Your Ultimate Guide to Sourcing Fruit Smoothie Vending
Guide to Fruit Smoothie Vending Machine
- Introduction: Navigating the Global Market for fruit smoothie vending machine
- Understanding fruit smoothie vending machine Types and Variations
- Key Industrial Applications of fruit smoothie vending machine
- Strategic Material Selection Guide for fruit smoothie vending machine
- In-depth Look: Manufacturing Processes and Quality Assurance for fruit smoothie vending machine
- Comprehensive Cost and Pricing Analysis for fruit smoothie vending machine Sourcing
- Spotlight on Potential fruit smoothie vending machine Manufacturers and Suppliers
- Essential Technical Properties and Trade Terminology for fruit smoothie vending machine
- Navigating Market Dynamics, Sourcing Trends, and Sustainability in the fruit smoothie vending machine Sector
- Frequently Asked Questions (FAQs) for B2B Buyers of fruit smoothie vending machine
- Strategic Sourcing Conclusion and Outlook for fruit smoothie vending machine
Introduction: Navigating the Global Market for fruit smoothie vending machine
The global market for fruit smoothie vending machines is experiencing dynamic growth, driven by a rising awareness of health and wellness among consumers. As a result, businesses and entrepreneurs across Africa, South America, the Middle East, and Europe are increasingly looking to capitalize on this trend. These machines not only provide a convenient option for busy individuals seeking nutritious snacks but also represent a lucrative investment opportunity for B2B buyers aiming to diversify their offerings and enhance customer satisfaction.
This guide serves as an essential resource for international B2B buyers, detailing the diverse types of fruit smoothie vending machines available in the marketplace. It will explore critical factors such as materials used in manufacturing, quality control standards, and reputable suppliers, ensuring buyers are equipped with the knowledge to make informed decisions. Additionally, we will delve into cost considerations, market trends, and frequently asked questions that can aid in navigating this competitive landscape.
By understanding the intricacies of the fruit smoothie vending machine market, buyers will be empowered to identify the right solutions tailored to their specific business needs. Whether you’re based in bustling urban centers of South Africa or the emerging markets of South America, this guide will provide actionable insights that support strategic sourcing and drive growth in your business endeavors. Prepare to unlock the potential of this innovative vending solution and enhance your product offerings in a health-conscious world.
Understanding fruit smoothie vending machine Types and Variations
Type Name | Key Distinguishing Features | Primary B2B Applications | Brief Pros & Cons for Buyers |
---|---|---|---|
Traditional Vending Machines | Manual selection; refrigerated compartments | Gyms, schools, offices | Pros: Familiarity, lower initial costs. Cons: Limited automation, higher labor costs. |
Smart Automated Machines | Touchscreen interface; cashless payment options | Airports, shopping malls | Pros: Enhanced user experience, real-time inventory tracking. Cons: Higher upfront investment, maintenance complexity. |
Compact Mobile Units | Small footprint; portable design | Events, festivals, pop-up shops | Pros: Flexibility, lower space requirements. Cons: Limited capacity, potentially higher per-unit costs. |
High-Volume Bulk Machines | Large capacity; rapid dispensing | Large corporate offices, universities | Pros: Efficiency in high-demand environments, cost-effective per serving. Cons: Requires significant space, potential for overstocking. |
Health-Focused Specialty Machines | Focus on organic ingredients; nutritional information display | Health clubs, wellness centers | Pros: Appeals to health-conscious consumers, premium pricing potential. Cons: Higher operational costs, niche market appeal. |
Traditional Vending Machines
Traditional vending machines are characterized by their manual selection process and refrigerated compartments that keep smoothies fresh. These machines are commonly found in gyms, schools, and office environments where users prefer straightforward, easy access to products. B2B buyers considering this type should evaluate the balance between initial costs and potential labor expenses, as these machines typically require staff for restocking and maintenance.
Smart Automated Machines
Smart automated machines leverage technology with touchscreen interfaces and cashless payment options, making them ideal for high-traffic areas like airports and shopping malls. These machines provide an enhanced user experience and can track inventory in real-time, which is valuable for managing stock levels effectively. However, the higher upfront investment and maintenance complexity should be carefully considered by B2B buyers looking to implement this technology in their operations.
Compact Mobile Units
Compact mobile units are designed for portability and have a small footprint, making them suitable for temporary events, festivals, and pop-up shops. Their flexibility allows businesses to adapt to different locations and customer demands. However, buyers should consider the limited capacity and potentially higher per-unit costs associated with these machines, which may not be ideal for long-term, high-volume sales.
High-Volume Bulk Machines
High-volume bulk machines are built for efficiency and can dispense smoothies rapidly, making them suitable for large corporate offices and universities. These machines can handle significant demand, providing a cost-effective solution per serving. However, they require considerable space and may lead to overstocking if demand fluctuates, which B2B buyers must account for in their purchasing decisions.
Health-Focused Specialty Machines
Health-focused specialty machines emphasize organic ingredients and often feature displays that provide nutritional information. They are particularly appealing to health-conscious consumers and can be found in health clubs and wellness centers. While these machines can command premium pricing, buyers should be aware of the higher operational costs and the niche market appeal, which could limit their overall customer base.
Related Video: Smoothie Vending Machine in Singapore / Drink making
Key Industrial Applications of fruit smoothie vending machine
Industry/Sector | Specific Application of fruit smoothie vending machine | Value/Benefit for the Business | Key Sourcing Considerations for this Application |
---|---|---|---|
Hospitality | In-room smoothie vending in hotels | Enhances guest experience, increases revenue | Compact design, payment system compatibility |
Corporate Offices | Employee wellness stations | Promotes health, boosts productivity | Bulk supply agreements, machine maintenance services |
Educational Institutions | Smoothie vending in cafeterias | Offers healthy options, attracts students | Nutritional compliance, energy efficiency |
Fitness Centers | On-site smoothie vending for members | Increases membership retention, promotes wellness | High-capacity blenders, quick service capabilities |
Retail | Smoothie kiosks in shopping malls | Attracts foot traffic, diversifies product offerings | Location analytics, customer engagement tools |
Hospitality
In the hospitality sector, fruit smoothie vending machines can be strategically placed in hotel lobbies or guest rooms, providing quick and convenient access to healthy beverage options. This not only enhances the guest experience but also serves as an additional revenue stream for hotels. Buyers in this sector should consider compact designs that fit within limited space and ensure compatibility with various payment systems to cater to international guests.
Corporate Offices
Corporate offices are increasingly adopting smoothie vending machines as part of their employee wellness initiatives. These machines can be placed in break rooms or common areas to provide nutritious options that promote health and well-being among employees. This leads to increased productivity and job satisfaction. Key sourcing considerations include establishing bulk supply agreements for consistent ingredient quality and ensuring reliable machine maintenance services to avoid downtime.
Educational Institutions
In educational institutions, fruit smoothie vending machines can be installed in cafeterias or common areas to provide students with healthy beverage choices. This not only meets the growing demand for nutritious options but also helps schools attract and retain students. Buyers should focus on nutritional compliance with local regulations and energy-efficient models that reduce operational costs while serving a large number of students efficiently.
Fitness Centers
Fitness centers can benefit significantly from on-site smoothie vending machines that cater to health-conscious members. These machines can offer a range of smoothies designed to enhance post-workout recovery and overall wellness. By providing quick and nutritious options, fitness centers can increase membership retention and satisfaction. Key considerations for buyers include high-capacity blenders for quick service and the ability to customize offerings based on customer preferences.
Retail
In the retail sector, particularly in shopping malls, smoothie kiosks can attract foot traffic and diversify product offerings. These machines can serve as a quick snack or meal replacement for shoppers on the go, enhancing the overall shopping experience. When sourcing fruit smoothie vending machines, retailers should consider location analytics to optimize placement and customer engagement tools that can promote loyalty programs or special offers.
Related Video: Alberts Smoothie Station | Your automated solution for fresh, personalized smoothies at work
Strategic Material Selection Guide for fruit smoothie vending machine
When selecting materials for fruit smoothie vending machines, it is essential to consider various factors including durability, cost, and compatibility with the intended media. Below are analyses of four common materials used in these machines, tailored specifically for international B2B buyers from regions such as Africa, South America, the Middle East, and Europe.
Stainless Steel
Key Properties: Stainless steel is known for its excellent corrosion resistance and ability to withstand high temperatures and pressures. It typically has a temperature rating of up to 500°F (260°C) and can handle pressures of around 150 psi.
Pros & Cons: The primary advantage of stainless steel is its durability and resistance to rust and staining, making it ideal for food-related applications. However, it can be more expensive than other materials, and manufacturing processes may require specialized equipment, increasing complexity.
Impact on Application: Stainless steel is highly compatible with various food products, including fruits and dairy, ensuring that the quality of smoothies is maintained without contamination.
Considerations for International Buyers: Compliance with food safety standards like the FDA in the U.S. or EFSA in Europe is crucial. Buyers should ensure that the stainless steel used meets relevant standards such as ASTM A240 for corrosion resistance.
Polycarbonate
Key Properties: Polycarbonate is a strong, transparent plastic that can withstand temperatures up to 250°F (121°C) and has good impact resistance.
Pros & Cons: Its lightweight nature and transparency make it an attractive option for display purposes. However, polycarbonate can be prone to scratching and may not withstand high temperatures as well as metals.
Impact on Application: Polycarbonate is suitable for components like smoothie containers and display panels, allowing for visibility while maintaining structural integrity.
Considerations for International Buyers: Buyers should check for compliance with food-grade certifications, such as FDA and EU regulations. Additionally, polycarbonate’s susceptibility to UV degradation may be a concern in regions with high sun exposure.
Aluminum
Key Properties: Aluminum is lightweight and has a good strength-to-weight ratio. It can handle temperatures up to 400°F (204°C) and has moderate corrosion resistance, especially when anodized.
Pros & Cons: The main advantage of aluminum is its cost-effectiveness and ease of manufacturing. However, it may require additional coatings to prevent corrosion, particularly in humid environments.
Impact on Application: Aluminum is often used for structural components and housing in vending machines, providing a balance between weight and strength.
Considerations for International Buyers: Buyers should be aware of local corrosion risks and ensure that aluminum components are adequately treated for specific environmental conditions. Compliance with relevant standards, such as ASTM B221 for aluminum extrusions, is also necessary.
Glass
Key Properties: Glass is non-reactive and can withstand a range of temperatures, although it is generally more fragile than other materials.
Pros & Cons: Glass provides an aesthetic appeal and is easy to clean, making it suitable for display purposes. However, its fragility can lead to breakage, and it is heavier than other options.
Impact on Application: Glass is commonly used for smoothie containers, enhancing the visual appeal of the product while ensuring no interaction with the contents.
Considerations for International Buyers: Buyers should ensure that the glass used is tempered or laminated to enhance safety and comply with local regulations regarding food safety and packaging materials.
Summary Table
Material | Typical Use Case for fruit smoothie vending machine | Key Advantage | Key Disadvantage/Limitation | Relative Cost (Low/Med/High) |
---|---|---|---|---|
Stainless Steel | Structural components, blending chambers | Excellent corrosion resistance, durable | Higher cost, manufacturing complexity | High |
Polycarbonate | Containers, display panels | Lightweight, transparent | Prone to scratching, limited temperature resistance | Medium |
Aluminum | Structural housing, frames | Cost-effective, lightweight | Requires coatings for corrosion resistance | Low |
Glass | Smoothie containers | Aesthetic appeal, non-reactive | Fragile, heavier than alternatives | Medium |
This guide provides an overview of the strategic material selection process for fruit smoothie vending machines, ensuring that international B2B buyers can make informed decisions based on their specific needs and regional considerations.
In-depth Look: Manufacturing Processes and Quality Assurance for fruit smoothie vending machine
Understanding Manufacturing Processes for Fruit Smoothie Vending Machines
The manufacturing of fruit smoothie vending machines involves several key stages that ensure the machines are efficient, durable, and user-friendly. For B2B buyers, understanding these processes is crucial in evaluating potential suppliers and ensuring that the machines meet their operational requirements.
Main Stages of Manufacturing
-
Material Preparation
– Selection of Materials: High-quality stainless steel, plastics, and electronic components are critical for durability and food safety. Suppliers should provide documentation regarding the source and quality of these materials.
– Pre-processing: This includes cutting, shaping, and treating materials to enhance performance and longevity. Buyers should inquire about the methods used, such as laser cutting or water jet cutting, which can influence precision and manufacturing time. -
Forming
– Molding and Shaping: The components, such as the blender housing and dispensing mechanisms, are typically molded using techniques like injection molding or blow molding. These techniques ensure uniformity and strength.
– Assembly of Components: Automated assembly lines may be used to ensure efficiency. Understanding the level of automation can give insights into the production capacity and consistency of output. -
Assembly
– Integration of Systems: This stage includes the assembly of electrical components, refrigeration units, and dispensing systems. Quality control during this phase is critical to ensure that all parts fit seamlessly and function correctly.
– Testing Assemblies: Preliminary tests are conducted to check for functionality and user interface responsiveness, which are essential for customer satisfaction. -
Finishing
– Surface Treatment: Final touches such as polishing, painting, or application of food-safe coatings are applied. This not only enhances aesthetic appeal but also protects against corrosion and wear.
– Final Assembly and Packaging: The final assembly is conducted with a focus on ease of transport and installation. Proper packaging safeguards the machines during shipping.
Quality Assurance Protocols
Quality assurance (QA) is pivotal in the manufacturing of fruit smoothie vending machines. It ensures that products meet safety standards and customer expectations.
International Standards
- ISO 9001: This standard outlines the requirements for a quality management system. Companies that comply with ISO 9001 demonstrate their ability to consistently provide products that meet customer and regulatory requirements.
- CE Marking: For machines sold in Europe, CE marking indicates compliance with European health, safety, and environmental protection standards.
- API Standards: These standards may apply if the machines include components that interact with food products, ensuring safety and hygiene.
Quality Control Checkpoints
-
Incoming Quality Control (IQC)
– Materials and components are inspected upon arrival to ensure they meet specified criteria. Buyers should request reports on IQC processes to understand the supplier’s commitment to quality. -
In-Process Quality Control (IPQC)
– Continuous monitoring occurs throughout the manufacturing process. This includes checks on assembly accuracy and functionality tests. B2B buyers can inquire about the frequency and methods of these checks. -
Final Quality Control (FQC)
– Before packaging, final inspections ensure that all machines function correctly and meet aesthetic standards. Buyers should seek detailed FQC reports to confirm that the machines are ready for market.
Common Testing Methods
- Functional Testing: Verifies that all operational features work as intended.
- Stress Testing: Assesses the durability and reliability of machines under simulated operational conditions.
- Safety Testing: Ensures compliance with electrical safety standards, crucial for machines that deal with food and beverages.
Verifying Supplier Quality Control
For international B2B buyers, especially from diverse markets such as Africa, South America, the Middle East, and Europe, it is essential to verify the quality control processes of potential suppliers. Here are actionable strategies:
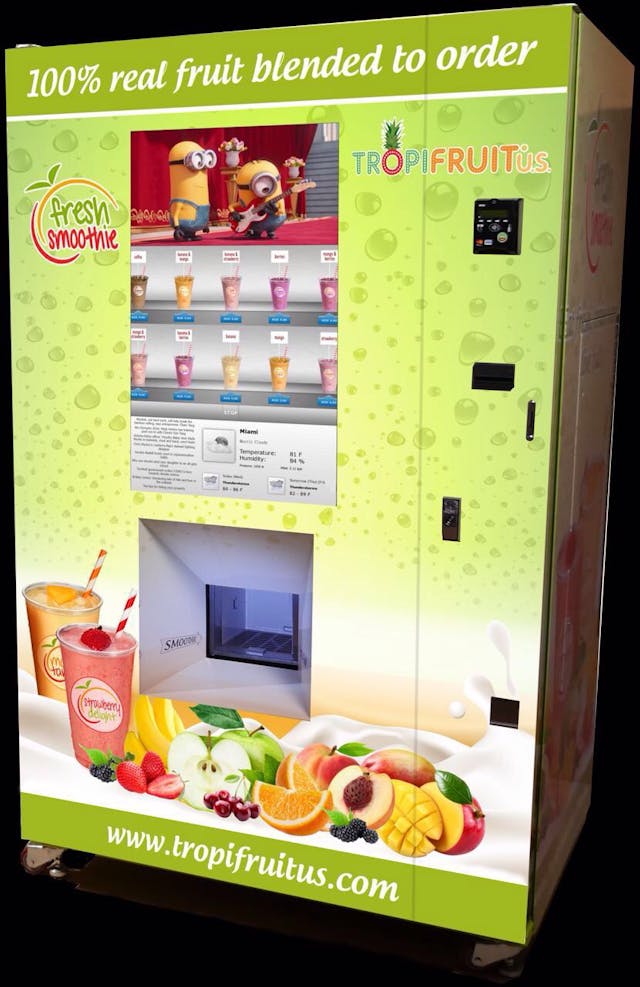
Illustrative Image (Source: Google Search)
- Supplier Audits: Conduct on-site audits to observe manufacturing processes and quality control measures firsthand. This is particularly important in regions with varying compliance standards.
- Quality Reports: Request detailed reports on IQC, IPQC, and FQC processes. This documentation should highlight compliance with international standards and any certifications obtained.
- Third-Party Inspections: Engage third-party inspection services to conduct independent assessments of the manufacturing facilities and processes. This adds an extra layer of credibility and assurance.
Navigating Quality Control Nuances
International buyers must be aware of specific nuances in quality control that vary by region:
- Regulatory Compliance: Different countries have distinct regulations regarding food safety and machinery standards. Understanding these is crucial for compliance and market entry.
- Cultural Expectations: The perception of quality can vary, influencing buyer-supplier relationships. Engaging with local representatives or consultants can facilitate smoother negotiations.
- Logistical Considerations: Shipping and installation logistics can impact product integrity. Buyers should ensure that suppliers have robust plans for transportation and handling.
Conclusion
A comprehensive understanding of the manufacturing processes and quality assurance protocols for fruit smoothie vending machines empowers B2B buyers to make informed purchasing decisions. By focusing on supplier capabilities, compliance with international standards, and effective quality control measures, buyers can secure machines that meet their operational needs and customer expectations.
Related Video: The dried fruit factory process
Comprehensive Cost and Pricing Analysis for fruit smoothie vending machine Sourcing
Understanding the cost structure and pricing dynamics of fruit smoothie vending machines is critical for international B2B buyers. This analysis delves into the various cost components, price influencers, and strategic tips to optimize procurement processes, particularly for buyers from Africa, South America, the Middle East, and Europe.
Cost Components
-
Materials: The primary materials in vending machines include stainless steel for durability, high-quality plastics for components, and electronic parts for operational efficiency. The choice of materials significantly influences both the initial cost and long-term maintenance.
-
Labor: Labor costs are associated with the assembly and manufacturing of the machines. In regions with lower labor costs, such as parts of Africa and South America, buyers may find more competitive pricing. However, it’s essential to consider the quality of workmanship, as it directly impacts product longevity.
-
Manufacturing Overhead: This includes costs related to factory operations, utilities, and administrative expenses. Efficient manufacturing processes can help reduce overhead costs, thus affecting the final price of the vending machines.
-
Tooling: The costs of specialized tools and molds needed for the production of vending machines can be substantial. These costs are typically amortized over the production volume, so larger orders can benefit from lower per-unit tooling costs.
-
Quality Control (QC): Ensuring the machines meet international quality standards is critical. QC processes involve testing and inspection costs that can add to the overall expense but are essential for maintaining product integrity.
-
Logistics: Shipping costs can vary widely based on the origin of the machines, destination, and chosen shipping method. Buyers should evaluate freight options and potential tariffs or customs duties that may apply.
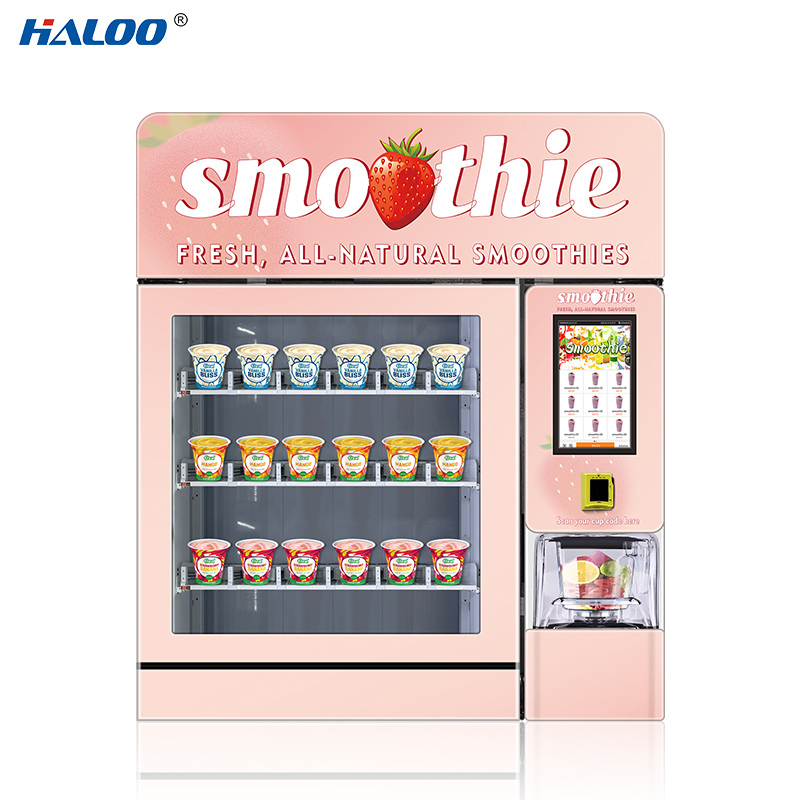
Illustrative Image (Source: Google Search)
- Margin: Supplier margins can vary based on market conditions, competition, and the perceived value of the product. Understanding the typical margins in your specific market can aid in negotiations.
Price Influencers
-
Volume/MOQ: The minimum order quantity (MOQ) can significantly affect pricing. Suppliers often provide discounts for bulk orders, making it beneficial for buyers to assess their demand forecasts accurately.
-
Specifications/Customization: Custom features, such as branding, size, and functionality, can impact pricing. Buyers should clearly define their requirements to avoid unexpected costs.
-
Materials: The quality and source of materials used in the machines can vary widely. Higher-quality materials may increase initial costs but can lead to reduced maintenance and replacement expenses over time.
-
Quality/Certifications: Machines that meet international safety and quality standards often come at a premium. Certifications can assure buyers of reliability and may be necessary for compliance in certain markets.
-
Supplier Factors: Supplier reputation, reliability, and service can influence pricing. A supplier with a proven track record may charge higher prices but can offer better support and warranty terms.
-
Incoterms: Understanding Incoterms is crucial for international transactions. They define the responsibilities of buyers and sellers in terms of shipping, insurance, and tariffs, impacting the total landed cost.
Buyer Tips
-
Negotiation: Always be prepared to negotiate terms and prices. Building a relationship with suppliers can lead to better pricing and terms over time.
-
Cost Efficiency: Evaluate the total cost of ownership, including maintenance, operating costs, and potential downtime. Sometimes, investing in a higher-quality machine can yield long-term savings.
-
Pricing Nuances: Be aware of regional price differences and the economic conditions that may affect pricing. Buyers from Africa and South America may find different pricing strategies compared to their European counterparts.
-
Research and Benchmarking: Conduct thorough market research to understand prevailing prices and features. Benchmarking against similar products can provide leverage in negotiations.
Disclaimer
The prices and cost structures discussed are indicative and can vary based on market conditions, supplier circumstances, and specific buyer requirements. Always conduct detailed due diligence and consult with multiple suppliers to obtain the most accurate pricing information tailored to your needs.
Spotlight on Potential fruit smoothie vending machine Manufacturers and Suppliers
- (No specific manufacturer data was available or requested for detailed profiling in this section for fruit smoothie vending machine.)*
Essential Technical Properties and Trade Terminology for fruit smoothie vending machine
Critical Technical Properties of Fruit Smoothie Vending Machines
When considering the procurement of fruit smoothie vending machines, understanding their technical properties is essential for making informed purchasing decisions. Here are several key specifications that international buyers should prioritize:
-
Material Grade
The material grade of a vending machine significantly impacts its durability and hygiene. Machines are typically made from stainless steel or high-grade plastic, both of which resist corrosion and are easy to clean. High-quality materials ensure longevity, which is a crucial factor for businesses operating in diverse climates. -
Capacity
Capacity refers to the volume of smoothies the machine can dispense within a specified timeframe. This is vital for high-traffic locations where demand can fluctuate. Understanding the capacity helps businesses estimate inventory needs and manage peak hours efficiently. -
Power Consumption
Energy efficiency is an increasingly important consideration, particularly in regions where electricity costs are high. Vending machines with lower power consumption not only reduce operational costs but also contribute to sustainability goals, appealing to environmentally conscious consumers. -
Cooling Technology
The type of cooling technology employed (e.g., compressor-based or thermoelectric) affects the machine’s ability to maintain optimal temperature and freshness of ingredients. This specification is particularly critical in warmer climates where product spoilage can occur more rapidly. -
User Interface
A user-friendly interface enhances customer experience and operational efficiency. Features such as touch screens, multilingual options, and customizable selections can significantly influence customer satisfaction and repeat business. -
Serviceability
The design and engineering of the machine should allow for easy maintenance and repairs. Machines that are difficult to service can lead to prolonged downtime, impacting revenue. Understanding serviceability can help buyers choose machines that minimize maintenance costs and maximize uptime.
Common Trade Terminology in the Vending Machine Industry
Familiarity with industry-specific jargon can facilitate smoother transactions and negotiations. Here are several essential terms that B2B buyers should understand:
-
OEM (Original Equipment Manufacturer)
An OEM is a company that produces components or products that are then marketed by another company under its brand name. For buyers, partnering with reputable OEMs ensures quality and reliability in the machines purchased. -
MOQ (Minimum Order Quantity)
MOQ refers to the smallest quantity of goods that a supplier is willing to sell. Understanding MOQ is crucial for budgeting and inventory management, as it can impact initial investment and operational scalability. -
RFQ (Request for Quotation)
An RFQ is a document sent to suppliers asking for price quotes on specific products or services. This process helps buyers compare pricing and terms, ensuring they secure the best deal for their investment. -
Incoterms (International Commercial Terms)
Incoterms are a set of standardized trade terms used in international shipping to clarify the responsibilities of buyers and sellers. Familiarity with these terms helps buyers understand shipping costs, risks, and responsibilities, which can vary significantly depending on the chosen Incoterm. -
Lead Time
Lead time is the duration from when an order is placed until it is delivered. For B2B buyers, understanding lead times is essential for planning inventory and ensuring that machines are available when needed, especially during peak seasons. -
Warranty
A warranty is a promise from the manufacturer regarding the condition of the product and the commitment to repair or replace it within a specified period. Knowing warranty terms is vital for risk management and can significantly influence the total cost of ownership.
By grasping these technical properties and trade terms, international B2B buyers can make more informed decisions when sourcing fruit smoothie vending machines, ultimately enhancing their operational efficiency and market competitiveness.
Navigating Market Dynamics, Sourcing Trends, and Sustainability in the fruit smoothie vending machine Sector
Market Overview & Key Trends
The fruit smoothie vending machine sector is experiencing significant transformation driven by evolving consumer preferences, technological advancements, and increasing health consciousness. Globally, the demand for healthy, convenient food options is rising, creating a lucrative market for B2B buyers. In regions such as Africa, South America, the Middle East, and Europe, this trend is particularly pronounced, as urbanization and busy lifestyles encourage on-the-go consumption.
Key trends influencing the market include the integration of smart technology in vending machines, such as cashless payment systems and mobile app connectivity, which enhance user experience and operational efficiency. Additionally, the rise of plant-based diets is pushing manufacturers to innovate with diverse smoothie offerings, catering to various dietary preferences, including vegan and gluten-free options.
Moreover, data analytics is becoming crucial for suppliers and operators. By leveraging customer purchasing data, businesses can tailor their product offerings and streamline inventory management, thereby maximizing profitability. International buyers should also be aware of the supply chain dynamics that vary by region, influenced by local agricultural practices and economic conditions. For instance, sourcing fruits locally in Africa and South America can reduce costs and support local economies, while European buyers may focus on quality certifications and sustainability.
Sustainability & Ethical Sourcing in B2B
As sustainability becomes a central theme in global commerce, the fruit smoothie vending machine sector is no exception. B2B buyers increasingly prioritize suppliers who demonstrate a commitment to environmental responsibility. This encompasses sourcing ingredients from ethical suppliers, utilizing biodegradable or recyclable packaging, and investing in energy-efficient machines.
The environmental impact of sourcing practices cannot be overlooked. For instance, opting for locally sourced fruits not only reduces carbon footprints associated with transportation but also supports regional farmers. Buyers should seek out suppliers with green certifications such as Fair Trade or Organic, which assure consumers of the ethical origins of their products.
Furthermore, the adoption of sustainable materials in vending machine construction is gaining traction. Machines made from recycled plastics or featuring energy-efficient refrigeration systems not only appeal to eco-conscious consumers but can also qualify for government incentives or grants aimed at promoting sustainable business practices. By aligning purchasing decisions with sustainable practices, buyers can enhance their brand reputation and meet the growing consumer demand for ethical products.
Brief Evolution/History
The concept of vending machines dates back to ancient times, but the specific sector of fruit smoothie vending machines has evolved rapidly over the past two decades. Initially limited to traditional snack and beverage options, vending machines have transitioned into modern hubs of health and convenience.
The introduction of freshly blended smoothies in vending machines began in the early 2000s, primarily in North America and parts of Europe, as consumers began seeking healthier alternatives. This innovation paved the way for sophisticated machines capable of blending real fruit on demand, offering consumers fresh, nutritious options. As technology has advanced, the integration of smart features and mobile connectivity has further transformed the landscape, making fruit smoothie vending machines a compelling investment for B2B buyers looking to capitalize on the health and wellness trend.
In summary, understanding market dynamics, prioritizing sustainability, and recognizing the evolution of technology are critical for international B2B buyers in the fruit smoothie vending machine sector. By aligning with these trends, businesses can position themselves advantageously in an increasingly competitive landscape.
Related Video: Is global trade transforming? | Counting the Cost
Frequently Asked Questions (FAQs) for B2B Buyers of fruit smoothie vending machine
-
What key factors should I consider when vetting suppliers for fruit smoothie vending machines?
When vetting suppliers, prioritize their industry experience, production capacity, and reputation. Look for suppliers with proven track records in the vending machine sector and positive customer reviews. Assess their compliance with international standards and certifications relevant to your region. It’s also beneficial to request references from other B2B clients and verify their ability to provide after-sales support and spare parts logistics. Establishing a relationship with suppliers who understand the local market dynamics in regions like Africa and South America can also enhance collaboration. -
Can I customize the design and functionality of the smoothie vending machines?
Yes, many manufacturers offer customization options to suit specific market needs. Discuss your requirements regarding machine size, color, branding, and software functionalities, such as payment systems that are popular in your target market. Customization can also extend to the types of smoothies offered, allowing you to cater to local tastes and preferences. Ensure that the supplier can deliver on these customizations within your timeline and budget constraints, and inquire about any additional costs associated with these changes. -
What are the typical minimum order quantities (MOQs) and lead times for international orders?
MOQs can vary significantly between suppliers, often ranging from 10 to 100 units depending on the manufacturer’s capacity and product line. Lead times are also influenced by the order size, customization, and shipping logistics, typically taking 4 to 12 weeks from order placement to delivery. For international buyers from regions like the Middle East or Europe, it’s crucial to discuss these details upfront and consider factors such as local shipping times and customs clearance, which can affect your overall timeline. -
What payment terms should I expect, and what are the best practices for securing transactions?
Payment terms can differ based on the supplier and the nature of the order. Common arrangements include a deposit upfront (20-50%) with the balance due upon shipment or delivery. For large transactions, consider using letters of credit or escrow services to mitigate risks. Ensure that you have a clear written agreement outlining payment schedules, penalties for late payment, and conditions for refunds or returns. Engaging a local financial advisor familiar with international trade can also provide valuable insight into navigating these transactions safely. -
How can I ensure the quality of the smoothie vending machines I purchase?
To ensure quality, request detailed product specifications and quality assurance (QA) certifications from the supplier. Ask about their quality control processes and if they conduct regular inspections during production. It’s beneficial to review third-party testing results and compliance with international standards such as ISO or CE certifications. Additionally, consider visiting the manufacturing facility if possible, or arranging for an independent inspection service to verify quality before shipment. -
What certifications and standards should I look for in fruit smoothie vending machines?
Certifications often vary by region, but common standards to look for include CE marking in Europe, UL certification in the U.S., and ISO certifications for quality management systems. For buyers in Africa and South America, local certifications may also be required. Ensure that the machines comply with health and safety regulations, particularly those related to food and beverage dispensing. Understanding these requirements can help you avoid legal issues and ensure customer safety. -
What logistics considerations should I keep in mind when importing vending machines?
Logistics is a critical aspect of the import process. Collaborate with a freight forwarder experienced in handling machinery to navigate shipping regulations effectively. Consider factors such as container sizes, shipping routes, and customs duties. It’s also important to plan for potential delays due to customs inspections, especially in regions like Africa and the Middle East. Ensure your supplier provides all necessary documentation, including commercial invoices and packing lists, to expedite the customs clearance process. -
How should I address disputes or issues with suppliers after the purchase?
Establish clear terms of engagement in your contract, including clauses for dispute resolution. If issues arise, initiate communication with the supplier promptly to discuss concerns and seek resolution. Utilize formal channels such as mediation or arbitration if necessary, especially for significant financial disputes. Document all communications and agreements to maintain clarity. Additionally, consider engaging local legal counsel who understands the commercial laws in your jurisdiction to assist with any complex disputes that may arise.
Strategic Sourcing Conclusion and Outlook for fruit smoothie vending machine
In the evolving landscape of the fruit smoothie vending machine market, strategic sourcing emerges as a critical component for international B2B buyers. Key takeaways underscore the importance of understanding regional preferences, supplier reliability, and technological advancements. Buyers from Africa, South America, the Middle East, and Europe should prioritize partnerships that not only meet quality standards but also align with local tastes and nutritional trends.
Value of Strategic Sourcing:
– Cost Efficiency: Leveraging local suppliers can reduce logistics costs while ensuring timely delivery.
– Market Adaptability: Engaging with vendors who understand local market dynamics fosters innovation and customization.
– Sustainability: Prioritizing suppliers with eco-friendly practices can enhance brand reputation and appeal to a growing environmentally conscious consumer base.
Looking ahead, the demand for healthy, convenient food options continues to rise, presenting a lucrative opportunity for B2B buyers. As technology advances, integrating smart vending solutions will not only improve operational efficiency but also enhance user experience. To capitalize on these trends, international buyers must remain proactive, continuously evaluating their sourcing strategies to adapt to market changes. Embrace this moment to innovate and secure a competitive edge in the fruit smoothie vending machine sector.