Your Ultimate Guide to Sourcing Good Places To Put Vending
Guide to Good Places To Put Vending Machines
- Introduction: Navigating the Global Market for good places to put vending machines
- Understanding good places to put vending machines Types and Variations
- Key Industrial Applications of good places to put vending machines
- Strategic Material Selection Guide for good places to put vending machines
- In-depth Look: Manufacturing Processes and Quality Assurance for good places to put vending machines
- Comprehensive Cost and Pricing Analysis for good places to put vending machines Sourcing
- Spotlight on Potential good places to put vending machines Manufacturers and Suppliers
- Essential Technical Properties and Trade Terminology for good places to put vending machines
- Navigating Market Dynamics, Sourcing Trends, and Sustainability in the good places to put vending machines Sector
- Frequently Asked Questions (FAQs) for B2B Buyers of good places to put vending machines
- Strategic Sourcing Conclusion and Outlook for good places to put vending machines
Introduction: Navigating the Global Market for good places to put vending machines
In today’s fast-paced global economy, the strategic placement of vending machines is a critical factor for businesses aiming to optimize revenue streams. Identifying good places to put vending machines can significantly influence sales, customer satisfaction, and brand visibility. Whether in bustling urban centers, high-traffic office complexes, or popular tourist destinations, the right location can enhance access to products while meeting consumer demands for convenience.
This comprehensive guide serves as a vital resource for international B2B buyers, particularly those operating in diverse markets across Africa, South America, the Middle East, and Europe, including Italy and the UAE. It delves into various aspects of vending machine placement, from types and materials to considerations around manufacturing quality control and supplier selection. Understanding these elements is essential for making informed sourcing decisions that align with specific market dynamics and consumer preferences.
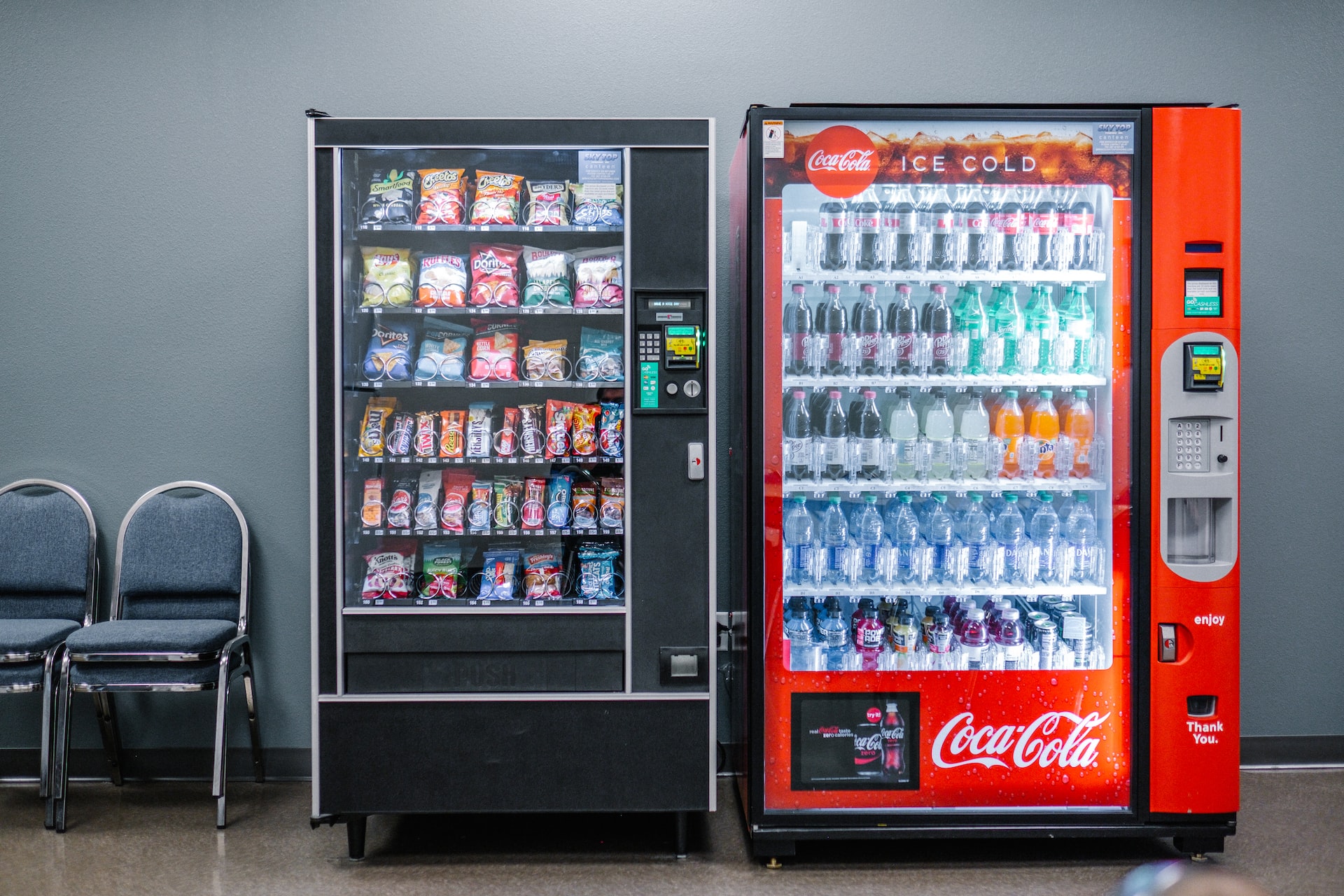
Illustrative Image (Source: Google Search)
Moreover, this guide addresses critical factors such as cost structures, market trends, and frequently asked questions, empowering buyers with the insights needed to navigate the complexities of vending machine deployment effectively. By leveraging this information, businesses can strategically position their vending machines to maximize profitability and enhance customer engagement, ultimately driving sustained growth in competitive landscapes.
Understanding good places to put vending machines Types and Variations
Type Name | Key Distinguishing Features | Primary B2B Applications | Brief Pros & Cons for Buyers |
---|---|---|---|
High Foot Traffic Areas | Locations with a large number of people passing by | Shopping malls, airports, schools | Pros: High sales potential; Cons: Higher competition. |
Workplace Environments | Areas where employees congregate | Office buildings, factories | Pros: Steady customer base; Cons: Limited operating hours. |
Public Transport Hubs | Accessibility for commuters | Train stations, bus terminals | Pros: Captive audience; Cons: Requires maintenance due to vandalism. |
Healthcare Facilities | Areas where patients and visitors gather | Hospitals, clinics | Pros: Essential for convenience; Cons: Regulatory compliance challenges. |
Educational Institutions | Locations where students frequently gather | Universities, colleges, high schools | Pros: Consistent demand; Cons: Seasonal usage fluctuations. |
High Foot Traffic Areas
High foot traffic areas, such as shopping malls, airports, and schools, are prime locations for vending machines. These sites attract large crowds, providing a high sales potential for a variety of products, from snacks to electronics. When considering vending machine placement in these areas, B2B buyers should evaluate foot traffic patterns and peak hours to maximize visibility and accessibility. However, competition can be fierce, necessitating unique product offerings or pricing strategies to stand out.
Workplace Environments
Workplace environments are ideal for vending machines, especially in office buildings and factories where employees gather during breaks. These locations benefit from a steady customer base, as employees often seek quick and convenient meal or snack options. B2B buyers should consider the specific needs of the workforce—healthy options may be more appealing in certain industries. However, operating hours may be limited to business hours, impacting sales potential outside of these times.
Public Transport Hubs
Public transport hubs, including train stations and bus terminals, provide excellent opportunities for vending machines due to the captive audience of commuters. These locations typically experience high foot traffic during peak travel times, allowing for consistent sales. B2B buyers should be aware of the need for robust machines that can withstand heavy use and potential vandalism. Maintenance and replenishment logistics are crucial considerations to ensure machines remain stocked and functional.
Healthcare Facilities
Healthcare facilities, such as hospitals and clinics, present unique opportunities for vending machines. Patients, visitors, and staff often seek convenient food and beverage options during long wait times. B2B buyers must consider regulatory compliance regarding product offerings, especially in healthcare settings. While these locations can provide essential convenience, they may also face challenges related to hygiene and product selection that align with health guidelines.
Educational Institutions
Educational institutions, including universities, colleges, and high schools, are key locations for vending machines, particularly for snacks and beverages. These environments typically see consistent demand from students throughout the academic year. B2B buyers should assess the demographic and preferences of the student body to tailor offerings effectively. However, it’s important to note the potential for seasonal usage fluctuations, as demand may drop during holidays and breaks.
Key Industrial Applications of good places to put vending machines
Industry/Sector | Specific Application of good places to put vending machines | Value/Benefit for the Business | Key Sourcing Considerations for this Application |
---|---|---|---|
Healthcare | Hospitals and clinics | Provides quick access to snacks and beverages for staff and visitors, enhancing satisfaction | Compliance with health regulations, machine hygiene standards |
Corporate Offices | Break rooms and common areas | Increases employee convenience and morale, reducing downtime for snacks and drinks | Machine size, variety of products, payment options |
Education | Schools and universities | Offers students easy access to food and drinks, promoting healthy snacking habits | Nutritional guidelines, age-appropriate products |
Transportation Hubs | Airports and train stations | Serves travelers with quick refreshments, improving customer experience | High durability, payment flexibility, machine placement |
Retail | Shopping malls and retail stores | Attracts foot traffic and provides impulse buying opportunities for customers | Product selection, machine visibility, maintenance support |
In the healthcare sector, placing vending machines in hospitals and clinics addresses the need for quick access to snacks and beverages, particularly for staff and visitors who may have limited time. These machines can be stocked with healthy options, aligning with wellness initiatives while enhancing visitor satisfaction. International buyers should consider compliance with local health regulations and the hygiene standards of the machines to ensure patient safety.
For corporate offices, vending machines in break rooms and common areas serve to increase employee convenience and morale. By offering a variety of snacks and beverages, companies can reduce downtime as employees no longer need to leave the premises for refreshments. Key considerations for B2B buyers include the size of the machines, the variety of products offered, and the available payment options to cater to diverse employee preferences.
In educational institutions, the installation of vending machines in schools and universities provides students with easy access to food and drinks, thereby promoting healthy snacking habits. These machines can feature nutritious options that comply with dietary guidelines. Buyers should focus on ensuring the products are age-appropriate and meet nutritional standards, as well as considering the machine’s placement for maximum visibility and accessibility.
Transportation hubs, such as airports and train stations, greatly benefit from vending machines that serve travelers with quick refreshments. This application enhances the customer experience by providing convenient options for those on the go. B2B buyers should consider the durability of machines to withstand high traffic and the flexibility of payment methods to cater to international travelers.
In the retail sector, placing vending machines in shopping malls and retail stores can attract foot traffic and create impulse buying opportunities. These machines can be strategically placed near entrances or high-traffic areas to maximize visibility. Buyers should evaluate product selection based on local consumer preferences, machine visibility, and the availability of maintenance support to ensure the machines remain stocked and functional.
Related Video: Kooler Ice Vending Machines – IM600XL vs. IM1000
Strategic Material Selection Guide for good places to put vending machines
When selecting materials for vending machines, it is essential to consider their properties, advantages, disadvantages, and how they align with the specific needs of international markets. Below are analyses of four common materials suitable for vending machine applications, particularly relevant to B2B buyers from Africa, South America, the Middle East, and Europe.
1. Stainless Steel
Key Properties:
Stainless steel is known for its excellent corrosion resistance, high strength, and ability to withstand extreme temperatures. It typically has a temperature rating of up to 1,000°F (538°C) and can handle moderate pressure.
Pros & Cons:
The durability of stainless steel makes it ideal for high-traffic areas, as it is resistant to dents and scratches. However, it is relatively expensive compared to other materials, which can increase the initial investment for vending machine manufacturers. Manufacturing complexity is moderate, requiring specialized welding techniques.
Impact on Application:
Stainless steel is compatible with a wide range of media, including food and beverages, making it a preferred choice for vending machines dispensing consumables.
Considerations for International Buyers:
Buyers in regions like Europe may prefer stainless steel due to compliance with health and safety standards (e.g., EU regulations). In contrast, buyers in Africa and South America should consider local availability and cost implications.
2. Powder-Coated Steel
Key Properties:
Powder-coated steel offers a protective finish that enhances corrosion resistance and aesthetic appeal. It can withstand temperatures up to 300°F (149°C) and is available in various colors.
Pros & Cons:
This material is cost-effective and provides a good balance between durability and appearance. However, it may not be as robust as stainless steel in high-impact scenarios, and the powder coating can chip or scratch over time.
Impact on Application:
Suitable for indoor vending machines, powder-coated steel is less ideal for outdoor use due to potential weathering. It is often used in applications where aesthetics are a priority.
Considerations for International Buyers:
Buyers should ensure that the powder coating complies with local environmental regulations, as some regions have strict guidelines regarding VOC emissions during manufacturing.
3. Aluminum
Key Properties:
Aluminum is lightweight, corrosion-resistant, and has excellent thermal conductivity. It can withstand temperatures up to 400°F (204°C) and is often used in applications requiring weight savings.
Pros & Cons:
The primary advantage of aluminum is its lightweight nature, which simplifies installation and transportation. However, it is less durable than steel and can be prone to dents and scratches. Manufacturing processes for aluminum can be more complex, especially for custom designs.
Impact on Application:
Aluminum is suitable for vending machines that require mobility, such as those in temporary locations or events. Its corrosion resistance makes it a good choice for humid environments.
Considerations for International Buyers:
In regions like the UAE, where humidity is high, aluminum’s properties are particularly beneficial. Buyers should verify that the aluminum used meets international standards, such as ASTM or DIN.
4. High-Density Polyethylene (HDPE)
Key Properties:
HDPE is a lightweight, impact-resistant plastic known for its excellent chemical resistance and durability. It can operate effectively at temperatures ranging from -40°F to 120°F (-40°C to 49°C).
Pros & Cons:
HDPE is highly resistant to impact and does not corrode, making it suitable for outdoor vending machines. However, it is less rigid than metals and may not provide the same level of security against vandalism.
Impact on Application:
This material is ideal for vending machines located in parks or outdoor settings where exposure to the elements is a concern. Its chemical resistance makes it suitable for dispensing various products, including beverages.
Considerations for International Buyers:
Buyers should check for compliance with food safety standards, especially in regions like South America, where regulations may vary significantly.
Summary Table
Material | Typical Use Case for good places to put vending machines | Key Advantage | Key Disadvantage/Limitation | Relative Cost (Low/Med/High) |
---|---|---|---|---|
Stainless Steel | High-traffic areas, food and beverage vending machines | Excellent durability and corrosion resistance | High initial cost, moderate manufacturing complexity | High |
Powder-Coated Steel | Indoor vending machines where aesthetics are a priority | Cost-effective, good appearance | Less durable than stainless steel, coating can chip | Medium |
Aluminum | Mobile vending machines, humid environments | Lightweight, corrosion-resistant | Less durable, prone to dents | Medium |
High-Density Polyethylene (HDPE) | Outdoor vending machines, parks, and events | Impact-resistant, chemical resistance | Less rigid, lower security against vandalism | Low |
This analysis provides a comprehensive overview for international B2B buyers, enabling informed decisions based on material properties, application suitability, and regional considerations.
In-depth Look: Manufacturing Processes and Quality Assurance for good places to put vending machines
When exploring the manufacturing processes and quality assurance (QA) relevant to the placement of vending machines, B2B buyers must consider various stages and standards that ensure product reliability and effectiveness. This section outlines the typical manufacturing stages, key techniques, and quality assurance measures that are essential for ensuring high-quality vending machines suitable for diverse markets, particularly in Africa, South America, the Middle East, and Europe.
Manufacturing Processes
Main Stages of Manufacturing
-
Material Preparation
– The initial stage involves sourcing high-quality materials such as stainless steel, plastic, and electronic components. Suppliers often prioritize materials that resist corrosion and wear to extend the life of vending machines.
– Key Techniques:- Material Selection: Ensure that materials meet regional regulations and standards, such as RoHS for electronics in the EU.
- Pre-Processing: This includes cutting, shaping, and treating materials to improve durability and functionality.
-
Forming
– This stage involves shaping materials into the required parts of the vending machine, including panels, frames, and internal components.
– Key Techniques:- CNC Machining: Utilizes computer numerical control for precise cutting and shaping, ensuring uniformity in parts.
- Metal Stamping: Efficient for producing high volumes of metal components with consistent quality.
-
Assembly
– The assembly process integrates various components into a cohesive unit, including mechanical parts, electronic systems, and user interfaces.
– Key Techniques:- Modular Assembly: Allows for easier repairs and upgrades by using standardized parts.
- Automated Assembly Lines: Increases efficiency and reduces labor costs while maintaining accuracy.
-
Finishing
– This final stage enhances the aesthetic and functional aspects of the vending machine.
– Key Techniques:- Painting and Coating: Protects against environmental factors and improves appearance.
- Quality Checks: Each machine undergoes a series of inspections to confirm that it meets design specifications and standards.
Quality Assurance
International Standards
B2B buyers should be familiar with various quality standards that govern the manufacturing of vending machines:
- ISO 9001: This standard focuses on quality management systems and is essential for any manufacturer aiming to improve customer satisfaction and operational efficiency.
- CE Marking: Required for products sold in the European Economic Area, indicating compliance with health, safety, and environmental protection standards.
- API Standards: Applicable for vending machines that dispense specific products, ensuring they meet industry regulations.
Quality Control Checkpoints
Quality control (QC) is a critical component of the manufacturing process, often divided into three main checkpoints:
-
Incoming Quality Control (IQC)
– Verification of raw materials and components upon arrival at the manufacturing facility. Suppliers should provide certificates of compliance to ensure materials meet required standards. -
In-Process Quality Control (IPQC)
– Continuous monitoring during the manufacturing process to identify defects early. This can include regular inspections and testing at various stages of production. -
Final Quality Control (FQC)
– A comprehensive evaluation of the completed vending machines, including functional tests, safety checks, and aesthetic assessments. This step ensures that the product is ready for market and meets all quality standards.
Common Testing Methods
- Functional Testing: Ensures that all components operate correctly, including payment systems, refrigeration units, and display screens.
- Durability Testing: Assesses the machine’s performance under extreme conditions, simulating real-world usage.
- Safety Testing: Validates that the machine complies with safety regulations to prevent hazards for users.
Verifying Supplier Quality Control
For international B2B buyers, especially in regions like Africa, South America, the Middle East, and Europe, verifying a supplier’s QC processes is crucial:
- Supplier Audits: Conduct on-site audits to review manufacturing processes, QC measures, and compliance with international standards. This helps build trust and ensures accountability.
- Quality Reports: Request detailed QC reports that outline testing results, defect rates, and corrective actions taken for any identified issues.
- Third-Party Inspections: Engage independent inspection services to evaluate the manufacturing process and product quality. This can provide an unbiased assessment of the supplier’s capabilities.
Quality Certification Nuances
Understanding the nuances of quality certifications is essential for B2B buyers:
- Regional Variations: Different markets may have specific requirements. For instance, EU regulations may differ significantly from those in the Middle East or Africa.
- Documentation: Ensure that all certifications are documented and up-to-date. This is crucial for compliance and for avoiding potential legal issues.
- Local Compliance: Some countries may require additional local certifications beyond international standards, which can affect import processes.
By focusing on these manufacturing processes and quality assurance measures, B2B buyers can ensure they select reliable vending machine suppliers that meet their operational needs and compliance requirements. This strategic approach not only mitigates risks but also enhances the potential for successful business outcomes in diverse international markets.
Related Video: Most Satisfying Factory Production Processes And Heavy-Duty Factory Machines!
Comprehensive Cost and Pricing Analysis for good places to put vending machines Sourcing
When considering the placement of vending machines in international markets, understanding the cost structure and pricing dynamics is crucial for B2B buyers. This section delves into the various cost components associated with sourcing vending machines and the factors that influence pricing, tailored specifically for buyers from Africa, South America, the Middle East, and Europe.
Cost Components
-
Materials: The type of materials used in vending machines significantly affects the overall cost. High-quality stainless steel and advanced electronic components may increase the price but can enhance durability and functionality. Buyers should consider local material availability, as sourcing locally can reduce costs.
-
Labor: Labor costs vary greatly by region. In emerging markets, such as parts of Africa and South America, labor may be less expensive, which can lead to lower manufacturing costs. However, in developed regions like Europe, labor costs can be significantly higher, impacting the final price of vending machines.
-
Manufacturing Overhead: This includes utilities, rent, and administrative expenses associated with the manufacturing facility. Understanding the supplier’s overhead costs can provide insights into their pricing strategy. For instance, suppliers in regions with higher operational costs may pass these expenses onto buyers.
-
Tooling: The initial setup costs for manufacturing vending machines, including molds and machinery, can be substantial. Custom designs may require more sophisticated tooling, which increases upfront costs. Buyers should inquire about these costs to gauge the impact on pricing.
-
Quality Control (QC): Investing in robust QC processes ensures that vending machines meet safety and functionality standards. This can add to the cost but is essential for minimizing returns and ensuring customer satisfaction.
-
Logistics: Shipping and handling fees can vary widely based on distance, mode of transport, and the Incoterms agreed upon. International buyers should consider these logistics costs when evaluating total expenditure.
- Margin: Supplier profit margins can vary based on competition and market demand. Understanding the typical margins within specific regions can help buyers negotiate better prices.
Price Influencers
-
Volume/MOQ: The minimum order quantity (MOQ) often affects pricing. Larger orders typically qualify for bulk discounts, providing a cost-effective solution for buyers looking to scale their vending machine operations.
-
Specifications/Customization: Custom vending machines tailored to specific market needs may incur higher costs. Buyers should assess whether the added functionality justifies the extra expense.
-
Quality/Certifications: Machines that comply with international safety and quality standards may cost more initially but can save money in the long run by reducing maintenance and operational failures.
-
Supplier Factors: The reputation and reliability of the supplier can influence pricing. Established suppliers may charge a premium, but their proven track record can mitigate risks associated with quality and service.
-
Incoterms: The choice of Incoterms affects shipping responsibilities and costs. Buyers should carefully select terms that align with their logistics capabilities to avoid unexpected charges.
Buyer Tips
-
Negotiation: Engage in negotiations to secure better pricing, especially if placing large orders. Understanding the supplier’s cost structure can enhance negotiation outcomes.
-
Cost-Efficiency: Focus on the Total Cost of Ownership (TCO), which includes purchase price, maintenance, and operational costs. Sometimes, a higher initial investment in quality machines can lead to lower long-term costs.
-
Pricing Nuances: International buyers should be aware of currency fluctuations and their potential impact on pricing. Locking in prices or negotiating fixed-rate contracts can help mitigate these risks.
Disclaimer
Prices and costs mentioned are indicative and can vary based on numerous factors, including regional economic conditions and market dynamics. Buyers are encouraged to conduct thorough market research and supplier evaluations before making purchasing decisions.
Spotlight on Potential good places to put vending machines Manufacturers and Suppliers
This section offers a look at a few manufacturers active in the ‘good places to put vending machines’ market. This is a representative sample for illustrative purposes; B2B buyers must conduct their own extensive due diligence before any engagement. Information is synthesized from public sources and general industry knowledge.
Essential Technical Properties and Trade Terminology for good places to put vending machines
When considering the placement of vending machines in various international markets, understanding the essential technical properties and trade terminology is crucial for making informed decisions. Here, we explore key specifications and terms that international B2B buyers should be familiar with.
Key Technical Properties
-
Material Grade
– Definition: The quality and type of materials used in the construction of vending machines, such as stainless steel, aluminum, or plastic.
– Importance: High-grade materials ensure durability and resistance to weather conditions, which is particularly important in outdoor or high-traffic areas. For instance, stainless steel is preferred for its corrosion resistance in humid climates, common in many African regions. -
Capacity and Size Specifications
– Definition: The volume of products a vending machine can hold, typically measured in terms of the number of selections and storage space.
– Importance: Selecting the right capacity is vital for meeting local demand. For example, urban areas may require larger machines with diverse offerings, while rural locations might benefit from smaller, specialized units. -
Power Requirements
– Definition: The electrical specifications needed to operate the vending machine, including voltage and wattage.
– Importance: Understanding power requirements helps ensure compatibility with local electrical standards, minimizing operational disruptions. This is critical in regions with varying electricity supply, such as parts of South America and Africa. -
User Interface Technology
– Definition: The type of payment systems and user interaction mechanisms, such as touchscreen interfaces, cash acceptors, or mobile payment options.
– Importance: Advanced user interfaces enhance customer experience and can significantly affect sales. In regions like the UAE, where technology adoption is high, machines with mobile payment options are increasingly preferred. -
Temperature Control
– Definition: The ability of the vending machine to maintain specific temperature ranges for perishable items.
– Importance: Effective temperature control is essential for food safety and product quality, especially in warmer climates. Machines designed for chilled or frozen goods must comply with local health regulations, making this feature a priority for B2B buyers.
Common Trade Terminology
-
OEM (Original Equipment Manufacturer)
– Definition: A company that produces parts and equipment that may be marketed by another manufacturer.
– Importance: Understanding OEM relationships can help buyers source quality machines that meet specific requirements while potentially reducing costs through bulk purchasing agreements. -
MOQ (Minimum Order Quantity)
– Definition: The smallest quantity of a product that a supplier is willing to sell.
– Importance: Knowing the MOQ is essential for budgeting and inventory management, especially for international buyers who may face higher shipping costs for smaller orders. -
RFQ (Request for Quotation)
– Definition: A document sent to suppliers to request pricing and terms for specific products or services.
– Importance: An RFQ helps buyers compare costs and terms from multiple suppliers, facilitating better negotiation and ensuring competitive pricing. -
Incoterms (International Commercial Terms)
– Definition: A set of predefined international trade terms that outline the responsibilities of buyers and sellers.
– Importance: Familiarity with Incoterms is crucial for understanding shipping responsibilities, risk management, and cost allocation, especially when dealing with international shipping logistics in diverse markets. -
Lead Time
– Definition: The time between the initiation of a process and its completion, particularly in manufacturing and delivery.
– Importance: Recognizing lead times helps buyers plan for inventory management and ensure timely availability of vending machines, particularly in regions with longer shipping durations.
By grasping these technical properties and trade terms, B2B buyers can make strategic decisions regarding the acquisition and placement of vending machines, ultimately leading to enhanced operational efficiency and customer satisfaction across various international markets.
Navigating Market Dynamics, Sourcing Trends, and Sustainability in the good places to put vending machines Sector
Market Overview & Key Trends
The global vending machine market is undergoing significant transformation, driven by technological advancements, changing consumer preferences, and increased focus on convenience. International B2B buyers, particularly from regions such as Africa, South America, the Middle East, and Europe, should be aware of several key trends shaping the sector. Digitalization is at the forefront, with the integration of cashless payment systems and mobile app functionalities allowing for more seamless transactions. This shift not only enhances user experience but also expands the potential customer base, particularly among younger demographics.
Health and wellness is another crucial trend. Vending machines are increasingly stocked with healthier options, appealing to health-conscious consumers. This trend is notably strong in urban areas of Europe and North America, but it is gaining traction in emerging markets as well. For B2B buyers, aligning product offerings with local health trends can provide a competitive edge.
Moreover, the rise of sustainable practices is compelling businesses to reconsider their sourcing and operational strategies. Increasing regulatory pressure and consumer demand for eco-friendly products mean that incorporating sustainable materials and practices into vending machine operations is not just a trend but a necessity for long-term viability. Buyers should prioritize suppliers who demonstrate a commitment to sustainability.
Sustainability & Ethical Sourcing in B2B
Sustainability is becoming a core consideration for B2B buyers in the vending machine sector. The environmental impact of vending machines extends beyond the products they dispense; it includes the energy consumed, the materials used for construction, and the waste generated. As businesses face increasing scrutiny regarding their carbon footprints, sourcing from suppliers that prioritize sustainable practices is essential.
Buyers should look for certifications such as ISO 14001 for environmental management and the Forest Stewardship Council (FSC) certification for materials. These certifications indicate a commitment to responsible sourcing and sustainability. Additionally, utilizing recyclable or biodegradable materials for vending machine components can significantly reduce environmental impact.
Moreover, ethical supply chains are critical in ensuring that all aspects of the vending machine business align with sustainability goals. This includes fair labor practices and transparency in sourcing. By prioritizing suppliers who adhere to ethical standards, B2B buyers not only contribute to a more sustainable future but also enhance their brand reputation, appealing to an increasingly conscious consumer base.
Brief Evolution/History
The vending machine industry has evolved significantly since its inception in the late 19th century. Initially offering simple products like cigarettes and candy, the sector has expanded to include a diverse range of goods, reflecting changes in consumer behavior and technology. The introduction of electronic payment systems in the 1980s marked a pivotal moment, paving the way for modern, smart vending machines that offer a variety of payment options and product selections.
Today, vending machines are seen not just as convenient snack dispensers but as innovative retail solutions. As international markets continue to grow, particularly in regions like Africa and South America, the potential for vending machines to adapt to local tastes and preferences presents a lucrative opportunity for B2B buyers. Understanding this historical context can provide valuable insights into current trends and future developments in the sector.
Related Video: Global Trade & Logistics – What is Global Trade?
Frequently Asked Questions (FAQs) for B2B Buyers of good places to put vending machines
-
What factors should I consider when vetting suppliers for vending machine locations?
When vetting suppliers, prioritize their experience and reputation in the vending industry. Look for verified reviews and testimonials from other B2B buyers, particularly those from your region. Ensure they have a solid understanding of local regulations and market preferences. Additionally, assess their supply chain capabilities, including sourcing quality products and maintaining consistent stock levels. Establish direct communication to gauge their responsiveness and willingness to customize solutions to fit your specific needs. -
How customizable are vending machines for different locations?
Many suppliers offer a range of customization options for vending machines, including product selection, branding, and machine design. It’s essential to communicate your requirements clearly, as this can impact the machine’s effectiveness in different environments. Consider local tastes and preferences when selecting products. Suppliers may also offer technological upgrades, such as cashless payment systems or smart inventory management, which can enhance the customer experience and operational efficiency. -
What are the typical minimum order quantities (MOQ) and lead times for vending machines?
Minimum order quantities can vary significantly by supplier and product type. For vending machines, MOQs may range from one unit to several, depending on the supplier’s capabilities and your negotiation. Lead times generally range from a few weeks to several months, influenced by factors like customization requests and shipping logistics. Always discuss these details upfront to ensure they align with your project timelines and operational plans. -
What payment options are commonly accepted by suppliers?
Most suppliers accept a variety of payment methods, including bank transfers, credit cards, and letters of credit, especially for international transactions. It’s crucial to clarify payment terms before placing an order, including deposits, full payment, and potential financing options. Be mindful of currency exchange rates and transaction fees that may apply. Establishing a clear payment agreement helps mitigate financial risks associated with international trade. -
How can I ensure quality assurance and certifications for vending machines?
Request documentation of quality assurance protocols and certifications from suppliers to ensure their products meet international standards. Look for certifications such as ISO 9001, which indicates a commitment to quality management systems. Additionally, inquire about the testing processes for vending machines and any warranties offered. Consider conducting site visits or third-party inspections to verify compliance with safety and quality standards before finalizing your order. -
What logistics considerations should I keep in mind when sourcing vending machines?
Logistics play a crucial role in the successful delivery of vending machines. Discuss shipping options, including air freight and sea freight, based on your budget and urgency. Ensure the supplier has experience handling customs clearance and compliance with local regulations in your country. Additionally, plan for local transportation and installation costs, which can vary based on location and machine size. Establishing a clear logistics plan will help avoid delays and unexpected expenses. -
What should I do in case of a dispute with a supplier?
In the event of a dispute, maintain open communication with your supplier to discuss the issue directly. Document all interactions and agreements related to the transaction. If a resolution cannot be reached, refer to the terms outlined in your contract regarding dispute resolution processes, such as mediation or arbitration. Utilizing a third-party mediator can often lead to a more amicable solution without resorting to legal action, which can be costly and time-consuming. -
How can I assess the profitability of vending machine locations?
To assess the profitability of potential vending machine locations, conduct thorough market research to understand foot traffic, customer demographics, and competition in the area. Utilize sales data from similar machines in comparable locations to estimate potential revenue. It’s also beneficial to engage with local businesses or facilities to gauge interest in hosting vending machines. Regularly review performance metrics after installation to make data-driven decisions about product offerings and location viability.
Strategic Sourcing Conclusion and Outlook for good places to put vending machines
The strategic placement of vending machines is crucial for optimizing revenue and enhancing customer satisfaction. Key insights reveal that high-traffic areas such as shopping malls, airports, educational institutions, and corporate offices provide excellent opportunities for vending machine installations. These locations not only guarantee consistent foot traffic but also cater to diverse consumer needs, from snacks to beverages.
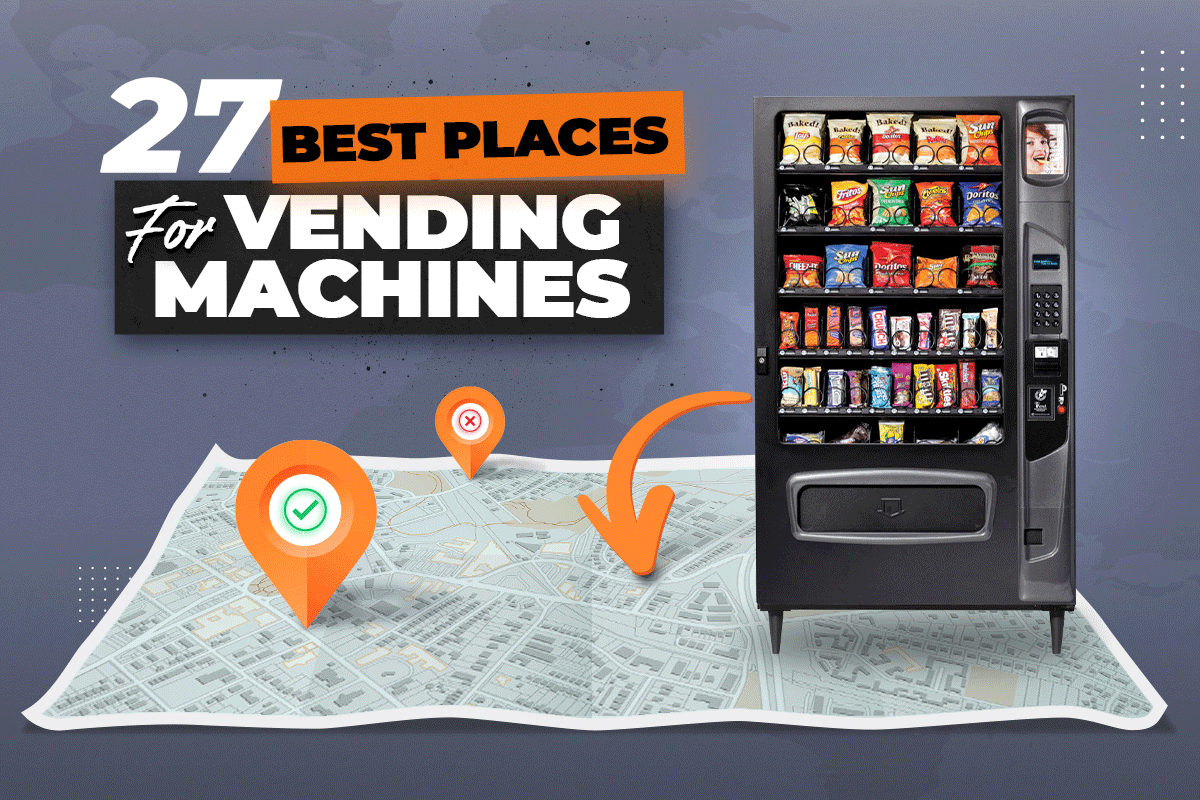
Illustrative Image (Source: Google Search)
Strategic sourcing plays a pivotal role in identifying the right suppliers and machine types to align with local consumer preferences. For international B2B buyers, understanding regional market dynamics is essential. In Africa and South America, consider the cultural context and local tastes; in the Middle East, compliance with local regulations is paramount; while in Europe, sustainability trends can influence purchasing decisions.
As you look to invest in vending machine opportunities, leverage local partnerships to navigate these complexities. Take action today by conducting thorough market research, identifying prime locations, and exploring innovative vending solutions that cater to your target audience. The right approach will not only enhance your operational efficiency but also position your business for sustainable growth in the evolving vending landscape.