Your Ultimate Guide to Sourcing Refurbished Vending
Guide to Refurbished Vending Machines For Sale
- Introduction: Navigating the Global Market for refurbished vending machines for sale
- Understanding refurbished vending machines for sale Types and Variations
- Key Industrial Applications of refurbished vending machines for sale
- Strategic Material Selection Guide for refurbished vending machines for sale
- In-depth Look: Manufacturing Processes and Quality Assurance for refurbished vending machines for sale
- Comprehensive Cost and Pricing Analysis for refurbished vending machines for sale Sourcing
- Spotlight on Potential refurbished vending machines for sale Manufacturers and Suppliers
- Essential Technical Properties and Trade Terminology for refurbished vending machines for sale
- Navigating Market Dynamics, Sourcing Trends, and Sustainability in the refurbished vending machines for sale Sector
- Frequently Asked Questions (FAQs) for B2B Buyers of refurbished vending machines for sale
- Strategic Sourcing Conclusion and Outlook for refurbished vending machines for sale
Introduction: Navigating the Global Market for refurbished vending machines for sale
In today’s dynamic global marketplace, refurbished vending machines stand out as a cost-effective solution for businesses looking to expand their service offerings without the hefty price tag of new equipment. These machines not only provide a sustainable option by reducing waste but also cater to the increasing demand for convenient, automated retail solutions across diverse sectors. For international B2B buyers—particularly those in Africa, South America, the Middle East, and Europe—understanding the nuances of refurbished vending machines can significantly impact sourcing decisions and operational efficiency.
This comprehensive guide delves into various aspects of refurbished vending machines, including types available in the market, the materials used in construction, and the importance of manufacturing quality control. Additionally, it highlights suppliers who specialize in refurbished models, offers insights into cost considerations, and analyzes current market trends. The guide also addresses common FAQs, empowering buyers with the knowledge needed to make informed purchasing decisions.
By leveraging the insights provided in this guide, B2B buyers can navigate the complexities of sourcing refurbished vending machines, ensuring they select high-quality equipment that meets their operational needs while maximizing return on investment. Whether you are a seasoned buyer or entering the vending machine market for the first time, this resource is designed to equip you with the necessary tools for success in the global arena.
Understanding refurbished vending machines for sale Types and Variations
Type Name | Key Distinguishing Features | Primary B2B Applications | Brief Pros & Cons for Buyers |
---|---|---|---|
Snack Vending Machines | Offers a variety of snacks, often adjustable shelves | Office break rooms, schools | Pros: Easy to stock; Cons: Limited to non-perishable items. |
Beverage Vending Machines | Dispenses cold drinks, often with refrigeration | Gyms, public transport stations | Pros: High demand; Cons: Requires power and maintenance. |
Combo Vending Machines | Combines snacks and beverages in one unit | Airports, malls | Pros: Versatile; Cons: More complex to maintain. |
Healthy Food Vending Machines | Focuses on nutritious options, often refrigerated | Hospitals, universities | Pros: Aligns with health trends; Cons: May have higher costs. |
Customized Vending Solutions | Tailored machines with specific products or branding | Corporate events, trade shows | Pros: Brand visibility; Cons: Higher initial investment. |
Snack Vending Machines
Snack vending machines are designed to offer a wide array of snack options, from chips to candy bars. They typically feature adjustable shelves to accommodate different product sizes. These machines are primarily utilized in environments such as office break rooms and schools, where quick snack access is essential. When considering a purchase, buyers should evaluate the machine’s capacity, ease of stocking, and the types of snacks that can be dispensed, keeping in mind that they are limited to non-perishable items.
Beverage Vending Machines
Beverage vending machines are equipped to dispense a variety of cold drinks, including sodas, juices, and bottled water. These machines often include refrigeration units to maintain optimal beverage temperatures. They are commonly found in gyms, public transport stations, and other high-traffic areas where hydration is a priority. Buyers should consider the power requirements, maintenance needs, and the machine’s capacity to ensure it meets demand, as these factors can significantly affect profitability.
Combo Vending Machines
Combo vending machines provide the convenience of offering both snacks and beverages in a single unit. This versatility makes them ideal for locations such as airports and malls, where customers may want a quick snack and drink. When purchasing, businesses should assess the complexity of the machine, as it may require more maintenance than single-product machines. However, the ability to cater to diverse customer needs can enhance sales opportunities.
Healthy Food Vending Machines
With an increasing focus on health and wellness, healthy food vending machines offer nutritious options such as salads, yogurt, and protein bars. These machines are often refrigerated to maintain freshness and are frequently placed in hospitals and universities. Buyers should consider the higher initial investment and ongoing costs associated with stocking perishable items, but the potential to attract health-conscious consumers can lead to increased revenue.
Customized Vending Solutions
Customized vending solutions are tailored to meet specific business needs, whether it be branding or product selection. These machines can range from offering niche products to featuring company logos and designs. They are particularly effective at corporate events and trade shows, where brand visibility is crucial. Buyers should weigh the benefits of increased brand exposure against the higher initial investment and ensure that the customization aligns with their target market’s preferences.
Related Video: USI 3160 ivend snack vending machine for sale used refurbished
Key Industrial Applications of refurbished vending machines for sale
Industry/Sector | Specific Application of Refurbished Vending Machines for Sale | Value/Benefit for the Business | Key Sourcing Considerations for this Application |
---|---|---|---|
Education | Snack and beverage vending in schools and universities | Increases student satisfaction and retention | Compliance with health regulations, payment system integration |
Healthcare | Medication dispensing in hospitals and clinics | Enhances patient adherence to medication schedules | Secure access, temperature control for sensitive items |
Corporate Offices | Employee refreshment stations | Boosts employee morale and productivity | Variety of products, ease of restocking |
Transportation | Vending at airports and train stations | Provides convenience for travelers | High durability, payment options for international users |
Retail | Point-of-sale for smaller retail locations | Expands product offerings without significant overhead | Size and placement, product customization options |
Education Sector
Refurbished vending machines in educational institutions serve as convenient snack and beverage outlets, enhancing the overall experience for students and staff. By providing accessible food options, schools and universities can improve student satisfaction and retention rates. International buyers should consider compliance with local health regulations and ensure the machines are equipped with modern payment systems that cater to the diverse student population, including cashless options.
Healthcare Sector
In hospitals and clinics, refurbished vending machines can be utilized for medication dispensing, allowing patients to access their medications conveniently. This application improves adherence to prescribed medication schedules, as patients can retrieve their doses without having to wait in long lines. For buyers in the healthcare sector, it is crucial to ensure that the vending machines are secure, temperature-controlled, and compliant with health regulations to maintain the integrity of the medications.
Corporate Offices
In corporate environments, refurbished vending machines offer a practical solution for providing employees with snacks and beverages. This not only boosts morale but also enhances productivity by reducing the time employees spend away from their workstations. B2B buyers should focus on the variety of products available and the ease of restocking, ensuring that the machines can accommodate diverse dietary preferences and are operationally efficient.
Transportation Sector
Vending machines at airports and train stations provide travelers with quick access to refreshments, making them an essential service in high-traffic areas. Refurbished machines can be strategically placed to cater to the needs of busy travelers, offering a range of products from snacks to beverages. When sourcing for this application, it is important to consider the machines’ durability and the availability of payment options that accommodate international travelers, such as credit card and mobile payment systems.
Retail Sector
In smaller retail locations, refurbished vending machines can act as a point-of-sale for various products, allowing businesses to expand their offerings without incurring significant overhead costs. This application is particularly beneficial in areas where foot traffic is high but space is limited. Buyers should evaluate the size and placement of the machines, as well as customization options for branding and product selection, to ensure they meet the specific needs of their retail environment.
Related Video: What to look for when buying used vending machines ✅
Strategic Material Selection Guide for refurbished vending machines for sale
When selecting materials for refurbished vending machines, it is essential to consider various factors that impact performance, durability, and cost. The choice of material can significantly influence the machine’s functionality, maintenance needs, and overall lifespan. Below are analyses of four common materials used in the construction of refurbished vending machines, focusing on their properties, advantages, disadvantages, and considerations for international buyers.
1. Stainless Steel
Key Properties: Stainless steel is known for its excellent corrosion resistance, high strength, and ability to withstand high temperatures. It typically has a temperature rating up to 800°F (427°C) and can handle pressures up to 150 psi, depending on the grade.
Pros & Cons: The primary advantage of stainless steel is its durability and resistance to rust and corrosion, making it ideal for machines exposed to moisture and varying temperatures. However, it can be more expensive than other materials and may require specialized manufacturing processes, which can increase costs.
Impact on Application: Stainless steel is compatible with a wide range of media, including food and beverages, which is crucial for vending machines. Its non-reactive nature ensures that it does not alter the taste or quality of the products dispensed.
Considerations for International Buyers: Buyers should ensure compliance with food safety standards such as FDA regulations in the U.S. or EFSA in Europe. Common grades like 304 and 316 are preferred due to their corrosion resistance and suitability for food applications.
2. Carbon Steel
Key Properties: Carbon steel is characterized by its high tensile strength and low cost. It typically has a temperature rating of up to 600°F (316°C) and can handle moderate pressure levels.
Pros & Cons: The primary advantage of carbon steel is its cost-effectiveness, making it a popular choice for budget-conscious buyers. However, it is susceptible to rust and corrosion if not properly coated or maintained, which can lead to increased maintenance costs.
Impact on Application: Carbon steel is suitable for non-corrosive environments and can be used for structural components of vending machines. However, it may not be suitable for machines dispensing food or beverages unless adequately protected.
Considerations for International Buyers: Buyers should be aware of the need for protective coatings to prevent corrosion. Compliance with local standards, such as ASTM in the U.S. and DIN in Europe, is also essential.
3. Aluminum
Key Properties: Aluminum is lightweight, corrosion-resistant, and has good thermal conductivity. It typically has a temperature rating of up to 400°F (204°C) and can withstand moderate pressure.
Pros & Cons: The lightweight nature of aluminum makes it easier to transport and install. However, it may not be as durable as stainless steel or carbon steel and can be more expensive than carbon steel.
Impact on Application: Aluminum is suitable for various applications, including exterior panels and internal components. Its corrosion resistance makes it ideal for machines in humid environments.
Considerations for International Buyers: Buyers should consider the specific alloy used, as different grades can have varying properties. Compliance with international standards such as JIS in Japan or EN in Europe is crucial for ensuring quality.
4. Plastic Composites
Key Properties: Plastic composites are lightweight and resistant to corrosion and chemicals. They can handle temperatures up to 180°F (82°C) and are generally not suitable for high-pressure applications.
Pros & Cons: The main advantage of plastic composites is their low weight and resistance to corrosion, making them ideal for specific components of vending machines. However, they may not be as strong as metal alternatives and can be less durable over time.
Impact on Application: Plastic composites are suitable for internal components that do not require high strength or pressure resistance. They are often used in areas where moisture exposure is a concern.
Considerations for International Buyers: Buyers should ensure that the plastic composites used are compliant with local regulations regarding food safety and environmental standards. Understanding the specific type of plastic and its properties is essential for ensuring suitability.
Material | Typical Use Case for refurbished vending machines for sale | Key Advantage | Key Disadvantage/Limitation | Relative Cost (Low/Med/High) |
---|---|---|---|---|
Stainless Steel | Exterior panels, internal components for food vending | Excellent corrosion resistance and durability | Higher cost, requires specialized manufacturing | High |
Carbon Steel | Structural components for non-food vending machines | Cost-effective, good strength | Susceptible to rust without protective coatings | Low |
Aluminum | Exterior panels, lightweight internal components | Lightweight, good corrosion resistance | Less durable than steel, can be more expensive | Medium |
Plastic Composites | Internal components, moisture-prone areas | Lightweight, corrosion-resistant | Less strength, not suitable for high-pressure areas | Low |
This strategic material selection guide aims to assist international B2B buyers in making informed decisions regarding the materials used in refurbished vending machines. Understanding the properties, advantages, disadvantages, and compliance requirements of each material is crucial for ensuring optimal performance and longevity of the machines in diverse environments.
In-depth Look: Manufacturing Processes and Quality Assurance for refurbished vending machines for sale
Manufacturing processes and quality assurance play a crucial role in ensuring that refurbished vending machines meet the high standards expected by international B2B buyers. This section delves into the typical stages involved in manufacturing refurbished vending machines and the quality control measures that are essential for maintaining product integrity and compliance with international standards.
Manufacturing Processes
The manufacturing process for refurbished vending machines typically involves several key stages, each critical to delivering a high-quality final product. Here’s an overview of these stages:
-
Material Preparation
– Sourcing Components: Refurbishment begins with sourcing high-quality parts. This may include electronic components, mechanical systems, and structural materials. Suppliers should provide documentation verifying the quality and origin of these parts.
– Inspection of Materials: Each component undergoes an incoming quality control (IQC) check to ensure it meets specifications and standards. This includes visual inspections and functional tests. -
Forming
– Structural Framework: The frame of the vending machine is constructed, typically using steel or aluminum. Techniques such as laser cutting and bending are common to ensure precision and durability.
– Electrical Assembly: Wiring and electronic components are installed during this stage. Automated and manual processes are often used to ensure correct assembly and functionality. -
Assembly
– Integration of Components: All parts, including refrigeration units, payment systems, and display interfaces, are integrated. This stage often involves both automated assembly lines and skilled labor to ensure proper alignment and functionality.
– Software Installation: Modern vending machines often come equipped with software for payment processing and inventory management. This software is installed and tested to ensure seamless operation. -
Finishing
– Surface Treatment: Finishing processes such as painting, powder coating, or plating are applied to enhance durability and aesthetics. This is also a point where any branding or design elements are added.
– Final Inspection: Before the machines are packaged, they undergo a final quality control (FQC) check to verify that all components are functioning correctly and that the machine meets the required standards.
Quality Assurance
Quality assurance is integral to the refurbishment process, ensuring that the final product is safe, reliable, and compliant with international standards. Here are key aspects of quality control relevant to refurbished vending machines:
-
International Standards
– ISO 9001: This standard outlines a framework for quality management systems (QMS) that can enhance customer satisfaction and operational efficiency. Suppliers should be able to demonstrate certification or compliance with ISO 9001.
– CE Marking: In Europe, CE marking indicates compliance with health, safety, and environmental protection standards. This is particularly relevant for electrical and electronic equipment. -
Industry-Specific Standards
– API Standards: The American Petroleum Institute standards may apply if the vending machines include fuel dispensing capabilities. Ensure that suppliers adhere to relevant API specifications.
– Local Regulations: In regions like Africa and South America, understanding local compliance requirements is vital. These may differ significantly from international standards. -
Quality Control Checkpoints
– Incoming Quality Control (IQC): Initial checks on materials and components to ensure they meet specifications.
– In-Process Quality Control (IPQC): Ongoing inspections during manufacturing to catch any defects early in the process.
– Final Quality Control (FQC): Comprehensive testing of the finished product to ensure it meets all operational and safety standards. -
Common Testing Methods
– Functional Testing: Each machine is tested for operational capabilities, including payment processing and mechanical functions.
– Durability Testing: Machines undergo stress tests to ensure they can withstand typical usage conditions.
– Safety Testing: Compliance with electrical safety standards is verified through rigorous testing.
Verifying Supplier Quality Control
For B2B buyers, verifying the quality control processes of suppliers is essential to ensure product reliability. Here are actionable steps to undertake:
-
Audits: Conduct regular audits of suppliers’ manufacturing facilities. This can be done in person or through third-party auditing firms. Audits should focus on adherence to quality standards and processes.
-
Quality Reports: Request detailed quality assurance reports from suppliers. These should include data from IQC, IPQC, and FQC stages, demonstrating the efficacy of their quality control measures.
-
Third-Party Inspections: Engage independent inspection agencies to evaluate the quality of refurbished vending machines before purchase. These inspections can provide an unbiased assessment of product quality and compliance with standards.
-
Certification Verification: Ensure that suppliers can provide certifications for their quality management systems and product compliance. This includes ISO certifications, CE markings, and other relevant industry certifications.
Navigating QC Nuances for International Buyers
International B2B buyers, especially from regions like Africa, South America, the Middle East, and Europe, should be aware of several nuances in quality control:
- Cultural Differences: Quality expectations may vary across regions. Engage with suppliers to understand their quality philosophies and practices.
- Logistics and Shipping: Consider how logistics may affect quality. Machines should be adequately packaged to prevent damage during transit. Ensure that suppliers have robust shipping protocols.
- After-Sales Support: Assess the supplier’s capability for after-sales service, including maintenance and parts supply. A strong support system is essential for ensuring long-term satisfaction with refurbished vending machines.
By understanding the intricacies of the manufacturing and quality assurance processes, international B2B buyers can make informed decisions when purchasing refurbished vending machines, ensuring they receive high-quality products that meet their operational needs.
Related Video: The Production Planning Process
Comprehensive Cost and Pricing Analysis for refurbished vending machines for sale Sourcing
The cost structure and pricing analysis for refurbished vending machines involve several components and influencers that international B2B buyers must consider. Understanding these elements can lead to more informed purchasing decisions and effective negotiations.
Cost Components
-
Materials: The primary cost driver is the quality and type of materials used in the refurbishment process. Components such as vending mechanisms, casings, and electronic parts significantly affect the overall cost. Buyers should inquire about the sourcing of these materials to ensure quality and sustainability.
-
Labor: Labor costs vary based on the location of the refurbishment facility. Skilled labor is essential for ensuring that the machines meet quality standards, and labor costs can be lower in regions with a favorable labor market. Buyers should evaluate the labor practices and expertise of the refurbishing company.
-
Manufacturing Overhead: This includes costs associated with utilities, facility maintenance, and administrative expenses. Understanding how overhead is calculated can provide insight into pricing. Buyers might negotiate for better rates if they are placing bulk orders.
-
Tooling: If specific tools are required for the refurbishment process, these costs must be factored in. Tooling costs can vary based on the complexity of the machines being refurbished. Buyers should ask if the supplier has the necessary tools in-house or if additional costs will be incurred.
-
Quality Control (QC): Effective quality control processes are crucial for refurbished machines. This includes testing and certification of the machines, which can add to the cost. Buyers should look for suppliers that provide certifications or warranties as part of their QC process.
-
Logistics: Shipping costs can vary significantly depending on the distance and method of transport. For international buyers, understanding Incoterms (International Commercial Terms) is essential, as they dictate who bears the cost and risk during shipping.
-
Margin: Finally, the supplier’s profit margin will influence the final price. Understanding the competitive landscape can help buyers assess whether margins are reasonable.
Price Influencers
-
Volume/MOQ (Minimum Order Quantity): Purchasing in larger quantities often leads to discounts. Buyers should consider their long-term needs to take advantage of bulk pricing.
-
Specifications/Customization: Custom features or specific configurations can increase costs. Buyers should be clear about their requirements upfront to avoid unexpected expenses.
-
Materials and Quality/Certifications: Higher quality materials and certified machines typically command higher prices. Buyers should weigh the benefits of quality against budget constraints.
-
Supplier Factors: The supplier’s reputation, reliability, and after-sales service can affect pricing. Established suppliers may charge more but offer better warranties and support.
Buyer Tips
-
Negotiation: Effective negotiation can significantly impact pricing. Buyers should prepare by researching market rates and being ready to discuss their needs openly.
-
Cost-Efficiency: Evaluate not just the purchase price but the total cost of ownership (TCO), which includes maintenance and operational costs over the machine’s lifespan.
-
Pricing Nuances for International Buyers: Different regions have varying market dynamics. Buyers from Africa, South America, the Middle East, and Europe should consider local economic conditions, import tariffs, and currency fluctuations that may affect pricing.
Disclaimer
Prices for refurbished vending machines can vary widely based on the factors discussed. It is crucial for buyers to conduct thorough research and obtain multiple quotes to ensure they are making a cost-effective decision.
Spotlight on Potential refurbished vending machines for sale Manufacturers and Suppliers
This section offers a look at a few manufacturers active in the ‘refurbished vending machines for sale’ market. This is a representative sample for illustrative purposes; B2B buyers must conduct their own extensive due diligence before any engagement. Information is synthesized from public sources and general industry knowledge.
Essential Technical Properties and Trade Terminology for refurbished vending machines for sale
When considering the purchase of refurbished vending machines, international B2B buyers must understand the essential technical properties and industry terminology that influence both product quality and trade efficiency. Below are critical specifications and common trade terms that will aid in informed decision-making.
Key Technical Properties of Refurbished Vending Machines
-
Material Grade
– Definition: This refers to the type and quality of materials used in the construction of the vending machine, such as stainless steel, aluminum, or plastic.
– Importance: High-grade materials ensure durability and resistance to corrosion, which is particularly vital in diverse climates across Africa, South America, and the Middle East. Buyers should look for machines made from materials that can withstand local environmental conditions. -
Capacity
– Definition: This specification indicates the number of items the vending machine can hold, often expressed in terms of the number of slots or total weight.
– Importance: Understanding capacity is crucial for inventory management and sales forecasting. Buyers should select machines that align with their expected customer traffic and product offerings. -
Power Consumption
– Definition: This measures the energy efficiency of the vending machine, typically indicated in watts.
– Importance: Efficient power usage reduces operational costs and is particularly significant for businesses in regions with high energy prices. A lower power consumption rating can lead to substantial savings over time. -
Payment System Compatibility
– Definition: This refers to the types of payment methods the machine accepts, such as coins, bills, credit cards, or mobile payments.
– Importance: Compatibility with various payment systems enhances consumer convenience and can increase sales. As payment technology evolves, machines that support multiple payment options will be more appealing to customers.
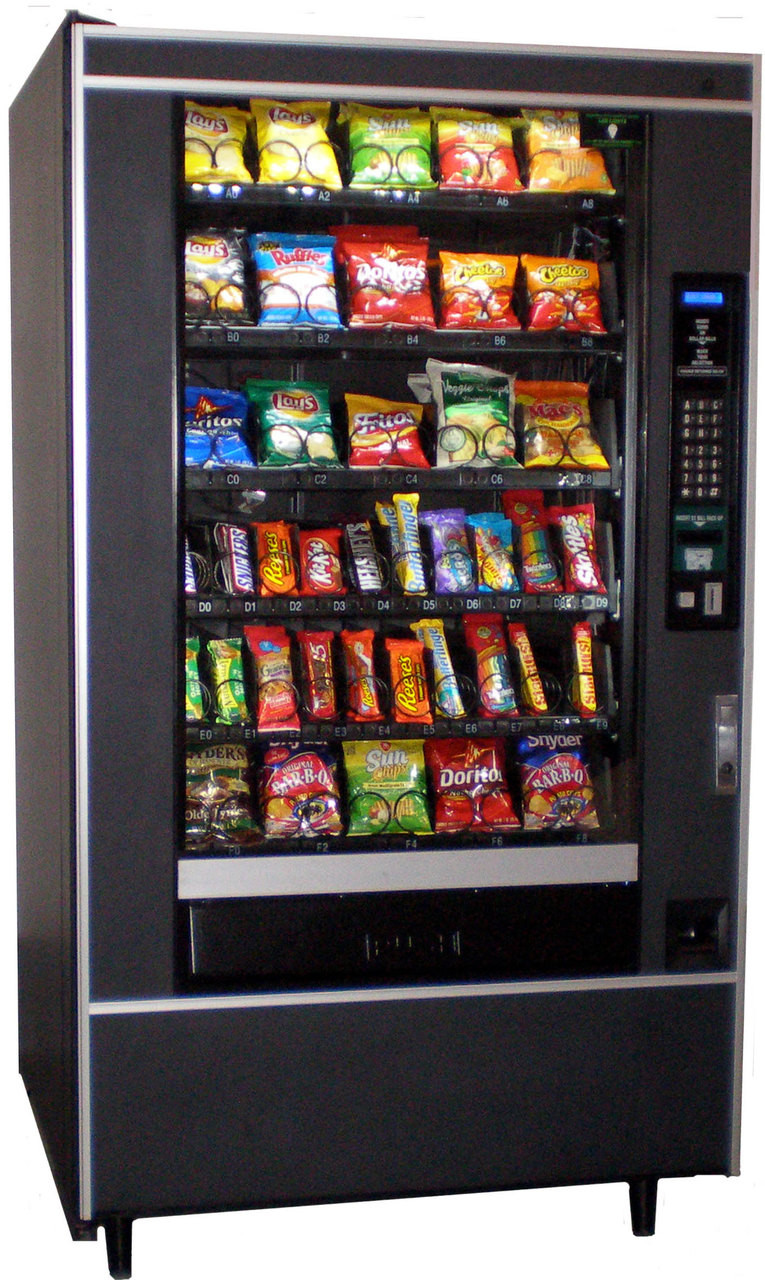
Illustrative Image (Source: Google Search)
-
Temperature Control
– Definition: This specification indicates the ability of the vending machine to maintain specific temperature ranges for perishable items.
– Importance: For machines that dispense food or beverages, effective temperature control is crucial to comply with health regulations and maintain product quality. Buyers should verify that the machines meet local food safety standards. -
Dimensions and Weight
– Definition: These specifications provide the physical size and weight of the vending machine.
– Importance: Understanding the dimensions is essential for space planning and installation. Furthermore, weight can affect transportation costs and logistics, especially when shipping internationally.
Common Trade Terminology
-
OEM (Original Equipment Manufacturer)
– Definition: A company that produces parts or equipment that may be marketed by another manufacturer.
– Relevance: Knowing whether a refurbished vending machine is from an OEM can indicate the quality and reliability of the components used. -
MOQ (Minimum Order Quantity)
– Definition: The smallest quantity of goods that a supplier is willing to sell.
– Relevance: Understanding MOQ helps in budget planning and inventory management, especially for businesses looking to scale operations. -
RFQ (Request for Quotation)
– Definition: A standard business process where a buyer requests pricing and delivery terms from suppliers.
– Relevance: Issuing an RFQ can help buyers compare multiple suppliers and negotiate better terms, ensuring they get the best deal possible. -
Incoterms (International Commercial Terms)
– Definition: A series of predefined commercial terms published by the International Chamber of Commerce (ICC) related to international commercial law.
– Relevance: Familiarity with Incoterms is vital for understanding shipping responsibilities and liabilities, reducing the risk of misunderstandings during international transactions.
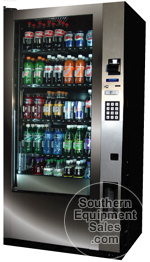
Illustrative Image (Source: Google Search)
-
Lead Time
– Definition: The amount of time it takes from placing an order to delivery.
– Relevance: Knowing the lead time is crucial for planning and ensuring that machines arrive when needed, which is especially important for seasonal businesses. -
Warranty
– Definition: A guarantee provided by the seller regarding the condition of the product and the terms of repair or replacement.
– Relevance: A robust warranty can provide peace of mind and reduce future costs related to repairs or replacements.
By understanding these technical properties and terms, B2B buyers can make well-informed decisions when purchasing refurbished vending machines, ensuring they meet their business needs effectively.
Navigating Market Dynamics, Sourcing Trends, and Sustainability in the refurbished vending machines for sale Sector
Market Overview & Key Trends
The market for refurbished vending machines is experiencing a notable shift driven by the increasing demand for cost-effective and sustainable solutions. As businesses and institutions look to optimize their operational costs, refurbished machines present a viable alternative to new equipment, often at a fraction of the price. This trend is particularly relevant for international B2B buyers in regions such as Africa, South America, the Middle East, and Europe, where budget constraints and economic fluctuations necessitate smarter purchasing decisions.
Emerging technologies are also influencing the market dynamics. The integration of IoT (Internet of Things) capabilities in vending machines allows for enhanced monitoring, inventory management, and user engagement. These advancements are crucial for buyers looking to improve service efficiency and customer satisfaction. Moreover, a shift towards cashless transactions and mobile payments is becoming standard, prompting manufacturers to refurbish machines that accommodate these payment methods.
As the refurbished vending machine sector evolves, buyers should be aware of the growing importance of supplier transparency and reliability. Ensuring that suppliers have a robust refurbishment process and quality assurance measures in place is essential for maintaining product quality and reliability.
Sustainability & Ethical Sourcing in B2B
Sustainability has become a critical consideration for B2B buyers, especially as global awareness of environmental issues rises. Refurbished vending machines represent a sustainable option by extending the lifecycle of existing products, thereby reducing waste and the demand for new raw materials. This practice not only conserves resources but also lowers the carbon footprint associated with manufacturing new machines.
Ethical sourcing is equally important, as buyers increasingly prefer suppliers who adhere to sustainable practices. This includes using environmentally friendly materials and ensuring that the refurbishment process is conducted with minimal environmental impact. Certifications such as ISO 14001 (Environmental Management) and adherence to local environmental regulations can serve as indicators of a supplier’s commitment to sustainability.
Buyers should also consider the benefits of partnering with suppliers who prioritize green practices, as this can enhance their own corporate social responsibility (CSR) profiles. Incorporating sustainability into procurement strategies can lead to stronger brand loyalty and a competitive edge in the marketplace.
Brief Evolution/History
The concept of refurbished vending machines has evolved significantly over the past few decades. Initially, the market was dominated by new machines, but increasing costs and environmental concerns have shifted focus towards refurbishment. This shift began in the early 2000s when businesses recognized the value of extending the life of existing machines rather than investing in new ones.
As technology advanced, refurbishment processes improved, allowing for more sophisticated upgrades. Today, refurbished vending machines can compete with new models in terms of functionality and features, making them an attractive option for cost-conscious international buyers. This evolution reflects broader trends in the circular economy, where the emphasis is placed on sustainability and resource efficiency.
Related Video: Incoterms for beginners | Global Trade Explained
Frequently Asked Questions (FAQs) for B2B Buyers of refurbished vending machines for sale
-
What should I consider when vetting suppliers of refurbished vending machines?
When vetting suppliers, prioritize their experience in the vending machine industry and their track record in refurbishing equipment. Look for certifications or memberships in recognized industry associations that demonstrate credibility. Request references from previous clients and verify their operational practices, including compliance with local regulations. Additionally, assess their after-sales support and warranty policies to ensure you are partnering with a reliable supplier. -
Can I customize refurbished vending machines to fit my brand?
Yes, many suppliers offer customization options for refurbished vending machines. You can request specific branding, color schemes, and features tailored to your market needs. Discuss your requirements with potential suppliers to understand the extent of customization they can provide. Keep in mind that customization may impact lead times and costs, so clarify these aspects upfront. -
What are the typical minimum order quantities (MOQ) and lead times for refurbished vending machines?
MOQs can vary significantly based on the supplier and the type of vending machines you are purchasing. Some suppliers may allow orders as low as one unit, while others may require a minimum of five or ten units. Lead times also differ, generally ranging from 4 to 12 weeks depending on the extent of refurbishment, customization, and shipping logistics. Always confirm these details before placing an order to avoid surprises. -
What payment terms should I expect when purchasing refurbished vending machines?
Payment terms can vary by supplier, but common practices include a deposit (often 30-50%) upfront, with the balance due upon delivery or installation. Some suppliers may offer financing options, allowing you to spread payments over time. Always negotiate terms that align with your cash flow needs and ensure to clarify any additional costs that may arise, such as shipping or customization fees. -
How can I ensure the quality of refurbished vending machines?
To ensure quality, request detailed information about the refurbishment process, including the standards used and any quality assurance measures in place. Ask for certifications or warranties that guarantee the machines have been thoroughly tested and are in good working order. It’s also advisable to request a trial period or a return policy, allowing you to assess the machines’ performance after delivery. -
What logistics considerations should I keep in mind when sourcing from international suppliers?
Logistics is crucial when sourcing refurbished vending machines internationally. Factor in shipping costs, customs duties, and potential delays in transit. Confirm the supplier’s ability to handle logistics, including whether they provide shipping services or if you need to arrange your own. Establish clear communication regarding delivery timelines and ensure that you have a reliable logistics partner to facilitate smooth transportation. -
What should I do in case of disputes with my supplier?
In the event of a dispute, first attempt to resolve the issue directly with the supplier through open communication. Document all interactions and agreements to maintain a clear record. If a resolution cannot be reached, refer to the terms outlined in your contract regarding dispute resolution, which may include mediation or arbitration. Familiarize yourself with local laws and regulations that govern international trade to understand your rights and obligations. -
Are there specific certifications I should look for in refurbished vending machines?
Yes, look for certifications that indicate compliance with safety and quality standards, such as ISO 9001 for quality management systems or CE marking for compliance with European health, safety, and environmental protection standards. Additionally, check if the machines meet local regulations in your country regarding food safety and electrical safety, particularly if they dispense consumables. These certifications can help ensure the machines are safe and reliable for your business operations.
Strategic Sourcing Conclusion and Outlook for refurbished vending machines for sale
As the demand for refurbished vending machines continues to rise, international B2B buyers must strategically navigate their sourcing decisions. Key takeaways include the importance of evaluating the quality and reliability of suppliers, understanding regional regulations, and leveraging technology to streamline procurement processes. By focusing on these factors, buyers can ensure they are making informed decisions that align with their operational goals and market needs.
Strategic sourcing not only enhances cost-efficiency but also promotes sustainability, a critical aspect for businesses aiming to reduce their environmental impact. Buyers from Africa, South America, the Middle East, and Europe should prioritize partnerships with reputable suppliers who offer warranties and after-sales support, ensuring long-term satisfaction and operational continuity.
Looking ahead, the refurbished vending machine market presents significant opportunities. Engaging with local distributors and participating in industry trade shows can provide valuable insights and networking opportunities, paving the way for successful partnerships. Now is the time for B2B buyers to act decisively, harnessing the potential of refurbished vending machines to enhance their offerings and meet evolving consumer preferences.