Your Ultimate Guide to Sourcing Oldest Vending Machine
Guide to Oldest Vending Machine
- Introduction: Navigating the Global Market for oldest vending machine
- Understanding oldest vending machine Types and Variations
- Key Industrial Applications of oldest vending machine
- Strategic Material Selection Guide for oldest vending machine
- In-depth Look: Manufacturing Processes and Quality Assurance for oldest vending machine
- Comprehensive Cost and Pricing Analysis for oldest vending machine Sourcing
- Spotlight on Potential oldest vending machine Manufacturers and Suppliers
- Essential Technical Properties and Trade Terminology for oldest vending machine
- Navigating Market Dynamics, Sourcing Trends, and Sustainability in the oldest vending machine Sector
- Frequently Asked Questions (FAQs) for B2B Buyers of oldest vending machine
- Strategic Sourcing Conclusion and Outlook for oldest vending machine
Introduction: Navigating the Global Market for oldest vending machine
Navigating the global market for the oldest vending machines presents a unique opportunity for international B2B buyers, particularly in regions such as Africa, South America, the Middle East, and Europe. The historical significance and evolution of vending machines reflect changing consumer behaviors, making them not only a nostalgic choice but also a viable business investment. As buyers seek to diversify their product offerings, understanding the various types of vending machines available—ranging from traditional coin-operated models to modern, tech-savvy solutions—is crucial.
This guide aims to equip buyers with comprehensive insights into the oldest vending machines, covering essential aspects such as types, materials, manufacturing processes, quality control measures, and supplier options. Additionally, we will delve into cost considerations and market trends, providing a holistic view of the vending machine landscape.
By addressing frequently asked questions and common challenges faced by buyers, this resource empowers decision-makers to make informed sourcing choices. Whether you are exploring vending machines for educational institutions, hospitality venues, or retail spaces, the information presented will help you identify reliable suppliers and negotiate effectively. Ultimately, this guide serves as a strategic tool to enhance your procurement process and ensure a successful investment in the timeless vending machine industry.
Understanding oldest vending machine Types and Variations
Type Name | Key Distinguishing Features | Primary B2B Applications | Brief Pros & Cons for Buyers |
---|---|---|---|
Mechanical Coin-Operated | Simple mechanism, requires manual interaction | Hospitality, retail, public spaces | Pros: Low maintenance, straightforward operation. Cons: Limited product range and less user engagement. |
Electronic Vending | Automated, programmable with digital displays | Office environments, schools, hospitals | Pros: Versatile product selection, real-time inventory tracking. Cons: Higher initial investment, potential technical issues. |
Refrigerated Vending | Temperature-controlled for perishable goods | Food service, convenience stores | Pros: Expands product offerings to include fresh items. Cons: Increased energy costs and maintenance complexity. |
Combination Vending | Offers snacks and beverages in one unit | Cafeterias, gyms, airports | Pros: Space-efficient, caters to diverse consumer preferences. Cons: Can be more expensive to stock and maintain. |
Specialty Vending | Focused on niche markets (e.g., electronics) | Tech stores, airports, event venues | Pros: Targets specific customer needs, unique offerings. Cons: Limited customer base and potentially higher costs. |
Mechanical Coin-Operated Vending Machines
Mechanical coin-operated vending machines are among the oldest vending types. They operate through a simple mechanism that requires manual interaction, typically involving inserting coins to dispense items. These machines are commonly found in hospitality settings, retail locations, and public spaces. B2B buyers should consider their low maintenance needs and straightforward operation; however, the limited product range may restrict consumer engagement and sales opportunities.
Electronic Vending Machines
Electronic vending machines have revolutionized the vending industry by integrating advanced technology. They feature programmable systems with digital displays that allow for a wide variety of products and real-time inventory tracking. These machines are ideal for office environments, schools, and hospitals, where diverse product offerings are essential. While their versatility and potential for increased sales are significant advantages, buyers should be prepared for a higher initial investment and possible technical challenges.
Refrigerated Vending Machines
Refrigerated vending machines cater specifically to perishable goods, making them an excellent choice for food service businesses and convenience stores. These machines maintain a controlled temperature, allowing for the sale of fresh items such as sandwiches, salads, and beverages. Their ability to expand product offerings significantly enhances revenue potential. However, B2B buyers must account for increased energy costs and the complexity of maintenance.
Combination Vending Machines
Combination vending machines provide a space-efficient solution by offering both snacks and beverages in one unit. This versatility makes them particularly suitable for cafeterias, gyms, and airports, where customer preferences can vary widely. The primary advantage is the ability to cater to a broader audience, potentially increasing sales. However, buyers should be aware that stocking and maintaining these machines can be more expensive due to their dual offerings.
Specialty Vending Machines
Specialty vending machines focus on niche markets, such as electronics or health products, and are often found in tech stores, airports, and event venues. These machines target specific customer needs, providing unique offerings that can attract a loyal customer base. While they can be lucrative, the limited customer base may pose a challenge for B2B buyers, who should evaluate the demand and potential costs associated with stocking these specialized machines.
Related Video: AI, Machine Learning, Deep Learning and Generative AI Explained
Key Industrial Applications of oldest vending machine
Industry/Sector | Specific Application of Oldest Vending Machine | Value/Benefit for the Business | Key Sourcing Considerations for this Application |
---|---|---|---|
Hospitality | Guest Service Enhancements | Provides 24/7 access to snacks and beverages, enhancing guest satisfaction | Machine durability, ease of restocking, payment options |
Education | Campus Convenience Services | Offers students quick access to food and drinks, saving time between classes | Size and placement, product variety, payment integration |
Healthcare | Patient and Staff Refreshment | Ensures access to nutritious snacks and drinks, promoting health and wellness | Hygiene standards, product selection, machine reliability |
Corporate Offices | Employee Engagement Solutions | Increases morale by providing convenient snack options, fostering a positive work environment | Capacity, energy efficiency, customizable options |
Transportation Hubs | Traveler Convenience | Offers quick access to refreshments, enhancing the travel experience | Location planning, product rotation, payment technology |
Hospitality
In the hospitality sector, the oldest vending machine serves as a valuable asset for enhancing guest services. Hotels and resorts can place these machines in lobbies or common areas to provide guests with 24/7 access to snacks and beverages. This not only improves guest satisfaction by meeting their immediate needs but also reduces the workload on staff during off-hours. Buyers in this sector should consider the machine’s durability, ease of restocking, and the variety of payment options available to accommodate diverse guest preferences.
Education
Educational institutions can leverage the oldest vending machine to improve campus convenience services. By placing these machines in high-traffic areas, schools and universities can offer students quick access to food and drinks, saving valuable time between classes. This application addresses the common issue of hunger during busy academic schedules. International buyers should focus on the machine’s size and placement to ensure optimal accessibility, as well as its ability to integrate various payment methods, including cashless options.
Healthcare
In healthcare settings, the oldest vending machine plays a crucial role in providing patient and staff refreshment options. Hospitals and clinics can use these machines to ensure access to nutritious snacks and beverages, promoting health and wellness among patients and staff alike. This application is particularly beneficial in environments where traditional dining options may be limited or unavailable. Buyers in this sector must prioritize hygiene standards, the selection of healthy products, and the reliability of the vending machines to maintain service quality.
Corporate Offices
Corporate offices can utilize the oldest vending machine as an employee engagement solution. By offering convenient snack options, companies can increase employee morale and foster a positive work environment. This application not only meets the needs of employees during busy workdays but also encourages social interactions in break areas. When sourcing these machines, businesses should consider their capacity, energy efficiency, and the availability of customizable options to fit their specific workplace culture.
Transportation Hubs
Transportation hubs, such as airports and train stations, can enhance traveler convenience through the deployment of the oldest vending machine. These machines provide quick access to refreshments, significantly improving the overall travel experience. By strategically placing vending machines in high-traffic areas, operators can cater to the needs of busy travelers. Key considerations for international buyers include location planning to optimize visibility and accessibility, product rotation to ensure freshness, and the implementation of advanced payment technologies to accommodate diverse customer preferences.
Related Video: Kooler Ice Vending Machines – IM600XL vs. IM1000
Strategic Material Selection Guide for oldest vending machine
When selecting materials for the oldest vending machine, it is crucial to consider the specific requirements of the application, including durability, cost, and environmental factors. Below is an analysis of four common materials used in vending machine construction, focusing on their properties, advantages, disadvantages, and considerations for international B2B buyers.
1. Stainless Steel
Key Properties: Stainless steel is known for its excellent corrosion resistance, high strength, and ability to withstand high temperatures and pressures. It typically has a temperature rating of up to 800°F (427°C) and can handle pressures exceeding 150 psi, making it suitable for various environments.
Pros & Cons: The primary advantage of stainless steel is its durability and resistance to rust and corrosion, which is essential for machines exposed to moisture and food products. However, it is relatively expensive compared to other materials and can be more complex to manufacture due to its hardness.
Impact on Application: Stainless steel is compatible with various media, including water, soft drinks, and snacks, making it ideal for vending machines. Its hygienic properties also make it suitable for food applications.
Considerations for International Buyers: Buyers in Africa, South America, the Middle East, and Europe should ensure compliance with local health and safety standards. Common standards such as ASTM A240 for stainless steel should be considered, along with the certification of food-grade materials.
2. Carbon Steel
Key Properties: Carbon steel is strong and cost-effective, with a typical tensile strength ranging from 400 to 600 MPa. However, it lacks inherent corrosion resistance and requires protective coatings.
Pros & Cons: The primary advantage of carbon steel is its low cost and high strength, making it suitable for structural components of vending machines. However, its susceptibility to corrosion can lead to maintenance issues, especially in humid environments.
Impact on Application: Carbon steel is suitable for non-corrosive fluids and dry goods but may not be ideal for vending machines dispensing beverages or perishable items without proper protective coatings.
Considerations for International Buyers: Buyers should be aware of the need for protective coatings to prevent corrosion and should comply with standards like ASTM A36 for structural steel. Additionally, local regulations regarding food safety and material certifications should be considered.
3. Aluminum
Key Properties: Aluminum is lightweight, has good corrosion resistance, and can withstand temperatures up to 400°F (204°C). It is also easy to fabricate and weld.
Pros & Cons: The main advantage of aluminum is its lightweight nature, which reduces shipping costs and makes installation easier. However, it is less durable than stainless steel and can be prone to denting and scratching.
Impact on Application: Aluminum is suitable for vending machines that require lightweight components, such as panels and frames. Its corrosion resistance makes it a good choice for machines located in humid environments.
Considerations for International Buyers: International buyers should consider the availability of aluminum grades that meet specific strength and corrosion resistance requirements. Compliance with standards such as ASTM B221 for aluminum extrusions is also essential.
4. Plastic (Polycarbonate)
Key Properties: Polycarbonate is a strong, impact-resistant plastic that can withstand temperatures up to 240°F (116°C). It is lightweight and has excellent clarity, making it ideal for transparent panels.
Pros & Cons: The primary advantage of polycarbonate is its impact resistance and lightweight nature, making it suitable for front panels and display areas. However, it may not be suitable for high-temperature applications and can be prone to scratching.
Impact on Application: Polycarbonate is ideal for vending machines that require visibility of products, such as snack or beverage dispensers. It is also resistant to many chemicals, making it versatile for various applications.
Considerations for International Buyers: Buyers should ensure that the polycarbonate used is food-safe and complies with relevant standards, such as FDA regulations for food contact materials. Understanding local regulations regarding plastic use in vending machines is also crucial.
Material | Typical Use Case for oldest vending machine | Key Advantage | Key Disadvantage/Limitation | Relative Cost (Low/Med/High) |
---|---|---|---|---|
Stainless Steel | Structural and exterior components for durability | Excellent corrosion resistance | Higher cost, complex manufacturing | High |
Carbon Steel | Structural components for non-corrosive applications | Cost-effective, high strength | Susceptible to corrosion without coatings | Low |
Aluminum | Lightweight panels and frames for easy installation | Lightweight, good corrosion resistance | Less durable than stainless steel | Med |
Plastic (Polycarbonate) | Transparent panels and displays for visibility | Impact-resistant, lightweight | Prone to scratching, limited temperature range | Med |
In-depth Look: Manufacturing Processes and Quality Assurance for oldest vending machine
Manufacturing Processes for the Oldest Vending Machine
The manufacturing of the oldest vending machines involves several critical stages that ensure the product is robust, reliable, and meets consumer expectations. Below are the main stages of manufacturing, along with key techniques used in the process.
1. Material Preparation
Material selection is fundamental in vending machine manufacturing. Common materials include:
- Metal: Steel and aluminum are often used for the machine’s chassis and panels due to their durability and corrosion resistance.
- Plastic: High-density polyethylene (HDPE) and polycarbonate are used for transparent panels and internal components.
- Electronic Components: Various electronic parts such as sensors, motors, and control systems are sourced from specialized suppliers.
Key Techniques:
– Material Sourcing: Engaging with certified suppliers to ensure materials meet international standards.
– Quality Inspection: Incoming Quality Control (IQC) processes are established to assess the quality of materials before they enter the production line.
2. Forming
The forming stage is where raw materials are shaped into the components of the vending machine. This stage includes:
- Cutting: Metal sheets are cut to size using laser cutting or waterjet cutting technologies.
- Bending: Using CNC bending machines, metal parts are shaped to form the machine’s structure.
- Injection Molding: Plastic parts are produced through injection molding techniques for precision and uniformity.
Key Techniques:
– CNC Machining: This technology enhances precision in forming metal parts, leading to tighter tolerances and better fit during assembly.
– Robotic Automation: In some advanced manufacturing settings, robotic arms are used for consistent and efficient handling of materials.
3. Assembly
The assembly stage involves putting together the various components of the vending machine. Key steps include:
- Component Assembly: Parts such as the chassis, doors, and electronic systems are assembled in a systematic manner.
- Wiring and Integration: Electrical components are wired according to schematics, ensuring proper functionality.
- Software Installation: If applicable, software that operates the vending machine is installed and configured.
Key Techniques:
– Lean Manufacturing: Employing lean principles to minimize waste and enhance efficiency during assembly.
– Modular Assembly: Using pre-assembled modules can significantly reduce assembly time and complexity.
4. Finishing
The finishing stage is crucial for both aesthetic appeal and protection against environmental factors. This includes:
- Painting and Coating: Machines are often powder-coated or painted to enhance durability and appearance.
- Quality Checks: A thorough inspection is conducted to ensure all components are fitted correctly and that the machine operates as intended.
Key Techniques:
– Electrostatic Painting: This method provides a high-quality finish and ensures even coverage.
– Environmental Testing: Machines may undergo tests to assess their performance under various environmental conditions.
Quality Assurance in Vending Machine Manufacturing
Quality assurance (QA) is essential in the manufacturing of vending machines to ensure compliance with international standards and reliability in operation. The following outlines the relevant QA practices.
Relevant International Standards
International standards such as ISO 9001 focus on maintaining quality management systems that enhance customer satisfaction. Other industry-specific standards include:
- CE Marking: Indicates compliance with European safety, health, and environmental protection standards.
- API Standards: Relevant for machines that dispense food and beverages, ensuring safety and hygiene.
Quality Control Checkpoints
Quality control (QC) checkpoints are integral to the manufacturing process:
- Incoming Quality Control (IQC): Inspects raw materials upon arrival to ensure they meet specifications.
- In-Process Quality Control (IPQC): Conducts checks during the manufacturing process to catch defects early.
- Final Quality Control (FQC): A comprehensive inspection of the finished product to verify it meets all specifications.
Common Testing Methods
Testing methods used in the QC process include:
- Functional Testing: Ensures that all operational components work correctly.
- Durability Testing: Assesses the machine’s performance under simulated usage conditions.
- Safety Testing: Verifies compliance with electrical safety standards.
Verifying Supplier Quality Control
For international B2B buyers, verifying the quality control processes of suppliers is crucial. Here are actionable steps to ensure quality:
- Supplier Audits: Conduct on-site audits of manufacturing facilities to assess their quality management systems and processes.
- Request Quality Reports: Ask suppliers for their quality assurance documentation, including past inspection reports and compliance certifications.
- Third-Party Inspections: Engage independent inspection agencies to perform quality checks before shipment.
- Certifications Verification: Validate the supplier’s certifications (ISO, CE, etc.) to ensure they adhere to international standards.
QC and Certification Nuances for International Buyers
B2B buyers from Africa, South America, the Middle East, and Europe should be aware of specific nuances when dealing with quality control and certification:
- Cultural Differences: Understand that manufacturing standards and practices may vary across regions. For example, some regions may prioritize cost over quality, which can impact product reliability.
- Regulatory Compliance: Each region may have different regulatory requirements for vending machines, particularly concerning food safety and electronic devices.
- Language Barriers: Ensure that quality documentation is available in languages that your team understands to avoid misinterpretations.
Conclusion
Investing in high-quality vending machines requires a keen understanding of the manufacturing processes and quality assurance practices involved. By focusing on material preparation, forming, assembly, and finishing while adhering to international quality standards, B2B buyers can ensure they source reliable and durable products. Additionally, verifying supplier QC through audits, reports, and third-party inspections is essential to mitigate risks and ensure compliance with regional standards. This knowledge empowers buyers to make informed decisions and foster successful international partnerships.
Related Video: Amazing scenes。Top 6 Most Popular Factory Manufacturing Videos in China
Comprehensive Cost and Pricing Analysis for oldest vending machine Sourcing
When considering the sourcing of the oldest vending machines, B2B buyers need to navigate a complex landscape of cost components and pricing influencers. Understanding these elements is crucial for making informed purchasing decisions that align with business objectives.
Cost Components
-
Materials: The choice of materials directly impacts the cost. Traditional vending machines may use metals and glass, while modern alternatives might incorporate plastics and electronics. Buyers should evaluate the trade-offs between cost and durability.
-
Labor: Labor costs vary significantly by region. Countries with lower labor costs might provide more competitive pricing but could compromise on craftsmanship. It’s important to assess the skill level of the workforce involved in the manufacturing process.
-
Manufacturing Overhead: This includes costs associated with utilities, rent, and administrative expenses. Understanding how these overheads are allocated can help buyers gauge the pricing structure of suppliers.
-
Tooling: Tooling costs can be substantial, especially for custom designs. Buyers should consider whether to invest in custom tooling for unique specifications or to opt for standard designs that may incur lower costs.
-
Quality Control (QC): Implementing robust QC processes ensures product reliability but adds to costs. Buyers should inquire about the QC measures suppliers have in place to ensure product quality.
-
Logistics: Shipping costs can vary widely based on distance, shipping method, and Incoterms. Buyers should factor in these logistics costs when evaluating total pricing.
-
Margin: Suppliers will typically add a margin to cover their costs and profit. Understanding market norms for margins in the vending machine industry can aid in negotiations.
Price Influencers
-
Volume/MOQ: Minimum order quantities (MOQ) significantly influence pricing. Ordering larger volumes often leads to lower per-unit costs, which can be a strategic move for larger businesses.
-
Specifications and Customization: Customized machines tailored to specific needs can lead to higher costs. Buyers should weigh the benefits of customization against potential price increases.
-
Materials and Quality: Higher-quality materials and certifications can increase costs. Buyers should consider whether the additional investment in quality aligns with their long-term operational goals.
-
Supplier Factors: The reputation and reliability of the supplier can influence pricing. Established suppliers may charge a premium for their proven track record, while newer companies might offer lower prices to gain market share.
-
Incoterms: The chosen Incoterm can have a substantial impact on the final price. Understanding the responsibilities for shipping, insurance, and tariffs is essential for accurate cost estimation.
Buyer Tips
-
Negotiation: Approach negotiations with clear objectives. Understanding the cost structure allows for more effective discussions with suppliers.
-
Cost-Efficiency: Consider the total cost of ownership (TCO) rather than just the purchase price. This includes maintenance, operational costs, and potential downtime.
-
Pricing Nuances: International buyers should be aware of currency fluctuations and their impact on pricing. Establishing contracts in stable currencies can mitigate risks.
-
Research: Conduct thorough market research to understand pricing trends and benchmarks in different regions, particularly in Africa, South America, the Middle East, and Europe.
-
Local Regulations: Be mindful of local regulations and standards that may affect the sourcing of vending machines. Compliance can lead to additional costs or delays.
Disclaimer
The prices mentioned in this analysis are indicative and subject to change based on market conditions, supplier negotiations, and specific project requirements. It is advisable for buyers to conduct detailed discussions with suppliers to obtain accurate and current pricing information.
Spotlight on Potential oldest vending machine Manufacturers and Suppliers
This section offers a look at a few manufacturers active in the ‘oldest vending machine’ market. This is a representative sample for illustrative purposes; B2B buyers must conduct their own extensive due diligence before any engagement. Information is synthesized from public sources and general industry knowledge.
Essential Technical Properties and Trade Terminology for oldest vending machine
To successfully navigate the procurement process for the oldest vending machines, international B2B buyers must understand key technical properties and industry terminology. This knowledge is crucial for making informed purchasing decisions and ensuring successful transactions.
Key Technical Properties of Vending Machines
-
Material Grade
– Definition: The quality of materials used in the manufacturing of vending machines, often specified by standards such as ASTM or ISO.
– Importance: High-grade materials ensure durability and longevity, which is essential for machines exposed to various environmental conditions. Buyers should prioritize machines constructed from stainless steel or reinforced plastics for optimal performance. -
Tolerance Levels
– Definition: The permissible limit of variation in a physical dimension of the vending machine components.
– Importance: Tighter tolerances enhance the precision and reliability of machine operations, reducing the likelihood of malfunctions. For B2B buyers, understanding these specifications helps in selecting machines that meet operational demands without frequent maintenance. -
Power Consumption
– Definition: The amount of electrical energy the vending machine uses during operation, typically measured in watts.
– Importance: Machines with lower power consumption reduce operational costs and are more sustainable. Buyers should assess energy efficiency ratings to ensure long-term savings and compliance with environmental regulations. -
Capacity
– Definition: The total number of items a vending machine can hold, which varies based on the type of products it dispenses.
– Importance: Capacity affects inventory management and the frequency of restocking. Buyers must consider their target market and location to select a machine that aligns with anticipated demand. -
User Interface
– Definition: The design and functionality of the machine’s display and input methods, which can include touchscreens, buttons, or mobile payment systems.
– Importance: An intuitive user interface enhances customer experience, leading to higher sales. Buyers should evaluate machines with modern interfaces that support multiple payment options, including cashless transactions.
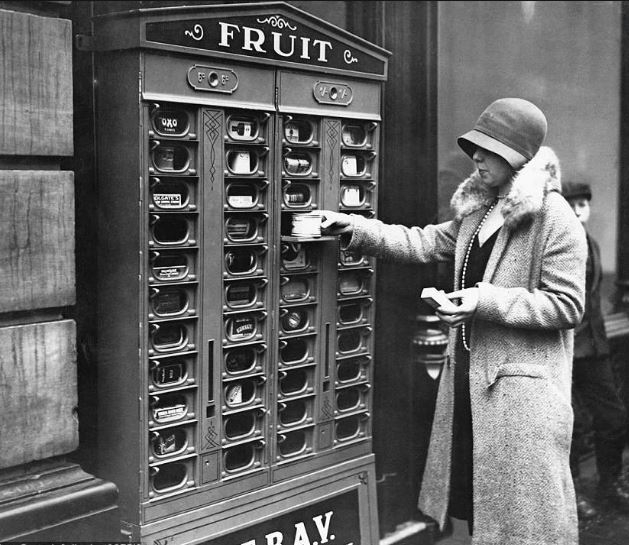
Illustrative Image (Source: Google Search)
Common Trade Terminology
-
OEM (Original Equipment Manufacturer)
– Definition: A company that produces parts or equipment that may be marketed by another manufacturer.
– Importance: Understanding OEM relationships is essential for buyers looking for specific parts or accessories for vending machines, ensuring compatibility and quality. -
MOQ (Minimum Order Quantity)
– Definition: The smallest quantity of a product that a supplier is willing to sell.
– Importance: Buyers must be aware of MOQs to manage budget constraints and ensure they do not overstock or understock based on demand forecasts. -
RFQ (Request for Quotation)
– Definition: A formal document used to request pricing from suppliers for specified products or services.
– Importance: Issuing an RFQ allows buyers to compare prices and terms from multiple suppliers, facilitating better negotiation and selection processes. -
Incoterms (International Commercial Terms)
– Definition: A set of rules that define responsibilities of buyers and sellers in international transactions.
– Importance: Familiarity with Incoterms is crucial for international buyers to understand shipping responsibilities, costs, and risks, thereby avoiding potential disputes during the procurement process. -
Lead Time
– Definition: The amount of time from placing an order to delivery.
– Importance: Buyers should consider lead times when planning inventory levels and ensuring that the vending machines are available when needed, especially in high-demand seasons. -
Warranty
– Definition: A guarantee provided by the manufacturer regarding the condition of the product and the commitment to repair or replace it if necessary within a specified period.
– Importance: A robust warranty can protect buyers from unforeseen costs due to defects or failures, making it an important factor in the purchasing decision.
Understanding these technical properties and trade terms will empower B2B buyers to make informed decisions when sourcing the oldest vending machines, ultimately leading to successful transactions and sustainable operations.
Navigating Market Dynamics, Sourcing Trends, and Sustainability in the oldest vending machine Sector
Market Overview & Key Trends
The global vending machine market, particularly the segment focused on traditional and oldest vending machines, is experiencing a renaissance driven by several key factors. Increased urbanization, particularly in regions like Africa and South America, is spurring demand for convenient food and beverage options in public spaces. Furthermore, technology integration, such as cashless payment systems and IoT connectivity, is reshaping how these machines operate and are maintained, enhancing user experience and operational efficiency.
Emerging B2B sourcing trends include a shift towards modular designs that allow for customization and flexibility in product offerings. This trend is particularly relevant for buyers in Europe and the Middle East, where consumer preferences for diverse and local products are on the rise. Additionally, sustainability is becoming a pivotal concern, with businesses seeking vending solutions that minimize environmental impact, such as energy-efficient machines and those that utilize recyclable materials.
For international B2B buyers, understanding regional market dynamics is crucial. In regions like Brazil and Colombia, localized vending solutions that cater to specific cultural tastes are essential. As vending machine operators seek to expand their footprints, they must navigate local regulations, consumer behaviors, and competition, especially from traditional food vendors and new market entrants. Embracing technological advancements will be key to staying competitive and meeting the evolving demands of consumers.
Sustainability & Ethical Sourcing in B2B
Sustainability is no longer a mere trend; it has become a requirement in the vending machine sector. The environmental impact of manufacturing and operating these machines is significant, with energy consumption and waste generation being primary concerns. B2B buyers must prioritize suppliers who are committed to reducing their carbon footprint through energy-efficient technologies, such as solar-powered machines or those with low-energy lighting.
Ethical sourcing practices are also increasingly important. Buyers should seek vendors who demonstrate transparency in their supply chains, ensuring that materials used in machines, such as plastics and metals, are sourced responsibly. Certifications like ISO 14001 for environmental management or the Forest Stewardship Council (FSC) for wood-based materials can serve as indicators of a supplier’s commitment to sustainability.
Moreover, the trend towards using biodegradable or recyclable materials in the construction and packaging of vending machines is gaining traction. By opting for suppliers who adhere to these practices, international B2B buyers can align their operations with global sustainability goals while appealing to environmentally conscious consumers.
Brief Evolution/History
The history of vending machines dates back to ancient times, with the first known device appearing in 215 B.C. in Greece, dispensing holy water. However, the modern vending machine as we know it began to take shape in the late 19th century with the introduction of machines that sold postcards and later, snacks and beverages. The evolution has been marked by significant technological advancements, from mechanical levers to electronic payments and touchscreen interfaces.
For B2B buyers, understanding this evolution is essential as it highlights the ongoing innovation in the sector. The integration of advanced technology in vending machines is not just about enhancing customer experience but also about optimizing operations and reducing costs. Buyers looking to invest in vending solutions must consider the historical context to appreciate the technological trends shaping the future of this sector.
Related Video: Global Trade & Logistics – What is Global Trade?
Frequently Asked Questions (FAQs) for B2B Buyers of oldest vending machine
-
What factors should I consider when vetting suppliers for the oldest vending machines?
When vetting suppliers, it’s crucial to assess their industry experience, customer reviews, and certifications. Look for suppliers with a proven track record in manufacturing vending machines, particularly those with historical models. Verify their compliance with international standards and regulations applicable in your region, such as ISO certifications. Additionally, consider their financial stability and ability to provide ongoing support, including maintenance and spare parts. -
Can I customize the oldest vending machine to fit my brand?
Yes, many suppliers offer customization options for vending machines. This can include branding with your company logo, color schemes, and even specific features tailored to your market’s needs. When discussing customization, be clear about your requirements and ask for examples of previous custom projects. Ensure the supplier has the capability to deliver these modifications without significantly extending lead times. -
What are the typical minimum order quantities (MOQs) and lead times for purchasing these machines?
Minimum order quantities vary by supplier and can range from a single unit to several dozen machines, depending on the customization level. Lead times also differ, typically ranging from 4 to 12 weeks after order confirmation. Factors influencing lead times include machine complexity, customization requests, and the supplier’s production capacity. Always confirm these details upfront to avoid unexpected delays. -
What payment terms should I expect when purchasing vending machines internationally?
Payment terms can vary significantly among suppliers. Common practices include a deposit upfront (usually 30-50%) with the balance due before shipment. Some suppliers may also offer letters of credit or payment upon delivery. It’s essential to discuss and agree on payment terms early in the negotiation process, considering factors like currency fluctuations and transaction fees that may affect the overall cost.
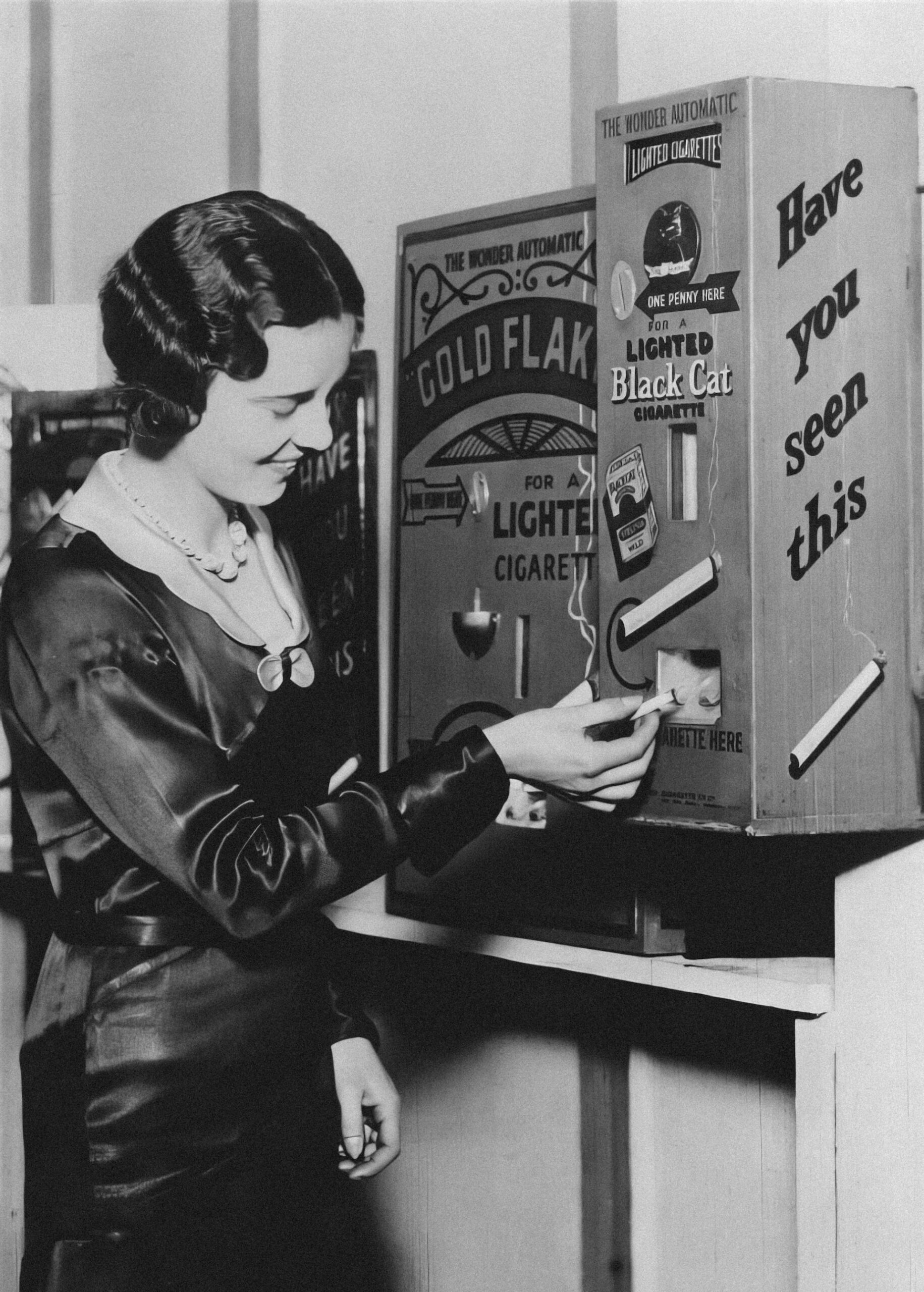
Illustrative Image (Source: Google Search)
-
How can I ensure quality assurance and certification for the vending machines I purchase?
Request documentation of quality assurance processes and certifications from your supplier. Key certifications to look for include ISO 9001 for quality management and CE marking for products sold in Europe. Additionally, inquire about the supplier’s quality control procedures during manufacturing, including testing for functionality and safety standards. A reputable supplier should provide a warranty or guarantee for their products. -
What logistics considerations should I keep in mind when importing vending machines?
Logistics is a critical aspect of importing vending machines. Consider the shipping method, whether by air or sea, based on urgency and cost. Ensure that your supplier can handle the logistics process, including packaging and documentation for customs clearance. Additionally, understand the import duties and taxes applicable in your country, as these can significantly impact the overall cost of the machines. -
How can I handle disputes with suppliers regarding my vending machine order?
To manage disputes effectively, establish clear communication channels and document all agreements in writing. If issues arise, address them promptly by referring to the contract and any agreed-upon terms. Mediation or arbitration may be necessary if the dispute cannot be resolved amicably. Consider including a dispute resolution clause in your contract to outline the preferred methods for resolving conflicts. -
What after-sales support should I expect from my vending machine supplier?
After-sales support is essential for ensuring the longevity and functionality of your vending machines. Inquire about the supplier’s warranty policy, including the duration and coverage. Additionally, ask about technical support availability, maintenance services, and access to spare parts. A reliable supplier should provide comprehensive training for your staff on machine operation and troubleshooting to minimize downtime.
Strategic Sourcing Conclusion and Outlook for oldest vending machine
In conclusion, the strategic sourcing of the oldest vending machine presents a unique opportunity for international B2B buyers, particularly those from Africa, South America, the Middle East, and Europe. By understanding the historical significance and market dynamics surrounding these machines, businesses can leverage their nostalgic appeal to differentiate themselves in competitive markets.
Key takeaways include the importance of evaluating supplier reliability, assessing the technological advancements in vending machine designs, and understanding regional consumer preferences. Additionally, fostering partnerships with local distributors can enhance market entry strategies and optimize supply chain efficiency.
As the market for vending solutions continues to evolve, forward-thinking businesses should embrace innovation while respecting the rich heritage of these machines. The blend of tradition and modernity not only appeals to diverse consumer bases but also opens new avenues for revenue generation.
Call to action: Engage with suppliers who can provide insights into the latest trends and historical context of vending machines. By strategically sourcing these unique products, you can position your business as a leader in the vending market, catering to the growing demand for diverse and innovative solutions.