Your Ultimate Guide to Sourcing Farmers Market Vending
Guide to Farmers Market Vending Machine
- Introduction: Navigating the Global Market for farmers market vending machine
- Understanding farmers market vending machine Types and Variations
- Key Industrial Applications of farmers market vending machine
- Strategic Material Selection Guide for farmers market vending machine
- In-depth Look: Manufacturing Processes and Quality Assurance for farmers market vending machine
- Comprehensive Cost and Pricing Analysis for farmers market vending machine Sourcing
- Spotlight on Potential farmers market vending machine Manufacturers and Suppliers
- Essential Technical Properties and Trade Terminology for farmers market vending machine
- Navigating Market Dynamics, Sourcing Trends, and Sustainability in the farmers market vending machine Sector
- Frequently Asked Questions (FAQs) for B2B Buyers of farmers market vending machine
- Strategic Sourcing Conclusion and Outlook for farmers market vending machine
Introduction: Navigating the Global Market for farmers market vending machine
The demand for farmers market vending machines is rapidly growing as consumers increasingly seek fresh, local produce in convenient formats. These innovative machines not only enhance accessibility to agricultural goods but also offer farmers a lucrative platform to sell directly to consumers, bypassing traditional retail channels. This guide is designed specifically for international B2B buyers, particularly from regions such as Africa, South America, the Middle East, and Europe, including countries like Poland and Argentina.
Navigating the global market for farmers market vending machines requires a comprehensive understanding of various factors, including the types of machines available, materials used in their construction, manufacturing and quality control practices, and potential suppliers. Buyers will also gain insights into the cost structures and market trends that influence pricing and demand.
By exploring frequently asked questions and addressing common concerns, this guide empowers B2B buyers to make informed sourcing decisions that align with their business needs. Whether you are looking to invest in vending machines for urban areas or rural markets, understanding these key components will enable you to effectively tap into the burgeoning demand for fresh produce, ultimately driving your business growth and meeting consumer expectations. This resource is your roadmap to successfully navigating the intricacies of the farmers market vending machine sector.
Understanding farmers market vending machine Types and Variations
Type Name | Key Distinguishing Features | Primary B2B Applications | Brief Pros & Cons for Buyers |
---|---|---|---|
Traditional Vending Machines | Standard vending machines with refrigerated sections | Urban farmers markets, festivals | Pros: Easy to operate and maintain; Cons: Limited product variety due to space constraints. |
Smart Vending Machines | Equipped with IoT technology for inventory tracking | High-tech farmers markets, urban areas | Pros: Real-time inventory management; Cons: Higher upfront costs and maintenance complexity. |
Mobile Vending Units | Transportable machines for various locations | Pop-up markets, events | Pros: Flexibility in location; Cons: May require additional logistics for transportation. |
Self-Serve Kiosks | Interactive touchscreens for customer engagement | Urban areas, tech-savvy markets | Pros: Enhanced customer experience; Cons: Higher initial investment and potential tech issues. |
Eco-Friendly Machines | Built from sustainable materials and energy-efficient | Eco-conscious markets, green initiatives | Pros: Attracts eco-conscious consumers; Cons: May have a higher cost due to sustainable materials. |
Traditional Vending Machines
Traditional vending machines are the most common type found in farmers markets. They typically feature refrigerated sections to keep fresh produce, dairy, and other perishables at the right temperature. These machines are ideal for urban farmers markets and festivals where foot traffic is high. B2B purchasing considerations include evaluating the machine’s capacity and ease of restocking, as well as the reliability of the refrigeration system to ensure product freshness.
Smart Vending Machines
Smart vending machines leverage IoT technology to provide real-time inventory tracking and customer engagement. They are suitable for high-tech farmers markets and urban areas where consumers expect modern conveniences. Buyers should consider the additional costs associated with technology and maintenance, but the benefits of improved efficiency and data analytics can justify the investment. These machines can also provide valuable insights into consumer preferences and inventory turnover.
Mobile Vending Units
Mobile vending units are transportable machines that can be set up at various locations, making them ideal for pop-up markets and events. They offer flexibility, allowing vendors to reach different customer bases without the need for a permanent setup. However, B2B buyers must consider the logistics of transportation and setup, as well as the potential for increased wear and tear compared to stationary machines. These units can be a great way to expand market reach.
Self-Serve Kiosks
Self-serve kiosks feature interactive touchscreens that enhance the customer experience by allowing consumers to browse products and make purchases at their own pace. These kiosks are well-suited for urban areas and tech-savvy markets. B2B buyers should weigh the benefits of increased customer engagement against the higher initial investment and potential technical issues that may arise. Proper training for staff and customers can mitigate some of these challenges.
Eco-Friendly Machines
Eco-friendly vending machines are designed with sustainable materials and energy-efficient systems, appealing to eco-conscious consumers. They are particularly effective in markets that prioritize green initiatives. B2B buyers should consider the long-term benefits of attracting a dedicated customer base, although the initial costs for sustainable materials may be higher. These machines can also enhance a vendor’s brand image by aligning with environmental values.
Related Video: how to create the BEST vendor booth for a market! Increase sales & overall vending experience
Key Industrial Applications of farmers market vending machine
Industry/Sector | Specific Application of Farmers Market Vending Machine | Value/Benefit for the Business | Key Sourcing Considerations for this Application |
---|---|---|---|
Agriculture | Direct sales of fresh produce | Increased revenue from direct consumer sales | Robustness in outdoor conditions, payment processing options |
Food & Beverage | Vending local artisanal foods | Supports local economies and diversifies product offerings | Customization for local preferences, refrigeration capacity |
Tourism & Hospitality | Offering local snacks and beverages at tourist sites | Enhances visitor experience and generates additional income | Location accessibility, aesthetic appeal |
Retail | Supplementary sales channel for grocery stores | Reduces overhead costs and expands product reach | Inventory management systems, remote monitoring capabilities |
Health & Wellness | Dispensing organic health products and supplements | Aligns with consumer trends towards health-conscious choices | Compliance with health regulations, product sourcing integrity |
Agriculture
Farmers market vending machines serve as a direct sales channel for fresh produce, allowing farmers to reach consumers without intermediaries. This setup not only boosts revenue but also reduces food waste by selling items that might not meet traditional market standards. International B2B buyers from regions like Africa and South America should consider machines that can withstand varying weather conditions and offer secure payment options, catering to diverse consumer preferences.
Food & Beverage
In the food and beverage sector, these vending machines can feature local artisanal products, enhancing community ties and providing consumers with unique options. They enable small producers to access a broader market and increase visibility. Buyers should focus on sourcing machines that allow customization for local tastes, as well as those equipped with adequate refrigeration to maintain product quality.
Tourism & Hospitality
Vending machines positioned at tourist attractions can offer local snacks and beverages, enhancing the visitor experience while generating additional revenue for businesses. By providing quick access to local delicacies, these machines can significantly improve tourist satisfaction. Buyers in this sector should prioritize machines that are visually appealing and strategically located for maximum foot traffic.
Retail
In retail environments, farmers market vending machines can act as supplementary sales channels for grocery stores, allowing them to offer a wider variety of products without the need for additional staff. This can lead to lower overhead costs and increased product reach. B2B buyers should consider machines with integrated inventory management systems to optimize stock levels and minimize waste.
Health & Wellness
These vending machines can also cater to the health and wellness industry by dispensing organic products and dietary supplements. With a growing consumer trend towards health-conscious eating, this application can significantly boost sales. Buyers should ensure compliance with local health regulations and focus on sourcing machines that maintain product integrity and freshness.
Related Video: How to Start a Vending Machine Business, Cost, Tips, How Much You Make
Strategic Material Selection Guide for farmers market vending machine
When selecting materials for farmers market vending machines, it is essential to consider their properties, advantages, limitations, and compliance with international standards. Below is an analysis of four common materials used in the construction of these machines, focusing on their suitability for various applications and the specific needs of international B2B buyers.
Stainless Steel
Key Properties: Stainless steel is renowned for its excellent corrosion resistance, high strength, and durability. It can withstand a wide range of temperatures and is often rated for high-pressure applications.
Pros & Cons: The primary advantage of stainless steel is its durability and resistance to corrosion, making it ideal for outdoor vending machines exposed to the elements. However, it tends to be more expensive than other materials and can be challenging to fabricate, which may increase manufacturing costs.
Impact on Application: Stainless steel is compatible with a variety of products, including fresh produce, dairy, and beverages. Its non-reactive nature ensures that food quality is maintained.
Considerations for International Buyers: Buyers from regions like Europe and the Middle East should ensure compliance with food safety standards such as EU regulations and local health codes. Common grades like 304 and 316 should meet ASTM standards.
Aluminum
Key Properties: Aluminum is lightweight, has good corrosion resistance, and is easily machinable. It has a lower density compared to stainless steel, which can be advantageous for reducing transportation costs.
Pros & Cons: The lightweight nature of aluminum makes it easy to install and transport. However, it is less durable than stainless steel and can be prone to denting and scratching. Its lower cost makes it an attractive option for budget-conscious buyers.
Impact on Application: Aluminum is suitable for vending machines that dispense dry goods or packaged items but may not be the best choice for wet or highly acidic products due to potential corrosion.
Considerations for International Buyers: Buyers should be aware of local recycling regulations, as aluminum is highly recyclable. Compliance with standards like ASTM B221 for aluminum alloys is essential, particularly in Europe.
Polycarbonate
Key Properties: Polycarbonate is a strong, transparent thermoplastic known for its impact resistance and lightweight characteristics. It can withstand a range of temperatures but has lower heat resistance compared to metals.
Pros & Cons: The transparency of polycarbonate allows for excellent product visibility, which can enhance sales. However, it is less durable than metals and may scratch easily. Its cost is generally lower than stainless steel but higher than basic plastics.
Impact on Application: Ideal for display cases and panels in vending machines, polycarbonate is suitable for dry products and packaged goods. It is not recommended for direct contact with hot or acidic items.
Considerations for International Buyers: Buyers in Africa and South America should check for compliance with local regulations regarding plastic use and recycling. Standards like ASTM D5767 for polycarbonate sheets should be considered.
Mild Steel
Key Properties: Mild steel is a low-carbon steel that offers good weldability and machinability. It is strong but lacks inherent corrosion resistance, requiring protective coatings for outdoor use.
Pros & Cons: The primary advantage of mild steel is its cost-effectiveness and availability. However, without proper treatment, it is susceptible to rust and corrosion, which can limit its lifespan.
Impact on Application: Mild steel can be used for structural components of vending machines but should be avoided in environments with high humidity or exposure to moisture.
Considerations for International Buyers: Compliance with local standards for coated steel, such as ASTM A123 for hot-dip galvanized steel, is critical, especially in humid regions like the Middle East.
Summary Table
Material | Typical Use Case for farmers market vending machine | Key Advantage | Key Disadvantage/Limitation | Relative Cost (Low/Med/High) |
---|---|---|---|---|
Stainless Steel | Outdoor vending machines for perishable goods | Excellent corrosion resistance and durability | Higher cost and complex manufacturing | High |
Aluminum | Lightweight vending machines for dry goods | Lightweight and easy to transport | Less durable, prone to denting | Medium |
Polycarbonate | Display panels for product visibility | Strong and transparent | Scratches easily, limited heat resistance | Medium |
Mild Steel | Structural components in vending machines | Cost-effective and readily available | Requires protective coating to prevent rust | Low |
This strategic material selection guide provides valuable insights for international B2B buyers, enabling them to make informed decisions based on performance, cost, and compliance with regional standards.
In-depth Look: Manufacturing Processes and Quality Assurance for farmers market vending machine
The manufacturing processes and quality assurance measures for farmers market vending machines are critical for ensuring product reliability and customer satisfaction. Below is a detailed overview of the key stages involved in manufacturing, the techniques employed, and the quality control measures that should be considered by international B2B buyers.
Manufacturing Processes
1. Material Preparation
The first step in the manufacturing process involves the selection and preparation of materials. Common materials used for vending machines include:
- Stainless Steel: For durability and corrosion resistance.
- Acrylic or Polycarbonate: For transparent panels that allow visibility of products.
- Electronics: Including microcontrollers and sensors for operational functionality.
Material preparation includes cutting, shaping, and treating the materials to enhance their properties (e.g., anti-corrosion treatments for metals). Suppliers should provide certifications for the materials used, ensuring compliance with international standards.
2. Forming
The forming process involves shaping the prepared materials into the desired components of the vending machine. This typically includes:
- CNC Machining: Precision cutting and shaping of metal parts to ensure accurate dimensions.
- Injection Molding: Used for creating plastic components, such as buttons and trays.
- Sheet Metal Fabrication: Bending and assembling metal sheets into the machine’s frame.
These techniques not only improve the structural integrity of the machine but also allow for customization based on specific requirements from B2B buyers.
3. Assembly
The assembly stage is where all the manufactured components come together. This process includes:
- Mechanical Assembly: Attaching the frame, panels, and internal components.
- Electrical Assembly: Installing the electronic systems, wiring, and control panels.
- Integration Testing: Conducting initial tests to ensure all components function together as intended.
Efficient assembly processes can significantly reduce lead times, which is crucial for B2B buyers looking to meet market demands quickly.
4. Finishing
Finishing processes enhance the aesthetic appeal and durability of the vending machines. Common finishing techniques include:
- Powder Coating: Provides a protective layer and can be customized in various colors.
- Screen Printing: Used for branding and operational instructions on the machine’s exterior.
- Final Inspection: Ensuring that all finishes are consistent and meet quality standards.
A well-finished product not only attracts customers but also stands up to outdoor conditions, which is particularly important for farmers market environments.
Quality Assurance
Quality assurance is paramount in the manufacturing of vending machines to ensure reliability and compliance with various international standards.
Relevant International Standards
International standards such as ISO 9001 for quality management systems ensure that manufacturers maintain consistent quality. Additionally, industry-specific certifications like CE (Conformité Européenne) for products sold in Europe and API (American Petroleum Institute) standards for specific components may apply depending on the machine’s features.
Quality Control Checkpoints
Quality control should be implemented at several checkpoints throughout the manufacturing process:
- Incoming Quality Control (IQC): Inspecting raw materials upon arrival to ensure they meet specified standards.
- In-Process Quality Control (IPQC): Monitoring processes during manufacturing to identify defects early.
- Final Quality Control (FQC): Conducting thorough testing on finished products before shipping.
These checkpoints help in maintaining high-quality standards and reducing the risk of defects reaching the market.
Common Testing Methods
Testing methods employed during quality assurance may include:
- Functional Testing: Ensuring that the vending machine operates correctly under normal conditions.
- Durability Testing: Assessing the machine’s performance under extreme conditions (temperature, humidity).
- Safety Testing: Ensuring compliance with electrical safety standards, particularly for machines operating in public spaces.
Verifying Supplier Quality Control
For international B2B buyers, verifying the quality control processes of suppliers is crucial. Here are some actionable steps:
- Conduct Audits: Regular audits of suppliers can provide insights into their quality control processes and adherence to standards.
- Request Quality Reports: Suppliers should provide documentation detailing their quality control measures, testing results, and compliance certifications.
- Third-Party Inspections: Engaging third-party inspectors can add an extra layer of assurance regarding the quality of the machines before purchase.
QC and Certification Nuances for International Buyers
International buyers, particularly from diverse regions like Africa, South America, the Middle East, and Europe, should be aware of the following:
- Local Regulations: Different regions may have specific regulations regarding vending machines. Ensure that the supplier complies with local laws.
- Cultural Preferences: Customization may be necessary to meet the cultural and operational preferences of local markets.
- Logistics and Supply Chain: Understanding the logistics of shipping and handling can impact the quality of products upon arrival.
By focusing on these manufacturing processes and quality assurance measures, B2B buyers can make informed decisions when sourcing farmers market vending machines. Ensuring that suppliers adhere to international standards and maintain rigorous quality control practices will not only enhance product reliability but also contribute to customer satisfaction in the competitive marketplace.
Related Video: Exploring 5 Intriguing Factory Mass Production Processes in China.
Comprehensive Cost and Pricing Analysis for farmers market vending machine Sourcing
Understanding the Cost Structure for Farmers Market Vending Machines
In sourcing farmers market vending machines, a comprehensive understanding of the cost structure is crucial for B2B buyers. The main components of cost include:
-
Materials: This encompasses the cost of raw materials such as metal, plastic, and electronic components. The choice of materials significantly affects both the durability and aesthetics of the vending machines.
-
Labor: Labor costs can vary widely depending on the location of manufacturing. Skilled labor is often more expensive, particularly in regions with higher wage standards.
-
Manufacturing Overhead: This includes costs associated with the facilities, utilities, and equipment used in the production process. Efficient manufacturing processes can help reduce these overheads.
-
Tooling: Initial tooling costs for custom designs or unique specifications can be substantial. These costs should be factored into the overall budget, especially for lower volume orders.
-
Quality Control (QC): Ensuring that the machines meet quality standards may involve additional costs for testing and certification.
-
Logistics: Shipping costs can be significant, particularly for international buyers. Factors like distance, mode of transport, and packaging can all influence logistics costs.
-
Margin: Suppliers typically include a profit margin in their pricing, which can vary based on market conditions and competition.
Price Influencers
Several factors can influence the pricing of farmers market vending machines:
-
Volume/MOQ: Higher order volumes often lead to discounts due to economies of scale. Buyers should negotiate Minimum Order Quantities (MOQs) that align with their business needs.
-
Specifications/Customization: Custom features can increase the cost. Buyers should clearly define their specifications to get accurate quotes.
-
Materials: The choice of materials can significantly impact the price. Premium materials will drive up costs but may offer better durability and aesthetics.
-
Quality/Certifications: Machines that meet specific international quality standards or certifications may be priced higher due to the added assurance of quality.
-
Supplier Factors: The supplier’s reputation, location, and production capabilities can influence pricing. Established suppliers may charge a premium for their reliability.
-
Incoterms: Understanding shipping terms is essential. Different Incoterms (e.g., FOB, CIF) can affect the total cost and responsibility for shipping and insurance.
Buyer Tips for Cost Efficiency
For international B2B buyers, particularly those from Africa, South America, the Middle East, and Europe, the following tips can enhance cost efficiency:
-
Negotiation: Always negotiate prices and terms. Suppliers may have flexibility, particularly with larger orders.
-
Total Cost of Ownership (TCO): Consider not just the purchase price but also installation, maintenance, and operational costs over the machine’s lifespan.
-
Pricing Nuances: Be aware that currency fluctuations, tariffs, and local taxes can impact the final price. It’s advisable to work with suppliers who understand international trade dynamics.
-
Supplier Relationships: Building strong relationships with suppliers can lead to better pricing and terms. Frequent communication and feedback can foster collaboration.
-
Market Research: Conduct thorough market research to understand regional pricing trends and supplier offerings. This knowledge can empower buyers during negotiations.
Disclaimer
Prices and costs mentioned in this analysis are indicative and may vary based on specific requirements, supplier negotiations, and market conditions. Always seek detailed quotes from multiple suppliers to get a comprehensive understanding of potential costs.
Spotlight on Potential farmers market vending machine Manufacturers and Suppliers
This section offers a look at a few manufacturers active in the ‘farmers market vending machine’ market. This is a representative sample for illustrative purposes; B2B buyers must conduct their own extensive due diligence before any engagement. Information is synthesized from public sources and general industry knowledge.
Essential Technical Properties and Trade Terminology for farmers market vending machine
Key Technical Properties of Farmers Market Vending Machines
When considering the procurement of farmers market vending machines, it’s crucial for B2B buyers to understand specific technical properties that influence performance, durability, and overall effectiveness. Below are essential specifications to consider:
-
Material Grade
The material of the vending machine should typically be stainless steel or high-grade aluminum. These materials provide durability, resistance to corrosion, and ease of cleaning, which are vital in outdoor environments. Selecting machines made from high-quality materials ensures longevity and reduces maintenance costs. -
Temperature Control Range
A critical specification is the temperature control capability, often ranging from -5°C to 5°C for refrigerated units. This range is essential to maintain the freshness of produce and other perishable items. For B2B buyers, understanding the temperature requirements ensures compliance with local food safety regulations, ultimately affecting product quality. -
Power Consumption
Assessing the power consumption of the vending machine is vital for operational cost analysis. Machines that utilize energy-efficient technologies can significantly reduce electricity bills, making them more sustainable and appealing to budget-conscious buyers. Look for units with energy-saving certifications to maximize cost efficiency. -
Capacity and Size
The internal capacity, often measured in cubic feet, is essential for determining how much product can be displayed and sold. Buyers should consider the volume of inventory they plan to offer and choose a machine that fits within their designated space. A well-sized vending machine optimizes product turnover and enhances sales potential. -
User Interface and Payment Options
A user-friendly interface with multiple payment options (credit/debit cards, mobile payments) can significantly enhance customer experience. Modern vending machines that offer contactless payment methods are particularly attractive, as they cater to changing consumer preferences and increase transaction speed. -
Security Features
Given the outdoor placement of many farmers market vending machines, robust security features, such as tamper-proof locks and reinforced glass, are essential. These features protect inventory and reduce the risk of theft, making it an important consideration for buyers looking to safeguard their investment.
Common Trade Terminology in Farmers Market Vending Machines
Understanding the jargon associated with vending machine procurement can facilitate smoother transactions and negotiations. Here are key terms that B2B buyers should be familiar with:
-
OEM (Original Equipment Manufacturer)
This term refers to companies that produce parts and equipment that may be marketed by another manufacturer. For buyers, partnering with an OEM can ensure high-quality components tailored specifically for vending machines, which can improve machine reliability and performance. -
MOQ (Minimum Order Quantity)
MOQ is the smallest number of units that a supplier is willing to sell. Understanding the MOQ is crucial for budgeting and inventory management. Buyers should negotiate MOQs that align with their sales projections to avoid overstocking or understocking. -
RFQ (Request for Quotation)
An RFQ is a document issued by a buyer to solicit price quotes from suppliers. This process helps buyers compare costs and terms from different vendors, ensuring they secure the best deal. Crafting a detailed RFQ can streamline the procurement process and enhance supplier relationships. -
Incoterms (International Commercial Terms)
These are internationally recognized rules that define the responsibilities of sellers and buyers in shipping contracts. Familiarity with Incoterms helps buyers understand shipping costs, risks, and obligations, ensuring clarity in international transactions. -
Lead Time
Lead time refers to the time taken from placing an order to receiving the goods. For farmers market vending machines, understanding lead time is essential for planning inventory and ensuring timely market availability. Buyers should communicate lead time expectations with suppliers to avoid disruptions.
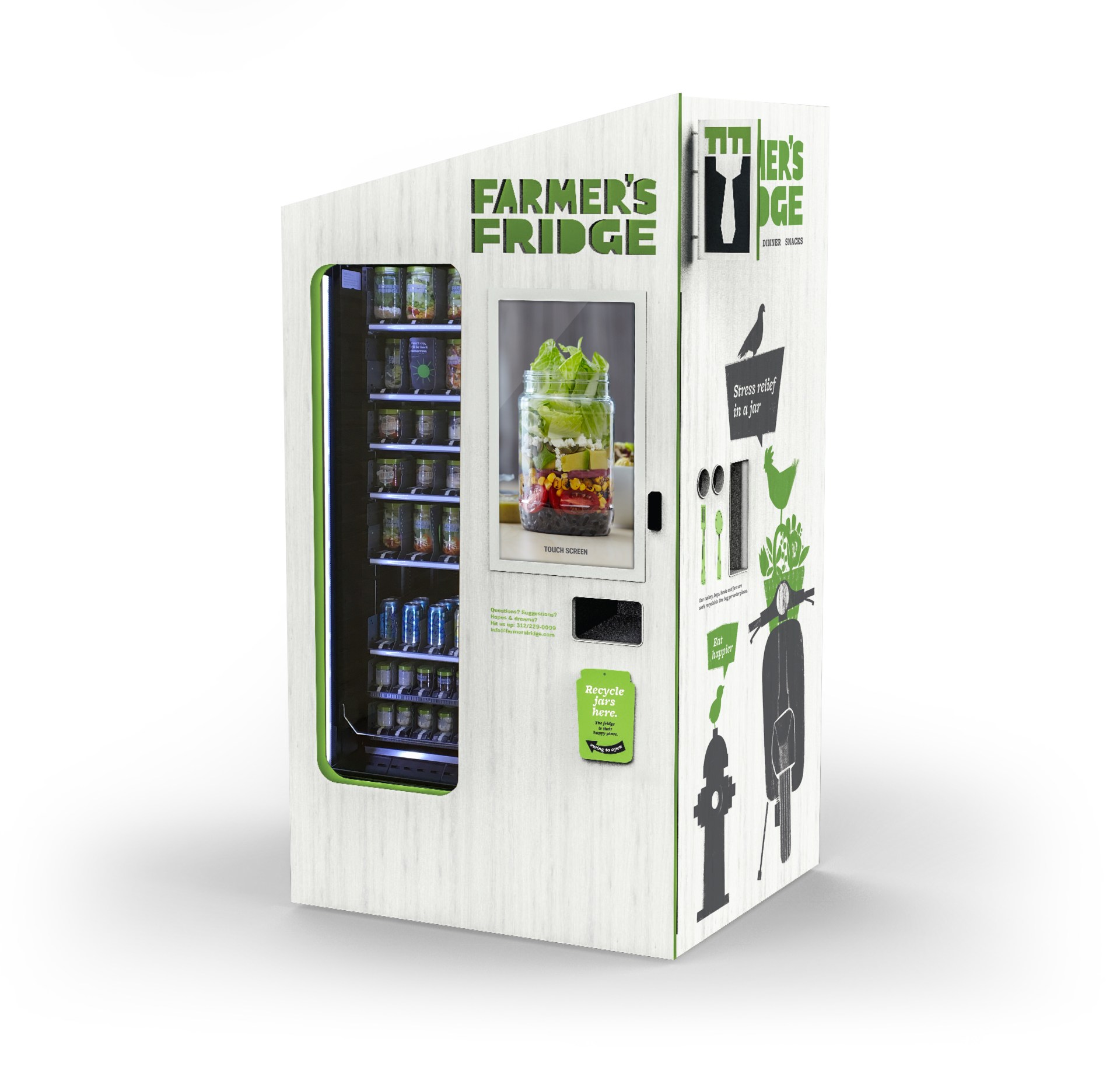
Illustrative Image (Source: Google Search)
- Warranty and Service Agreement
A warranty is a guarantee provided by the manufacturer regarding the condition of the machine. A service agreement outlines the terms for maintenance and repairs. Both are critical for buyers to understand, as they impact the long-term viability and operational costs of the vending machine.
By grasping these technical properties and trade terminologies, international B2B buyers from regions like Africa, South America, the Middle East, and Europe can make informed decisions when investing in farmers market vending machines, ultimately enhancing their business operations and customer satisfaction.
Navigating Market Dynamics, Sourcing Trends, and Sustainability in the farmers market vending machine Sector
The farmers market vending machine sector is witnessing a transformative phase driven by several global trends and technological advancements. As international B2B buyers, particularly from regions such as Africa, South America, the Middle East, and Europe, it’s crucial to understand these dynamics to make informed sourcing decisions.
Market Overview & Key Trends
The demand for farmers market vending machines is on the rise due to a growing consumer preference for fresh, locally sourced products. This trend is fueled by increased health consciousness and sustainability awareness among consumers, especially in urban areas. Additionally, the COVID-19 pandemic has accelerated the shift towards contactless shopping solutions, making vending machines an appealing option for both vendors and consumers.
Technological Integration: Innovative technologies such as IoT (Internet of Things) and AI (Artificial Intelligence) are being integrated into vending machines, enabling real-time inventory management, personalized consumer experiences, and enhanced payment options, including mobile wallets. These advancements allow for better tracking of consumer preferences and optimize stock levels, reducing waste and increasing profitability.
Sourcing Trends: Buyers are increasingly looking for suppliers that can provide customized solutions tailored to local tastes and preferences. This includes sourcing unique local products that resonate with regional consumers, thereby enhancing the vending machine’s appeal. Additionally, partnerships with local farmers and producers are becoming essential for ensuring product freshness and quality.
Market Dynamics: The competitive landscape is evolving, with new entrants emerging alongside established players. International buyers should consider factors such as machine customization, ease of maintenance, and supplier reliability when evaluating potential partners. Moreover, understanding local regulations and compliance requirements is vital for successful market entry, particularly in diverse regions like Africa and South America.
Sustainability & Ethical Sourcing in B2B
Sustainability is increasingly becoming a cornerstone of business strategy in the farmers market vending machine sector. The environmental impact of sourcing practices cannot be overlooked. B2B buyers should prioritize vendors who utilize eco-friendly materials and packaging to minimize waste and carbon footprint.
Importance of Ethical Supply Chains: Establishing ethical supply chains is critical for maintaining brand integrity and consumer trust. Buyers should seek suppliers who demonstrate transparency in their sourcing practices, ensuring that products are sourced from farms that employ sustainable farming methods and fair labor practices. This not only supports local economies but also enhances the overall consumer perception of the brand.
Green Certifications and Materials: Look for vendors that offer products with recognized sustainability certifications, such as USDA Organic, Fair Trade, or Rainforest Alliance. These certifications not only validate the ethical sourcing of products but also appeal to the increasingly eco-conscious consumer base. Additionally, consider using machines made from recycled or sustainable materials to further enhance the environmental credentials of your vending solutions.
Brief Evolution/History
The concept of vending machines has evolved significantly since their inception in the late 19th century, initially offering simple snacks and beverages. The introduction of farmers market vending machines marks a pivotal shift towards providing fresh, healthy food options, reflecting changing consumer demands. Over the last two decades, advancements in technology and a growing emphasis on sustainability have transformed these machines into sophisticated retail solutions capable of offering a diverse range of products. As the market continues to evolve, international B2B buyers must stay abreast of these changes to leverage new opportunities effectively.
Related Video: Is global trade transforming? | Counting the Cost
Frequently Asked Questions (FAQs) for B2B Buyers of farmers market vending machine
-
What criteria should I use to vet suppliers for farmers market vending machines?
When vetting suppliers, prioritize their experience in the industry and their reputation. Check for certifications that indicate compliance with international standards, such as ISO or CE. Request references from previous clients, particularly those in your region, to gauge reliability and service quality. Additionally, consider their manufacturing capabilities, technology used, and customer support services. A supplier with a robust track record and transparent operations is more likely to meet your needs effectively. -
Can I customize the farmers market vending machines for my specific market?
Most suppliers offer customization options, allowing you to tailor the vending machines to suit local preferences and regulations. Discuss your requirements regarding design, functionality, and product offerings. Ensure that the supplier has experience in creating custom solutions and can provide examples of previous projects. It’s also important to clarify any additional costs associated with customization, including design fees and extended lead times. -
What are the typical minimum order quantities (MOQ) and lead times for these machines?
Minimum order quantities can vary significantly by supplier, often ranging from 5 to 50 units. It’s advisable to confirm this upfront to avoid unexpected costs. Lead times typically depend on the complexity of the machines and the level of customization required, generally falling between 4 to 12 weeks. Always discuss and negotiate these terms before placing an order, as they can impact your inventory management and market launch. -
What payment terms should I expect when ordering vending machines internationally?
Payment terms can vary among suppliers, but common practices include upfront deposits (20-50%) with the balance due before shipment. Some suppliers may offer credit terms for established buyers. It’s crucial to clarify these terms in your contract, including payment methods accepted (e.g., bank transfers, letters of credit). Consider using a secure payment platform to minimize risks associated with international transactions. -
How can I ensure the quality of the vending machines I order?
Request detailed quality assurance processes from your supplier, including testing protocols and certifications. Consider asking for product samples or visiting the manufacturing facility if feasible. Additionally, establish clear quality standards in your contract, outlining acceptable tolerances and inspection procedures. Engaging third-party inspection services can provide an added layer of assurance before machines are shipped. -
What certifications should I look for in farmers market vending machines?
Look for certifications that ensure the machines meet safety and operational standards, such as CE marking for Europe or UL certification for North America. These certifications indicate compliance with regulatory requirements and can enhance your product’s credibility. Additionally, inquire about environmental certifications like ISO 14001, which demonstrates the supplier’s commitment to sustainable practices, an increasingly important factor in many markets.
-
What logistics considerations should I keep in mind when importing vending machines?
Logistics can be complex, particularly with large machinery. Confirm the supplier’s shipping methods and whether they handle customs clearance. Understand the associated costs, including tariffs and taxes, to budget accordingly. It’s also wise to establish a clear timeline for delivery and consider using a logistics partner experienced in international shipping to navigate potential challenges. -
How should I handle disputes with suppliers?
Establishing a clear contract with defined terms and conditions is crucial for minimizing disputes. Include clauses outlining conflict resolution methods, such as mediation or arbitration, and specify the jurisdiction for legal matters. Maintain open communication with your supplier to address issues as they arise. If a dispute occurs, document all correspondence and agreements to support your case, ensuring you have a comprehensive record of interactions.
Strategic Sourcing Conclusion and Outlook for farmers market vending machine
The integration of farmers market vending machines into the supply chain offers a unique opportunity for B2B buyers to enhance their product offerings and reach a growing consumer base focused on fresh, local produce. As highlighted throughout this guide, strategic sourcing is critical in identifying reliable suppliers, optimizing costs, and ensuring product quality.
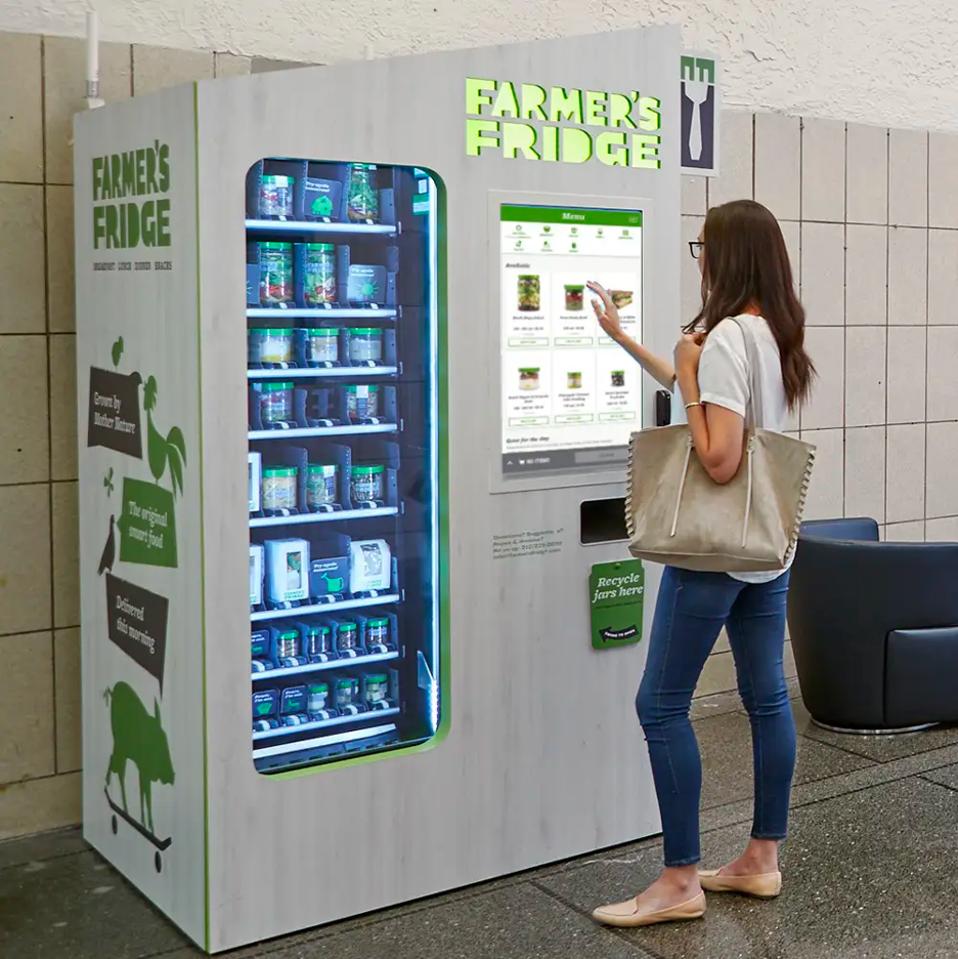
Illustrative Image (Source: Google Search)
Key takeaways include:
– Market Demand: Increasing consumer preference for convenience and fresh produce positions vending machines as an attractive retail option.
– Supplier Relationships: Establishing strong partnerships with local farmers can enhance product diversity and sustainability.
– Technology Integration: Investing in smart vending solutions can streamline operations and improve customer engagement.
As international buyers from Africa, South America, the Middle East, and Europe explore this innovative market, it is essential to assess local regulations, consumer preferences, and logistical challenges. The future of farmers market vending machines is promising, with potential for growth in urban areas and underserved communities.
Take action today by leveraging this guide to refine your sourcing strategies and capitalize on the expanding market for fresh, local food solutions. Embrace this opportunity to innovate and meet the evolving demands of consumers in your region.