Your Ultimate Guide to Sourcing Plan B Vending Machine
Guide to Plan B Vending Machine
- Introduction: Navigating the Global Market for plan b vending machine
- Understanding plan b vending machine Types and Variations
- Key Industrial Applications of plan b vending machine
- Strategic Material Selection Guide for plan b vending machine
- In-depth Look: Manufacturing Processes and Quality Assurance for plan b vending machine
- Comprehensive Cost and Pricing Analysis for plan b vending machine Sourcing
- Spotlight on Potential plan b vending machine Manufacturers and Suppliers
- Essential Technical Properties and Trade Terminology for plan b vending machine
- Navigating Market Dynamics, Sourcing Trends, and Sustainability in the plan b vending machine Sector
- Frequently Asked Questions (FAQs) for B2B Buyers of plan b vending machine
- Strategic Sourcing Conclusion and Outlook for plan b vending machine
Introduction: Navigating the Global Market for plan b vending machine
In today’s rapidly evolving global marketplace, the Plan B vending machine stands as a vital solution for businesses aiming to enhance accessibility to emergency contraceptives. As awareness around reproductive health grows, so does the demand for discreet and convenient access to such products, particularly in regions like Africa, South America, the Middle East, and Europe. This guide serves as a comprehensive resource for international B2B buyers, equipping them with critical insights necessary for informed sourcing decisions.
The scope of this guide encompasses various dimensions of the Plan B vending machine market, including types of machines, materials used, manufacturing and quality control processes, and supplier networks. Additionally, it will address cost considerations and provide a detailed analysis of the market landscape, empowering buyers to navigate potential challenges effectively.
By delving into frequently asked questions, this guide aims to demystify the complexities of sourcing Plan B vending machines. It highlights best practices for selecting suppliers who adhere to regulatory standards and quality benchmarks, ensuring that buyers can confidently invest in machines that meet the diverse needs of their target markets.
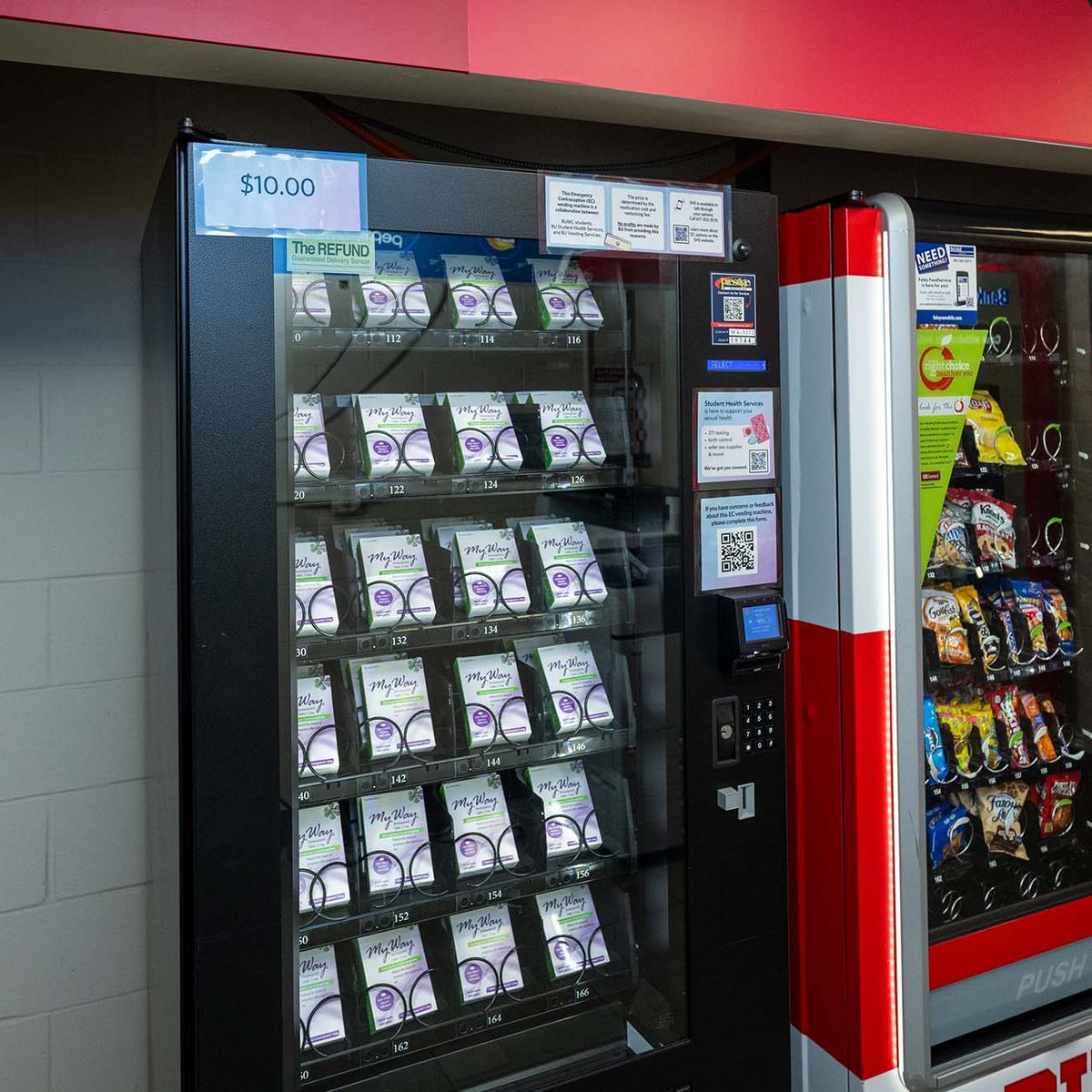
Illustrative Image (Source: Google Search)
Engaging with this guide will enable businesses to make strategic decisions that not only align with their operational goals but also contribute to broader public health initiatives. As the demand for accessible reproductive health solutions continues to rise, investing in Plan B vending machines presents a unique opportunity for growth and impact across multiple regions.
Understanding plan b vending machine Types and Variations
Type Name | Key Distinguishing Features | Primary B2B Applications | Brief Pros & Cons for Buyers |
---|---|---|---|
Traditional Plan B Vending | Standard design, offers basic emergency contraceptives | Pharmacies, universities | Pros: Low cost, easy to operate. Cons: Limited product range. |
Smart Vending Machines | Digital interfaces, inventory tracking, payment options | Corporate offices, events | Pros: Enhanced user experience, data analytics. Cons: Higher initial investment. |
Mobile Plan B Vending Units | Compact, often on wheels for mobility | Festivals, pop-up events | Pros: Flexible placement, caters to transient populations. Cons: May require frequent restocking. |
Automated Health Kiosks | Multi-purpose, includes health information and products | Hospitals, clinics | Pros: Offers additional health services, educational resources. Cons: Complex maintenance. |
Eco-Friendly Vending Machines | Sustainable materials, promotes eco-conscious products | Schools, environmentally-focused businesses | Pros: Appeals to eco-conscious consumers, aligns with CSR initiatives. Cons: Potentially higher costs. |
Traditional Plan B Vending
Traditional Plan B vending machines are the most common type found in pharmacies and educational institutions. They typically offer a limited selection of emergency contraceptives in a straightforward design. For B2B buyers, these machines are cost-effective and easy to manage, making them suitable for locations with high foot traffic. However, their limited product range may not meet all customer needs, which is a consideration for businesses aiming to provide comprehensive reproductive health options.
Smart Vending Machines
Smart vending machines incorporate digital technology, allowing for features such as touch screens, real-time inventory tracking, and various payment options, including mobile payments. These machines are particularly effective in corporate environments and events where user experience is paramount. For B2B buyers, investing in smart vending machines can enhance customer engagement and provide valuable data analytics. However, the initial investment is higher, which may require careful budget planning.
Mobile Plan B Vending Units
Mobile plan B vending units are designed for flexibility and can be relocated easily, making them ideal for festivals and pop-up events. Their compact nature allows businesses to cater to diverse and transient populations effectively. For B2B buyers, these units represent an opportunity to reach customers in non-traditional settings. However, they may require more frequent restocking, which can complicate inventory management.
Automated Health Kiosks
Automated health kiosks serve multiple purposes, offering not only emergency contraceptives but also health information and other related products. They are often placed in hospitals and clinics, providing a valuable service to patients. B2B buyers should consider these kiosks for their ability to deliver additional health resources and education. On the downside, their complexity can lead to higher maintenance costs, which may deter some buyers.
Eco-Friendly Vending Machines
Eco-friendly vending machines are constructed from sustainable materials and focus on promoting environmentally conscious products. They are particularly appealing to schools and businesses with a commitment to corporate social responsibility (CSR). For B2B buyers, these machines can enhance brand image and attract eco-conscious consumers. However, the potential for higher costs may require a thorough cost-benefit analysis before purchase.
Related Video: Machine Learning in 2024 – Beginner’s Course
Key Industrial Applications of plan b vending machine
Industry/Sector | Specific Application of plan b vending machine | Value/Benefit for the Business | Key Sourcing Considerations for this Application |
---|---|---|---|
Healthcare | Emergency contraceptive distribution | Increases accessibility to reproductive health options | Regulatory compliance, temperature control, and security |
Education | Student health and wellness support | Promotes safe and responsible health choices | Payment systems, product range, and maintenance support |
Hospitality | Guest convenience in hotels and resorts | Enhances guest experience and satisfaction | Product variety, branding options, and supply chain logistics |
Retail | 24/7 availability of personal care products | Drives impulse purchases and increases sales volume | Inventory management, product sourcing, and marketing strategies |
Corporate Offices | Employee wellness and health initiatives | Supports workplace health and productivity | Customization options, user-friendly interface, and support services |
Healthcare
In the healthcare sector, plan b vending machines serve a critical role by providing emergency contraceptives directly to consumers. This application addresses the urgent need for accessible reproductive health options, particularly in areas with limited pharmacy hours or in regions where such products may face stigma. International buyers should consider regulatory compliance for medical devices, the need for temperature control to ensure product efficacy, and enhanced security features to prevent theft and misuse.
Education
Schools and universities are increasingly installing plan b vending machines to support student health and wellness initiatives. By providing emergency contraceptives discreetly, educational institutions can promote responsible health choices among students. For international buyers in this sector, it’s essential to focus on the integration of payment systems that cater to the student demographic, as well as a diverse product range that meets varied health needs, along with ongoing maintenance support for machine functionality.
Hospitality
In the hospitality industry, plan b vending machines enhance guest convenience by offering personal care products, including emergency contraceptives. This service not only improves the guest experience but also positions hotels and resorts as responsible and caring establishments. Buyers in this sector should prioritize product variety to cater to diverse clientele, branding options that align with their corporate identity, and efficient supply chain logistics to maintain stock levels and ensure availability.
Retail
Retailers can leverage plan b vending machines to provide 24/7 access to personal care products, capitalizing on impulse purchases. This application is particularly beneficial in high-traffic areas where traditional retail hours may limit sales. B2B buyers in this field should focus on effective inventory management systems to ensure product availability, strategic sourcing of popular items, and innovative marketing strategies to attract customers to the vending machines.
Corporate Offices
Corporate environments can utilize plan b vending machines as part of employee wellness programs, providing easy access to health-related products. This initiative not only supports employee health but also boosts productivity by fostering a supportive workplace culture. International buyers should consider customization options that reflect the company’s values, a user-friendly interface for ease of use, and robust support services to ensure smooth operation and maintenance of the machines.
Related Video: How to Start a Vending Machine Business, Cost, Tips, How Much You Make
Strategic Material Selection Guide for plan b vending machine
When selecting materials for a Plan B vending machine, it is essential to consider various factors that will influence the machine’s performance, durability, and compliance with international standards. Below is an analysis of four common materials used in the construction of vending machines, focusing on their properties, advantages and disadvantages, and specific considerations for international B2B buyers.
Stainless Steel
Key Properties: Stainless steel is known for its excellent corrosion resistance, high strength, and ability to withstand a wide range of temperatures. It typically has a temperature rating of up to 800°F and is resistant to rust and staining.
Pros & Cons: The primary advantage of stainless steel is its durability and longevity, making it suitable for high-traffic environments. However, it is more expensive than other materials and can be challenging to manufacture due to its toughness.
Impact on Application: Stainless steel is highly compatible with various media, including food and beverages, making it ideal for vending machines. Its resistance to corrosion ensures that it maintains hygiene standards.
Considerations for International Buyers: Compliance with international standards such as ASTM A240 for stainless steel is crucial. Buyers from regions like Europe and the Middle East may prefer specific grades, such as 304 or 316, for enhanced corrosion resistance.
Aluminum
Key Properties: Aluminum is lightweight, corrosion-resistant, and has a good strength-to-weight ratio. It can withstand temperatures up to 400°F and is non-magnetic.
Pros & Cons: The lightweight nature of aluminum makes it easy to handle and install, reducing shipping costs. However, it is less durable than stainless steel and can be prone to denting and scratching.
Impact on Application: Aluminum is suitable for non-corrosive environments and is often used in vending machines that dispense snacks or beverages. Its lightweight properties allow for easy relocation of machines.
Considerations for International Buyers: Buyers should be aware of the different aluminum grades (e.g., 6061, 5052) and their respective properties. Compliance with standards like ASTM B221 is important, especially in regions like South America, where local regulations may vary.
Plastic Composites
Key Properties: Plastic composites are lightweight, resistant to corrosion, and can be molded into various shapes. They typically have a temperature rating of around 180°F.
Pros & Cons: The primary advantage of plastic composites is their versatility and lower cost compared to metals. However, they may not withstand heavy impacts and can degrade under UV exposure.
Impact on Application: Ideal for internal components of vending machines, plastic composites can be used for trays and panels. Their resistance to corrosion makes them suitable for machines dispensing beverages.
Considerations for International Buyers: Compliance with safety standards such as ISO 9001 is essential. Buyers should also consider the environmental impact of plastic materials, especially in regions with strict regulations on plastic use.
Carbon Steel
Key Properties: Carbon steel is strong and cost-effective, with a temperature rating of up to 600°F. However, it is susceptible to corrosion without proper treatment.
Pros & Cons: The main advantage of carbon steel is its affordability and strength, making it suitable for structural components. On the downside, it requires protective coatings to prevent rust, which can increase maintenance costs.
Impact on Application: Carbon steel is often used in the framework of vending machines but is not suitable for direct contact with food or beverages unless properly coated.
Considerations for International Buyers: Buyers should ensure compliance with standards like ASTM A36. In regions like Africa, where humidity can be high, protective coatings and treatments are crucial to prolong the machine’s lifespan.
Summary Table
Material | Typical Use Case for plan b vending machine | Key Advantage | Key Disadvantage/Limitation | Relative Cost (Low/Med/High) |
---|---|---|---|---|
Stainless Steel | External casing and structural components | Excellent durability and corrosion resistance | Higher cost and manufacturing complexity | High |
Aluminum | Lightweight components and frames | Lightweight and easy to handle | Less durable; prone to dents | Medium |
Plastic Composites | Internal trays and panels | Versatile and cost-effective | Less impact resistance and UV degradation | Low |
Carbon Steel | Structural framework | Strong and cost-effective | Susceptible to corrosion; requires protection | Low |
This guide provides a comprehensive overview of material selection for Plan B vending machines, helping international B2B buyers make informed decisions based on performance, cost, and compliance with regional standards.
In-depth Look: Manufacturing Processes and Quality Assurance for plan b vending machine
Manufacturing Processes for Plan B Vending Machines
The manufacturing of Plan B vending machines involves several critical stages that ensure the final product meets both functionality and quality standards. Understanding these processes is essential for international B2B buyers aiming to make informed purchasing decisions.
Main Stages of Manufacturing
-
Material Preparation
– The first step involves sourcing high-quality materials, typically metals (such as steel or aluminum) and plastics. It’s essential to ensure that materials comply with relevant international standards to guarantee durability and safety.
– Suppliers should provide certification for materials, such as ISO 9001 for quality management systems, to assure buyers of the materials’ reliability. -
Forming
– This stage includes processes like cutting, bending, and shaping the raw materials into components of the vending machine. Advanced techniques such as laser cutting and CNC machining are often employed for precision.
– For B2B buyers, it’s crucial to inquire about the technologies used in forming processes, as they can significantly affect the machine’s durability and performance. -
Assembly
– The assembly process integrates all components into a functional unit. This may involve automated assembly lines as well as manual labor, depending on the complexity of the machine and the manufacturer’s capabilities.
– Buyers should assess the assembly methods used, as efficiency and skill level can impact the overall quality of the final product. -
Finishing
– Finishing processes, such as painting, coating, or applying decals, are crucial for both aesthetics and protection against wear and tear. Techniques like powder coating or electroplating can enhance durability.
– It’s advisable for buyers to check the types of finishes offered and the environmental regulations adhered to, especially when considering markets in Africa, South America, and the Middle East.
Quality Assurance Processes
Quality assurance (QA) is a vital aspect of the manufacturing process for Plan B vending machines, ensuring that products meet specified requirements and are free from defects.
International Standards and Certifications
- ISO 9001: This standard focuses on quality management systems and is crucial for manufacturers targeting international markets. It ensures consistent quality and customer satisfaction.
- CE Marking: For products sold in Europe, CE marking indicates compliance with health, safety, and environmental protection standards. Buyers should verify this certification to ensure market acceptance.
- API Standards: In regions with specific regulatory requirements, such as the Middle East, compliance with API (American Petroleum Institute) standards may be necessary, especially if the vending machines are used in specialized environments.
Quality Control Checkpoints
-
Incoming Quality Control (IQC)
– This initial checkpoint assesses the quality of materials upon receipt. It is essential to ensure that all incoming components meet the specified standards before they enter the production line. -
In-Process Quality Control (IPQC)
– IPQC occurs during the manufacturing process, where operators monitor production parameters to catch defects early. This can involve real-time inspections and testing of components.
– B2B buyers should inquire about the frequency and methods of IPQC to ensure ongoing quality throughout production. -
Final Quality Control (FQC)
– The FQC stage involves comprehensive testing of the completed vending machines to ensure they function correctly and meet all specifications. This may include functionality tests, safety checks, and performance evaluations.
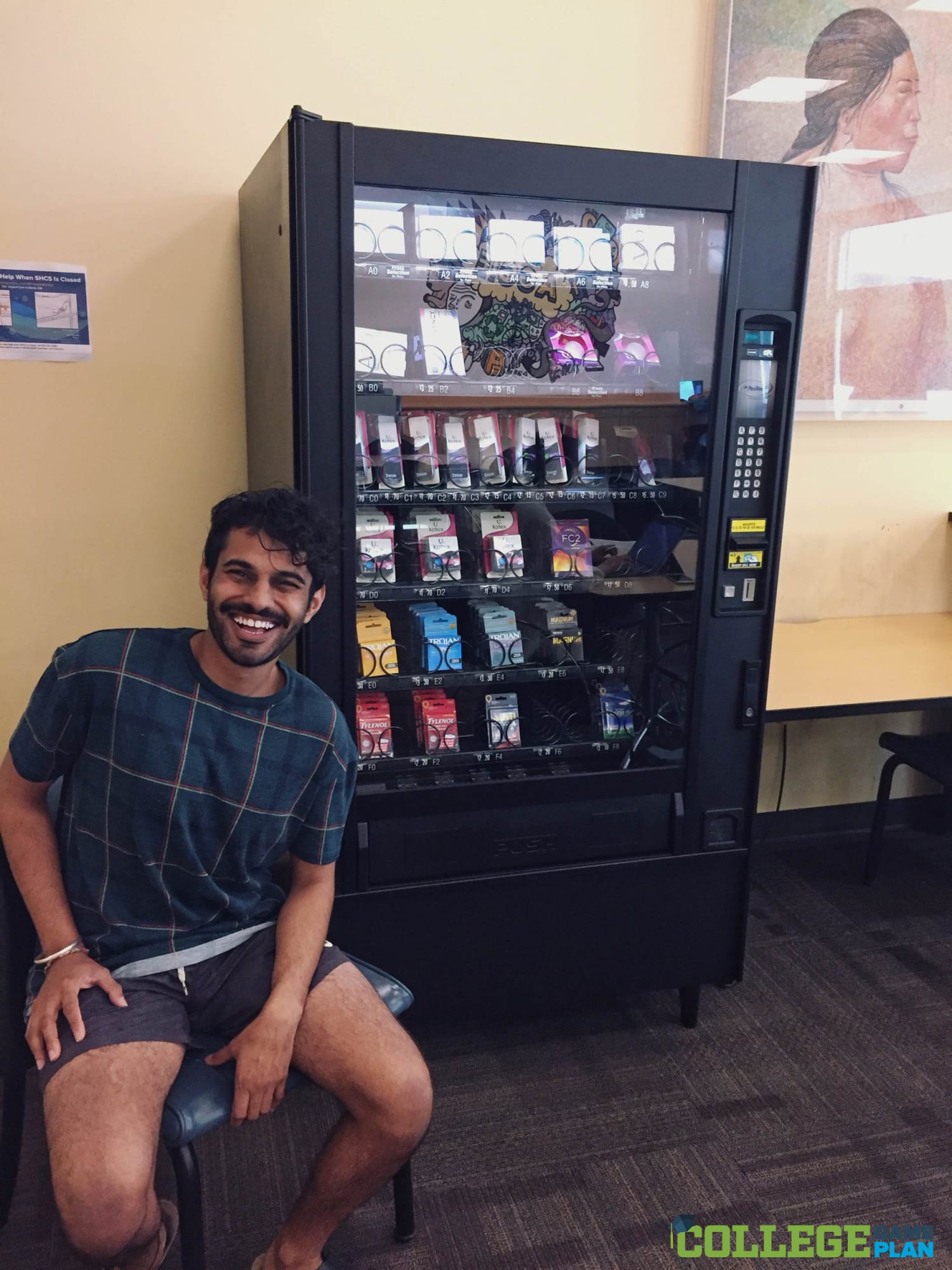
Illustrative Image (Source: Google Search)
Common Testing Methods
- Functional Testing: Verifies that all machine features operate as intended.
- Stress Testing: Assesses how the machine performs under extreme conditions.
- Safety Testing: Ensures compliance with safety regulations and standards.
Verifying Supplier Quality Control
For international B2B buyers, verifying a supplier’s quality control processes is crucial. Here are several actionable strategies:
-
Conduct Audits: Regularly scheduled audits can provide insights into a supplier’s manufacturing processes and adherence to quality standards. Buyers should establish a schedule for these audits to ensure ongoing compliance.
-
Request Quality Reports: Suppliers should be able to provide detailed quality reports, including data from IQC, IPQC, and FQC stages. These reports can help buyers assess the reliability of the manufacturing process.
-
Third-Party Inspections: Engaging third-party inspection services can add an extra layer of assurance. These services can evaluate the manufacturing process and final product quality, providing independent validation.
Quality Control and Certification Nuances for International Buyers
International buyers, particularly from diverse regions like Africa, South America, the Middle East, and Europe, should be aware of the following nuances:
-
Regional Regulations: Different regions may have specific regulatory requirements that impact quality certifications. For example, European buyers must ensure CE compliance, while Middle Eastern buyers might focus on local certifications.
-
Supply Chain Transparency: Understanding the entire supply chain is essential. Buyers should inquire about the origin of materials and manufacturing practices to ensure ethical sourcing and adherence to local laws.
-
Cultural Sensitivity: Recognizing cultural differences in business practices can facilitate better communication and negotiation with suppliers. Building relationships based on trust can enhance the overall purchasing experience.
By focusing on these manufacturing processes and quality assurance practices, international B2B buyers can make informed decisions when sourcing Plan B vending machines. This approach not only mitigates risks but also enhances the likelihood of acquiring high-quality products that meet specific market needs.
Related Video: The Production Planning Process
Comprehensive Cost and Pricing Analysis for plan b vending machine Sourcing
In the sourcing of Plan B vending machines, understanding the comprehensive cost structure and pricing dynamics is essential for international B2B buyers. This section delves into the key components of costs, the factors influencing pricing, and actionable insights for effective procurement.
Cost Components
-
Materials: The primary cost driver in manufacturing vending machines is the raw materials used, such as metal, plastics, electronic components, and refrigeration systems. Prices for these materials can fluctuate based on global supply chain conditions and availability.
-
Labor: Labor costs vary significantly by region. In countries with a higher cost of living, such as those in Western Europe, labor costs may account for a larger portion of the overall expense compared to emerging markets in Africa or South America, where labor may be more affordable.
-
Manufacturing Overhead: This includes costs related to factory operation, utilities, equipment maintenance, and indirect labor. These costs are often fixed and can be spread over the volume of production, affecting the unit price.
-
Tooling: Initial investments in tooling and molds can be substantial, particularly for customized machines. These costs should be amortized over the expected production volume to assess their impact on pricing.
-
Quality Control (QC): Ensuring that machines meet quality standards incurs additional costs. This includes testing, inspections, and certifications, which are particularly important for international markets where compliance with local regulations is mandatory.
-
Logistics: Transportation costs, including shipping, warehousing, and handling, can significantly affect the total cost. Factors such as distance, mode of transport, and fuel prices play a crucial role.
- Margin: Suppliers typically add a profit margin to cover their operational costs and ensure business sustainability. This margin can vary widely based on competition, market demand, and the perceived value of the product.
Price Influencers
-
Volume/MOQ: Minimum Order Quantities (MOQs) can greatly influence pricing. Larger orders often qualify for bulk discounts, which can lead to significant savings.
-
Specifications/Customization: Custom features or specific configurations can increase costs. Buyers should weigh the benefits of customization against potential price hikes.
-
Materials: The choice of materials impacts both the cost and quality. Higher-quality materials may lead to increased upfront costs but can offer better longevity and lower maintenance in the long run.
-
Quality/Certifications: Machines that meet international quality standards or have specific certifications may command higher prices. Buyers should consider the long-term benefits of investing in certified products.
-
Supplier Factors: The reputation and reliability of the supplier can influence pricing. Established suppliers may charge more due to their proven track record, while less-known manufacturers might offer lower prices to enter the market.
-
Incoterms: Understanding Incoterms is crucial for international transactions. They define the responsibilities of buyers and sellers in terms of shipping, insurance, and tariffs, which can affect the overall cost.
Buyer Tips
-
Negotiation: Engage in negotiations with suppliers to explore price reductions, especially for larger orders. Building a strong relationship can lead to better terms over time.
-
Cost-Efficiency: Evaluate the Total Cost of Ownership (TCO), which includes initial purchase price, maintenance, and operational costs. This holistic view can guide better purchasing decisions.
-
Pricing Nuances: Be aware that pricing can vary significantly between regions. Buyers from Africa, South America, the Middle East, and Europe should conduct market research to understand local pricing dynamics and currency fluctuations.
-
Supplier Selection: Prioritize suppliers with a strong reputation for quality and service, even if their prices are slightly higher. This can lead to reduced long-term costs associated with repairs and replacements.
Disclaimer
The prices and cost structures discussed are indicative and can vary based on market conditions, supplier negotiations, and specific project requirements. It is recommended to conduct thorough market research and supplier assessments to obtain accurate pricing for your specific needs.
Spotlight on Potential plan b vending machine Manufacturers and Suppliers
This section offers a look at a few manufacturers active in the ‘plan b vending machine’ market. This is a representative sample for illustrative purposes; B2B buyers must conduct their own extensive due diligence before any engagement. Information is synthesized from public sources and general industry knowledge.
Essential Technical Properties and Trade Terminology for plan b vending machine
In the competitive landscape of vending machine distribution, particularly for the Plan B vending machine, understanding its essential technical properties and trade terminology is crucial for international B2B buyers. Below, we explore the critical specifications and commonly used trade terms that can enhance purchasing decisions.
Key Technical Properties
-
Material Grade
– Definition: The quality and type of materials used in the machine’s construction, such as stainless steel or high-grade plastics.
– Importance: Affects durability, resistance to corrosion, and overall machine longevity. For buyers in regions with varied climates, selecting a machine with appropriate material grades can reduce maintenance costs and improve reliability. -
Capacity
– Definition: The number of items the vending machine can hold, often measured in liters or units.
– Importance: Determines inventory management and sales potential. Buyers should evaluate capacity in relation to expected foot traffic and product turnover to ensure optimal operation. -
Power Consumption
– Definition: The amount of electricity the machine requires to operate effectively, often stated in watts.
– Importance: Understanding power consumption is vital for calculating operational costs. Machines with lower energy requirements can offer significant savings, particularly in regions with high electricity prices. -
Temperature Control Range
– Definition: The range of temperatures the machine can maintain for perishable products.
– Importance: Critical for ensuring product safety and quality, especially in markets where food safety regulations are stringent. This feature is particularly relevant for buyers in the food and beverage sector. -
User Interface
– Definition: The system through which consumers interact with the vending machine, including touchscreen, buttons, and payment methods.
– Importance: A user-friendly interface can enhance customer experience and increase sales. Buyers should consider the interface’s adaptability to local payment methods, especially in diverse markets.
Common Trade Terminology
-
OEM (Original Equipment Manufacturer)
– Definition: A company that produces parts and equipment that may be marketed by another manufacturer.
– Significance: Understanding OEM relationships can help buyers assess product quality and support options. Working with established OEMs often ensures better reliability and warranty coverage. -
MOQ (Minimum Order Quantity)
– Definition: The smallest quantity of a product that a supplier is willing to sell.
– Significance: Buyers must consider MOQ to manage inventory effectively and avoid excess stock. This is particularly important in emerging markets where cash flow management is crucial. -
RFQ (Request for Quotation)
– Definition: A document sent to suppliers requesting pricing and terms for a specific quantity of goods.
– Significance: An essential tool for procurement, RFQs allow buyers to compare prices and terms from multiple suppliers, ensuring competitive rates and favorable conditions. -
Incoterms (International Commercial Terms)
– Definition: A set of pre-defined international trade terms published by the International Chamber of Commerce (ICC).
– Significance: Understanding Incoterms is vital for clarifying shipping responsibilities, costs, and risks between buyers and sellers. It helps in minimizing disputes during international transactions. -
Lead Time
– Definition: The time taken from placing an order until it is received.
– Significance: Knowledge of lead times is essential for inventory planning and meeting market demands. Buyers should communicate clearly with suppliers to understand lead times, especially when dealing with international shipments.
By familiarizing themselves with these technical properties and trade terms, international B2B buyers can make informed decisions when sourcing Plan B vending machines, ensuring they select products that meet their operational needs and market demands.
Navigating Market Dynamics, Sourcing Trends, and Sustainability in the plan b vending machine Sector
Market Overview & Key Trends
The plan b vending machine sector is experiencing significant transformation driven by several global factors. The increasing demand for convenience and on-the-go solutions has led to a surge in automated vending services, catering to diverse consumer preferences, including health-conscious options and local products. For international B2B buyers, particularly from Africa, South America, the Middle East, and Europe, understanding these dynamics is critical for competitive positioning.
Emerging technologies such as IoT (Internet of Things) and AI (Artificial Intelligence) are reshaping the vending landscape. These innovations enable real-time inventory management and personalized customer experiences through data analytics, enhancing operational efficiency and customer satisfaction. For instance, vending machines equipped with AI can analyze purchasing patterns and adjust stock accordingly, thereby optimizing supply chains.
Moreover, sustainability is becoming a cornerstone of sourcing strategies. Many buyers are prioritizing vendors that offer eco-friendly machines and products, reflecting a growing consumer preference for brands that demonstrate social responsibility. The integration of cashless payment systems is another trend gaining traction, driven by the global shift towards digital transactions. This trend not only improves customer convenience but also streamlines revenue tracking for businesses.
As a result, B2B buyers should focus on partnerships with suppliers that leverage technology, offer sustainable practices, and align with evolving consumer behaviors to stay ahead in this rapidly changing market.
Sustainability & Ethical Sourcing in B2B
Sustainability is no longer a niche concern but a fundamental expectation in the plan b vending machine sector. The environmental impact of vending machines, from energy consumption to waste generation, necessitates a shift towards greener practices. B2B buyers must consider the carbon footprint of the machines they source, opting for energy-efficient models that utilize renewable resources.
Ethical sourcing is equally important. Buyers should prioritize suppliers who adhere to ethical labor practices and transparency in their supply chains. This includes ensuring fair wages and safe working conditions for those involved in the production of vending machines and their components. Certifications such as ISO 14001 for environmental management and Fair Trade can serve as indicators of a supplier’s commitment to sustainability.
Additionally, incorporating biodegradable materials and recyclable components into vending machines can significantly reduce waste. Buyers should seek out vendors who provide products with green certifications or use sustainable materials, as these factors are increasingly influencing purchasing decisions in the B2B landscape.
Brief Evolution/History
The evolution of vending machines dates back to ancient times, with early iterations providing simple goods like holy water in temples. However, the modern plan b vending machine concept emerged in the 20th century, initially serving snacks and beverages. Over the decades, advancements in technology have transformed these machines into sophisticated systems capable of offering a wide range of products, including healthy options and even personal care items.
The rise of the digital age has further propelled this evolution, enabling features such as cashless payments and remote monitoring. Today, the sector is not just about convenience but also about aligning with consumer values, particularly regarding sustainability and ethical sourcing. As international markets continue to expand, B2B buyers must be aware of these historical trends to inform their sourcing strategies and adapt to a continuously evolving landscape.
Related Video: International Trade 101 | Economics Explained
Frequently Asked Questions (FAQs) for B2B Buyers of plan b vending machine
-
What should I consider when vetting suppliers for plan B vending machines?
When vetting suppliers, prioritize their industry experience and reputation. Check for certifications relevant to your market, such as ISO standards or local compliance. Request references from previous clients to gauge reliability and service quality. Additionally, assess their production capacity to ensure they can meet your demand. It’s also beneficial to visit their facilities if feasible, or utilize virtual tours to better understand their operations. -
Can I customize the plan B vending machines to suit my brand?
Yes, many suppliers offer customization options for plan B vending machines. You can tailor the design, size, and product offerings to align with your brand identity and target market preferences. Discuss your specific requirements with potential suppliers early in the negotiation process. Ensure that they provide a clear outline of customization capabilities, timelines, and any additional costs involved. -
What are the typical minimum order quantities (MOQs) and lead times for these machines?
Minimum order quantities can vary widely among suppliers, typically ranging from 10 to 100 units. Lead times also depend on the complexity of customization and the supplier’s production schedule, generally ranging from 4 to 12 weeks. When negotiating, inquire about bulk order discounts and express shipping options to minimize delays, especially if you are operating within tight timelines. -
What payment terms should I expect when purchasing plan B vending machines?
Payment terms can differ by supplier, but common practices include a deposit of 30-50% upfront with the balance due prior to shipment. Some suppliers may offer credit terms for established businesses. It’s advisable to clarify payment methods (e.g., bank transfer, credit card) and any associated fees. Always ensure that the payment terms are documented in the contract to avoid misunderstandings. -
What quality assurance processes should I expect from suppliers?
Reputable suppliers should have a robust quality assurance (QA) process in place, including inspections at various production stages. Request details about their QA protocols, such as testing for functionality, safety standards, and compliance certifications. Additionally, inquire whether they provide warranties or guarantees for their machines, which can protect your investment and enhance your confidence in the purchase. -
How are logistics handled for shipping plan B vending machines internationally?
Logistics for international shipments of plan B vending machines typically involve freight forwarders who manage shipping, customs clearance, and delivery. Confirm with suppliers whether they handle logistics or if you need to engage a third-party provider. Understand the shipping costs, estimated delivery times, and insurance options. Ensure that all shipping documentation is clear to avoid delays in customs. -
What should I do if there are disputes or issues with my order?
In case of disputes, refer to the terms outlined in your purchase agreement, which should include procedures for resolving conflicts. Maintain clear documentation of all communications and agreements with the supplier. Many suppliers have customer service or support teams to address issues promptly. If necessary, consider mediation or arbitration as a means to resolve significant disputes without resorting to legal action. -
What certifications should I look for in plan B vending machines?
Look for certifications that demonstrate compliance with safety and operational standards relevant to your market. Key certifications may include CE marking in Europe, UL certification in the U.S., or local certifications based on your region’s regulations. These certifications ensure that the machines meet essential safety, energy efficiency, and performance criteria, which can enhance your credibility with end-users.
Strategic Sourcing Conclusion and Outlook for plan b vending machine
In the competitive landscape of the vending machine industry, particularly for innovative solutions like the Plan B vending machine, strategic sourcing is essential for international B2B buyers. By leveraging global supply chains, businesses can access cutting-edge technology, diverse product offerings, and cost-effective solutions tailored to local markets. This approach not only enhances product availability but also ensures compliance with regional regulations, catering to the unique demands of consumers in Africa, South America, the Middle East, and Europe.
As markets evolve, the need for adaptable sourcing strategies becomes paramount. Buyers should focus on building relationships with suppliers who understand local market nuances and can provide ongoing support. Engaging with vendors that offer customizable options and robust after-sales services can significantly enhance your competitive edge.
Looking ahead, the demand for innovative vending solutions is set to grow. Now is the time for international B2B buyers to explore partnerships that not only align with their business goals but also contribute to sustainable practices. Embrace the opportunity to transform your vending offerings by investing in strategic sourcing, ensuring your business remains at the forefront of this dynamic industry.