Your Ultimate Guide to Sourcing Mini Beverage Vending
Guide to Mini Beverage Vending Machine
- Introduction: Navigating the Global Market for mini beverage vending machine
- Understanding mini beverage vending machine Types and Variations
- Key Industrial Applications of mini beverage vending machine
- Strategic Material Selection Guide for mini beverage vending machine
- In-depth Look: Manufacturing Processes and Quality Assurance for mini beverage vending machine
- Comprehensive Cost and Pricing Analysis for mini beverage vending machine Sourcing
- Spotlight on Potential mini beverage vending machine Manufacturers and Suppliers
- Essential Technical Properties and Trade Terminology for mini beverage vending machine
- Navigating Market Dynamics, Sourcing Trends, and Sustainability in the mini beverage vending machine Sector
- Frequently Asked Questions (FAQs) for B2B Buyers of mini beverage vending machine
- Strategic Sourcing Conclusion and Outlook for mini beverage vending machine
Introduction: Navigating the Global Market for mini beverage vending machine
In today’s fast-paced global economy, the mini beverage vending machine stands out as a versatile solution for businesses seeking to enhance customer convenience and satisfaction. These compact vending solutions cater to a growing demand for quick access to refreshments, making them invaluable assets in various sectors, including hospitality, corporate environments, and retail. As international B2B buyers, particularly from regions like Africa, South America, the Middle East, and Europe, understanding the nuances of this market is crucial for making informed sourcing decisions.
This comprehensive guide delves into the essential aspects of mini beverage vending machines, covering various types—from traditional soda dispensers to innovative coffee machines. It also highlights key materials used in manufacturing, ensuring durability and efficiency, and outlines the critical manufacturing and quality control processes that guarantee product reliability. Buyers will gain insights into identifying reputable suppliers and understanding the cost dynamics involved in procurement.
Furthermore, the guide offers a detailed market overview, including trends and demand forecasts, empowering buyers to navigate potential challenges and opportunities in their respective regions. To facilitate a smooth purchasing experience, a dedicated FAQ section addresses common inquiries and concerns, streamlining the decision-making process.
By equipping international B2B buyers with this knowledge, the guide not only enhances their sourcing capabilities but also fosters strategic partnerships that can drive growth and innovation in the competitive beverage landscape.
Understanding mini beverage vending machine Types and Variations
Type Name | Key Distinguishing Features | Primary B2B Applications | Brief Pros & Cons for Buyers |
---|---|---|---|
Traditional Snack & Drink | Combines snacks and beverages in one unit | Offices, schools, gyms | Pros: Versatile, compact; Cons: Limited beverage variety |
Cold Beverage Dispenser | Focused on chilled drinks with refrigeration | Restaurants, cafes, convenience stores | Pros: Freshness guaranteed; Cons: Higher energy costs |
Smart Vending Machines | Equipped with IoT technology for cashless transactions | Airports, malls, corporate settings | Pros: Enhanced customer experience; Cons: Initial investment |
Eco-Friendly Machines | Utilizes sustainable materials and energy-efficient tech | Eco-conscious businesses, campuses | Pros: Positive brand image; Cons: Potentially higher costs |
Customizable Beverage Stations | Allows for user customization of drinks | Events, trade shows, festivals | Pros: Engages customers; Cons: Requires maintenance |
Traditional Snack & Drink
This type of mini beverage vending machine offers a combination of snacks and drinks, making it suitable for environments like offices, schools, and gyms. Its compact design maximizes space efficiency while providing a variety of options. B2B buyers should consider the machine’s capacity and the range of products it can hold, as well as the demand for both snacks and beverages in their location. The main advantage lies in its versatility, though it may offer a limited selection of beverages compared to specialized machines.
Cold Beverage Dispenser
Cold beverage dispensers are specifically designed to keep drinks chilled, making them ideal for restaurants, cafes, and convenience stores. These machines often feature refrigeration units that ensure drinks are served at optimal temperatures. B2B buyers should evaluate energy consumption and maintenance requirements, as these machines can incur higher operating costs. The freshness and quality of the beverages are significant selling points, although they may not be as versatile as machines that also offer snacks.
Smart Vending Machines
Equipped with IoT technology, smart vending machines facilitate cashless transactions and provide real-time inventory management. These machines are increasingly popular in high-traffic areas such as airports, malls, and corporate settings. For B2B buyers, the enhanced customer experience and operational efficiency are key advantages, but the initial investment can be substantial. Buyers should weigh the long-term benefits against upfront costs and consider the technological support needed for maintenance.
Eco-Friendly Machines
These machines focus on sustainability, utilizing eco-friendly materials and energy-efficient technologies. They appeal to environmentally conscious businesses and educational institutions looking to enhance their green credentials. When considering eco-friendly machines, B2B buyers should assess the potential for higher costs versus the long-term benefits of a positive brand image. While these machines may attract a niche market, they also require a commitment to sustainability practices.
Customizable Beverage Stations
Customizable beverage stations allow users to tailor their drinks, making them popular at events, trade shows, and festivals. These machines engage customers by offering a unique experience, which can enhance brand loyalty. B2B buyers should consider the level of maintenance required and the potential for increased customer engagement. While these stations can be a hit with consumers, they may necessitate more frequent servicing and oversight to ensure a smooth operation.
Related Video: Machine Learning in 2024 – Beginner’s Course
Key Industrial Applications of mini beverage vending machine
Industry/Sector | Specific Application of mini beverage vending machine | Value/Benefit for the Business | Key Sourcing Considerations for this Application |
---|---|---|---|
Hospitality | Hotel lobbies and conference rooms | Enhances guest experience, increases revenue | Compact design, payment options, energy efficiency |
Corporate Offices | Employee break rooms | Provides convenient access to refreshments | Inventory management, customization options, service support |
Educational Institutions | Campus common areas | Offers students quick access to beverages | Durability, payment flexibility, ease of use |
Retail | Shopping malls and stores | Attracts foot traffic, boosts impulse purchases | Product variety, security features, easy restocking |
Transportation Hubs | Airports and train stations | Serves high foot traffic, reduces wait times | Robust construction, payment integration, 24/7 operation |
Hospitality
In the hospitality sector, mini beverage vending machines are strategically placed in hotel lobbies and conference rooms to enhance guest experience. They provide a quick and convenient option for guests to grab refreshments without the need for staff intervention. This not only increases revenue through additional sales but also improves customer satisfaction. International buyers should consider features such as compact design and energy efficiency, ensuring the machines fit seamlessly into varied hotel environments while minimizing operational costs.
Corporate Offices
Mini beverage vending machines serve as essential amenities in corporate office break rooms, offering employees easy access to drinks throughout the day. This convenience can lead to higher employee satisfaction and productivity. Buyers in this sector should prioritize inventory management capabilities and customization options that align with corporate branding, as well as reliable service support to ensure the machines remain operational and stocked.
Educational Institutions
In educational settings, mini beverage vending machines are ideal for placement in campus common areas, providing students with quick access to beverages between classes. This can enhance the campus experience and support a healthy lifestyle by offering a variety of drink options. For international buyers, durability and ease of use are critical considerations, as machines must withstand heavy usage while being user-friendly for a diverse student body.
Retail
In retail environments such as shopping malls and stores, mini beverage vending machines can attract foot traffic and boost impulse purchases. Positioned near entrances or high-traffic areas, these machines serve as convenient refreshment options for shoppers. Key sourcing considerations include product variety to cater to different consumer preferences, security features to prevent theft, and easy restocking processes to ensure availability.
Transportation Hubs
Mini beverage vending machines are particularly beneficial in transportation hubs like airports and train stations, where they cater to high foot traffic and help reduce wait times for travelers. These machines can offer a range of beverages, from soft drinks to healthy options, appealing to diverse customer needs. Buyers should focus on robust construction to withstand the demands of busy environments, along with payment integration for a seamless purchasing experience, ensuring 24/7 operation to meet passenger needs.
Related Video: How to make a MINI vending machine
Strategic Material Selection Guide for mini beverage vending machine
When selecting materials for mini beverage vending machines, it is crucial to consider various factors that influence performance, durability, and overall cost-effectiveness. Here, we analyze four common materials used in the construction of these machines, focusing on their properties, advantages, disadvantages, and specific considerations for international B2B buyers.
Stainless Steel
Key Properties:
Stainless steel is known for its excellent corrosion resistance, high strength, and ability to withstand high temperatures and pressures. Its composition typically includes chromium, which enhances its resistance to oxidation and staining.
Pros & Cons:
The primary advantages of stainless steel are its durability and low maintenance requirements. It is highly resistant to rust and corrosion, making it ideal for environments where moisture is prevalent, such as in beverage vending. However, stainless steel can be more expensive than other materials and may require specialized manufacturing processes, which can increase production costs.
Impact on Application:
Stainless steel is compatible with a wide range of beverages, including acidic drinks that might corrode other materials. Its non-reactive nature ensures that the taste of the beverages remains unaffected.
Considerations for International Buyers:
Buyers from regions such as Africa and South America should ensure compliance with local food safety standards, which often require the use of food-grade stainless steel. In Europe, adherence to standards like EN 10088 for stainless steel quality is essential.
Polycarbonate
Key Properties:
Polycarbonate is a high-performance plastic known for its impact resistance and clarity. It has a high thermal resistance, allowing it to function effectively in varying temperature conditions.
Pros & Cons:
The advantages of polycarbonate include its lightweight nature and excellent durability against impacts, making it suitable for vending machine components that may experience frequent handling. However, it is less resistant to certain chemicals and UV radiation, which can lead to degradation over time.
Impact on Application:
Polycarbonate is ideal for transparent panels in vending machines, allowing visibility of the products inside. However, its chemical compatibility should be assessed, especially for beverages with high acidity.
Considerations for International Buyers:
Buyers should check for compliance with regulations such as REACH in Europe, which governs the use of chemicals in materials. In regions like the Middle East, ensuring that the material can withstand local climatic conditions is crucial.
Aluminum
Key Properties:
Aluminum is lightweight, corrosion-resistant, and has good thermal conductivity. It is also easily machinable, which allows for cost-effective manufacturing processes.
Pros & Cons:
The main advantages of aluminum are its low weight and resistance to corrosion, making it suitable for portable vending machines. However, its strength is lower than that of stainless steel, which may limit its use in high-stress applications.
Impact on Application:
Aluminum is often used in the frames and structural components of vending machines. Its lightweight nature allows for easier transportation and installation, but care must be taken with beverage types that may react with aluminum.
Considerations for International Buyers:
Buyers should ensure that the aluminum used meets standards like ASTM B221 for structural applications. Additionally, they should consider local regulations regarding the use of aluminum in food contact applications.
Glass
Key Properties:
Glass is a rigid, non-porous material that offers excellent chemical resistance and aesthetic appeal. It can withstand high temperatures and is completely recyclable.
Pros & Cons:
The primary advantage of glass is its ability to maintain product integrity and taste, as it does not leach chemicals. However, glass is heavy and can be fragile, which poses challenges in terms of transport and safety.
Impact on Application:
Glass is often used for beverage containers within vending machines, providing a premium feel and visibility. However, its weight and breakability can limit its application in high-traffic areas.
Considerations for International Buyers:
Compliance with safety standards is critical, especially in regions like Europe, where regulations may dictate the thickness and treatment of glass used in food applications.
Summary Table
Material | Typical Use Case for mini beverage vending machine | Key Advantage | Key Disadvantage/Limitation | Relative Cost (Low/Med/High) |
---|---|---|---|---|
Stainless Steel | Structural components, exterior casing | Excellent corrosion resistance, durable | Higher cost, complex manufacturing | High |
Polycarbonate | Transparent panels, internal components | Lightweight, impact-resistant | Limited chemical resistance, UV degradation | Medium |
Aluminum | Frames, structural elements | Lightweight, corrosion-resistant | Lower strength compared to steel | Medium |
Glass | Beverage containers | Maintains product integrity, aesthetic appeal | Heavy, fragile | Medium |
This strategic material selection guide provides valuable insights for international B2B buyers, helping them make informed decisions that align with their operational needs and compliance requirements.
In-depth Look: Manufacturing Processes and Quality Assurance for mini beverage vending machine
Manufacturing a mini beverage vending machine involves several critical stages, each designed to ensure that the final product is not only functional but also meets the quality expectations of international B2B buyers. This section explores the typical manufacturing processes, quality assurance protocols, and relevant international standards that are essential for buyers, particularly those from Africa, South America, the Middle East, and Europe.
Manufacturing Processes
1. Material Preparation
The first stage in the manufacturing process is material preparation, which involves sourcing high-quality raw materials that meet specific technical requirements. Key materials include:
- Metal Components: Typically, stainless steel or aluminum is used for the machine’s exterior due to their durability and resistance to corrosion.
- Electrical Components: These include wiring, circuit boards, and control systems, which must comply with international safety standards.
- Plastic Parts: Used for internal components and user interfaces, plastics must be chosen for their strength and aesthetic appeal.
Key Techniques: Material selection is based on mechanical properties, environmental conditions, and cost efficiency. Suppliers should provide material certifications to confirm compliance with industry standards.
2. Forming
In this stage, the raw materials are shaped into the necessary components through various forming techniques, including:
- Stamping: Used for creating metal parts, ensuring precision and reducing waste.
- Injection Molding: Commonly employed for plastic components, allowing for complex shapes and high-volume production.
- CNC Machining: Utilized for precision parts that require tight tolerances.
Key Techniques: Advanced forming technologies such as laser cutting and water jet cutting may also be employed to enhance precision and reduce lead times.
3. Assembly
Once components are formed, the next step is assembly. This process can involve:
- Sub-assembly: Grouping related components (like the payment system or refrigeration unit) before integrating them into the main machine.
- Final Assembly: Combining all sub-assemblies into a complete vending machine. This step often requires specialized tools and fixtures to ensure proper alignment and functionality.
Key Techniques: Lean manufacturing principles are often applied to streamline assembly processes, reduce waste, and improve efficiency.
4. Finishing
The final stage of manufacturing is finishing, which enhances the appearance and durability of the vending machine. This includes:
- Surface Treatment: Processes such as powder coating or anodizing are employed to protect against corrosion and improve aesthetics.
- Quality Checks: Throughout the finishing process, visual inspections and automated systems check for defects and ensure compliance with design specifications.
Quality Assurance
Quality assurance is paramount in the production of mini beverage vending machines, ensuring that products are safe, reliable, and meet customer expectations. Key components of a robust quality assurance system include:
Relevant International Standards
- ISO 9001: This standard provides a framework for quality management systems, ensuring consistent product quality and continuous improvement.
- CE Marking: Required for products sold in the European Economic Area, indicating compliance with health, safety, and environmental protection standards.
- API Standards: Depending on the machine’s use (e.g., in food service), adherence to API standards may be necessary.
Quality Control Checkpoints
- Incoming Quality Control (IQC): This involves inspecting materials and components as they arrive at the manufacturing facility to ensure they meet specified requirements.
- In-Process Quality Control (IPQC): Quality checks during the manufacturing process help identify defects early, minimizing waste and rework.
- Final Quality Control (FQC): A comprehensive inspection of the finished product to verify functionality, safety, and compliance with design specifications.
Common Testing Methods
Testing methods may include:
– Functional Testing: Ensuring all machine components operate as intended.
– Electrical Safety Testing: Verifying that the electrical components meet safety standards.
– Durability Testing: Simulating real-world usage to assess the machine’s longevity.
Verification of Supplier Quality Control
For international B2B buyers, verifying a supplier’s quality control processes is essential. Here are strategies to consider:
- Supplier Audits: Conducting regular audits of suppliers to assess their manufacturing practices and quality assurance protocols. This may involve on-site visits or third-party assessments.
- Quality Reports: Requesting detailed quality reports that outline inspection results, testing outcomes, and any corrective actions taken.
- Third-Party Inspections: Engaging independent inspection agencies to evaluate product quality before shipment can provide additional assurance of compliance.
Quality Control and Certification Nuances
Understanding the nuances of quality control and certification is crucial for international B2B buyers, especially those in diverse markets such as Africa, South America, the Middle East, and Europe. Here are some considerations:
- Local Regulations: Different regions may have specific regulatory requirements that must be adhered to, such as local safety standards and environmental regulations.
- Cultural Expectations: Buyers should consider cultural differences in quality perceptions and customer expectations, which may influence product design and features.
- Supply Chain Transparency: Building relationships with suppliers that prioritize transparency can facilitate smoother communication regarding quality issues and compliance.
By focusing on these manufacturing processes and quality assurance practices, international B2B buyers can make informed decisions when sourcing mini beverage vending machines. Understanding the intricacies of manufacturing and quality control will not only help in selecting reliable suppliers but also in ensuring that the final products meet the high standards expected in the global market.
Related Video: Complete Can Beverage Production Line
Comprehensive Cost and Pricing Analysis for mini beverage vending machine Sourcing
Cost Structure of Mini Beverage Vending Machines
Understanding the cost structure of mini beverage vending machines is crucial for international B2B buyers aiming to optimize their sourcing strategies. The primary components of costs include:
- Materials: The choice of materials significantly impacts the overall cost. High-quality stainless steel, for example, is preferable for durability but may increase initial costs. Additionally, the selection of electronic components, refrigeration systems, and display technologies can also affect pricing.
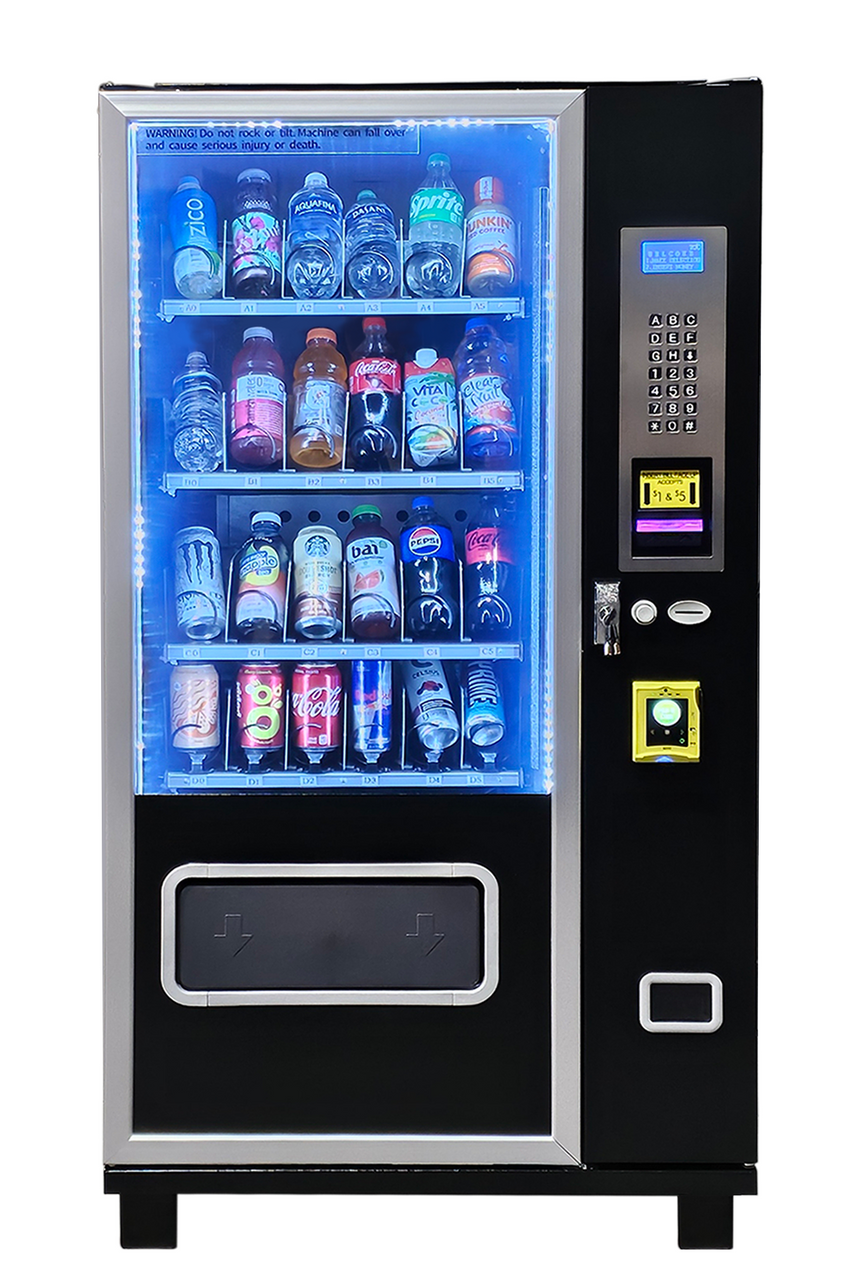
Illustrative Image (Source: Google Search)
-
Labor: Labor costs vary by region. In countries with higher labor costs, such as France or Germany, the manufacturing expenses will be greater. Conversely, sourcing from regions with lower labor costs, such as parts of Africa or South America, can reduce overall expenses.
-
Manufacturing Overhead: This includes indirect costs related to production, such as utilities, rent, and administrative expenses. Efficient production methods and facilities can help mitigate these costs.
-
Tooling: Custom tooling for specific designs can be a significant upfront investment. Buyers should evaluate whether standard models meet their needs or if custom designs justify the additional expense.
-
Quality Control (QC): Robust QC processes ensure product reliability and compliance with international standards. Investing in effective QC can reduce long-term costs associated with product failures or recalls.
-
Logistics: Transportation and shipping costs are often underestimated. Factors such as distance, shipping method, and customs duties can greatly influence the total cost.
-
Margin: Suppliers typically add a profit margin to cover risks and their operational costs. Understanding the average margins in specific regions can aid buyers in negotiating better deals.
Price Influencers
Several factors can influence the pricing of mini beverage vending machines:
-
Volume and Minimum Order Quantity (MOQ): Higher purchase volumes can lead to discounts. Buyers should consider their demand forecasts to negotiate favorable terms.
-
Specifications and Customization: Custom designs or features (e.g., payment systems, branding) can increase costs. Buyers should clearly communicate their requirements to avoid unexpected charges.
-
Materials: The quality and source of materials used can significantly influence the price. Premium materials usually come with higher costs, but they can offer better durability and lower maintenance in the long run.
-
Quality Certifications: Machines that comply with international safety and quality standards may command higher prices. Buyers should assess whether these certifications are necessary for their market.
-
Supplier Factors: The reputation and reliability of the supplier can affect pricing. Established suppliers might charge a premium for their track record, while newer entrants may offer lower prices to gain market share.
-
Incoterms: Understanding shipping terms can help buyers minimize costs. FOB (Free On Board) and CIF (Cost, Insurance, and Freight) are common terms that can affect pricing and liability.
Buyer Tips for Cost Efficiency
International B2B buyers, particularly from regions such as Africa, South America, the Middle East, and Europe, should consider the following strategies to enhance cost efficiency:
-
Negotiate Terms: Engage suppliers in discussions about pricing, payment terms, and delivery schedules. Being well-informed about market prices can strengthen your negotiation position.
-
Total Cost of Ownership (TCO): Look beyond initial purchase prices. Factor in operational costs, maintenance, and potential downtime to assess the true cost of the vending machines over their lifecycle.
-
Pricing Nuances: Be aware of regional pricing differences. For example, European suppliers may have higher prices due to stricter regulations, while suppliers in developing regions may offer more competitive rates but could have varying quality standards.
-
Conduct Market Research: Stay informed about market trends and pricing fluctuations in different regions. Understanding local market dynamics can help buyers make more informed sourcing decisions.
Disclaimer
Prices for mini beverage vending machines can vary widely based on the factors mentioned above. The insights provided are indicative and should not be considered as fixed pricing. Buyers are encouraged to conduct thorough research and engage with multiple suppliers to obtain accurate quotations tailored to their specific needs.
Spotlight on Potential mini beverage vending machine Manufacturers and Suppliers
This section offers a look at a few manufacturers active in the ‘mini beverage vending machine’ market. This is a representative sample for illustrative purposes; B2B buyers must conduct their own extensive due diligence before any engagement. Information is synthesized from public sources and general industry knowledge.
Essential Technical Properties and Trade Terminology for mini beverage vending machine
Key Technical Properties for Mini Beverage Vending Machines
When selecting a mini beverage vending machine, understanding its technical specifications is crucial for ensuring compatibility with your business needs. Here are several key properties to consider:
-
Material Grade: The construction materials used in the vending machine (e.g., stainless steel, plastic) affect durability, maintenance, and aesthetic appeal. Stainless steel offers high resistance to corrosion and is easy to clean, making it ideal for high-traffic environments. Buyers should assess the material’s grade to ensure it meets local health and safety regulations.
-
Temperature Control Range: This specification defines the operational temperature range for maintaining beverages at optimal conditions. A wider range allows for versatility in offering various drink types, from chilled sodas to hot coffees. Understanding this range is essential for businesses in climates with extreme temperatures.
-
Power Consumption: Energy efficiency is increasingly important in today’s market. Knowing the machine’s power consumption (usually measured in watts) helps in estimating operational costs. Opting for machines with lower energy usage not only reduces electricity bills but can also enhance sustainability initiatives, a key consideration for many companies.
-
Capacity and Size: The machine’s capacity (number of beverages it can hold) and dimensions determine its suitability for the intended location. Businesses must evaluate the available space and expected foot traffic to ensure the machine meets demand without taking up excessive space.
-
Payment Options: Modern vending machines offer various payment methods, including cash, credit cards, and mobile payments. Understanding the payment options available is critical for ensuring customer convenience and maximizing sales opportunities. Machines equipped with multiple payment options tend to attract more users.
Common Trade Terminology
Familiarity with industry terminology can greatly enhance communication and negotiation processes in the procurement of mini beverage vending machines. Here are some essential terms:
-
OEM (Original Equipment Manufacturer): This term refers to companies that produce equipment or components that are purchased by another company and sold under that company’s brand name. Understanding OEM relationships is vital when considering customization options for your vending machines.
-
MOQ (Minimum Order Quantity): MOQ indicates the smallest quantity of a product that a supplier is willing to sell. Knowing the MOQ helps businesses plan their purchasing strategy, ensuring they meet supplier requirements while managing inventory effectively.
-
RFQ (Request for Quotation): An RFQ is a formal document sent to suppliers requesting pricing and terms for specific products or services. For B2B buyers, issuing an RFQ is an essential step in evaluating potential suppliers, comparing costs, and negotiating favorable terms.
-
Incoterms: Short for International Commercial Terms, these are standardized trade terms used in international sales contracts. They define the responsibilities of buyers and sellers regarding shipping, insurance, and tariffs. Familiarity with Incoterms is crucial for international buyers to avoid misunderstandings and ensure compliance with trade regulations.
-
Lead Time: This term refers to the amount of time it takes from placing an order until the product is delivered. Understanding lead times helps businesses plan their operations and manage customer expectations effectively.
By grasping these technical properties and industry terms, international B2B buyers can make informed decisions that align with their operational requirements and market dynamics. This knowledge not only facilitates smoother transactions but also ensures that the chosen vending machine meets both functional and commercial objectives.
Navigating Market Dynamics, Sourcing Trends, and Sustainability in the mini beverage vending machine Sector
Market Overview & Key Trends
The mini beverage vending machine sector is experiencing dynamic growth driven by several global trends. As urbanization continues in regions like Africa and South America, demand for convenient, on-the-go beverage options is surging. This trend is further amplified by the rising health consciousness among consumers, leading to an increased preference for healthier beverage choices, including organic and low-sugar options.
Emerging technologies are reshaping the B2B landscape, with smart vending machines equipped with IoT capabilities allowing for real-time inventory management and customer interaction. These machines can utilize mobile payment systems, enhancing customer convenience and encouraging impulse purchases. For international buyers, investing in vendors that integrate these technologies can significantly improve operational efficiency and customer satisfaction.
Additionally, sustainability is becoming a key consideration in sourcing decisions. Buyers are increasingly seeking suppliers who prioritize eco-friendly practices, from machine design to the sourcing of materials. As a result, manufacturers are innovating with recyclable materials and energy-efficient designs, appealing to environmentally conscious consumers and businesses alike.
In summary, international B2B buyers should focus on suppliers who offer innovative technologies, cater to health trends, and demonstrate a commitment to sustainability to stay competitive in the mini beverage vending machine market.
Sustainability & Ethical Sourcing in B2B
Sustainability is a critical concern within the mini beverage vending machine sector, particularly as consumers and businesses alike prioritize environmental stewardship. The environmental impact of vending machines includes energy consumption, waste generation, and resource depletion. Therefore, buyers should prioritize suppliers who demonstrate a commitment to reducing their carbon footprint through energy-efficient machines and sustainable practices.
Ethical sourcing is essential for creating a responsible supply chain. This involves selecting vendors who not only comply with local and international labor laws but also promote fair trade practices. Buyers should inquire about the sourcing of materials used in machines, ensuring that they come from suppliers with responsible production processes.
Certifications such as Energy Star, Green Seal, and ISO 14001 can serve as indicators of a supplier’s commitment to sustainability. Utilizing materials that are recyclable or made from recycled content further enhances the environmental profile of vending machines. Buyers should look for these certifications and materials when sourcing mini beverage vending machines, as they not only contribute to a positive brand image but also meet the growing consumer demand for eco-friendly products.
Brief Evolution/History
The evolution of mini beverage vending machines has been marked by significant technological advancements. Initially designed for simple cash transactions, these machines have transformed into sophisticated systems incorporating touch screens, mobile payment options, and even AI-driven inventory management.
The first wave of vending machines focused primarily on snacks and cold beverages, but the introduction of healthier options in the early 2000s marked a pivotal shift. Today, these machines offer a wide range of beverages, including fresh juices and plant-based drinks, reflecting changing consumer preferences.
As the market continues to evolve, international B2B buyers must adapt to these changes by aligning with suppliers that embrace innovation and sustainability to meet the demands of modern consumers.
Related Video: International Trade 101 | Economics Explained
Frequently Asked Questions (FAQs) for B2B Buyers of mini beverage vending machine
-
What should I consider when vetting suppliers for mini beverage vending machines?
When vetting suppliers, focus on their industry experience, customer reviews, and certifications. Verify their manufacturing capabilities and ensure they comply with international quality standards such as ISO or CE. Request case studies or references from previous clients, particularly those in your region, to assess reliability. Additionally, consider their after-sales service and support, as ongoing maintenance is crucial for vending machine operations. -
Can I customize the mini beverage vending machines to fit my brand?
Yes, many suppliers offer customization options for mini beverage vending machines. This can include branding with your logo, color schemes, and specific features such as product selection or payment methods. Discuss your requirements upfront to ensure the supplier can meet your needs. Be sure to inquire about any additional costs associated with customization and the impact on lead times. -
What is the typical minimum order quantity (MOQ) for these machines, and how does it affect pricing?
The MOQ for mini beverage vending machines varies by supplier, typically ranging from 5 to 50 units. Ordering in bulk can significantly reduce the per-unit cost, making it more economical for larger operations. If you have a lower budget, negotiate with suppliers for flexibility in MOQ or consider joining with other businesses to meet the quantity requirement. -
What are the lead times for receiving my order, and how can I expedite the process?
Lead times can vary based on supplier location, order size, and customization requirements, generally ranging from 4 to 12 weeks. To expedite the process, provide clear specifications and confirm your order promptly. Consider suppliers who maintain stock or offer quick-ship options. Communication is key; maintain regular contact with the supplier to monitor progress and address any potential delays. -
What quality assurance measures should I expect from suppliers?
Suppliers should implement rigorous quality assurance (QA) protocols, including inspections during manufacturing and pre-shipment. Request documentation of these QA processes, including test reports and certifications. Ensure that the machines are compliant with safety and health regulations relevant to your market, such as FDA or local health department standards, to avoid any legal issues. -
What payment terms are common in international transactions for vending machines?
Common payment terms include a deposit upfront (typically 30-50%) with the balance due before shipment. Some suppliers may offer letters of credit or escrow services to secure transactions. Always clarify payment methods accepted, such as bank transfers or online payment systems, and consider currency fluctuations in your budgeting to mitigate risks. -
How should I approach logistics and shipping for my vending machines?
Logistics for mini beverage vending machines involves coordinating shipping methods that suit your budget and timeline. Discuss with suppliers whether they handle shipping or if you need to arrange it. Consider freight forwarders familiar with handling vending machines to ensure proper packaging and handling. Be aware of import duties and taxes in your region that may affect the total cost. -
What steps can I take if a dispute arises with my supplier?
In case of a dispute, first attempt to resolve the issue amicably through direct communication. Document all correspondence and agreements. If necessary, refer to the terms outlined in your contract, which should include dispute resolution clauses such as mediation or arbitration. Consider involving a legal advisor experienced in international trade to navigate complex issues and protect your interests.
Strategic Sourcing Conclusion and Outlook for mini beverage vending machine
In conclusion, the strategic sourcing of mini beverage vending machines presents a significant opportunity for international B2B buyers, especially in diverse markets such as Africa, South America, the Middle East, and Europe. Key takeaways emphasize the importance of evaluating supplier capabilities, understanding local market dynamics, and leveraging technology for enhanced customer engagement. By prioritizing these factors, businesses can optimize their procurement processes, ensuring they select machines that align with consumer preferences and operational requirements.
The value of strategic sourcing cannot be overstated; it not only minimizes costs but also strengthens supply chain resilience and fosters innovation. Buyers should consider establishing long-term partnerships with manufacturers that demonstrate reliability and a commitment to quality.
Looking ahead, as the global market continues to evolve, the demand for mini beverage vending machines is set to rise. Now is the time for B2B buyers to act decisively—invest in modern vending solutions that cater to changing consumer habits and preferences. Embrace this opportunity to enhance your offerings and drive growth in your respective markets.