Unlock Profits with Discount Vending Machines: The B2B
Guide to Discount Vending Machines
- Introduction: Navigating the Global Market for discount vending machines
- Understanding discount vending machines Types and Variations
- Key Industrial Applications of discount vending machines
- Strategic Material Selection Guide for discount vending machines
- In-depth Look: Manufacturing Processes and Quality Assurance for discount vending machines
- Comprehensive Cost and Pricing Analysis for discount vending machines Sourcing
- Spotlight on Potential discount vending machines Manufacturers and Suppliers
- Essential Technical Properties and Trade Terminology for discount vending machines
- Navigating Market Dynamics, Sourcing Trends, and Sustainability in the discount vending machines Sector
- Frequently Asked Questions (FAQs) for B2B Buyers of discount vending machines
- Strategic Sourcing Conclusion and Outlook for discount vending machines
Introduction: Navigating the Global Market for discount vending machines
Navigating the global market for discount vending machines presents a unique opportunity for B2B buyers seeking cost-effective solutions to enhance their product offerings. As consumer preferences shift towards convenience and affordability, discount vending machines have emerged as vital tools for businesses across various sectors, from retail to hospitality. These machines not only provide a range of affordable products but also cater to the growing demand for cashless and automated purchasing experiences.
This comprehensive guide delves into the essential aspects of discount vending machines, offering insights into types, materials, manufacturing quality control, and suppliers. Buyers will also find detailed information on cost structures, market trends, and answers to frequently asked questions, all designed to facilitate informed sourcing decisions.
For international B2B buyers from regions such as Africa, South America, the Middle East, and Europe, understanding the nuances of this market is crucial. The guide aims to empower you with the knowledge needed to identify reliable suppliers, assess machine specifications, and ultimately enhance your business’s operational efficiency. With the right insights, you can confidently navigate the complexities of sourcing discount vending machines, ensuring that your investments yield maximum returns while meeting the needs of your customers.
Understanding discount vending machines Types and Variations
Type Name | Key Distinguishing Features | Primary B2B Applications | Brief Pros & Cons for Buyers |
---|---|---|---|
Traditional Vending Machines | Standard machines offering bulk discounts on snacks and drinks | Offices, schools, gyms | Pros: Wide variety of products; Cons: Limited payment options and slower turnover. |
Smart Vending Machines | Equipped with IoT technology for real-time inventory tracking | Retail stores, airports | Pros: Enhanced customer engagement; Cons: Higher initial investment costs. |
Seasonal Discount Machines | Offer discounts on seasonal products like holiday items | Retail outlets, event venues | Pros: Attracts customers during peak seasons; Cons: Requires careful inventory management. |
Mobile Vending Units | Flexible, transportable machines for on-the-go sales | Events, festivals, construction sites | Pros: High mobility; Cons: Limited product range due to space constraints. |
Bulk Discount Vending Machines | Focused on large quantities of single items at reduced prices | Warehouses, distribution centers | Pros: Cost-effective for bulk purchases; Cons: Requires significant upfront investment. |
Traditional Vending Machines
Traditional vending machines are the most recognizable type, dispensing snacks and beverages at discounted prices. They serve well in environments like offices, schools, and gyms where quick access to refreshments is needed. When considering a purchase, buyers should evaluate product variety and machine reliability, as well as the potential for cashless payment options to enhance customer convenience.
Smart Vending Machines
Smart vending machines integrate IoT technology, allowing for real-time inventory management and data analytics. These machines are particularly suited for retail environments and transportation hubs, such as airports, where customer engagement and product availability are crucial. Buyers should consider the higher initial costs against the potential for increased sales through enhanced user experiences and operational efficiencies.
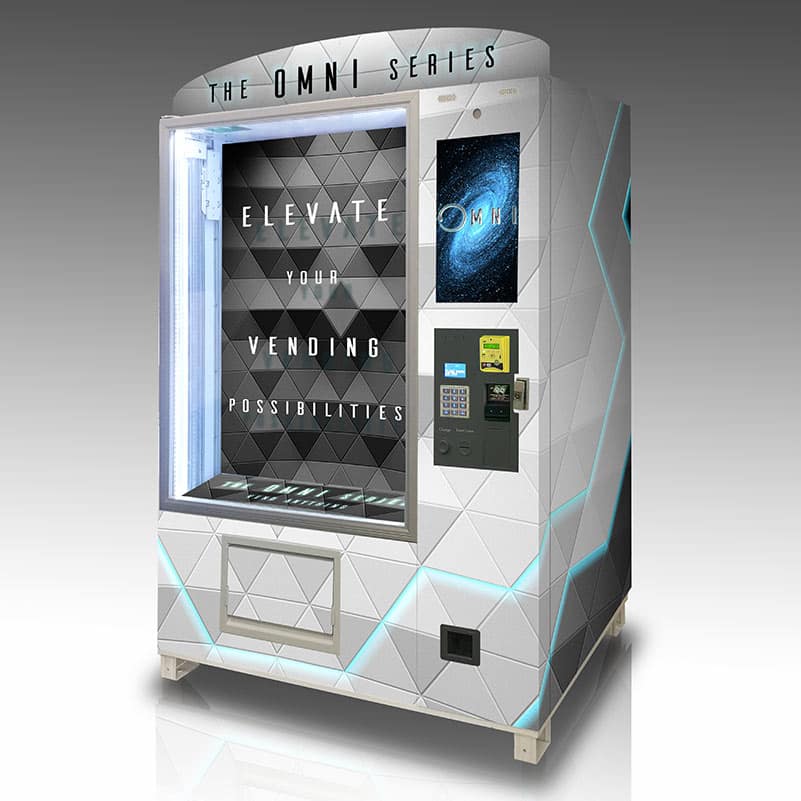
Illustrative Image (Source: Google Search)
Seasonal Discount Machines
Seasonal discount machines are designed to offer products that align with specific times of the year, like holiday-themed snacks or beverages. These machines can be strategically placed in retail outlets or event venues to maximize sales during peak seasons. B2B buyers need to assess the demand for seasonal items and manage inventory effectively to avoid overstocking or wastage.
Mobile Vending Units
Mobile vending units provide flexibility and convenience, allowing businesses to sell products at various locations, such as festivals, events, or construction sites. Their mobility is a significant advantage, but buyers must consider the limited range of products that can be offered due to space constraints. Additionally, understanding local regulations for mobile food sales is essential for compliance.
Bulk Discount Vending Machines
Bulk discount vending machines cater to businesses looking to purchase large quantities of products at reduced prices. These machines are typically found in warehouses and distribution centers, where cost efficiency is paramount. Buyers should evaluate the upfront investment and ongoing maintenance costs against the savings achieved through bulk purchasing.
Related Video: FINTECH BUSINESS MODELS EXPLAINED
Key Industrial Applications of discount vending machines
Industry/Sector | Specific Application of discount vending machines | Value/Benefit for the Business | Key Sourcing Considerations for this Application |
---|---|---|---|
Retail | Employee break rooms | Increases employee satisfaction and productivity | Machine capacity, product variety, and payment options |
Education | Campus convenience stores | Provides affordable snacks and drinks for students | Durability, ease of use, and energy efficiency |
Transportation | Transit stations | Offers quick, low-cost meal options for commuters | Location placement, machine maintenance, and product freshness |
Healthcare | Hospital waiting areas | Enhances patient and visitor experience with affordable options | Compliance with health regulations, hygiene standards, and accessibility |
Hospitality | Hotels and resorts | Enhances guest experience with convenient snack options | Customization options, aesthetic design, and payment solutions |
Retail: Employee Break Rooms
Discount vending machines in retail environments serve as a vital resource for employee break rooms. By providing affordable snacks and beverages, these machines contribute to increased employee satisfaction and productivity. Retailers benefit from reduced overhead costs associated with traditional catering services. Buyers should consider machine capacity and product variety to ensure that the vending solutions meet the diverse preferences of their workforce while also evaluating payment options to enhance user convenience.
Education: Campus Convenience Stores
In educational institutions, discount vending machines act as convenient campus convenience stores. They cater to students looking for affordable snacks and drinks between classes, helping to foster a supportive learning environment. The machines can be strategically placed in high-traffic areas to maximize accessibility. Buyers in this sector should focus on the durability of the machines and their ease of use, ensuring they can withstand frequent usage while being energy efficient to align with sustainability goals.
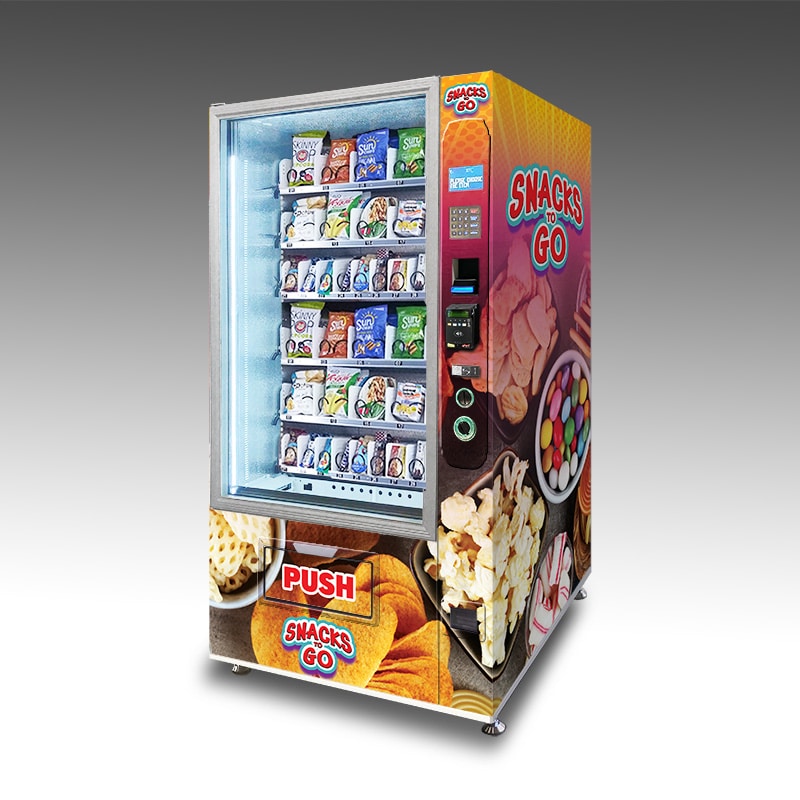
Illustrative Image (Source: Google Search)
Transportation: Transit Stations
In transportation hubs like bus and train stations, discount vending machines offer quick, low-cost meal options for commuters. These machines can alleviate hunger during travel, enhancing the overall commuter experience. The strategic placement of machines in waiting areas ensures that they are easily accessible. When sourcing for this application, businesses should prioritize location placement, machine maintenance, and the freshness of the products to meet the demands of on-the-go consumers.
Healthcare: Hospital Waiting Areas
In healthcare settings, discount vending machines in hospital waiting areas provide patients and visitors with affordable snack options. This enhances the overall experience during potentially stressful times, making it easier for families to access quick refreshments. Compliance with health regulations and hygiene standards is critical, as is ensuring accessibility for all visitors. Buyers should focus on sourcing machines that meet these standards while also considering the aesthetic design to fit the hospital environment.
Hospitality: Hotels and Resorts
In the hospitality industry, discount vending machines can significantly enhance the guest experience by offering convenient snack options. They can be placed in lobbies or near guest rooms, providing easy access to affordable food and drinks. This not only improves guest satisfaction but also drives additional revenue for the hotel. When sourcing machines for this application, businesses should consider customization options, aesthetic design, and various payment solutions to cater to diverse guest preferences.
Related Video: Kooler Ice Vending Machines – IM600XL vs. IM1000
Strategic Material Selection Guide for discount vending machines
When selecting materials for discount vending machines, it is crucial to consider their properties, advantages, limitations, and compliance with international standards. This guide analyzes four common materials used in the construction of vending machines, providing actionable insights for international B2B buyers.
1. Stainless Steel
Key Properties:
Stainless steel is known for its excellent corrosion resistance, high tensile strength, and ability to withstand extreme temperatures. Common grades used include 304 and 316, with 316 offering superior resistance to chlorides and other corrosive environments.
Pros & Cons:
Stainless steel is highly durable and can endure heavy usage, making it ideal for vending machines located in high-traffic areas. However, it is more expensive than other materials, which may affect overall project budgets. Manufacturing complexity can also be higher due to the need for specialized tools.
Impact on Application:
Stainless steel is compatible with a wide range of media, including food and beverages, making it a popular choice for vending machines. Its smooth surface is easy to clean, which is essential for hygiene in food-related applications.
Considerations for International Buyers:
Buyers should ensure compliance with food safety regulations, such as FDA standards in the U.S. or EFSA in Europe. Understanding local standards like ASTM or DIN is also critical, especially regarding corrosion resistance and mechanical properties.
2. Mild Steel
Key Properties:
Mild steel is characterized by its good weldability and ductility. It has a lower tensile strength compared to stainless steel but is generally sufficient for structural components.
Pros & Cons:
The primary advantage of mild steel is its cost-effectiveness, making it a popular choice for budget-conscious projects. However, it is prone to rust and corrosion if not properly coated or treated, which can lead to higher maintenance costs over time.
Impact on Application:
Mild steel is suitable for internal components of vending machines where exposure to moisture is minimal. However, for external parts, it may require protective coatings, which can complicate manufacturing.
Considerations for International Buyers:
Buyers in humid regions, such as parts of Africa and South America, should be particularly cautious about corrosion resistance. Compliance with local standards for coatings and finishes is essential to ensure longevity.
3. Aluminum
Key Properties:
Aluminum is lightweight, corrosion-resistant, and has good thermal conductivity. It is often used in applications where weight savings are critical.
Pros & Cons:
The lightweight nature of aluminum makes it easy to handle and install, which can reduce shipping and labor costs. However, it is less durable than steel and may not withstand heavy impacts, making it less suitable for high-traffic environments.
Impact on Application:
Aluminum is ideal for components that require frequent handling or transport, such as vending machine doors or panels. Its corrosion resistance makes it suitable for outdoor installations.
Considerations for International Buyers:
Buyers should consider the specific alloy used, as properties can vary significantly. Compliance with international standards such as JIS or ISO is important, particularly for applications involving food or beverages.
4. Polycarbonate
Key Properties:
Polycarbonate is a high-performance plastic known for its impact resistance and clarity. It can withstand a wide range of temperatures and is often used for transparent components.
Pros & Cons:
The primary advantage of polycarbonate is its shatter resistance, making it ideal for safety applications. However, it can be more expensive than traditional plastics and may not provide the same structural support as metals.
Impact on Application:
Polycarbonate is commonly used for vending machine windows or display areas, allowing customers to see products without compromising safety. It is also easy to mold into complex shapes.
Considerations for International Buyers:
Buyers should verify compliance with environmental regulations regarding plastics in their respective regions. Understanding local recycling practices is also essential, especially in regions where sustainability is a growing concern.
Summary Table
Material | Typical Use Case for discount vending machines | Key Advantage | Key Disadvantage/Limitation | Relative Cost (Low/Med/High) |
---|---|---|---|---|
Stainless Steel | Structural and external components | Excellent corrosion resistance | Higher cost, complex manufacturing | High |
Mild Steel | Internal structural components | Cost-effective | Prone to rust, requires protective coatings | Low |
Aluminum | Doors and panels, especially in outdoor settings | Lightweight, easy to handle | Less durable than steel | Medium |
Polycarbonate | Windows and display areas | Shatter-resistant | More expensive than traditional plastics | Medium |
This guide provides a comprehensive overview of the materials used in discount vending machines, enabling international B2B buyers to make informed decisions based on their specific requirements and regional considerations.
In-depth Look: Manufacturing Processes and Quality Assurance for discount vending machines
Manufacturing Processes for Discount Vending Machines
The manufacturing of discount vending machines involves several critical stages designed to ensure efficiency and product quality. Understanding these stages is essential for international B2B buyers, particularly those from Africa, South America, the Middle East, and Europe. The primary stages include material preparation, forming, assembly, and finishing.
1. Material Preparation
Material preparation is the foundational step in the manufacturing process. Common materials used include:
- Metal Sheets: Typically steel or aluminum for the frame and casing.
- Plastic Components: Used for internal parts and sometimes for outer casings.
- Electronic Components: Circuit boards, sensors, and displays are crucial for machine functionality.
During this stage, materials are sourced from reputable suppliers who meet international standards. Buyers should verify the quality of raw materials through certifications such as ISO 9001, ensuring that they meet quality benchmarks.
2. Forming
Once materials are prepared, the forming process begins. This includes:
- Cutting: Metal sheets are cut into specific shapes using laser cutting or shearing techniques.
- Bending: Components are bent to create the desired shapes, often using CNC bending machines for precision.
- Molding: For plastic parts, injection molding is commonly employed to create complex shapes and designs.
This phase requires skilled operators and advanced machinery to ensure that components are formed accurately, minimizing waste and defects.
3. Assembly
The assembly process is where individual components come together to form the vending machine. Key techniques include:
- Mechanical Assembly: Parts are fitted together using screws, bolts, and other fasteners. Robotics can be utilized for efficiency.
- Electrical Assembly: Circuit boards and wiring harnesses are installed, ensuring proper connectivity between electronic components.
- Quality Checks: After assembly, initial quality checks are conducted to ensure that all parts are correctly installed and function as intended.
B2B buyers should seek suppliers that have a structured assembly process, including detailed documentation of assembly procedures.
4. Finishing
The finishing stage enhances the machine’s aesthetics and durability. This includes:
- Painting and Coating: Machines are often powder-coated or painted to prevent rust and improve appearance.
- Labeling: Clear labels are applied for operation instructions, payment options, and product information.
- Final Inspection: A thorough inspection is performed to ensure that the machine meets both aesthetic and operational standards.
Quality Assurance in Manufacturing
Quality assurance (QA) is critical in the manufacturing of discount vending machines. It encompasses various international and industry-specific standards, checkpoints, and testing methods that ensure product reliability and safety.
International Standards
Adhering to international standards is vital for the credibility of the product in global markets. Key standards include:
- ISO 9001: This standard outlines criteria for a quality management system, ensuring consistent quality in products and services.
- CE Marking: For machines sold in Europe, CE marking indicates compliance with health, safety, and environmental protection standards.
- API Standards: Relevant in certain regions, these standards apply to the performance and safety of vending machines.
B2B buyers should confirm that suppliers are certified and regularly audited for compliance with these standards.
Quality Control Checkpoints
Quality control (QC) checkpoints are essential throughout the manufacturing process. Common checkpoints include:
- Incoming Quality Control (IQC): Materials are inspected upon arrival to ensure they meet specifications.
- In-Process Quality Control (IPQC): Continuous monitoring during manufacturing to detect defects early.
- Final Quality Control (FQC): A comprehensive check before the product is shipped, ensuring that it meets all operational and safety standards.
Implementing these checkpoints allows manufacturers to catch issues early, reducing the risk of defective products reaching the market.
Common Testing Methods
Testing methods vary but typically include:
- Functional Testing: Ensures all machine features operate as intended.
- Stress Testing: Evaluates the machine’s durability under simulated operational conditions.
- Electrical Safety Testing: Assesses the safety of electrical components and circuitry.
B2B buyers should request detailed reports on testing results to gauge the reliability of the machines they intend to purchase.
Verifying Supplier Quality Control
For international B2B buyers, verifying a supplier’s quality control measures is crucial. Here are actionable steps to consider:
- Conduct Audits: Regular audits of suppliers help assess their adherence to quality standards. This can be performed internally or through third-party services.
- Request Documentation: Suppliers should provide quality assurance documents, including compliance certificates, testing results, and audit reports.
- Third-Party Inspections: Engage third-party inspection agencies to conduct independent quality assessments before shipment.
Quality Control Nuances for International Buyers
International buyers should be aware of specific nuances in quality control, particularly when sourcing from regions like Africa, South America, the Middle East, and Europe:
- Regulatory Differences: Understand the specific regulations governing vending machines in the target market. Different countries may have varying requirements for safety and performance.
- Cultural Considerations: Communication styles and business practices may differ, affecting negotiations and quality expectations. Building strong relationships with suppliers can facilitate better quality assurance practices.
- Shipping and Handling: Ensure that suppliers have protocols in place for safe shipping and handling to prevent damage during transport, which can affect the machine’s quality upon arrival.
By comprehensively understanding manufacturing processes and quality assurance practices, B2B buyers can make informed decisions when sourcing discount vending machines, ultimately leading to successful partnerships and customer satisfaction.
Related Video: Most Satisfying Factory Production Processes And Heavy-Duty Factory Machines!
Comprehensive Cost and Pricing Analysis for discount vending machines Sourcing
Analyzing the cost structure and pricing dynamics of discount vending machines is crucial for international B2B buyers, especially those from Africa, South America, the Middle East, and Europe. Understanding these components will aid in making informed purchasing decisions and securing favorable terms.
Cost Structure Breakdown
The total cost of discount vending machines can be categorized into several key components:
-
Materials: The choice of materials significantly impacts pricing. Common materials include steel for the chassis and plastic for the exterior. Higher-grade materials may increase upfront costs but can enhance durability and reduce maintenance over time.
-
Labor: Labor costs vary by region and manufacturing practices. In countries with lower labor costs, such as Vietnam and Indonesia, the total cost may be reduced, but potential trade-offs may include quality and production speed.
-
Manufacturing Overhead: This includes costs associated with factory operations, such as utilities, rent, and equipment depreciation. Efficient production processes can help minimize these costs.
-
Tooling: Customization often necessitates specific tooling, which can be a significant initial investment. Buyers should consider whether they need standard models or custom machines, as this will affect tooling costs.
-
Quality Control (QC): Implementing strict QC processes ensures that machines meet required standards, but it also adds to the overall cost. Buyers should inquire about the supplier’s QC practices to understand how they impact pricing.
-
Logistics: Shipping and handling costs can vary widely based on the supplier’s location, chosen Incoterms, and the volume of the order. International shipping can introduce delays and additional fees.
-
Margin: Suppliers typically include a profit margin in their pricing. Understanding the average market margin can provide leverage in negotiations.
Price Influencers
Several factors can influence the pricing of discount vending machines:
-
Volume/MOQ: Bulk purchases often lead to lower per-unit costs. Buyers should assess their needs to negotiate a minimum order quantity (MOQ) that fits their budget.
-
Specifications/Customization: Machines tailored to specific requirements (e.g., payment systems, product offerings) can incur additional costs. Buyers should balance their customization needs with budget constraints.
-
Materials and Quality Certifications: Machines with higher quality certifications (like ISO standards) may cost more upfront but can lead to lower total ownership costs due to fewer repairs and higher reliability.
-
Supplier Factors: The reputation and reliability of the supplier can impact pricing. Established suppliers may command higher prices due to their track record, while newer entrants may offer lower prices to gain market share.
-
Incoterms: Understanding the terms of shipping (e.g., FOB, CIF) is crucial. Incoterms affect who bears the shipping costs and risks, influencing the total landed cost.
Buyer Tips
To optimize purchasing outcomes, international B2B buyers should consider the following strategies:
-
Negotiate: Engage suppliers in discussions about pricing, especially if ordering in bulk. Leverage competing quotes to secure better deals.
-
Assess Total Cost of Ownership (TCO): Evaluate not just the purchase price but also the ongoing costs, including maintenance, repairs, and energy consumption. A lower initial price may lead to higher costs over time.
-
Understand Pricing Nuances: Different regions may have varying pricing strategies. For example, suppliers in Europe may offer different pricing structures compared to those in Africa or South America due to local market conditions and costs.
-
Conduct Market Research: Stay informed about market trends and competitor pricing. This knowledge can empower buyers during negotiations and help identify fair pricing.
Disclaimer
Prices for discount vending machines can fluctuate based on market conditions, raw material costs, and supplier pricing strategies. The insights provided are indicative and should be validated through direct engagement with suppliers for accurate and current pricing information.
Spotlight on Potential discount vending machines Manufacturers and Suppliers
This section offers a look at a few manufacturers active in the ‘discount vending machines’ market. This is a representative sample for illustrative purposes; B2B buyers must conduct their own extensive due diligence before any engagement. Information is synthesized from public sources and general industry knowledge.
Essential Technical Properties and Trade Terminology for discount vending machines
Essential Technical Properties of Discount Vending Machines
When evaluating discount vending machines for international markets, several technical properties stand out as critical for ensuring performance, reliability, and customer satisfaction.
-
Material Grade: The construction material of vending machines typically includes stainless steel or high-grade plastic. Stainless steel is preferred for its durability and resistance to corrosion, which is essential in high-traffic environments. For B2B buyers, understanding the material grade helps assess the longevity and maintenance needs of the machine.
-
Dimensions and Weight: The size and weight of a vending machine are vital for installation and transport logistics. Machines need to fit in designated spaces, and their weight impacts shipping costs and handling. Buyers should consider local regulations regarding size limits in public spaces and transportation methods.
-
Power Requirements: Different vending machines have varying power needs, often requiring specific voltage and amperage. Knowing the power specifications is crucial for ensuring compatibility with local electrical systems. This can prevent operational failures and additional installation costs.
-
Capacity: This refers to the number of items a vending machine can hold, impacting its profitability. A higher capacity machine can serve more customers before needing restocking, which is particularly beneficial in busy areas. Buyers should evaluate their target market and customer volume to select an appropriate capacity.
-
Payment Systems: Modern vending machines may support various payment methods, including cash, credit/debit cards, and mobile payment options. Understanding the payment capabilities is essential for catering to customer preferences and ensuring a smooth transaction experience.
-
Temperature Control: For machines that dispense perishable items, temperature control is crucial. Machines should maintain specific temperature ranges to ensure product freshness. Buyers should inquire about the temperature range and insulation properties to meet local health regulations.
Common Trade Terminology in Vending Machine Procurement
Familiarity with industry jargon can significantly enhance communication and negotiation processes in the procurement of discount vending machines. Here are key terms to understand:
-
OEM (Original Equipment Manufacturer): This term refers to companies that produce parts and equipment that may be marketed by another manufacturer. For buyers, knowing whether a vending machine is sourced from an OEM can provide insights into quality assurance and warranty options.
-
MOQ (Minimum Order Quantity): This is the smallest amount of product that a supplier is willing to sell. Understanding MOQ is crucial for budgeting and inventory management, particularly for buyers operating on tight margins or in regions with variable demand.
-
RFQ (Request for Quotation): An RFQ is a document sent to suppliers to solicit price quotes for specific products. B2B buyers should use RFQs to compare pricing and terms from multiple vendors, enabling informed purchasing decisions.
-
Incoterms (International Commercial Terms): These are standardized trade terms that define the responsibilities of buyers and sellers in international transactions. Familiarity with Incoterms helps buyers understand shipping costs, risk management, and delivery obligations.
-
Lead Time: This refers to the time taken from placing an order until it is delivered. Understanding lead time is essential for inventory planning and ensuring that machines are available when needed, especially in competitive markets.
-
Warranty: A warranty is a promise from the manufacturer regarding the condition of the machine and the service it will provide. Knowing warranty terms is essential for risk management and evaluating the long-term value of the investment.
By comprehensively understanding these technical properties and industry terms, B2B buyers from Africa, South America, the Middle East, and Europe can make informed decisions when procuring discount vending machines, ultimately enhancing their operational efficiency and customer satisfaction.
Navigating Market Dynamics, Sourcing Trends, and Sustainability in the discount vending machines Sector
Market Overview & Key Trends
The discount vending machine sector is witnessing transformative changes driven by technological advancements and shifting consumer preferences. Global factors such as urbanization, the rising demand for convenience, and the growth of cashless transactions are fueling market expansion. In particular, B2B buyers from regions like Africa, South America, the Middle East, and Europe should note the increasing integration of IoT (Internet of Things) in vending machines. This technology allows for real-time inventory management and enhances customer experience through personalized offerings.
Emerging trends also include the adoption of eco-friendly machines and sustainable product offerings. As consumers become more environmentally conscious, the demand for machines that offer organic, fair-trade, or locally sourced products is on the rise. Additionally, the shift toward remote monitoring capabilities is enabling operators to optimize their supply chains and reduce operational costs, making it crucial for B2B buyers to consider suppliers who invest in these technologies.
Furthermore, understanding regional market dynamics is essential. For example, in Africa, the growth of mobile payment systems has revolutionized vending machine transactions, while in Europe, stringent regulations regarding food safety and sustainability are shaping product offerings. B2B buyers should stay abreast of these developments to make informed sourcing decisions that align with both market demands and regulatory requirements.
Sustainability & Ethical Sourcing in B2B
Sustainability is becoming a cornerstone of business strategy within the discount vending machine sector. The environmental impact of vending operations—such as energy consumption, waste generation, and product sourcing—requires B2B buyers to prioritize sustainable practices. This includes selecting machines that utilize energy-efficient technologies and materials that reduce carbon footprints.
Moreover, ethical sourcing is gaining traction as consumers increasingly demand transparency in supply chains. B2B buyers should seek suppliers that prioritize ethical labor practices and environmentally friendly materials. Certifications such as Fair Trade, Organic, and FSC (Forest Stewardship Council) can help buyers identify products that meet sustainability standards. These certifications not only enhance brand reputation but also resonate with the growing base of eco-conscious consumers.
Implementing a sustainability framework can also lead to cost savings. For instance, energy-efficient vending machines can significantly lower operational costs over time. Additionally, suppliers who prioritize sustainability often have stronger resilience against supply chain disruptions, making them more reliable partners for B2B buyers.
Brief Evolution/History
The discount vending machine industry has evolved significantly since its inception in the early 20th century. Initially, vending machines offered simple snacks and beverages, but technological advancements have transformed them into sophisticated retail solutions. The introduction of electronic payment systems in the 1990s marked a turning point, allowing for cashless transactions and broader product assortments.
In recent years, the focus has shifted towards smart vending solutions that incorporate IoT technologies and sustainability practices. This evolution not only addresses consumer demands for convenience and choice but also aligns with the increasing emphasis on ethical sourcing and environmental stewardship. As the sector continues to innovate, B2B buyers have the opportunity to leverage these advancements to enhance their operations and meet market expectations.
Related Video: What global trade deals are really about (hint: it’s not trade) | Haley Edwards | TEDxMidAtlantic
Frequently Asked Questions (FAQs) for B2B Buyers of discount vending machines
-
What should I consider when vetting suppliers for discount vending machines?
When vetting suppliers, prioritize their experience in the vending industry, production capacity, and reputation. Request references from past clients, and assess their financial stability through credit checks. Additionally, verify their compliance with international standards and local regulations, particularly if you are sourcing from regions like Asia or Europe. Ensure they have a robust quality assurance process to minimize the risk of defects. -
Can I customize the vending machines to fit my brand?
Yes, many manufacturers offer customization options for discount vending machines. This can include branding with your logo, color schemes, and specific product selections. When discussing customization, inquire about design capabilities, lead times, and any additional costs associated with custom features. This ensures that the machines align with your business identity and meet customer preferences. -
What are the typical minimum order quantities (MOQs) and lead times?
MOQs for discount vending machines can vary significantly by supplier. Generally, you may find MOQs ranging from 5 to 50 units, depending on the manufacturer’s production capabilities and your customization requirements. Lead times typically range from 4 to 12 weeks, influenced by factors such as production schedules, shipping times, and any custom modifications. Always clarify these details upfront to avoid surprises in your supply chain. -
What payment terms should I expect when sourcing internationally?
Payment terms can vary widely, but common practices include advance payment, letter of credit, or staggered payments tied to production milestones. Assess the risks associated with each payment method, especially when dealing with international suppliers. It’s advisable to negotiate terms that provide adequate protection, such as partial payments upon order confirmation and the balance upon delivery, to mitigate risks in case of disputes. -
How can I ensure the quality of the machines meets my standards?
To ensure quality, request certifications from suppliers that demonstrate compliance with international safety and quality standards, such as ISO 9001. Establish clear quality control measures and inspection protocols before shipment. Consider engaging third-party inspection services to verify the machines meet your specifications and quality expectations. This proactive approach helps prevent costly issues after delivery. -
What logistics considerations should I keep in mind when importing vending machines?
Logistics for importing vending machines can be complex. First, evaluate shipping options, including freight forwarding services that specialize in heavy machinery. Factor in customs clearance processes, import duties, and local regulations in your destination country. Collaborating with experienced logistics providers can streamline the process, ensuring timely delivery and compliance with all legal requirements. -
What should I do if I encounter a dispute with my supplier?
In case of a dispute, start by communicating directly with your supplier to resolve the issue amicably. Document all correspondence for reference. If direct negotiation fails, consult your contract for dispute resolution procedures, which may include mediation or arbitration. Engaging a legal expert familiar with international trade can provide guidance on the best course of action and help protect your interests. -
Are there specific certifications I should look for in vending machines?
Yes, look for certifications that indicate compliance with safety and operational standards relevant to your market. Common certifications include CE marking in Europe, UL listing in North America, and compliance with local electrical safety standards. These certifications ensure that the vending machines are safe for consumer use and meet regulatory requirements, which is critical for minimizing liability and ensuring customer trust.
Strategic Sourcing Conclusion and Outlook for discount vending machines
As the demand for discount vending machines continues to grow across diverse markets, strategic sourcing emerges as a pivotal element for international B2B buyers. Key takeaways from this guide emphasize the importance of understanding local consumer behavior, evaluating supplier reliability, and leveraging technology for inventory management. By engaging in strategic sourcing, businesses can not only enhance operational efficiency but also ensure a competitive edge in pricing and product variety.
B2B buyers from Africa, South America, the Middle East, and Europe should prioritize partnerships with suppliers who demonstrate flexibility and innovation in their offerings. This approach will facilitate tailored solutions that cater to regional preferences and economic conditions. As the vending machine landscape evolves with advancements in payment technology and product selection, now is the time to invest in strategic sourcing initiatives.
Looking forward, businesses that adopt a proactive stance in sourcing will be well-positioned to capitalize on emerging trends and consumer demands. Embrace the opportunity to enhance your vending machine offerings and explore new markets—take the first step in transforming your sourcing strategy today.