Your Ultimate Guide to Sourcing Food Vending Machines For
Guide to Food Vending Machines For Sale
- Introduction: Navigating the Global Market for food vending machines for sale
- Understanding food vending machines for sale Types and Variations
- Key Industrial Applications of food vending machines for sale
- Strategic Material Selection Guide for food vending machines for sale
- In-depth Look: Manufacturing Processes and Quality Assurance for food vending machines for sale
- Comprehensive Cost and Pricing Analysis for food vending machines for sale Sourcing
- Spotlight on Potential food vending machines for sale Manufacturers and Suppliers
- Essential Technical Properties and Trade Terminology for food vending machines for sale
- Navigating Market Dynamics, Sourcing Trends, and Sustainability in the food vending machines for sale Sector
- Frequently Asked Questions (FAQs) for B2B Buyers of food vending machines for sale
- Strategic Sourcing Conclusion and Outlook for food vending machines for sale
Introduction: Navigating the Global Market for food vending machines for sale
In an era where convenience is paramount, food vending machines have emerged as a vital solution for businesses seeking to meet the demands of an increasingly fast-paced world. These machines not only provide immediate access to food and beverages but also serve as a strategic investment for companies looking to enhance customer satisfaction and optimize operational efficiency. As international B2B buyers from regions such as Africa, South America, the Middle East, and Europe explore opportunities in this growing market, understanding the nuances of food vending machines becomes essential.
This comprehensive guide delves into the various types of food vending machines available, examining their materials, manufacturing processes, and quality control measures. It will also spotlight key suppliers and provide insights into cost considerations to help buyers navigate their purchasing decisions effectively. Additionally, an overview of the market trends and frequently asked questions will empower businesses to make informed choices that align with their unique needs.
By equipping international buyers with the knowledge needed to select the right food vending machines, this guide aims to facilitate strategic sourcing and foster successful partnerships. Whether you are in Vietnam or the UAE, understanding the dynamics of this market will position your business to thrive in the competitive landscape of food service solutions.
Understanding food vending machines for sale Types and Variations
Type Name | Key Distinguishing Features | Primary B2B Applications | Brief Pros & Cons for Buyers |
---|---|---|---|
Traditional Snack Vending | Dispenses packaged snacks and beverages | Offices, schools, public areas | Pros: Low maintenance, easy stocking. Cons: Limited fresh options. |
Fresh Food Vending | Offers perishable items like sandwiches and salads | Hospitals, universities | Pros: Healthier options, attractive to health-conscious consumers. Cons: Requires more maintenance and temperature control. |
Automated Coffee Machines | Provides various coffee beverages, often customizable | Cafes, offices | Pros: High demand for coffee, customizable drinks. Cons: Higher initial investment, requires regular maintenance. |
Combo Vending Machines | Combines snacks and fresh food in one unit | Airports, train stations | Pros: Versatile offerings, maximizes space. Cons: Complex inventory management. |
Healthy Food Vending | Focused on nutritious snacks and meals | Gyms, corporate wellness programs | Pros: Appeals to health trends, can boost brand image. Cons: May have higher costs and require specialized suppliers. |
Traditional Snack Vending
Traditional snack vending machines are the most common type found in various public and private spaces. They primarily dispense packaged snacks, candies, and beverages. These machines are ideal for offices, schools, and public areas where quick, convenient access to snacks is desired. Buyers appreciate their low maintenance requirements and ease of stocking, but the limited selection of fresh options may not meet the growing consumer demand for healthier choices.
Fresh Food Vending
Fresh food vending machines are designed to offer perishable items such as sandwiches, salads, and wraps. These machines are well-suited for locations like hospitals and universities, where fresh meals are in high demand. The key advantage is their ability to cater to health-conscious consumers seeking nutritious meals. However, they require more frequent maintenance and temperature control to ensure food safety and quality, which can be a consideration for B2B buyers.
Automated Coffee Machines
Automated coffee machines provide a range of coffee beverages, from espresso to cappuccino, often with customizable options. They are particularly popular in cafes and office settings where coffee consumption is high. The primary benefit is the ability to meet the constant demand for coffee, which can drive additional revenue. However, the initial investment is higher compared to traditional vending machines, and regular maintenance is necessary to ensure optimal performance.
Combo Vending Machines
Combo vending machines combine the features of snack and fresh food vending in one unit, allowing for a diverse offering. These machines are particularly effective in high-traffic areas such as airports and train stations, where consumers appreciate having multiple options in one location. While they maximize space utilization and cater to varied tastes, they also present challenges in inventory management due to the different types of products offered.
Healthy Food Vending
Healthy food vending machines focus on providing nutritious snacks and meals, appealing to the growing health-conscious demographic. These machines are often found in gyms and corporate wellness programs, aligning with trends towards healthier eating. The benefits include enhancing brand image and meeting consumer demand for better food options. However, they may incur higher costs and require specialized suppliers, making them a more complex investment for B2B buyers.
Related Video: 10 Food Vending Machines You Won’t Believe Exist!
Key Industrial Applications of food vending machines for sale
Industry/Sector | Specific Application of food vending machines for sale | Value/Benefit for the Business | Key Sourcing Considerations for this Application |
---|---|---|---|
Education | Student Cafeterias and Common Areas | Provides convenient access to meals, reducing hunger and improving focus | Compliance with food safety regulations, variety of healthy options |
Corporate Offices | Break Rooms and Lounge Areas | Enhances employee satisfaction and productivity through accessible food options | Energy efficiency, customizable product offerings, payment options |
Hospitals and Healthcare | Patient and Visitor Areas | Offers easy access to nutritious snacks and meals, supporting recovery and visitor comfort | Nutritional value, hygiene standards, user-friendly interface |
Transportation Hubs | Airports and Train Stations | Serves travelers with quick meal options, enhancing customer experience | Space constraints, payment systems, product rotation to minimize waste |
Retail Environments | Shopping Malls and Grocery Stores | Increases foot traffic and impulse purchases, providing a diverse food selection | Shelf life of products, branding opportunities, integration with loyalty programs |
Education
In educational institutions, food vending machines are strategically placed in student cafeterias and common areas. They solve the problem of limited access to nutritious meals, especially during busy schedules, helping students maintain energy levels and focus on their studies. B2B buyers in this sector should prioritize machines that comply with local food safety regulations and offer a variety of healthy options to cater to diverse dietary needs.
Corporate Offices
Corporate offices utilize food vending machines in break rooms and lounge areas to enhance employee satisfaction. By providing convenient access to meals and snacks, these machines contribute to improved productivity and morale. International buyers should consider energy-efficient models with customizable product offerings and flexible payment options to meet the needs of their workforce effectively.
Hospitals and Healthcare
In hospitals, food vending machines are essential in patient and visitor areas, offering easy access to nutritious snacks and meals. This availability supports patient recovery and enhances visitor comfort during their stay. Buyers in this sector must focus on machines that meet high hygiene standards, provide nutritional information, and feature user-friendly interfaces for all demographics.
Transportation Hubs
Transportation hubs such as airports and train stations deploy food vending machines to serve travelers with quick meal options. This application enhances customer experience by providing accessible food choices during transit. Key considerations for B2B buyers include accommodating space constraints, ensuring reliable payment systems, and implementing product rotation strategies to minimize waste and maximize freshness.
Retail Environments
In shopping malls and grocery stores, food vending machines increase foot traffic and encourage impulse purchases by offering a diverse selection of food products. This application enhances the shopping experience and provides additional revenue streams for retailers. Buyers should focus on the shelf life of products, branding opportunities for promotional purposes, and the ability to integrate these machines with existing loyalty programs to attract repeat customers.
Related Video: Crane Fresh Food Shopper Vending Machine
Strategic Material Selection Guide for food vending machines for sale
When selecting materials for food vending machines, international B2B buyers must consider several factors that impact performance, durability, and compliance with local regulations. Below is an analysis of four common materials used in the construction of food vending machines, highlighting their properties, advantages, disadvantages, and considerations for buyers from diverse regions including Africa, South America, the Middle East, and Europe.
Stainless Steel
Key Properties:
Stainless steel is known for its excellent corrosion resistance, high strength, and ability to withstand high temperatures and pressures. It typically has a temperature rating of up to 1000°F (537°C) and is resistant to various chemicals.
Pros & Cons:
Stainless steel is highly durable and easy to clean, making it ideal for food applications. However, it can be more expensive than other materials and may require complex manufacturing processes, such as welding and polishing.
Impact on Application:
This material is suitable for environments where hygiene is paramount, such as in food vending machines that dispense hot or cold beverages and snacks. Its resistance to rust and staining makes it compatible with a wide range of food products.
Specific Considerations for Buyers:
Buyers should ensure compliance with food safety standards such as FDA regulations and European Union directives. Common standards like ASTM A240 for stainless steel can guide material selection.
Polycarbonate
Key Properties:
Polycarbonate is a high-performance thermoplastic with excellent impact resistance and clarity. It can withstand temperatures ranging from -40°F to 240°F (-40°C to 116°C) and has good UV resistance.
Pros & Cons:
The main advantage of polycarbonate is its lightweight nature and shatter resistance, making it ideal for transparent panels in vending machines. However, it may not be as durable as metals and can be prone to scratching.
Impact on Application:
Polycarbonate is often used for the viewing windows of vending machines, allowing customers to see the products inside. It is also effective in protecting sensitive electronic components from external damage.
Specific Considerations for Buyers:
Buyers should consider UV stability and the potential for scratching, which can affect product visibility. Compliance with local safety standards, such as those set by ANSI or ISO, is also crucial.
Aluminum
Key Properties:
Aluminum is lightweight, corrosion-resistant, and has good thermal conductivity. It can handle temperatures up to 800°F (427°C) and is often anodized for enhanced durability.
Pros & Cons:
Aluminum’s lightweight nature makes it easy to handle and install, and it is generally less expensive than stainless steel. However, it may not be suitable for high-stress applications due to lower strength compared to steel.
Impact on Application:
Aluminum is often used in the structural components of vending machines, including frames and panels. Its thermal properties make it suitable for machines that require temperature regulation.
Specific Considerations for Buyers:
International buyers should ensure that the aluminum grades used comply with standards like ASTM B221. Additionally, anodizing processes should meet local environmental regulations.
Glass
Key Properties:
Glass is a rigid material that offers excellent transparency and aesthetic appeal. It can withstand moderate temperatures but is generally more fragile than other materials.
Pros & Cons:
The primary advantage of glass is its ability to provide a clear view of the products inside the vending machine. However, its fragility can lead to breakage, and it is heavier than other materials.
Impact on Application:
Glass is commonly used for doors and panels in vending machines, enhancing the visual appeal and allowing for product visibility. It is suitable for environments where aesthetics are important.
Specific Considerations for Buyers:
Buyers should consider the type of glass used (e.g., tempered glass) to ensure safety and durability. Compliance with safety standards, such as those from the American National Standards Institute (ANSI), is essential.
Summary Table
Material | Typical Use Case for food vending machines for sale | Key Advantage | Key Disadvantage/Limitation | Relative Cost (Low/Med/High) |
---|---|---|---|---|
Stainless Steel | Structural components, internal frameworks | High durability and corrosion resistance | Higher cost, complex manufacturing | High |
Polycarbonate | Viewing windows, protective panels | Lightweight, shatter-resistant | Prone to scratching, lower durability | Medium |
Aluminum | Frames, panels, structural components | Lightweight, cost-effective | Lower strength compared to steel | Medium |
Glass | Doors, display panels | Excellent transparency and aesthetics | Fragile, heavier than alternatives | Medium |
This strategic material selection guide should aid international B2B buyers in making informed decisions when sourcing food vending machines, ensuring compliance with local regulations and suitability for their specific applications.
In-depth Look: Manufacturing Processes and Quality Assurance for food vending machines for sale
The manufacturing process for food vending machines involves multiple stages, each crucial for ensuring a high-quality final product. Understanding these stages and the associated quality assurance practices is essential for B2B buyers, especially those operating in diverse markets like Africa, South America, the Middle East, and Europe.
Manufacturing Process Stages
-
Material Preparation
– Sourcing: Quality vending machines start with high-grade materials. Common materials include stainless steel for durability and plastic for various components. Suppliers should provide certifications for the materials used, ensuring they meet international standards.
– Pre-processing: Before manufacturing, materials undergo cutting, bending, and surface treatment. This stage often involves laser cutting and CNC machining for precision. -
Forming
– Fabrication Techniques: Techniques such as welding, stamping, and molding are utilized to shape the machine components. For instance, the chassis may be welded from steel plates, while internal components might be molded from high-strength plastics.
– Automation: Many manufacturers employ robotic systems in forming processes, enhancing precision and reducing human error. This is particularly beneficial in high-volume production settings. -
Assembly
– Component Integration: This stage involves assembling the various components, including refrigeration units, electronic systems, and payment mechanisms. A systematic approach, often using assembly lines, ensures efficiency.
– Testing During Assembly: As components are integrated, preliminary tests (e.g., electrical tests) are conducted to ensure functionality before moving on to final assembly. -
Finishing
– Surface Treatment: After assembly, the machines undergo surface treatments such as powder coating or painting to enhance appearance and protect against corrosion.
– Final Assembly and Quality Checks: The final product is assembled, and a series of quality checks are conducted to ensure all systems operate correctly.
Quality Assurance Standards
B2B buyers must be aware of the various international and industry-specific standards that govern the manufacturing of food vending machines.
- ISO 9001: This standard focuses on quality management systems. It ensures that manufacturers have processes in place for consistent quality and customer satisfaction.
- CE Marking: For products sold in Europe, CE marking indicates conformity with health, safety, and environmental protection standards. Buyers should verify that the machines are CE marked to ensure compliance.
- API Standards: In certain regions, adherence to American Petroleum Institute (API) standards may be required, particularly for machines incorporating oil-based products.
Quality Control Checkpoints
Quality control (QC) checkpoints are integral to the manufacturing process. Here are the typical checkpoints:
-
Incoming Quality Control (IQC):
– Materials and components are inspected upon arrival at the manufacturing facility. This ensures that only high-quality inputs are used in production. -
In-Process Quality Control (IPQC):
– During manufacturing, regular checks are performed at various stages to catch defects early. This includes monitoring dimensions, tolerances, and functionality of components. -
Final Quality Control (FQC):
– Before shipment, each vending machine undergoes a thorough inspection. This includes functional tests, safety checks, and aesthetic evaluations to ensure that all specifications are met.
Common Testing Methods
B2B buyers should be familiar with various testing methods employed during the QC process:
- Electrical Testing: Ensures all electronic components function correctly, including payment systems and sensors.
- Mechanical Testing: Checks the structural integrity and durability of the machine, including stress tests on parts like the door and internal shelves.
- Temperature Testing: Particularly important for machines with refrigeration units, this test confirms that temperature controls are functioning within specified limits.
Verifying Supplier Quality Control
When sourcing food vending machines, it is vital for international buyers to verify the quality control practices of suppliers. Here are key steps:
- Supplier Audits: Conducting audits at the manufacturing site allows buyers to assess the QC processes firsthand. This includes reviewing their quality management systems and compliance with international standards.
- Requesting Quality Reports: Buyers should ask for detailed reports on the QC tests conducted, including any certifications received from recognized third-party organizations.
- Third-party Inspections: Engaging third-party inspection services can provide an unbiased evaluation of the manufacturing processes and product quality.
Nuances for International B2B Buyers
For buyers from Africa, South America, the Middle East, and Europe, several nuances may affect procurement:
- Regulatory Compliance: Different regions have varying regulations regarding food safety and machine standards. Buyers should ensure that suppliers comply with local regulations.
- Cultural Considerations: Understanding cultural expectations regarding product functionality and aesthetics can enhance buyer-supplier relationships.
- Logistical Challenges: Shipping and customs regulations can vary significantly. Buyers should work with suppliers who have experience in international logistics to ensure smooth delivery.
By understanding the manufacturing processes and quality assurance practices related to food vending machines, international B2B buyers can make informed purchasing decisions. Ensuring compliance with standards and rigorous quality checks not only protects the buyer’s investment but also enhances customer satisfaction in their respective markets.
Related Video: Parle-G Biscuits Manufacturing process – Food Factory Tour- Modern Food factory, Mega Factory II
Comprehensive Cost and Pricing Analysis for food vending machines for sale Sourcing
When considering the procurement of food vending machines, a thorough understanding of the cost structure and pricing dynamics is essential for international B2B buyers, especially those operating in Africa, South America, the Middle East, and Europe. This analysis will provide insights into the various cost components, pricing influencers, and actionable tips for navigating the procurement process effectively.
Cost Components
-
Materials: The primary costs arise from the raw materials used to manufacture vending machines. This includes metals for the chassis, plastics for the casing, and electronic components for functionality. Buyers should consider sourcing materials locally when possible to mitigate import costs.
-
Labor: Labor costs vary significantly by region. In countries with lower labor costs, such as some parts of Asia, manufacturers may offer competitive pricing. However, labor costs in Europe and North America can be substantially higher, affecting the overall price of the machines.
-
Manufacturing Overhead: This encompasses costs related to utilities, factory maintenance, and administrative expenses associated with production. A higher overhead can lead to increased machine prices, so it is crucial to inquire about the manufacturer’s operational efficiency.
-
Tooling: Custom tooling for machine components can add significant costs, particularly for specialized designs. Buyers should weigh the benefits of customization against the associated tooling costs, especially for smaller orders.
-
Quality Control (QC): Rigorous QC processes ensure the machines meet safety and operational standards. While this may increase initial costs, it is critical for long-term reliability and customer satisfaction.
-
Logistics: Shipping and handling costs can vary greatly depending on the distance from the manufacturer to the buyer’s location. Buyers should factor in freight costs, customs duties, and potential tariffs when budgeting.
-
Margin: Manufacturers typically apply a profit margin that can range from 10% to 30%, depending on the complexity and customization of the machines. Understanding this margin can aid in negotiations.
Price Influencers
-
Volume/MOQ: Pricing often improves with larger order quantities. Buyers should assess their capacity to purchase in bulk to take advantage of economies of scale.
-
Specifications/Customization: Machines with specific features or custom branding will generally cost more. It’s important to balance the need for customization with budget constraints.
-
Materials and Quality: Higher-quality materials and certifications (e.g., ISO, CE) can increase costs but also enhance durability and reliability. Buyers should evaluate whether the additional investment aligns with their operational needs.
-
Supplier Factors: The reputation and location of the supplier can influence pricing. Established suppliers with a track record of reliability may charge a premium, but this can lead to better after-sales support.
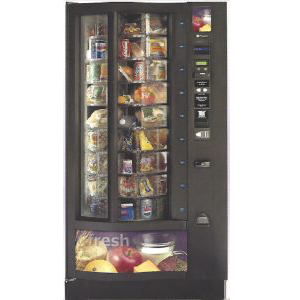
Illustrative Image (Source: Google Search)
- Incoterms: Understanding the agreed Incoterms is vital as they dictate who bears the costs and risks during shipping. Terms like FOB (Free on Board) or CIF (Cost, Insurance, and Freight) can significantly impact the total landed cost.
Buyer Tips
-
Negotiate Effectively: Leverage your understanding of the cost structure to negotiate better prices. Being informed about the various components allows for strategic discussions around pricing.
-
Focus on Cost-Efficiency: Consider the Total Cost of Ownership (TCO), which includes purchase price, maintenance, and operational costs over the machine’s lifecycle, rather than just the initial purchase price.
-
Understand Pricing Nuances: International buyers should be aware that prices can fluctuate based on currency exchange rates and geopolitical factors. Regularly check market trends and forecasts to time your purchases effectively.
-
Request Detailed Quotes: Always ask for itemized quotes to understand what is included in the price. This transparency can help identify potential areas for cost savings.
By applying these insights, B2B buyers can make informed decisions when sourcing food vending machines, ensuring they achieve the best value for their investment while navigating the complexities of international trade.
Spotlight on Potential food vending machines for sale Manufacturers and Suppliers
This section offers a look at a few manufacturers active in the ‘food vending machines for sale’ market. This is a representative sample for illustrative purposes; B2B buyers must conduct their own extensive due diligence before any engagement. Information is synthesized from public sources and general industry knowledge.
Essential Technical Properties and Trade Terminology for food vending machines for sale
When considering the purchase of food vending machines, understanding the essential technical properties and industry terminology is crucial for making informed decisions. Below is an overview of key specifications and common jargon relevant to international B2B buyers.
Critical Technical Specifications
-
Material Grade
– Definition: Refers to the quality and type of materials used in the construction of the vending machine, such as stainless steel, plastic, or aluminum.
– B2B Importance: High-grade materials ensure durability, resistance to corrosion, and longevity, which are essential for machines operating in various environments, especially in humid or high-traffic areas. -
Capacity
– Definition: The total volume or number of items a vending machine can hold, often measured in liters or number of compartments.
– B2B Importance: Understanding capacity helps businesses choose machines that meet their volume requirements, optimizing inventory management and reducing restocking frequency.
-
Power Consumption
– Definition: The amount of electricity a vending machine uses, typically measured in watts.
– B2B Importance: Lower power consumption translates to reduced operational costs, which is vital for profitability, especially in regions with high electricity prices. -
Temperature Control Range
– Definition: The range of temperatures that the machine can maintain, crucial for machines selling perishable items.
– B2B Importance: Ensuring appropriate temperature control is critical for food safety and compliance with local health regulations, protecting both the supplier and the buyer. -
User Interface
– Definition: The design and functionality of the machine’s display and payment systems, including touchscreens or button interfaces.
– B2B Importance: An intuitive user interface enhances customer experience, potentially increasing sales and reducing technical support needs.
Common Trade Terminology
-
OEM (Original Equipment Manufacturer)
– Definition: A company that produces parts and equipment that may be marketed by another manufacturer.
– Importance: Understanding OEM relationships can help buyers identify reputable suppliers and ensure compatibility with existing systems. -
MOQ (Minimum Order Quantity)
– Definition: The smallest quantity of a product that a supplier is willing to sell.
– Importance: Knowing the MOQ is essential for budgeting and inventory planning, especially for new market entrants or smaller businesses. -
RFQ (Request for Quotation)
– Definition: A document sent to suppliers requesting a price quote for specific products or services.
– Importance: Submitting RFQs allows buyers to compare pricing and terms from multiple suppliers, aiding in cost-effective purchasing decisions. -
Incoterms (International Commercial Terms)
– Definition: A set of predefined international trade terms that clarify the responsibilities of buyers and sellers.
– Importance: Familiarity with Incoterms helps buyers understand shipping costs, risks, and responsibilities, minimizing disputes and ensuring smoother transactions. -
Lead Time
– Definition: The amount of time from placing an order until it is delivered.
– Importance: Knowing the lead time is crucial for supply chain management and helps businesses plan for inventory needs and market demands effectively.
By familiarizing themselves with these specifications and terms, international B2B buyers can navigate the complexities of the food vending machine market more effectively, ensuring they make strategic purchasing decisions that align with their business goals.
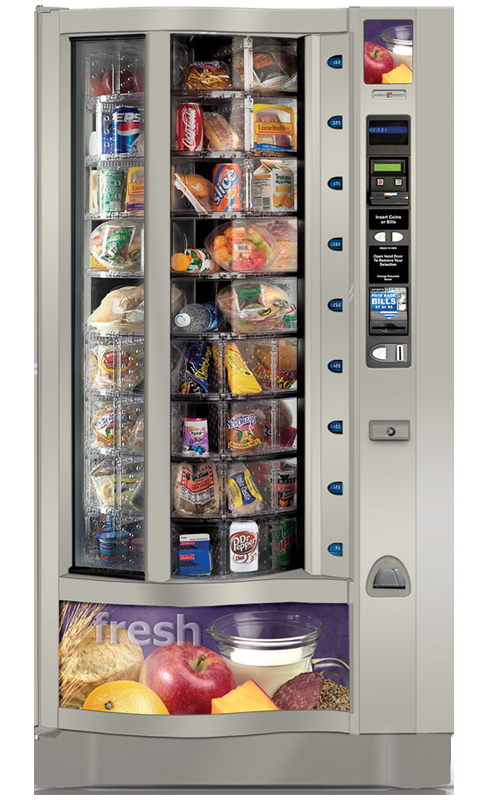
Illustrative Image (Source: Google Search)
Navigating Market Dynamics, Sourcing Trends, and Sustainability in the food vending machines for sale Sector
In the rapidly evolving landscape of food vending machines, several key trends are shaping the market dynamics for international B2B buyers, particularly from regions such as Africa, South America, the Middle East, and Europe.
Market Overview & Key Trends
The global food vending machine market is primarily driven by the increasing demand for convenience and healthy food options. Consumers are seeking quick access to nutritious snacks and meals, which has prompted manufacturers to innovate and enhance the functionality of vending machines. In regions like Africa and South America, where urbanization is on the rise, the adoption of vending machines is expected to surge. Key trends include the integration of technology, such as cashless payment systems and IoT capabilities, which allow for real-time inventory management and customer interaction.
Moreover, sustainability is becoming a significant factor influencing purchasing decisions. Buyers are increasingly looking for machines that offer eco-friendly options, such as energy-efficient models and those that support biodegradable packaging. Emerging markets are also witnessing a shift towards machines that cater to local tastes and dietary preferences, which can be a crucial factor for success in diverse markets. Companies that can provide customizable solutions will likely gain a competitive edge.
International B2B buyers should be aware of the regulatory environment in their respective countries, particularly regarding health and safety standards. Understanding local consumer behavior and preferences is essential for sourcing machines that align with market demands.
Sustainability & Ethical Sourcing in B2B
The environmental impact of food vending machines is a growing concern among businesses and consumers alike. The sector is increasingly focusing on sustainability, with many manufacturers adopting eco-friendly practices in production and sourcing. Ethical supply chains are essential, as they not only reduce environmental footprints but also enhance brand reputation.
For B2B buyers, prioritizing vendors with sustainability certifications can lead to better sourcing decisions. Certifications such as ISO 14001 (Environmental Management) and LEED (Leadership in Energy and Environmental Design) signal a commitment to sustainable practices. Additionally, the use of recyclable materials and energy-efficient technologies is becoming a standard requirement.
Investing in machines that promote healthy eating and minimize waste, such as those that use digital displays to showcase nutritional information, can also appeal to the growing consumer base that values health and wellness. As the focus on sustainability continues to rise, aligning procurement strategies with eco-friendly practices can provide a competitive advantage.
Brief Evolution/History
The evolution of food vending machines has been marked by significant technological advancements and changing consumer preferences. Initially designed to dispense simple snacks, modern vending machines now offer a wide array of products, including fresh meals, beverages, and even healthy options. The introduction of cashless payment systems and touchless interactions has transformed the user experience, making it more convenient and appealing.
The shift towards healthier options began in the early 2000s as awareness of nutrition increased. Today, vending machines are often seen in workplaces, schools, and public spaces, reflecting their integration into daily life. This evolution underscores the importance of innovation and adaptability in meeting consumer demands, making it a crucial consideration for international B2B buyers looking to invest in this sector.
Related Video: Incoterms for beginners | Global Trade Explained
Frequently Asked Questions (FAQs) for B2B Buyers of food vending machines for sale
-
What factors should I consider when vetting suppliers of food vending machines?
When vetting suppliers, prioritize their experience in the food vending machine industry, checking their reputation through customer reviews and testimonials. Assess their manufacturing capabilities and whether they can meet your specific requirements. Verify certifications and compliance with international safety standards, particularly those relevant to food handling. Request references from previous clients to gauge their reliability and service quality. Finally, consider the supplier’s financial stability to ensure they can fulfill large orders consistently. -
Can I customize the food vending machines to fit my branding and product offerings?
Yes, many suppliers offer customization options for food vending machines. This can include branding elements such as logos, colors, and machine design. You may also request specific configurations for product selection, payment systems, and technology integration (e.g., cashless payment options). Discuss your requirements upfront and ensure that the supplier can accommodate them. Be aware that customization may affect the lead time and minimum order quantity (MOQ). -
What are the typical minimum order quantities (MOQ) and lead times for food vending machines?
Minimum order quantities can vary significantly between suppliers, often ranging from 5 to 50 units, depending on the machine’s complexity and customization. Lead times typically range from 4 to 12 weeks after the order is confirmed, influenced by the supplier’s production capacity and your customization requests. It’s advisable to discuss these details early in the negotiation process to align your expectations and timeline with the supplier’s capabilities. -
What payment terms are generally offered for international B2B transactions?
Payment terms can vary widely based on the supplier’s policies and your negotiation. Common arrangements include full payment upfront, a deposit with the balance due before shipment, or net terms (e.g., 30 or 60 days post-delivery). For international transactions, consider using secure payment methods such as letters of credit or escrow services to mitigate risks. Always clarify payment terms in the contract to avoid misunderstandings. -
What quality assurance measures and certifications should I look for?
Ensure that the supplier adheres to international quality standards, such as ISO 9001 for quality management systems and ISO 22000 for food safety management. Request documentation of quality assurance processes, including testing procedures for machine functionality and safety. Certifications from recognized organizations can provide additional assurance of the supplier’s commitment to quality. Regular audits and inspections should also be part of their quality management practices. -
How can I manage logistics and shipping for my food vending machine orders?
Logistics management is crucial for timely delivery. Discuss shipping options with your supplier, including Incoterms that clarify responsibilities for shipping costs and risks. Consider working with a freight forwarder experienced in international shipping to streamline the process. Be mindful of customs regulations in your country and ensure all necessary documentation is prepared in advance to avoid delays. Tracking shipments can help you stay informed about delivery timelines. -
What should I do if I encounter disputes with my supplier?
In the event of a dispute, communication is key. Start by addressing the issue directly with the supplier to seek a resolution. If informal discussions do not resolve the matter, refer to the terms outlined in your contract regarding dispute resolution processes, such as mediation or arbitration. It is advisable to include an arbitration clause in your contract that specifies the governing law and jurisdiction. Keeping thorough records of all communications can also support your case. -
Are there specific logistical challenges I should anticipate when sourcing food vending machines internationally?
Yes, several logistical challenges may arise, including customs delays, shipping costs, and compliance with local regulations regarding food safety and machine operation. Understand the customs requirements in your country, as well as any import tariffs that may apply. Additionally, consider the potential need for local installation and maintenance services, which may require coordination with local suppliers. Proper planning and risk assessment can help mitigate these challenges effectively.
Strategic Sourcing Conclusion and Outlook for food vending machines for sale
In summary, effective strategic sourcing of food vending machines offers significant advantages for international B2B buyers, particularly in emerging markets such as Africa, South America, the Middle East, and Europe. By understanding local consumer preferences, regulatory environments, and supply chain dynamics, buyers can optimize their procurement processes.
Key Takeaways:
– Market Research: Conduct thorough market analysis to align product offerings with regional demands.
– Supplier Relationships: Build strong partnerships with reliable suppliers to ensure quality and timely delivery.
– Cost Management: Leverage competitive pricing and explore financing options to enhance ROI.
Investing in food vending machines not only caters to the growing demand for convenient food options but also positions businesses to capitalize on evolving consumer trends. As you explore opportunities in this sector, consider the long-term benefits of strategic sourcing as a pathway to sustainable growth.
Call to Action: As the global marketplace becomes increasingly interconnected, now is the time to take proactive steps towards sourcing food vending machines. Engage with suppliers who understand your market and can provide tailored solutions to meet your unique needs. Embrace this opportunity to enhance your business portfolio and cater to the evolving demands of your customers.