Unlock Profits with Huge Vending Machines: Your Ultimate
Guide to Huge Vending Machine
- Introduction: Navigating the Global Market for huge vending machine
- Understanding huge vending machine Types and Variations
- Key Industrial Applications of huge vending machine
- Strategic Material Selection Guide for huge vending machine
- In-depth Look: Manufacturing Processes and Quality Assurance for huge vending machine
- Comprehensive Cost and Pricing Analysis for huge vending machine Sourcing
- Spotlight on Potential huge vending machine Manufacturers and Suppliers
- Essential Technical Properties and Trade Terminology for huge vending machine
- Navigating Market Dynamics, Sourcing Trends, and Sustainability in the huge vending machine Sector
- Frequently Asked Questions (FAQs) for B2B Buyers of huge vending machine
- Strategic Sourcing Conclusion and Outlook for huge vending machine
Introduction: Navigating the Global Market for huge vending machine
In today’s fast-paced commercial landscape, huge vending machines have emerged as a vital tool for businesses aiming to enhance customer engagement and streamline operations. These machines not only provide convenience but also serve as a dynamic marketing platform, offering diverse products ranging from snacks and beverages to electronics and personal care items. As international B2B buyers, particularly from Africa, South America, the Middle East, and Europe, understanding the nuances of this market is critical for making informed purchasing decisions.
This guide delves into the comprehensive landscape of huge vending machines, covering essential aspects such as types and functionalities, materials and manufacturing processes, quality control measures, and leading suppliers. Additionally, we will explore the cost structures associated with acquiring and maintaining these machines, as well as the current market trends that influence pricing and demand.
By empowering buyers with knowledge about frequently asked questions and industry best practices, this resource serves as an invaluable tool for sourcing decisions. Whether you are in Indonesia or France, navigating the global market for huge vending machines can significantly enhance your operational efficiency and customer satisfaction. Equip yourself with the insights needed to capitalize on this growing trend and make strategic investments that align with your business goals.
Understanding huge vending machine Types and Variations
Type Name | Key Distinguishing Features | Primary B2B Applications | Brief Pros & Cons for Buyers |
---|---|---|---|
Snack Vending Machines | Large capacity for snacks, customizable selections | Offices, schools, public areas | Pros: High snack demand, easy restocking; Cons: Limited to non-perishable items. |
Beverage Vending Machines | Dispenses a variety of drinks, including cold and hot options | Gyms, offices, vending locations | Pros: High turnover, diverse offerings; Cons: Requires refrigeration, maintenance costs. |
Combination Vending Machines | Offers both snacks and beverages in one unit | Airports, shopping malls | Pros: Versatile, maximizes space; Cons: More complex to maintain and operate. |
Healthy Food Vending Machines | Focus on nutritious options, often refrigerated | Hospitals, universities, gyms | Pros: Growing demand for healthy choices; Cons: Higher initial investment, limited inventory. |
Specialty Vending Machines | Unique offerings such as electronics or personal care items | Retail stores, events, trade shows | Pros: Niche market appeal, high profit margins; Cons: Limited customer base, higher risk. |
Snack Vending Machines
Snack vending machines are designed to hold a large variety of snacks, from chips to candy bars, and often feature customizable selections tailored to consumer preferences. These machines are ideal for environments such as offices, schools, and public areas where quick snack options are in high demand. When purchasing, B2B buyers should consider the machine’s capacity, ease of restocking, and the variety of snacks it can hold. While they offer high demand and easy maintenance, buyers should note that they are limited to non-perishable items, which may restrict product offerings.
Beverage Vending Machines
Beverage vending machines provide a wide range of drinks, including sodas, juices, and even hot beverages like coffee. These machines are commonly found in gyms, offices, and vending locations where hydration is a priority. B2B buyers should evaluate the machine’s cooling capabilities, selection variety, and maintenance requirements. The advantages include high turnover rates and diverse offerings, but potential downsides include the need for refrigeration and ongoing maintenance costs, which can add to the overall operational expenses.
Combination Vending Machines
Combination vending machines are versatile units that dispense both snacks and beverages, making them suitable for high-traffic areas like airports and shopping malls. They maximize space efficiency and cater to varied consumer needs in one machine. When considering a purchase, buyers should assess the layout, product capacity, and operational complexity. While they provide the benefit of versatility and increased sales potential, they can be more complex to maintain and operate than single-product machines.
Healthy Food Vending Machines
With a growing focus on health and wellness, healthy food vending machines offer nutritious options such as salads, wraps, and fruit. These machines are particularly well-suited for hospitals, universities, and gyms where health-conscious consumers are prevalent. B2B buyers should consider the machine’s refrigeration requirements, product variety, and initial investment costs. Although they meet the increasing demand for healthier choices, they often require a higher upfront investment and may have limited inventory compared to traditional vending options.
Specialty Vending Machines
Specialty vending machines provide unique offerings beyond traditional snacks and beverages, such as electronics, personal care items, or even meal kits. They are typically found in retail stores, events, and trade shows, targeting niche markets. B2B buyers should evaluate the specific product offerings, market demand, and potential profit margins. While these machines can attract a specific customer base and yield high profit margins, they also carry higher risks due to limited customer appeal and potential inventory challenges.
Related Video: Pros And Cons Of Starting A Vending Machine Business
Key Industrial Applications of huge vending machine
Industry/Sector | Specific Application of huge vending machine | Value/Benefit for the Business | Key Sourcing Considerations for this Application |
---|---|---|---|
Retail | Automated retail for consumer goods | Increased sales through 24/7 availability | Payment systems compatibility, product variety |
Healthcare | Dispensing medical supplies and personal care items | Improved accessibility for patients and staff | Compliance with health regulations, secure storage |
Education | Providing snacks and beverages in schools | Enhanced student satisfaction and nutrition | Nutritional standards compliance, age-appropriate options |
Transportation | Vending machines at airports and train stations | Convenience for travelers, reduced wait times | Space optimization, energy efficiency, payment options |
Manufacturing | Parts vending for industrial tools and components | Streamlined operations, reduced downtime | Inventory management systems, robust construction |
Retail
Huge vending machines in the retail sector are revolutionizing how businesses engage with consumers. These machines allow retailers to offer a wide array of products, from electronics to snacks, in a self-service format. The key benefits include enhanced customer experience through 24/7 availability and reduced staffing costs. International B2B buyers should consider payment system compatibility and the machine’s ability to accommodate diverse product ranges to cater to varying consumer preferences across different regions.
Healthcare
In healthcare settings, huge vending machines serve a crucial role by dispensing medical supplies and personal care items. This application addresses the need for immediate access to essential items, particularly in emergency situations or during off-hours. Buyers in this sector must prioritize compliance with health regulations, ensuring that machines can securely store sensitive items and maintain proper hygiene standards. Additionally, the ability to track inventory and usage patterns can enhance operational efficiency.
Education
Educational institutions are increasingly adopting huge vending machines to provide students with healthy snacks and beverages. This application not only promotes better nutrition but also enhances student satisfaction by offering convenient food options on campus. For B2B buyers, it is essential to ensure that the products offered meet nutritional standards and are appropriate for different age groups. Furthermore, machines should be placed strategically to maximize accessibility during peak hours.
Transportation
In the transportation sector, huge vending machines positioned at airports and train stations provide travelers with quick access to food and beverages. This application significantly reduces wait times and enhances the overall travel experience. Buyers should focus on space optimization within vending machines to accommodate high foot traffic, as well as energy efficiency to minimize operational costs. Additionally, offering diverse payment options can cater to international travelers, enhancing convenience.
Manufacturing
Huge vending machines are increasingly utilized in manufacturing environments for parts vending, enabling easy access to tools and components. This application helps streamline operations and reduce downtime by ensuring that workers can quickly obtain necessary items without leaving their workstations. B2B buyers should consider robust construction to withstand industrial environments, as well as the integration of inventory management systems to track usage and optimize stock levels. This can lead to significant cost savings and improved productivity.
Related Video: How to Start a Vending Machine Business, Cost, Tips, How Much You Make
Strategic Material Selection Guide for huge vending machine
When selecting materials for huge vending machines, it is crucial to consider properties that directly impact performance, durability, and compliance with international standards. Below is an analysis of four common materials used in the construction of vending machines, focusing on their key properties, advantages, disadvantages, and specific considerations for international B2B buyers.
1. Stainless Steel
Key Properties: Stainless steel is known for its excellent corrosion resistance, particularly against moisture and various chemicals. It can withstand high temperatures and pressures, making it suitable for diverse environments.
Pros & Cons: The durability of stainless steel is a significant advantage, as it resists wear and tear over time. However, it tends to be more expensive than other materials, which can impact the overall cost of the vending machine. Manufacturing complexity is moderate, requiring specialized equipment for cutting and welding.
Impact on Application: Stainless steel is compatible with a wide range of media, including food and beverages, making it an ideal choice for vending machines that dispense consumables.
Considerations for International Buyers: Buyers should ensure compliance with food safety standards and certifications, such as ASTM and ISO. In regions like Europe and the Middle East, preferences for stainless steel grades (e.g., AISI 304 or 316) may vary based on local regulations.
2. Carbon Steel
Key Properties: Carbon steel offers good strength and toughness, making it suitable for structural components of vending machines. However, it has lower corrosion resistance compared to stainless steel.
Pros & Cons: The primary advantage of carbon steel is its cost-effectiveness, making it a popular choice for budget-conscious projects. The downside is its susceptibility to rust and corrosion, necessitating protective coatings or treatments.
Impact on Application: Carbon steel is best suited for non-corrosive environments or where additional protective measures can be implemented.
Considerations for International Buyers: Compliance with standards such as ASTM A36 is important. Buyers in Africa and South America may find carbon steel more accessible and cost-effective, but they should be aware of the need for regular maintenance to prevent corrosion.
3. Aluminum
Key Properties: Aluminum is lightweight and has good corrosion resistance, particularly when anodized. It can withstand moderate temperatures but is not as robust under high-pressure conditions.
Pros & Cons: The lightweight nature of aluminum makes it easy to transport and install, reducing overall labor costs. However, its lower strength compared to steel can limit its use in heavy-duty applications.
Impact on Application: Aluminum is suitable for components that do not require high structural integrity, such as housing or decorative elements in vending machines.
Considerations for International Buyers: Buyers should consider the specific aluminum alloy used, as properties can vary significantly. Compliance with international standards like JIS and EN is essential, especially in Europe.
4. Polycarbonate
Key Properties: Polycarbonate is a high-impact plastic known for its transparency and strength. It is resistant to UV light and can withstand a range of temperatures.
Pros & Cons: The main advantage of polycarbonate is its lightweight and shatter-resistant properties, making it ideal for transparent panels in vending machines. However, it can be more expensive than traditional plastics and may not be suitable for high-temperature applications.
Impact on Application: Polycarbonate is ideal for areas requiring visibility, such as display windows or front panels, but may not be suitable for structural components.
Considerations for International Buyers: Buyers should verify the material’s compliance with safety standards and regulations in their region, particularly in terms of food contact safety in Europe and the Middle East.
Summary Table
Material | Typical Use Case for huge vending machine | Key Advantage | Key Disadvantage/Limitation | Relative Cost (Low/Med/High) |
---|---|---|---|---|
Stainless Steel | Structural and exterior components for food vending | Excellent corrosion resistance | Higher cost compared to alternatives | High |
Carbon Steel | Structural components in non-corrosive environments | Cost-effective | Susceptible to rust without treatment | Low |
Aluminum | Housing and decorative elements | Lightweight and easy to install | Lower strength than steel | Medium |
Polycarbonate | Transparent panels and display windows | Shatter-resistant and UV resistant | Not suitable for high-temperature use | Medium |
This guide provides a comprehensive overview of material selection for huge vending machines, allowing international B2B buyers to make informed decisions based on performance, cost, and compliance with regional standards.
In-depth Look: Manufacturing Processes and Quality Assurance for huge vending machine
Manufacturing Processes for Huge Vending Machines
The production of huge vending machines involves a series of carefully planned stages, each critical to ensuring the final product meets both quality and functionality standards. Below is a breakdown of the typical manufacturing processes.
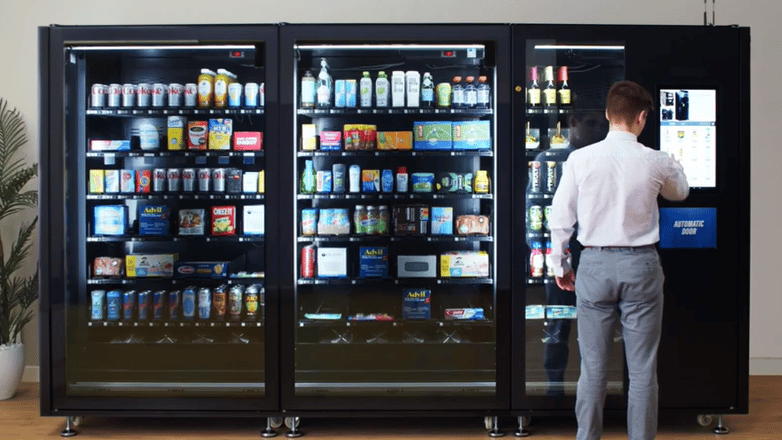
Illustrative Image (Source: Google Search)
1. Material Preparation
The first step in manufacturing is sourcing high-quality raw materials. Common materials used in vending machine production include:
- Metal Components: Steel and aluminum for structural integrity and durability.
- Plastic Parts: ABS and polycarbonate for exterior panels and internal components.
- Electronic Components: Circuit boards, sensors, and payment systems.
Key Techniques:
– Material Testing: Ensure materials meet industry standards for strength and durability.
– Inventory Management: Implement just-in-time (JIT) practices to minimize waste and reduce holding costs.
2. Forming
Once the materials are prepared, they undergo various forming processes to create the machine’s components.
- Cutting: Laser cutting or water jet cutting for precise dimensions.
- Bending: CNC bending machines to form metal panels into the required shapes.
- Injection Molding: Used for producing plastic parts with high accuracy.
Key Techniques:
– CAD Software: Utilize computer-aided design (CAD) to optimize component designs and layouts.
– Prototyping: Create prototypes to evaluate design before mass production, reducing risk of costly errors.
3. Assembly
The assembly stage involves integrating all components into a complete vending machine.
- Sub-Assembly: Components such as payment systems and refrigeration units are pre-assembled.
- Main Assembly Line: Final assembly where all sub-assemblies are combined, ensuring alignment and fit.
Key Techniques:
– Lean Manufacturing: Streamline processes to reduce waste and improve efficiency.
– Workstation Organization: Implement standardized workstations to enhance productivity and reduce assembly time.
4. Finishing
The finishing stage includes painting, branding, and quality checks.
- Surface Treatment: Powder coating or painting to enhance aesthetics and protect against corrosion.
- Branding: Application of logos and decals as per client specifications.
Key Techniques:
– Quality Control Inspections: Conduct inspections after finishing to ensure quality standards are maintained.
– Environmental Compliance: Ensure all finishing processes comply with environmental regulations relevant to the target market.
Quality Assurance Standards
Quality assurance (QA) is paramount in the manufacturing of huge vending machines, ensuring they are safe, reliable, and meet customer expectations. Key international standards and industry-specific certifications include:
- ISO 9001: Focuses on quality management systems, emphasizing customer satisfaction and continuous improvement.
- CE Marking: Required for products sold within the European Economic Area, ensuring compliance with safety and health regulations.
- API Certification: Important for components related to the oil and gas industry, ensuring they meet rigorous performance standards.
QC Checkpoints
Quality control checkpoints are essential throughout the manufacturing process:
- Incoming Quality Control (IQC): Inspect raw materials upon arrival to ensure they meet specifications.
- In-Process Quality Control (IPQC): Monitor production processes at various stages to detect and rectify issues early.
- Final Quality Control (FQC): Comprehensive testing of the finished product before shipment.
Common Testing Methods
B2B buyers should be aware of the following testing methods employed during the QC process:
- Functional Testing: Ensuring all components operate as intended under various conditions.
- Stress Testing: Assessing the machine’s durability and performance under extreme conditions.
- Electrical Safety Testing: Verifying that electrical components meet safety standards.
Verification of Supplier Quality Control
When sourcing huge vending machines, international B2B buyers can implement several strategies to verify supplier quality control:
- Supplier Audits: Conduct on-site audits to assess manufacturing practices and adherence to quality standards.
- Quality Assurance Reports: Request detailed reports from suppliers that outline their QC processes and results.
- Third-Party Inspections: Engage independent inspection services to conduct quality assessments before shipment.
QC and Certification Nuances for International Buyers
B2B buyers from Africa, South America, the Middle East, and Europe should consider the following nuances:
- Regional Compliance: Understand and comply with local regulations and standards, as they may differ significantly between regions.
- Cultural Considerations: Recognize that manufacturing practices and quality expectations may vary; therefore, clear communication with suppliers is essential.
- Documentation: Ensure all quality certifications and compliance documents are available in the preferred language and format for easier verification.
Conclusion
A comprehensive understanding of manufacturing processes and quality assurance practices is crucial for B2B buyers of huge vending machines. By focusing on quality at every stage—from material preparation to final inspections—buyers can ensure that they source reliable, high-quality machines that meet their operational needs. By adopting rigorous verification processes and staying informed about international standards, buyers can mitigate risks and foster successful supplier relationships.
Related Video: The Most Sophisticated Manufacturing Process In The World Inside The Fab | Intel
Comprehensive Cost and Pricing Analysis for huge vending machine Sourcing
When sourcing huge vending machines, understanding the cost structure and pricing dynamics is crucial for international B2B buyers. This analysis delves into the various cost components, price influencers, and practical buyer tips tailored for stakeholders from Africa, South America, the Middle East, and Europe.
Cost Components
-
Materials: The cost of raw materials is one of the largest components in the manufacturing of vending machines. This includes metal, plastic, electronic components, and refrigeration systems. Sourcing quality materials can significantly affect the durability and performance of the machines.
-
Labor: Labor costs vary by region and can impact the final price. In countries with higher wage standards, such as those in Europe, labor costs are typically higher, whereas regions in Africa or South America may offer lower labor costs, which can be beneficial for price-sensitive buyers.
-
Manufacturing Overhead: This includes costs related to the facilities, utilities, and administrative expenses associated with production. Buyers should inquire about the manufacturing processes and facilities used by suppliers to assess the overhead costs indirectly reflected in the pricing.
-
Tooling: Custom tooling for unique designs or specifications can add to the initial setup costs. It’s essential for buyers to consider whether they require customized solutions, as this will influence both the upfront and ongoing costs.
-
Quality Control (QC): Ensuring that machines meet quality standards incurs additional costs. Effective QC processes can lead to higher upfront costs but may save buyers money in the long run by reducing maintenance and warranty claims.
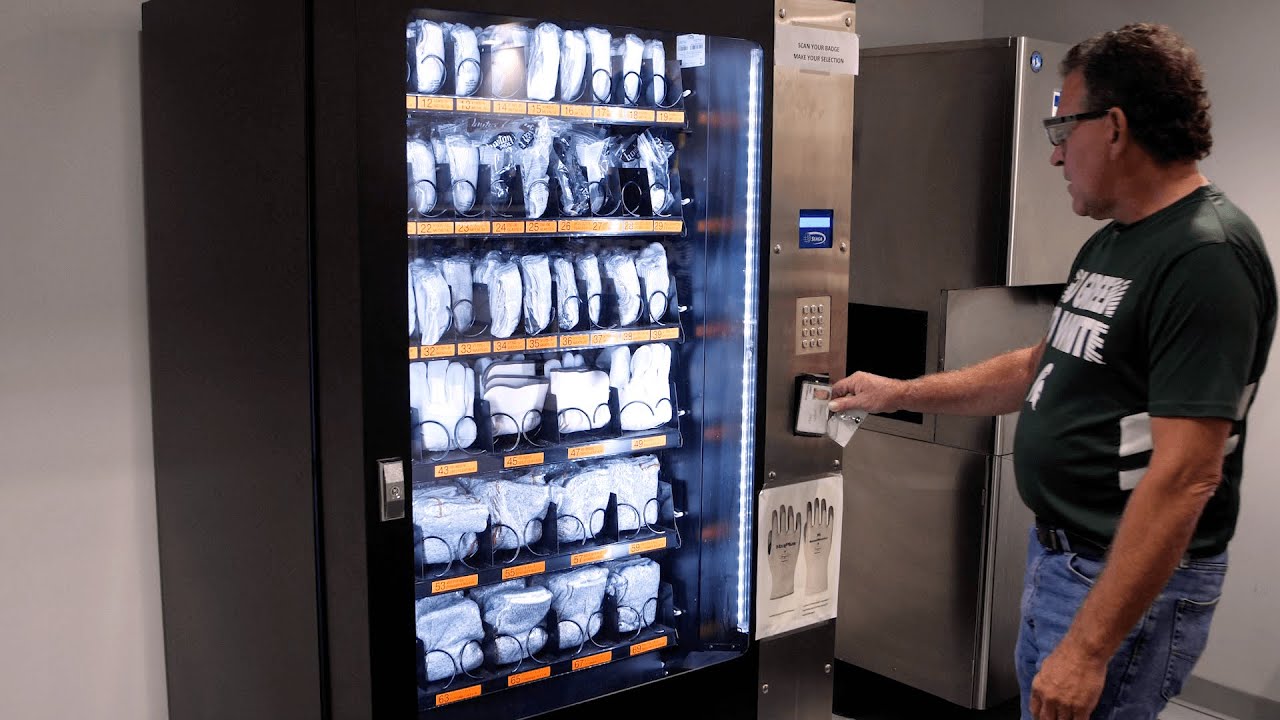
Illustrative Image (Source: Google Search)
-
Logistics: Transportation costs, including shipping and handling, are significant, particularly for bulky items like vending machines. Factors like distance, shipping mode, and import tariffs should be factored into the total cost.
-
Margin: Finally, suppliers will include a profit margin in their pricing. Understanding typical margins in the industry can aid buyers in evaluating the competitiveness of quotes received.
Price Influencers
-
Volume/MOQ: Bulk orders often lead to lower per-unit costs. Buyers should negotiate minimum order quantities (MOQs) to benefit from economies of scale.
-
Specifications/Customization: More complex designs or additional features can increase costs. Be clear about requirements to avoid unexpected expenses.
-
Materials: The choice of materials can significantly influence pricing. High-quality, durable materials may have higher upfront costs but can reduce long-term operational costs.
-
Quality and Certifications: Machines that meet specific international standards or certifications may come at a premium. However, they offer assurances of reliability and compliance, which can be crucial for regulatory environments.
-
Supplier Factors: The reputation and reliability of the supplier can influence pricing. Established suppliers with proven track records may charge more but can provide better service and support.
-
Incoterms: Understanding shipping terms (Incoterms) can affect the total landed cost. Buyers should clarify responsibilities for shipping costs, insurance, and customs duties.
Buyer Tips
-
Negotiate: Always seek to negotiate terms and prices. Leverage multiple quotes to create competitive pressure among suppliers.
-
Focus on Cost-Efficiency: Evaluate the total cost of ownership (TCO), which includes purchase price, maintenance, and operational costs. A lower initial price may not always equate to better value over time.
-
Understand Pricing Nuances: Pricing can vary significantly based on regional market dynamics. Buyers from Africa, South America, and the Middle East should be aware of local economic conditions that may influence supplier pricing strategies.
-
Request Detailed Quotes: Ensure that quotes break down costs into components, allowing for better comparison and understanding of what drives the price.
Disclaimer
Prices and cost structures can vary widely based on market conditions, supplier capabilities, and specific project requirements. This analysis provides indicative pricing frameworks and should be used as a guideline rather than a definitive pricing model. Always conduct thorough due diligence and obtain multiple quotes before making sourcing decisions.
Spotlight on Potential huge vending machine Manufacturers and Suppliers
This section offers a look at a few manufacturers active in the ‘huge vending machine’ market. This is a representative sample for illustrative purposes; B2B buyers must conduct their own extensive due diligence before any engagement. Information is synthesized from public sources and general industry knowledge.
Essential Technical Properties and Trade Terminology for huge vending machine
Key Technical Properties of Huge Vending Machines
When evaluating huge vending machines for international trade, several technical properties are critical for ensuring quality, durability, and operational efficiency. Here are the key specifications:
-
Material Grade
– Definition: Refers to the quality and type of materials used in the construction of the vending machine, such as stainless steel or high-grade plastics.
– B2B Importance: Higher-grade materials ensure longevity and resistance to corrosion, which is particularly important in diverse climates across Africa, South America, the Middle East, and Europe. Buyers should prioritize machines made from materials that can withstand environmental factors and heavy usage. -
Capacity
– Definition: The amount of product the vending machine can hold, usually measured in terms of number of items or volume.
– B2B Importance: Understanding capacity is crucial for businesses aiming to maximize sales in high-traffic areas. A larger capacity may reduce the frequency of restocking, saving time and labor costs, which is particularly advantageous for operations in remote locations. -
Power Consumption
– Definition: The amount of electricity the vending machine uses during operation, often measured in watts.
– B2B Importance: With energy costs varying significantly across regions, selecting a machine with low power consumption can lead to substantial savings over time. This is especially relevant for businesses in areas where electricity costs are high or where sustainability is a priority. -
User Interface
– Definition: The design and functionality of the machine’s display and payment system, including touchscreens and cashless payment options.
– B2B Importance: A user-friendly interface can enhance customer satisfaction and encourage repeat business. As cashless transactions become more popular, machines equipped with modern payment solutions can cater to a wider audience, particularly in urban areas. -
Dimensions and Weight
– Definition: The physical size and weight of the vending machine, usually specified in inches or centimeters.
– B2B Importance: Buyers must consider the dimensions and weight for shipping and installation purposes. Ensuring that the machine fits in the intended location and can be easily transported is critical to avoiding logistical challenges. -
Temperature Control
– Definition: The ability of the vending machine to maintain specific temperatures for perishable items, often controlled by advanced refrigeration technology.
– B2B Importance: For machines selling food and beverages, effective temperature control is essential for food safety and quality. Buyers should assess the refrigeration capabilities, especially in warmer climates.
Common Trade Terminology
Understanding industry jargon is essential for effective communication and negotiation in B2B transactions. Here are key terms to know:
-
OEM (Original Equipment Manufacturer)
– Definition: A company that produces parts or equipment that may be marketed by another manufacturer.
– Usage: In the context of vending machines, an OEM might supply the machine’s components, ensuring compatibility and reliability. -
MOQ (Minimum Order Quantity)
– Definition: The smallest quantity of goods a supplier is willing to sell.
– Usage: Buyers should be aware of MOQ requirements, as they can impact inventory levels and cash flow. Negotiating MOQs can lead to better pricing and availability. -
RFQ (Request for Quotation)
– Definition: A document issued by a buyer to solicit price quotes from suppliers for specific products or services.
– Usage: An RFQ for vending machines can help buyers compare pricing and terms from different suppliers, facilitating informed decision-making.
-
Incoterms (International Commercial Terms)
– Definition: A series of predefined international trade terms published by the International Chamber of Commerce (ICC).
– Usage: Understanding Incoterms is crucial for clarifying the responsibilities of buyers and sellers in shipping logistics, including who bears the costs and risks during transportation. -
Lead Time
– Definition: The time taken from placing an order to the delivery of the product.
– Usage: Buyers should inquire about lead times to ensure that machines arrive when needed, particularly for seasonal demands or new product launches. -
Warranty
– Definition: A guarantee provided by the manufacturer regarding the condition of the product and the promise to repair or replace it if necessary.
– Usage: A strong warranty can provide peace of mind for buyers, ensuring that they are protected against defects or malfunctions, which is crucial for maintaining operational efficiency.
By understanding these essential properties and terminology, B2B buyers can make informed decisions when sourcing huge vending machines for their markets.
Navigating Market Dynamics, Sourcing Trends, and Sustainability in the huge vending machine Sector
Market Overview & Key Trends
The global vending machine market has seen significant evolution, driven by changing consumer behaviors and technological advancements. Key factors influencing the market include increased demand for convenience, the rise of cashless payment systems, and the growing popularity of healthy snack options. International B2B buyers, particularly in regions such as Africa, South America, the Middle East, and Europe, should note that the integration of technology, such as IoT-enabled machines and AI-driven inventory management systems, is becoming commonplace. This tech-savvy approach not only enhances user experience but also streamlines operations for vendors, enabling them to monitor stock levels and consumer preferences in real-time.
Emerging trends include a shift towards customized vending solutions that cater to local tastes and dietary preferences. For instance, buyers in Africa may focus on vending machines that offer local snacks and beverages, while European markets may lean towards machines providing organic or vegan options. Additionally, the rise of sustainability consciousness among consumers is prompting manufacturers to design machines that minimize energy consumption and utilize eco-friendly materials. B2B buyers must stay attuned to these trends to align their sourcing strategies with market demands, ensuring they remain competitive.
Sustainability & Ethical Sourcing in B2B
Sustainability is becoming a crucial aspect of the vending machine sector. The environmental impact of traditional vending machines—often characterized by high energy consumption and non-recyclable materials—has led to a demand for greener alternatives. Buyers should prioritize sourcing machines that are energy-efficient, use recyclable components, and are designed for easy maintenance and longevity.
Moreover, ethical sourcing is essential in establishing a responsible supply chain. This includes selecting suppliers who uphold fair labor practices and demonstrate a commitment to environmental stewardship. Certifications such as ISO 14001 for environmental management and fair trade labels can serve as indicators of a supplier’s commitment to sustainability. Buyers should actively seek partnerships with manufacturers who are transparent about their sourcing practices and who utilize ‘green’ materials in their products, as this not only reduces environmental impact but also enhances brand reputation in an increasingly eco-conscious market.
Brief Evolution/History
The vending machine industry dates back to ancient Greece, where the first devices dispensed holy water. However, the modern vending machine as we know it emerged in the early 20th century, primarily offering snacks and beverages in public spaces. Over the decades, the sector has evolved significantly, adapting to technological advancements and changing consumer preferences. The introduction of electronic payment systems in the 1980s revolutionized the market, paving the way for a diverse range of products and services, including fresh food and even electronics in some regions. As we move forward, the focus on technology integration and sustainability will continue to shape the future of the vending machine sector, offering vast opportunities for international B2B buyers.
Related Video: Is global trade transforming? | Counting the Cost
Frequently Asked Questions (FAQs) for B2B Buyers of huge vending machine
-
What criteria should I consider when vetting suppliers for huge vending machines?
When vetting suppliers, focus on their industry experience, reputation, and financial stability. Request references and case studies to assess their previous projects. Verify certifications such as ISO, CE, or specific local standards relevant to your region. Evaluate their production capabilities, lead times, and their ability to provide after-sales support. Additionally, consider their responsiveness to inquiries and willingness to engage in transparent communication. -
Can I customize the huge vending machines to meet specific market needs?
Yes, most manufacturers offer customization options for huge vending machines. You can specify size, design, product selection, and features such as payment systems or branding elements. Discuss your requirements in detail with the supplier to understand the limits of customization and any associated costs. Ensure that the supplier has a proven track record of delivering customized solutions that align with your business needs. -
What are the typical minimum order quantities (MOQ) and lead times for huge vending machines?
MOQs can vary widely depending on the supplier and the complexity of the machines. Generally, expect MOQs to range from 5 to 50 units for large orders. Lead times typically range from 4 to 12 weeks, depending on production schedules and customization requirements. Always clarify these details before finalizing your order to ensure they align with your business timeline and inventory management strategies.
-
What payment terms should I negotiate when purchasing huge vending machines?
Payment terms can vary by supplier but often include options like a deposit followed by balance upon delivery or a net payment term after delivery. It’s advisable to negotiate terms that provide you with flexibility while ensuring the supplier’s confidence. Consider using escrow services for larger transactions to mitigate risk. Make sure to also clarify currency, payment methods, and any potential additional fees associated with international transactions. -
How can I ensure quality assurance and certification for huge vending machines?
Request documentation for quality assurance processes and certifications from the supplier. Look for international standards such as ISO 9001 or specific safety certifications relevant to your market. Conduct factory visits if possible, or request third-party inspections. Additionally, inquire about warranties and post-purchase support, as these can be indicative of the manufacturer’s confidence in their product quality. -
What logistics considerations should I be aware of when importing huge vending machines?
Logistics for importing vending machines require careful planning. Consider shipping methods (air vs. sea), which will affect costs and lead times. Ensure compliance with customs regulations in your country, which may include tariffs and import duties. Work closely with your supplier to understand packaging requirements and potential damages during transit. It’s advisable to partner with a logistics provider experienced in handling large machinery to facilitate smooth transportation. -
How should I handle disputes with suppliers regarding huge vending machines?
Establish clear terms in your contract regarding dispute resolution, including methods such as mediation or arbitration. Document all communications and agreements throughout the purchasing process to provide evidence if needed. In case of a dispute, approach the supplier directly to discuss the issue and seek a resolution. If necessary, escalate the matter through legal channels based on the contract’s terms, but aim for amicable solutions to maintain a professional relationship. -
What are the best practices for maintaining huge vending machines after purchase?
Regular maintenance is crucial for ensuring the longevity and efficiency of your vending machines. Establish a maintenance schedule that includes routine checks on hardware, software updates, and restocking procedures. Train staff on operational best practices and troubleshooting common issues. Additionally, consider a service agreement with the supplier for ongoing support and repairs, which can help minimize downtime and maintain customer satisfaction.
Strategic Sourcing Conclusion and Outlook for huge vending machine
In conclusion, strategic sourcing for huge vending machines presents a significant opportunity for international B2B buyers. By prioritizing supplier relationships, understanding regional market dynamics, and leveraging technology, businesses can enhance their operational efficiency and customer satisfaction. Buyers should focus on identifying reputable suppliers who not only offer competitive pricing but also demonstrate reliability and innovation in their offerings.
Furthermore, the importance of local market insights cannot be overstated, especially for buyers in diverse regions such as Africa, South America, the Middle East, and Europe. Tailoring vending machine solutions to meet local preferences and regulations will be crucial in maximizing market penetration and profitability.
As the vending machine industry continues to evolve with advancements in technology and consumer behavior, staying informed and adaptable will be key. We encourage B2B buyers to actively engage in strategic sourcing discussions and partnerships that foster growth and sustainability. Embrace this opportunity to transform your vending operations and position your business for success in the global marketplace.