Your Ultimate Guide to Sourcing Big Bills For A Vending
Guide to Big Bills For A Vending Machine
- Introduction: Navigating the Global Market for big bills for a vending machine
- Understanding big bills for a vending machine Types and Variations
- Key Industrial Applications of big bills for a vending machine
- Strategic Material Selection Guide for big bills for a vending machine
- In-depth Look: Manufacturing Processes and Quality Assurance for big bills for a vending machine
- Comprehensive Cost and Pricing Analysis for big bills for a vending machine Sourcing
- Spotlight on Potential big bills for a vending machine Manufacturers and Suppliers
- Essential Technical Properties and Trade Terminology for big bills for a vending machine
- Navigating Market Dynamics, Sourcing Trends, and Sustainability in the big bills for a vending machine Sector
- Frequently Asked Questions (FAQs) for B2B Buyers of big bills for a vending machine
- Strategic Sourcing Conclusion and Outlook for big bills for a vending machine
Introduction: Navigating the Global Market for big bills for a vending machine
In today’s fast-paced global economy, the ability to accept large denominations in vending machines is crucial for enhancing customer convenience and maximizing sales potential. Big bills for vending machines represent not only a technological advancement but also a strategic opportunity for businesses across diverse markets, including Africa, South America, the Middle East, and Europe. By accommodating larger bills, vending operators can cater to a wider customer base, reduce the frequency of cash replenishment, and ultimately drive revenue growth.
This comprehensive guide is designed to empower B2B buyers with the essential knowledge needed to navigate the intricacies of sourcing big bills for vending machines. We will cover a variety of critical topics, including the different types of bill acceptors available, the materials used in their manufacturing, and the quality control measures that ensure reliability and durability. Additionally, we will provide insights into the leading suppliers in the market, cost considerations, and frequently asked questions that often arise during the procurement process.
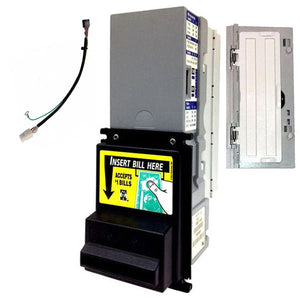
Illustrative Image (Source: Google Search)
By equipping international buyers with actionable insights and thorough market analysis, this guide aims to facilitate informed sourcing decisions that align with their business objectives. Whether you are based in Kenya, Australia, or elsewhere, understanding the dynamics of big bills for vending machines will position your business for success in an increasingly competitive landscape.
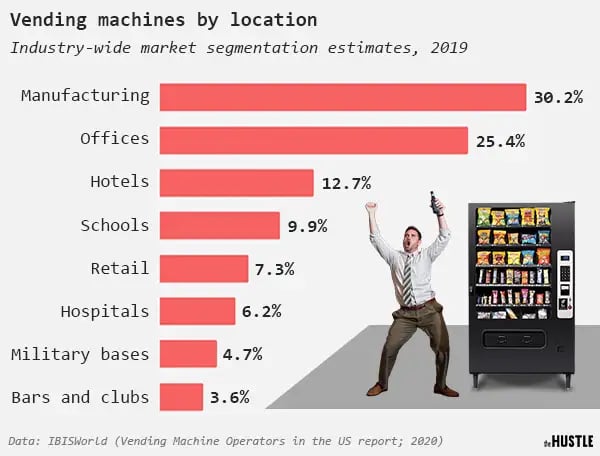
Illustrative Image (Source: Google Search)
Understanding big bills for a vending machine Types and Variations
Type Name | Key Distinguishing Features | Primary B2B Applications | Brief Pros & Cons for Buyers |
---|---|---|---|
High Denomination Notes | Typically $20, $50, or higher denominations | Large venues, casinos, airports | Pros: Reduces the need for change; Cons: May lead to cash flow issues if not managed properly. |
Coin-Operated Vending Bills | Adapted to accept large bills with a coin return | Convenience stores, public transport | Pros: Flexible payment options; Cons: Maintenance can be complex due to mixed currency handling. |
Electronic Bill Validators | Digital systems for verifying large bills | Amusement parks, entertainment venues | Pros: Enhanced security against counterfeiting; Cons: Higher initial investment costs. |
Custom Currency Solutions | Tailored systems for specific markets or events | Festivals, trade shows, exhibitions | Pros: Unique branding opportunities; Cons: Limited usability outside specific events. |
Integrated Payment Systems | Combines cash, card, and mobile payment options | Large retail chains, shopping malls | Pros: Comprehensive payment solutions; Cons: Requires advanced technology and support. |
High Denomination Notes
High denomination notes, such as $20 and $50 bills, are essential for vending machines located in high-traffic areas like casinos and airports. These machines are designed to minimize the need for change, making transactions quicker and more efficient. When purchasing vending machines for these locations, buyers should consider the volume of cash transactions and ensure that the machine can handle larger bills without frequent jams or malfunctions.
Coin-Operated Vending Bills
Coin-operated vending machines that accept large bills are increasingly popular in convenience stores and public transport systems. These machines provide an option for customers to pay with larger denominations while offering a coin return feature. Buyers should evaluate the operational costs and maintenance requirements, as the complexity of handling mixed currency can lead to increased servicing needs.
Electronic Bill Validators
Electronic bill validators are advanced systems that verify the authenticity of large bills before accepting them. These are particularly useful in amusement parks and entertainment venues where cash handling is frequent. Buyers should weigh the benefits of enhanced security against the initial costs, as these systems may require significant investment but can reduce losses from counterfeit bills.
Custom Currency Solutions
Custom currency solutions are designed to meet the unique needs of specific markets or events, such as festivals and trade shows. These vending machines can be branded for promotional purposes, offering a tailored experience for customers. Buyers must consider the limited usability of these machines outside designated events, which may affect their overall return on investment.
Integrated Payment Systems
Integrated payment systems combine cash, card, and mobile payment options, making them suitable for large retail chains and shopping malls. These systems enhance customer convenience by offering multiple payment methods, which can lead to increased sales. However, buyers should be prepared for the higher technological demands and ongoing support required to maintain these systems effectively.
Related Video: How To Start A Vending Machine Business in 2025 (FREE COURSE)
Key Industrial Applications of big bills for a vending machine
Industry/Sector | Specific Application of big bills for a vending machine | Value/Benefit for the Business | Key Sourcing Considerations for this Application |
---|---|---|---|
Retail | High-value item vending | Increased sales of premium products | Machine compatibility, currency acceptance, maintenance support |
Hospitality | In-room vending services | Enhanced guest experience, convenience | Inventory management, product variety, payment options |
Transportation | Ticket vending machines | Efficient ticketing, reduced queue times | Durability, user interface design, software integration |
Healthcare | Medical supply vending | Quick access to essential supplies | Compliance with health regulations, secure payment systems |
Education | Campus vending solutions | Catering to student needs, generating revenue | Product selection, pricing strategy, cash management |
Retail
In the retail sector, big bills for vending machines are utilized to facilitate the sale of high-value items such as electronics or luxury goods. These machines enable retailers to offer premium products in a self-service format, enhancing customer convenience and potentially increasing sales volume. Buyers in this sector should consider machine compatibility with various bill denominations, ensuring that the vending machines can accept larger bills without issues, and should also prioritize maintenance support to minimize downtime.
Hospitality
In the hospitality industry, big bills are essential for in-room vending services, allowing guests to purchase snacks, beverages, or other amenities directly from their rooms. This not only enhances the guest experience by providing convenience but also generates additional revenue for hotels. International buyers must focus on inventory management systems that can track sales in real-time and ensure a diverse product offering that meets guest preferences. Additionally, payment options should be flexible to accommodate international currencies.
Transportation
Transportation hubs such as airports and train stations often deploy vending machines equipped to handle big bills for ticket sales. This application streamlines the ticket purchasing process, significantly reducing wait times and enhancing customer satisfaction. Buyers should prioritize the durability of these machines, as they must withstand high traffic and potential vandalism. Furthermore, integrating user-friendly interfaces and software that can manage various payment methods is crucial for operational efficiency.
Healthcare
In healthcare settings, vending machines stocked with medical supplies or over-the-counter medications can provide quick access to essential items for both patients and staff. Utilizing big bills in these machines ensures that users can purchase items without needing exact change, which is particularly important in emergency situations. Buyers in this sector need to ensure compliance with health regulations and prioritize secure payment systems to protect sensitive information and transactions.
Education
Vending machines on college campuses that accept big bills cater to the diverse needs of students, providing easy access to food, beverages, and supplies. This not only meets the immediate demands of students but also creates a revenue stream for educational institutions. Buyers should consider product selection carefully to align with student preferences and dietary needs, as well as implement effective pricing strategies to ensure competitiveness. Additionally, robust cash management systems are necessary to handle larger transactions efficiently.
Related Video: How to Start a Vending Machine Business, Cost, Tips, How Much You Make
Strategic Material Selection Guide for big bills for a vending machine
When selecting materials for big bills in vending machines, it is crucial to consider their properties, advantages, disadvantages, and how they align with the specific needs of international B2B buyers. Here, we analyze four common materials: Stainless Steel, Aluminum, Polycarbonate, and Acrylic. Each material has unique characteristics that can significantly impact the performance and durability of vending machines.
Stainless Steel
Key Properties: Stainless steel is known for its excellent corrosion resistance, high strength, and durability. It can withstand high temperatures and pressures, making it suitable for various environments.
Pros & Cons: The primary advantage of stainless steel is its longevity and resistance to rust and staining, which is essential for vending machines that may be exposed to moisture. However, it is relatively expensive compared to other materials, which can increase the overall cost of the vending machine. Manufacturing complexity is moderate, as it requires specialized tools for cutting and welding.
Impact on Application: Stainless steel is compatible with a wide range of media, including water and food products, making it an ideal choice for vending machines dispensing beverages or snacks.
Considerations for International Buyers: Buyers should ensure compliance with international standards such as ASTM A240 for stainless steel sheets. In regions like Africa and South America, where humidity can be high, stainless steel’s corrosion resistance is particularly beneficial.
Aluminum
Key Properties: Aluminum is lightweight, corrosion-resistant, and has good thermal conductivity. It is also relatively easy to machine and fabricate.
Pros & Cons: The main advantage of aluminum is its low weight, which can reduce shipping costs and ease installation. It is also cost-effective compared to stainless steel. However, aluminum is less durable than stainless steel and can be prone to denting. Its lower strength may limit its use in high-stress applications.
Impact on Application: Aluminum is suitable for vending machines that require lightweight components, particularly in portable models. However, it may not be ideal for machines that need to withstand heavy usage or harsh environments.
Considerations for International Buyers: Buyers should check for compliance with standards such as ASTM B221 for aluminum extrusions. In regions with high temperatures, aluminum’s thermal properties can be advantageous, but care must be taken to prevent deformation under stress.
Polycarbonate
Key Properties: Polycarbonate is a strong, impact-resistant thermoplastic with excellent clarity and UV resistance. It can withstand a wide range of temperatures.
Pros & Cons: Polycarbonate’s key advantage is its high impact resistance, making it ideal for protective covers on vending machines. It is also lightweight and can be molded into complex shapes. However, it is more susceptible to scratching and may require coatings for UV protection, which can increase costs.
Impact on Application: This material is particularly suitable for transparent panels or windows in vending machines, allowing visibility of products while protecting them from external damage.
Considerations for International Buyers: Buyers should ensure that polycarbonate meets relevant safety and quality standards, such as ISO 4892 for UV exposure. In regions like the Middle East, where UV exposure is high, selecting UV-stabilized polycarbonate is crucial.
Acrylic
Key Properties: Acrylic is a lightweight, shatter-resistant plastic with excellent optical clarity. It is available in various colors and finishes.
Pros & Cons: Acrylic offers great aesthetic flexibility and can be manufactured at a lower cost than glass, providing a cost-effective solution for display panels. However, it is less impact-resistant than polycarbonate and can scratch easily, which may affect long-term appearance.
Impact on Application: Acrylic is commonly used for display cases and signage on vending machines, enhancing product visibility while being lightweight.
Considerations for International Buyers: Compliance with standards such as ASTM D4802 for acrylic sheets is essential. Buyers in Europe may prefer acrylic due to its aesthetic appeal, while those in harsher climates should consider its limitations regarding impact resistance.
Summary Table
Material | Typical Use Case for big bills for a vending machine | Key Advantage | Key Disadvantage/Limitation | Relative Cost (Low/Med/High) |
---|---|---|---|---|
Stainless Steel | Structural components, coin mechanisms | Excellent corrosion resistance | Higher cost, moderate manufacturing complexity | High |
Aluminum | Lightweight frames, portable machines | Cost-effective, lightweight | Less durable, prone to denting | Medium |
Polycarbonate | Protective covers, transparent panels | High impact resistance | Susceptible to scratching, UV protection needed | Medium |
Acrylic | Display cases, signage | Aesthetic flexibility, cost-effective | Less impact-resistant, scratches easily | Low |
This strategic material selection guide provides international B2B buyers with essential insights to make informed decisions when sourcing materials for vending machines designed to handle big bills. Each material’s unique properties and considerations can help optimize the performance and longevity of vending machines across diverse markets.
In-depth Look: Manufacturing Processes and Quality Assurance for big bills for a vending machine
Manufacturing Processes for Big Bills in Vending Machines
The manufacturing of components designed for handling big bills in vending machines involves several critical stages that ensure the final products are both functional and reliable. For B2B buyers, understanding these processes can aid in selecting the right suppliers and ensuring that the products meet the necessary standards.
Main Stages of Manufacturing
-
Material Preparation
– The first step involves selecting high-quality materials suitable for durability and functionality. Common materials include high-grade metals, plastics, and electronic components.
– Material Testing: Before usage, raw materials undergo rigorous testing to confirm their mechanical properties and resistances, such as tensile strength and corrosion resistance. -
Forming
– Techniques: This stage employs various techniques such as stamping, injection molding, and CNC machining to shape the components.
– Precision Tools: Using precision tools ensures that components fit perfectly within the vending machine, which is crucial for the accurate handling of big bills. -
Assembly
– Components are assembled in a clean and controlled environment to prevent contamination. This stage often includes the integration of electronic systems that read and validate bills.
– Automated vs. Manual Assembly: Depending on the complexity, some parts may be assembled manually while others might utilize automated assembly lines to enhance efficiency. -
Finishing
– The final stage involves surface treatments such as painting, plating, or coating to enhance aesthetics and protect against wear.
– Quality Assurance During Finishing: Each piece is inspected to ensure it meets the required finish and functionality standards, which is particularly important for electronic components.
Quality Assurance in Manufacturing
Quality assurance is crucial in the manufacturing of vending machine components, particularly when dealing with international standards and regulations.
International Standards and Certifications
- ISO 9001: This is a global standard that outlines the requirements for a quality management system (QMS). Manufacturers seeking ISO 9001 certification demonstrate their ability to provide products that meet customer and regulatory requirements consistently.
- CE Marking: This indicates conformity with health, safety, and environmental protection standards for products sold within the European Economic Area (EEA). It is essential for B2B buyers in Europe to ensure that their suppliers hold this certification.
- API Standards: For components that may interact with cash handling mechanisms, adherence to American Petroleum Institute (API) standards may be relevant, particularly in ensuring the reliability and safety of the equipment.
Quality Control Checkpoints
Quality control (QC) throughout the manufacturing process is vital to maintaining standards. Common QC checkpoints include:
- Incoming Quality Control (IQC): This involves inspecting raw materials upon arrival to ensure they meet specified standards before they are used in production.
- In-Process Quality Control (IPQC): Regular checks during the manufacturing process ensure that each stage adheres to quality standards. This includes monitoring machinery performance and product dimensions.
- Final Quality Control (FQC): Before shipping, a final inspection verifies that the finished products meet all specifications and quality standards.
Common Testing Methods
Testing methods employed to ensure product quality may include:
- Functional Testing: Verifying that the components operate correctly under expected conditions.
- Durability Testing: Assessing how well the components withstand wear and tear over time, which is critical for vending machines that operate in various environments.
- Environmental Testing: Simulating different environmental conditions (e.g., humidity, temperature) to ensure that products perform reliably.
Verifying Supplier Quality Control
For B2B buyers, particularly those from Africa, South America, the Middle East, and Europe, verifying a supplier’s quality control processes is essential. Here are actionable steps:
- Conduct Audits: Regular audits of supplier facilities can help verify adherence to quality standards. This can be done in-house or through third-party services.
- Request Quality Reports: Suppliers should provide documentation detailing their QC processes, testing results, and any certifications they hold.
- Third-Party Inspections: Engaging third-party inspection services can provide an unbiased assessment of a supplier’s production processes and adherence to quality standards.
Quality Control Nuances for International Buyers
International buyers should be aware of specific nuances related to quality control that may impact their procurement strategies:
- Cultural Differences: Understanding cultural attitudes towards quality and manufacturing can influence communication and expectations. For instance, buyers in Africa may face different challenges than those in Europe regarding supply chain reliability.
- Regulatory Compliance: Each region may have its own regulations regarding product safety and quality. B2B buyers must ensure their suppliers comply with local laws to avoid potential legal issues.
- Supply Chain Transparency: Demand transparency in the supply chain to ensure that all components meet the necessary quality standards, which is particularly relevant when sourcing from multiple countries.
In summary, a thorough understanding of the manufacturing processes and quality assurance protocols is vital for international B2B buyers looking to procure components for vending machines that handle big bills. By focusing on these aspects, buyers can ensure they select reliable suppliers who meet their quality expectations and regulatory requirements.
Related Video: Business English Vocabulary : VV 47 – Manufacturing & Production Process (1) | English Vocabulary
Comprehensive Cost and Pricing Analysis for big bills for a vending machine Sourcing
Analyzing the cost structure and pricing for sourcing big bills for vending machines is essential for international B2B buyers, particularly those in regions such as Africa, South America, the Middle East, and Europe. Understanding the key components of costs, the factors influencing pricing, and effective negotiation strategies can significantly enhance procurement efficiency and cost-effectiveness.
Cost Components
-
Materials: The choice of materials significantly impacts the overall cost of big bills for vending machines. High-quality materials may incur higher initial costs but can lead to lower long-term maintenance and replacement expenses.
-
Labor: Labor costs vary widely depending on the geographical location of the manufacturing facility. Regions with lower labor costs may offer competitive pricing, but it is essential to assess the skill level and expertise of the workforce, as these factors influence the product quality.
-
Manufacturing Overhead: This includes indirect costs related to production, such as utilities, rent, and equipment maintenance. Buyers should inquire about how these costs are calculated and factored into the overall pricing.
-
Tooling: The cost of tooling (molds, dies, etc.) is a significant factor, especially for customized solutions. Initial tooling costs can be high, but they are amortized over larger production runs, making it crucial to consider the volume of orders.
-
Quality Control (QC): Implementing stringent QC processes ensures product reliability but can add to the cost. Buyers should evaluate the QC measures in place and their associated costs to make informed decisions.
-
Logistics: Transportation and shipping costs can vary significantly based on the distance from the supplier, shipping methods, and Incoterms. Understanding these costs is vital for accurate budgeting.
-
Margin: Suppliers typically add a margin to cover their costs and profit. This margin can vary based on the supplier’s market positioning and the complexity of the product.
Price Influencers
-
Volume/MOQ: Purchasing in larger quantities can lead to reduced per-unit costs. Buyers should negotiate Minimum Order Quantities (MOQs) to achieve better pricing.
-
Specifications/Customization: Custom specifications can increase costs due to the need for specialized materials or processes. Buyers should clearly define their requirements to avoid unexpected expenses.
-
Quality and Certifications: Products that meet specific industry certifications may command higher prices. Buyers should assess whether these certifications are necessary for their market.
-
Supplier Factors: The supplier’s reputation, reliability, and history of service can influence pricing. It’s beneficial to conduct thorough supplier evaluations to ensure long-term partnerships.
-
Incoterms: The choice of Incoterms affects the allocation of costs and risks between the buyer and seller. Familiarity with these terms can help buyers negotiate better shipping and handling costs.
Buyer Tips
-
Negotiation: Engage suppliers in discussions regarding pricing and payment terms. Building a relationship can lead to better deals and more favorable terms.
-
Cost-Efficiency: Analyze the Total Cost of Ownership (TCO), which includes all costs associated with the procurement process, such as purchase price, maintenance, and disposal costs. This holistic view helps in making informed decisions.
-
Pricing Nuances: International buyers should be aware of currency fluctuations, tariffs, and local market conditions that can impact pricing. Understanding the local economic landscape is crucial for effective negotiation.
-
Supplier Diversification: Avoid relying on a single supplier to mitigate risks associated with price increases or supply disruptions. Having multiple suppliers can provide leverage in negotiations.
-
Long-Term Contracts: Consider negotiating long-term contracts for better pricing stability and supply assurance. This strategy can be particularly beneficial in volatile markets.
By understanding the comprehensive cost structure and pricing dynamics, international B2B buyers can make more informed decisions when sourcing big bills for vending machines, leading to improved procurement outcomes and enhanced operational efficiency.
Spotlight on Potential big bills for a vending machine Manufacturers and Suppliers
This section offers a look at a few manufacturers active in the ‘big bills for a vending machine’ market. This is a representative sample for illustrative purposes; B2B buyers must conduct their own extensive due diligence before any engagement. Information is synthesized from public sources and general industry knowledge.
Essential Technical Properties and Trade Terminology for big bills for a vending machine
Key Technical Properties for Big Bills in Vending Machines
When procuring components for vending machines that accept big bills, it’s essential to understand the technical specifications that influence performance and reliability. Below are critical properties that B2B buyers should consider:
-
Material Grade
The material used for the bill validator’s components must be durable and resistant to wear and tear. Common materials include stainless steel and high-grade plastics. The choice of material affects the longevity of the validator and its ability to withstand environmental factors such as humidity and temperature fluctuations, which is particularly important for machines deployed in varying climates across Africa, South America, the Middle East, and Europe. -
Tolerance
Tolerance refers to the allowable deviation from a specified dimension. In the context of bill validators, high precision is necessary to ensure that the device accurately recognizes and processes bills without jams or misreads. Tighter tolerances can lead to higher costs, but investing in precision can reduce maintenance and operational disruptions, which is vital for maintaining customer satisfaction. -
Operating Temperature Range
Vending machines can be exposed to extreme temperatures, depending on their location. The operating temperature range of the bill validator must accommodate these conditions to ensure optimal performance. This specification is crucial for international deployments, as machines in hotter climates may require additional cooling mechanisms.
-
Power Consumption
The energy efficiency of bill validators is increasingly important, especially in regions with high energy costs. Understanding the power consumption specifications helps businesses estimate operating costs and select models that align with sustainability goals. Low power consumption also contributes to longer operational life and less heat generation. -
Interface Compatibility
Compatibility with existing vending machine systems and payment processing networks is essential. This includes understanding communication protocols (like RS232 or USB) and the ability to integrate with various payment systems. Ensuring that components work seamlessly together can reduce installation time and costs. -
Security Features
With increasing concerns over fraud, security features such as anti-skimming technology and encryption capabilities are essential. Buyers should look for validators that offer robust security measures to protect against counterfeit bills and ensure secure transactions.
Common Trade Terminology
Understanding industry jargon is crucial for effective communication and negotiation in the B2B marketplace. Here are several key terms relevant to the procurement of vending machine components:
-
OEM (Original Equipment Manufacturer)
An OEM is a company that produces parts or equipment that may be marketed by another manufacturer. When sourcing big bill validators, working with OEMs ensures that you receive parts that meet specific quality standards and are compatible with your vending machines. -
MOQ (Minimum Order Quantity)
This term refers to the smallest number of units that a supplier is willing to sell. Understanding the MOQ helps businesses manage inventory and cash flow. For international buyers, negotiating MOQs can lead to significant cost savings, especially when sourcing from suppliers in different regions. -
RFQ (Request for Quotation)
An RFQ is a document that buyers send to suppliers asking for price quotes for specific products or services. It’s a vital tool for comparing costs and terms across different suppliers, ensuring that buyers can make informed purchasing decisions. -
Incoterms (International Commercial Terms)
These are a set of predefined international rules that clarify the responsibilities of buyers and sellers in shipping and logistics. Familiarity with Incoterms helps buyers understand shipping costs, risks, and responsibilities, which is particularly important when dealing with international suppliers. -
Lead Time
Lead time is the amount of time it takes from placing an order to receiving the goods. Understanding lead times is essential for supply chain management, especially for businesses that need to maintain inventory levels to meet customer demand. -
Warranty Period
This term refers to the duration during which a manufacturer guarantees the performance of their product. Knowing the warranty period helps buyers assess the risk associated with a purchase and plan for potential future costs related to repairs or replacements.
By grasping these technical specifications and trade terms, B2B buyers can make informed decisions, ensuring that they procure the right components for their vending machines while optimizing costs and operational efficiency.
Navigating Market Dynamics, Sourcing Trends, and Sustainability in the big bills for a vending machine Sector
Market Overview & Key Trends
The vending machine sector is experiencing significant transformation driven by several global factors. The rise in urbanization and changing consumer lifestyles are pushing the demand for convenient access to goods, including food, beverages, and other essentials. This trend is particularly strong in emerging markets across Africa, South America, the Middle East, and Europe, where busy urban environments necessitate quick service solutions.
International B2B buyers should be aware of the latest technological advancements impacting the vending machine market. Contactless payment options and smart vending machines equipped with IoT capabilities are becoming increasingly popular. These technologies enhance consumer experience and operational efficiency, allowing for real-time inventory management and data analytics. As a buyer, investing in these technologies can provide a competitive edge in the marketplace.
Another key trend is the shift towards healthier product offerings. Consumers are becoming more health-conscious, prompting vending machine operators to stock healthier snacks and drinks. This trend opens up opportunities for B2B buyers to source innovative products that align with consumer preferences. Furthermore, understanding local tastes and preferences is crucial for success in diverse markets, especially in regions like Kenya and Brazil, where local products can greatly enhance the appeal of vending offerings.
Sustainability & Ethical Sourcing in B2B
Sustainability is no longer just a buzzword; it is a critical component of modern business strategies, especially in the vending machine sector. The environmental impact of traditional vending operations, such as excessive packaging and waste, has drawn scrutiny from consumers and regulators alike. B2B buyers must prioritize ethical sourcing and sustainable practices to remain competitive and responsible.
Investing in ‘green’ certifications and materials, such as biodegradable packaging and energy-efficient machines, can significantly reduce the environmental footprint of vending operations. Buyers should seek suppliers who demonstrate commitment to sustainability through certifications like ISO 14001 or other recognized environmental standards. This not only enhances brand reputation but also meets the growing consumer demand for responsible business practices.
Additionally, establishing a transparent supply chain can help mitigate risks associated with unethical sourcing practices. Buyers should engage with suppliers who prioritize fair labor practices and sustainable sourcing, thus ensuring that their vending products align with ethical standards. This approach not only builds trust with consumers but also fosters loyalty among partners and stakeholders.
Brief Evolution/History
The vending machine industry has evolved significantly since its inception in the late 19th century. Initially, vending machines dispensed simple items like postcards and gum. However, advancements in technology and changing consumer behaviors have transformed these machines into sophisticated retail solutions.
In recent decades, the introduction of electronic payment systems, touchscreen interfaces, and remote inventory management has revolutionized the sector. Today, vending machines are equipped to handle a diverse array of products, catering to various consumer needs while embracing sustainability. As the market continues to grow, B2B buyers must stay informed about these historical shifts to navigate future trends effectively.
Related Video: ONESOURCE Global Trade: A Truly Global Solution
Frequently Asked Questions (FAQs) for B2B Buyers of big bills for a vending machine
-
1. How can I effectively vet suppliers for big bills for vending machines?
To vet suppliers, start by researching their reputation in the industry. Look for reviews and testimonials from other B2B buyers, particularly those from your region. Verify their business credentials, such as registration and certifications, and assess their financial stability. Request references and conduct background checks. It’s also beneficial to visit their facilities if possible or arrange for a virtual tour. Establishing a solid relationship can also aid in gauging reliability, so consider initiating conversations with their sales and customer service teams. -
2. Can I customize the big bills for my vending machines?
Yes, many suppliers offer customization options for big bills to ensure they meet your specific vending machine requirements. This can include variations in size, material, and design. When discussing customization, be clear about your specifications and the intended use of the bills. Engage in detailed discussions with your supplier’s technical team to explore available options. Ensure that the customization aligns with local regulations and the capabilities of your vending machines. -
3. What are the typical minimum order quantities (MOQ) and lead times for big bills?
Minimum order quantities vary by supplier and often depend on the customization required. Generally, MOQs can range from a few hundred to several thousand units. Lead times are typically influenced by production schedules, customization requests, and shipping logistics. On average, you can expect lead times of 4-12 weeks. Always clarify these details upfront and consider placing smaller initial orders to test product quality before committing to larger volumes. -
4. What quality assurance measures should I look for in suppliers?
When sourcing big bills, prioritize suppliers who implement strict quality assurance (QA) protocols. Look for certifications such as ISO 9001, which indicates adherence to international quality management standards. Request details about their QA processes, including material inspections, production monitoring, and final product testing. It’s also advisable to inquire about their return policies and warranty offerings, which can provide insight into their commitment to quality and customer satisfaction. -
5. How do I handle logistics and shipping for international orders?
Logistics can be complex when importing big bills for vending machines. Work with suppliers who have experience in international shipping and can provide a comprehensive shipping plan. Discuss shipping methods, estimated delivery times, and customs clearance processes. Understand the total landed cost, including shipping, tariffs, and taxes. Using a freight forwarder can simplify the process, as they can manage logistics and ensure compliance with international trade regulations. -
6. What should I do if there’s a dispute with my supplier?
In case of a dispute, start by reviewing your contract to understand the agreed terms and conditions. Communicate directly with your supplier to express your concerns and seek a resolution. Maintain a professional demeanor and document all communications. If the dispute cannot be resolved amicably, consider mediation or arbitration as outlined in your contract. Having a clear dispute resolution clause can save time and costs in the long run. -
7. What payment options are typically available for international orders?
Most suppliers offer various payment options, including wire transfers, letters of credit, and online payment platforms. Wire transfers are common but can carry high fees, while letters of credit provide security for both parties. Discuss payment terms upfront, including deposits, full payment timelines, and any potential discounts for early payment. Be cautious of suppliers requesting full payment upfront, as this can increase risk; instead, negotiate terms that protect both parties. -
8. Are there specific regulations I need to be aware of when importing big bills?
Yes, each country has specific regulations concerning the importation of currency and related items. Research the regulations in your country regarding the importation of big bills for vending machines. This may include compliance with local currency laws, labeling requirements, and potential tariffs. Consulting with legal experts or customs brokers can provide clarity and help navigate the complexities of international trade laws, ensuring that your import activities are compliant and smooth.
Strategic Sourcing Conclusion and Outlook for big bills for a vending machine
In conclusion, the strategic sourcing of big bills for vending machines presents a pivotal opportunity for international B2B buyers. Key takeaways emphasize the importance of understanding local market dynamics, ensuring compliance with regional regulations, and maintaining quality standards throughout the sourcing process.
Investing in strategic sourcing not only optimizes procurement costs but also enhances the overall operational efficiency of vending machine businesses. By collaborating with reliable suppliers and manufacturers, buyers can secure high-quality components tailored to their specific needs, ultimately driving customer satisfaction and loyalty.
As we look to the future, it is essential for B2B buyers from Africa, South America, the Middle East, and Europe to remain agile and informed about emerging trends in the vending machine industry. Engaging in continuous market research and fostering strong supplier relationships will be crucial.
Now is the time to act—leverage strategic sourcing to position your business for success in a competitive landscape. Embrace innovation and quality in your procurement strategies to stay ahead of the curve and meet the evolving demands of consumers globally.