Your Ultimate Guide to Sourcing Inventory Vending Machine
Guide to Inventory Vending Machine
- Introduction: Navigating the Global Market for inventory vending machine
- Understanding inventory vending machine Types and Variations
- Key Industrial Applications of inventory vending machine
- Strategic Material Selection Guide for inventory vending machine
- In-depth Look: Manufacturing Processes and Quality Assurance for inventory vending machine
- Comprehensive Cost and Pricing Analysis for inventory vending machine Sourcing
- Spotlight on Potential inventory vending machine Manufacturers and Suppliers
- Essential Technical Properties and Trade Terminology for inventory vending machine
- Navigating Market Dynamics, Sourcing Trends, and Sustainability in the inventory vending machine Sector
- Frequently Asked Questions (FAQs) for B2B Buyers of inventory vending machine
- Strategic Sourcing Conclusion and Outlook for inventory vending machine
Introduction: Navigating the Global Market for inventory vending machine
In today’s fast-paced global economy, inventory vending machines have emerged as a vital asset for businesses seeking efficient inventory management and enhanced customer service. These automated solutions not only streamline the supply chain by providing real-time access to products but also reduce overhead costs, making them an attractive option for diverse industries ranging from manufacturing to retail. For international B2B buyers, particularly those in Africa, South America, the Middle East, and Europe, understanding the intricacies of inventory vending machines is essential for making informed purchasing decisions.
This comprehensive guide will explore various aspects of inventory vending machines, including their types—from traditional models to advanced smart machines—materials used in manufacturing, and the critical importance of quality control in ensuring longevity and reliability. Additionally, buyers will benefit from insights into suppliers and their capabilities, cost considerations, and an analysis of current market trends.
Moreover, the guide will address common FAQs, demystifying the complexities surrounding these machines. By empowering B2B buyers with detailed knowledge and actionable insights, this resource aims to facilitate strategic sourcing decisions, ultimately enhancing operational efficiency and customer satisfaction. Whether you are in Colombia, Turkey, or any other global market, navigating the landscape of inventory vending machines will position your business for success in an increasingly competitive environment.
Understanding inventory vending machine Types and Variations
Type Name | Key Distinguishing Features | Primary B2B Applications | Brief Pros & Cons for Buyers |
---|---|---|---|
Traditional Vending Machines | Standard design with mechanical dispensing systems | Office break rooms, schools, hospitals | Pros: Familiarity, easy maintenance. Cons: Limited product range, slower technology. |
Smart Vending Machines | Equipped with touchscreen interfaces and IoT capabilities | Retail environments, tech-savvy locations | Pros: Enhanced user experience, real-time inventory tracking. Cons: Higher initial cost, requires tech support. |
Automated Inventory Dispensers | Focused on dispensing specific items like tools or parts | Manufacturing, warehouses, laboratories | Pros: Increased efficiency, precise inventory control. Cons: Limited to specific applications, higher complexity. |
Mobile Vending Solutions | Portable units that can be relocated easily | Events, construction sites, festivals | Pros: Flexibility, can serve various locations. Cons: May lack the full range of products compared to fixed units. |
Cold Beverage Vending Machines | Specially designed for chilled drinks | Cafes, offices, gyms | Pros: Attracts impulse purchases, maintains product quality. Cons: Higher energy costs, requires regular maintenance. |
Traditional Vending Machines
Traditional vending machines are the most recognizable type, featuring a mechanical dispensing system that offers snacks, beverages, and other convenience items. These machines are commonly found in office break rooms, schools, and hospitals. Buyers appreciate their straightforward design and ease of maintenance, but they may find the limited product range and slower dispensing technology a drawback, especially in high-traffic areas.
Smart Vending Machines
Smart vending machines integrate advanced technology, including touchscreen interfaces and IoT capabilities, allowing for a more interactive user experience. These machines are ideal for retail environments and tech-savvy locations where enhanced customer engagement is crucial. While they provide real-time inventory tracking and analytics, the higher initial investment and need for ongoing technical support can be a concern for some buyers.
Automated Inventory Dispensers
Automated inventory dispensers are designed specifically for dispensing tools, parts, or other specialized items in sectors like manufacturing, warehouses, and laboratories. These machines offer increased efficiency and precise inventory control, reducing waste and improving operational productivity. However, their complexity and limited application scope may deter some buyers who require more versatile solutions.
Mobile Vending Solutions
Mobile vending solutions are portable units that can be relocated to various locations, making them ideal for events, construction sites, and festivals. Their flexibility allows businesses to reach customers in multiple venues, enhancing sales opportunities. However, these machines may not offer the same extensive product range as fixed installations, potentially limiting their effectiveness in some scenarios.
Cold Beverage Vending Machines
Cold beverage vending machines are specifically designed to dispense chilled drinks, making them popular in cafes, offices, and gyms. They attract impulse purchases by providing immediate access to refreshing beverages while maintaining product quality through temperature control. Buyers should consider the higher energy costs and the need for regular maintenance, which can impact overall profitability.
Related Video: Pros And Cons Of Starting A Vending Machine Business
Key Industrial Applications of inventory vending machine
Industry/Sector | Specific Application of inventory vending machine | Value/Benefit for the Business | Key Sourcing Considerations for this Application |
---|---|---|---|
Manufacturing | Spare parts vending for production lines | Reduces downtime, ensures immediate access to parts | Size and capacity, integration with existing systems |
Construction | Tools and equipment dispensing | Streamlines workflow, minimizes tool loss | Durability, outdoor suitability, inventory management |
Healthcare | Medical supplies dispensing | Enhances patient care, reduces waste | Compliance with health regulations, security features |
Retail | Consumer goods vending | Increases sales opportunities, enhances customer experience | Payment options, product variety, location placement |
Automotive | Automotive parts vending | Improves service efficiency, reduces inventory costs | Compatibility with parts, real-time inventory tracking |
Manufacturing
In the manufacturing sector, inventory vending machines are utilized for dispensing spare parts directly to production lines. This application significantly reduces equipment downtime by ensuring immediate access to necessary components, which is crucial for maintaining productivity. Buyers in this sector must consider the machine’s size and capacity, as well as its ability to integrate with existing inventory management systems for seamless operation.
Construction
Construction sites often face challenges with tool availability and loss. Inventory vending machines can dispense tools and equipment on-site, streamlining workflows and minimizing the risk of tool theft or misplacement. For international buyers, particularly in regions like Africa and South America, sourcing machines that are durable and suitable for outdoor conditions is essential. Additionally, effective inventory management features can help track tool usage and availability.
Healthcare
In healthcare settings, inventory vending machines can dispense essential medical supplies, such as gloves, syringes, and personal protective equipment (PPE). This application enhances patient care by ensuring that healthcare professionals have immediate access to necessary items while also reducing waste through better inventory control. Buyers should prioritize machines that comply with health regulations and feature robust security systems to prevent unauthorized access.
Retail
Retail environments can leverage inventory vending machines to offer consumer goods, enhancing customer experience and increasing sales opportunities. These machines can be strategically placed in high-traffic areas to attract customers. Key considerations for buyers in this sector include diverse payment options, the variety of products offered, and the machine’s placement to maximize visibility and accessibility.
Automotive
In the automotive industry, inventory vending machines can dispense automotive parts and tools, improving service efficiency in repair shops and dealerships. This application not only reduces inventory costs but also ensures that technicians have quick access to the parts they need. International buyers should focus on sourcing machines that are compatible with a wide range of automotive parts and offer real-time inventory tracking to manage stock effectively.
Related Video: How to Start a Vending Machine Business, Cost, Tips, How Much You Make
Strategic Material Selection Guide for inventory vending machine
When selecting materials for inventory vending machines, international B2B buyers must consider several factors that impact performance, durability, and compliance with regional standards. Below is an analysis of four common materials used in the construction of inventory vending machines, focusing on their properties, advantages, disadvantages, and specific considerations for buyers from Africa, South America, the Middle East, and Europe.
1. Stainless Steel
Key Properties:
Stainless steel is known for its excellent corrosion resistance, high strength, and ability to withstand a range of temperatures. It is often rated for high-pressure applications, making it suitable for various environments.
Pros & Cons:
– Advantages: Durable, resistant to corrosion, and easy to clean, which is crucial for maintaining hygiene in vending machines.
– Disadvantages: Higher initial costs compared to other materials and can be more challenging to machine, leading to increased manufacturing complexity.
Impact on Application:
Stainless steel is compatible with a wide range of media, including food and beverages, making it ideal for vending machines that dispense consumables.
Considerations for International Buyers:
Compliance with food safety standards (e.g., FDA in the U.S. or EFSA in Europe) is essential. Buyers should verify that the stainless steel meets relevant standards such as ASTM A240 or EN 10088.
2. Carbon Steel
Key Properties:
Carbon steel is characterized by its high strength and toughness. It is suitable for structural components of vending machines but requires protective coatings to prevent rust.
Pros & Cons:
– Advantages: Cost-effective and readily available, making it a popular choice for budget-conscious projects.
– Disadvantages: Susceptible to corrosion if not properly coated, which can lead to maintenance issues over time.
Impact on Application:
While suitable for non-corrosive environments, carbon steel may not be ideal for machines exposed to moisture or harsh chemicals.
Considerations for International Buyers:
Buyers should ensure that the carbon steel used complies with standards like ASTM A36 or EN 10025. Additionally, they should consider the availability of protective coatings in their region.
3. Aluminum
Key Properties:
Aluminum is lightweight, corrosion-resistant, and has good thermal conductivity. It is often used for components that require a balance of strength and weight.
Pros & Cons:
– Advantages: Lightweight, making it easier to transport and install, and generally more resistant to corrosion than carbon steel.
– Disadvantages: Lower strength compared to stainless steel and can be more expensive than carbon steel.
Impact on Application:
Aluminum is suitable for a variety of applications, including machines that dispense snacks and beverages, where weight savings are beneficial.
Considerations for International Buyers:
Buyers should check for compliance with standards such as ASTM B221 for aluminum extrusions and ensure that the alloy used is appropriate for their specific application.
4. Polycarbonate
Key Properties:
Polycarbonate is a high-performance plastic known for its impact resistance and transparency. It is often used for protective covers and components in vending machines.
Pros & Cons:
– Advantages: Lightweight, shatter-resistant, and allows for visibility of the products inside the machine.
– Disadvantages: Less heat resistant than metals and can be prone to scratching.
Impact on Application:
Polycarbonate is ideal for front panels or windows in vending machines, providing visibility while protecting the contents.
Considerations for International Buyers:
Buyers should ensure that the polycarbonate used meets relevant safety and quality standards, such as ISO 9001, and consider the environmental impact of plastic materials in their regions.
Material | Typical Use Case for inventory vending machine | Key Advantage | Key Disadvantage/Limitation | Relative Cost (Low/Med/High) |
---|---|---|---|---|
Stainless Steel | Structural components, food/beverage dispensing | Excellent corrosion resistance | Higher initial costs | High |
Carbon Steel | Structural frames, non-corrosive environments | Cost-effective | Susceptible to corrosion | Low |
Aluminum | Lightweight components, visibility panels | Lightweight and corrosion-resistant | Lower strength than stainless steel | Medium |
Polycarbonate | Protective covers, visibility panels | Shatter-resistant and transparent | Less heat resistant, prone to scratches | Medium |
This guide provides a strategic overview of material selection for inventory vending machines, emphasizing the need for compliance with regional standards and the importance of understanding the specific applications and environments in which these machines will operate.
In-depth Look: Manufacturing Processes and Quality Assurance for inventory vending machine
Manufacturing Processes for Inventory Vending Machines
The manufacturing process of inventory vending machines involves several key stages, each critical to ensuring the final product meets quality and performance standards. Understanding these stages can help B2B buyers from Africa, South America, the Middle East, and Europe make informed purchasing decisions.
Main Stages of Manufacturing
-
Material Preparation
– The first step involves sourcing high-quality raw materials, typically including metals like steel and aluminum, plastics, and electronic components.
– Key Techniques: Advanced material handling systems and inventory management software are employed to ensure materials are available and to minimize waste. -
Forming
– This stage encompasses various processes such as cutting, bending, and welding. For example, metal sheets are cut to size and then bent into the desired shape for the machine casing.
– Key Techniques: CNC (Computer Numerical Control) machines are commonly used for precision cutting and shaping, ensuring uniformity and reducing human error. -
Assembly
– In this stage, the formed components are assembled. This includes the integration of electronic systems, user interfaces, and mechanical parts.
– Key Techniques: Automated assembly lines may be utilized alongside manual assembly to balance efficiency and craftsmanship. Robotics can play a role in improving accuracy and speed during this phase. -
Finishing
– The final stage involves surface treatments, painting, and the application of decals or branding. This not only enhances the aesthetic appeal but also provides corrosion resistance.
– Key Techniques: Powder coating and electroplating are popular finishing methods that offer durability and a professional look.
Quality Assurance in Manufacturing
Quality assurance (QA) is integral to the production of inventory vending machines, ensuring that each unit meets international standards and customer expectations.
International Standards
- ISO 9001: This standard outlines criteria for a quality management system, emphasizing a process-based approach to enhance customer satisfaction.
- CE Marking: Required for products sold within the European Economic Area, indicating conformity with health, safety, and environmental protection standards.
- API Standards: Relevant for machines that might be used in the oil and gas sectors, ensuring safety and reliability.
Quality Control Checkpoints
-
Incoming Quality Control (IQC)
– Incoming materials are inspected for defects and compliance with specifications. This involves visual inspections and material testing. -
In-Process Quality Control (IPQC)
– Ongoing checks during the manufacturing process help identify issues early. This can include measurements of component dimensions and functional tests of assemblies. -
Final Quality Control (FQC)
– Before shipping, the finished vending machines undergo a comprehensive inspection. This may include performance testing, safety checks, and verification of features.
Common Testing Methods
- Functional Testing: Ensures that all features of the vending machine operate correctly.
- Stress Testing: Assesses durability under extreme conditions to simulate long-term usage.
- Safety Testing: Verifies compliance with safety standards, crucial for protecting end-users.
How B2B Buyers Can Verify Supplier Quality Control
For international B2B buyers, particularly those from regions like Africa, South America, the Middle East, and Europe, verifying a supplier’s quality control processes is essential. Here are actionable steps:
-
Supplier Audits
– Conduct on-site audits to assess manufacturing capabilities and quality assurance practices. This provides insights into the supplier’s operations and commitment to quality. -
Request Quality Reports
– Suppliers should provide documentation of their quality control processes, including results from IQC, IPQC, and FQC phases. Look for trends in defect rates and corrective actions taken. -
Third-Party Inspections
– Engage third-party inspection services to independently verify compliance with international standards. This can add an additional layer of assurance regarding the quality of the products.
Quality Control and Certification Nuances for International Buyers
When sourcing inventory vending machines, B2B buyers should be aware of the following nuances:
- Regional Compliance: Different regions have unique regulations that affect product certification. For instance, CE marking is essential for European markets, while UL certification may be necessary for North American buyers.
- Cultural Considerations: Understanding the cultural context of suppliers can enhance communication and collaboration, especially in regions with different business practices.
- Post-Sale Support: Ensure that suppliers offer robust post-sale support, including warranty terms and service agreements, which can be critical for maintaining operational efficiency.
By familiarizing themselves with these manufacturing processes and quality assurance practices, B2B buyers can make informed decisions, ensuring they partner with reliable suppliers who meet their quality expectations.
Related Video: Lean Manufacturing – Lean Factory Tour – FastCap
Comprehensive Cost and Pricing Analysis for inventory vending machine Sourcing
When sourcing inventory vending machines, understanding the comprehensive cost structure and pricing analysis is crucial for international B2B buyers. This analysis will help you make informed decisions, optimize costs, and effectively negotiate with suppliers.
Cost Components
-
Materials: The primary materials for vending machines include metals, plastics, electronic components, and glass. Prices can vary significantly based on quality and specifications. Sustainable materials may incur higher costs but can appeal to environmentally conscious consumers.
-
Labor: Labor costs depend on the region of manufacturing. In countries with lower labor costs, such as parts of Africa and South America, you may find competitive pricing. However, consider the potential trade-offs in quality and compliance with international standards.
-
Manufacturing Overhead: This encompasses costs related to factory operations, including utilities, rent, and administrative expenses. Overhead can be a significant factor in the total cost, particularly in regions with high operational costs.
-
Tooling: Custom tooling for specific designs can add substantial upfront costs. However, investing in tooling can lead to cost efficiencies in mass production, especially for high-volume orders.
- Quality Control (QC): Implementing robust quality control measures is essential to ensure product reliability. QC costs can include testing, inspections, and certifications, which may vary depending on the industry standards and regulatory requirements.
-
Logistics: Shipping and handling costs can fluctuate based on the origin of the machine, destination, and chosen transportation method. It’s vital to account for these costs in your total budget, especially when importing from distant suppliers.
-
Margin: Supplier margins can vary widely based on their market position and competitive strategy. Understanding the typical margins in your target markets can aid in negotiation.
Price Influencers
-
Volume/MOQ (Minimum Order Quantity): Larger orders often lead to reduced per-unit costs. Buyers should negotiate for favorable terms, especially if they can commit to higher volumes.
-
Specifications and Customization: Customized machines tailored to specific operational needs can significantly influence costs. While customization may increase the price, it can enhance functionality and user experience.
-
Materials and Quality Certifications: Higher quality materials and certifications (like ISO or CE) can raise costs but may also enhance the machine’s durability and compliance with local regulations.
-
Supplier Factors: The supplier’s reputation, experience, and location can impact pricing. Established suppliers may charge more due to perceived reliability and service quality.
-
Incoterms: Understanding Incoterms (International Commercial Terms) is crucial. They determine who is responsible for shipping, insurance, and tariffs, affecting the overall cost and risk associated with the purchase.
Buyer Tips
-
Negotiation: Leverage your position as a buyer by comparing multiple suppliers. Don’t hesitate to negotiate terms and prices, especially when placing bulk orders.
-
Cost-Efficiency: Focus on the total cost of ownership (TCO), not just the purchase price. Consider long-term operational costs, maintenance, and energy efficiency when evaluating options.
-
Pricing Nuances: Be aware of regional pricing variations. For example, sourcing from suppliers in Africa or South America may offer lower base prices, but consider potential logistics challenges and delays.
-
Quality Assurance: Prioritize suppliers who can provide quality assurance and after-sales support. This can mitigate risks associated with machine performance and longevity.
Disclaimer
Prices for inventory vending machines can vary widely based on the aforementioned factors. It is advisable to conduct thorough market research and obtain multiple quotes to ensure competitive pricing tailored to your specific needs.
Spotlight on Potential inventory vending machine Manufacturers and Suppliers
This section offers a look at a few manufacturers active in the ‘inventory vending machine’ market. This is a representative sample for illustrative purposes; B2B buyers must conduct their own extensive due diligence before any engagement. Information is synthesized from public sources and general industry knowledge.
Essential Technical Properties and Trade Terminology for inventory vending machine
Key Technical Properties of Inventory Vending Machines
When considering an investment in inventory vending machines, understanding their technical specifications is crucial for making informed purchasing decisions. Here are several key properties that B2B buyers should focus on:
-
Material Grade: The materials used in vending machines, such as stainless steel or high-grade plastic, directly affect durability and maintenance costs. Stainless steel, for example, offers resistance to corrosion and wear, making it ideal for high-traffic environments. Buyers should assess the material grade to ensure longevity and reduced operational costs.
-
Capacity: This refers to the volume or number of items the vending machine can hold. A larger capacity may be beneficial for businesses with high demand, while smaller machines may be more suitable for niche products. Understanding capacity helps buyers gauge how often they will need to restock, impacting labor and logistics.
-
Power Consumption: Vending machines vary in energy efficiency. Machines that consume less power can lead to significant savings over time, particularly in regions where electricity costs are high. Buyers should inquire about energy ratings and operational costs to optimize their budget.
-
User Interface: The ease of use of the machine’s interface can affect customer satisfaction and sales. Machines equipped with touch screens and multiple language options can cater to a diverse clientele, increasing user engagement. Buyers should prioritize user-friendly designs to enhance customer experience.
-
Connectivity Features: Modern vending machines often include connectivity options such as IoT capabilities, allowing for real-time inventory tracking and remote management. This feature can streamline operations and improve inventory control, making it a critical consideration for B2B buyers looking to optimize supply chains.
-
Security Features: Given that vending machines often hold valuable inventory, security is paramount. Features such as reinforced locks, surveillance cameras, and alarm systems can deter theft. Buyers should evaluate the security measures in place to protect their investments.
Common Trade Terminology
Understanding industry jargon is essential for effective communication and negotiation in B2B transactions. Here are several common terms related to inventory vending machines:
-
OEM (Original Equipment Manufacturer): This term refers to companies that produce parts or equipment that may be marketed by another manufacturer. For buyers, partnering with an OEM can ensure high-quality components tailored for specific vending machine models.
-
MOQ (Minimum Order Quantity): This is the smallest number of units that a supplier is willing to sell. Understanding MOQ is essential for buyers to evaluate the feasibility of stocking certain products. It can also impact cash flow and inventory management strategies.
-
RFQ (Request for Quotation): An RFQ is a document sent to suppliers to request pricing and availability for specific products or services. For B2B buyers, issuing an RFQ is a strategic way to compare offers and negotiate better terms.
-
Incoterms: These are international commercial terms that define the responsibilities of buyers and sellers in global trade. Familiarity with terms such as FOB (Free on Board) and CIF (Cost, Insurance, and Freight) can help buyers understand shipping costs and risks involved in transactions.
-
Lead Time: This refers to the amount of time it takes from placing an order to receiving the product. Knowing the lead time is vital for inventory planning, especially for businesses that require consistent stock levels to meet customer demand.
-
Warranty: A warranty is a guarantee provided by the manufacturer regarding the condition of the product and the commitment to repair or replace it within a specified period. Buyers should carefully review warranty terms to ensure adequate protection for their investment.
By understanding these technical properties and trade terms, B2B buyers can make informed decisions that optimize their investment in inventory vending machines, ultimately enhancing operational efficiency and profitability.
Navigating Market Dynamics, Sourcing Trends, and Sustainability in the inventory vending machine Sector
Market Overview & Key Trends
The inventory vending machine sector is currently experiencing significant growth driven by several global factors. Increasing urbanization, particularly in regions like Africa and South America, is pushing demand for convenient access to goods. Additionally, the rise of e-commerce has led to a growing expectation for on-demand services, with vending machines serving as an effective solution for businesses looking to enhance their distribution channels.
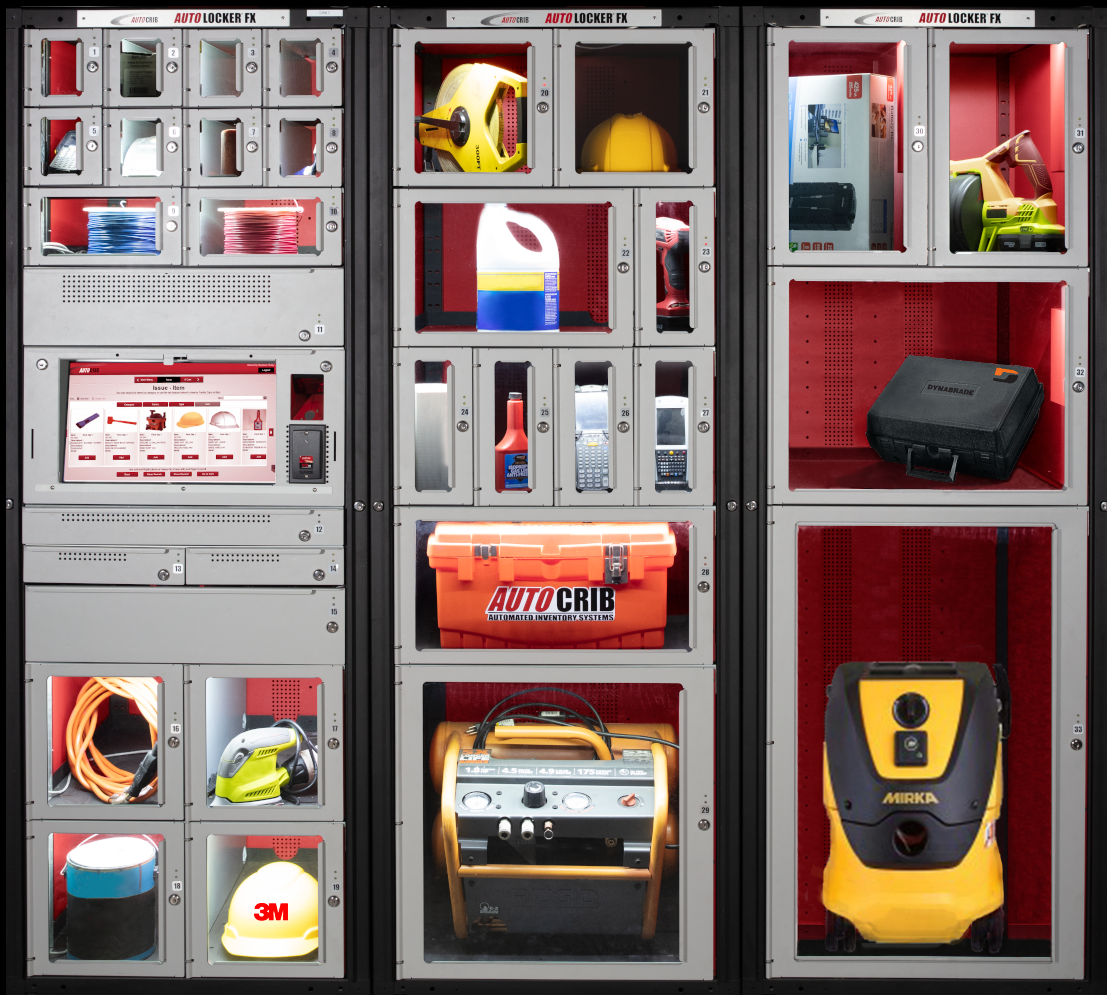
Illustrative Image (Source: Google Search)
Emerging technologies such as IoT (Internet of Things) are reshaping the functionality of vending machines. International B2B buyers should be aware of trends such as cashless payment systems, real-time inventory tracking, and machine learning capabilities that optimize stock levels based on consumer behavior. For buyers in regions like Turkey and Colombia, leveraging these technologies can improve operational efficiency and customer satisfaction.
Moreover, sustainability is becoming a crucial consideration. Buyers are increasingly looking for machines that utilize eco-friendly materials and energy-efficient designs. As the market dynamics shift, companies that prioritize innovation and sustainability will likely gain a competitive edge, making it essential for international buyers to align their sourcing strategies accordingly.
Sustainability & Ethical Sourcing in B2B
Sustainability in the inventory vending machine sector is not merely a trend; it is becoming a necessity. Environmental impacts associated with traditional manufacturing processes and materials are prompting businesses to seek out greener alternatives. For B2B buyers, this means sourcing machines made from recyclable materials and those designed for energy efficiency.
Ethical sourcing practices are equally important. Buyers should consider suppliers that demonstrate transparency in their supply chains, ensuring that materials are sourced responsibly. This includes certifications such as ISO 14001 for environmental management systems, which indicate a commitment to reducing environmental impact.
Investing in “green” certified products not only enhances brand reputation but also meets the growing consumer demand for environmentally responsible practices. By prioritizing sustainability and ethical sourcing, B2B buyers can contribute to a more sustainable future while also appealing to a conscientious customer base.
Brief Evolution/History
The concept of vending machines dates back to ancient times, but the modern inventory vending machine has evolved significantly since its inception. Initially, these machines dispensed simple items like cigarettes and candies. However, advancements in technology have transformed them into sophisticated units capable of handling a wide range of products, including electronics and healthy food options.
In recent years, the focus has shifted towards integrating smart technology and enhancing user experiences. The rise of touchless payment options and data analytics has made vending machines more efficient and user-friendly, catering to the evolving needs of consumers. For B2B buyers, understanding this evolution is crucial for making informed purchasing decisions that align with current market demands.
Related Video: Global Trade & Logistics – What is Global Trade?
Frequently Asked Questions (FAQs) for B2B Buyers of inventory vending machine
-
What criteria should I use to vet suppliers of inventory vending machines?
When vetting suppliers, consider their industry experience, reputation, and customer reviews. Verify their certifications and compliance with international standards, especially if you’re sourcing from regions with different regulations. Request case studies or references from previous clients to assess their reliability. Additionally, evaluate their production capabilities, lead times, and after-sales support to ensure they can meet your business needs. -
Can I customize the inventory vending machines to fit my specific requirements?
Yes, many manufacturers offer customization options for inventory vending machines. You can request modifications in terms of size, design, and functionality to align with your brand and operational needs. Discuss your requirements with the supplier early in the negotiation process to understand the extent of customization available and any associated costs. Ensure that any agreed-upon specifications are documented to avoid misunderstandings later. -
What is the minimum order quantity (MOQ) for purchasing inventory vending machines?
MOQs can vary significantly by supplier and machine type. Some manufacturers may require a minimum order of five to ten units, while others might be more flexible, especially for first-time buyers. It’s essential to discuss MOQs upfront and consider negotiating terms that suit your budget and business model. If you’re uncertain about your needs, consider starting with a smaller order to test the market before committing to larger quantities. -
What are the typical lead times for delivery of inventory vending machines?
Lead times can range from a few weeks to several months, depending on the supplier’s production capacity, your order size, and the complexity of any customizations. It is crucial to communicate your timeline requirements clearly when placing your order. Additionally, consider potential delays related to logistics, especially if shipping internationally. Always ask for a detailed timeline and maintain regular communication with the supplier to stay updated on your order status. -
What quality assurance measures should I expect from suppliers?
Reputable suppliers will have established quality assurance (QA) processes to ensure their machines meet industry standards. Expect them to provide certifications such as ISO 9001 or CE marking, which indicate compliance with quality management systems and safety regulations. Request information on their testing procedures, warranty policies, and return processes to ensure you are protected in case of defects or malfunctions. -
How do I handle payment and financial transactions with international suppliers?
When dealing with international suppliers, consider secure payment methods such as letters of credit, PayPal, or escrow services to mitigate risks. Discuss payment terms upfront, including deposits and final payments, and ensure you have a clear invoice detailing all costs. Be aware of currency exchange rates and any additional fees related to international transactions. Establishing a good relationship with your supplier can also facilitate smoother financial dealings.
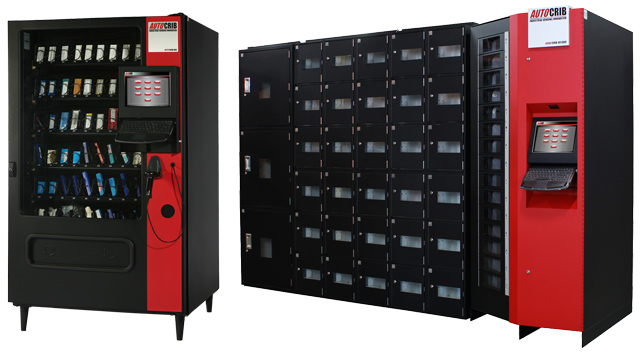
Illustrative Image (Source: Google Search)
-
What logistics options are available for importing inventory vending machines?
Logistics for importing vending machines can involve several options, including air freight for speed and sea freight for cost-effectiveness. Discuss with your supplier the best logistics solutions based on your delivery needs and budget. Additionally, consider working with a freight forwarder experienced in handling machinery to navigate customs regulations and ensure compliance with local laws. Always plan for potential delays in customs clearance and shipping. -
How can I resolve disputes with suppliers regarding inventory vending machines?
To effectively resolve disputes, maintain clear documentation of all agreements, communications, and transactions. If issues arise, address them directly and promptly with the supplier, aiming for a collaborative solution. Many suppliers will have formal dispute resolution processes, such as mediation or arbitration. If necessary, consult legal advice to understand your rights and obligations under the contract, especially when dealing with international laws and regulations.
Strategic Sourcing Conclusion and Outlook for inventory vending machine
As international B2B buyers navigate the evolving landscape of inventory vending machines, strategic sourcing emerges as a pivotal factor for success. By leveraging data-driven insights and market trends, businesses can optimize their procurement processes, ensuring they select the right suppliers that align with their operational needs. This approach not only enhances supply chain efficiency but also drives cost savings and improves service delivery.
Key takeaways for buyers include understanding the unique value propositions of vending machine solutions tailored to diverse industries and recognizing the importance of supplier reliability and innovation. Investing in advanced technology, such as IoT-enabled vending machines, can further streamline inventory management and provide real-time data analytics for informed decision-making.
Looking ahead, the demand for inventory vending machines is poised to grow, particularly in regions like Africa, South America, the Middle East, and Europe. Buyers are encouraged to stay proactive in exploring partnerships and evaluating emerging technologies that can enhance their operational capabilities. Embrace strategic sourcing as a pathway to unlocking new opportunities and driving competitive advantage in your market. Act now to position your business at the forefront of this dynamic industry.