Your Ultimate Guide to Sourcing Medicine Vending Machine
Guide to Medicine Vending Machine
- Introduction: Navigating the Global Market for medicine vending machine
- Understanding medicine vending machine Types and Variations
- Key Industrial Applications of medicine vending machine
- Strategic Material Selection Guide for medicine vending machine
- In-depth Look: Manufacturing Processes and Quality Assurance for medicine vending machine
- Comprehensive Cost and Pricing Analysis for medicine vending machine Sourcing
- Spotlight on Potential medicine vending machine Manufacturers and Suppliers
- Essential Technical Properties and Trade Terminology for medicine vending machine
- Navigating Market Dynamics, Sourcing Trends, and Sustainability in the medicine vending machine Sector
- Frequently Asked Questions (FAQs) for B2B Buyers of medicine vending machine
- Strategic Sourcing Conclusion and Outlook for medicine vending machine
Introduction: Navigating the Global Market for medicine vending machine
As global healthcare systems evolve, medicine vending machines have emerged as a vital solution to enhance access to pharmaceuticals, particularly in underserved regions. These innovative devices not only offer convenience but also ensure the efficient distribution of essential medications, thereby addressing critical healthcare gaps in Africa, South America, the Middle East, and Europe. By integrating technology with healthcare, these machines facilitate timely access to medications, especially in areas where traditional pharmacies may be lacking.
This comprehensive guide delves into the multifaceted world of medicine vending machines, exploring various types and materials used in their construction, alongside insights into manufacturing and quality control processes. International B2B buyers will benefit from a thorough examination of potential suppliers, cost structures, and market trends, empowering them to make informed sourcing decisions. The guide also addresses frequently asked questions, providing clarity on operational aspects and best practices.
Understanding the intricacies of medicine vending machines is crucial for international buyers aiming to enhance their healthcare offerings. By leveraging the insights presented in this guide, stakeholders can navigate the global market effectively, ensuring they procure solutions that meet the unique needs of their respective regions. Whether you are a buyer from Argentina or Australia, this guide is designed to equip you with the knowledge necessary to capitalize on the growing demand for accessible healthcare solutions.
Understanding medicine vending machine Types and Variations
Type Name | Key Distinguishing Features | Primary B2B Applications | Brief Pros & Cons for Buyers |
---|---|---|---|
Automated Pharmacy Kiosks | Full-service dispensing, user-friendly interface | Hospitals, clinics, pharmacies | Pros: High convenience, reduces wait times. Cons: High initial cost. |
Over-the-Counter (OTC) Machines | Dispenses common medications and health products | Airports, supermarkets, gyms | Pros: Easy access for consumers. Cons: Limited product range. |
Prescription-Only Machines | Requires verification for medication dispensing | Hospitals, specialty clinics | Pros: Ensures compliance with regulations. Cons: Slower service. |
Mobile Medicine Vending Units | Portable, can be deployed in various locations | Events, outdoor festivals, remote areas | Pros: Flexibility and accessibility. Cons: Limited inventory space. |
Telehealth Integrated Machines | Combines telehealth consultations with dispensing | Rural clinics, underserved areas | Pros: Expands access to healthcare. Cons: Technology dependence. |
Automated Pharmacy Kiosks
Automated pharmacy kiosks are sophisticated machines that offer a full range of pharmaceutical services, including medication dispensing and patient consultations. These kiosks are ideal for hospitals, clinics, and pharmacies looking to enhance patient experience by minimizing wait times. When considering purchasing, buyers should evaluate the kiosk’s integration with existing pharmacy systems, maintenance requirements, and overall cost versus potential savings in labor and time.
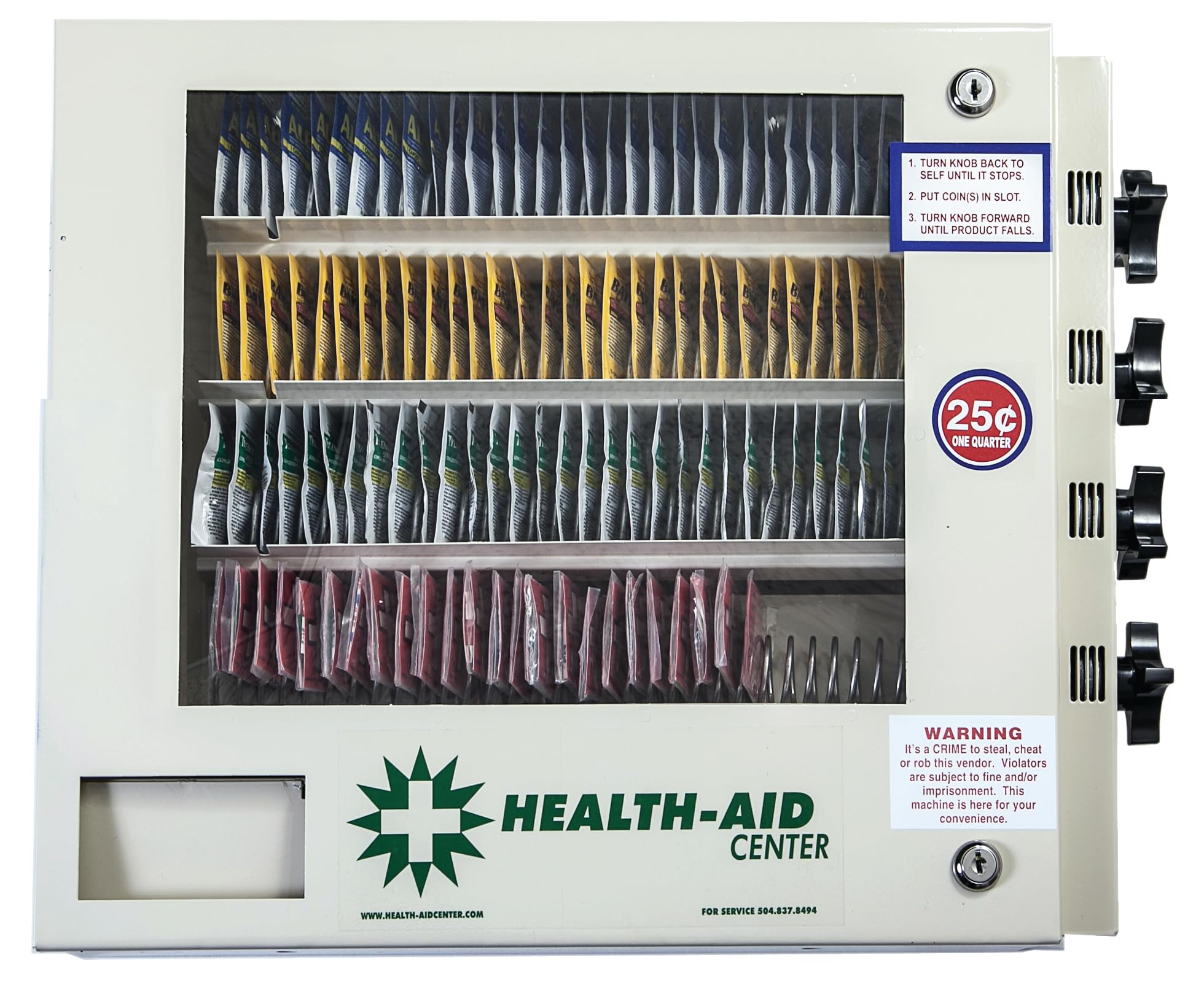
Illustrative Image (Source: Google Search)
Over-the-Counter (OTC) Machines
OTC medicine vending machines are designed to dispense readily available health products, such as pain relievers, cold medications, and personal care items. Commonly found in high-traffic areas like airports, supermarkets, and gyms, these machines cater to consumers seeking quick access to essential items. Buyers should consider the machine’s product range, pricing strategies, and the surrounding competition to ensure profitability.
Prescription-Only Machines
These machines are designed to dispense prescription medications after verifying the patient’s identity and prescription details, thus ensuring compliance with healthcare regulations. They are particularly suited for hospitals and specialty clinics where controlled access to medications is crucial. B2B buyers should assess the machine’s security features, user interface, and the integration capability with electronic health records to streamline operations.
Mobile Medicine Vending Units
Mobile medicine vending units provide flexibility by allowing healthcare providers to set up temporary locations for medication dispensing during events or in remote areas. These units are particularly useful for health fairs, outdoor festivals, or in regions lacking stable healthcare facilities. Buyers must evaluate the unit’s inventory capacity, transportation logistics, and the ability to maintain the required medication storage conditions.
Telehealth Integrated Machines
Telehealth integrated machines combine remote consultations with medication dispensing, making them an innovative solution for rural clinics and underserved areas. These machines enable patients to have virtual consultations before receiving medications, thus expanding healthcare access. Key considerations for B2B buyers include the reliability of the telehealth technology, patient privacy measures, and the machine’s ability to support various telehealth platforms.
Related Video: 24 Hour PPE Vending Machine OTC Medicine Vending Machine With Touch Screen
Key Industrial Applications of medicine vending machine
Industry/Sector | Specific Application of Medicine Vending Machine | Value/Benefit for the Business | Key Sourcing Considerations for this Application |
---|---|---|---|
Healthcare Facilities | Emergency medicine dispensing in hospitals | Quick access to critical medications, reducing wait times | Compliance with health regulations, secure payment systems |
Corporate Offices | On-site health support for employees | Enhances employee wellbeing and productivity | Stock management capabilities, variety of medications offered |
Educational Institutions | Student health services in universities and colleges | Convenient access to over-the-counter medicines | Vending machine size and placement, service and maintenance |
Remote Work Sites | Medicine access for workers in isolated locations | Ensures health safety and reduces downtime | Robustness for outdoor environments, inventory tracking |
Travel and Transportation | Medicine vending at airports and bus stations | Provides travelers with essential medications on-the-go | High visibility, multilingual interfaces, temperature control |
Healthcare Facilities
In hospitals, medicine vending machines are utilized to dispense emergency medications quickly, particularly in high-stress environments such as emergency rooms. This application addresses the critical need for rapid access to essential drugs, minimizing delays that could affect patient outcomes. International B2B buyers in this sector should prioritize machines that comply with local health regulations and ensure secure payment systems to maintain patient confidentiality and safety.
Corporate Offices
Corporate environments are increasingly adopting medicine vending machines to provide on-site health support for employees. These machines can dispense common over-the-counter medications such as pain relievers, cold remedies, and first-aid supplies. By improving access to healthcare products, companies can enhance employee wellbeing and productivity. Buyers should consider the variety of medications offered, stock management capabilities, and the machine’s ability to integrate with corporate wellness programs.
Educational Institutions
Universities and colleges are leveraging medicine vending machines to offer convenient health services to students. These machines typically dispense over-the-counter medications and first-aid supplies, helping students manage minor health issues without needing to visit a pharmacy. This application is particularly relevant in regions with high student populations, ensuring that healthcare access is readily available. Buyers must evaluate the machine’s size and placement within campus facilities, as well as service and maintenance options to ensure consistent operation.
Remote Work Sites
In remote work environments, such as construction sites or mining operations, medicine vending machines play a crucial role in ensuring that workers have immediate access to essential medications. This application helps to maintain health safety standards and minimizes downtime due to health-related issues. Buyers in these sectors should look for robust machines designed for outdoor conditions, as well as inventory tracking systems that keep essential supplies readily available.
Travel and Transportation
Airports and bus stations are ideal locations for medicine vending machines, providing travelers with easy access to necessary medications while on the go. These machines can alleviate the stress of managing health issues during travel, offering items like allergy medications, pain relievers, and first-aid supplies. When sourcing for this application, key considerations include high visibility to attract users, multilingual interfaces to accommodate diverse travelers, and temperature control to ensure medication efficacy.
Related Video: 24 HOURS medical need provide by Smart medicine vending machine
Strategic Material Selection Guide for medicine vending machine
When selecting materials for medicine vending machines, it is essential to consider their properties, advantages, disadvantages, and the specific needs of international B2B buyers. Below is an analysis of four common materials used in the construction of medicine vending machines.
1. Stainless Steel
Key Properties:
Stainless steel is known for its excellent corrosion resistance, high strength, and ability to withstand high temperatures and pressures. It is often rated for various environments, making it suitable for both indoor and outdoor applications.
Pros & Cons:
The durability of stainless steel is a significant advantage, as it can withstand wear and tear while maintaining its appearance. However, it can be more expensive than other materials, and its manufacturing process can be complex, requiring specialized equipment.
Impact on Application:
Stainless steel is compatible with a wide range of media, including various pharmaceuticals and cleaning agents, making it ideal for medicine vending machines. Its non-reactive nature ensures that it does not leach harmful substances into the medicines stored.
Considerations for International Buyers:
Buyers should ensure compliance with international standards such as ASTM A240 for stainless steel. Different regions may have specific grades preferred, such as 304 or 316 for enhanced corrosion resistance in humid environments.
2. Polycarbonate
Key Properties:
Polycarbonate is a lightweight, impact-resistant thermoplastic with good optical clarity. It can withstand a range of temperatures and has decent chemical resistance.
Pros & Cons:
Its lightweight nature makes polycarbonate easy to handle and install, reducing shipping costs. However, it is less durable than metals and can become brittle over time, especially when exposed to UV light.
Impact on Application:
Polycarbonate is often used for transparent panels in vending machines, allowing visibility of the products inside. Its chemical resistance makes it suitable for storing certain medicines, but it may not be appropriate for all types of pharmaceuticals.
Considerations for International Buyers:
Buyers should check for compliance with safety standards like ISO 9001. In regions with high UV exposure, such as parts of Africa and South America, UV-stabilized polycarbonate is recommended to prolong the material’s lifespan.
3. Aluminum
Key Properties:
Aluminum is lightweight, corrosion-resistant, and has good thermal conductivity. It is also relatively easy to machine and fabricate, making it a popular choice for various applications.
Pros & Cons:
The primary advantage of aluminum is its low weight, which can reduce transportation costs. However, it is less strong than stainless steel and may require protective coatings to enhance its corrosion resistance.
Impact on Application:
Aluminum is suitable for non-pressurized applications and can be used in the structural components of vending machines. It is compatible with many pharmaceuticals, but care must be taken to ensure that it does not react with certain medications.
Considerations for International Buyers:
Buyers should ensure that the aluminum used meets standards such as ASTM B221. In regions with high humidity, it is advisable to consider anodized aluminum for improved corrosion resistance.
4. Glass
Key Properties:
Glass is a rigid, non-porous material that is chemically inert and can withstand a wide range of temperatures. It is also transparent, allowing for visibility of the contents.
Pros & Cons:
Glass provides excellent protection against contamination and is easy to clean. However, it is fragile and can break easily, which may pose challenges in high-traffic environments.
Impact on Application:
Glass is commonly used for display panels in vending machines, ensuring that products are visible while being protected. Its inert nature makes it suitable for storing sensitive medications.
Considerations for International Buyers:
Buyers should consider the safety standards applicable in their region, such as EN 12150 for tempered glass. In markets where safety is a concern, such as the Middle East, using laminated glass can provide additional protection against breakage.
Summary Table
Material | Typical Use Case for medicine vending machine | Key Advantage | Key Disadvantage/Limitation | Relative Cost (Low/Med/High) |
---|---|---|---|---|
Stainless Steel | Structural components, exterior casing | Excellent durability and corrosion resistance | Higher cost, complex manufacturing | High |
Polycarbonate | Transparent panels for visibility | Lightweight and impact-resistant | Less durable, can become brittle | Medium |
Aluminum | Structural components, lightweight parts | Low weight, easy to fabricate | Less strength, may require coatings | Medium |
Glass | Display panels for product visibility | Chemically inert, easy to clean | Fragile, risk of breakage | Medium |
This guide provides valuable insights for international B2B buyers looking to select the appropriate materials for medicine vending machines, ensuring compliance with regional standards and addressing specific application needs.
In-depth Look: Manufacturing Processes and Quality Assurance for medicine vending machine
The manufacturing and quality assurance processes for medicine vending machines are critical for ensuring that these devices function reliably and safely in delivering pharmaceuticals. Below is a detailed overview of the typical manufacturing processes, quality control standards, and actionable insights for B2B buyers from various regions.
Manufacturing Processes
The manufacturing of medicine vending machines involves several key stages, each contributing to the overall functionality and safety of the final product.
1. Material Preparation
This initial stage involves sourcing high-quality materials that meet industry standards. Common materials include:
– Metals: Used for the frame and structural components, ensuring durability.
– Plastics: Employed for the casing and internal compartments, chosen for their resistance to chemicals and ease of cleaning.
– Electronic components: These include sensors, control panels, and payment systems, which must comply with electronic safety standards.
2. Forming
In this stage, raw materials are shaped into components through processes such as:
– Cutting: Metal and plastic sheets are cut to size.
– Molding: Plastics are molded into specific shapes for various parts of the machine.
– Welding: Metal components are welded together to form the machine’s frame.
3. Assembly
The assembly phase is where the machine begins to take shape. Key activities include:
– Component Integration: Electronic components, vending mechanisms, and storage units are assembled.
– Wiring: Electrical systems are installed, ensuring that all components are correctly connected for optimal performance.
– Software Installation: The machine’s operating system and user interface software are uploaded and configured.
4. Finishing
The final stage involves preparing the machine for market. This includes:
– Painting and Coating: To enhance durability and aesthetics, protective coatings are applied.
– Quality Checks: Before final assembly, each unit undergoes initial testing to ensure it meets design specifications.
Quality Assurance
Quality assurance is paramount in the manufacturing of medicine vending machines. It ensures that the final product is safe, reliable, and compliant with international regulations.
International Standards
B2B buyers should ensure that their suppliers adhere to relevant international standards, including:
– ISO 9001: This standard focuses on quality management systems and continuous improvement, ensuring consistent product quality.
– CE Marking: Required for products sold in the European Economic Area, indicating compliance with health, safety, and environmental protection standards.
– API Standards: For machines that dispense pharmaceuticals, adherence to standards set by the American Petroleum Institute ensures safety and efficacy.
Quality Control Checkpoints
Quality control processes typically include several checkpoints throughout the manufacturing process:
- Incoming Quality Control (IQC): Materials are inspected upon arrival to ensure they meet specified standards.
- In-Process Quality Control (IPQC): Continuous monitoring during manufacturing helps identify defects early in the process.
- Final Quality Control (FQC): A thorough inspection of the finished machine, including functionality tests, to ensure it meets all specifications.
Common Testing Methods
To verify the quality of the machines, several testing methods are employed:
– Functional Testing: Ensures that all features operate correctly.
– Stress Testing: Assesses the machine’s durability under simulated usage conditions.
– Electrical Safety Testing: Checks for compliance with electrical safety standards.
Verifying Supplier Quality Control
B2B buyers can take several steps to verify the quality control measures of potential suppliers:
- Conduct Audits: Regular audits can help assess the supplier’s adherence to quality standards and identify areas for improvement.
- Request Quality Reports: Suppliers should provide documentation demonstrating compliance with relevant standards and results from internal quality tests.
- Third-party Inspections: Engaging independent inspectors can provide an unbiased evaluation of the manufacturing processes and quality assurance measures.
Quality Control and Certification Nuances
For international B2B buyers, particularly those from Africa, South America, the Middle East, and Europe, understanding the nuances of quality control and certification is vital:
- Regional Regulations: Different regions may have specific regulations regarding medical devices. Buyers should familiarize themselves with local laws and requirements, such as those enforced by the South African Bureau of Standards (SABS) or the European Medicines Agency (EMA).
- Cultural Considerations: Engage with suppliers who understand the local market dynamics and can navigate the regulatory landscape effectively.
- Supplier Reputation: Investigate the supplier’s reputation in the market. Positive feedback from previous clients can be a strong indicator of reliability and quality.
Conclusion
In summary, the manufacturing processes and quality assurance for medicine vending machines involve meticulous planning, execution, and oversight. B2B buyers should prioritize suppliers who demonstrate robust quality control systems and compliance with international standards. By understanding these processes, buyers can make informed decisions that ensure they procure reliable and safe medicine vending machines, ultimately contributing to better healthcare delivery in their regions.
Related Video: SMART Quality Control for Manufacturing
Comprehensive Cost and Pricing Analysis for medicine vending machine Sourcing
When sourcing medicine vending machines, understanding the comprehensive cost structure and pricing dynamics is essential for international B2B buyers. This analysis covers the key components that influence costs, pricing, and strategies to optimize expenditure.
Cost Components
-
Materials: The primary component of the cost structure is the materials used in the manufacturing of vending machines. This includes the metal framework, electronic components, refrigeration systems, and specialized software. The choice of materials directly impacts durability, functionality, and cost.
-
Labor: Labor costs are variable and can differ significantly based on the region of production. In countries with higher labor costs, such as those in Europe, prices may be inflated compared to regions in South America or Africa where labor is generally cheaper.
-
Manufacturing Overhead: This encompasses all indirect costs associated with production, such as utilities, rent, and administrative expenses. Efficient manufacturing processes can help reduce these overheads, thus lowering the overall cost.
-
Tooling: Tooling refers to the expenses incurred in creating the molds and tools necessary for production. This is a fixed cost that can be amortized over large production runs, making it important to consider minimum order quantities (MOQs).
-
Quality Control (QC): Ensuring the machines meet industry standards and certifications is crucial. QC costs can vary based on the complexity of the machines and the regulatory requirements in different regions.
-
Logistics: Shipping and handling costs can significantly affect the total price. Factors such as distance, shipping method, and customs duties should be considered, especially when importing machines from regions like Europe to Africa or South America.
-
Margin: Suppliers typically add a profit margin on top of their costs. This margin can vary based on competition, brand reputation, and market demand.
Price Influencers
Several factors can influence the pricing of medicine vending machines:
-
Volume/MOQ: Larger orders often result in lower unit prices due to economies of scale. Buyers should negotiate MOQs to secure better pricing.
-
Specifications/Customization: Custom features such as payment systems, user interfaces, and specific drug storage capabilities can lead to increased costs. Clearly defining needs upfront can help manage these expenses.
-
Materials: The quality and type of materials selected can greatly affect pricing. Higher-quality components may lead to increased initial costs but could offer better longevity and performance.
-
Quality/Certifications: Machines that meet specific certifications (e.g., ISO, CE) may command higher prices due to the additional costs involved in compliance.
-
Supplier Factors: The reputation and reliability of the supplier can affect pricing. Established suppliers may charge a premium, but they often provide better after-sales support and warranty terms.
-
Incoterms: Understanding the terms of shipping and responsibilities for costs during transit can impact overall pricing. Buyers should clarify who is responsible for customs, insurance, and delivery.
Buyer Tips
-
Negotiation: Buyers should be prepared to negotiate prices, especially for bulk orders. Understanding the supplier’s cost structure can provide leverage during discussions.
-
Cost-Efficiency: Evaluate the total cost of ownership (TCO) rather than just the purchase price. Consider maintenance, operation costs, and energy efficiency when assessing value.
-
Pricing Nuances: International buyers should be aware of currency fluctuations, tariffs, and trade agreements that may affect prices. It’s prudent to factor in these elements during budgeting.
Disclaimer
The prices discussed in this analysis are indicative and may vary based on the specific requirements, supplier negotiations, and market conditions. Buyers are encouraged to conduct thorough market research and obtain multiple quotes to ensure competitive pricing.
Spotlight on Potential medicine vending machine Manufacturers and Suppliers
This section offers a look at a few manufacturers active in the ‘medicine vending machine’ market. This is a representative sample for illustrative purposes; B2B buyers must conduct their own extensive due diligence before any engagement. Information is synthesized from public sources and general industry knowledge.
Essential Technical Properties and Trade Terminology for medicine vending machine
Critical Specifications for Medicine Vending Machines
When considering a medicine vending machine, understanding its technical properties is crucial for ensuring it meets operational needs and regulatory standards. Here are some key specifications:
-
Material Grade
– Definition: The quality of materials used in the construction of the vending machine, typically stainless steel or high-grade plastic.
– B2B Importance: High-quality materials ensure durability and resistance to corrosion, which is vital for machines dispensing pharmaceuticals. This impacts maintenance costs and longevity, crucial for businesses operating in diverse environments. -
Temperature Control Range
– Definition: The operational range of temperatures that the vending machine can maintain, often between 2°C to 25°C for medications.
– B2B Importance: Proper temperature control is essential for preserving the efficacy of medicines. Buyers must ensure machines can maintain required temperatures to comply with health regulations and avoid product spoilage. -
Power Consumption
– Definition: The amount of energy the vending machine consumes during operation, measured in watts.
– B2B Importance: Understanding power consumption helps businesses calculate operational costs and assess the machine’s energy efficiency, which is increasingly important for sustainability-focused organizations. -
Capacity and Size
– Definition: The total number of items the vending machine can hold and its physical dimensions.
– B2B Importance: Capacity affects how often the machine needs to be restocked, influencing labor costs and service frequency. Size considerations are also crucial for placement in different environments, from hospitals to pharmacies. -
User Interface
– Definition: The design and functionality of the machine’s interface, including touchscreens, payment options, and multilingual support.
– B2B Importance: A user-friendly interface enhances customer experience and can reduce the need for customer service. For international markets, multilingual support is vital to cater to diverse populations. -
Security Features
– Definition: Mechanisms in place to prevent theft or tampering, such as locks, alarms, or surveillance systems.
– B2B Importance: Security is paramount for protecting valuable inventory, especially in areas with high foot traffic. Robust security features can also influence insurance costs and liability.
Common Trade Terminology
Familiarity with industry jargon is essential for effective communication and negotiation in the B2B market for medicine vending machines. Here are some common terms:
-
OEM (Original Equipment Manufacturer)
– Definition: A company that produces parts or equipment that may be marketed by another manufacturer.
– Relevance: Understanding OEM relationships can help buyers identify reputable suppliers and ensure quality components are used in machines. -
MOQ (Minimum Order Quantity)
– Definition: The smallest quantity of a product that a supplier is willing to sell.
– Relevance: Knowing the MOQ is essential for budgeting and inventory planning, especially for smaller businesses or startups. -
RFQ (Request for Quotation)
– Definition: A document issued by a buyer to solicit price quotes from suppliers for specific products.
– Relevance: An RFQ helps buyers compare prices and terms from different suppliers, enabling informed purchasing decisions. -
Incoterms (International Commercial Terms)
– Definition: A set of international trade terms that define responsibilities of buyers and sellers.
– Relevance: Familiarity with Incoterms is crucial for understanding shipping costs, responsibilities, and risks associated with international transactions. -
Lead Time
– Definition: The time taken from placing an order to the delivery of the product.
– Relevance: Understanding lead times is vital for planning inventory and ensuring timely availability of vending machines in the market. -
Warranty Period
– Definition: The duration during which the manufacturer is responsible for repairing or replacing defective parts.
– Relevance: A comprehensive warranty can provide peace of mind and reduce long-term maintenance costs, making it an important factor in purchasing decisions.
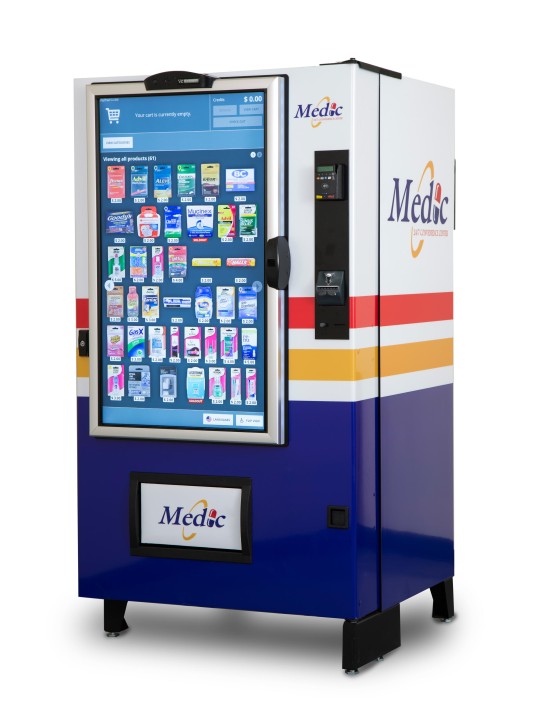
Illustrative Image (Source: Google Search)
By grasping these technical specifications and industry terms, international B2B buyers can make more informed decisions when investing in medicine vending machines, ultimately enhancing operational efficiency and compliance with health regulations.
Navigating Market Dynamics, Sourcing Trends, and Sustainability in the medicine vending machine Sector
Market Overview & Key Trends
The medicine vending machine sector is witnessing transformative growth driven by several global factors. The increasing need for accessible healthcare solutions, especially in underserved regions across Africa, South America, the Middle East, and Europe, is a primary driver. As urbanization accelerates, the demand for convenient, 24/7 access to medications is rising. This trend is particularly relevant for B2B buyers in the pharmaceutical and healthcare sectors, who must consider how these machines can enhance service delivery and patient outcomes.
Emerging technologies such as IoT (Internet of Things) are reshaping the landscape of medicine vending machines. Features like real-time inventory management, user-friendly interfaces, and enhanced security measures are becoming standard. B2B buyers should look for suppliers that incorporate these technologies to ensure efficiency and reliability. Furthermore, the integration of telehealth services with vending machines is a growing trend, allowing users to consult with pharmacists remotely before purchasing medications.
Market dynamics are also influenced by regulatory changes. In many regions, governments are promoting the use of vending machines to combat medication shortages and improve public health responses. Buyers should stay informed about local regulations that may affect the deployment of these machines. Additionally, as competition intensifies, the emphasis on customization and localization of offerings is crucial. B2B buyers should prioritize partnerships with suppliers that can tailor machines to meet the unique needs of their markets.
Sustainability & Ethical Sourcing in B2B
Sustainability is becoming increasingly important in the medicine vending machine sector. The environmental impact of production and disposal of these machines is significant, making it essential for B2B buyers to consider eco-friendly practices. Suppliers that use sustainable materials and processes can help mitigate environmental damage and enhance corporate social responsibility (CSR) efforts.
Ethical sourcing is equally vital. Buyers should seek suppliers that prioritize ethical supply chains, ensuring that materials are sourced responsibly and labor practices are fair. Certifications such as ISO 14001 for environmental management and Fair Trade can guide buyers in selecting vendors committed to sustainability. Additionally, using recyclable or biodegradable materials in machine construction can significantly reduce the ecological footprint.
Incorporating ‘green’ certifications into procurement strategies not only aids in compliance with increasing regulatory demands but also appeals to an environmentally conscious consumer base. By prioritizing sustainability and ethical sourcing, B2B buyers can enhance their brand reputation and foster customer loyalty.
Brief Evolution/History
The concept of vending machines dates back to the 1880s, but the evolution of medicine vending machines is a more recent phenomenon. Initially, these machines offered over-the-counter drugs, gradually expanding to include prescription medications as regulations evolved. The early 2000s marked a significant turning point with the integration of technology, allowing for more sophisticated machines capable of dispensing a wider range of healthcare products.
Today, medicine vending machines are increasingly equipped with features such as biometric authentication and telemedicine capabilities, reflecting the growing intersection of technology and healthcare. This evolution has not only improved accessibility but has also provided B2B buyers with innovative solutions to meet the demands of a rapidly changing market. Understanding this history helps buyers appreciate the advancements in technology and the potential for future developments in the sector.
Related Video: Global Trade & Logistics – What is Global Trade?
Frequently Asked Questions (FAQs) for B2B Buyers of medicine vending machine
-
What criteria should I use to vet suppliers of medicine vending machines?
When vetting suppliers, prioritize their experience in the industry, customer reviews, and compliance with local regulations. Request certifications such as ISO 9001 or CE marking to ensure quality standards. Evaluate their product range to see if they offer customization options and consider their after-sales support. It’s also beneficial to visit their facilities or request virtual tours to assess their manufacturing capabilities and commitment to quality. -
Can I customize the medicine vending machines according to my market needs?
Yes, many suppliers offer customization options for medicine vending machines. This can include tailored software, branding, and specific medicine selections based on local demand. Before finalizing your order, discuss your requirements with the supplier to ensure they can meet your specifications. Look for suppliers who have experience working with clients in your region, as they may better understand local needs. -
What is the minimum order quantity (MOQ) for medicine vending machines, and what are typical lead times?
MOQs can vary significantly among suppliers, typically ranging from 1 to 10 units for initial orders. Larger orders may have lower MOQs. Lead times can also differ based on customization and supplier location, generally ranging from 4 to 12 weeks. Always confirm these details before placing an order to avoid unexpected delays and ensure timely delivery to your market. -
What payment terms should I expect when sourcing medicine vending machines?
Payment terms will vary by supplier but commonly include options like a 30% deposit upon order confirmation and the remaining balance before shipment. Some suppliers may offer letters of credit or payment through escrow services for added security. It’s essential to clarify payment methods and timelines upfront to align expectations and avoid disputes later in the transaction process. -
How can I ensure quality assurance and certification for the machines I purchase?
Ensure the supplier provides detailed documentation of their quality assurance processes and certifications. Look for compliance with international standards, such as ISO 13485 for medical devices. Request samples before bulk orders to test machine performance and reliability. Additionally, consider third-party inspections to verify that the machines meet the agreed-upon specifications and quality standards. -
What logistics considerations should I keep in mind when importing medicine vending machines?
Logistics can be complex when importing machinery. Ensure you understand shipping costs, import duties, and local regulations regarding medical devices. Work with experienced freight forwarders who can handle customs clearance and provide guidance on documentation required for import. Establish a timeline for delivery that includes buffer periods for potential delays in shipping or customs processing. -
What should I do if a dispute arises with my supplier?
In the event of a dispute, first attempt to resolve the issue directly with the supplier through open communication. If that fails, refer to the contract terms regarding dispute resolution. Mediation or arbitration can be effective alternatives to litigation. Consider including a clause in your contract that outlines the dispute resolution process to minimize complications later. -
How do I assess the market demand for medicine vending machines in my region?
Conduct thorough market research to identify local healthcare needs and consumer behavior regarding medication access. Analyze competitors and existing vending machine models to gauge their success. Engaging with local pharmacies, hospitals, and healthcare professionals can provide valuable insights. Additionally, consider pilot programs or focus groups to test the market before making large investments in vending machines.
Strategic Sourcing Conclusion and Outlook for medicine vending machine
In conclusion, the strategic sourcing of medicine vending machines presents a transformative opportunity for B2B buyers across diverse regions, including Africa, South America, the Middle East, and Europe. By leveraging these automated solutions, businesses can enhance accessibility to essential medications while optimizing operational efficiencies. Key takeaways include the importance of selecting reliable suppliers that prioritize compliance with local health regulations, as well as the need for robust maintenance plans to ensure uninterrupted service.
The value of strategic sourcing cannot be overstated; it not only reduces costs but also fosters long-term partnerships that can enhance innovation and service delivery. As global health challenges continue to evolve, the demand for convenient access to medications will only increase.
International B2B buyers are encouraged to take proactive steps now—assess your current health service delivery methods, explore available technology, and engage with reputable vendors to position your business at the forefront of this evolving market. Embrace the future of healthcare distribution with medicine vending machines, and make a lasting impact on your community’s health and wellbeing.