Your Ultimate Guide to Sourcing Clothing Vending Machine
Guide to Clothing Vending Machine
- Introduction: Navigating the Global Market for clothing vending machine
- Understanding clothing vending machine Types and Variations
- Key Industrial Applications of clothing vending machine
- Strategic Material Selection Guide for clothing vending machine
- In-depth Look: Manufacturing Processes and Quality Assurance for clothing vending machine
- Comprehensive Cost and Pricing Analysis for clothing vending machine Sourcing
- Spotlight on Potential clothing vending machine Manufacturers and Suppliers
- Essential Technical Properties and Trade Terminology for clothing vending machine
- Navigating Market Dynamics, Sourcing Trends, and Sustainability in the clothing vending machine Sector
- Frequently Asked Questions (FAQs) for B2B Buyers of clothing vending machine
- Strategic Sourcing Conclusion and Outlook for clothing vending machine
Introduction: Navigating the Global Market for clothing vending machine
In an era where convenience meets fashion, clothing vending machines are revolutionizing the retail landscape across the globe. These innovative solutions not only cater to the fast-paced lifestyle of consumers but also open new avenues for businesses looking to expand their reach in the competitive marketplace. As international B2B buyers, particularly from Africa, South America, the Middle East, and Europe, understanding the dynamics of this burgeoning sector is crucial for making informed sourcing decisions.
This guide delves into the multifaceted world of clothing vending machines, offering comprehensive insights into various types available, the materials used in their construction, and best practices for manufacturing and quality control. We will also explore the landscape of suppliers, providing you with a curated list of reliable partners who can meet your specific needs. Cost considerations are paramount in any investment, and this guide will break down potential expenditures, enabling you to budget effectively.
Furthermore, we address common questions and challenges that B2B buyers face in this niche market. By equipping you with the knowledge to navigate the complexities of sourcing clothing vending machines, this guide aims to empower your business decisions, ensuring you remain competitive and responsive to consumer demands in diverse markets. Embrace the opportunity to leverage this growing trend and elevate your offerings today.
Understanding clothing vending machine Types and Variations
Type Name | Key Distinguishing Features | Primary B2B Applications | Brief Pros & Cons for Buyers |
---|---|---|---|
Traditional Clothing Vending | Standard design, typically glass-fronted | Shopping malls, airports, universities | Pros: Low initial investment; Cons: Limited inventory flexibility |
Smart Clothing Vending | Integrated technology for inventory management | Tech-savvy retail environments | Pros: Real-time inventory tracking; Cons: Higher upfront costs |
Eco-Friendly Vending | Made from sustainable materials, promotes eco-awareness | Eco-conscious brands, events | Pros: Appeals to green consumers; Cons: Potentially higher maintenance |
Customizable Vending | Modular design, customizable product offerings | Events, pop-up shops | Pros: Tailored to specific demographics; Cons: Longer lead times for setup |
Automated Fashion Kiosks | Offers a wide variety of clothing and accessories | Urban centers, tourist hotspots | Pros: Diverse product range; Cons: Requires strategic location selection |
Traditional Clothing Vending
Traditional clothing vending machines are characterized by their straightforward design, often featuring a glass front that displays the available items. These machines are commonly found in high-traffic areas such as shopping malls, airports, and universities. For B2B buyers, the key consideration is the low initial investment required, making it accessible for small businesses. However, they may face limitations in inventory flexibility, as restocking can be cumbersome and slow.
Smart Clothing Vending
Smart clothing vending machines integrate advanced technology for enhanced functionality, including real-time inventory management and cashless payment options. They are particularly suited for tech-savvy retail environments where efficiency is paramount. B2B buyers should evaluate the initial investment against the potential for increased sales through improved customer experience. While these machines offer significant advantages, the higher upfront costs may be a barrier for some businesses.
Eco-Friendly Vending
These machines focus on sustainability, utilizing environmentally friendly materials and promoting eco-awareness. They are ideal for brands that align with green values and target eco-conscious consumers, making them suitable for events and eco-focused retail outlets. Buyers should consider the appeal of sustainability to their target market, although the higher maintenance costs could impact profitability.
Customizable Vending
Customizable clothing vending machines feature a modular design that allows businesses to tailor product offerings to specific demographics or events. This flexibility is advantageous for pop-up shops and seasonal events, where consumer preferences may vary. B2B buyers should weigh the benefits of customization against longer lead times for setup and potential supply chain complexities.
Automated Fashion Kiosks
Automated fashion kiosks offer a diverse range of clothing and accessories, often incorporating touch screens for user interaction. These kiosks are best suited for urban centers and tourist hotspots, where foot traffic is high. For B2B buyers, the main consideration is strategic location selection to maximize visibility and sales. While they provide a wide variety of products, the need for careful placement can complicate logistics and inventory management.
Related Video: A Practical Introduction to Large Language Models (LLMs)
Key Industrial Applications of clothing vending machine
Industry/Sector | Specific Application of clothing vending machine | Value/Benefit for the Business | Key Sourcing Considerations for this Application |
---|---|---|---|
Retail | Automated clothing sales in urban centers | Increased accessibility and convenience for customers | Machine size, payment options, and inventory management |
Hospitality | Guest services in hotels and resorts | Enhanced guest experience and additional revenue streams | Customization options, product range, and maintenance |
Transportation & Logistics | Employee uniforms at transit hubs | Streamlined uniform distribution and reduced downtime | Durability, security features, and replenishment systems |
Education | On-campus clothing sales for students | Convenience for students and reduced operational costs | Product variety, payment systems, and machine placement |
Events & Festivals | On-site merchandise sales at large gatherings | Instant access to branded apparel and increased sales | Branding options, stock management, and machine mobility |
Retail
In urban retail environments, clothing vending machines serve as automated sales points, providing easy access to apparel for consumers. These machines can be strategically placed in high-traffic areas, allowing retailers to reach customers who may not have time to visit a traditional store. For international B2B buyers, considerations include machine dimensions to fit space constraints, integration with various payment systems, and effective inventory management to ensure popular items are always in stock.
Hospitality
In the hospitality sector, clothing vending machines can enhance guest experiences in hotels and resorts by offering essentials such as swimwear, loungewear, or branded merchandise. This service not only caters to guest needs but also presents an additional revenue stream for the establishment. For buyers in this sector, customization options for machine branding, a diverse product range, and reliable maintenance services are crucial for maximizing guest satisfaction and operational efficiency.
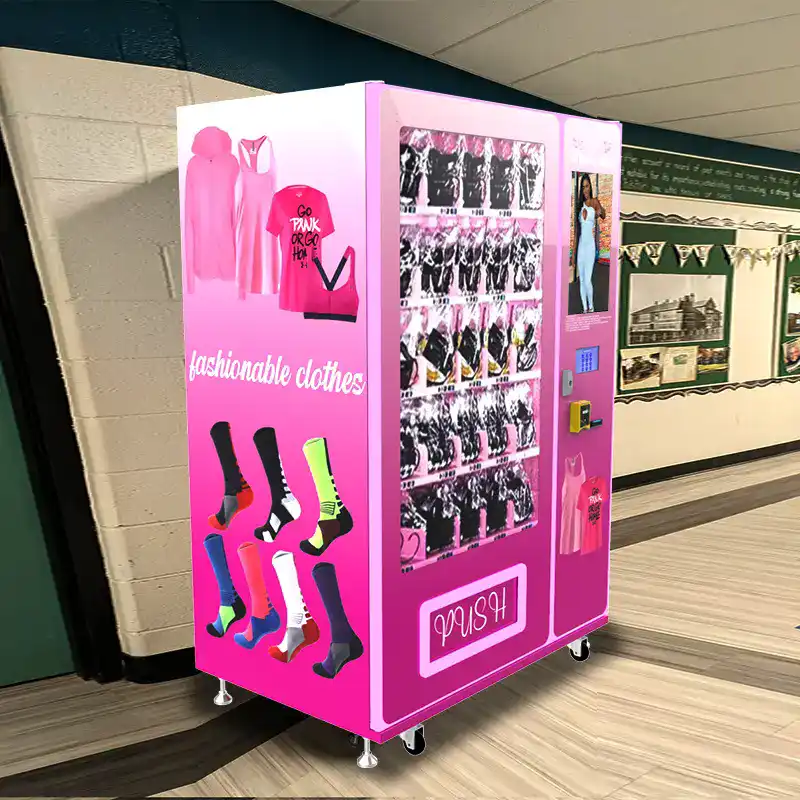
Illustrative Image (Source: Google Search)
Transportation & Logistics
Transportation hubs like airports and bus stations can utilize clothing vending machines to provide employees with easy access to uniforms and workwear. This application helps reduce downtime associated with uniform distribution and ensures staff are always dressed appropriately. B2B buyers in this sector should focus on sourcing machines with durable designs, enhanced security features to prevent theft, and efficient replenishment systems to maintain stock levels.
Education
On college and university campuses, clothing vending machines can offer students convenient access to branded apparel and everyday clothing items. This not only serves the immediate needs of students but can also help institutions reduce operational costs associated with traditional retail outlets. Buyers in the education sector should consider the variety of products offered, ease of payment systems, and optimal machine placement to maximize visibility and usage.
Events & Festivals
At large events and festivals, clothing vending machines provide an efficient way to sell branded merchandise, such as t-shirts and hats. This instant access to apparel can significantly boost sales and enhance the event experience for attendees. B2B buyers focusing on this application should evaluate branding options for the machines, stock management capabilities to handle fluctuating demand, and mobility features to allow for easy relocation as needed.
Related Video: DIY Vending Machine – Arduino based Mechatronics Project
Strategic Material Selection Guide for clothing vending machine
When selecting materials for clothing vending machines, it is crucial to consider factors such as durability, cost, manufacturing complexity, and suitability for the intended application. Below is an analysis of four common materials used in the construction of clothing vending machines, along with actionable insights for international B2B buyers.
1. Stainless Steel
Key Properties:
Stainless steel is known for its excellent corrosion resistance, high strength, and ability to withstand extreme temperatures. It typically has a temperature rating of up to 800°C and can handle significant pressure without deforming.
Pros & Cons:
Stainless steel is highly durable and resistant to rust, making it ideal for high-traffic environments. However, it is more expensive than other materials and can be challenging to manufacture due to its toughness. The end product is suitable for various climates, but the initial cost may be a barrier for some buyers.
Impact on Application:
Stainless steel is compatible with a wide range of media, including moisture and various cleaning agents, which is essential for maintaining hygiene in clothing vending machines.
Considerations for International Buyers:
Buyers from Africa, South America, the Middle East, and Europe should ensure compliance with local regulations regarding materials used in vending machines. Standards such as ASTM and DIN may apply, and preferences for stainless steel grades can vary by region.
2. Powder-Coated Steel
Key Properties:
Powder-coated steel offers a protective layer that enhances corrosion resistance and provides a visually appealing finish. The coating can withstand temperatures up to 200°C and is generally resistant to scratches and fading.
Pros & Cons:
This material is cost-effective and provides a good balance between durability and aesthetics. However, the powder coating can chip or scratch, exposing the underlying steel to corrosion over time. It is suitable for indoor applications but may not perform well in extreme outdoor conditions.
Impact on Application:
The powder coating makes this material compatible with various cleaning agents, but care should be taken to avoid harsh chemicals that could degrade the finish.
Considerations for International Buyers:
Buyers should consider local climate conditions when selecting powder-coated steel. In humid environments, additional protective measures may be necessary to prolong the lifespan of the coating. Compliance with local standards for coatings is also essential.
3. Aluminum
Key Properties:
Aluminum is lightweight, corrosion-resistant, and has a good strength-to-weight ratio. It can withstand temperatures up to 600°C, making it suitable for various applications.
Pros & Cons:
Aluminum is easy to manufacture and can be anodized for enhanced corrosion resistance. However, it is less durable than stainless steel and may not withstand impacts as well. The cost is generally moderate, making it an attractive option for many buyers.
Impact on Application:
Aluminum is compatible with most media used in vending machines and is particularly advantageous in environments where weight is a concern.
Considerations for International Buyers:
Buyers should ensure that the aluminum grades used meet local standards, such as JIS in Japan or EN in Europe. Additionally, in regions with high salt exposure, such as coastal areas, special anodizing treatments may be necessary.
4. High-Density Polyethylene (HDPE)
Key Properties:
HDPE is a thermoplastic known for its high impact resistance and chemical stability. It can operate effectively in temperatures ranging from -40°C to 60°C.
Pros & Cons:
HDPE is lightweight and cost-effective, making it an excellent choice for budget-conscious buyers. However, it may not offer the same level of durability as metals and can be susceptible to UV degradation if not treated. It is best suited for indoor applications.
Impact on Application:
HDPE is compatible with various cleaning agents and is easy to maintain, which is advantageous for vending machine hygiene.
Considerations for International Buyers:
Buyers should verify that HDPE products comply with local food safety and environmental regulations, particularly in regions with stringent standards.
Summary Table
Material | Typical Use Case for clothing vending machine | Key Advantage | Key Disadvantage/Limitation | Relative Cost (Low/Med/High) |
---|---|---|---|---|
Stainless Steel | High-traffic environments, outdoor use | Excellent corrosion resistance | High cost, manufacturing complexity | High |
Powder-Coated Steel | Indoor applications, aesthetic designs | Cost-effective, good aesthetics | Susceptible to chipping | Medium |
Aluminum | Lightweight, portable vending machines | Lightweight, easy to manufacture | Less durable than steel | Medium |
High-Density Polyethylene (HDPE) | Indoor, budget-friendly vending machines | Lightweight, cost-effective | Susceptible to UV degradation | Low |
This material selection guide provides actionable insights for B2B buyers to make informed decisions when sourcing materials for clothing vending machines, taking into account both performance and regional considerations.
In-depth Look: Manufacturing Processes and Quality Assurance for clothing vending machine
Manufacturing Processes for Clothing Vending Machines
The manufacturing of clothing vending machines involves several critical stages, each contributing to the overall functionality and quality of the final product. Understanding these stages can help international B2B buyers make informed decisions when sourcing from suppliers.
1. Material Preparation
Material preparation is the foundational step in the manufacturing process. It involves selecting high-quality materials that are durable and suitable for various environmental conditions. Common materials include:
- Metal: Typically steel or aluminum for the machine’s frame, providing strength and stability.
- Plastic: Used for components like display panels and internal mechanisms, often requiring UV resistance for outdoor machines.
- Electronic Components: Including payment systems, touch screens, and sensors, which must meet specific quality and safety standards.
Buyers should ensure that suppliers use materials compliant with international standards, as this can affect the machine’s longevity and performance.
2. Forming
In this stage, raw materials are shaped into components using various techniques:
- CNC Machining: For precision parts, ensuring that dimensions meet specifications.
- Injection Molding: Common for plastic parts, allowing for complex shapes and high-volume production.
- Sheet Metal Fabrication: For the machine’s exterior, providing robustness and aesthetic appeal.
B2B buyers should inquire about the machinery used in this stage, as advanced technology can enhance precision and reduce waste.
3. Assembly
The assembly process combines all manufactured components into a functional machine. Key activities in this stage include:
- Mechanical Assembly: Involves fitting together metal and plastic parts, often requiring skilled labor to ensure proper alignment and functionality.
- Electrical Assembly: Installation of wiring, control panels, and payment systems. This is crucial for the machine’s operational efficiency.
Buyers should assess the supplier’s assembly line efficiency and workforce training, as this can impact lead times and product quality.
4. Finishing
Finishing involves the final touches that enhance both the appearance and durability of the vending machines. This includes:
- Surface Treatment: Such as powder coating or painting to protect against corrosion and improve aesthetics.
- Quality Control Checks: Conducted throughout the assembly and finishing processes to ensure that all parts meet quality standards.
B2B buyers can request samples of finished products to evaluate the quality of finishes and overall craftsmanship.
Quality Assurance in Manufacturing
Quality assurance (QA) is essential in the manufacturing of clothing vending machines to ensure that they meet both international and industry-specific standards. The following outlines the key elements of a robust QA process.
International Standards
Adherence to international standards is crucial for ensuring product safety and reliability. Key standards include:
- ISO 9001: Focuses on quality management systems, ensuring that suppliers have processes in place for consistent quality.
- CE Marking: Indicates compliance with European safety, health, and environmental protection standards, essential for machines sold in Europe.
B2B buyers from Africa, South America, the Middle East, and Europe should verify that suppliers possess these certifications, as they can facilitate smoother market entry.
Industry-Specific Standards
In addition to general standards, there are industry-specific certifications that may apply:
- API Standards: Relevant for machines that involve complex electronic systems, ensuring reliability and performance.
- Local Compliance Regulations: Depending on the region, there may be additional certifications required for vending machines.
B2B buyers should familiarize themselves with local compliance requirements in their target markets to avoid regulatory issues.
Quality Control Checkpoints
Effective quality control involves multiple checkpoints throughout the manufacturing process:
- Incoming Quality Control (IQC): Inspection of raw materials upon arrival to ensure they meet specifications.
- In-Process Quality Control (IPQC): Continuous monitoring during the manufacturing process to catch defects early.
- Final Quality Control (FQC): Comprehensive testing of the finished product to verify functionality and safety.
B2B buyers should inquire about the specific QC protocols employed by suppliers to understand their commitment to quality.
Common Testing Methods
Testing methods play a critical role in quality assurance. Common methods include:
- Functional Testing: Ensuring that all mechanical and electronic components work as intended.
- Durability Testing: Simulating long-term use to assess wear and tear.
- Safety Testing: Checking for electrical safety and compliance with regulatory standards.
Buyers can request detailed testing reports from suppliers to confirm that these methods are rigorously applied.
Verifying Supplier Quality Control
To ensure that suppliers maintain high-quality standards, B2B buyers should consider the following verification strategies:
- Supplier Audits: Conducting on-site audits to evaluate manufacturing processes, quality control systems, and compliance with international standards.
- Quality Assurance Reports: Requesting regular reports that detail quality control measures, test results, and any corrective actions taken.
- Third-Party Inspections: Engaging independent inspection services to evaluate products before shipment, providing an unbiased assessment of quality.
Buyers from diverse regions should also be aware of potential cultural differences in manufacturing practices and communication styles, which can affect the quality assurance process.
Conclusion
Understanding the manufacturing processes and quality assurance practices behind clothing vending machines is vital for international B2B buyers. By focusing on material selection, forming techniques, assembly methods, and rigorous quality control, buyers can make informed decisions that ensure they source reliable and high-quality machines. Leveraging international standards and conducting thorough supplier evaluations will further enhance the purchasing process, ultimately leading to successful business outcomes.
Related Video: Amazing Garment Manufacturing Process from Fabric to Finished Product Inside the Factory
Comprehensive Cost and Pricing Analysis for clothing vending machine Sourcing
When sourcing clothing vending machines, understanding the comprehensive cost structure and pricing dynamics is crucial for international B2B buyers. This knowledge not only helps in budget planning but also aids in making informed purchasing decisions that can significantly impact profitability.
Cost Components
-
Materials: The choice of materials directly influences the machine’s durability and cost. Common materials include steel for the frame and high-quality plastics for the display and dispensing mechanisms. Opting for eco-friendly or recycled materials may increase initial costs but can appeal to environmentally conscious consumers.
-
Labor: Labor costs vary significantly by region. In countries with higher labor costs, such as parts of Europe, manufacturing expenses can be substantial. Conversely, sourcing from regions with lower labor costs, such as parts of Asia or South America, may provide more competitive pricing but could introduce quality control challenges.
-
Manufacturing Overhead: This includes expenses related to the facility, equipment, and utilities needed for production. Buyers should consider manufacturers that optimize overhead costs through efficient production processes, as this can lead to lower prices for bulk orders.
-
Tooling: Customization of vending machines often requires specialized tooling. Initial tooling costs can be high, especially for unique designs or features. However, these costs can be amortized over larger production runs, making it essential to negotiate Minimum Order Quantities (MOQs) that align with your budget.
-
Quality Control (QC): Implementing stringent QC processes is vital to ensure product reliability and customer satisfaction. While increased QC measures can raise costs, they can save money in the long run by reducing returns and enhancing brand reputation.
-
Logistics: Shipping costs vary based on the distance from the manufacturer to the buyer’s location and the chosen mode of transport. It’s essential to consider Incoterms, as they determine who is responsible for shipping costs and risks. For instance, choosing FOB (Free On Board) may reduce costs for buyers by allowing them to handle shipping logistics.
-
Margin: Suppliers typically add a profit margin to cover their costs and ensure profitability. Understanding the typical margins in your region can help buyers negotiate better pricing terms.
Price Influencers
-
Volume/MOQ: Higher order volumes often lead to lower unit prices due to economies of scale. Buyers should assess their demand to negotiate favorable terms with suppliers.
-
Specifications/Customization: Custom features can significantly impact pricing. While customization may align products more closely with market needs, it’s essential to balance these enhancements against cost implications.
-
Materials and Quality Certifications: Machines made from higher-quality materials or those that comply with international safety and quality standards may command higher prices. Ensure that the added cost aligns with your target market’s expectations.
-
Supplier Factors: The reliability and reputation of the supplier can influence pricing. Established suppliers may charge a premium for their proven track record, while newer entrants might offer lower prices to gain market share.
Buyer Tips
-
Negotiation: Engage in open discussions with suppliers to explore flexible pricing options. Demonstrating long-term purchasing potential can leverage better deals.
-
Cost-Efficiency: Always analyze the Total Cost of Ownership (TCO), which includes initial purchase price, maintenance, and operational costs over the machine’s lifespan. This approach can prevent short-term savings from leading to long-term losses.
-
International Pricing Nuances: Be aware of currency fluctuations and regional market conditions that can affect pricing. In regions such as Africa and South America, local economic factors may introduce additional costs that should be factored into negotiations.
Disclaimer
The prices referenced in this analysis are indicative and may vary based on market conditions, supplier negotiations, and specific buyer requirements. It is advisable to conduct thorough market research and obtain multiple quotes before making purchasing decisions.
Spotlight on Potential clothing vending machine Manufacturers and Suppliers
- (No specific manufacturer data was available or requested for detailed profiling in this section for clothing vending machine.)*
Essential Technical Properties and Trade Terminology for clothing vending machine
Key Technical Properties of Clothing Vending Machines
When selecting clothing vending machines, understanding the essential technical properties can significantly influence purchasing decisions. Here are critical specifications to consider:
-
Material Grade
– Definition: This refers to the quality and type of materials used in the construction of the vending machine, including metals, plastics, and glass.
– B2B Importance: High-grade materials ensure durability and resistance to wear and tear, which is crucial for machines placed in high-traffic locations. Buyers should prioritize machines made from corrosion-resistant materials, especially in humid or coastal environments. -
Capacity
– Definition: The number of clothing items a vending machine can hold, typically measured in units or kilograms.
– B2B Importance: Higher capacity machines can cater to larger customer bases, making them more suitable for busy locations like malls or airports. Buyers should evaluate capacity against expected foot traffic to optimize inventory management. -
Size and Footprint
– Definition: The physical dimensions of the vending machine, including height, width, and depth.
– B2B Importance: Understanding the size is essential for space planning in retail environments. A compact design may be preferable in urban areas with limited space, whereas larger machines might be suitable for more expansive locations. -
Power Requirements
– Definition: The electrical specifications necessary for the machine to operate, including voltage and amperage.
– B2B Importance: Compatibility with local power standards is crucial for installation. Buyers should ensure that the machine meets the electrical infrastructure of their location to avoid additional installation costs. -
User Interface
– Definition: The design and functionality of the machine’s interface, including touchscreens, payment systems, and language options.
– B2B Importance: An intuitive user interface can enhance customer satisfaction and increase sales. Machines equipped with multilingual options are particularly beneficial in diverse markets, catering to a broader customer base.
Common Trade Terms in the Clothing Vending Machine Industry
Familiarity with industry terminology is essential for effective communication and negotiation. Here are common jargon terms relevant to B2B buyers:
-
OEM (Original Equipment Manufacturer)
– Definition: A company that produces parts or equipment that may be marketed by another manufacturer.
– Importance: Understanding OEM relationships can help buyers identify reliable suppliers and negotiate better terms based on the quality and reputation of the original manufacturer. -
MOQ (Minimum Order Quantity)
– Definition: The smallest quantity of a product that a supplier is willing to sell.
– Importance: Knowing the MOQ is crucial for budgeting and inventory planning. Buyers should assess their needs against the MOQ to avoid overstocking or incurring higher costs. -
RFQ (Request for Quotation)
– Definition: A document sent to suppliers to request pricing and other details for specific products or services.
– Importance: An RFQ helps buyers compare different suppliers based on pricing, delivery terms, and product specifications, facilitating informed decision-making. -
Incoterms (International Commercial Terms)
– Definition: A series of pre-defined commercial terms published by the International Chamber of Commerce (ICC) that clarify the responsibilities of buyers and sellers.
– Importance: Familiarity with Incoterms helps buyers understand shipping responsibilities, insurance, and liability, which is vital for international transactions and logistics planning. -
Lead Time
– Definition: The time taken from placing an order to receiving the goods.
– Importance: Understanding lead times allows buyers to plan inventory levels and manage customer expectations effectively. Buyers should negotiate lead times to align with their operational needs.
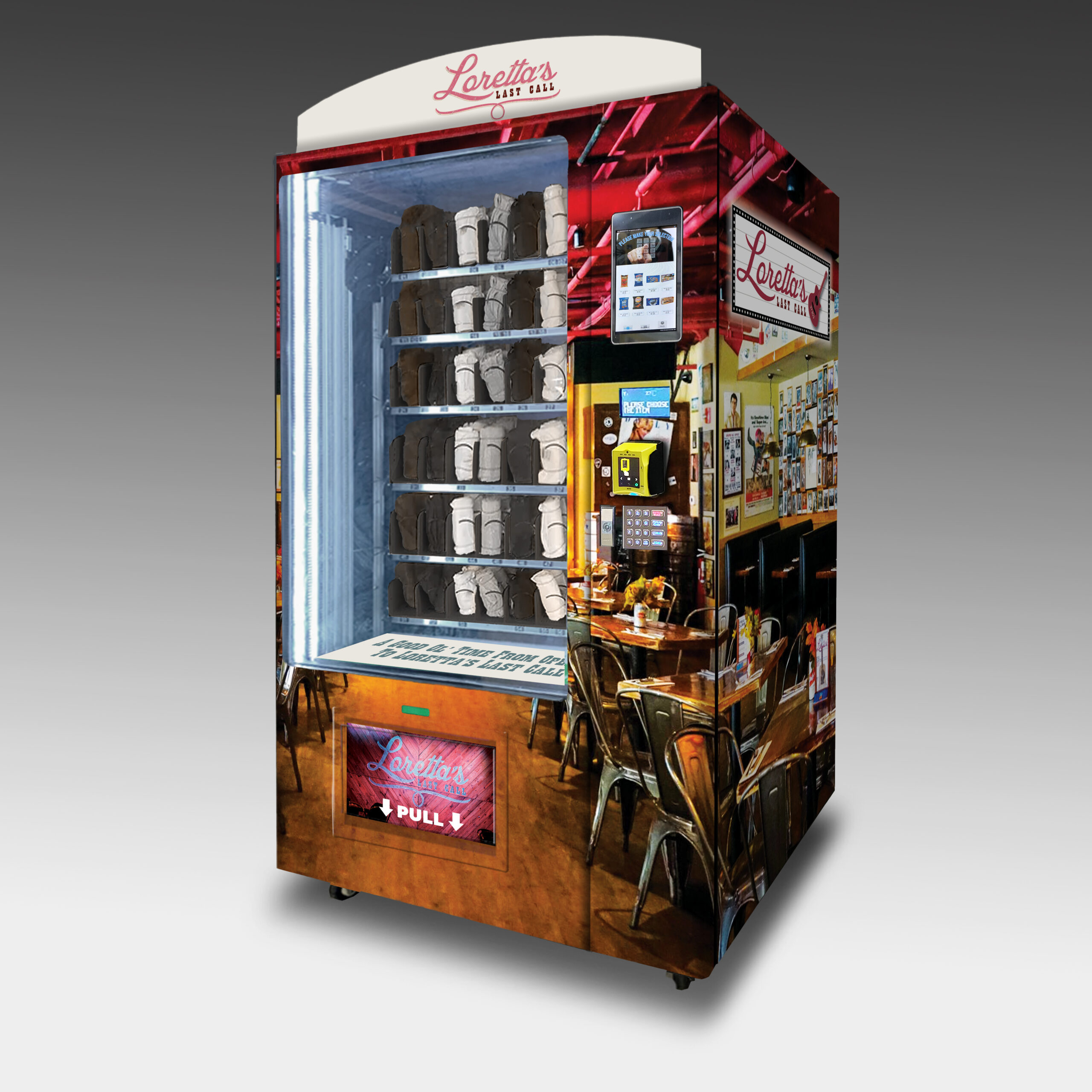
Illustrative Image (Source: Google Search)
- Warranty
– Definition: A guarantee provided by the manufacturer regarding the condition of the machine and the period during which repairs or replacements will be covered.
– Importance: A strong warranty can mitigate risks associated with machinery malfunctions. Buyers should carefully evaluate warranty terms to ensure long-term support and service reliability.
By grasping these technical properties and trade terms, international B2B buyers can make informed decisions when investing in clothing vending machines, ensuring they select solutions that best fit their operational needs and market dynamics.
Navigating Market Dynamics, Sourcing Trends, and Sustainability in the clothing vending machine Sector
Market Overview & Key Trends
The clothing vending machine sector is experiencing significant growth driven by evolving consumer behaviors, technological advancements, and urbanization. International B2B buyers are increasingly drawn to this market due to the rising demand for convenience and instant access to fashion items, particularly in densely populated urban areas across Africa, South America, the Middle East, and Europe. Key trends include the integration of smart technology, such as AI and IoT, which enhance inventory management and customer engagement through personalized shopping experiences.
Emerging sourcing trends focus on local production to reduce lead times and enhance supply chain resilience. Buyers are encouraged to explore partnerships with local manufacturers to meet regional demand while minimizing transportation costs. Moreover, the rise of e-commerce is influencing the design of clothing vending machines, making them more user-friendly with touch screens and cashless payment options, appealing to a tech-savvy demographic.
The market dynamics are also shaped by the competitive landscape, where companies are differentiating themselves through unique product offerings and enhanced customer experiences. As urban environments evolve, the proliferation of pop-up retail spaces and mobile vending solutions presents new opportunities for B2B buyers to invest in adaptable and scalable vending solutions that align with local consumer preferences.
Sustainability & Ethical Sourcing in B2B
Sustainability has become a critical focus in the clothing vending machine sector, as environmental concerns gain prominence globally. B2B buyers must consider the environmental impact of their sourcing decisions, particularly in the context of fast fashion. The use of sustainable materials and eco-friendly production processes can significantly reduce the carbon footprint associated with clothing vending machines.
Ethical supply chains are essential for maintaining brand reputation and consumer trust. Buyers should prioritize partnerships with suppliers who adhere to fair labor practices and demonstrate a commitment to sustainability. Certifications such as GOTS (Global Organic Textile Standard) and OEKO-TEX can provide assurance that the materials used meet rigorous environmental and social criteria.
Incorporating recycled materials in vending machine designs and promoting sustainable fashion choices can resonate well with environmentally-conscious consumers. By aligning their sourcing strategies with sustainability goals, international B2B buyers can not only enhance their market appeal but also contribute positively to the global effort against climate change.
Brief Evolution/History
The concept of vending machines has evolved significantly since their inception in the early 20th century, initially offering simple snacks and beverages. The introduction of clothing vending machines can be traced back to the late 1990s when innovative entrepreneurs began to recognize the potential for automated retail in the fashion industry. Over the past two decades, advancements in technology, coupled with shifts in consumer behavior towards convenience and immediacy, have propelled the growth of clothing vending machines.
Today, these machines are equipped with sophisticated technology, offering a wide range of apparel options from basic clothing to luxury items. As the market continues to evolve, international B2B buyers have the opportunity to leverage this growth by adopting innovative vending solutions that cater to diverse consumer needs and preferences across various regions.
Related Video: International Trade Explained
Frequently Asked Questions (FAQs) for B2B Buyers of clothing vending machine
-
What factors should I consider when vetting suppliers of clothing vending machines?
When vetting suppliers, prioritize their experience in the industry, production capabilities, and existing client testimonials. Verify their compliance with international standards relevant to your region, such as CE or ISO certifications. Assess their financial stability and reputation by checking their credit ratings and business history. Additionally, engage in direct communication to gauge their responsiveness and willingness to customize products to meet your specific requirements. -
Can clothing vending machines be customized to suit my brand?
Yes, many suppliers offer customization options for clothing vending machines. This can include branding elements like logos, color schemes, and specific machine designs tailored to your target market. When discussing customization, inquire about the minimum order quantities (MOQ) and any additional costs associated with bespoke modifications. Ensure that the supplier can provide mock-ups or prototypes before final production to align with your expectations. -
What are the typical minimum order quantities (MOQ) and lead times for purchasing clothing vending machines?
Minimum order quantities can vary significantly based on the supplier’s production capacity and the complexity of the machines. Generally, MOQs range from 5 to 50 units. Lead times can also differ, typically ranging from 4 to 12 weeks, depending on whether the machines are in stock or require manufacturing. It’s advisable to discuss these aspects upfront and plan your procurement strategy accordingly to avoid delays in your market entry. -
What payment terms should I expect when sourcing clothing vending machines internationally?
Payment terms vary by supplier and may include options like upfront payments, letters of credit, or installment payments. Typically, a 30-50% deposit is required before production, with the balance due upon shipment or delivery. Ensure to clarify all payment terms in the contract to avoid any misunderstandings. Additionally, consider utilizing secure payment methods that provide buyer protection, especially when dealing with new suppliers. -
How can I ensure quality assurance and certification for clothing vending machines?
Request copies of all relevant quality assurance certifications from your supplier, such as ISO 9001 or CE marking, which indicate compliance with international safety and quality standards. It’s also wise to inquire about their quality control processes, including inspections during manufacturing and before shipment. If possible, arrange for third-party inspections to validate the product quality before accepting delivery, especially when sourcing from overseas suppliers. -
What logistics considerations should I keep in mind when importing clothing vending machines?
Logistics planning is crucial when importing vending machines. Assess shipping options, including air freight for quicker delivery or sea freight for cost efficiency. Consider the total landed cost, which includes shipping, customs duties, and taxes. Collaborate with a freight forwarder experienced in handling machinery to navigate customs regulations effectively. Ensure that your supplier provides the necessary documentation, such as commercial invoices and packing lists, to facilitate smooth customs clearance. -
How should I handle disputes with suppliers?
To effectively manage disputes, maintain clear and documented communication with your supplier throughout the procurement process. Establish a written agreement detailing terms, responsibilities, and dispute resolution procedures. If a disagreement arises, attempt to resolve it amicably through direct negotiation. If that fails, consider mediation or arbitration as alternatives to litigation. Being proactive in addressing issues can help preserve your business relationship and mitigate potential losses. -
What are the best practices for after-sales support and maintenance of clothing vending machines?
After-sales support is critical for the longevity of your vending machines. Ensure that your supplier offers comprehensive warranties and service agreements, including maintenance schedules and troubleshooting support. Familiarize yourself with the machine’s operational guidelines and training materials provided by the supplier. Establish a local service network or partner with a maintenance provider to address issues promptly, ensuring minimal downtime and customer satisfaction.
Strategic Sourcing Conclusion and Outlook for clothing vending machine
As the clothing vending machine market evolves, strategic sourcing becomes increasingly vital for international B2B buyers. By prioritizing partnerships with reliable suppliers and manufacturers, businesses can ensure a steady supply of high-quality, diverse products that meet local demands across regions like Africa, South America, the Middle East, and Europe.
Key Takeaways:
– Market Research: Understanding regional preferences is crucial. Tailor your offerings to align with cultural trends and consumer behaviors to drive sales.
– Supplier Relationships: Foster strong, transparent relationships with suppliers to enhance negotiation leverage and ensure product quality and availability.
– Technology Integration: Leverage advancements in vending machine technology to offer a seamless shopping experience, including cashless payment options and smart inventory management systems.
Looking ahead, the clothing vending machine sector presents significant opportunities for growth and innovation. B2B buyers are encouraged to stay agile and responsive to market changes, embracing sustainable practices and technological advancements. Now is the time to explore strategic sourcing options that not only enhance your product offerings but also position your business as a leader in this burgeoning market. Embrace the future of retail—your next successful partnership could be just around the corner.