Your Ultimate Guide to Sourcing Ramen Noodle Vending Machine
Guide to Ramen Noodle Vending Machine
- Introduction: Navigating the Global Market for ramen noodle vending machine
- Understanding ramen noodle vending machine Types and Variations
- Key Industrial Applications of ramen noodle vending machine
- Strategic Material Selection Guide for ramen noodle vending machine
- In-depth Look: Manufacturing Processes and Quality Assurance for ramen noodle vending machine
- Comprehensive Cost and Pricing Analysis for ramen noodle vending machine Sourcing
- Spotlight on Potential ramen noodle vending machine Manufacturers and Suppliers
- Essential Technical Properties and Trade Terminology for ramen noodle vending machine
- Navigating Market Dynamics, Sourcing Trends, and Sustainability in the ramen noodle vending machine Sector
- Frequently Asked Questions (FAQs) for B2B Buyers of ramen noodle vending machine
- Strategic Sourcing Conclusion and Outlook for ramen noodle vending machine
Introduction: Navigating the Global Market for ramen noodle vending machine
In the rapidly evolving landscape of automated food service solutions, the ramen noodle vending machine stands out as a game-changer for international markets. These machines not only cater to the growing consumer demand for quick, convenient meals but also offer an innovative way to tap into diverse culinary preferences. As B2B buyers, particularly from Africa, South America, the Middle East, and Europe, understanding the dynamics of this market is crucial for making informed purchasing decisions.
This comprehensive guide delves into the essential elements surrounding ramen noodle vending machines, covering various types and materials used in their production, as well as insights into manufacturing processes and quality control standards. It also provides a thorough analysis of suppliers, cost structures, and the overall market landscape. By addressing common FAQs, we equip buyers with the knowledge necessary to navigate this niche yet lucrative segment effectively.
As the global market for vending solutions continues to expand, this guide empowers international B2B buyers to identify reliable partners and optimize their sourcing strategies. With actionable insights tailored for regions such as Colombia and Germany, you will be better positioned to capitalize on the growing trend of automated food services and enhance your business offerings. Embrace the future of dining convenience and discover how ramen noodle vending machines can elevate your business strategy.
Understanding ramen noodle vending machine Types and Variations
Type Name | Key Distinguishing Features | Primary B2B Applications | Brief Pros & Cons for Buyers |
---|---|---|---|
Traditional Ramen Vending Machine | Dispenses hot ramen in cups; often includes a variety of flavors | Restaurants, food courts, convenience stores | Pros: Popular and familiar; easy to operate. Cons: Limited menu options; requires regular maintenance. |
Automated Ramen Dispenser | Fully automated, can prepare ramen with fresh ingredients on-demand | High-traffic areas, corporate offices | Pros: Fresh and customizable; can attract tech-savvy customers. Cons: Higher initial investment; complex maintenance. |
Instant Ramen Vending Machine | Offers pre-packaged instant ramen; usually includes hot water dispenser | Schools, universities, and public transport | Pros: Low operational cost; quick service. Cons: Quality may not match fresh options; limited appeal. |
Gourmet Ramen Vending Machine | Focuses on premium, gourmet ramen options; often features unique flavors | Upscale venues, specialty shops | Pros: Attracts food enthusiasts; higher profit margins. Cons: Higher price point; niche market appeal. |
Multi-Functional Snack Machine | Combines ramen with other snacks and beverages; versatile usage | Airports, shopping malls, and event venues | Pros: Diverse offerings increase sales; caters to various customer preferences. Cons: Requires more space; potential for inventory management issues. |
Traditional Ramen Vending Machine
Traditional ramen vending machines are prevalent in various food service environments, dispensing hot ramen in cups. They typically offer a selection of flavors and are ideal for restaurants and food courts. The primary advantage of this type is its familiarity and ease of operation, making it a reliable choice for businesses. However, buyers should consider the limited menu options and the need for regular maintenance, which can affect operational efficiency.
Automated Ramen Dispenser
Automated ramen dispensers represent the latest in vending technology, preparing ramen with fresh ingredients on-demand. These machines are suitable for high-traffic areas such as corporate offices and shopping centers, where consumers seek quick yet quality meals. The main benefits include customization and freshness, appealing to a tech-savvy clientele. However, potential buyers should be aware of the higher initial investment and the complexity of maintenance compared to traditional machines.
Instant Ramen Vending Machine
Instant ramen vending machines are designed for quick service, offering pre-packaged instant ramen with a hot water dispenser. They are particularly suited for educational institutions and public transport hubs, where speed and convenience are paramount. The operational costs are low, and they provide fast service, making them attractive for budget-conscious buyers. However, the quality may not match that of fresh ramen, which could limit customer satisfaction.
Gourmet Ramen Vending Machine
Gourmet ramen vending machines focus on premium offerings, featuring unique flavors and high-quality ingredients. These machines are ideal for upscale venues and specialty shops aiming to attract food enthusiasts. The main advantage lies in the potential for higher profit margins due to the premium pricing. However, buyers should note that this niche market may limit overall sales volume, requiring careful consideration of location and target demographic.
Multi-Functional Snack Machine
Multi-functional snack machines combine ramen with a variety of other snacks and beverages, providing a versatile option for locations such as airports and shopping malls. This type increases sales potential by catering to diverse customer preferences. The main drawback is the requirement for more space and the complexities of inventory management. Buyers should evaluate the trade-offs between variety and operational efficiency when considering this option.
Related Video: Cup Ramen Noodles Vending Machine Cup Noodles Museum
Key Industrial Applications of ramen noodle vending machine
Industry/Sector | Specific Application of ramen noodle vending machine | Value/Benefit for the Business | Key Sourcing Considerations for this Application |
---|---|---|---|
Education | Campus dining facilities | Provides affordable, quick meal options for students | Space requirements, payment system compatibility |
Hospitality | Hotel lobbies and waiting areas | Enhances guest experience with convenient food options | Machine size, variety of noodle offerings |
Corporate Offices | Employee break rooms | Boosts employee satisfaction and morale | Nutritional content, machine maintenance service |
Healthcare Facilities | Hospital waiting rooms | Offers nutritious meals for visitors and staff | Hygiene standards, energy efficiency |
Transportation Hubs | Airports and train stations | Serves travelers with quick meal solutions | Reliability, adaptability to different environments |
Education Sector
In educational institutions, ramen noodle vending machines can be strategically placed in campus dining facilities or near libraries. These machines provide students with quick, affordable meal options, catering to their busy schedules. The challenge lies in ensuring the machine can handle high foot traffic and is equipped with a variety of flavors to meet diverse student preferences. International buyers must consider space requirements and payment system compatibility, particularly in regions like Africa and South America, where cash transactions may still be prevalent.
Hospitality Sector
Hotels can significantly enhance guest experiences by placing ramen noodle vending machines in lobbies or waiting areas. This convenient food option allows guests to enjoy a quick meal without needing to leave the premises. The key is to provide a range of flavors and ensure the machine is easy to use. For buyers in Europe and the Middle East, sourcing machines that comply with local regulations regarding food safety and quality is crucial.
Corporate Offices
In corporate environments, placing ramen noodle vending machines in employee break rooms can boost satisfaction and morale. Employees appreciate having access to quick meal options, especially during busy workdays. Buyers should focus on the nutritional content of the offerings and the machine’s maintenance service, ensuring that the machines remain stocked and functional. This is particularly relevant for companies in South America and Africa, where employee wellness is increasingly prioritized.
Healthcare Facilities
Ramen noodle vending machines serve a vital role in healthcare facilities, especially in hospital waiting rooms. They provide visitors and staff with nutritious meal options, addressing the need for quick sustenance in high-stress environments. Buyers must ensure that the machines meet strict hygiene standards and energy efficiency requirements, particularly in regions with varying energy costs. This is essential for maintaining operational costs while ensuring patient and visitor satisfaction.
Transportation Hubs
Airports and train stations can leverage ramen noodle vending machines to cater to travelers seeking quick meal solutions. These machines offer a convenient way for passengers to grab a bite before boarding, thus enhancing their travel experience. Reliability and adaptability to different environments are critical factors for international buyers, particularly in Europe, where high passenger volumes necessitate machines that can withstand heavy use without frequent downtime.
Related Video: Ramen Vending Machine Restaurant
Strategic Material Selection Guide for ramen noodle vending machine
When selecting materials for ramen noodle vending machines, it is essential to consider their properties, advantages, disadvantages, and compliance with international standards. Below is an analysis of four common materials used in the construction of these machines, focusing on their suitability for different applications and environments.
1. Stainless Steel (e.g., 304, 316)
Key Properties:
Stainless steel is known for its excellent corrosion resistance, high strength, and ability to withstand high temperatures. Grades 304 and 316 are particularly popular, with 316 offering superior resistance to chlorides, making it ideal for environments with high humidity or exposure to salty air.
Pros & Cons:
Stainless steel is durable and easy to clean, which is crucial for food safety. However, it can be more expensive than other materials and may require specialized manufacturing techniques to achieve desired shapes and finishes.
Impact on Application:
Stainless steel is compatible with food products and can maintain structural integrity under high-temperature conditions, essential for cooking ramen noodles. Its non-reactive nature ensures that the food’s flavor is not compromised.
Specific Considerations:
International buyers should ensure compliance with food safety standards such as the FDA in the U.S. or EFSA in Europe. Additionally, understanding local regulations regarding stainless steel grades can help avoid issues related to corrosion and hygiene.
2. Carbon Steel
Key Properties:
Carbon steel is valued for its high tensile strength and affordability. However, it is prone to rust and corrosion if not properly coated or treated.
Pros & Cons:
While carbon steel offers a cost-effective solution for structural components, its susceptibility to corrosion limits its use in environments with high moisture or exposure to food products unless adequately protected with coatings.
Impact on Application:
Carbon steel can be used in non-contact areas of the vending machine, such as the frame or support structures. However, its use in direct food contact areas is discouraged due to potential rusting and contamination.
Specific Considerations:
Buyers in humid regions, such as parts of Africa and South America, should consider the necessity of protective coatings or alternative materials to ensure longevity and compliance with health regulations.
3. Aluminum
Key Properties:
Aluminum is lightweight, corrosion-resistant, and has good thermal conductivity. It is often used in components that require frequent handling or movement.
Pros & Cons:
The main advantage of aluminum is its low weight, which can reduce shipping costs and ease installation. However, it is less durable than stainless steel and can be more expensive than carbon steel.
Impact on Application:
Aluminum is suitable for parts of the vending machine that require thermal efficiency, such as heating elements. Its resistance to corrosion makes it a good choice for areas exposed to moisture.
Specific Considerations:
International buyers should verify that the aluminum used meets relevant standards (e.g., ASTM or DIN) for food safety. Additionally, understanding the local market for aluminum grades can help in selecting the right material for specific applications.
4. Polycarbonate
Key Properties:
Polycarbonate is a high-performance plastic known for its impact resistance and clarity. It is often used for transparent components in vending machines.
Pros & Cons:
The primary advantage of polycarbonate is its lightweight and shatter-resistant properties, making it ideal for display panels. However, it may not withstand high temperatures as well as metals and can be prone to scratching.
Impact on Application:
Polycarbonate is suitable for areas where visibility of the product is essential, such as front panels. However, it should not be used in areas exposed to high heat or direct contact with hot food.
Specific Considerations:
Buyers should ensure that the polycarbonate used is BPA-free and complies with food safety regulations. Understanding local recycling regulations for plastics can also influence material selection.
Summary Table
Material | Typical Use Case for ramen noodle vending machine | Key Advantage | Key Disadvantage/Limitation | Relative Cost (Low/Med/High) |
---|---|---|---|---|
Stainless Steel (e.g., 304) | Cooking and food contact areas | Excellent corrosion resistance | Higher cost and complex manufacturing | High |
Carbon Steel | Structural components | Cost-effective and strong | Prone to rust; not suitable for food contact | Low |
Aluminum | Heating elements and external panels | Lightweight and corrosion-resistant | Less durable than stainless steel | Medium |
Polycarbonate | Display panels and non-heat areas | Shatter-resistant and lightweight | Limited heat resistance and prone to scratches | Medium |
This comprehensive analysis provides B2B buyers with the necessary insights to make informed decisions regarding material selection for ramen noodle vending machines, considering both performance and compliance with international standards.
In-depth Look: Manufacturing Processes and Quality Assurance for ramen noodle vending machine
Manufacturing Processes for Ramen Noodle Vending Machines
The manufacturing process of ramen noodle vending machines involves several critical stages, each contributing to the overall quality and functionality of the final product. Understanding these stages is essential for B2B buyers to ensure they select suppliers that maintain high standards.
1. Material Preparation
The first stage in the manufacturing process is material preparation. This involves sourcing high-quality materials that meet international standards. Common materials used include stainless steel for the machine casing, high-grade plastic for components, and electronic parts such as circuit boards.
Key Techniques:
– Supplier Evaluation: Ensure suppliers are vetted for quality and reliability.
– Material Testing: Conduct tests to verify that materials are free from defects and meet specifications.
2. Forming
In the forming stage, materials are shaped into the necessary components of the vending machine. This often involves processes like stamping, bending, and machining.
Key Techniques:
– CNC Machining: Computer Numerical Control (CNC) machining ensures precision in creating parts such as the machine’s frame and internal mechanisms.
– Injection Molding: Used for creating plastic components, ensuring consistency and reducing waste.
3. Assembly
Once individual components are formed, the next stage is assembly. This involves putting together various parts to create the complete vending machine.
Key Techniques:
– Automated Assembly Lines: These enhance efficiency and reduce human error during the assembly process.
– Manual Assembly Checks: Skilled technicians perform checks to ensure that parts are assembled correctly and function as intended.
4. Finishing
The finishing stage includes painting, coating, and installing electronic components. This not only improves the aesthetic appeal but also protects the machine from wear and corrosion.
Key Techniques:
– Powder Coating: Provides a durable finish that is resistant to scratches and chemicals.
– Quality Control Inspections: Each machine undergoes a thorough inspection before it leaves the factory.
Quality Assurance Protocols
Quality assurance is paramount in the manufacturing of ramen noodle vending machines. International standards and industry-specific regulations guide the QC process, ensuring that machines are safe, reliable, and effective.
Relevant International Standards
- ISO 9001: This standard outlines criteria for a quality management system, focusing on consistent quality in products and services.
- CE Marking: This indicates compliance with health, safety, and environmental protection standards for products sold within the European Economic Area.
- API Standards: Applicable for machines using certain technologies or materials, ensuring safety and performance.
Quality Control Checkpoints
To maintain high-quality standards, manufacturers implement several checkpoints throughout the production process:
-
Incoming Quality Control (IQC):
– Focuses on the inspection of raw materials and components upon arrival at the factory.
– Ensures that only materials meeting specifications are used. -
In-Process Quality Control (IPQC):
– Conducted at various stages of the manufacturing process.
– Involves ongoing inspections and testing to detect defects early. -
Final Quality Control (FQC):
– The last stage where the finished product is thoroughly tested.
– Involves functionality tests and safety checks to ensure the vending machine operates correctly.
Common Testing Methods
- Functional Testing: Verifies that all machine components work as intended.
- Durability Testing: Assesses the machine’s performance under various conditions to ensure longevity.
- Electrical Safety Testing: Ensures that all electrical components comply with safety standards.
Verifying Supplier Quality Control
B2B buyers must take proactive steps to verify the quality assurance processes of potential suppliers. Here are key strategies:
- Supplier Audits: Conduct on-site audits to review manufacturing processes and quality control measures.
- Request Quality Reports: Ask for detailed reports that outline the QC procedures and results from previous production batches.
- Third-Party Inspections: Engage third-party inspection services to assess the quality of products before shipment. This adds an additional layer of assurance.
Navigating QC and Certification Nuances for International Buyers
When sourcing ramen noodle vending machines, international buyers should be aware of the nuances in quality control and certification that may vary by region:
- Regional Standards: Familiarize yourself with specific regulations and quality standards in your region (e.g., regulations in Africa, South America, the Middle East, and Europe).
- Documentation Requirements: Ensure that suppliers provide all necessary certification documents, including ISO certifications and CE markings, to facilitate smoother customs clearance and compliance with local laws.
- Cultural Considerations: Understand the business practices in your supplier’s region, as these can influence quality assurance methods and communication.
Conclusion
By understanding the manufacturing processes and quality assurance protocols involved in the production of ramen noodle vending machines, B2B buyers can make informed decisions. Ensuring that suppliers adhere to international standards and robust QC measures is vital for acquiring reliable and efficient vending solutions. This approach not only enhances the buyer’s reputation but also contributes to customer satisfaction and business success.
Related Video: How to Make a Cup Noodle Vending Machine from Cardboard
Comprehensive Cost and Pricing Analysis for ramen noodle vending machine Sourcing
The cost structure for sourcing ramen noodle vending machines comprises several critical components that directly influence pricing and overall value. Understanding these elements can empower international B2B buyers, particularly from diverse regions such as Africa, South America, the Middle East, and Europe, to make informed purchasing decisions.
Cost Components
-
Materials: The primary materials include stainless steel for the machine body, electronic components, and the vending mechanism. High-quality materials not only enhance durability but also affect the initial cost.
-
Labor: Labor costs vary significantly based on geographical location. In regions with lower labor costs, such as parts of Asia, the overall production cost can be reduced, but this may impact quality.
-
Manufacturing Overhead: This encompasses utilities, facility costs, and administrative expenses associated with production. Buyers should inquire about the manufacturing environment to ensure compliance with international standards.
-
Tooling: Tooling costs are essential for custom designs. If modifications are required to accommodate specific features or branding, these costs will be added to the overall price.
-
Quality Control (QC): Investing in robust QC processes ensures that machines meet safety and operational standards. Buyers should assess how much of the budget is allocated to QC, as this can significantly impact the longevity and reliability of the vending machines.
-
Logistics: Shipping costs can fluctuate based on the distance from the supplier, shipping method, and current freight rates. Additionally, understanding tariffs and import duties is vital for accurate cost estimation.
-
Margin: Suppliers typically add a profit margin to their total costs. This margin can vary based on competition, demand, and the uniqueness of the vending machine features.
Price Influencers
Several factors can influence the pricing of ramen noodle vending machines:
-
Volume/MOQ: Larger orders often lead to better pricing. Establishing a minimum order quantity (MOQ) can help buyers negotiate lower unit costs.
-
Specifications/Customization: Customized machines will typically incur higher costs due to additional design and manufacturing requirements. Buyers should clearly define their needs upfront to avoid unexpected expenses.
-
Materials: The choice between standard and premium materials can greatly affect pricing. Premium materials may offer better performance and longevity, justifying a higher upfront cost.
-
Quality/Certifications: Machines that meet international certifications (e.g., CE, ISO) may carry a premium price but provide assurance of quality and safety, which is particularly important in regulated markets.
-
Supplier Factors: The reputation, reliability, and location of the supplier can also impact pricing. Buyers should consider suppliers with proven track records to mitigate risks.
-
Incoterms: The agreed-upon Incoterms (e.g., FOB, CIF) affect logistics and insurance costs, which should be factored into the total cost analysis.
Buyer Tips
-
Negotiation: Engage suppliers in discussions about pricing, especially regarding bulk orders. Leverage competitive quotes to negotiate better terms.
-
Cost-Efficiency: Look beyond the initial purchase price. Consider operational costs, maintenance, and potential downtime to evaluate the Total Cost of Ownership (TCO).
-
Pricing Nuances for International Buyers: Be aware of currency fluctuations, payment terms, and international shipping complexities. Establish clear communication regarding these factors to avoid misunderstandings.
-
Local Regulations: Ensure that the vending machines comply with local health and safety regulations in your target market. This may affect both initial costs and long-term operational expenses.
In conclusion, while sourcing ramen noodle vending machines involves various cost components and pricing influencers, understanding these elements can lead to better decision-making for international B2B buyers. Always approach suppliers with a clear strategy and knowledge of the market dynamics to secure the best possible deal.
Spotlight on Potential ramen noodle vending machine Manufacturers and Suppliers
This section offers a look at a few manufacturers active in the ‘ramen noodle vending machine’ market. This is a representative sample for illustrative purposes; B2B buyers must conduct their own extensive due diligence before any engagement. Information is synthesized from public sources and general industry knowledge.
Essential Technical Properties and Trade Terminology for ramen noodle vending machine
Key Technical Properties for Ramen Noodle Vending Machines
When considering the procurement of ramen noodle vending machines, understanding critical technical properties is essential. Here are some key specifications that international B2B buyers should focus on:
-
Material Grade
The material used in the construction of vending machines, typically stainless steel or high-grade plastic, affects durability and hygiene. Stainless steel is preferred for its resistance to corrosion and ease of cleaning, which is crucial in food service environments. Selecting the right material ensures longevity and compliance with health regulations. -
Power Consumption
The energy efficiency of the vending machine is vital for operational costs. Machines should have specifications indicating their power requirements (typically measured in watts). Lower power consumption translates to reduced electricity bills, making it a significant factor for businesses operating in regions with high energy costs. -
Temperature Control Range
The ability to maintain a specific temperature range is critical for preserving the quality of ramen noodles. Machines should specify their temperature control capabilities, ensuring that noodles are kept at the optimal serving temperature without compromising safety or taste. -
Capacity
Capacity refers to the number of servings the machine can hold and dispense at one time. This is typically measured in liters or the number of trays available for product storage. Understanding capacity helps buyers assess whether the machine meets their expected demand, particularly in high-traffic areas. -
User Interface Technology
The user interface can significantly influence customer experience. Modern vending machines may feature touch screens, QR code scanning, or mobile payment options. A user-friendly interface encourages higher usage rates, making it an important consideration for attracting customers. -
Safety Standards Compliance
Compliance with local and international safety standards (e.g., CE, UL) is crucial for ensuring the machine operates safely and effectively. Buyers should verify that the machine meets relevant regulatory requirements in their target market, thereby reducing the risk of liability issues.
Common Trade Terminology
Understanding industry terminology can enhance communication and negotiation between suppliers and buyers. Here are some essential terms:
-
OEM (Original Equipment Manufacturer)
This term refers to a company that produces parts and equipment that may be marketed by another manufacturer. For buyers, engaging with OEMs can ensure that they receive high-quality machines tailored to their specifications. -
MOQ (Minimum Order Quantity)
MOQ is the smallest quantity a supplier is willing to sell. Understanding this term helps buyers plan their purchases effectively and avoid overstocking or understocking issues. -
RFQ (Request for Quotation)
An RFQ is a document issued by a buyer to solicit price quotes from suppliers. This process helps buyers compare pricing and terms across different vendors, facilitating informed decision-making. -
Incoterms (International Commercial Terms)
These are a series of predefined commercial terms published by the International Chamber of Commerce (ICC) related to international commercial law. Understanding Incoterms is vital for determining the responsibilities of buyers and sellers regarding shipping, insurance, and tariffs. -
Lead Time
Lead time refers to the time taken from placing an order to receiving it. This is crucial for inventory management and planning, especially for businesses with tight schedules or specific product launches. -
Warranty Period
This term specifies the duration for which the manufacturer guarantees the product against defects. A longer warranty period can be an indicator of product quality and reliability, making it an important factor in the purchasing decision.
By familiarizing themselves with these technical properties and trade terms, international B2B buyers can make more informed decisions when sourcing ramen noodle vending machines, ensuring they choose products that meet their operational needs and market demands.
Navigating Market Dynamics, Sourcing Trends, and Sustainability in the ramen noodle vending machine Sector
Market Overview & Key Trends
The ramen noodle vending machine sector is experiencing transformative growth fueled by several global drivers. Increasing urbanization, particularly in regions like Africa and South America, is driving demand for convenient food solutions. The rise in fast-paced lifestyles has led to a heightened need for quick, accessible meals, making vending machines an attractive option for consumers.
Emerging technologies such as IoT (Internet of Things) are reshaping the vending landscape, enabling machine operators to monitor stock levels in real-time and optimize supply chains. Buyers from Europe, especially Germany, are increasingly investing in advanced vending solutions that offer cashless payment systems and enhanced user interfaces. Moreover, sustainability is becoming a critical factor in purchasing decisions. International B2B buyers are now seeking vendors who can provide eco-friendly machines and sustainable sourcing practices, which are vital for compliance with evolving regulations in various regions.
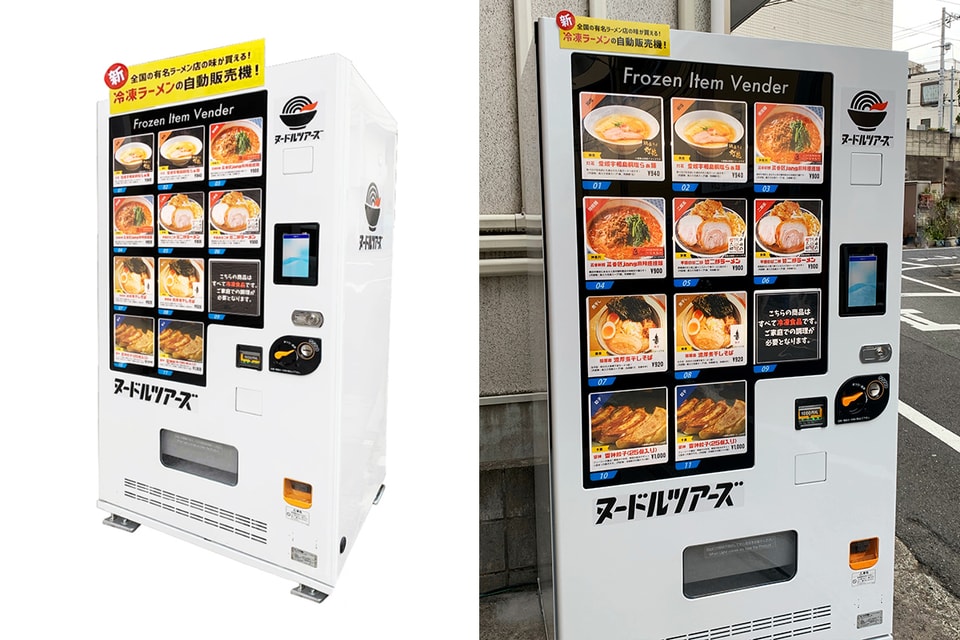
Illustrative Image (Source: Google Search)
Additionally, the market is witnessing a trend toward customization. Vendors are offering machines that can cater to local tastes, such as incorporating regional flavors into their ramen offerings. This localization strategy helps businesses tap into diverse consumer preferences across different markets, particularly in multicultural regions.
Sustainability & Ethical Sourcing in B2B
Sustainability is not just a trend; it is becoming a necessity in the ramen noodle vending machine sector. The environmental impact of single-use plastics and packaging waste has prompted buyers to seek out solutions that minimize ecological footprints. Many manufacturers are responding by utilizing biodegradable materials and recyclable packaging for their products.
Ethical sourcing is increasingly crucial as buyers prioritize transparency in their supply chains. This includes ensuring that ingredients used in ramen production are sourced from suppliers who adhere to fair labor practices and sustainable agricultural methods. As a result, certifications such as Fair Trade and Rainforest Alliance are becoming significant indicators of ethical sourcing for B2B buyers.
Moreover, the adoption of energy-efficient vending machines can significantly reduce operational costs and carbon footprints. Buyers should look for machines equipped with features like LED lighting, energy-saving modes, and materials that contribute to a lower environmental impact. Investing in these sustainable solutions not only aligns with corporate social responsibility goals but also resonates with a growing consumer base that values environmental stewardship.
Brief Evolution/History
The evolution of ramen noodle vending machines can be traced back to Japan in the 1970s, where the concept of automated food dispensing began to gain traction. Initially, these machines offered simple, pre-packaged ramen cups. Over the decades, advancements in technology and changes in consumer preferences have led to more sophisticated machines capable of preparing fresh ramen on-site.
The globalization of food culture has further propelled the popularity of ramen vending machines beyond Japan, especially in urban centers across Europe, South America, and Africa. Today, these machines not only serve traditional ramen but also cater to diverse dietary needs, including vegetarian and gluten-free options. This evolution underscores the importance of adaptability in the vending machine sector, as businesses strive to meet the demands of an increasingly diverse customer base.
By understanding these dynamics, international B2B buyers can make informed decisions that align with market trends and consumer expectations.
Related Video: The Most Famous Ramen Vending Machine Restaurant
Frequently Asked Questions (FAQs) for B2B Buyers of ramen noodle vending machine
-
What should I consider when vetting suppliers for ramen noodle vending machines?
When vetting suppliers, prioritize their experience in manufacturing vending machines, specifically for ramen. Check for certifications such as ISO 9001, which indicates quality management standards. Request references or case studies from other international clients. Additionally, assess their production capacity and lead times to ensure they can meet your demand. A reliable supplier should also offer transparent communication regarding pricing, customization options, and after-sales support. -
Can I customize the vending machines to fit my market needs?
Yes, many suppliers offer customization options for their vending machines. This can include alterations in design, size, and features tailored to your local market preferences, such as multilingual interfaces or payment systems that cater to your region. Discuss your specific requirements with potential suppliers early in the negotiation process to ensure they can accommodate your needs without significantly impacting lead times or costs. -
What are the typical minimum order quantities (MOQ) and lead times for these machines?
Minimum order quantities for ramen noodle vending machines vary by supplier but typically range from 5 to 20 units for customized orders. Standard models may have lower MOQs. Lead times can vary widely depending on customization and supplier location, often ranging from 6 to 12 weeks. It’s crucial to clarify these details upfront to align your inventory needs with the supplier’s production schedule, especially if you’re entering a new market. -
What payment terms should I expect when purchasing vending machines internationally?
Payment terms can differ significantly among suppliers. Common practices include a deposit (usually 30-50%) upfront, with the balance due upon completion or delivery of the machines. For international transactions, consider using secure payment methods like letters of credit or escrow services to protect your investment. Discuss potential financing options, especially if ordering a large quantity, as some suppliers may offer installment plans or trade financing. -
What quality assurance measures should I look for?
Ensure your supplier has robust quality assurance processes in place. This includes regular inspections during production and adherence to international safety standards. Request documentation of their QA practices, such as testing reports and compliance certifications. It’s also beneficial to negotiate for pre-shipment inspections or trials, allowing you to verify the machines meet your specifications before they are shipped. -
How do logistics and shipping work for vending machines?
Logistics for vending machines can be complex due to their size and weight. Discuss with your supplier about their logistics capabilities, including shipping methods, costs, and estimated delivery times. Understand the import regulations in your country, as customs clearance can cause delays. Consider partnering with a freight forwarder who specializes in heavy machinery to facilitate smoother logistics and ensure compliance with local laws. -
What should I do if there’s a dispute with my supplier?
In case of a dispute, first attempt to resolve the issue directly with the supplier through open communication. If that fails, refer to the terms outlined in your contract, particularly regarding dispute resolution mechanisms. Many suppliers may agree to mediation or arbitration as a first step. It’s advisable to have a legal expert familiar with international trade laws to guide you through the process and protect your interests. -
Are there any certifications that the vending machines should have?
Yes, certifications can greatly influence your purchasing decision. Look for compliance with international safety standards such as CE for Europe or UL for North America. These certifications ensure that the vending machines are safe for consumer use. Additionally, certifications related to energy efficiency can enhance your machine’s appeal, particularly in markets where sustainability is prioritized. Always request documentation of these certifications from the supplier.
Strategic Sourcing Conclusion and Outlook for ramen noodle vending machine
In conclusion, the strategic sourcing of ramen noodle vending machines presents a compelling opportunity for international B2B buyers, especially those operating in regions such as Africa, South America, the Middle East, and Europe. Key takeaways include the importance of understanding local consumer preferences, the necessity of evaluating supplier reliability, and the advantages of integrating technology for enhanced user experience.
Investing in high-quality vending machines can significantly elevate brand visibility and customer engagement, making them a valuable addition to any business model. As the demand for convenient food options continues to rise globally, aligning sourcing strategies with market trends will be crucial.
Looking ahead, businesses should actively seek partnerships with innovative suppliers who can offer flexibility and adaptability to meet evolving consumer demands. This proactive approach not only ensures competitive pricing but also fosters long-term growth. International buyers are encouraged to explore these opportunities and leverage strategic sourcing to enhance their market presence. Embrace the future of automated food retailing and secure a position at the forefront of this expanding industry.