Optimize Your Vending Machine Maintenance for Maximum
Guide to Vending Machine Maintenance
- Introduction: Navigating the Global Market for vending machine maintenance
- Understanding vending machine maintenance Types and Variations
- Key Industrial Applications of vending machine maintenance
- Strategic Material Selection Guide for vending machine maintenance
- In-depth Look: Manufacturing Processes and Quality Assurance for vending machine maintenance
- Comprehensive Cost and Pricing Analysis for vending machine maintenance Sourcing
- Spotlight on Potential vending machine maintenance Manufacturers and Suppliers
- Essential Technical Properties and Trade Terminology for vending machine maintenance
- Navigating Market Dynamics, Sourcing Trends, and Sustainability in the vending machine maintenance Sector
- Frequently Asked Questions (FAQs) for B2B Buyers of vending machine maintenance
- Strategic Sourcing Conclusion and Outlook for vending machine maintenance
Introduction: Navigating the Global Market for vending machine maintenance
In the rapidly evolving landscape of global commerce, vending machines have emerged as pivotal players in the retail environment, offering convenience and accessibility to consumers worldwide. However, the effectiveness of these machines hinges significantly on regular and effective maintenance. For international B2B buyers, particularly from Africa, South America, the Middle East, and Europe, understanding the nuances of vending machine maintenance is crucial. This guide serves as a comprehensive resource, illuminating the critical aspects of maintenance strategies that ensure optimal performance and longevity of vending machines.
The scope of this guide encompasses a variety of essential topics, including types of maintenance services, materials required for repairs, manufacturing and quality control standards, and insights into reliable suppliers. Additionally, it offers a detailed analysis of costs associated with maintenance and an overview of current market trends. By addressing frequently asked questions, this guide empowers buyers to make informed sourcing decisions that align with their operational needs and budgetary constraints.
Equipped with this knowledge, B2B buyers will not only enhance their procurement strategies but also foster stronger relationships with suppliers, ensuring that their vending operations remain efficient and profitable. This resource is designed to navigate the complexities of vending machine maintenance, ultimately contributing to sustained business growth and customer satisfaction.
Understanding vending machine maintenance Types and Variations
Type Name | Key Distinguishing Features | Primary B2B Applications | Brief Pros & Cons for Buyers |
---|---|---|---|
Preventive Maintenance | Scheduled checks and servicing to prevent issues | Retail environments, offices, schools | Pros: Reduces downtime, extends machine life. Cons: Requires regular scheduling and potential costs. |
Corrective Maintenance | Repairs conducted after a malfunction occurs | All vending machine locations | Pros: Immediate response to issues. Cons: Can lead to longer downtimes and increased costs if not managed well. |
Predictive Maintenance | Uses data analytics to predict failures | High-traffic locations, tech-savvy environments | Pros: Minimizes unexpected breakdowns, cost-efficient over time. Cons: Requires investment in technology and training. |
Remote Monitoring | Real-time tracking of machine performance | Large networks of machines, franchises | Pros: Instant alerts for issues, efficient management. Cons: Initial setup can be expensive and complex. |
Cleaning and Sanitization | Regular cleaning to maintain hygiene standards | Food and beverage vending machines | Pros: Ensures compliance with health regulations, enhances customer satisfaction. Cons: Labor-intensive and may disrupt service during cleaning. |
Preventive Maintenance
Preventive maintenance involves routine inspections and servicing of vending machines to identify and address potential issues before they escalate. This type of maintenance is particularly suitable for retail environments, offices, and educational institutions where machines are frequently used. B2B buyers should consider the cost of regular maintenance contracts against the potential savings from reduced downtime and extended equipment lifespan.
Corrective Maintenance
Corrective maintenance refers to repairs made after a vending machine has malfunctioned. This approach is common across all vending machine locations, as it addresses immediate issues. While it can provide quick fixes, businesses should be cautious of the potential for longer downtimes and increased operational costs if problems are not managed proactively. Buyers must weigh the benefits of immediate repairs against the risk of recurring issues.
Predictive Maintenance
Predictive maintenance leverages data analytics to forecast when a machine might fail, allowing for timely interventions. This method is best suited for high-traffic locations and businesses that are technologically inclined. Although it can minimize unexpected breakdowns, predictive maintenance requires initial investments in technology and training, making it crucial for buyers to evaluate the long-term cost-effectiveness of such systems.
Remote Monitoring
Remote monitoring systems enable real-time performance tracking of vending machines, alerting operators to any issues as they arise. This type of maintenance is particularly beneficial for large networks of machines, such as those operated by franchises. While it offers significant management efficiencies, the initial setup can be complex and costly. Buyers should consider their capacity to manage and respond to alerts effectively.
Cleaning and Sanitization
Regular cleaning and sanitization are essential for maintaining hygiene standards, especially in food and beverage vending machines. This maintenance type is vital for compliance with health regulations and improving customer satisfaction. However, it can be labor-intensive and may require machines to be temporarily out of service during cleaning. B2B buyers should factor in the balance between maintaining hygiene and minimizing service disruptions when planning their maintenance schedules.
Key Industrial Applications of vending machine maintenance
Industry/Sector | Specific Application of vending machine maintenance | Value/Benefit for the Business | Key Sourcing Considerations for this Application |
---|---|---|---|
Retail | Regular servicing of snack and beverage machines | Ensures product availability and customer satisfaction | Availability of local service providers, parts compatibility |
Healthcare | Maintenance of vending machines for medical supplies | Provides quick access to essential items, enhancing patient care | Compliance with health regulations, reliability of service |
Education | Upkeep of vending machines in schools and universities | Supports student convenience, promotes healthy options | Nutritional compliance, payment system integration |
Hospitality | Maintenance of vending machines in hotels | Enhances guest experience, increases revenue streams | Brand reputation, machine reliability, service responsiveness |
Transportation | Servicing vending machines in airports and train stations | Provides travelers with quick access to refreshments | Location accessibility, machine adaptability to high traffic |
Key Industrial Applications of Vending Machine Maintenance
Retail
In the retail sector, vending machines are commonly used for snacks and beverages, providing convenience to customers. Regular maintenance ensures that machines are stocked, clean, and functioning properly, which is crucial for customer satisfaction and retention. International buyers in this sector should consider the availability of local service providers who can offer timely repairs and parts compatibility to minimize downtime and maintain operational efficiency.
Healthcare
Vending machines in healthcare settings often dispense medical supplies or healthy snacks, providing quick access to essential items for patients and staff. Maintenance is critical to ensure that these machines remain stocked and compliant with health regulations. Buyers in this sector must prioritize sourcing vendors who understand the specific compliance requirements, reliability of service, and the need for quick response times to avoid disruptions in patient care.
Education
Educational institutions utilize vending machines to offer convenient food and drink options for students. Regular maintenance not only ensures that machines are operational but also that they provide healthy choices, aligning with nutritional guidelines. B2B buyers in this sector should focus on suppliers that can integrate payment systems and ensure compliance with health standards, thus enhancing the overall student experience.
Hospitality
In the hospitality industry, vending machines serve guests in hotels, providing a variety of snacks and beverages. Proper maintenance of these machines is essential for enhancing the guest experience and generating additional revenue streams. Buyers should consider the reputation of service providers, the reliability of machines, and how quickly they can respond to service requests, as these factors can significantly impact guest satisfaction.
Transportation
Vending machines located in airports and train stations cater to travelers in need of quick refreshments. Maintenance in these high-traffic areas is vital to ensure machines are consistently stocked and operational. International buyers must assess the adaptability of machines to different environments and the accessibility of service providers to ensure that machines are well-maintained and capable of meeting the demands of a diverse customer base.
Related Video: How to Start a Vending Machine Business, Cost, Tips, How Much You Make
Strategic Material Selection Guide for vending machine maintenance
When selecting materials for vending machine maintenance, it is crucial to consider their properties, advantages, disadvantages, and applicability in various international markets. Below is an analysis of four common materials used in vending machine maintenance, focusing on their performance characteristics and implications for B2B buyers from Africa, South America, the Middle East, and Europe.
1. Stainless Steel
Key Properties:
Stainless steel is known for its excellent corrosion resistance, high strength, and ability to withstand extreme temperatures. It typically has a temperature rating of up to 800°F (427°C) and is resistant to various chemicals.
Pros & Cons:
The durability of stainless steel makes it a preferred choice for components exposed to moisture and food products. However, it is more expensive than other materials, such as carbon steel, and can be challenging to machine due to its hardness.
Impact on Application:
Stainless steel is compatible with a wide range of media, including water, soft drinks, and snacks. Its hygienic properties make it suitable for food-related applications.
Considerations for International Buyers:
Compliance with international standards such as ASTM A240 and DIN 1.4301 is essential. Buyers should also consider local regulations regarding food safety and material certifications.
2. Carbon Steel
Key Properties:
Carbon steel is known for its high strength and toughness, with a typical temperature rating of around 400°F (204°C). It is less corrosion-resistant than stainless steel but can be treated for enhanced durability.
Pros & Cons:
This material is cost-effective and easy to manufacture, making it a popular choice for structural components. However, it is susceptible to rusting and may require protective coatings, which can add to maintenance costs.
Impact on Application:
Carbon steel is suitable for non-corrosive applications but may not be ideal for environments with high humidity or exposure to liquids.
Considerations for International Buyers:
Buyers should ensure compliance with ASTM A36 or equivalent standards. The cost-effectiveness of carbon steel can be appealing, but its long-term maintenance needs should be factored into the total cost of ownership.
3. Plastic (Polypropylene)
Key Properties:
Polypropylene is a lightweight, flexible plastic with good chemical resistance and a temperature rating of up to 200°F (93°C). It is not as strong as metals but is highly resistant to moisture and corrosion.
Pros & Cons:
The low weight and cost of polypropylene make it an attractive option for various components, particularly in non-structural applications. However, its lower strength limits its use in high-stress environments.
Impact on Application:
Polypropylene is ideal for components that require frequent cleaning and exposure to food products, such as trays and containers.
Considerations for International Buyers:
Buyers should verify compliance with food safety regulations and standards such as FDA and EU regulations. The availability of recycled polypropylene can also be a selling point in environmentally conscious markets.
4. Aluminum
Key Properties:
Aluminum is lightweight, has good corrosion resistance, and can withstand temperatures up to 600°F (316°C). It is also easy to machine and fabricate.
Pros & Cons:
Aluminum’s strength-to-weight ratio makes it suitable for various applications, including structural components. However, it can be more expensive than carbon steel and may not be as durable under extreme conditions.
Impact on Application:
Aluminum is compatible with a range of media and is often used for components that require a balance of strength and weight.
Considerations for International Buyers:
Buyers should ensure compliance with standards such as ASTM B221. The lightweight nature of aluminum can reduce shipping costs, making it an appealing choice for international transactions.
Material | Typical Use Case for vending machine maintenance | Key Advantage | Key Disadvantage/Limitation | Relative Cost (Low/Med/High) |
---|---|---|---|---|
Stainless Steel | Structural components, food contact areas | Excellent corrosion resistance | Higher cost, machining complexity | High |
Carbon Steel | Non-corrosive structural components | Cost-effective, strong | Susceptible to rust, requires protection | Low |
Plastic (Polypropylene) | Trays, containers, non-structural parts | Lightweight, cost-effective | Lower strength, limited high-stress use | Low |
Aluminum | Structural and decorative components | Good strength-to-weight ratio | More expensive, less durable in extremes | Medium |
This guide provides a comprehensive overview of material options for vending machine maintenance, helping international B2B buyers make informed decisions based on their specific needs and market conditions.
In-depth Look: Manufacturing Processes and Quality Assurance for vending machine maintenance
In the competitive landscape of vending machine maintenance, understanding the manufacturing processes and quality assurance standards is crucial for B2B buyers. This section explores the key manufacturing stages, techniques, quality control (QC) measures, and international standards that guide the industry.
Manufacturing Processes
The manufacturing of vending machines involves several critical stages, each designed to ensure the final product meets the necessary functional and aesthetic requirements. The main stages include:
1. Material Preparation
This initial stage involves sourcing high-quality materials that meet the specifications required for vending machine construction. Materials typically include steel for the chassis, plastic for housing, and electronic components for functionality. Key considerations in this phase include:
- Sourcing: Establishing reliable suppliers who can provide materials that comply with international standards.
- Material Testing: Conducting tests to verify that the materials meet durability and safety requirements.
2. Forming
Forming processes shape the prepared materials into the components of the vending machine. Common techniques include:
- Sheet Metal Stamping: Used for creating the outer casing and internal structures.
- Injection Molding: Employed for plastic parts, ensuring precise shapes and sizes.
- Laser Cutting: Utilized for creating intricate designs and ensuring high accuracy.
These processes require advanced machinery and skilled operators to maintain quality throughout production.
3. Assembly
Once the components are formed, they are assembled into a complete vending machine. This stage includes:
- Sub-assembly: Smaller groups of components are pre-assembled before final assembly.
- Integration of Electronics: Installing wiring, control boards, and payment systems.
- Quality Checks: Continuous inspections during assembly to identify defects early.
4. Finishing
The finishing stage enhances the vending machine’s appearance and functionality. Techniques include:
- Painting and Coating: Applying protective finishes to prevent corrosion and wear.
- Quality Control Checks: Final inspections to ensure all components function correctly and meet design specifications.
Quality Assurance
Quality assurance is vital in ensuring that vending machines are safe, reliable, and meet customer expectations. International standards and specific industry requirements guide these processes.
Relevant International Standards
B2B buyers should be familiar with several international standards that influence manufacturing and quality assurance:
- ISO 9001: This standard focuses on quality management systems, ensuring that manufacturers consistently provide products that meet customer and regulatory requirements.
- CE Marking: A certification indicating conformity with health, safety, and environmental protection standards for products sold within the European Economic Area.
- API Standards: Relevant for components that may affect the machine’s performance, particularly in specific markets like oil and gas.
Quality Control Checkpoints
The quality control process includes multiple checkpoints to ensure product integrity:
- Incoming Quality Control (IQC): Inspecting materials upon arrival to confirm they meet specifications.
- In-Process Quality Control (IPQC): Monitoring the manufacturing process to catch defects early.
- Final Quality Control (FQC): Conducting thorough inspections of the completed vending machines to ensure they meet all standards.
Common Testing Methods
To verify the quality of vending machines, manufacturers may employ various testing methods, including:
- Functional Testing: Ensuring all components operate correctly.
- Stress Testing: Simulating real-world conditions to identify potential weaknesses.
- Safety Testing: Checking for compliance with safety standards, particularly for electrical components.
Verifying Supplier Quality Control
For international B2B buyers, verifying the quality control practices of potential suppliers is critical. Here are some actionable steps:
- Conduct Audits: Arrange for on-site audits to evaluate the manufacturing processes and quality control measures in place.
- Request Quality Reports: Suppliers should provide documentation of their quality control processes, including test results and compliance certificates.
- Engage Third-Party Inspectors: Utilize independent inspection services to assess the quality of products before shipment. This is particularly important for buyers in regions like Africa and South America, where local regulations may differ.
QC and Certification Nuances for International Buyers
B2B buyers from Africa, South America, the Middle East, and Europe must navigate various certification and quality control nuances:
- Understanding Local Regulations: Each region may have specific requirements for product safety and quality. Buyers should familiarize themselves with these regulations to ensure compliance.
- Leveraging Certifications: Suppliers with internationally recognized certifications (e.g., ISO, CE) are often more reliable and can streamline compliance with local regulations.
- Building Relationships: Establishing strong relationships with suppliers can facilitate better communication regarding quality assurance practices and any necessary adjustments to meet local standards.
In summary, understanding the manufacturing processes and quality assurance measures for vending machine maintenance is essential for international B2B buyers. By focusing on key stages, relevant standards, and effective verification methods, buyers can ensure they partner with reputable suppliers who deliver high-quality products.
Related Video: China’s Top 5 Manufacturing and Mass Production Videos | by @miracleprocess
Comprehensive Cost and Pricing Analysis for vending machine maintenance Sourcing
Cost Structure in Vending Machine Maintenance
Understanding the cost structure for vending machine maintenance is vital for international B2B buyers. The primary cost components include:
-
Materials: This encompasses replacement parts such as motors, sensors, and electronic components. Quality materials can significantly impact the durability and efficiency of vending machines.
-
Labor: Skilled labor for maintenance, including technicians who perform repairs and routine checks, is a significant cost factor. Labor costs can vary widely depending on the region, with higher rates often found in Europe compared to Africa or South America.
-
Manufacturing Overhead: This includes costs associated with the production of components, such as facility expenses, utilities, and indirect labor. Overhead can be a substantial part of the overall cost, influencing pricing strategies.
-
Tooling: This refers to the equipment and tools needed for maintenance and repairs. Investment in quality tooling can lead to greater efficiency and lower long-term costs.
-
Quality Control (QC): Ensuring that all parts meet specified standards incurs additional costs. QC processes are essential for maintaining high service levels and reducing future repair needs.
-
Logistics: Transportation costs for parts and maintenance teams can vary by region and impact overall pricing. Consideration of logistics is crucial, especially for international buyers who must factor in shipping times and costs.
-
Margin: Suppliers typically add a margin to cover risks and ensure profitability. This can vary based on market competition and the specific service level agreements.
Price Influencers
Several factors can influence the pricing of vending machine maintenance services:
-
Volume/MOQ (Minimum Order Quantity): Larger orders often lead to discounts, making it beneficial for buyers to consolidate maintenance needs.
-
Specifications/Customization: Customization of maintenance services can lead to increased costs. Buyers should clearly define their needs to avoid unexpected charges.
-
Materials: The quality and type of materials used will impact pricing. Higher-quality materials may incur a higher upfront cost but can lead to lower long-term maintenance expenses.
-
Quality and Certifications: Suppliers with recognized quality certifications may charge a premium, but this can assure buyers of reliability and compliance with international standards.
-
Supplier Factors: The reputation and reliability of the supplier can influence pricing. Established suppliers may charge more due to their proven track record.
-
Incoterms: Understanding Incoterms is essential for international transactions, as they define the responsibilities of buyers and sellers regarding shipping, insurance, and tariffs.
Buyer Tips
For B2B buyers, especially in regions like Africa, South America, the Middle East, and Europe, effective negotiation and understanding of costs can lead to better deals:
-
Negotiate: Engage suppliers in discussions about pricing, especially for larger contracts or long-term agreements. Flexibility in payment terms or volume commitments can result in better pricing.
-
Focus on Cost-Efficiency: Assess the total cost of ownership rather than just initial pricing. Consider long-term maintenance costs and potential downtime when evaluating supplier offers.
-
Understand Pricing Nuances: Be aware of local market conditions that can affect pricing, such as currency fluctuations, regional labor costs, and material availability.
-
Evaluate Total Cost of Ownership (TCO): Calculate not only the upfront costs but also ongoing maintenance, repair, and potential downtime costs to make informed decisions.
-
Stay Informed on Market Trends: Keeping abreast of industry trends can provide leverage in negotiations and help buyers understand when to commit to long-term contracts versus seeking flexibility.
Disclaimer
Prices and costs mentioned are indicative and can vary based on the specific needs, market conditions, and supplier negotiations. Always conduct thorough due diligence to obtain accurate quotes and service agreements tailored to your requirements.
Spotlight on Potential vending machine maintenance Manufacturers and Suppliers
This section offers a look at a few manufacturers active in the ‘vending machine maintenance’ market. This is a representative sample for illustrative purposes; B2B buyers must conduct their own extensive due diligence before any engagement. Information is synthesized from public sources and general industry knowledge.
Essential Technical Properties and Trade Terminology for vending machine maintenance
Key Technical Properties for Vending Machine Maintenance
Understanding the essential technical properties of vending machines is crucial for international B2B buyers, especially when considering long-term maintenance and operational efficiency. Here are several critical specifications:
-
Material Grade
– Definition: The classification of materials used in the construction of vending machines, such as stainless steel, plastic, or aluminum.
– Importance: Higher-grade materials enhance durability and resistance to corrosion, which is vital for machines exposed to various environments. For instance, stainless steel is preferred in humid regions, as it minimizes maintenance needs and extends the life of the machine. -
Tolerance Levels
– Definition: The allowable limits of variation in the dimensions of machine parts.
– Importance: Proper tolerance ensures that components fit together correctly, preventing operational failures. In vending machines, precise tolerances in parts like coin mechanisms are essential for reliable performance, which directly affects customer satisfaction. -
Power Consumption
– Definition: The amount of electricity a vending machine uses during operation.
– Importance: Energy-efficient machines reduce operational costs and are more environmentally friendly. B2B buyers should consider power ratings, especially in regions with high electricity costs, as this can significantly impact profit margins over time.
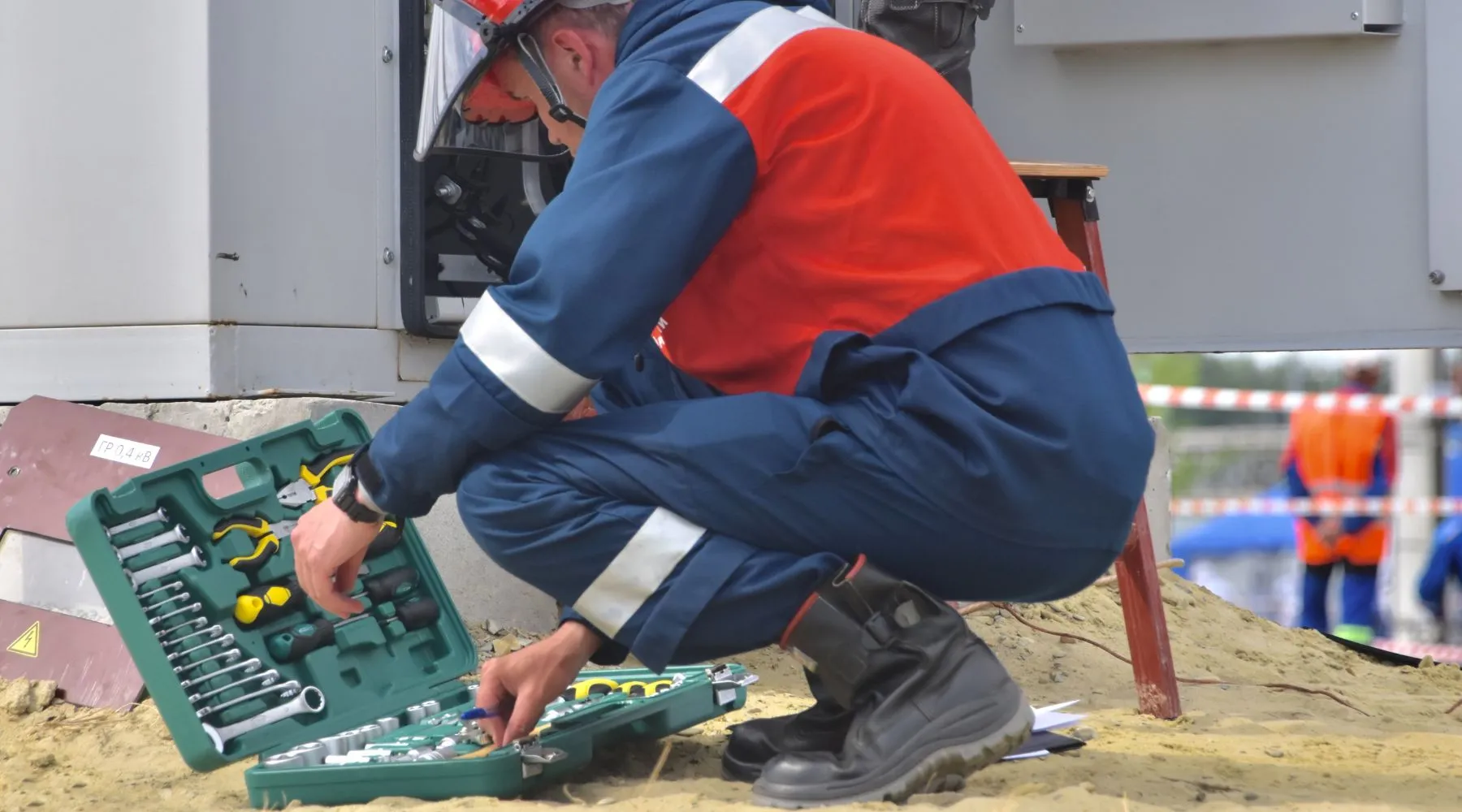
Illustrative Image (Source: Google Search)
-
Capacity Specifications
– Definition: The maximum number of products a vending machine can hold and dispense.
– Importance: Understanding capacity is critical for inventory management. Buyers need to align machine capacity with expected sales volume to ensure that machines are stocked appropriately and do not lead to lost sales due to stockouts. -
Temperature Range
– Definition: The operating temperature range within which the vending machine can function effectively.
– Importance: For machines dispensing perishable items, maintaining the right temperature is crucial. Buyers should ensure that machines can handle local climate conditions, particularly in hot regions, to prevent product spoilage.
Common Trade Terms in Vending Machine Maintenance
Familiarity with industry jargon is essential for effective communication and negotiation. Here are some common terms:
-
OEM (Original Equipment Manufacturer)
– Definition: A company that produces parts or equipment that may be marketed by another manufacturer.
– Usage: When sourcing parts for maintenance, buyers often prefer OEM parts to ensure compatibility and reliability, which can reduce downtime. -
MOQ (Minimum Order Quantity)
– Definition: The smallest quantity of a product that a supplier is willing to sell.
– Usage: Understanding MOQ is crucial for buyers to manage inventory levels and costs effectively. Suppliers may impose MOQs to ensure cost efficiency in production.
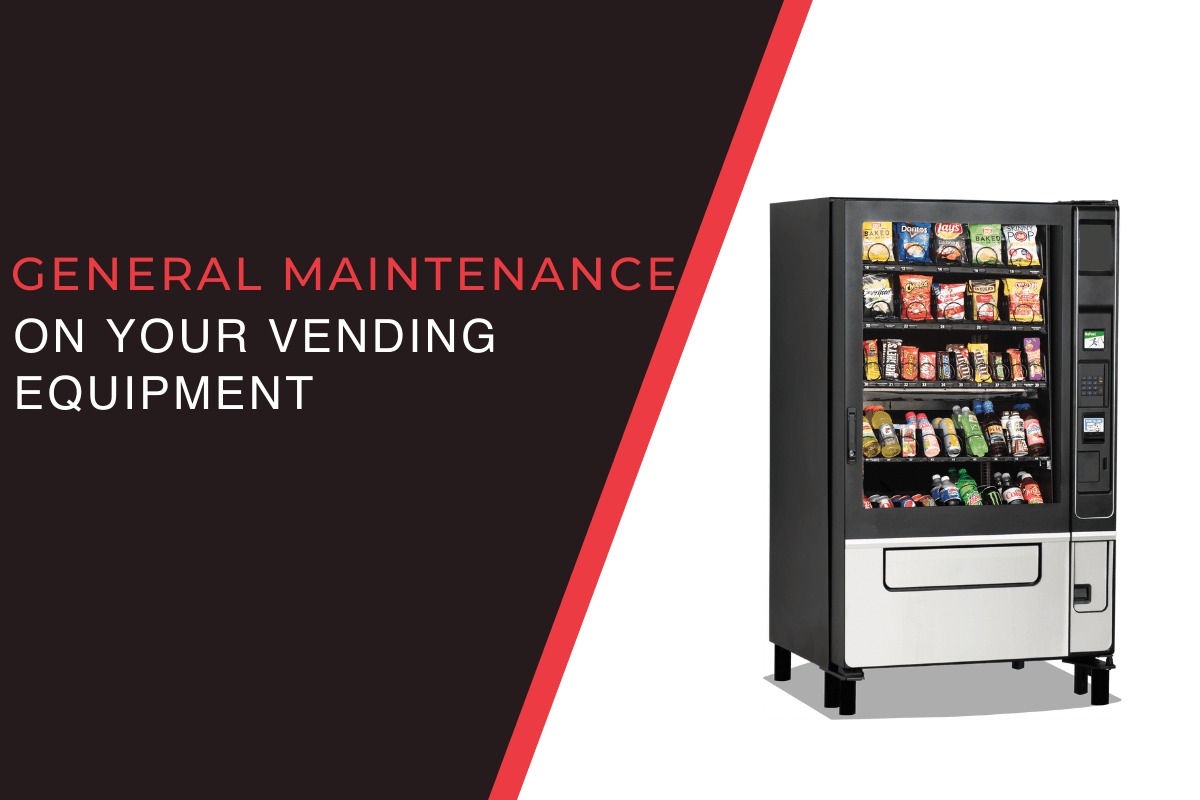
Illustrative Image (Source: Google Search)
-
RFQ (Request for Quotation)
– Definition: A document issued by a buyer to request price proposals from suppliers for specific products or services.
– Usage: This is a standard practice in procurement, allowing buyers to compare offers and make informed decisions based on pricing and terms. -
Incoterms (International Commercial Terms)
– Definition: A set of international rules that define the responsibilities of sellers and buyers for the delivery of goods under sales contracts.
– Usage: Familiarity with Incoterms helps buyers understand shipping responsibilities, costs, and risks, which is crucial for international transactions, especially when sourcing from different continents. -
Lead Time
– Definition: The amount of time from the initiation of a process until its completion, particularly in the context of manufacturing and delivery.
– Usage: Understanding lead times is vital for inventory planning and ensuring that vending machines are operational when needed.
By grasping these technical properties and trade terms, B2B buyers can make more informed decisions when purchasing and maintaining vending machines, ultimately enhancing operational efficiency and profitability.
Navigating Market Dynamics, Sourcing Trends, and Sustainability in the vending machine maintenance Sector
Market Overview & Key Trends
The global vending machine maintenance sector is experiencing significant growth driven by several factors. Increasing urbanization and busy lifestyles, particularly in regions like Africa and South America, are fueling the demand for convenient, on-the-go food and beverage options. According to recent market studies, the vending machine industry is expected to reach $25 billion by 2025, with a notable shift towards automation and smart technology integration.
Emerging trends include the adoption of IoT (Internet of Things) devices, which allow for real-time monitoring of machine performance and inventory levels. This technology is particularly beneficial for international B2B buyers, enabling predictive maintenance and reducing downtime. Additionally, cashless payment systems are becoming a standard, catering to consumer preferences for contactless transactions. In regions such as Europe, buyers are increasingly looking for advanced vending solutions that incorporate features like personalization and user-friendly interfaces.
Furthermore, sustainability is becoming a crucial consideration in sourcing decisions. As environmental awareness grows, buyers are prioritizing vendors who offer eco-friendly machines and maintenance practices. This shift is particularly evident in the Middle East and Europe, where regulatory frameworks are encouraging businesses to adopt greener solutions.
Sustainability & Ethical Sourcing in B2B
Sustainability is no longer just a trend; it is a crucial factor influencing the vending machine maintenance sector. The environmental impact of vending machines—ranging from energy consumption to waste generation—necessitates a focus on sustainable practices. International B2B buyers are increasingly aware of the importance of sourcing from companies that prioritize sustainability, including those that use energy-efficient machines and eco-friendly materials.
Ethical supply chains are vital in maintaining a competitive edge. Buyers should seek vendors that can provide transparency regarding their sourcing practices, ensuring that materials used in vending machines are sustainably obtained. This includes the use of certified materials and compliance with international environmental standards. Certifications such as ISO 14001 for environmental management systems can serve as indicators of a vendor’s commitment to sustainability.
Moreover, incorporating ‘green’ certifications in vending machine maintenance not only enhances brand reputation but also meets the growing consumer demand for environmentally responsible products. As a result, international buyers should prioritize partnerships with suppliers who demonstrate a strong commitment to sustainability and ethical sourcing practices.
Brief Evolution/History
The vending machine industry has evolved significantly since its inception in the late 19th century. Originally designed to dispense simple products like postcards and gum, vending machines have transformed into sophisticated retail solutions offering a wide array of goods, including fresh food and beverages. The introduction of electronic payment systems in the 1990s marked a pivotal change, allowing for cashless transactions and enhanced user experiences.
In recent years, the focus has shifted towards automation and sustainability, driven by technological advancements and changing consumer preferences. As B2B buyers navigate this dynamic landscape, understanding the historical context of vending machine maintenance can inform better sourcing decisions and strategic partnerships.
Related Video: ONESOURCE Global Trade: A Truly Global Solution
Frequently Asked Questions (FAQs) for B2B Buyers of vending machine maintenance
-
How do I vet suppliers for vending machine maintenance services?
When vetting suppliers, consider their industry experience, client testimonials, and certifications. Conduct background checks to confirm their reputation and reliability in the market. Request references and follow up with previous clients to assess their satisfaction with the services provided. Additionally, evaluate their response time and customer support capabilities to ensure they can meet your specific maintenance needs. -
Can I customize vending machine maintenance services to fit my business needs?
Yes, many suppliers offer customizable maintenance packages tailored to your specific operational requirements. Discuss your unique needs with potential suppliers, including service frequency, machine types, and additional services like remote monitoring or inventory management. Ensure the supplier can adapt their service offerings to align with your business objectives, enhancing efficiency and reducing downtime. -
What are the minimum order quantities (MOQ) and lead times for maintenance services?
Minimum order quantities for vending machine maintenance can vary by supplier and the scope of services required. Some suppliers may have flexible MOQs based on the type of contract (e.g., annual vs. ad-hoc services). Lead times also depend on the availability of parts and the supplier’s scheduling capabilities. Always clarify these terms upfront to avoid delays in service delivery. -
What payment terms should I expect when sourcing maintenance services?
Payment terms can vary widely among suppliers. Common practices include upfront deposits, milestone payments based on service delivery, or net payment terms (e.g., net 30 or net 60). It’s crucial to negotiate terms that suit your cash flow and budget. Ensure you understand any penalties for late payments and inquire about discounts for early payments or long-term contracts. -
What quality assurance measures should I look for in maintenance services?
Look for suppliers that adhere to recognized quality assurance standards, such as ISO certifications or industry-specific guidelines. Inquire about their maintenance protocols and whether they use certified technicians for service delivery. Additionally, assess their warranty policies and post-service support, which can indicate the quality and reliability of their maintenance services. -
Are there specific certifications I should verify with suppliers?
Yes, you should verify relevant certifications such as ISO 9001 for quality management systems, as well as any local or regional certifications pertinent to vending machine operations. Additionally, check for specialized training certifications for technicians, which can demonstrate their expertise in handling specific types of machines. This ensures that the maintenance services you receive meet industry standards. -
What logistics considerations should I keep in mind when sourcing maintenance services?
Logistics play a crucial role in the timely delivery of maintenance services. Confirm the supplier’s geographic coverage and their ability to service your location efficiently. Discuss response times for urgent maintenance needs and how they handle parts inventory to minimize downtime. Understanding their logistics processes can help you assess the reliability of their service delivery. -
How can disputes over maintenance services be resolved effectively?
Establish clear communication channels and service level agreements (SLAs) with your supplier to minimize disputes. In the event of a disagreement, begin by discussing the issue directly with the supplier to seek a resolution. If necessary, consider mediation or arbitration as alternative dispute resolution methods. Ensure both parties document all agreements and communications to support a fair resolution process.
Strategic Sourcing Conclusion and Outlook for vending machine maintenance
In conclusion, strategic sourcing for vending machine maintenance is a pivotal element for international B2B buyers aiming to enhance operational efficiency and customer satisfaction. By prioritizing partnerships with reliable service providers, businesses can ensure timely repairs, minimize downtime, and maintain optimal machine performance. Investing in preventive maintenance not only reduces long-term costs but also extends the lifespan of vending machines, translating to higher returns on investment.
Key takeaways for buyers include evaluating potential vendors based on their service quality, geographic coverage, and responsiveness. Establishing clear service level agreements (SLAs) will also ensure accountability and performance benchmarks are met consistently.
Looking ahead, the vending machine market is poised for innovation, with advancements in technology and customer engagement. International buyers from regions such as Africa, South America, the Middle East, and Europe should actively seek out partnerships that align with their growth objectives. Now is the time to invest in strategic sourcing for vending machine maintenance, paving the way for enhanced service delivery and customer loyalty in an increasingly competitive landscape. Embrace these insights to drive your business forward and capitalize on emerging opportunities.