending machines should ideally have low power consumption ratings, often below 200 watts. This consideration not only reduces electricity bills but also aligns with sustainability goals, which is increasingly important for international buyers. -
Payment System Compatibility
The vending machine should support multiple payment methods, including cash, credit/debit cards, and mobile payments (e.g., NFC technology). Compatibility with various payment systems is essential to cater to a wider customer base and enhance sales opportunities. This feature is particularly relevant in regions where cashless transactions are preferred. -
Temperature Control
For machines that dispense perishable items, maintaining the right temperature is crucial. Buyers should look for vending machines with adjustable temperature settings and reliable refrigeration systems. This ensures product safety and quality, which is essential for maintaining customer satisfaction and trust. -
Connectivity Options
Modern vending machines often come equipped with IoT capabilities, allowing for remote monitoring and management. Features like Wi-Fi or GSM connectivity facilitate real-time inventory tracking, sales data analysis, and maintenance alerts. This connectivity is a significant advantage for businesses aiming to optimize operations and enhance service delivery.
Common Trade Terminology
Familiarity with industry terminology is essential for effective communication and negotiation in the procurement process. Here are several key terms that B2B buyers should understand:
-
OEM (Original Equipment Manufacturer)
Refers to a company that produces parts or equipment that may be marketed by another manufacturer. For buyers, engaging with OEMs can lead to customized solutions tailored to specific needs, enhancing the overall value proposition. -
MOQ (Minimum Order Quantity)
This term indicates the smallest quantity of a product that a supplier is willing to sell. Understanding MOQ is critical for buyers to manage inventory effectively and ensure that they meet supplier requirements without overcommitting. -
RFQ (Request for Quotation)
An RFQ is a standard business process to invite suppliers to submit price quotes for specific products or services. For international buyers, issuing an RFQ is a strategic step to obtain competitive pricing and assess supplier capabilities. -
Incoterms (International Commercial Terms)
These are a series of pre-defined international rules that clarify the responsibilities of buyers and sellers regarding the delivery of goods. Understanding Incoterms is essential for buyers to navigate shipping costs, risk transfer, and insurance obligations effectively. -
Lead Time
This term refers to the amount of time from the initiation of a process until its completion. In the context of vending machines, lead time is critical for planning and ensuring timely product delivery, especially in markets with high demand.
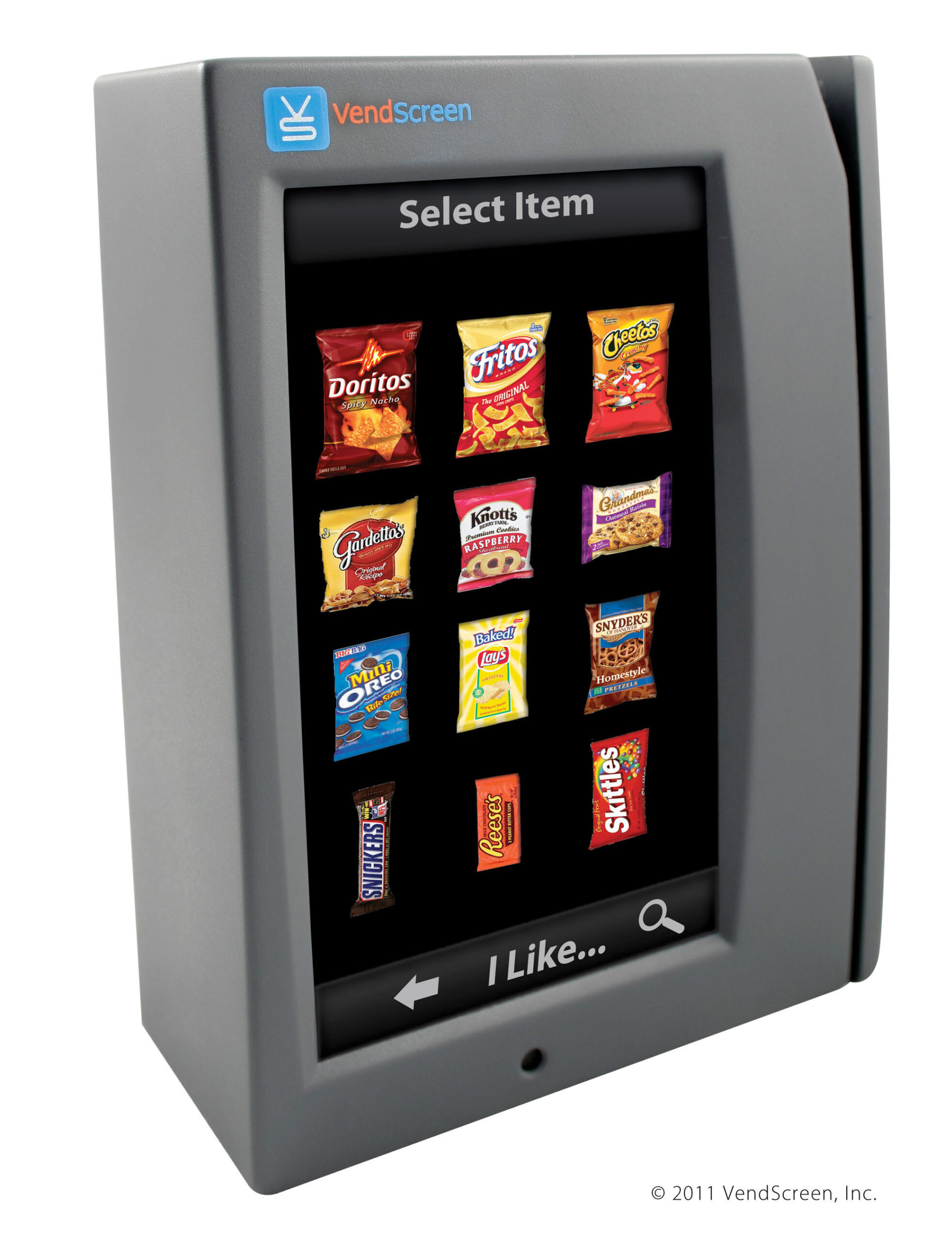
Illustrative Image (Source: Google Search)
- Warranty Period
The warranty period is the duration during which the manufacturer guarantees the performance of the vending machine. Buyers should consider warranty terms as they reflect the manufacturer’s confidence in their product quality and can significantly influence long-term maintenance costs.
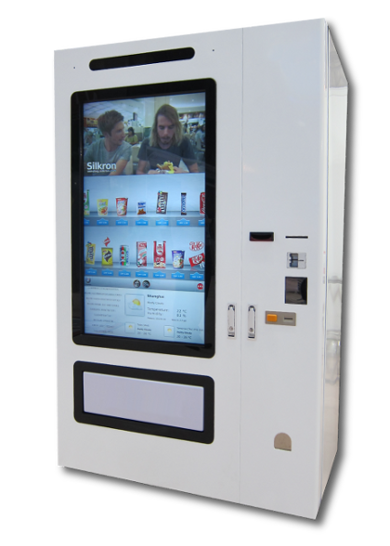
Illustrative Image (Source: Google Search)
By familiarizing themselves with these technical properties and trade terms, international B2B buyers can make more informed purchasing decisions, optimize their procurement processes, and ultimately enhance their business operations.
Navigating Market Dynamics, Sourcing Trends, and Sustainability in the small touch screen vending machine Sector
Global demand for small touch screen vending machines is on the rise, driven by several factors including increasing urbanization, the need for contactless payment solutions, and a growing emphasis on convenience in consumer lifestyles. In regions like Africa and South America, where traditional retail infrastructure may be lacking, these machines offer an innovative solution for reaching consumers in urban and remote areas alike. Furthermore, the integration of advanced technologies such as IoT (Internet of Things) and AI (Artificial Intelligence) is revolutionizing the vending machine sector. This technology allows for real-time inventory management, dynamic pricing, and enhanced user experiences through personalized interactions.
Emerging trends in sourcing for small touch screen vending machines reflect a shift towards automation and smart technology. B2B buyers are increasingly seeking suppliers who can offer integrated solutions that combine hardware with software, enabling seamless operations and analytics. In Europe, for instance, there is a significant move towards machines that can accommodate cashless transactions, reflecting broader consumer preferences. Additionally, in the Middle East, the demand for machines that cater to local tastes and preferences is growing, encouraging suppliers to focus on customization.
Sustainability & Ethical Sourcing in B2B
The environmental impact of manufacturing and operating small touch screen vending machines cannot be overlooked. With rising concerns over waste and energy consumption, B2B buyers are prioritizing sustainability in their sourcing decisions. This involves evaluating the entire lifecycle of vending machines, from materials used to energy efficiency during operation. Buyers should consider suppliers that utilize recycled materials and low-energy components, as well as those that have robust recycling programs for end-of-life machines.
Ethical sourcing is also becoming increasingly important. Companies are expected to uphold high standards in their supply chains, ensuring fair labor practices and environmentally responsible sourcing of materials. Certifications such as ISO 14001 (Environmental Management) and Fair Trade can serve as indicators of a supplier’s commitment to sustainability. By partnering with ethically responsible manufacturers, B2B buyers not only enhance their brand reputation but also contribute positively to global sustainability efforts.
Brief Evolution/History
The small touch screen vending machine sector has evolved significantly over the past few decades. Initially, vending machines were predominantly mechanical, offering limited product options and requiring cash transactions. The introduction of electronic payment systems in the late 20th century marked a pivotal shift, allowing for a broader range of products and improved user experiences. As technology advanced, touch screens became commonplace, offering consumers interactive interfaces that enhanced engagement and convenience. Today, these machines are equipped with smart technologies that allow for data collection and analysis, enabling businesses to better understand consumer preferences and optimize their offerings. This evolution reflects the broader trends of digitization and automation in retail, positioning small touch screen vending machines as a vital component of modern consumer experiences.
Related Video: What Is International Trade?
Frequently Asked Questions (FAQs) for B2B Buyers of small touch screen vending machine
-
What factors should I consider when vetting suppliers for small touch screen vending machines?
When vetting suppliers, assess their industry reputation, experience, and customer reviews. Check for certifications that ensure compliance with international standards. Evaluate their production capacity and technology used in manufacturing. Additionally, inquire about their after-sales service and support, as well as their ability to provide spare parts and maintenance. Conducting factory visits or virtual inspections can also provide insights into their operations. -
Can I customize the vending machines to fit my branding and product offerings?
Yes, many manufacturers offer customization options for small touch screen vending machines. You can typically request specific branding elements such as logos, colors, and design features. Additionally, inquire about modifying the product mix to cater to local preferences, including snack types and pricing structures. Ensure you communicate your requirements clearly during the negotiation phase to avoid misunderstandings. -
What are the typical minimum order quantities (MOQs) and lead times for these machines?
MOQs vary significantly among suppliers, often ranging from 10 to 50 units for small touch screen vending machines. Lead times can also differ based on the supplier’s location, production capacity, and the complexity of your customization. Generally, expect a lead time of 4 to 12 weeks after placing an order. Always clarify these details upfront to manage your inventory planning and cash flow effectively. -
What payment terms are commonly accepted by suppliers?
Payment terms can vary, but most suppliers accept methods like bank transfers, letters of credit, and sometimes PayPal for smaller orders. Typically, a deposit of 30% to 50% is required upfront, with the balance due before shipment. Negotiate favorable terms that align with your cash flow needs, and consider using escrow services for larger transactions to mitigate risks. -
What quality assurance processes should suppliers have in place?
Reputable suppliers should have established quality assurance (QA) protocols, including regular inspections during production and final testing of the machines. Ask for details about their QA certifications, such as ISO 9001, and their process for addressing defects. Request samples before full production to evaluate quality, and consider third-party inspections if you are sourcing from overseas suppliers. -
How can I ensure my logistics needs are met when importing these machines?
Discuss logistics with your supplier early in the negotiation process. Ensure they have experience with international shipping and can provide options for freight forwarding, customs clearance, and insurance. Calculate the total landed cost, including shipping, tariffs, and handling fees, to avoid unexpected expenses. Collaborating with a logistics partner familiar with your region can also streamline the import process. -
What steps should I take in case of a dispute with the supplier?
Establish clear communication channels and document all agreements and correspondences with your supplier. In the event of a dispute, attempt to resolve the issue amicably through direct negotiation. If that fails, refer to the terms outlined in your contract regarding dispute resolution, which may include mediation or arbitration. Consider involving a legal professional experienced in international trade for guidance if necessary. -
What certifications should I look for in small touch screen vending machines?
Look for certifications that demonstrate compliance with safety and quality standards, such as CE marking for Europe or UL certification for the U.S. market. Additionally, check for certifications specific to electrical safety and environmental compliance, like RoHS or WEEE. These certifications not only ensure product quality but also enhance your brand’s reputation in your local market, making it easier to gain customer trust.
Strategic Sourcing Conclusion and Outlook for small touch screen vending machine
In conclusion, the strategic sourcing of small touch screen vending machines presents a significant opportunity for international buyers, especially in emerging markets across Africa, South America, the Middle East, and Europe. Key takeaways include the importance of evaluating suppliers based on technological innovation, adaptability to local market needs, and comprehensive after-sales support. Establishing partnerships with manufacturers that prioritize sustainability and energy efficiency can also enhance your competitive edge.
As you navigate the procurement landscape, remember that strategic sourcing is not merely a transactional approach; it is a long-term investment that can drive profitability and brand loyalty. Engage with suppliers who demonstrate a commitment to quality and customer satisfaction, and leverage technology to streamline your supply chain processes.
Looking ahead, the demand for smart vending solutions is set to grow. By taking proactive steps now—whether it’s through attending trade shows, participating in webinars, or collaborating with industry experts—you can position your business to capitalize on this evolving market. Take action today to secure your place in the future of vending innovation.