Your Ultimate Guide to Sourcing Automatic Products Vending
Guide to Automatic Products Vending Machines
- Introduction: Navigating the Global Market for automatic products vending machines
- Understanding automatic products vending machines Types and Variations
- Key Industrial Applications of automatic products vending machines
- Strategic Material Selection Guide for automatic products vending machines
- In-depth Look: Manufacturing Processes and Quality Assurance for automatic products vending machines
- Comprehensive Cost and Pricing Analysis for automatic products vending machines Sourcing
- Spotlight on Potential automatic products vending machines Manufacturers and Suppliers
- Essential Technical Properties and Trade Terminology for automatic products vending machines
- Navigating Market Dynamics, Sourcing Trends, and Sustainability in the automatic products vending machines Sector
- Market Overview & Key Trends
- Sustainability & Ethical Sourcing in B2B
- Brief Evolution/History
- Frequently Asked Questions (FAQs) for B2B Buyers of automatic products vending machines
- Strategic Sourcing Conclusion and Outlook for automatic products vending machines
Introduction: Navigating the Global Market for automatic products vending machines
In an increasingly digital and fast-paced world, automatic products vending machines stand out as a pivotal solution for B2B buyers looking to streamline product distribution and enhance customer engagement. These machines not only offer convenience but also cater to diverse consumer needs, making them an essential investment for businesses across various sectors. As global markets expand, particularly in regions like Africa, South America, the Middle East, and Europe, understanding the nuances of vending machine technology becomes crucial for informed sourcing decisions.
This guide provides a comprehensive overview of the automatic products vending machine landscape, covering key aspects such as types of machines, materials used in manufacturing, quality control standards, and a detailed analysis of suppliers. It also explores cost considerations and market trends, ensuring that buyers are equipped with the information necessary to make strategic purchasing decisions.
By delving into frequently asked questions, this resource empowers international B2B buyers to navigate the complexities of vending machine procurement with confidence. Whether you are looking to enhance your product distribution strategy or invest in cutting-edge technology, this guide is your roadmap to understanding the global market dynamics of automatic products vending machines, enabling you to make decisions that align with your business goals and market demands.
Understanding automatic products vending machines Types and Variations
Type Name | Key Distinguishing Features | Primary B2B Applications | Brief Pros & Cons for Buyers |
---|---|---|---|
Snack and Beverage Machines | Dispense snacks and drinks; often refrigerated | Offices, schools, airports | Pros: Easy to set up, high demand. Cons: Limited product range, maintenance needed. |
Bulk Vending Machines | Dispense items in bulk, such as nuts or candy | Events, gyms, convenience stores | Pros: Lower cost per unit, customizable offerings. Cons: Requires bulk supply management. |
Automated Retail Machines | Larger units with touchscreen interfaces; sell electronics or clothing | Malls, tech stores, airports | Pros: High-tech appeal, varied product range. Cons: High initial investment, technical support needed. |
Personal Care Product Machines | Dispense hygiene and personal care products | Hotels, gyms, public restrooms | Pros: Convenient for consumers, recurring sales. Cons: Limited to consumables, may require frequent restocking. |
Specialty Product Machines | Target niche markets (e.g., organic foods, local products) | Farmers’ markets, health stores | Pros: Attracts specific customer segments, promotes local products. Cons: Limited audience, possible higher costs. |
Snack and Beverage Machines
Snack and beverage vending machines are among the most common types found in various locations, including offices, schools, and transportation hubs. These machines typically offer a range of snacks, drinks, and sometimes refrigerated items. For B2B buyers, these machines are appealing due to their high demand and relatively easy setup process. However, they may require regular maintenance and restocking to ensure a diverse product offering, which can be a logistical consideration for businesses.
Bulk Vending Machines
Bulk vending machines are designed to dispense products in larger quantities, such as candy, nuts, or other snacks. They are frequently used in settings like gyms, convenience stores, and during events where quick access to snacks is crucial. B2B buyers appreciate the cost-effectiveness of bulk purchasing, which can lead to lower prices per unit. However, managing inventory and ensuring a steady supply of bulk products can pose challenges.
Automated Retail Machines
Automated retail machines represent a more advanced vending solution, often featuring touchscreen interfaces and offering a wider variety of products, including electronics and clothing. These machines are suitable for high-traffic areas such as malls and airports. The high-tech nature and diverse product offerings can attract a tech-savvy customer base. However, the initial investment can be substantial, and ongoing technical support may be necessary, which should be factored into purchasing decisions.
Personal Care Product Machines
These machines focus on dispensing personal care items, such as hygiene products and cosmetics, and are commonly found in hotels, gyms, and public restrooms. They provide convenience for consumers who may need these products on-the-go, creating potential for recurring sales. For B2B buyers, the appeal lies in meeting customer needs in a convenient manner. However, the limited product range and the need for frequent restocking can be drawbacks to consider.
Specialty Product Machines
Specialty product vending machines cater to niche markets, offering items like organic foods or locally sourced products. These machines are often placed in farmers’ markets or health stores. They can attract specific customer segments looking for unique products, enhancing brand loyalty. However, the limited audience and potentially higher costs for specialty items may restrict broader market appeal, which is an important consideration for B2B buyers evaluating their investment.
Related Video: Automatic Products Snack Vending Machine @Multigenerational Center – Henderson, NV USA
Key Industrial Applications of automatic products vending machines
Industry/Sector | Specific Application of Automatic Products Vending Machines | Value/Benefit for the Business | Key Sourcing Considerations for this Application |
---|---|---|---|
Retail | 24/7 Product Dispensing | Increases sales through convenience and accessibility | Product compatibility, payment system integration, machine reliability |
Healthcare | Medication Dispensing | Ensures timely access to medications, reducing wait times | Compliance with health regulations, secure dispensing mechanisms, user-friendly interfaces |
Education | Stationery and Supplies | Provides students and staff easy access to essential supplies | Inventory management systems, customization options, durable construction |
Manufacturing | Spare Parts Distribution | Minimizes downtime by providing immediate access to critical parts | Inventory tracking solutions, machine adaptability, local support services |
Hospitality | Snack and Beverage Sales | Enhances guest experience with quick service options | Product variety, payment flexibility, machine aesthetics suitable for the environment |
Retail Applications
In the retail sector, automatic products vending machines serve as 24/7 product dispensing units that increase sales by providing consumers with convenient access to a wide range of products. This application is particularly beneficial in urban areas where foot traffic is high and traditional store hours may not align with customer needs. International B2B buyers should consider factors such as product compatibility, payment system integration, and the reliability of the machines to ensure seamless operations.
Healthcare Applications
In healthcare, automatic vending machines are utilized for medication dispensing, allowing patients and healthcare professionals to access medications quickly and efficiently. This application reduces wait times and enhances patient satisfaction, especially in high-traffic hospitals or clinics. Buyers in this sector must prioritize compliance with health regulations, secure dispensing mechanisms, and user-friendly interfaces to cater to diverse patient needs and ensure safety.
Education Applications
Automatic vending machines in educational institutions provide students and staff with easy access to stationery and other essential supplies. This application alleviates the need for dedicated supply stores on campus, streamlining the procurement process. B2B buyers in this sector should focus on inventory management systems, customization options for branding, and durable construction to withstand heavy usage in school environments.
Manufacturing Applications
In manufacturing, automatic vending machines are employed for spare parts distribution, which minimizes equipment downtime by allowing immediate access to critical components. This application is vital for maintaining operational efficiency in production lines. Buyers should consider inventory tracking solutions to manage stock levels effectively, machine adaptability to various parts, and the availability of local support services for maintenance.
Hospitality Applications
In the hospitality industry, vending machines are used for snack and beverage sales, enhancing the guest experience by providing quick and convenient service options. This application is particularly useful in hotels, resorts, and conference centers where guests may desire refreshments at any hour. Key considerations for B2B buyers include product variety to cater to diverse tastes, payment flexibility to accommodate different payment methods, and machine aesthetics that align with the establishment’s branding.
Related Video: Kooler Ice Vending Machines – IM600XL vs. IM1000
Strategic Material Selection Guide for automatic products vending machines
When selecting materials for automatic products vending machines, it is crucial to consider the specific requirements of the application, including durability, cost, and environmental factors. Here, we analyze four common materials used in the construction of these machines, focusing on their properties, advantages, disadvantages, and considerations for international B2B buyers.
1. Stainless Steel
Key Properties: Stainless steel is known for its excellent corrosion resistance, high strength, and ability to withstand high temperatures and pressures. Common grades used include 304 and 316, with the latter offering superior resistance to chlorides.
Pros & Cons: Stainless steel is highly durable and requires minimal maintenance, making it ideal for outdoor or high-traffic environments. However, it is more expensive than carbon steel and can be challenging to machine, leading to higher manufacturing costs.
Impact on Application: Stainless steel is compatible with a wide range of media, including food and beverages, making it a preferred choice for vending machines dispensing consumables. Its corrosion resistance ensures longevity in humid or corrosive environments.
Considerations for International Buyers: Compliance with food safety standards (e.g., FDA, EU regulations) is essential. Buyers should also consider the availability of specific grades in their region, as well as local standards such as ASTM or DIN.
2. Carbon Steel
Key Properties: Carbon steel is characterized by its strength and affordability. It typically has lower corrosion resistance compared to stainless steel but can be treated with coatings or galvanization.
Pros & Cons: The primary advantage of carbon steel is its cost-effectiveness, making it suitable for budget-sensitive projects. However, its susceptibility to rust and corrosion can limit its application in outdoor or moist environments unless adequately protected.
Impact on Application: Carbon steel is suitable for structural components of vending machines where corrosion is not a significant concern. It is often used in frames and supports.
Considerations for International Buyers: Buyers should ensure that the carbon steel used meets local standards for structural integrity. Coating options may also need to comply with environmental regulations in regions like Europe and North America.
3. Aluminum
Key Properties: Aluminum is lightweight, corrosion-resistant, and has good thermal conductivity. It is often used in applications where weight savings are critical.
Pros & Cons: The lightweight nature of aluminum makes it easy to handle and install, reducing shipping costs. However, it is generally less strong than steel and may require thicker sections to achieve the same strength, which can increase costs.
Impact on Application: Aluminum is often used in components that require frequent handling or where weight is a concern, such as in portable vending machines. Its corrosion resistance is beneficial for outdoor use.
Considerations for International Buyers: Buyers should be aware of the specific aluminum alloys available and their properties, as these can vary significantly. Compliance with local standards for aluminum products is also critical.
4. Polycarbonate
Key Properties: Polycarbonate is a high-performance plastic known for its impact resistance and clarity. It can withstand a wide range of temperatures and is often used for transparent panels in vending machines.
Pros & Cons: The primary advantage of polycarbonate is its lightweight and shatter-resistant properties, making it ideal for safety and visibility. However, it can be more expensive than other plastics and may not provide the same structural support as metals.
Impact on Application: Polycarbonate is commonly used for windows and display panels in vending machines, allowing customers to see products while protecting them from the elements.
Considerations for International Buyers: Buyers should consider UV resistance and compliance with safety standards, especially in regions with high sunlight exposure. The availability of specific grades may vary by region.
Summary Table
Material | Typical Use Case for automatic products vending machines | Key Advantage | Key Disadvantage/Limitation | Relative Cost (Low/Med/High) |
---|---|---|---|---|
Stainless Steel | Structural components, food contact surfaces | Excellent corrosion resistance | High cost, difficult to machine | High |
Carbon Steel | Frames and supports | Cost-effective | Susceptible to corrosion | Low |
Aluminum | Portable units, panels | Lightweight, good corrosion resistance | Less strong than steel | Medium |
Polycarbonate | Windows and display panels | Impact-resistant, transparent | More expensive, less structural support | Medium |
This guide provides a comprehensive overview of material selection for automatic products vending machines, offering actionable insights for international B2B buyers to make informed decisions based on their specific needs and regional considerations.
In-depth Look: Manufacturing Processes and Quality Assurance for automatic products vending machines
Manufacturing Processes for Automatic Products Vending Machines
The manufacturing of automatic products vending machines involves a series of well-defined stages, each critical to ensuring the final product meets the required performance and quality standards. For international B2B buyers, particularly those from regions like Africa, South America, the Middle East, and Europe, understanding these processes can aid in making informed purchasing decisions.
Main Stages of Manufacturing
-
Material Preparation
– The first step involves sourcing high-quality raw materials, including steel, plastics, and electronic components. Suppliers should provide certification for the materials used, ensuring compliance with international standards.
– Key Techniques: Laser cutting and CNC machining are commonly employed to prepare materials with precision, ensuring that all components fit together seamlessly. -
Forming
– This stage includes processes like bending, stamping, and molding to create the machine’s structural components. The forming techniques chosen can significantly affect the durability and aesthetic appeal of the vending machine.
– Key Techniques: Hydraulic presses and injection molding machines are often used to shape materials accurately, which is essential for both functionality and design. -
Assembly
– Once the components are formed, they are assembled into the final product. This involves integrating mechanical parts, electronic systems, and user interfaces.
– Key Techniques: Automated assembly lines may be utilized to enhance efficiency and reduce human error. Skilled labor is also crucial during this phase for precise assembly and quality checks. -
Finishing
– The final stage includes painting, coating, and adding any decals or branding elements. This not only enhances the machine’s appearance but also provides protection against wear and environmental factors.
– Key Techniques: Powder coating and screen printing are popular methods for achieving a durable and attractive finish.
Quality Assurance Practices
Quality assurance (QA) is paramount in the manufacturing of vending machines to ensure reliability and customer satisfaction. Adhering to international standards can enhance marketability and trust among buyers.
Relevant International Standards
- ISO 9001: This is a globally recognized standard for quality management systems (QMS). It emphasizes a process-oriented approach to managing quality, ensuring that the manufacturing process is consistently evaluated and improved.
- CE Marking: For machines sold in Europe, CE marking indicates compliance with health, safety, and environmental protection standards.
- API Standards: In regions where specific industry standards apply, such as the American Petroleum Institute for machines used in petroleum distribution, compliance is crucial.
Quality Control Checkpoints
-
Incoming Quality Control (IQC)
– Raw materials and components are inspected upon arrival to ensure they meet specified requirements. This prevents defective materials from entering the production line. -
In-Process Quality Control (IPQC)
– Throughout the manufacturing process, various checkpoints are established to monitor quality. This includes testing for proper assembly, dimensions, and functionality at different stages of production. -
Final Quality Control (FQC)
– Before shipping, each vending machine undergoes thorough testing. This includes functionality tests, safety checks, and performance evaluations to ensure the product operates as intended.
Common Testing Methods
- Functional Testing: Verifying that all components work together properly.
- Durability Testing: Simulating extended use to assess wear and tear.
- Safety Testing: Ensuring compliance with safety regulations to protect users.
Verification of Supplier Quality Control
For B2B buyers, particularly those in diverse international markets, verifying a supplier’s quality control processes is essential for mitigating risks associated with product quality.
-
Audits
– Conducting regular audits of suppliers can provide insight into their manufacturing processes and quality management systems. Buyers should look for compliance with ISO standards and other relevant certifications. -
Reports
– Requesting quality assurance reports from suppliers can help verify their adherence to quality standards and protocols. This should include data on defect rates, testing outcomes, and corrective actions taken. -
Third-Party Inspections
– Engaging third-party inspection services can provide an unbiased assessment of the manufacturing and quality assurance processes. This is particularly useful for buyers who may not have the resources to conduct in-house inspections.
Quality Control and Certification Nuances for International Buyers
Understanding the nuances of quality control and certification is vital for international B2B buyers. Different regions may have varying standards and expectations. For instance:
- Europe: Strong emphasis on CE marking and compliance with environmental regulations.
- Middle East: Increasing focus on sustainability and energy efficiency standards.
- Africa and South America: Buyers should be aware of local regulations that might affect the import and operation of vending machines.
By familiarizing themselves with these standards and processes, buyers can ensure that they procure high-quality vending machines that meet both their needs and regulatory requirements in their respective markets.
In conclusion, a comprehensive understanding of the manufacturing processes and quality assurance practices will empower international B2B buyers to make informed decisions, ensuring they partner with suppliers that prioritize quality and compliance.
Related Video: Most Satisfying Factory Production Processes And Heavy-Duty Factory Machines!
Comprehensive Cost and Pricing Analysis for automatic products vending machines Sourcing
Understanding Cost Components in Vending Machine Sourcing
When sourcing automatic product vending machines, international B2B buyers must carefully analyze the cost structure to ensure a competitive edge. The primary cost components involved in vending machine production include:
-
Materials: This includes the cost of metal, plastic, electronic components, and any specialized materials required for custom features. Bulk purchasing can significantly reduce material costs.
-
Labor: Labor costs encompass wages for assembly workers, engineers, and quality control personnel. Regions with lower labor costs, such as parts of Africa and South America, may offer advantages.
-
Manufacturing Overhead: This includes indirect costs such as utilities, rent, and administrative expenses that contribute to the production process. Efficient manufacturing processes can help minimize overhead.
-
Tooling: The cost of molds and fixtures necessary for production can be substantial, particularly for customized machines. Buyers should consider the impact of tooling costs on the overall pricing.
-
Quality Control (QC): Ensuring that machines meet international standards requires investment in quality checks and testing. Certifications may add to costs but are essential for market acceptance.
-
Logistics: Transportation costs, including shipping and handling, play a crucial role in the total cost structure. Incoterms can influence logistics costs significantly.
-
Margin: Suppliers typically add a profit margin to cover their costs and ensure profitability. Understanding the expected margins in different markets can aid in negotiations.
Key Price Influencers
Several factors influence the pricing of automatic vending machines, which buyers should consider:
-
Volume/MOQ (Minimum Order Quantity): Larger orders often lead to better pricing. Buyers should assess their needs to determine the most cost-effective ordering strategy.
-
Specifications and Customization: Custom features or specifications can increase costs. Buyers must balance the desire for customization with budget constraints.
-
Materials and Quality Certifications: The choice of materials directly impacts the machine’s durability and aesthetic appeal. Higher quality materials typically command higher prices but can result in lower maintenance costs.
-
Supplier Factors: The reputation and reliability of the supplier can influence pricing. Established suppliers may charge more but offer better service and quality assurance.
-
Incoterms: Understanding shipping terms is critical. Different Incoterms can shift responsibility for costs and risks between buyers and sellers, impacting total expenditure.
Buyer Tips for Effective Sourcing
For B2B buyers, especially from diverse regions like Africa, South America, the Middle East, and Europe, the following strategies can enhance cost-efficiency:
-
Negotiate Strategically: Leverage volume and long-term relationships to negotiate better prices. Be prepared to discuss and justify your needs to suppliers.
-
Evaluate Total Cost of Ownership (TCO): Consider not just the purchase price but also maintenance, operational costs, and potential downtime. A higher initial investment in quality machines can lead to lower TCO over time.
-
Understand Pricing Nuances: Currency fluctuations, tariffs, and local market conditions can affect pricing. Buyers should stay informed about these factors to make better purchasing decisions.
-
Conduct Market Research: Gather insights on competitors’ pricing and product offerings to inform negotiations and ensure competitive pricing strategies.
Conclusion
While sourcing automatic vending machines involves various cost components and pricing influencers, a strategic approach can lead to significant savings and enhanced operational efficiency. Buyers are encouraged to analyze all aspects of the cost structure and leverage negotiation tactics to secure the best deals.
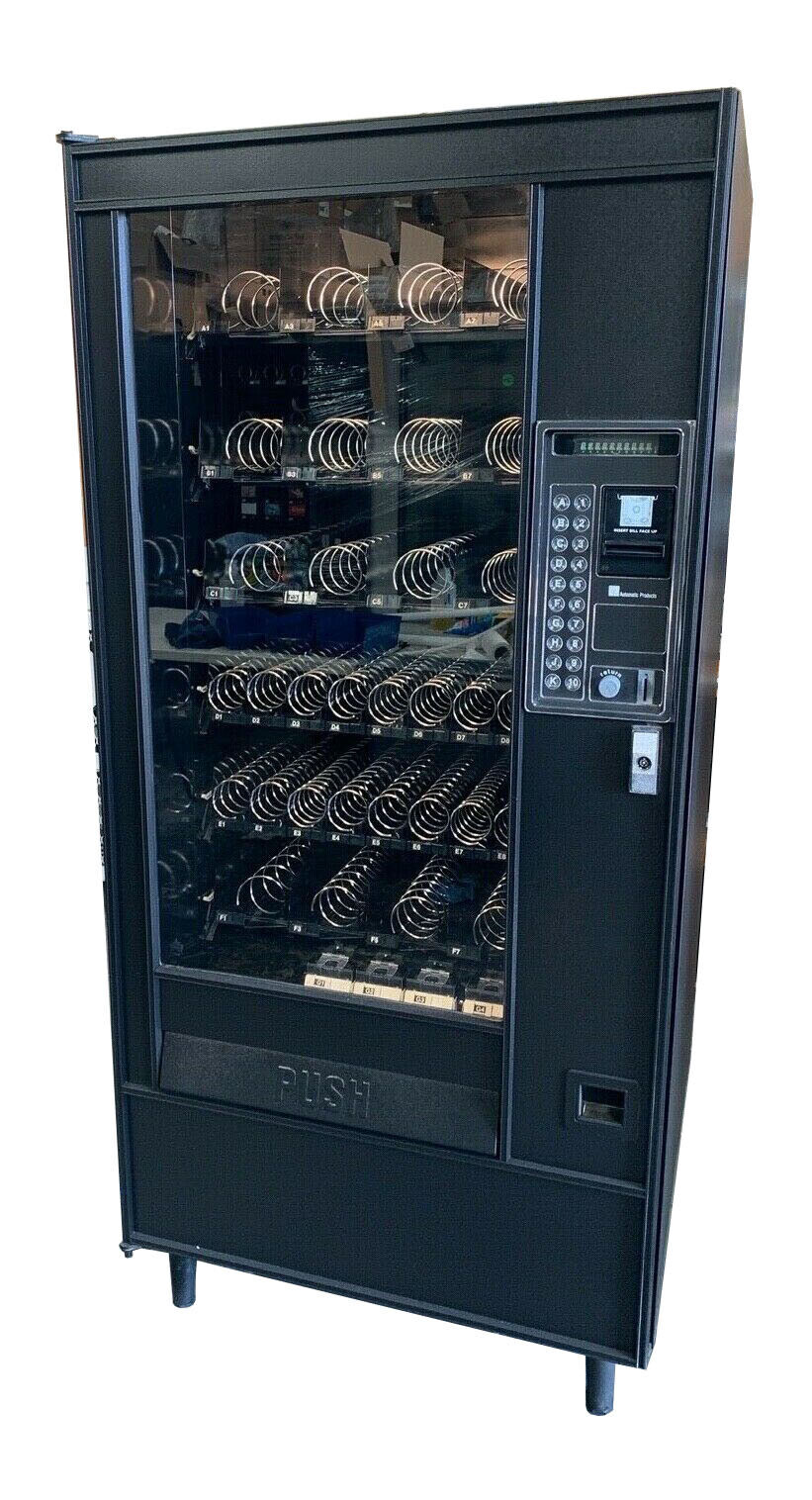
Illustrative Image (Source: Google Search)
- Disclaimer: Prices and costs mentioned are indicative and can vary based on numerous factors, including location, supplier agreements, and market conditions.*
Spotlight on Potential automatic products vending machines Manufacturers and Suppliers
This section offers a look at a few manufacturers active in the ‘automatic products vending machines’ market. This is a representative sample for illustrative purposes; B2B buyers must conduct their own extensive due diligence before any engagement. Information is synthesized from public sources and general industry knowledge.
Essential Technical Properties and Trade Terminology for automatic products vending machines
Automatic products vending machines have become vital in various markets, offering convenience and efficiency for both consumers and businesses. Understanding the technical properties and trade terminology associated with these machines is essential for international B2B buyers, particularly in regions like Africa, South America, the Middle East, and Europe. Below are critical specifications and commonly used terms that will enhance your purchasing decisions.
Key Technical Properties
-
Material Grade
– Definition: This refers to the quality and type of materials used in the construction of the vending machine, such as stainless steel, plastic, or composite materials.
– Importance: High-grade materials ensure durability and resistance to wear and tear, which is crucial for machines placed in high-traffic areas. Buyers should consider the environmental conditions (humidity, temperature) in their region when selecting materials. -
Tolerance
– Definition: Tolerance indicates the permissible limit of variation in dimensions and physical properties of machine components.
– Importance: Accurate tolerances are critical for the smooth operation of the vending machine. For instance, misaligned components can lead to malfunction or product jams, impacting customer satisfaction and operational efficiency. -
Power Consumption
– Definition: This specification measures the amount of energy the machine uses, typically expressed in watts.
– Importance: Understanding power consumption is vital for calculating operating costs and ensuring compliance with local energy regulations. Machines with lower energy consumption are not only cost-effective but also environmentally friendly. -
Capacity
– Definition: Capacity refers to the amount of product a vending machine can hold, often measured in the number of items or volume.
– Importance: A higher capacity machine is beneficial in high-demand areas, as it reduces the frequency of restocking. Buyers should assess their target market’s needs to determine the appropriate capacity.
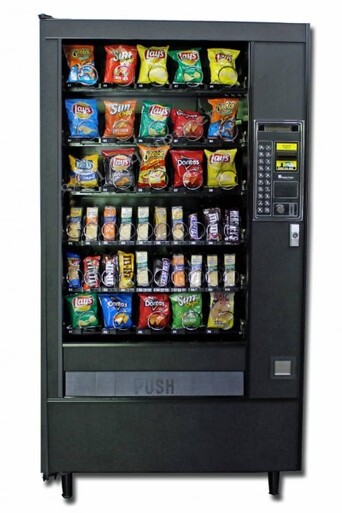
Illustrative Image (Source: Google Search)
- User Interface
– Definition: This encompasses the design and functionality of the machine’s display, buttons, and payment systems.
– Importance: A user-friendly interface enhances customer experience and can significantly influence sales. Machines that support various payment methods (cash, card, mobile payment) are increasingly preferred.
Common Trade Terminology
-
OEM (Original Equipment Manufacturer)
– Definition: A company that produces parts or equipment that may be marketed by another manufacturer.
– Usage: Understanding OEM relationships can help buyers identify reliable suppliers and ensure that parts are compatible with their vending machines. -
MOQ (Minimum Order Quantity)
– Definition: The smallest quantity of a product that a supplier is willing to sell.
– Usage: Knowing the MOQ is essential for budgeting and inventory planning. Buyers should negotiate MOQs that align with their operational needs. -
RFQ (Request for Quotation)
– Definition: A document that solicits price bids from suppliers for specific products or services.
– Usage: Submitting an RFQ allows buyers to compare prices and terms from multiple vendors, aiding in informed purchasing decisions.
-
Incoterms (International Commercial Terms)
– Definition: A set of rules that define the responsibilities of sellers and buyers in international transactions.
– Usage: Familiarity with Incoterms helps buyers understand shipping costs, risks, and responsibilities, which can significantly impact the total cost of procurement. -
Lead Time
– Definition: The time between placing an order and receiving the product.
– Usage: Understanding lead times is crucial for inventory management and ensuring that machines are available when needed, especially in peak seasons. -
Warranty Period
– Definition: The duration during which the manufacturer guarantees the product against defects.
– Usage: A longer warranty period can provide peace of mind and reduce long-term costs associated with repairs or replacements.
By familiarizing yourself with these technical properties and trade terms, you can make more informed decisions when procuring automatic products vending machines, ensuring that they meet the specific needs of your market and operational goals.
Navigating Market Dynamics, Sourcing Trends, and Sustainability in the automatic products vending machines Sector
Market Overview & Key Trends
The automatic products vending machines sector is experiencing dynamic growth, driven by several global factors. Increasing urbanization and the demand for convenience are propelling the market, particularly in densely populated areas across Africa, South America, the Middle East, and Europe. Additionally, the rise of contactless payments and digital technologies is reshaping traditional vending operations. International B2B buyers should note the trend towards smart vending machines that incorporate IoT (Internet of Things) technologies, enabling real-time inventory management and enhanced customer engagement through personalized marketing.
Emerging trends also include the diversification of product offerings beyond snacks and beverages to include health-oriented products, electronics, and even cosmetics. This shift caters to evolving consumer preferences, particularly in urban centers where consumers are looking for healthier options. Furthermore, sustainability is becoming a pivotal consideration in sourcing decisions. Buyers are increasingly seeking vendors who prioritize eco-friendly practices, such as using recyclable materials and energy-efficient technologies.
Understanding these market dynamics is crucial for international B2B buyers, as they navigate a landscape where agility and innovation are essential to staying competitive. Buyers should also pay attention to regional variations in consumer behavior, which can affect product selection and marketing strategies.
Sustainability & Ethical Sourcing in B2B
Sustainability has emerged as a critical component in the automatic products vending machines sector, influencing purchasing decisions and supplier relationships. The environmental impact of vending machines, particularly regarding energy consumption and waste generation, has prompted buyers to seek solutions that minimize their ecological footprint. This includes selecting machines that utilize renewable energy sources, such as solar panels, and those that are designed for energy efficiency.
Ethical sourcing is equally important, as businesses are increasingly held accountable for their supply chain practices. Buyers should prioritize suppliers who adhere to ethical standards, ensuring fair labor practices and transparency throughout the production process. Certifications such as ISO 14001 (Environmental Management) and FSC (Forest Stewardship Council) can provide assurance of a vendor’s commitment to sustainability.
Furthermore, integrating ‘green’ materials—like biodegradable plastics and recycled metals—into the manufacturing of vending machines not only enhances brand reputation but also meets growing consumer demand for environmentally responsible products. By focusing on sustainability and ethical sourcing, B2B buyers can create a competitive advantage and appeal to a conscientious customer base.
Brief Evolution/History
The evolution of vending machines dates back to ancient Greece, where simple machines dispensed holy water. However, the modern era of vending machines began in the late 19th century with the introduction of coin-operated machines selling postcards and cigarettes. The sector saw significant technological advancements in the 20th century, including the introduction of electronic payment systems and refrigerated units for perishable goods.
Today, the automatic products vending machines landscape is characterized by rapid innovation, with a focus on enhancing user experience through technology and sustainability. The integration of smart technology, such as mobile apps for cashless transactions and inventory tracking, reflects the ongoing transformation within this sector. Understanding this historical context helps B2B buyers appreciate the current dynamics and future potential of the vending machine market.
Related Video: Global Trade & Logistics – What is Global Trade?
Frequently Asked Questions (FAQs) for B2B Buyers of automatic products vending machines
-
How can I effectively vet suppliers for automatic products vending machines?
When sourcing vending machines, it’s crucial to conduct thorough supplier vetting. Start by checking the supplier’s credentials, including business licenses and certifications. Look for reviews and testimonials from previous clients, especially those within your region. Engaging in direct communication to discuss your specific needs can also reveal their customer service quality. Additionally, consider requesting samples or visiting their production facility if feasible. This due diligence will help ensure you partner with a reliable and reputable supplier. -
Can I customize the vending machines to fit my brand?
Yes, many suppliers offer customization options for vending machines. You can request modifications in design, color, branding, and product selection to align with your brand identity. It’s essential to communicate your specific requirements clearly during the negotiation phase. Be aware that customization may affect the minimum order quantity (MOQ) and lead times, so ensure these details are discussed upfront to avoid any misunderstandings later. -
What are the typical minimum order quantities (MOQs) and lead times for vending machines?
Minimum order quantities for automatic vending machines can vary significantly based on the supplier and the level of customization. Generally, MOQs can range from 10 to 50 units. Lead times typically range from 4 to 12 weeks, depending on the complexity of the order and the supplier’s production capacity. Always confirm these details with your supplier and factor them into your planning to ensure timely delivery. -
What payment methods are commonly accepted for international purchases?
For international transactions, suppliers often accept various payment methods, including wire transfers, letters of credit, and payment platforms like PayPal or Escrow services. It’s advisable to negotiate favorable payment terms, such as a deposit upfront and the balance upon delivery. Additionally, ensure that the payment method you choose offers a degree of buyer protection to mitigate risks associated with international trade. -
What quality assurance processes should I expect from suppliers?
Reputable suppliers will have a robust quality assurance (QA) process in place. This typically includes inspections at various stages of production, testing of the vending machines for functionality, and compliance with international standards. Request documentation of their QA procedures and certifications, such as ISO 9001, which indicates a commitment to quality management. This information will help you gauge the reliability of the machines you plan to purchase. -
What certifications should I look for in vending machines?
When sourcing vending machines, look for certifications that demonstrate compliance with safety and quality standards. Common certifications include CE (European Conformity) for Europe, UL (Underwriters Laboratories) for North America, and ISO certifications for quality management. These certifications not only ensure that the machines meet specific safety and performance standards but also enhance their marketability in your region.
-
How can I handle logistics and shipping for vending machines?
Logistics can be complex when importing vending machines, so it’s crucial to work with a supplier experienced in international shipping. Discuss shipping options, including freight methods (air or sea), and confirm who will bear the shipping costs. Ensure that you understand customs regulations in your country and work with a freight forwarder who can assist with documentation and clearance processes to avoid delays. -
What steps should I take if I encounter disputes with a supplier?
If a dispute arises, the first step is to communicate directly with the supplier to seek resolution. Document all communications and agreements made. If the issue remains unresolved, refer to the terms outlined in your contract, which may include mediation or arbitration clauses. Consider involving a legal professional with experience in international trade to navigate the dispute effectively. Maintaining a professional demeanor throughout the process can help preserve your business relationship.
Strategic Sourcing Conclusion and Outlook for automatic products vending machines
As the market for automatic products vending machines continues to evolve, strategic sourcing emerges as a critical component for international B2B buyers looking to maximize their investments. Key takeaways include the importance of understanding regional consumer preferences, leveraging technology for enhanced user experiences, and ensuring compliance with local regulations. By aligning sourcing strategies with market trends, businesses can not only improve operational efficiencies but also enhance customer satisfaction.
Investing in high-quality machines that offer a diverse product range and seamless payment options can differentiate your business in competitive markets across Africa, South America, the Middle East, and Europe. Furthermore, building strong relationships with suppliers will facilitate better pricing, improved service, and access to innovative products that meet the changing demands of consumers.
Looking ahead, the automatic products vending machine sector is poised for significant growth, driven by advancements in technology and changing consumer behaviors. Now is the time for B2B buyers to act: evaluate your sourcing strategies, explore partnerships, and invest in solutions that will not only meet today’s demands but also anticipate the needs of tomorrow’s market. Embrace this opportunity to lead in a dynamic and exciting industry landscape.