Your Ultimate Guide to Sourcing Mini Vending Machine
Guide to Mini Vending Machine
- Introduction: Navigating the Global Market for mini vending machine
- Understanding mini vending machine Types and Variations
- Key Industrial Applications of mini vending machine
- Strategic Material Selection Guide for mini vending machine
- In-depth Look: Manufacturing Processes and Quality Assurance for mini vending machine
- Comprehensive Cost and Pricing Analysis for mini vending machine Sourcing
- Spotlight on Potential mini vending machine Manufacturers and Suppliers
- Essential Technical Properties and Trade Terminology for mini vending machine
- Navigating Market Dynamics, Sourcing Trends, and Sustainability in the mini vending machine Sector
- Frequently Asked Questions (FAQs) for B2B Buyers of mini vending machine
- Strategic Sourcing Conclusion and Outlook for mini vending machine
Introduction: Navigating the Global Market for mini vending machine
In today’s fast-paced, convenience-driven world, mini vending machines have emerged as a game-changing solution for businesses seeking to maximize their footprint while catering to diverse consumer needs. These compact machines not only fit seamlessly into limited spaces but also offer a wide array of products, making them ideal for offices, gyms, and retail environments. For international B2B buyers, particularly those operating in Africa, South America, the Middle East, and Europe, investing in mini vending machines represents a strategic opportunity to enhance customer engagement and drive sales.
This comprehensive guide delves into the essential aspects of the mini vending machine market, covering types, materials, manufacturing and quality control, suppliers, cost considerations, and market trends. Additionally, it addresses common FAQs to empower buyers with the knowledge necessary to make informed sourcing decisions.
By understanding the intricacies of mini vending machines—from selecting the right supplier to navigating local regulations—B2B buyers can optimize their investments, ensuring they align with market demands and regulatory requirements. This guide serves as a crucial resource for businesses looking to harness the potential of mini vending machines, providing actionable insights that foster growth and profitability in an increasingly competitive landscape.
Understanding mini vending machine Types and Variations
Type Name | Key Distinguishing Features | Primary B2B Applications | Brief Pros & Cons for Buyers |
---|---|---|---|
Compact Snack Machines | Small footprint, typically offering snacks and beverages | Offices, gyms, small retail spaces | Pros: Space-efficient, easy to stock. Cons: Limited product variety. |
Wall-Mounted Machines | Mounted on walls, saving floor space | Co-working spaces, schools, hospitals | Pros: Customizable, sleek design. Cons: Installation complexity. |
Specialty Product Vending | Designed for niche markets (e.g., vape, electronics) | Nightclubs, universities, specialty shops | Pros: Targeted offerings can attract specific demographics. Cons: Regulatory compliance challenges. |
Miniature Combo Machines | Combines snacks and drinks in a single unit | Small cafes, break rooms, waiting areas | Pros: Versatile, maximizes sales potential. Cons: May require more maintenance. |
Cashless Payment Machines | Equipped with advanced payment options (e.g., mobile, card) | High-tech workplaces, urban environments | Pros: Enhanced customer convenience, faster transactions. Cons: Higher initial investment. |
Compact Snack Machines
Compact snack machines are ideal for businesses with limited space, such as small offices and gyms. These machines typically offer a selection of snacks and beverages, catering to the quick consumption habits of users. When purchasing, consider the machine’s capacity and the types of products that will best suit your clientele. These machines are easy to stock and maintain, making them a practical choice for B2B buyers looking for simplicity and efficiency.
Wall-Mounted Machines
Wall-mounted vending machines are designed to save floor space while providing easy access to products. They are particularly suitable for environments like co-working spaces, schools, and hospitals where space is at a premium. Buyers should consider the installation requirements and the machine’s customizability to ensure it aligns with their branding and product offerings. The sleek design and functionality appeal to modern aesthetics, making them a popular choice for contemporary settings.
Specialty Product Vending
Specialty product vending machines cater to niche markets, such as vape products or electronics. These machines are often found in nightclubs, universities, and specialty shops, targeting specific demographics with unique offerings. B2B buyers must navigate regulatory compliance when sourcing these machines, especially in regions with strict laws regarding age-restricted items. Understanding local regulations and customer preferences is crucial for ensuring the success of these machines in the market.
Miniature Combo Machines
Miniature combo machines combine snacks and drinks in a single unit, making them versatile options for small cafes, break rooms, and waiting areas. By offering a wider variety of products, these machines can maximize sales potential. Buyers should evaluate the machine’s maintenance requirements and the balance of snack-to-drink offerings to meet customer demands effectively. These machines can enhance customer satisfaction by providing a one-stop solution for refreshments.
Cashless Payment Machines
Cashless payment machines are equipped with advanced payment options such as mobile payments and card readers, making them ideal for high-tech workplaces and urban environments. These machines cater to the growing trend of cashless transactions, providing enhanced convenience for customers. However, they often come with a higher initial investment. B2B buyers should assess the target market’s payment preferences and the potential return on investment when considering these machines for their operations.
Related Video: How to Make a Mini Vending Machine Using Standard Printer, 8.5 x11, Canva and Photoshop Instructions
Key Industrial Applications of mini vending machine
Industry/Sector | Specific Application of mini vending machine | Value/Benefit for the Business | Key Sourcing Considerations for this Application |
---|---|---|---|
Corporate Offices | Snack and beverage dispensing | Increases employee satisfaction and productivity | Supplier reliability, product variety, and healthy options |
Educational Institutions | Student snack and drink access | Enhances student convenience and campus engagement | Compliance with health regulations, payment options, and machine durability |
Healthcare Facilities | Quick access to essential items | Supports patient and visitor needs for convenience | Compliance with safety standards, product sourcing, and maintenance services |
Fitness Centers | Nutritional supplements and snacks | Meets member dietary needs and boosts membership retention | Product range, supplier partnerships, and machine placement strategies |
Retail Environments | Specialty items (e.g., electronics, cosmetics) | Expands product offerings and attracts diverse customers | Market research, inventory management, and promotional strategies |
Corporate Offices
Mini vending machines in corporate offices serve as convenient snack and beverage dispensers, significantly enhancing employee satisfaction and productivity. By providing quick access to refreshments, companies can reduce downtime during work hours. International B2B buyers should prioritize suppliers that offer a diverse range of healthy options to cater to modern health-conscious employees. Additionally, reliability in product delivery and machine maintenance is crucial to ensure continuous operation.
Educational Institutions
In educational settings, mini vending machines can be strategically placed to provide students with easy access to snacks and drinks. This not only enhances convenience but also fosters a sense of community on campus. For B2B buyers in this sector, it’s essential to ensure compliance with local health regulations regarding food and beverage offerings. Furthermore, machines should support various payment options, including cashless transactions, to accommodate the tech-savvy student population.
Healthcare Facilities
Healthcare facilities utilize mini vending machines to offer patients and visitors quick access to essential items such as water, snacks, and hygiene products. This application addresses the need for convenience in often stressful environments. Buyers in this sector must consider sourcing products that comply with safety standards, ensuring that all items are suitable for consumption. Additionally, establishing reliable maintenance services is vital to keep these machines operational and hygienic.
Fitness Centers
Fitness centers leverage mini vending machines to provide nutritional supplements, energy bars, and healthy snacks that cater to the dietary needs of their members. This not only enhances the overall gym experience but also encourages healthy eating habits among patrons. When sourcing machines for fitness centers, B2B buyers should focus on suppliers that offer a wide product range and establish strong partnerships to ensure timely restocking. Understanding member preferences through market research can further enhance product selection.
Retail Environments
In retail environments, mini vending machines are increasingly used to dispense specialty items like electronics, cosmetics, or other niche products. This application helps retailers expand their offerings and attract a more diverse customer base. B2B buyers should conduct thorough market research to identify trending products and ensure effective inventory management. Additionally, developing promotional strategies that highlight the convenience of these machines can drive customer engagement and sales.
Related Video: How to make a MINI vending machine
Strategic Material Selection Guide for mini vending machine
When selecting materials for mini vending machines, it is crucial to consider the properties, advantages, and limitations of each option. This decision impacts not only the performance and durability of the machines but also their compliance with international standards, particularly for buyers in Africa, South America, the Middle East, and Europe. Below are analyses of four common materials used in the construction of mini vending machines.
1. Stainless Steel
Key Properties:
Stainless steel is known for its excellent corrosion resistance, high strength, and ability to withstand high temperatures. It typically has a temperature rating of up to 800°F (427°C) and is resistant to various chemicals.
Pros & Cons:
The durability of stainless steel makes it ideal for high-traffic environments. It is easy to clean, which is essential for hygiene in vending applications. However, it can be more expensive than other materials, and its manufacturing complexity may lead to higher production costs.
Impact on Application:
Stainless steel is suitable for environments where hygiene is paramount, such as food and beverage dispensing. Its resistance to corrosion ensures longevity, especially in humid or wet conditions.
Considerations for International Buyers:
Buyers should ensure that the stainless steel used complies with relevant standards such as ASTM A240 or EN 10088. Additionally, understanding local regulations regarding food safety and hygiene is vital.
2. Powder-Coated Steel
Key Properties:
Powder-coated steel offers a protective layer that enhances corrosion resistance and provides a variety of color options. The coating can withstand temperatures up to 200°F (93°C) without degrading.
Pros & Cons:
This material is cost-effective and provides a visually appealing finish, making it popular for aesthetic-focused applications. However, the powder coating can chip or scratch, exposing the underlying steel to corrosion.
Impact on Application:
Ideal for less demanding environments, powder-coated steel is suitable for indoor vending machines. It may not perform as well in outdoor settings or areas with high moisture.
Considerations for International Buyers:
Buyers should check for compliance with local environmental regulations regarding coatings. Standards such as ASTM D3359 for adhesion testing may be relevant.
3. Polycarbonate
Key Properties:
Polycarbonate is a lightweight, impact-resistant plastic that can withstand temperatures from -40°F to 240°F (-40°C to 116°C). It is also resistant to UV radiation.
Pros & Cons:
The primary advantage of polycarbonate is its durability and resistance to impact, making it ideal for high-traffic areas. However, it can be more susceptible to scratching and may not have the same aesthetic appeal as metal options.
Impact on Application:
Polycarbonate is often used for windows or transparent sections of vending machines, allowing visibility of products while providing protection. It is suitable for environments where weight and impact resistance are critical.
Considerations for International Buyers:
Buyers should ensure that the polycarbonate used meets standards such as ASTM D635 for flammability. Additionally, understanding local recycling regulations for plastics is important.
4. Aluminum
Key Properties:
Aluminum is lightweight, corrosion-resistant, and has a temperature rating of up to 1,200°F (649°C). It is also highly malleable, allowing for various designs.
Pros & Cons:
Aluminum is cost-effective and provides good strength-to-weight ratios, making it easy to transport and install. However, it can be less durable than stainless steel in high-wear applications and may require additional coatings for enhanced corrosion resistance.
Impact on Application:
Aluminum is suitable for both indoor and outdoor vending machines, especially in environments where weight is a concern. Its aesthetic versatility allows for creative designs.
Considerations for International Buyers:
Buyers should verify that aluminum complies with standards such as ASTM B221 for extruded aluminum. Understanding local environmental regulations regarding aluminum recycling is also essential.
Summary Table
Material | Typical Use Case for mini vending machine | Key Advantage | Key Disadvantage/Limitation | Relative Cost (Low/Med/High) |
---|---|---|---|---|
Stainless Steel | Food and beverage vending machines | Excellent corrosion resistance | Higher cost and manufacturing complexity | High |
Powder-Coated Steel | Indoor vending machines with aesthetic focus | Cost-effective and visually appealing | Susceptible to chipping and scratching | Medium |
Polycarbonate | Transparent sections of vending machines | Lightweight and impact-resistant | More prone to scratching | Medium |
Aluminum | Both indoor and outdoor vending machines | Lightweight and versatile | Less durable than stainless steel | Low |
This guide provides actionable insights for international B2B buyers, helping them make informed decisions regarding the material selection for mini vending machines. Understanding the properties, advantages, and limitations of each material is essential for optimizing performance and compliance in various markets.
In-depth Look: Manufacturing Processes and Quality Assurance for mini vending machine
The manufacturing of mini vending machines involves a series of intricate processes that ensure the final product meets the quality expectations of international B2B buyers. Understanding these processes and the associated quality assurance protocols is vital for making informed purchasing decisions.
Manufacturing Processes for Mini Vending Machines
The production of mini vending machines typically unfolds in several key stages:
1. Material Preparation
This initial stage involves sourcing high-quality materials, such as metals, plastics, and electronic components. Suppliers should be evaluated based on their ability to provide materials that meet industry standards. For example, stainless steel is often preferred for its durability and corrosion resistance, while high-grade plastics are chosen for their lightweight and aesthetic appeal.
2. Forming
In this phase, the raw materials are shaped into components. Common techniques include:
- CNC Machining: Utilized for precision cutting of metal and plastic parts, ensuring a high level of accuracy in the dimensions of components.
- Injection Molding: A widely used method for producing plastic parts, allowing for complex shapes and designs that can enhance functionality.
- Sheet Metal Fabrication: Often employed to create the outer casing of the vending machine, providing strength and protection for internal components.
These techniques must be performed under strict controls to ensure that each part meets the specified tolerances.
3. Assembly
Once the components are formed, they are assembled into the final product. This process typically includes:
- Mechanical Assembly: Connecting various parts using screws, bolts, and adhesive materials.
- Electrical Assembly: Integrating wiring, sensors, and control systems that enable the machine to operate efficiently. This stage may involve the installation of cashless payment systems, touchscreens, and inventory management software.
Effective assembly is crucial for ensuring that all components function harmoniously, which directly impacts the machine’s reliability and user experience.
4. Finishing
The final stage of manufacturing involves finishing touches that enhance both the aesthetic and functional qualities of the vending machine. Common practices include:
- Painting and Coating: Applying protective coatings to prevent rust and wear while also providing an appealing finish.
- Quality Inspection: Conducting visual and functional inspections to verify that the machine meets design specifications before it moves to the quality assurance phase.
Quality Assurance in Mini Vending Machine Manufacturing
Quality assurance is a critical aspect of the manufacturing process that ensures the final product meets both regulatory standards and customer expectations. The following are key components of quality assurance for mini vending machines:
International Standards
B2B buyers should ensure that suppliers adhere to international quality standards, such as:
- ISO 9001: This standard focuses on quality management systems and is essential for ensuring consistent quality throughout the manufacturing process.
- CE Marking: Relevant for products sold in Europe, indicating compliance with health, safety, and environmental protection standards.
Industry-Specific Certifications
Depending on the target market, certain certifications may also be necessary:
- API (American Petroleum Institute): Particularly relevant for machines that dispense fuel-related products.
- FDA Approval: Required for machines that dispense food or medical products, ensuring compliance with safety regulations.
Quality Control Checkpoints
To maintain high standards, manufacturers implement various quality control (QC) checkpoints:
- Incoming Quality Control (IQC): Inspection of raw materials and components upon arrival to ensure they meet specified standards.
- In-Process Quality Control (IPQC): Continuous monitoring during the manufacturing stages to detect and rectify defects early.
- Final Quality Control (FQC): Comprehensive testing of the finished product to verify that it operates as intended and meets all quality benchmarks.
Common Testing Methods
Testing methods employed during quality assurance may include:
- Functional Testing: Assessing the operational capabilities of the vending machine, including payment processing and product dispensing.
- Durability Testing: Subjecting the machine to stress tests to evaluate its performance under various conditions.
- Safety Testing: Ensuring that the machine complies with safety regulations, such as electrical safety standards.
Verifying Supplier Quality Control
B2B buyers must take proactive steps to verify the quality control practices of potential suppliers:
-
Audits: Conducting regular audits of suppliers to assess their adherence to quality standards. This can include reviewing their manufacturing processes, QC checkpoints, and compliance with regulations.
-
Quality Reports: Requesting detailed quality reports that outline testing results, inspection findings, and any corrective actions taken in response to defects.
-
Third-Party Inspections: Engaging third-party inspection services can provide an unbiased assessment of the supplier’s quality control practices. This is particularly important for buyers in regions with varying quality standards, such as Africa, South America, and the Middle East.
Nuances for International B2B Buyers
Understanding the nuances of quality assurance is crucial for international buyers, particularly those from Africa, South America, the Middle East, and Europe. Here are some considerations:
-
Regulatory Compliance: Different regions have specific regulations that may affect product design and manufacturing. Buyers must ensure that their suppliers are compliant with local laws and international standards to avoid potential legal issues.
-
Cultural Differences: Communication styles and business practices can vary significantly across regions. Establishing clear expectations regarding quality standards and delivery timelines is essential for successful partnerships.
-
Supply Chain Transparency: Buyers should seek suppliers who prioritize transparency in their operations, as this fosters trust and facilitates smoother transactions.
By understanding the manufacturing processes and quality assurance measures associated with mini vending machines, B2B buyers can make informed decisions that enhance their business success and ensure compliance with international standards.
Related Video: Inside Massive Factory Producing The Brand New 2024 Mini – Production Line
Comprehensive Cost and Pricing Analysis for mini vending machine Sourcing
When sourcing mini vending machines, understanding the comprehensive cost structure and pricing dynamics is essential for international B2B buyers, particularly those operating in diverse markets such as Africa, South America, the Middle East, and Europe. Below is an analysis of the cost components, pricing influencers, and actionable buyer tips.
Cost Components
-
Materials: The primary materials used in manufacturing mini vending machines include metal, plastic, glass, and electronic components. The choice of materials significantly affects the durability and aesthetic appeal of the machines. For example, stainless steel may increase costs but offer better longevity and resistance to wear.
-
Labor: Labor costs vary by region and can be a significant portion of the overall expense. In countries with higher wage standards, such as those in Western Europe, labor costs could be more substantial than in regions like Africa or South America. Understanding local labor markets can help in negotiating better pricing.
-
Manufacturing Overhead: This includes costs related to factory operations, utilities, and administrative expenses. Efficient manufacturing processes can lower overhead, contributing to more competitive pricing for buyers.
-
Tooling: The initial investment in tooling (molds, dies, etc.) is crucial, especially if customization is required. Buyers should inquire about these costs, as they can be amortized over larger orders, reducing the per-unit price for bulk purchases.
-
Quality Control (QC): Implementing stringent QC measures is vital to ensure product reliability. While it may add to initial costs, effective QC can reduce long-term expenses associated with returns and repairs.
-
Logistics: Shipping and handling costs can vary widely depending on the origin and destination of the machines. Buyers should consider Incoterms (International Commercial Terms) that define shipping responsibilities to manage logistics costs effectively.
-
Margin: Suppliers typically add a profit margin to cover their costs and risks. Understanding standard margins in the industry can help buyers gauge whether they are receiving a fair price.
Price Influencers
-
Volume/MOQ: Minimum Order Quantity (MOQ) can significantly affect pricing. Higher volume orders generally lead to lower per-unit costs due to economies of scale.
-
Specifications/Customization: Custom features or specific designs can increase costs. Buyers should balance the need for customization with budget constraints.
-
Materials: As mentioned earlier, the choice of materials directly impacts cost. Investing in higher-quality materials can enhance machine durability but may also raise the initial investment.
-
Quality/Certifications: Machines that meet specific industry certifications or quality standards may command higher prices. However, they can also reduce liability and enhance customer trust.
-
Supplier Factors: Supplier reputation, experience, and geographic location can influence pricing. Established suppliers may charge more due to perceived reliability.
-
Incoterms: Understanding the implications of Incoterms is crucial for budgeting logistics costs. Terms like FOB (Free On Board) or CIF (Cost, Insurance, and Freight) dictate who bears the shipping costs and risks.
Buyer Tips
-
Negotiation: Leverage volume purchasing to negotiate better prices. Suppliers are often willing to provide discounts for larger orders or long-term contracts.
-
Cost Efficiency: Consider the Total Cost of Ownership (TCO), which includes purchase price, maintenance, and operational costs over the machine’s lifespan. Sometimes, a higher initial investment can lead to lower long-term costs.
-
Pricing Nuances: International buyers should be aware of currency fluctuations and potential tariffs that can affect pricing. Building relationships with suppliers who understand these dynamics can provide valuable insights.
-
Research Local Regulations: Ensure compliance with local laws and regulations, as failure to do so can incur additional costs or delays.
-
Transparency and Documentation: Request detailed quotes that break down all costs. This transparency helps identify hidden fees and provides a clearer picture for budgeting.
Disclaimer
The prices and cost structures discussed herein are indicative and can vary based on market conditions, supplier negotiations, and specific buyer requirements. Always conduct thorough market research and consult multiple suppliers to ensure competitive pricing tailored to your needs.
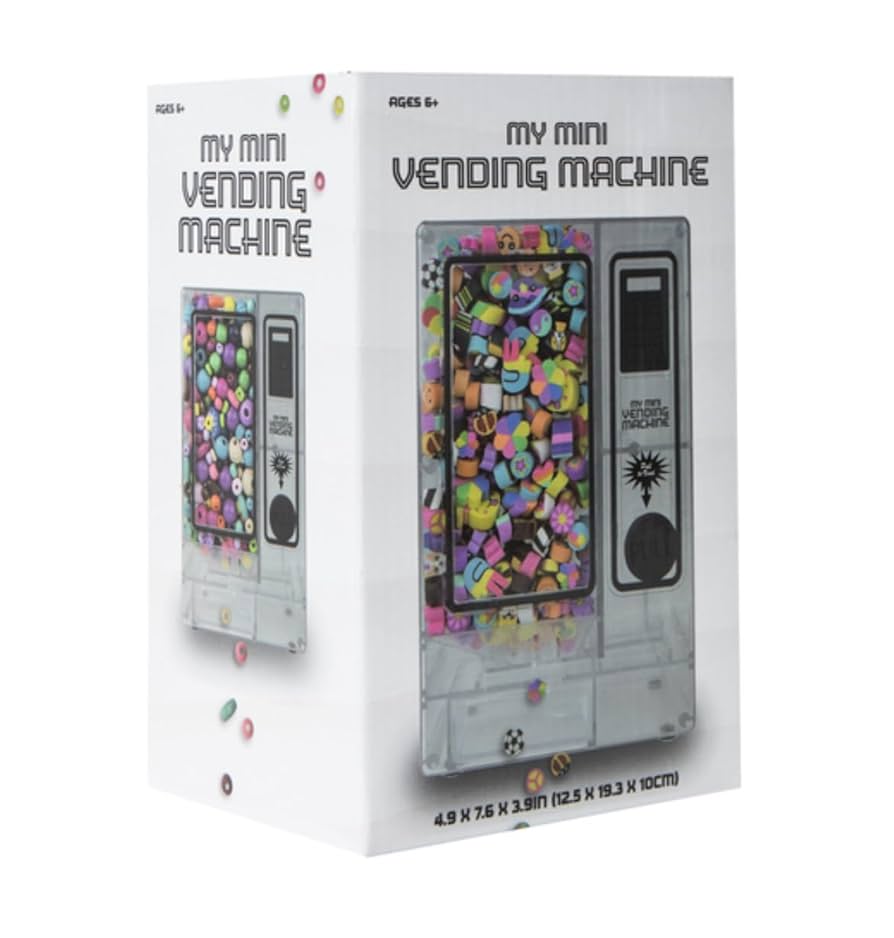
Illustrative Image (Source: Google Search)
Spotlight on Potential mini vending machine Manufacturers and Suppliers
This section offers a look at a few manufacturers active in the ‘mini vending machine’ market. This is a representative sample for illustrative purposes; B2B buyers must conduct their own extensive due diligence before any engagement. Information is synthesized from public sources and general industry knowledge.
Essential Technical Properties and Trade Terminology for mini vending machine
When considering the procurement of mini vending machines, understanding the essential technical specifications and industry terminology is crucial for making informed decisions. This section outlines the critical properties of mini vending machines and clarifies common trade terms that are important for B2B buyers.
Critical Technical Properties
-
Material Grade
– Definition: Refers to the type of materials used in the construction of the vending machine, such as stainless steel, plastic, or tempered glass.
– B2B Importance: High-quality materials ensure durability and resistance to wear and tear, which is vital for machines placed in high-traffic areas. Investing in robust materials can reduce maintenance costs and prolong machine lifespan. -
Capacity
– Definition: This indicates the number of items a vending machine can hold, usually measured in terms of product slots or total weight.
– B2B Importance: Understanding capacity helps buyers align their inventory with expected customer demand. A machine with higher capacity can serve more customers and minimize restocking frequency, optimizing operational efficiency.
-
Power Consumption
– Definition: The amount of electrical energy the vending machine requires for operation, typically measured in watts.
– B2B Importance: Lower power consumption translates to reduced operational costs, especially for businesses with multiple machines. This factor is critical for budget-conscious buyers and those focused on sustainability. -
Payment Options
– Definition: The types of payment methods the machine accepts, such as cash, credit/debit cards, or mobile payments.
– B2B Importance: Offering diverse payment options enhances customer convenience and can significantly increase sales. Understanding payment systems is essential for targeting various customer demographics. -
Dimensions and Weight
– Definition: The physical size and weight of the vending machine.
– B2B Importance: Knowing the dimensions is crucial for ensuring that the machine fits in the intended location. Additionally, weight can impact shipping costs and installation logistics. -
User Interface
– Definition: The design and functionality of the machine’s display, buttons, or touchscreen.
– B2B Importance: A user-friendly interface can improve customer experience and reduce transaction times, leading to higher sales volumes. It’s essential to consider interface design when selecting a machine for specific environments.
Common Trade Terms
-
OEM (Original Equipment Manufacturer)
– Definition: A company that produces parts or equipment that may be marketed by another manufacturer.
– Relevance: Understanding OEM relationships can help buyers find reliable suppliers and ensure they receive quality components tailored to their needs. -
MOQ (Minimum Order Quantity)
– Definition: The smallest quantity of a product that a supplier is willing to sell.
– Relevance: Knowing the MOQ is essential for budgeting and inventory planning. It can also affect negotiation strategies when sourcing multiple machines. -
RFQ (Request for Quotation)
– Definition: A document sent to suppliers to request pricing and other details for a specific quantity of goods.
– Relevance: Submitting an RFQ allows buyers to compare prices, terms, and capabilities among different vendors, aiding in informed purchasing decisions. -
Incoterms (International Commercial Terms)
– Definition: A series of pre-defined commercial terms published by the International Chamber of Commerce (ICC) relating to international commercial law.
– Relevance: Familiarity with Incoterms is vital for understanding shipping responsibilities, costs, and risks, especially when sourcing machines from international suppliers. -
Lead Time
– Definition: The time it takes from placing an order to receiving the goods.
– Relevance: Knowing lead times helps in planning inventory and understanding how quickly a supplier can meet demand, which is crucial for maintaining machine uptime. -
Warranty
– Definition: A guarantee provided by the manufacturer regarding the condition of the product and the terms of repair or replacement.
– Relevance: Understanding warranty terms can protect your investment and ensure long-term support for the machines, making it a key consideration in procurement.
By grasping these technical specifications and trade terms, international B2B buyers from regions such as Africa, South America, the Middle East, and Europe can make more informed decisions when sourcing mini vending machines, ultimately enhancing operational success and profitability.
Navigating Market Dynamics, Sourcing Trends, and Sustainability in the mini vending machine Sector
Market Overview & Key Trends
The mini vending machine sector is experiencing robust growth, fueled by several global drivers, including urbanization, increasing consumer demand for convenience, and technological advancements. In regions like Africa and South America, the rising middle class is driving the demand for accessible products in urban areas, while in Europe and the Middle East, the focus is on enhancing workplace environments and offering diverse snack options.
Emerging B2B tech trends include the integration of cashless payment systems and IoT capabilities. These technologies enable real-time inventory management, enhancing operational efficiency and customer experience. For international B2B buyers, particularly in emerging markets, investing in mini vending machines equipped with smart technologies can yield significant competitive advantages. Additionally, sustainable practices are becoming a pivotal consideration. Buyers are increasingly looking for suppliers who prioritize eco-friendly materials and energy-efficient machines, aligning with global sustainability goals.
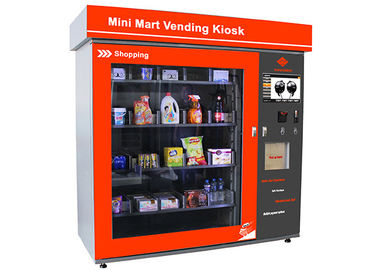
Illustrative Image (Source: Google Search)
Understanding local market dynamics is crucial for B2B success. For instance, in countries like Nigeria, where traditional retail infrastructure may be lacking, mini vending machines can fill significant gaps in the supply chain. Conversely, in France, there’s a growing trend toward gourmet and health-focused products. Thus, tailoring product offerings based on regional consumer preferences can enhance profitability and market penetration.
Sustainability & Ethical Sourcing in B2B
Sustainability is not just a trend; it is becoming a necessity in the mini vending machine sector. The environmental impact of vending machines encompasses energy consumption, waste generation, and sourcing of materials. As awareness of climate change grows, B2B buyers are increasingly prioritizing suppliers who demonstrate a commitment to sustainability.
Ethical sourcing involves selecting suppliers who adhere to responsible practices, including fair labor conditions and environmentally friendly manufacturing processes. Buyers should seek out suppliers that offer green certifications and use recyclable or biodegradable materials in their machines and products. For example, machines made with recycled plastics or those that utilize energy-efficient technologies can significantly reduce the carbon footprint associated with vending operations.
Furthermore, establishing a transparent supply chain is crucial. Buyers should engage with vendors who provide traceability regarding their sourcing methods. This not only enhances brand reputation but also builds trust with consumers who are becoming more conscious of the products they purchase.
Brief Evolution/History
The mini vending machine has evolved from traditional bulk vending units to sophisticated, space-efficient solutions that cater to modern consumer needs. Initially popularized in the late 20th century, these machines were primarily used for snacks and beverages. However, as consumer preferences shifted toward convenience and variety, manufacturers began to innovate, leading to the development of machines that dispense a wide array of products, including healthy snacks, personal care items, and even electronics.
The introduction of technology, such as cashless payment systems and touchscreens, has further transformed the landscape, making mini vending machines a viable option for businesses and consumers alike. This evolution reflects broader trends in retail and consumer behavior, presenting significant opportunities for international B2B buyers to tap into this growing market.
Related Video: Global Trade & Logistics – What is Global Trade?
Frequently Asked Questions (FAQs) for B2B Buyers of mini vending machine
-
What should I consider when vetting suppliers for mini vending machines?
When vetting suppliers, prioritize their reputation, reliability, and experience in the vending industry. Look for suppliers with positive reviews and testimonials from previous B2B clients. Verify their compliance with local regulations and certifications, particularly regarding safety and product quality. Establish clear communication channels and inquire about their ability to customize machines according to your specifications. It’s also wise to request references and assess their customer service responsiveness to gauge how they handle inquiries and issues. -
Can mini vending machines be customized to suit my business needs?
Yes, many suppliers offer customization options for mini vending machines. You can request modifications such as branding, product selection, and payment systems (including cashless options). Discuss your specific requirements with potential suppliers to understand their customization capabilities and any associated costs. Ensure that the customization aligns with your target market’s preferences, as tailored machines can enhance customer engagement and increase sales. -
What are the typical minimum order quantities (MOQ) and lead times for mini vending machines?
Minimum order quantities (MOQ) can vary significantly among suppliers, often ranging from 1 to 10 units for mini vending machines. Lead times typically depend on the complexity of the order and the supplier’s production capacity, generally ranging from 2 to 12 weeks. It’s essential to discuss these factors upfront to plan your inventory effectively. If you’re testing the market, consider negotiating lower MOQs or exploring suppliers who offer flexible ordering options to minimize risk. -
What payment terms should I expect when sourcing mini vending machines?
Payment terms can vary widely based on supplier policies and the order size. Common arrangements include upfront payments, deposits followed by balance payments upon delivery, or credit terms for established businesses. It’s crucial to clarify payment methods accepted (such as bank transfers or letters of credit) and any potential currency exchange implications, especially for international transactions. Always ensure that payment terms are documented to avoid misunderstandings. -
How do I ensure quality assurance and certification for mini vending machines?
To ensure quality assurance, request documentation of compliance with industry standards and certifications from your suppliers. Look for certifications like ISO 9001 for quality management or CE marking for safety compliance in Europe. Conducting factory visits or audits, if possible, can provide additional assurance regarding manufacturing practices. Establish a clear quality control process, including inspections upon delivery, to verify that the machines meet your specifications and standards. -
What logistics considerations should I keep in mind when importing mini vending machines?
Logistics play a crucial role in the successful importation of mini vending machines. Consider shipping methods (air vs. sea), costs, and transit times. Ensure your supplier can handle export documentation and understand customs regulations in your country. Factor in potential import duties and taxes, which can affect your overall costs. Working with a reputable freight forwarder can simplify the logistics process and help navigate any complexities in international shipping. -
How can I resolve disputes with suppliers over mini vending machine orders?
To resolve disputes effectively, first, maintain clear communication with your supplier. Document all interactions and agreements in writing to establish a clear record. If issues arise, refer to the contract terms for guidance on dispute resolution procedures. Many suppliers are open to negotiation and may offer solutions like refunds or replacements. If the dispute escalates, consider mediation or arbitration as a means to reach an amicable resolution without resorting to legal action. -
What are the key factors influencing the total cost of ownership for mini vending machines?
The total cost of ownership for mini vending machines includes several factors beyond the initial purchase price. Consider ongoing costs such as maintenance, restocking, and utilities (especially if machines are refrigerated). Evaluate the supplier’s warranty and support services, as these can significantly impact long-term expenses. Additionally, factor in potential revenue from product sales, which can offset costs. Conducting a comprehensive cost analysis will help you make informed decisions that align with your financial goals.
Strategic Sourcing Conclusion and Outlook for mini vending machine
In the evolving landscape of the mini vending machine market, strategic sourcing emerges as a critical component for success. Buyers must prioritize building strong supplier relationships, which not only enhance product availability but also foster collaborative growth opportunities. Understanding local market demands and regulatory requirements is essential, particularly for international buyers navigating diverse legal landscapes across Africa, South America, the Middle East, and Europe.
Key takeaways include the importance of evaluating suppliers based on reliability and product diversity, ensuring compliance with local regulations, and adapting offerings to meet customer preferences. As mini vending machines gain traction in various settings—from offices to gyms—there is significant potential for profit when sourcing strategies are meticulously crafted.
Looking ahead, the global demand for convenience solutions presents a unique opportunity for international B2B buyers. By leveraging effective sourcing practices, businesses can position themselves competitively in this dynamic market. Now is the time to act: explore partnerships with reputable suppliers, invest in innovative vending solutions, and tap into emerging trends. Embrace the journey of transforming your vending machine business into a thriving venture that meets the evolving needs of your customers.