Your Ultimate Guide to Sourcing Desktop Vending Machine
Guide to Desktop Vending Machine
- Introduction: Navigating the Global Market for desktop vending machine
- Understanding desktop vending machine Types and Variations
- Key Industrial Applications of desktop vending machine
- Strategic Material Selection Guide for desktop vending machine
- In-depth Look: Manufacturing Processes and Quality Assurance for desktop vending machine
- Comprehensive Cost and Pricing Analysis for desktop vending machine Sourcing
- Spotlight on Potential desktop vending machine Manufacturers and Suppliers
- Essential Technical Properties and Trade Terminology for desktop vending machine
- Navigating Market Dynamics, Sourcing Trends, and Sustainability in the desktop vending machine Sector
- Frequently Asked Questions (FAQs) for B2B Buyers of desktop vending machine
- Strategic Sourcing Conclusion and Outlook for desktop vending machine
Introduction: Navigating the Global Market for desktop vending machine
In today’s fast-paced global economy, desktop vending machines have emerged as a vital solution for businesses seeking to enhance employee satisfaction and optimize operational efficiency. These compact vending units not only provide quick access to refreshments but also serve as a strategic asset in fostering a productive work environment. For international B2B buyers from diverse regions such as Africa, South America, the Middle East, and Europe, understanding the nuances of this market is essential for informed decision-making.
This comprehensive guide delves into the multifaceted world of desktop vending machines, covering a wide array of topics including types, materials, manufacturing and quality control, supplier options, cost considerations, and market dynamics. By exploring these critical elements, buyers can identify the most suitable products tailored to their specific needs, whether for corporate offices, coworking spaces, or educational institutions.
Furthermore, the guide addresses frequently asked questions, offering insights that empower businesses to navigate challenges and capitalize on opportunities within the vending machine landscape. With this resource, B2B buyers will be equipped to make strategic sourcing decisions, ensuring they invest wisely in solutions that not only meet their operational requirements but also align with their organizational goals. As the demand for innovative workplace solutions continues to grow, desktop vending machines represent a significant opportunity to enhance service offerings and drive employee engagement across various markets.
Understanding desktop vending machine Types and Variations
Type Name | Key Distinguishing Features | Primary B2B Applications | Brief Pros & Cons for Buyers |
---|---|---|---|
Snack and Beverage Vending | Offers a variety of snacks and drinks | Offices, break rooms, schools | Pros: High demand, easy to stock. Cons: Limited product range may not meet all employee preferences. |
Fresh Food Vending | Refrigerated units for perishable items | Hospitals, universities, corporate cafeterias | Pros: Healthy options appeal to health-conscious consumers. Cons: Requires regular maintenance and restocking. |
Coffee Vending Machines | Specializes in hot beverages | Offices, cafes, convenience stores | Pros: High profit margins on beverages. Cons: May require specialized maintenance and training for staff. |
Specialty Item Vending | Focuses on niche products (e.g., electronics) | Tech companies, event venues, hotels | Pros: Unique offerings can attract specific customer segments. Cons: Higher initial investment and potential for slow turnover. |
Combination Vending | Combines snacks, drinks, and fresh items | Multi-purpose locations like gyms and malls | Pros: Versatile product range meets diverse needs. Cons: Complexity in inventory management. |
Snack and Beverage Vending
Snack and beverage vending machines are among the most common types found in various B2B environments. These machines typically offer a wide selection of snacks, soft drinks, and sometimes healthy options. They are ideal for offices, break rooms, and schools where quick access to refreshments is necessary. When considering these machines, buyers should assess the variety of products available, as a limited selection may not cater to all employee preferences. Additionally, the ease of stocking and maintaining these machines is a significant advantage, making them a popular choice.
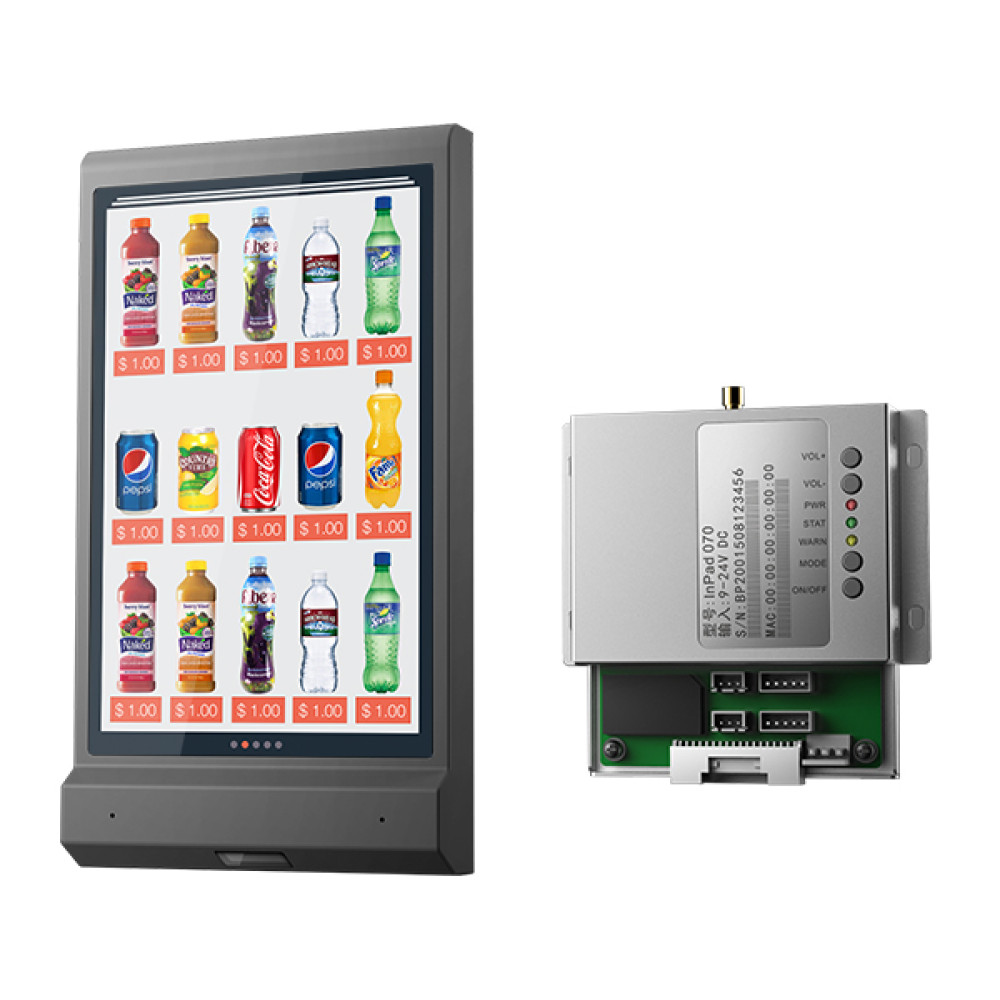
Illustrative Image (Source: Google Search)
Fresh Food Vending
Fresh food vending machines provide refrigerated options, allowing for the sale of perishable items such as salads, sandwiches, and fruits. These machines are particularly well-suited for locations like hospitals, universities, and corporate cafeterias, where healthy eating is a priority. Buyers should consider the need for regular maintenance and restocking to ensure food safety and quality. While the appeal of healthy options can attract a diverse customer base, the operational complexity and higher maintenance requirements may pose challenges for some businesses.
Coffee Vending Machines
Coffee vending machines focus on providing hot beverages, including various coffee types, teas, and sometimes specialty drinks. These machines are commonly found in offices, cafes, and convenience stores, where the demand for coffee is high. For B2B buyers, the potential for high profit margins on beverages is a significant advantage. However, it is essential to consider the need for specialized maintenance and possibly training for staff to operate these machines effectively. The quality of the beverage can significantly impact customer satisfaction, making it crucial to choose reputable suppliers.
Specialty Item Vending
Specialty item vending machines cater to niche markets by offering unique products, such as electronics, beauty products, or even local artisan goods. These machines are ideal for tech companies, event venues, and hotels looking to provide exclusive items to their customers. While they can attract specific customer segments and enhance brand image, buyers should be aware of the higher initial investment and the potential for slower turnover, depending on the product demand. Understanding the target market and consumer preferences is vital for success in this segment.
Combination Vending
Combination vending machines offer a versatile range of products, typically including snacks, beverages, and fresh food items. They are perfect for multi-purpose locations such as gyms, malls, and large office complexes, where diverse consumer needs must be met. The primary consideration for buyers is the complexity of inventory management, as maintaining a balanced stock of different product types can be challenging. However, the ability to cater to a broader audience enhances the potential for increased sales, making these machines a compelling option for various business settings.
Related Video: Machine Learning in 2024 – Beginner’s Course
Key Industrial Applications of desktop vending machine
Industry/Sector | Specific Application of Desktop Vending Machine | Value/Benefit for the Business | Key Sourcing Considerations for this Application |
---|---|---|---|
Office & Corporate | Snack and beverage provision | Increases employee satisfaction and productivity | Variety of product offerings, payment options, and size |
Education | Study supplies dispensing | Reduces downtime for students and staff | Security features, product range, and ease of use |
Healthcare | Medication distribution | Ensures timely access to essential medications | Compliance with health regulations, temperature control |
Manufacturing | Personal protective equipment (PPE) vending | Enhances safety and compliance on-site | Durability, ease of inventory management, and replenishment |
Hospitality | Mini-bar services in hotel rooms | Boosts guest experience and additional revenue | Customization options, payment methods, and product selection |
In the office and corporate sector, desktop vending machines serve as convenient snack and beverage providers, promoting a better work environment. They can significantly enhance employee satisfaction and productivity by reducing the need for staff to leave the premises for refreshments. International buyers should consider the variety of products offered, payment options available, and the machine’s size to fit their specific office layout.
In educational institutions, desktop vending machines can dispense study supplies such as stationery and snacks, minimizing downtime for students and staff. This application is particularly beneficial in high-traffic areas like libraries and student lounges. Buyers from regions like Africa and South America should look for machines with security features to prevent theft, a diverse product range, and user-friendly designs that cater to the younger demographic.
In the healthcare industry, these machines can be utilized for the timely distribution of medications, ensuring that staff and patients have quick access to essential drugs. This application addresses the critical need for efficiency in healthcare settings. Buyers must prioritize compliance with health regulations, temperature control capabilities for sensitive medications, and robust security features to prevent unauthorized access.
Within the manufacturing sector, desktop vending machines can be employed to dispense personal protective equipment (PPE), which is crucial for maintaining safety standards on-site. This application not only streamlines access to necessary gear but also enhances compliance with safety regulations. International buyers should focus on the durability of the machines, ease of inventory management, and reliable replenishment systems to ensure continuous availability of PPE.
In the hospitality industry, desktop vending machines can enhance guest experiences by providing mini-bar services in hotel rooms. This not only adds convenience for guests but also generates additional revenue for hotels. Buyers should seek machines that offer customization options to align with brand identity, a range of payment methods to accommodate different guest preferences, and a diverse selection of products to cater to various tastes.
Related Video: How to Start a Vending Machine Business, Cost, Tips, How Much You Make
Strategic Material Selection Guide for desktop vending machine
When selecting materials for desktop vending machines, it’s crucial to consider the performance characteristics, cost implications, and regulatory compliance of each material. The following analysis focuses on four common materials used in the construction of desktop vending machines: stainless steel, aluminum, plastic, and glass. Each material has unique properties that can significantly affect the machine’s functionality and longevity.
Stainless Steel
Key Properties: Stainless steel is known for its excellent corrosion resistance, high strength, and ability to withstand high temperatures and pressures. It typically has a temperature rating up to 800°F (427°C) and can handle significant mechanical stress.
Pros & Cons: The primary advantage of stainless steel is its durability and resistance to rust and staining, making it ideal for environments where hygiene is critical, such as food and beverage vending. However, stainless steel can be more expensive than other materials and may require specialized manufacturing processes, increasing overall costs.
Impact on Application: Stainless steel is compatible with a wide range of media, including water, soft drinks, and snacks. Its non-reactive nature ensures that it does not contaminate the products stored within.
Considerations for International Buyers: Compliance with international standards such as ASTM and DIN is essential, especially in regions like Europe where regulations on food safety are stringent. Buyers from Africa and South America should also consider local sourcing options to reduce costs.
Aluminum
Key Properties: Aluminum is lightweight, corrosion-resistant, and has a good strength-to-weight ratio. It can withstand temperatures up to 400°F (204°C) and is often used in applications requiring lightness and mobility.
Pros & Cons: The main advantage of aluminum is its cost-effectiveness and ease of manufacturing, allowing for intricate designs and rapid production. However, it is less durable than stainless steel and may not be suitable for high-pressure applications.
Impact on Application: Aluminum is suitable for dry goods and non-corrosive liquids. Its lightweight nature makes it ideal for portable vending machines, but it may not be appropriate for products that require a high level of hygiene.
Considerations for International Buyers: Buyers in the Middle East and Europe should ensure that aluminum components meet relevant standards, such as JIS and EN, to ensure product safety and quality.
Plastic
Key Properties: Plastics, such as ABS and polycarbonate, are versatile materials known for their low weight and good impact resistance. They can typically handle temperatures up to 200°F (93°C) but may be less effective in high-temperature environments.
Pros & Cons: Plastics are cost-effective and can be molded into complex shapes, making them suitable for custom designs. However, they may not have the same durability as metals and can be susceptible to UV degradation over time.
Impact on Application: Plastic is often used for components that do not come into direct contact with food or beverages, such as outer casings or internal mechanisms. Its chemical resistance varies by type, which is critical for compatibility with specific products.
Considerations for International Buyers: Buyers should ensure that plastics used in vending machines comply with food safety regulations, especially in Europe where strict guidelines exist. Additionally, sourcing from local manufacturers can help mitigate import costs.
Glass
Key Properties: Glass is non-porous, resistant to staining, and can withstand high temperatures. It is often used in display panels and for holding beverages.
Pros & Cons: The aesthetic appeal of glass can enhance the product’s marketability, providing a premium look. However, glass is fragile and can break easily, making it less suitable for high-traffic environments.
Impact on Application: Glass is ideal for displaying products, allowing customers to see the contents without opening the machine. It is compatible with most products but requires careful handling and installation.
Considerations for International Buyers: Compliance with safety standards regarding glass usage is crucial, particularly in regions with strict consumer protection laws. Buyers should also consider the logistics of transporting glass components, which can be challenging.
Summary Table
Material | Typical Use Case for desktop vending machine | Key Advantage | Key Disadvantage/Limitation | Relative Cost (Low/Med/High) |
---|---|---|---|---|
Stainless Steel | Food and beverage storage | Excellent durability and corrosion resistance | Higher cost, complex manufacturing | High |
Aluminum | Portable vending machines | Lightweight and cost-effective | Less durable, lower pressure tolerance | Medium |
Plastic | Non-contact components, casings | Cost-effective, versatile | Susceptible to UV degradation | Low |
Glass | Display panels for products | Aesthetic appeal, non-porous | Fragile, requires careful handling | Medium |
This guide provides actionable insights for international B2B buyers in selecting the right materials for desktop vending machines, ensuring compliance with local regulations and optimizing product performance.
In-depth Look: Manufacturing Processes and Quality Assurance for desktop vending machine
The manufacturing process for desktop vending machines is a multi-stage operation that requires precision engineering and strict quality assurance protocols. For B2B buyers, understanding these processes is crucial for making informed purchasing decisions, especially when sourcing from different regions, including Africa, South America, the Middle East, and Europe. Below is an overview of the typical manufacturing stages, quality control measures, and international standards that govern the production of desktop vending machines.
Manufacturing Processes
1. Material Preparation
The first stage in the manufacturing process involves selecting and preparing the materials needed for the vending machines. Common materials include:
- Metal Components: Steel or aluminum for the frame and structural elements, chosen for durability and strength.
- Plastics: High-density polyethylene (HDPE) or polycarbonate for outer panels and internal compartments, valued for their lightweight and impact-resistant properties.
- Electronic Components: Circuit boards, sensors, and payment systems, which require careful selection to ensure compatibility and reliability.
Material quality is paramount; suppliers should provide certifications and test reports to verify material properties.
2. Forming
In this stage, the prepared materials undergo various forming techniques to create the components of the vending machine. Key techniques include:
- Cutting: Laser or water jet cutting is often used for precision parts, ensuring tight tolerances.
- Bending: Metal sheets are bent using CNC machines to form the structure of the vending machine.
- Injection Molding: Used for producing plastic parts, allowing for complex shapes and high-volume production.
Each technique must be executed with precision to maintain the integrity of the components.
3. Assembly
Once the components are formed, they move to the assembly line where they are put together. This stage typically involves:
- Mechanical Assembly: Components are joined using screws, bolts, and welding techniques.
- Electrical Assembly: Wiring and installation of electronic components are completed, ensuring all connections are secure and functional.
- Final Assembly: The machine is assembled as a whole, integrating all parts and systems.
Proper assembly practices are critical to ensure the functionality and longevity of the vending machines.
4. Finishing
The final stage of manufacturing focuses on the aesthetic and functional finishing of the vending machines. This includes:
- Painting or Coating: Protective coatings or paints are applied to enhance durability and aesthetic appeal.
- Quality Inspection: Each machine undergoes a thorough inspection for any cosmetic or functional defects.
Finishing techniques not only improve the machine’s appearance but also contribute to its resistance to wear and tear.
Quality Assurance
Quality assurance (QA) is an integral part of the manufacturing process, ensuring that products meet specified standards and customer expectations. For international B2B buyers, understanding the QA measures in place is essential.
International Standards
Desktop vending machines must comply with various international standards, which may include:
- ISO 9001: This standard focuses on quality management systems and is essential for ensuring consistent quality in manufacturing processes.
- CE Marking: In Europe, CE marking signifies conformity with health, safety, and environmental protection standards.
- API Certification: In certain industries, API certification may be required, particularly for machines that handle food products.
These certifications provide assurance that the products are manufactured in accordance with established quality standards.
Quality Control Checkpoints
Quality control (QC) should be integrated at multiple checkpoints throughout the manufacturing process:
- Incoming Quality Control (IQC): Raw materials are inspected upon arrival to ensure they meet required specifications.
- In-Process Quality Control (IPQC): Ongoing inspections are conducted during production to catch defects early and minimize waste.
- Final Quality Control (FQC): The completed machines undergo comprehensive testing to ensure they function correctly and meet quality standards.
Common testing methods include functionality tests, stress tests, and safety assessments, which are essential to verify the machine’s operational integrity.
Verifying Supplier Quality Control
B2B buyers must take proactive steps to verify the quality control measures of their suppliers. Here are some actionable insights:
- Conduct Audits: Regular audits of suppliers can help ensure compliance with quality standards. Buyers should establish audit schedules and criteria.
- Request Quality Reports: Suppliers should provide documentation detailing their QC processes, including results from inspections and tests.
- Third-Party Inspections: Engaging third-party inspection agencies can provide an unbiased assessment of the supplier’s quality control practices.
Buyers should also consider regional compliance nuances. For instance, African markets may have different regulatory requirements compared to those in Europe or South America. Understanding these nuances can help buyers navigate potential barriers and ensure compliance with local laws.
Conclusion
For international B2B buyers, particularly those in Africa, South America, the Middle East, and Europe, a thorough understanding of the manufacturing processes and quality assurance measures for desktop vending machines is vital. By focusing on the key stages of manufacturing, relevant international standards, and effective QC strategies, buyers can make informed decisions and select suppliers that meet their quality expectations. This knowledge not only enhances procurement strategies but also fosters successful long-term partnerships with manufacturers.
Related Video: The Most Sophisticated Manufacturing Process In The World Inside The Fab | Intel
Comprehensive Cost and Pricing Analysis for desktop vending machine Sourcing
To effectively navigate the sourcing of desktop vending machines, international B2B buyers must understand the comprehensive cost structure and pricing dynamics involved. This knowledge will empower buyers from regions such as Africa, South America, the Middle East, and Europe (including Spain and Poland) to make informed purchasing decisions.
Cost Components
-
Materials: The primary cost driver in desktop vending machines is the raw materials used in production. Common materials include high-grade plastics, metals, electronic components, and dispensing mechanisms. The choice of materials can significantly impact both quality and price.
-
Labor: Labor costs vary greatly depending on the manufacturing location. Countries with lower labor costs may offer competitive pricing but could compromise on quality. Conversely, manufacturers in Europe may have higher labor costs but often deliver superior craftsmanship and adherence to quality standards.
-
Manufacturing Overhead: This includes expenses related to utilities, rent, equipment maintenance, and indirect labor. Efficient manufacturing processes can help reduce overhead costs, allowing suppliers to offer more competitive pricing.
-
Tooling: Custom tooling for specialized designs or unique features can add to initial costs but may be necessary for high-volume orders. Buyers should evaluate whether the tooling costs can be amortized over a sufficient order quantity to justify the expense.
-
Quality Control (QC): Investing in robust QC processes ensures that the machines meet safety and performance standards. While this may raise initial costs, it can reduce long-term expenses related to returns and warranty claims.
-
Logistics: Shipping costs depend on the distance from the manufacturer and the chosen Incoterms. Consideration of logistics is crucial, especially for international buyers who must factor in import duties, taxes, and freight charges.
-
Margin: Supplier margins can vary based on market competition, brand reputation, and product uniqueness. Understanding typical margins in different regions helps buyers negotiate better deals.
Price Influencers
-
Volume/MOQ: Larger orders can lead to significant discounts. Buyers should assess their demand forecasts and negotiate Minimum Order Quantities (MOQs) that align with their purchasing capabilities.
-
Specifications/Customization: Custom features may increase costs. Buyers should determine which specifications are essential and which can be standardized to optimize pricing.
-
Materials and Quality: Higher-quality materials and certifications (e.g., CE, ISO) often justify a higher price. Buyers should weigh the benefits of investing in quality against their budget constraints.
-
Supplier Factors: Established suppliers with proven reliability may charge a premium, but their products often come with better support and warranty options. Newer suppliers may offer lower prices but can come with higher risks.
-
Incoterms: The chosen Incoterms affect cost responsibilities. Buyers should understand how terms like FOB (Free On Board) or CIF (Cost, Insurance, and Freight) impact the overall price.
Buyer Tips
-
Negotiation: Always approach negotiations armed with market data. Understanding local pricing trends and competitor offerings can strengthen your position.
-
Cost-Efficiency: Focus on Total Cost of Ownership (TCO) rather than just the purchase price. This includes maintenance, operational costs, and potential downtime.
-
Pricing Nuances: Be aware that pricing can vary significantly across regions due to economic conditions, currency fluctuations, and local competition. Buyers in Africa and South America may face different pricing strategies compared to those in Europe.
-
Disclaimer for Indicative Prices: Always request formal quotes, as prices can fluctuate based on material costs, labor rates, and other economic factors. Prices quoted may serve as a guideline but should not be seen as fixed.
By understanding these cost components and pricing influences, B2B buyers can make strategic decisions that align with their business needs while optimizing their sourcing efforts for desktop vending machines.
Spotlight on Potential desktop vending machine Manufacturers and Suppliers
This section offers a look at a few manufacturers active in the ‘desktop vending machine’ market. This is a representative sample for illustrative purposes; B2B buyers must conduct their own extensive due diligence before any engagement. Information is synthesized from public sources and general industry knowledge.
Essential Technical Properties and Trade Terminology for desktop vending machine
When sourcing desktop vending machines, understanding the essential technical properties and industry terminology is crucial for making informed purchasing decisions. This section provides key specifications and commonly used trade terms that will assist international B2B buyers, particularly from Africa, South America, the Middle East, and Europe.
Key Technical Properties
-
Material Grade
– The construction material of a vending machine, typically stainless steel or high-grade plastic, influences durability and aesthetic appeal. A higher material grade often correlates with better resistance to corrosion and wear, which is particularly important for machines located in high-traffic areas. -
Temperature Control Range
– This specification defines the operational temperature range for refrigerated items. Machines designed to store food and beverages should maintain a temperature between 0°C to 4°C (32°F to 39°F) for optimal freshness. Understanding this range helps ensure compliance with local health regulations. -
Power Consumption
– Measured in watts, power consumption indicates how much energy the machine uses during operation. Lower power consumption is vital for reducing operational costs, especially in regions where electricity prices are high. Buyers should seek energy-efficient models, often labeled with energy certifications. -
Capacity
– This refers to the number of items the machine can hold, often listed in terms of product slots or total volume (liters). Capacity is critical for determining whether a vending machine can meet the demands of its intended location, such as a busy office or a public space. -
User Interface
– The design and functionality of the user interface, including touchscreens or buttons, significantly impact the customer experience. Machines with intuitive interfaces are likely to have higher usage rates and customer satisfaction, which can enhance profitability. -
Payment Options
– Modern vending machines may support various payment methods, including cash, credit/debit cards, and mobile payments. Offering multiple payment options can increase sales by catering to diverse customer preferences.
Common Trade Terminology
-
OEM (Original Equipment Manufacturer)
– This term refers to companies that produce parts and equipment that may be marketed by another manufacturer. For buyers, partnering with an OEM can ensure that they receive high-quality components and machines that meet industry standards. -
MOQ (Minimum Order Quantity)
– MOQ is the smallest number of units a supplier is willing to sell. Understanding MOQ is crucial for budgeting and inventory management, especially for businesses looking to minimize upfront costs while ensuring adequate supply. -
RFQ (Request for Quotation)
– An RFQ is a document sent to suppliers requesting price quotes for specific products or services. It allows buyers to compare offers and negotiate better terms. Buyers should prepare detailed RFQs to receive accurate and competitive quotes. -
Incoterms (International Commercial Terms)
– These are internationally recognized rules that define the responsibilities of buyers and sellers in international transactions. Familiarity with Incoterms helps buyers understand shipping costs, risk management, and delivery obligations, which can vary significantly across different countries. -
Lead Time
– This refers to the amount of time from placing an order to receiving the product. For B2B buyers, understanding lead times is essential for planning inventory and ensuring that machines are available when needed. -
Warranty and Service Agreement
– A warranty is a guarantee provided by the manufacturer regarding the condition of the machine. A service agreement outlines the terms for maintenance and repair. Buyers should carefully review these terms to ensure long-term support and reliability of their investment.
By familiarizing themselves with these technical properties and trade terms, B2B buyers can make more informed decisions, ultimately leading to successful procurement of desktop vending machines that meet their specific needs.
Navigating Market Dynamics, Sourcing Trends, and Sustainability in the desktop vending machine Sector
Market Overview & Key Trends
The desktop vending machine market is experiencing robust growth, driven by several global factors including urbanization, changing consumer behavior, and technological advancements. Increased demand for convenient, on-the-go snack and beverage solutions is evident, especially in corporate environments and educational institutions. International B2B buyers should note the rising trend of smart vending machines, which incorporate IoT technology for inventory management, payment processing, and user engagement. This technology enables operators to track sales in real-time and optimize product offerings, thus enhancing profitability.
Emerging sourcing trends highlight a shift towards local suppliers, particularly in Africa and South America, where logistics and supply chain disruptions have prompted businesses to seek more reliable, regional partners. Additionally, the use of data analytics is becoming crucial in understanding consumer preferences, allowing for tailored product selections in desktop vending machines. In Europe, countries like Spain and Poland are leading in the adoption of eco-friendly vending solutions, reflecting a broader market dynamism that prioritizes sustainability alongside innovation.
Moreover, the proliferation of cashless payment options, including mobile wallets and contactless cards, is reshaping the purchasing experience in vending. Buyers should consider these technological enhancements as they evaluate potential suppliers and product offerings, ensuring they align with contemporary consumer expectations.
Sustainability & Ethical Sourcing in B2B
Sustainability is a significant consideration in the desktop vending machine sector, with buyers increasingly prioritizing environmentally friendly practices. The production and disposal of vending machines can have considerable environmental impacts, from energy consumption to waste generation. As such, international B2B buyers must emphasize the importance of ethical supply chains that minimize these impacts.
Key strategies include sourcing machines made from recyclable materials and opting for energy-efficient models that reduce electricity consumption. Certifications such as Energy Star or ISO 14001 can serve as indicators of a manufacturer’s commitment to sustainability. Moreover, incorporating local and organic products into vending machine offerings not only supports local economies but also appeals to environmentally conscious consumers.
Incorporating a life-cycle approach to procurement will enable buyers to assess the environmental footprint of their vending solutions comprehensively. By fostering partnerships with suppliers committed to sustainable practices, businesses can enhance their brand reputation and meet the growing consumer demand for responsible sourcing.
Brief Evolution/History
The desktop vending machine has evolved significantly since its inception in the early 20th century. Initially designed to dispense simple products like gum and candy, these machines have transformed into sophisticated units capable of offering a wide array of snacks and beverages, including fresh food items. The introduction of electronic payment systems in the 1980s marked a pivotal moment, allowing for greater convenience and expanding the potential customer base.
In recent years, the integration of technology has further revolutionized the sector, with smart vending machines enabling cashless transactions and real-time inventory management. This evolution reflects broader trends in consumer behavior, emphasizing the need for convenience, choice, and enhanced user experiences. As international B2B buyers navigate this dynamic landscape, understanding the historical context can provide valuable insights into future developments and opportunities in the desktop vending machine market.
Related Video: Is global trade transforming? | Counting the Cost
Frequently Asked Questions (FAQs) for B2B Buyers of desktop vending machine
-
How can I vet suppliers for desktop vending machines?
When sourcing desktop vending machines, it’s essential to conduct thorough supplier vetting. Start by checking their business credentials and certifications relevant to your region, such as ISO standards. Engage in direct communication to assess their responsiveness and expertise. Request references or case studies from previous clients, particularly those in similar markets. Consider using third-party platforms for supplier ratings and reviews. Finally, visiting their manufacturing facility, if possible, can provide invaluable insights into their operational capabilities. -
What customization options are typically available for desktop vending machines?
Most manufacturers offer a range of customization options to suit your business needs. Common customizations include branding (like adding your logo), product selection (types of snacks or beverages), and machine color. Ensure you discuss your specific requirements during the initial consultation. Some suppliers may also offer technology integrations, such as cashless payment systems or inventory management software. Be clear about your expectations to avoid misalignment during production. -
What are the typical minimum order quantities (MOQ) and lead times?
Minimum order quantities can vary significantly among suppliers, often ranging from 10 to 100 units depending on the manufacturer. It’s advisable to inquire about MOQs early in your discussions to ensure they align with your purchasing capacity. Lead times can also differ, typically ranging from 4 to 12 weeks, influenced by production schedules and customization requirements. Always confirm these details in writing to avoid unexpected delays in your supply chain. -
What payment terms should I expect when purchasing desktop vending machines?
Payment terms for B2B transactions can vary widely. Common practices include a deposit upfront (typically 30-50%) with the balance due upon delivery or installation. Some suppliers may offer financing options or payment plans for larger orders. It’s crucial to clarify these terms upfront and discuss any potential discounts for early payment. Additionally, consider using secure payment methods or escrow services to protect your investment during the transaction. -
What quality assurance (QA) certifications should I look for?
When sourcing desktop vending machines, look for suppliers with recognized quality assurance certifications. ISO 9001 is a standard that ensures consistent quality management. Other certifications like CE (for Europe) or RoHS compliance (restricting hazardous substances) are also important, depending on your region. Request documentation to verify these certifications, as they can indicate the manufacturer’s commitment to quality and safety standards. -
How can I manage logistics and shipping for international orders?
Logistics can be complex when importing desktop vending machines. Engage a freight forwarder experienced in handling electronic goods to navigate customs regulations and shipping routes. Discuss delivery terms (Incoterms) with your supplier to clarify responsibilities for shipping costs and risks. Ensure that machines are packed securely to prevent damage during transit. Additionally, consider purchasing insurance for high-value shipments to mitigate potential losses. -
What should I do if there’s a dispute with the supplier?
Disputes can arise from delays, quality issues, or miscommunication. First, attempt to resolve the issue directly with the supplier through open communication. Document all correspondences and agreements. If direct negotiation fails, refer to your purchase agreement for dispute resolution clauses, which may include mediation or arbitration. Involving a third-party mediator can help facilitate a resolution. If necessary, consult legal counsel familiar with international trade laws relevant to your jurisdiction. -
Are there any specific regulations I need to be aware of when importing vending machines?
Yes, regulations may vary by country and region, so it’s vital to research the specific requirements for importing vending machines. Common regulations include compliance with electrical safety standards and environmental laws, such as waste disposal requirements for electronic products. Check for any import tariffs or taxes that may apply. Engaging a local customs broker can help navigate these regulations and ensure compliance with all legal requirements, minimizing the risk of delays or fines.
Strategic Sourcing Conclusion and Outlook for desktop vending machine
The desktop vending machine market presents a significant opportunity for international B2B buyers, particularly in emerging markets across Africa, South America, the Middle East, and established regions like Europe. Key takeaways emphasize the importance of strategic sourcing to optimize procurement processes, enhance supply chain efficiency, and ensure the delivery of high-quality products that meet diverse customer needs.
Investing in desktop vending machines not only caters to the growing demand for convenient access to snacks and beverages but also aligns with trends towards healthier options and technological advancements such as cashless payment systems. As businesses seek to improve workplace satisfaction and productivity, vending solutions can play a pivotal role in enhancing employee experience.
Looking ahead, B2B buyers are encouraged to leverage strategic sourcing strategies, including supplier partnerships and market analysis, to navigate the complexities of global trade and supply chain challenges. By prioritizing these practices, organizations can position themselves to capitalize on the evolving vending landscape.
Engage with suppliers who understand regional preferences and compliance requirements, ensuring that your vending solutions are not only innovative but also culturally relevant. Now is the time to invest in desktop vending machines—position your business for success in a competitive market.
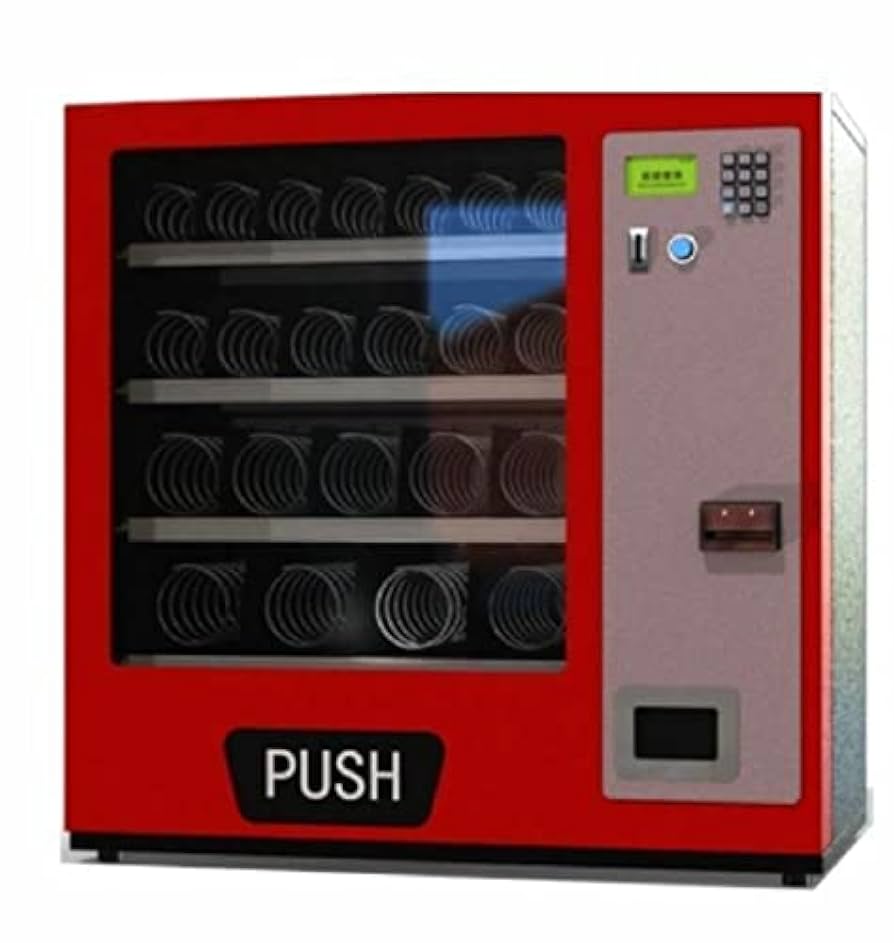
Illustrative Image (Source: Google Search)