Your Ultimate Guide to Sourcing Counter Top Vending Machine
Guide to Counter Top Vending Machine
- Introduction: Navigating the Global Market for counter top vending machine
- Understanding counter top vending machine Types and Variations
- Key Industrial Applications of counter top vending machine
- Strategic Material Selection Guide for counter top vending machine
- In-depth Look: Manufacturing Processes and Quality Assurance for counter top vending machine
- Comprehensive Cost and Pricing Analysis for counter top vending machine Sourcing
- Spotlight on Potential counter top vending machine Manufacturers and Suppliers
- Essential Technical Properties and Trade Terminology for counter top vending machine
- Navigating Market Dynamics, Sourcing Trends, and Sustainability in the counter top vending machine Sector
- Frequently Asked Questions (FAQs) for B2B Buyers of counter top vending machine
- Strategic Sourcing Conclusion and Outlook for counter top vending machine
Introduction: Navigating the Global Market for counter top vending machine
The global market for countertop vending machines presents a unique opportunity for businesses seeking efficient and innovative solutions for product distribution. As consumer preferences shift towards convenience and accessibility, these machines have evolved into essential tools for retailers, office managers, and service providers across various sectors. From Africa to South America and throughout Europe and the Middle East, the demand for countertop vending machines is on the rise, driven by the increasing need for contactless transactions and quick service.
This comprehensive guide delves into the multifaceted world of countertop vending machines, providing international B2B buyers with critical insights that empower informed sourcing decisions. We explore the various types of machines available, including traditional snack and beverage units, as well as advanced models offering healthy options and cashless payment systems. Additionally, we cover materials and manufacturing processes, ensuring that buyers understand quality control standards and supplier credentials.
Cost considerations are also a key focus, as we analyze market trends and provide tips for negotiating favorable terms. The guide addresses frequently asked questions, offering clarity on common concerns related to installation, maintenance, and operational efficiency. By equipping buyers with this essential knowledge, we enable them to navigate the global market effectively, ensuring they make strategic investments that enhance their business operations and customer satisfaction.
Understanding counter top vending machine Types and Variations
Type Name | Key Distinguishing Features | Primary B2B Applications | Brief Pros & Cons for Buyers |
---|---|---|---|
Snack Vending Machines | Offers a variety of packaged snacks and beverages | Offices, break rooms, schools | Pros: High demand, low maintenance. Cons: Limited fresh food options. |
Coffee Vending Machines | Dispenses various coffee types, including specialty options | Cafés, offices, convenience stores | Pros: High profit margins, customizable. Cons: Requires regular maintenance and supply restocking. |
Fresh Food Vending Machines | Designed for perishable items like sandwiches and salads | Hospitals, universities, workplaces | Pros: Appeals to health-conscious consumers. Cons: Higher spoilage risk and requires refrigeration. |
Combination Vending Machines | Multi-functional, offering snacks, beverages, and fresh food | Airports, malls, hotels | Pros: Versatile, caters to diverse preferences. Cons: More complex to maintain and manage inventory. |
Specialty Vending Machines | Focused on niche products (e.g., electronics, beauty products) | Retail, trade shows, events | Pros: Targeted market appeal, unique offerings. Cons: Limited consumer base and higher initial investment. |
Snack Vending Machines
Snack vending machines are the most common type found in various business environments. They typically offer a selection of packaged snacks, candy, and beverages. These machines are particularly suitable for high-traffic areas such as offices, break rooms, and schools, where quick snack options are in demand. When considering a purchase, B2B buyers should evaluate the machine’s capacity, ease of restocking, and the variety of products it can hold to maximize sales potential.
Coffee Vending Machines
Coffee vending machines provide a range of coffee options, including espresso, cappuccino, and other specialty drinks. Ideal for offices, cafés, and convenience stores, these machines can significantly enhance employee satisfaction and customer experience. Buyers should consider factors such as the machine’s brewing technology, maintenance requirements, and the availability of customizable drink options to ensure it meets their specific needs.
Fresh Food Vending Machines
Fresh food vending machines are designed for perishable items, offering options like sandwiches, salads, and fruit. These machines cater to health-conscious consumers and are commonly found in hospitals, universities, and workplaces. B2B buyers must account for the refrigeration needs, potential spoilage, and the necessity for regular supply restocking when evaluating these machines.
Combination Vending Machines
Combination vending machines are versatile units that dispense snacks, beverages, and fresh food all in one. They are particularly suited for locations like airports, malls, and hotels, where consumer preferences can vary widely. Buyers should assess the machine’s layout, inventory management capabilities, and the ease of operation to effectively serve diverse customer needs.
Specialty Vending Machines
Specialty vending machines focus on niche markets, offering unique products such as electronics, beauty items, or gourmet snacks. These machines are often seen at retail locations, trade shows, and events, targeting specific consumer interests. When considering these machines, B2B buyers should evaluate the product demand, initial investment costs, and the potential for attracting a dedicated customer base.
Related Video: FINTECH BUSINESS MODELS EXPLAINED
Key Industrial Applications of counter top vending machine
Industry/Sector | Specific Application of Counter Top Vending Machine | Value/Benefit for the Business | Key Sourcing Considerations for this Application |
---|---|---|---|
Food & Beverage | Snack and beverage dispensing in offices | Increases employee satisfaction and productivity | Product variety, payment systems, and maintenance support |
Healthcare | Dispensing of medical supplies and snacks | Provides quick access to essential items for staff and patients | Compliance with health regulations, ease of cleaning |
Education | Providing snacks and drinks in schools and universities | Enhances student experience and reduces downtime | Nutritional value of offerings, vending machine size |
Retail | 24/7 automated retail for convenience items | Expands sales opportunities without additional staffing | Location analysis, security features, and inventory management |
Hospitality | Offering quick grab-and-go meals in hotels | Improves guest experience and generates additional revenue | Menu variety, freshness of products, and branding options |
Food & Beverage
In the food and beverage sector, countertop vending machines serve as an effective solution for snack and drink dispensing in office environments. These machines provide employees with convenient access to refreshments, which can enhance satisfaction and productivity. B2B buyers should consider the variety of products offered, the integration of cashless payment systems, and the availability of maintenance support to ensure seamless operation.
Healthcare
Countertop vending machines in healthcare settings can dispense medical supplies, snacks, and beverages to both staff and patients. This application addresses the critical need for quick access to essential items, especially during busy shifts. Buyers in this sector must prioritize compliance with health regulations, the ease of cleaning the machines, and the reliability of the dispensing mechanisms to ensure safety and efficiency.
Education
In educational institutions, countertop vending machines are strategically placed to provide snacks and drinks to students and staff. This application not only enhances the overall student experience but also reduces downtime between classes. Buyers should focus on the nutritional value of offerings, the size and capacity of the machines to accommodate high traffic, and the potential for branding opportunities to align with school values.
Retail
Countertop vending machines in the retail sector offer 24/7 automated access to convenience items, allowing businesses to expand their sales opportunities without the need for additional staffing. This application is particularly beneficial in high-traffic areas where traditional retail options may not be viable. Key considerations for buyers include conducting a thorough location analysis, ensuring robust security features, and implementing effective inventory management systems to optimize stock levels.
Hospitality
In the hospitality industry, countertop vending machines can be utilized to provide guests with quick grab-and-go meal options, enhancing their overall experience. This application can generate additional revenue for hotels while catering to the needs of busy travelers. Buyers should consider the variety and freshness of products offered, the branding options available to align with the hotel’s image, and the overall user experience to ensure guest satisfaction.
Related Video: How to Start a Vending Machine Business, Cost, Tips, How Much You Make
Strategic Material Selection Guide for counter top vending machine
When selecting materials for countertop vending machines, international B2B buyers must consider several factors, including durability, cost, and compatibility with the intended application. Here, we analyze four common materials used in the construction of countertop vending machines: stainless steel, aluminum, plastic, and glass. Each material has unique properties, advantages, and limitations that can significantly impact the performance and longevity of the vending machine.
Stainless Steel
Key Properties:
Stainless steel is renowned for its excellent corrosion resistance, high strength, and ability to withstand high temperatures and pressures. It typically has a temperature rating of up to 870 °C (1600 °F) and offers good resistance to a variety of chemicals.
Pros & Cons:
Stainless steel is highly durable and resistant to wear, making it ideal for high-traffic environments. However, it is relatively expensive compared to other materials, which can impact overall project budgets. Additionally, the manufacturing complexity can be higher, requiring specialized tools and techniques.
Impact on Application:
Stainless steel is compatible with a wide range of media, including beverages and snacks, and is easy to clean, which is crucial for hygiene in food service applications.
Considerations for International Buyers:
Buyers should ensure compliance with international standards such as ASTM A240 for stainless steel. In regions like Africa and South America, local sourcing may be limited, affecting lead times and costs.
Aluminum
Key Properties:
Aluminum is lightweight and has good corrosion resistance, with a melting point around 660 °C (1220 °F). It is also a good conductor of heat, which can be beneficial for temperature-sensitive products.
Pros & Cons:
Aluminum is less expensive than stainless steel and easier to machine, allowing for more complex designs. However, it is less durable and can be prone to denting and scratching, which may affect its aesthetic appeal over time.
Impact on Application:
Aluminum is suitable for vending machines that require lightweight components, but it may not be ideal for high-temperature applications due to its lower thermal resistance.
Considerations for International Buyers:
Buyers should check for compliance with standards such as ASTM B221 for aluminum extrusions. In Europe, specific alloy compositions may be preferred, while in the Middle East, local climatic conditions may affect material choices.
Plastic
Key Properties:
Plastic materials, such as ABS or polycarbonate, are lightweight and can be molded into complex shapes. They typically have a lower temperature rating (around 100 °C or 212 °F) but offer good impact resistance.
Pros & Cons:
Plastic is cost-effective and allows for colorful designs, making it appealing for branding. However, it may not be as durable as metal options and can be susceptible to UV degradation, especially in outdoor applications.
Impact on Application:
Plastic is ideal for non-food applications or for components that do not require high strength. Its compatibility with various media is generally good, but care must be taken with hot items.
Considerations for International Buyers:
Compliance with food safety standards (e.g., FDA regulations) is crucial for vending machines dispensing food items. Buyers in regions with stringent regulations, such as Europe, should ensure that the selected plastic meets local safety standards.
Glass
Key Properties:
Glass is a non-porous material that offers excellent aesthetic appeal and is resistant to staining. It can withstand high temperatures, depending on the type of glass used (e.g., tempered glass).
Pros & Cons:
Glass provides a premium look and is easy to clean, enhancing the machine’s hygiene. However, it is fragile and can shatter upon impact, which poses safety risks and potential replacement costs.
Impact on Application:
Glass is often used in display panels for vending machines, allowing customers to see products clearly. However, it is not suitable for structural components that require high durability.
Considerations for International Buyers:
Buyers must consider safety standards for glass in vending machines, especially in public spaces. Compliance with standards such as EN 12150 for tempered glass is essential in Europe and other regions.
Summary Table
Material | Typical Use Case for counter top vending machine | Key Advantage | Key Disadvantage/Limitation | Relative Cost (Low/Med/High) |
---|---|---|---|---|
Stainless Steel | Structural components, exterior panels | Highly durable, corrosion-resistant | High cost, complex manufacturing | High |
Aluminum | Lightweight structures, internal components | Cost-effective, easy to machine | Less durable, prone to dents | Medium |
Plastic | Non-structural components, decorative elements | Lightweight, colorful designs | Less durable, UV degradation | Low |
Glass | Display panels, aesthetic features | Premium look, easy to clean | Fragile, safety risks | Medium |
This guide provides a comprehensive overview of material selection for countertop vending machines, enabling international B2B buyers to make informed decisions based on their specific needs and regional considerations.
In-depth Look: Manufacturing Processes and Quality Assurance for counter top vending machine
The manufacturing of countertop vending machines involves several critical stages, each designed to ensure the final product meets both functional and quality standards. This section delves into the primary manufacturing processes, quality assurance measures, and international standards that B2B buyers should consider when sourcing these machines.
Manufacturing Processes
The manufacturing process for countertop vending machines typically consists of four main stages: material preparation, forming, assembly, and finishing.
1. Material Preparation
In this initial stage, raw materials are sourced and prepared for production. Common materials include:
– Metal: Steel or aluminum for structural components.
– Plastic: High-density polyethylene (HDPE) or polycarbonate for external casing and internal parts.
– Electronic Components: Circuit boards, sensors, and payment systems.
Key Techniques:
– Cutting and Shaping: Metals are cut into specified dimensions using laser cutting or CNC machining. Plastics may be molded or extruded.
– Quality Checks: Initial inspections ensure that materials meet specifications, reducing waste and ensuring compliance with standards.
2. Forming
This stage involves shaping the prepared materials into parts that will comprise the vending machine.
Key Techniques:
– Stamping: Used for creating metal panels and parts.
– Injection Molding: Commonly employed for creating plastic components.
– Bending and Welding: Metal components are bent to shape and welded together for structural integrity.
3. Assembly
The assembly stage is where individual components come together to form the complete vending machine.
Key Techniques:
– Mechanical Assembly: Components are assembled using screws, bolts, or welding.
– Electrical Assembly: Integration of electronic components, including wiring and circuit boards, is performed.
– Functional Testing: Each machine undergoes preliminary tests to ensure that all systems function as intended.
4. Finishing
The final stage involves applying protective and aesthetic finishes to the vending machines.
Key Techniques:
– Painting and Coating: Machines are often powder-coated for durability and aesthetics.
– Quality Assurance: Final inspections are conducted to ensure that the machine meets all design specifications and quality standards.
Quality Assurance
Quality assurance (QA) is a critical aspect of the manufacturing process, ensuring that countertop vending machines are safe, reliable, and compliant with international standards.
International Standards
B2B buyers should familiarize themselves with the following standards:
– ISO 9001: This standard focuses on quality management systems and is essential for ensuring consistent quality in manufacturing.
– CE Marking: Indicates conformity with health, safety, and environmental protection standards for products sold within the European Economic Area.
– API Standards: Relevant for machines that dispense food or beverages, ensuring safety and hygienic standards are met.
Quality Control Checkpoints
Quality control (QC) is typically divided into several checkpoints throughout the manufacturing process:
-
Incoming Quality Control (IQC):
– Inspect incoming materials to ensure they meet specified requirements.
– Conduct tests on a sample basis for critical components. -
In-Process Quality Control (IPQC):
– Monitor production processes at various stages to identify and address defects early.
– Use statistical process control (SPC) methods to maintain consistency. -
Final Quality Control (FQC):
– Conduct comprehensive testing on finished machines, including functionality and safety tests.
– Review documentation and certifications to ensure compliance with relevant standards.
Common Testing Methods
B2B buyers should be aware of the following common testing methods used to verify product quality:
– Functional Testing: Ensures that all machine components work together as intended.
– Stress Testing: Evaluates the machine’s durability under various conditions.
– Electrical Safety Testing: Verifies that electrical components comply with safety standards.
Verifying Supplier Quality Control
When sourcing countertop vending machines, B2B buyers should take proactive steps to verify the quality control measures of their suppliers:
- Audits: Conduct regular audits of suppliers’ manufacturing facilities to assess compliance with quality standards.
- Quality Reports: Request detailed quality reports that document testing results and compliance with standards.
- Third-Party Inspections: Engage third-party inspectors to perform independent assessments of the manufacturing process and final products.
QC/Certifications for International Buyers
For international buyers, particularly from Africa, South America, the Middle East, and Europe, understanding the nuances of QC and certifications is crucial:
- Regional Standards: Different regions may have specific standards and certifications that must be adhered to. For example, UL certifications are critical for North American markets, while IEC standards are essential for electrical safety in Europe.
- Import Regulations: Familiarize yourself with the import regulations of your country, as certain certifications may be required to clear customs.
- Supplier Diversity: Consider sourcing from suppliers that hold multiple certifications, as this can indicate a higher level of commitment to quality and safety.
Conclusion
Understanding the manufacturing processes and quality assurance measures for countertop vending machines is essential for international B2B buyers. By focusing on material preparation, forming, assembly, and finishing stages, alongside robust quality control practices, buyers can ensure they source reliable and compliant products. Familiarity with international standards and proactive verification methods will further enhance the procurement process, enabling successful business operations across diverse markets.
Related Video: Made in China 2.0: Top 10 Factory Processes You Must See
Comprehensive Cost and Pricing Analysis for counter top vending machine Sourcing
Cost Structure of Counter Top Vending Machines
When sourcing counter top vending machines, understanding the cost structure is crucial for B2B buyers. The primary components of cost include:
-
Materials: The choice of materials significantly impacts the overall cost. High-quality stainless steel, durable plastics, and electronic components can drive prices up but ensure longevity and reliability.
-
Labor: Labor costs vary based on geographic location. In regions with higher labor costs, such as Europe, manufacturers may charge more. Conversely, sourcing from regions with lower labor costs can reduce expenses.
-
Manufacturing Overhead: This encompasses costs related to factory operations, including utilities, equipment maintenance, and indirect labor. Efficient manufacturing processes can help minimize these costs.
-
Tooling: Initial tooling costs for customized machines can be substantial. Buyers should consider whether the investment in specialized tooling is justified by the expected return.
-
Quality Control (QC): Investing in rigorous QC processes ensures product reliability, which can reduce long-term maintenance costs. However, this will add to the initial cost.
-
Logistics: Shipping and handling costs can vary widely based on distance, shipping method, and packaging. Buyers should factor in these costs when evaluating total expenditure.
-
Margin: Supplier margins can vary based on competition and market demand. Understanding the typical margins in the vending machine market can provide insight into pricing strategies.
Price Influencers
Several factors influence the pricing of counter top vending machines:
-
Volume/MOQ (Minimum Order Quantity): Larger orders typically attract volume discounts. Establishing a relationship with suppliers can also lead to better pricing over time.
-
Specifications/Customization: Custom features such as branding, specialized payment systems, or unique sizes can increase costs. Standard models are usually less expensive.
-
Materials and Quality Certifications: Higher quality materials and certifications (like ISO or CE) can raise costs but may be essential for certain markets. Buyers should assess the importance of these factors based on their target audience.
-
Supplier Factors: The reliability and reputation of the supplier can influence pricing. Established suppliers may charge a premium due to their track record.
-
Incoterms: Understanding shipping terms (like FOB, CIF) is essential. They affect not only the total cost but also the responsibilities for shipping and insurance.
Buyer Tips for Cost-Efficiency
B2B buyers should implement strategies to ensure cost efficiency when sourcing counter top vending machines:
-
Negotiation: Leverage volume and long-term partnership potential to negotiate better prices. Many suppliers are willing to offer discounts for larger commitments or repeat business.
-
Total Cost of Ownership (TCO): Evaluate the total cost, including maintenance, energy consumption, and potential downtime. A lower upfront cost may not be the best value if operational costs are high.
-
Understanding Pricing Nuances: Different regions may have varying pricing structures. For instance, buyers from Africa or South America may encounter additional tariffs or shipping costs that affect the final price. Familiarizing oneself with local regulations can help avoid unexpected expenses.
-
Consider Local Suppliers: Whenever possible, consider sourcing from local suppliers to reduce shipping costs and lead times. This is particularly beneficial for maintenance and support.
Disclaimer
Prices for counter top vending machines can vary widely based on specifications, supplier relationships, and market conditions. It is advisable to conduct thorough market research and obtain multiple quotes to ensure competitive pricing and value for money.
Spotlight on Potential counter top vending machine Manufacturers and Suppliers
This section offers a look at a few manufacturers active in the ‘counter top vending machine’ market. This is a representative sample for illustrative purposes; B2B buyers must conduct their own extensive due diligence before any engagement. Information is synthesized from public sources and general industry knowledge.
Essential Technical Properties and Trade Terminology for counter top vending machine
When considering the procurement of countertop vending machines, it is essential for international B2B buyers to understand the technical specifications and relevant trade terminology that can influence purchasing decisions. This knowledge not only facilitates better negotiations but also ensures that the machines meet operational requirements efficiently.
Critical Technical Specifications
-
Material Grade
– Definition: The quality of materials used in the construction of the vending machine, typically stainless steel or high-grade plastics.
– Importance: High-grade materials ensure durability, resistance to corrosion, and longevity of the machine, which is crucial in high-traffic environments. For instance, machines in humid climates like those in parts of Africa or South America need materials that withstand moisture. -
Capacity
– Definition: The number of items the vending machine can hold, often measured in cubic feet or number of selections.
– Importance: Understanding capacity is vital for matching the machine to the expected customer volume. A higher capacity can reduce restocking frequency, which is essential for maximizing operational efficiency in diverse markets. -
Power Consumption
– Definition: The amount of electricity the vending machine consumes, usually expressed in watts or kilowatt-hours.
– Importance: Low power consumption is crucial for reducing operational costs, especially in regions where electricity is expensive or supply is inconsistent. Buyers should look for energy-efficient models that comply with local energy regulations. -
Temperature Control
– Definition: The ability of the machine to maintain specific temperatures for food and beverages, typically ranging from refrigeration (around 4°C) to room temperature.
– Importance: This is particularly significant for machines dispensing perishable items. Effective temperature control can prevent spoilage, ensuring product quality and safety, which is vital for customer satisfaction.
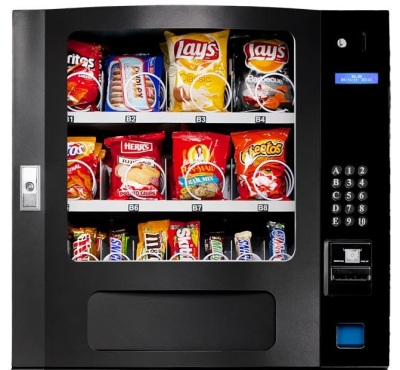
Illustrative Image (Source: Google Search)
-
Connectivity Options
– Definition: The available options for connecting the vending machine to payment systems, including cash, card, and mobile payments.
– Importance: Diverse connectivity options enhance customer convenience and can significantly affect sales. Machines that support mobile payments may appeal more to tech-savvy consumers in urban areas of Europe or South America. -
User Interface
– Definition: The design and functionality of the machine’s display and selection buttons.
– Importance: An intuitive user interface can enhance the customer experience and reduce transaction time. This is especially important in busy environments where quick service is a priority.
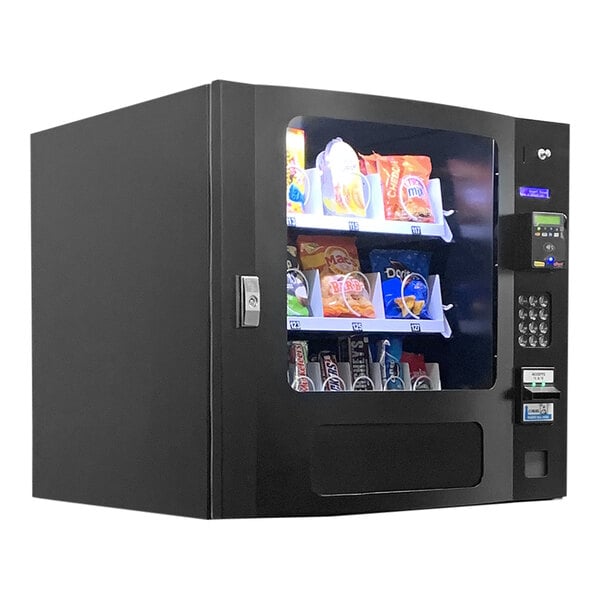
Illustrative Image (Source: Google Search)
Common Trade Terminology
-
OEM (Original Equipment Manufacturer)
– Definition: A company that produces parts and equipment that may be marketed by another manufacturer.
– Significance: Understanding OEM relationships can help buyers identify reliable suppliers and ensure they are sourcing quality components for their machines. -
MOQ (Minimum Order Quantity)
– Definition: The smallest quantity of a product that a supplier is willing to sell.
– Significance: Knowing the MOQ is crucial for budgeting and inventory management. Buyers should assess their needs against the MOQ to avoid excess inventory or unmet demand. -
RFQ (Request for Quotation)
– Definition: A document that solicits price quotes from suppliers for specific products or services.
– Significance: Utilizing RFQs allows buyers to compare offers and negotiate better terms, ensuring they obtain the best value for their investment. -
Incoterms (International Commercial Terms)
– Definition: A set of predefined commercial terms published by the International Chamber of Commerce (ICC) related to international commercial law.
– Significance: Familiarity with Incoterms helps buyers understand their responsibilities regarding shipping, insurance, and tariffs, which is essential for smooth international transactions. -
Lead Time
– Definition: The time between the initiation of an order and its completion.
– Significance: Understanding lead times allows buyers to plan their inventory and minimize downtime. It is particularly important in industries where machine availability directly impacts revenue. -
Warranty
– Definition: A guarantee provided by the manufacturer regarding the condition of the product and the terms of repair or replacement.
– Significance: A robust warranty can be a significant factor in decision-making, providing peace of mind regarding the longevity and reliability of the vending machine.
By grasping these specifications and terms, B2B buyers can make informed decisions that enhance operational efficiency and profitability while navigating the complexities of international procurement.
Navigating Market Dynamics, Sourcing Trends, and Sustainability in the counter top vending machine Sector
Market Overview & Key Trends
The countertop vending machine sector is experiencing a notable transformation driven by technological advancements, consumer preferences, and changing market dynamics. Global drivers such as urbanization, increased consumer demand for convenience, and a growing emphasis on contactless transactions are reshaping the market landscape. For B2B buyers in regions like Africa, South America, the Middle East, and Europe, understanding these trends is crucial for making informed sourcing decisions.
Emerging technologies such as IoT integration, cashless payment systems, and AI-driven inventory management are becoming standard features in modern vending machines. These innovations not only enhance user experience but also streamline operations for businesses. Additionally, sustainability is gaining traction, with manufacturers increasingly adopting eco-friendly materials and practices, appealing to environmentally conscious consumers and businesses alike.
International buyers should also be aware of the competitive landscape, which is marked by both established players and new entrants. The latter often focus on niche markets, providing tailored solutions that meet specific regional needs. This dynamic creates opportunities for strategic partnerships and collaborations, allowing buyers to leverage local knowledge and enhance their product offerings.
Sustainability & Ethical Sourcing in B2B
Sustainability is no longer an option but a necessity in the countertop vending machine sector. The environmental impact of traditional vending machines, often characterized by high energy consumption and waste generation, is prompting manufacturers to adopt greener practices. B2B buyers must prioritize suppliers that demonstrate a commitment to sustainability, as this not only mitigates environmental risks but also aligns with the increasing consumer demand for responsible sourcing.
Ethical supply chains are integral to this sustainability movement. Buyers should seek vendors that provide transparency regarding their sourcing practices, particularly in the procurement of materials used in vending machines. Certifications such as FSC (Forest Stewardship Council) for wood products or ISO 14001 for environmental management systems can serve as reliable indicators of a supplier’s commitment to sustainability.
Moreover, the use of recyclable materials and energy-efficient technologies can significantly reduce the carbon footprint of vending machines. By choosing suppliers that prioritize these ‘green’ certifications and materials, international buyers can enhance their brand reputation while contributing to global sustainability efforts.
Brief Evolution/History
The countertop vending machine has evolved significantly since its inception in the early 20th century. Initially designed to dispense basic snacks and beverages, these machines have transformed into sophisticated retail solutions. The advent of digital technology in the late 1990s marked a pivotal shift, introducing features such as electronic payment systems and remote monitoring capabilities.
As consumer preferences shifted towards convenience and personalization, vending machines adapted accordingly, offering a wider range of products and customizable options. Today, the integration of IoT and AI technologies not only enhances operational efficiency but also provides valuable consumer insights, shaping the future of the vending industry. For B2B buyers, understanding this evolution can inform strategic decisions regarding product selection and supplier partnerships.
Related Video: Global Trade & Logistics – What is Global Trade?
Frequently Asked Questions (FAQs) for B2B Buyers of counter top vending machine
-
1. What should I consider when vetting suppliers for countertop vending machines?
When vetting suppliers, prioritize their experience in manufacturing countertop vending machines and their reputation in international markets. Check for certifications such as ISO 9001, which indicates quality management standards. Request references from previous clients, particularly those in your region, to gauge reliability and customer service. Additionally, inquire about their production capacity and any experience with custom designs, as this can impact lead times and fulfillment. -
2. Can countertop vending machines be customized for my business needs?
Yes, many manufacturers offer customization options for countertop vending machines. You can request specific features such as size, design, and technology integration (like cashless payment systems). Discuss your requirements with potential suppliers early in the negotiation process to ensure they can meet your needs. Customization may affect pricing and lead times, so factor these into your budget and timeline. -
3. What are the typical minimum order quantities (MOQ) and lead times for countertop vending machines?
MOQs can vary significantly among suppliers, ranging from a single unit to several dozen, depending on the manufacturer’s policies and production capabilities. Lead times typically span from 4 to 12 weeks, influenced by factors such as customization, order size, and shipping logistics. To avoid delays, communicate your requirements clearly and confirm production timelines during negotiations. -
4. What payment options are available for international purchases of countertop vending machines?
Payment methods for international transactions often include wire transfers, letters of credit, and escrow services. Each option has its own advantages; for example, letters of credit provide security for both parties, while escrow services can protect your funds until delivery is confirmed. Discuss payment terms with suppliers, ensuring they align with your cash flow and financial policies. -
5. How can I ensure quality assurance and certifications for countertop vending machines?
Request documentation of quality assurance processes from suppliers, including inspection reports and testing procedures. Look for compliance with international standards, such as CE marking for European markets or UL certification in the United States. Conducting a factory audit, if feasible, can provide firsthand insight into the supplier’s quality control measures and production practices. -
6. What logistics considerations should I keep in mind when sourcing countertop vending machines?
Logistics play a crucial role in international sourcing. Evaluate shipping options and associated costs, including customs duties and taxes, to determine the total landed cost of your machines. Collaborate with suppliers to understand their shipping capabilities and choose reliable freight forwarders experienced in handling such equipment. Ensure that your delivery terms, such as Incoterms, are clearly defined to avoid misunderstandings. -
7. How should I handle disputes with suppliers?
To manage disputes effectively, establish clear communication channels and document all agreements in writing. If issues arise, approach the supplier directly to resolve them amicably. Consider incorporating dispute resolution clauses in contracts, such as mediation or arbitration, to facilitate a structured approach to conflict resolution. Having a legal advisor familiar with international trade can also be beneficial. -
8. What are the best practices for after-sales support and maintenance of countertop vending machines?
After-sales support is crucial for the longevity of your investment. Ensure that suppliers offer warranty periods and maintenance services. Discuss the availability of spare parts and technical support in your region, which can minimize downtime. It’s also wise to request training for your staff on machine operation and troubleshooting to enhance operational efficiency and customer satisfaction.
Strategic Sourcing Conclusion and Outlook for counter top vending machine
In conclusion, strategic sourcing for countertop vending machines is essential for international B2B buyers looking to maximize value and enhance operational efficiency. By prioritizing suppliers that offer innovative technology, reliable service, and sustainable practices, businesses can ensure they remain competitive in diverse markets such as Africa, South America, the Middle East, and Europe.
Key takeaways include:
- Understanding Market Dynamics: Familiarize yourself with regional consumer preferences and regulatory frameworks to align your sourcing strategies effectively.
- Evaluating Suppliers: Conduct thorough due diligence on potential suppliers, assessing their track record, financial stability, and technological capabilities.
- Leveraging Technology: Embrace advancements such as cashless payment systems and smart inventory management to boost profitability and customer satisfaction.
As you move forward, consider adopting a holistic approach to sourcing that not only focuses on cost but also on quality, sustainability, and innovation. This will empower your business to adapt to evolving market trends and consumer needs. Engage with suppliers who share your vision for a more connected and efficient future, and take proactive steps to secure your position in the countertop vending machine market. The time to act is now—invest in strategic sourcing for lasting success.