Your Ultimate Guide to Sourcing Omny Vending Machines
Guide to Omny Vending Machines
- Introduction: Navigating the Global Market for omny vending machines
- Understanding omny vending machines Types and Variations
- Key Industrial Applications of omny vending machines
- Strategic Material Selection Guide for omny vending machines
- In-depth Look: Manufacturing Processes and Quality Assurance for omny vending machines
- Comprehensive Cost and Pricing Analysis for omny vending machines Sourcing
- Spotlight on Potential omny vending machines Manufacturers and Suppliers
- Essential Technical Properties and Trade Terminology for omny vending machines
- Navigating Market Dynamics, Sourcing Trends, and Sustainability in the omny vending machines Sector
- Frequently Asked Questions (FAQs) for B2B Buyers of omny vending machines
- Strategic Sourcing Conclusion and Outlook for omny vending machines
Introduction: Navigating the Global Market for omny vending machines
Navigating the global market for omny vending machines presents a unique opportunity for B2B buyers to tap into a burgeoning sector characterized by innovation and consumer demand. These advanced machines, capable of offering a wide range of products from snacks to electronics, are becoming essential fixtures in diverse environments such as offices, schools, and public spaces. As the global economy evolves, understanding the intricacies of sourcing these machines is critical for businesses aiming to stay competitive.
This comprehensive guide will equip international B2B buyers, particularly from regions such as Africa, South America, the Middle East, and Europe (including key markets like Saudi Arabia and Spain), with actionable insights necessary for informed sourcing decisions. We will explore various aspects including the different types of omny vending machines, suitable materials, manufacturing and quality control standards, and reliable suppliers. Additionally, we will delve into cost considerations and market trends, alongside addressing frequently asked questions that can clarify common concerns.
By leveraging the knowledge contained within this guide, businesses can foster stronger supplier partnerships, optimize their inventory strategies, and ensure compliance with local regulations. Ultimately, this resource serves not only as a roadmap for navigating the complexities of the vending machine market but also as a catalyst for driving profitability and sustainable growth in a rapidly evolving landscape.
Understanding omny vending machines Types and Variations
Type Name | Key Distinguishing Features | Primary B2B Applications | Brief Pros & Cons for Buyers |
---|---|---|---|
Snack and Beverage Machines | Dispenses snacks and drinks in various sizes | Offices, schools, hospitals | Pros: High demand, easy to stock. Cons: Requires regular maintenance and monitoring. |
Healthy Food Vending Machines | Focuses on nutritious options and dietary needs | Gyms, schools, corporate wellness programs | Pros: Appeals to health-conscious consumers. Cons: Limited product range may affect sales. |
Industrial Vending Machines | Tailored for tools and equipment in workplaces | Manufacturing, construction sites | Pros: Reduces waste, tracks inventory. Cons: Higher initial investment costs. |
Automated Retail Machines | Advanced tech for self-checkout and product selection | Retail stores, airports, event venues | Pros: Enhances customer experience, reduces labor costs. Cons: Technical issues can disrupt service. |
Specialty Item Vending Machines | Dispenses niche products like electronics or cosmetics | Airports, shopping malls | Pros: Targets specific markets, high margins. Cons: Limited customer base may affect turnover. |
Snack and Beverage Machines
Snack and beverage vending machines are the most common type, found in various locations such as offices, schools, and hospitals. They offer a wide selection of snacks and drinks, catering to diverse consumer preferences. For B2B buyers, key considerations include the machine’s capacity, ease of restocking, and payment options. Regular maintenance is essential to ensure optimal operation, which can impact profitability if neglected.
Healthy Food Vending Machines
These machines focus on providing nutritious food options, appealing to health-conscious consumers. They are commonly placed in gyms, schools, and corporate wellness programs. When considering a healthy food vending machine, buyers should evaluate product variety, supplier partnerships for fresh inventory, and compliance with health regulations. While they attract a specific customer base, their limited product range can sometimes hinder sales.
Industrial Vending Machines
Designed for workplaces, industrial vending machines dispense tools, parts, and maintenance supplies. They are particularly beneficial in manufacturing and construction settings, where inventory control is critical. B2B buyers should assess features like inventory tracking, automated reordering capabilities, and the machine’s ability to withstand industrial environments. Although the initial investment is higher, the potential for reduced waste and improved efficiency can lead to significant long-term savings.
Automated Retail Machines
These advanced vending solutions incorporate technology for self-checkout and product selection, often found in retail stores, airports, and event venues. They enhance the customer experience by offering convenience and reducing labor costs. B2B buyers should consider the machine’s user interface, payment processing options, and technical support for troubleshooting. However, reliance on technology can pose risks, as technical issues may disrupt service and lead to customer dissatisfaction.
Specialty Item Vending Machines
Specialty vending machines cater to niche markets, offering products such as electronics, cosmetics, or gourmet foods. They are strategically placed in high-traffic areas like airports and shopping malls to target specific consumer demographics. For B2B buyers, evaluating the product sourcing, market demand, and potential profit margins is crucial. While these machines can yield high profits, their limited customer base may affect turnover, making thorough market research essential before investment.
Related Video: How to use an OMNY card vending machine
Key Industrial Applications of omny vending machines
Industry/Sector | Specific Application of omny vending machines | Value/Benefit for the Business | Key Sourcing Considerations for this Application |
---|---|---|---|
Manufacturing | On-site tool and equipment vending | Reduces downtime by providing immediate access to tools | Supplier reliability, inventory management systems, bulk pricing |
Healthcare | Dispensing medical supplies and PPE | Streamlines supply management, ensures compliance | Regulatory compliance, product quality assurance, supply chain transparency |
Education | Snack and beverage vending in schools and universities | Enhances student satisfaction, promotes healthy eating | Product variety, local sourcing, nutritional compliance |
Hospitality | 24/7 access to snacks and drinks in hotels | Increases guest convenience, boosts ancillary revenue | Customization options, payment system compatibility, service support |
Construction | Vending for safety gear and personal protective equipment | Ensures worker safety, minimizes delays in project timelines | Compliance with safety regulations, product availability, vendor support |
In the manufacturing sector, omny vending machines are utilized for on-site tool and equipment dispensing. This application significantly reduces downtime by providing immediate access to essential tools and equipment, ensuring that production lines remain operational. For international buyers, particularly in regions like Africa and South America, sourcing reliable suppliers who can maintain consistent inventory levels is crucial to avoid disruptions.
In healthcare, these machines serve as dispensers for medical supplies and personal protective equipment (PPE). This application not only streamlines supply management but also ensures compliance with health regulations. Buyers in the Middle East and Europe must prioritize suppliers who can guarantee product quality and adherence to local regulations to ensure patient safety and operational efficiency.
The education sector benefits from omny vending machines by providing snacks and beverages in schools and universities. This application enhances student satisfaction and promotes healthy eating habits. For B2B buyers in Europe, sourcing products that align with nutritional guidelines and offering a diverse selection to cater to various dietary needs is essential for maximizing this opportunity.
In the hospitality industry, omny vending machines offer 24/7 access to snacks and drinks in hotels, enhancing guest convenience and boosting ancillary revenue. International buyers should consider customization options that reflect local tastes and preferences, as well as ensuring compatibility with various payment systems to accommodate diverse clientele.
Finally, in the construction industry, these machines are instrumental in vending safety gear and personal protective equipment (PPE). This application is vital for ensuring worker safety and minimizing delays in project timelines. Buyers need to focus on compliance with safety regulations and ensure that vendors can provide timely support and product availability to maintain operational efficiency.
Strategic Material Selection Guide for omny vending machines
When selecting materials for omny vending machines, it is crucial to consider factors such as durability, cost, and compliance with international standards. Below is an analysis of four common materials used in the construction of these machines, focusing on their properties, advantages, disadvantages, and implications for international B2B buyers.
1. Stainless Steel
Key Properties: Stainless steel is known for its excellent corrosion resistance, high strength, and ability to withstand a wide range of temperatures. It typically has a temperature rating of up to 800°F (427°C) and can handle high-pressure environments.
Pros & Cons: The primary advantage of stainless steel is its durability and resistance to rust and staining, making it ideal for vending machines exposed to various environmental conditions. However, it is relatively expensive compared to other materials and can be challenging to fabricate due to its hardness.
Impact on Application: Stainless steel is particularly suitable for vending machines that dispense food and beverages, as it meets hygiene standards and is easy to clean.
Considerations for International Buyers: Buyers from regions like Europe and the Middle East should ensure compliance with food safety regulations, such as those set by the European Food Safety Authority (EFSA). In contrast, buyers in Africa and South America may need to consider local standards and certifications.
2. Powder-Coated Steel
Key Properties: Powder-coated steel offers a protective layer that enhances corrosion resistance and provides a variety of color options. The coating can withstand temperatures up to 400°F (204°C).
Pros & Cons: This material is cost-effective and allows for aesthetic customization, which can attract customers. However, it may not be as durable as stainless steel, as the coating can chip or scratch, leading to corrosion over time.
Impact on Application: Powder-coated steel is suitable for vending machines located in indoor environments where aesthetic appeal is essential, but it may not be ideal for outdoor use.
Considerations for International Buyers: Buyers should check for compliance with local environmental regulations regarding coatings and finishes. In regions like Europe, adherence to REACH regulations may be necessary.
3. Aluminum
Key Properties: Aluminum is lightweight, resistant to corrosion, and has a good strength-to-weight ratio. It typically operates effectively within a temperature range of -50°F to 150°F (-45°C to 65°C).
Pros & Cons: The main advantage of aluminum is its lightweight nature, which reduces shipping costs and makes installation easier. However, it is less durable than stainless steel and can be prone to dents and scratches.
Impact on Application: Aluminum is ideal for vending machines that require portability or frequent relocation, such as those used in events or temporary setups.
Considerations for International Buyers: Buyers should be aware of the varying standards for aluminum alloys in different regions. For example, European buyers may refer to EN standards, while those in South America may need to consider local specifications.
4. Glass
Key Properties: Glass offers excellent visibility for product displays and can be treated for increased strength and thermal resistance. Tempered glass can withstand impacts and is often used in front panels.
Pros & Cons: The primary advantage of glass is its aesthetic appeal and ability to showcase products effectively. However, it is fragile and can break easily, leading to higher replacement costs.
Impact on Application: Glass is commonly used in vending machines that prioritize product visibility, such as those dispensing snacks or beverages.
Considerations for International Buyers: Compliance with safety standards is critical, especially in regions where glass is used in public spaces. Buyers should ensure that the glass used meets local safety regulations, such as those outlined by ASTM or DIN standards.
Summary Table
Material | Typical Use Case for omny vending machines | Key Advantage | Key Disadvantage/Limitation | Relative Cost (Low/Med/High) |
---|---|---|---|---|
Stainless Steel | Food and beverage dispensing machines | Excellent durability and corrosion resistance | Higher cost and manufacturing complexity | High |
Powder-Coated Steel | Indoor vending machines requiring aesthetic appeal | Cost-effective and customizable | Less durable; coating can chip | Medium |
Aluminum | Portable vending machines for events | Lightweight and easy to install | Less durable; prone to dents | Medium |
Glass | Machines emphasizing product visibility | Aesthetic appeal and visibility | Fragile; higher replacement costs | Medium |
This strategic material selection guide aims to assist international B2B buyers in making informed decisions when sourcing components for omny vending machines, ensuring compliance with local standards while maximizing performance and profitability.
In-depth Look: Manufacturing Processes and Quality Assurance for omny vending machines
The manufacturing process for omny vending machines is a multi-stage operation that emphasizes precision and quality at every step. Understanding these stages can provide international B2B buyers with insights into the reliability and performance of the machines they intend to procure.
Manufacturing Process
1. Material Preparation
The manufacturing journey begins with the careful selection and preparation of materials. Key materials include metals for the chassis, plastics for the housing, and electronic components for the vending mechanism. Suppliers must ensure that all materials comply with international standards such as ISO 9001 to guarantee quality and consistency.
During this stage, raw materials undergo rigorous testing for durability and safety. Buyers should request documentation from suppliers regarding the material specifications and compliance certifications to ensure that the materials meet local regulations in their respective countries.
2. Forming
The forming stage involves shaping the prepared materials into the required components. This process typically utilizes techniques such as stamping, bending, and injection molding. Advanced technology, including CNC machining, is often employed to ensure precision in forming parts like the vending machine body and internal mechanisms.
For B2B buyers, it is crucial to understand the forming techniques used, as they directly impact the machine’s durability and functionality. Inquire about the machinery and technology utilized in this phase to assess the supplier’s capability to produce high-quality components.
3. Assembly
Once the individual parts are formed, the assembly process begins. This phase includes integrating mechanical, electronic, and software components. Each machine is assembled under strict operational procedures to ensure that all elements fit together seamlessly.
Key techniques in assembly may include automated assembly lines and manual assembly, depending on the complexity of the machine. Buyers should look for suppliers who implement lean manufacturing principles to reduce waste and improve efficiency during assembly.
4. Finishing
The final stage of manufacturing is finishing, which involves painting, coating, and adding any branding elements to the vending machines. This not only enhances the aesthetic appeal but also provides additional protection against wear and tear. Powder coating is a common finishing method that offers durability and resistance to corrosion.
At this stage, B2B buyers should request details about the finishing processes and materials used, as these can affect the machine’s lifespan and maintenance requirements.
Quality Assurance
Quality assurance (QA) is a critical aspect of the manufacturing process, ensuring that each machine meets industry standards and customer expectations.
International Standards
For global operations, compliance with ISO 9001 is essential. This certification indicates that the manufacturer adheres to quality management principles, which can significantly reduce risks associated with product failures. Additionally, CE marking is necessary for vending machines sold in Europe, signifying compliance with health, safety, and environmental protection standards.
Industry-Specific Standards
In regions like the Middle East and Africa, local regulations may also dictate specific quality benchmarks. For instance, products may require certification from local authorities to ensure that they meet regional safety and operational standards.
QC Checkpoints
Quality control throughout the manufacturing process is typically segmented into several checkpoints:
-
Incoming Quality Control (IQC): This involves inspecting raw materials and components upon arrival at the manufacturing facility. It ensures that all incoming materials meet predefined specifications.
-
In-Process Quality Control (IPQC): Continuous checks during the manufacturing process monitor the quality of production. This includes real-time assessments of assembly and forming processes.
-
Final Quality Control (FQC): Before shipment, finished machines undergo rigorous testing to ensure they function correctly and meet all quality standards. This may include operational tests and safety inspections.
Common Testing Methods
Testing methods for vending machines may include:
- Functional testing: Ensures all mechanical and electronic components work as intended.
- Stress testing: Simulates extreme conditions to test durability.
- Safety testing: Checks for compliance with safety standards, particularly for electrical components.
Verifying Supplier Quality Control
B2B buyers must take proactive steps to verify the quality control measures of potential suppliers. Here are some actionable strategies:
-
Supplier Audits: Conduct thorough audits of suppliers’ manufacturing facilities to assess their processes and adherence to quality standards. This may include reviewing their quality management systems and practices.
-
Request Reports: Ask suppliers for quality assurance reports, including data on defect rates and customer feedback. This information can provide insights into the reliability of the supplier’s products.
-
Third-Party Inspections: Engage third-party inspection agencies to conduct independent assessments of the manufacturing process and final products. This adds an additional layer of verification to ensure compliance with international standards.
-
Certifications and Compliance: Verify that suppliers possess relevant certifications (e.g., ISO 9001, CE marking) and maintain a transparent approach to regulatory compliance.
Conclusion
Understanding the manufacturing processes and quality assurance measures for omny vending machines equips international B2B buyers with the knowledge necessary to make informed purchasing decisions. By focusing on material preparation, forming, assembly, and finishing, as well as robust quality control practices, buyers can ensure they partner with reliable suppliers who deliver high-quality products tailored to their market needs.
Related Video: Most Satisfying Factory Production Processes And Heavy-Duty Factory Machines!
Comprehensive Cost and Pricing Analysis for omny vending machines Sourcing
Understanding the cost structure and pricing of omny vending machines is essential for international B2B buyers, especially those from Africa, South America, the Middle East, and Europe. This analysis will delve into the various components of costs, factors influencing prices, and practical tips for negotiation and purchasing.
Cost Components of omny Vending Machines
-
Materials: The primary cost driver for vending machines is the raw materials used in production, including metals, plastics, and electronic components. High-quality materials may incur higher initial costs but can lead to lower maintenance and replacement rates.
-
Labor: Labor costs encompass the wages of workers involved in manufacturing, assembly, and quality control. Depending on the region, labor costs can vary significantly. For instance, labor in Europe may be more expensive than in Africa or South America.
-
Manufacturing Overhead: This includes indirect costs associated with the production process, such as utilities, rent, and administrative expenses. Efficient manufacturing processes can help minimize these overhead costs.
-
Tooling: Custom tooling is often required for specific machine designs or features, which can be a substantial upfront investment. Buyers should consider whether the supplier has existing tooling that can accommodate their needs to reduce costs.
-
Quality Control (QC): Implementing rigorous QC processes ensures that the machines meet safety and performance standards, which may involve additional costs. However, investing in quality can reduce long-term expenses related to defects and returns.
-
Logistics: Shipping and handling costs can vary based on the destination, weight, and dimensions of the vending machines. Buyers should be aware of these costs, especially when importing to regions with strict import regulations.
-
Margin: Suppliers typically build a profit margin into their pricing, which can vary based on competition and market demand. Understanding the supplier’s pricing strategy can help buyers negotiate better terms.
Price Influencers
Several factors can significantly influence the pricing of omny vending machines:
-
Volume/MOQ (Minimum Order Quantity): Larger orders often lead to reduced per-unit costs due to economies of scale. Buyers should assess their projected demand to leverage bulk purchasing benefits.
-
Specifications/Customization: Custom features or specific design requests can increase production costs. It is essential to clarify which specifications are crucial for your market to avoid unnecessary expenses.
-
Materials and Quality Certifications: Higher quality materials and compliance with international standards (such as ISO certifications) can lead to increased costs but ensure reliability and safety, which can enhance customer satisfaction.
-
Supplier Factors: The reputation, reliability, and negotiation flexibility of the supplier can affect pricing. Established suppliers may have higher costs due to their quality assurance processes, but they may also offer better service and reliability.
-
Incoterms: Understanding the terms of shipment, such as FOB (Free on Board) or CIF (Cost, Insurance, and Freight), is crucial for determining total landed costs. Different Incoterms can shift responsibilities and costs between buyers and sellers.
Buyer Tips
-
Negotiation: Engage in open discussions with suppliers about pricing and terms. Leverage your purchasing volume to negotiate better rates, especially if you can commit to long-term contracts.
-
Cost-Efficiency: Analyze the Total Cost of Ownership (TCO), which includes not only the purchase price but also maintenance, operation, and disposal costs. This holistic view can help identify the best value options.
-
Pricing Nuances for International Buyers: Be aware of currency fluctuations, import duties, and taxes that may affect the final cost. Establish relationships with local agents or distributors who understand the market dynamics.
-
Supplier Assessment: Conduct thorough due diligence on potential suppliers. Look for those with proven track records, transparent pricing, and strong after-sales support.
-
Disclaimer for Indicative Prices: Always request detailed quotations and be aware that prices can vary based on the factors discussed. Indicative prices should be treated as a starting point for negotiations.
By understanding these components and leveraging this knowledge, international B2B buyers can make informed decisions that optimize their sourcing strategies for omny vending machines.
Spotlight on Potential omny vending machines Manufacturers and Suppliers
This section offers a look at a few manufacturers active in the ‘omny vending machines’ market. This is a representative sample for illustrative purposes; B2B buyers must conduct their own extensive due diligence before any engagement. Information is synthesized from public sources and general industry knowledge.
Essential Technical Properties and Trade Terminology for omny vending machines
Key Technical Properties of Omny Vending Machines
Understanding the technical specifications of omny vending machines is crucial for international B2B buyers seeking to optimize their investment. Here are several critical properties that should be considered:
-
Material Grade
– Definition: This refers to the quality of materials used in constructing the vending machine, such as stainless steel or high-grade plastics.
– B2B Importance: Higher-grade materials enhance durability and resistance to wear and tear, which is vital for machines placed in high-traffic areas. Opting for robust materials can reduce maintenance costs and extend the machine’s lifespan. -
Tolerance Levels
– Definition: Tolerance indicates the permissible limit of variation in a machine’s dimensions or performance parameters.
– B2B Importance: Accurate tolerances ensure that components fit together seamlessly, which is essential for reliable operation and minimizing breakdowns. Understanding tolerance levels can help buyers select machines that meet their operational standards. -
Power Consumption
– Definition: This specifies the amount of electrical power the vending machine uses during operation.
– B2B Importance: Machines with lower power consumption can significantly reduce operating costs, particularly in regions where electricity prices are high. Buyers should look for energy-efficient models that comply with local energy regulations. -
Capacity
– Definition: Capacity refers to the volume of products the machine can hold, typically measured in number of items or weight.
– B2B Importance: Selecting a machine with the right capacity is crucial for meeting customer demand without frequent restocking. This is particularly important in busy locations where high turnover is expected. -
User Interface
– Definition: This encompasses the design and functionality of the machine’s touchscreen or keypad, which customers use to select products.
– B2B Importance: A user-friendly interface can enhance customer experience and increase sales. Machines with intuitive navigation and multiple language options can cater to a broader audience. -
Connectivity Features
– Definition: This includes options for cashless payments, remote monitoring, and inventory management systems.
– B2B Importance: Advanced connectivity features enable real-time data tracking, which helps businesses optimize inventory and respond quickly to consumer trends. Adopting modern payment solutions can also appeal to tech-savvy customers.
Common Trade Terms in the Vending Machine Industry
Familiarity with industry terminology is essential for effective communication and negotiation in the vending machine sector. Here are some key terms:
-
OEM (Original Equipment Manufacturer)
– Definition: An OEM produces parts or equipment that may be marketed by another manufacturer.
– Importance: Understanding OEM relationships can help buyers identify reliable suppliers who provide high-quality components for their vending machines. -
MOQ (Minimum Order Quantity)
– Definition: The smallest quantity of a product that a supplier is willing to sell.
– Importance: Knowing the MOQ is essential for budgeting and inventory planning, especially for businesses in regions with fluctuating demand. -
RFQ (Request for Quotation)
– Definition: A document sent to suppliers to request pricing and availability of specific products or services.
– Importance: An RFQ is a critical step in the procurement process, enabling buyers to compare costs and terms from multiple suppliers efficiently. -
Incoterms (International Commercial Terms)
– Definition: A series of pre-defined commercial terms published by the International Chamber of Commerce (ICC) that outline responsibilities of buyers and sellers in international transactions.
– Importance: Understanding Incoterms can help buyers clarify shipping responsibilities, risks, and costs, which is especially important for international transactions. -
Lead Time
– Definition: The time taken from placing an order to delivery.
– Importance: Knowing the lead time helps businesses plan their inventory and manage customer expectations, particularly in competitive markets.
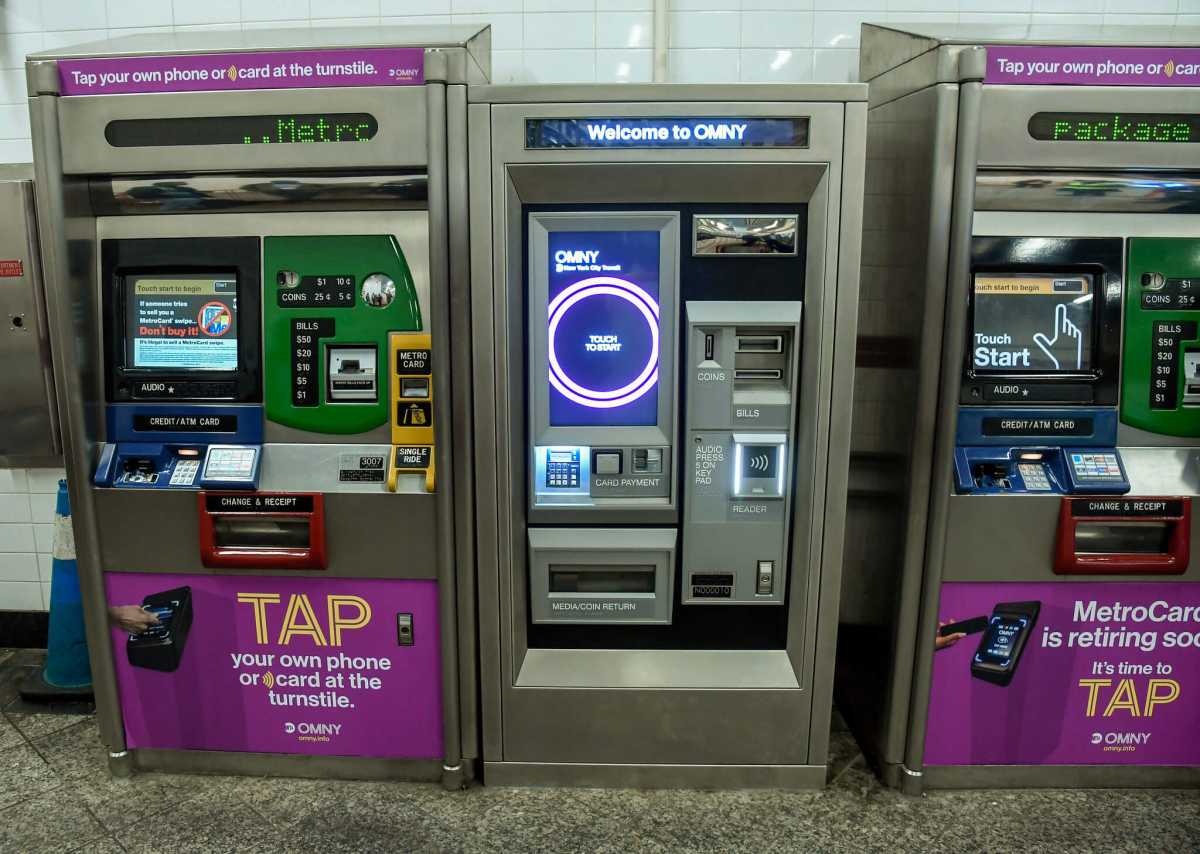
Illustrative Image (Source: Google Search)
- Warranty
– Definition: A guarantee provided by the manufacturer regarding the condition of the product, covering repairs or replacements for a specified period.
– Importance: A comprehensive warranty can protect buyers from unexpected costs and is a key factor in evaluating supplier reliability.
By understanding these technical properties and trade terms, international B2B buyers can make informed decisions when sourcing omny vending machines, ensuring they choose the right products for their specific market needs.
Navigating Market Dynamics, Sourcing Trends, and Sustainability in the omny vending machines Sector
Market Overview & Key Trends
The global vending machine market is experiencing significant growth, driven by urbanization, changing consumer habits, and advancements in technology. As international B2B buyers from regions like Africa, South America, the Middle East, and Europe look to capitalize on this trend, understanding the current and emerging dynamics is crucial. A notable driver is the increasing demand for convenience, which has led to the rise of omny vending machines—a new breed of machines that offer a wider range of products including healthy snacks, beverages, and even electronics.
B2B technology trends are also influencing the market. The integration of cashless payment systems, IoT connectivity, and data analytics is transforming traditional vending operations. For example, contactless payments have surged, particularly post-pandemic, as consumers prioritize hygiene. Moreover, the adoption of smart vending solutions enables real-time inventory management, allowing businesses to optimize stock levels based on consumer behavior patterns. This data-driven approach not only enhances operational efficiency but also improves customer satisfaction.
Additionally, sustainability is becoming a focal point. Buyers are increasingly favoring suppliers who demonstrate commitment to eco-friendly practices. This includes sourcing from local suppliers to reduce transportation emissions and investing in energy-efficient machines. Understanding these trends is vital for B2B buyers aiming to remain competitive in a rapidly evolving market landscape.
Sustainability & Ethical Sourcing in B2B
In the context of omny vending machines, sustainability and ethical sourcing are no longer optional; they are essential components of a successful business strategy. The environmental impact of vending machines is significant, primarily due to energy consumption and waste generation. By prioritizing sustainability, businesses can mitigate these impacts while also appealing to a growing base of eco-conscious consumers.
Ethical supply chains are critical for fostering trust and loyalty among customers. B2B buyers should seek suppliers who adhere to ethical sourcing standards, ensuring that products are produced and distributed responsibly. This includes verifying that suppliers use green certifications and materials, such as biodegradable packaging and sustainably sourced ingredients. Additionally, engaging with suppliers who have a transparent sourcing process can enhance brand reputation and consumer confidence.
Investing in green technologies—like energy-efficient vending machines that utilize renewable energy sources—can further reduce environmental footprints. By integrating these practices, international buyers not only contribute to global sustainability efforts but also position themselves as leaders in responsible business practices.
Brief Evolution/History
The evolution of vending machines has been marked by technological advancements and shifts in consumer preferences. Initially, vending machines offered basic snacks and beverages, but the introduction of digital technology in the late 20th century set the stage for a revolution. The emergence of smart vending machines in the 21st century, which feature touchscreens and cashless payment options, transformed the industry by enhancing user experience.
Today, omny vending machines are at the forefront, combining cutting-edge technology with a diverse product offering. They cater to a wide range of consumer needs—from healthy food options to electronic gadgets—reflecting the changing landscape of consumer behavior. As international B2B buyers navigate this sector, understanding its evolution helps in making informed sourcing decisions that align with market trends and consumer expectations.
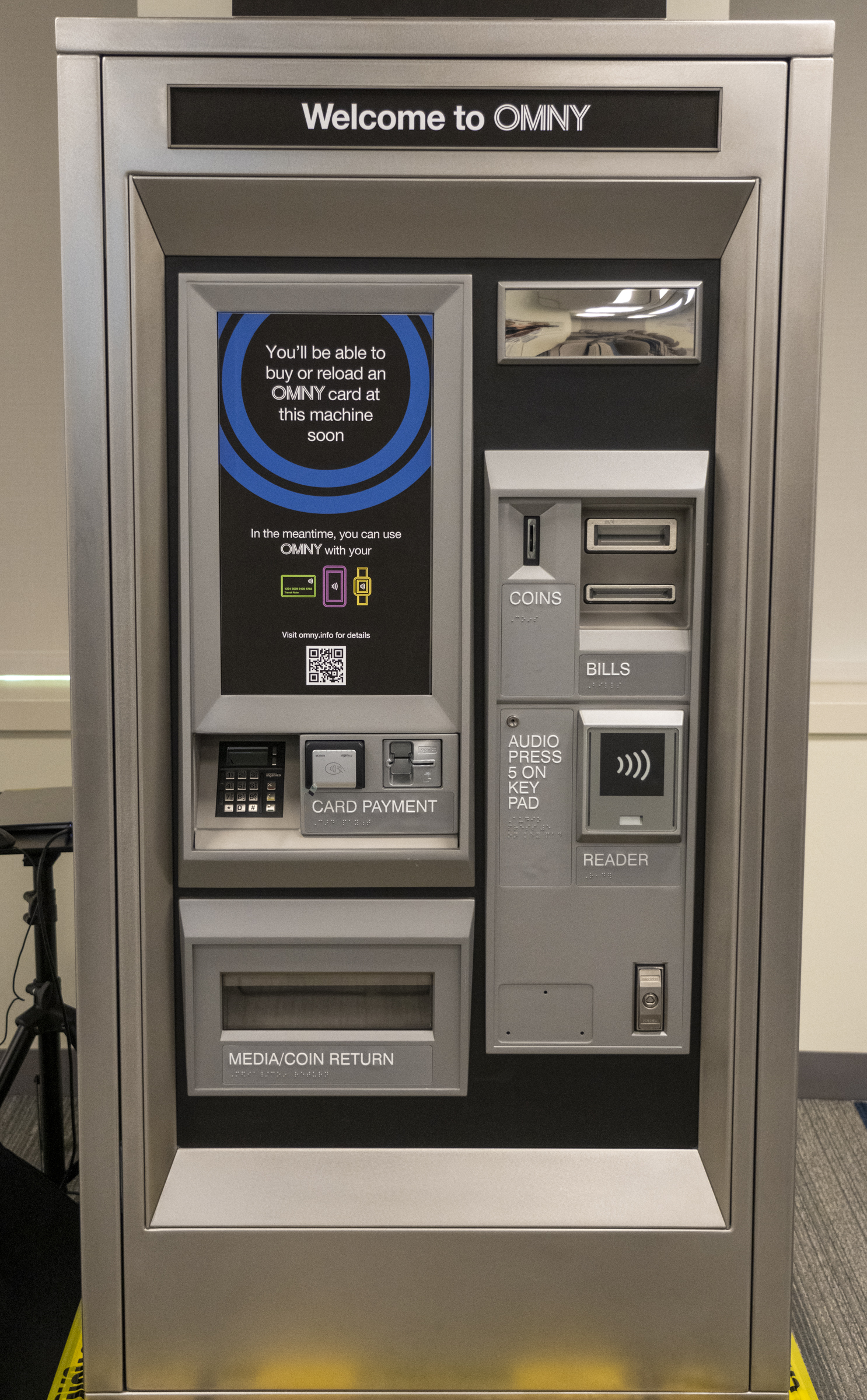
Illustrative Image (Source: Google Search)
Frequently Asked Questions (FAQs) for B2B Buyers of omny vending machines
-
What criteria should I use to vet suppliers of omny vending machines?
When vetting suppliers, prioritize their reliability, industry experience, and customer reviews. Investigate their track record in delivering quality products on time and their ability to respond to issues effectively. Check for certifications relevant to vending machines, such as ISO compliance or safety standards. Additionally, consider their financial stability and capacity to handle international trade complexities, including customs regulations and import/export laws pertinent to your region, especially in Africa, South America, the Middle East, and Europe. -
Can omny vending machines be customized to fit my business needs?
Yes, many suppliers offer customization options for omny vending machines. This can include altering the machine’s size, design, or product offerings to match your specific market demands. When discussing customization, ensure you communicate your target audience preferences and any legal requirements in your region. Request samples or prototypes if possible, and verify the supplier’s ability to meet your customization needs within the stipulated timeline. -
What are the minimum order quantities (MOQ) and lead times for omny vending machines?
MOQs for omny vending machines vary by supplier and can range from a single unit to several dozen. It’s essential to clarify these terms before initiating any orders. Lead times can also differ based on the supplier’s production capacity, customization requests, and shipping logistics. Typically, expect lead times to range from a few weeks to several months, particularly for international shipments. Confirm these details upfront to align your inventory needs with supplier capabilities. -
What payment methods are commonly accepted when sourcing omny vending machines?
Most suppliers accept various payment methods, including bank transfers, credit cards, and letters of credit, which are particularly beneficial for international transactions. Ensure that you understand the payment terms, such as deposits, payment upon delivery, or installment plans. Negotiate terms that provide you with adequate protection against potential supply chain disruptions, especially if you are new to international trade. -
How can I ensure quality assurance (QA) and compliance with certifications for omny vending machines?
Request documentation from suppliers that verifies compliance with industry standards and local regulations. Quality assurance processes should include product testing and certifications, such as CE marking in Europe or other relevant local certifications. Establish a quality control plan that includes regular inspections and audits of both the manufacturing process and the final product before shipment to minimize risks associated with defects. -
What logistics considerations should I be aware of when importing omny vending machines?
Logistics play a critical role in the successful import of omny vending machines. Ensure you understand shipping costs, insurance, customs duties, and potential delays at borders. Work with suppliers who have experience in international shipping and can assist with documentation required for customs clearance. Additionally, consider the local infrastructure in your target market to ensure timely delivery and installation of the machines. -
How can disputes with suppliers be effectively managed?
To manage disputes, establish clear contracts that outline terms of service, delivery schedules, and liability clauses. Include mechanisms for conflict resolution, such as mediation or arbitration, to address issues amicably. Maintain open communication with suppliers to resolve misunderstandings promptly. If disputes arise, document all interactions and transactions, as this information can be crucial for negotiations or legal proceedings. -
What are the ongoing support options available after purchasing omny vending machines?
After purchasing, inquire about the supplier’s support services, which may include maintenance, repair services, and technical assistance. A good supplier will offer training for your staff on machine operation and troubleshooting. Additionally, check if they provide warranty coverage and how claims are processed. Establishing a strong post-purchase relationship can help you address any issues efficiently and ensure your vending machines operate smoothly.
Strategic Sourcing Conclusion and Outlook for omny vending machines
The journey toward successful strategic sourcing for omny vending machines is multifaceted, requiring a keen understanding of both market dynamics and supplier relationships. Key takeaways for international B2B buyers include the importance of establishing robust partnerships with reliable suppliers, which can lead to cost efficiencies and improved product offerings. Furthermore, navigating legal requirements is critical to ensure compliance and protect your business interests in diverse markets.
As the vending machine landscape evolves, particularly in regions like Africa, South America, the Middle East, and Europe, the demand for innovative and tailored solutions continues to grow. Strategic sourcing not only enhances operational efficiency but also empowers businesses to respond swiftly to changing consumer preferences and market trends.
Looking ahead, the potential for growth in the vending industry is significant. Buyers are encouraged to leverage this moment to refine their sourcing strategies, engage with forward-thinking suppliers, and embrace technology-driven solutions. The future of vending is bright for those who prioritize strategic sourcing—positioning their businesses for long-term success in a competitive marketplace. Engage now to capitalize on these opportunities and drive your business forward.