Your Ultimate Guide to Sourcing Avenue C Vending Machines
Guide to Avenue C Vending Machines
- Introduction: Navigating the Global Market for avenue c vending machines
- Understanding avenue c vending machines Types and Variations
- Key Industrial Applications of avenue c vending machines
- Strategic Material Selection Guide for avenue c vending machines
- In-depth Look: Manufacturing Processes and Quality Assurance for avenue c vending machines
- Comprehensive Cost and Pricing Analysis for avenue c vending machines Sourcing
- Spotlight on Potential avenue c vending machines Manufacturers and Suppliers
- Essential Technical Properties and Trade Terminology for avenue c vending machines
- Navigating Market Dynamics, Sourcing Trends, and Sustainability in the avenue c vending machines Sector
- Frequently Asked Questions (FAQs) for B2B Buyers of avenue c vending machines
- Strategic Sourcing Conclusion and Outlook for avenue c vending machines
Introduction: Navigating the Global Market for avenue c vending machines
In an increasingly competitive marketplace, Avenue C vending machines stand out as a transformative solution for businesses aiming to enhance customer experience and streamline operations. These advanced vending systems not only offer a diverse range of products but also incorporate cutting-edge technology that caters to the evolving demands of consumers. For international B2B buyers, particularly those from Africa, South America, the Middle East, and Europe, understanding the nuances of Avenue C vending machines is crucial for making informed purchasing decisions.
This guide provides a comprehensive overview of the Avenue C vending machine landscape, including types of machines, materials used, and manufacturing and quality control standards. We will delve into supplier options, analyze cost considerations, and explore the broader market trends influencing this sector. Furthermore, a dedicated FAQ section will address common queries, ensuring that buyers have all the information needed to navigate their purchasing journey confidently.
By equipping buyers with actionable insights and a thorough understanding of Avenue C vending machines, this guide empowers stakeholders to make strategic sourcing decisions that align with their business goals. Whether you are looking to invest in new vending solutions or enhance existing operations, this resource will serve as your roadmap to success in the global market.
Understanding avenue c vending machines Types and Variations
Type Name | Key Distinguishing Features | Primary B2B Applications | Brief Pros & Cons for Buyers |
---|---|---|---|
Traditional Vending | Standard snack and beverage options | Offices, schools, public spaces | Pros: Easy to use; Cons: Limited product range. |
Smart Vending | Touchscreen interface with cashless payment | Corporate environments, gyms | Pros: Enhanced user experience; Cons: Higher cost. |
Micro Market | Self-service kiosks with a variety of items | Employee break rooms, convenience | Pros: Flexible inventory; Cons: Requires management. |
Healthy Vending | Focus on nutritious snacks and drinks | Health-focused organizations | Pros: Meets dietary needs; Cons: Higher pricing. |
Customized Vending | Tailored selections based on location and demand | Specialty retail, events | Pros: Increased sales potential; Cons: Complexity in setup. |
Traditional Vending
Traditional vending machines are the most recognizable type, offering a selection of snacks and beverages. These machines are suitable for various environments, including offices, schools, and public spaces. When considering a purchase, B2B buyers should evaluate the machine’s capacity, ease of restocking, and the variety of products it can accommodate. While these machines are user-friendly and require minimal maintenance, their limited product offerings may not meet the diverse needs of modern consumers.
Smart Vending
Smart vending machines incorporate advanced technology, such as touchscreens and cashless payment options, making them ideal for corporate environments and gyms. These machines enhance the consumer experience by providing interactive interfaces and real-time inventory tracking. B2B buyers should consider the initial investment costs and the potential for higher returns through improved customer engagement. However, the sophisticated technology can lead to increased maintenance requirements and operational costs.
Micro Market
Micro markets consist of self-service kiosks that offer a broader range of products, including fresh food and beverages. These setups are commonly found in employee break rooms and convenience stores. Buyers interested in micro markets should assess the level of management required, as they often necessitate regular inventory checks and restocking. Their flexibility in inventory allows businesses to cater to specific customer preferences, but they also require a higher initial investment and ongoing operational oversight.
Healthy Vending
Healthy vending machines focus on providing nutritious snacks and beverages, catering to health-conscious consumers. These machines are ideal for health-focused organizations, such as gyms and wellness centers. When purchasing, B2B buyers should evaluate the variety and quality of healthy options available, as well as the potential for higher pricing. While healthy vending can attract a niche market, it may not appeal to all demographics, potentially limiting sales opportunities.
Customized Vending
Customized vending machines allow businesses to tailor their product offerings based on location and consumer demand. This flexibility makes them suitable for specialty retail environments and events. B2B buyers should consider the complexity involved in setting up these machines, including sourcing products and managing inventory. While customized vending can lead to increased sales by meeting specific customer needs, it requires careful planning and management to ensure success.
Related Video: CS 198-126: Lecture 12 – Diffusion Models
Key Industrial Applications of avenue c vending machines
Industry/Sector | Specific Application of avenue c vending machines | Value/Benefit for the Business | Key Sourcing Considerations for this Application |
---|---|---|---|
Corporate Offices | Employee snack and beverage provision | Enhances employee satisfaction and productivity | Need for reliable supply chains and local product preferences |
Educational Institutions | Student meal and snack options | Provides convenient access to food, reducing downtime | Consideration of nutritional value and pricing for students |
Healthcare Facilities | Patient and staff nourishment | Improves overall health outcomes through accessible nutrition | Compliance with health regulations and dietary requirements |
Manufacturing Plants | Quick access to refreshments for workers | Boosts morale and reduces time away from work | Robustness and reliability under high-traffic conditions |
Transportation Hubs | 24/7 access to food and beverages for travelers | Meets diverse customer needs and generates additional revenue | Variety of product offerings and payment system compatibility |
Corporate Offices
In corporate environments, avenue c vending machines serve as an essential solution for providing employees with snacks and beverages. By offering a variety of healthy and indulgent options, these machines enhance employee satisfaction and productivity. For international B2B buyers, it is crucial to ensure that vending machines can accommodate local tastes and dietary preferences while maintaining a reliable supply chain for consistent product availability.
Educational Institutions
Avenue c vending machines in educational settings offer students quick access to meals and snacks, which is vital for maintaining energy levels throughout the day. By reducing downtime spent searching for food options, these machines contribute to a more efficient learning environment. Buyers from educational institutions should consider the nutritional value of the offerings, as well as pricing strategies that cater to budget-conscious students.
Healthcare Facilities
In healthcare settings, avenue c vending machines can provide nourishment for both patients and staff. By ensuring easy access to healthy food options, these machines play a significant role in improving overall health outcomes. Buyers in this sector must prioritize compliance with health regulations, focusing on dietary requirements and ensuring that products cater to various health needs, such as gluten-free or low-sugar options.
Manufacturing Plants
Manufacturing plants benefit from the installation of avenue c vending machines, which provide quick access to refreshments for workers. This convenience boosts employee morale and minimizes the time workers spend away from their tasks. B2B buyers in this sector should consider the robustness of the machines, ensuring they can withstand high-traffic conditions and operate efficiently in potentially harsh environments.
Transportation Hubs
Avenue c vending machines in transportation hubs, such as airports and bus stations, offer 24/7 access to food and beverages for travelers. This not only meets diverse customer needs but also generates additional revenue for the facility. International buyers should focus on the variety of product offerings and ensure compatibility with various payment systems, including mobile payment options, to enhance user experience and convenience.
Related Video: Sci6 Q3 – Characteristics and Uses of Simple Machines
Strategic Material Selection Guide for avenue c vending machines
When selecting materials for Avenue C vending machines, it is essential to consider properties that affect performance, durability, and cost-effectiveness. Here, we analyze four common materials used in the construction of these machines, highlighting their key properties, advantages, disadvantages, and specific considerations for international B2B buyers.
Stainless Steel
Key Properties:
Stainless steel is known for its excellent corrosion resistance, high strength-to-weight ratio, and ability to withstand extreme temperatures. It typically has a temperature rating of up to 800°F (427°C) and can handle significant pressure variations.
Pros & Cons:
Stainless steel is highly durable and easy to clean, making it suitable for food and beverage applications. However, it tends to be more expensive than other materials and can be complex to manufacture due to its hardness.
Impact on Application:
This material is ideal for external panels and internal components that come into contact with food products, ensuring hygiene and compliance with health standards.
Considerations for International Buyers:
Buyers from regions like Europe and the Middle East should ensure compliance with local food safety regulations. Standards such as ASTM A240 for stainless steel grades are crucial for ensuring quality.
Aluminum
Key Properties:
Aluminum is lightweight, corrosion-resistant, and has a good strength-to-weight ratio. It can typically withstand temperatures up to 400°F (204°C) and is less susceptible to thermal expansion compared to other metals.
Pros & Cons:
Aluminum is cost-effective and easy to fabricate, making it a popular choice for many components. However, it is less durable than stainless steel and may dent or scratch easily.
Impact on Application:
Aluminum is often used for internal structures and non-load-bearing parts of vending machines, where weight savings are critical.
Considerations for International Buyers:
In regions like South America and Africa, where environmental conditions may vary, buyers should consider the local availability of aluminum grades that meet specific standards, such as ASTM B221.
Polycarbonate
Key Properties:
Polycarbonate is a high-performance thermoplastic known for its impact resistance and transparency. It can withstand temperatures up to 270°F (132°C) and has excellent UV resistance.
Pros & Cons:
Polycarbonate is lightweight and provides good insulation properties. However, it can be more expensive than other plastics and may yellow over time when exposed to UV light.
Impact on Application:
This material is often used for display panels and protective covers in vending machines, where visibility of products is essential.
Considerations for International Buyers:
Buyers should ensure that the polycarbonate used complies with local standards for safety and environmental impact, particularly in Europe, where regulations on plastics are stringent.
Mild Steel
Key Properties:
Mild steel is a low-carbon steel known for its good weldability and ductility. It can handle moderate temperatures and pressures but has limited corrosion resistance unless treated.
Pros & Cons:
Mild steel is cost-effective and easy to manufacture, making it suitable for structural components. However, it is prone to rusting and may require protective coatings, which can increase maintenance costs.
Impact on Application:
This material is often used for the framework and internal structures of vending machines, where strength is necessary but exposure to corrosive environments is limited.
Considerations for International Buyers:
For buyers in humid climates, such as parts of Africa and South America, it is crucial to consider the need for protective coatings to prevent corrosion. Compliance with local standards, such as DIN 10130 in Europe, is also important.
Summary Table
Material | Typical Use Case for avenue c vending machines | Key Advantage | Key Disadvantage/Limitation | Relative Cost (Low/Med/High) |
---|---|---|---|---|
Stainless Steel | External panels, food contact components | Excellent corrosion resistance | Higher cost, complex manufacturing | High |
Aluminum | Internal structures, non-load-bearing parts | Lightweight, cost-effective | Less durable, prone to dents | Medium |
Polycarbonate | Display panels, protective covers | Impact-resistant, good visibility | More expensive, UV degradation | Medium |
Mild Steel | Framework, internal structures | Cost-effective, easy to manufacture | Prone to rust, requires protective coatings | Low |
This strategic material selection guide aims to assist international B2B buyers in making informed decisions regarding the materials used in Avenue C vending machines, considering both performance and regional compliance.
In-depth Look: Manufacturing Processes and Quality Assurance for avenue c vending machines
Manufacturing Processes for Avenue C Vending Machines
The manufacturing of Avenue C vending machines is a complex process that ensures the delivery of high-quality, reliable products for international markets. Understanding these processes can help B2B buyers make informed decisions when sourcing these machines.
Key Stages of Manufacturing
-
Material Preparation
– The first step involves sourcing high-quality materials such as steel, plastics, and electronic components. Suppliers are selected based on their ability to provide materials that meet international quality standards.
– Materials undergo rigorous testing for durability and compliance with regulations to ensure they can withstand various environmental conditions, especially for regions in Africa and South America where climate factors may be a concern. -
Forming
– This stage involves the shaping of materials using techniques such as stamping, molding, and machining. Advanced CNC machines are often employed to ensure precision in the manufacturing process.
– Automation plays a significant role in this stage, enhancing efficiency and consistency, which is crucial for meeting the demands of large-scale production. -
Assembly
– The assembly process combines various components, including the vending machine’s mechanical, electrical, and software systems. This step is critical as it directly affects the machine’s functionality and user experience.
– Employing lean manufacturing principles can help minimize waste and improve efficiency during assembly. Teams are trained to adhere to strict guidelines to ensure every unit meets the same high standards. -
Finishing
– This final stage includes surface treatments, painting, and quality checks before the machines are packaged for shipment. Finishing processes are tailored to enhance the aesthetic appeal and longevity of the machines, vital for attracting customers in diverse markets.
– The finishing touches also involve the installation of branding elements, which can be customized based on the buyer’s specifications, providing an opportunity for branding and market differentiation.
Quality Assurance in Manufacturing
Quality assurance (QA) is a critical aspect of the manufacturing process for Avenue C vending machines. A robust QA framework not only ensures compliance with international standards but also builds trust with B2B buyers.
International Standards and Compliance
- ISO 9001: This standard focuses on quality management systems and is essential for manufacturers to demonstrate their commitment to continuous improvement and customer satisfaction.
- CE Marking: For European markets, CE marking indicates compliance with health, safety, and environmental protection standards. This is particularly relevant for buyers in Germany and other EU countries.
- API Standards: In markets like the Middle East, adherence to API standards can be crucial, especially if the machines are integrated into environments involving oil and gas sectors.
Quality Control Checkpoints
-
Incoming Quality Control (IQC)
– This checkpoint involves assessing the quality of raw materials and components before they enter the production line. Regular audits of suppliers are recommended to ensure they meet specified standards. -
In-Process Quality Control (IPQC)
– IPQC involves monitoring the manufacturing process in real-time. This includes inspections at various stages to identify defects early, ensuring that issues are addressed before moving to the next phase. -
Final Quality Control (FQC)
– At this stage, completed vending machines undergo thorough testing to verify they meet all specifications and performance standards. This includes functional testing, safety checks, and aesthetic inspections.
Common Testing Methods
- Functional Testing: Ensures that all components operate as intended, including payment systems, refrigeration units, and user interfaces.
- Durability Testing: Machines are subjected to stress tests to assess their resilience against wear and tear, particularly important for buyers in regions with extreme weather conditions.
- Compliance Testing: Machines are evaluated against relevant safety and environmental standards to ensure they are fit for market entry in different regions.
Verifying Supplier Quality Control
For international B2B buyers, especially in Africa, South America, the Middle East, and Europe, verifying a supplier’s quality control processes is crucial.
- Supplier Audits: Regular audits can help assess a supplier’s adherence to quality standards. Buyers should request audit reports and certifications to ensure compliance with relevant standards.
- Quality Reports: Suppliers should provide detailed quality reports that outline testing methods, results, and any corrective actions taken. This transparency is essential for building trust.
- Third-Party Inspections: Engaging third-party inspection services can provide an unbiased assessment of the manufacturing process and product quality. This is particularly beneficial for buyers unfamiliar with local suppliers.
Quality Control Nuances for International Buyers
Understanding the nuances of quality control is vital for B2B buyers from different regions.
- Cultural Differences: Recognize that quality expectations may vary between markets. For instance, European buyers may have stricter compliance standards compared to some African or South American markets.
- Regulatory Challenges: Buyers should be aware of the specific regulations that apply in their region, which may affect the quality assurance processes of suppliers.
- Communication Barriers: Clear communication regarding quality expectations is essential. Buyers should ensure that language barriers do not impede understanding of quality standards and requirements.
In summary, a deep understanding of the manufacturing processes and quality assurance protocols for Avenue C vending machines empowers B2B buyers to make informed sourcing decisions. By focusing on quality at every stage of the production process and ensuring compliance with international standards, buyers can ensure they invest in reliable, high-quality vending solutions that meet their specific market needs.
Related Video: SMART Quality Control for Manufacturing
Comprehensive Cost and Pricing Analysis for avenue c vending machines Sourcing
Cost Structure of Avenue C Vending Machines
When considering the sourcing of Avenue C vending machines, it is crucial to understand the various cost components that contribute to the overall price. The primary elements include:
-
Materials: The quality and type of materials used in the construction of vending machines significantly impact cost. High-grade metals, plastics, and electronic components are essential for durability and functionality.
-
Labor: Labor costs can vary widely depending on the manufacturing location. In regions like Africa and South America, labor may be less expensive, but quality control and skilled labor availability should be assessed.
-
Manufacturing Overhead: This includes costs related to utilities, facility maintenance, and administrative expenses. Understanding the manufacturer’s operational efficiency can provide insights into potential cost savings.
-
Tooling: Initial tooling costs for custom designs or modifications can be substantial. Buyers should evaluate whether the investment aligns with their expected volume and long-term use.
-
Quality Control (QC): Ensuring that the machines meet safety and operational standards incurs additional costs. Buyers should consider the certification requirements specific to their regions, which may necessitate more rigorous QC processes.
-
Logistics: Shipping costs are a significant factor, especially for international buyers. Factors such as distance, mode of transport, and customs fees can greatly influence the total cost.
-
Margin: Suppliers typically include a profit margin in their pricing, which can vary based on market conditions and competition.
Price Influencers
Several key influencers affect the pricing of Avenue C vending machines:
-
Volume/MOQ (Minimum Order Quantity): Bulk purchases often lead to discounts. Buyers should negotiate to meet their requirements while maximizing cost-efficiency.
-
Specifications/Customization: Custom features can increase costs. Buyers need to clearly define their specifications to avoid unnecessary expenses.
-
Materials and Quality Certifications: Higher quality materials and certifications can raise prices. However, they may also result in lower maintenance costs and longer lifespan.
-
Supplier Factors: The reputation and reliability of the supplier can influence pricing. Established suppliers may charge a premium but often provide better service and warranty options.
-
Incoterms: Understanding the shipping terms is crucial. Different Incoterms (e.g., FOB, CIF) can alter the total cost and risk associated with the shipment.
Buyer Tips for International B2B Sourcing
-
Negotiate Effectively: Leverage your purchasing power, especially if considering bulk orders. Establishing a good relationship with suppliers can also lead to better terms and pricing.
-
Focus on Total Cost of Ownership (TCO): Evaluate not just the purchase price but also the long-term operational costs, including maintenance, energy consumption, and potential downtime.
-
Understand Pricing Nuances: Each region may have different pricing models and expectations. Buyers from Europe, for instance, may encounter stricter regulations compared to those in Africa or South America, affecting overall costs.
-
Conduct Market Research: Stay informed about market trends and pricing fluctuations. Engaging with industry groups or local trade associations can provide valuable insights.
-
Evaluate Supplier Locations: Consider sourcing from suppliers in regions with favorable trade agreements or lower tariffs to optimize costs.
-
Request Detailed Quotes: Ensure that all quotes include a breakdown of costs to facilitate comparison and negotiation.
Disclaimer
Prices for Avenue C vending machines can vary widely based on the factors discussed above. Buyers should conduct thorough due diligence and consider obtaining multiple quotes to ensure competitive pricing that aligns with their specific needs.
Spotlight on Potential avenue c vending machines Manufacturers and Suppliers
- (No specific manufacturer data was available or requested for detailed profiling in this section for avenue c vending machines.)*
Essential Technical Properties and Trade Terminology for avenue c vending machines
When considering avenue c vending machines, understanding their essential technical properties and trade terminology is crucial for making informed purchasing decisions. This knowledge not only aids in selecting the right equipment but also enhances negotiation strategies and overall operational efficiency.
Key Technical Properties
-
Material Grade
– Avenue c vending machines are typically constructed from high-grade stainless steel or durable plastics. The choice of material impacts the machine’s longevity, maintenance needs, and resistance to environmental factors. Buyers should prioritize machines made from corrosion-resistant materials, especially in humid climates, to ensure durability and reduce long-term costs. -
Capacity
– The capacity of a vending machine refers to the number of items it can hold, which is critical for determining its suitability for different locations. A higher capacity machine is essential in high-traffic areas to minimize restocking frequency. For B2B buyers, understanding the expected foot traffic and consumption patterns will help in selecting the right capacity to maximize revenue. -
Power Consumption
– This specification indicates how much energy the machine requires to operate. Machines with lower power consumption can lead to significant cost savings over time, especially in regions where electricity costs are high. B2B buyers should consider energy-efficient models that comply with local energy regulations, as this can also enhance the brand’s sustainability profile.
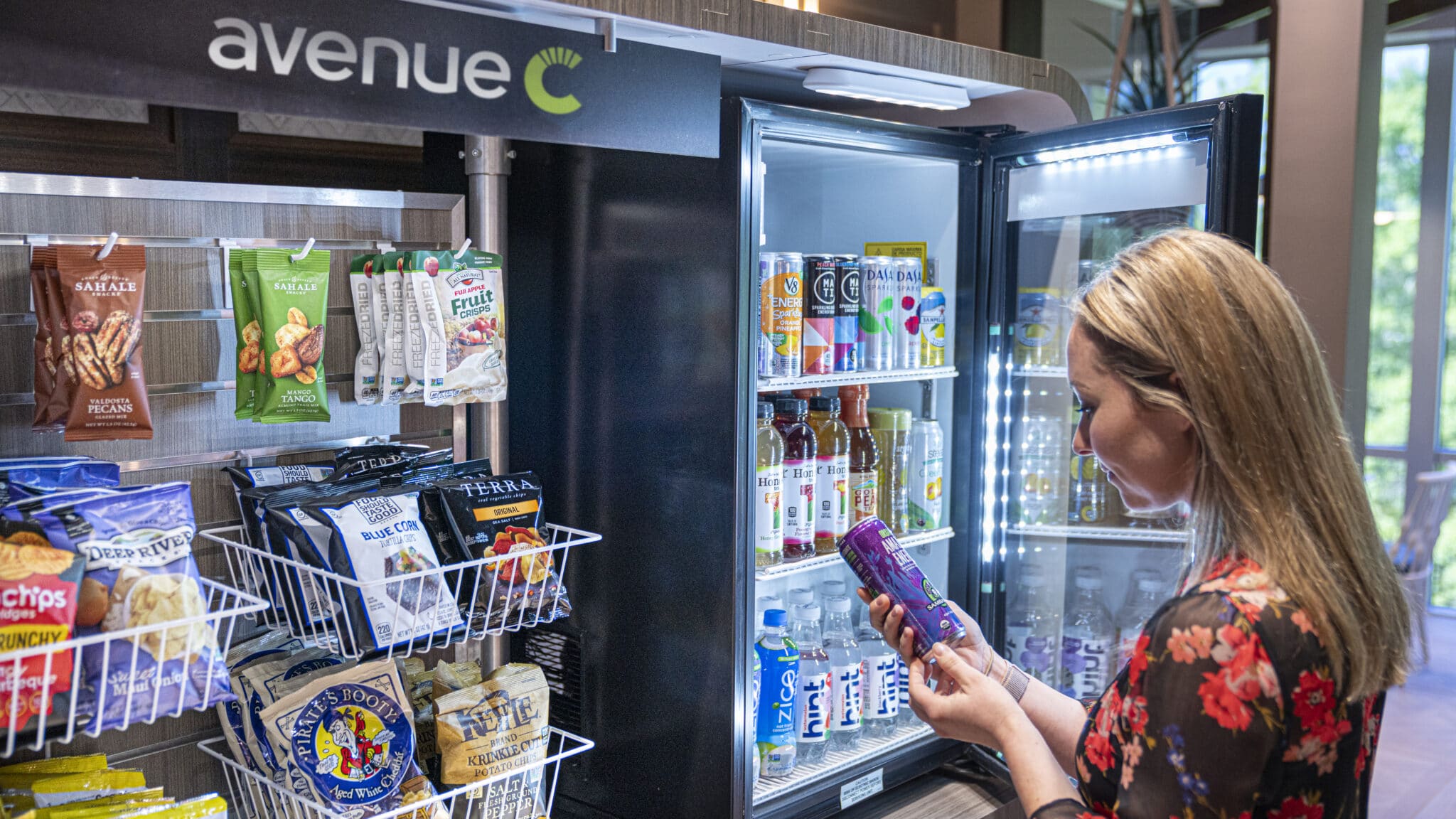
Illustrative Image (Source: Google Search)
-
Connectivity Options
– Avenue c vending machines often feature advanced connectivity options, such as Wi-Fi or cellular connections. These capabilities enable remote monitoring, inventory management, and cashless payment options. For international buyers, understanding the connectivity infrastructure in their region is vital to leverage these features effectively and enhance operational efficiency. -
Temperature Control
– For machines that dispense perishable goods, temperature control is a critical property. This feature ensures that items remain fresh and safe for consumption. Buyers should assess the temperature range and stability of the machine, especially in warmer climates, to maintain product quality and reduce waste. -
User Interface
– The user interface includes the display, payment systems, and overall ease of use. A well-designed interface can enhance customer experience and increase sales. B2B buyers should consider machines with intuitive interfaces and diverse payment options, including mobile wallets, to cater to varying customer preferences.
Common Trade Terminology
-
OEM (Original Equipment Manufacturer)
– An OEM refers to a company that produces parts and equipment that may be marketed by another manufacturer. Understanding this term is essential for buyers looking to source components or machines directly from manufacturers to ensure quality and compatibility. -
MOQ (Minimum Order Quantity)
– This term indicates the smallest quantity of a product that a supplier is willing to sell. Knowing the MOQ is critical for budget planning and inventory management, especially for international buyers who may face higher shipping costs if they order below the MOQ. -
RFQ (Request for Quotation)
– An RFQ is a formal document sent to suppliers requesting a price quote for specific products or services. B2B buyers should prepare detailed RFQs to receive accurate and comparable quotes, which is crucial for effective budgeting and decision-making.
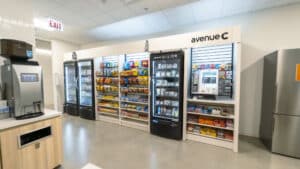
Illustrative Image (Source: Google Search)
-
Incoterms (International Commercial Terms)
– These are standardized trade terms used in international shipping to define the responsibilities of buyers and sellers. Understanding Incoterms is vital for B2B transactions to clarify shipping costs, risk, and delivery responsibilities, helping to prevent misunderstandings and disputes. -
Lead Time
– Lead time refers to the time taken from placing an order to delivery. It is an important factor in planning inventory and ensuring timely product availability. Buyers should inquire about lead times to align their operational needs with supplier capabilities. -
Warranty Period
– This term refers to the duration for which a manufacturer guarantees the functionality of the machine. A longer warranty period can indicate higher quality and reliability. B2B buyers should carefully review warranty terms to ensure adequate protection against defects or operational failures.
Understanding these technical properties and trade terms will empower international B2B buyers to navigate the complexities of purchasing avenue c vending machines, ultimately leading to more strategic decisions and successful outcomes.
Navigating Market Dynamics, Sourcing Trends, and Sustainability in the avenue c vending machines Sector
Market Overview & Key Trends
The avenue c vending machines sector is witnessing transformative changes driven by technological advancements and shifting consumer behaviors. One major global driver is the increasing demand for contactless payment options, particularly following the COVID-19 pandemic. This trend has accelerated the integration of mobile payment systems, allowing international B2B buyers to tap into a tech-savvy customer base eager for convenience and safety. Additionally, the rise of healthy eating trends has prompted vending machine suppliers to diversify their offerings, catering to consumers seeking nutritious options.
For B2B buyers from regions like Africa, South America, the Middle East, and Europe, understanding local market dynamics is essential. In Kenya, for instance, the growing urban population is creating a demand for vending solutions in densely populated areas. Meanwhile, in Germany, there’s a focus on high-tech, energy-efficient machines that align with strict environmental regulations. Emerging technologies such as IoT (Internet of Things) and AI (Artificial Intelligence) are also enhancing operational efficiencies, providing real-time inventory management, and predictive analytics that can inform purchasing decisions.
Furthermore, sustainability is becoming a critical factor in sourcing decisions. Buyers are increasingly looking for vendors who can demonstrate a commitment to environmentally friendly practices, from sourcing materials to energy consumption. The move towards remote monitoring and management of vending machines not only reduces operational costs but also enhances service delivery, making it a key trend for international buyers to consider.
Sustainability & Ethical Sourcing in B2B
As environmental consciousness rises, the avenue c vending machines sector is under pressure to adopt sustainable practices. The environmental impact of vending operations, particularly in terms of energy consumption and waste generation, is significant. International B2B buyers must prioritize suppliers who implement energy-efficient technologies, such as LED lighting and low-energy refrigeration systems, to minimize carbon footprints.
Ethical sourcing is increasingly becoming a non-negotiable aspect of supply chains. Buyers should seek vendors who utilize sustainable materials in their vending machines, such as recycled plastics or responsibly sourced metals. Certifications like LEED (Leadership in Energy and Environmental Design) or ISO 14001 (Environmental Management) can serve as indicators of a supplier’s commitment to sustainability. Furthermore, engaging with suppliers who adhere to fair labor practices and promote local sourcing can enhance brand reputation and consumer trust, especially in emerging markets.
For buyers in diverse regions, including the Middle East and South America, understanding the local regulatory landscape regarding sustainability can provide a competitive edge. Collaborating with vendors who are proactive about compliance with local environmental laws can help mitigate risks and foster long-term partnerships.
Brief Evolution/History
The avenue c vending machines sector has evolved significantly over the past few decades, transitioning from traditional snack dispensers to sophisticated, technology-driven solutions. Initially focused on convenience, these machines have now integrated advanced features such as touchscreen interfaces, cashless payment systems, and remote monitoring capabilities. The shift began in the late 1990s, driven by the need for improved customer experience and operational efficiency.
As consumer preferences have changed, so too have the offerings within vending machines, with an increased focus on healthy, organic, and locally sourced products. This evolution has positioned avenue c vending machines as not just a convenience tool but a reflection of broader lifestyle trends, making them a relevant and strategic investment for B2B buyers worldwide. By understanding this history, buyers can better anticipate future trends and align their sourcing strategies accordingly.
Related Video: Is global trade transforming? | Counting the Cost
Frequently Asked Questions (FAQs) for B2B Buyers of avenue c vending machines
-
What should I consider when vetting suppliers for Avenue C vending machines?
When vetting suppliers, prioritize their reputation and experience in the vending machine industry. Look for established companies with positive reviews and references from previous clients, particularly in your region. Verify their certifications and compliance with local regulations to ensure product safety and quality. Additionally, assess their customer support capabilities, as this will be crucial for maintenance and troubleshooting after purchase. A supplier with a robust after-sales service can be invaluable for long-term operations. -
Can Avenue C vending machines be customized to meet specific market needs?
Yes, Avenue C vending machines offer a range of customization options. Buyers can often select product assortments tailored to local tastes, branding elements, and payment systems, including cashless options. When discussing customization with suppliers, provide insights into your target market’s preferences and requirements. This will not only enhance customer satisfaction but also maximize sales potential in your region. Ensure to obtain samples or mock-ups before finalizing designs to avoid costly mistakes. -
What is the minimum order quantity (MOQ) for Avenue C vending machines, and how does it affect pricing?
The MOQ for Avenue C vending machines can vary by supplier and region. Generally, larger orders may lead to reduced pricing per unit due to economies of scale. It’s advisable to inquire about bulk purchase discounts and financing options if your initial order exceeds the MOQ. This approach can help manage cash flow and justify the investment. If you anticipate future growth, consider negotiating favorable terms for subsequent orders as part of your initial agreement. -
What are the typical lead times for delivery of Avenue C vending machines?
Lead times for delivery can vary significantly based on the supplier’s location, order size, and customization requirements. Typically, you can expect a timeframe ranging from 4 to 12 weeks. It’s essential to communicate your timeline needs upfront and request a detailed production and shipping schedule from your supplier. This proactive approach helps mitigate delays and allows for better planning in your operations, especially if you aim to launch in alignment with local market events or seasons. -
What quality assurance measures should I look for in Avenue C vending machines?
Quality assurance is crucial when sourcing Avenue C vending machines. Ensure that the supplier adheres to international quality standards, such as ISO certifications. Request information on their testing processes, including performance and safety checks conducted during manufacturing. Additionally, inquire about warranty terms and after-sales support to address any potential issues post-purchase. Understanding these measures will help you gauge the reliability and longevity of the machines in your specific operating conditions. -
Are there specific certifications required for importing Avenue C vending machines into my region?
Yes, importing Avenue C vending machines may require compliance with local regulations and certifications. These can include safety standards, electrical certifications, and health regulations, particularly in regions like Europe, where compliance is stringent. Research the requirements specific to your country or region, and ensure that your supplier can provide the necessary documentation to facilitate a smooth import process. This preparation can prevent costly delays and fines during customs clearance. -
What logistics considerations should I keep in mind when sourcing Avenue C vending machines?
Logistics play a vital role in the successful procurement of Avenue C vending machines. Consider factors such as shipping methods, costs, and timelines. Evaluate whether the supplier offers direct shipping or if you need to coordinate with third-party logistics providers. Additionally, factor in import duties and taxes that may apply to your purchase. Establish clear communication with your supplier regarding shipping terms and responsibilities to avoid misunderstandings and ensure timely delivery. -
How can I resolve disputes with suppliers over Avenue C vending machines?
Dispute resolution should be planned proactively in your supplier agreements. Include clear terms regarding returns, warranties, and service levels to minimize conflicts. If a dispute arises, initiate communication with your supplier to discuss the issue directly and seek an amicable resolution. If necessary, refer to your contract for mediation or arbitration clauses. Maintaining a professional relationship and open lines of communication can often lead to satisfactory solutions without escalating to legal action.
Strategic Sourcing Conclusion and Outlook for avenue c vending machines
In conclusion, strategic sourcing for Avenue C vending machines presents a compelling opportunity for international B2B buyers across diverse regions, including Africa, South America, the Middle East, and Europe. By focusing on the unique value propositions of these machines—such as innovative technology, customizable options, and a strong commitment to sustainability—buyers can enhance their product offerings and meet the evolving demands of consumers.
Key Takeaways:
- Cost Efficiency: Leveraging strategic sourcing can significantly reduce procurement costs, enabling businesses to allocate resources more effectively.
- Supplier Relationships: Building strong partnerships with reputable suppliers fosters reliability and ensures consistent product quality, which is crucial in competitive markets.
- Market Adaptability: Avenue C vending machines are designed to cater to various consumer preferences, making them a versatile choice for different geographical markets.
As the demand for automated retail solutions continues to rise, now is the time for international buyers to evaluate their sourcing strategies. Embrace the potential of Avenue C vending machines to not only enhance your portfolio but also to drive sustainable growth in your market. Take the next step: assess your needs, engage with suppliers, and position your business at the forefront of the vending revolution.