Mastering Vending Machine Products: A Comprehensive Guide
Guide to Vending Machine Products
- Introduction: Navigating the Global Market for vending machine products
- Understanding vending machine products Types and Variations
- Key Industrial Applications of vending machine products
- Strategic Material Selection Guide for vending machine products
- In-depth Look: Manufacturing Processes and Quality Assurance for vending machine products
- Comprehensive Cost and Pricing Analysis for vending machine products Sourcing
- Spotlight on Potential vending machine products Manufacturers and Suppliers
- Essential Technical Properties and Trade Terminology for vending machine products
- Navigating Market Dynamics, Sourcing Trends, and Sustainability in the vending machine products Sector
- Frequently Asked Questions (FAQs) for B2B Buyers of vending machine products
- Strategic Sourcing Conclusion and Outlook for vending machine products
Introduction: Navigating the Global Market for vending machine products
In an increasingly fast-paced retail environment, vending machine products are more than just a convenience; they represent a dynamic opportunity for international B2B buyers to tap into evolving consumer behaviors. As urbanization accelerates and lifestyles shift, the demand for accessible, on-the-go solutions has surged, making vending machines a lucrative investment across diverse regions, including Africa, South America, the Middle East, and Europe.
This guide serves as a comprehensive resource for navigating the global market of vending machine products. It covers essential topics such as types of vending machines, materials used, manufacturing and quality control standards, and supplier evaluations. Additionally, it delves into cost considerations, market trends, and addresses common FAQs to equip buyers with the knowledge needed for informed sourcing decisions.
By leveraging insights from this guide, B2B buyers can identify key suppliers and technologies that align with their business needs, facilitating smarter purchasing strategies. Understanding the intricacies of vending machine products empowers companies to enhance customer engagement, optimize inventory management, and ultimately drive profitability. Whether you are a buyer in Colombia seeking innovative solutions or a distributor in Egypt looking to expand your product offerings, this guide provides the critical framework to succeed in the global vending machine market.
Understanding vending machine products Types and Variations
Type Name | Key Distinguishing Features | Primary B2B Applications | Brief Pros & Cons for Buyers |
---|---|---|---|
Snack Vending Machines | Dispenses packaged snacks; typically has a glass front | Offices, schools, public areas | Pros: Low maintenance; high demand. Cons: Limited health options. |
Beverage Vending Machines | Offers various drinks; often refrigerated | Gyms, universities, transportation hubs | Pros: High turnover; diverse selection. Cons: Requires power and maintenance. |
Healthy Vending Machines | Focus on nutritious snacks and beverages | Corporate wellness programs, schools | Pros: Appeals to health-conscious consumers. Cons: Higher initial investment. |
Smart Vending Machines | Equipped with IoT technology for real-time monitoring | Tech-savvy locations, luxury venues | Pros: Enhanced inventory management; data analytics. Cons: Higher cost; requires tech support. |
Automated Retail Kiosks | Larger format; can sell electronics or apparel | Airports, shopping malls | Pros: High-value products; multifunctional. Cons: Complex logistics; higher security needs. |
Snack Vending Machines
Snack vending machines are designed to dispense a variety of packaged snacks, from chips to candy bars. They are commonly found in offices, schools, and public areas, offering convenience to consumers. For B2B buyers, the low maintenance requirements and high consumer demand make these machines appealing. However, they often lack healthy options, which could deter health-conscious clients.
Beverage Vending Machines
These machines provide a range of beverages, including soft drinks, juices, and bottled water, often featuring refrigeration to keep drinks cool. They are ideal for placement in gyms, universities, and transportation hubs due to their high turnover rates. B2B buyers should consider the diverse selection these machines offer, although they require consistent power and maintenance to operate effectively.
Healthy Vending Machines
Targeting the growing market of health-conscious consumers, healthy vending machines focus on offering nutritious snacks and beverages. These machines are suitable for corporate wellness programs and schools, promoting healthier eating habits. While they may require a higher initial investment, the appeal to health-focused consumers can lead to increased sales and customer loyalty, making them a worthwhile consideration for B2B buyers.
Smart Vending Machines
Equipped with Internet of Things (IoT) technology, smart vending machines allow for real-time monitoring of inventory and sales data. This feature is particularly beneficial for tech-savvy locations and luxury venues where customer experience is a priority. While the initial investment is higher, the enhanced inventory management and data analytics capabilities can lead to better decision-making and increased profitability for B2B buyers.
Automated Retail Kiosks
Automated retail kiosks are larger vending machines capable of dispensing high-value items such as electronics or apparel. These kiosks are often seen in airports and shopping malls, providing consumers with convenient access to a wide range of products. B2B buyers should weigh the benefits of multifunctionality and higher product value against the complexities of logistics and increased security needs associated with these machines.
Related Video: CS 198-126: Lecture 12 – Diffusion Models
Key Industrial Applications of vending machine products
Industry/Sector | Specific Application of Vending Machine Products | Value/Benefit for the Business | Key Sourcing Considerations for this Application |
---|---|---|---|
Healthcare | Medication dispensing | Improved patient compliance and reduced medication errors | Regulatory compliance, security features, and temperature control |
Education | Snack and beverage vending for schools | Enhanced student satisfaction and increased revenue for schools | Product variety, health regulations, and payment options |
Corporate Offices | Office supplies vending | Increased employee productivity and reduced downtime | Inventory management system, product range, and replenishment frequency |
Hospitality | Food and beverage vending in hotels | 24/7 availability of refreshments and increased guest satisfaction | Quality of products, payment integration, and location analysis |
Transportation | Vending machines at airports and train stations | Convenience for travelers and additional revenue stream | Space constraints, product selection, and security measures |
Healthcare: Medication Dispensing
In healthcare settings, vending machines are increasingly used for medication dispensing, providing patients with easy access to prescribed medications. This application addresses the challenge of medication adherence by offering a secure and efficient way to dispense drugs. For international B2B buyers, especially in regions like Africa and South America, sourcing machines that comply with local health regulations and feature robust security measures is crucial. Additionally, temperature control is essential for medications that require refrigeration, making it a vital consideration in procurement.
Education: Snack and Beverage Vending for Schools
Schools leverage vending machines to provide snacks and beverages, enhancing student satisfaction and generating additional revenue. This application helps address the need for convenient food options on campus, particularly during breaks. Buyers in Europe and the Middle East should consider local health regulations regarding nutritional standards, as well as the variety of products offered to cater to diverse student preferences. Implementing a robust inventory management system can also help in efficiently managing restocking schedules.
Corporate Offices: Office Supplies Vending
Vending machines that dispense office supplies are becoming popular in corporate environments, allowing employees to quickly access necessary items without leaving their workspaces. This application boosts productivity by minimizing downtime spent searching for supplies. For B2B buyers in regions like Africa and Europe, it is essential to ensure that the vending machines have an effective inventory management system in place. Additionally, considerations around product range and replenishment frequency are important to maintain a seamless operation.
Hospitality: Food and Beverage Vending in Hotels
Hotels utilize vending machines to offer food and beverages, providing guests with 24/7 access to refreshments. This application enhances guest satisfaction by ensuring that food options are readily available, especially during late hours. B2B buyers in the hospitality sector must prioritize the quality of products and the integration of payment systems that accommodate various payment methods. Furthermore, conducting a location analysis to determine the best spots for vending machines can optimize guest engagement.
Transportation: Vending Machines at Airports and Train Stations
Vending machines located in transportation hubs like airports and train stations cater to the needs of travelers seeking quick snacks and beverages. This application addresses the convenience factor, providing an additional revenue stream for operators. Key sourcing considerations for B2B buyers include managing space constraints, ensuring a diverse product selection that appeals to international travelers, and implementing security measures to protect the machines and their contents.
Related Video: How to Start a Vending Machine Business, Cost, Tips, How Much You Make
Strategic Material Selection Guide for vending machine products
When selecting materials for vending machine products, it is essential to consider various factors that influence performance, durability, and cost. Below is an analysis of four common materials used in vending machine construction, focusing on their properties, advantages and disadvantages, application impacts, and specific considerations for international B2B buyers.
1. Stainless Steel
Key Properties: Stainless steel is known for its excellent corrosion resistance, high strength, and ability to withstand extreme temperatures. It typically has a temperature rating of up to 800°F (427°C) and is highly resistant to rust and staining.
Pros & Cons: The primary advantage of stainless steel is its durability and long lifespan, making it suitable for high-traffic environments. However, it is more expensive than other materials, which can increase the overall cost of vending machine products. Manufacturing complexity can also be higher due to the need for specialized tools and techniques.
Impact on Application: Stainless steel is compatible with a wide range of media, including food and beverages, making it ideal for vending machines. Its non-reactive nature ensures that it does not alter the taste or quality of the products dispensed.
Considerations for International Buyers: Buyers in regions like Africa and South America should ensure compliance with local health and safety regulations regarding food contact materials. Common standards such as ASTM and ISO certifications are essential for ensuring product quality and safety.
2. Polycarbonate
Key Properties: Polycarbonate is a high-impact, transparent plastic known for its excellent clarity and UV resistance. It can withstand temperatures from -40°F to 240°F (-40°C to 115°C) and has a high impact resistance, making it less likely to shatter.
Pros & Cons: The key advantage of polycarbonate is its lightweight nature, which reduces shipping costs and makes installation easier. However, it may not be as durable as metals in high-stress applications and can be prone to scratching.
Impact on Application: Polycarbonate is often used for transparent panels in vending machines, allowing visibility of products while providing adequate protection. It is compatible with a variety of media, but care must be taken with hot products as excessive heat can deform the material.
Considerations for International Buyers: Buyers should verify that the polycarbonate used complies with food safety standards in their region. For example, in Europe, compliance with REACH regulations is crucial.
3. Aluminum
Key Properties: Aluminum is lightweight, corrosion-resistant, and has a good strength-to-weight ratio. It can handle temperatures up to 1,200°F (649°C) and is often treated with anodizing to enhance its corrosion resistance.
Pros & Cons: The primary advantage of aluminum is its lower weight compared to stainless steel, which can lead to cost savings in shipping and installation. However, it is less durable under heavy impact and can be more expensive than some plastics.
Impact on Application: Aluminum is commonly used in the structural components of vending machines, providing a good balance of strength and weight. It is suitable for various media, including non-corrosive liquids.
Considerations for International Buyers: Buyers should ensure that aluminum components meet relevant international standards, such as ASTM or DIN, to guarantee quality and performance. Additionally, understanding local recycling regulations can be beneficial, as aluminum is highly recyclable.
4. Glass
Key Properties: Glass is a rigid, transparent material that offers excellent visibility and aesthetic appeal. It can withstand moderate temperatures but is susceptible to breakage under impact.
Pros & Cons: The advantage of glass is its premium look and feel, which can enhance the customer experience. However, its fragility can lead to higher replacement costs and safety concerns, particularly in high-traffic areas.
Impact on Application: Glass is often used for display panels in vending machines, providing a clear view of products. It is compatible with a wide range of products but requires careful handling and installation to prevent breakage.
Considerations for International Buyers: Buyers must consider local regulations regarding glass use in vending machines, especially in terms of safety and consumer protection. Compliance with standards such as EN 12150 (for tempered glass) is essential in Europe.
Summary Table
Material | Typical Use Case for vending machine products | Key Advantage | Key Disadvantage/Limitation | Relative Cost (Low/Med/High) |
---|---|---|---|---|
Stainless Steel | Structural components, food contact surfaces | Excellent durability and corrosion resistance | Higher cost, manufacturing complexity | High |
Polycarbonate | Transparent panels | Lightweight, good impact resistance | Prone to scratching, lower durability | Medium |
Aluminum | Structural components | Lightweight, good strength-to-weight ratio | Less durable under heavy impact | Medium |
Glass | Display panels | Premium look and visibility | Fragile, higher replacement costs | Medium |
This strategic material selection guide provides a comprehensive overview for international B2B buyers, helping them make informed decisions that align with their operational needs and regional compliance requirements.
In-depth Look: Manufacturing Processes and Quality Assurance for vending machine products
In the competitive landscape of vending machine products, understanding the manufacturing processes and quality assurance protocols is essential for international B2B buyers. This section outlines the key stages of manufacturing, the techniques employed, and the quality control measures that ensure product reliability and compliance with international standards.
Manufacturing Processes
The manufacturing of vending machine products typically involves several key stages, including material preparation, forming, assembly, and finishing. Each stage is critical in ensuring that the final product meets the necessary specifications and quality standards.
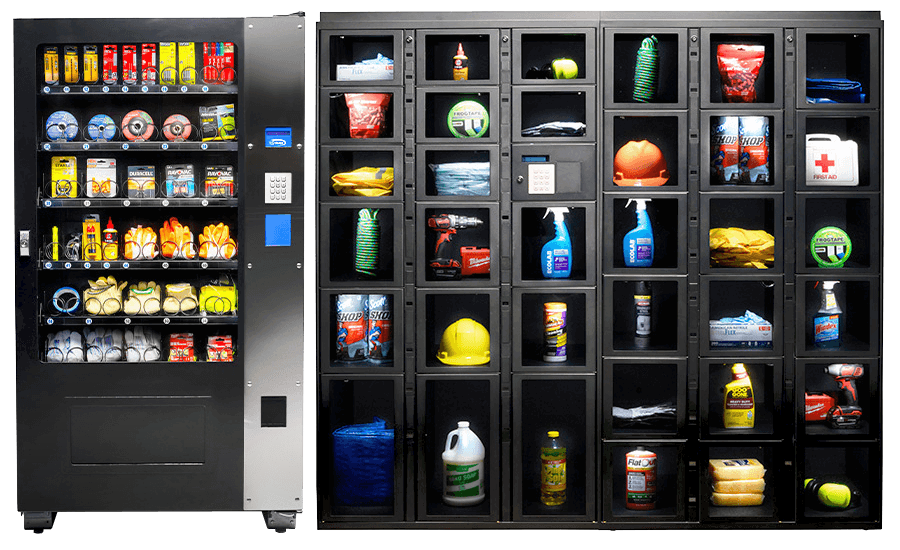
Illustrative Image (Source: Google Search)
1. Material Preparation
The first step in the manufacturing process is the preparation of materials. This involves sourcing high-quality raw materials such as metals, plastics, and electronic components. Suppliers should be vetted for their sourcing practices to ensure materials are durable and compliant with environmental regulations.
- Key Considerations:
- Verify the origin of materials, especially metals and plastics, to ensure they meet international standards.
- Check for certifications that confirm the materials’ quality and sustainability.
2. Forming
In this stage, raw materials are shaped into parts that will form the structure of the vending machine. Common techniques used in forming include:
- Stamping: Used for creating metal parts through high-pressure machines.
- Injection Molding: Essential for producing plastic components with precision.
- Laser Cutting: Provides high accuracy in cutting metal and other materials.
These techniques should be chosen based on the specific requirements of the machine components, balancing cost and performance.
3. Assembly
Once the components are formed, they are assembled into the final product. This process often involves:
- Automated Assembly Lines: Utilizing robotics for precision and speed.
- Manual Assembly: For complex parts requiring skilled labor.
During this stage, it is crucial to maintain strict assembly protocols to prevent defects.
- Best Practices:
- Implement a systematic approach to assembly, including detailed work instructions.
- Utilize tools like assembly jigs to ensure consistent quality across units.
4. Finishing
The final stage involves the application of finishes that enhance the product’s durability and aesthetics. Common finishing techniques include:
- Painting or Powder Coating: Provides a protective layer and improves appearance.
- Electroplating: Used for metal parts to enhance corrosion resistance.
- Quality Inspections: Conducted post-finishing to ensure that the finishes meet the required standards.
Quality Assurance
Quality assurance is a critical component of the manufacturing process for vending machine products. It ensures that every unit meets international quality standards and customer expectations.
International Standards
Compliance with established international standards is vital for B2B buyers. Key standards include:
- ISO 9001: Focuses on quality management systems, ensuring consistent quality across processes.
- CE Marking: Required for products sold in the European Economic Area, indicating compliance with health, safety, and environmental protection standards.
- API (American Petroleum Institute): Relevant for components used in vending machines that require safety and reliability in various environments.
Quality Control Checkpoints
Quality control is typically structured around several key checkpoints throughout the manufacturing process:
- Incoming Quality Control (IQC): Inspects raw materials upon arrival to ensure they meet specifications.
- In-Process Quality Control (IPQC): Monitors quality during the manufacturing process to catch defects early.
- Final Quality Control (FQC): Conducts thorough inspections of finished products before shipping.
Common Testing Methods
Quality control incorporates various testing methods to ensure product reliability, including:
- Functional Testing: Verifies that the vending machine operates as intended.
- Durability Testing: Assesses the machine’s performance under different conditions to ensure longevity.
- Safety Testing: Ensures that the machine complies with safety regulations, protecting users and operators.
Verifying Supplier Quality Control
For international B2B buyers, verifying a supplier’s quality control processes is crucial to mitigate risks associated with product quality. Here are actionable strategies:
- Conduct Audits: Request to perform on-site audits of the manufacturing facilities to evaluate their processes and quality control measures.
- Review Quality Reports: Ask for detailed quality control reports that outline the processes, results of inspections, and any corrective actions taken.
- Third-Party Inspections: Engage independent inspection agencies to conduct assessments of the manufacturing process and product quality before shipment.
Quality Control and Certification Nuances
International buyers, particularly from regions like Africa, South America, the Middle East, and Europe, should be aware of specific nuances in quality control and certification:
- Local Regulations: Understand the local regulations and standards applicable in your region. For example, CE marking is crucial for products sold in Europe, while different certifications may apply in Africa or South America.
- Cultural Factors: Be mindful of cultural differences that may affect communication and expectations regarding quality. Establish clear communication channels with suppliers to ensure mutual understanding.
- Supply Chain Dynamics: Consider the complexities of international supply chains, including potential delays and compliance issues that can affect quality. Build relationships with reliable logistics partners to ensure timely delivery and compliance with quality standards.
By focusing on these manufacturing processes and quality assurance practices, B2B buyers can make informed decisions when sourcing vending machine products, ensuring they receive high-quality, reliable products that meet their operational needs.
Related Video: China’s Top 5 Manufacturing and Mass Production Videos | by @miracleprocess
Comprehensive Cost and Pricing Analysis for vending machine products Sourcing
To effectively navigate the sourcing of vending machine products, international B2B buyers must understand both the cost structure and pricing dynamics that influence their purchasing decisions. A comprehensive analysis reveals critical components and factors that can aid in making informed decisions, particularly for buyers from Africa, South America, the Middle East, and Europe.
Cost Components
-
Materials: The cost of raw materials, such as metals, plastics, and electronic components, constitutes a significant portion of the overall expense. Prices can fluctuate based on global supply chain conditions, so buyers should stay informed about market trends affecting these materials.
-
Labor: Labor costs vary by region and impact the manufacturing price of vending machines. For buyers sourcing from countries with higher labor costs, it’s crucial to evaluate whether the benefits of local sourcing outweigh potential savings from overseas suppliers.
-
Manufacturing Overhead: This includes expenses related to utilities, factory maintenance, and administrative costs. Understanding the overhead costs can help buyers assess the competitiveness of supplier pricing.
-
Tooling: Initial tooling costs for custom designs or specialized vending machines can be significant. Buyers should factor in these costs when considering customized orders, especially for unique product offerings.
-
Quality Control (QC): Ensuring product quality is critical, especially in vending machines that must endure frequent usage. Invest in suppliers who demonstrate rigorous QC processes to avoid future costs related to product failures or customer dissatisfaction.
-
Logistics: Shipping costs can vary widely based on the origin and destination of the products. Buyers should consider the full logistics chain, including freight costs, customs duties, and local delivery charges, to gauge the total expenditure.
- Margin: Suppliers typically include a profit margin in their pricing, which can vary by manufacturer. Understanding the standard margins in the industry can provide leverage during negotiations.
Price Influencers
-
Volume/MOQ (Minimum Order Quantity): Larger orders often lead to lower per-unit costs. Buyers should assess their demand to negotiate favorable terms based on volume.
-
Specifications and Customization: Custom features or specifications can increase costs significantly. Buyers should clearly communicate their requirements to avoid unexpected expenses.
-
Materials and Quality Certifications: Higher-quality materials or certifications (e.g., ISO) can lead to increased prices. Buyers should weigh the benefits of quality against cost to ensure value for money.
-
Supplier Factors: The reputation and reliability of suppliers can influence pricing. Established suppliers may charge a premium for their experience and quality assurance.
-
Incoterms: Understanding Incoterms is crucial for determining who bears responsibility for shipping and risk at various points in the supply chain. This knowledge can help buyers make more cost-effective decisions.
Buyer Tips
-
Negotiation: Always engage in negotiations with a clear understanding of the cost components. This empowers buyers to discuss pricing more effectively and seek discounts or better terms.
-
Cost-Efficiency: Evaluate the Total Cost of Ownership (TCO), which includes not just the purchase price but also maintenance, logistics, and lifecycle costs. This holistic view can lead to smarter sourcing decisions.
-
Pricing Nuances for International Buyers: When sourcing from different regions, be aware of currency fluctuations, potential tariffs, and regional market conditions. Local partnerships can also help navigate these complexities.
Disclaimer
Prices for vending machine products can vary significantly based on market conditions, supplier relationships, and order specifics. The figures presented are indicative and should be verified with suppliers for accurate quotations.
Spotlight on Potential vending machine products Manufacturers and Suppliers
- (No specific manufacturer data was available or requested for detailed profiling in this section for vending machine products.)*
Essential Technical Properties and Trade Terminology for vending machine products
Key Technical Properties of Vending Machine Products
Understanding the essential technical properties of vending machine products is crucial for international B2B buyers to make informed purchasing decisions. Here are several key specifications that should be considered:
-
Material Grade
– Definition: This refers to the quality and type of materials used in the construction of vending machines, such as stainless steel, plastic, or glass.
– Importance: High-grade materials enhance durability, resistance to corrosion, and overall machine longevity, which is essential for reducing maintenance costs and ensuring reliability in various environments. -
Tolerance
– Definition: Tolerance indicates the allowable deviation in dimensions and mechanical properties of machine components.
– Importance: Precise tolerances ensure that parts fit together correctly, which is vital for the proper functioning of vending machines. Inaccurate tolerances can lead to malfunctions or increased wear and tear, impacting operational efficiency. -
Power Consumption
– Definition: This specification measures the energy required for the vending machine to operate, usually indicated in watts or kilowatts.
– Importance: Lower power consumption is desirable as it translates to reduced operational costs, particularly in regions where energy prices are high. Additionally, energy-efficient machines can appeal to environmentally conscious consumers.
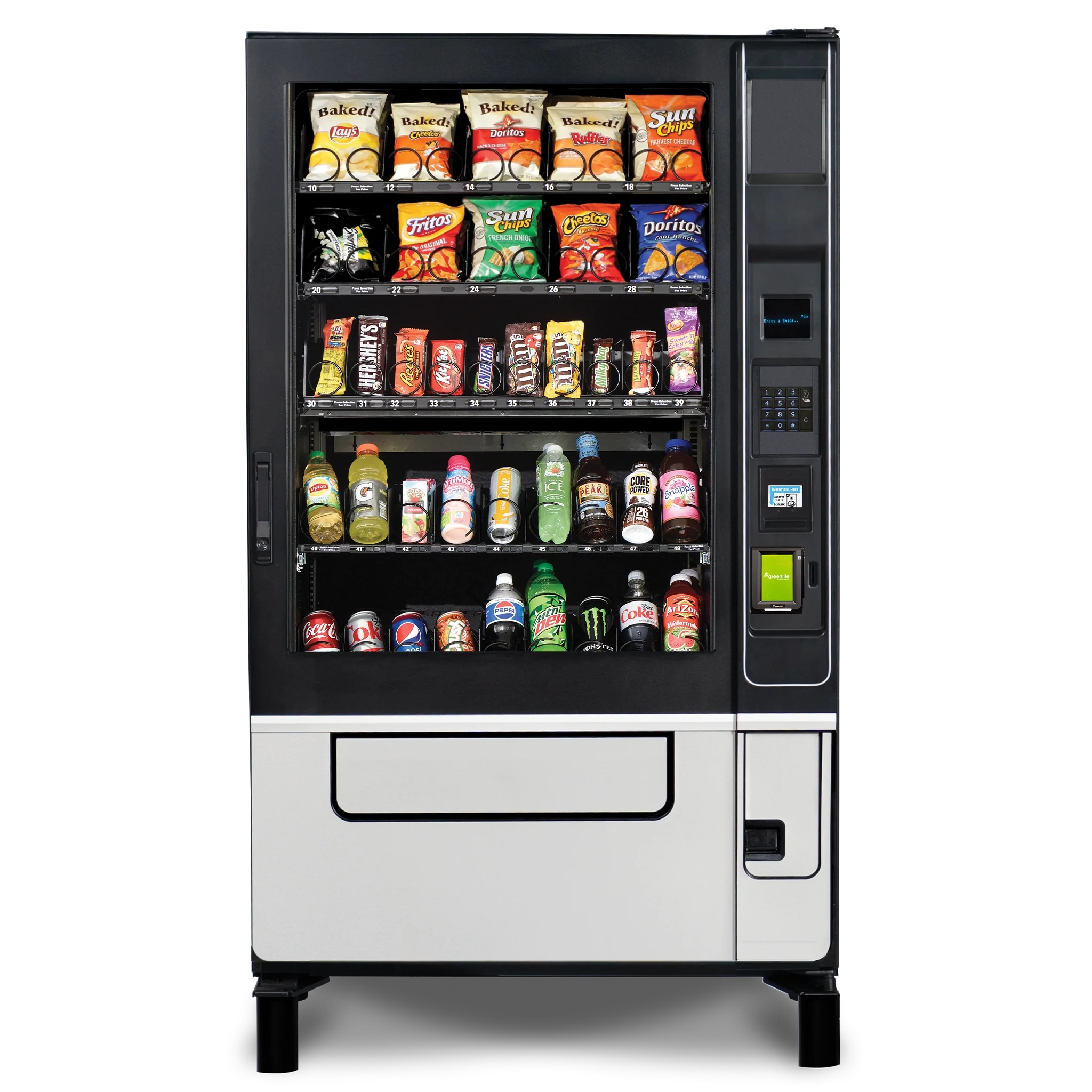
Illustrative Image (Source: Google Search)
-
Capacity
– Definition: Capacity refers to the number of items a vending machine can hold, often measured in number of slots or volume.
– Importance: Understanding capacity is crucial for inventory management and sales forecasting. A machine with a larger capacity can serve more customers and generate higher revenue, making it essential for locations with high foot traffic. -
Technology Integration
– Definition: This encompasses the inclusion of features such as cashless payment systems, remote monitoring, and inventory management software.
– Importance: Advanced technology improves customer experience, enhances sales tracking, and facilitates efficient inventory management. For B2B buyers, investing in technologically integrated machines can lead to long-term savings and increased profitability.
Common Trade Terminology in the Vending Machine Industry
Familiarity with industry-specific terminology is essential for effective communication and negotiation in the vending machine sector. Below are key terms that B2B buyers should know:
-
OEM (Original Equipment Manufacturer)
– Definition: An OEM is a company that produces parts or equipment that may be marketed by another manufacturer.
– Relevance: Engaging with OEMs can provide buyers access to high-quality components and machines tailored to their specifications, often resulting in better pricing and product reliability. -
MOQ (Minimum Order Quantity)
– Definition: MOQ is the smallest number of units a supplier is willing to sell.
– Relevance: Understanding MOQ helps buyers assess their purchasing capacity and negotiate better terms, especially when entering new markets where demand may be uncertain. -
RFQ (Request for Quotation)
– Definition: An RFQ is a document issued by a buyer to solicit price bids from suppliers for specific products or services.
– Relevance: Issuing RFQs enables buyers to compare offers, assess market prices, and secure favorable terms, ensuring cost-effectiveness in procurement. -
Incoterms (International Commercial Terms)
– Definition: Incoterms are a set of rules that define the responsibilities of sellers and buyers regarding shipping, risk, and insurance.
– Relevance: Familiarity with Incoterms is critical for international transactions, as they clarify costs and risks associated with shipping, helping buyers avoid unexpected expenses. -
Lead Time
– Definition: Lead time refers to the amount of time it takes from placing an order to receiving the product.
– Relevance: Understanding lead times is vital for inventory planning and ensuring that vending machines are stocked in a timely manner, which can directly impact customer satisfaction and sales.
By grasping these technical properties and trade terminologies, B2B buyers can navigate the vending machine market more effectively, ensuring that their procurement processes align with their operational goals and customer needs.
Navigating Market Dynamics, Sourcing Trends, and Sustainability in the vending machine products Sector
Market Overview & Key Trends
The vending machine products sector is undergoing a significant transformation, driven by technological advancements and shifting consumer preferences. Global drivers such as urbanization, increased on-the-go consumption, and the demand for contactless payment solutions are reshaping the market landscape. For international B2B buyers, particularly from Africa, South America, the Middle East, and Europe, understanding these dynamics is crucial for making informed sourcing decisions.
Emerging B2B Tech Trends: Smart vending machines equipped with IoT capabilities are gaining traction. These machines provide real-time inventory management, allowing businesses to monitor sales data remotely and optimize product offerings based on consumer behavior. For instance, platforms like Selfly Cloud offer advanced analytics that enable businesses to tailor their inventory to local tastes, improving customer satisfaction and sales.
Sourcing Trends: There’s a noticeable shift towards integrated product-service solutions, known as Product-as-a-Service (PaaS). This model allows businesses to provide not just products but also ongoing support and maintenance, fostering long-term relationships with customers. For buyers in emerging markets, adopting PaaS can lead to cost savings and improved service delivery.
Market Dynamics: The competitive landscape is increasingly characterized by sustainability initiatives. Buyers are now prioritizing vendors that demonstrate environmental stewardship through ethical sourcing practices. Additionally, the rise of e-commerce is influencing vending machine placements, with more machines being installed in high-traffic areas like transport hubs and shopping malls to capture the growing footfall.
Sustainability & Ethical Sourcing in B2B
Sustainability is not merely a trend; it has become a fundamental expectation for businesses in the vending machine products sector. The environmental impact of traditional vending operations, particularly concerning energy consumption and product waste, has prompted a shift towards more sustainable practices.
Importance of Ethical Supply Chains: B2B buyers are increasingly scrutinizing their supply chains for ethical practices. This includes evaluating suppliers based on their labor practices, environmental impact, and compliance with international standards. Establishing transparent supply chains helps mitigate risks and enhance brand reputation.
Green Certifications and Materials: Buyers should seek vendors who utilize eco-friendly materials and possess certifications like ISO 14001 or LEED. These certifications indicate a commitment to environmental management and sustainability. Incorporating biodegradable packaging, energy-efficient machines, and products sourced from sustainable practices not only helps reduce the carbon footprint but also resonates with environmentally conscious consumers.
Brief Evolution/History
The vending machine industry has evolved significantly since its inception in the early 20th century, transitioning from simple mechanical devices to sophisticated automated retail solutions. Initially, vending machines offered basic items like cigarettes and candy; however, advancements in technology have led to the introduction of smart machines capable of dispensing a wide variety of products, including fresh food and beverages.
This evolution has been fueled by the integration of digital payment systems, real-time inventory management, and data analytics. These innovations have transformed vending machines into convenient, efficient, and sustainable retail solutions, aligning with the modern consumer’s expectations for accessibility and variety. For B2B buyers, understanding this historical context can inform their sourcing strategies and investment decisions in the current market.
Related Video: Global Trade & Logistics – What is Global Trade?
Frequently Asked Questions (FAQs) for B2B Buyers of vending machine products
-
What should I consider when vetting suppliers of vending machine products?
When vetting suppliers, focus on their reputation, experience, and customer reviews. Verify their certifications and compliance with international standards, particularly regarding safety and quality. Request samples of their vending machines to assess quality firsthand. Additionally, inquire about their production capacity and reliability in meeting deadlines. Establishing a strong communication line can also help gauge their responsiveness and willingness to collaborate. -
Can I customize vending machines to suit my market’s preferences?
Most suppliers offer customization options, allowing you to tailor the vending machines to meet local tastes and preferences. This can include adjusting product selections, machine designs, and branding elements. Discuss your specific requirements with potential suppliers and ensure they have the capability to provide the necessary modifications. It’s essential to review their previous customization projects to evaluate their expertise in this area. -
What are the typical minimum order quantities (MOQs) and lead times for vending machines?
Minimum order quantities can vary significantly between suppliers and often depend on the type of vending machine. Generally, MOQs range from a few units to several dozen. Lead times can also differ, typically ranging from 4 to 12 weeks, depending on the complexity of the machines and the supplier’s current workload. Always clarify these details upfront to align your purchasing schedule with your business needs. -
What payment terms should I expect when sourcing vending machines internationally?
Payment terms can vary, but many suppliers require a deposit (often 30-50%) upon order confirmation, with the balance due before shipment or upon delivery. It’s advisable to negotiate terms that align with your cash flow and risk tolerance. Additionally, consider using secure payment methods and contracts that outline terms clearly to protect both parties in the transaction. -
What quality assurance measures should suppliers provide?
Reputable suppliers will have quality assurance processes in place, including testing machines for functionality and safety before shipment. Request documentation of their QA protocols, such as inspection reports or compliance certifications. Understanding their warranty policies is also crucial; a solid warranty can indicate the manufacturer’s confidence in their product quality. -
How do logistics and shipping work for international orders of vending machines?
Logistics for international orders involve coordination between the supplier, shipping companies, and customs authorities. Discuss with your supplier how they handle shipping, including freight costs, delivery timelines, and insurance. Ensure that they provide all necessary documentation for customs clearance to avoid delays. Familiarize yourself with local import regulations to ensure smooth delivery. -
What steps should I take if a dispute arises with a supplier?
In the event of a dispute, maintain clear and open communication with the supplier to address the issue directly. Refer to the contract terms to clarify responsibilities and obligations. If necessary, consider mediation or arbitration as a means to resolve conflicts amicably. It’s also advisable to document all communications and transactions, as this can be beneficial if legal action becomes necessary. -
What certifications should I look for in vending machine products?
Key certifications to look for include ISO standards, CE marking for safety in Europe, and local certifications relevant to your market (such as SONCAP in Nigeria). These certifications demonstrate compliance with quality and safety regulations. Request documentation from suppliers that verifies their compliance with these standards to ensure that the products you source meet necessary safety and operational requirements.
Strategic Sourcing Conclusion and Outlook for vending machine products
In summary, strategic sourcing in the vending machine sector is crucial for international B2B buyers aiming to enhance operational efficiency and customer satisfaction. By leveraging smart vending technologies, such as real-time inventory management and advanced analytics, businesses can not only optimize their product offerings but also respond dynamically to consumer preferences. Furthermore, adopting sustainable practices—like reducing food waste through intelligent inventory management—can significantly bolster a company’s reputation and profitability.
As the market continues to evolve with innovations such as AI-driven vending solutions and Product-as-a-Service (PaaS) models, buyers are encouraged to stay ahead of these trends. Embracing these advancements will enable businesses to foster long-term relationships with suppliers, ensuring a competitive edge in the marketplace.
For international B2B buyers in regions like Africa, South America, the Middle East, and Europe, now is the time to engage with suppliers who prioritize strategic sourcing and innovative solutions. By doing so, you position your business not only for immediate success but also for sustained growth in a rapidly changing retail landscape. Take action today to explore partnerships that will elevate your vending machine offerings and meet the demands of tomorrow’s consumers.