Your Ultimate Guide to Sourcing Can Drink Vending Machine
Guide to Can Drink Vending Machine
- Introduction: Navigating the Global Market for can drink vending machine
- Understanding can drink vending machine Types and Variations
- Key Industrial Applications of can drink vending machine
- Strategic Material Selection Guide for can drink vending machine
- In-depth Look: Manufacturing Processes and Quality Assurance for can drink vending machine
- Comprehensive Cost and Pricing Analysis for can drink vending machine Sourcing
- Spotlight on Potential can drink vending machine Manufacturers and Suppliers
- Essential Technical Properties and Trade Terminology for can drink vending machine
- Navigating Market Dynamics, Sourcing Trends, and Sustainability in the can drink vending machine Sector
- Frequently Asked Questions (FAQs) for B2B Buyers of can drink vending machine
- Strategic Sourcing Conclusion and Outlook for can drink vending machine
Introduction: Navigating the Global Market for can drink vending machine
The global market for can drink vending machines is witnessing unprecedented growth, fueled by the surge in urbanization and the demand for convenient, on-the-go beverage options. These automated systems not only meet consumer needs but also offer lucrative opportunities for international B2B buyers looking to capitalize on evolving consumer preferences. As businesses and entrepreneurs from Africa, South America, the Middle East, and Europe seek to enhance their product offerings, understanding the dynamics of the can drink vending machine market becomes essential.
This comprehensive guide serves as a valuable resource, covering critical aspects such as types of vending machines, materials used in manufacturing, quality control measures, and sourcing reliable suppliers. Additionally, it delves into cost considerations, market trends, and frequently asked questions, equipping buyers with actionable insights to make informed sourcing decisions.
With a focus on empowering B2B buyers, this guide addresses the specific needs of international markets, providing tailored strategies to navigate the complexities of vending machine procurement. By leveraging this knowledge, businesses can optimize their investments, streamline operations, and enhance customer satisfaction, ultimately positioning themselves for success in this competitive landscape. Whether you are a seasoned player or a newcomer, understanding the intricacies of can drink vending machines is your key to unlocking new opportunities in the global market.
Understanding can drink vending machine Types and Variations
Type Name | Key Distinguishing Features | Primary B2B Applications | Brief Pros & Cons for Buyers |
---|---|---|---|
Standard Can Drink Machine | Dispenses standard-sized cans, typically 330ml or 355ml | Offices, schools, public transport hubs | Pros: Simple operation, low maintenance; Cons: Limited to standard can sizes. |
Multi-Product Can Vending Machine | Offers a variety of canned beverages in one unit | Convenience stores, malls, event venues | Pros: Versatile; attracts diverse customer base; Cons: Higher initial investment. |
Smart Can Vending Machine | Features IoT connectivity for inventory management and payment options | Corporate offices, tech hubs, high-traffic areas | Pros: Real-time data analytics, remote monitoring; Cons: Higher complexity and potential for technical issues. |
Compact Can Vending Machine | Smaller footprint, ideal for limited space | Small offices, gyms, residential buildings | Pros: Space-efficient, cost-effective; Cons: Limited product range. |
Refrigerated Can Drink Machine | Maintains optimal temperature for beverages | Outdoor events, festivals, stadiums | Pros: Enhances product appeal; Cons: Higher energy consumption. |
Standard Can Drink Machine
The Standard Can Drink Machine is designed for dispensing conventional can sizes, making it a staple in many environments. It is ideal for offices, schools, and public transport hubs where quick access to beverages is essential. When considering this type, buyers should evaluate the machine’s capacity and reliability, as consistent performance is crucial in high-traffic areas. While maintenance is generally low, the limitation to standard can sizes may restrict beverage variety.
Multi-Product Can Vending Machine
The Multi-Product Can Vending Machine offers a diverse selection of canned beverages, catering to various tastes and preferences. This versatility makes it suitable for convenience stores, malls, and event venues. Buyers should focus on the machine’s ability to handle different can types and the ease of restocking. Although the initial investment is higher, the potential for increased sales through diverse offerings can justify the cost.
Smart Can Vending Machine
Equipped with IoT technology, the Smart Can Vending Machine allows for enhanced inventory management and payment options, making it a forward-thinking choice for corporate offices and tech hubs. These machines can provide real-time data on stock levels and sales trends, aiding in strategic decision-making. However, buyers must consider the complexity of these systems and the potential for technical issues. The benefits of improved operational efficiency can outweigh these challenges.
Compact Can Vending Machine
The Compact Can Vending Machine is designed for environments with limited space, such as small offices or gyms. Its smaller footprint makes it a cost-effective solution for buyers looking to provide beverage options without requiring extensive floor space. While these machines are typically less expensive, they often have a limited product range, which could restrict customer choice. Buyers should assess space requirements and expected beverage demand before purchasing.
Refrigerated Can Drink Machine
The Refrigerated Can Drink Machine is essential for maintaining the ideal temperature of beverages, particularly in outdoor settings like events and festivals. This type attracts customers looking for refreshingly cold drinks, making it suitable for high-traffic venues such as stadiums. However, the energy consumption of these machines can be significant, so buyers should consider operational costs alongside the potential for increased sales from chilled products.
Related Video: Cheap vs Expensive Drink Vending Machine
Key Industrial Applications of can drink vending machine
Industry/Sector | Specific Application of can drink vending machine | Value/Benefit for the Business | Key Sourcing Considerations for this Application |
---|---|---|---|
Hospitality | Hotel lobbies and guest areas | Enhances guest experience and convenience | Reliable supply chain for beverage inventory, machine durability |
Corporate Offices | Break rooms and common areas | Increases employee satisfaction and productivity | Energy-efficient models, payment system compatibility |
Educational Institutions | School campuses and university facilities | Provides accessible beverage options for students | Compliance with health regulations, variety of drink options |
Transportation Hubs | Airports and train stations | Reduces wait times and enhances customer service | High-capacity machines, robust payment systems |
Retail | Shopping malls and supermarkets | Boosts impulse purchases and customer engagement | Customizable branding options, machine maintenance support |
Hospitality
In the hospitality industry, can drink vending machines are strategically placed in hotel lobbies and guest areas to enhance the guest experience. By providing a range of beverage options, hotels can cater to the diverse preferences of their clientele. This solution not only increases convenience for guests but also drives additional revenue for the hotel. International buyers should prioritize sourcing machines that are durable and capable of handling high foot traffic, while ensuring a reliable supply chain for beverage inventory.
Corporate Offices
Corporate offices utilize can drink vending machines in break rooms and common areas to improve employee satisfaction. These machines offer quick access to refreshing beverages, which can boost morale and productivity. For B2B buyers, selecting energy-efficient vending machines is crucial to reduce operational costs. Additionally, compatibility with various payment systems, including contactless options, can enhance the user experience and encourage more frequent purchases.
Educational Institutions
Schools and universities benefit from can drink vending machines on their campuses by providing students with convenient access to beverages throughout the day. This can help meet the hydration needs of students and promote healthier choices. Buyers in this sector must consider compliance with health regulations and the need for a variety of drink options to cater to different age groups. Machines should also be designed to withstand heavy usage and be easily maintained.
Transportation Hubs
In transportation hubs like airports and train stations, can drink vending machines play a vital role in reducing wait times and enhancing customer service. Travelers appreciate the convenience of grabbing a quick drink while on the go. B2B buyers in this industry should focus on high-capacity machines that can handle increased demand during peak travel times. Robust payment systems and the ability to stock a variety of beverages are essential to meet diverse traveler preferences.
Retail
In retail environments such as shopping malls and supermarkets, can drink vending machines can significantly boost impulse purchases and customer engagement. They serve as convenient refreshment options for shoppers, encouraging longer visits and increased spending. Buyers should look for customizable branding options to align the vending machine’s appearance with their store’s image. Additionally, ensuring ongoing maintenance support for these machines is crucial to minimize downtime and maintain customer satisfaction.
Related Video: How to Start a Vending Machine Business, Cost, Tips, How Much You Make
Strategic Material Selection Guide for can drink vending machine
When selecting materials for can drink vending machines, it is crucial to consider properties that affect performance, durability, and compliance with international standards. Below is an analysis of four common materials used in the manufacturing of these machines, focusing on their key properties, advantages, disadvantages, and specific considerations for international B2B buyers.
Stainless Steel
Key Properties: Stainless steel is known for its excellent corrosion resistance, high strength, and ability to withstand temperature variations. It typically has a pressure rating suitable for various operational environments.
Pros & Cons: The durability of stainless steel makes it ideal for vending machines that are exposed to outdoor elements or high-traffic areas. However, it is relatively expensive compared to other materials, which could impact the overall cost of the vending machine. Manufacturing complexity is moderate, as it requires specialized welding techniques.
Impact on Application: Stainless steel is compatible with a wide range of beverages, including carbonated drinks, juices, and teas, due to its inert nature. It also meets hygiene standards, which is critical for food-related applications.
Considerations for International Buyers: Buyers from regions like Africa, South America, and the Middle East should ensure that the stainless steel used complies with local food safety regulations. Common standards include ASTM A240 and EN 10088. Additionally, the cost may vary significantly based on local market conditions.
Powder-Coated Steel
Key Properties: Powder-coated steel offers good corrosion resistance and is available in various colors and finishes. It has a moderate temperature rating and can withstand typical operational pressures.
Pros & Cons: The aesthetic appeal of powder-coated steel makes it a popular choice for vending machines in public spaces. It is generally less expensive than stainless steel but may not be as durable in harsh environments. The manufacturing process involves applying a powder coating, which can add complexity.
Impact on Application: This material is suitable for indoor applications and can handle a variety of drinks. However, it may not be ideal for outdoor use due to potential chipping and fading over time.
Considerations for International Buyers: Compliance with local environmental regulations regarding coatings is essential. Buyers should check for standards such as ASTM D3359 for adhesion and ASTM B117 for corrosion resistance, especially in humid climates.
Aluminum
Key Properties: Aluminum is lightweight, corrosion-resistant, and has good thermal conductivity. It typically has a lower pressure rating compared to steel but is sufficient for many vending machine applications.
Pros & Cons: The lightweight nature of aluminum makes it easy to transport and install, reducing shipping costs. However, it is less durable than stainless steel and can be prone to dents and scratches. Manufacturing processes for aluminum are generally simpler, allowing for cost-effective production.
Impact on Application: Aluminum is suitable for a variety of beverages, but care must be taken with acidic drinks, which may react with the metal. Its lightweight nature can be advantageous in high-traffic areas.
Considerations for International Buyers: Buyers should ensure that the aluminum used meets international standards such as ASTM B221 for extrusions. In regions with high humidity, additional protective coatings may be required to enhance durability.
Composite Materials
Key Properties: Composite materials combine various substances to enhance properties such as strength, weight, and corrosion resistance. They can be engineered for specific performance characteristics.
Pros & Cons: Composites can offer excellent durability and resistance to environmental factors while being lightweight. However, they can be more expensive to produce and may require specialized manufacturing techniques.
Impact on Application: Composites are versatile and can be designed to handle various beverages while providing insulation properties. Their resistance to corrosion makes them suitable for both indoor and outdoor applications.
Considerations for International Buyers: It is crucial to verify that composite materials comply with relevant safety and environmental standards. Buyers should look for certifications like ISO 9001 for quality management systems and ensure compatibility with local regulations.
Material | Typical Use Case for can drink vending machine | Key Advantage | Key Disadvantage/Limitation | Relative Cost (Low/Med/High) |
---|---|---|---|---|
Stainless Steel | High-traffic outdoor vending machines | Excellent corrosion resistance | Higher cost compared to other materials | High |
Powder-Coated Steel | Indoor vending machines in public spaces | Aesthetic appeal and customization | Less durable in harsh environments | Medium |
Aluminum | Lightweight vending machines for easy transport | Lightweight and cost-effective | Prone to dents and scratches | Medium |
Composite Materials | Versatile applications for various environments | Enhanced durability and insulation | Higher production costs | High |
This strategic material selection guide provides valuable insights for international B2B buyers looking to invest in can drink vending machines, ensuring they make informed decisions that align with their operational needs and market conditions.
In-depth Look: Manufacturing Processes and Quality Assurance for can drink vending machine
The manufacturing process for can drink vending machines involves several critical stages, each requiring precise execution and quality control to ensure the final product meets the highest standards. Understanding these processes and quality assurance measures can empower B2B buyers, especially those operating in regions such as Africa, South America, the Middle East, and Europe, to make informed purchasing decisions.
Manufacturing Process
Material Preparation
The initial phase of manufacturing involves selecting high-quality materials that will ensure durability and functionality. Common materials used include stainless steel for the chassis due to its resistance to corrosion and wear, and plastic components for internal mechanisms. Buyers should ensure that suppliers adhere to environmental regulations like RoHS and REACH, which dictate the safe use of certain materials.
Forming
The forming process is crucial for shaping the components of the vending machine. This typically involves techniques such as CNC machining and laser cutting. These methods provide precision and allow for complex designs that enhance functionality, such as the integration of advanced cooling systems and user interfaces. For B2B buyers, understanding the forming capabilities of a supplier can help gauge the quality and reliability of the machines.
Assembly
Once components are formed, they undergo assembly. This stage is often modular, with separate teams handling refrigeration units, dispensing mechanisms, and electronic systems. Automated assembly lines are frequently used to enhance efficiency and reduce human error. During this stage, it is essential to integrate IoT sensors for real-time monitoring and predictive maintenance. Buyers should inquire about the assembly process to ensure that it aligns with best practices in quality control.
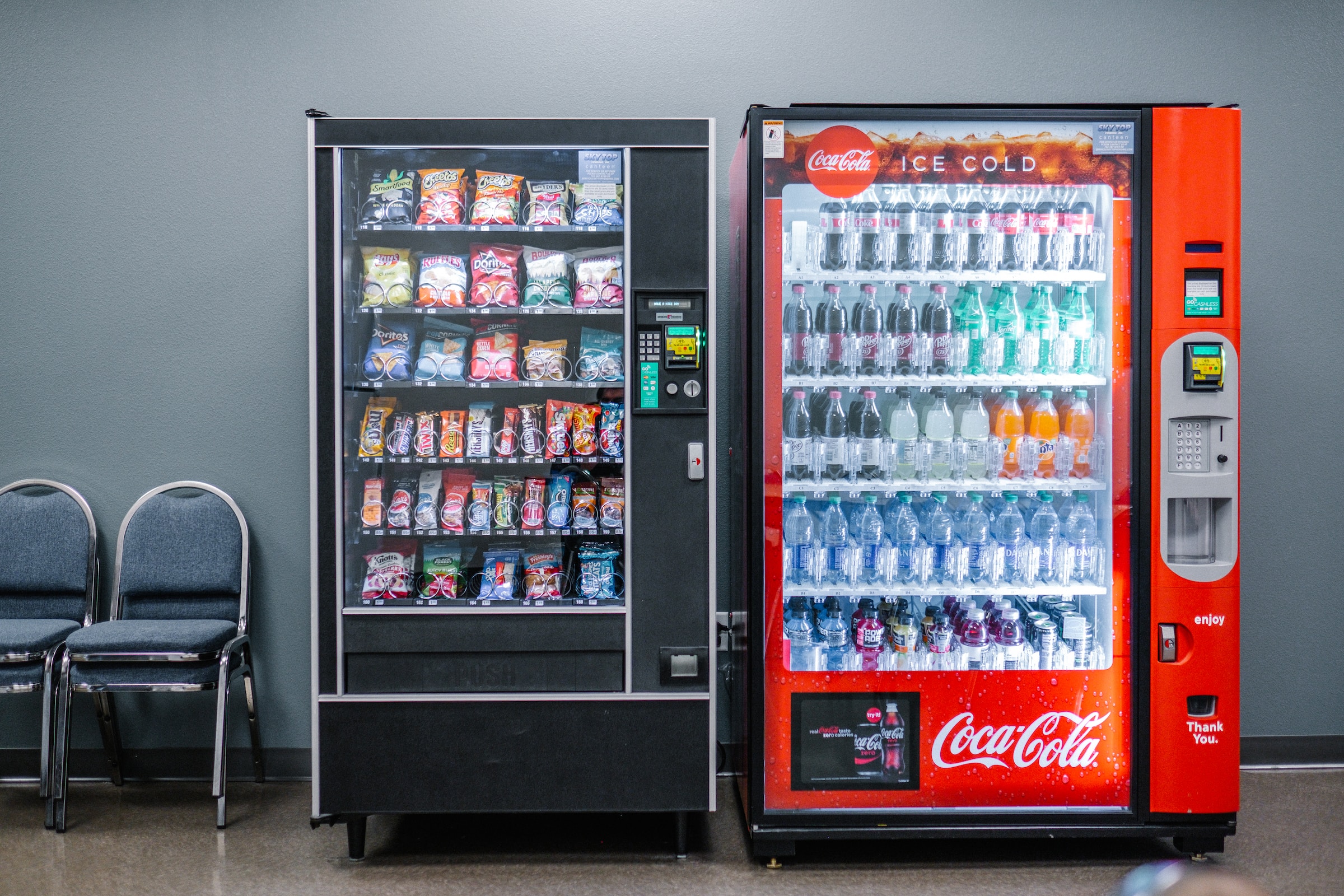
Illustrative Image (Source: Google Search)
Finishing
The finishing process includes surface treatment, painting, and installation of user interfaces. This is where aesthetics meet functionality. Powder coating is a popular finishing method that provides a durable and visually appealing surface. Additionally, quality checks should be conducted at this stage to ensure that all components are functioning correctly and meet design specifications.
Quality Control
Quality control (QC) is vital throughout the manufacturing process to ensure that the can drink vending machines meet international standards and customer expectations.
International Standards
B2B buyers should look for suppliers that comply with relevant international standards such as:
– ISO 9001: Focuses on quality management systems and continuous improvement.
– CE Marking: Indicates compliance with European health, safety, and environmental protection standards.
– UL Certification: Ensures safety standards for electrical components.
These certifications are critical for buyers in regions like Europe, where compliance is mandatory for market entry.
Quality Control Checkpoints
Quality control checkpoints are strategically placed throughout the manufacturing process:
- Incoming Quality Control (IQC): Inspecting raw materials upon receipt to ensure they meet specifications.
- In-Process Quality Control (IPQC): Conducting checks during manufacturing to identify defects early.
- Final Quality Control (FQC): A comprehensive assessment of the finished product before shipping.
These checkpoints help maintain product integrity and reduce the likelihood of defects reaching the market.
Common Testing Methods
Testing methods employed in quality assurance may include:
– Mechanical testing: Assessing the durability and functionality of components.
– Thermal performance testing: Evaluating the efficiency of refrigeration units.
– Electrical safety testing: Ensuring compliance with safety regulations for electrical components.
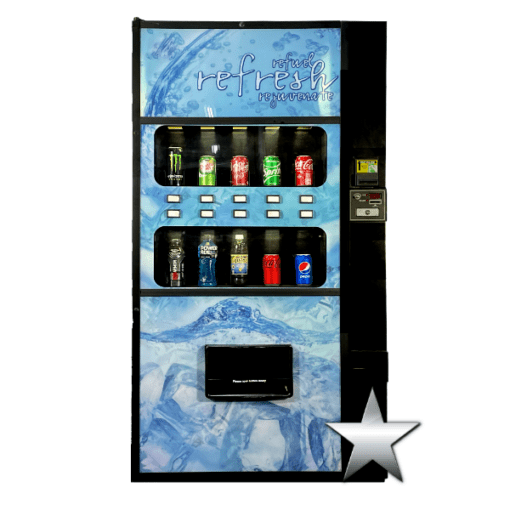
Illustrative Image (Source: Google Search)
B2B buyers should request documentation of these tests to verify quality standards.
Verifying Supplier Quality Control
To ensure that suppliers adhere to high-quality standards, B2B buyers can implement several verification strategies:
- Audits: Conducting regular audits of supplier facilities to assess compliance with quality standards and manufacturing processes.
- Reports: Requesting detailed quality reports, including test results and inspection records, can provide insights into a supplier’s commitment to quality.
- Third-party Inspection: Engaging independent inspectors to evaluate manufacturing practices and product quality can offer an unbiased view of a supplier’s capabilities.
Quality Control Nuances for International Buyers
International buyers must be aware of specific quality control nuances that may affect their purchasing decisions:
- Regulatory Compliance: Different regions have varying regulations regarding product safety and quality. Buyers from Africa and South America should ensure that suppliers can meet local standards while also adhering to international regulations.
- Cultural Expectations: Understanding cultural expectations around product functionality and aesthetics can influence buyer-supplier relationships. For instance, buyers in Europe may prioritize energy efficiency and eco-friendly materials.
- Supply Chain Transparency: In regions with complex supply chains, transparency regarding sourcing and production processes is crucial. Buyers should seek suppliers that provide clear documentation and traceability of materials.
By understanding the manufacturing processes and quality assurance measures in can drink vending machine production, international B2B buyers can make informed decisions that align with their business goals and market requirements. This thorough approach not only safeguards investments but also enhances the potential for long-term partnerships in the vending machine industry.
Related Video: Awesome Satisfying Manufacturing Machines | Ingenious Tools & Industrial Factory Production Insights
Comprehensive Cost and Pricing Analysis for can drink vending machine Sourcing
Understanding the cost structure and pricing dynamics of can drink vending machines is crucial for international B2B buyers looking to optimize their sourcing strategies. This analysis focuses on the components that contribute to costs, the factors influencing pricing, and actionable tips for buyers across Africa, South America, the Middle East, and Europe.
Cost Components
-
Materials: The choice of materials significantly impacts the overall cost. Common materials include stainless steel for durability and plastics for lighter components. High-quality materials can increase initial costs but may reduce maintenance and replacement expenses.
-
Labor: Labor costs vary widely by region. In countries with lower labor costs, such as those in parts of Africa and South America, the manufacturing cost may be reduced. However, ensure that quality standards are not compromised.
-
Manufacturing Overhead: This includes costs associated with factory operations, utilities, and management. Efficient production processes can help minimize overhead costs, but this often requires investment in technology and training.
-
Tooling: Custom tooling for specific designs can be a significant upfront cost. Buyers should consider the implications of tooling costs on pricing, especially when opting for unique designs or features.
-
Quality Control (QC): Implementing stringent QC measures ensures product reliability but also adds to costs. Investing in quality assurance can prevent costly recalls and enhance brand reputation.
-
Logistics: Shipping and handling costs are critical, particularly for international buyers. Factors such as shipping distance, mode of transport, and local tariffs can significantly influence overall costs.
-
Margin: Manufacturers typically apply a profit margin to cover risks and ensure sustainability. Understanding industry standards for margins can help buyers gauge the fairness of pricing.
Price Influencers
-
Volume/MOQ: Minimum Order Quantities (MOQ) can affect pricing. Larger orders often lead to discounted rates, allowing buyers to negotiate better deals.
-
Specifications/Customization: Custom features or specifications can lead to higher costs. Buyers should assess the necessity of customization against its potential to enhance sales.
-
Materials: The quality and type of materials selected can drastically alter pricing. Sustainable or high-performance materials may command premium prices.
-
Quality/Certifications: Machines that meet international safety and quality certifications may have higher upfront costs but can be more appealing to end-users, potentially justifying the investment.
-
Supplier Factors: The reliability, reputation, and location of suppliers can influence pricing. Established suppliers may offer better terms due to their experience and operational efficiencies.
-
Incoterms: Understanding Incoterms (International Commercial Terms) is vital for cost management in international transactions. They define responsibilities for shipping, insurance, and tariffs, impacting the total landed cost.
Buyer Tips
-
Negotiation: Engage suppliers in discussions about pricing, especially regarding volume discounts and payment terms. Building a long-term relationship can lead to better pricing over time.
-
Cost-Efficiency: Evaluate the Total Cost of Ownership (TCO), which includes purchase price, maintenance, and operational costs. A lower initial price may lead to higher long-term expenses.
-
Pricing Nuances: International buyers should be aware of currency fluctuations, which can affect pricing. Consider hedging strategies or negotiating fixed prices to mitigate risks.
-
Research and Benchmarking: Investigate market prices and competitor offerings to better inform negotiations. Understanding market trends can help buyers make informed decisions.
Disclaimer
Prices can vary significantly based on specific requirements, supplier negotiations, and market conditions. This analysis serves as a guide, and buyers are encouraged to conduct thorough research and obtain multiple quotes to ensure competitive pricing.
Spotlight on Potential can drink vending machine Manufacturers and Suppliers
- (No specific manufacturer data was available or requested for detailed profiling in this section for can drink vending machine.)*
Essential Technical Properties and Trade Terminology for can drink vending machine
Key Technical Properties of Can Drink Vending Machines
Understanding the technical specifications of can drink vending machines is crucial for making informed purchasing decisions. Here are the essential properties to consider:
-
Material Grade: The primary materials used in vending machines, such as stainless steel and high-density plastics, must meet specific grades for durability and corrosion resistance. Stainless steel, for instance, is preferred for its strength and hygiene, which is vital in food and beverage applications. Selecting the right material ensures longevity and reduces maintenance costs.
-
Temperature Range: This specification indicates the operational limits for refrigeration systems within the machine. Can drink vending machines typically operate between 0°C to 4°C to maintain optimal beverage quality. Understanding this range is vital for ensuring product freshness, especially in warmer climates found in regions like Africa and the Middle East.
-
Power Consumption: The energy efficiency of a vending machine is measured in kilowatts (kW). Machines with lower power consumption not only reduce operational costs but also align with sustainability goals. B2B buyers should look for machines with energy-efficient compressors and LED lighting to minimize electricity use.
-
Capacity and Dimensions: The internal capacity, often specified in liters or number of cans, directly impacts how many products can be offered without frequent restocking. Understanding the dimensions is essential for space planning in the intended installation area, whether in a high-traffic office or outdoor public space.
-
User Interface Technology: Modern vending machines often come equipped with touchscreens, mobile payment options, and user-friendly interfaces. These technologies enhance the customer experience and can lead to increased sales. For B2B buyers, investing in advanced user interfaces can differentiate their offerings in competitive markets.
-
Compliance Standards: Vending machines must comply with various safety and health regulations, which can vary by region. Standards such as CE (Europe) or UL (United States) ensure that machines are safe for consumer use. Familiarity with these standards is crucial for buyers to avoid legal issues and ensure product acceptance in their markets.
Common Trade Terms in Vending Machine Procurement
Navigating the procurement process requires familiarity with specific industry jargon. Here are some common terms that B2B buyers should know:
-
OEM (Original Equipment Manufacturer): This term refers to companies that produce parts or equipment that may be marketed by another manufacturer. Understanding OEM relationships is crucial for buyers looking to source components or complete machines, as it affects pricing, quality, and warranty options.
-
MOQ (Minimum Order Quantity): This is the smallest number of units that a supplier is willing to sell. Knowing the MOQ helps buyers plan their purchases effectively, ensuring they meet supplier requirements while optimizing inventory levels.
-
RFQ (Request for Quotation): An RFQ is a document sent to suppliers requesting pricing and terms for specified products or services. It is an essential tool for buyers to compare costs and negotiate favorable terms, ensuring they receive competitive pricing for can drink vending machines.
-
Incoterms (International Commercial Terms): These are standardized terms that define the responsibilities of buyers and sellers regarding shipping, delivery, and risk transfer. Familiarity with Incoterms helps buyers understand their obligations and costs associated with international shipping, crucial for transactions across regions like Africa and Europe.
-
Lead Time: This term refers to the amount of time it takes from placing an order to receiving the goods. Understanding lead time is vital for inventory management and ensuring that vending machines are available when needed, particularly in fast-paced markets.
-
Warranty Period: This indicates the duration during which the manufacturer is responsible for repairing or replacing faulty products. Knowing the warranty terms is essential for buyers to assess the long-term value and reliability of the vending machines they are investing in.
By understanding these properties and terms, B2B buyers can make informed decisions when selecting can drink vending machines that meet their operational needs and market demands.
Navigating Market Dynamics, Sourcing Trends, and Sustainability in the can drink vending machine Sector
Market Overview & Key Trends
The global can drink vending machine market is witnessing substantial growth, driven by urbanization, changing consumer lifestyles, and a rising demand for convenient beverage options. International B2B buyers, particularly from Africa, South America, the Middle East, and Europe, should be aware of several key trends shaping the market. First, the integration of technology is paramount; smart vending machines equipped with IoT capabilities are enhancing operational efficiency through remote monitoring and real-time inventory management. This trend is especially relevant for regions with limited access to on-site maintenance services.
Additionally, there is a growing emphasis on energy-efficient machines that minimize operational costs and environmental impact. For example, machines that utilize eco-friendly refrigerants and advanced cooling technologies are becoming increasingly popular. Another notable trend is the customization of product offerings; buyers can now source machines that accommodate a wider variety of beverages, including health-oriented options like cold brew coffees and organic juices, appealing to health-conscious consumers.
Moreover, the rise of cashless payment systems, including mobile wallets and contactless cards, is transforming the consumer experience. This shift presents an opportunity for B2B buyers to invest in machines that are equipped for diverse payment methods, catering to a tech-savvy customer base. Understanding these dynamics is crucial for international buyers looking to penetrate or expand within the can drink vending machine market.
Sustainability & Ethical Sourcing in B2B
Sustainability has become a critical concern for businesses, particularly in the beverage sector. For B2B buyers in the can drink vending machine market, prioritizing environmentally friendly practices is not only beneficial for the planet but also enhances brand reputation among increasingly eco-conscious consumers. The sourcing of ingredients plays a vital role in this regard; establishing partnerships with suppliers who adhere to sustainable agricultural practices and provide ethically sourced materials is essential.
Moreover, utilizing packaging made from recycled or biodegradable materials can significantly reduce the environmental footprint of beverage products. Certifications such as Fair Trade, Rainforest Alliance, or Organic can further bolster a company’s commitment to sustainability and ethical sourcing, making products more appealing to consumers who prioritize these values.
Buyers should also consider the energy consumption of vending machines. Opting for models that comply with energy efficiency standards can lead to lower operational costs and a reduced carbon footprint. By incorporating sustainability into their sourcing strategies, international B2B buyers can differentiate themselves in a competitive market while contributing to global environmental goals.
Brief Evolution/History
The can drink vending machine industry has evolved significantly since its inception in the mid-20th century. Initially, machines offered limited selections of carbonated beverages, often requiring coins for transactions. Over the decades, technological advancements have transformed these machines into sophisticated retail solutions. The introduction of electronic payment systems, touchscreen interfaces, and IoT integration has enhanced user experience and operational efficiency.
In recent years, the focus has shifted towards sustainability and ethical sourcing, reflecting broader societal trends. This evolution is not just about convenience; it encompasses a commitment to environmental stewardship and consumer health. As the market continues to grow, international B2B buyers must navigate these changes effectively to capitalize on emerging opportunities.
Related Video: Global Trade & Logistics – What is Global Trade?
Frequently Asked Questions (FAQs) for B2B Buyers of can drink vending machine
-
What criteria should I use to vet suppliers of can drink vending machines?
When vetting suppliers, prioritize those with a proven track record in the vending machine industry, ideally with certifications like ISO 9001 or CE. Review their portfolio for successful projects and client testimonials. It’s also crucial to assess their manufacturing capabilities, technology integration, and after-sales support. Conducting site visits or virtual tours can provide insights into their operations. Lastly, consider their financial stability to ensure they can fulfill long-term commitments. -
Can I customize can drink vending machines to suit my specific market?
Yes, many manufacturers offer customization options, including machine size, drink selection, branding, and payment systems. Customizing your vending machines to cater to local preferences can enhance customer satisfaction and sales. Discuss your requirements with potential suppliers early in the negotiation process, ensuring they can accommodate your specific needs without significantly increasing lead times or costs. -
What are the typical minimum order quantities (MOQs) and lead times for can drink vending machines?
MOQs can vary significantly by manufacturer, often ranging from 10 to 100 units, depending on the complexity of the machines and customization options. Lead times typically span from 4 to 12 weeks, influenced by production schedules and component availability. Always confirm these details during negotiations, as this information is critical for planning your inventory and cash flow. -
What payment terms should I expect when sourcing can drink vending machines internationally?
Payment terms can vary widely, but common arrangements include a deposit (20-50%) upon order confirmation, with the balance due before shipment. For international transactions, consider using secure payment methods like letters of credit or escrow services to mitigate risk. Always clarify payment terms upfront to avoid misunderstandings that could delay your order.
-
How can I ensure quality assurance and necessary certifications for my vending machines?
Request detailed information on the manufacturer’s quality control processes, including inspections and testing protocols. Certifications such as ISO 22000 or HACCP indicate adherence to food safety standards, while CE marks ensure compliance with EU regulations. Before finalizing your order, ask for documentation proving these certifications to ensure your machines meet safety and quality standards in your target market. -
What logistics considerations should I keep in mind when importing can drink vending machines?
Logistics can be complex when importing vending machines due to their size and weight. Work with suppliers who have experience in international shipping and can assist with customs clearance. Consider shipping methods (air vs. sea), which will affect costs and delivery times. Additionally, ensure proper packaging to prevent damage during transit and clarify responsibilities for freight and insurance with your supplier. -
How should I handle disputes with suppliers during the procurement process?
Establish clear communication channels and documentation practices to minimize disputes. Draft a comprehensive contract outlining terms, responsibilities, and timelines. In case of a dispute, first attempt to resolve the issue through direct communication. If unresolved, consider mediation or arbitration as outlined in your contract. Being proactive and maintaining a good relationship with your supplier can often prevent misunderstandings from escalating. -
What after-sales support can I expect from vending machine suppliers?
After-sales support varies by supplier but should ideally include installation assistance, maintenance services, and technical support. Inquire about warranty terms and what they cover, as well as the availability of spare parts. A reliable supplier will also provide training for your staff on machine operation and troubleshooting. Establishing a good after-sales relationship is crucial for ensuring the longevity and performance of your vending machines.
Strategic Sourcing Conclusion and Outlook for can drink vending machine
In summary, the can drink vending machine market presents a wealth of opportunities for international B2B buyers, particularly those in Africa, South America, the Middle East, and Europe. Strategic sourcing is paramount; it involves not only selecting high-quality ingredients and reliable equipment but also fostering partnerships with trusted suppliers who can ensure consistency and compliance with safety regulations.
Key takeaways include understanding market demands through comprehensive research, investing in advanced vending technology that enhances operational efficiency, and implementing robust quality control measures to maintain product integrity. Moreover, leveraging innovative marketing and distribution strategies will significantly enhance your market penetration.
As you navigate this dynamic landscape, consider the long-term implications of your sourcing decisions. By prioritizing sustainability, technological integration, and consumer preferences, you position your business for sustained growth.
Looking ahead, now is the time to capitalize on these trends. Engage with reputable manufacturers and suppliers, explore emerging markets, and adapt to evolving consumer behaviors. The future of the vending machine industry is bright, and with strategic sourcing, your business can lead the way.