Your Ultimate Guide to Sourcing Beauty Vending Machines
Guide to Beauty Vending Machines
- Introduction: Navigating the Global Market for beauty vending machines
- Understanding beauty vending machines Types and Variations
- Key Industrial Applications of beauty vending machines
- Strategic Material Selection Guide for beauty vending machines
- In-depth Look: Manufacturing Processes and Quality Assurance for beauty vending machines
- Comprehensive Cost and Pricing Analysis for beauty vending machines Sourcing
- Spotlight on Potential beauty vending machines Manufacturers and Suppliers
- Essential Technical Properties and Trade Terminology for beauty vending machines
- Navigating Market Dynamics, Sourcing Trends, and Sustainability in the beauty vending machines Sector
- Frequently Asked Questions (FAQs) for B2B Buyers of beauty vending machines
- Strategic Sourcing Conclusion and Outlook for beauty vending machines
Introduction: Navigating the Global Market for beauty vending machines
In today’s rapidly evolving retail landscape, beauty vending machines have emerged as a transformative solution, offering unparalleled convenience and accessibility for consumers. These automated retail units cater to a growing demand for on-the-go beauty products, providing a unique shopping experience that resonates with modern consumers. For international B2B buyers, particularly those from Africa, South America, the Middle East, and Europe, understanding the intricacies of this market is essential for making informed sourcing decisions.
This comprehensive guide delves into the various aspects of beauty vending machines, including the different types available, materials used in their construction, and the manufacturing and quality control processes that ensure product reliability. Additionally, we will explore key suppliers and the cost structures associated with these machines, enabling buyers to weigh investment options effectively.
By equipping yourself with this knowledge, you empower your business to capitalize on emerging trends within the beauty industry. Whether you are considering introducing beauty vending machines to your portfolio or seeking to enhance your existing offerings, the insights provided here will facilitate strategic decision-making. From understanding market dynamics to addressing frequently asked questions, this guide serves as a crucial resource for navigating the global beauty vending machine market, ensuring you stay ahead in a competitive landscape.
Understanding beauty vending machines Types and Variations
Type Name | Key Distinguishing Features | Primary B2B Applications | Brief Pros & Cons for Buyers |
---|---|---|---|
Skincare Vending Machines | Offers a variety of skincare products, often with a focus on local or natural ingredients. | Spas, beauty salons, retail stores | Pros: Appeals to health-conscious consumers; Cons: Limited product range can restrict sales. |
Makeup Vending Machines | Stocks cosmetic items like lipsticks, foundations, and eye products. Often includes digital displays for tutorials. | Airports, malls, event venues | Pros: Attracts impulse buyers; Cons: Requires regular inventory updates to stay relevant. |
Haircare Vending Machines | Focuses on hair products such as shampoos, conditioners, and styling tools. May offer personalized recommendations. | Gyms, hotels, salons | Pros: Complements services offered in gyms and hotels; Cons: Space limitations can restrict offerings. |
Beauty Subscription Boxes | Provides a rotating selection of beauty products with subscription options for regular customers. | E-commerce platforms, retail stores | Pros: Encourages customer loyalty; Cons: Higher logistical costs for managing subscriptions. |
Customized Beauty Machines | Allows users to create personalized beauty products based on skin type and preferences. | High-end retailers, luxury brands | Pros: Unique selling proposition; Cons: High initial investment and maintenance costs. |
Skincare Vending Machines
Skincare vending machines are designed to cater to the growing demand for natural and locally sourced skincare products. They often feature a selection of moisturizers, serums, and treatments that align with current beauty trends. B2B buyers should consider the local market’s preferences when selecting products to stock, as consumer interest in sustainability and natural ingredients continues to rise.
Makeup Vending Machines
These machines provide a range of cosmetic products, including makeup essentials and accessories. They often incorporate technology, allowing for interactive experiences such as virtual try-ons or beauty tutorials. B2B buyers should evaluate the location of their machines, as high foot traffic areas like airports and shopping malls can significantly enhance sales potential.
Haircare Vending Machines
Haircare vending machines focus on essential hair products, from shampoos to styling tools. They may also include features that offer personalized recommendations based on hair type. For B2B buyers, placement in gyms or hotels can create additional value, as guests and members often seek convenient access to haircare solutions post-workout or during travel.
Beauty Subscription Boxes
These vending solutions offer a curated selection of beauty products through subscription services, appealing to consumers who enjoy trying new items regularly. B2B applications include e-commerce platforms and retail settings. Buyers should consider the logistics involved in managing subscriptions, as customer retention and satisfaction are critical to success in this competitive market.
Customized Beauty Machines
Customized beauty machines provide a unique experience by allowing users to create personalized beauty products tailored to their specific needs. This innovative approach can attract high-end clientele and enhance brand loyalty. B2B buyers must weigh the initial investment and ongoing maintenance costs against the potential for higher margins and customer engagement in luxury markets.
Key Industrial Applications of beauty vending machines
Industry/Sector | Specific Application of Beauty Vending Machines | Value/Benefit for the Business | Key Sourcing Considerations for this Application |
---|---|---|---|
Retail | In-store beauty product vending | Increased foot traffic, impulse buying | Machine size, product variety, payment options, maintenance support |
Hospitality | Hotel lobby and spa vending | Enhanced guest experience, additional revenue stream | Product selection, branding opportunities, machine aesthetics |
Transportation | Airport beauty vending stations | Convenience for travelers, quick access to essentials | Durability, security features, product shelf-life |
Events and Festivals | Mobile beauty vending for events | On-the-spot sales, brand visibility | Portability, product mix, ease of operation |
Corporate Offices | Employee wellness stations with beauty products | Improved employee satisfaction, branding consistency | Product assortment, machine design, maintenance services |
Retail
Beauty vending machines in retail environments serve as an innovative solution to enhance customer engagement. Positioned strategically, these machines attract foot traffic and encourage impulse buying, particularly in high-traffic areas such as shopping malls. For international B2B buyers, considerations include ensuring the machines can accommodate diverse product lines tailored to local consumer preferences, integrating secure payment systems, and providing ongoing maintenance support to minimize downtime.
Hospitality
In hotels and spas, beauty vending machines can significantly elevate guest experiences by offering convenient access to beauty products. These machines can be placed in lobbies or spa areas, providing guests with essential items on the go. For buyers in the hospitality sector, key factors include selecting aesthetically pleasing machines that align with the hotel’s branding, curating a product selection that resonates with the target clientele, and ensuring a reliable supply chain for product replenishment.
Transportation
Airport beauty vending stations cater to the unique needs of travelers seeking convenience. By providing quick access to beauty essentials, these machines enhance the travel experience and can generate additional revenue for airport operators. International buyers should consider the durability of the machines, especially in high-traffic areas, and ensure that security features are robust to prevent theft or damage.
Events and Festivals
Mobile beauty vending machines are ideal for events and festivals, allowing brands to capitalize on high foot traffic. These machines enable on-the-spot sales, providing attendees with immediate access to products while increasing brand visibility. For B2B buyers, the focus should be on the portability of the machines, the variety of products offered, and the ease of operation to facilitate quick sales transactions.
Corporate Offices
Incorporating beauty vending machines in corporate offices promotes employee wellness and satisfaction by providing convenient access to beauty products during work hours. This not only enhances the work environment but also reinforces the company’s brand image. Buyers in this sector should prioritize product assortment that caters to diverse employee needs, machine design that complements the office aesthetic, and reliable maintenance services to ensure continuous operation.
Related Video: Sci6 Q3 – Characteristics and Uses of Simple Machines
Strategic Material Selection Guide for beauty vending machines
When selecting materials for beauty vending machines, it is essential to consider the unique requirements of the beauty and cosmetics industry, including aesthetics, durability, and functionality. Below, we analyze four common materials used in the construction of beauty vending machines, focusing on their properties, advantages, disadvantages, and specific considerations for international B2B buyers.
1. Stainless Steel
Key Properties: Stainless steel is known for its excellent corrosion resistance, high strength, and ability to withstand a wide range of temperatures. It is often rated for high-pressure applications, making it suitable for environments where durability is essential.
Pros & Cons:
– Advantages: Stainless steel is highly durable and resistant to rust and stains, making it ideal for beauty products that may spill or leak. It also has a sleek, modern appearance that enhances the aesthetic appeal of vending machines.
– Disadvantages: The primary drawback is its higher cost compared to other materials. Additionally, manufacturing processes can be complex, requiring specialized equipment and skills.
Impact on Application: Stainless steel is compatible with a variety of media, including liquids and powders. Its non-reactive nature ensures that beauty products remain uncontaminated.
Considerations for Buyers: International buyers should ensure compliance with food safety standards and certifications, such as ASTM and ISO, especially in regions like Europe and the Middle East where regulations can be stringent.
2. Acrylic
Key Properties: Acrylic is a lightweight, transparent thermoplastic that offers good impact resistance and clarity. It can be easily molded into various shapes and is available in a range of colors.
Pros & Cons:
– Advantages: Acrylic is cost-effective and allows for creative designs due to its versatility. It provides excellent visibility for products, enhancing customer engagement.
– Disadvantages: While it is impact-resistant, acrylic can scratch easily and is less durable than metals. It may also warp under high temperatures.
Impact on Application: Acrylic is suitable for displaying beauty products but may not be ideal for areas exposed to heat or direct sunlight.
Considerations for Buyers: Buyers should consider the environmental impact of acrylic and look for suppliers who adhere to sustainability practices. Compliance with local regulations regarding plastic use is also crucial, especially in regions with strict environmental laws.
3. Powder-Coated Steel
Key Properties: Powder-coated steel combines the strength of steel with a durable finish that is resistant to scratches, chipping, and fading. The coating process enhances the material’s corrosion resistance.
Pros & Cons:
– Advantages: This material is cost-effective and offers a wide range of color options, allowing for customization. The powder coating provides a protective layer that enhances durability.
– Disadvantages: If the coating is damaged, the underlying steel can be susceptible to rust. Additionally, the manufacturing process can be more complex than standard steel.
Impact on Application: Powder-coated steel is suitable for both indoor and outdoor applications, making it versatile for various environments.
Considerations for Buyers: Buyers should ensure that the powder coating meets industry standards for durability and environmental safety. Understanding local regulations regarding coatings and finishes is essential for compliance.
4. Glass
Key Properties: Glass is a non-porous, chemically resistant material that offers excellent clarity and aesthetic appeal. It can withstand high temperatures and is easy to clean.
Pros & Cons:
– Advantages: Glass provides a premium look and feel, enhancing the overall customer experience. It is also highly resistant to chemical reactions with beauty products.
– Disadvantages: Glass is fragile and can break easily, posing safety risks. It is also heavier than other materials, which may affect the design and transport of vending machines.
Impact on Application: Glass is ideal for showcasing products but requires careful handling and installation to prevent breakage.
Considerations for Buyers: International buyers should consider the shipping and handling costs associated with glass. Compliance with safety standards, such as tempered glass regulations, is also crucial, especially in regions with high safety expectations.
Summary Table
Material | Typical Use Case for beauty vending machines | Key Advantage | Key Disadvantage/Limitation | Relative Cost (Low/Med/High) |
---|---|---|---|---|
Stainless Steel | Structural components, exterior casing | Excellent durability and corrosion resistance | Higher cost, complex manufacturing | High |
Acrylic | Product display panels | Cost-effective, versatile design | Scratches easily, less durable than metals | Med |
Powder-Coated Steel | Framework and structural elements | Customizable colors, durable finish | Susceptible to rust if damaged | Low |
Glass | Product visibility and aesthetics | Premium look, chemically resistant | Fragile, heavier than alternatives | Med |
This strategic material selection guide provides valuable insights for international B2B buyers, enabling them to make informed decisions when sourcing materials for beauty vending machines.
In-depth Look: Manufacturing Processes and Quality Assurance for beauty vending machines
The manufacturing processes for beauty vending machines encompass several critical stages that ensure the final product is functional, aesthetically pleasing, and compliant with international standards. For international B2B buyers, particularly those from regions such as Africa, South America, the Middle East, and Europe, understanding these processes is essential for making informed purchasing decisions.
Manufacturing Processes
1. Material Preparation
The first step in the manufacturing of beauty vending machines involves the selection and preparation of materials. Common materials include:
- Metal: Often used for structural components, providing durability and stability.
- Plastic: Used for aesthetic parts and internal mechanisms due to its lightweight and customizable nature.
- Glass: Utilized for display sections, ensuring visibility of products.
Before fabrication, materials undergo rigorous quality checks to confirm they meet specified standards. This includes visual inspections and tests for durability and resilience.
2. Forming
Once materials are prepared, the forming stage begins. Key techniques used in this stage include:
- Stamping: Used to create metal panels and frames. This method allows for high precision and repeatability.
- Injection Molding: Commonly employed for plastic components, this technique ensures that complex shapes can be manufactured efficiently and consistently.
- Laser Cutting: Utilized for creating intricate designs and precise dimensions, especially in metal parts.
These processes are critical in shaping the individual components of the vending machine, which must fit together seamlessly.
3. Assembly
The assembly phase is where the various components come together to form the complete vending machine. This includes:
- Mechanical Assembly: Installing hardware such as locks, motors, and product dispensing mechanisms.
- Electrical Assembly: Wiring and integrating electronic components, including payment systems, display screens, and sensors.
- Software Integration: Programming the machine’s operating system to manage inventory, user interactions, and payment processing.
Efficient assembly practices often utilize techniques like lean manufacturing to minimize waste and enhance productivity.
4. Finishing
The final stage involves finishing touches that enhance both functionality and appearance. This may include:
- Surface Treatment: Applying coatings or paints to protect against corrosion and improve aesthetics.
- Quality Checks: Conducting thorough inspections to ensure all components function correctly and meet design specifications.
- Packaging: Preparing the machine for shipment, ensuring it is secured to prevent damage during transportation.
Quality Assurance
Quality assurance (QA) is vital in the manufacturing of beauty vending machines, ensuring that every unit produced meets international standards and customer expectations.
Relevant International Standards
For B2B buyers, understanding the applicable quality standards is crucial. Key standards include:
- ISO 9001: This international standard specifies requirements for a quality management system, ensuring consistent quality and continuous improvement.
- CE Marking: Required for products sold within the European Economic Area, indicating conformity with health, safety, and environmental protection standards.
- API Standards: Relevant for components that may interact with cosmetics or other health-related products, ensuring safety and efficacy.
Quality Control Checkpoints
Quality control (QC) checkpoints are strategically placed throughout the manufacturing process:
- Incoming Quality Control (IQC): Inspects raw materials upon arrival to ensure they meet specified standards.
- In-Process Quality Control (IPQC): Conducted during manufacturing to monitor processes and identify defects early.
- Final Quality Control (FQC): A comprehensive inspection of the finished product before it is packaged and shipped.
Each of these checkpoints is designed to capture and rectify defects at various stages, minimizing the risk of poor-quality products reaching the market.
Common Testing Methods
Testing methods play a significant role in quality assurance. Common methods include:
- Functional Testing: Ensures that all mechanical and electronic systems operate as intended.
- Durability Testing: Simulates long-term use to assess the machine’s resilience and performance over time.
- Safety Testing: Evaluates the machine for potential hazards, ensuring compliance with safety regulations.
Verification of Supplier Quality Control
B2B buyers can verify a supplier’s QC processes through several methods:
- Supplier Audits: Conducting on-site evaluations of the supplier’s facilities and processes to ensure they adhere to quality standards.
- Quality Reports: Requesting documentation that outlines the results of quality checks and testing throughout the manufacturing process.
- Third-Party Inspections: Engaging independent inspection agencies to evaluate the manufacturing process and the final product, providing an unbiased assessment of quality.
QC and Certification Nuances for International Buyers
International buyers, especially from diverse markets like Africa, South America, the Middle East, and Europe, must navigate various regulatory environments. Key considerations include:
- Understanding Local Regulations: Each region may have unique requirements for product safety and quality. Buyers should familiarize themselves with these to ensure compliance.
- Language and Communication: Ensuring clear communication with suppliers regarding quality expectations can prevent misunderstandings and enhance product outcomes.
- Cultural Sensitivity: Recognizing cultural differences in business practices can foster better relationships and improve negotiation outcomes.
By understanding these manufacturing processes and quality assurance practices, international B2B buyers can make more informed decisions, ensuring they select reliable suppliers that meet their quality expectations for beauty vending machines.
Related Video: Most Satisfying Factory Production Processes And Heavy-Duty Factory Machines!
Comprehensive Cost and Pricing Analysis for beauty vending machines Sourcing
When sourcing beauty vending machines, understanding the cost structure and pricing strategy is critical for international B2B buyers. This analysis delves into the various components that contribute to the overall cost and the factors influencing pricing, providing actionable insights for buyers, particularly from Africa, South America, the Middle East, and Europe.
Cost Components
-
Materials: The primary materials include steel, plastics, and electronic components. The choice of materials significantly affects durability and aesthetics. High-quality materials may increase initial costs but can enhance the machine’s lifespan and reduce long-term maintenance.
-
Labor: Labor costs can vary widely based on the location of the manufacturing facility. For instance, labor in regions like South Africa may be lower than in Europe, impacting overall production costs. Understanding local labor market conditions can aid in negotiating better pricing.
-
Manufacturing Overhead: This includes costs related to utilities, rent, and equipment maintenance. Efficient production processes can minimize overheads, which is crucial for maintaining competitive pricing.
-
Tooling: Customization often requires specialized tooling, which can lead to higher initial costs. However, these costs can be amortized over larger production runs, making them more manageable for bulk orders.
-
Quality Control (QC): Investing in robust QC processes ensures that the machines meet international standards and certifications, which is essential for markets in Europe and North America. While this may increase upfront costs, it can prevent costly recalls and reputational damage.
-
Logistics: Shipping costs, including freight and insurance, are substantial factors in total costs. Buyers should consider the implications of Incoterms (International Commercial Terms) when negotiating contracts, as they dictate who is responsible for shipping, insurance, and tariffs.
-
Margin: Manufacturers typically apply a profit margin that can range from 10% to 30% depending on the market dynamics and competition. Understanding the manufacturer’s cost structure can help in negotiating a fair price.
Price Influencers
-
Volume/MOQ: Minimum order quantities (MOQ) can significantly impact pricing. Larger orders usually lead to lower per-unit costs due to economies of scale. Buyers should assess their demand forecasts to negotiate better terms.
-
Specifications/Customization: Custom features or specific branding requirements can increase costs. Buyers should balance the need for customization with budget constraints, as bespoke solutions often come at a premium.
-
Materials and Quality Certifications: The choice of materials and the presence of certifications (like ISO or CE) can influence both cost and price. Products with higher quality certifications may attract a higher price but can also lead to better market acceptance.
-
Supplier Factors: The reliability and reputation of the supplier can impact pricing. Established suppliers may charge more due to their track record and quality assurance, while newer entrants might offer lower prices to gain market share.
Buyer Tips
-
Negotiation: Effective negotiation strategies can lead to significant cost savings. Buyers should prepare by researching market prices and understanding the supplier’s cost structure.
-
Cost-Efficiency: Evaluate the total cost of ownership (TCO) rather than just the purchase price. Consider maintenance, operational costs, and potential resale value to make informed decisions.
-
Pricing Nuances for International Buyers: Understanding local market conditions, currency fluctuations, and trade tariffs is crucial for international buyers. Engaging with local experts can provide insights into navigating these complexities.
-
Disclaimer for Indicative Prices: It is essential for buyers to note that prices can fluctuate based on market conditions, changes in material costs, and other external factors. Always seek updated quotes before finalizing any purchases.
By being aware of these cost components and price influencers, B2B buyers can make more informed decisions when sourcing beauty vending machines, ensuring they achieve the best possible value for their investment.
Spotlight on Potential beauty vending machines Manufacturers and Suppliers
This section offers a look at a few manufacturers active in the ‘beauty vending machines’ market. This is a representative sample for illustrative purposes; B2B buyers must conduct their own extensive due diligence before any engagement. Information is synthesized from public sources and general industry knowledge.
Essential Technical Properties and Trade Terminology for beauty vending machines
Key Technical Properties of Beauty Vending Machines
Understanding the essential technical properties of beauty vending machines is crucial for B2B buyers, especially those looking to invest in this innovative retail solution. Here are several critical specifications to consider:
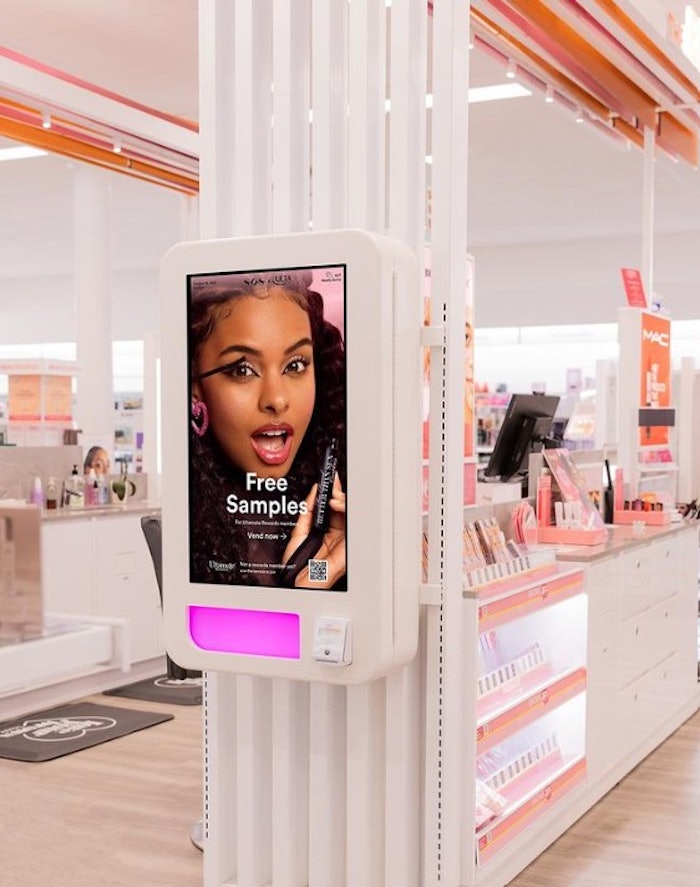
Illustrative Image (Source: Google Search)
-
Material Grade
– Definition: The quality of materials used in the construction of the vending machine, often indicated by standards such as stainless steel (AISI 304 or 316) or high-grade plastics.
– Importance: Higher-grade materials ensure durability, resistance to corrosion, and a longer lifespan, which is essential for machines placed in high-traffic areas. -
Temperature Control Range
– Definition: The operational temperature range within which the machine can effectively store products without compromising their quality, typically between 0°C to 25°C.
– Importance: For cosmetics and skincare products, maintaining the right temperature is vital to prevent spoilage or degradation, ensuring product efficacy and customer satisfaction. -
Power Consumption
– Definition: The amount of electrical energy the machine requires to operate, usually measured in watts.
– Importance: Lower power consumption translates to reduced operational costs, which is particularly important for businesses in regions with high energy prices. Additionally, energy-efficient machines can enhance brand reputation. -
User Interface Technology
– Definition: The type of display and interaction mechanism used, such as touchscreens, QR code scanning, or mobile app integration.
– Importance: An intuitive user interface enhances customer experience, making it easier for users to browse products and complete purchases, which can lead to increased sales.
-
Storage Capacity
– Definition: The total number of products the machine can hold, often categorized by size and type of product.
– Importance: Understanding storage capacity helps businesses assess the machine’s suitability for their target market and sales volume, ensuring that popular items are always available. -
Payment Options
– Definition: The variety of payment methods accepted by the vending machine, including credit/debit cards, mobile wallets, and cash.
– Importance: A wider range of payment options can attract more customers, particularly in diverse markets where payment preferences vary significantly.
Common Trade Terminology
Familiarity with industry terminology is crucial for effective communication and negotiation in the B2B space. Here are some common terms related to beauty vending machines:
-
OEM (Original Equipment Manufacturer)
– Definition: A company that produces parts or equipment that may be marketed by another manufacturer.
– Usage: Buyers may choose to work with OEMs for customized vending machines tailored to specific branding needs. -
MOQ (Minimum Order Quantity)
– Definition: The smallest quantity of a product that a supplier is willing to sell.
– Usage: Understanding MOQ is critical for buyers to plan their budgets and inventory effectively, especially when entering new markets. -
RFQ (Request for Quotation)
– Definition: A document issued by a buyer to request price quotes from suppliers for specific products or services.
– Usage: An RFQ helps streamline the procurement process, allowing buyers to compare costs and terms from multiple vendors. -
Incoterms (International Commercial Terms)
– Definition: A set of predefined international rules that clarify the responsibilities of buyers and sellers in international transactions.
– Usage: Familiarity with Incoterms helps buyers understand shipping responsibilities, risks, and costs, essential for successful cross-border transactions. -
Lead Time
– Definition: The amount of time from placing an order until the product is delivered.
– Usage: Knowing the lead time is vital for inventory management and ensuring timely availability of products for customers.
- Warranty Period
– Definition: The duration during which the manufacturer guarantees the machine against defects in materials or workmanship.
– Usage: Understanding warranty terms can help buyers assess the reliability of the product and the potential costs of maintenance or replacement.
Incorporating this knowledge into your purchasing decisions can lead to more informed and strategic investments in beauty vending machines, ultimately enhancing your business’s operational efficiency and customer satisfaction.
Navigating Market Dynamics, Sourcing Trends, and Sustainability in the beauty vending machines Sector
Market Overview & Key Trends
The beauty vending machine sector is witnessing significant transformation driven by technological advancements and changing consumer behaviors. Globally, the demand for convenience and on-the-go beauty solutions is propelling the growth of this market. International B2B buyers, particularly in regions like Africa, South America, the Middle East, and Europe, are increasingly interested in integrating beauty vending machines into their retail strategies. This trend is fueled by the rise of e-commerce, mobile payment solutions, and digital marketing, which enhance customer engagement and streamline purchasing processes.
Emerging technologies such as AI and machine learning are being leveraged to personalize consumer experiences. For instance, some vending machines now utilize facial recognition to recommend products tailored to individual skin types. Additionally, touchless payment systems have become essential, especially in a post-pandemic world where hygiene is a priority. Buyers should look for machines equipped with smart inventory management systems that provide real-time data analytics, ensuring optimal stock levels and minimizing waste.
Market dynamics are also influenced by regional preferences. In Africa, for example, the growing middle class is driving demand for affordable, quality beauty products. In contrast, European markets are leaning towards premium offerings, with a strong emphasis on luxury brands. Understanding these local nuances is crucial for B2B buyers aiming to make informed sourcing decisions.
Sustainability & Ethical Sourcing in B2B
As environmental concerns become paramount, sustainability in the beauty vending machine sector is gaining traction. Buyers are increasingly prioritizing suppliers that adhere to ethical sourcing practices, emphasizing the importance of transparent supply chains. This includes sourcing ingredients from sustainable farms and ensuring fair labor practices throughout the production process.
The use of eco-friendly materials in the construction of vending machines is another vital consideration. Machines designed with recyclable materials not only appeal to environmentally conscious consumers but also align with global sustainability goals. Certifications such as FSC (Forest Stewardship Council) and Cradle to Cradle can serve as indicators of a supplier’s commitment to sustainability.
Moreover, brands that actively engage in reducing their carbon footprint through initiatives like energy-efficient machines or solar-powered units are gaining competitive advantages. B2B buyers should prioritize partnerships with companies that demonstrate a commitment to sustainability, as this not only enhances brand reputation but also resonates with a growing segment of environmentally-conscious consumers.
Brief Evolution/History
The concept of vending machines dates back to the early 1880s, primarily offering products like cigarettes and candy. However, the beauty vending machine sector has evolved significantly over the past two decades. The introduction of technology has transformed these machines from simple dispensers into sophisticated retail units capable of delivering a wide range of beauty products.
The rise of e-commerce and mobile technology has further accelerated this evolution, enabling brands to reach consumers directly through vending machines located in high-traffic areas. As urbanization continues to grow, especially in developing regions, the demand for accessible beauty solutions through vending machines is expected to increase. This evolution presents B2B buyers with unique opportunities to invest in innovative retail solutions that cater to a diverse and growing consumer base.
Related Video: Is global trade transforming? | Counting the Cost
Frequently Asked Questions (FAQs) for B2B Buyers of beauty vending machines
-
What should I look for when vetting suppliers of beauty vending machines?
When vetting suppliers, prioritize companies with a proven track record in the beauty industry. Assess their experience by reviewing client testimonials and case studies. Ensure they possess necessary certifications, such as ISO or CE, which indicate adherence to quality and safety standards. Additionally, check their financial stability and request samples of their machines to evaluate quality firsthand. Engaging in direct communication can also provide insights into their reliability and customer service. -
Can I customize beauty vending machines to fit my brand?
Yes, many suppliers offer customization options for beauty vending machines. You can typically request modifications in terms of color, branding, and product selection. Ensure you communicate your specific needs during the initial discussions. It’s advisable to ask for a design mock-up before production begins to avoid any discrepancies. Customization can help align the vending machine with your brand image, enhancing customer recognition and engagement. -
What is the minimum order quantity (MOQ) for beauty vending machines, and what are the typical lead times?
MOQs for beauty vending machines can vary widely among suppliers, ranging from 5 to 50 units depending on the manufacturer. It’s crucial to clarify this early in negotiations. Typical lead times can also differ based on the complexity of the order and customization requests, usually ranging from 4 to 12 weeks. Always confirm these details and factor in potential delays related to international shipping, especially if you are sourcing from different continents. -
What payment terms should I expect when ordering beauty vending machines?
Payment terms can differ based on supplier policies and your negotiation leverage. Common arrangements include a 30% deposit upfront with the balance due before shipment. Some suppliers may offer flexible terms, such as letters of credit or payment upon delivery, especially for larger orders. Always ensure that payment methods are secure and documented to protect your investment. It’s also wise to discuss currency fluctuations if dealing with international suppliers. -
How can I ensure quality assurance (QA) and compliance with certifications?
To ensure QA, inquire about the supplier’s quality control processes and whether they conduct regular inspections during production. Request copies of relevant certifications that comply with international standards, such as ISO 9001 for quality management. Additionally, consider third-party inspections before shipment to verify that the machines meet your specifications and industry regulations. Documenting these processes can help mitigate risks associated with quality issues. -
What logistics considerations should I be aware of when importing beauty vending machines?
Logistics play a crucial role in the successful importation of beauty vending machines. Consider the shipping methods, customs duties, and potential tariffs that may apply to your order. Engage with logistics providers experienced in handling similar goods to ensure proper handling and timely delivery. It’s also beneficial to track shipments and maintain communication with your supplier to address any unforeseen delays or issues during transport. -
How should I handle disputes with suppliers?
To effectively manage disputes, establish clear contracts that outline terms, conditions, and expectations. If issues arise, initiate open communication with the supplier to resolve the matter amicably. Document all correspondence and agreements for reference. If necessary, escalate the issue to mediation or arbitration, as specified in your contract. Understanding the legal framework for international trade in your respective countries can also provide guidance on resolving disputes. -
What factors should I consider for product selection in beauty vending machines?
When selecting products for your beauty vending machines, consider market trends and customer preferences in your target regions. Conduct market research to identify popular beauty items and their price points. Diversifying the product range can attract a broader customer base. Additionally, ensure that the products have a reasonable shelf life and comply with local regulations. Partnering with reputable beauty brands can enhance credibility and attract more customers to your vending machines.
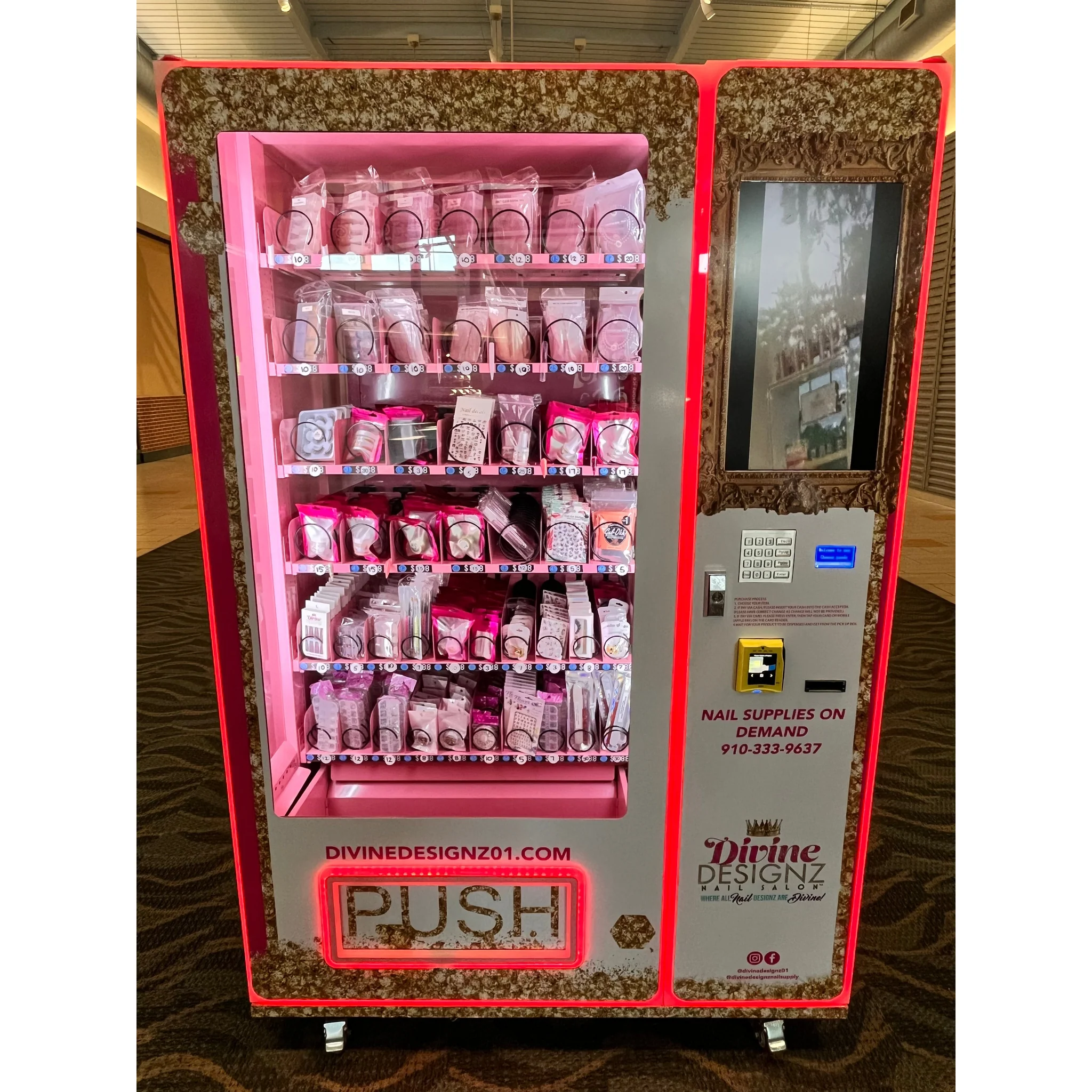
Illustrative Image (Source: Google Search)
Strategic Sourcing Conclusion and Outlook for beauty vending machines
In conclusion, the strategic sourcing of beauty vending machines presents a unique opportunity for international B2B buyers, especially those operating in emerging markets across Africa, South America, the Middle East, and Europe. By leveraging localized supply chains, businesses can enhance their operational efficiency while ensuring they meet the diverse demands of consumers in these regions. Key takeaways include the importance of evaluating suppliers based on quality, price, and service, as well as the need for adaptability in sourcing strategies to align with market trends.
Investing in beauty vending machines not only opens new revenue streams but also elevates brand visibility and accessibility. As consumer preferences continue to evolve towards convenience and personalization, the demand for automated retail solutions will only grow.
B2B buyers are encouraged to conduct thorough market research and engage with suppliers who demonstrate innovative approaches and robust support systems. By doing so, you can position your business for success in this dynamic landscape. Embrace the potential of beauty vending machines and take actionable steps today to capitalize on this expanding market.