Your Ultimate Guide to Sourcing Carvanna Car Vending Machine
Guide to Carvanna Car Vending Machine
- Introduction: Navigating the Global Market for carvanna car vending machine
- Understanding carvanna car vending machine Types and Variations
- Key Industrial Applications of carvanna car vending machine
- Strategic Material Selection Guide for carvanna car vending machine
- In-depth Look: Manufacturing Processes and Quality Assurance for carvanna car vending machine
- Comprehensive Cost and Pricing Analysis for carvanna car vending machine Sourcing
- Spotlight on Potential carvanna car vending machine Manufacturers and Suppliers
- Essential Technical Properties and Trade Terminology for carvanna car vending machine
- Navigating Market Dynamics, Sourcing Trends, and Sustainability in the carvanna car vending machine Sector
- Frequently Asked Questions (FAQs) for B2B Buyers of carvanna car vending machine
- Strategic Sourcing Conclusion and Outlook for carvanna car vending machine
Introduction: Navigating the Global Market for carvanna car vending machine
In today’s rapidly evolving automotive market, the Carvana car vending machine stands out as a revolutionary solution for vehicle sales and distribution. This innovative approach not only enhances the buying experience for consumers but also optimizes inventory management for businesses. For international B2B buyers, particularly those in regions like Africa, South America, the Middle East, and Europe, understanding the nuances of this technology is critical to making informed sourcing decisions.
This comprehensive guide delves into the various aspects of the Carvana car vending machine, including the different types available, the materials used in their construction, and the manufacturing and quality control processes that ensure reliability and efficiency. We will also explore potential suppliers, pricing structures, and the market dynamics that influence the adoption of this technology across diverse regions.
By equipping international buyers with actionable insights and a deeper understanding of the Carvana car vending machine, this guide empowers businesses to navigate the complexities of sourcing and implementing this cutting-edge solution. Whether you are considering entry into new markets or optimizing your current operations, the knowledge gained from this resource will be invaluable in enhancing your competitive edge in the global automotive landscape.
Understanding carvanna car vending machine Types and Variations
Type Name | Key Distinguishing Features | Primary B2B Applications | Brief Pros & Cons for Buyers |
---|---|---|---|
Standard Car Vending Machine | Vertical storage, automated retrieval system | Urban car dealerships, rental services | Pros: Space-efficient, reduces labor costs. Cons: High initial investment. |
Hybrid Car Vending Machine | Combines electric and traditional vehicle options | Eco-friendly dealerships, car-sharing services | Pros: Appeals to environmentally conscious consumers. Cons: May require specialized maintenance. |
Luxury Car Vending Machine | High-end finishes, climate control for vehicles | Luxury car dealerships, premium rentals | Pros: Enhances brand image, attracts affluent customers. Cons: Limited market appeal, higher operational costs. |
Mobile Car Vending Machine | Portable design, easy relocation | Pop-up dealerships, events, festivals | Pros: Flexibility in location, low setup costs. Cons: Limited inventory, potential logistical challenges. |
Multi-Brand Car Vending Machine | Offers vehicles from various manufacturers | Multi-brand dealerships, franchise operations | Pros: Broadens customer base, diverse inventory. Cons: Complex inventory management. |
Standard Car Vending Machine
The Standard Car Vending Machine is designed for efficient vertical storage and automated retrieval, making it ideal for urban car dealerships and rental services. It maximizes space while minimizing the need for staff, thus reducing labor costs. However, the initial investment can be substantial, which may deter smaller businesses.
Hybrid Car Vending Machine
This variation integrates electric and traditional combustion engine vehicles, catering to eco-conscious consumers. It is particularly suitable for dealerships emphasizing sustainability and car-sharing services. While it appeals to a growing market segment, the need for specialized maintenance can add to operational complexities.
Luxury Car Vending Machine
Tailored for high-end vehicles, this vending machine features climate control and premium finishes, enhancing the customer experience. It is primarily used by luxury car dealerships and premium rental services to attract affluent clients. While it elevates brand perception, the operational costs can be significantly higher, limiting its feasibility for some businesses.
Mobile Car Vending Machine
The Mobile Car Vending Machine is characterized by its portability, allowing it to be easily relocated for pop-up dealerships or events. This flexibility can be advantageous for businesses looking to reach diverse markets without a permanent location. However, the limited inventory and potential logistical challenges may restrict its effectiveness.
Multi-Brand Car Vending Machine
This type accommodates vehicles from various manufacturers, making it suitable for multi-brand dealerships and franchise operations. It allows businesses to cater to a broader customer base with diverse inventory options. However, managing such a wide range of vehicles can complicate inventory control and operational processes.
Related Video: Carvana – Car Vending Machine
Key Industrial Applications of carvanna car vending machine
Industry/Sector | Specific Application of carvanna car vending machine | Value/Benefit for the Business | Key Sourcing Considerations for this Application |
---|---|---|---|
Automotive Retail | Automated car sales and distribution | Streamlined purchasing process, reduced overhead | Integration with local payment systems, logistics support |
Fleet Management | Vehicle acquisition and management | Efficient fleet expansion, reduced procurement time | Compatibility with fleet management software, service support |
E-commerce | Online car sales platform | Enhanced customer experience, increased sales volume | Website integration, customer data security |
Car Rental Services | Self-service vehicle rental | Improved customer satisfaction, reduced labor costs | User-friendly interface, maintenance support |
Used Car Dealerships | Trade-in and resale of vehicles | Increased inventory turnover, simplified sales process | Quality assurance protocols, warranty options |
Automotive Retail
In the automotive retail sector, the Carvana car vending machine serves as an innovative solution for automated car sales and distribution. By allowing customers to select and purchase vehicles through a digital interface, businesses can streamline their purchasing processes and significantly reduce overhead costs associated with traditional dealership operations. International B2B buyers should consider the integration of local payment systems and logistics support to ensure a seamless transaction experience.
Fleet Management
For fleet management companies, the Carvana vending machine can facilitate vehicle acquisition and management. This application allows businesses to efficiently expand their fleet by purchasing vehicles directly through the machine, thus minimizing procurement times. Buyers in this sector should evaluate the compatibility of the vending machine with existing fleet management software and the availability of service support to maintain operational efficiency.
E-commerce
In the e-commerce realm, the Carvana vending machine can be integrated into online car sales platforms, enhancing customer experience and increasing sales volume. This technology allows for a more engaging shopping process, which can attract a broader customer base. B2B buyers must focus on website integration capabilities and customer data security to protect sensitive information during transactions.
Car Rental Services
Car rental services can benefit from implementing the Carvana vending machine as a self-service vehicle rental solution. This application not only improves customer satisfaction by providing a quick and easy rental process but also reduces labor costs associated with traditional rental operations. Key considerations for international buyers include ensuring a user-friendly interface and reliable maintenance support to keep the machines operational.
Used Car Dealerships
Used car dealerships can utilize the Carvana vending machine for trade-in and resale of vehicles, leading to increased inventory turnover and a simplified sales process. This technology allows dealerships to streamline their operations, making it easier to manage vehicle sales. Buyers should consider establishing quality assurance protocols and warranty options to enhance customer trust and satisfaction in this application.
Strategic Material Selection Guide for carvanna car vending machine
When selecting materials for the Carvana car vending machine, it is essential to consider various factors, including performance, durability, manufacturing complexity, and cost. Below, we analyze four common materials used in the construction of these machines, focusing on their properties, advantages, disadvantages, and implications for international B2B buyers.
1. Stainless Steel (e.g., AISI 304)
Key Properties:
Stainless steel is known for its excellent corrosion resistance, high strength, and ability to withstand extreme temperatures. It typically has a temperature rating up to 870°C (1600°F) and can handle moderate pressure.
Pros & Cons:
The primary advantage of stainless steel is its durability and resistance to rust and corrosion, making it suitable for outdoor applications. However, it is relatively expensive compared to other materials and can be challenging to machine, which may increase manufacturing costs.
Impact on Application:
Stainless steel is compatible with various media, including water, oils, and chemicals, making it an excellent choice for components exposed to these substances.
Considerations for International Buyers:
Buyers from regions like Africa and South America should ensure compliance with local corrosion resistance standards. In Europe, adherence to ASTM and EN standards is crucial.
2. Carbon Steel (e.g., A36)
Key Properties:
Carbon steel offers good tensile strength and is generally less expensive than stainless steel. It is suitable for applications with a maximum temperature of around 400°C (752°F) and moderate pressure.
Pros & Cons:
While carbon steel is cost-effective and easy to fabricate, it is prone to corrosion if not adequately protected. This limitation necessitates additional coatings or treatments, which can add to the total cost.
Impact on Application:
Carbon steel is well-suited for structural components of the vending machine that do not come into direct contact with corrosive substances.
Considerations for International Buyers:
Buyers should be aware of local standards regarding carbon steel grades and coatings, especially in humid climates where corrosion is a concern.
3. Aluminum (e.g., 6061-T6)
Key Properties:
Aluminum is lightweight, corrosion-resistant, and has good thermal conductivity. It typically withstands temperatures up to 150°C (302°F) and is suitable for low-pressure applications.
Pros & Cons:
The key advantage of aluminum is its lightweight nature, which can reduce shipping costs and ease installation. However, it is less durable than steel and may not be suitable for high-stress applications.
Impact on Application:
Aluminum is ideal for parts that require a balance between weight and strength, such as panels and frames.
Considerations for International Buyers:
Buyers should check for compliance with local aluminum standards and consider the implications of aluminum’s lower strength in high-stress environments.
4. Polycarbonate
Key Properties:
Polycarbonate is a high-performance plastic known for its impact resistance and transparency. It can withstand temperatures ranging from -40°C to 120°C (-40°F to 248°F).
Pros & Cons:
Polycarbonate is lightweight and offers excellent visibility, making it ideal for display panels. However, it may not be as durable as metals and can be susceptible to scratching.
Impact on Application:
It is commonly used for protective covers and windows in the vending machine, providing visibility while protecting internal components.
Considerations for International Buyers:
International buyers should ensure that polycarbonate used complies with safety and environmental regulations in their respective regions, particularly concerning UV resistance and impact standards.
Summary Table
Material | Typical Use Case for carvanna car vending machine | Key Advantage | Key Disadvantage/Limitation | Relative Cost (Low/Med/High) |
---|---|---|---|---|
Stainless Steel (e.g., AISI 304) | Structural components, external casing | Excellent corrosion resistance | High cost, difficult to machine | High |
Carbon Steel (e.g., A36) | Structural supports, non-corrosive parts | Cost-effective, easy to fabricate | Prone to corrosion without treatment | Low |
Aluminum (e.g., 6061-T6) | Panels, frames, lightweight components | Lightweight, good thermal conductivity | Less durable than steel | Medium |
Polycarbonate | Protective covers, display panels | Lightweight, excellent visibility | Susceptible to scratching | Medium |
This material selection guide provides valuable insights for international B2B buyers, allowing them to make informed decisions tailored to their specific operational environments and compliance requirements.
In-depth Look: Manufacturing Processes and Quality Assurance for carvanna car vending machine
The manufacturing processes and quality assurance (QA) protocols for Carvana’s car vending machines are designed to ensure high-quality products that meet international standards. Understanding these processes is crucial for B2B buyers, particularly those from Africa, South America, the Middle East, and Europe, as they navigate supplier selection and quality verification.
Manufacturing Processes
Material Preparation
The manufacturing of Carvana’s car vending machines begins with careful material selection. Key materials include:
- Steel: Used for structural integrity, ensuring the machine can support the weight of vehicles and withstand environmental factors.
- Glass: High-strength tempered glass is utilized for transparency and security.
- Electronic Components: These are essential for the machine’s operation, including sensors, payment systems, and digital displays.
Before production, materials undergo rigorous inspections to confirm their quality and compliance with specifications.
Forming
The forming process involves several techniques to shape materials into the required components of the vending machine:
- Laser Cutting: This technology provides precision in cutting metal sheets, ensuring accurate dimensions for structural parts.
- CNC Machining: Computer Numerical Control (CNC) machines are used for creating intricate designs and features in metal and plastic components.
- Bending and Forming: Metal sheets are bent and shaped using hydraulic presses to create the frame and housing of the machine.
These techniques ensure that each component is produced to exact specifications, minimizing discrepancies that could affect the overall functionality.
Assembly
Once individual components are formed, assembly takes place in a systematic manner:
- Sub-assembly: Components are first grouped into sub-assemblies (e.g., electronic systems, structural frameworks) before final assembly. This stage allows for easier troubleshooting and quality checks.
- Integration: Sub-assemblies are integrated into the main structure, including the installation of electronic systems and safety features.
- Final Assembly: The complete machine is assembled, ensuring that all parts fit correctly and function as intended.
Finishing
The finishing stage enhances both aesthetics and durability:
- Painting and Coating: The exterior is coated with weather-resistant paint to protect against the elements and provide visual appeal.
- Quality Checks: Each machine undergoes a final inspection to ensure all components are functioning correctly before shipping.
Quality Assurance
Quality assurance is critical in maintaining the standards expected from Carvana’s vending machines. The following are key aspects of their QA processes:
International Standards
Carvana adheres to several international quality standards, including:
- ISO 9001: This standard ensures that the manufacturing process is consistent and meets customer requirements.
- CE Marking: This indicates compliance with European health, safety, and environmental protection standards.
- API Standards: Relevant for components that may interact with fuel or other automotive fluids.
These certifications are essential for B2B buyers, as they signify a commitment to quality and safety.
Quality Control Checkpoints
Quality control is integrated into every stage of the manufacturing process through various checkpoints:
- Incoming Quality Control (IQC): Raw materials and components are inspected upon arrival to ensure they meet specified standards.
- In-Process Quality Control (IPQC): Regular inspections during the manufacturing process help catch any defects early on, reducing waste and rework.
- Final Quality Control (FQC): Before shipment, each vending machine undergoes a comprehensive inspection to verify that all features are operational and meet quality standards.
Common Testing Methods
To ensure reliability and performance, several testing methods are employed:
- Functional Testing: Verifies that all electronic components work correctly.
- Durability Testing: Machines are subjected to stress tests to ensure they can withstand real-world conditions.
- Safety Testing: Compliance with safety standards is assessed, including electrical safety and structural integrity.
Verifying Supplier Quality
B2B buyers should adopt a proactive approach to verify supplier quality:
- Supplier Audits: Conduct regular audits of suppliers to assess compliance with quality standards and manufacturing processes.
- Quality Reports: Request detailed quality reports that outline inspection results and compliance with international standards.
- Third-Party Inspections: Engage independent inspection services to validate the quality of products before shipment.
Quality Control Nuances for International Buyers
When purchasing from international suppliers, especially in regions like Africa, South America, the Middle East, and Europe, buyers should be aware of specific nuances:
- Regulatory Compliance: Ensure that the supplier understands and complies with local regulations and standards in the buyer’s region.
- Cultural Differences: Be mindful of communication styles and business practices that may differ across cultures, which could impact quality assurance processes.
- Shipping and Logistics: Consider the logistics of transporting large machinery and the potential for damage during transit. Choose suppliers with robust packaging and handling protocols.
By understanding these manufacturing processes and quality assurance measures, B2B buyers can make informed decisions when selecting suppliers for Carvana car vending machines, ensuring they invest in high-quality, reliable products that meet international standards.
Related Video: Mercedes MANUFACTURING Process 🚘 Car Factory Assembly Line
Comprehensive Cost and Pricing Analysis for carvanna car vending machine Sourcing
The cost structure for sourcing Carvana car vending machines involves multiple components that must be carefully analyzed by international B2B buyers. Understanding these components and their interplay can lead to more informed purchasing decisions, especially for buyers from Africa, South America, the Middle East, and Europe.
Cost Components
-
Materials
– The primary materials for Carvana vending machines include steel, glass, and advanced electronic components. Prices can fluctuate based on market conditions, tariffs, and local availability. Buyers should assess the current market rates and consider sourcing materials locally where feasible to reduce costs. -
Labor
– Labor costs vary significantly across regions. For instance, labor might be cheaper in parts of South America compared to Europe. Understanding local labor regulations and wage standards is crucial for accurate cost forecasting. -
Manufacturing Overhead
– This encompasses utilities, rent, and administrative costs associated with the production facility. Buyers should inquire about the manufacturer’s overhead costs, as they can impact the final pricing of the vending machines. -
Tooling
– Custom tooling may be required for specific vending machine designs. This cost is often a one-time expense but should be factored into the total cost of ownership. -
Quality Control (QC)
– Ensuring product quality through rigorous QC processes can add to the cost. Buyers should prioritize suppliers with strong QC protocols to minimize future maintenance and warranty claims. -
Logistics
– Shipping costs depend on the origin and destination of the machines. Incoterms also play a crucial role in determining who bears the shipping costs, which can affect overall pricing. Buyers should consider logistics costs in their total cost assessments. -
Margin
– Suppliers typically add a margin to their costs, which can vary widely. Buyers should evaluate multiple suppliers to gauge acceptable margins and negotiate terms accordingly.
Price Influencers
-
Volume/MOQ
– Minimum Order Quantities (MOQs) can significantly affect pricing. Higher volumes usually lead to lower per-unit costs. Buyers should assess their needs and negotiate MOQs that align with their purchasing capabilities. -
Specifications/Customization
– Custom features or specifications can increase costs. Buyers should define their requirements clearly to avoid unexpected expenses during production. -
Materials and Quality
– The choice of materials directly influences both durability and pricing. Certifications for quality standards can also impact costs. Buyers should ensure that they are not compromising on quality for price. -
Supplier Factors
– Supplier reliability and reputation can influence pricing. Established suppliers may charge a premium, but they often provide better quality assurance and customer service. -
Incoterms
– Understanding Incoterms is vital for international transactions. They determine the responsibilities of buyers and sellers regarding shipping, insurance, and tariffs. Familiarity with these terms can help avoid hidden costs.
Buyer Tips
-
Negotiation: Leverage the insights gained from analyzing cost components to negotiate better pricing. Being informed about market rates can empower buyers during discussions.
-
Cost-Efficiency: Evaluate the total cost of ownership (TCO) rather than just the initial purchase price. Consider maintenance, potential downtime, and operational efficiency in the long run.
-
Pricing Nuances: International buyers should be aware of currency fluctuations, import duties, and local taxes that may affect the overall cost. Conduct thorough due diligence before finalizing agreements.
Disclaimer
Prices and costs mentioned in this analysis are indicative and subject to change based on market conditions, supplier negotiations, and specific buyer requirements. Always conduct a comprehensive market analysis to obtain the most accurate pricing for your sourcing needs.
Spotlight on Potential carvanna car vending machine Manufacturers and Suppliers
This section offers a look at a few manufacturers active in the ‘carvanna car vending machine’ market. This is a representative sample for illustrative purposes; B2B buyers must conduct their own extensive due diligence before any engagement. Information is synthesized from public sources and general industry knowledge.
Essential Technical Properties and Trade Terminology for carvanna car vending machine
Key Technical Properties of Carvana Car Vending Machines
Understanding the technical specifications of Carvana car vending machines is crucial for international B2B buyers, particularly those in Africa, South America, the Middle East, and Europe. Below are critical specifications that impact procurement decisions:
-
Material Grade
– Definition: The quality and type of materials used in the construction of the vending machine, including steel, aluminum, and glass.
– Importance: High-grade materials ensure durability and resistance to environmental factors, which is essential for machines operating in varying climates. This affects long-term maintenance costs and operational efficiency. -
Load Capacity
– Definition: The maximum weight the vending machine can safely hold and dispense.
– Importance: A higher load capacity allows for a wider variety of vehicle models to be stored and dispensed. This is particularly relevant in markets with diverse vehicle preferences, enabling better customer service and inventory management. -
Power Consumption
– Definition: The amount of electrical energy the machine requires to operate, typically measured in kilowatts (kW).
– Importance: Energy-efficient models reduce operational costs and align with sustainability initiatives, making them more attractive to environmentally-conscious buyers and investors. -
User Interface Technology
– Definition: The software and hardware systems that facilitate customer interaction with the vending machine, including touchscreen displays and mobile app integration.
– Importance: An intuitive user interface enhances customer experience, which is crucial in competitive markets. A seamless transaction process can lead to higher sales and customer satisfaction rates. -
Safety Features
– Definition: Mechanisms and protocols designed to protect users and vehicles during operation, such as emergency stop buttons, surveillance cameras, and fire safety systems.
– Importance: Safety is paramount in B2B transactions, especially when dealing with high-value items like cars. Ensuring compliance with local regulations and international safety standards can mitigate liability and enhance brand reputation. -
Dimensions and Footprint
– Definition: The physical size of the vending machine, including height, width, and depth.
– Importance: Understanding the dimensions helps buyers assess space requirements for installation. In densely populated areas or smaller dealerships, optimizing space is critical to operational efficiency.
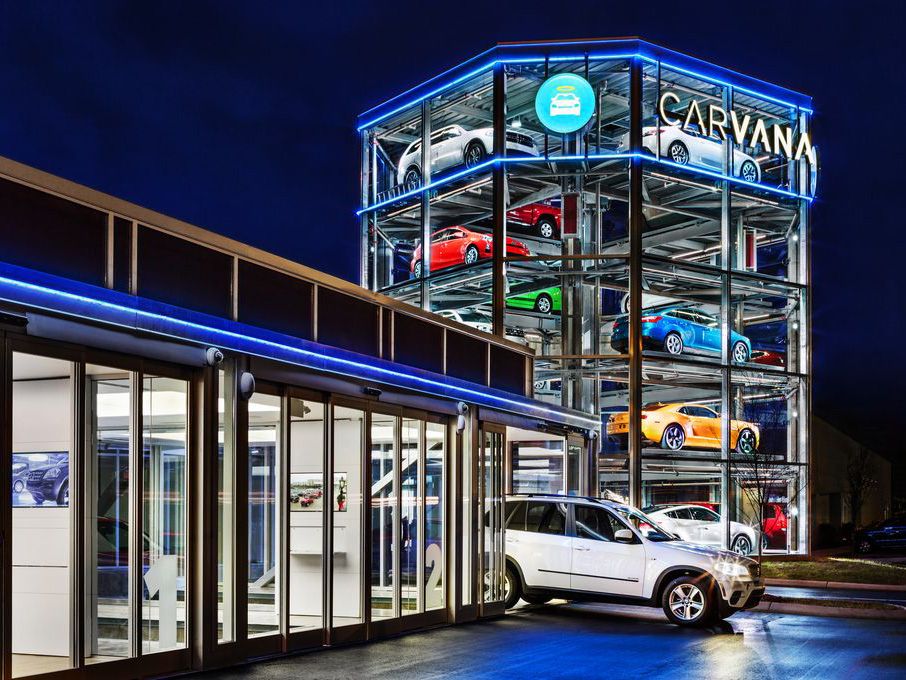
Illustrative Image (Source: Google Search)
Common Trade Terminology
Familiarity with industry jargon is essential for effective communication and negotiation in B2B transactions. Here are some common terms related to Carvana car vending machines:
-
OEM (Original Equipment Manufacturer)
– Definition: A company that produces parts or equipment that may be marketed by another manufacturer.
– Relevance: Buyers often seek OEM parts for repairs or replacements to ensure compatibility and quality. -
MOQ (Minimum Order Quantity)
– Definition: The smallest quantity of a product that a supplier is willing to sell.
– Relevance: Understanding MOQ helps buyers manage inventory levels and negotiate better pricing. It is particularly important for small businesses looking to enter the market. -
RFQ (Request for Quotation)
– Definition: A document used to solicit price quotes from suppliers for specific products or services.
– Relevance: Submitting an RFQ allows buyers to compare prices and terms from multiple vendors, ensuring they make informed purchasing decisions. -
Incoterms (International Commercial Terms)
– Definition: A series of pre-defined commercial terms published by the International Chamber of Commerce (ICC) that outline the responsibilities of buyers and sellers in international transactions.
– Relevance: Knowledge of Incoterms helps buyers understand shipping costs, insurance, and liability during the transport of vending machines, which is critical for budgeting and risk management. -
Lead Time
– Definition: The time taken from placing an order to receiving the goods.
– Relevance: Understanding lead times is essential for planning and inventory management, especially in markets where demand can fluctuate rapidly. -
Warranty Terms
– Definition: The conditions under which a product is guaranteed against defects or failures.
– Relevance: Buyers should carefully review warranty terms to understand their rights and responsibilities, which can significantly impact long-term operational costs and risk mitigation strategies.
By comprehensively understanding these technical properties and trade terminologies, B2B buyers can make informed decisions that align with their business goals and market demands.
Navigating Market Dynamics, Sourcing Trends, and Sustainability in the carvanna car vending machine Sector
In the rapidly evolving automotive sector, the Carvana car vending machine concept has emerged as a significant innovation in vehicle sales and distribution. This section explores the market dynamics, sourcing trends, and sustainability considerations crucial for international B2B buyers, particularly from Africa, South America, the Middle East, and Europe.
Market Overview & Key Trends
The global automotive market is currently experiencing a shift towards digitization and automation, driven by technological advancements and changing consumer preferences. Carvana, a pioneer in the car vending machine model, leverages digital platforms to streamline the car buying process, making it more efficient and user-friendly. This trend is particularly relevant for B2B buyers in emerging markets such as Kenya and Brazil, where digital penetration is increasing rapidly.
Key trends influencing this market include:
- Increased Demand for Contactless Transactions: Post-pandemic, buyers favor touchless experiences. Car vending machines provide an automated, safe way to purchase vehicles without direct interaction.
- Integration of AI and Big Data: These technologies enhance inventory management and customer experience, allowing buyers to predict trends and optimize their purchasing strategies.
- Expansion of Online Marketplaces: As e-commerce continues to grow, companies are increasingly investing in online platforms to reach broader audiences, especially in regions with lower physical dealership presence.
International B2B buyers should stay informed about these trends to effectively navigate the evolving landscape, ensuring they align their sourcing strategies with market demands.
Sustainability & Ethical Sourcing in B2B
Sustainability has become a cornerstone of modern business practices, and the automotive sector is no exception. The environmental impact of vehicle production and disposal is significant, making ethical sourcing a critical concern for B2B buyers.
Key considerations include:
- Sustainable Materials: Increasingly, manufacturers are adopting recycled and eco-friendly materials in vehicle production, which not only reduces environmental impact but also appeals to environmentally conscious consumers.
- Green Certifications: B2B buyers should seek suppliers who hold recognized environmental certifications, such as ISO 14001 or LEED, to ensure compliance with sustainability standards.
- Carbon Footprint Reduction: Buyers can enhance their brand reputation by partnering with suppliers committed to reducing their carbon footprints through energy-efficient practices and renewable energy sources.
By prioritizing sustainability and ethical sourcing, international buyers can not only contribute to environmental stewardship but also meet the growing demand for responsible business practices among consumers.
Brief Evolution/History
The concept of car vending machines originated in the United States, with Carvana leading the charge in 2013. This innovative approach to car sales has disrupted traditional dealership models by offering a unique, technology-driven alternative. The vending machine model simplifies the car buying process, allowing customers to select and purchase vehicles online and retrieve them from automated vending facilities. This evolution reflects broader trends in consumer behavior towards digital solutions and the demand for more efficient and transparent purchasing experiences.
In conclusion, the Carvana car vending machine sector represents a dynamic intersection of technology, sustainability, and evolving consumer preferences. For international B2B buyers, understanding these trends and prioritizing ethical sourcing will be key to capitalizing on opportunities in this innovative market.
Related Video: Picking Up My New Car at The Carvana Vending Machine!
Frequently Asked Questions (FAQs) for B2B Buyers of carvanna car vending machine
-
What should I consider when vetting suppliers for Carvana car vending machines?
When vetting suppliers, prioritize their track record in manufacturing and supplying car vending machines. Check for certifications such as ISO 9001 for quality management and safety standards. Request references from previous clients, especially those in your region, to assess reliability. Additionally, evaluate their customer support, warranty terms, and after-sales service to ensure they can assist you post-purchase. -
Can I customize the Carvana car vending machine for my market?
Yes, many suppliers offer customization options to cater to local market needs. This may include branding, size adjustments, and technology enhancements, such as payment systems compatible with local currencies. Discuss your specific requirements with potential suppliers and request prototypes or design mockups to ensure the final product meets your expectations. -
What are the minimum order quantities (MOQ) and lead times for purchasing a Carvana car vending machine?
MOQs can vary significantly based on the supplier and your location. Some suppliers may require a minimum order of one unit, while others may set a higher threshold. Lead times typically range from 8 to 16 weeks, depending on customization and manufacturing schedules. It’s advisable to clarify these details upfront to plan your inventory and financing accordingly. -
What payment options are available when sourcing Carvana car vending machines?
Payment options vary by supplier but often include wire transfers, letters of credit, and payment through escrow services for added security. Some suppliers may offer financing options or installment plans for larger orders. Ensure that the payment terms align with your budget and financial strategy, and consider negotiating favorable terms that mitigate risk. -
How can I ensure quality assurance (QA) and certifications for the Carvana car vending machines?
Request documentation of quality assurance processes from suppliers, including testing procedures and quality control measures. Look for relevant certifications such as CE marking for safety compliance in Europe or other local certifications applicable in your region. Establish a clear QA protocol that includes inspections during production and before shipment to ensure adherence to your standards. -
What logistics considerations should I keep in mind when importing a Carvana car vending machine?
Logistics can be complex when importing machinery. Consider the shipping method (air vs. sea), which impacts cost and delivery time. Work with suppliers who have experience in international shipping to navigate customs regulations and tariffs. Additionally, ensure that you have a reliable logistics partner to handle the transportation and installation of the vending machines at your location. -
How can I handle disputes with suppliers regarding the Carvana car vending machines?
To minimize disputes, establish clear contracts detailing product specifications, delivery timelines, and payment terms. Include a dispute resolution clause outlining steps for mediation or arbitration. If issues arise, communicate promptly with the supplier to address concerns and seek a resolution. Keeping documentation of all transactions and communications will support your position in any dispute. -
What ongoing support can I expect from suppliers after purchasing a Carvana car vending machine?
Most reputable suppliers offer ongoing support, including maintenance services, software updates, and troubleshooting assistance. Verify the terms of their after-sales service, including response times for support requests and availability of spare parts. Establishing a solid relationship with your supplier can also facilitate better support and quicker resolutions to any operational challenges you may encounter.
Strategic Sourcing Conclusion and Outlook for carvanna car vending machine
The Carvana car vending machine presents a transformative opportunity for international B2B buyers, particularly in emerging markets across Africa, South America, the Middle East, and Europe. By embracing strategic sourcing, companies can capitalize on the efficiency, transparency, and customer engagement that this innovative solution offers. Key takeaways include the importance of understanding local market dynamics, leveraging technology for operational excellence, and ensuring compliance with regional regulations.
Investing in Carvana vending machines not only enhances the customer experience but also streamlines inventory management and reduces operational costs. For businesses in regions like Kenya and Thailand, adopting such technology can significantly improve their competitive edge in the automotive sector.
Looking ahead, the integration of AI and data analytics into vending machine operations will further enhance decision-making and customer service. International B2B buyers are encouraged to explore partnerships with Carvana to leverage these advancements. The future of automotive retail is here, and it’s time to take decisive action to stay ahead of the curve. Embrace the change and elevate your business to new heights with Carvana’s innovative solutions.