Your Ultimate Guide to Sourcing Ppe Vending Machines
Guide to Ppe Vending Machines
- Introduction: Navigating the Global Market for ppe vending machines
- Understanding ppe vending machines Types and Variations
- Key Industrial Applications of ppe vending machines
- Strategic Material Selection Guide for ppe vending machines
- In-depth Look: Manufacturing Processes and Quality Assurance for ppe vending machines
- Comprehensive Cost and Pricing Analysis for ppe vending machines Sourcing
- Spotlight on Potential ppe vending machines Manufacturers and Suppliers
- Essential Technical Properties and Trade Terminology for ppe vending machines
- Navigating Market Dynamics, Sourcing Trends, and Sustainability in the ppe vending machines Sector
- Frequently Asked Questions (FAQs) for B2B Buyers of ppe vending machines
- Strategic Sourcing Conclusion and Outlook for ppe vending machines
Introduction: Navigating the Global Market for ppe vending machines
In today’s rapidly evolving global marketplace, PPE vending machines have emerged as a vital solution for businesses seeking to enhance workplace safety and efficiency. These automated systems provide easy access to personal protective equipment (PPE), ensuring that employees can swiftly obtain the necessary gear to maintain compliance with health and safety regulations. This is particularly important in regions where the demand for PPE is surging due to heightened awareness of workplace safety, especially in sectors such as construction, manufacturing, and healthcare.
This comprehensive guide will explore the multifaceted landscape of PPE vending machines, covering key aspects such as the various types of machines available, the materials used in PPE production, and insights into manufacturing and quality control standards. Additionally, we will provide an overview of reputable suppliers, a breakdown of cost considerations, and an analysis of current market trends. Frequently asked questions will also be addressed to clarify common concerns faced by B2B buyers.
By navigating this guide, international buyers from Africa, South America, the Middle East, and Europe—including key markets like Italy and Brazil—will be empowered to make informed sourcing decisions. Understanding the nuances of PPE vending machines not only enhances procurement strategies but also contributes to safer work environments, ultimately driving business success in a competitive landscape.
Understanding ppe vending machines Types and Variations
Type Name | Key Distinguishing Features | Primary B2B Applications | Brief Pros & Cons for Buyers |
---|---|---|---|
Standard PPE Vending Machine | Offers a range of PPE items like gloves, masks, and goggles. | Manufacturing, construction, healthcare | Pros: Versatile, easy to use. Cons: Limited customization options. |
Mobile PPE Vending Machine | Compact design for portability, often battery-operated. | Outdoor sites, remote locations | Pros: Flexible deployment, ideal for temporary sites. Cons: Smaller inventory capacity. |
Smart PPE Vending Machine | Equipped with IoT capabilities for inventory management and monitoring. | Large enterprises, industrial sectors | Pros: Real-time data tracking, reduces waste. Cons: Higher initial investment. |
Customized PPE Vending Machine | Tailored to specific industry needs, with unique configurations. | Specialized industries, niche markets | Pros: Meets specific demands, enhances efficiency. Cons: Longer lead time for delivery. |
Automated PPE Dispensing Station | Uses sensors and touchless technology for hygienic dispensing. | Laboratories, healthcare facilities | Pros: Enhances safety and hygiene. Cons: Higher maintenance requirements. |
Standard PPE Vending Machine
Standard PPE vending machines are designed to dispense a variety of personal protective equipment, including gloves, masks, and goggles. They are widely used in industries such as manufacturing and construction, where workers need easy access to safety gear. When purchasing, buyers should consider the machine’s capacity, ease of use, and the range of PPE items it offers. While they provide versatility, the downside is that they may lack customization options for specific industry needs.
Mobile PPE Vending Machine
Mobile PPE vending machines are compact and often battery-operated, making them ideal for deployment at outdoor sites or remote locations. These machines allow for quick access to PPE when and where it is needed, which is especially valuable in construction or field operations. Buyers should evaluate the machine’s portability and battery life as key purchasing factors. However, these machines typically have a smaller inventory capacity, which could limit the range of PPE available at any given time.
Smart PPE Vending Machine
Smart PPE vending machines integrate IoT technology, enabling real-time inventory management and monitoring. They are particularly beneficial for large enterprises and industrial sectors, where tracking usage and managing stock levels is crucial. When considering these machines, buyers should assess the software capabilities and data analytics features. While they offer significant advantages in reducing waste and optimizing inventory, they generally come with a higher initial investment.
Customized PPE Vending Machine
Customized PPE vending machines are specifically tailored to meet the unique needs of particular industries or applications. These machines can be configured to dispense specialized PPE, making them ideal for niche markets such as oil and gas or pharmaceuticals. Buyers should focus on the customization options available and the lead time for delivery, as these machines may take longer to produce. The main benefit is that they address specific demands, although this can also lead to increased costs.
Automated PPE Dispensing Station
Automated PPE dispensing stations utilize sensors and touchless technology to provide hygienic dispensing of equipment. They are especially relevant in environments like laboratories and healthcare facilities, where safety and hygiene are paramount. Key considerations for buyers include the station’s maintenance requirements and the technology used. Although they enhance safety and reduce the risk of contamination, they may require more frequent maintenance compared to traditional vending machines.
Related Video: Select PPE Vending Machine Solution
Key Industrial Applications of ppe vending machines
Industry/Sector | Specific Application of PPE Vending Machines | Value/Benefit for the Business | Key Sourcing Considerations for this Application |
---|---|---|---|
Construction | On-site safety gear distribution | Immediate access to PPE, reducing downtime | Durability, ease of use, and payment options |
Manufacturing | Personal protective equipment for workers | Enhances worker safety, compliance with regulations | Inventory management, replenishment frequency |
Oil & Gas | Emergency PPE for remote locations | Quick response to hazards, ensures regulatory compliance | Weather resistance, ease of transport |
Mining | PPE for underground workers | Protects against dust and falling hazards | Customization for different environments |
Healthcare | Infection control supplies | Ensures staff safety, promotes hygiene standards | Sterilization options, compliance with health standards |
Construction
In the construction industry, PPE vending machines are strategically placed on job sites to provide workers with immediate access to essential safety gear such as helmets, gloves, and eye protection. This reduces downtime caused by workers leaving the site to procure gear, thus enhancing productivity. For international buyers, especially in regions like Africa and South America, machines must be ruggedized to withstand harsh environments and provide diverse payment options to accommodate various worker demographics.
Manufacturing
Manufacturers utilize PPE vending machines to ensure that all employees have easy access to personal protective equipment, such as earplugs, safety goggles, and gloves. This practice not only enhances workplace safety but also ensures compliance with industry regulations. For B2B buyers from Europe and the Middle East, considerations include machine capacity for high-use environments and the ability to monitor inventory levels to prevent stockouts.
Oil & Gas
In the oil and gas sector, PPE vending machines serve as a critical resource in remote locations where immediate access to safety gear is paramount. These machines can dispense specialized equipment like flame-resistant clothing and respirators, ensuring workers are equipped to handle hazardous conditions. Buyers in regions like the Middle East must ensure that the machines are designed for extreme temperatures and can operate in rugged conditions.
Mining
Mining operations benefit significantly from PPE vending machines that provide essential gear for underground workers, including dust masks and protective suits. These machines help mitigate risks associated with dust inhalation and falling objects, thereby enhancing worker safety. Buyers should focus on customization options for specific mining environments and ensure that the machines can withstand the physical demands of such settings, particularly in regions like Africa where mining is prevalent.
Healthcare
In healthcare settings, PPE vending machines are increasingly important for providing staff with infection control supplies such as masks, gloves, and gowns. These machines promote hygiene and ensure that healthcare workers have immediate access to necessary protective equipment, especially during health crises. International buyers need to consider sterilization options for the machines and ensure compliance with local health standards, particularly in Europe where regulations are stringent.
Strategic Material Selection Guide for ppe vending machines
When selecting materials for PPE vending machines, it is essential to consider various factors including durability, cost, and compliance with international standards. Here, we analyze four common materials used in the construction of PPE vending machines, focusing on their properties, advantages, disadvantages, and specific considerations for international B2B buyers.
1. Stainless Steel
Key Properties: Stainless steel is known for its excellent corrosion resistance, high strength, and ability to withstand a wide range of temperatures. It typically has a temperature rating of up to 800°C and good mechanical properties under pressure.
Pros & Cons: The primary advantage of stainless steel is its durability and longevity, making it ideal for outdoor or harsh environments. However, it can be relatively expensive compared to other materials and may require complex manufacturing processes, which can increase costs.
Impact on Application: Stainless steel is compatible with various media, including corrosive substances, making it suitable for vending machines that dispense chemical PPE.
Considerations for International Buyers: Buyers should ensure compliance with standards such as ASTM A240 for stainless steel. In regions like Europe, adherence to EN standards is crucial, while in Africa and South America, local regulations may vary.
2. Polycarbonate
Key Properties: Polycarbonate is a lightweight thermoplastic with high impact resistance and a temperature tolerance ranging from -40°C to 120°C. It offers good clarity and UV resistance.
Pros & Cons: The key advantage of polycarbonate is its lightweight nature, which reduces shipping and handling costs. However, it is less resistant to scratches compared to glass or metal, which may affect its longevity in high-traffic areas.
Impact on Application: Polycarbonate is often used for transparent panels in vending machines, allowing visibility of the PPE inside. Its chemical resistance makes it suitable for various environments.
Considerations for International Buyers: Buyers should verify compliance with safety standards such as ISO 7396 for medical devices. In Europe, REACH regulations may apply, necessitating careful selection of grades.
3. Mild Steel
Key Properties: Mild steel is characterized by its good weldability and machinability, with a typical yield strength of around 250 MPa. It has a temperature rating of up to 300°C but is prone to corrosion.
Pros & Cons: Mild steel is cost-effective and widely available, making it an attractive option for budget-conscious buyers. However, it requires protective coatings to prevent rust, which can add to maintenance costs.
Impact on Application: Suitable for internal structures of vending machines, mild steel is often used in applications where exposure to harsh environments is minimal.
Considerations for International Buyers: Compliance with standards such as ASTM A36 is essential. Buyers in the Middle East and Africa should consider the local climate and potential corrosion issues when selecting mild steel.
4. Aluminum
Key Properties: Aluminum is lightweight, corrosion-resistant, and has a temperature rating of around -200°C to 600°C. It offers good strength-to-weight ratio and is easily recyclable.
Pros & Cons: The primary advantage of aluminum is its lightweight nature, which facilitates easy installation and transportation. However, it can be more expensive than mild steel and may require additional treatments for enhanced corrosion resistance.
Impact on Application: Aluminum is often used in the framework of vending machines, especially in environments where weight is a concern.
Considerations for International Buyers: Buyers should ensure compliance with standards such as ASTM B221 for aluminum extrusions. In Europe, EN 573 standards are relevant, while buyers in South America should consider local regulations regarding aluminum use.
Summary Table
Material | Typical Use Case for PPE Vending Machines | Key Advantage | Key Disadvantage/Limitation | Relative Cost (Low/Med/High) |
---|---|---|---|---|
Stainless Steel | Outdoor vending machines, chemical PPE | Excellent durability and corrosion resistance | High cost, complex manufacturing | High |
Polycarbonate | Transparent panels for visibility in vending machines | Lightweight, good impact resistance | Scratches easily, less durable than glass | Medium |
Mild Steel | Internal structures of vending machines | Cost-effective, widely available | Prone to corrosion, requires protective coating | Low |
Aluminum | Framework for lightweight vending machines | Lightweight, recyclable | Higher cost, may require corrosion treatment | Medium |
This strategic material selection guide provides international B2B buyers with critical insights into the materials used in PPE vending machines, enabling informed decision-making that aligns with their operational needs and regulatory compliance.
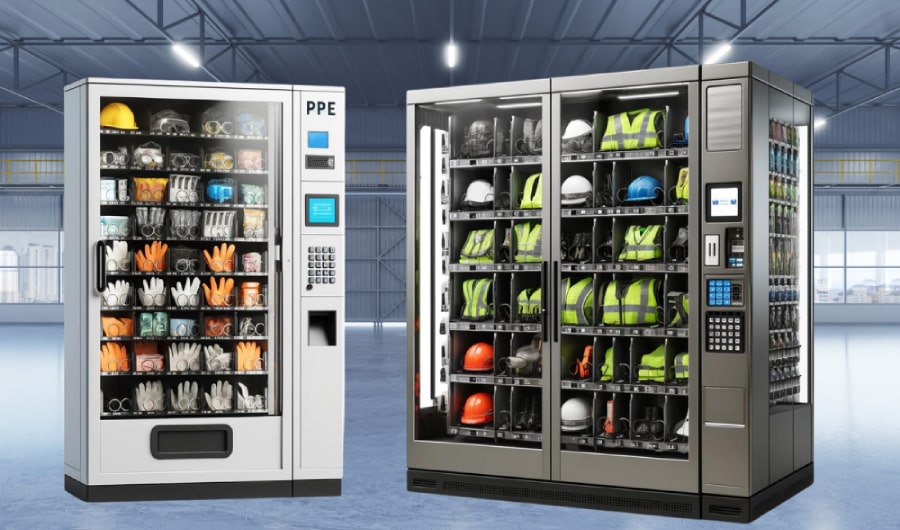
Illustrative Image (Source: Google Search)
In-depth Look: Manufacturing Processes and Quality Assurance for ppe vending machines
The manufacturing process of PPE vending machines is a critical factor for international B2B buyers, especially those in regions such as Africa, South America, the Middle East, and Europe. Understanding these processes and the associated quality assurance measures can help buyers make informed decisions when selecting suppliers. Below is a detailed overview of the key stages in manufacturing and the quality control practices that ensure the machines meet international standards.
Manufacturing Processes
1. Material Preparation
The first stage in the manufacturing of PPE vending machines involves the careful selection and preparation of materials. Common materials include:
- Steel or Aluminum: Used for the machine’s frame and casing due to their strength and durability.
- Plastic Components: Often used for internal mechanisms and user interfaces.
- Electronic Components: Sensors, displays, and payment systems that require high-quality electronic parts.
Materials are typically sourced from certified suppliers to ensure compliance with international standards. It is essential for buyers to verify the material specifications and certifications, as these can impact the machine’s durability and functionality.
2. Forming
Once materials are prepared, the forming stage takes place. This involves various techniques such as:
- CNC Machining: Used to create precise components from metal sheets.
- Injection Molding: Commonly used for producing plastic parts, ensuring uniformity and accuracy.
- Bending and Stamping: These methods shape metal parts into required forms for the machine structure.
Advanced forming techniques are crucial for achieving the machine’s design specifications and operational efficiency.
3. Assembly
The assembly stage integrates all components into a cohesive unit. This process typically includes:
- Sub-assembly: Individual parts, such as the vending mechanism and electronic systems, are assembled separately before being integrated into the main unit.
- Final Assembly: All sub-assemblies are combined, wiring is connected, and the machine is prepared for testing.
During assembly, attention to detail is vital to ensure that all components work harmoniously. Buyers should inquire about the assembly techniques used and the qualifications of assembly personnel.
4. Finishing
The finishing stage enhances the machine’s aesthetics and protects it from environmental factors. Key activities include:
- Painting or Powder Coating: Provides a durable finish that resists wear and corrosion.
- Quality Inspections: Visual and functional checks ensure that the machine meets design specifications.
Finishing processes are also important for branding, as machines can be customized with logos and colors.
Quality Assurance
Quality assurance is a cornerstone of the manufacturing process for PPE vending machines. Compliance with international standards not only ensures product reliability but also builds trust with buyers.
International Standards
B2B buyers should be familiar with the following standards relevant to PPE vending machines:
- ISO 9001: This standard focuses on quality management systems and ensures that manufacturers consistently meet customer and regulatory requirements.
- CE Marking: Required for products sold in the European Economic Area, indicating conformity with health, safety, and environmental protection standards.
- API Standards: For machines that may interface with specific industrial applications, ensuring compatibility and safety.
Quality Control Checkpoints
Quality control checkpoints during the manufacturing process are critical for maintaining high standards:
- Incoming Quality Control (IQC): Inspection of raw materials and components upon arrival to ensure they meet specifications.
- In-Process Quality Control (IPQC): Ongoing inspections during the manufacturing process to catch defects early.
- Final Quality Control (FQC): Comprehensive testing of the finished machine before it leaves the factory, including functionality tests and safety checks.
Common Testing Methods
Testing methods used to validate the quality of PPE vending machines include:
- Functional Testing: Ensures that all machine features operate as intended.
- Durability Testing: Simulates long-term use to assess the machine’s lifespan.
- Safety Testing: Checks for electrical safety, mechanical integrity, and compliance with relevant standards.
Verifying Supplier Quality Control
International buyers must have strategies in place to verify the quality control processes of potential suppliers:
- Audits: Conducting regular audits of suppliers’ facilities can provide insights into their manufacturing and quality assurance processes.
- Quality Reports: Requesting documentation that outlines quality control measures, testing results, and compliance with standards can offer transparency.
- Third-Party Inspections: Engaging third-party organizations to perform independent inspections can validate a supplier’s claims regarding quality.
Quality Control Nuances for International Buyers
For international B2B buyers, particularly those from diverse regions like Africa, South America, the Middle East, and Europe, understanding regional compliance and quality nuances is crucial. Factors to consider include:
- Local Regulations: Familiarize yourself with local regulations regarding PPE vending machines, as these may vary significantly.
- Cultural Expectations: Different regions may have varying expectations regarding product quality, support, and warranty terms.
- Supply Chain Logistics: Assess the supplier’s ability to meet delivery timelines and manage logistics, particularly for international shipments.
By understanding the manufacturing processes and quality assurance measures associated with PPE vending machines, international B2B buyers can make more informed decisions, ensuring they select reliable suppliers that meet their operational needs and compliance requirements.
Related Video: SMART Quality Control for Manufacturing
Comprehensive Cost and Pricing Analysis for ppe vending machines Sourcing
Cost Structure of PPE Vending Machines
Understanding the cost structure of PPE vending machines is crucial for international B2B buyers aiming to optimize their sourcing strategy. The primary cost components include:
-
Materials: The cost of high-quality materials, such as steel for the machine body and components for the vending mechanism, significantly impacts the overall price. Opting for durable and rust-resistant materials can increase initial costs but enhance longevity and reduce maintenance expenses.
-
Labor: Labor costs vary significantly depending on the region. For instance, manufacturing in countries with higher wage standards (like parts of Europe) will generally result in higher prices compared to regions with lower labor costs (such as parts of Africa and South America).
-
Manufacturing Overhead: This includes utilities, facility costs, and indirect labor. Efficient factories often pass on savings to buyers, making it essential to evaluate the operational efficiency of potential suppliers.
-
Tooling: Custom tooling for specialized machines can be a substantial upfront cost. Buyers should assess whether the tooling cost is amortized over a larger order volume to achieve better pricing.
-
Quality Control (QC): Implementing rigorous QC processes adds to manufacturing costs but ensures that the machines meet safety and functionality standards. Investing in quality can prevent costly recalls or repairs down the line.
-
Logistics: Shipping costs can fluctuate based on distance, mode of transport, and current freight rates. Understanding the logistics involved, including customs duties and taxes, is vital for accurate total cost calculations.
-
Margin: Suppliers will typically include a margin that reflects their operational costs and profit goals. This margin can vary based on market conditions and supplier negotiation.
Price Influencers
Several factors influence the pricing of PPE vending machines:
-
Volume/MOQ (Minimum Order Quantity): Higher order volumes generally lead to better pricing due to economies of scale. Buyers should negotiate MOQs that align with their needs without overcommitting.
-
Specifications/Customization: Custom features or specifications can significantly increase costs. Buyers should clearly define their requirements to avoid unexpected charges during the production process.
-
Materials: The choice of materials impacts both price and durability. High-quality, certified materials may cost more but offer better protection and longevity, which can lead to lower total cost of ownership.
-
Quality/Certifications: Machines that meet international safety and quality certifications may carry a premium price. However, these certifications can enhance marketability and consumer trust.
-
Supplier Factors: Supplier reliability, reputation, and geographic location can influence pricing. Engaging with suppliers who have a proven track record can lead to more favorable pricing and terms.
-
Incoterms: Understanding Incoterms is essential for managing shipping costs and responsibilities. Terms like FOB (Free on Board) and CIF (Cost, Insurance, and Freight) can significantly affect the total landed cost.
Buyer Tips
For international B2B buyers, particularly from Africa, South America, the Middle East, and Europe, consider the following tips:
-
Negotiate Effectively: Engage suppliers in discussions about pricing, especially when placing large orders. Leveraging volume can often yield discounts.
-
Focus on Cost-Efficiency: Analyze not just the purchase price but the total cost of ownership, including maintenance, operation, and potential resale value.
-
Understand Pricing Nuances: Be aware that pricing can vary significantly by region due to local economic conditions, currency fluctuations, and import tariffs.
-
Build Relationships: Cultivating strong relationships with suppliers can lead to better terms and pricing flexibility over time.
-
Stay Informed: Regularly review market trends and material costs to make timely sourcing decisions. Being proactive can help secure favorable pricing before potential increases.
Disclaimer
Prices mentioned in this analysis are indicative and can vary based on current market conditions, supplier negotiations, and specific buyer requirements. Always conduct thorough due diligence and request detailed quotes from multiple suppliers to ensure competitive pricing.
Spotlight on Potential ppe vending machines Manufacturers and Suppliers
This section offers a look at a few manufacturers active in the ‘ppe vending machines’ market. This is a representative sample for illustrative purposes; B2B buyers must conduct their own extensive due diligence before any engagement. Information is synthesized from public sources and general industry knowledge.
Essential Technical Properties and Trade Terminology for ppe vending machines
Critical Technical Properties of PPE Vending Machines
When considering the procurement of PPE vending machines, it is crucial to understand their technical specifications. Below are some key properties that international B2B buyers should evaluate:
-
Material Grade: The materials used in the construction of vending machines, such as stainless steel or high-grade plastic, directly affect durability and resistance to environmental factors. High-quality materials reduce maintenance costs and enhance the lifespan of the machines, making them a sound investment for businesses operating in diverse climates, particularly in regions like Africa and South America.
-
Size and Capacity: The dimensions and storage capacity of a PPE vending machine determine its usability in various environments. Machines designed for high-traffic areas should have larger capacities to accommodate frequent use without the need for constant refilling. Buyers should assess their specific needs based on employee numbers and usage patterns.
-
Power Requirements: Understanding the power specifications, including voltage and energy consumption, is vital for operational efficiency. Some machines may require specific voltage levels or energy sources, which can impact installation costs and energy bills. Buyers should consider the infrastructure available in their facilities to ensure compatibility.
-
User Interface: A user-friendly interface is essential for facilitating quick access to PPE. Touchscreen displays, multi-language support, and easy navigation can significantly enhance user experience. Machines with advanced interfaces may also reduce training time and improve overall compliance with safety protocols.
-
Payment Options: Diverse payment methods (e.g., credit/debit cards, mobile payments, cash) enhance the accessibility of PPE vending machines. Understanding the payment landscape in your target market is crucial, especially in regions where digital payment adoption varies.
Common Trade Terminology in PPE Vending Machines
Familiarity with industry jargon is essential for effective communication during procurement. Here are some terms that B2B buyers should know:
-
OEM (Original Equipment Manufacturer): This term refers to companies that produce components or complete products for another brand, which then sells them under its name. Understanding OEM relationships can help buyers assess the quality and reliability of the machines.
-
MOQ (Minimum Order Quantity): This indicates the smallest number of units a supplier is willing to sell. Knowing the MOQ is vital for budgeting and inventory management, especially for businesses in regions with fluctuating demand.
-
RFQ (Request for Quotation): This is a formal process where buyers request pricing information from suppliers. An RFQ can help buyers obtain competitive pricing and terms, ensuring they secure the best deal for their PPE vending machines.
-
Incoterms: These are international commercial terms that define the responsibilities of buyers and sellers in international transactions. Understanding Incoterms is crucial for managing shipping costs, insurance, and risk during transportation, especially for buyers importing machines from manufacturers in other regions.
-
Warranty and Service Agreements: These terms outline the manufacturer’s commitment to repair or replace defective machines and the terms of service maintenance. Understanding warranty options can significantly impact the total cost of ownership and operational uptime.
By grasping these technical properties and trade terms, international B2B buyers can make informed decisions when sourcing PPE vending machines, ensuring they meet their operational needs while optimizing their investment.
Navigating Market Dynamics, Sourcing Trends, and Sustainability in the ppe vending machines Sector
Market Overview & Key Trends
The global market for Personal Protective Equipment (PPE) vending machines is witnessing significant growth, driven by several factors including increasing health awareness, regulatory compliance, and the need for convenient access to safety gear. Particularly in emerging markets across Africa, South America, the Middle East, and Europe, the demand for PPE vending solutions is on the rise. The proliferation of industries such as construction, healthcare, and manufacturing, alongside the impact of the COVID-19 pandemic, has heightened the urgency for accessible PPE.
Current sourcing trends indicate a shift towards digitalization and automation. Companies are increasingly adopting smart vending machines equipped with IoT capabilities that allow for real-time inventory management and data analytics. This trend not only optimizes supply chains but also enhances user experience by providing timely information on product availability. Furthermore, as businesses prioritize workplace safety, there is a growing emphasis on the integration of high-quality PPE products within vending machines, ensuring compliance with international safety standards.
International B2B buyers should also be aware of regional dynamics influencing market entry strategies. For example, in Europe, stringent regulations regarding workplace safety are pushing companies to invest in PPE vending solutions. Conversely, in Africa and South America, the focus may be more on cost-effectiveness and scalability. Understanding these regional nuances is crucial for buyers looking to navigate the evolving landscape of PPE vending machines.
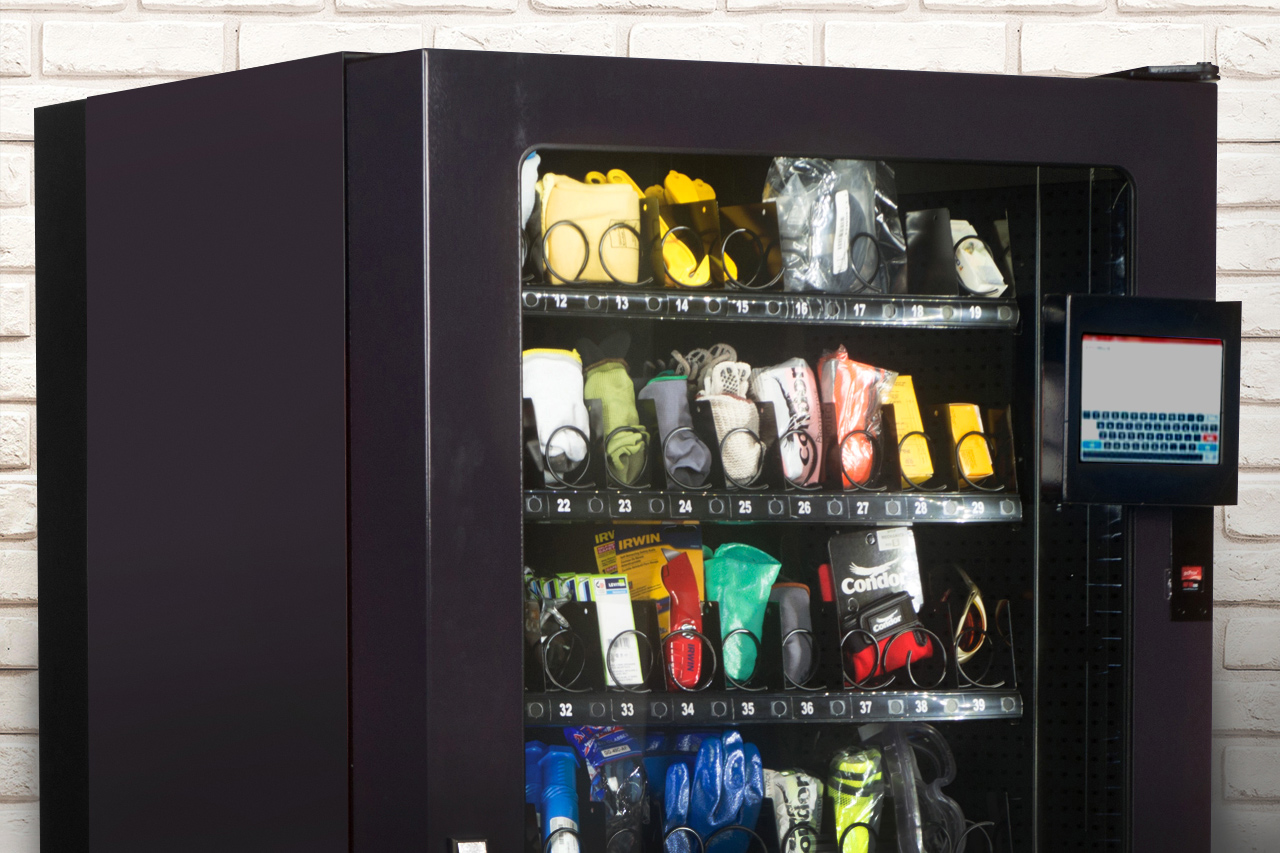
Illustrative Image (Source: Google Search)
Sustainability & Ethical Sourcing in B2B
As sustainability becomes a central theme in global business practices, the PPE vending machine sector is not exempt from this shift. Environmental impacts associated with the production and disposal of PPE are significant, prompting buyers to seek out eco-friendly solutions. For instance, sourcing PPE made from biodegradable or recyclable materials can greatly reduce environmental footprints and align with corporate social responsibility (CSR) objectives.
Moreover, the importance of ethical supply chains cannot be overstated. Buyers must ensure that their suppliers adhere to ethical labor practices and sustainable sourcing methods. Certifications such as ISO 14001 for environmental management and Fair Trade can serve as indicators of a supplier’s commitment to sustainability. By prioritizing suppliers with these credentials, businesses not only enhance their brand reputation but also contribute to a more responsible and transparent supply chain.
Incorporating “green” materials in PPE vending machines, such as using recycled plastics for machine casings or sourcing PPE from manufacturers that utilize renewable energy, can further bolster sustainability efforts. By aligning procurement strategies with sustainable practices, B2B buyers can not only meet regulatory requirements but also cater to a growing consumer demand for environmentally responsible products.
Brief Evolution/History
The concept of vending machines has evolved significantly since their inception in the late 19th century. Initially designed for dispensing snacks and beverages, the application of vending technology has expanded into various sectors, including safety equipment. The introduction of PPE vending machines can be traced back to the early 2000s, driven by the need for accessible safety gear in high-risk workplaces.
Over the past two decades, technological advancements have transformed these machines into smart solutions capable of integrating with inventory management systems and providing data analytics. This evolution reflects the broader trend of digitization in supply chain management, positioning PPE vending machines as a critical component in enhancing workplace safety and compliance. As the market continues to evolve, international B2B buyers must stay informed about technological innovations and emerging trends to capitalize on the opportunities presented by this sector.
Related Video: Global Trade & Logistics – What is Global Trade?
Frequently Asked Questions (FAQs) for B2B Buyers of ppe vending machines
-
What should I consider when vetting suppliers of PPE vending machines?
When vetting suppliers, focus on their experience in the industry, reputation, and compliance with international safety standards. Request references and case studies from previous clients. Verify certifications such as ISO or regional equivalents that demonstrate quality assurance. Additionally, assess their ability to provide after-sales support and maintenance services, which are crucial for the longevity of your investment. -
Can PPE vending machines be customized to fit my specific needs?
Yes, many manufacturers offer customization options for PPE vending machines. You can request specific features such as size, branding, and the types of PPE offered. Discuss your requirements with potential suppliers to ensure they can accommodate your needs. Customization may also include software integration for inventory management or payment systems, which can enhance operational efficiency. -
What are the typical minimum order quantities (MOQ) and lead times for PPE vending machines?
MOQs can vary significantly among suppliers, often ranging from 1 to 10 units for initial orders. Lead times typically range from 4 to 12 weeks, depending on the supplier’s production capacity and your customization requests. Always confirm these details upfront to avoid delays in your procurement process. Building a relationship with your supplier may also lead to more flexible terms in the future. -
What payment options are generally available for international purchases of PPE vending machines?
Payment options vary by supplier but commonly include bank transfers, letters of credit, and online payment platforms. For international transactions, ensure that you understand the currency exchange rates and any additional fees that may apply. It’s advisable to negotiate payment terms upfront, such as deposits and balance payments upon delivery, to protect your investment. -
How can I ensure the quality and safety of the PPE vending machines I purchase?
To ensure quality, request documentation proving that the machines comply with relevant safety standards and regulations, such as CE marking in Europe or ANSI certifications in the U.S. Conduct a factory audit if possible, or ask for third-party inspection reports. Establishing quality benchmarks with your supplier will help maintain standards throughout the production process.
-
What logistics considerations should I keep in mind when importing PPE vending machines?
Logistics are crucial in the procurement process. Ensure that your supplier can handle shipping arrangements, including customs clearance and duties specific to your country. Familiarize yourself with import regulations and tariffs that may affect the overall cost. Working with a logistics partner experienced in international trade can streamline the shipping process and mitigate potential delays. -
What should I do if there is a dispute with my PPE vending machine supplier?
In the event of a dispute, refer to the contract signed with your supplier, which should outline the terms for conflict resolution. Start by communicating directly with the supplier to address the issue. If an agreement cannot be reached, consider mediation or arbitration as outlined in your contract. Having legal counsel familiar with international trade laws can also be beneficial in resolving disputes. -
How can I stay updated on compliance and regulatory changes affecting PPE vending machines?
Stay informed by subscribing to industry newsletters, joining relevant trade associations, and following regulatory bodies in your region. Networking with other businesses in the PPE industry can provide insights into changes in compliance requirements. Additionally, maintain a close relationship with your supplier, as they should also keep you informed about any changes that might affect your operations.
Strategic Sourcing Conclusion and Outlook for ppe vending machines
In conclusion, the strategic sourcing of PPE vending machines presents a unique opportunity for international B2B buyers to enhance workplace safety while optimizing operational efficiency. As companies navigate the complexities of global supply chains, prioritizing reliable suppliers and innovative technologies will be crucial. The integration of PPE vending machines not only provides immediate access to essential safety gear but also streamlines inventory management, reducing waste and improving compliance with safety regulations.
For buyers in Africa, South America, the Middle East, and Europe, understanding local market dynamics and regulatory requirements will be vital in selecting the right vending solutions. Emphasizing long-term partnerships with suppliers who demonstrate adaptability and sustainability can further enhance value and service delivery.
Looking ahead, investing in PPE vending machines will not only be a proactive measure for health and safety but also a strategic move to bolster operational resilience. Engage with suppliers, explore advanced solutions, and take actionable steps today to secure a safer, more efficient future for your workforce.