Your Ultimate Guide to Sourcing Ammunition Vending Machine
Guide to Ammunition Vending Machine
- Introduction: Navigating the Global Market for ammunition vending machine
- Understanding ammunition vending machine Types and Variations
- Key Industrial Applications of ammunition vending machine
- Strategic Material Selection Guide for ammunition vending machine
- In-depth Look: Manufacturing Processes and Quality Assurance for ammunition vending machine
- Comprehensive Cost and Pricing Analysis for ammunition vending machine Sourcing
- Spotlight on Potential ammunition vending machine Manufacturers and Suppliers
- Essential Technical Properties and Trade Terminology for ammunition vending machine
- Navigating Market Dynamics, Sourcing Trends, and Sustainability in the ammunition vending machine Sector
- Frequently Asked Questions (FAQs) for B2B Buyers of ammunition vending machine
- Strategic Sourcing Conclusion and Outlook for ammunition vending machine
Introduction: Navigating the Global Market for ammunition vending machine
In an increasingly complex global landscape, the demand for efficient and secure ammunition distribution solutions is on the rise. Ammunition vending machines represent a pivotal innovation in this arena, merging convenience with safety and regulatory compliance. These automated systems are designed to meet the needs of military, law enforcement, and private security sectors, offering a streamlined approach to ammunition procurement. With the ability to operate in various environments—from remote locations to urban centers—these machines ensure that critical supplies are readily available when needed.
This comprehensive guide delves into the multifaceted world of ammunition vending machines, covering essential topics such as types of machines, materials used, manufacturing and quality control processes, supplier networks, cost considerations, and market trends. Each section is crafted to equip international B2B buyers, particularly those from Africa, South America, the Middle East, and Europe, with the insights necessary for informed sourcing decisions.
By understanding the intricacies of this specialized market, buyers can better navigate supplier relationships, optimize inventory management, and enhance their procurement strategies. The guide also addresses common FAQs, providing clarity on operational best practices and compliance requirements. Empowering buyers with this knowledge not only fosters successful partnerships but also contributes to a more secure and efficient ammunition supply chain.
Understanding ammunition vending machine Types and Variations
Type Name | Key Distinguishing Features | Primary B2B Applications | Brief Pros & Cons for Buyers |
---|---|---|---|
Standard Ammunition Vending Machine | Offers a wide range of ammunition types and calibers | Military bases, shooting ranges | Pros: Versatile product range; Cons: May require regular maintenance. |
Smart Ammunition Vending Machine | Integrated with advanced technology for tracking and inventory management | Law enforcement agencies, military operations | Pros: Real-time inventory tracking; Cons: Higher initial investment. |
Mobile Ammunition Vending Machine | Portable design for easy relocation and setup | Field operations, temporary installations | Pros: Flexibility in deployment; Cons: Limited storage capacity. |
Automated Ammunition Dispenser | Fully automated system for dispensing ammunition | Large military operations, high-demand environments | Pros: Reduces human error; Cons: High setup costs and complexity. |
Customizable Ammunition Vending Unit | Tailored configurations based on specific needs | Specialized military units, private security firms | Pros: Meets unique operational requirements; Cons: Longer lead times for production. |
Standard Ammunition Vending Machine
Standard ammunition vending machines are designed to offer a broad selection of ammunition types and calibers, making them ideal for military bases and shooting ranges. These machines typically feature user-friendly interfaces and can accommodate various ammunition brands. B2B buyers should consider the machine’s maintenance requirements and the availability of service support, as regular upkeep is essential to ensure reliability and functionality.
Smart Ammunition Vending Machine
Smart ammunition vending machines incorporate advanced technology, such as RFID and IoT capabilities, for real-time inventory tracking and management. These systems are particularly beneficial for law enforcement agencies and military operations where accountability and security are paramount. Buyers should evaluate the total cost of ownership, including software subscriptions and potential training for personnel, to fully understand the investment needed for these sophisticated solutions.
Mobile Ammunition Vending Machine
Designed for portability, mobile ammunition vending machines can be easily relocated to different sites, making them suitable for field operations and temporary installations. Their compact design allows for quick setup and deployment in various environments. When purchasing, B2B buyers should assess the machine’s storage capacity and the types of ammunition it can dispense, as these factors will influence operational efficiency.
Automated Ammunition Dispenser
Automated ammunition dispensers offer a fully automated solution for dispensing ammunition, minimizing human intervention. This type of machine is ideal for large military operations or environments with high demand for ammunition, as it helps to reduce errors and streamline the supply chain. Buyers need to consider the complexity and costs associated with installation and maintenance, as these systems can require significant upfront investment.
Customizable Ammunition Vending Unit
Customizable ammunition vending units allow for tailored configurations based on specific operational needs, making them suitable for specialized military units or private security firms. These machines can be equipped with various features, such as enhanced security measures or unique product assortments. B2B buyers should keep in mind the longer lead times for production and customization, as these factors can impact project timelines and budgets.
Related Video: CS 198-126: Lecture 12 – Diffusion Models
Key Industrial Applications of ammunition vending machine
Industry/Sector | Specific Application of ammunition vending machine | Value/Benefit for the Business | Key Sourcing Considerations for this Application |
---|---|---|---|
Defense & Military | On-site ammunition dispensing for training | Enhanced operational readiness and efficiency | Compliance with military standards, secure supply chain |
Law Enforcement | Quick access to ammunition for tactical units | Improved response times and mission effectiveness | Reliability of supply, compatibility with diverse calibers |
Sporting Goods | Ammunition sales at shooting ranges | Increased convenience for customers, higher sales | Variety of calibers, local regulations on sales |
Outdoor Recreation | Ammunition vending at hunting locations | Accessibility for hunters, boost in local sales | Seasonal demand fluctuations, regional hunting regulations |
Private Security Firms | Emergency ammunition supply for security personnel | Immediate access to necessary resources | Supplier reliability, emergency response capabilities |
Defense & Military
In defense and military applications, ammunition vending machines serve as on-site dispensing units for training exercises and operational readiness. These machines streamline the procurement process, allowing personnel to access necessary ammunition quickly and efficiently. For international buyers, particularly in regions with developing defense sectors, ensuring compliance with military standards and establishing a secure supply chain are critical considerations. This guarantees that the equipment meets safety regulations while providing uninterrupted access to essential resources.
Law Enforcement
For law enforcement agencies, ammunition vending machines provide quick access to ammunition for tactical units during operations. This capability significantly reduces response times, ensuring that officers have the necessary resources to effectively manage incidents. Buyers from regions such as Africa and South America should prioritize suppliers that offer reliable products compatible with a variety of calibers, as well as those that adhere to local regulations regarding ammunition storage and distribution.
Sporting Goods
Ammunition vending machines at shooting ranges enhance customer experience by offering convenient access to ammunition on-site. This not only boosts sales but also encourages repeat visits from customers who appreciate the ease of obtaining their supplies. B2B buyers in Europe and the Middle East should focus on sourcing machines that provide a diverse range of calibers, ensuring they meet the needs of various shooting sports while adhering to local regulations regarding the sale of ammunition.
Outdoor Recreation
In outdoor recreation, particularly hunting, vending machines strategically placed at hunting locations provide hunters with easy access to ammunition. This convenience can lead to increased sales and customer satisfaction. Buyers should consider the seasonal demand fluctuations typical in this industry and partner with suppliers who understand regional hunting regulations to ensure compliance and product availability during peak seasons.
Private Security Firms
Private security firms benefit from ammunition vending machines as they provide emergency supply options for security personnel. This ensures that guards and response teams have immediate access to necessary ammunition in critical situations. For international buyers, especially in volatile regions, sourcing from suppliers known for their reliability and emergency response capabilities is essential. This guarantees that the machines are always stocked and ready to meet urgent demands.
Related Video: Shoot Smart Presents : The Ammo Depot, The first Ammo Vending Machine in Texas / VIDEO
Strategic Material Selection Guide for ammunition vending machine
When selecting materials for ammunition vending machines, it is crucial to consider various factors that impact performance, durability, and compliance. Below are analyses of four common materials used in the construction of these machines, focusing on their properties, advantages, disadvantages, and specific considerations for international B2B buyers.
1. Stainless Steel
Key Properties: Stainless steel exhibits excellent corrosion resistance, high tensile strength, and can withstand a wide range of temperatures. It is often used in environments where exposure to moisture or corrosive substances is a concern.
Pros & Cons: The primary advantage of stainless steel is its durability and longevity, making it an ideal choice for vending machines that will see heavy use. However, it is generally more expensive than other materials, which can impact initial investment costs. Manufacturing complexity can also be higher due to its toughness, requiring specialized tools and techniques.
Impact on Application: Stainless steel is compatible with various media, including water and oil, making it suitable for machines that may dispense different types of ammunition or related products.
Considerations for International Buyers: Compliance with standards such as ASTM A240 is essential. Buyers from regions like Africa and South America should also consider the availability of stainless steel and potential import tariffs.
2. Carbon Steel
Key Properties: Carbon steel is known for its high strength and hardness. It can handle significant loads and pressure, making it suitable for structural components of vending machines.
Pros & Cons: Carbon steel is cost-effective and widely available, which makes it a popular choice for many manufacturers. However, it is susceptible to corrosion and may require protective coatings, which can add to maintenance costs. Additionally, it may not perform well in extreme environments without proper treatment.
Impact on Application: While carbon steel can be used for structural parts, its susceptibility to corrosion limits its use in areas exposed to moisture or harsh chemicals.
Considerations for International Buyers: Buyers should ensure that the carbon steel used meets local standards, such as DIN or JIS, particularly in regions with stringent quality regulations.
3. Aluminum
Key Properties: Aluminum is lightweight, corrosion-resistant, and has good thermal conductivity. It is often used in applications where weight is a critical factor.
Pros & Cons: The lightweight nature of aluminum allows for easy transportation and installation, making it an attractive option for vending machines. However, it is generally less durable than steel and can be more expensive than carbon steel. Additionally, its lower strength may limit its use in high-load applications.
Impact on Application: Aluminum is suitable for components that require frequent handling or movement, such as doors or panels, but may not be ideal for structural supports.
Considerations for International Buyers: Compliance with standards like ASTM B221 is necessary. Buyers should also consider local sourcing options to minimize costs related to shipping and tariffs.
4. Polycarbonate
Key Properties: Polycarbonate is a strong, impact-resistant thermoplastic that offers excellent clarity and UV resistance. It is often used for transparent components in vending machines.
Pros & Cons: The primary advantage of polycarbonate is its lightweight and shatter-resistant properties, making it ideal for safety and visibility. However, it may not withstand high temperatures as well as metals and can be more expensive than other plastics.
Impact on Application: Polycarbonate is perfect for display panels or protective covers, allowing visibility of the products while ensuring safety.
Considerations for International Buyers: Buyers should verify compliance with relevant safety standards and consider the availability of polycarbonate in their region, as sourcing can vary significantly.
Summary Table
Material | Typical Use Case for ammunition vending machine | Key Advantage | Key Disadvantage/Limitation | Relative Cost (Low/Med/High) |
---|---|---|---|---|
Stainless Steel | Structural components, exterior casing | Excellent corrosion resistance | Higher cost, complex manufacturing | High |
Carbon Steel | Structural parts, load-bearing components | Cost-effective, high strength | Susceptible to corrosion | Low |
Aluminum | Lightweight panels, doors | Lightweight, easy to handle | Less durable than steel | Medium |
Polycarbonate | Display panels, protective covers | Impact-resistant, UV resistant | Limited temperature resistance | Medium |
This guide serves as a strategic reference for international B2B buyers looking to select the most suitable materials for their ammunition vending machines, ensuring they meet both performance and compliance requirements in their respective markets.
In-depth Look: Manufacturing Processes and Quality Assurance for ammunition vending machine
The manufacturing of ammunition vending machines involves a series of intricate processes and rigorous quality assurance protocols to ensure reliability and safety. For international B2B buyers, particularly from Africa, South America, the Middle East, and Europe, understanding these processes can be crucial for making informed procurement decisions.
Manufacturing Processes
1. Material Preparation
The manufacturing process begins with the selection of high-quality materials. Common materials include steel for the machine frame and components, glass or reinforced plastics for the display and dispensing mechanisms, and electronic components for operational functionality.
- Material Selection: It is essential to choose materials that not only meet operational requirements but also comply with regional regulations concerning safety and environmental impact.
- Preparation Techniques: Materials undergo cutting, shaping, and treatment (such as galvanization or powder coating) to enhance durability and resistance to wear.
2. Forming
In this stage, the prepared materials are shaped into the components necessary for the machine’s assembly.
- Techniques Used:
- CNC Machining: Computer Numerical Control (CNC) machines are employed for precision cutting and shaping of metal parts, ensuring accuracy and repeatability.
- Stamping and Molding: For parts that require complex shapes, stamping and injection molding techniques are utilized, particularly for plastic components.
This stage is crucial as it sets the foundation for the machine’s functionality and reliability.
3. Assembly
The assembly process involves putting together the various components to create the complete vending machine.
- Subassembly Groups: Components such as the dispensing unit, payment systems, and control boards are often pre-assembled before final assembly.
- Integration of Systems: This includes the installation of electronic systems for payment processing, inventory tracking, and user interface, ensuring that all systems work seamlessly together.
Efficient assembly techniques reduce production time and enhance the overall quality of the final product.
4. Finishing
Finishing touches are applied to improve aesthetics and protect against environmental factors.
- Surface Treatment: Techniques such as powder coating or painting are employed to provide a protective layer that also enhances the machine’s appearance.
- Quality Checks: At this stage, final quality checks are performed to ensure that all components are functioning correctly and that the machine meets design specifications.
Quality Assurance
Quality assurance (QA) is a critical component of the manufacturing process, ensuring that the machines meet both international standards and specific industry requirements.
International Standards
For B2B buyers, it is essential to verify that suppliers adhere to recognized international standards, such as:
- ISO 9001: This standard focuses on quality management systems, ensuring that manufacturers consistently provide products that meet customer and regulatory requirements.
- CE Marking: In Europe, CE marking indicates conformity with health, safety, and environmental protection standards.
- API Standards: For machines designed for military or law enforcement use, compliance with American Petroleum Institute (API) standards may also be required.
Quality Control Checkpoints
The QA process includes several critical checkpoints to ensure quality throughout the manufacturing cycle:
- Incoming Quality Control (IQC): Materials are inspected upon arrival to confirm they meet specified standards.
- In-Process Quality Control (IPQC): Ongoing inspections during the manufacturing process help catch defects early, allowing for timely corrections.
- Final Quality Control (FQC): A thorough inspection of the finished product ensures it meets all design and functional specifications before shipment.
Common Testing Methods
Testing is crucial to validate the performance and safety of ammunition vending machines:
- Functional Testing: Machines are tested for operational performance, including payment processing, product dispensing, and software functionality.
- Stress Testing: Components undergo stress tests to evaluate durability under heavy use conditions.
- Safety Testing: Compliance with safety standards is verified through rigorous testing of electrical and mechanical systems.
Verification of Supplier Quality Control
B2B buyers must establish a robust verification process to ensure that suppliers adhere to quality standards.
- Supplier Audits: Conducting regular audits of suppliers’ facilities can provide insights into their manufacturing processes and quality control measures.
- Quality Reports: Requesting detailed quality reports, including testing results and certifications, can help buyers assess a supplier’s commitment to quality.
- Third-Party Inspections: Engaging third-party inspection services can provide an unbiased evaluation of the manufacturing process and final product quality.
Quality Control Nuances for International Buyers
International buyers should be aware of specific nuances in quality control when sourcing ammunition vending machines:
- Regulatory Compliance: Different regions may have distinct regulatory requirements regarding ammunition handling and vending. Understanding these regulations is essential for compliance and operational success.
- Cultural Differences: Communication styles and business practices can vary significantly across regions. Establishing clear expectations and understanding local norms can enhance supplier relationships and facilitate smoother transactions.
- Logistical Considerations: Shipping and transportation can impact the quality of the final product. Buyers should discuss packaging and handling procedures with suppliers to mitigate damage during transit.
In summary, the manufacturing processes and quality assurance protocols for ammunition vending machines are complex yet vital for ensuring a reliable product. For B2B buyers, particularly those operating in diverse international markets, understanding these elements can significantly influence procurement decisions and operational success. By focusing on quality, compliance, and effective supplier relationships, businesses can enhance their operational capabilities and market offerings.
Related Video: Fast Automatic Ammo Production Factory – Modern Ammunition Manufacturing Process – Ammunition Plant
Comprehensive Cost and Pricing Analysis for ammunition vending machine Sourcing
To effectively navigate the cost structure and pricing landscape for sourcing ammunition vending machines, international B2B buyers must consider several key components that influence overall expenses and pricing strategies. Understanding these factors will enable buyers to make informed decisions and optimize their procurement processes.
Cost Components
-
Materials: The primary materials involved in manufacturing ammunition vending machines include high-grade steel for the machine structure, advanced electronics for payment and inventory management systems, and durable components to withstand environmental challenges. The choice of materials significantly impacts the overall cost, with higher quality materials often leading to increased durability and reduced long-term maintenance costs.
-
Labor: Labor costs can vary widely based on the region and the complexity of the machine. Skilled labor is essential for assembly and quality control. In regions with higher labor costs, such as parts of Europe, buyers may find that sourcing from countries with lower labor costs, like some South American or African nations, can yield significant savings.
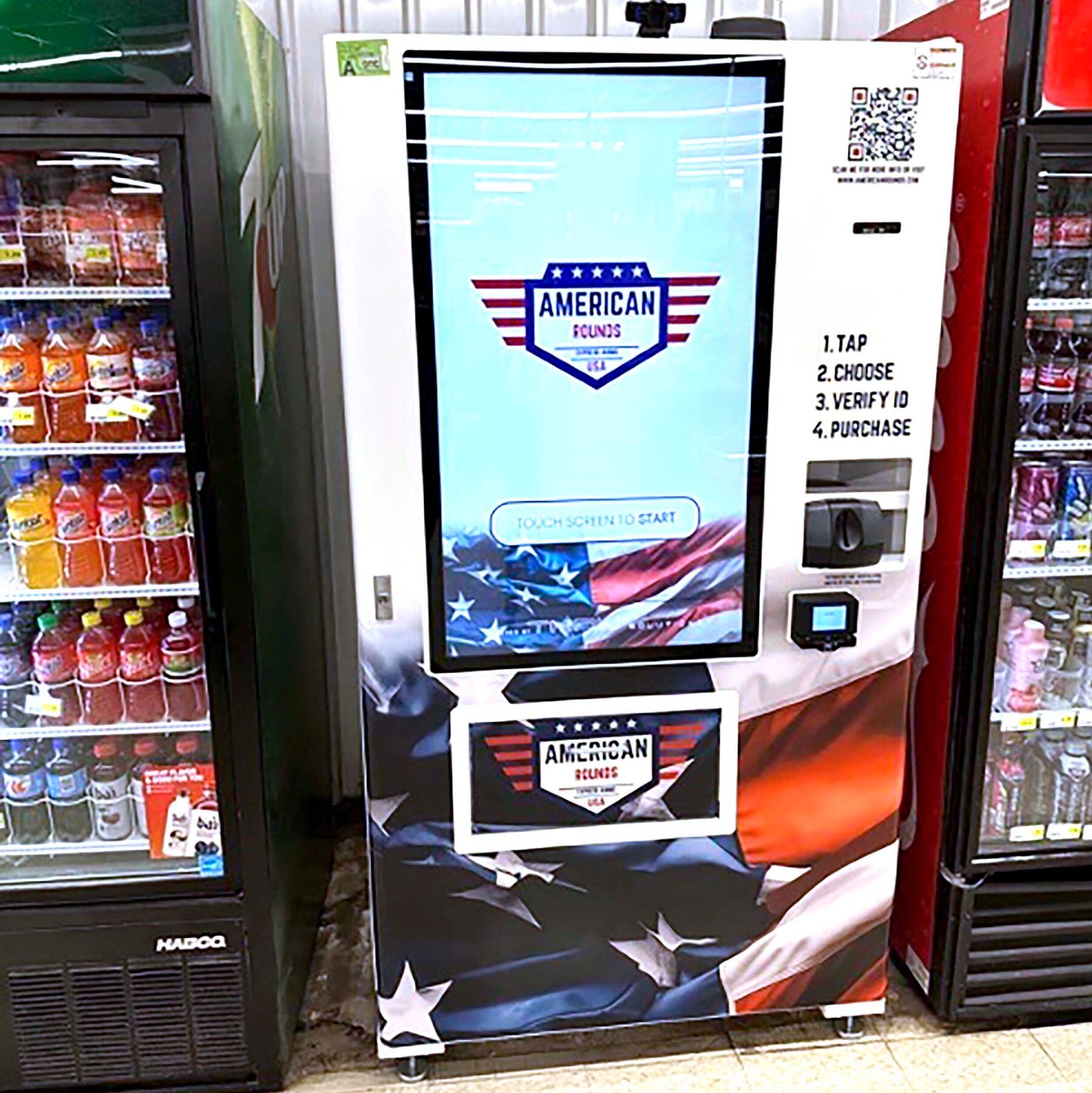
Illustrative Image (Source: Google Search)
-
Manufacturing Overhead: This includes costs associated with factory operations, utilities, and administrative expenses. Efficient manufacturing processes and economies of scale can help reduce overhead costs, making it vital for buyers to assess the production capabilities of potential suppliers.
-
Tooling: The initial investment in tooling can be substantial, especially for custom or specialized machines. Buyers should inquire about tooling costs and whether these are included in the quoted price or charged separately.
-
Quality Control (QC): Rigorous QC processes are essential to ensure the reliability and safety of ammunition vending machines. Costs associated with QC should be factored into the overall price. Suppliers with established QC certifications may command higher prices but offer greater assurance of product quality.
-
Logistics: Transportation and shipping costs can vary significantly depending on the destination, the method of transport, and the chosen Incoterms. International buyers must consider these costs, which can add a substantial amount to the total expenditure.
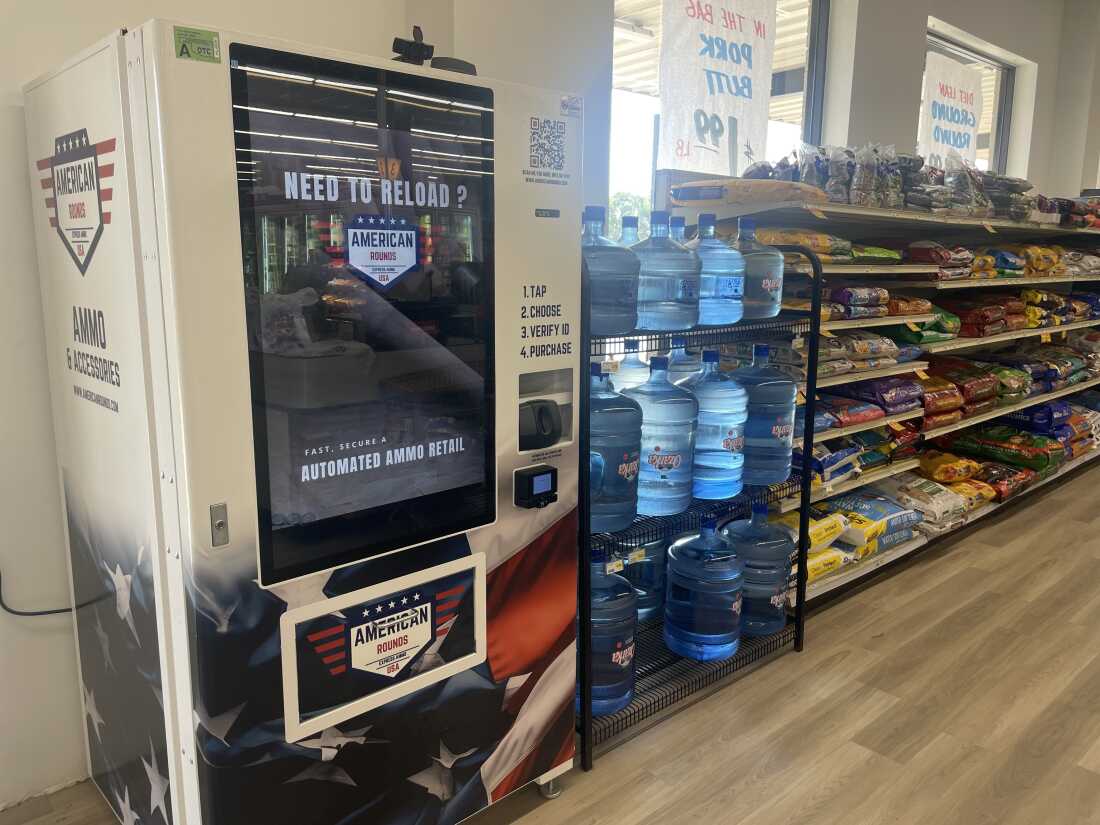
Illustrative Image (Source: Google Search)
- Margin: Supplier profit margins will affect the final price. Buyers should explore different suppliers to understand their pricing structures and negotiate for better terms.
Price Influencers
Several factors can influence the pricing of ammunition vending machines:
-
Volume/MOQ: Larger orders typically lead to lower per-unit costs due to economies of scale. Buyers should determine their Minimum Order Quantity (MOQ) to negotiate better pricing.
-
Specifications/Customization: Customization options can significantly impact pricing. Standard models will generally be more cost-effective than bespoke solutions. Buyers should weigh the benefits of customization against the additional costs involved.
-
Materials and Quality/Certifications: The choice of materials and the presence of quality certifications (e.g., ISO, CE) can affect both the cost and perceived value of the machines. Higher quality standards often justify higher prices.
-
Supplier Factors: The reputation and reliability of suppliers can influence pricing. Established suppliers may have higher prices due to their brand value and reliability, while emerging suppliers may offer lower prices to gain market share.
-
Incoterms: The chosen Incoterms can have a significant impact on logistics costs and responsibilities. Buyers should select terms that align with their logistical capabilities and financial strategies.
Buyer Tips
-
Negotiation: Engaging in negotiations with suppliers can yield better pricing and terms. Highlighting long-term partnership potential can be advantageous.
-
Cost-Efficiency: Consider the Total Cost of Ownership (TCO) rather than just the initial purchase price. This includes maintenance, energy consumption, and potential downtime costs.
-
Pricing Nuances: Be aware of pricing nuances in international markets. For example, currency fluctuations can affect pricing, as can regional tariffs and import duties.
-
Research Local Markets: Understanding regional market conditions in Africa, South America, the Middle East, and Europe can provide insights into competitive pricing and sourcing strategies.
-
Request Indicative Prices: Always ask for indicative pricing from multiple suppliers to gauge the market rate. This can provide leverage in negotiations and help identify fair pricing.
Disclaimer
Prices can vary significantly based on specifications, supplier relationships, and market conditions. Buyers should always request updated quotes and assess the complete cost structure before making procurement decisions.
Spotlight on Potential ammunition vending machine Manufacturers and Suppliers
This section offers a look at a few manufacturers active in the ‘ammunition vending machine’ market. This is a representative sample for illustrative purposes; B2B buyers must conduct their own extensive due diligence before any engagement. Information is synthesized from public sources and general industry knowledge.
Essential Technical Properties and Trade Terminology for ammunition vending machine
Key Technical Properties of Ammunition Vending Machines
When considering the procurement of ammunition vending machines, it is crucial to understand the specific technical properties that can affect both performance and compliance. Here are several critical specifications to consider:
-
Material Grade
– Definition: This refers to the quality and type of materials used in the construction of the vending machine, such as stainless steel or high-grade plastics.
– Importance: High-quality materials ensure durability and resistance to environmental factors, which is essential for machines placed in outdoor or high-traffic areas. This directly impacts the machine’s lifespan and maintenance costs. -
Tolerance Levels
– Definition: Tolerance levels indicate the acceptable limits of variation in dimensions and performance of machine components.
– Importance: Precise tolerances ensure that the ammunition is stored and dispensed correctly, reducing the risk of jams or misfires. For B2B buyers, understanding tolerances can help in assessing the reliability and safety of the vending machine. -
Capacity and Size
– Definition: This specification includes the number of ammunition types the machine can hold and its physical dimensions.
– Importance: A larger capacity can lead to fewer restocking trips and higher sales potential. Buyers must assess the space available for installation and the expected volume of sales. -
Power Requirements
– Definition: This covers the electrical specifications needed to operate the vending machine, including voltage and wattage.
– Importance: Understanding power requirements is essential for installation planning and ensuring compatibility with existing electrical systems. It also affects operational costs. -
Security Features
– Definition: These are built-in systems designed to prevent unauthorized access and ensure safe transactions, such as biometric scanners or reinforced locks.
– Importance: Given the sensitive nature of ammunition sales, robust security features are crucial for compliance with legal regulations and for protecting assets.
Common Trade Terminology in the Ammunition Vending Machine Industry
Familiarity with specific industry jargon can greatly enhance communication and negotiation effectiveness. Here are several essential terms:
-
OEM (Original Equipment Manufacturer)
– Definition: A company that produces parts or equipment that may be marketed by another manufacturer.
– Significance: Understanding OEM relationships can help buyers identify reputable sources for high-quality machines and parts, ensuring better reliability and service. -
MOQ (Minimum Order Quantity)
– Definition: The smallest quantity of a product that a supplier is willing to sell.
– Significance: Knowing the MOQ helps buyers in planning their purchases and managing inventory levels, which is particularly important in markets with fluctuating demand. -
RFQ (Request for Quotation)
– Definition: A document that a buyer sends to suppliers requesting pricing and terms for a specific product or service.
– Significance: Submitting an RFQ can help buyers gather competitive pricing and terms, facilitating informed decision-making. -
Incoterms (International Commercial Terms)
– Definition: A set of international rules that define the responsibilities of sellers and buyers for the delivery of goods under sales contracts.
– Significance: Familiarity with Incoterms is essential for understanding shipping responsibilities, costs, and risks, particularly for international buyers. -
Lead Time
– Definition: The time it takes from placing an order to receiving the product.
– Significance: Understanding lead times is crucial for inventory management and planning, especially in a business environment where timely access to ammunition is critical. -
Warranty Period
– Definition: The duration for which the manufacturer guarantees the product against defects.
– Significance: Knowing the warranty period can influence purchasing decisions, as it reflects the manufacturer’s confidence in the product and can reduce long-term costs related to repairs and replacements.
By understanding these specifications and terms, international B2B buyers can make more informed decisions when sourcing ammunition vending machines, ensuring they meet both operational needs and compliance standards.
Navigating Market Dynamics, Sourcing Trends, and Sustainability in the ammunition vending machine Sector
Market Overview & Key Trends
The ammunition vending machine sector is witnessing transformative growth fueled by several global drivers. Increasing demand for self-service solutions in military, law enforcement, and civilian markets is propelling advancements in vending technology. This trend is particularly pronounced in regions like Africa, South America, the Middle East, and Europe, where rapid urbanization and rising security concerns are driving the need for accessible ammunition supplies.
Emerging B2B technologies, such as IoT-enabled vending machines, are revolutionizing inventory management. These machines provide real-time data analytics, allowing operators to monitor stock levels, track sales patterns, and streamline reordering processes. This capability is crucial for international buyers seeking to maintain optimal inventory levels while minimizing operational costs.
Additionally, there is a growing focus on customizability and user experience. Vending solutions that cater to specific needs—such as different caliber ammunition or specialized training rounds—are becoming increasingly popular. Buyers from diverse regions can leverage this trend by sourcing machines that offer tailored solutions to meet local market demands.
Moreover, partnerships and collaborations among manufacturers, suppliers, and technology providers are strengthening the supply chain dynamics. This collaborative approach not only enhances product offerings but also fosters innovation, enabling international buyers to access cutting-edge solutions that drive competitive advantage.
Sustainability & Ethical Sourcing in B2B
As sustainability becomes a focal point across industries, the ammunition vending machine sector is not left behind. The environmental impact of ammunition production and vending necessitates a commitment to ethical sourcing and responsible manufacturing practices. International buyers are increasingly prioritizing suppliers who adhere to stringent environmental standards and demonstrate a commitment to reducing their carbon footprint.
Ethical supply chains are vital for ensuring the integrity of the sourcing process. Buyers should seek vendors who utilize sustainable materials, such as recycled metals and eco-friendly packaging, in their vending machines and ammunition products. Certifications like ISO 14001 (Environmental Management) and ISO 50001 (Energy Management) can serve as benchmarks for assessing a supplier’s sustainability practices.
Incorporating green materials not only aligns with global sustainability goals but can also enhance brand reputation and customer loyalty. By promoting environmentally responsible practices, businesses can appeal to a broader customer base, particularly in regions where consumers are increasingly conscientious about environmental issues. International buyers should prioritize partnerships with suppliers who share these values, as this can lead to a more resilient and responsible supply chain.
Brief Evolution/History
The concept of vending machines has evolved significantly since their inception in the late 19th century, transitioning from simple mechanisms dispensing snacks to sophisticated machines capable of offering complex products like ammunition. The introduction of self-service ammunition vending machines emerged in response to the growing demand for quick and secure access to ammunition for law enforcement and military personnel.
In recent years, technological advancements have further propelled this sector, integrating features such as biometric authentication, digital payment systems, and inventory tracking. This evolution reflects a broader shift towards automation and efficiency in the defense industry, enabling international B2B buyers to adapt to changing market dynamics and consumer preferences. As the sector continues to evolve, the focus on innovative solutions and sustainability will be crucial for long-term success.
Related Video: Global Trade & Logistics – What is Global Trade?
Frequently Asked Questions (FAQs) for B2B Buyers of ammunition vending machine
-
What should I consider when vetting suppliers for ammunition vending machines?
When vetting suppliers, prioritize their experience in the industry and their understanding of international regulations. Verify their certifications and compliance with local laws in your region, especially concerning ammunition handling and vending. Request references from other clients and assess their ability to provide ongoing support and maintenance. Additionally, evaluate their supply chain reliability, including lead times and product availability, to ensure they can meet your operational demands consistently. -
Can I customize an ammunition vending machine to fit my specific needs?
Yes, many suppliers offer customization options for ammunition vending machines. Discuss your requirements regarding size, product selection, and branding. Customization can also include security features, payment methods, and user interfaces tailored to your target market. Ensure that the supplier can accommodate these modifications within your budget and timeline, and request samples or prototypes to evaluate the final product before full-scale production. -
What are typical minimum order quantities (MOQ) and lead times for ammunition vending machines?
MOQs can vary significantly based on the supplier and the complexity of the vending machine. Generally, expect MOQs to range from 1 to 10 units for standard models, while custom machines may require higher quantities. Lead times typically span from 4 to 12 weeks, depending on the customization level and supplier capacity. It’s crucial to discuss these parameters upfront to align your procurement schedule with your operational needs. -
How do I ensure quality assurance and certifications for the machines?
Request comprehensive documentation from suppliers that outlines their quality assurance processes and relevant certifications, such as ISO standards. Look for evidence of third-party testing and compliance with international safety regulations. Establish a clear agreement regarding quality control measures, including inspections and testing before shipment. Periodically review the supplier’s performance to ensure they maintain the agreed standards throughout the partnership. -
What logistics considerations should I keep in mind when sourcing from international suppliers?
Logistics is critical in the procurement process for ammunition vending machines. Assess the supplier’s shipping capabilities, including their experience with customs clearance and handling of sensitive products like ammunition. Determine the shipping costs and timelines, and consider using a freight forwarder to manage logistics efficiently. Additionally, familiarize yourself with import/export regulations in your country to avoid compliance issues that could delay delivery. -
How can I resolve disputes with suppliers during the procurement process?
To manage disputes effectively, establish clear communication channels and a framework for conflict resolution from the outset. Document all agreements, including timelines, costs, and quality expectations, in a formal contract. If issues arise, approach the supplier with specific concerns and seek a collaborative solution. If necessary, consider mediation or arbitration to resolve disputes without damaging the business relationship. Always maintain a professional demeanor to facilitate productive discussions. -
What payment terms should I negotiate with international suppliers?
Payment terms can vary widely, so it’s essential to negotiate terms that protect your cash flow while ensuring supplier commitment. Common arrangements include deposits of 30-50% upfront, with the balance due upon delivery or after installation. Consider using secure payment methods, such as letters of credit or escrow services, to mitigate risk. It’s advisable to conduct due diligence on the supplier’s financial stability to ensure they can fulfill their obligations. -
What ongoing support and maintenance should I expect after purchasing an ammunition vending machine?
Post-purchase support is vital for the longevity of your vending machines. Discuss with suppliers about warranties, technical support, and maintenance services offered. A good supplier should provide training for your staff on machine operation and troubleshooting, as well as access to spare parts. Ensure that there is a clear service agreement that outlines response times for repairs and ongoing maintenance schedules to minimize downtime and ensure operational efficiency.
Strategic Sourcing Conclusion and Outlook for ammunition vending machine
In conclusion, the success of an ammunition vending machine operation hinges on effective strategic sourcing and robust supplier relationships. Key takeaways for international B2B buyers include the importance of understanding local market demands, aligning product offerings with customer preferences, and selecting reliable wholesale partners. By prioritizing quality, affordability, and consistency in supply, businesses can enhance profitability and operational efficiency.
As global security concerns rise, the demand for efficient ammunition distribution solutions is paramount. This presents a unique opportunity for buyers from Africa, South America, the Middle East, and Europe to invest in innovative vending solutions that meet local needs. By leveraging advanced technology and strategic sourcing practices, businesses can position themselves competitively in the evolving landscape of ammunition supply.
Now is the time to act. Engage with leading manufacturers and suppliers to explore tailored solutions that can streamline your operations and meet the growing demands of your market. Embrace this opportunity to transform your business and stay ahead in a rapidly changing environment.