Your Ultimate Guide to Sourcing Businesses Looking For
Guide to Businesses Looking For Vending Machines
- Introduction: Navigating the Global Market for businesses looking for vending machines
- Understanding businesses looking for vending machines Types and Variations
- Key Industrial Applications of businesses looking for vending machines
- Strategic Material Selection Guide for businesses looking for vending machines
- In-depth Look: Manufacturing Processes and Quality Assurance for businesses looking for vending machines
- Comprehensive Cost and Pricing Analysis for businesses looking for vending machines Sourcing
- Spotlight on Potential businesses looking for vending machines Manufacturers and Suppliers
- Essential Technical Properties and Trade Terminology for businesses looking for vending machines
- Navigating Market Dynamics, Sourcing Trends, and Sustainability in the businesses looking for vending machines Sector
- Frequently Asked Questions (FAQs) for B2B Buyers of businesses looking for vending machines
- Strategic Sourcing Conclusion and Outlook for businesses looking for vending machines
Introduction: Navigating the Global Market for businesses looking for vending machines
In today’s fast-paced global economy, businesses are increasingly recognizing the value of vending machines as a versatile solution for enhancing customer engagement and operational efficiency. Whether it’s providing snacks in a corporate office or offering health-conscious options in a gym, vending machines cater to diverse consumer needs while requiring minimal staffing. For international B2B buyers from regions like Africa, South America, the Middle East, and Europe—including key markets such as Spain and France—understanding the vending machine landscape is crucial for making informed purchasing decisions.
This comprehensive guide delves into the various aspects of vending machines, including types, materials, manufacturing quality control, and sourcing from reliable suppliers. It also outlines cost considerations and provides insights into current market trends that can affect buying choices. By addressing common FAQs, this resource equips buyers with the knowledge necessary to navigate the complexities of global sourcing.
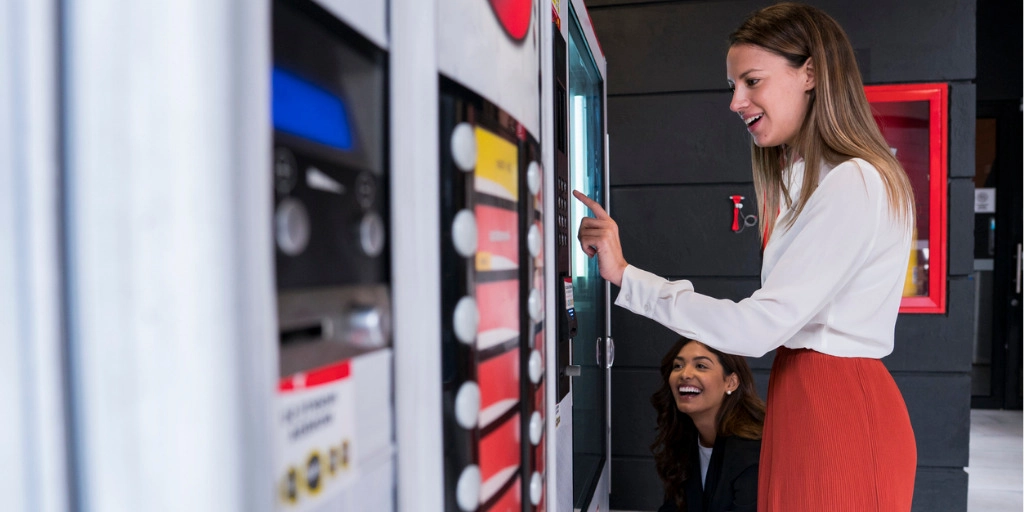
Illustrative Image (Source: Google Search)
Empowering businesses with actionable insights, this guide aims to facilitate effective sourcing strategies, ensuring that buyers can select the right vending machines that align with their operational goals and consumer preferences. Understanding these elements will not only optimize the purchasing process but also enhance the overall value derived from vending machine investments, setting the stage for success in an increasingly competitive marketplace.
Understanding businesses looking for vending machines Types and Variations
Type Name | Key Distinguishing Features | Primary B2B Applications | Brief Pros & Cons for Buyers |
---|---|---|---|
Snack and Beverage Machines | Offers a variety of snacks and drinks in a compact unit | Offices, schools, gyms | Pros: High demand, easy to maintain; Cons: Requires regular restocking and maintenance. |
Healthy Vending Machines | Focus on nutritious snacks and drinks | Health clubs, schools, hospitals | Pros: Meets health trends, attracts health-conscious consumers; Cons: Higher initial costs. |
Specialty Product Machines | Dispenses niche products like electronics or personal care | Airports, hotels, specialty stores | Pros: Unique offerings can drive traffic; Cons: Limited customer base and higher operational complexity. |
Cashless Payment Vending | Equipped with digital payment systems | Urban areas, tech-savvy environments | Pros: Convenient for users, reduces cash handling; Cons: Requires reliable internet access and maintenance. |
Customizable Vending Solutions | Tailored machines to meet specific client needs | Corporate offices, event venues | Pros: Enhanced customer satisfaction, tailored offerings; Cons: Higher upfront costs and longer lead times. |
Snack and Beverage Machines
Snack and beverage vending machines are the most common type found in various settings such as offices, schools, and gyms. They typically offer a range of popular snacks and drinks, making them appealing for quick consumption. For B2B buyers, these machines are attractive due to their high demand and relatively simple maintenance. However, they require regular restocking and can become a logistical challenge if not managed properly.
Healthy Vending Machines
With a growing trend towards health and wellness, healthy vending machines focus on providing nutritious snacks and beverages. They are ideally placed in locations such as health clubs, schools, and hospitals where health-conscious consumers are prevalent. While these machines can attract a dedicated customer base, they often come with higher initial costs due to the premium nature of the products offered. B2B buyers should consider the demographic and health trends in their target market when investing in these machines.
Specialty Product Machines
Specialty vending machines dispense unique items such as electronics, personal care products, or even gourmet food items. These machines are often found in airports, hotels, and specialty retail locations. Their key advantage lies in offering products that are not typically available in standard vending machines, which can drive foot traffic. However, B2B buyers should be aware that the customer base for these machines may be limited, and operational complexity can increase due to the variety of products offered.
Cashless Payment Vending
Cashless payment vending machines are equipped with digital payment systems, allowing customers to pay using credit cards, mobile wallets, or other electronic means. These machines are particularly well-suited for urban areas and tech-savvy environments where convenience is a priority. The primary benefits include reduced cash handling and increased customer convenience. However, B2B buyers must ensure reliable internet access and ongoing maintenance to keep these machines functioning optimally.
Customizable Vending Solutions
Customizable vending solutions offer tailored machines that meet specific client needs, such as branding or product selection. These machines are commonly used in corporate offices and event venues, where businesses want to enhance customer satisfaction through personalized offerings. While these solutions can lead to increased engagement and loyalty, they typically involve higher upfront costs and longer lead times for production and installation. B2B buyers should weigh the benefits of customization against their budget and time constraints.
Related Video: FINTECH BUSINESS MODELS EXPLAINED
Key Industrial Applications of businesses looking for vending machines
Industry/Sector | Specific Application of businesses looking for vending machines | Value/Benefit for the Business | Key Sourcing Considerations for this Application |
---|---|---|---|
Education | Snack and beverage vending for schools and universities | Enhances student satisfaction and convenience | Compliance with health regulations, payment system options |
Healthcare | Medicine and health supplies vending in hospitals | Provides immediate access to essential items | Security features, temperature control for perishables |
Corporate Offices | Refreshment and snack vending in office environments | Boosts employee morale and productivity | Variety of product offerings, machine aesthetics |
Transportation Hubs | Vending machines for snacks and drinks in airports and stations | Meets traveler demands for quick refreshments | High durability, cashless payment systems |
Retail | Vending solutions for retail spaces and shopping malls | Increases sales opportunities and customer engagement | Customization options, integration with existing retail systems |
Education
In educational institutions, vending machines serve as a convenient source of snacks and beverages for students and staff. They alleviate the need for students to leave campus for refreshments, thereby enhancing satisfaction and engagement. Buyers in this sector must consider compliance with health regulations to ensure the offerings are nutritious. Additionally, payment system options that cater to a younger demographic, such as mobile payments or contactless cards, are essential for maximizing usage.
Healthcare
Hospitals and clinics utilize vending machines to provide immediate access to essential medical supplies, snacks, and beverages for both patients and staff. This application addresses the need for quick access to items during emergencies or long wait times. Buyers should focus on machines with security features to prevent theft and ensure the integrity of health supplies. Furthermore, temperature control is crucial for maintaining the efficacy of perishable items, making it a key consideration for sourcing.
Corporate Offices
Vending machines in corporate environments offer snacks and beverages that can significantly boost employee morale and productivity. By providing easy access to refreshments, companies can create a more pleasant work atmosphere. When sourcing machines, businesses should look for a variety of product offerings to cater to diverse employee preferences. Aesthetics also play a role, as a visually appealing vending machine can enhance the overall office environment.
Transportation Hubs
Airports and train stations benefit from vending machines that cater to travelers’ needs for quick snacks and drinks. These machines provide a convenient solution for passengers on the go, ensuring they have access to refreshments without long waits. Buyers should prioritize high durability and reliability in vending machines, as they will be subject to heavy usage. Additionally, incorporating cashless payment systems can streamline transactions and improve user experience.
Retail
In retail spaces and shopping malls, vending machines serve as an innovative solution to increase sales opportunities. They can be strategically placed to attract customers and enhance their shopping experience. Retail buyers should consider customization options that allow for branding and product selection tailored to the target demographic. Integration with existing retail systems can also enhance operational efficiency, making it a vital consideration during sourcing.
Related Video: How I Turned Vending Machines Into A $300K Business | On The Job
Strategic Material Selection Guide for businesses looking for vending machines
When selecting materials for vending machines, businesses must consider various factors that influence performance, durability, and compliance with international standards. Below, we analyze four common materials used in the construction of vending machines, focusing on their properties, advantages, disadvantages, and specific considerations for international B2B buyers.
Stainless Steel
Key Properties: Stainless steel is known for its excellent corrosion resistance, high strength, and ability to withstand high temperatures. It can handle pressures typically encountered in vending machine applications without deforming.
Pros & Cons: The primary advantages of stainless steel include its durability and resistance to rust and staining, making it ideal for environments where hygiene is crucial, such as food and beverage vending. However, stainless steel is generally more expensive than other materials and can be challenging to fabricate, which may increase manufacturing costs.
Impact on Application: Stainless steel is compatible with a wide range of media, including beverages and snacks, and is easy to clean, which is essential for maintaining hygiene standards.
Considerations for International Buyers: Compliance with standards such as ASTM A240 for stainless steel grades is crucial. Buyers in regions like Europe and the Middle East should ensure that the selected grade meets local regulations regarding food safety.
Aluminum
Key Properties: Aluminum is lightweight, corrosion-resistant, and has good thermal conductivity. It can withstand moderate temperatures and pressures, making it suitable for various vending machine components.
Pros & Cons: The lightweight nature of aluminum makes it easier to transport and install, reducing overall costs. However, it is less durable than stainless steel and can be prone to scratching and denting, which may affect the aesthetic appeal of the vending machine over time.
Impact on Application: Aluminum is suitable for non-corrosive environments and can be used for external panels and frames. Its thermal properties can help maintain the temperature of refrigerated items.
Considerations for International Buyers: Buyers should be aware of the specific aluminum grades and their properties, such as those outlined in the ASTM B221 standard. Compliance with local recycling and environmental regulations is also important, especially in Europe.
High-Density Polyethylene (HDPE)
Key Properties: HDPE is a thermoplastic known for its high strength-to-density ratio, impact resistance, and chemical resistance. It performs well in a range of temperatures but is less effective under high-pressure conditions.
Pros & Cons: One of the key advantages of HDPE is its lower cost compared to metals, making it an attractive option for budget-conscious projects. However, it may not be suitable for high-heat applications and can degrade under prolonged exposure to UV light unless treated.
Impact on Application: HDPE is often used for internal components and storage bins within vending machines, particularly for snacks and non-perishable items. Its chemical resistance makes it suitable for various products.
Considerations for International Buyers: Compliance with standards like ASTM D638 for tensile properties is essential. Buyers should also consider the environmental impact of plastic materials and any local regulations regarding their use.
Glass
Key Properties: Glass is a rigid material that offers excellent visibility and aesthetic appeal. It can be treated to enhance durability and resistance to breakage.
Pros & Cons: The primary advantage of glass is its transparency, allowing customers to see products clearly, which can enhance sales. However, glass is heavy, fragile, and can be expensive to replace if broken.
Impact on Application: Glass is often used in vending machine doors and display cases, providing a premium look and feel. It is suitable for a variety of products, including beverages and snacks, but requires careful handling.
Considerations for International Buyers: Buyers should ensure that the glass used complies with safety standards such as ANSI Z97.1, especially in regions with strict regulations regarding consumer safety.
Summary Table
Material | Typical Use Case for businesses looking for vending machines | Key Advantage | Key Disadvantage/Limitation | Relative Cost (Low/Med/High) |
---|---|---|---|---|
Stainless Steel | External panels and structural components | Excellent corrosion resistance, durable | Higher cost, complex to manufacture | High |
Aluminum | Frames and non-load-bearing panels | Lightweight, cost-effective | Less durable, prone to scratches | Medium |
High-Density Polyethylene (HDPE) | Internal components and storage bins | Lower cost, good chemical resistance | Not suitable for high heat, UV degradation | Low |
Glass | Doors and display cases | Excellent visibility, aesthetic appeal | Heavy, fragile, expensive to replace | Medium |
This guide provides a comprehensive overview of material options for vending machines, helping international B2B buyers make informed decisions based on performance, cost, and compliance with local standards.
In-depth Look: Manufacturing Processes and Quality Assurance for businesses looking for vending machines
Manufacturing Processes for Vending Machines
When engaging in the procurement of vending machines, understanding the manufacturing processes is crucial for ensuring quality and efficiency. The manufacturing of vending machines typically involves several key stages, each with its own set of techniques and practices.
1. Material Preparation
Material preparation is the foundational stage of the manufacturing process. This stage involves sourcing high-quality materials such as steel, plastics, and electronic components. Key techniques include:
- Material Sourcing: Manufacturers often procure materials from certified suppliers to ensure quality and compliance with international standards.
- Cutting and Shaping: Materials are cut and shaped using advanced machinery like laser cutters and CNC machines, which ensure precision and reduce waste.
2. Forming
During the forming stage, the prepared materials are molded into parts that will become the machine’s structure. Techniques used include:
- Stamping: Metal sheets are stamped into specific shapes required for the chassis and doors of the vending machine.
- Injection Molding: This technique is commonly used for plastic components, allowing for complex shapes and designs that enhance usability and aesthetics.
3. Assembly
The assembly stage is where the various parts come together to form a complete vending machine. This includes:
- Sub-Assembly: Components like the refrigeration unit, payment systems, and control panels are assembled separately before being integrated into the main unit.
- Final Assembly: The sub-assemblies are brought together in a clean, organized environment. Automated systems may be used to streamline this process, ensuring efficiency and consistency.
4. Finishing
Finishing processes add the final touches to the vending machines. This can include:
- Painting and Coating: Machines are often powder-coated or painted to provide a durable, attractive finish that can withstand outdoor conditions.
- Quality Inspection: Before the machines are packaged and shipped, they undergo a thorough inspection to ensure they meet quality standards.
Quality Assurance in Vending Machine Manufacturing
Quality assurance (QA) is a critical component of the manufacturing process, particularly for B2B buyers who need reliable and durable products. Several international and industry-specific standards guide quality assurance in this sector.
Relevant International Standards
- ISO 9001: This standard focuses on quality management systems and is widely recognized across industries. Manufacturers seeking ISO 9001 certification demonstrate their commitment to quality and continuous improvement.
- CE Marking: Particularly important in the European market, CE marking indicates that the vending machines meet EU safety, health, and environmental protection standards.
QC Checkpoints
Quality control (QC) involves multiple checkpoints throughout the manufacturing process, including:
- Incoming Quality Control (IQC): This initial stage checks the quality of raw materials and components before they enter the production line.
- In-Process Quality Control (IPQC): Inspections during the manufacturing process ensure that each stage meets the specified quality standards.
- Final Quality Control (FQC): A comprehensive inspection is conducted on the completed machines to verify their functionality and appearance before shipping.
Common Testing Methods
Testing methods used to ensure quality include:
- Functional Testing: Ensures that all mechanical and electronic components operate correctly.
- Durability Testing: Machines are subjected to stress tests to evaluate their performance under various conditions.
- Safety Testing: Compliance with safety standards is verified through rigorous testing of electrical and mechanical components.
Verifying Supplier Quality Control
For international B2B buyers, especially from Africa, South America, the Middle East, and Europe, verifying a supplier’s quality control processes is essential. Here are actionable steps to ensure the reliability of your vending machine suppliers:
Audits and Reports
- Conduct Supplier Audits: Regular audits can help assess the manufacturer’s adherence to quality standards. Audits should evaluate the entire manufacturing process, from material sourcing to final assembly.
- Request Quality Reports: Suppliers should provide documentation of their quality control processes, including records of inspections and tests performed.
Third-Party Inspections
Engaging a third-party inspection agency can provide an unbiased assessment of the supplier’s quality practices. These agencies can conduct inspections at various stages of production and provide detailed reports on compliance with international standards.
Navigating QC/Cert Nuances for International Buyers
When sourcing vending machines, it is essential to understand the nuances of quality control and certification, especially in a global context:
- Regional Compliance: Different regions may have specific compliance requirements. For instance, machines exported to Europe must adhere to CE marking requirements, while those sold in the US may need to comply with UL standards.
- Documentation and Transparency: Suppliers should be transparent about their certifications and quality processes. B2B buyers should request copies of relevant certifications and quality assurance documentation to ensure compliance.
By understanding the manufacturing processes and quality assurance practices associated with vending machines, international B2B buyers can make informed decisions, ensuring they procure reliable and high-quality products that meet their operational needs.
Related Video: Most Satisfying Factory Production Processes And Heavy-Duty Factory Machines!
Comprehensive Cost and Pricing Analysis for businesses looking for vending machines Sourcing
When sourcing vending machines, understanding the comprehensive cost structure and pricing dynamics is crucial for international B2B buyers, particularly those from Africa, South America, the Middle East, and Europe. This analysis provides actionable insights into cost components, price influencers, and effective negotiation strategies.
Cost Components
-
Materials: The cost of raw materials is a significant component of vending machine pricing. Common materials include metal, plastic, glass, and electronic components. The choice of materials can directly affect the durability and aesthetics of the machines.
-
Labor: Labor costs encompass wages for manufacturing workers and assembly line personnel. In regions with higher labor costs, such as Western Europe, this can significantly increase the overall price of vending machines.
-
Manufacturing Overhead: This includes all indirect costs associated with production, such as utilities, rent, and equipment maintenance. Efficient production processes can help minimize overhead costs.
-
Tooling: Custom tooling for specific vending machine designs can be a substantial initial investment. Buyers should consider whether the tooling costs are justified by the expected volume of machines.
-
Quality Control (QC): Ensuring that vending machines meet specific quality standards involves additional costs. Certifications for quality assurance can also influence pricing, particularly for buyers requiring compliance with international standards.
-
Logistics: Transportation and shipping costs can vary widely based on the distance from the manufacturer and the mode of transport. Incoterms will dictate who bears these costs, impacting the final price.
-
Margin: Suppliers will typically include a profit margin in their pricing. This margin can vary based on competition and market demand.
Price Influencers
-
Volume/MOQ: Purchasing in larger quantities can lead to significant discounts. Suppliers often have minimum order quantities (MOQ) that can affect pricing dynamics.
-
Specifications/Customization: Custom features can increase costs. Buyers should evaluate the necessity of customization against standard options to optimize budget allocation.
-
Materials: The choice of materials not only affects durability but also influences price. High-quality materials may incur higher upfront costs but can result in lower maintenance expenses.
-
Quality/Certifications: Compliance with local regulations and industry standards can affect pricing. Machines with higher certifications may command a premium.
-
Supplier Factors: The reputation, reliability, and financial stability of suppliers can influence pricing. Established suppliers may offer better warranties and support, justifying a higher price.
-
Incoterms: Understanding shipping terms (like FOB, CIF, etc.) is essential. Different terms can shift costs and risks, impacting the total price.
Buyer Tips
-
Negotiation: Leverage volume purchasing and long-term contracts to negotiate better pricing. Building strong relationships with suppliers can also facilitate favorable terms.
-
Cost-Efficiency: Conduct a Total Cost of Ownership (TCO) analysis, considering not only the purchase price but also installation, maintenance, and operational costs.
-
Pricing Nuances: International buyers should be aware of currency fluctuations and import duties, which can affect overall costs. Engage in thorough market research to understand local pricing dynamics.
-
Local Market Insights: Buyers from regions like Africa and South America may find unique local suppliers who offer competitive pricing. Exploring regional vendors can yield cost-effective options.
In conclusion, navigating the complexities of vending machine sourcing requires a keen understanding of cost structures and pricing dynamics. By considering the outlined components and influencers, international B2B buyers can make informed decisions that align with their operational needs and budget constraints. Always remember to assess indicative prices against your specific requirements and market conditions.
Spotlight on Potential businesses looking for vending machines Manufacturers and Suppliers
This section offers a look at a few manufacturers active in the ‘businesses looking for vending machines’ market. This is a representative sample for illustrative purposes; B2B buyers must conduct their own extensive due diligence before any engagement. Information is synthesized from public sources and general industry knowledge.
Essential Technical Properties and Trade Terminology for businesses looking for vending machines
When exploring vending machines for your business, understanding essential technical properties and trade terminology is crucial. This knowledge not only facilitates informed decision-making but also ensures that your investments yield optimal returns.
Critical Technical Properties
-
Material Grade
– Definition: Refers to the quality and type of materials used in the construction of the vending machine, such as stainless steel, plastic, or tempered glass.
– Importance: High-grade materials enhance durability, making machines resistant to wear and tear, which is particularly important in high-traffic environments. This can lead to lower maintenance costs and longer service life. -
Dimensions and Weight
– Definition: The physical size and weight of the vending machine, including height, width, depth, and total weight.
– Importance: Understanding dimensions is vital for space planning, especially in locations with limited area. Additionally, weight can impact transportation costs and installation requirements. -
Power Consumption
– Definition: The amount of electrical power the vending machine requires to operate efficiently.
– Importance: Low power consumption is essential for reducing operational costs. It is particularly significant for businesses in regions where electricity costs are high. Energy-efficient models can also contribute to sustainability goals. -
Capacity
– Definition: The volume of products the vending machine can hold, usually measured in number of items or liters.
– Importance: A higher capacity means less frequent restocking, which is crucial for businesses aiming to maximize operational efficiency. It allows for a more diverse product offering, catering to a wider customer base. -
Payment Options
– Definition: The types of payment methods accepted by the vending machine, such as cash, credit/debit cards, mobile payments, or cryptocurrency.
– Importance: Offering multiple payment options can increase sales by accommodating customer preferences. In regions with a high usage of digital payments, this feature can be a significant competitive advantage.
Common Trade Terminology
-
OEM (Original Equipment Manufacturer)
– Definition: A company that produces parts and equipment that may be marketed by another manufacturer.
– Relevance: Understanding OEM relationships can help businesses identify reputable suppliers and negotiate better terms for parts and services. -
MOQ (Minimum Order Quantity)
– Definition: The smallest quantity of a product that a supplier is willing to sell.
– Relevance: Knowing the MOQ helps businesses manage inventory and cash flow effectively, especially when sourcing vending machines and components. -
RFQ (Request for Quotation)
– Definition: A document sent to suppliers to solicit price and availability for specific products or services.
– Relevance: Crafting an RFQ can lead to competitive pricing and better supplier terms, allowing businesses to make cost-effective purchasing decisions. -
Incoterms (International Commercial Terms)
– Definition: A set of international rules that define the responsibilities of sellers and buyers in international transactions.
– Relevance: Familiarity with Incoterms is vital for understanding shipping logistics, risk management, and cost allocation in international trade. -
Lead Time
– Definition: The amount of time between the initiation of a process and its completion, particularly in manufacturing and delivery.
– Relevance: Knowing the lead time helps businesses plan for inventory management and ensures that they can meet customer demands without delays.
Understanding these technical properties and trade terms equips international B2B buyers with the insights needed to make strategic decisions when investing in vending machines, ensuring alignment with business objectives and market demands.
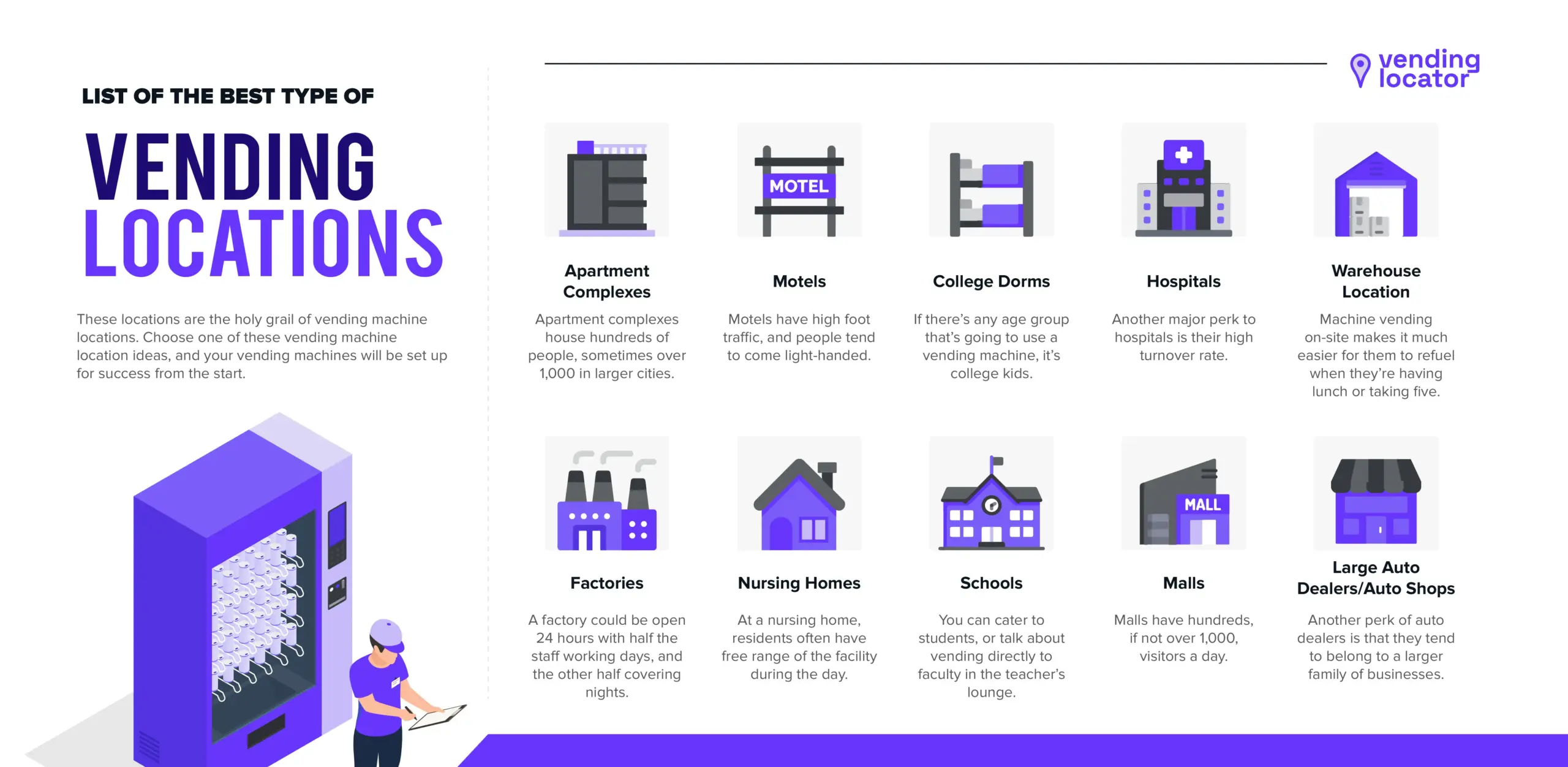
Illustrative Image (Source: Google Search)
Navigating Market Dynamics, Sourcing Trends, and Sustainability in the businesses looking for vending machines Sector
Market Overview & Key Trends
The vending machine sector is experiencing significant transformation driven by technological advancements and shifting consumer preferences. In emerging markets across Africa and South America, there is a growing demand for automated retail solutions that provide convenience and enhance customer experience. Key drivers include urbanization, increasing disposable incomes, and a demand for 24/7 access to products. B2B buyers are particularly focused on sourcing machines that integrate digital payment solutions, such as mobile wallets and contactless payments, to cater to tech-savvy consumers.
In Europe, especially in countries like Spain and France, there is a notable trend towards customization and personalization of vending offerings. Machines are increasingly equipped with IoT capabilities, allowing operators to monitor inventory in real-time and adjust stock based on consumer preferences. Furthermore, the rise of health-conscious consumers has led to an increased demand for vending machines that offer healthy snacks and beverages, reflecting a broader shift towards wellness.
Additionally, sustainability is becoming a pivotal factor in sourcing decisions. Buyers are now prioritizing suppliers that offer eco-friendly vending solutions, such as energy-efficient machines and recyclable packaging options. As the market evolves, B2B buyers must stay ahead of these trends to ensure they are meeting the demands of their customers while also aligning with global sustainability goals.
Sustainability & Ethical Sourcing in B2B
The environmental impact of vending machines extends beyond their operational energy consumption; it encompasses the entire supply chain, from production to disposal. B2B buyers are increasingly aware of the importance of ethical sourcing and are looking for manufacturers that prioritize sustainability in their operations. This includes using materials that are recyclable or biodegradable and ensuring that the production processes minimize carbon footprints.
Certifications such as ISO 14001 for environmental management and the use of eco-labels can help buyers identify suppliers committed to sustainable practices. Furthermore, the adoption of energy-efficient machines not only reduces operational costs but also appeals to environmentally conscious consumers.
Investing in vending machines that utilize renewable energy sources, such as solar panels, is another way to enhance sustainability. For businesses looking to establish a competitive edge, integrating sustainability into their sourcing strategy not only aligns with corporate social responsibility goals but also meets the growing consumer demand for eco-friendly products.
Brief Evolution/History
The vending machine industry has evolved significantly since its inception in the late 19th century, when simple machines dispensed items like postcards and chewing gum. The introduction of electrical vending machines in the early 20th century marked a major turning point, allowing for a wider array of products, including snacks and beverages.
In recent decades, the advent of technology has further revolutionized the sector. The integration of cashless payment systems and touchless interfaces has enhanced user convenience, while data analytics has empowered operators to optimize inventory and improve customer engagement. As the industry continues to adapt to changing consumer behaviors and technological advancements, the focus on sustainability and ethical sourcing is poised to shape its future trajectory.
Related Video: Global Trade & Logistics – What is Global Trade?
Frequently Asked Questions (FAQs) for B2B Buyers of businesses looking for vending machines
-
What should I consider when vetting suppliers for vending machines?
When vetting suppliers, assess their experience, reputation, and reliability. Look for companies that have a proven track record in international trade and can provide references from previous clients. Check their certifications and compliance with international standards, which is crucial for quality assurance. Additionally, consider their capacity to customize machines according to your specific needs, and confirm their ability to meet your order volumes consistently. -
Can vending machines be customized to suit my business needs?
Yes, many suppliers offer customization options for vending machines. This can include branding, product selection, and features tailored to your target market. Discuss your specific requirements with potential suppliers to understand the range of customization available. Ensure that the supplier can provide samples or prototypes before finalizing your order to ensure that the machines meet your expectations. -
What are the typical minimum order quantities (MOQ) and lead times for vending machines?
MOQs can vary significantly between suppliers, typically ranging from a few units to several dozen. Discuss your needs with suppliers to find out their specific MOQs. Lead times also vary based on the complexity of the order and customization level, generally ranging from 4 to 12 weeks. It’s advisable to plan ahead and communicate clearly with suppliers to avoid delays in your operations. -
What payment terms are commonly accepted when sourcing vending machines internationally?
Payment terms can vary widely depending on the supplier and your negotiation. Common methods include bank transfers, letters of credit, and escrow services. Some suppliers may require a deposit upfront, with the balance due upon delivery or installation. Always ensure that payment terms are clearly defined in the contract to prevent misunderstandings and protect your investment. -
How can I ensure quality assurance and compliance with international standards?
To ensure quality assurance, request certifications such as ISO or CE from suppliers, which indicate compliance with international manufacturing standards. Conduct pre-shipment inspections or quality audits, if possible. Engage third-party inspection services to verify the quality of the machines before they leave the supplier’s facility. Establish a clear agreement on quality expectations in your purchase contract. -
What logistics considerations should I keep in mind when importing vending machines?
Logistics is critical when importing vending machines. Choose a reliable freight forwarder familiar with the import regulations in your country. Consider the size and weight of the machines, as this can impact shipping costs. Ensure that all necessary documentation, including customs declarations and import permits, is prepared in advance to avoid delays. Discuss with your supplier about packaging to prevent damage during transit. -
How should I handle disputes with suppliers?
To handle disputes effectively, establish clear terms in your contract regarding dispute resolution. This may include mediation, arbitration, or litigation, depending on the nature of the issue. Maintain open communication with the supplier to address concerns promptly. If a resolution cannot be reached, consult with legal professionals specializing in international trade to explore your options and protect your interests. -
What after-sales support should I expect from vending machine suppliers?
After-sales support is crucial for long-term success. Suppliers should offer training for your staff, maintenance services, and readily available spare parts. Confirm the warranty period and what it covers. It’s beneficial to have a local representative or service center to assist with any issues that may arise. Establish a clear communication channel for ongoing support and assistance.
Strategic Sourcing Conclusion and Outlook for businesses looking for vending machines
In conclusion, strategic sourcing is crucial for businesses seeking to invest in vending machines. By understanding the market dynamics and supplier capabilities, international B2B buyers can make informed decisions that enhance operational efficiency and customer satisfaction. Key takeaways include the importance of aligning vending machine choices with local consumer preferences, ensuring compliance with regional regulations, and leveraging technology for inventory management and payment solutions.
For buyers from Africa, South America, the Middle East, and Europe, it is vital to conduct thorough market research and build strong relationships with suppliers to optimize sourcing strategies. Engaging in collaborative partnerships can lead to innovative solutions that address specific regional challenges while maximizing profitability.
As the vending industry evolves with advancements in technology and changing consumer behaviors, the potential for growth and diversification remains significant. Now is the time to act—evaluate your sourcing strategies, explore new opportunities, and position your business for success in this dynamic market. Embrace the future of vending machines and unlock their full potential to drive your business forward.