Your Ultimate Guide to Sourcing Mountain Dew Vending Machine
Guide to Mountain Dew Vending Machine
- Introduction: Navigating the Global Market for mountain dew vending machine
- Understanding mountain dew vending machine Types and Variations
- Key Industrial Applications of mountain dew vending machine
- Strategic Material Selection Guide for mountain dew vending machine
- In-depth Look: Manufacturing Processes and Quality Assurance for mountain dew vending machine
- Comprehensive Cost and Pricing Analysis for mountain dew vending machine Sourcing
- Spotlight on Potential mountain dew vending machine Manufacturers and Suppliers
- Essential Technical Properties and Trade Terminology for mountain dew vending machine
- Navigating Market Dynamics, Sourcing Trends, and Sustainability in the mountain dew vending machine Sector
- Frequently Asked Questions (FAQs) for B2B Buyers of mountain dew vending machine
- Strategic Sourcing Conclusion and Outlook for mountain dew vending machine
Introduction: Navigating the Global Market for mountain dew vending machine
As global markets evolve, the demand for innovative vending solutions, such as the Mountain Dew vending machine, is surging. This specialized vending machine not only meets the growing consumer preference for convenient beverage options but also provides a lucrative opportunity for businesses across various sectors. For international B2B buyers, particularly in Africa, South America, the Middle East, and Europe, investing in a Mountain Dew vending machine can enhance customer engagement and drive sales.
This guide comprehensively explores the Mountain Dew vending machine landscape, detailing types of machines available, the materials used in their construction, and the manufacturing and quality control processes that ensure durability and efficiency. We will also examine potential suppliers, providing insights into their reliability and product offerings, alongside a clear breakdown of costs involved, including initial investment and ongoing maintenance.
Understanding the market trends surrounding beverage vending machines is essential for making informed purchasing decisions. This guide also addresses common FAQs, empowering buyers with the knowledge needed to navigate the complexities of international sourcing. By leveraging the insights provided, buyers will be equipped to make strategic decisions that align with their business objectives and customer needs, ultimately driving profitability in a competitive landscape.
Understanding mountain dew vending machine Types and Variations
Type Name | Key Distinguishing Features | Primary B2B Applications | Brief Pros & Cons for Buyers |
---|---|---|---|
Traditional Snack Vending | Dispenses a variety of snacks along with Mountain Dew | Offices, schools, public transport | Pros: Versatile; Cons: Limited beverage variety |
Refrigerated Beverage Unit | Focused solely on cold drinks, including multiple Mountain Dew flavors | Retail, gyms, hotels | Pros: High demand for cold drinks; Cons: Higher maintenance costs |
Combo Vending Machine | Combines snacks and drinks in one unit | Malls, airports, entertainment venues | Pros: Maximizes space; Cons: More complex to manage |
Smart Vending Machine | Features cashless payment and inventory tracking | Tech-savvy locations, universities | Pros: Modern appeal; Cons: Higher initial investment |
Customizable Vending Machine | Allows for branding and product selection based on location | Corporate events, trade shows | Pros: Tailored offerings; Cons: Longer lead times for setup |
Traditional Snack Vending
Traditional snack vending machines are designed to dispense a variety of snacks along with Mountain Dew beverages. These machines are particularly suitable for environments such as offices, schools, and public transport stations. They provide a convenient option for customers looking for quick snacks and drinks. When considering a purchase, buyers should evaluate the machine’s capacity, product selection, and ease of restocking, as well as the potential for generating consistent revenue.
Refrigerated Beverage Unit
Refrigerated beverage units focus exclusively on cold drinks, prominently featuring various Mountain Dew flavors. These machines are ideal for high-traffic areas such as retail stores, gyms, and hotels, where the demand for cold beverages is significant. Buyers should consider the energy efficiency of the unit, its size relative to available space, and the reliability of refrigeration technology to ensure optimal performance and customer satisfaction.
Combo Vending Machine
Combo vending machines offer a convenient solution by combining snacks and drinks into one unit. This type is especially effective in malls, airports, and entertainment venues, where foot traffic is high. Buyers should assess the machine’s layout, product variety, and potential for cross-selling items, as well as the ease of maintenance and the need for regular inventory checks to ensure product freshness.
Smart Vending Machine
Smart vending machines incorporate advanced technology, such as cashless payment options and inventory tracking systems. These machines appeal to tech-savvy locations like universities and modern workplaces. Buyers should weigh the benefits of increased sales through cashless transactions against the higher upfront costs and potential technical support needs. Additionally, the ability to gather data on consumer preferences can help businesses tailor their offerings.
Customizable Vending Machine
Customizable vending machines allow businesses to select products and branding that best fit their target market. This flexibility makes them suitable for corporate events and trade shows, where showcasing a brand is crucial. Buyers should consider the machine’s adaptability, lead times for customization, and the initial investment required to set up unique offerings. The ability to change product selections based on consumer demand can significantly enhance customer engagement.
Related Video: Machine Learning in 2024 – Beginner’s Course
Key Industrial Applications of mountain dew vending machine
Industry/Sector | Specific Application of mountain dew vending machine | Value/Benefit for the Business | Key Sourcing Considerations for this Application |
---|---|---|---|
Retail | In-store beverage sales | Increases impulse purchases, enhances customer experience | Machine size, payment options, brand visibility |
Hospitality | Hotel lobbies and guest areas | Provides convenient access to refreshments for guests | Energy efficiency, maintenance support, product variety |
Educational Institutions | Campus vending solutions | Offers students a quick beverage option, boosts sales | Machine durability, security features, product selection |
Corporate Offices | Breakroom and lounge installations | Improves employee satisfaction, encourages breaks | Custom branding, service frequency, reliability of supply |
Events and Exhibitions | Temporary installations for festivals and fairs | Attracts attendees, boosts event engagement | Mobility, ease of setup, payment integration options |
Retail
In retail environments, Mountain Dew vending machines serve as a strategic tool to enhance customer engagement and drive sales. They are often placed near high-traffic areas, encouraging impulse purchases. For international B2B buyers, it’s crucial to consider factors such as machine size to fit store layouts, payment options to accommodate diverse customer preferences, and the visibility of branding to attract attention. The right machine can significantly improve the shopping experience and increase overall beverage sales.
Hospitality
In the hospitality sector, Mountain Dew vending machines are commonly installed in hotel lobbies and guest areas, providing guests with easy access to refreshing beverages. This convenience can enhance guest satisfaction and foster a positive impression of the hotel. Buyers from this industry should prioritize energy-efficient models to reduce operational costs, as well as reliable maintenance support to ensure machines are always stocked and functional. The variety of products offered can also be tailored to regional tastes to maximize appeal.
Educational Institutions
Mountain Dew vending machines are increasingly popular in educational institutions, providing students with quick access to beverages between classes. This application not only caters to student needs but also generates additional revenue for the institution. For international buyers, considerations should include the machine’s durability to withstand heavy usage, security features to prevent vandalism, and a selection of products that align with health trends among students. Offering a mix of traditional and low-calorie options can enhance the machine’s attractiveness.
Corporate Offices
In corporate environments, Mountain Dew vending machines in break rooms and lounges can significantly improve employee satisfaction by providing a convenient refreshment option during breaks. This can lead to increased productivity and morale. B2B buyers should focus on custom branding opportunities to align with corporate identity, as well as the frequency of service to ensure machines are consistently stocked. Reliability of supply is also crucial to avoid downtime and maintain employee satisfaction.
Events and Exhibitions
Mountain Dew vending machines can be utilized at events and exhibitions to attract attendees and enhance their experience. These machines provide a quick refreshment option, encouraging longer stays and greater engagement with the event. For international buyers, key sourcing considerations include the mobility of the machines for easy setup, ease of integration with payment systems, and the ability to customize the machine for specific branding or promotional needs. The right vending solution can be a significant draw at any event, contributing to its overall success.
Related Video: How to Start a Vending Machine Business, Cost, Tips, How Much You Make
Strategic Material Selection Guide for mountain dew vending machine
When selecting materials for Mountain Dew vending machines, several factors must be considered, including durability, cost, manufacturing complexity, and compatibility with the intended environment. Here, we analyze four common materials used in the construction of vending machines, focusing on their properties, advantages, disadvantages, and specific considerations for international B2B buyers.
Stainless Steel
Key Properties: Stainless steel is known for its excellent corrosion resistance, high strength, and ability to withstand temperature variations. It typically has a temperature rating of up to 800°F (427°C) and can handle high-pressure environments.
Pros & Cons: The primary advantage of stainless steel is its durability and long lifespan, making it ideal for outdoor and high-traffic locations. However, it is more expensive than other materials and can be challenging to fabricate due to its hardness.
Impact on Application: Stainless steel is compatible with various media, including carbonated beverages like Mountain Dew, without leaching harmful substances. Its non-porous surface also aids in easy cleaning and hygiene.
Specific Considerations: International buyers should ensure compliance with food safety standards such as ASTM A240 for stainless steel. In Europe, EN 10088-1 specifies the requirements for stainless steel used in food contact applications.
Aluminum
Key Properties: Aluminum is lightweight and has good corrosion resistance, especially when anodized. It can withstand temperatures up to 400°F (204°C) and is less dense than steel.
Pros & Cons: The lightweight nature of aluminum makes it easier to transport and install. However, it is less durable than stainless steel and may not withstand heavy impacts as well.
Impact on Application: Aluminum is suitable for indoor vending machines and environments with lower humidity. Its compatibility with beverages is generally good, but care must be taken to avoid reactions with acidic drinks.
Specific Considerations: Buyers in Africa and South America should consider local corrosion factors, as aluminum may corrode in coastal areas. Compliance with local standards, such as ISO 9001 for quality management, is also essential.
Polycarbonate
Key Properties: Polycarbonate is a high-impact thermoplastic known for its transparency and UV resistance. It can handle temperatures ranging from -40°F to 240°F (-40°C to 116°C).
Pros & Cons: The key advantage of polycarbonate is its lightweight nature and high impact resistance, making it ideal for areas prone to vandalism. However, it is less scratch-resistant than glass and may yellow over time.
Impact on Application: Polycarbonate is often used for the outer panels of vending machines, providing visibility for products while protecting them from external damage. It is compatible with beverages but may not be suitable for environments with extreme temperatures.
Specific Considerations: Buyers should ensure that polycarbonate complies with safety standards such as ASTM D256 for impact resistance. In Europe, compliance with REACH regulations for chemical safety is crucial.
Galvanized Steel
Key Properties: Galvanized steel is steel that has been coated with a layer of zinc to prevent corrosion. It can withstand temperatures up to 500°F (260°C) and offers moderate strength.
Pros & Cons: The cost-effectiveness of galvanized steel makes it a popular choice for budget-conscious projects. However, it is heavier than aluminum and may not be as durable as stainless steel in high-impact situations.
Impact on Application: Galvanized steel is suitable for structural components of vending machines, providing strength and durability. It is compatible with beverages but may require additional coatings for enhanced corrosion resistance in humid environments.
Specific Considerations: Buyers should be aware of the galvanization standards, such as ASTM A123, to ensure quality. In regions with high humidity, additional protective coatings may be necessary.
Material | Typical Use Case for mountain dew vending machine | Key Advantage | Key Disadvantage/Limitation | Relative Cost (Low/Med/High) |
---|---|---|---|---|
Stainless Steel | Structural components, outer casing | Excellent durability and corrosion resistance | Higher cost and manufacturing complexity | High |
Aluminum | Internal components, lightweight structures | Lightweight and easy to install | Less durable under heavy impact | Medium |
Polycarbonate | Outer panels for visibility | High impact resistance and transparency | Less scratch-resistant, may yellow | Medium |
Galvanized Steel | Structural components | Cost-effective and strong | Heavier and less durable than stainless steel | Low |
This guide provides a comprehensive overview of material selection for Mountain Dew vending machines, emphasizing the importance of understanding material properties and compliance with international standards for B2B buyers.
In-depth Look: Manufacturing Processes and Quality Assurance for mountain dew vending machine
Manufacturing Processes for Mountain Dew Vending Machines
The manufacturing of Mountain Dew vending machines involves a series of meticulously planned stages designed to ensure efficiency, durability, and performance. The key stages in the manufacturing process include material preparation, forming, assembly, and finishing.
Material Preparation
In this initial stage, raw materials such as metal sheets, plastics, and electronic components are sourced. Suppliers are often selected based on their compliance with international standards and their ability to provide materials that meet specific quality requirements. Key considerations include:
- Supplier Certification: Ensure that suppliers are certified according to relevant international standards, such as ISO 9001, which indicates a commitment to quality management systems.
- Material Specifications: Materials must meet specific standards for durability, corrosion resistance, and aesthetic appeal.
Forming
The forming stage involves shaping the prepared materials into components. This may include processes like stamping, bending, and molding for metal and plastic parts. Techniques commonly used in this phase include:
- CNC Machining: Computer Numerical Control (CNC) machines are utilized for precise cutting and shaping of metal parts, ensuring uniformity and high-quality finishes.
- Injection Molding: For plastic components, injection molding is employed to create complex shapes efficiently.
Assembly
Once components are formed, the next step is assembly. This phase is critical as it involves integrating various parts into a functional vending machine. Key activities include:
- Sub-assembly: Components such as refrigeration units, payment systems, and control panels are assembled separately before the final assembly.
- Automated Assembly Lines: Many manufacturers use automated lines to increase efficiency and reduce the risk of human error.
Finishing
The finishing stage focuses on the final touches that enhance the machine’s appearance and functionality. This includes:
- Painting and Coating: Applying protective coatings to prevent rust and enhance aesthetic appeal. This process may also include applying branding materials.
- Quality Checks: Each machine undergoes a series of quality checks to ensure it meets design specifications and operational standards.
Quality Assurance in Manufacturing
Quality assurance (QA) is paramount in the production of Mountain Dew vending machines. Adhering to international standards and implementing rigorous quality control measures ensures that products are reliable and meet customer expectations.
International Standards
For B2B buyers, understanding the relevant international and industry-specific standards is crucial. Key certifications include:
- ISO 9001: This certification demonstrates that the manufacturer adheres to a quality management system, ensuring consistent quality in products and services.
- CE Marking: For machines sold in Europe, CE marking indicates compliance with EU safety, health, and environmental protection standards.
- API Standards: If applicable, the American Petroleum Institute (API) standards may apply, particularly for machines involving fluid dispensing.
Quality Control Checkpoints
Quality control checkpoints during the manufacturing process include:
- Incoming Quality Control (IQC): Materials and components are inspected upon arrival to ensure they meet specifications.
- In-Process Quality Control (IPQC): Regular inspections during the manufacturing process help identify defects early, reducing waste and rework.
- Final Quality Control (FQC): The finished product is thoroughly tested to ensure it meets all operational and safety standards before shipping.
Common Testing Methods
Various testing methods are employed to ensure the quality and performance of vending machines:
- Functional Testing: Each machine is tested for operational performance, including the dispensing mechanism, payment processing, and refrigeration systems.
- Durability Testing: Machines undergo stress tests to ensure they can withstand heavy use over time.
- Electrical Safety Testing: Compliance with electrical safety standards is verified through rigorous testing to prevent hazards.
Verifying Supplier Quality Control
For international B2B buyers, it is essential to verify the quality control processes of potential suppliers. Effective strategies include:
- Supplier Audits: Conducting audits of potential suppliers to assess their manufacturing practices, quality control measures, and adherence to standards.
- Quality Reports: Requesting detailed quality reports that outline testing results, defect rates, and compliance with international standards.
- Third-party Inspections: Engaging third-party inspection agencies to provide unbiased assessments of the manufacturing processes and product quality.
Quality Control and Certification Nuances for International Buyers
When dealing with international suppliers, particularly from regions such as Africa, South America, the Middle East, and Europe, buyers should be aware of specific nuances:
- Regulatory Compliance: Different regions have varying regulations and standards. Understanding local regulations can help ensure compliance and smooth market entry.
- Cultural Differences: Be mindful of cultural differences in business practices and communication styles that may affect negotiations and quality assurance processes.
- Language Barriers: Clear communication regarding quality expectations is essential. Utilizing professional translation services can help bridge language gaps.
Conclusion
Manufacturing Mountain Dew vending machines involves a complex interplay of processes and quality assurance measures. For international B2B buyers, a thorough understanding of these processes, adherence to quality standards, and proactive verification of supplier capabilities are crucial for ensuring a successful purchasing experience. By focusing on these elements, buyers can secure reliable, high-quality vending machines that meet their operational needs.
Related Video: SMART Quality Control for Manufacturing
Comprehensive Cost and Pricing Analysis for mountain dew vending machine Sourcing
Understanding the Cost Structure for Mountain Dew Vending Machines
When sourcing Mountain Dew vending machines, international B2B buyers must navigate a multifaceted cost structure that includes various components. The primary cost components consist of:
-
Materials: The core materials for vending machines include stainless steel for durability, plastic for components, and electronic parts for payment processing. Prices for these materials can fluctuate based on global market conditions.
-
Labor: Labor costs vary significantly based on the manufacturing location. For instance, labor rates in Asia might be lower compared to Europe, impacting overall pricing.
-
Manufacturing Overhead: This encompasses expenses related to factory operations, utilities, and maintenance. Efficient manufacturing processes can help minimize these costs, ultimately affecting the price of the machines.
-
Tooling: Initial tooling costs for custom designs can be substantial. Buyers should consider whether standard models can meet their needs to avoid these upfront costs.
-
Quality Control (QC): Ensuring that machines meet safety and performance standards is critical. QC costs can vary based on the level of certification required, which is particularly important for markets in Europe and North America.
-
Logistics: Shipping costs depend on the distance from the manufacturer to the buyer, the mode of transport, and any tariffs or duties. Incoterms play a crucial role in defining who is responsible for these costs.
-
Margin: Suppliers typically include a profit margin in their pricing. Understanding the market rates can help buyers negotiate better deals.
Influencers on Pricing
Several factors can influence the pricing of Mountain Dew vending machines:
-
Volume/MOQ: Buying in bulk can significantly reduce the per-unit cost. Suppliers often provide discounts for large orders, making it essential for buyers to assess their needs accurately.
-
Specifications/Customization: Custom features, such as branding or specific payment systems, can increase costs. Buyers should weigh the benefits of customization against the additional expenses.
-
Materials Quality/Certifications: Higher quality materials and certifications (such as ISO or CE) can raise costs but may lead to longer-lasting machines and better performance.
-
Supplier Factors: The reputation and reliability of the supplier can impact pricing. Established suppliers may command higher prices due to their proven track record.
-
Incoterms: Different shipping terms can affect total costs. Buyers should be aware of the responsibilities and risks associated with various Incoterms to manage costs effectively.
Tips for Buyers
International B2B buyers should consider the following strategies to enhance cost-efficiency:
-
Negotiate Effectively: Leverage volume purchases and long-term relationships to negotiate better terms. Understanding the supplier’s cost structure can provide leverage during negotiations.
-
Evaluate Total Cost of Ownership (TCO): Consider not just the purchase price but also operational costs, maintenance, and potential downtime. A lower upfront cost may lead to higher long-term expenses.
-
Understand Pricing Nuances: Pricing can vary widely based on region, with potential tariffs affecting final costs. Buyers from Africa, South America, the Middle East, and Europe should stay informed about local market conditions and regulations.
-
Research Suppliers: Evaluate multiple suppliers to understand pricing trends and options. A thorough comparison can reveal potential savings and better quality options.
-
Be Mindful of Currency Fluctuations: For international transactions, currency exchange rates can affect final costs. Consider locking in prices or using financial instruments to hedge against currency risk.
Disclaimer
The prices and cost components discussed are indicative and can vary based on multiple factors, including market conditions and specific supplier agreements. Buyers are encouraged to conduct thorough market research and obtain multiple quotes to ensure competitive pricing.
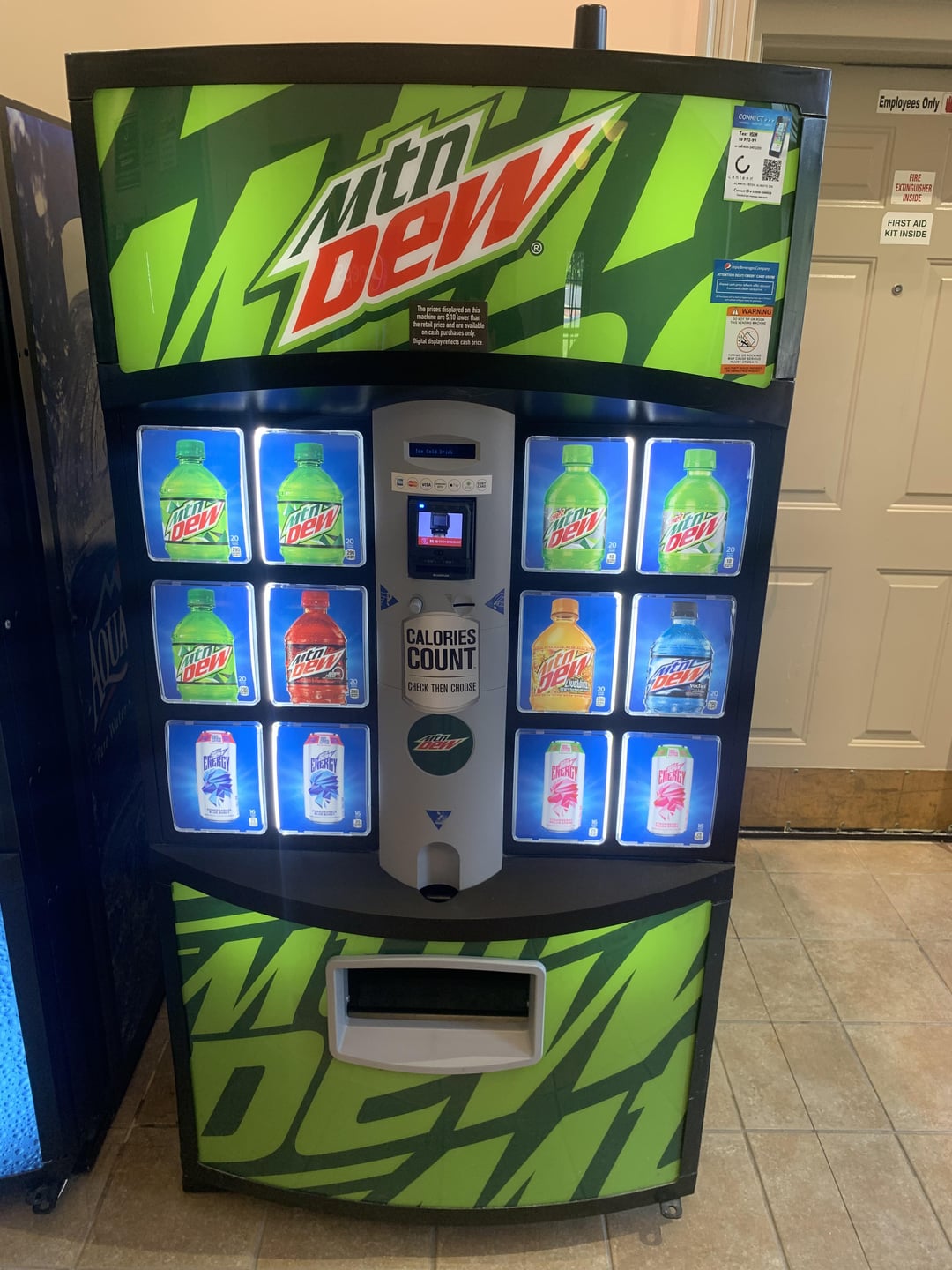
Illustrative Image (Source: Google Search)
Spotlight on Potential mountain dew vending machine Manufacturers and Suppliers
This section offers a look at a few manufacturers active in the ‘mountain dew vending machine’ market. This is a representative sample for illustrative purposes; B2B buyers must conduct their own extensive due diligence before any engagement. Information is synthesized from public sources and general industry knowledge.
Essential Technical Properties and Trade Terminology for mountain dew vending machine
Key Technical Properties of Mountain Dew Vending Machines
When considering the procurement of Mountain Dew vending machines, international B2B buyers should pay close attention to several essential technical properties that influence performance, durability, and user experience. Here are the critical specifications:
-
Material Grade
Vending machines are typically constructed from high-quality materials such as stainless steel and robust plastics. Stainless steel is preferred for its resistance to corrosion and durability, making it suitable for various environments, including humid or outdoor settings. Understanding the material grade ensures that the machine can withstand local climate conditions and reduce maintenance costs. -
Cooling Technology
The cooling mechanism employed in the vending machine is vital for maintaining product quality. Options include compressor-based cooling and thermoelectric systems. Compressor systems are more effective for larger volumes and offer quicker cooling times, while thermoelectric systems may be more energy-efficient for smaller units. Buyers should assess the cooling technology based on their specific operational needs and energy cost considerations.
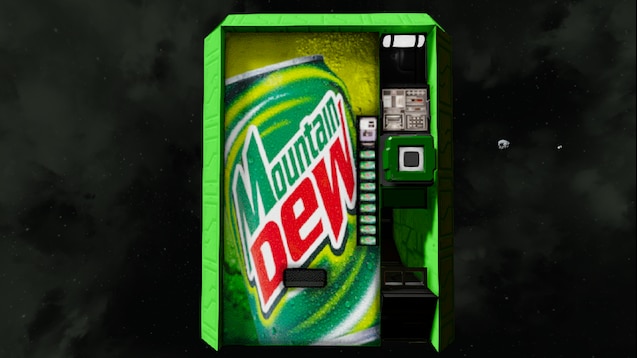
Illustrative Image (Source: Google Search)
-
Capacity and Size
Capacity refers to the number of cans or bottles the machine can hold, typically ranging from 200 to 600 units. Size specifications include height, width, and depth, which must align with the intended installation location. Evaluating capacity is crucial for ensuring that the machine meets anticipated demand and maximizes sales opportunities. -
Power Requirements
Understanding the power specifications, such as voltage and current requirements, is essential for installation. Most vending machines operate on standard voltages (e.g., 110V or 220V). Ensuring compatibility with local electrical systems will prevent operational issues and reduce installation complexities. -
User Interface
The user interface includes the payment systems (cash, card, mobile payment) and the display technology (LED screens, touch interfaces). A well-designed interface enhances customer experience and can improve sales. Buyers should consider the target market’s preferences for payment methods and the ease of use of the interface. -
Security Features
Vending machines should include robust security measures to prevent theft and vandalism. This may involve reinforced locks, anti-tamper technology, and surveillance options. Understanding these features is crucial for protecting investment and ensuring continuous operation.
Common Trade Terminology in Vending Machine Procurement
Familiarity with industry jargon is essential for effective communication and negotiation in the vending machine market. Here are several key terms:
-
OEM (Original Equipment Manufacturer)
An OEM refers to a company that produces parts or equipment that may be marketed by another manufacturer. In the context of vending machines, OEMs provide the core components, which may be customized for branding or functionality. -
MOQ (Minimum Order Quantity)
MOQ is the smallest quantity of a product that a supplier is willing to sell. Understanding MOQ helps buyers gauge their purchasing power and negotiate better terms, especially when sourcing multiple machines. -
RFQ (Request for Quotation)
An RFQ is a document that a buyer sends to suppliers to solicit price quotes for specific products or services. This is an essential step in the procurement process, allowing buyers to compare offers and make informed decisions. -
Incoterms (International Commercial Terms)
Incoterms are a set of international rules that define the responsibilities of sellers and buyers for the delivery of goods. Familiarity with terms like FOB (Free on Board) or CIF (Cost, Insurance, and Freight) is crucial for understanding shipping costs and responsibilities. -
Lead Time
Lead time refers to the time it takes from placing an order until the product is delivered. Knowing the lead time helps buyers plan their inventory and sales strategies effectively. -
Warranty Period
This term indicates the duration for which the manufacturer guarantees the machine’s performance and will cover repairs or replacements. Understanding warranty terms is essential for assessing long-term costs and potential risks associated with the purchase.
By grasping these technical properties and trade terms, international B2B buyers can make informed decisions that align with their operational needs and market conditions.
Navigating Market Dynamics, Sourcing Trends, and Sustainability in the mountain dew vending machine Sector
Market Overview & Key Trends
The mountain dew vending machine sector is experiencing a notable shift driven by several global dynamics. First, the increasing urbanization in regions such as Africa and South America has led to a higher demand for convenient beverage solutions. The rise of the health-conscious consumer is also influencing product offerings; buyers are now seeking vending machines that not only dispense popular sugary drinks like Mountain Dew but also healthier alternatives.
In terms of technology, the integration of IoT (Internet of Things) capabilities into vending machines is becoming a key trend. This allows operators to monitor inventory levels in real-time, optimize restocking schedules, and analyze customer preferences through data analytics. For international B2B buyers, investing in smart vending solutions can enhance operational efficiency and customer engagement.
Moreover, sustainability is becoming a critical factor in sourcing decisions. Vending machines that utilize eco-friendly materials and energy-efficient technologies are gaining traction. Buyers from Europe, particularly in Germany and Spain, are increasingly prioritizing suppliers who demonstrate a commitment to sustainable practices. The market is also seeing a rise in mobile payment solutions, catering to the preferences of tech-savvy consumers, which can significantly enhance sales and customer satisfaction.
Sustainability & Ethical Sourcing in B2B
Sustainability is no longer just a buzzword; it has become a core aspect of the business strategy in the mountain dew vending machine sector. The environmental impact of vending machines—ranging from energy consumption to waste generation—necessitates a focus on eco-friendly practices. International B2B buyers are encouraged to seek out vending machines designed with energy-efficient components, such as LED lighting and advanced cooling systems, which can significantly reduce electricity usage.
Furthermore, ethical sourcing in the supply chain is paramount. Buyers should prioritize suppliers who adhere to responsible sourcing practices, ensuring that materials used in vending machine production are obtained without exploiting labor or harming the environment. Certifications such as FSC (Forest Stewardship Council) and ISO 14001 for environmental management can serve as indicators of a supplier’s commitment to sustainability.
Investing in sustainable and ethically sourced vending machines not only aligns with global trends but also enhances brand reputation and consumer loyalty, particularly in markets that value corporate social responsibility.
Brief Evolution/History
The vending machine industry has evolved significantly since its inception in the early 20th century. Initially designed to dispense simple products, the sector has transformed into a sophisticated channel for beverage distribution, particularly with the introduction of machines that offer a variety of drinks, including carbonated beverages like Mountain Dew.
With advancements in technology, modern vending machines are now equipped with touch screens, cashless payment options, and even interactive marketing features. This evolution has not only improved user experience but also streamlined operations for B2B buyers, making it easier to manage inventory and respond to consumer trends. As the industry continues to innovate, the focus on sustainability and ethical sourcing will shape its future trajectory, presenting valuable opportunities for international buyers.
Related Video: Is global trade transforming? | Counting the Cost
Frequently Asked Questions (FAQs) for B2B Buyers of mountain dew vending machine
-
What should I consider when vetting suppliers for Mountain Dew vending machines?
When vetting suppliers, prioritize their industry experience and reputation. Verify their certifications, such as ISO or CE, which ensure compliance with international standards. Request references from previous clients, particularly those within your region, to gauge reliability and service quality. Additionally, evaluate their production capacity to meet your volume needs and assess their customer support structure to ensure timely communication. -
Can I customize Mountain Dew vending machines to fit my brand?
Yes, many suppliers offer customization options, including branding, color schemes, and machine features. When discussing customization, clarify your requirements upfront and inquire about the additional costs and lead times associated with these modifications. Ensure that the supplier can provide visual mock-ups or prototypes to align expectations and avoid miscommunication during the production phase. -
What is the typical minimum order quantity (MOQ) for Mountain Dew vending machines?
The MOQ can vary widely based on the supplier and your location. Generally, suppliers may set an MOQ ranging from 10 to 50 units for standard models. For customized machines, the MOQ might be higher due to the additional resources required for production. Always confirm the MOQ before proceeding and assess whether it aligns with your budget and market demand. -
What are the average lead times for ordering Mountain Dew vending machines?
Lead times typically range from 4 to 12 weeks, depending on factors such as order size, customization, and supplier location. It’s essential to discuss lead times during the negotiation phase and consider potential delays in logistics, especially if shipping internationally. Building in buffer time for unforeseen circumstances can prevent disruptions in your vending machine rollout. -
What quality assurance certifications should I look for in vending machines?
Look for certifications that ensure product safety and quality, such as ISO 9001 for quality management systems, CE marking for compliance with EU standards, and RoHS for hazardous substances. Additionally, inquire about the supplier’s internal quality control processes, including testing procedures for machine functionality and durability, to ensure the machines will perform reliably in various environments. -
How should I handle logistics and shipping for my vending machine order?
Discuss logistics options with your supplier, including shipping methods and costs. Consider whether you need door-to-door delivery or if you can manage pick-up from a port. Ensure you understand the customs regulations for your country and any associated duties or taxes. It may be beneficial to work with a freight forwarder familiar with international shipments to streamline the process. -
What steps can I take to resolve disputes with my supplier?
Establish clear communication channels and document all agreements to mitigate disputes. If issues arise, address them promptly and professionally, ideally through direct negotiation. Should a resolution not be reached, refer to the terms outlined in your contract regarding dispute resolution, which may involve mediation or arbitration. Keeping records of all correspondence will be crucial if formal proceedings become necessary. -
What payment terms are commonly offered for international orders?
Payment terms can vary, but common options include a deposit upfront (usually 30-50%) with the balance due before shipping. Some suppliers may offer letters of credit or payment through escrow services for added security. Discuss and negotiate payment terms early in the process to ensure they are manageable for your cash flow and align with your purchasing strategy.
Strategic Sourcing Conclusion and Outlook for mountain dew vending machine
In conclusion, strategic sourcing for Mountain Dew vending machines presents a unique opportunity for international B2B buyers across Africa, South America, the Middle East, and Europe. Understanding regional preferences and market dynamics is crucial for successful procurement. Buyers should focus on suppliers that not only offer competitive pricing but also demonstrate reliability and quality in their products.
Key takeaways include:
- Supplier Relationships: Establish strong partnerships with suppliers who can provide consistent product availability and support.
- Market Research: Conduct thorough market analysis to understand local consumer behaviors and preferences, which can influence vending machine placement and product selection.
- Technology Integration: Look for vending machines equipped with advanced technologies, such as cashless payment systems and inventory management features, to enhance customer experience and operational efficiency.
As the demand for convenience and instant refreshment continues to grow, investing in Mountain Dew vending machines can yield significant returns. International buyers are encouraged to seize this opportunity by leveraging strategic sourcing methods that align with their business goals. By doing so, they can ensure a competitive edge in an evolving marketplace.