Unlock Profits with Used Vending Machines for Sale Nearby:
Guide to Used Vending Machines For Sale Nearby
- Introduction: Navigating the Global Market for used vending machines for sale nearby
- Understanding used vending machines for sale nearby Types and Variations
- Key Industrial Applications of used vending machines for sale nearby
- Strategic Material Selection Guide for used vending machines for sale nearby
- In-depth Look: Manufacturing Processes and Quality Assurance for used vending machines for sale nearby
- Comprehensive Cost and Pricing Analysis for used vending machines for sale nearby Sourcing
- Spotlight on Potential used vending machines for sale nearby Manufacturers and Suppliers
- Essential Technical Properties and Trade Terminology for used vending machines for sale nearby
- Navigating Market Dynamics, Sourcing Trends, and Sustainability in the used vending machines for sale nearby Sector
- Frequently Asked Questions (FAQs) for B2B Buyers of used vending machines for sale nearby
- Strategic Sourcing Conclusion and Outlook for used vending machines for sale nearby
Introduction: Navigating the Global Market for used vending machines for sale nearby
In today’s dynamic global market, the demand for used vending machines is rapidly increasing, driven by their cost-effectiveness and versatility. For B2B buyers from regions such as Africa, South America, the Middle East, and Europe, sourcing these machines locally can lead to significant savings and operational efficiencies. Whether you’re looking to expand your current offerings or enter the vending sector, understanding the nuances of the used vending machine market is crucial.
This guide serves as an essential resource, providing a comprehensive overview of various types of used vending machines, including food, beverage, and specialty machines. We delve into the materials used in their construction, ensuring that you can assess durability and reliability. Additionally, we cover critical aspects like manufacturing standards and quality control processes, which are vital for maintaining operational integrity.
Moreover, this guide outlines key suppliers and their offerings, enabling you to make informed decisions based on reputation and service quality. We also discuss pricing strategies and market trends that can impact your purchasing power, alongside frequently asked questions that address common concerns.
By equipping international B2B buyers with the knowledge needed to navigate this market, you will be empowered to make strategic sourcing decisions that align with your business goals. Whether you’re based in the UAE, Colombia, or elsewhere, this guide is tailored to enhance your procurement strategy in the used vending machine sector.
Understanding used vending machines for sale nearby Types and Variations
Type Name | Key Distinguishing Features | Primary B2B Applications | Brief Pros & Cons for Buyers |
---|---|---|---|
Snack Vending Machines | Designed for snacks, chips, and candy | Offices, schools, and convenience stores | Pros: Easy to stock, quick sales. Cons: Limited product variety. |
Beverage Vending Machines | Dispenses drinks, including sodas and juices | Restaurants, gyms, and public spaces | Pros: High demand, quick turnover. Cons: Requires refrigeration. |
Combo Vending Machines | Offers both snacks and beverages in one unit | Airports, malls, and large venues | Pros: Versatile, maximizes space. Cons: More complex maintenance. |
Healthy Food Vending Machines | Focuses on healthier snack options | Workplaces, schools, and gyms | Pros: Appeals to health-conscious consumers. Cons: Higher upfront costs. |
Specialty Vending Machines | Customized for specific products (e.g., electronics, cosmetics) | Retail settings, events, and exhibitions | Pros: Unique offerings can attract niche markets. Cons: May require specialized knowledge for operation. |
Snack Vending Machines
Snack vending machines are specifically designed to dispense a variety of snacks, such as chips, candy, and granola bars. They are ideal for high-traffic areas like offices and schools, where quick, easy access to snacks is appreciated. When purchasing, consider the machine’s capacity and the types of snacks you wish to offer, as well as the ease of restocking and maintenance. These machines typically have a lower upfront investment but may offer limited product variety.
Beverage Vending Machines
These machines are tailored to dispense beverages, ranging from sodas to bottled water and juices. They are commonly found in gyms, restaurants, and public spaces due to their high demand and quick turnover. When considering a beverage vending machine, buyers should focus on the refrigeration capabilities and the variety of drinks offered. While they can generate significant sales, they also require more frequent maintenance and restocking.
Combo Vending Machines
Combo vending machines provide both snacks and beverages within a single unit, making them a versatile option for locations like airports and malls. Their dual offerings maximize space and cater to a wider customer base. Buyers should evaluate the machine’s layout and the ease of stocking both types of products. While they can attract more customers, these machines may involve more complex maintenance compared to single-product machines.
Healthy Food Vending Machines
These machines emphasize healthier snack options, catering to the growing demand for nutritious food choices in workplaces, schools, and gyms. They often feature fresh fruits, nuts, and low-calorie snacks. When purchasing, businesses should consider the machine’s ability to keep products fresh and the potential for higher upfront costs. However, they can tap into a health-conscious market, potentially leading to increased sales.
Specialty Vending Machines
Specialty vending machines are customized to dispense unique products, such as electronics, cosmetics, or gourmet foods. They are often used in retail settings, events, and exhibitions to attract niche markets. Buyers should consider the specific needs of their target audience and the machine’s operational requirements. Although they can offer distinct advantages in terms of product differentiation, they may require specialized knowledge for effective operation and maintenance.
Related Video: How to Find Vending Machines for Sale in South Africa | Starting a Vending Machine Business
Key Industrial Applications of used vending machines for sale nearby
Industry/Sector | Specific Application of used vending machines for sale nearby | Value/Benefit for the Business | Key Sourcing Considerations for this Application |
---|---|---|---|
Food & Beverage | Snack and beverage distribution in offices and factories | Increased employee satisfaction and productivity | Machine capacity, product variety, and payment systems |
Healthcare | Medication dispensing in clinics and hospitals | Improved patient adherence to medication schedules | Compliance with health regulations, security features |
Education | Campus food services and supplies | Enhanced student experience and convenience | Durability, product range, and payment options |
Retail | Point-of-sale for small items in convenience stores | Increased sales through 24/7 availability | Size, product compatibility, and maintenance support |
Events & Entertainment | Concession stands for events like concerts and festivals | Streamlined service and increased revenue during events | Mobility, ease of setup, and product storage capabilities |
Food & Beverage
Used vending machines are ideal for distributing snacks and beverages in workplaces, significantly enhancing employee morale and productivity. They solve the problem of accessibility to quick refreshments, especially in remote areas or large facilities. International buyers should consider the machine’s capacity and product variety to cater to diverse tastes, as well as the payment systems available, which can impact user experience.
Healthcare
In healthcare settings, used vending machines can be repurposed for medication dispensing, providing patients with easy access to their prescribed drugs. This application addresses the challenge of patient compliance by ensuring medications are available at the right time. Buyers in this sector must prioritize compliance with health regulations, ensuring machines have necessary security features to protect sensitive information and medications.
Education
Used vending machines serve as convenient food service points on educational campuses, allowing students to access meals and snacks quickly. This application enhances the student experience, catering to their busy schedules. Buyers from educational institutions should focus on the machines’ durability and the range of products offered, ensuring they meet the dietary needs of a diverse student body while also considering payment options that facilitate easy transactions.
Retail
In the retail sector, used vending machines can function as additional points-of-sale for small items in convenience stores. This 24/7 availability allows retailers to increase sales without needing additional staff, catering to customers looking for quick purchases. Buyers should evaluate machine size to fit their store layout, product compatibility to meet customer demands, and maintenance support to ensure smooth operations.
Events & Entertainment
For events like concerts and festivals, used vending machines can effectively serve as concession stands, providing attendees with quick access to food and drinks. This application streamlines service during high-traffic periods, enhancing the overall event experience and boosting revenue. Buyers should consider the machines’ mobility for easy setup, ease of product storage, and the capability to handle high-volume sales during events.
Related Video: What to look for when buying used vending machines ✅
Strategic Material Selection Guide for used vending machines for sale nearby
When selecting materials for used vending machines, international B2B buyers must consider various factors that influence performance, durability, and compliance with regional standards. Below is an analysis of common materials used in vending machines, focusing on their properties, advantages, disadvantages, and specific considerations for buyers from Africa, South America, the Middle East, and Europe.
1. Stainless Steel
Key Properties:
Stainless steel is renowned for its corrosion resistance and high strength-to-weight ratio. It can withstand a wide range of temperatures and pressures, making it suitable for various environments.
Pros & Cons:
Stainless steel is highly durable and resistant to rust, which is crucial for machines exposed to moisture. However, it is more expensive than other materials, and its manufacturing can be complex due to the need for specialized tools.
Impact on Application:
This material is compatible with a variety of media, including food and beverages, making it ideal for vending machines. Its non-reactive nature ensures that it does not contaminate the products inside.
Considerations for International Buyers:
Buyers should ensure compliance with food safety standards (e.g., FDA, EU regulations) and consider local preferences for finishes (e.g., brushed vs. polished). Common standards such as ASTM or DIN may apply, depending on the region.
2. Carbon Steel
Key Properties:
Carbon steel offers good strength and is cost-effective, but it is susceptible to corrosion without adequate protective coatings.
Pros & Cons:
While carbon steel is relatively inexpensive and easy to fabricate, its durability can be compromised in humid or corrosive environments. Protective coatings can mitigate this, but they add to the overall cost.
Impact on Application:
Carbon steel is suitable for structural components of vending machines but may not be ideal for areas exposed to moisture unless properly treated.
Considerations for International Buyers:
Buyers should be aware of the need for protective coatings in humid climates, particularly in regions like Africa and South America. Compliance with local standards for structural integrity is also essential.
3. Aluminum
Key Properties:
Aluminum is lightweight, corrosion-resistant, and has good thermal conductivity, making it suitable for various applications.
Pros & Cons:
The lightweight nature of aluminum allows for easier transport and installation. However, it is less durable than stainless steel and can be prone to denting under impact.
Impact on Application:
Aluminum is often used for the outer casing of vending machines, providing a balance between aesthetics and functionality. Its corrosion resistance makes it suitable for outdoor use.
Considerations for International Buyers:
Buyers should consider the local climate when selecting aluminum, as extreme temperatures can affect its performance. Compliance with local standards for weight and material safety is also important.
4. Polycarbonate
Key Properties:
Polycarbonate is a high-performance plastic known for its impact resistance and transparency.
Pros & Cons:
While polycarbonate is lightweight and can be molded into complex shapes, it is less resistant to UV light and can yellow over time. It is also less durable than metals.
Impact on Application:
This material is often used for windows and display areas in vending machines, allowing visibility of products while providing protection.
Considerations for International Buyers:
Buyers should ensure that polycarbonate components comply with local safety and environmental regulations. UV resistance is particularly important in sunny regions like the Middle East.
Summary Table
Material | Typical Use Case for used vending machines for sale nearby | Key Advantage | Key Disadvantage/Limitation | Relative Cost (Low/Med/High) |
---|---|---|---|---|
Stainless Steel | Structural and external components in food vending machines | Excellent corrosion resistance, durable | High cost, complex manufacturing | High |
Carbon Steel | Structural components, internal frames | Cost-effective, strong | Susceptible to corrosion without coatings | Low |
Aluminum | Outer casing, display areas | Lightweight, corrosion-resistant | Less durable, prone to denting | Medium |
Polycarbonate | Windows and display sections | Impact-resistant, allows visibility | Less UV resistant, can yellow over time | Medium |
This strategic material selection guide provides essential insights for B2B buyers in the vending machine market, helping them make informed decisions that align with their operational needs and regional compliance requirements.
In-depth Look: Manufacturing Processes and Quality Assurance for used vending machines for sale nearby
Understanding the Manufacturing Process of Used Vending Machines
The manufacturing of used vending machines involves several key stages that ensure the machines are functional, durable, and meet the necessary standards for resale. For B2B buyers, particularly those from Africa, South America, the Middle East, and Europe, understanding these stages is crucial for making informed purchasing decisions.
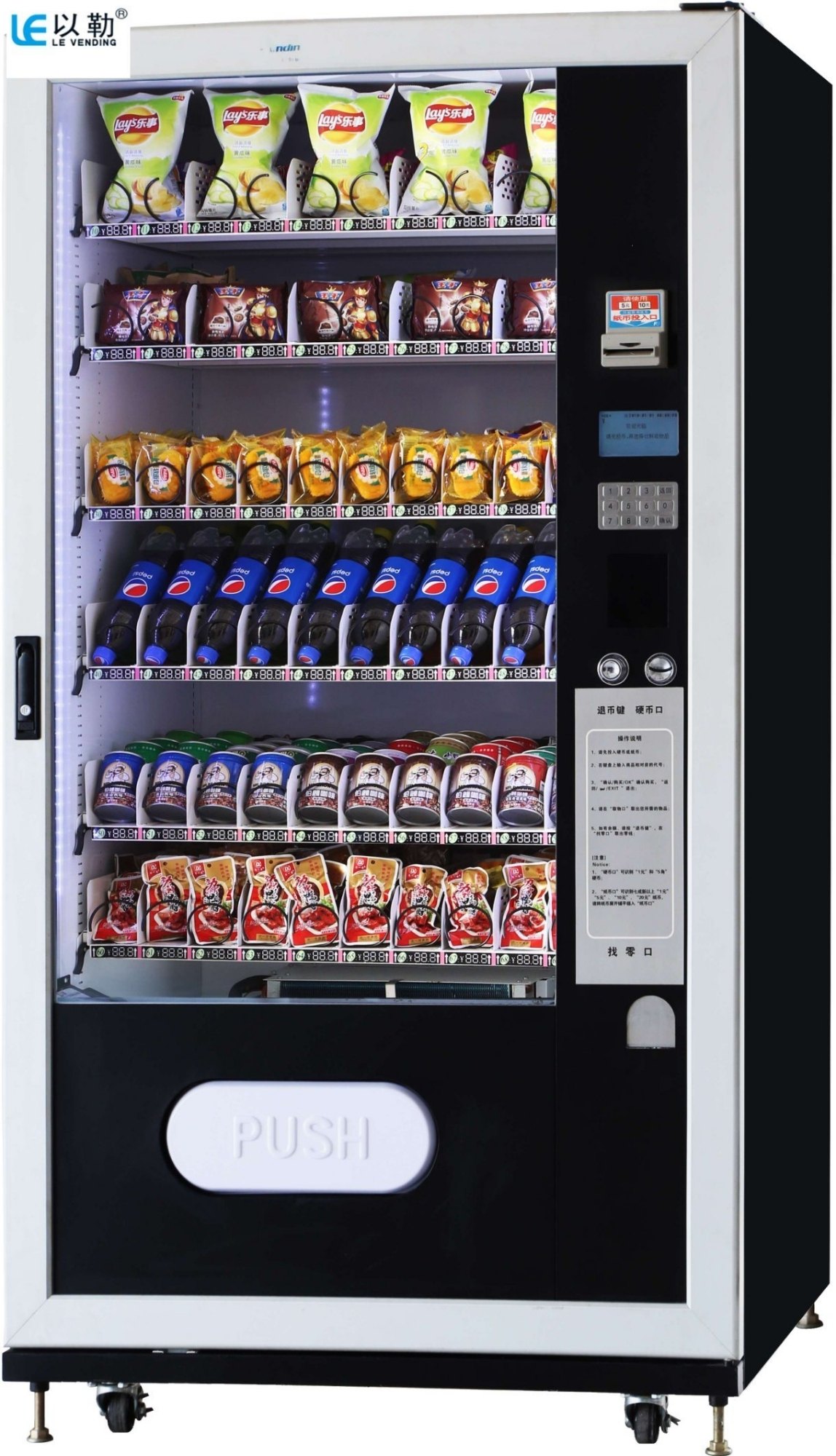
Illustrative Image (Source: Google Search)
Main Stages of Manufacturing
-
Material Preparation
– Sourcing: Quality raw materials are sourced, including metals, plastics, and electronic components. Suppliers should provide material certifications to ensure compliance with relevant standards.
– Cutting and Shaping: Metals are cut and shaped using techniques such as laser cutting or stamping. This process requires precision to maintain structural integrity. -
Forming
– Molding and Casting: Plastic components may be produced through injection molding, while metal parts can be cast. Techniques like CNC machining are often used to achieve tight tolerances.
– Assembly of Subcomponents: Individual parts such as coin mechanisms, displays, and refrigeration units are assembled. This stage often employs automated assembly lines to enhance efficiency. -
Assembly
– Final Assembly: All components are brought together, including wiring and software installation. The assembly line may include stations for different functions, such as electronics integration and final casing.
– Quality Control Checks: At various points in the assembly process, quality checks are performed to ensure that parts are assembled correctly and function as intended. -
Finishing
– Surface Treatment: This can include painting, powder coating, or anodizing to enhance durability and appearance. Proper finishing not only improves aesthetics but also protects against corrosion.
– Final Inspection: Once the machines are fully assembled, a thorough inspection is conducted to ensure they meet all specifications before shipping.
Quality Assurance Standards
For B2B buyers, understanding the quality assurance measures in place is vital to ensure they are investing in reliable products. Various international and industry-specific standards govern the manufacturing processes of used vending machines.
Relevant International Standards
- ISO 9001: This standard outlines the criteria for a quality management system. Compliance indicates that the manufacturer has a systematic approach to managing their processes and ensuring quality.
- CE Marking: This signifies that the product complies with EU safety, health, and environmental protection standards. It is essential for machines sold in European markets.
- API Standards: For vending machines that dispense food or beverages, adherence to standards set by the American Petroleum Institute (API) may be necessary.
Quality Control Checkpoints
- Incoming Quality Control (IQC): Materials and components are inspected upon arrival to ensure they meet required specifications.
- In-Process Quality Control (IPQC): Quality checks are performed at various stages of the manufacturing process to catch defects early.
- Final Quality Control (FQC): The finished product undergoes a comprehensive inspection, including functionality tests and safety checks.
Testing Methods
To verify the quality of used vending machines, manufacturers employ various testing methods, including:
– Functional Testing: Each machine is tested to ensure all components work correctly, including payment systems, refrigeration units, and user interfaces.
– Durability Testing: Machines are subjected to stress tests to assess their performance under different conditions, simulating real-world usage.
– Compliance Testing: Ensuring the machines meet all regulatory standards, which may involve third-party certification bodies.
Verifying Supplier Quality Control
For international B2B buyers, particularly those operating in diverse regulatory environments, verifying a supplier’s quality control measures is essential. Here are several strategies to ensure quality:
-
Supplier Audits: Conduct regular audits of suppliers’ manufacturing facilities to assess their compliance with quality standards. This can include reviewing their quality management systems and manufacturing processes.
-
Requesting Quality Reports: Suppliers should provide documentation of their quality control processes, including inspection reports and compliance certificates.
-
Third-Party Inspections: Engaging third-party inspection agencies can offer an unbiased assessment of the manufacturer’s processes and products, ensuring adherence to international standards.
-
Certifications Verification: Verify any certifications claimed by the supplier, such as ISO or CE, through official channels to ensure authenticity.
Considerations for International Buyers
B2B buyers from regions like Africa, South America, the Middle East, and Europe must navigate various challenges related to quality assurance in used vending machines. Here are some key points to consider:
-
Cultural and Regulatory Differences: Understand the local regulations that may affect the import and use of vending machines in your region. This includes compliance with safety and health standards.
-
Logistics and Supply Chain: Consider the logistics involved in shipping used machines, including potential tariffs and import duties. Ensure your supplier is familiar with the logistics of international shipping.
-
Warranty and Support: Establish clear terms regarding warranties and after-sales support. Given the complexities of used machinery, having a reliable support system is crucial for maintenance and troubleshooting.
In conclusion, a thorough understanding of the manufacturing processes and quality assurance practices for used vending machines is vital for B2B buyers. By focusing on these aspects, buyers can make informed decisions that align with their operational needs and regulatory requirements.
Related Video: Most Satisfying Factory Production Processes And Heavy-Duty Factory Machines!
Comprehensive Cost and Pricing Analysis for used vending machines for sale nearby Sourcing
When considering the acquisition of used vending machines, understanding the comprehensive cost structure and pricing analysis is crucial for international B2B buyers. This analysis not only aids in budget planning but also enhances negotiation strategies and overall purchasing decisions.
Cost Components
-
Materials: The primary cost driver for used vending machines is the materials used in their construction. This includes the casing, mechanical parts, and electronic components. Buyers should assess the quality and condition of these materials, as they directly impact the machine’s lifespan and functionality.
-
Labor: Labor costs encompass the workforce involved in refurbishing and maintaining the vending machines. This includes the costs of disassembling, cleaning, repairing, and reassembling the machines. Labor costs can vary significantly based on the geographic location of the supplier.
-
Manufacturing Overhead: This includes indirect costs associated with production, such as utilities, rent, and administrative expenses. Understanding these overheads can help buyers gauge the overall pricing strategy of suppliers.
-
Tooling: If customization is required, tooling costs may be incurred. This involves the creation of specialized tools or molds necessary for modifications, which can increase the overall cost of the machines.
-
Quality Control (QC): Effective quality control processes ensure that the vending machines meet safety and operational standards. QC costs should be factored into the pricing, as rigorous testing can enhance reliability but may also increase the purchase price.
-
Logistics: Transportation and shipping costs are critical, especially for international buyers. These costs can vary based on distance, mode of transport, and any tariffs or duties applicable to the destination country.
-
Margin: Supplier profit margins can vary widely based on market conditions, competition, and the perceived value of the vending machines. Understanding the margin can help buyers assess whether they are receiving a fair price.
Price Influencers
Several factors can influence the pricing of used vending machines:
-
Volume/MOQ: Bulk purchases may lead to lower per-unit costs. Suppliers often offer discounts for larger orders, making it advantageous for buyers to consolidate their purchases.
-
Specifications/Customization: Machines with specific features or customizations typically come at a premium. Buyers should evaluate their needs against the potential added costs of custom features.
-
Materials and Quality Certifications: Machines constructed with high-quality materials or certified for safety and performance may carry higher prices. Buyers should weigh the importance of certifications against cost.
-
Supplier Factors: The reputation and reliability of the supplier can significantly affect pricing. Established suppliers may charge more due to perceived quality and service levels.
-
Incoterms: Understanding international shipping terms can impact the total cost. Terms like FOB (Free on Board) and CIF (Cost, Insurance, and Freight) dictate who bears the cost and risk at different points in the shipping process.
Buyer Tips
-
Negotiation: Always negotiate pricing. Suppliers expect some level of discussion and may have flexibility in their pricing, especially for larger orders.
-
Cost-Efficiency: Evaluate the total cost of ownership, not just the initial purchase price. Consider maintenance, operational efficiency, and potential downtime when calculating costs.
-
Pricing Nuances: Be aware of the differences in pricing strategies across regions. For instance, suppliers in the UAE may have different pricing models compared to those in Colombia or South Africa due to varying market demands and operational costs.
-
Disclaimer for Indicative Prices: Prices for used vending machines can fluctuate based on market conditions, machine condition, and specific buyer requirements. It is essential to obtain quotes from multiple suppliers to ensure competitive pricing.
By thoroughly understanding these cost structures and pricing influences, international B2B buyers can make informed decisions, leading to more effective sourcing of used vending machines.
Spotlight on Potential used vending machines for sale nearby Manufacturers and Suppliers
This section offers a look at a few manufacturers active in the ‘used vending machines for sale nearby’ market. This is a representative sample for illustrative purposes; B2B buyers must conduct their own extensive due diligence before any engagement. Information is synthesized from public sources and general industry knowledge.
Essential Technical Properties and Trade Terminology for used vending machines for sale nearby
When considering the purchase of used vending machines, understanding their technical properties and trade terminology is crucial for making informed decisions. This knowledge not only aids in assessing the machines’ suitability but also ensures smooth transactions across international borders.
Critical Technical Specifications
-
Material Grade
– Definition: Refers to the quality of materials used in the construction of the vending machine, often specified in terms of metal types (e.g., stainless steel, aluminum).
– Importance: High-grade materials enhance durability and resistance to corrosion, which is vital for machines exposed to various environmental conditions, particularly in regions with high humidity or extreme temperatures. -
Capacity
– Definition: This specification indicates the volume or number of items a vending machine can hold, measured in terms of product slots or total weight.
– Importance: Understanding capacity is essential for businesses aiming to meet consumer demand effectively. A machine with insufficient capacity may lead to lost sales, while an overly large machine may incur higher operational costs. -
Power Requirements
– Definition: Details the electrical specifications needed for operation, including voltage (e.g., 110V, 220V) and wattage.
– Importance: Ensuring that the power requirements match the local electrical supply is critical to avoid operational failures. This is particularly important for international buyers who may encounter different electrical standards. -
Temperature Control
– Definition: Refers to the ability of the vending machine to maintain specific temperatures for perishable items, often expressed in degrees Celsius or Fahrenheit.
– Importance: For machines selling food or beverages, effective temperature control is vital for product safety and quality. Buyers must verify that the machines meet local health regulations regarding food storage. -
Dimensions and Weight
– Definition: The physical size and weight of the vending machine, typically provided in inches or centimeters.
– Importance: Knowledge of dimensions is essential for determining placement options, especially in confined spaces. The weight can also influence transportation costs and logistics.
Common Trade Terminology
-
OEM (Original Equipment Manufacturer)
– Definition: Refers to the company that originally manufactured the vending machine or its components.
– Importance: Identifying whether parts are OEM can affect the reliability and compatibility of replacement parts, which is crucial for maintenance and repair. -
MOQ (Minimum Order Quantity)
– Definition: The smallest quantity of a product that a supplier is willing to sell.
– Importance: Understanding MOQ is important for budgeting and inventory planning. It helps buyers gauge whether they can meet the supplier’s requirements or if they need to source from another vendor. -
RFQ (Request for Quotation)
– Definition: A formal request sent to suppliers to obtain pricing and terms for specific products.
– Importance: Issuing an RFQ allows buyers to compare offers from different suppliers, ensuring competitive pricing and favorable terms. -
Incoterms (International Commercial Terms)
– Definition: A set of predefined international trade terms that delineate the responsibilities of buyers and sellers regarding the delivery of goods.
– Importance: Familiarity with Incoterms is essential for international transactions, as they clarify who is responsible for shipping costs, insurance, and risk during transit. -
Warranty Period
– Definition: The time frame during which the manufacturer or seller guarantees the machine against defects or failures.
– Importance: A longer warranty period can indicate a higher quality product and provides peace of mind for the buyer, reducing the risk of unexpected costs.
By understanding these technical specifications and trade terms, international buyers can make more informed decisions, ensuring that their investment in used vending machines aligns with their operational needs and market demands.
Navigating Market Dynamics, Sourcing Trends, and Sustainability in the used vending machines for sale nearby Sector
The global market for used vending machines is witnessing dynamic changes fueled by various factors influencing B2B buying behaviors. Key drivers include the increasing demand for cost-effective solutions in retail and food service, as businesses seek to maximize operational efficiency while minimizing expenditures. Emerging technological trends such as cashless payment systems and IoT connectivity are reshaping the functionality of vending machines, making them more attractive to buyers. Additionally, the rise of e-commerce platforms facilitates access to a broader selection of used vending machines, allowing buyers from regions like Africa, South America, the Middle East, and Europe to source equipment with greater ease.
International buyers are also increasingly focused on local sourcing to reduce shipping costs and environmental impacts. This trend is particularly relevant in regions like the UAE, where local suppliers are becoming more prominent. Furthermore, the post-pandemic environment has shifted consumer preferences, with a growing emphasis on hygiene and contactless solutions in vending operations. Buyers should be aware of these trends to leverage opportunities effectively, ensuring they remain competitive in their respective markets.
Sustainability & Ethical Sourcing in B2B
Sustainability is becoming a cornerstone of purchasing decisions in the used vending machine sector. The environmental impact of manufacturing new machines is significant, prompting buyers to consider the benefits of purchasing used equipment. This not only reduces waste but also conserves resources by extending the life cycle of existing machines.
Moreover, ethical sourcing practices are gaining traction, with buyers increasingly demanding transparency in supply chains. Green certifications and eco-friendly materials are becoming critical factors in sourcing decisions. Buyers should look for suppliers that can demonstrate adherence to sustainability standards, such as those certified by organizations like the Forest Stewardship Council (FSC) or other relevant bodies. Implementing sustainable practices not only enhances brand reputation but also aligns with the growing consumer preference for eco-conscious businesses.
Brief Evolution/History
The vending machine industry has evolved significantly over the decades, transitioning from simple coin-operated devices to sophisticated machines equipped with advanced technology. Initially focused on snack and beverage dispensing, the market has expanded to include a diverse range of products, from fresh food to electronics. The introduction of digital payment methods and smart vending solutions has further transformed the landscape, providing buyers with more options than ever before.
This evolution has also influenced the used vending machine market, as older models are being refurbished and upgraded to meet modern standards. As a result, international B2B buyers can find a plethora of options that cater to their specific needs, allowing for cost-effective and sustainable purchasing decisions.
Related Video: Incoterms for beginners | Global Trade Explained
Frequently Asked Questions (FAQs) for B2B Buyers of used vending machines for sale nearby
-
What should I consider when vetting suppliers of used vending machines?
When vetting suppliers, prioritize their reputation and experience in the industry. Request references from previous clients and check online reviews. It’s crucial to verify the supplier’s certifications and ensure they comply with local regulations in your region. Additionally, assess their customer service responsiveness and willingness to provide post-sale support. Engaging in direct communication can help gauge their reliability and transparency. -
Can I customize the vending machines to fit my specific needs?
Many suppliers offer customization options for used vending machines, including branding, selection of products, and payment systems. Before finalizing your purchase, clearly communicate your requirements to the supplier and confirm what customization services are available. Ensure that any modifications are documented in the contract to avoid misunderstandings. This will help tailor the machines to better suit your target market’s preferences. -
What are the typical minimum order quantities (MOQ) and lead times for used vending machines?
Minimum order quantities can vary significantly between suppliers, often depending on the machine type and condition. Some suppliers may offer single units, while others might have higher MOQs. Lead times for delivery can also vary based on location and the supplier’s inventory. Generally, expect anywhere from a few weeks to several months. Always clarify these details before placing an order to align your inventory needs with the supplier’s capabilities. -
What payment terms should I expect when purchasing used vending machines?
Payment terms can vary widely among suppliers. Common practices include full payment upfront, deposits with balance upon delivery, or even financing options. It’s essential to negotiate terms that work for your cash flow and budget. Be cautious of any upfront fees and ensure that the payment method is secure. Document all agreements in writing to prevent any disputes later. -
How can I ensure quality assurance for the used vending machines I purchase?
Request detailed information about the quality assurance processes that the supplier follows. Look for warranties or guarantees that cover the machines for a specified period. Ask for inspection reports or certifications that verify the machines’ functionality and safety standards. If possible, consider visiting the supplier’s facility to conduct a personal inspection of the machines before purchase, ensuring they meet your quality expectations. -
What certifications should I look for when buying used vending machines?
Ensure that the used vending machines comply with local and international standards, such as CE, UL, or ISO certifications. These certifications indicate that the machines meet safety and performance criteria. Additionally, inquire about any health and safety certifications relevant to food or beverage dispensing, especially if you are operating in regions with strict regulatory environments. This will help mitigate risks associated with compliance. -
What logistics considerations should I keep in mind when purchasing used vending machines?
Logistics play a critical role in the procurement of used vending machines. Assess the supplier’s shipping capabilities, including costs and estimated delivery times. Additionally, consider the local customs regulations that may affect the importation of machines into your country. Establish a clear plan for receiving and installing the machines, including any necessary transportation and handling services to ensure they arrive in good condition. -
How can I handle disputes with suppliers regarding used vending machines?
To effectively manage disputes, maintain clear and thorough documentation of all transactions, communications, and agreements. If an issue arises, attempt to resolve it directly with the supplier through open dialogue. If necessary, refer to any contracts or warranties in place. Should informal negotiations fail, consider mediation or arbitration as alternatives to legal proceedings, as these methods can be more efficient and less costly for resolving international disputes.
Strategic Sourcing Conclusion and Outlook for used vending machines for sale nearby
In summary, strategic sourcing of used vending machines offers significant advantages for international B2B buyers, particularly in emerging markets across Africa, South America, the Middle East, and Europe. By leveraging local suppliers, businesses can access cost-effective solutions while supporting regional economies. Understanding the nuances of each market—such as regulatory requirements, consumer preferences, and payment methods—can enhance purchasing decisions and mitigate risks.
Buyers should focus on building strong relationships with suppliers to ensure reliability and quality. Conducting thorough market research will also help identify the best options and negotiate favorable terms. Additionally, considering logistics and after-sales support is crucial to maximize the value derived from these investments.
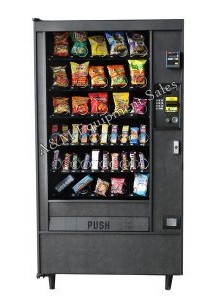
Illustrative Image (Source: Google Search)
Looking ahead, as the demand for vending solutions continues to grow, the opportunity to capitalize on used vending machines presents a promising avenue for business expansion. We encourage international buyers to actively explore local markets and engage with suppliers to harness this potential. By doing so, you can not only improve your bottom line but also contribute to sustainable economic growth in your region. Take the next step in your sourcing strategy today and unlock the benefits that used vending machines can offer your business.