Your Ultimate Guide to Sourcing First Aid Vending Machine
Guide to First Aid Vending Machine
- Introduction: Navigating the Global Market for first aid vending machine
- Understanding first aid vending machine Types and Variations
- Key Industrial Applications of first aid vending machine
- Strategic Material Selection Guide for first aid vending machine
- In-depth Look: Manufacturing Processes and Quality Assurance for first aid vending machine
- Comprehensive Cost and Pricing Analysis for first aid vending machine Sourcing
- Spotlight on Potential first aid vending machine Manufacturers and Suppliers
- Essential Technical Properties and Trade Terminology for first aid vending machine
- Navigating Market Dynamics, Sourcing Trends, and Sustainability in the first aid vending machine Sector
- Frequently Asked Questions (FAQs) for B2B Buyers of first aid vending machine
- Strategic Sourcing Conclusion and Outlook for first aid vending machine
Introduction: Navigating the Global Market for first aid vending machine
In an era where health and safety are paramount, first aid vending machines have emerged as a vital resource for businesses and public spaces. These innovative solutions not only provide immediate access to essential medical supplies but also enhance workplace safety protocols and compliance with health regulations. For international B2B buyers, particularly those in Africa, South America, the Middle East, and Europe, understanding the landscape of first aid vending machines is crucial for making informed purchasing decisions.
This comprehensive guide delves into the various types of first aid vending machines available, examining key factors such as materials used, manufacturing and quality control processes, and the most reliable suppliers in the market. Additionally, we will provide insights into cost considerations, market trends, and frequently asked questions that will empower businesses to navigate their options effectively.
By leveraging this guide, B2B buyers will be equipped to assess the unique needs of their organizations and choose the right first aid vending machine that aligns with their operational goals. Whether you are a procurement officer in a multinational corporation or a small business owner in need of efficient safety solutions, this resource aims to enhance your sourcing strategy, ensuring that your workplace remains prepared and compliant in the face of emergencies.
Understanding first aid vending machine Types and Variations
Type Name | Key Distinguishing Features | Primary B2B Applications | Brief Pros & Cons for Buyers |
---|---|---|---|
Traditional Vending Machine | Dispenses pre-packaged first aid supplies | Offices, factories, schools | Pros: Familiar technology; easy to restock. Cons: Limited customization and may require frequent maintenance. |
Smart Vending Machine | IoT-enabled, inventory tracking, user interaction | Hospitals, clinics, large corporations | Pros: Real-time data on stock levels; customizable user interface. Cons: Higher initial investment; requires reliable internet access. |
Mobile First Aid Unit | Portable units with a variety of supplies | Events, construction sites | Pros: Flexibility in location; can be tailored to specific needs. Cons: Limited stock capacity; may require regular servicing. |
Automated Defibrillator Vending Machine | Specialized for AEDs and emergency supplies | Public spaces, gyms, schools | Pros: Quick access to critical supplies; enhances safety compliance. Cons: Higher cost; requires education on usage. |
Customizable First Aid Station | Tailored setups for specific environments | Industrial sites, remote locations | Pros: Meets specific workplace needs; can include unique supplies. Cons: Longer lead time for setup; potential higher costs. |
Traditional Vending Machine
Traditional first aid vending machines are designed to dispense pre-packaged first aid supplies such as band-aids, antiseptic wipes, and gauze. They are commonly found in offices, factories, and schools where quick access to basic medical supplies is essential. While these machines are familiar and easy to maintain, their limited customization options and the need for regular restocking can be drawbacks for businesses looking for a more tailored solution.
Smart Vending Machine
Smart vending machines represent a technological advancement in first aid supply management. Equipped with IoT capabilities, these machines provide real-time inventory tracking and a customizable user interface. They are particularly suitable for hospitals, clinics, and large corporations, where monitoring stock levels is crucial for operational efficiency. However, the higher initial investment and dependency on reliable internet access may deter some buyers.
Mobile First Aid Unit
Mobile first aid units offer flexibility and adaptability, making them ideal for events or construction sites where medical needs can vary significantly. These portable units can be stocked with a variety of first aid supplies tailored to specific situations. While they provide convenience and quick access, their limited stock capacity and need for regular servicing can be a concern for businesses that require extensive supplies on-site.
Automated Defibrillator Vending Machine
Automated defibrillator vending machines are specialized units designed to store and dispense Automated External Defibrillators (AEDs) and other emergency medical supplies. These machines are essential in public spaces, gyms, and schools, where immediate access to life-saving equipment can make a significant difference. While they enhance safety compliance, their higher cost and the necessity for user education on proper usage can pose challenges for potential buyers.
Customizable First Aid Station
Customizable first aid stations allow businesses to create a tailored setup that meets their specific workplace needs. These stations can include a variety of unique supplies based on the environment, making them ideal for industrial sites and remote locations. While they offer a personalized approach, the longer lead time for setup and potential higher costs may be considerations for businesses looking to implement these solutions.
Related Video: 1. Risk Communication. Models. Definitions
Key Industrial Applications of first aid vending machine
Industry/Sector | Specific Application of First Aid Vending Machine | Value/Benefit for the Business | Key Sourcing Considerations for this Application |
---|---|---|---|
Manufacturing | On-site emergency supplies for workers | Quick access to essential first aid, reducing downtime | Compliance with health regulations, product variety |
Hospitality | Guest and staff first aid stations | Enhances safety perception, improves guest experience | User-friendly design, 24/7 availability |
Education | Emergency response in schools | Immediate care for injuries, promoting a safe environment | Adaptability for various age groups, maintenance support |
Construction | First aid provisions on construction sites | Minimizes injury impact, ensures legal compliance | Robustness against harsh environments, refill logistics |
Corporate Offices | Health and safety support for employees | Boosts employee morale, reduces liability risks | Customization options, integration with health programs |
Manufacturing
In the manufacturing sector, first aid vending machines are critical for providing immediate access to emergency supplies for workers exposed to potential hazards. These machines can be strategically placed near production lines to ensure that any injuries can be addressed swiftly, significantly reducing the downtime associated with workplace injuries. International buyers should consider sourcing machines that comply with local health and safety regulations and offer a comprehensive range of products tailored to specific industrial risks.
Hospitality
In the hospitality industry, first aid vending machines serve both guests and staff, enhancing the overall safety perception of the establishment. By providing quick access to essential first aid items, hotels and resorts can improve guest experiences while also preparing staff for emergencies. Key considerations for B2B buyers include the aesthetic design of the machines, ease of use, and the ability to restock items in a timely manner to maintain service quality.
Education
Schools and educational institutions can benefit significantly from first aid vending machines, which ensure that immediate care is available for injuries that may occur on campus. These machines can be placed in high-traffic areas, allowing for quick responses to accidents, thus fostering a safer learning environment. Buyers in this sector should focus on machines that are user-friendly and capable of catering to various age groups, ensuring that children can easily access the necessary supplies.
Construction
On construction sites, first aid vending machines play a vital role in minimizing the impact of injuries. Given the high-risk nature of construction work, having immediate access to first aid supplies can be life-saving. B2B buyers in this field should prioritize sourcing machines that are durable and designed to withstand harsh environments, as well as those that facilitate easy restocking to ensure continuous availability of supplies.
Corporate Offices
For corporate offices, first aid vending machines provide essential health and safety support for employees. By offering immediate access to first aid supplies, companies can boost employee morale and reduce potential liability risks associated with workplace injuries. Buyers should look for machines that can be customized to meet specific organizational health programs and that feature easy integration into existing safety protocols.
Related Video: First Aid – Initial Steps Training
Strategic Material Selection Guide for first aid vending machine
When selecting materials for first aid vending machines, it is crucial to consider factors such as durability, cost, and compliance with international standards. Below is an analysis of four common materials used in the construction of these machines, focusing on their properties, advantages, disadvantages, and specific considerations for international B2B buyers.
1. Stainless Steel
Key Properties:
Stainless steel is known for its excellent corrosion resistance and high strength-to-weight ratio. It can withstand a wide range of temperatures and pressures, making it suitable for various environments.
Pros & Cons:
The durability of stainless steel is one of its primary advantages, as it can withstand harsh conditions without significant wear. However, it tends to be more expensive than other materials, which can affect the overall cost of the vending machine. Manufacturing complexity can also be higher due to the need for specialized equipment for cutting and welding.
Impact on Application:
Stainless steel is compatible with a wide variety of first aid supplies, ensuring that items remain uncontaminated. Its non-porous surface is easy to clean, which is essential for maintaining hygiene in medical applications.
Considerations for International Buyers:
Compliance with standards such as ASTM A240 for stainless steel is crucial. Buyers from regions like Europe and the Middle East should ensure that the material meets local regulations regarding food and medical safety.
2. Polycarbonate
Key Properties:
Polycarbonate is a high-performance plastic known for its impact resistance and clarity. It can operate effectively in a temperature range of -40°C to 120°C.
Pros & Cons:
One of the key advantages of polycarbonate is its lightweight nature, which reduces shipping costs and makes installation easier. However, it is less durable than metals and can be susceptible to scratching and UV degradation over time.
Impact on Application:
Polycarbonate is ideal for transparent panels in vending machines, allowing visibility of the contents. This visibility can enhance user interaction and trust in the machine’s offerings.
Considerations for International Buyers:
Buyers should check for compliance with standards such as ISO 11607 for packaging materials used in sterilized medical devices. In regions like Africa and South America, where UV exposure can be high, ensuring UV-stabilized polycarbonate is critical.
3. Aluminum
Key Properties:
Aluminum is lightweight, corrosion-resistant, and has good thermal conductivity. It can be anodized for enhanced durability and aesthetic appeal.
Pros & Cons:
Aluminum offers a good balance between cost and performance, making it a popular choice for many applications. However, it is not as strong as stainless steel and may require additional reinforcements in high-stress areas.
Impact on Application:
Aluminum is suitable for structural components of vending machines, providing adequate support without adding excessive weight. Its corrosion resistance helps maintain the integrity of the machine in various environments.
Considerations for International Buyers:
Buyers should ensure that aluminum components meet standards such as ASTM B221 for extruded aluminum products. In regions like the Middle East, where humidity can affect metal performance, selecting high-grade aluminum is advisable.
4. Powder-Coated Steel
Key Properties:
Powder-coated steel combines the strength of steel with a protective coating that enhances corrosion resistance and aesthetics. The coating can withstand a range of temperatures and is available in various colors.
Pros & Cons:
The key advantage of powder-coated steel is its durability and resistance to scratches and fading. However, if the coating is damaged, the underlying steel can corrode, which may lead to long-term maintenance issues.
Impact on Application:
This material is particularly effective for external surfaces of vending machines, providing a robust barrier against environmental factors. The aesthetic appeal of powder coating can also enhance the machine’s visibility and branding.
Considerations for International Buyers:
Compliance with environmental regulations regarding coatings is essential. Buyers should verify that the powder coating meets standards like ASTM D3359 for adhesion testing, especially in regions where environmental conditions can vary significantly.
Summary Table
Material | Typical Use Case for first aid vending machine | Key Advantage | Key Disadvantage/Limitation | Relative Cost (Low/Med/High) |
---|---|---|---|---|
Stainless Steel | Structural components, exterior casing | Excellent corrosion resistance | Higher cost, complex manufacturing | High |
Polycarbonate | Transparent panels for visibility | Lightweight, impact-resistant | Susceptible to scratches and UV degradation | Medium |
Aluminum | Structural supports, internal components | Good balance of cost and performance | Not as strong as stainless steel | Medium |
Powder-Coated Steel | External surfaces, aesthetic components | Durable and visually appealing | Risk of corrosion if coating is damaged | Medium |
This guide provides international B2B buyers with actionable insights into material selection for first aid vending machines, ensuring that they make informed decisions that align with their operational needs and compliance requirements.
In-depth Look: Manufacturing Processes and Quality Assurance for first aid vending machine
Manufacturing Processes for First Aid Vending Machines
The manufacturing of first aid vending machines involves several critical stages that ensure the final product meets quality and safety standards. These stages typically include material preparation, forming, assembly, and finishing. Each step is crucial in creating a reliable and effective vending machine that can dispense first aid supplies efficiently.
1. Material Preparation
Material preparation is the initial stage where raw materials are sourced and prepared for the manufacturing process. Common materials include:
- Metal Components: Typically steel or aluminum for the frame, providing durability and strength.
- Plastic Parts: Used for the outer casing and internal compartments, selected for their resistance to wear and environmental factors.
- Electronic Components: Such as sensors, displays, and payment systems that enhance user interaction and operational efficiency.
During this stage, suppliers should verify the quality of materials, ensuring they meet industry standards such as ISO 9001. Buyers should inquire about the sourcing of materials to ensure they come from reputable suppliers.
2. Forming
In the forming stage, the prepared materials are shaped into the components of the vending machine. This may involve techniques such as:
- Stamping: For metal parts, where sheets are pressed into shape.
- Injection Molding: Used for producing plastic components by injecting molten plastic into molds.
- Laser Cutting: Employed for precision cutting of metal and plastic parts.
The forming process should be monitored closely to maintain consistency and precision in dimensions. B2B buyers can request samples or prototypes to assess the manufacturing capabilities before placing larger orders.
3. Assembly
The assembly stage brings together all the components to create the final product. Key activities include:
- Mechanical Assembly: Combining metal frames, plastic casings, and internal mechanisms.
- Electrical Assembly: Integrating the electronic components, including wiring and circuit boards.
- Quality Checks: Conducting initial quality control checks (IQC) during assembly to catch defects early.
Buyers should consider asking for documentation on assembly procedures and any certifications that confirm adherence to safety standards. This ensures that the assembly process aligns with international guidelines, which is particularly important for markets in Africa, South America, the Middle East, and Europe.
4. Finishing
The finishing stage includes painting, coating, or applying protective layers to enhance the machine’s appearance and longevity. This may involve:
- Powder Coating: A common method for metal parts that provides a durable finish resistant to scratches and corrosion.
- Screen Printing or Decals: For branding and instructions on the machine’s surface.
This stage is also an opportunity for final inspections to ensure that the machine meets aesthetic and functional standards. B2B buyers should verify the finishing techniques used and their compliance with relevant standards, as this can affect the machine’s usability and lifespan.
Quality Assurance in Manufacturing
Quality assurance (QA) is a crucial aspect of manufacturing first aid vending machines. It encompasses various processes and standards that ensure the machines are safe, reliable, and compliant with international regulations.
Relevant International Standards
International standards play a significant role in ensuring the quality of first aid vending machines. Key standards include:
- ISO 9001: This standard focuses on quality management systems, ensuring that manufacturers consistently provide products that meet customer and regulatory requirements.
- CE Marking: Required for products sold within the European Economic Area, indicating compliance with safety and health standards.
- API Standards: Applicable for machines that may dispense pharmaceutical products, ensuring they meet specific safety and efficacy criteria.
B2B buyers should prioritize suppliers who are certified under these standards, as it reflects their commitment to quality and reliability.
Quality Control Checkpoints
Quality control (QC) checkpoints are critical in the manufacturing process, ensuring that quality is maintained at every stage. Common QC checkpoints include:
- Incoming Quality Control (IQC): Inspects raw materials upon arrival to ensure they meet specified standards.
- In-Process Quality Control (IPQC): Conducted during the manufacturing process to identify and rectify defects as they occur.
- Final Quality Control (FQC): A thorough inspection of the completed machines before they are dispatched to ensure they meet all specifications and standards.
B2B buyers should inquire about the specific QC procedures employed by manufacturers and request access to QC reports and inspection records.
Common Testing Methods
Manufacturers typically employ various testing methods to ensure the functionality and safety of first aid vending machines, including:
- Functional Testing: Verifying that all components operate correctly, including the dispensing mechanism and payment systems.
- Environmental Testing: Assessing the machine’s performance under various environmental conditions, such as humidity, temperature, and exposure to dust.
- Safety Testing: Ensuring that the machine complies with electrical safety standards to prevent hazards during use.
Verifying Supplier Quality Control
B2B buyers can take several steps to verify a supplier’s quality control processes:
- Audits: Conducting regular audits of the manufacturing facility to assess compliance with quality standards and practices.
- Reports: Requesting detailed QC reports that outline inspection results, defect rates, and corrective actions taken.
- Third-Party Inspections: Engaging third-party inspection services to perform independent evaluations of the manufacturing process and finished products.
QC and Certification Nuances for International Buyers
International buyers, particularly from regions such as Africa, South America, the Middle East, and Europe, must consider the following nuances:
- Local Regulations: Understanding the specific regulations and standards applicable in their markets to ensure compliance.
- Cultural Differences: Recognizing that different regions may have varying expectations regarding quality and safety standards, necessitating tailored approaches to supplier selection.
- Logistical Considerations: Ensuring that the supply chain is robust enough to handle potential delays or issues in quality assurance.
By carefully evaluating manufacturing processes and quality assurance practices, B2B buyers can secure first aid vending machines that meet their operational needs and regulatory requirements.
Related Video: A Day in the Life: Machine Operator & Quality Assurance Technician
Comprehensive Cost and Pricing Analysis for first aid vending machine Sourcing
When sourcing first aid vending machines, understanding the cost structure and pricing dynamics is crucial for international B2B buyers, especially those from regions like Africa, South America, the Middle East, and Europe. Below is a comprehensive analysis of the key components that influence costs and pricing, along with actionable insights for buyers.
Cost Components
-
Materials: The primary materials include the machine casing, dispensing mechanisms, and first aid supplies. The choice of materials (e.g., steel vs. plastic) significantly affects the overall cost. High-quality materials may incur higher upfront costs but can lead to lower maintenance expenses over time.
-
Labor: Labor costs vary by region and can be influenced by local wage standards and the availability of skilled workers. In markets with lower labor costs, such as certain parts of Africa and South America, manufacturers may offer competitive pricing.
-
Manufacturing Overhead: This includes utilities, rent, and administrative expenses associated with the production process. Buyers should consider suppliers who can optimize overhead costs through efficient operations.
-
Tooling: Custom tooling for specific machine designs can be a significant investment. If the buyer requires a customized vending machine, tooling costs can substantially increase the overall expense.
-
Quality Control (QC): Implementing rigorous QC processes adds to manufacturing costs but is essential for ensuring product reliability and safety. Machines that pass stringent quality certifications may come at a premium but offer peace of mind.
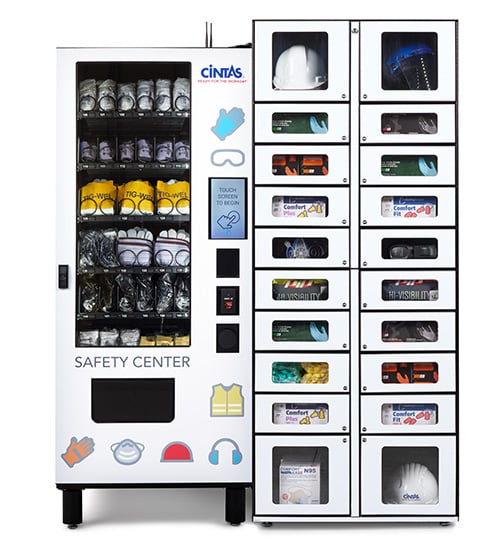
Illustrative Image (Source: Google Search)
-
Logistics: Shipping costs can vary greatly depending on the distance, mode of transport, and volume of goods. Buyers should explore different shipping options and consider Incoterms that can influence cost and risk allocation.
-
Margin: Suppliers typically add a profit margin to the total cost, which can vary widely based on market competition and perceived value. Understanding the market rates in the specific region can help in negotiating better prices.
Price Influencers
-
Volume/MOQ (Minimum Order Quantity): Bulk orders often lead to lower per-unit costs. Buyers should assess their demand to negotiate favorable terms for larger orders.
-
Specifications/Customization: Customizing features or sizes can drive up costs. Buyers should clearly define their needs to avoid unnecessary expenses.
-
Materials and Quality/Certifications: Higher quality and certified materials generally cost more. Buyers should weigh the long-term benefits of investing in quality against initial costs.
-
Supplier Factors: Supplier reputation, reliability, and location can significantly impact pricing. Building strong relationships with suppliers can lead to better pricing and terms.
-
Incoterms: Understanding the implications of different Incoterms (e.g., FOB, CIF) is essential. This affects who bears the cost and risk during transportation, influencing the total landed cost of the product.
Buyer Tips
-
Negotiation: Engage in open discussions with suppliers about pricing. Leverage market research to support your position and seek volume discounts or favorable payment terms.
-
Cost-Efficiency: Consider the Total Cost of Ownership (TCO) rather than just the purchase price. Analyze long-term costs associated with maintenance, operation, and potential downtime.
-
International Pricing Nuances: Be aware of currency fluctuations and tariffs that can affect pricing. Understanding the economic landscape in the supplier’s country can aid in effective negotiation.
-
Local Partnerships: Establishing partnerships with local distributors or agents can help navigate regional nuances and reduce logistical complexities.
Disclaimer
The prices discussed in this analysis are indicative and can vary based on numerous factors, including market conditions, supplier negotiations, and specific buyer requirements. Always conduct thorough due diligence and request detailed quotations before making purchasing decisions.
Spotlight on Potential first aid vending machine Manufacturers and Suppliers
This section offers a look at a few manufacturers active in the ‘first aid vending machine’ market. This is a representative sample for illustrative purposes; B2B buyers must conduct their own extensive due diligence before any engagement. Information is synthesized from public sources and general industry knowledge.
Essential Technical Properties and Trade Terminology for first aid vending machine
Key Technical Properties of First Aid Vending Machines
When evaluating first aid vending machines for international procurement, several technical specifications are critical. Understanding these properties can help buyers make informed decisions that align with their operational needs.
-
Material Grade
The material used in manufacturing vending machines significantly impacts durability and safety. Common materials include stainless steel, which offers corrosion resistance and strength, and high-grade plastics, which are lightweight and easy to clean. Selecting the right material is essential to ensure the machine withstands various environmental conditions, especially in outdoor settings. -
Capacity
This refers to the amount of first aid supplies the machine can hold. A standard vending machine may accommodate anywhere from 50 to 200 items, depending on its design and intended use. For B2B buyers, understanding capacity helps in assessing how often the machine will need to be restocked, which can influence operational efficiency and cost management. -
Power Supply Options
First aid vending machines can operate on different power supplies, including battery-operated and electric models. Battery-operated machines offer flexibility in placement, especially in remote areas without power access. Electric models, while requiring a power source, often provide features like digital interfaces and temperature control for sensitive supplies. -
User Interface
A clear and intuitive user interface is vital for quick access to first aid supplies. Many machines now come with touchscreens and multilingual support, enhancing usability in diverse environments. For international buyers, evaluating the user interface is crucial to ensure it meets the needs of all potential users.
-
Size and Dimensions
The physical dimensions of the vending machine affect where it can be installed. Buyers should consider space limitations in their facilities or public areas. Compact models are ideal for tight spaces, while larger machines may offer more capacity. -
Security Features
Given the nature of the supplies, security is paramount. Many vending machines are equipped with locking mechanisms and tamper-proof designs. Understanding these features is essential for buyers concerned about theft or unauthorized access, particularly in high-traffic areas.
Common Trade Terminology in the Industry
Navigating the first aid vending machine market requires familiarity with specific jargon. Here are several key terms that international B2B buyers should understand:
-
OEM (Original Equipment Manufacturer)
This term refers to a company that produces parts or equipment that may be marketed by another manufacturer. In the context of vending machines, an OEM may provide the core technology or components, which can be customized for specific buyers. Understanding OEM relationships can help buyers assess the reliability and quality of the machines. -
MOQ (Minimum Order Quantity)
MOQ denotes the minimum number of units a supplier is willing to sell. This is crucial for buyers, as it affects inventory management and pricing strategies. Understanding MOQs can help in negotiating better terms and managing stock levels efficiently.
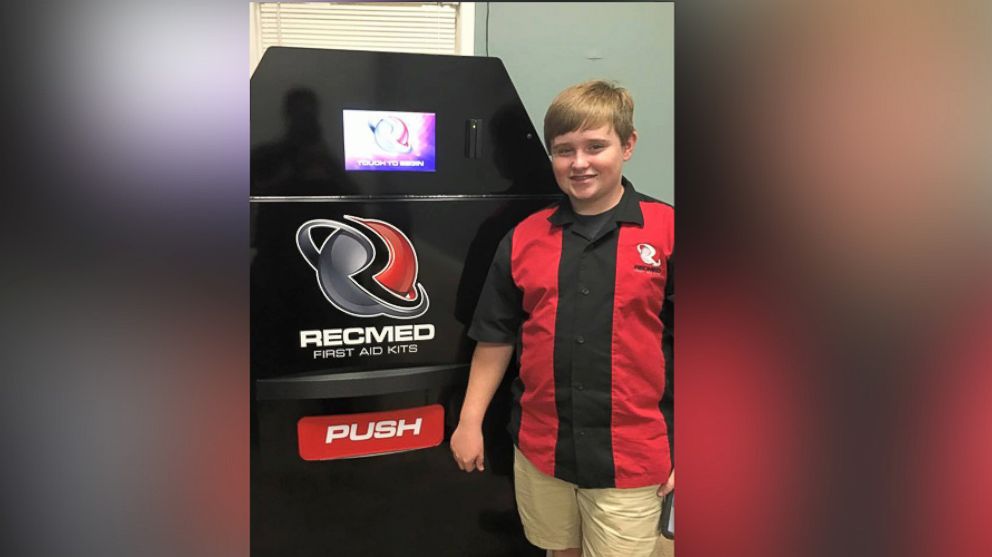
Illustrative Image (Source: Google Search)
-
RFQ (Request for Quotation)
An RFQ is a document sent to suppliers to solicit price quotes for specific goods or services. Buyers should use RFQs to compare prices, features, and terms from different vendors, ensuring they get the best deal. -
Incoterms (International Commercial Terms)
These are predefined international trade terms that clarify the responsibilities of buyers and sellers regarding shipping, insurance, and tariffs. Familiarity with Incoterms helps buyers understand their obligations and manage risks associated with international shipping. -
Lead Time
This term refers to the time it takes from placing an order to receiving the goods. For first aid vending machines, understanding lead times is essential for planning deployments, especially in emergency preparedness scenarios. -
Warranty Period
This specifies the duration during which the manufacturer will repair or replace faulty products. Buyers should always inquire about warranty terms, as this can indicate the manufacturer’s confidence in their product and provide peace of mind for the buyer.
By grasping these technical properties and industry terms, international B2B buyers can make informed decisions when procuring first aid vending machines, ensuring they meet both operational needs and compliance requirements.
Navigating Market Dynamics, Sourcing Trends, and Sustainability in the first aid vending machine Sector
Market Overview & Key Trends
The global market for first aid vending machines is experiencing significant growth driven by increasing awareness of workplace safety, health emergencies, and the need for immediate access to medical supplies. In regions such as Africa, South America, the Middle East, and Europe, key drivers include urbanization, rising healthcare costs, and the proliferation of health and safety regulations. These factors have led businesses to seek efficient solutions for first aid accessibility, particularly in high-traffic areas like offices, schools, and public spaces.
Emerging technology trends are transforming the first aid vending machine sector. Innovations such as smart vending machines equipped with IoT capabilities allow for real-time inventory management and usage tracking, enhancing operational efficiency. Furthermore, the integration of contactless payment systems and mobile app connectivity is appealing to tech-savvy consumers and businesses alike. B2B buyers are increasingly looking for machines that offer customizable configurations to meet specific needs, such as allergy-friendly products or specialized medical supplies for different industries.
Market dynamics are also influenced by the growing demand for compliance with health regulations and the need for businesses to demonstrate corporate responsibility. International buyers should be aware of the diverse regulatory environments in their respective regions, as this can impact sourcing decisions and supplier relationships. Engaging with local suppliers who understand these regulations can facilitate smoother market entry and compliance adherence.
Sustainability & Ethical Sourcing in B2B
Sustainability is becoming a critical consideration in the procurement of first aid vending machines. Buyers are increasingly recognizing the environmental impact of their purchasing decisions, prompting a shift towards sustainable practices. This includes the use of eco-friendly materials in the construction of vending machines, such as recycled plastics and sustainably sourced metals. Additionally, manufacturers are exploring energy-efficient technologies to minimize power consumption, aligning their products with global sustainability goals.
The importance of ethical supply chains cannot be overstated. B2B buyers are encouraged to partner with suppliers who prioritize transparency and ethical sourcing. This includes ensuring that raw materials are obtained responsibly and that labor practices adhere to international standards. Certifications such as ISO 14001 (Environmental Management) and Fair Trade can serve as indicators of a supplier’s commitment to sustainability and ethical practices.
Incorporating ‘green’ certifications and materials into the procurement process not only enhances brand reputation but can also lead to cost savings over time. By choosing sustainable options, businesses can reduce waste and improve operational efficiency, which is increasingly becoming a competitive advantage in the B2B marketplace.
Brief Evolution/History
The concept of vending machines providing first aid supplies dates back to the early 2000s, when organizations began recognizing the need for accessible medical care in public and workplace settings. Initially, these machines were simplistic, offering basic supplies like bandages and antiseptics. However, as the healthcare landscape evolved, so did the machines.
Today, first aid vending machines are sophisticated units equipped with advanced technology, offering a wide array of medical supplies tailored to specific needs. The shift towards smart vending solutions, which leverage data analytics and connectivity, reflects a broader trend in the B2B sector towards automation and efficiency. This evolution not only addresses immediate medical needs but also aligns with the growing emphasis on workplace safety and compliance, making first aid vending machines an essential component of modern health and safety strategies.
Related Video: Is global trade transforming? | Counting the Cost
Frequently Asked Questions (FAQs) for B2B Buyers of first aid vending machine
-
What should I consider when vetting suppliers for first aid vending machines?
When vetting suppliers, focus on their reputation, experience in the market, and product quality. Check for certifications such as ISO or compliance with local health regulations. Request references from other businesses in your region to assess reliability. Also, consider their ability to offer customization options, as well as after-sales support, which is crucial for maintenance and servicing. -
Can first aid vending machines be customized to fit specific needs?
Yes, many suppliers offer customization options for first aid vending machines. This may include branding with your company logo, selecting specific products to stock, or altering machine dimensions to fit your space. Clearly communicate your requirements during the procurement process to ensure the final product meets your expectations and complies with local regulations. -
What are the typical minimum order quantities (MOQs) and lead times for first aid vending machines?
MOQs can vary significantly by supplier, ranging from one unit for smaller suppliers to larger quantities for established manufacturers. Lead times typically depend on customization requirements, with standard models taking 4-6 weeks, while customized solutions may take longer. Always confirm these details upfront to align your procurement plans with your operational needs. -
What payment terms are usually offered for international purchases?
Payment terms can vary by supplier but commonly include options like advance payment, letter of credit, or staggered payments based on production milestones. It is advisable to negotiate terms that provide sufficient protection for your investment, such as partial payments before shipment and the remainder upon delivery. Ensure that any agreed terms are documented in the purchase contract. -
How can I ensure the quality of the first aid vending machines I purchase?
To ensure quality, request certifications such as CE, FDA, or other relevant local certifications that validate product safety and compliance. Conduct a factory audit if possible, or request samples before placing a large order. Establish a clear quality assurance process, including inspections at various stages of production and upon delivery. -
What logistics considerations should I keep in mind when importing these machines?
Logistics considerations include shipping methods, customs clearance, and delivery timelines. Choose a freight forwarder experienced with your target markets to navigate customs regulations efficiently. Be aware of potential duties and taxes that may apply upon import, and factor these into your total cost of acquisition. Ensure that the machines are adequately insured during transit. -
What steps should I take if there are disputes with the supplier?
In the event of a dispute, first attempt to resolve the issue directly with the supplier through open communication. Refer to the terms outlined in your contract regarding dispute resolution, which may include mediation or arbitration. If necessary, escalate the issue to a legal professional who specializes in international trade to explore your options for resolution. -
How important is after-sales support for first aid vending machines?
After-sales support is crucial for ensuring the ongoing functionality of your first aid vending machines. This includes maintenance, repairs, and the ability to restock supplies. Before finalizing your purchase, confirm the supplier’s policies on after-sales service, availability of spare parts, and response times for service requests to ensure you can maintain operational efficiency.
Strategic Sourcing Conclusion and Outlook for first aid vending machine
In conclusion, the strategic sourcing of first aid vending machines presents a valuable opportunity for businesses across Africa, South America, the Middle East, and Europe. By prioritizing the procurement of high-quality, reliable machines, companies can enhance workplace safety and accessibility to essential medical supplies. Key takeaways include the importance of evaluating supplier credentials, understanding local regulations, and considering the integration of technology for inventory management and user engagement.
The value of strategic sourcing cannot be overstated; it not only reduces costs but also fosters long-term partnerships that can lead to innovation and improved service delivery. As global markets continue to evolve, businesses must stay ahead by adopting practices that ensure efficiency and responsiveness to customer needs.
Looking forward, international B2B buyers are encouraged to take proactive steps in sourcing first aid vending machines that align with their operational goals. Engage with reputable suppliers, explore local market dynamics, and leverage technology to stay competitive. The future of workplace health and safety is here—embrace it by investing in the right solutions today.