Your Ultimate Guide to Sourcing Personal Protective
Guide to Personal Protective Equipment Vending Machines
- Introduction: Navigating the Global Market for personal protective equipment vending machines
- Understanding personal protective equipment vending machines Types and Variations
- Key Industrial Applications of personal protective equipment vending machines
- Strategic Material Selection Guide for personal protective equipment vending machines
- In-depth Look: Manufacturing Processes and Quality Assurance for personal protective equipment vending machines
- Comprehensive Cost and Pricing Analysis for personal protective equipment vending machines Sourcing
- Spotlight on Potential personal protective equipment vending machines Manufacturers and Suppliers
- Essential Technical Properties and Trade Terminology for personal protective equipment vending machines
- Navigating Market Dynamics, Sourcing Trends, and Sustainability in the personal protective equipment vending machines Sector
- Frequently Asked Questions (FAQs) for B2B Buyers of personal protective equipment vending machines
- Strategic Sourcing Conclusion and Outlook for personal protective equipment vending machines
Introduction: Navigating the Global Market for personal protective equipment vending machines
In an increasingly safety-conscious world, personal protective equipment (PPE) vending machines have emerged as a vital solution for businesses across various industries. These automated systems not only streamline the distribution of essential safety gear but also ensure that employees have immediate access to PPE, thus enhancing workplace safety and compliance. For international B2B buyers, particularly those operating in regions such as Africa, South America, the Middle East, and Europe, understanding the intricacies of the PPE vending machine market is crucial for making informed sourcing decisions.
This comprehensive guide covers a wide range of topics essential for navigating the global PPE vending machine landscape. From types of machines and the materials used in manufacturing to the quality control measures that ensure safety standards, we delve into every aspect of the market. Buyers will also find insights into reputable suppliers, cost considerations, and current market trends. Additionally, we address common FAQs to clarify any uncertainties that may arise during the purchasing process.
By equipping B2B buyers with actionable insights and a thorough understanding of the PPE vending machine ecosystem, this guide empowers decision-makers to enhance their sourcing strategies. Embracing these innovations not only supports compliance with safety regulations but also fosters a culture of health and safety within organizations, ultimately leading to improved productivity and employee satisfaction.
Understanding personal protective equipment vending machines Types and Variations
Type Name | Key Distinguishing Features | Primary B2B Applications | Brief Pros & Cons for Buyers |
---|---|---|---|
Standard PPE Vending Machines | Dispenses a variety of PPE items like gloves, masks, and goggles | Manufacturing, construction, healthcare | Pros: Cost-effective, easy to restock. Cons: Limited customization options. |
Smart PPE Vending Machines | Integrated with IoT for inventory tracking and analytics | Warehousing, logistics, and large facilities | Pros: Real-time monitoring, data insights. Cons: Higher initial investment. |
Mobile PPE Vending Units | Portable units designed for temporary or remote job sites | Oil & gas, mining, and outdoor events | Pros: Flexibility and mobility. Cons: Limited stock capacity. |
Customizable PPE Vending Machines | Tailored to specific industry needs with bespoke item selection | Specialized industries like pharmaceuticals | Pros: Tailored solutions, improved compliance. Cons: Higher costs and longer lead times. |
Multi-Functional Vending Machines | Combines PPE with other supplies like tools or first aid kits | General industry, emergency services | Pros: Space-saving, versatile. Cons: Complexity in management. |
Standard PPE Vending Machines
Standard PPE vending machines are designed to dispense essential personal protective equipment such as gloves, masks, and safety goggles. These machines are primarily used in sectors like manufacturing, construction, and healthcare, where safety compliance is critical. Buyers should consider ease of restocking and the machine’s ability to handle high-traffic environments, although customization options may be limited.
Smart PPE Vending Machines
Smart PPE vending machines leverage Internet of Things (IoT) technology to provide real-time inventory tracking and analytics. They are particularly beneficial in warehousing, logistics, and large facilities where monitoring usage patterns can optimize inventory levels. While the data insights can enhance operational efficiency, the higher initial investment may deter some buyers.
Mobile PPE Vending Units
Designed for portability, mobile PPE vending units are ideal for temporary job sites, such as those found in the oil and gas or mining industries. These units can easily be moved to different locations, providing flexibility for outdoor events or remote operations. However, their limited stock capacity may necessitate more frequent refills.
Customizable PPE Vending Machines
Customizable PPE vending machines offer tailored solutions to meet specific industry needs, often including a bespoke selection of items. They are particularly useful in specialized industries like pharmaceuticals, where compliance with safety regulations is paramount. While they provide enhanced functionality, buyers should be aware of the higher costs and longer lead times associated with these machines.
Multi-Functional Vending Machines
These machines combine PPE with other essential supplies, such as tools or first aid kits, making them versatile options for general industry and emergency services. By saving space and providing multiple functionalities, they can enhance operational efficiency. However, the complexity of managing diverse inventory types can pose challenges for buyers.
Related Video: 1. Risk Communication. Models. Definitions
Key Industrial Applications of personal protective equipment vending machines
Industry/Sector | Specific Application of Personal Protective Equipment Vending Machines | Value/Benefit for the Business | Key Sourcing Considerations for this Application |
---|---|---|---|
Construction | On-site PPE distribution | Immediate access to safety gear, reducing downtime | Compatibility with local regulations and standards |
Manufacturing | Employee safety gear access | Enhances worker safety, minimizes injury costs | Variety of PPE types and sizes, ease of restocking |
Oil & Gas | Emergency response equipment | Quick access to critical gear during incidents | Certification for hazardous environments, durability |
Healthcare | Infection control supplies | Ensures compliance with health regulations | Sterilization options, inventory management capabilities |
Mining | Respiratory protection and safety gear | Protects workers from hazardous environments | Robustness in extreme conditions, local sourcing options |
Construction
In the construction industry, personal protective equipment (PPE) vending machines serve as a vital resource on job sites where immediate access to safety gear is crucial. These machines can be strategically placed at various points on-site to provide workers with helmets, gloves, and high-visibility vests without the need to return to a central location. This convenience significantly reduces downtime, ensuring that projects remain on schedule. For international buyers, it’s important to consider local safety regulations and standards when sourcing these machines to ensure compliance and effectiveness.
Manufacturing
Manufacturers benefit from PPE vending machines by ensuring that employees have consistent access to safety equipment, such as goggles, earplugs, and gloves, thereby enhancing overall workplace safety. These machines can be integrated into existing safety protocols to streamline the distribution of PPE, ultimately leading to lower injury rates and reduced costs associated with workplace accidents. Buyers in regions such as South America and Europe should focus on the variety of PPE types and sizes available, ensuring that machines can cater to a diverse workforce.
Oil & Gas
In the oil and gas sector, personal protective equipment vending machines are essential for providing quick access to emergency response gear, such as fire-retardant clothing and safety helmets. These machines can be placed in remote locations, allowing workers to obtain necessary equipment during emergencies without delay. For international buyers, key considerations include ensuring that the equipment meets industry-specific certifications for hazardous environments and that the machines are durable enough to withstand extreme weather conditions.
Healthcare
Healthcare facilities utilize PPE vending machines to distribute essential infection control supplies, including masks, gloves, and gowns, to staff and visitors. This ensures compliance with health regulations and enhances overall safety within the facility. For buyers in the Middle East and Africa, sourcing machines that offer sterilization options and effective inventory management capabilities is critical to maintaining hygiene standards and ensuring that supplies are always available when needed.
Mining
In the mining industry, PPE vending machines provide critical respiratory protection and safety gear to workers exposed to hazardous conditions. These machines can be strategically located in mines to ensure that employees have immediate access to necessary equipment, thereby protecting their health and safety. Buyers should consider the robustness of the machines to withstand extreme conditions and the availability of local sourcing options to ensure timely replenishment of supplies.
Related Video: Personal Protective Equipment (PPE): An Overview of the Basics | Your ACSA Safety Training
Strategic Material Selection Guide for personal protective equipment vending machines
When selecting materials for personal protective equipment (PPE) vending machines, international B2B buyers must consider various factors, including durability, cost, and compliance with local standards. Below is an analysis of four common materials used in the construction of these machines, along with their properties, advantages, disadvantages, and specific considerations for buyers from Africa, South America, the Middle East, and Europe.
1. Stainless Steel
Key Properties:
Stainless steel is renowned for its excellent corrosion resistance and high strength. It can withstand a wide range of temperatures and pressures, making it suitable for various environments.
Pros & Cons:
Stainless steel is highly durable and resistant to rust, which is essential for vending machines exposed to the elements. However, it can be more expensive than other materials and may require specialized manufacturing processes, increasing production complexity.
Impact on Application:
Due to its corrosion resistance, stainless steel is ideal for vending machines located in humid or coastal areas, ensuring longevity and reliability.
Specific Considerations:
Buyers should ensure compliance with international standards such as ASTM A240 for stainless steel grades. In regions like Europe, adherence to EN standards is also crucial for quality assurance.
2. Powder-Coated Steel
Key Properties:
Powder-coated steel offers a protective layer that enhances corrosion resistance while providing aesthetic appeal. The coating can withstand moderate temperatures and is available in various colors.
Pros & Cons:
This material is cost-effective and allows for customization in appearance. However, the powder coating can chip or scratch, exposing the steel underneath and potentially leading to rust over time.
Impact on Application:
Powder-coated steel is suitable for indoor vending machines or those in low-humidity environments. Its aesthetic versatility can enhance branding efforts.
Specific Considerations:
International buyers should verify that the powder coating complies with local regulations regarding VOC emissions and durability standards, such as ISO 12944 for corrosion protection.
3. Polycarbonate
Key Properties:
Polycarbonate is a lightweight, impact-resistant thermoplastic that can endure high temperatures and is inherently UV resistant, making it suitable for outdoor applications.
Pros & Cons:
Its lightweight nature makes installation easier, and it provides excellent visibility for the contents of the vending machine. However, polycarbonate can be more susceptible to scratching and may not be as durable as metals in high-impact scenarios.
Impact on Application:
Polycarbonate is ideal for vending machines that require visibility of products, especially in retail environments. It is also suitable for machines exposed to sunlight.
Specific Considerations:
Buyers should consider compliance with safety standards such as ANSI Z87.1 for impact resistance. Additionally, understanding regional preferences for plastic materials is essential, as some areas may have stricter regulations regarding plastic use.
4. Aluminum
Key Properties:
Aluminum is lightweight, corrosion-resistant, and has good thermal properties. It can be anodized for additional protection, enhancing its durability.
Pros & Cons:
Aluminum is cost-effective and easy to fabricate, making it a popular choice for vending machines. However, it may not be as strong as stainless steel and can be dented more easily.
Impact on Application:
Aluminum is suitable for machines in moderate climates where extreme durability is not a primary concern. Its lightweight nature facilitates easier transportation and installation.
Specific Considerations:
International buyers should ensure that the aluminum used meets standards such as ASTM B221 for structural applications. Additionally, understanding local market preferences for aluminum versus steel can influence purchasing decisions.
Summary Table
Material | Typical Use Case for personal protective equipment vending machines | Key Advantage | Key Disadvantage/Limitation | Relative Cost (Low/Med/High) |
---|---|---|---|---|
Stainless Steel | Outdoor machines in humid or coastal areas | Excellent corrosion resistance, durability | Higher cost, complex manufacturing | High |
Powder-Coated Steel | Indoor machines or low-humidity environments | Cost-effective, customizable appearance | Susceptible to chipping, less durable | Medium |
Polycarbonate | Retail or outdoor machines requiring visibility | Lightweight, impact-resistant | Scratches easily, less durable than metals | Medium |
Aluminum | Moderate climate machines | Lightweight, easy to fabricate | Not as strong as stainless steel | Low |
This strategic material selection guide provides essential insights for international B2B buyers, helping them make informed decisions tailored to their specific market needs and compliance requirements.
In-depth Look: Manufacturing Processes and Quality Assurance for personal protective equipment vending machines
The manufacturing of personal protective equipment (PPE) vending machines involves several critical stages, each designed to ensure that the final product meets the stringent requirements of safety, usability, and durability. For B2B buyers, particularly those from Africa, South America, the Middle East, and Europe, understanding these processes is essential for making informed purchasing decisions.
Manufacturing Processes
1. Material Preparation
The first step in manufacturing PPE vending machines is material preparation. This involves selecting high-quality materials that can withstand various environmental conditions. Common materials include:
- Stainless Steel: Known for its resistance to corrosion and durability, stainless steel is often used for the outer casing.
- Plastic Composites: Lightweight and resistant to impact, plastics are used for internal components and mechanisms.
- Electronics: Components such as sensors, displays, and payment systems are sourced from reputable suppliers to ensure compatibility and reliability.
2. Forming
Once materials are prepared, the forming process begins. This stage typically includes:
- Cutting and Shaping: Sheets of metal and plastic are cut into precise shapes using CNC machines. This ensures uniformity and accuracy in dimensions.
- Bending and Welding: Metal components are bent into shape and welded together to create the structure of the vending machine. Robotic welding is commonly used for its precision and efficiency.
3. Assembly
The assembly stage involves combining all components into a cohesive unit. Key processes include:
- Component Installation: Internal mechanisms, such as dispensing systems and electronic controls, are installed. This may include integrating RFID technology for inventory tracking.
- Electrical Wiring: All electronic components are wired according to strict safety standards to prevent short circuits and ensure functionality.
4. Finishing
The final stage involves applying protective finishes and conducting aesthetic enhancements. This may include:
- Painting and Coating: A powder coating is often applied to enhance corrosion resistance and provide a visually appealing finish.
- Quality Checks: Before leaving the factory, each machine undergoes a series of quality checks to ensure functionality and safety.
Quality Assurance
Quality assurance is crucial in the manufacturing of PPE vending machines. It involves adhering to international standards and implementing specific quality control measures throughout the production process.
Relevant International Standards
For B2B buyers, familiarity with international standards can provide assurance of quality. Key standards include:
- ISO 9001: This standard focuses on quality management systems and is applicable to manufacturers of PPE vending machines. It emphasizes customer satisfaction and continuous improvement.
- CE Marking: Required for products sold in the European Economic Area, CE marking indicates compliance with health, safety, and environmental protection standards.
- API Standards: For machines intended for use in hazardous environments, adherence to American Petroleum Institute (API) standards may be necessary.
Quality Control Checkpoints
The manufacturing process incorporates several checkpoints to ensure quality:
- Incoming Quality Control (IQC): Raw materials are inspected upon arrival to ensure they meet specified standards.
- In-Process Quality Control (IPQC): Inspections are conducted at various stages of production to identify defects early.
- Final Quality Control (FQC): The completed machines undergo rigorous testing to ensure they function correctly and meet safety standards.
Common Testing Methods
Testing methods employed in the quality assurance process include:
- Functional Testing: Ensuring all electronic components operate as intended.
- Durability Testing: Subjecting the machine to stress tests to evaluate its performance under various conditions.
- Compliance Testing: Verifying adherence to industry-specific standards, such as those outlined by ISO or CE.
Verifying Supplier Quality Control
B2B buyers can take several steps to verify the quality control processes of their suppliers:
- Conduct Audits: Regular audits of the manufacturing facility can provide insight into the supplier’s adherence to quality standards.
- Request Quality Reports: Suppliers should provide documentation that details their quality control processes, including any certifications received.
- Engage Third-Party Inspectors: Utilizing third-party inspection services can help ensure that the products meet the required standards and specifications before they are shipped.
Quality Control and Certification Nuances
Understanding the nuances of quality control and certification is vital for international B2B buyers, especially those from diverse regions such as Africa, South America, the Middle East, and Europe. Factors to consider include:
- Regional Regulations: Different regions may have specific regulatory requirements that affect the certification process. For example, PPE vending machines used in healthcare settings may require additional certifications.
- Cultural Expectations: Buyers should be aware that expectations for quality and safety can vary between regions. Engaging with local experts can help bridge this gap.
- Supply Chain Transparency: Buyers should prioritize suppliers who demonstrate transparency in their sourcing and manufacturing processes, as this can significantly impact the overall quality of the product.
By understanding the manufacturing processes and quality assurance practices associated with PPE vending machines, international B2B buyers can make informed decisions that enhance their operational efficiency and safety standards. This knowledge is especially crucial for buyers in regions with varying regulatory landscapes, as it enables them to align their purchasing strategies with global best practices.
Related Video: Amazing Production Process with Modern Machines and Skilful Workers
Comprehensive Cost and Pricing Analysis for personal protective equipment vending machines Sourcing
When sourcing personal protective equipment (PPE) vending machines, understanding the comprehensive cost structure and pricing dynamics is crucial for international B2B buyers. This analysis delves into the essential cost components, price influencers, and practical buyer tips that will enable informed decision-making, especially for businesses operating in diverse markets like Africa, South America, the Middle East, and Europe.
Cost Components
-
Materials: The primary materials for PPE vending machines include metal, plastics, and electronic components. The choice of materials significantly impacts both the durability and cost of the machines. For example, machines made with high-grade stainless steel may have a higher upfront cost but offer better longevity.
-
Labor: Labor costs are tied to the production location. Countries with lower labor costs may offer cheaper machines, but this can sometimes compromise quality. Consider the balance between labor costs and the skill level of workers when evaluating suppliers.
-
Manufacturing Overhead: This includes costs associated with running the manufacturing facility, such as utilities, rent, and equipment maintenance. Efficient factories may pass on savings to buyers, making it essential to assess a supplier’s operational efficiency.
-
Tooling: The initial investment in molds and tools for production can be significant, especially for customized machines. This cost is often amortized over larger production runs, so minimum order quantities (MOQs) can influence overall pricing.
-
Quality Control (QC): Implementing rigorous QC processes ensures that machines meet safety and operational standards. While this adds to the cost, it can prevent future expenses related to product failures or recalls.
-
Logistics: Shipping and handling costs can vary dramatically based on the destination and shipping method. International buyers should factor in customs duties, taxes, and potential tariffs, especially when importing from regions with different trade agreements.
-
Margin: Suppliers typically include a profit margin in their pricing. Understanding the market standard can help buyers negotiate better terms.
Price Influencers
-
Volume/MOQ: Ordering in bulk usually results in lower per-unit costs. Buyers should evaluate their capacity to stock machines and negotiate MOQs that align with their budget and storage capabilities.
-
Specifications/Customization: Customized features, such as branding or additional functionalities, can increase costs. Buyers should weigh the benefits of customization against the added expense.
-
Materials and Quality Certifications: Higher-quality materials and compliance with international safety standards may increase initial costs but can lead to lower maintenance and replacement costs over time.
-
Supplier Factors: The reputation and reliability of suppliers affect pricing. Established suppliers may command higher prices due to their proven track record, while newer entrants might offer competitive rates to gain market share.
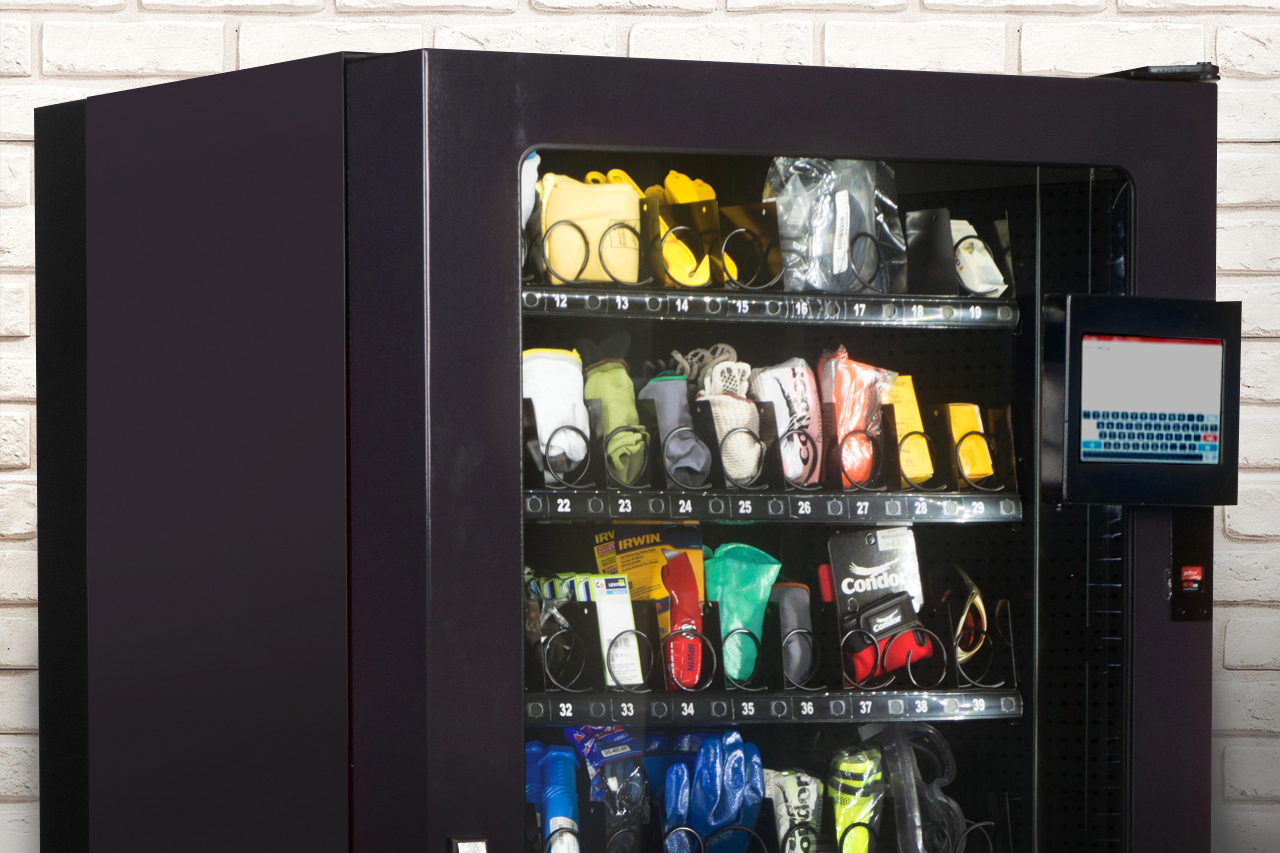
Illustrative Image (Source: Google Search)
- Incoterms: The agreed-upon shipping terms can impact total costs. For instance, choosing DDP (Delivered Duty Paid) can simplify logistics for buyers but may come at a premium.
Buyer Tips
-
Negotiate Terms: Leverage your purchasing power by negotiating payment terms, delivery schedules, and price breaks for larger orders.
-
Focus on Cost-Efficiency: Look beyond the initial price. Evaluate the Total Cost of Ownership (TCO), which includes maintenance, operational efficiency, and potential downtime.
-
Understand Pricing Nuances: Different regions may have varying pricing structures due to local economic conditions, currency fluctuations, and demand-supply dynamics. Buyers from Africa, South America, the Middle East, and Europe should be aware of these factors when sourcing.
-
Engage Multiple Suppliers: Obtaining quotes from several suppliers can provide a clearer picture of the market and help in negotiating better prices.
Disclaimer
The prices discussed in this analysis are indicative and may vary based on specific project requirements, supplier negotiations, and market conditions. Always conduct thorough research and obtain multiple quotes to ensure competitive pricing.
Spotlight on Potential personal protective equipment vending machines Manufacturers and Suppliers
This section offers a look at a few manufacturers active in the ‘personal protective equipment vending machines’ market. This is a representative sample for illustrative purposes; B2B buyers must conduct their own extensive due diligence before any engagement. Information is synthesized from public sources and general industry knowledge.
Essential Technical Properties and Trade Terminology for personal protective equipment vending machines
Key Technical Properties of Personal Protective Equipment Vending Machines
When investing in personal protective equipment (PPE) vending machines, it is crucial to understand the essential technical properties that can impact functionality, durability, and overall value. Here are several critical specifications:
-
Material Grade
– The material grade refers to the quality and type of materials used in the construction of the vending machine. Common materials include stainless steel and high-grade plastics, which provide resistance to corrosion and impact.
– B2B Importance: High-quality materials ensure longevity and reliability, reducing maintenance costs and downtime. -
Capacity
– This specification indicates the number of PPE items the machine can hold. It can vary widely based on the model and intended use, from a few dozen items to several hundred.
– B2B Importance: Understanding capacity helps businesses assess how often the machine will need restocking, impacting operational efficiency and inventory management. -
Dimensions and Weight
– Dimensions (height, width, depth) and weight affect placement options and transportation logistics. Compact models may be suitable for smaller facilities, while larger units may require specific installation considerations.
– B2B Importance: Knowing the dimensions ensures that the vending machine fits the designated space while considering transport and installation logistics. -
Power Consumption
– This property refers to the energy required for the vending machine to operate, typically measured in watts. Energy-efficient models can significantly reduce operational costs.
– B2B Importance: Lower power consumption not only reduces electricity bills but also aligns with sustainability goals, which is increasingly important for corporate responsibility. -
User Interface
– A user-friendly interface, which may include touch screens, multilingual options, and clear instructions, enhances the customer experience.
– B2B Importance: A well-designed user interface minimizes user errors and increases the efficiency of equipment access, leading to higher employee satisfaction and productivity.
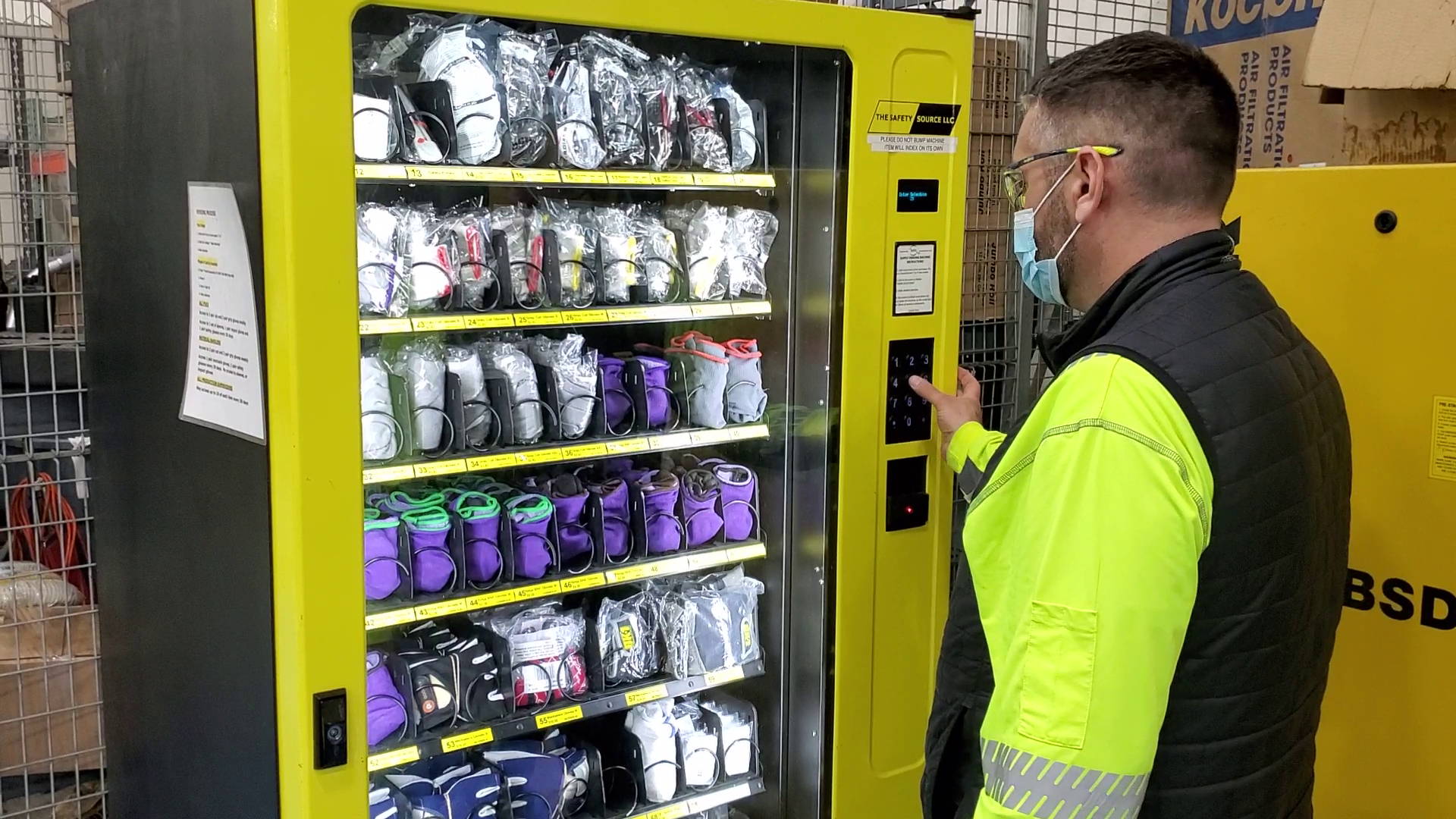
Illustrative Image (Source: Google Search)
Common Trade Terminology in PPE Vending Machines
Understanding industry jargon can streamline the purchasing process and improve negotiations. Here are some essential terms:
-
OEM (Original Equipment Manufacturer)
– An OEM is a company that manufactures products or components that are sold under another company’s brand name. In the context of PPE vending machines, it refers to the companies that produce the machines themselves.
– Importance: Knowing the OEM helps buyers ensure they are sourcing from reputable manufacturers with a proven track record of quality. -
MOQ (Minimum Order Quantity)
– MOQ refers to the smallest number of units a supplier is willing to sell. This is particularly relevant when purchasing vending machines or bulk PPE stock.
– Importance: Understanding MOQ is critical for budget planning and inventory management, ensuring that companies meet their operational needs without overcommitting resources. -
RFQ (Request for Quotation)
– An RFQ is a formal document that an organization sends to suppliers to request pricing and other terms for specific products or services.
– Importance: Utilizing RFQs can lead to competitive pricing and better procurement terms, enabling buyers to make informed purchasing decisions. -
Incoterms (International Commercial Terms)
– Incoterms are a set of international rules that define the responsibilities of buyers and sellers in the shipping and delivery of goods. They cover aspects like shipping costs, insurance, and risk transfer.
– Importance: Familiarity with Incoterms helps international buyers understand their obligations and risks, facilitating smoother cross-border transactions. -
Lead Time
– Lead time is the duration between placing an order and receiving the product. This can vary based on the supplier, manufacturing schedules, and logistics.
– Importance: Knowing the lead time is essential for planning inventory levels and ensuring that PPE is available when needed, particularly in industries with strict safety regulations.
By comprehensively understanding these technical properties and trade terms, international B2B buyers can make more informed decisions when selecting personal protective equipment vending machines that align with their operational needs and strategic goals.
Navigating Market Dynamics, Sourcing Trends, and Sustainability in the personal protective equipment vending machines Sector
Market Overview & Key Trends
The personal protective equipment (PPE) vending machine sector is witnessing robust growth driven by several global factors. As workplace safety regulations become stricter, companies are increasingly adopting automated solutions to ensure immediate access to PPE. This trend is particularly pronounced in industries such as construction, manufacturing, and healthcare. In regions like Africa and South America, the rise in industrial activities and urbanization is propelling demand for PPE vending solutions, offering a convenient way to manage safety equipment efficiently.
Key technological advancements are shaping the market dynamics. Smart vending machines equipped with IoT technology allow for real-time inventory management and usage tracking, enabling businesses to optimize stock levels and reduce waste. Additionally, contactless payment options have become essential, particularly post-pandemic, as they enhance user convenience and hygiene. For international buyers, particularly from emerging markets like Colombia and Argentina, investing in such technology can lead to significant operational efficiencies and improved compliance with safety standards.
Furthermore, the market is witnessing an increase in customization. Companies are seeking vending machines tailored to specific industry needs, which may include specialized PPE for hazardous environments. As a result, suppliers that can offer flexible solutions and integrate with existing systems are likely to gain a competitive edge. Understanding these trends will be crucial for B2B buyers aiming to navigate the evolving landscape of PPE vending solutions effectively.
Sustainability & Ethical Sourcing in B2B
Sustainability is becoming a pivotal concern in the PPE vending machine sector. The environmental impact of PPE production and disposal is significant, prompting companies to seek eco-friendly alternatives. B2B buyers are increasingly prioritizing suppliers who demonstrate a commitment to sustainability, which includes using recycled materials, biodegradable products, and energy-efficient manufacturing processes.
Ethical sourcing practices are equally important. Buyers should ensure that their suppliers adhere to fair labor practices and have transparent supply chains. This not only mitigates reputational risks but also aligns with the values of socially conscious consumers and businesses. Certifications such as ISO 14001 for environmental management and Fair Trade can serve as indicators of a supplier’s commitment to ethical practices.
Incorporating sustainable practices into the procurement process not only helps in compliance with local and international regulations but can also lead to cost savings in the long run. By choosing ‘green’ materials and suppliers, businesses can enhance their brand image and appeal to a growing market segment that values corporate responsibility.
Brief Evolution/History
The evolution of personal protective equipment vending machines reflects broader changes in workplace safety and technology. Initially, these machines served basic functions, offering limited PPE options in industrial settings. However, as awareness of workplace safety expanded and technology advanced, the machines transformed into sophisticated units capable of tracking inventory, managing supply chains, and integrating with payment systems.
The COVID-19 pandemic accelerated the adoption of PPE vending machines, as companies sought to provide easy access to safety gear while minimizing human contact. Today, these machines are not only prevalent in traditional industries but are also finding applications in healthcare facilities, public spaces, and educational institutions, marking a significant shift in how organizations approach safety and compliance. As the market continues to evolve, innovations in technology and sustainability will play a crucial role in shaping the future of PPE vending solutions.
Related Video: Global Trade & Logistics – What is Global Trade?
Frequently Asked Questions (FAQs) for B2B Buyers of personal protective equipment vending machines
-
What criteria should I use to vet suppliers of personal protective equipment (PPE) vending machines?
When vetting suppliers, consider their industry experience, client testimonials, and certifications. Ensure they comply with international standards for PPE, such as ISO certifications. Request references from past clients, especially those in your region, to gauge reliability and service quality. Additionally, evaluate their financial stability and capacity for after-sales support, which is crucial for long-term partnerships. -
Can I customize the PPE vending machines to fit specific needs?
Yes, many suppliers offer customization options for PPE vending machines. You can tailor the machine’s inventory based on the specific requirements of your industry or workplace. Additionally, customization may extend to branding, machine size, and software features, allowing you to enhance user experience. Discuss your needs directly with suppliers to explore available options and any associated costs. -
What is the minimum order quantity (MOQ) and typical lead time for PPE vending machines?
The MOQ can vary widely among suppliers, typically ranging from one unit for smaller operations to larger quantities for bulk orders. Lead times also depend on the supplier’s production capacity and customization requirements, often ranging from 4 to 12 weeks. It’s advisable to confirm these details during initial discussions to align your procurement schedule with your operational needs. -
What payment options are typically available for international buyers?
Suppliers generally offer several payment options, including wire transfers, letters of credit, and PayPal. For larger orders, letters of credit are often preferred as they provide security for both parties. Ensure to discuss and agree on payment terms upfront, including deposit amounts and milestones, to avoid disputes later in the transaction process. -
How can I ensure quality assurance and necessary certifications for PPE?
Request documentation from suppliers that verifies compliance with relevant safety standards and certifications, such as CE marking in Europe or ANSI standards in the US. Conduct a factory audit if possible, or utilize third-party inspection services to assess product quality before shipment. This proactive approach helps mitigate risks associated with non-compliance and ensures that the PPE vending machines meet your safety requirements. -
What logistics considerations should I be aware of when importing PPE vending machines?
Logistics play a critical role in the procurement process. Consider shipping methods, customs clearance, and potential tariffs based on your country’s regulations. Work with suppliers who have experience in international shipping and can provide guidance on documentation required for customs. Additionally, ensure that the machines are adequately packaged to withstand transport conditions. -
How should I handle disputes with suppliers regarding PPE vending machines?
Establish clear communication channels and outline dispute resolution procedures in your contract. Common methods include mediation and arbitration, which can be less costly than litigation. Maintain comprehensive records of all transactions, communications, and agreements to support your case if disputes arise. Consider including clauses that specify jurisdiction and governing law to facilitate smoother resolutions. -
What support should I expect from suppliers post-purchase?
Suppliers should provide comprehensive post-purchase support, including installation, maintenance, and troubleshooting services. Confirm the warranty terms and inquire about the availability of spare parts and technical assistance. A reliable supplier will also offer training for your staff on how to operate the machines effectively, ensuring a smooth integration into your operations.
Strategic Sourcing Conclusion and Outlook for personal protective equipment vending machines
In conclusion, strategic sourcing for personal protective equipment (PPE) vending machines is essential for international B2B buyers seeking to enhance workplace safety and operational efficiency. By leveraging advanced sourcing strategies, businesses can secure high-quality PPE while optimizing costs and ensuring timely supply chain management. Key takeaways include the importance of evaluating supplier reliability, understanding local regulatory requirements, and embracing technological advancements in vending solutions that cater to diverse market needs.
As global demand for PPE continues to rise, especially in regions like Africa, South America, the Middle East, and Europe, investing in smart vending solutions will not only streamline access to essential safety gear but also bolster employee confidence in workplace safety protocols.
International buyers are encouraged to conduct thorough market research, establish strategic partnerships, and remain adaptable to changing industry trends. The future of PPE vending machines is promising, with opportunities for innovation and growth. Now is the time to act—invest in strategic sourcing to ensure your organization is well-equipped to meet the challenges of tomorrow.